Вертикально сверлильный станок(агрегат)



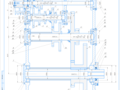

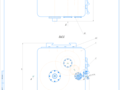
- Добавлен: 25.01.2023
- Размер: 528 KB
- Закачек: 0
Описание
Вертикально сверлильный станок(агрегат)
Состав проекта
![]() |
![]() |
![]() ![]() ![]() ![]() |
![]() ![]() ![]() |
![]() ![]() ![]() ![]() |
![]() |
![]() |
![]() ![]() ![]() ![]() |
![]() |
Дополнительная информация
Спецификация.spw

Винт М4 х 14 ГОСТ 11644-75
Винт М3 х 8 ГОСТ 11644-75
Винт М5 х 16 ГОСТ 17475-80
Шайба 7019-0628 ГОСТ 14734-69
Шайба 3 Н ГОСТ 6402-70
Мaнжета 1-17 х 35-1 2 ГОСТ 8752-79
Мaнжета 1-45 х 65-1 ГОСТ 8752-79
Подшипник 209 ГОСТ 8338-75
Подшипник 106 ГОСТ 8338-75
Подшипник 104 ГОСТ 8338-75
Подшипник 203 ГОСТ 8338-75
Шпонка 10 х 8 х 80 ГОСТ 23360-78
Винт М10 х 45 ГОСТ 1491-80
ГОрожанкина ПЗ.docx
Выбор условий технологического использования станка
Определение основных технических характеристик проектируемого станка ..
Составление кинематической схемы привода и кинематический расчет ..
)Режим работы привода главного движения .
)Определение числа ступеней коробки и структуры привода .
)Определение передаточных отношений передач привода
)Определение чисел зубьев ..
)Проверочный расчет частот вращения .
Определение расчетных значений крутящих моментов . .
Определение межосевых расстояний
Расчет параметров передач .
Проектирование ременных передач
Предварительное определение диаметров валов
Проверочный расчет вала
Расчеты шпоночных соединений
Список литературы ..
Компоновка металлорежущих станков определяется пространственным положением их шпинделей и взаимным расположением основных функциональных узлов. В соответствии с расположением рабочих шпинделей встречаются станки горизонтальных вертикальных наклонных и комбинированных компоновок. Практически они встречаются в пределах любой группы современных станков. Например имеются станки вертикально- и горизонтально-сверлильные вертикально- и горизонтально-фрезерные вертикально- и горизонтально-расточные и т. д.
Принципы по которым складывались эти компоновки неразрывно связанны с совместной работой человека и машины и поэтому они подчинены физическим возможностям человека - его росту силе утомляемости при различных положениях и т. д.
К указанным традиционным станкам в частности относятся вертикально-сверлильные принципиальная компоновка которых наилучшим образом отвечает требованиям работы сверловщика при обработке деталей средних габаритов.
Все встречающиеся компоновки вертикально-сверлильных станков могут быть разделены на следующие три большие группы: типа кронштейн агрегат (или подвижный моноблок) и пресс (неподвижный моноблок). Эти названия носят условный характер но их смысл отражает сущность компоновочных решений.
Станки с компоновкой типа кронштейн (см. рис.1(а)) характеризуются тем что коробка скоростей 2 оформлена в виде самостоятельного узла расположенного на верхней части колонны 3. Шпиндель коробка подач и механизм подач размещаются в корпусе 1 образуя один законченный архитектурный узел. Этот узел по традиции называют кронштейном (отсюда и название компоновки). Долгое время компоновка вертикально-сверлильных станков типа кронштейн считалась классической. С такой компоновкой изготовлялись все отечественные вертикально-сверлильные станки средних и больших размеров. Однако в 60-х годах прошлого столетия наша станкостроительная промышленность как и многие передовые зарубежные фирмы перешла на агрегатную компоновку.
Встречаются также станки промежуточных типов в которых встречаются элементы указанных компоновок. Например современные вертикально-сверлильные станки с программным управлением выполняются в основном по агрегатной компоновке а механизм подач с тиристорным приводом монтируется на колонне в том месте где в компоновках типа кронштейн устанавливалась коробка скоростей.
Высокую производительность современные станки обеспечивают за счёт быстроходности мощности и широкой автоматизации. В современных тяжелых станках мощность только главного электродвигателя достигает 150 кВт а всего на одном станке иногда устанавливают несколько десятков электродвигателей. Вес уникальных станков достигает нескольких тысяч тонн.
Высокого уровня достигла автоматизация станков. Имеются например автоматические линии состоящие из сотен сложных станков и включающие контрольные и сборочные операции.
При конструкционном оформлении для придания станку требуемых качеств и функций используют разнообразные механизмы с применением гидравлики электрики пневматики; применяют также детали сложных конструкционных форм с высокими требованиями к их качественным показателям внедряют прогрессивные принципы проектирования (агрегатирование унификация); изыскивают наиболее рациональные компоновки станков разрабатывают новые системы управления циклом.
Наряду с развитием и совершенствованием существующих обработки появились станки на базе принципиально новых ТП. К таким процессам относят электроэрозионную обработку использующую воздействие электронного разряда на металл; электрохимические методы обработки обработку сфокусированным лучом высокой энергии обработку тонкой струей жидкости при сверхвысоком давлении ультразвуковой метод когда поверхность подвергается воздействию абразивных частиц при колебании инструмента с высокой частотой и другие методы.
Таким образом станки которые называют металлорежущими включают более широкую группу машина - орудий обрабатывающих не только металлы но и другие материалы различными методами.
Для выполнения таких разнообразных технологических задач с высокими требованиями к качеству продукции и производительности процесса в станках необходимо использовать новейшие достижения инженерной мысли.
Тип станка – вертикально-сверлильный(Агрегат);
Диапазон регулирования Rn = 60;
Размерная характеристика станка: 20;
Обрабатываемый материал: констр. сталь твердость НВ260 320;
Характер обработки: черновая;
Компоновка привода: раздельная;
Структура привода: сложенная;
Способ регулирования: ступенчатое;
Электродвигатель: 1-скоростной
Способ переключения скоростей: ручное;
Сборочная единица: коробка передач .
Знаменатель ряда значений скоростей главного движения: =14 (принят как рекомендуемое значение для сверлильных станков);
Анализ аналогичных станков
У всех наибольший диаметр сверла 20 мм.
Определение основных технических характеристик проектируемого станка
Наибольший диаметр сверления
Наименьший диаметр сверления принимаемый в расчет при проектировании станка определяется зависимостью:
Минимальная глубина резания
Smin = 015 мм (из таблицы со станками)
Максимальная скорость резания для конструкционной стали
Где cv tv xv yv m T n - параметры зависящие от механических свойств инструмента и обрабатываемого материала:
Максимальная скорость резания (для алюминия). Скорость резания алюминия 100 500 ммин.Т. к. у алюминия НВ обычно 15 35 НВ а алюминиевый сплав АК21М2Н5 - 100 НВ то примем алюминиевый сплав
Максимальную скорость резания принимаем по стали: Vmax=333 ммин.
Максимальное число оборотов шпинделя
Минимальное число оборотов шпинделя
; принимаем nmin=40 мин-1
Рэ=15 кВт (из таблицы со станками)
Составление кинематической схемы привода и кинематический расчет
Выбираем электродвигатель 2ПБ-132МГ :
Определение числа ступеней коробки и структуры привода.
Для сверлильно-вертикального станка знаменатель ряда равен :
Принимаем ряд частот вращения шпинделя:
Структура нормальная:
Структурная сетка привода модуля главного движения
Принципиально кинематическая схема привода модуля главного движения.
Рис.3 Диаграмма частот вращения привода главного движения
Определение передаточных отношений передач привода
Определение чисел зубьев
где - коэффициент проскальзывания ремня;
Для диаметра вала электродвигателя 2ПБ-132МГ соответствует диаметр шкива;
Определим числа зубьев шестерён
Для исключения подрезания зубьев примем условие zmin=18 20. Увеличим количество зубьев в 2 раза.
Для исключения подрезания зубьев примем условие zmin=18 20. Увеличим количество зубьев в 7 раза.
Проверочный расчет частот вращения
Допустимое отклонение частоты вращения:
Таким образом подобранные числа зубьев и диаметры шкивов подходят для данной схемы.
Определение расчетных значений крутящих моментов
Определение мощности на валах привода.
- КПД подшипников качения;
- КПД зубчатого зацепления;
. - КПД ременной передачи;
Определение крутящих моментов на валах:
Предварительный расчёт валов.
Приближённо определяем диаметры валов по условию прочности для среднеуглеродистой стали (в = 5 ÷8 МПа) для напряжения кр = 500÷285 кПа:
Ограничение по жёсткости (для допускаемого угла закручивания [] (44 ÷88) ×10-3 рад (~025 ÷ 05) 0 на 1 мм. длины вала):
Так как диапазоны минимально допустимых по условию жёсткости диаметров валов больше чем по условию прочности принимаем за ориентировочный наименьший допускаемый - диаметр по условию жёсткости.
Округляем до стандартного значения по ГОСТ 12081 – 72 в сторону увеличения. Имеем: dI = 20 мм.; dII = 25 мм.; dIII = 35 мм; dIV = 50 мм.
Расчёт межосевого расстояния.
Расчёт производим по следующей формуле:
Ка – вспомогательный коэффициент: для прямозубых передач
u – передаточное число: ;
Т2H - крутящий момент на колесе;
ba bd – коэффициенты учитывающие ширину зуба ba==
= 01 т. к. bd = а то bd = ;
КН – коэффициент учитывающий неравномерность
распределения нагрузки по ширине венца;
НР – допускаемое контактное напряжение
H lim – предел контактной выносливости поверхности зубьев
соответствующий эквивалентному числу циклов перемен
H lim b = предел контактной выносливости поверхности зубьев
соответствующий базовому числу циклов перемен напряжений:
КHL – коэффициент долговечности: ориентировочно нагрузку станка принимаю за постоянную а NНЕ > NHO тогда КHL = 1 где NHE и NHO – эквивалентное и базовое число циклов перемен напряжений соответственно.
SH – коэффициент безопасности: SH = 12;
ZR – коэффициент учитывающий шероховатость сопряжённых поверхностей зубьев;
ZV – коэффициент учитывающий окружную скорость;
KL – коэффициент учитывающий влияние смазки;
= 09 по нормам точности зубчатых передач для станка нормальной точности;
Определяем межосевое расстояние:
Расчет параметров передач
Модуль первой ступени:
Модуль второй ступени:
Принимаем стандартные модули: =20; =25; =35
Уточняем межосевое расстояние по формуле:
Геометрический расчёт зубчатой передачи.
Нахождение делительного диаметра колёс.
d1 = m12 ×z1 = 2 ×36=72 мм;
d2 = m12 ×z2 = 2 ×36=72 мм;
d3 = m3456 ×z3 = 2 ×30=60 мм;
d4 = m3456 ×z4 = 2 × 42 =84 мм;
d5 = m3456 ×z5 = 2 × 24= 48 мм;
d6 = m3456 ×z6 = 2×48 = 96 м;
d7 = m78910 ×z7 = 25 × 38 = 95 мм;
d8 = m78910 ×z8 = 25×38 = 95 мм;
d9 = m78910 ×z8 = 25×20 = 50 мм.
d10 = m78910 ×z7 = 25 × 56 = 140 мм;
d11 = m11121314 ×z8 = 35×70 = 245 мм.
d12 = m11121314 ×z7 = 35 × 35 = 1225 мм;
d13 = m11121314 ×z8 = 35×21 = 735 мм.
d14 = m11121314 ×z8 = 35×84 = 294 мм.
Определение ширины колес.
b= а × аw где а = 01
b w1 = а × а1-2 = 01 × = 72 мм; примем 8 мм
b w1’ = а × а1-3 = 01 × = 95 мм; примем 10 мм
b w2 = а × а2-3 = 01 × = 184 мм; примем 19 мм
Расчёт вала на прочность
1 Расчет валов на прочность.
Выполним расчет на прочность предпоследнего вала (смотри чертёж). Силы в зацеплении:
где угол зацепления по ГОСТ 13755-81
Определим нагрузку в опорах.
Вертикальная плоскость.
Горизонтальная плоскость.
Находим изгибающий момент в горизонтальной плоскости.
My(l1)=Ray* l1=343*116=398*10 3 Н*м
My(x)=Ray*x-Fr2*(x-l1)
My(l1+l2)=Ray*(l1+l2)-Fr8*l2=343*(116+161)-702*161=-18*10 3 Н*м
My(х)=Ray*x-Fr8*(x-l1)+Fr13*(х-(l1+l2))
My(l1+l2+l3)=Ray*(l1+l2+l3)-Fr8*(l2+l3)+Fr13*l3=0
Находим изгибающий момент в вертикальной плоскости.
Mx(l1)=Rax*l1=-840*161=-1352*10 3 Н*м
Mx(x)=Rax*x+Ft8*(x-l1)
Mx(l1+l2)=Rax*(l1+l2)+Ft8*l2=-840*(116+161)+1720*161=442*10 3 Н*м
Mx(х)=Rаx*x+Ft8*(x-l1)-Ft13*(х-(l1+l2))
Mx(l1+l2+l3)=Rаx*(l1+l2+l3)+Ft2*(l2+l3)-Ft7*l3 =0
Суммарный изгибающий момент
М(l1+l2)==477*103 Н*м
Опасным сечением является место расположения колеса 7
Максимальный изгибающий момент М=141 x103 Нм
Крутящий момент Т=8171 Нм
Примем что нормальные напряжения изменяются по симметричному циклу
а касательные напряжения- по пульсирующему циклу
Материал вала - сталь 45(т=500 МПа в=750 МПа -1=330 МПа
а=м=05 х =103 x Т(2 x WK)
а=м =(8171 х 103)(2 х8414)=485 МПа
а =(141 х 103)4207=355 МПа
Запас прочности рассчитывается по формуле:
-1D и -1D пределы выносливости вала в рассматриваемом сечении
К и К - эффективные коэффициенты концентрации напряжений
Кd и Кd - коэффициенты влияния абсолютных размеров поперечного сечения
КF и КF - коэффициенты влияния качества поверхности
К - коэффициент влияния поверхностного упрочнения
К =23 К=215 [2таб.10.10]:
Кd = Кd=085 [2 таб.10.7]:
КF =085 КF=09 [2таб.10.8]:
D- коэффициент влияния асимметрии цикла для рассматриваемого сечения вала
- коэффициент чувствительности материала к асимметрии цикла напряжений
Так как [S]=15÷20 то условие прочности выполняется
4 Проверка подшипников на грузоподъемность
Проведем расчет для третьего вала.
Наиболее нагруженной опорой является опора А.
Выбираем подшипник №106-шарикоподшипник радиальный однорядный.
Требуемый ресурс Lh=10000ч
Эквивалентная нагрузка:
P=(X х V х Fr+Y х Fв) х K х K
Р=(1х1х1584)х13х1=20592 Н
Эквивалентная долговечность:
Lhe=Lh х Khe=10000 х 0125=1250часов
Требуемый ресурс на расчетном режиме:
Lе=60 х 10-6 х n х Lhe=60 х 106 х 200 х 1250=15 млн.об.
Расчетная динамическая грузоподъемность:
Подшипник пригоден так как расчетная динамическая грузоподъемность меньше требуемой.
5 Проверка подшипников на долговечность
Lh>Lhe 1258>1250 час
Расчёт ремённой передачи
Исходные денные: d2 = 1096 мм.
По диаграмме (Анурьев)выбираем тип ремня Z
Количество ремней определяется исходя из мощности электродвигателя и номинальной мощности передаваемой одним ремнём для i = 18 и мощность передаваемая одним ремнём = 07 кВт (Анурьев стр. 748)
Расчет шпоночного соединения
шпоночное соединение удовлетворяет условию прочности.
Список использованной литературы
Проников А.С. Расчет и конструирование металлорежущих станков-
Изд. 2-е. -Высшая школа 1968 стр.1-431
Дунаев П.Ф. Леликов О.П. Конструирование узлов и деталей машин:
Учеб. Пособие для машиностроит. спец. Вузов. 4-е изд. перераб. и
доп.- М.:Высш. шк. 1985-416с.
Анурьев В.М. справочник конструктора-машиностроителя.-
М.:Машиностроение 1982.
Методические указания к лабораторным работам по курсам: Оборудование машиностроительного производства Промышленное
оборудование Металлорежущие станки и промышленные роботы
Уфимск. гос. авиац. техн. ун-т; Сост. Акмаев О.К. Уфа 1999.-24с.
Лист 2.cdw

Лист1_посл.cdw

Перед сборкой гладкие цилиндрические и резьбовые соединения
Механизм должен работать без рывков и заеданий.
Отклонения размеров валов h12