Цилиндрический косозубый редуктор




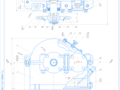
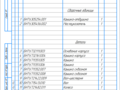
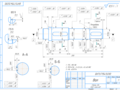
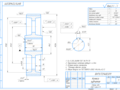
- Добавлен: 24.01.2023
- Размер: 609 KB
- Закачек: 0
Описание
Состав проекта
![]() |
![]() ![]() ![]() ![]() |
![]() ![]() ![]() ![]() |
![]() ![]() ![]() ![]() |
![]() ![]() ![]() |
![]() ![]() ![]() ![]() |
![]() ![]() ![]() ![]() |
Дополнительная информация
Спецификация.spw

Шайба мазеудерживающая
Манжета ГОСТ 8752-79
Отдушина ГОСТ 50370-92
Подшипник ГОСТ 8338-75
Шайба ГОСТ 14734-69
Шпонка ГОСТ 29175-91
Колесо.cdw

Нормальный исходный контур
Направление линии зуба
Гр. II 230 260HB ГОСТ 8479-70
Неуказанные литейные радиуся -4 5мм.
Острые кромки притупить
Размеры обеспеч. инстр.
Общие допуски по ГОСТ30893.1-2002: H14
Редуктор.cdw

Передаваемая мощность P = 4
Частота вращения выходного вала n
Номинальный вращающий момент на выходном валу T
Передачное число редуктора u = 5.
Расчетный суммарный срок службы 14000 часов.
Технические требования:
Ведущий вал собранного редуктора должен проворачиваться
Перед обкаткой залить масло индустриальное И-40А
ГОСТ 20799-75 или масло трансмиссионное ТЭп-15
ГОСТ 36252-79. Уровень масла контролировать маслоуказателем
Шум передач должен быть равномерным без металлических стуков.
Корректировать уровень звуковой мощности не выше 98 дБА.
Течь масла в местах неподвижных соединений не допускается.
Требования к манжетным соединениям валов по ГОСТ 8752-79.
После обкатки редуктор осмотреть
при необходимости подтянуть
подшипники и болтовые соединения.
Грунтовку наружных поверхностей
кроме выходных концов валов
произвести грунтом ВА-03к коричневый ГОСТ 19024-73.V.Ж
записка.doc
Расчет будет производиться по [1].
Pвых = 42 кВт; nвых = 206 мин-1; L = 14000 часов.
По табл. 3.1 [1] выбираем ориентировочные значения КПД для передач.
Требуемая мощность электродвигателя: кВт.
Uцеп. = 2-3; Uред. = 3-5; Uобщ. = Uцеп.* Uред. = 3*5 = 15
Требуемая частота электродвигателя:
Рассчитываем общее передаточное число:
Принимаем значения передаточных чисел для цилиндрического редуктора и цепной передачи по ГОСТ 2185-66.
Значения передаточного числа
Подбираем электродвигатель с номинальной мощностью равной или несколько превышающей расчетную. Принимаем электродвигатель единой серии А4 типа 100L22880 для которого Pном = 55 кВт; nдв.ас = 2880 мин-1. (см. табл. 3.3 [1]).
Условие выполняется.
Определяем частоты вращения валов привода:
-частота вращения вала электродвигателя и ведущего вала редуктора:
-частота вращения ведомого вала редуктора и вала рабочей машины:
Определение мощностей и передаваемых крутящих моментов
Определение мощностей на валах привода:
-потребляя мощность электродвигателя
-мощность на ведущем валу редуктора
-мощность на ведомом валу редуктора
-мощность на ведущем рабочей машины
Определяем вращающие моменты на валах привода:
-момент на валу электродвигателя
-момент на ведущем валу двигателя
-момент на ведомом валу двигателя
-момент на валу рабочей машины
Данные расчета представим виде таблицы (табл. 2).
Сводная таблица данных кинематического расчета
Передаточное число U
Расчет передач: проектный и проверочный расчеты. Расчет передач на ЭВМ и сравнительный анализ
Выбор материала и способа термообработки колес
Выбор материала для изготовления зубчатой пары для обеспечения одинаковой долговечности обоих колес и ускорения их приработки твердость материала шестерни следует назначать больше твердости материала колеса. Разность твердостей для колес с Ннв 350 НВ рекомендуется у косозубых передач (20-70) НВ.
Для изготовления шестерни и колеса передачи редуктора выбираем сталь 40Х (ГОСТ 4553). Термообработка – улучшение: для шестрени – до твердости Ннв1 = 217 для колеса – до твердости Ннв2 = 170 (см. табл. 3.4).
1 Расчет допускаемых контактных напряжений
Допускаемые напряжения определяются для шестерни и колеса по формуле:
где - предел контактной выносливости поверхностей зубьев соответствующий базовому числу циклов напряжений (табл. 5.2):
SН – коэффициент запаса прочности; SН =11 [6];
ZN – коэффициент долговечности:
– базовое число циклов нагружений соответствующее пределу выносливости вычисляем по формуле:
где Ннв – твердость материала рассчитываемого зубчатого колеса в единицах НВ;
NK – число циклов перемены напряжений соответствующее заданному сроку службы передачи при постоянной нагрузке [6]:
NK = 60 · с · n · Lh
где с– число колес находящихся в зацеплении с рассчитываемым;
Lh – срок службы привода ч (см. задание);
n – частота вращения рассчитываемого зубчатого колеса.
NK1 = 60 · с · n1 · Lh = 60 · 1 · 2880 · 14000 = 24192 · 106 циклов;
NK2 = 60 · с · n2 · Lh = 60 · 1 · 576 · 14000 = 48384 · 106 циклов.
ZR – коэффициент учитывающий влияние исходной шероховатости сопряженных поверхностей зубьев [7 с. 24];
ZV – коэффициент учитывающий влияние окружной скорости [7 с. 24];
ZL – коэффициент учитывающий влияние вязкости смазного материала [7 с. 24];
ZX – коэффициент учитывающий размер зубчатого колеса [7 с.24];
ZW – коэффициент учитывающий влияние перепада твердостей материала сопряженных поверхностей зубьев.
При проектировочных расчетах по ГОСТ 21354–87 [7 с. 57] рекомендует принимать
ZR × ZV × ZL × ZX· ZW = 09.
так как NH lim 1 NK 1 и NH lim2 > NK 2 то
Для цилиндрической косозубой передачи для расчета [6 с. 342] принимается:
НР = 045(НР 1 + НР 2) > НР min
при выполнении условия НР 1–2 123 НР min
НР = 045(НР 1 + НР 2) = 045 (31647 + 27096) = 26434 МПа;
НР m 123 · НР min = 123 · 27096 = 33328 МПа.
Так как НР меньше минимального из двух значений НР 1 и НР 2 в качестве расчетного напряжения принимаем минимальное значение НР = НР 2 = 27096 МПа.
2 Определение допускаемых напряжений изгиба
Допускаемые напряжения изгиба при расчете на выносливость FP определяются по формуле
где – предел выносливости зубьев при изгибе соответствующий базовому числу циклов напряжений; выбирается по табл. 5.3 в зависимости от способа термической или химико-термической обработки [6 с. 343 табл. 18.7]; [7 с. 47 табл. 16];
Yt – коэффициент учитывающий технологию изготовления; Yt=1 [7 с. 34];
YZ – коэффициент учитывающий способ получения заготовки зубчатого колеса: поковка и штамповка YZ = 1; прокат YZ = 09; литье YZ = 08 [7 с. 34];
Yg – коэффициент учитывающий влияние шлифования переходной поверхности зуба; для нешлифованной переходной поверхности принимают Yg = 1 ([7 с. 34]);
Yd – коэффициент учитывающий влияние деформированного упрочнения или электрохимической обработки переходной поверхности; если этого нет то Yd = 1 [7 с. 34];
YA – коэффициент учитывающий влияние двустороннего приложения нагрузки (реверс); при одностороннем приложении нагрузки YA = 1 при двухстороннем– YA = 07–08.
YR – коэффициент учитывающий влияние шероховатости переходной поверхности; при отсутствии полирования переходной поверхности зуба YR = 1 [7 с. 36];
YХ – коэффициент учитывающий размер зубчатого колеса при da ≤ 300 мм YХ = 1 [7 с. 37];
Yd – опорный коэффициент учитывающий чувствительность материала к концентрации напряжений; для модуля передачи от 1 до 8мм этот коэффициент убывает от 11 до 092; примем Yd = 10 [7 с. 36];
SF – коэффициент безопасности SF = 14–17 [7 c. 35];
YN – коэффициент долговечности [7 c. 29].
NK – общее число циклов перемены напряжений при нагрузках с постоянными амплитудами: NK = 60 · с · n · Lh [6 с. 343]; [8 с.93 194];
qF– показатель кривой усталости: для зубчатых колес с однородной структурой материала включая закаленные при нагреве ТВЧ со сквозной закалкой и зубчатых колес со шлифованной переходной поверхностью независимо от твердости и термообработки их зубьев qF = 6; qF = 9 – для зубчатых колес с нешлифованной переходной поверхностью при твердости поверхности зуба ННВ > 350 [8 с.194]; [7 с. 32].
принимаем YN1=1 YN2=1 т.к. YN1(2) YFlim
F lim b 1 = 175 · 217 · 1· 1 · 1 · 1 · 1 = 37975 МПа
F lim b 2 = 175 · 170 · 1· 1 · 1 · 1 · 1 = 2975 МПа.
NK1 = 24192· 106 циклов
NK2 = 48384 · 106 циклов.
FP 1 = 37975 · 1 · 1 · 1 · 1 17 = 33456 МПа
FP 2 = 2975 · 1 · 1 · 1 · 1 17 = 27794 МПа.
3 Проектировочный расчет передачи
Проектировочный расчет передач служит только для предварительного определения размеров и не отменяет расчета на контактную выносливость.
При проектировочном расчете определяется один из геометрических параметров передачи– межосевое расстояние аw или делительный диаметр шестерни d1 [7 с. 57]. Предпочтительным считается расчет аw так как его значение сразу дает представление о габаритах передачи.
Делительный диаметр шестерни:
где Kd – вспомогательный коэффициент; Kd = 675 – для косозубых и шевронных передач; Kd = 770 – для прямозубых передач [6 с.331]; [7 с. 57].
Ориентировочное значение межосевого расстояния [6 с.332; 7 с. 57]
где знак «плюс» используется при расчете передач внешнего зацепления а «минус» – для передач внутреннего зацепления;
Ka – вспомогательный коэффициент: для прямозубых передач Ka = 495 для косозубых и шевронных передач Ka = 430 [6 с. 332; 7 с. 57];
Т2 – вращающий момент на колесе (на ведомом звене);
u – передаточное число передачи;
КH – коэффициент учитывающий неравномерность распределения нагрузки по длине контактных линий принимают в зависимости от твердости колес и параметра bd по графику (рис. 5.3):
bd = b2 d1 = 05 ba(u ± 1)
bd– коэффициент ширины колеса относительно делительного диаметра шестерни;
ba– коэффициент ширины колеса относительно межосевого расстояния; принимают из стандартного ряда чисел в зависимости от положения колес относительно опор (см. с. 22).
Передача косозубая расположение колес – симметричное следовательно
bd = 05 [04(5 + 1)] = 12;
Полученное ориентировочное межосевое расстояние округляем до стандартного значения по предпочтительному ряду (табл. 5.4 с.55). Принимаем аw = 120 мм.
Нормальный модуль при принятой термообработке колес рекомендуется выбирать из диапазона
mn = (001–002) аw = (001–002) · 120 = 12–24 мм.
Из стандартного ряда модулей (табл. 5.5 с. 55) принимаем m=2мм. Значение модуля менее 15 мм для силовых передач задавать не рекомендуется.
Рабочая ширина колеса
b2 = ba · аw = 04 · 120 = 48 мм;
b1 = b2 + (2–7) мм = 48 + (2–7) = 50-55 мм.
Принимаем b1 = 55 мм.
Угол наклона зубьев для косозубого зацепления без смещения рекомендуется = 7–18°.
Предварительно приняв коэффициент осевого перекрытия = 1 [8 с. 174 табл. 9.1] определим минимальный угол наклона зубьев:
min = arcsin(4mn b2) = arcsin(848) = 959.
Величиной угла можно задаться например = 10°.
Суммарное число зубьев [2 с. 13]
z = (2 · аw · cos ) m = (2 · 120 · cos 7527) 2 = 11896.
Принимаем z = z1 + z2 = 118.
Определим числа зубьев шестерни z1 и колеса z2.
z1 = z (u +1) =118 (5 +1) = 1967;
z2 = z – z1 = 118 – 20 = 98.
Фактическое передаточное число uф = z2 z1 = 9820 = 49.
u = (uф – u) u · 100% = ((5 – 49) 5) · 100%) = 2% ≤ 4%.
Для того чтобы вписать косозубую цилиндрическую передачу в заданное межосевое расстояние аw = 125мм при принятых числах зубьев зубчатых колес уточним угол наклона зубьев:
cos = m (z1 + z2)(2 · аw) = 2 (20 + 98) (2 · 120) = 0983°;
Определим делительные диаметры диаметры вершин и впадин зубьев зубчатых колес:
d1 = m · z1 cos = 2 · 20 0983 = 4068 мм;
d2 = m · z2 cos = 2 · 98 0983 = 19932 мм;
dа1= d1 + 2 · m = 4068 + 2 · 2 = 4468 мм;
dа2 = d2 + 2 · m = 19932 + 2 · 2 = 20332 мм;
df1= d1 – 25 · m = 4068 – 2 · 25 = 3568 мм;
df2 = d2 – 25 · m = 19932 – 2 · 25 = 19432 мм.
Выполним проверку межосевого расстояния:
аw = (d1 + d2) 2 = (4068 + 19932) 2 = 120 мм.
Вычислим величину усилий действующих в зацеплении и изобразим схему действия сил (рис. 5.2):
Ft = 2 · Т2 d2 = 2 ·70367 19932 = 70606 Н;
Fr = Ft · tg αtw cos = 70606 ·tg 20° 0983 = 26134 Н;
Fа = Ft · tg = 70606 ·tg 10°47'53'' = 103545 Н.
Рис. 2. Схема сил действующих в косозубом цилиндрическом зацеплении
4 Проверочный расчет передачи на контактную усталость
Контактная выносливость устанавливается сопоставлением действующих в полюсе зацепления расчетного Н и допускаемого НР контактных напряжений [6 с. 330]; [7 с. 14]:
где Н0 – контактное напряжение в полюсе зацепления при KН = 1 [7 с. 14]:
Коэффициент нагрузки KН определяют по зависимости [6 с. 327]; [7 с. 14].
KН = KА · KHv · KH · KHα
где KA = 1– коэффициент учитывающий внешнюю динамическую нагрузку [6 с. 327]; [7 табл. 6 с. 15];
KHv – коэффициент учитывающий внутреннюю динамическую нагрузку возникающую в зацеплении до зоны резонанса [6 с. 328]; [7 табл. 6 с. 16]:
где Hv – удельная окружная динамическая сила Нмм [6 с.328]; [7 табл. 6 с. 16].
где Н – коэффициент учитывающий влияние вида зубчатой передачи и модификации профиля головок зубьев (табл. 5.7);
g0 – коэффициент учитывающий влияние разности шагов зацепления зубьев шестерни и колеса (табл. 5.8);
– окружная скорость зубчатых колес:
KHα – коэффициент учитывающий распределение нагрузки между зубьями; для прямозубых передач и косозубых при осевом коэффициенте перекрытия ≤ 1 KHα = 1; при > 1 см. табл. 5.9;
– осевой коэффициент перекрытия: = b2 · s
ZE – коэффициент учитывающий механические свойства материалов сопряженных зубчатых колес; для стальных колес ZE = 190 [7 табл. 6 с. 15];
ZH – коэффициент учитывающий форму сопряженных поверхностей зубьев в полюсе зацепления [7 табл. 6 с. 15]:
где αt – делительный угол профиля в торцовом сечении: αt = α = 20° [8 с. 174 табл. 9.1];
b – основной угол наклона для косозубой передачи:
αt – угол зацепления для косозубой передачи без смещения;
tg αt = tg α cos [8 с. 174 табл. 9.1];
Z – коэффициент учитывающий суммарную длину контактных линий [7 с. 15 табл. 6]; для косозубых передач при ≥ 1
α – коэффициент торцового перекрытия [8 с. 175 табл. 9.1]:
α = [188 – 32 (1 z1 ± 1 z2)] cos .
Для рассчитываемого объекта имеем следующие данные: редуктор цилиндрический косозубый одноступенчатый частота вращения ведущего вала n1 = 2880 мин-1 передаточное число редуктора uф=
= 49; частота вращения ведомого вала n2 = 576 мин-1 вращающие моменты на валах Т1 = 14655 Н · м; Т2 = 70367 Н · м; z1 = 20; z2 =
= 98; = 1047533°'; m = 2 мм; a = 120мм; b2 = 48 мм; d1=
= 44678 мм; Ft = 70606 Н.
tg αt = tgα cos = tg20° cos 104753° = 036;
α = [188 – 32 (1 20 + 1 98)] cos104753° = 16592;
= · 44678 · 2880 (60 ·103) = 67373 мс.
Для данной скорости колес степень точности – 9-я (см. табл. 5.6).
KHv = 1+ (4816 · 48)70606 = 1327; KHα = 10; KА =10; KH = 112;
KН = 10 · 1327 · 112 · 10 = 1486.
Определим процент перегрузки:
Н = НР – Н НР ·100% = 26557–27096 27096 · 100 % = 4%.
Условие прочности выполняется. По принятым в машиностроении нормам допускаются отклонения +5% (перегрузка) и –10% (недогрузка).
Если отклонение выходит за указанные пределы то размеры и другие параметры необходимо откорректировать. Рекомендуется в небольших пределах изменить ширину колеса (при перегрузках – увеличить при недогрузках – уменьшить); изменить межосевое расстояние; выбрать другой режим термообработки поверхностей зубьев и соответственно изменить твердость поверхности зубьев что приведет к увеличению или уменьшению НР.
5 Проверочный расчет передачи на изгибную усталость
Расчетом определяется напряжение в опасном сечении на переходной поверхности зуба для каждого зубчатого колеса. Выносливость зубьев необходимая для предотвращения их усталостного излома устанавливают сопоставлением расчетного напряжения от изгиба и допускаемого напряжения: F ≤ FP.
Расчетное местное напряжение при изгибе [7 с. 29]
где KF – коэффициент нагрузки: KF = KА · KFv · KF · KFα;
KFv – коэффициент учитывающий внутреннюю динамическую нагрузку возникающую в зацеплении до зоны резонанса [7 с. 30 табл. 13]:
гдеFv – удельная окружная динамическая сила Нмм [7 с. 30 табл. 13]:
F – коэффициент учитывающий влияние вида зубчатой передачи и модификации профиля головок зубьев (табл. 5.7);
KF – коэффициент учитывающий неравномерность распределения нагрузки по длине контактных линий принимают в зависимости от параметра bd по графику (рис. 5.4);
KFα – коэффициент учитывающий распределение нагрузки между зубьями (табл. 5.9);
YFS – коэффициент учитывающий форму зуба и концентрацию напряжений (рис. 5.5).
Для определения менее прочного звена необходимо рассчитать отношение FP YFS проверку производить по тому из колес пары укоторого это отношение меньше;
Y– коэффициент учитывающий наклон зуба; Y =13888;
Y – коэффициент учитывающий перекрытие зубьев; для косозубых передач при ≥ 1
Y= 1 1.6592 = 0.602;
Следовательно KF = KА· KFv · KF · KFα = 1·198·135·135 = 361.
Y = 1 – · 120° = 1 – 13888 · (9387° 120°) = 09387 > 07
Y = 1 α = 1 16592 = 0602.
Определим эквивалентные числа зубьев шестерни и колеса [7 с.62 табл. 20]:
ZV1 = Z1 cos3 = 20 cos39387° = 20825;
ZV2 = Z2 cos3 = 98 cos39387° = 10205.
Следовательно YFS 1 = 408; YFS 2 = 36 (рис. 5.5).
Определим отношение FP YFS:
FP 1 YFS 1 = 22338 408 = 5475;
FP 2 YFS 2 = 175 36 = 4861.
Расчет по изгибным напряжениям ведем для колеса так как FP1 YFS 2 FP 2 YFS 2:
Условие прочности выполняется: 6416МПа 27096 МПа.
Значение F1 значительно меньше FP2 однако это нельзя рассматривать как недогрузку передачи так как основным критерием работоспособности данной передачи является контактная усталость.
6 Расчет цепной передачи
Исходные данные для расчета цепной передачи
По табл.7.11 по передаточному числу принимаем число зубьев меньшей звездочки z1 = 27 тогда число зубьев большой звездочки
z2 = z1 × u = 27 × 278 = 75.
Рекомендуемое число зубьев меньшей звездочки z1
z1 при передаточном числе u
Втулочная и роликовая
Определяем коэффициент учитывающий условия эксплуатации:
kэ = kд × kа × kрег × kсм × kреж × kн
где kд – коэффициент динамичности нагрузки при спокойной нагрузке; kд = 1 [9 с. 68];
kа – коэффициент учитывающий межосевое расстояние; примем kа = 1 при a = (30–50) × t;
kн – коэффициент учитывающий наклон передачи к горизонту если линия центров наклонена до 60°; kн = 1;
kрег – коэффициент зависящий от способа регулирования натяжения цепи; при регулировке оси одной из звездочек kрег = 1;
kсм – коэффициент учитывающий характер смазки; при регулярной капельной смазке kсм = 1;
kреж – коэффициент зависящий от продолжительности работы в сутки; при односменной работе kреж = 1.
kэ = 1 × 1 × 1 × 1 × 1 × 1 = 1.
Ориентировочно допускаемое давление в шарнирах определим по табл. 7.12 в зависимости от частоты вращения меньшей звездочки n2 = 206 мин–1.
Допускаемое среднее давление [p] для роликовых цепей при z1 = 27.
Определим ориентировочное значение шага цепи принимая число рядов цепи m = 1:
Зададимся двумя смежными шагами цепи ПР по ГОСТ 13568–75 (табл.7.13) и рассчитаем оба варианта.
Цепь приводных роликов ПР-1905-3180 имеет параметры:
Разрушающая нагрузка Q H
Рассчитываем проекцию опорной поверхности шарнира
A = B×d = 13×596 = 7748 мм2.
Рассчитываем скорость цепи:
Рассчитываем окружную силу:
Допускаемое среднее давление [p] = 257 для роликовых цепей при шаге цепи t = 1905 мм. (табл. 7.12).
Условие [p] > p выполняется.
A = B×d = 965×508 = 4902 мм2.
Допускаемое среднее давление [p] = 281 для роликовых цепей при шаге цепи t = 15876 мм. (табл. 7.12).
Цепь шага t = 1905 мм имеет условие по допускаемому среднему давлению выше чем у цепи с шагом t = 15786 мм:
Дальнейшие расчеты выполняем для цепи шага t = 1905 мм.
Определяем число зубьев в цепи:
Округляем до четного: Lt = 132.
Межосевое расстояние оптимальное a = 40t = 40*1905 = 762 мм.
Уточняем межосевое расстояние цепной передаче по формуле:
Для свободного провисания цепи предусматриваем возможность уменьшения межосевого расстояния на 04% т.е. на 767*0004 = 3мм.
Определяем диаметры делительных окружностей звездочек:
Определяем диаметры наружных окружностей звездочек:
Рассчитываем силы действующие на цепь:
где Kf – коэффициент учитывающий расположение цепи (для горизонтально расположенной Kf = 7 (c151[1])).
Рассчитываем расчетную нагрузку на валы:
Проверяем коэффициент запаса прочности:
Предварительный расчет диаметров валов
Различают расчеты валов на статическую и усталостную прочность жесткость и колебания причем расчеты на прочность и жесткость могут иметь как проектировочный так и проверочный характер. При проектировочном расчете диаметры валов могут определяться исходя из условий прочности на совместное действие изгиба и кручения. На начальной стадии проектирования когда нет данных о величине изгибающих моментов производится предварительный расчет на статическую прочность по крутящему моменту:
где [] – допускаемое напряжение кручения [1 3–5] МПа – для ведущего вала и Мпа для ведомого.
Вычисляем диаметр ведущего вала:
Принимаем по ГОСТ 120080-66 dв1=24 мм диаметр под подшипник dп=30 мм
диаметр под муфту dм= __ мм вычисляем диаметр ведомого вала:
Принимаем по ГОСТ 120080-66 dв1=28 мм диаметр под подшипник dп=35 мм.
Остальные размеры определяем конструктивно.
Принимаем диаметр ведущего вала:
на выходе под полумуфту 24 мм;
под манжетное уплотнение 30 мм;
под подшипники 30 мм;
Вал изготовлен как вал-шестерня.
Принимаем диаметр ведомого вала:
на выходе под звездочку 31 мм;
под манжетное уплотнение 35 мм;
под подшипники 35 мм;
под зубчатое колесо 40мм.
Материал для ведущего и ведомого вала – Сталь 40 ГОСТ 1050-88.
Подбор и проверочный расчет муфт
По заданию требуется выбрать упругую муфту для соединения входного вала редуктора с валом электродвигателя.
Упругая соединительная муфта предназначена для соединения соосных вращающихся валов и передачи ими крутящего момента от ведущего вала к ведомому.
Размеры муфты принимаются по государственным или отраслевым стандартам в зависимости от расчетного вращающего момента Тр и диаметра вала под полумуфты dвых.
Расчетный вращающий момент рассчитывается по формуле:
где Тном – номинальный момент действующий на вал;
Kреж – коэффициент режима работы (Kреж = 11–14 при спокойной работе и небольших разгоняемых массах)
Тр = 15105·11 = 166 Нм.
Выбираем муфту с упругой звездочкой 63-2-28-I.2-24-I.1 ГОСТ 14084-93. Одна втулка для длинного цилиндрического конца вала диаметра 28 мм (на вал электродвигателя). Вторая – для короткого цилиндрического конца вала 24 мм (на быстроходный вал редуктора).
Предварительный подбор подшипников
Проектирование опорных узлов ведут на основании кинематической схемы узла и силовой характеристики механизма намечают тип и класс точности подшипника.
Условие для выбора типа подшипников:
для шариковых радиальных;
для упорных шариковых;
для упорных роликовых.
Подставим значения и вычислим .
Условие выполняется и в качестве схемы установки подшипников выбираем установку шариковых радиальных подшипников. Применяемые в узлах со сравнительно легкими условиями эксплуатации и при отсутствии высоких требований к жесткости опор в радиальном и осевом направлениях.
Для ведущего вала с диаметром под подшипником в 30 мм согласно ГОСТ 8338-75 выбираем шариковые радиальные подшипники легкой серии №206.
Для ведомого вала с диаметром под подшипником в 30 мм согласно ГОСТ 8338-75 выбираем шариковые радиальные подшипники легкой серии №207.
Характеристики подшипников записаны в талб. 4.
Характеристики подшипников ведущего и ведомого вала
Компоновочная схема и выбор способа смазывания передач и подшипников определение размеров корпусных деталей
Компоновка редуктора выполняется для:
- размещения внутри зубчатых колес так чтобы получить минимальные внутренние размеры редуктора;
- определения расстояния между опорами валов и длин консольных участков;
- определение точек приложения сил нагружающих валы.
Зная размеры цилиндрической передачи (межосевое расстояние и диаметры колес) валов и подшипников качения приступаем к компоновке редуктора предварительно рассчитав элементы корпуса редуктора.
Проводим вертикальную осевую линию – ось ведомого вала. Используя межосевое расстояние (120 мм) проводим ось ведущего вала. Далее следует вычертить очертания зубчатого зацепления и ступиц колес. Чертим валы располагаем и вычерчиваем на них по размерам подшипники качения крышки подшипников.
Результатом компоновки являются расстояния между опорами валов определяемые замером их на чертеже.
На следующем этапе прорабатывается конструктивное оформление деталей и узлов редуктора.
Расчет элементов корпуса будет производиться по [2].
Толщина стенки редуктора: мм.
Расстояние от внутренней поверхности стенки редуктора до боковой поверхности вращающейся части: мм. Принимаем 8 мм.
Радиальный зазор от поверхности вершин зубьев до внутренней поверхности стенки редуктора: мм. Конструктивно принимаем со стороны зубчатого колеса – 8мм со стороны шестерни - 18 мм.
Расстояние от боковой поверхности элементов вращающихся вместе с валами до боковой поверхности неподвижных наружных частей редуктора: мм. Принимаем 8 мм.
Болты соединяющие крышку корпуса и корпус по периметру редуктора: мм. Принимаем М10. Болты соединяющие крышку корпуса и корпус у бобышек подшипников: мм. Принимаем М12.
Ширина фланцев крышки корпуса и корпуса:
ширина фланцев крышки корпуса и корпуса по периметру редуктора конструктивно принимаем равным 27 мм;
ширина фланцев крышки корпуса и корпуса по периметру редуктора конструктивно принимаем равным 33 мм.
Выбор смазки будет производиться по [5].
Выбор способа смазывания.
Для редукторов общего назначения применяют непрерывное смазывание жидким маслом (окунанием в масляную ванну).
В зависимости от контактного напряжения и скорости передачи по табл. 11.1 [5] выбираем рекомендуемую кинематическую вязкость масла 28 (что соответствует окружной скорости зубчатой передачи 2 5 (а точнее -4816) мс и контактному напряжению – до 600 МПа – (а точнее – 26557 МПа)). По табл. 11.2 [5] выбираем смазку И-Г-А-32 ГОСТ 17479.4-87.
Определение количества масла.
Для одноступенчатых редукторов при окунании в масляную ванну кол-во масла определяют из расчета 04-08 л на 1 кВт передаваемой мощности.
Таким образом передаваемая мощность: 4555 кВт. Тогда объем масла: 182–364 л. Тогда глубина масляной ванны (исходя из того что ее длина равна 270 мм а ширина – 74 мм должна быть примерно равна (182 364)*1000000(270*74)=91 182 мм).
Принимаем глубину масляной ванны: 42 мм. Тогда объём масла составит: 270*74*421000000=084 л.
Контроль уровня масла производится с помощью жезлового маслоуказателя установленного в стенке корпуса редуктора.
Слив масла осуществляется через сливное отверстие.
Подшипники смазываются маслом зацепления.
Для того что бы избежать излишнего смазывания подшипников ведущего вала установлены мазеудерживающие шайбы.
Расчет валов по эквивалентному моменту
Редукторные валы испытывают два вида деформации – изгиб и кручение. Деформация кручения на валах возникает под действием вращающих моментов приложенных со стороны двигателя и рабочей машины. Деформация изгиба вызывается силами в зубчатом закрытой цепной передачи и консольными силами со стороны открытых передач и муфт.
1 Расчет ведущего вала
Данные для расчета ведущего вала:
T1=14655 Н; a1=50 мм; z1=z2=50 мм; d1=40мм.
Вычислим величину усилий действующих в зацеплении и изобразим схему действия сил (рис 4):
Ft1 = 2 · Т1 d1 = 2 ·14655 004 = 73275 Н;
Fr1 =038· Ft1 = 038· 73275 = 27845 Н;
Fа1 = 02· Ft1 =02· 73275=14655 Н.
Консульная нагрузка на ведущий вал со стороны муфты:
Направление силы Fk неизвестно. Оно может быть любым по отношению к силам действующим в зацеплении. Поэтому реакции от силы Fk не совпадают с направлением реакций опор сил в зацеплении зубчатой передачи и их определяют отдельно.
Вычерчиваем расчетную силу нагружения вала. (рис 4а)
Определяем реакции опор в вертикальной плоскости zy от сил Fr1 и Fа1 (рис 4б)
Проверим правильность определений реакций:
Реакции определены правильно.
Строим эпюру изгибающим моментов MИВ(Mх) в вертикальной плоскости(рис 4в)
Заметим что эпюры изгибающих и крутящих моментов необходимы для проверочного расчета на усталость а не для подбора подшипников но рекомендуется их строить сразу после определения реакций опор.
Определение реакции опор в горизонтальной плоскости xz от силы Ft2 (рис 4г)
Строим эпюру изгибающим моментов MИГ(My) в вертикальной плоскости(рис 4д)
Определяем реакции опор от консольной силы Fk (рис 4е)
Проверим правильность определений реакций:
Строим эпюру изгибающих моментов МFk от сил Fk (рис 4ж)
Строим эпюры крутящего момента передача вращающего момента происходит вдоль оси вала от середины ступицы шестерни до точки приложения консольной нагрузки. При этом кручении момент равен моменту Мk1=T1=14655 H·м.(рис 4з)
Определяем суммарные реакции:
Рассчитываем суммарных изгибающих моментов (рис 4и):
Эквивалентный момент вычисляем по формуле (рис 4к):
Выполняем проверку вала в опасном сечении на статическую прочность т.е. под подшипником в сечении D т.к. максимальным эквивалентный момент М2э=348 Н·м.
где =60 Мпа – допускаемое напряжение изгиба.
Диаметр вала в рассчитываемом сечении dв=30 мм.
Условие на статическую прочность dв>dp выполняется.
2 Расчет ведомого вала
Данные для расчета ведомого вала:
T2=70367 Н; a2=48 мм; z1=z2=48 мм; d1=199 мм.
Вычислим величину усилий действующих в зацеплении и изобразим схему действия сил (рис):
Ft = 2 · Т2 d2 = 2 ·70367 019932 = 70606 Н;
Fr2 =038· Ft2 = 038· 70606 = 26134 Н;
Fа2 = 02· Ft2 =02· 70606 =130545 Н.
Нагрузка на ведомый вал со стороны звездочки :
Вычерчиваем расчетную силу нагружения вала. (Рис 5а)
Определяем реакции опор в вертикальной плоскости zy от сил Fr1 и Fа1 (рис 5б)
Строим эпюру изгибающим моментов MИВ(Mх) в вертикальной плоскости(рис 5в)
Определение реакции опор в горизонтальной плоскости xz от силы Ft2 (рис 5г)
Строим эпюру изгибающим моментов MИГ(My) в вертикальной плоскости(рис 5д)
Определяем реакции опор от звездочки Fв (рис 5е)
Строим эпюру изгибающих моментов Мв от сил Fв (рис 5ж)
Строим эпюры крутящего момента передача вращающего момента происходит вдоль оси вала от середины ступицы колеса до точки приложения консольной нагрузки. При этом кручении момент равен моменту Мk2=T2=70367 H·м. (рис 5з)
Рассчитываем суммарных изгибающих моментов (рис 5и):
Эквивалентный момент вычисляем по формуле (рис 5к):
Выполняем проверку вала в опасном сечении на статическую прочность т.е. под подшипником в сечении D т.к. максимальным эквивалентный момент М2э=10669 Н·м.
Диаметр вала в рассчитываемом сечении dв=35 мм.
Подбор подшипников по динамической грузоподъемности
Проверочный расчет предварительно выбранных подшипников выполняется отдельно для быстроходного и тихоходного вала. Пригодность подшипников определяется сопоставлением расчетной динамической грузоподъемности Сrp Н. с базовой величиной Сr H. Или базовой долговечности L10h ч. с требуемой Lh ч. по условиям:
Сrp ≤ Cr или L10h ≥ Lh
Требуемая долговечность подшипника Lh предусмотрена ГОСТ 16162-85 и составляет для зубчатых колес Lh ≥ 13500 часов.
Базовая динамическая грузоподъёмность подшипника Cr представляет собой постоянную радиальную нагрузку которую подшипник может воспринять при базовой долговечности составляющей 106 оборотов внутреннего кольца.
Расчетная динамическая грузоподъёмность Сrp H и базовая долговечность L10h ч определяются:
где RE – эквивалентная динамическая нагрузка Н;
m – показатель степени m = 3.
1 Расчет долговечности подшипников ведущего вала
V = 14; Kб = 1; KT = 1; Rr=4033 Н.
а) Рассчитываем RE по формуле:
б) Вычисляем динамическую грузоподъёмность и базовую долговечность:
2 Расчет долговечности подшипников ведомого вала
V = 14; Kб = 1; KT = 1; Rr=44233 Н.
Подбор и проверочный расчет шпоночных и шлицевых соединений
Расчет будет произведен по рекомендациям из [4].
Рассчитываем шпонки на смятие.
Рис.6 Эскиз шпонки ГОСТ 29175–91.
Должно выполняться условие: МПа где = 60 100 МПа для шпонки под полумуфтой (см. стр. 48 [4]).
МПа где Т Нмм – крутящий момент на валу d мм – диаметр вала h мм – высота шпонки мм – расчетная длина шпонки b мм – ширина шпонки мм – глубина паза вала.
Крутящий момент: T1 = 14655 Нм.
Шпонка под полумуфтой.
Диаметр вала: d = 24мм.
Шпонка под полумуфтой bxhxL=8x7x28:
Крутящий момент: T2 = 70367 Нм;
Диаметры вала: под звездочкой – d = 31 мм; под колесом – d = 40 мм.
Шпонка под звездочкой bxhxL=12x8x50: МПа. Шпонка под колесом bxhxL=12х8х56: МПа.
Условие МПа выполняется. Прочность шпоночных соединений обеспечена.
Назначение посадок шероховатостей поверхностей выбор степеней точности и назначение допусков формы и расположения поверхностей
Назначение квалитетов точности параметров шероховатости поверхностей отклонений формы и расположение поверхностей должно сопровождаться анализом служебного назначения деталей и технологических возможностей при обработке. С возрастанием точности стоимость обработки резко повышается. Из экономических соображений нужно назначать квалитеты сравнительно грубые однако обеспечивающие необходимое качество деталей узлов и машин.
При выборе квалитетов точности и назначении посадок будем руководствоваться рекомендациями:
-посадки колеса на валы: Н7р6
-посадка глухих крышек в корпус: Н7h11
-посадка сквозных крышек в корпус: Н7h8
-поле допуска ширины шпонки: js9
-поле допуска ширины шпоночного паза на валу: P9
-поле допуска ширины шпоночного паза в отверстиях: P9
-поле допуска диаметра вала под подшипниками: L0k6
-поле допуска диаметра расточек в корпусе под подшипники: H7l0
Для обеспечения указанных посадок посадочные поверхности деталей необходимо обработать до шероховатости не грубее RA 1.6. При этом торцовые поверхности деталей контактирующие с другими деталями должны иметь шероховатость не ниже RA 3.2 второстепенные поверхности механически обрабатываемых деталей не ниже RA 12.5 второстепенные механически необрабатываемые поверхности деталей оставляем в состоянии поставки т.е. со стандартной шероховатостью. Поверхности валов под манжетными уплотнениями должны иметь шероховатость не ниже RA 0.4.
Расчет валов на выносливость
Исследовав эпюры эпюры изгибающих и крутящих моментов определяем опасное сечение вала которым является сечение D – посадка подшипника на вал.
Материал вала: сталь 40Х
НВ = 217; в = 600 Нмм2; т = 340 Нмм2;
Определяем напряжение в опасных сечениях вала Нмм2:
а) нормальные напряжения изменяются по симметричному циклу при котором амплитуда напряжений а равна расчетным напряжениям изгиба и МПА:
где М – суммарный изгибающий момент в рассматриваемом сечении вала Нм;
Wнетто- осевой момент сопротивления сечения вала (таблица 11.1[4])
б) касательные напряжения изменяются по нулевому циклу при котором амплитуда равна половине расчетных напряжений кручения
Где Мк – крутящий момент Н·м;
- полярный момент инерции сопротивления сечения вала определяем по таблице 11.1[4]
Определяем коэффициент концентрации нормальных и касательных напряжений для расчетного сечения вала (таблице 11.2[4]):
где (K)2 и (K)2 – эффективные концентрации напряжений K = 3.1 K = 2.2;
KF –коэффициент влияния шероховатости KF = 1.1;
Kd –коэффициент влияния абсолютных размеров поперечного сечения Kd=0.88;
в) определяем пределы выносливости в расчетном сечении вала Нмм2:
где -1 и -1 – предел выносливости гладких образцов при симметричном цикле изгиба и кручения Нмм2:
г) определяем коэффициенты запаса прочности по нормальным и касательным напряжениям:
д) определяем общий коэффициент запаса прочности в опасном сечении
Условия на выносливость выполняются.12.2 Ведомый вал
Наиболее нагруженным сечение тихоходного вала является точка D (место посадки подшипника).
НВ = 170; в = 600 Нмм2; т = 340 Нмм2;
где Мк – крутящий момент Н·м;
где (K)2 и (K)2 – эффективные концентрации напряжений K = 2.1 K = 1.7;
Условия на выносливость выполняются.
Описание сборки редуктора
Перед сборкой внутреннюю полость корпуса (3 и 4) тщательно очищают и покрывают маслостойкой краской.
Сборку редуктора производят согласно сборочному чертежу начиная с узлов валов.
На ведущий вал (9) надевают мазеудерживающие кольца (14) и подшипники 7000206 ГОСТ 8338-75 (35).
На ведомый вал (10) надевается зубчатое колесо (11) предварительно вставив шпонку в паз (44). Далее следует установить распорное кольцо (18) и подшипники 7000207 ГОСТ 8338-75 (36).
После этого необходимо установить узлы валов в специальные отверстия в основании корпуса (3). Далее следует установить распорные кольца (151617 и 19) после чего на основание надевается крышка корпуса (4).
Теперь следует произвести регулировку редуктора.
После регулировки необходимо закрутить маслосливное отверстие пробкой (13) вместе с прокладкой (22). Вкрутить жезловый маслоуказатель (2) вместе с прокладкой (24) в корпус (3). Залить 084 литра масла после чего прикрутить крышку люка (1) вместе прокладкой (23) и с отдушиной (34).
После сборки редуктор обкатывается согласно техническим требованиям.
Регулировки подшипников и зацеплений
Для нормальной работы подшипников достаточно обеспечить свободное вращение валов (свободное вращение внутренних колец подшипников относительно внешних).
Сначала редуктор собирается без регулировочных прокладок (20 и 21). По образовавшимся зазорам между крышками подшипников (6 и 8 на ведущем валу и 5 и 7 – на ведомом) приблизительно определяется необходимое число прокладок. Затем глухие крышки подшипников (5 и 6) откручиваются и прокладки устанавливаются. Далее следует прикрутить снятые крышки и проверить проворачиваемость валов. При необходимости следует еще раз снять крышки подшипников и изменить число прокладок. После точного определения необходимого числа прокладок и обеспечения свободного вращения валов следует распределить прокладки между противоположными крышками не изменив при этом их суммарного количества для каждого вала.
Следует также отметить что регулировка каждого вала осуществляется отдельно (когда один вал регулируется – второй из корпуса вынут).
После того как подшипники отрегулированы необходимо отрегулировать зацепление. Основной критерий: свободное вращение валов. Регулировка зацепления осуществляется перемещением прокладок из-под одной крышки под противоположную.
После того как свободное вращение валов (без стуков и заедания) достигнуто необходимо проверить качество регулировки зацепления по пятну контакта. Для этого необходимо снять крышку корпуса и окрасить зубья большего коле специальной краской после чего собрать редуктор и провернуть тихоходный вал на полный оборот. После этого следует снять крышку корпуса и изучить пятно контакта на зубьях шестерни. Оно должно составлять не менее 50%.
Прикладная механика. Курсовое проектирование Под ред. А.Т. Скобейды Минск.: БНТУ 2010 г.
Курсовое проектирование деталей машин Чернавский С.А. и др. – М.: Машиностроение 1987 г.
Кудрявцев В.Н. Курсовое проектирование деталей машин Справочное пособие. – Ленинград «Машиностроение» 1984 г.
Дунаев П.Ф. Леликов О.П. Конструирование узлов и деталей машин. Мн.: Высшая школа 1998 г.
Скойбеда А.Т. Кузьмин А.В. Макейчик Н.Н. Детали машин и основы конструирования. Мн.: «Высшая школа» 2006 г.
Шейнблит А.Е. Курсовое проектирование деталей машин. – М.: Высшая школа 1991 г.
Анурьев В.И. Справочник конструктора-машиностроителя в трех томах. Том 2. – М.: «Машиностроение» 2001 г.
эпюры.frw

вертикальная плоскость (zy)
горизонтальная плоскость (zx)
эпюра крутящего момента
Вал.cdw

Рекомендуемые чертежи
Свободное скачивание на сегодня
- 25.10.2022