Технология изготовления вала-шестерни


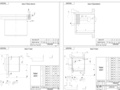
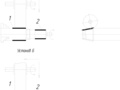
- Добавлен: 24.01.2023
- Размер: 334 KB
- Закачек: 0
Описание
Состав проекта
![]() |
![]() ![]() ![]() ![]() |
![]() ![]() ![]() |
![]() ![]() ![]() ![]() |
![]() ![]() ![]() |
Дополнительная информация
Drawing1.dwg

Содержание1.doc
2 Выбор режимов работы предприятия и фонды времени .6
3 Определение типа производства .6
4 Расчеты по программе выпуска ..6
Разработка технологического процесса изготовления
1 Служебное назначение вала-шестерни и его поверхностей 8
1.1 Служебное назначение вала-шестерни ..8
1.2 Служебное назначение поверхностей вала-шестерни ..8
2 Критический анализ технических требований на деталь 8
3 Технологические требования на деталь 9
4 Методы контроля основных технических требований
5 Анализ технологичности конструкции вала-шестерни ..10
6 Выбор вида и формы организации технологического процесса
изготовления вала-шестерни .11
7 Выбор исходной заготовки и метода ее получения 11
7.1 Выбор вида заготовки .11
7.2 Выбор метода получения заготовки .12
8 Выбор технологических баз и определение
последовательности обработки .12
8.1 Анализ вариантов базирования .12
8.2 Последовательность обработки поверхностей заготовки 15
9 Выбор способа обработки и определение количества
10 Технологический маршрут изготовления вала-шестерни 17
11 Расчет припусков межпереходных размеров и допусков 19
12 Уточнение оборудования .20
13 Выбор технологической оснастки 22
13.1 Выбор приспособлений 22
13.2 Уточнение режущего инструмента ..22
14 Выбор смазочно-охлаждающей жидкости 24
15 Расчет режимов резания ..24
16 Нормирование операций технологического процесса .25
Наладка.dwg

Операция 10 Токарная
Операция 15 Токарная
Операция 20 Радиально-сверлильная
Операция 25 Внутришлифовальная
Наименование и модель станка
Радиально-сверлильнай 2М55
1.1 Формулировка целей.doc
Целью курсовой работы является разработка технологического процесса изготовления вала-шестерни. Для достижения этой цели необходимо выбрать заготовку технологические базы и разработать технологический маршрут изготовления вала-шестерни.
2 Выбор режимов работы предприятия и фонды времени
В данной курсовой работе выбран односменный режим работы. Для принятого режима в соответствии с [1] действительный годовой фонд времени работы оборудования равен 2040 часов для металлорежущих станков массой до 10 тонн а действительный (эффективный) годовой фонд времени рабочих принят 1520 часов при рабочей неделе 36 часов и продолжительности основного отпуска 36 дней.
3 Определение типа производства
Так как годовая программа выпуска изделий равна 1500 штук и масса вала-шестерни составляет 4.88 кг то по [1] определено что при диапазоне годовой программы выпуска изделий от 500 до 35000 штук при массе детали от 2.5 до 5.0 кг тип производства соответствует среднесерийному.
4 Расчет по программе выпуска
Срок выпуска изделия С лет определится по формуле
где - программа выпуска по неизменным чертежам штук;
- годовая программа штук
Такт выпуска с определится по формуле
где - действительный фонд работы оборудования час
Программа в месяц штук определится по формуле
Программа в смену штук определится по формуле
где р – количество рабочих смен в месяце р = 22 [1]
Принимается = 6 штук
Величина партии деталей n определится по формуле
где - количество запусков изделия в год = 12 [1]
Вывод: изготовление вала-шестерни связано со среднесерийным типом
производства при его изготовлении на универсальном оборудовании с числовым программным управлением. Стоимость этого оборудования должна окупиться через 3 года
РАЗРАБОТКА ТЕХНОЛОГИЧЕСКОГО ПРОЦЕССА
ИЗГОТОВЛЕНИЯ ВАЛА-ШЕСТЕРНИ
1 Служебное назначение вала-шестерни и его поверхностей
1.1 Служебное назначение вала-шестерни
Служебное назначение конического вала-шестерни заключается в передаче вращательного движения коническому зубчатому колесу с изменением частоты вращения от 0.017 до 16.233 и крутящего момента величиной от 1 до 142.58 .
Вал-шестерня предназначен для работы в закрытом корпусе в масляном тумане созданном маслом марки ИГС-100 ГОСТ 17479.4-87 при температуре масла от плюс 50 до 60 ºС. Хвостовик вала-шестерни предназначен для работы в окружающей среде при температуре плюс 20 ºС. При работе вала возможно попадание на его поверхность пылевидных материалов с концентрацией пыли 1000 кгм3. Влажность окружающей среды составляет не более 75 процентов
1.2 Служебное назначение поверхностей вала-шестерни
Функции поверхностей определены в соответствии с рабочим сборочным чертежом редуктора рисунок 1
5810111415171819 – свободные поверхности;
– исполнительная поверхность;
– основные поверхности;
121316 – вспомогательные поверхности
Рисунок 1 – Функциональное назначение поверхностей вала-шестерни
2 Критический анализ технических требований на деталь
Анализ служебного назначения вала-шестерни и его поверхностей показал что в чертеж необходимо добавить следующие технические требования:
- перпендикулярность торцевой поверхности диаметром 62 мм к основной поверхности вала-шестерни диаметром 55 мм;
- соосность оси делительного конуса и оси опорной шейки вала-шестерни диаметром 55 мм;
- перпендикулярность торцевой поверхности диаметром 40 мм относительно шейки вала диаметром 39 мм;
- симметричность шпоночного паза и оси шейки вала диаметром 39 мм;
- соосность оси шейки вала диаметром 39 мм и оси вала диаметром 55 мм
3 Технические требования на деталь
Для определения технических требований было проанализировано служебное назначение поверхностей вала-шестерни (рисунок 1). Анализ показал что при изготовлении вала-шестерни необходимо обеспечить следующие требования:
- перпендикулярность торцевой поверхности диаметром 62 мм к основной поверхности вала-шестерни диаметром 55 мм допускаемое отклонение ±0.025∅62 [2];
- соосность оси делительного конуса и оси опорной шейки вала-шестерни диаметром 55 мм допускаемая погрешность Т = 8 мкм [2];
- перпендикулярность торцевой поверхности диаметром 40 мм относительно шейки вала диаметром 39 мм допускаемое отклонение ±0.003∅39 [2];
- симметричность шпоночного паза и оси шейки вала диаметром 39 мм допускаемое отклонение Т = 3 мкм [2];
- соосность оси шейки вала диаметром 39 мм и оси вала диаметром 55 мм допускаемая погрешность Т = 8 мкм [2]
Остальные технические требования указаны на чертеже
4 Методы контроля основных технических требований на деталь
При изготовлении вала-шестерни необходимо проконтролировать торцевое биение торцевой поверхности 3 к поверхности 6 допускаемое отклонение ±0.025∅62 [2]
Контроль торцевого биения проводится в соответствии с рисунком 2
– индикатор 1ИГП 11300 ГОСТ 6933-72 цена деления 1 мкм;
– стойка CI ГОСТ 10197-70;
– плита 1-0-400×400 ГОСТ 10905-86;
– опора призматическая ГОСТ 12194-66
Рисунок 2 – Схема контроля торцевого биения вала-шестерни
Для контроля шейки вала ∅55k6 выбрана калибр-скоба 8113-0142 k6 по ГОСТ 18362-73 [3]
5 Анализ технологичности конструкции вала-шестерни
Вал-шестерня как объект проектирования имеет простые конструктивные формы минимальное количество видов обрабатываемых поверхностей и геометрических размеров однотипных элементов его конструкции. Обеспечивается соответствие конструкции проектируемого вала-шестерни наиболее вероятному виду заготовки и методу ее получения. Для унификации канавок вала-шестерни целесообразнее использовать один и тот же резец. Поэтому канавки на валу нарезаются шириной 5 мм
Как объект изготовления вал-шестерня отвечает следующим характеристикам:
- конструктивные формы позволяющие применять производительные методы механической обработки и использовать высокопроизводительное оборудование;
- возможность применения прогрессивного технологического процесса;
- обеспечение условий врезания и выхода режущего инструмента а также хорошего доступа для обработки и измерения поверхности вала-шестерни;
- обеспечение удобств базирования вала-шестерни при его обработке достижение достаточной жесткости конструкции.
При эксплуатации проектируемой детали обеспечены хорошие условия взаимозаменяемости одного вала другим удобство замены шпонки в шпоночном пазу вала-шестерни. Также достигнуто удобство технического обслуживания ремонта в процессе эксплуатации.
Таким образом конструкция вала-шестерни является технологичной
6 Выбор вида и формы организации технологического процесса изготовления вала-шестерни
Так как годовая программа выпуска изделия составляет 1500 штук на предприятии определен среднесерийный тип производства и обработка проектируемого вала в основном связана с обработкой на токарных станках то целесообразно организовать непоточное производство с организацией участков по типу оборудования (участок токарных станков фрезерных). Данная форма организации производства характерна для выпуска изделий в относительно небольших количествах
7 Выбор исходной заготовки и метода ее получения
7.1 Выбор вида заготовки
Деталь представляет собой коническую вал-шестерню из стали марки 40Х
ГОСТ 4543-71. При его изготовлении в качестве исходной заготовки можно выбрать полуфабрикат – прокат или заготовку полученную пластическим деформированием.
Вал-шестерню целесообразнее изготовлять из полуфабриката – проката так как материал вала Сталь 40Х вал имеет максимальный диаметр 63 мм при длине 262 мм. Вал имеет сложную конфигурацию: количество ступеней пять перепад диаметров – 4 мм тип производства – среднесерийный с годовой программой выпуска 1500 штук. Среди проката целесообразнее предпочесть горячекатаную сталь калиброванной так как:
- стоимость горячекатаного проката меньше калиброванного;
- вал-шестерня не имеет необрабатываемых поверхностей поэтому высокая точность исходной заготовки не требуется
Из литературного источника [4] выбирается круглый горячекатаный прокат из стали 40Х диаметром 70 мм обычной точности В второй категории для холодной механической обработки который обозначается следующим образом:
Данный прокат имеет следующий химический состав:
- содержание углерода С % 0.4;
- содержание хрома Cr % 0.6;
- твердость по Бриннелю НВ 217;
- предел текучести Т Нмм2 785;
- предел прочности В Нмм2 980;
- относительное удлинение % 10;
- относительное изменение площади % 45
Эскиз исходной заготовки представлен в соответствии с рисунком 3
Рисунок 3 – Заготовка
7.2 Выбор метода получения заготовки
Для горячекатаного проката применимы следующие способы резки:
- на токарно-отрезном станке (точность резки составляет от 0.3 до 0.8 мм);
- с помощью ленточной пилы (точность резки – от плюс-минус 1.5 до 5 мм ширина реза – от 0.8 до 1.3 мм)
Проанализировав характеристики отрезки выбирается токарно-отрезной станок так как его точность резки выше
8 Выбор технологических баз и определение последовательности обработки
8.1 Анализ вариантов базирования
При изготовлении вала-шестерни необходимо решить две задачи.
Задача №1. Обеспечить перпендикулярность торцевой поверхности 3 диаметром 62 мм к поверхности 6 диаметром 55 мм. Допускаемое торцевое биение 0.025∅62
Рассмотрены два варианта базирования обеспечивающие решение поставленной задачи. Погрешность при первом варианте базирования γ мкм рисунок 4 составит
γ = СПИД ток.оп. = 0.01062 мкм [2]
Рисунок 4 – Эскиз технологической наладки
При втором варианте базирования рисунок 5 суммарная погрешность γ мкм определится по формуле
где γ1 – погрешность первого звена мкм;
γ2 – погрешность второго звена мкм
γ1 = = СПИД ток.оп. = 0.01062 мкм [2]
γ2 = = СПИД ток.оп. = 0.006120 мкм [2]
γ = 0.01062 + 0.006120 = 0.01662 мкм
Рисунок 5 – Эскиз технологической наладки
Вывод: применяется второй вариант базирования так как:
- он обеспечивает требуемую точность;
- его можно реализовать практически
Задача №2. Обеспечить соосность оси делительного конуса и оси опорной шейки вала-шестерни диаметром 55 мм. Допускаемая погрешность Т = 20 мкм
Рассмотрены два варианта базирования обеспечивающие решение поставленной задачи. Погрешность при первом варианте базирования А мкм рисунок 6 составит
А = СПИД зуб.оп. = 6 мкм [2]
Рисунок 6 – Эскиз технологической наладки
При втором варианте базирования рисунок 7 суммарная погрешность А мкм определится по формуле
где А1 – погрешность первого звена мкм;
А2 – погрешность второго звена мкм
А1 = В = СПИД зуб.оп. = 6 мкм [2]
А2 = Г = СПИД ток.оп. = 6 мкм [2]
Рисунок 7 – Эскиз технологической наладки
8.2 Последовательность обработки поверхностей заготовки
Принятый вариант базирования определяет следующую последовательность обработки вала-шестерни:
- обработка торцев и зацентровка;
- последующая обработка с центровых отверстий
9 Выбор способов обработки и определение количества переходов
Последовательность обработки поверхностей заготовки сведена
Таблица 1 – Последовательность обработки поверхностей заготовки
Хвостовик вала ∅39 k6
Точение получистовое
Обтачивание черновое
Шейка вала с резьбой
Обтачивание чистовое
Поверхность под подшипники
Шлифование предварительное
Продолжение таблицы 1
Обтачивание получистовое
Фрезерование шпоночного паза 12Р9
Торец ∅62 длина 217 мм
10 Технологический маршрут изготовления вала-шестерни
Маршрут обработки поверхностей заготовки представлен в таблице 2
Таблица 2 – Маршрут обработки заготовки
Наименование и содержание операции
Схема технологической наладки
Отрезка прутка ∅70 и длиной 262 мм
Токарно-отрезной станок
Править пруток 70×262
Правильно-калибровочный стан типа ПК-90
Фрезерно-центровальная
Фрезеровать два торца 1 одновременно и центровать два отверстия 2
Двусторонний фрезерно-центровальный полуавтомат последовательного действия МР-76М
Точить поверхн. 1234 точить фаски 56 проточить канавки 78 нарезать резьбу 10.
Точить конусную поверхн. 9
Токарно-винторезный станок 16К20Ф3
Фрезеровать шпоночный паз 12Р9
Шпоночно-фрезерный полуавтомат модификации 692А
Продолжение таблицы 2
Шлифовать наружные поверхн. 12. Б.Переустановить
Шлифовать поверхн. 34.
Круглошлифоваль-ный станок 3М151
Фрезеровать 19 зубьев с модулем
Зубофрезерный полуавтомат модели 5С277П
Шлифовать наружные поверхности 12. Переустановить.
Шлифовать поверхность 3
Зачистить заусенцы на торцах зубьев
Полуавтомат для снятия заусенцев 5525
11 Расчет припусков межпереходных размеров и допусков
Схема для определения количества переходов при обработке цилиндрической поверхности ∅55 мм представлена в соответствии с рисунком 8
Рисунок 8 – Схема для определения количества переходов при обработке цилиндрической поверхности ∅55 мм
Схема для определения количества переходов при обработке торцевой поверхности ∅62 мм представлена в соответствии с рисунком 9
Рисунок 9 – Схема для определения количества переходов при обработке торцевой поверхности ∅62 мм
Величины припусков межпереходных размеров и допусков остальных поверхностей указаны в таблице 1
12 Уточнение оборудования
Из литературного источника [6] выбирается токарный станок 16К20Ф3 со следующими техническими характеристиками:
- наибольший диаметр обрабатываемой заготовки над станиной м 0.4;
- расстояние между центрами м 1;
- наибольший диаметр обрабатываемой заготовки над супортом м 0.2;
- частота вращения шпинделя с-1 0.21 – 33.3;
- мощность привода подачи Вт 6160;
- шаг нарезаемой метрической резьбы мм 0.5 – 112;
- скорость быстрого перемещения по осям координат мс:
- мощность электродвигателя привода главного движения Вт 7500
Из литературного источника [4] выбирается зубофрезерный полуавтомат для прямозубых конических колес модели 5С277П со следующими техническими характеристиками:
- наибольший диаметр обрабатываемого колеса м 0.50;
- наибольший модуль обрабатываемых колес мм 12;
- число зубьев нарезаемых колес 10 – 150;
- расстояние от торца шпинделя бабки заготовки
до центра стола м 0.115 – 0.415;
- частота вращения дисковых фрез с-1 0.33 – 1.33;
- время рабочего хода при нарезании одного зуба с 10 – 120;
- мощность электродвигателя привода главного движения Вт 5500
Из литературного источника [4] выбирается круглошлифовальный станок модели 3М151 со следующими техническими характеристиками:
- наибольшие размеры устанавливаемой заготовки м:
- высота центров над столом м 0.125;
- частота вращения шпинделя заготовки
с бесступенчатым регулированием с-1 0.83 – 30;
- наибольшие размеры шлифовального круга м:
а) наружный диаметр 0.6;
- частота вращения шпинделя шлифовального круга с-1
- скорость врезной подачи шлифовальной бабки мммин 0.1 – 4;
- мощность электродвигателя привода главного движения Вт 10000
Из литературного источника [4] выбирается фрезерно-центровальный станок модели МР-76М со следующими техническими характеристиками:
- размеры обрабатываемой детали мм:
а) диаметр 25 - 800;
б) длина 250 - 1000;
- фрезерные головки:
- число скоростей шпинделя 7;
- число оборотов шпинделя мин-1 270 – 1254;
- подача мммин 20 – 400;
- сверлильные головки:
- число скоростей шпинделя 6;
- число оборотов шпинделя мин-1 238 – 1125;
- подача мммин 20 – 300;
- диаметр применяемого центровального сверла мм 8;
- вес станка кг 8700
Из литературного источника [4] выбирается шпоночно-фрезерный станок модели 692А со следующими техническими характеристиками:
- размеры размеры рабочей поверхности стола мм:
- перемещение гильзы со шпинделем мм 60; - число скоростей шпинделя 16;
- число оборотов шпинделя мин-1 50 - 1600;
- мощность электродвигателя привода главного движения Вт 5500;
- число подач стола мммин:
- продольная и поперечная 2950;
13 Выбор технологической оснастки
13.1 Выбор приспособлений
Из литературного источника [4] выбирается трехкулачковый самоцентрирующий патрон ГОСТ 24351 – 80 со следующими характеристиками мм:
- диаметр заготовки 80
Из литературного источника [4] выбираются центры А-1-4-Н
ГОСТ 8742 - 75 со следующими характеристиками мм:
- угол конуса градус 45
Из литературного источника [4] выбирается призматическая опора
ГОСТ 12194 - 66 со следующими характеристиками мм:
13.2 Уточнение режущего инструмента
Из литературного источника [4] выбирается проходной прямой резец
ГОСТ 18869-73 со следующими характеристиками:
- сечение державки мм 25×20;
- материал режущей части Т1458;
- главный угол в плане φ градус 45;
- главный задний угол α градус 8;
- главный передний угол γ градус 12
Из литературного источника [4] выбирается канавочный прямой резец
ГОСТ 18874-73 со следующими характеристиками:
- сечение державки мм 8×8×50;
- материал режущей части Т14К8;
- главный угол в плане φ градус 90;
- главный задний угол α градус 10;
- главный передний угол γ градус 16
Из литературного источника [4] выбирается резьбовой правый резец
ГОСТ 18885-73 со следующими характеристиками:
- сечение державки мм 25×16;
- угол при вершине в плане градус 60;
- главный задний угол α градус 12;
- главный передний угол γ градус 0;
- шаг резьбы мм 1.25 – 5;
Из литературного источника [4] выбирается отрезной прямой резец
ГОСТ 18884-73 со следующими характеристиками:
- сечение державки мм 40×25;
- главный передний угол γ градус 12;
Из литературного источника [4] выбирается торцевая фреза
ГОСТ 9304-69 со следующими характеристиками:
- диаметр фрезы мм 80;
- внутренний диаметр фрезы мм 32;
Из литературного источника [4] выбирается центровочное сверло
ГОСТ 14952-75 со следующими характеристиками:
- материал режущей части Р6М5;
- длина сверла мм 80
Из литературного источника [4] выбирается шпоночная фреза
ГОСТ 17021-71 со следующими характеристиками:
- длина режущей части мм 26;
Из литературного источника [4] выбирается шлифовальный круг
ПП350×50 со следующими характеристиками мм:
- внутренний диаметр 50;
- шлифовальный материал 4А
Из литературного источника [4] выбирается дисковая модульная фреза
ГОСТ 10996-64 со следующими характеристиками:
- диаметр фрезы мм 63;
- материал режущей части Т5К10;
- внутренний диаметр фрезы мм 22;
- модуль нарезаемого зуба мм 2 – 4;
- главный передний угол γ градус 0
14 Выбор смазочно-охлаждающей жидкости
Для операции 10 принимается смазочно-охлаждающая жидкость (СОЖ) «Укринол-1» (3%). Данная СОЖ представляет собой эмульсию без химически активных присадок. Способ подвода - струйное охлаждение с расходом до 50 лч [11]
Для операции 15 принимается СОЖ «Укринол-1» (3%). Способ подвода - свободно падающая струя с расходом до 60 лч [11]
Для операции 30 принимается СОЖ «МР-1». Способ подвода - свободно падающая струя с расходом до 100 лч [11]
15 Расчет режимов резания
Расчет режимов резания производится аналитическим методом. Результаты расчетов представлены в таблице 3
Таблица 3 - Режимы резания
Наимено-вание модель станка
Зубофре-зерный полуавтомат
16 Нормирование операций технологического процесса
Для среднесерийного производства определенного в данной курсовой работе норма штучно-калькуляционного времени ТШТ К мин определится по формуле
ТШТ К = ТО+ ТВ+ ТОБС+ ТОТД+ ТП Зn (8)
гдеТО– основное время мин;
ТВ– вспомогательное время мин;
ТОБС– время на обслуживание мин;
ТОТД– время на отдых мин;
ТП З– подготовительно-заключительное время мин;
n– величина партии деталей шт
Основное время ТО мин определяется по формуле
гдеL – длина обрабатываемой поверхности с учетом величин врезания и перебега инструмента мм;
n – частота вращения шпинделя обмин;
Вспомогательное время время на обслуживание время на отдых подготовительно-заключительное время определяется по справочной литературе [9]
Для операции 10 штучно-калькуляционное время составляет
ТШТ К = 0.44 мин для операции 15 - 10 мин для операции 20 – 1.65 мин для операции 25 – 3 мин для операции 30 – 135.6 мин.
ФЕДЕРАЛЬНОЕ АГЕНСТВО ПО ОБРАЗОВАНИЮ
ГОСУДАРСТВЕННОЕ ОБРАЗОВАТЕЛЬНОЕ УЧРЕЖДЕНИЕ
ВЫСШЕГО ПРОФЕССИОНАЛЬНОГО ОБРАЗОВАНИЯ
ИВАНОВСКИЙ ГОСУДАРСТВЕННЫЙ
АРХИТЕКТУРНО-СТРОИТЕЛЬНЫЙ УНИВЕРСИТЕТ
Автомобильно–дорожный факультет
Кафедра «Подъёмно-транспортные строительные
дорожные машины и системы гидроприводов»
РАСЧЕТНО – ПОЯСНИТЕЛЬНАЯ ЗАПИСКА К
«ТЕХНОЛОГИЯ МАШИНОСТРОЕНИЯ ПРОИИЗВОДСТВО И
НА ТЕМУ «ИЗГОТОВЛЕНИЕ ВАЛА-ШЕСТЕРНИ»
ЗАДАНИЕ НА ВЫПОЛНЕНИЕ КУРСОВОЙ РАБОТЫ
«ТЕХНОЛОГИЯ МАШИНОСТРОЕНИЯ ПРОИЗВОДСТВО И
Студент Мозжухин Сергей Александрович
Тема: изготовление вала-шестерни
Исходные данные для проектирования:
Годовая программа выпуска .. . . 1500
Программа выпуска по неизменным чертежам шт 4500
подпись дата фамилия инициалы
стр. 26 табл. 3 ил. 9
ТЕХНОЛОГИЧЕСКИЙ ПРОЦЕСС МЕХАНИЧЕСКАЯ ОБРАБОТКА ДЕТАЛЬ БАЗИРОВАНИЕ ЗАГОТОВКА ПРИСПОСОБЛЕНИЕ РАЗМЕРНЫЙ АНАЛИЗ МАРШРУТ ПРИПУСК РЕЖИМЫ РЕЗАНИЯ ВАЛ-ШЕСТЕРНЯ БАЗА МЕЖПЕРЕХОДНЫЙ РАЗМЕР
В курсовом работе разработан технологический процесс изготовления вала-шестерни
В настоящее время машиностроительная отрасль России развивается в условиях рыночной экономики. Такая тенденция заставляет производителей машиностроительной продукции выпускать более технологичную продукцию. В результате этого значительно повысился уровень культуры проектирования работ инженером - конструктором и инженером - технологом. В условии рыночной экономики производитель обязан предусматривать все варианты производства изделия как с технико-экономической точки зрения так и с технологической.
В данной курсовой работе разработан технологический процесс изготовления вала-шестерни. Разработка производилась с учётом экономичности и технологичности производства изделия. Было выбрано обоснованное с технико-экономической точки зрения оборудование – станки с числовым программным управлением и оснастка для производства детали а также определен наиболее рациональный вид материала для изготовления вала-шестерни – прокат.
Рекомендуемые чертежи
- 24.01.2023
Свободное скачивание на сегодня
- 23.08.2014