Технология ремонта газораспределительного механизма автомобиля КАМАЗ 53212 с разработкой технологии восстановления толкателя




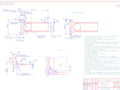
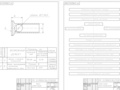
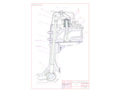
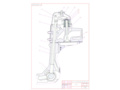
- Добавлен: 25.01.2023
- Размер: 1 MB
- Закачек: 2
Описание
Состав проекта
![]() |
![]() |
![]() ![]() ![]() ![]() |
![]() ![]() ![]() ![]() |
![]() ![]() ![]() |
![]() ![]() ![]() |
![]() ![]() ![]() |
![]() ![]() ![]() ![]() |
![]() ![]() ![]() |
![]() ![]() |
![]() ![]() ![]() |
![]() ![]() ![]() ![]() |
![]() |
Дополнительная информация
толкатель1.dwg

Карта дефектации Айзат.dwg

механизм газораспределения КамАЗ 740.dwg

механизм газораспределения КамАЗ 740 Артур.dwg

Рекомендуемые чертежи
- 25.01.2023
- 29.04.2021
- 28.03.2021
- 25.10.2022
- 23.05.2021
- 02.05.2021