Техпроцесс изготовления зубчатого колеса



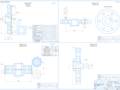
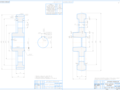
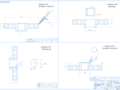
- Добавлен: 24.01.2023
- Размер: 458 KB
- Закачек: 0
Описание
Состав проекта
![]() |
![]() ![]() ![]() |
![]() ![]() ![]() ![]() |
![]() ![]() ![]() |
![]() ![]() ![]() ![]() |
![]() ![]() ![]() ![]() |
![]() ![]() ![]() |
![]() ![]() ![]() |
Дополнительная информация
записка.docx
Разработка оптимального технологического процесса изготовления и ремонта каждой конкретной детали может нести значительную экономическую выгоду в масштабах целого предприятия. Поэтому такое большое внимание уделяется созданию новых перспективных способов создания изделий.
Технический процесс ведет к увеличению сложности проектируемых объектов повышению их качества надежности и долговечности требуя применения новых технологических решений улучшения качества и сокращения сроков проектных работ. Достичь положительных результатов возможно лишь в случае использования современных средств САПР на всех этапах проектирования а на этапе конструкторского проектирования заложены возможности использования прогрессивных технологических решений.
В связи с этим повышаются требования предъявляемые к конструктору который должен обладать широким кругозором в вопросах проектирования производства и эксплуатации проектируемых объектов.
Целью курсовой работы является закрепление углубление и обобщение полученных знаний а так же приобретение практических навыков для разработки технологических процессов изготовления и ремонта деталей с использованием прогрессивных технологий и анализа технологических решений.
Технология изготовления
1 Анализ назначения и технологичности детали
Зубчатое колесо устанавливается в коробке передачи и служит для передачи вращающего момента. Зубчатый венец колеса испытывает большие нагрузки приводящие к износу выкрашиванию зубьев.
Деталь имеет удобные базовые поверхности что позволяет на всех операциях использовать стандартные приспособления.
Конструктивно деталь считаем технологичной. Зубчатое колесо изготавливается из стали 45 ГОСТ 1050-88
Рабочий чертёж детали представлен в графической части курсовой работы.
Химический состав Стали 45 приведен ниже по ГОСТ 1050-74
углерод C - 040 050%;
марганец Mn - 050 080 %;
сера S - не более 004 %;
фосфор P - не более 005 %;
хром Cr - около 03 %;
предел текучести т = 360 МПа;
предел прочности в = 610 МПа;
ударная вязкость aн = 600 кДжм2;
относительное удлинение при растяжении 5 = 16 %;
относительное сужение при растяжении = 40 %;
твердость отожженной стали HB 197;
стоимость одной тонны проката 10 250 мм - 185 136 .
Заготовка изготавливается штампованием с последующей механической обработкой.
На рисунке 1.1 представлен чертеж детали.
Метод выполнения заготовки для детали определяется назначением и конструкцией детали материалом техническими требованиями масштабом и серийностью выпуска а также экономичностью изготовления.
Деталь изготавливается из Стали 45 штамповкой поэтому конфигурация наружного контура и внутренних поверхностей не вызывает значительных трудностей при получении заготовки
В остальном деталь достаточно технологична допускает применение высокопроизводительных режимов обработки имеет хорошие базовые поверхности для первоначальных операций и довольно проста по конструкции.
Рисунок 1.1 - чертеж детали
Изготовление любой детали начинается с заготовки которая с помощью механической пластической термической химической и (или) иной обработки доводится до формы размеров и качества готовой детали заданных конструктором.
Расчёт себестоимости для конкретных способов получения заготовок предполагая что чистовая механическая обработка для всех вариантов одинакова можно осуществлять по следующим зависимостям:
где mш - масса прутка перед штамповкой кг (на 2 8 % больше массы готовой детали); mш= 3465 гр.
- цена 1 кг проката;
Cш.р - стоимость штамповочных работ (Cш.р = 0005 mш );
Cш.р=0005*3465 = 017
qш - накладные расходы штамповочного цеха (50 100 %);
Cшт - стоимость штампа (Cшт = 10 mш );
nшт - количество заготовок изготавливаемых одним штампом (до 10 тыс.); nшт = 10000
- штучно-калькуляционное время черновой обработки детали;
q - накладные расходы механического цеха в % к основной зарплате (100 200 %).
где mот - масса отливки кг (на 5 15 % больше массы готовой детали);
Ц1м - цена 1 кг жидкого металла (см. табл. 2.1 пункт 10);
Cл - стоимость литейных работ (Cл = 0008 mш );
qл - накладные расходы литейного цеха (50 100 %);
Cмод - стоимость модели (Cмод = mот );
nмод - количество заготовок изготавливаемых одной моделью (для деревянных - до 100 для металлических - до 10 тыс.).
Вывод: Из расчетов видно что наиболее экономично изготавливать деталь штамповкой.
На рисунке 1.2 представлен чертеж заготовки.
Рисунок 1.2 – чертеж заготовки
2Выбор маршрута механической обработки
Маршрут обработки детали представлен в таблице 1.1
Таблица 1.1 – Маршрут обработки детали
Наименование операции и перехода
Расточить отверстие 65 мм до 695 мм.
Подрезать торец с 124 мм до 695 мм t=3мм.
Подрезать торец с 380 мм до 300 мм t=3мм.
Подрезать торец с 300 мм до 124 мм на глубину L=10 мм t=16 мм
Снять фаску 125x45° на 380 мм.
Снять фаску 325 x45° на 695.
Токарный многорезцовый копировальный полуавтомат 1Н713. Закрепить в 3-х кулачковом патроне;
Обточить торец с 124 мм до 120 на длине l=40мм.
Подрезать торец с 300 до 120 на глубину L= 10 мм t=16 мм.
Обточить торец с 380 мм до 365 на длине l=55мм.
Снять фаску 5x45° на 365.
Снять фаску 5x45° на 120.
Снять фаску 325x45° на 695.
Рассверлить 6 отверстий с 34 до 40 на длину l=35 мм
Вертикально-сверлильный станок
Потянуть шпоночный паз в отверстии 695 мм шириной b=20 мм длинной l=85 мм глубиной t=49 мм.
Вертикальный протяжной полуавтомат
Фрезеровать зубья на 365 m=45 z= 80 b= 55
Зубофрезерный полуавтомат
Закалка ТВЧ зубьев на глубину 14 17 мм до 45 48 HRC.
Шлифовать отверстие 695 мм до 70 H7 мм на длине l=85 мм.
Внутришлифовальный станок 3А228В
Закрепить в мембранном патроне
3Расчет и назначение припусков
На основании выбранного технологического маршрута обработки детали и способа получения заготовки производим расчёт припусков на механическую обработку.
Технологический маршрут обработки поверхности 70H7 состоит из растачивания фрезерования шпоночного паза и окончательного шлифования.
При обработке цилиндрической поверхности минимальный припуск для каждого i-го перехода можно оценить:
i - погрешность установки заготовки на данной операции мм
Минимальный припуск под растачивание:
Минимальный припуск под протягивание шпоночного паза:
Минимальный припуск под шлифование:
4Расчёт режимов резания
Операция 005 Токарная
Исходными данными для этого являются принятый маршрут механической обработки детали и назначенные припуски для каждого перехода что соответствует глубинам резания ti .
Мы принимаем материал лезвия инструмента Твёрдосплавная пластина Т15К6 период стойкости которой равен Т=120 мин.
В зависимости от вида обработки назначим подачу инструмента s . В нашем случае s=2ммоб.
Затем определяется скорость резания v ммин.
где Cv - коэффициент скорости резания определяемый;
T - период стойкости инструмента мин;
t - глубина резания мм;
s - подача инструмента ммоб;
m x y - показатели степеней.
Cv = 300; Т = 120 мин; t = 2.25мм; s =2ммоб; m = 02; y = 04.
После оценки v произведем вычисление проекций силы резания по координатным осям Н
t - глубина резания мм;
v - скорость резания ммин;
xi yi ni - показатели степеней (см. табл. 9).
При чистовом точении:
Определим крутящий момент при резании Mк Нм
где D – обрабатываемый диаметр м.
Mк = 595 0065 2=193 Нм
Определим мощность резания N кВт
где = 314 - число Пифагора;
n - частота вращения шпинделя станка обмин
По паспортным данным станка 1Н713 принимаем n=330 мин-1.
Тогда мощность резания:
Определим основное время Tо (мин) и штучно-калькуляционное Tшк (мин) для каждой операции. Общая зависимость для основного времени
k - количество проходов инструмента;
n - частота вращения шпинделя станка (обмин) или число двойных ходов в минуту для станков с прямолинейным движением;
Штучно-калькуляционное время для каждой операции вычисляется как сумма
Tшк = Tо + Tв + Tоб + Tф (1.10)
где Tв - вспомогательное время
Tоб - время обслуживания станка
Tф - время на физические надобности рабочего
Tв = (001 02) Tо=0015 0146=00019 мин
Tоб=(1 6)% Tо=0050146=00066 мин
Tф=(4 8)%( Tо + Tв)=005 (0146+00019)=00067 мин(1.11)
В зависимости от вида обработки назначим подачу инструмента s . В нашем случае s=07ммоб.
Затем определяется скорость резания v ммин по формуле 1.4
Частота вращения шпинделя станка мин -1 по формуле 1.8 равна
По паспортным данным станка 1Н713 принимаем n=250мин-1
По формулам 1.9-1.11 получим
Tв = (001 02) Tо=0015019 = 00028 мин
Tоб=(1 6)% Tо=005019 = 00095 мин
Tф=(4 8)%( Tо + Tв)=005(019+00028) = 00096 мин
Подрезать торец с 380 мм до 300 мм t = 3мм.
По паспортным данным станка 1Н713 принимаем n=80 мин-1.
Tв = (001 02) Tо= 0015082 = 00123 мин
Tоб=(1 6)% Tо=005082 = 00385 мин
Tф=(4 8)%( Tо + Tв) = 005(082+00123) = 0039 мин
Подрезать торец с 300 мм до 124 мм на глубину L=10 мм t=16 мм.
По паспортным данным станка 1Н713 принимаем n=110 мин-1.
По формулам 1.9-1.11 при чистовом точении получим
Tв = (001 02) Tо= 0015118 = 0017 мин
Tоб=(1 6)% Tо= 005118 = 0081 мин
Tф=(4 8)%( Tо + Tв) = 005(118+0017) = 0082 мин
В зависимости от вида обработки назначим подачу инструмента s . В нашем случае s=05ммоб.
По паспортным данным станка 1Н713 принимаем n= 63 мин-1
Tв = (001 02) Tо=0015058=00082 мин
Tоб=(1 6)% Tо=005058=0034 мин
Tф=(4 8)%( Tо + Tв)=005(058+00082)=0035 мин
По паспортным данным станка 1Н713 принимаем n=440 мин-1
Tв = (001 02) Tо= 00150034 = 000061 мин
Tоб=(1 6)% Tо= 0050034 = 00027 мин
Tф=(4 8)%( Tо + Tв) = 005(0034+000061) = 00028 мин
Tв = (001 02) Tо=0015019=00028 мин
Tоб=(1 6)% Tо=005019=00095 мин
Tф=(4 8)%( Tо + Tв)=005(019+00028)=00096 мин
Tоб=(1 6)% Tо= 005082 = 00385 мин
По паспортным данным станка 1Н713 принимаем n= 250 мин-1
Tв = (001 02) Tо=0015026=00039 мин
Tоб=(1 6)% Tо=005026=0013 мин
Tф=(4 8)%( Tо + Tв)=005(026+00039)=0014 мин
Подрезать торец с 300 мм до 120 мм на глубину L=10 мм t=16 мм.
По паспортным данным станка 1Н713 принимаем n = 110 мин-1
Tв = (001 02) Tо= 0015118 = 00177 мин
Tоб=(1 6)% Tо= 005118 = 0059 мин
Tф=(4 8)%( Tо + Tв)=005(118+00177) = 0062 мин
Tв = (001 02) Tо=0015138 = 00207 мин
Tоб=(1 6)% Tо=005138 = 00685 мин
Tф=(4 8)%( Tо + Tв)=005 (138+00207) = 00693 мин
По паспортным данным станка 1Н713 принимаем n= 80 мин-1
Tв = (001 02) Tо=00150275= 00041 мин
Tоб= (1 6)% Tо= 0050275= 00137мин
Tф = (4 8)%( Tо + Tв) = 0050275+00041) = 00139 мин
По паспортным данным станка 1Н713 принимаем n= 250мин-1
Tв = (001 02) Tо= 00150088 = 000132 мин
Tоб = (1 6)% Tо= 0050088 = 00044 мин
Tф = (4 8)%( Tо + Tв) = 005 (0088+000132) = 00054 мин
Tв = (001 02) Tо=00150034=000061 мин
Tоб=(1 6)% Tо=0050034=00027 мин
Tф=(4 8)%( Tо + Tв)=005(0034+000061)=00028 мин
Операция 010 Сверлильная
Скорость резания при сверлении стали в = 610 МПа сверлом P18:
где kv – Поправочный коэффициент на скорость резания при сверлении;
T – период стойкости инструмента.
Зная v определяется частота вращения шпинделя станкамин-1 по формуле 1.8
По паспортным данным станка 1Н713 принимаем n=360 мин-1
где D - диаметр отверстия мм;
M кр =31 D2 S07 (1.14)
M кр =31 402 107 981=4835 Н м.
По формулам 1.9-1.11 получим основное и штучно-калькуляционное время
Tв = (001 02) Tо= 0015028 = 00042 мин
Tоб=(1 6)% Tо= 005028 = 0014 мин
Tф=(4 8)%( Tо + Tв) = 005(028+00042) = 00142 мин
Операция 015 Протяжная
Режим резания при протягивании - это подача на зуб и скорость резания.
Подача на зуб определена конструкцией протяжки
где F - сила резания на 1 мм режущей кромки кгмм в зависимости
от подачи на зуб и материала F=21168 Нмм.
- периметр лезвия т.е. обрабатываемый периметр мм;
Принимаем скорость резания V=5ммин.
Основное время рассчитываем по формуле.
где k - соотношение между скоростью рабочего и обратного хода;
V - скорость рабочего хода в ммин.;
q - количество одновременно обрабатываемых деталей;
lp.x - длина рабочего хода.
lp.x = ln + lp.ч.+ lдоп(1.18)
где ln - длина протягиваемой поверхности в мм
lдоп - длина перебега протяжки lдоп 30-50 мм.
где Vр.х - скорость рабочего хода Vр.х= 15 115ммин;
Vо.х - скорость обратного хода Vо.х= 20ммин.
lp.x=85+100+30=215 мм
Тогда основное время по формуле (1.17)
Вспомогательное время
Tв = (001 02) Tо= 0015 0053 = 000079 мин
Время обслуживания станка
Tоб=(1 6)% Tо= 005 0053 = 00026 мин
Время на физические надобности рабочего
Tф = (4 8)%( Tо + Tв) = 005 (0053+000079) = 00027 мин
Штучно-калькуляционное время определяем по формуле (1.11)
Операция 020 Зубофрезерная
База – внутреннее отверстие диаметром 695 мм.
Фрезеровать трехзаходной червячной фрезой m = 45 z =80 на диаметре 365 мм .
Выбираем подачу S=2 ммоб.
Скорость резания находим по формуле:
где S – осевая подача фрезы ммоб;
T – стойкость зуборезного инструмента мин
Частоту вращения фрезы находим по формуле:
где Dи – диаметр фрезы мм.
По паспорту станка принимаем частоту вращения n= 800 мин-1
Необходимую мощность рассчитываем по формуле:
гдеS - осевая подача фрезы;
Du - диаметр фрезы мм;
Основное время находим по формуле:
где n – частота вращения фрезы;
z – количество зубьев колеса;
k – количество заходов фрезы.
Фрезеруем два зубчатых колеса одновременно тогда ширина венца будет равна:
Tв = (001 02) Tо= 0015193 = 003 мин
Tоб = (1 6)% Tо= 005193 = 01 мин
Tф=(4 8)%( Tо + Tв) = 005(193+003) = 0102 мин
Операция 030 Шлифовальная
При шлифовании примем v = 20 мс.
Частота вращения шпинделя станка мин-1 принимаем n=6000 мин-1.
Для шлифовальных операций силы резания не оценивают из-за их малости а сразу определяют мощность NкВт
где CN-коэффициент мощности резания CN=01 52;
Vз- окружная скорость заготовки Vз= 10..150 ммин;
s – продольная подача s= 12 10 ммин;
D- шлифуемый диаметр мм;
b- ширина шлифуемой поверхности мм;
z- показатель степени z = 03 10.
где tвр = 005 мин. - время врезания;
a - припуск на сторонумм;
aвых- слой снимаемый при выходемм;
nд.х- число двойных ходов;
где Lр.х -длина рабочего хода круга для сквозных отверстий
Tв = (001 02) Tо=0015079=0012 мин
Tоб=(1 6)% Tо=005079=0039 мин
Tф=(4 8)%( Tо + Tв)=005(079+0012)=042 мин
5Выбор инструментов приспособлений и оборудования
Основным критерием при выборе оборудования является номинальная мощность привода станка Nпр которая должна на 5 10 % превышать вычисленную мощность резания N а также габариты заготовки то есть возможность установки её на данном станке. Вторым требованием к оборудованию является способность обеспечить необходимые или близкие параметры режимов резания - частоту вращения шпинделя n подачу s и т.д. При этом надо учитывать что передаточные числа коробок скоростей современных станков выбраны по закону геометрической прогрессии то есть nma - знаменатель прогрессии (чаще 126 или 141); m - число скоростей. Третий критерий выбора оборудования - его габариты масса и стоимость.
Для изготовления детали используем следующий станок:
Токарный многорезцовый копировальный полуавтомат 1Н713. Полуавтомат предназначен для токарной обработки деталей в патроне деталей сложной конфигурации: обточки цилиндрических конических и сферических поверхностей в условиях серийного крупносерийного производства. Его характеристики представлены в таблице 1.2
Таблица 1.2. Характеристики токарного многорезцового копировального полуавтомата 1Н713
Наибольший обрабатываемый диаметр мм
Наибольший ход инструмента мм
Частоты вращения шпинделя
Мощность главного привода
Вертикально-сверлильный станок 2Н150
Станок предназначен для сверления отверстий в деталях из черных и цветных металлов а также других материалов диаметром не более 50 мм. Технологические возможности: сверление зенкерование зенкование и нарезание резьбы.
Это оборудование имеет простую конструкцию что обеспечивает легкость управления надежность и долговечность этого работы.
Его характеристики представлены в таблице 1.3.
Таблица 1.3 Характеристики вертикально-сверлильного станка 2Н150
Вертикальный протяжной полуавтомат 7Б64Т
Станки 7Б64 применяются для механической обработки протягиванием сквозных отверстий различной конфигурации: круглых шлицевых прямоугольных со шпоночными пазами.
Его характеристики представлены в таблице 1.4.
Таблица 1.4 Характеристики вертикального протяжного полуавтомата 7Б64Т
Номинальная сила тягикН
Наибольший ход протяжки мм
Зубофрезерный полуавтомат 5304В
Станки модели 5304в предназначены для фрезерования цилиндрических прямозубых и косозубых колес из чугуна стали легированных сталей легких сплавов методом обкатки червячной фрезой.
Его характеристики представлены в таблице 1.5.
Таблица 1.5 Характеристики зубофрезерного полуавтомата 5304В
Макс. Размеры нарезаемого венцамм
Частоты вращения фрезы
Внутришлифовальный станок 3А228В.
Универсальный внутришлифовальный станок модели 3А228 предназначен для шлифования цилиндрических и конических развёрнутых и глухих отверстий. На станке можно производить шлифование внутреннего и наружного торцов одним внутришлифовальным шпинделем с одной установкой изделия.
Его характеристики представлены в таблице 1.6.
Таблица 1.6 Характеристики внутришлифовального станка 3А228В
Макс. диаметр шлифованиямм
Макс. длина шлифования изделия мм
Диаметр шлифуемого отверстия мм
Макс. длина шлиф. мм
Частота вращения детали мин-1
Частота вр.шлифкруга для внутр. шлифования мин-1
Габариты длина×ширина мм
Мощность электродвигателя кВт
Технология ремонта изделия.
1. Анализ возможных дефектов.
Изнашивание – это процесс постепенного изменения размеров и формы тела при работе.
Основными дефектами зубчатого колеса могут быть:
-износ рабочего профиля зубьев
-износ и смятие торцов зубьев
-задиры на рабочем профиле
-износ посадочного отверстия шпоночных канавок и шлицов.
Чертеж детали с указанием поверхностей которые могут быть подвержены износу представлен на рисунке 2.1.
Рисунок 2.1 – Чертеж детали
2Маршрут оборудование и режимы восстановления
Маршрут восстановления детали представлен в таблице 2.1.
Таблица 2.1-Маршут восстановления детали
Износ зубьев (поверхность 1)
Наплавка в среде СО2
Наплавить на 365 слой толщиной t=3мм на длину 55мм.
Точить с 371 мм до 365 мм на длину 55 мм t=3 мм.
Токарно-винторезный станок 16К20
Фрезеровать зубья на 365 m=45 z= 80b= 55
Закалка ТВЧ зубьев на глубину 14 17 мм до 45 50 HRC
Износ отверстия(поверхность 2)
Расточить отверстие с 70 до 78 на длину l=85 мм
Запрессовать в отверстие втулку с наружным диаметром 78 Н7 мм и внутренним 70 мм усилие P=320 кН.
Износ шпоночного паза (поверхность 3)
Строгать шпоночный паз в отверстии 695 мм шириной b=20 мм длинной l=85 мм глубиной t=49 мм.
Поперечно строгальный станок 7Е35
Подрезать торец с 120 мм до 70Н7 мм t=15 мм.
Наплавить под флюсом с 120 мм до 70Н7 мм t=3 мм.
Подрезать торец с 120 мм до 70Н7 мм t=2 мм.
Для восстановления поверхности 1 используем наплавку в среде CO2. Для этого наплавляем слой t=3 мм на 365 на длину 55 мм.
Наплавка в среде углекислого газа CO2 имеет следующие преимущества:
- качество наплавленного металла выше по сравнению с вибродуговой в жидкости;
- меньше снижение r - всего на 15 20 %.
Параметры и режимы восстановления:
-проволока марки Св-08ГС диаметром 08 мм;
-частота вращения детали n=3 мин -1 ;
-шаг наплавки t=3 ммоб;
-скорость подачи электродной проволоки v =5 ммин;
После наплавки требуется подрезать торец с 371 мм до 365 мм на длину 55 мм t=3 мм. После токарной операции фрезеруем зубья на 365 m=45 z= 80 b= 55 Следующей операцией является закалка ТВЧ зубьев 1 15 мм до 45 50 HRC.
Для восстановления поверхности 2 расточим отверстие с 70 до 78 на длину l=85 мм. Затем запрессуем втулку в отверстие с наружным диаметром 78 Н7 мм и внутренним 70 мм усилие запрессовки Р=320 кН.
Для восстановления поверхности 3 необходимо строгать шпоночный паз в отверстии 695 мм шириной b=20 мм длинной l=85 мм глубиной t=49 мм. Назначим подачу инструмента s=02 ммоб.
Скорость резания V ммин.:
Сv = 611; yv = 066; m = 012; kv = 078.
Pz = Cрz txpz Sypz kpz(2.2)
Cpz = 191; ypz = 075; kpz = 112.
Мощность потребная на резание:
Число двойных ходов в минуту равно:
где L1 - длина хода стола с учетом перебега и врезания;
По паспортным данным станка 7Е35 принимаем n = 150 ммин.
где L - длина пути проходимого резцом в направлении подачи;
B -ширина поверхности обработки;
n -число двойных ходов;
Tв = (001 02) Tо= 0015 093 = 00139 мин
Tоб=(1 6)% Tо=005093= 00465 мин
Tф=(4 8)%( Tо + Tв)=005 (093+00139) = 00472 мин
Для восстановления поверхности 4 подрезаем торец с 120 мм до 70 мм t=15 мм. Назначим подачу инструмента s=05 ммоб.
Затем определяется скорость резания по формуле (1.4):
Частота вращения шпинделя станка по формуле (1.8):
По паспортным данным станка 16К20 принимаем n=315 мин-1.
Определим основное время Tо по формуле (1.9):
Штучно-калькуляционное время по формуле (1.11):
Tв = (001 02) Tо= 0015 02 = 0003 мин
Tоб=(1 6)% Tо=00502= 001 мин
Tф=(4 8)%( Tо + Tв)=005 (02+0003) = 001015 мин
Затем используем наплавку под флюсом. Для этого наплавляем слой t=3 мм с 120 мм до 70 мм.
Это такой сварочный процесс при котором подача электродной проволоки и её перемещение вдоль детали подача защитных и легирующих материалов в зону дуги осуществляется механизированным способом. Преимущества:
-стабильно высокое качество шва;
-повышение производительности труда;
-возможность использования рабочих низкой квалификации. Параметры и режимы восстановления:
-проволока марки МП-50 диаметром 16 мм;
-скорость подачи электродной проволоки v =2 ммин;
После наплавки подрезаем торец с 120 мм до 70 мм t=2 мм.
В соответствии с исходными данными деталь получаем механической обработкой.
На основании расчетов курсовой работы были выбраны типы станков которые необходимы для производства деталей в соответствии с данным вариантом.
Для всех типов станков рассчитана подача скорость резания частота вращения шпинделя и основное время. В соответствии с расчетами составлена таблица с расчётом времени по каждой операции.
В соответствии с конструкцией детали был проведен анализ возможных дефектов и предложены методы восстановления.
Список использованной литературы
Восстановление деталей машин: Справочник Ф. И. Пантелеенко [и др.]; Под ред. Иванова В. П. - М.: Машиностроение 2003. - 672с.
Методические указания к практическим занятиям для выполнения курсовой работы студентам специальности 190205 «Подъемно-транспортные строительные дорожные машины и оборудование» Могилев 2007 г.
Общемашиностроительные нормативы режимов резания для технического нормирования работ на металлорежущих станках. Часть 1. М. «Машиностроение» 1974 411 с.
Общемашиностроительные нормативы режимов резания для технического нормирования работ на металлорежущих станках. Часть 2. М. «Машиностроение» 1974 200 с.
Хасуи А. Наплавка и напыление А. Хасуи О. Моригаки ; Пер. с яп.; Под ред. В. С. Степина Н. Г. Шестеркина. - М. : Машиностроение 198.
второй лист.cdw

Коэффициент смещения
Угол накл. линии зуб.
Операционные эскизы
Сталь 45 ГОСТ 1050-74
ДМ МШ126 09.08.04.010
титульник.docx
Министерство образования и науки Российской Федерации Государственное учреждение высшего профессионального образования «Белорусско-Российский университет»
«Технология производства и ремонта машин»
«Разработка технологических процессов изготовления и ремонта изделия»
Пояснительная записка
МШ-126-09.08.04.010 ПЗ
первый лист.cdw

Угол накл. линии зуб.
Твердость поверхности зубьев 200 240
Неуказанные радиусы закруглкния 2 3 мм
Остальные технические требования по СТБ 1014-95
Неуказанные штамповочные радиусы R=2мм
Сталь 45 ГОСТ 1050-74
ДМ МШ126 09.08.04.010
третий лист.cdw

Операционные эскизы
Сталь 45 ГОСТ 1050-74
ДМ МШ126 09.08.04.010
содержание.docx
1 Анализ назначения и технологичности детали . ..5
2 Выбор маршрута механической обработки .8
3 Расчет и назначение припусков ..9
4 Расчёт режимов резания 10
5 Выбор инструментов приспособлений и оборудования . 27
Технология ремонта изделия 32
1 Анализ возможных дефектов 32
2 Маршрут оборудование и режимы восстановления . .. .33
Список использованной литературы . ..39
Подъемно-транспортные машины.doc
Министерство образования и науки Российской Федерации
Федеральное агентство по образованию
Государственное учреждение высшего профессионального образования
Белорусско-Российский университет
Проректор по учебной работе
Рег. № ТД УМОТ-112тип
ПОДЪЕМНО-ТРАНСПОРТНЫЕ МАШИНЫ
для специальности1-36 11 01 Подъемно-транспортные строительные дорожные машины и оборудование
Факультет Автомеханический
Кафедра Строительные дорожные подъемно-транспортные машины и оборудование
По дневной форме обучения
По заочной форме обучения
Практические занятия
Лабораторные занятия
Всего аудиторных часов по дисциплине
Самостоятельная работа
Составитель: ст. преподаватель Костюшко А.Н.
Рабочая программа составлена в соответствии с типовой программой по дисциплине «Подъемно-транспортные машины» утвержденной 10.10. 2003г. рег. номер ТД-УМОТ-112тип
Рассмотрена и рекомендована к утверждению в качестве рабочего варианта на заседании кафедры «Строительные дорожные подъемно-транспортные машины и оборудование»
04.2009 г. протокол № 16
Зав. кафедрой СДПТМиО
Одобрена и рекомендована к утверждению на президиуме научно-методического совета университета
04.2009г. протокол № 6
Председатель президиума научно-методического совета университета
Рабочая программа согласована:
Зав. научно-библиографическим отделом
Начальник учебно-методического отдела
ПОЯСНИТЕЛЬНАЯ ЗАПИСКА
Дисциплина «Подъемно-транспортные машины» обеспечивает фундаментальную подготовку по вопросам конструирования и расчетов механизмов и отраслевых узлов деталей машин осуществляющих выполнение механических процессов по перемещению штучных грузов и сыпучих материалов.
1.Цель преподавания дисциплины
Целью преподавания дисциплины является формирование знаний умений и навыков проектирования расчета и эксплуатации грузоподъемных транспортирующих и погрузочно-разгрузочных машин применяемых при строительстве при механизации процессов по перемещению грузов.
2.Задачи изучения дисциплины
В результате изучения дисциплины студент должен знать:
-области применения основных видов подъемно-транспортных машин;
-тенденции развития подъемно-транспортных машин;
-конструктивное исполнение грузоподъемных машин;
-конструктивное исполнение транспортирующих машин;
-конструктивное исполнение погрузочно-разгрузочных машин;
-особенности расчета механизмов и узлов ПТМ;
-основы выбора основных параметров ПТМ;
-способы повышения надежности ПТМ.
-рассчитывать типовые механизмы кранов;
-обосновывать выбор грузозахватных приспособлений;
-определять основные параметры машин с учетом требований нормативных документов;
-выполнять необходимые расчеты исходя из требования обеспечения надежности и долговечности проектируемых устройств;
-соблюдать основные положения норм техники безопасности регламентируемых “Правилами устройства и безопасной эксплуатации грузоподъемных кранов”.
3. Перечень дисциплин с указанием разделов (тем) усвоение которых необходимо для изучения данной дисциплины
Данная дисциплина базируется на ранее изучаемых дисциплинах: строительная механика и металлические конструкции электро- и гидропривод детали машин теоретическая механика (все в полном объеме).
СОДЕРЖАНИЕ ДИСЦИПЛИНЫ
1 График учебного процесса распределение рейтинг-баллов по учебным модулям и видам занятий
Лаб.зан. баллы minmax
2 Наименование тем лекционных и лабораторных занятий и объем в часах
Самостоятельная работа
Тема. Основные вопросы
Краткий исторический очерк развития ПТМ. Перспективы и тенденции развития ПТМ. Место дисциплины в учебном процессе.
Простейшие грузоподъемные устройства
Грузоподъемные машины. Обзор конструкций ГПМ. Классификация ГПМ определения.
Расчет ГПМ. Общие положения. Весовые нагрузки. Нагрузки от оси инерции. Ветровые нагрузки. Расчетное сочетание нагрузок. Режимы эксплуатации ГПМ. Методика учета режима эксплуатации при прочностных расчетах.
Выбор кинематической схемы механизма подъема. Расчет каната полиспаста
Грузоподъемные приспособления. Крюки. Петли. Специальные захваты. Стропы. Магниты.
Стальные канаты цепи
Грузовые итоговые органы ГПМ. Гибкие органы ГПМ. Стальные канаты. Цепи. Расчет.
Полиспасты. Типы полиспастов. Определение усилий в канатах полиспаста.
Коуши. Зажимы для канатов. Расчеты. Типы. Крепление канатов с элементами металлоконструкции ГПМ.
Изучение процесса торможения
Остановы и тормоза. Остановы. Типы. Область применения. Расчет роликового останова.
Ленточные тормоза. Расчет. Тепловой расчет тормоза
Колодочные тормоза: электромагнитные гидравлические. Конструкции. Расчет.
Расчет механизма передвижения крановой тележки. Процесс неустановившегося движения
Дисковые тормоза замыкаемые весом груза с размыкающимися поверхностями трения. Конические тормоза с неразмыкающимися поверхностями. Расчет.
Сопротивление передвижению крановой тележки.
Привод ГПМ. Характеристика приводов. Электрический привод. Выбор мощности и типы электродвигателей. Механические характеристики крановых и электродвигателей.
Механизмы подъема и изменения вылета. Схемы механизмов. Установившееся движение. Разгон и торможение механизма.
Расчет механизма передвижения крановой тележки
Выбор электродвигателя механизма подъема. Определение усилий в стреловом полиспасте. Статический и кинематический расчеты механизмов. Приборы безопасности.
Исследование динамических нагрузок в канатах механизма подъема
Механизмы передвижения. Механизм передвижения с приводными колесами. Схемы. Сопротивление передвижению. Колеса. Типы. Расчет.
Механизм передвижения консольных и велосипедных кранов. Расчет. Статический расчет механизма.
Кинематический расчет механизмов. Процессы неустановившегося движения. Разгон и торможение
Расчет механизма поворот а
Механизм передвижения с канатной и цепной тягой.
Исследование тяговой способности приводов.
Механизмы поворота. Схемы механизмов поворота. Определение моментов сопротивления повороту в опорах крана.
Кран с внешней верхней опорой. Кран на неподвижной колонне. Конструкции. Статический расчет механизма.
Предохранительные устройства
Кинематический расчет. Процессы пуска и торможения. Выбор мощности эл. двигателя. Предохранительные устройства механизмов.
Элементы поворотных кранов. Колонны. Расчет. Траверсы. Фундаменты. Противовесы.
Исследование работы ленточного конвейера
Устойчивость кранов. Определение коэффициентов собственной и грузовой устойчивости кранов стрелового типа
Металлические конструкции. Материалы. Основные положения расчета и конструирования. Металлические конструкции мостовых кранов.
Расчет ленточного конвейера
Башенные и автомобильные краны. Конструкция выносных опор. Стрелы автомобильных кранов
Транспортирующие машины. Производительность. Мощность привода конвейера. Общая теория приводов.
Ленточные конвейеры. Основные элементы. Конструкции. Расчет конвейера методом обхода по «контуру». Распределение и сосредоточения сопротивления.
Тяговые органы конвейеров
Цепные конвейеры. Пластинчатые конвейеры. Основные элементы. Тяговый расчет.
Элеваторы. Ленточные элеваторы. Расчет.
Тема 21. Винтовые конвейеры. Конструкция.
Расчет цепного конвейера
Пневматические устройства всасывающего и нагнетательного типов. Область применения. Схемы.
Вспомогательные устройства конвейеров.
Бункера. Затворы. Питатели
Изучение работы и конструкции пластинчатого конвейера
3. Курсовой проект его характеристика
Содержание курсового проекта включает три части:
)предварительные расчеты механизмов - расчет механизма подъема расчет механизма передвижения или поворота;
)проектирование механизмов - подъема передвижения сборочного чертежа по указанию преподавателя (например тормоз крюковая подвеска и пр.);
) проектирование общего вида крана уточненные расчеты оформление пояснительной записки и окончательная корректировка чертежей.
Примерная тематика курсовых проектов представлена в приложении А.
Перечень этапов выполнения курсового проекта и количества баллов за каждый из них представлен в таблице.
Предварительные расчеты механизмов
Проектирование механизма подъема
Проектирование механизма передвижения или поворота
Проектирование общего вида крана и сборочного чертежа
Уточненные расчеты оформление пояснительной записки и окончательная корректировка чертежей
Итого за выполнение курсового проекта
Защита курсового проекта
Итоговая оценка курсового проекта представляет собой сумму баллов за выполнение и защиту курсового проекта и выставляется в соответствии с приведенной шкалой:
по пятибалльной системе:
Весовые нагрузки. Нагрузки от сил инерции. Ветровые нагрузки. Расчетное сочетание нагрузок.
Полиспасты. Типы. Расчет канатов и цепей.
Стальные проволочные канаты.
Полиспасты типы. Определение усилий в канатах.
Ленточные конвейеры. Типы. Тяговый расчет.
Колодочные тормоза: электромагнитные гидравлические. Расчет. Конструкции. Дисковые и конические тормоза.
Цепной конвейер. Типы. Тяговый расчет.
Схемы механизмов подъема. Статический кинематические расчеты. Разгон и торможение механизма.
Механизмы передвижения с приводными колесами. Схемы. Статический кинематический расчеты механизма. Разгон торможение механизма.
Механизм поворота. Схемы. Статический кинематический расчет. Разгон и торможение механизма.
Для самостоятельной подготовки студенты заочной формы обучения должны руководствоваться пунктом 2.2.
2 Контрольная работа
Студент выполняет одну контрольную работу состоящую из двух заданий:
№ 1 Расчет механизма подъема грузоподъемного крана – 8 семестр (20 стр.)
№ 2 Расчет конвейера – 8 семестр (20 стр.)
Контрольная работа выполняется в соответствии с “Методическими указаниями к выполнению контрольных работ по ПТМ” специальности Т.05.06.00.
УЧЕБНО-МЕТОДИЧЕСКИЕ МАТЕРИАЛЫ ПО ДИСЦИПЛИНЕ
1 Основная литература
Автор название место издания издательство год издания учебной литературы
Количество экземпляров
Александров М.П. Грузоподъемные машины. Учебник для ВУЗов. – М.: Изд-во МГТУ им. Н.П. Баумана. – Высшая школа 2000. – 552 с.
Доп. Мин. обр. РФ в кач. У для студ. вузов обуч. по напр. подготовки диплом. спец. «Транспортные машины и трансп. техн. комплексы»
Вайнсон Н.А. Подъемно-транспортные машины. М.: Машиностроение 1989. – 563 с.
Доп. Госкомитетом СССР по нар. обр. в кач. У для студ. вузов обуч. по спец. «Подъемно-транспортные строительные и дорожные машины»
Справочник по кранам: В 2 т.
Т.1. Характеристика материалов и нагрузок. Основы расчета кранов их приводов и металлических конструкций В.И. Брауде М.М. Гохберг И.Е. Звягин и др.; Под общ. ред. М.М. Гохберга. – М.: Машиностроение 1988. – 536 с.
Т.2. Характеристика и конструктивные схемы кранов. Крановые механизмы их детали и узлы. Техническая эксплуатация кранов М.П. Александров М.М. Гохберг А.А. Ковин и др.; Под общ. ред. М.М. Гохберга. – Л.: Машиностроение 1988. – 559 с.
Спиваковский А.О. Дьячков В.К. Транспортирующие машины. – М.: Машиностроение 1983. – 504 с.
2 Дополнительная литература
Правила устройства и безопасной эксплуатации грузоподъемных кранов. – 4-е изд. Минск: «ДНЭКОС» 2008. – 226 с.
Парницкий А.Б. Шабашов А.Н. Лысяков А.Г. Мостовые краны общего назначения М.: Машиностроение 1971. – 352 с.
Подъемно-транспортные машины. Аталс конструкций Под ред. Александрова М.П. и Решетова А.Н. – М. 1987. – 187 с.
Казак С.А. Динамика мостовых кранов.М.: Машиностроение 1968. – 160 с.
Расчеты грузоподъемных и транспортирующих машин Ф.К. Иванченко В.С. Бондарев Н.П. Колесник и др. – Киев: Издательское объединение «Вища школа». Головное изд-во 1978. – 576 с.
Допущено МВ и ССО УССР в кач. УП для студ. техн. наук
Иванов В.И. Иванов Е.Е. Специальные грузоподъемные машины Под ред. В.И. Иванова. – Мн.: Беларуская навука 1997. – 335 с.
3 Перечень наглядных и других пособий методических указаний по проведению конкретных видов учебных занятий а также материалов к используемым в учебном процессе техническим средствам
3.1Методические указания
Савицкий В.П. Лягушев Г.С Жариков B.C. Костюшко А.Н. Пискун И.А. Подъемно-транспортные машины. Методические указания для выполнения лабораторных работ. Могилев.: Белорусско-Российский университет 2005. – 75 с. (25 экз).
Костюшко А.Н. Методические указания к выполнению курсового проекта. Могилев: Белорусско-Российский университет 2004. –16 с. (100 экз).
Лягушев Г.С Борисов Н.К. Строительная механика и расчет металлоконструкций. Методические указания к практическим занятиям. Могилев: МГТУ 2002. – 46 с. (100 экз).
Иванов В.И. Грузоподъемные машины. Методические указания к практическим занятиям по дисциплине «Грузоподъемные машины» для студентов специальности 190205 «Подъемно-транспортные строительные дорожные машины и оборудование». Могилев: Белорусско-Российский университет 2007. – 30 с. (75 экз).
Костюшко А.Н. Методические указания к выполнению контрольных работ для студентов заочной формы обучения по дисциплине «Подъемно-транспортные машины» специальности Т.05.06.00 «Строительные дорожные и подъемно-транспортные машины и оборудование» Могилев.: Белорусско-Российский университет 2005. – 25с. (100 экз).
Костюшко А.Н. Методические указания для выполнения курсового проекта по дисциплине «Подъемно-транспортные машины для студентов специальности 1-36 11 01 «Подъемно-транспортные строительные дорожные машины и оборудование».
Плакаты по устройству отдельных механизмов кранов (2.1.4.1; 2.1.9.)
Плакаты по конструкции кранов (2.1.3.1; 2.1.6.1; 2.1.10.1; 2.1.12; 2.1.13.1; 2.1.1)
3.3Перечень программного обеспечения используемого в учебном
KOVSH - программа расчета рабочего оборудования.
Компас - программный пакет для создания конструкторской документации.
3.4 Технические средства используемые при преподавании дисциплины
Стенд для исследования свободных колебаний.
Стенд для исследования механизма передвижения тележки и ее конструкции.
Таль пневматическая ОПП-224.
Таль червячная ТЧ-5.
Тормозная установка ДМ-38.