Коробка передач - Курсовая работа по деталям машин



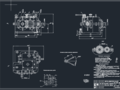
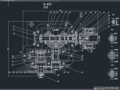
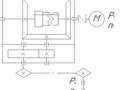
- Добавлен: 11.05.2021
- Размер: 7 MB
- Закачек: 1
Описание
Курсовая работа по деталям машин.
Состав проекта
![]() ![]() ![]() |
![]() ![]() ![]() |
![]() |
![]() ![]() ![]() |
Дополнительная информация
Содержание
Введение
1 Выбор электродвигателя и кинематический расчет
2 Определение мощностей и передаваемых крутящих моментов
3 Расчет передач
3.1 Расчет конической передачи с прямым зубом быстроходной ступени коробки передач
3.2 Расчет цилиндрической косозубой передачи тихоходной ступени коробки передач
3.3 Расчет цепной передачи
4 Предварительный расчет диаметров валов
5 Подбор и проверочный расчет муфт
5.1 Муфта упругая втулочно-пальцевая
5.2 Кулачковая сцепная муфта
6 Предварительный подбор подшипников
7 Компоновочная схема и выбор способа смазывания передач и подшипников, определение размеров корпусных деталей
8 Расчет валов по эквивалентному моменту
8.1 Проверочный расчет ведущего вала
8.2 Проверочный расчет промежуточного вала
8.3 Проверочный расчет ведомого вала
9 Расчет подшипников на долговечность
9.1 Расчет подшипников ведущего вала
9.2 Расчет подшипников промежуточного вала
9.3 Расчет подшипников ведомого вала
10 Подбор и проверочный расчет шпоночных соединений
11 Назначение посадок, шероховатости поверхностей, выбор степеней точности и назначение допусков формы и расположения поверхностей
12 Расчет валов на выносливость
12.1 Расчет ведущего вала
12.2 Расчет промежуточного вала
12.3 Расчет ведомого вала
13 Расчет механизмов управления
14 Описание сборки коробки
15 Регулировка подшипников и зацеплений
15.1 Регулировка зубчатых зацеплений
15.2 Регулировка подшипников
16 Описание монтажной схемы. Сборка и регулировка привода
Литература
Введение
Редуктором называется механизм, состоящий из зубчатых или червячных передач, выполненный в виде отдельного органа и служащий для передачи вращения от вала двигателя к валу рабочей машины.
Назначение редуктора - понижение угловой скорости и повышение вращающего момента ведомого вала по сравнению с ведущим.
Применение редукторов обусловлено экономическими соображениями. Масса и стоимость двигателя при одинаковой мощности понижаются с увеличением его быстроходности. Оказывается, экономически целесообразным применение быстроходных двигателей с понижающей передачей, вместо тихоходного двигателя без передачи. Наиболее широко используются асинхронные двигатели с частотой 750 и 1500 оборотов в минуту.
Редуктор состоит из корпуса, в котором размещают элементы передачи - зубчатые колеса, валы, подшипники и т.д.
Редукторы классифицируют по следующим основным признакам: типу передачи (зубчатые, червячные или зубчато-червячные); числу ступеней (одноступенчатые, двухступенчатые и т.д.); типу зубчатых колес (цилиндрические, конические и т.д.); относительному расположению валов в пространстве (горизонтальные, вертикальные); особенностям кинематической схемы (развернутая, соосная, с раздвоенной ступенью и т.д.). В данном проекте разрабатывается двухступенчатая коническоцилиндрическая реверсивная коробка передач.
Зубчатые передачи являются основным видом передач в машиностроении. Их основные преимущества: высокая нагрузочная способность, и, как следствие, малые габариты; большая долговечность и надежность работы; высокий КПД; постоянство передаточного отношения; возможность применения в широком диапазоне мощностей, скоростей, передаточных отношений. Недостатки: шум при работе, невозможность бесступенчатого изменения передаточного числа, незащищенность при перегрузках, возможность возникновения значительных динамических нагрузок из-за вибрации.
Подшипники служат опорами для валов. Они воспринимают радиальные и осевые нагрузки, приложенные к валу, и сохраняют заданное положение оси вращения вала. В данной коробке передач используются шариковые радиальноупорные, роликовые радиально-упорные подшипники, а также шариковые радиальные подшипники, которые воспринимают радиальную и осевую нагрузки в конической и цилиндрической передачах.
Описание сборки коробки
Перед сборкой внутреннюю полость корпуса коробки тщательно очищают и покрывают маслостойкой краской. Сборку производят в соответствии с чертежом общего вида коробки, начиная с узлов валов:
- на шлицы быстроходного вала 9 устанавливают муфту 17, втулки 15, в которые закладывают шпонки 57 и ставят шестерни 14, после чего на вал устанавливают втулку 16 и насаживают подшипники 45 и 47, предварительно нагретые в масле до 80100°С, подшипник 47 фиксируют стопорным кольцом 41;
- на промежуточный вал-шестерню 21 напрессовывают нагретые подшипники 46, затягивают их гайками 18 с шайбами 59, после чего устанавливают колесо конической передачи 20, фиксируют его в осевом направлении шайбой с болтом 33;
- на тихоходный вал 30 устанавливают зубчатое колесо 29, затем устанавливают втулку 28 и подшипники 48, нагретые предварительно в масле.
Собранные валы укладывают в основание корпуса коробки 3 и надевают крышку корпуса 4, покрывая предварительно поверхности стыка крышки и корпуса спиртовым лаком. Для базирования крышки относительно корпуса используют конические штифты 58. После этого ставят крышки подшипников 10,19,25,26 с прокладками 11 и 24. Проверяют проворачиванием валов отсутствие заклинивания подшипников (валы должны проворачиваться от руки) и закрепляют крышки винтами 34.
Затем ввертывают пробку маслоспускного отверстия 5 с прокладкой 6 и пробку уровня 7. Заливают в корпус масло и закрывают смотровое отверстие крышкой-отдушиной 2 с прокладкой из картона 8; закрепляют крышку винтами 32.
Собранную коробку обкатывают и подвергают испытанию на стенде по программе, устанавливаемой техническими условиями.
Регулировка подшипников и зацеплений
15.1 Регулировка зубчатых зацеплений
Для регулировки зубчатых зацеплений необходимо весь комплект валов с зубчатыми колесами смещать в осевом направлении до совпадения средней плоскости колеса с осью шестерни. Этого добиваются переносом части прокладок 11 и 24 с одной стороны корпуса на другую. Чтобы при этом сохранилась регулировка подшипников, суммарная толщина набора прокладок должна оставаться без изменения.
Для проверки правильности положения оси шестерни относительно средней плоскости зубчатого колеса на рабочую поверхность шестерни наносят тонкий слой краски, после чего проворачиванием вала получают на зубьях колеса отпечатки, по характеру которых судят о правильности зацепления.
При смещении зубчатого колеса положение его регулируют постановкой прокладок. При правильном зацеплении краска должна покрывать поверхность зуба колеса по высоте не менее чем на 60 % и по длине не менее чем на 75%.
Проверка правильности межцентрового расстояния производится при помощи измерения величины радиального зазора, который, так же как и для зубчатых передач, должен быть равен 0,25 m.
Проверка величины радиального зазора 1 производится при помощи свинцовой полоски, закладываемой в центральную впадину колеса. Свинцовую полоску укладывают на всю длину впадины червячного колеса, после чего ее зажимают устанавливаемым в подшипнике валом без его вращения.
Толщину вынутой полоски замеряют микрометром или штангенциркулем.
При отсутствии радиального зазора шестерня по окружности выступов будет соприкасаться со впадиной зубчатого колеса, что вызовет чрезмерный нагрев и выход из строя зубчатой пары. Чрезмерная величина зазора также вызывает неправильную работу передачи.
Регулировка зацеплений осуществляется посредством изменения числа регулировочных прокладок позиций 11 и 24, установленных между корпусом позиции 2 и 3 и крышками подшипников позиций 10, 19, 25, 26.
Для начала следует собрать все узлы валов коробки. Установить их в основание корпуса. Надеть крышку корпуса на основание. Установить крышки подшипников с наборами прокладок.
Далее следует проверить проворачиваемость валов. Они должны вращаться без стуков и заедания. При необходимости следует переместить какое-то количество прокладок из-под одной крышки подшипников под противоположную.
Добившись требуемой плавности вращения валов, необходимо снять крышку корпуса и покрасить все зубья большего колеса первой ступени специальной краской. Затем необходимо надеть крышку корпуса и крышки подшипников. Далее необходимо провернуть входной вал коробки так, чтобы большее колесо первой ступени сделало полный оборот. Теперь следует проверить пятно контакта на меньшем колесе первой ступени. Оно должно составлять не менее 75%.
Такую же операцию необходимо произвести и для колес второй ступени.
ГМ.dwg
Твердость зубьев 54 58 HRC
твердость сердцевины 240 280 НВ
остальных поверхностей 229 241 НВ. 2*. Размеры обеспеч. инстр. 3. Точность зубчатого колеса по ГОСТ 1643-81. 4. Общие допуски по ГОСТ 30893.1-2002.
*. Размеры для справок. 2. Поверхности соединения "корпус-крышка" перед сборкой покрыть уплотнительной пастой типа "Герметик" 3. После сборки валы должны проворачиваться свободно
без стуков и заедания 4. Коробку обкатать согласно программе испытаний. 5. После обкатки масло из редуктора слить и залить масло индустриальное И-70А ГОСТ 20799-75 в количестве 3 л. 6. Наружные поверхности корпуса покрыть коррозионностойкой эмалью
внутренние поверхности корпуса покрыть маслостойкой эмалью
цвет - серый. 7. Регулировку осевой игры подшипников поз.48 производить набором прокладок поз. 24.
Техническая характеристика Номинальная мощность привода
Крутящий момент на ведомом валу
Нм 228.7 Частота вращения ведомого вала
мин-1 365 Передаточное число редуктора
Расчетный срок слежбы редуктора
Положения рукоятки механизма переключения
Кинематическая схема привода
Коэффициент смещения
Межосевое расстояние
Технические требования