Завод по производству извести 550 тыс тонн




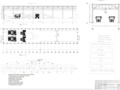
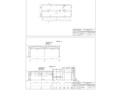
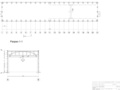

- Добавлен: 24.01.2023
- Размер: 4 MB
- Закачек: 0
Описание
Состав проекта
![]() |
![]() ![]() ![]() ![]() |
![]() ![]() ![]() ![]() |
![]() ![]() ![]() |
![]() ![]() ![]() ![]() |
![]() ![]() ![]() |
![]() ![]() ![]() ![]() |
![]() ![]() ![]() ![]() |
![]() ![]() ![]() |
![]() ![]() ![]() ![]() |
Дополнительная информация
план разрез проектирование пром зданий копия.dwg

осн. 3-х слойный рубер. ковер 15
втопленный в мастику 10
рулонная пороизоляция
плитный пенополистирол 50
защитный слой рубероида
осн. гидроизоляц. ковер 20 (4слоя)
Блокированное промышленное здание
Кафедра "Архитектура промыш-
ленных и гражданских зданий
Архитектурно-конструктивный
План на отметке 0.000;
комплекс на а1 28.dwg

Завод по производству молотой извести мощностью 550 тыс. т
Схема компоновки оборудования в дробильно сортировочном цехе
План на отметке 0.000
Продольный и поперечные разрезы
Операторная схема технологического процесса получения молотой негашеной извести. 1.Складирование известняка 2.Дробление известняка 3.Сортировка известняка 4.Обжиг известняка 5.Очистка отходящих газов 6.Измельчение известняка. 7.Складирование извести
Функциональная схема получения молотой негашой извести
Известняк в сырьевом бункере
Известь на складе готовой продукции
Кафедра технологии строительных материалов изделий и конструкций
готовый ген план.dwg
-отдельно стоящее дерево
дробильно-сортировочный цех
-10-15-758-231гр.-КП.
Завод по производству извести
план разрез на курсяк - копия.dwg

27 мая пояснилка.docx
Выбрана технологическая схема производства молотой негашеной извести. Для обжига извести предложена шахтная печь.
Выполнены расчет конструктивных размеров печи расчет материального баланса расчет времени обжига.
Рассмотрены и предложены конструкционные материалы для изготовления печи.
Пояснительная записка на 51 с. рис 13 табл. 9 список литературы 7 наим.
Графическая часть на 3 листах формата А1 и 1 листа формата А2.
1 Печи для обжига известняка
Описание технологической схемы производства молотой негашеной извести
Расчет материального баланса процесса обжига известняка
Расчет времени обжига
Расчет конструктивных размеров шахтной печи
Расчет горения природного газа
Определение количества топлива для обжига 1 кг извести
Материальный и тепловой балансы печи
Расчет удельных расходов теплоты условного топлива и к.п.д. печи
Список использованной литературы
Большое количество извести используется в качестве вяжущего для приготовления строительных растворов. Строительным раствором называют смесь вяжущего вещества воды и мелкого заполнителя (песка).
Известковые растворы применяют при кирпичной и каменной кладках (кладочные растворы) и для отделки стен зданий (штукатурные растворы). При этом строительная воздушная известь используется для сооружений не подвергающихся действию воды (например надземных).
Гидравлическую известь применяют наряду с воздушной но получают водостойкие строительные растворы. Гидравлическая известь используется для сооружения конструкций находящихся во влажных эксплуатационных условиях — фундаментов и цоколей больших зданий оросительных каналов; при изготовлении растворов для кладки и штукатурки в сухих и влажных условиях; при изготовлении известково-шлаковых и известково-зольных вяжущих.
В качестве вяжущего известь применяют в тонко измельченном виде. Тонкое измельчение ее достигается помолом в мельницах или гашением.
Образование прочного камня при твердении известкового раствора на основе гашеной воздушной извести происходит вследствие высыхания геля гидрата окиси кальция и его последующей карбонизации (образования ) за счет поглощения из воздуха.
Способность затвердевать в воде гидравлической извести придают силикаты и алюмоферриты кальция образующиеся при химическом взаимодействии СаО с при обжиге. Прочность раствора на основе гидравлической извести создается как за счет твердения и карбонизации окиси кальция находящейся в составе гидравлической извести так и за счет гидратации и твердения силикатов и алюмоферритов кальция. Поэтому строительные растворы на гидравлической извести в начале твердения выдерживают в течение 7—21 дней на воздухе.
Основное количество выпускаемой извести (около 75%) используется для технологических целей.
Для получения силикатного кирпича применяют быстрогасящуюся воздушную кальциевую известь. Для изготовления ячеистого и тяжелого силикатных бетонов используют воздушную кальциевую известь со средними сроками гашения. Более стойкие и долговечные изделия из ячеистого бетона получают при использовании в качестве вяжущего гидравлической извести.
В большом количестве известь применяют в производстве различных химических продуктов: кальцинированной питьевой и каустической соды в производстве карбида кальция хлорной извести бертолетовой соли углекислоты синтетического каучука. Известь служит необходимым реагентом во многих химических процессах.
Крупнейший потребитель воздушной негашеной извести — металлургическая промышленность (производство чугуна к стали).
В сахарной промышленности известь применяют в виде известкового молока при очистке сока сахарной свеклы и сахарного тростника.
В виде известкового раствора известь используют для обработки кожи животных тканей сырых материалов в производстве клея и т. д. Молотую известь и известняк используют для нейтрализации кислых почв.
1.Печи для обжига известняка
Обжиг карбонатного сырья (известняк или мел) производится для удаления СО2 и получения жженой извести:
Температуру диссоциации СаСО3 принято считать равной 898 °С. При этой температуре парциальное давление СО2 в равновесной системе равно 101 Па. При более низких температурах значительные выходы СаО и СО2 достигаются только при достаточном разрежении. Температура в зоне обжига 1100—1250 °С так как для полного разложения необходимо прогреть весь кусок известняка для того чтобы в середине его не оставалось необожженной извести. Зависимость продолжительности обжига известняка от величины кусков и температуры приведена на рис. 1.
Топливом для известковообжигательных печей служит кокс антрацит природный газ и печной газ от герметичных карбидных печей.
Обожженная известь в химической промышленности применяется в производстве карбида кальция кальцинированной соды.
Технологическое назначение шахтных печей в содовом производстве несколько иное чем в производстве карбида кальция. Различие заключается в том что в содовом производстве отходящие дымовые газы СО2 являются основным продуктом необходимым для карбонизации аммонизированного рассола а известь используется для регенерации аммиака полученного из растворов хлорида аммония. Это вызвано тем что СО2 полученную в таких печах используют в качестве сырья в дальнейшем технологическом процессе. От качества карбонатного сырья в значительной мере зависит качество полученных материалов.
Расход карбонатного сырья на 1 т соды составляет примерно 2000 кг а на 1 т карбида кальция 910—950 кг.
Известняк или мел загружают в печь в виде куска размером от 40 до 120 мм. От размера куска и температуры зависит скорость разложения СаСО3; эти зависимости приведены на рис. 2.
Качество получаемой извести зависит также от равномерности измельчения карбонатного сырья поступающего в печь так как мелкие куски СаСО3требуют для обжига меньше времени чем крупные и при длительном обжиге могут давать так называемый «перекал» или «намертво» обожженную медленно гасящуюся известь. Содержащиеся в меле и известняке примеси SiO2 и полуторных окислов (Fe2O3 + Аl2О3) способствуют шлакообразованию в печи отрицательно влияют на процесс обжига и качество получаемой извести.
Технологическое топливо
В качестве твердого технологического топлива используется кокс или антрацит.
Влажность топлива зависит от условий хранения и выпадения атмосферных осадков. Топливо должно быть в виде куска с размерами от 30 до 80 мм.
Для обжига известняка применяют шахтные печи следующих типов:
) печи пересыпные на твердом топливе;
) печи пересыпные на газообразном топливе;
) печи с кипящим слоем.
Печь шахтная пересыпная на твердом топливе
На рис. 3 приведена конструкция шахтной пересыпной печи на твердом топливе для содового производства.
В зависимости от производительности печи вертикальная кирпичная шахта имеет различные размеры. Диаметр печи меняется от 23 до 8 м высота от 123 до 366 м. Внутренний диаметр печи зависит от величины съема извести с 1 м2 сечения. Увеличение диаметра печи связано с неравномерностью распределения шихты и воздуха по ее сечению.
Выгрузное устройство в печи — улита имеет диаметр 45 м. В зоне обжига шахта имеет цилиндрическую форму. Вверху и внизу шахта имеет коническую форму. Сужение в верхней части обусловлено уменьшением габарита загрузочного механизма и облегчением более равномерного распределения шихты. Сужение в низу печи вызвано использованием улиты с диаметром 45 м и с целью улучшения теплообмена между охлаждаемой известью и нагревающимся воздухом при меньшем сечении печи. Шахта печи покоится на восьми массивных чугунных опорных колоннах на которые положено чугунное кольцо являющееся основанием огнеупорной футеровки. Опорные колонны установлены на бетонный фундамент. Зону обжига в печи футеруют хромомагнезитовым кирпичом марки МХС7 и МХС14 в два слоя 1-й толщиной 340 мм и 2-й — 230 мм. Хромомагнезитовый кирпич обладает высокой огнеупорностью и термостойкостью и может находиться в работе между капитальными ремонтами более продолжительное время чем шамотный. В зоне подогрева и охлаждения 1-й слой футеровки кладут из шамотного кирпича толщиной 340 мм и 2-й — из красного. Между слоями кирпича оставляют воздушный зазор 20 мм позволяющий расширяться футеровке во время нагревания печи. Швы кладки должны быть не более 1 мм в зоне обжига и не более 2 мм в зоне подогрева и охлаждения.
Необходимо помнить что при футеровке шахтной известково-обжигательной печи нельзя допускать попадания в шамотный порошок известковой пыли так как при обжиге это может вызвать образование плава в стыках между кирпичами и разрушение футеровки. Снаружи футеровка заключена в металлический кожух предназначенный для создания герметичности и механической прочности печи. Кожух сваривают из листовой стали внизу толщиной 16 мм в середине 14 мм и вверху 12 мм. Между кожухом и кладкой предусматривается термоизоляционная прослойка в виде засыпки из молотого шамота толщиной в зоне обжига 130 мм а в зоне охлаждения и подогрева 90 мм.
Необходимый для горения кокса воздух подают специальным вентилятором в печь снизу с избытком на 5—6% от теоретически необходимого.
Загрузочное устройство (рис. 4) предназначено для равномерного распределения как карбонатного сырья по гранулометрическому составу так и топлива между кусками карбонатного сырья по сече- сечению печи. При высыпании кускового материала происходит раз- разделение (агрегация) кусков: более крупные откатываются в сторону а более мелкие сосредоточиваются в середине.
Рис. 4. Загрузочное устройство
Так если ссыпать из загрузочного устройства шихту в центр печи то обнаружится что около стен окажутся крупные куски а в центре мелкие. Такое распределение нежелательно поскольку газы проходящие через толщину содержимого печи будут проходить в большом количестве около стен печи между большими кусками и в меньшем в середине печи. В общем обжиг будет идти неравномерно по сечению печи.
Для обеспечения равномерного распределения шихты по сечению
имеются два устройства: первое — нижний конус имеющий спиралеобразную форму которая способствует падению кусков шихты в разные места сечения. Кроме того прикрепленный к конусу отбойник в виде стальной полосы отражает ударяющиеся об нее куски направляя их в середину сечения. Этот нижний конус при опускании делает кроме того поворот вокруг оси на 60° чем обеспечивает дополнительное рассеивание кусков шихты. Второе устройство — это средний поворотный бункер который поворачивается при каждой загрузке шихты на 60°.
Поворотный бункер уменьшает сегрегацию при его загрузке из вагонеток воздушно-канатной дороги.
Погрузочное устройство имеет второй конус выше расположенный. Два конуса обеспечивают до некоторой степени герметичность загрузочного устройства на верху печи.
Выгрузочное устройство.
В качестве выгрузочного устройства принимается улита с диаметром 45 м конструкция ее приведена на рис. 5.
Рис. 5. Выгрузочное устройство
Улита сделана из чугуна СЧ 16-36 и состоит из двух половин скрепляемых болтами. Поверхность улиты выполнена в виде спирали с наклонными плоскостями. Она имеет съемный колпак через который поступает воздух в центральную часть печи при помощи специального вентилятора остальная часть воздуха поступает с боков улиты при помощи второго вентилятора через выходящую из печи известь. Колпак на улите лучше применять остроконечный вместо плоского и несколько смещенный по отношению оси улиты. Колпак в этом случае будет совершать круговое движение что будет способствовать разрыхлению образовавшихся козлов.
Вследствие трения об улиту известь совершает в печи вращение при котором происходит трение между кусками и ее измельчение.
Улита лежит на восьми роликах опираясь на них стальным кольцом и катится по круговому рельсовому пути представляющему собой такое же стальное кольцо. Улита вращается при помощи электромотора конической пары состоящей из венцовой шестерни зубьями обращенными вниз и приводной шестерни связанной с червячным редуктором. При вращении улиты выходящая из нее известь движется по периферии улиты чем обеспечивается равномерное оседание шихты по всему сечению печи. Известь равномерно осыпается по периферии улиты на расположенный ниже транспортер. При дутье не превышающим 3000 Па хорошее уплотнение в месте выгрузки получается при установке двух лопастных выгружателей.
Печь шахтная пересыпная на газовом топливе.
На рис. 6 приведена конструкция шахтной пересыпной печи на газовом топливе производительностью 200 тсутки известняка.
Известково-обжигательная лечь представляет собой прямую шахту круглого сечения с внутренним диаметром 43 м выложенную из огнеупорного шамота-легковеса. Внутри шахта футерована огнеупорным шамотным доменным кирпичом. В зоне горения шахта постепенно переходит из круглой в квадратную с закругленными углами. Для строительной прочности и предотвращения подсосов атмосферного воздуха шахта снаружи заключена в металлический кожух. Между кладкой печи и кожухом имеется шов толщиной 65 мм заполненный теплоизоляционной засыпкой из сухого молотого трепела. Вся шахта покоится на железобетонной плите опирающейся на железобетонные столбы. Для установки выгрузного механизма железобетонная плита имеет консоли а шахта проемы перекрываемые металлическими балками заделанными в кладку печи.
Питание печи известняком производится из бункера к которому подвешен электровибрационный питатель. Дозирование обеспечивается регулированием продолжительности работы электровибрационного питателя с помощью реле времени.
Подъем ковша с известняком из приямка скипового подъемника до загрузочного устройства печи и спуск порожнего ковша осуществляется электролебедкой. Загрузочное устройство печи (рис. 7) состоит из двух конических воронок и двух клапанов открываемых и закрываемых поочередно специальным устройством установленным на стволе скипового подъемника. Верхний клапан поднимается вверх а нижний неравнобокий конус опускается вниз и при подъеме поворачивается на 34° чем обеспечивается распределение известняка по поперечному сечению шахты печи. Для более равномерного распределения известняка в печи верхняя воронка загрузочного устройства перед каждой разгрузкой поворачивается на углы 60° 180° 240° 300° и 360°.
Печь оборудована верхним и нижним радиоактивными указателями уровня загрузки материала являющимися датчиками автоматической загрузки печи известняком. Выгрузка извести из печи происходит при возвратно-поступательном движении каретки. Мелкие куски извести проваливаются через щелевидные отверстия в ка- каретке (между колосниками) а более крупные куски сходят с торцовых сторон каретки. Печь работает на искусственной тяге создаваемой дымососом. Подача воздуха в печь осуществляется специально установленным вентилятором. Для герметизации низа печи установлен шлюзовой затвор.
Трубопроводы отходящих газов снабжены герметичными поворотными шиберами с дистанционным управлением. При аварийной установке дымососа шибера в трубопроводах отходящих газов автоматически переключаются на режим естественной тяги.
Дымовые газы перед выбросом их в атмосферу проходят очистку в циклонах НИИОГАЗ ЦН-15. Замер температуры и разрежения в шахте предусмотрен на трех горизонтах. Кроме этого предусмотрен замер температуры отходящих газов и разрежения на верху печи. Подача газа и первичного воздуха производится в двух ярусах через специальные балки охлаждаемые водой. На каждом ярусе установлено по две балки причем направление балок одного горизонта перпендикулярно к направлению балок другого. На каждом гори- горизонте предусмотрено по шесть периферийных газовых вводов для возможности подачи незначительного количества газов.
Трубопроводы газа и воздуха оборудованы расходомерами для раздельного учета расхода воздуха и газа подаваемого по горизонтам. На подводящих к печи трубопроводах газа и воздуха также установлены расходомеры и приборы для автоматического поддержания заданного соотношения газ — воздух.
Подводящий к печи газопровод оснащен задвижкой и предохрани-
предохранительным запорным клапаном который автоматически отключает подачу газа в печь в случаях: падения разрежения в шахте печи падения давления газа и воздуха в подводящих трубопроводах прекращения подачи охлаждающей воды в балки или повышения температуры воды в балках выше допустимой (85 °С). Подбор печей производят по каталогу Гипрострома.
Печь шахтная пересыпная на газовом топливе с центральной газовой горелкой.
На рис. 8 приведена конструкция шахтной печи с центральной газовой горелкой.
Отличительным признаком рассматриваемой конструкции шахтной печи от печей с балочными горелками является то что в зоне охлаждения печи
устанавливается горелка для подачи 50% расходуемого газового топлива и рециркуляционного газа из выхлопного патрубка дымососа печи при изменении системы подачи газа периферийными горелками. Для осуществления подачи топливного газа в зону охлаждения шахтной печи необходимо уменьшить скорость горения его при определенных температурах. Это достигается уменьшением концентрации реагирующих компонентов в смеси (например метан и кислород). Разбавление осуществляется введением инертных компонентов (например N2 CO2 Н2О).
Уменьшение концентрации метана и кислорода за счет введения в горючую смесь инертных газов обусловливает резкое снижение скорости реакции. В этом случае скорость горения принимает вид:
где k — константа равная 10-10 см3с; с1 с2 — концентрации реагирующих веществ моль*см3; R — газовая постоянная; Е —- минимальная величина энергии обеспечивающая столкновение реагирующих молекул (энергия активации) Джмоль; Т — температура К; n — содержание добавленных к газовоздушной смеси инертных примесей (сверх 100%).
В печах с центральным вводом газа имеется полyая возможность направленного регулирования сжигания метана так как это обусловливает самовоспламенение газа при более высоких температурах соответствующих концу зоны обжига.
Применение газа с газовоздушной инертной смесью с коэффициентом инертности выше единицы обусловливает смещение пределов взрываемости в область значений превышающих реальную концентрацию газа в газовоздушно-инертной смеси.
На температуру воспламенения газовоздушно-инертной смеси влияет средний диаметр межкусковых пустот в плотном слое материала dcpn а также повышение значений коэффициента инертности т. На рис. 9 приведена зависимость температуры от коэффициента инертности.
Зависимость нижнего предела воспламенения газовоздушно-инертной смеси от температуры приведена на рис. 10.
Известково-обжигательная печь представляет собой вертикальную шахту круглого сечения выложенную огнеупорным шамотным кирпичом верхняя часть шахты (в зоне отбора дымовых газов) выкладывается в два слоя толщиной 230 мм средняя (зона подогрева и обжига внутренним диаметром 32 м) в два слоя: внутренний слой толщиной 345 мм из огнеупорногодоменного кирпича и наружный толщиной 230 мм из огнеупорного шамота-легковеса.
В зоне охлаждения извести шахта внутри с круглой формой постепенно переходит в квадратную 2200 X 2200 мм для установки выгрузочного устройства.
Для обеспечения строительной прочности и предотвращения подсосов атмосферного воздуха в шахту печь снаружи заключена в металлический кожух. Между кладкой печи и кожухом имеется шов толщиной 65 мм заполненный теплоизоляционной засыпкой из сухого молотого трепеля.
Верх печи перекрыт металлической плитой на которую опирается загрузочное устройство и головка скипового подъемника.
Вся шахта печи покоится на железобетонной плите опирающейся на железобетонные столбы. Для установки выгрузочного механизма шахта печи имеет проемы перекрываемые металлическими балками заделанными в кладку печи а для установки привода железобетонная плита имеет консоли. Питание печи известняком производится при помощи скипового подъемника. Загрузка ковша скипового подъемника производится с помощью вибропитателя.
Подъем ковша с известняком из приямка скипового подъемника до загрузочного устройства печи и спуск порожнего ковша осуществляется электролебедкой.
Загрузочное устройство печи состоит из двух конических воронок и двух клапанов открываемых поочередно специальным устройством установленным на стволе скипового подъемника.
Верхний клапан поднимается вверх а нижний неравнобокий конус опускается вниз и при подъеме поворачивается чем обеспечивается распределение известняка по поперечному сечению шахты печи.
Для более равномерного распределения шихты в печи воронка загрузочного устройства перед каждой загрузкой поворачивается на углы прогрессивно возрастающие с каждым циклом.
В печи предусмотрено автоматическое поддерживание заданного уровня загрузки печи.
Скиповой подъемник с лебедкой и загрузочное устройство печи работают в автоматическом режиме.
Датчиками автоматической загрузки печи известняком являются верхний и нижний указатели уровня загрузки которыми оборудована печь. Заполнение ковша подъемника должно производиться регулированием продолжительности работы вибропитателя с помощью реле времени. Выгрузка извести из печи.производится выгрузочным механизмом представляющим собой металлический стол набранный из наклонных колосников расположенный под шахтой и имеющий возвратно-поступательное движение. Над столом выгрузного механизма в шахте печи установлен полый металлический гребень (рассекатель).
Печь работает на природном газе. Подача газа в зону обжига осуществляется центральной горелкой что позволяет вести обжиг в центральном круге печи. Обжиг известняка в периферийном кольце производится двумя ярусами периферийных фурменных воздухоохлаждаемых горелок конструкции ВНИИстром. В каждом ярусе установлено по 8 горелок.
Печь работает при искусственной тяге создаваемой дымососом. Подача воздуха в печь осуществляется вентилятором. Для герметизации низа печи установлен шлюзовой затвор.
Для предотвращения воспламенения газа в зоне охлаждения в центральную газовую горелку подаются инертные отработанные газы отбираемые от выхлопного патрубка дымососа. Подача рециркуляционного инертного газа осуществляется вентилятором.
Трубопроводы отходящих газов снабжены герметичными поворотными шиберами с дистанционным управлением которые при аварийной остановке дымососа автоматически переключаются на режим естественной тяги.
Замер температуры и разрежения в шахте печи предусмотрен на трех горизонтах и у центральной горелки а также температуры отходящих газов и разрежения на верху печи.
Подача воздуха на горение производится: 1) через низ печи под выгрузочный механизм и 2) непосредственно в зону обжига через периферийные фурменные горелки.
Трубопроводы газа воздуха и рециркуляционного газа оборудованы расходомерами. На подводящих к печи трубопроводах также установлены расходомеры и приборы для автоматического поддержания заданного соотношения газ — воздух и газ — рециркуляционный газ. Газопровод оснащен задвижкой и предохранительно запорным клапаном который автоматически отключает подачу газа в печь в случаях: падения разрежения в шахте печи падения или повышения давления газа и воздуха в подводящих трубопроводах прекращения подачи инертных рециркуляционных газов и повышения температуры в зоне центральной горелки свыше 600 °С.
Печь с кипящим слоем.
Особенность обжига в кипящем слое состоит в том что при движении нагретого газа через слой мелкозернистого известняка происходит непрерывная циркуляция частиц. Большая поверхность соприкосновения их с газовым теплоносителем способствует быстрому протеканию физико-химических процессов что позволяет осуществить процесс обжига в комнатных установках при высокой интенсивности.
В печах с многоступенчатыми кипящими слоями движение известняка из камеры в камеру осуществляется путем последовательного перетока по трубам минуя поток газов.
Печи могут работать как на природном газе так и на мазуте. Оптимальная температура обжига известняка 1000—1050 °С. При этих условиях получается известь с содержанием 854% СаОакт и 238% СО2.
На рис. 11 приведена конструкция печи для обжига известняка в кипящем слое производительностью 300 тсутки на природном газе.
Печь имеет вид цилиндрической шахты состоящей из четырех камер. В двух верхних камерах осуществляется предварительный подогрев известняка в остальных — обжиг и охлаждение. Камеры подогрева и обжига выполнены из огнеупорного материала. Свод печи выполнен из подвесных огнеупорных блоков. Газораспределительные решетки в камерах подогрева и обжига изготовлены из огнеупорного бетона в виде сводов с отверстиями в которые вставлены сопла из нержавеющей стали. Футеровка печи заключено в металлический кожух.
Газораспределительная решетка камеры охлаждения выполнена металлической. Для предотвращения просыпания материала в дутьевую камеру на поверхность решетки укладывается металлическая сетка а затем слой керамических шаров диаметром 20 мм.высотой 200 мм; толщина решетки 70 мм. Известняк поступает в верхнюю камеру где в псевдоожиженном состоянии соприкасается с горячими газами нагреваясь до 585 СС. Из нее по переточным трубам известняк переходит во вторую камеру подогрева и нагревается до 700 °С. После этого подогретый известняк по внешнему перетоку поступает в камеру обжига где при средней температуре 1000 °С происходит обжиг. Горячие газы из камеры обжига сначала направляются в циклон где большая часть пылп осаждается после чего пропускается через вышерасположенные камеры. Обожженная известь перетекает в камеру охлаждения. В ней известь охлаждается отдавая тепло подводимому в печь воздуху который нагревается до температуры 300 °С.
Охлажденная известь через переточную трубу покидает печь и транспортируется в сборники. В качестве топлива используется в данном случае природный газ который сжигается непосредственно в слое и служит псевдоожижающим агентом. Особенностью приведенной конструкции печи является оборудование ее горячими циклонами благодаря которым используется большая часть пылевидной обожженной извести выносимой из камеры обжига с потоком газов. Кроме того улучшается работа газораспределительных решеток верхних камер так как продуваемый через них газ оказывается менее запыленным. Горячий циклон выполнен из малоуглеродистой стали и футерован внутри огнеупорным материалом.
Производительность печи Р=200 т извести в сутки
Средний химический состав известняка (%) : СаСО3 - 935; МgСО3 - 05; R2О3+S Н2О - 3; (под R2О3 понимают полуторные окислы т. е. Аl2О3 и Fе2О3) .
Топливо - природный газ Елшанского месторождения (Саратовскаяобл.).
Объемный состав исходного топлива ( % ): СН4 - 932; С2Н6 -О7; С3Н8 -О6; C4H10- N2-49.
Плотность сухого газа ρс.г=0765 кгм3 .
Коэффициент избытка воздуха α = 125.
Относительная влажность воздуха φ=75%.
Температура поступающего воздуха известняка и природного газаtв tи tг= 16° С.
Температура уходящих газов t yx=350 °С.
Температура выгружаемой извести t изв =50°С.
Температура обжига tобж= 1080 °С.
Степень обжига известняка =943%.
Максимальная действительная температура обжига известняка колеблется в пределах 1000-1200°С.
ОПИСАНИЕ ТЕХНОЛОГИЧЕСКОЙ СХЕМЫ МОЛОТОЙ НЕГАШЕНОЙ ИЗВЕСТИ
Рис. 12. Технологическая схема производства молотой негашеной извести
- склад сырья 2 - мостовой кран 3 - промежуточный бункер 4 - пластинчатый питатель5 - инерционный грохот 6 - бункер известняка фракции менее 50 мм 7 – наклонный ленточный транспортер 8 - горизонтальный ленточный транспортер 9 - бункер 10 - автоматический дозатор 11 - ковш 12 - шахтная печь 13 - пластинчатый транспортер 14 - молотковая дробилка 15 - элеватор 16 - бункер извести 17 - ящичный питатель18 - шаровая мельница 19 – пневмовинтовой насос 20 - склад молотой извести
Мостовой грейферный кран 2 загружает фракционированный известняк со склада сырья в промежуточный бункер 3 откуда он пластинчатым питателем 4 подается на виброгрохот 5 для отсева кусков размером менее 50 мм. Отсеянная мелочь известняка накапливается в бункере отходов 6 из которого ока вывозится автотранспортом на склад отходов известняка. В зависимости от количества отходов и наличия потребителей фракция известняка менее 50 мм используется в дальнейшем либо для переработки на известняковую муку либо продается другим организациям (заводам силикатного кирпича строительным организациям).
Очищенная фракция известняка наклонным ленточным транспортером 7 подается на горизонтальный ленточный транспортер 8 с плужковыми сбрасывателями и далее в приемные бункера 9 печей. Из бункера определенная фракция известняка автоматическим дозатором 10 подается в ковш 11 скипового подъемника и далее загружается в шахтную лечь 12.
В печи известняк по мере опускания подвергается нагреванию до 1000—1200°С и разлагается на СаО и . Образующиеся газообразные продукты удаляются из печи дымососом через газоочистное устройство а известь охлажденная в нижней части печи движущимся навстречу холодным воздухом через выгрузочный механизм поступает на общий для всех печей пластинчатый транспортер 13.
Пластинчатый транспортер подает комовую известь в молотковую дробилку 14 где она измельчается до размера кусков менее 25 мм и ковшовым элеватором 15 загружается в бункер 16. Из бункера дробленая известь ящичным питателем 17 равномерно загружается в шаровую мельницу 18. Молотая известь из мельницы забирается пневматическим насосом 19 и транспортируется на силосный склад молотой извести 20 откуда она направляется потребителю автомобильным или железнодорожным транспортом.
РАСЧЕТ МАТЕРИАЛЬНОГО БАЛАНСА ПРОЦЕССА ОБЖИГА ИЗВЕСТНЯКА
Количество неразложившегося СаСО3 в извести определяют из следующего равенства:
СаСО3 - содержание СаСО3 в известняке;
х - искомое количество неразложившегосяСаСО3 в извести %;
- выход СаО из 1 КГ СаСОз ;
МgCОз - содержание МgСОз в известняке %;
35 и 8435-молекулярная масса соответственно MgO и МgСОз ;
CaO+MgO - активность извести (85%).
После подстановки значении в формулу (2.1) и преобразования получим:
При обжиге 1 кг известняка выделяется:
СО2 из СаСО3 .. (0935 - 0057) = 0386 кг
СО2 ИЗ МgCО3 .. 0005=0003 кг
Расход известняка на 1 кг извести стандартного качества составляет
Известняк массой 100 кг содержит (кг): СаСО3 - 935; МgСО3 - 05; R2О3+ S Н2О - 3.
При обжиге разлагается СаСО3 935· 0943=878 кг.
Неразложившийся остаток СаСО3935-878=57 кг.
По реакциям получается:
Для получения 200 т извести в сутки расход карбонатного сырья по массе составит 200000·172 = 344000 кгсутки=4 кгс.
Состав и расход известняка на 1 кг извести по массе приведены в табл.1
Состав расхода известняка
Кол-во компонентов составляющих 1 кг известняка кг
Расход известняка на 1 кг извести кг
На основании приведенного выше расчета составляем материальный баланс процесса обжига известняка (табл. 2).
Количество СаО в выпускаемой из печи извести будет равно 4916 кг.
Содержание СаО в извести равно:
Из 100 кг известняка получается стандартной 85%-ной извести:
Следовательно материальный расчет выполнен правильно.
Материальный баланс обжига на 100 кг известняка
Н2О из известняка 03
Теоретически для получения 1 кг СаО необходимо затратить для обжига
кг СаСО3. Как видно практически при обжиге известняка получается меньшее количество жженой извести и углекислого газа так как не весь известняк загруженный в печь разлагается.
РАСЧЕТ ВРЕМЕНИ ОБЖИГА
Время нахождения известняка в печи зависит отв личины кусков загружаемого материала температурного перепада и коэффициента теплопередачи. Время нахождения известняка в печи обычно рассчитывают по зонам: в зоне нагревания tн в зоне обжига tоб и в зоне охлаждения tox :
t = tн + tоб + tох .
Для расчета t к принятым ранее исходным данным добавляем показатели температуры.
- Средний радиус куска известняка d (принимается
Ввиду малого содержания карбоната магния в известняке при расчете времени обжига последнего в печи это содержание не учитывают.
Количество теплоты переходящей от среды к телу зависит от температурного перепада площади тела времени соприкосновения фаз и коэффициента теплопередачи К выражающего число ватт переходящее в 1 с через 1 м2 площади при разности температур 1 оС:
где α - коэффициент теплоотдачи от газа к известняку Вт (м2 * оС);
- толщина подогреваемого слоя куска известняка равная радиусу куска r м;
λ - теплопроводность известнякаВт (м * оС).
Принимаем следующее значение α: для зоны нагрева αн= 1396; для зоны обжига αоб =2093 и для зоны охлаждения αох= 1163.
Для известняка λ= 23 Вт (м· оС) .
Время нахождения известняка в печи рассчитываем следующим образом:
Чтобы нагреть кусок известняка от 16оС до температуры его разложения (856оС) ему следует сообщить количество теплоты определяемое с одной стороны по формуле:
где с – удельная теплоемкость равная 233 кДж(кг * оС)
m – маса шара равная
С другой стороны количество теплоты сообщаемое куску известняка радиусом r за время tн составляет
где Кн - коэффициент теплопередачи в зоне подогрева Вт(м2 * оС);
S – площадь поверхности куска известняка м2 ;
Δtн – разность температур оС;
tн – время нахождения известняка в зоне нагрева с
Определяем значения Кн Δtн и S:
Так как Q1=Q2 то подставляя числовые значения в формулы (2) и (3) получаем:
Отсюда для куска с r=0.06 м
Количество теплоты поступающей при обжиге к шарообразному куску известняка через его поверхность:
Для разложения этого куска известняка ему необходимо сообщить количество теплоты.
где m– масса известняка
827 – удельное количество теплоты на разложение СаСО3
Учитывая что в известняке содержится 935% СаСОз и степень обжига составляет 943% получим:
Для определения Qз необходимо учесть среднюю теплопроводность известняка и извести. Для извести λ=062 Вт(м*оС)
Определяем коэффициент теплопередачи и температурный перепал в зоне обжига:
Температурный перепад равен:
Площадь поверхности куска известняка составляет
Подставляем числовые значения в формулу (4):
Так как Q3 = Q4 то следовательно
Масса куска известняка начального радиусаrпосле обжига составляет
где - масса куска известняка до обжига кг;
- выход извести из 1 кг массы известняка (см. табл. 2)
При охлаждении куска известняка до 50 оС он отдает количество теплоты
где 0795 – удельная теплоемкость извести кДж(кг*оС)
Количество теплоты отдаваемой площадью поверхности куска полученной извести в зоне охлаждения определяют по формуле
Определяем коэффициент теплопередачи и средне логарифмическую разность температур:
Следовательно подставляя числовые значения в формулу (5) получим:
Из равенства Q5 = Q6 следует
Полное время нахождения известняка в печи составит
t = 103 + 114 + 605 = 2775 ч.
РАСЧЕТ КОНСТРУКТИВНЫХ РАЗМЕРОВ ШАХТНОЙ ПЕЧИ
Полезный объем шахты Vш (м3 ) определяем из уравнения:
где t– время пребывания материала в печи ч;
γ – масса 1 м3 извести равная 800 кгм3;
Р– производительность печи (кг извести в сутки).
Тогда полезный оббьем шахты составит
Отношение высоты шахты к среднему диаметру принимаем
Рабочая высота шахты:
Далее в зоне подогрева внутренний диаметр сужается до 43 м. Между слоем шамота и корпусом укладывается теплоизоляционный слой – шамот ЛБ-13 толщиной 230 мм ГОСТ 5040-68 и слой теплоизоляционной засыпки толщиной 65 мм. Высота зоны подогрева – 72 м. В нижней части зоны подогрева круглое сечение постепенно сужаясь переходит в квадратное. В зоне обжига сечение шахты 374x374 м. Увеличивается толщина теплоизоляционного слоя до 500 мм по осям квадрата. В этой зоне установлено 2 яруса балочных и периферийных горелок. Высота зоны 72 м. В зоне охлаждения квадратное сечение постепенно сужается до размера 26x26 м на уровне выгрузочной решетки. В кладке увеличивается слой легковеса. Высота зоны – 5 м. Таким образом высота шахты составляет 194 м общая высота печи достигает 35 м. В кладке шахты предусмотрены гляделки 5 отверстия 3 для установки приборов и лазы. Необходимый уровень материала в печи поддерживается автоматически при помощи датчика уровня установленного в отверстиях 7 шахты и посылающего управляющий сигнал электродвигателю скиповой лебедки.
РАСЧЕТ ГОРЕНИЯ ПРИРОДНОГО ГАЗА
Определим количество воздуха состав и количество продуктов горения методом расчета процесса горения топлива. Расчет производим на 100 м3 газа. Для проверки расчета составляем материальный баланс при α = 1.
Расхождение составляет 0064 %
Определяем теплотворную способность газа используя тепловые эффекты реакций горения горючих элементов:
Начальная энтальпия продуктов горения будет равна:
Для определения действительной температуры горения топлива поI-t-диаграмме определяем энтальпию продуктов сгорания за вычетом теплоты потерянной в окружающую среду:
где п - пирометрический коэффициент полезного действия горения.
Для шахтных печей работающих на газообразном топливе п= 067 073.
Тепловой баланс зоны охлаждения на 1 кг извести
С известью нагретой в зоне обжига до 940 0С
где СИ – теплоемкость извести при температуре 940 °С кДжкг·°С.
С известью выгружаемой из печи при 50 0С
Потери тепла в окружающую среду принимаем равными 4 % от тепла извести поступающей в зону охлаждения
С воздухом проходящим через зону охлаждения
Определяем по разности между теплом вносимым в зону охлаждения с известью и теплом потраченным в окружающую среду и с уносимым продуктом
Это значение используем в тепловом балансе зоны обжига.
Предварительный тепловой баланс зоны обжига на 1 кг извести
где В - искомое количество топлива м3
С воздухом поступающим из зоны охлаждения
С материалом поступающим из зоны подогрева в зону обжига
где К - расход известняка на 1 кг извести кг;
Сизв - удельная теплоемкость известняка при t’об=9400 0С равная 111 кДж(кг*oС)
где 1780 - количество теплоты необходимой для разложения 1 кг СаСОз в СаО
На потери в окружающую среду
Принимаем п2=4% количества теплоты вносимой в шахту печи топливом
где n2 - потерянное количество теплоты в окружающую среду к количеству теплоты поступающей в зону обжига
С известью переходящей из зоны обжига в зону охлаждения
С продуктами горения топлива переходящими из зоны обжига в зону подогрева
С углекислотой выделенной при разложении СаСОз
Приход тепла –35200*В + 2517 кДжкг
Расход тепла – 18281*В + 4405 кДжкг
I' = 070·3400 = 2380 кДжм3
По I-t - диаграмме tд= 1510oС.
ОПРЕДЕЛЕНИЕ КОЛИЧЕСТВА ТОПЛИВА ДЛЯ ОБЖИГА 1 КГ ИЗВЕСТИ
Составляем тепловые балансы по зонам печи. Обозначим через В м3 количество топлива необходимого для обжига 1 кг извести стандартного качества. Из теплового баланса зоны обжига определим В.
Для определения расхода топлива приравниваем приход теплоты к его расходу и решаем уравнение относительно В:
200В + 2517 = 18281 В + 4405
МАТЕРИАЛЬНЫ И ТЕПЛОВОЙ БАЛАНС ПЕЧИ
На основании приведенных расчетов материальных балансов обжига известняка и горения топлива а также подсчитанного расхода топлива составляем сводный материальный баланс известковообжигательной печи. Рассчитываем состав и количество отходящих из печи газов на 1 кг извести.
от сгорания топлива: 0988·011 =0109 м3 ;
от разложения СаСОз и МgСОз
Всего: V со2 = 0109+0341 =045 м3
или Gco2=V со2ρсо2 =045·1977=089 кг.
от сгорания топлива: 1939· 011 = 021 м3 ;
от нагрева известняка:
Всего: VH2O=021+0064=0274 м3
илиGH2O=VH2O ρH2O=0274·0804=022 кг.
Азота: VN2 =925·011=1017 м3
или GN2 =VN2ρN2=1017·1251=1272 кг.
Кислорода: VO2 =0485·011 =0053 м3
илиGO2=VO2ρO2 =0053·1429=0076 кг
Vα = Vco2 + VH2O+ VN2 + VO2 = 045 + 0274 + 1017+ 0053 =1794 м3
Gα = Gco2 + GH2O+ GN2 + GO2 = 089 + 022 + 1 272 + 0076 =2458 кг.
Объемный расход дымовых газов составит
Следовательно на основании данного расчета составляем сводные балансы печи
Сводный тепловой баланс зоны обжига на 1 кг извести (с подстановкой величины расхода топлива)
С воздухом проходящим через зону охлаждения
С известняком и магнезиальной известью нагретыми до 940 оС
На разложение углекислого кальция
С известью нагретой до 940 оС
С продуктами горения топлива нагретыми
Теплота теряемая от разложения СаСОз нагретого до 940 оС
Тепловой баланс зоны подогрева на 1 кг извести
С продуктами сгорания топлива
С углекислотой выделенной при разложении СаСОз нагретого до 940 оС
На испарение влаги из известняка
С углекислотой выделен-ной при разложении МgСОз
На нагрев известняка то 0 до 940 оС (из баланса зоны обжига)
В окружающую среду (п3=2% от количества теплоты поступающей с топливом)
Унос с продуктами горения из шахты печи (по разновидности баланса 2549-1970)
Сводный тепловой баланс известково-обжигательной
печи на 1 кг извести
На испарение влаги известняка
С отходящими продуктами горения топлива
С известью выгружаемой из печи
РАСЧЕТ УДЕЛЬНИХ РАСХОДОВ ТЕПЛОТЫ УСЛОВНОГО ТОПЛИВА И К. П. Д. ПЕЧИ
Определяем удельное количество теплоты на получение 1 кг извести:
Удельный расход условного топлива равен:
где - теплотворная способность условного топлива равная
Для современных работающих газовых печей производительностью 15-200 т извести в сутки удельные расходы составляют: теплоты 4106- 5866 кДжкг условного топлива 13-14 %. Коэффициент полезного действия печи определяем как отношение полезно расходуемой теплоты на технологические процессы к общему количеству теплоты поступившей в печь:
Следовательно 80% теплоты от общего количества затраченной полезно расходуется на обжиг извести.
Предложена технологическая схема производства молотой негашеной извести.
Произведен теплотехнический расчет шахтной печи. Были выполнены:
расчет времени обжига известняка по зонам печи. Общее время обжига - 2775 ч.
расчет конструктивных разменов шахтной печи: Dср= 43 м Н = 1936 м.
расчет горения топлива.
составлены теплотехнический и материальные балансы.
рассчитаны удельное количество теплоты Q= 3870 кДж удельный расход условного топлива Ву = 132% КПД печи равный 80%.
СПИСОК ИСПОЛЬЗОВАННОЙ ЛИТЕРАТУРЫ
Монастырев А.В. Производство извести: Учеб. – М.: Высш. шк. 1971. – 272 с.
Монастырев А.В. Александров А.В. Печи для производства извести: Справочник. – М.: Металлургия 1979. – 232 с.
Никифорова Н.М. Теплотехника и теплотехническое оборудование предприятий промышленности строительных материалов и изделий: Учеб. – М.: Высш. шк. 1981. – 271с.
Роговой М.И. Кондакова М.Н. Сагановский М.Н. Расчеты и задачи по теплотехническому оборудованию предприятий промышленности строительных материалов: Учеб.пособие – М.: Стройиздат 1975-320с.
Косенко Н.Ф. Комлев В.Г. Инженерно-технологические расчеты в производстве вяжущих материалов и изделий из них: Учеб.пособие - Иваново: Иван.гос. хим-технол. ун-т 1991. – 108 с.
Расчет теплотехнического оборудования и физико-химические основы тпепловых процессов в производстве силикатного кирпича: Учеб. пособие Под ред. В.Г. Комлева. – Иваново: ИГХТУ 1996. – 88 с.
Капш М.П. Вентиляционные установки. – М.: Высш. шк. 1967.
продольный разрез с оборудованием.dwg

план разрез на курсяк.dwg

курсовая пояснилка.docx 13 мая.docx
Почти все минеральные вяжущие вещества получают путем грубого и тонкого измельчения исходных материалов и полупродуктов с последующей термической обработкой. В этих условиях протекают разнообразные физико - химические процессы обеспечивающие получение продукта с требуемыми свойствами.
Минеральные вяжущие используются в подавляющем большинстве случаев в смеси с водой и с так называемыми заполнителями которые представляют собой минеральные (а иногда и органические) материалы состоящие из отдельных зерен кусков волокон разных размеров.
Строительные изделия на основе вяжущих бывают различной формы и размеров начиная от набольших плиток и кончая крупными элементами сборных железобетонных конструкций.
I.Технология производства
1 Сырье и его свойства.
Исходными материалами для производства воздушной извести являются многие разновидности известково-магнезиальных карбонатных пород (известняки мел доломитизированные известняки доломиты и др.). Все они относятся к осадочным породам и широко распространены на территории нашей страны. В состав известняков входят углекислый кальций СаСОз и небольшое количество различных примесей (глина кварцевый песок доломит пирит гипс и др.).
Теоретически карбонат кальция состоит из 56% СаО и 44% СО2. Он встречается в виде двух минералов — кальцита и арагонита.
Кальцит или известковый шпат кристаллизуется в гексагональной системе. Его кристаллы имеют форму ромбоэдров. Плотность кальцита 26—28 гсм3; твердость по десятибалльной шкале (шкала Мооса) — 3. Кальцит хорошо растворяется при обычной температуре в слабой соляной кислоте с выделением углекислого газа. Доломит при таких условиях не разлагается (этим пользуются при определении вида горных пород).
Арагонит — менее распространенный минерал кристаллизуется в ромбической системе. Его плотность 29—З гсм3 твердость 35—4. При нагревании до температуры 300— 400° С арагонит превращается в кальцит рассыпаясь в порошок.
В доломитовых известняках в качестве примеси присутствует доломит СаСОз MgCOe. Теоретически доломит состоит из 5427% СаСОз и 4573% MgCO3 или 3041% СаО 2187% MgO и 4772% СО2. Плотность доломита 285—295 гсм3. Доломитовые породы почти нацело слагаются минералом доломитом с тем или иным содержанием глинистых песчаных железистых и тому подобных примесей.
Чистые известково-магнезиальные породы — белого цвета однако они часто бывают окрашены примесями окислов железа в желтоватые красноватые бурые и тому подобные тона а углистыми примесями — в серые и даже черные цвета. Количество и вид примесей к карбонатным породам размеры частиц примесей а также равномерность распределения их в основной массе в большой степени отражаются на технологии производства извести выборе печей для обжига оптимальной температуре и продолжительности обжига а также на свойствах получаемого продукта.
Обычно чистые и плотные известняки обжигаются при температурах до 1100—1250° С. Чем больше карбонатная порода содержит примесей доломита глины песка и т. п. тем ниже должна быть оптимальная температура обжига (900—1150° С) для получения мягкообожженной извести. Такая известь хорошо гасится водой и дает тесто с высокими пластичными свойствами.
Раньше считали что высококачественную известь можно получать только из чистых известняков с малым содержанием примесей (до 2—3%). Новые исследования показали что из известняков со значительным количеством примесей глины и тонкодисперсного кварцевого песка (до 5—7%) равномерно распределенных в общей массе при правильном ведении обжига также можно получать известь дающую при гашении высокий выход пластичного теста. При этом лучшую по качеству известь получают из пород в которых равномерно распределенные примеси присутствуют в виде частичек размером до 1 мкм.
Примеси гипса нежелательны. При содержании в извести даже около 05—1% гипс сильно снижает пластичность известкового теста. Значительно влияют на свойства извести железистые примеси (особенно пирита) которые уже при температурах 1200° С и более вызывают образование в процессе обжига легкоплавких эвтектик способствующих интенсивному росту крупных кристаллов окиси кальция медленно реагирующих с водой при гашении извести и вызывающих явления связанные с понятием «пережог».
Физико-механические свойства пород также отражаются на технологии извести. Для обжига в высоких шахтных печах пригодны лишь те породы которые характеризуются значительной механической прочностью (прочность на сжатие не менее 20—30 МПа); куски породы должны быть однородными неслоистыми; они не должны рассыпаться и распадаться на более мелкие части во время нагревания обжига и охлаждения.
Рассыпаться во время обжига склонны крупнокристаллические известняки состоящие из кристаллов кальцита размерами 1—3 мм. Мягкие разновидности известково-магнезиальных пород (мел и т. п.) надо обжигать в печах в которых материал не подвергается сильному измельчению.
Известково-магнезиальные породы в зависимости от их химического состава являются сырьем для производства не только воздушной но и гидравлической извести а также портландцемента. В табл. 1 приведена примерная классификация известково-магнезиальных горных пород применяемых для производства воздушной и гидравлической извести а также их разновидностей. Таблица 1.Примерная классификация сырья для производстваизвестковых вяжущих веществ
Доломитизированный мергелистый известняк
Маломагнезиальная жирная
Маломагнезиальная тощая
Магнезиальная гидравлическая
По ГОСТ 21-27-76 в зависимости от химического состава карбонатные породы делят на семь классов: А Б В Г Д Е Ж (табл. 2).
Таблица 2. Требования к химическому составу известняков для производства известковых вяжущих
Глинистые примеси (SiO2 + Al2O3 + Fe2O3) не более
Для производства воздушной извести применяют следующие виды известково-магнезиальных карбонатных пород: зернисто-кристаллический мраморовидный известняк; плотный кристаллический известняк; землисто-рыхлый известняк (или мел); известковый туф; известняк-ракушечник; оолитовый известняк; доломитовый известняк; доломит.
Мрамор по химическому составу (СаСО3 или СаСО3 + MgCO3) — наиболее чистое сырье однако в связи с высокими декоративными свойствами он используется в качестве отделочного материала и поэтому в производстве извести за редким исключением не применяется.
Плотные известняки имеют мелкозернистую кристаллическую структуру содержат обычно небольшое количество примесей и отличаются высокой прочностью. Плотные известняки наиболее широко используются для получения извести.
Мел — мягкая рыхлая горная порода легко рассыпающаяся на мелкие куски. Его обычно обжигают лишь во вращающихся печах так как при обжиге в шахтных печах он легко крошится что нарушает процесс обжига.
Известняковый туф отличается ноздреватым строением и большой пористостью; иногда его используют для производства извести во вращающихся и шахтных печах (в зависимости от прочности).
Известняк-ракушечник состоит из раковин сцементированных углекислым кальцием. Представляет собой малопрочную горную породу поэтому редко применяется для изготовления извести.
Доломитовый известняк — горная порода состоящая из отдельных шариков карбоната кальция сцементированных тем же веществом.
Доломитовые известняки и доломиты по своим физико-механическим свойствам сходны с плотными известняками. Иногда доломиты залегают в природе в виде рыхлых скоплений.
Объемная масса плотных известняков составляет 2400— 2800 мела — 1400—2400 кгм8. Влажность известняков колеблется в пределах 3—10 а мела —15—25%.
Широкое распространение карбонатных горных пород способствует развитию производства извести почти во всех экономических районах страны.
Сырьем для производства воздушной извести могут служить не только специально добываемые для этой цели карбонатные породы но и отходы при добыче известняков для нужд металлургической химической строительной и других отраслей промышленности. Наконец для этой цели в ряде случаев используются побочные продукты в виде дисперсного карбоната кальция или гидрата окиси кальция (карбонатные отходы сахарного и содового производства гидратная известь от производства ацетилена и др.).
2 Материал и требования к нему
Тонкоизмельченная негашеная известь имеет ряд преимуществ при изготовлении растворов и бетонов перед гидратной известью в виде порошка или теста. В этом случае нет отходов и все компоненты тонкоизмельченной извести рационально используются во время твердения (в том числе силикаты алюминаты ферриты и карбонат кальция). Молотая негашеная известь характеризуется меньшей водопотребностью чем гашеная известь. Удельная поверхность молотой негашеной извести обычно значительно меньше удельной поверхности гидратной извести. Поэтому требуемую удобоукладываемость растворной или бетонной смеси на молотой негашеной извести получают при пониженном количестве воды. Снижение же водопотребности растворных и бетонных смесей способствует увеличению их прочности при твердении. Кроме того негашеная известь гидратируясь в уже уложенных в дело растворах и бетонах связывает большое количество воды переходящей в твердую фазу. Как известно окись кальция при переходе в гидрат связывает 3213% воды от своей массы. Все это способствует получению растворов бетонов и изделий на молотой негашеной извести повышенной плотности и прочности по сравнению с получаемыми на гашеной извести.
При гидратном твердении молотой негашеной извести выделяется значительное количество тепла. Поэтому изделия на такой извести при температурах ниже нуля твердеют более спокойно и имеют лучшие показатели прочности так как окружающие условия способствуют быстрому отводу тепла и уменьшению термических напряжений.
Указанные преимущества молотой негашеной извести способствуют ее применению в производстве различных строительных материалов и изделий.
Благоприятные результаты при гидратном твердении молотой негашеной извести можно получить лишь при следующих условиях обеспечивающих нормальный ход процессов ее твердения:
· применение извести тонкого помола;
· соблюдение определенного водоизвесткового отношения;
· отвод тепла или использование других приемов не допускающих разогревания твердеющего раствора или бетона до температур вызывающих интенсивное испарение воды (особенно при кипении);
· прекращение перемешивания растворной или бетонной смеси на определенном этапе гидратации извести.
При грубом помоле извести создаются условия для возникновения местных очагов перегрева материала кипения воды и разрыхления структуры схватывающихся новообразований что сопровождается появлением значительных растягивающих напряжений и деформаций вызывающих снижение прочности а иногда и разрушение твердеющего раствора или бетона. Поэтому негашеную известь следует измельчать до удельной поверхности 3500—5000 см2г причем остаток на сите № 02 должен быть близким к нулю а на сите № 008 не превышать 4—6%.
Отрицательно влияет на гидратное твердение негашеной извести пережог. Замедленная гидратация крупных кристаллов окиси кальция (крупнее 10—20 мкм) в уже затвердевшем известковом камне вызывает дополнительные некомпенсируемые напряжения. Поэтому количество пережога в молотой негашеной извести не должно превышать 3—5%. Гидратное твердение негашеной извести протекает нормально при содержании воды в растворной или бетонной смеси лишь в пределах 100—150% массы извести. Точнее количество воды устанавливают с учетом интенсивности отвода тепла и скорости гидратации извести в растворной или бетонной смеси. При малом содержании воды (60—80% массы извести) температура резко повышается и интенсивно образуется пар который разрыхляет структуру препятствуя схватыванию и твердению массы. При избытке воды (200—250%) частицы извести отделяются одна от другой водными пленками адсорбирующимися на их поверхности и образуется не схватывающаяся и очень медленно твердеющая пластическая масса. При гидратации нормально обожженной извести практически в течение первого часа после затворения ее водой выделяется 1160 кДж на 1 кг окиси кальция. В результате изделие из раствора или бетона на молотой негашеной извести сильно разогревается причем если температура поднимается до 100° С возникают те отрицательные явления о которых говорилось раньше. Для предупреждения интенсивного разогревания смеси при гидратации извести используют различные приемы и в частности несколько увеличивают расход воды охлаждают ее частично гасят известь перед ее применением и т. п.
Одним из простых способов является замедление скорости гидратации а следовательно и интенсивности тепловыделения с помощью различных веществ (гипса сульфата натрия сульфитно-дрожжевой бражки и др.). ССБ СДБ и им подобные поверхностно-активные вещества вводимые в воду для гашения в количестве 02--1% адсорбируются на кристаллических зародышах гидрата окиси кальция препятствуя их росту и замедляя вследствие этого дальнейшее растворение в воде и гидратацию окиси кальция. Возможно что поверхностно-активные вещества уменьшают скорость гашения также вследствие адсорбции их на частичках окиси кальция.
Замедление скорости гидратации при добавках 2--5% гипса от массы извести объясняют образованием пленок гидрата окиси и сульфата кальция на поверхности еще не прореагировавших частичек окиси кальция.
В тех случаях когда известь наряду с очень активными частичками окиси кальция содержит медленно гасящиеся частички пережога целесообразно в соответствии с рекомендациями Б.Н. Виноградова применять комбинированную добавку состоящую из замедлителя и ускорителя гашения. Ускоритель в составе добавки действует преимущественно на пережженные частички значительно ускоряя их гашение и обеспечивая их превращение в гидрат до твердения системы. Так влияет например смесь СДБ и хлористого кальция. Необходимое количество добавок нужно устанавливать опытом для каждой партии извести с учетом ее свойств. Наконец при гидратном твердении молотой негашеной извести необходимо на определенной ступени взаимодействия ее с водой прекращать механические воздействия на растворную или бетонную смесь.
Перемешивание вибрация и т. п. в течение всего периода гидратации извести нарушают ее схватывание и твердение. Точным же регулированием продолжительности механических воздействий на растворные и бетонные смеси во время их перемешивания в мешалках или вибрации в формах можно добиться гидратации какой-то части окиси кальция. Она будет происходить в условиях свободных деформаций смеси с последующим гидратным твердением остальной части в спокойном состоянии без нарушения возникающих структурных связей между образующимися частичками гидрата окиси кальция. На практике такой эффект дает двухступенчатое перемешивание растворных или бетонных смесей на молотой негашеной извести заключающееся в следующем. Вначале смесь извести с заполнителями и водой взятой в количестве 80--90% общего ее содержания перемешивают 2--3 мин и затем выдерживают 05--1 ч. При этом гидратируется наиболее активная часть извести что сопровождается интенсивными объемными деформациями. После такой выдержки продолжительность которой в зависимости от извести уточняют опытным путем вторично перемешивают смесь с остальной частью воды и укладывают ее в формы (при изготовлении изделий). В формах в спокойном состоянии и протекает твердение бетона обусловливаемое гидратацией еще непрореагировавшей части окиси кальция. Возникающие при этом деформации уже не столь интенсивны и не разрушаютизделия
Магнезиальной и доломитовой сортов
Содержание активных СаО + MgO в пересчете на сухое вещество % не менее
а) в негашеной извести без добавок
б) в негашеной извести с добавкой
Содержание активной MgO % не более
Содержание углекислоты СО2 % не более
Строительную воздушную негашеную известь делят на три сорта: 1 2 и 3-й. негашеная молотая известь должна соответствовать требованиям указанным в Таблице 3
*В скобках указано содержание MgO для доломитовой извести.
3 Производство извести
Производство молотой негашеной извести состоит из следующих основных операций: добычи и подготовки известняка обжига и последующего помола известняка. Известняки добывают обычно открытым способом в карьерах после удаления верхних покрывающих непродуктивных слоев. Плотные известково-магнезиальные породы взрывают. Полученную массу известняка в виде крупных и мелких кусков погружают в транспортные средства обычно одноковшовым экскаватором. В зависимости от расстояния между карьером и заводом известняк доставляют на завод ленточными конвейерами автосамосвалами железнодорожным и водным транспортом.
Так как размеры глыб добытой горной породы нередко достигают 500 - 800 мм и более то возникает необходимость дробления их и сортировки всей полученной после дробления массы на нужные фракции. Это осуществляется на дробильно-сортировочных установках работающих по открытому или замкнутому циклу с использованием щековых молотковых и другого типа дробилок. Дробить и сортировать известняк целесообразно непосредственно на карьере и доставлять на завод лишь рабочие фракции.
Обжиг является основной технологической операцией в производстве воздушной извести. При этом протекает ряд сложных физико-химических процессов определяющих качество продукта. Целью обжига являются:
) возможно полное разложение СаСО3 и MgCO3 . CaCO3 на СаО MgO и СО2;
) получение высококачественного продукта с оптимальной микроструктурой частичек их пор. Обжигают известняк в различных печах: шахтных вращающихся и кипящего слоя; используют также установки для обжига известняка во взвешенном состоянии и т. д. Наибольшее распространение получили шахтные известеобжигательные печи. В зависимости от вида применяемого топлива и способа его сжигания различают шахтные печи работающие:
) на короткопламенном твердом топливе вводимом обычно в шахту перемежающимися с известняком слоями такой способ обжига называют пересыпным а сами печи - пересыпными;
) на любом твердом топливе газифицируемом или сжигаемом в выносных топках;
) на жидком топливе;
) на газообразном топливе.
По характеру процессов протекающих в шахтной печи по её высоте различают три зоны. В верхней части печи - зона подогрева - материал подсушивается и подогревается раскаленными дымовыми газами и из него выгорают органические примеси. В средней части печи располагается зона обжига где температура обжигаемого материала изменяется в пределах 850 - 1200 - 900о С; здесь известняк разлагается и из него удаляется углекислый газ. В зоне охлаждения - нижней части печи - известь охлаждается с 900 до 50 - 100о С поступающим с низу воздухом который в свою очередь нагревается и попадает в зону обжига для поддержания горения.
Противоточное движение обжигаемого материала и горячих газов в шахтной печи позволяет хорошо использовать тепло отходящих газов на подогрев сырья а тепло обожженного материала - на подогрев воздуха переходящего в зону обжига. Поэтому пересыпные шахтные печи экономичны по расходу топлива однако известь в них загрязняется золой топлива. Обжиг на природном газе или жидком топливе позволяет значительно улучшить качество извести однако конструкции шахтных печей использующих эти виды топлива требуют усовершенствования особенно в отношении подачи топлива в печь.
Вращающиеся печи для обжига извести позволяют получать мягко обожжённую известь высокого качества из известняка и мягких карбонатных пород (мела туфа ракушечника) в виде мелких кусков. В них можно механизировать и автоматизировать процессы обжига применять все виды топлива - пылевидное твердое жидкое и газообразное но они отличаются большим расходом топлива повышенными капиталовложениями и расходомэлектроэнергии
Весьма эффективным является обжиг в «кипящем» слое обеспечивающий быструю передачу большого количества тепла от газа к обжигаемому материалу. Обжигают известь в кипящем слое в реакторе представляющим собой металлическую шахту разделенную по высоте на 3 - 5 зон. По периферии реактора расположены горелки для газа или мазута. Многозонность реактора позволяет получать известь высокого качества при небольшом расходе топлива. Применение в известковой промышленности установок для обжига карбонатных пород в кипящем слое позволяет рационально использовать большое количество мелких фракций сырья образующихся обычно на карьерах и заводах шахтными и даже вращающимися печами.
Обжиг измельченного известняка во взвешенном состоянии осуществляют в обжиговых трубах или циклонных топках в которых тонкоизмельченные частички карбонатного сырья увлекаются потоком раскаленных газов и обжигаются. Осаждается обожженная известь из газового потока в пылеосадительных устройствах.
После обжига полученную комовую известь транспортируют ленточным конвейером со стальной лентой на помол в мельницу. После него молотую известь отправляют на склад.
Обоснование общей технологии производства молотой негашёной извести и видов основного оборудования.
Известняк одноковшовым элеватором поднимается до устройства предварительного подогрева в верхний бункер а затем с помощью трубопровода распределяется в вертикальном подогревателе. Известняк нагревается газами около 1100оС в хвостовой части печи. Хорошо обожженная активная известь попадает в вертикальный кулер охлаждается холодным воздухом из нижней части. Затем проходит через электромагнитный вибрационный выгружатель для следующего процесса. Холодный воздух в куллере нагревается до температуры 600 ~ 700оС затем направляется в печь в качестве вторичного воздуха для горения топлива. Охлажденная известь ковшовым конвейером направляется в силос затем фасуется и готова для вывоза.
Технологический процесс.
Известь вяжущий материал получаемый обжигом и последующей переработкой известняка мела и других известково-магнезиальных горных пород. Чистая известь плохо растворима в воде (около 01% при 20 °С); плотностью около 34 гсм3. В зависимости от содержания в породе MgO различают следующие виды извести: кальциевую (содержит до 5% по массе MgO) магнезиальную (5-20%) и доломитовую (20-40%). В зависимости от химического состава и условий твердения известь подразделяют на воздушную которая твердеет в воздушно-сухих условиях и гидравлическую которая твердеет на воздухе и в воде.
Форма факела многоканальной горелки а также его длина адаптируется к процессу обжига и потребностям по распределению температуры внутри тела вращающейся печи кроме того длину и форму пламени можно регулировать. Температура пламени контролируется более того можно осуществлять контроль за областью наивысшей температуры. В связи с этим происходит предотвращение пережога материала.
Вертикальный подогреватель.
Используется вертикальный подогреватель для вращающейся печи. Нагретая известь имеет высокую температуру. Вертикальный подогреватель может выдержать высокие температуры выхлопных газов известь внутри нагревателя нагревается полностью но не полностью разлагается таким образом по сравнению с другими формами поворотной печи потребление тепловой энергии в печи низкая потребление тепловой энергии составляет менее 5016 кДж кг извести.
Вращающаяся печь: используется вертикальные нагреватель и охладитель коническая форма хвоста и головы печи. Пластины головной части печи охлаждаются воздухом соответственно продлевается время нахождения материала в печи. Хвостовая и головня части печи используют особые листообразное герметическое оборудование. Вращающиеся печи для обжига извести позволяют получать мягко обожжённую известь высокого качества из известняка и мягких карбонатных пород (мела туфа ракушечника) в виде мелких кусков.
Подогреватель состоит из ряда отдельных камер. В каждой камере сырье и выхлопные газы образует противоточный теплообмен количество газов и материала можно отдельно регулировать гарантируя достижение высокого процента теплообмена. Теплообменные параметры целиком контролируется электронной системой PLC идеально комбинируется с системой печи позволяя увеличить производительность снизить энергозатраты повысить качество продукции. Камеры подогревателя полностью самостоятельны. Потоки воздуха сырья в каждой камере можно отдельно контролировать в связи с этим можно достичь температурный баланс в каждой камере.
Охладитель: холодный воздух и горячий материал соприкасаются непосредственно образуя процесс теплообмена. Вторичный воздух высокой температуры может достигать свыше 600оС,благоприятен для обжига. Оборудование охладителя имеет мало движущихся деталей. Выгружаемый из вращающейся печи разогретый до высоких температур материал (известняк или доломит) загружается в охладитель. Сверху вниз и в обратном направлении струями охлаждающего воздуха осуществляется теплообмен. Разогретый воздух после охлаждения материала вновь используется для процесса горения.
Вращающиеся печи допускают возможность полной механизации и автоматизации процесса обжига. Наконец в них можно применять все виды топлива — пылевидное твердое жидкое и газообразное.
Терморегулирующее оборудование.
Терморегулирование: оборудование системы обжига регулируется контролируется и сигнализируется используя централизованный контроль со стороны PLC в главном зале управления. Также есть дисплей всех контрольных точек и необходимые приборы контроля блокировки. В целом система имеет высокий уровень автоматизации. Многоканальная газовая горелка: форма пламени может быть скорректирована чтобы улучшить эффективность сгорания. На основании использования теории образования NO2 в процессе сжигания топлива контролируется содержание NO2 в дымовых газах. Конструкция многоканальной горелки позволяет ощутимо снизить содержание NO2 в дымовых газах. что соответствует достижению мирового стандарта.
Охладитель состоит из рядов камер. Каждая камера охлаждения состоит из воздушной форсунки и разгрузчика материала что обеспечивает высокую реакцию теплообмена между воздухом и материалом. Тепловые параметры охладителя контролируются электронной системой PLC.
Разделен на несколько зон охлаждения поэтому гарантируется равномерная скорость воздуха охлаждения в плоскости внутренней части охладителя нет «мертвых углов». Внутри установлена решетка предотвращающая заторы от печного настыла и снижающая степень повреждения оборудования.
Система очистки от дымовых газов у вращающейся печи.
Согласно требованиям применяется теплообменник подогревающий первичный воздух до 200С и подающий его в горелку с выгрузочного конца печи в качестве воздуха для поддержания горения. Выбросы после снижения температуры поступают в пылеуловитель. Дым высокой температуры из печи очищенный предварительно выбрасывается вентилятором через трубу в атмосферу. Концентрация пыли после очистки сохраняется в пределах установленныхгосударственным стандартом.
Система производства использует управление PLC мониторинг CRT целая управляющая система состоит из комплекта PLC. Система управления производит сбор сигналов питания оборудования состояния аварийной работы и производит измерение и регулирование давления расхода и температуры и на блочном щите автоматически отображает рисунки процессов проводит установление параметров и выдает команды всех операций. Своевременно и произвольно печатает отчетность и при неисправности будет подавать сигнал светозвуковой тревоги.
Система управления PLC предназначена для интеграции 3 различного контроля и регулирования технологических параметров для управления программами технологического процесса предупреждения аварии печати отчетности основных параметров и статуса оборудования а также для других функций.
Режим работы предприятия производственные программы по выпуску негашёной извести и по сырью.
Для данного предприятия по производству негашёной извести имеющее в своём составе непрерывно действующее оборудование следует предусмотреть трёхсменную каждодневную работу с остановкой оборудования только для проведения капитального ремонта.
При непрерывном режиме годовой фонд времени предприятия составит:
Определение годового фонда времени работы технологического оборудования
Производственная программа предприятия по выпуску продукции
Наименование выпускаемой продукции
Количество продукции т
Известь негашёная молотая
Производственная программа предприятия по сырью
Вид сырьевого компонента
Анализ технологического процесса
Технологический передел процесс и его содержание
Количественная характеристика параметров процесса
Материальные и энергетические потоки.
Складирование известняка; процесс механический: загрузка и выдача материала с частичным его усреднением зернового состава; технологическое оборудование-сырьевой бункер.
Характеристика известняка: наибольшая крупность кусков-400мм. Плотность известняка 2600 кг. Плотность насыпная-1450 кг влажность 5%; прочность на сжатие 20 Мпа содержание СаС=95%
М1- количество известняка поступающего в сырьевой бункер;
М2-Количество известняка выходящего из бункера;
М2п- механические потери в питателе и в транспортирующем устройстве.
Материальный баланс:
Дробление известняка; процесс механический: измельчение раздавливанием и истиранием; аппарат щековая дробилка
Наибольшая крупность 400 мм; крупность дробления: фракция известняка по требованиям к загрузке известеобжиговой печи 30-50 мм
-количество известняка выходящего из дробилки;
-возврат известняка после сортировки;
-механические потери известняка при транспортировании и в аспирационных устройствах. Материальный баланс:
сортировка известняка по крупности; процесс механический: разделение смеси зёрен на фракции рассеиванием сквозь сита; аппарат-вибрационный грохот
Зерновой состав известняка поступающего на грохот:
—количество верхнего отсева
—нижний отсев(отходы)
—выход деловой фракции
—механические потери при грохочении и транспортировании.
Примечание: значения приняты по графику зернового состава выходящего из дробилки.
Обжиг известняка; аппарат—вращающаяся печь на газовом топливе; совокупность процессов.
Крупность известняка загружаемого в печь
1 тепловой процесс нагрев известняка до температуры обжига
Температура известняка на входе +10ºС; начало разложения известняка при t=850 ºС; температура известняка в зоне обжига t=950 ºС; температура отходящих дымовых газов t=200 ºС
—потери в виде выноса пыли из печи
количество теплоты на нагрев известняка;
потери теплоты с отходящими дымовыми газами.
2 Массообменный процесс: обезвоживания известняка
Исходная влажность известняка—5%
Конечная влажность—0%
количество теплоты на испарение воды;
количество известняка поступающего в зону испарения;
количество обезвоженного известняка;
количество испарённой воды;
3 Химический процесс: декарбонизация известняка переход известняка в известь
Содержание CaO+MgО в готовом продукте 90%
затраты теплоты на химическую реакцию
количество получаемой извести;
количество летучего
4Тепловой процесс: охлаждение выходящей извести воздухом
Температура извести на выходе из печи 100 ºС; температура воздуха подаваемого в печь 10 ºС
количество выходящей извести из вращающейся печи;
механические потери извести при транспортировке на склад;
теплота уносимая известью;
Очистка отходящих от печи газов от пыли; процесс гидродинамический; технологическое оборудование: электрофильтры циклоны
Концентрация пыли в выбрасываемом в атмосферу газе не должна превышать 30мгм3 степень очистки отходящих газов—не менее 99%
количество пыли осаждаемой в пылеосадительной системе.
Складирование извести; технологическое оборудование бункер извести.
1 Механический процесс: загрузка извести в складские емкости выгрузка в транспортные средства с частичным усреднением химического и зернового составов
количество извести на складе.
2 Тепловой процесс—самопроизвольно остывание извести на складе
Температура извести отгружаемой в транспортные средства ºС
количество извести отгружаемой на складе потребителям
потери теплоты известью при остывании
Количество известняка поступающего на склад:
Количество известняка поступающего в дробилку:
Количество известняка поступающего на грохот:
Количество известняка поступающего в печь:
Выбор технологического и транспортного оборудования.
где К – коэффициент использования оборудования;
Nфакт – фактическая производительность;
Nном – номинальная производительность.
Шековая дробилка СМД – 110А:
Размер кусков до измельчения мм 600
Размер измельченного продукта мм 20- 40
Габаритные размеры м:
Мощность электродвигателя кВт 100
Производительность 50
Инерционный горизонтальный грохот С—724 :
Полезная площадь сит 24
Габаритные размеры м
Мощность электродвигателя кВт 10
Производительность м3ч до 350
Шахтная пересыпная печь:
Расход тепла на 1 кг извести кДж: 3530 – 5030
Расход условного топлива % от массы извести 12 – 17
Удельный расход электроэнергии кВтчт 10
Производительность тсут 300
Расчет складов выбор оборудования складов.
Склады завода получают сырьё и топливо по железной дороге. Транспортируется в самозагружающихся вагонах. Сырьё поступает на склад в фракционном виде сначала оно поступает в бункера дробильно-сортировочной установки а после дробления ленточными транспортёрами распределяют по приёмным бункерам обжиговой печи. Для доставки известняка со склада к приёмным бункерам применяют опрокидные вагонетки узкой колеи которые откатывают при помощи манёвренных лебёдок МОЛ1 и МОЛ2; Бульдозеры; мостовые и грейферные краны с грузоподъёмностью 5 и 10 т.
Требуемый объём хранящихся на складе сырьевого материала (известняка)
Где -суточный расход сырьевого материала
З—норма запаса материала на складе сутки.
К—коэффициент использования объёма склада 075-085
Длинна склада определяется по формуле
—коэффициент заполнения бункера 09
—количество материала выходящего из бункера
t—время на которое создается запас ч;
Расчёт аппарата для обжига шахтная печь
Производительность печи Р=200 т извести в сутки
Средний химический состав известняка (%) : СаСО3 - 935; МgСО3 - 05; R2О3+S Н2О - 3; (под R2О3 понимают полуторные окислы т. е. Аl2О3 и Fе2О3) .
Топливо - природный газ Елшанского месторождения (Саратовская обл.).
Объемный состав исходного топлива ( % ): СН4 - 932; С2Н6 -О7; С3Н8 -О6; C4H10- N2-49.
Плотность сухого газа ρс.г=0765 кгм3 .
Коэффициент избытка воздуха α = 125.
Относительная влажность воздуха φ=75%.
Температура поступающего воздуха известняка и природного газа tв tи tг= 16° С.
Температура уходящих газов t yx=350 °С.
Температура выгружаемой извести t изв =50°С.
Температура обжига tобж= 1080 °С.
Степень обжига известняка =943%.
Максимальная действительная температура обжига известняка колеблется в пределах 1000-1200°С.
Количество неразложившегося СаСО3 в извести определяют из следующего равенства:
СаСО3 - содержание СаСО3 в известняке;
х - искомое количество неразложившегосяСаСО3 в извести %;
- выход СаО из 1 КГ СаСОз ;
МgCОз - содержание МgСОз в известняке %;
35 и 8435-молекулярная масса соответственно MgO и МgСОз ;
CaO+MgO - активность извести (85%).
После подстановки значении в формулу (2.1) и преобразования получим:
При обжиге 1 кг известняка выделяется:
СО2 из СаСО3 .. (0935 - 0057) = 0386 кг
СО2 ИЗ МgCО3 .. 0005=0003 кг
Расход известняка на 1 кг извести стандартного качества составляет
Известняк массой 100 кг содержит (кг): СаСО3 - 935; МgСО3 - 05; R2О3+ S Н2О - 3.
При обжиге разлагается СаСО3 935· 0943=878 кг.
Неразложившийся остаток СаСО3935-878=57 кг.
По реакциям получается:
Состав расхода известняка
Кол-во компонентов составляющих 1 кг известняка кг
Расход известняка на 1 кг извести кг
На основании приведенного выше расчета составляем материальный баланс процесса обжига известняка (табл. 2).
Количество СаО в выпускаемой из печи извести будет равно 4916 кг.
Содержание СаО в извести равно:
Из 100 кг известняка получается стандартной 85%-ной извести:
Следовательно материальный расчет выполнен правильно.
Материальный баланс обжига на 100 кг известняка
Н2О из известняка 03
Теоретически для получения 1 кг СаО необходимо затратить для обжига
кг СаСО3. Как видно практически при обжиге известняка получается меньшее количество жженой извести и углекислого газа так как не весь известняк загруженный в печь разлагается.
РАСЧЕТ ГОРЕНИЯ ПРИРОДНОГО ГАЗА
Определим количество воздуха состав и количество продуктов горения методом расчета процесса горения топлива. Расчет производим на 100 м3 газа. Для проверки расчета составляем материальный баланс при α = 1.
Расхождение составляет 0064 %
Определяем теплотворную способность газа используя тепловые эффекты реакций горения горючих элементов:
Начальная энтальпия продуктов горения будет равна:
Для определения действительной температуры горения топлива поI-t-диаграмме определяем энтальпию продуктов сгорания за вычетом теплоты потерянной в окружающую среду:
где п - пирометрический коэффициент полезного действия горения.
Для шахтных печей работающих на газообразном топливе п= 067 073.
Тепловой баланс зоны охлаждения на 1 кг извести
С известью нагретой в зоне обжига до 940 0С
где СИ – теплоемкость извести при температуре 940 °С кДжкг·°С.
С известью выгружаемой из печи при 50 0С
Потери тепла в окружающую среду принимаем равными 4 % от тепла извести поступающей в зону охлаждения
С воздухом проходящим через зону охлаждения
Определяем по разности между теплом вносимым в зону охлаждения с известью и теплом потраченным в окружающую среду и с уносимым продуктом
Это значение используем в тепловом балансе зоны обжига.
РАСЧЕТ КОНСТРУКТИВНЫХ РАЗМЕРОВ ШАХТНОЙ ПЕЧИ
Полезный объем шахты Vш (м3 ) определяем из уравнения:
где t– время пребывания материала в печи ч;
γ – масса 1 м3 извести равная 800 кгм3;
Р– производительность печи (кг извести в сутки).
Тогда полезный оббьем шахты составит
Отношение высоты шахты к среднему диаметру принимаем
Рабочая высота шахты:
Предварительный тепловой баланс зоны обжига на 1 кг извести
где В - искомое количество топлива м3
С воздухом поступающим из зоны охлаждения
С материалом поступающим из зоны подогрева в зону обжига
где К - расход известняка на 1 кг извести кг;
Сизв - удельная теплоемкость известняка при t’об=9400 0С равная 111 кДж(кг*oС)
где 1780 - количество теплоты необходимой для разложения 1 кг СаСОз в СаО
На потери в окружающую среду
Принимаем п2=4% количества теплоты вносимой в шахту печи топливом
где n2 - потерянное количество теплоты в окружающую среду к количеству теплоты поступающей в зону обжига
С известью переходящей из зоны обжига в зону охлаждения
С продуктами горения топлива переходящими из зоны обжига в зону подогрева
С углекислотой выделенной при разложении СаСОз
Приход тепла –35200*В + 2517 кДжкг
Расход тепла – 18281*В + 4405 кДжкг
I' = 070·3400 = 2380 кДжм3
По I-t - диаграмме tд= 1510oС.
ОПРЕДЕЛЕНИЕ КОЛИЧЕСТВА ТОПЛИВА ДЛЯ ОБЖИГА 1 КГ ИЗВЕСТИ
Составляем тепловые балансы по зонам печи. Обозначим через В м3 количество топлива необходимого для обжига 1 кг извести стандартного качества. Из теплового баланса зоны обжига определим В.
Для определения расхода топлива приравниваем приход теплоты к его расходу и решаем уравнение относительно В:
200В + 2517 = 18281 В + 4405
Контроль производственного процесса и готовой продукции.
Отбор средней пробы. Каждые 2 часа из печи отбирают известь в количестве около 50кг методом квартования получают пробу 5 кг и помещают её в герметически закрываемый сосуд. Первичную пробу извести 20 кг отобранную за смену методом квартования сокращают до 5 кг получая среднюю пробу которую испытывают.
Подготовка проб для проведения испытания.
Среднюю пробу комовой извести разбивают на куски до 20 мм перемешивают и последовательным квартованием отбирают 500 г которые измельчают до полного прохождения через сито с сеткой 09 по ГОСТ 3584—53. От просеянной пробы отбирают квартованием 60 г извести растирают её в ступке до полного прохождения сквозь сито 02 и хранят в герметично закрытом сосуде.
Среднюю пробу порошкообразной извести перемешивают и последовательным квартованием отбирают 300г которые помещают в герметично закрытый сосуд.
Полученный порошок используют для испытаний в соответствии с ГОСТ 9179—70 «Известь строительная».
Определение суммарного содержания активных CaO и MgO при содержании в извести MgO до 5%
Навеску негашеной комовой или молотой извести массой 4-5 г предварительно растирают в течение 5 минут в фарфоровой ступке. Навеску растертой извести массой 1 г помещают в коническую колбу вместимостью 250 мл добавляют 100-150 мл дистиллированной воды кладут 3-5 стеклянных бус или оплавленных стеклянных палочек длиной 5-7 мм закрывают стеклянной воронкой или часовым стеклом и нагревают 5-7 минут до температуры кипения. Раствор охлаждают до температуры 20-30 °С промывают стенки колбы и стеклянную воронку (или часовое стекло) кипяченой дистиллированной водой добавляют 2-3 капли 1 %-ного спиртового раствора фенолфталеина и титруют при постоянном взбалтывании 1н раствором соляной кислоты НСl до полного обесцвечивания раствора. Титрование считают законченным если в течение 8 минут при периодическом взбалтывании раствор остается бесцветным.
Содержание СаО и МgО в процентах по массе (активность)Аопределяют по формуле
гдеV– количество 1н раствора соляной кислоты пошедшее на титрование мл;К– поправка к титру 1н раствора соляной кислоты; 2804 – количество оксида кальция соответствующее 1 мл 1н раствора соляной кислоты умноженное на 100;G навеска извести взятая для титрования г.
Определение содержания непогасившихся зёрен.
В металлический сосуд цилиндрической формы вместимостью 2—3 л наливают 1—15 л нагретой до температуры 85—90° С воды и всыпают 02 кг извести непрерывно перемешивая содержимое до окончания интенсивного выделения пара (кипения). Полученное тесто закрывают крышкой и выдерживают два часа затем разбавляют холодной водой до консистенции известкового молока и промывают на сите с сеткой № 063 слабой непрерывной струей слегка растирая мягкие кусочки стеклянной палочкой с резиновым наконечником. Остаток на сите высушивают при температуре 105—110° С до постоянной массы. Содержание непогасившихся зерен в процентах вычисляют по формуле
где m — остаток на сите после высушивания г
Мероприятия по технике безопасности охране труда и защите окружающей среды
При производстве и применении извести необходимо руководствоваться «Общими правилами по технике безопасности и промышленной санитарии для предприятий промышленности строительных материалов» и специальными Правилами по технике безопасности для известковых заводов (СН 215 и др.).
На известковых заводах опасность для обслуживающего персонала может возникнуть при нарушении нормального хода технологических процессов и неправильном ведении работ. Особое внимание в частности необходимо уделять предотвращению появления в помещениях углекислого газа (СО2) окиси углерода (СО) и известковой пыли.
Повышенная опасность отравления углекислым газом и окисью углерода имеется на загрузочной площадке шахтных и вращающихся печей. Поэтому сырье загружают только с помощью механизмов (скиповых шахтных и других подъемников) не требующих присутствия на загрузочной площадке людей.
Пыль содержащая гашеную и особенно негашеную известь раздражающе действует на органы дыхания слизистые оболочки и влажную кожу. Поэтому необходимо в местах выделения известковой пыли устраивать отсосы оборудовать помольные агрегаты эффективными обеспыливающими устройствами а весь транспорт и бункера герметически закрывать кожухами крышками и т. д. Также тщательно следует выполнять все мероприятия по технике безопасности при ликвидации зависаний кускового материала возникающих иногда в шахтных печах. Устранять зависания нужно через смотровые окна при помощи специальных металлических штырей.
Чтобы предотвратить ожоги лица и рук при эксплуатации печей пользоваться смотровыми окнами (гляделками) следует очень осторожно и не подходить к ним вплотную. Смотровые окна должны открываться специальными приспособлениями на расстоянии.
Нельзя допускать разбрызгивания известкового молока— оно разъедает кожу лица и рук. Известковое молоко следует транспортировать и хранить в закрытых резервуарах. Опасные места должны быть ограждены барьером.
При гашении извести особенно в холодное время года образуется сильный туман затрудняющий обслуживание гасильных аппаратов и вредно отражающийся на здоровье работающих. Для улучшения условий труда необходим отсос пара у мест его образования; зимой следует подавать теплый воздух к местам гашения.
Все рабочие на известковых заводах должны быть обеспечены специальной одеждой предусмотренной правилами техники безопасности для тех или иных видов работ.
«Процессы и аппараты технологии строительных изделий и материалов.»
«Механическое оборудование» В.А. Бауман.
«Производство извести» А.В.Монастырёв
Волженский А. В. Минеральные вяжущие вещества: (технология и свойства). Учебник для вузов. – М.: Стройиздат 1979. – 476 с
Воробьев В. А. Комар А. Г. Строительные материалы. Учебник для вузов.
продольный разрез с оборудованием_recover.dwg

Рекомендуемые чертежи
- 07.06.2014
- 08.04.2024
- 12.12.2016
Свободное скачивание на сегодня
Другие проекты
- 20.08.2014