Технологический процесс изготовления развертки




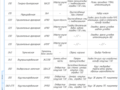
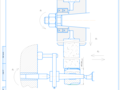
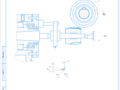
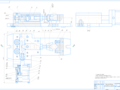
- Добавлен: 24.01.2023
- Размер: 1 MB
- Закачек: 0
Описание
Состав проекта
![]() |
![]() |
![]() ![]() ![]() ![]() |
![]() ![]() ![]() ![]() |
![]() ![]() ![]() ![]() |
![]() |
![]() ![]() ![]() |
![]() ![]() ![]() ![]() |
![]() ![]() ![]() ![]() |
![]() ![]() ![]() |
![]() ![]() ![]() ![]() |
![]() ![]() ![]() ![]() |
Дополнительная информация
фрезер присп.cdw

* - размеры для справок
Допуск погрешности базирования 0
Усилие на прижиме при давлении воздуха в сети 4 кгмм
должно быть не менее 200 кгс.
наладка заточн.cdw

Универсально-заточная
Универсально-заточной
Круг 12А2-20 125x32x13x5 АС2 6350 М2 - 01 100%
Головка делительная автоматическая
наладка круглошлиф.cdw

мс А 1кл ГОСТ 2424-83
Патрон поводковый ГОСТ 2571-71
центр вращ. А-1-2Н ГОСТ 8742-75
хомутик ГОСТ 2578-70
Наименование операции
* - размер для справок.
записка новая.doc
1 Назначение изделия описание его конструкции. Технические требования к изготовлению изделия
2 Анализ технологичности изделия
3 Материал изделия его состав и свойства. Режимы термообработки
4 Определение массы изделия
5 Определение типа производства и операционной партии изделий
ТЕХНОЛОГИЧЕСКАЯ ЧАСТЬ
1 Выбор метода получения заготовки
2 Назначение технологических схем обработки поверхностей
3 Проектирование маршрута обработки изделия
4 Выбор технологических баз оборудования и оснастки
5 Определение припусков межоперационных размеров и допусков
6 Конструирование заготовки определение ее массы
коэффициента использования материала и стоимости
7 Расчет режимов резания и основного времени
8 Расчет норм штучного и штучно-калькуляционного времени
КОНСТРУКТОРСКАЯ ЧАСТЬ
1 Выбор и описание конструкции станочного приспособления
2 Расчет приспособления
3 Расчет измерительного инструмента
Одним из главных элементов любого машиностроительного производства является инструментальная оснастка обеспечивающая надёжность функционирования каждого отдельного станка и производственной системы в целом.
Роль инструментальной оснастки в условиях высокоавтоматизированного гибкого производства возросла так что способна определить конструкцию и схему построения отдельных станков и систем.
В последние годы конструкции инструментов претерпели существенные изменения и основные отличительные особенности современных инструментов можно свести к следующим направлениям:
использовать в качестве режущих элементов механически закреплённых многогранных неперетачиваемых пластин в результате чего гарантированна неизменность и оптимальность геометрических параметров а также их точность;
применение малоразмерных инструментов в монолитном исполнении позволило распространить твердый сплав практически на все диапазоны размеров а также использование их для резьбообработки и мелкомодульных зуборезных и других инструментов ранее традиционно изготовлявшихся из быстрорежущей стали;
использование при изготовлении панели инструментов новых инструментальных материалов а именно синтетических сверхтвердых материалов на основе нитрида бора;
применение одно- и многослойных износостойких покрытий наносимых на твёрдые сплавы и быстрорежущие стали;
использование подвода СОЖ под высоким давлением непосредственно в зону резания и использование СОЖ для обратной транспортировки стружки что позволяет повысить эффективность механообработки;
разработка различных модульных систем инструментов представляющих органическое сочетание групп режущих и вспомогательных инструментов что позволяет повысить универсальность инструментов и автоматизацию производства но возможности сократить число элементов в наборе и охватить как можно более широкий круг технических задач.
Значительно изменилась и технология изготовления самих инструментов в связи с появлением новых технологических процессов а также конструктивным изменением инструментов. Основными технологическими направлениями развития инструментального производства являются:
широкое использование методов пластической деформации при получении заготовок инструментов (продольно-винтовой прокат горячая экструзия и т.п.);
использование абразивного инструмента из синтетических алмазов и нитрида бора позволяющие существенно снизить шероховатость режущих поверхностей и повысить их физико-механические свойства;
использование методов порошковой металлургии в том числе для получения биметаллического инструмента;
применение специальных высокоточных и высокопрочных абразивов в сочетании с эффективной высоконапорной системой обильного охлаждения и очистки охлаждающей жидкости создало возможность глубинного шлифования и вышлифовки стружечных канавок резьб и т.п.;
автоматизация технологических процессов применение автоматических загрузочных устройств роботов манипуляторов автоматических линий станков с ЧПУ;
концентрация и совмещение операций применение высокоэффективной оснастки и групповой технологии;
внедрение новейших методов термической обработки износостойких покрытий;
расширение области применения электрофизических и электрохимических методов обработки.
В дипломном проекте согласно заданию предусматривается разработка технологического процесса изготовления развертки. В проектируемом техпроцессе предполагается заменить ряд станков на более современные модели применить приспособления с быстродействующими зажимами что позволит повысить качество снизить трудоемкость и себестоимость изготовления развертки.
1Назначение изделия описание его конструкции. Технические требования к изготовлению изделия
Развертка применяется для окончательной обработки отверстий с целью получения высокой точности и высокого класса шероховатости поверхности. Развертывание обеспечивает 6 8 квалитет точности и шероховатость Rа=16 04 мкм.
Развертка во многом напоминает зенкер; основное ее отличие от зенкера заключается в том что она снимает значительно меньший припуск и имеет большее число зубьев - от 6 до 12. Режущая часть развертки расположена к оси под углом р и выполняет основную работу резания.
Калибрующая часть служит для направления инструмента при работе для калибрования отверстий и сохранения размера инструмента после его переточки. У развертки калибрующая часть состоит из двух участков: цилиндрического и конического так называемого обратного конуса.
Обратный конус делается для уменьшения трения инструмента об обработанную поверхность и меньшего увеличения диаметра отверстия.
Развертка 2963-4081 является насадной и применяется для чернового развертывания отверстия.
Основные элементы развертки представлены на рис. 1.1
А - заборная( режущая) часть
Б - калибрующая часть -цилиндрический участок
В - калибрующая часть выполненная с обратной конусностью
Д - паз для торцевой шпонки оправки на которой крепится развертка
Е - отверстие конусное 1: 30; основная конструкторская база
Ж - выточка; необходима для уменьшения длины базового отверстия
Основные технические требования к изготовлению развертки:
Корпус развертки изготавливается из стали 40Х с закалкой и отпуском до твердости 37 47 HRCЭ режущая часть – пластины твердого сплава 26250 ВК8 ГОСТ 25425-82.
Допуск радиального биения относительно оси отверстия режущей части -0025 мм калибрующей части - 0015 мм.
Допуск смещения оси шпоночного паза относительно оси конусного отверстия 008 мм.
Точность диаметральных размеров без предельных отклонений должна находиться пределах 14 квалитета а линейные размеры выполняются с предельными отклонениями ± IT14 2.
Маркируется обозначение инструмента и марка материала режущей части.
Технологичность изделия определяющая трудоемкость его изготовления оценивается по качественным показателям на основе анализа рабочего чертежа и технических требований.
По своей конструкции развертка относится к деталям типа «втулки»; с точки зрения рационального метода получения заготовки детали типа «втулки» не достаточно технологичны так как при применении проката в качестве заготовки значительная часть металла будет уходить в стружку а получение отверстий методом горячей штамповки в условиях серийного производства экономически не целесообразно так как требуется применение дорогостоящих штампов и оборудования.
Показатели точности и шероховатости находятся в экономических пределах (7 квалитет точности и шероховатость Rа = 04 мкм); не требуется применения тонкого шлифования или доводки.
Возможно применение на основных операциях стандартного режущего мерительного инструмента и оснастки.
Для реализации принципа постоянства баз необходимо использование специальных оправок что удорожает себестоимость изготовления развертки.
Возможно применение типовых схем обработки для большинства поверхностей базовое конусное отверстие может быть обработано по типовой схеме для насадного инструмента.
Отсутствуют труднодоступные для обработки поверхности; за исключением выточки в конусном отверстии D= 28 мм которую можно обработать только расточным резцом.
Проведенный анализ позволяет сделать вывод о том что развертка является достаточно технологичным изделием.
3 Материал изделия его состав и свойства.
Режимы термообработки
Корпус развертки изготовлен из стали 40Х ГОСТ 4543-80. Сталь 40Х относится к группе улучшаемых конструкционных легированных сталей. Улучшаемые конструкционные легированные стали содержат от 03 до 045% углерода и обычно подвергаются закалке с высоким отпуском что приводит к повышению прочности и пластичности.
В инструментальном производстве сталь 40Х широко применяется для изготовления корпусов сборного инструмента.
Химический состав и механические свойства стали
Температура закалки °С
Температура отпуска °С
Твёрдость после отпуска НRСэ
Режущая часть развертки изготовлена из пластинок металлокерамического твердого сплава ВК6.
Твердый сплав ВК8 относится к группе вольфрамовых (однокарбидных) сплавов состоящих из зерен карбида вольфрама сцементированных кобальтом. Вольфрамовые сплавы более вязки и менее хрупки чем титановольфрамовые но менее износостойкие. Инструменты из сплавов ВК8 применяют в основном при черновой обработке заготовок из чугуна.
Химический состав и механические свойства твердого сплава
Предел прочноости МПа
Расчетная масса изделия ориентировочно определяется по формуле:
Мизд = Vобщ×ρ кг (1.1)
Где V общ - общий объем изделия определенный расчетным путем мм3
ρ - плотность материала корпуса изделия кгмм3; для стали Р6М5
На рис 1.2 представлен эскиз развертки для определения ее объема.
Обьем развертки без учета внутренних полостей:
Рабочая часть - цилиндр; диаметр равен среднему диаметру учитывающему глубину стружечных канавок: Днар = 57016 мм. h = 6 мм.
Дср = 57016 – 6 = 51016 мм. Принимаем Дср = 51 мм. L = 40 мм.
Понижение – цилиндр: Д2=55 мм L2=15 мм
Обьем внутренних полостей:
Отверстие конусное - правое: Дmax = 27мм dmin = 265мм L = 16мм
левое: Дmax = 26мм dmin = 255мм L = 16мм
Выточка - цилиндр: Д5=28 мм L5=23 мм.
Паз: а=12 мм в=14 мм l=55 - 26=23 мм – призма.
Общий обьем развертки:
V = (V1 + V2) – (V3 + V4 + V5 + V6) = (816714 + 356194) – (8988 + 83283 + 141551 + 4872) = 811474 мм3.
Масса развертки Мизд = 811474 785 10-6 = 0637 кг.
5 Определение типа производства и величины операционной партии
Для определения типа производства используем заданный годовой объем выпуска разверток и массу изделия.
По заданию годовой объем выпуска разверток составляет 2000 шт.; масса развертки 0637 кг.
Используя эти данные устанавливаем тип производства - среднесерийное [1 с. 24 табл. 3.1]
Среднесерийное производство характеризуется ограниченной номенклатурой изделий сравнительно большим объемом выпуска. Обработку ведут периодически повторяющимися партиями.
При серийном производстве используются универсальные станки оснащенные как специальными так и универсальными приспособлениями. Также используют и специализированные станки и полуавтоматы.
В серийном производстве технологический процесс изготовления изделий преимущественно дифференцирован т. е. расчленен на отдельные операции выполняемые на определенных станках.
Количество изделий в партии для одновременного запуска определяем по формуле:
где N - годовой объем выпуска изделий шт.
а - число дней на которое необходимо иметь запас изделий
F -число рабочих дней в году.
В нашем случае: N = 2000F=250 дней а = 60 дней.
Выбор метода получения заготовки зависит от конструктивных форм и размеров готовой детали марки материала объема выпуска изделий и типа производства. При решении этого вопроса необходимо стремиться к максимальному приближению конфигурации заготовки к конфигурации готовой детали т. е. снижению отходов но при этом необходимо учитывать и себестоимость получения заготовки особенно в условиях серийного производства.
Для корпусов режущего инструмента широко применяется прокат круглый горячекатаный по ГОСТ 2590-71. Так как по своей конструкции развертка имеет наружную поверхность ступенчатую и ступень меньшего диаметра имеет незначительную длину (1=15 мм) по сравнению с общей длиной развертки (L = 55 мм) и небольшую разницу в диаметрах ( Дmах = 57 мм и dmin = 55 мм) то в качестве заготовки наиболее рационально использование круглого проката. Применяем как наиболее дешевый - прокат обычной точности В — ГОСТ 2590-71.
Отрезку заготовки производим в заготовительном отделении на ножовочном станке мод. 872М; режущий инструмент - полотно ножовочное из стали Р6М5 толщиной b = 2 мм.
Технологические схемы обработки назначаем с учетом требуемой точности размеров и шероховатости поверхностей используя рабочий чертеж развертки и таблицы экономической точности.
Основные поверхности и элементы развертки изображены на рис. 2.1.
Таблица 2.1 Технологические схемы обработки поверхностей
Поверхности или элементы
Параметры по чертежу
Пооследовательностьтехнологических переходов
Обеспечиваемые параметры
Точение однократное Термообработка
Шлифование предварительное
Стружечные канавки 8
Передняя поверхность 9
Назначаем план обработки развертки с учетом ее конструктивных особенностей типа производства и технологических схем обработки.
Операция 005 Подрезать торец центровать под сверление; сверлить зенкеровать развернуть конусное отверстие; расточить выточку; точить понижение снять фаски
Операция 010 Точить рабочую часть и заборную фаску; подрезать второй торец
Операция 015 Маркировать
Операция 020 Фрезеровать паз
Операция 025 Фрезеровать стружечные канавки
Операция 030 Фрезеровать задние углы 12°
Операция 035 Фрезеровать пазы под пластины твердого сплава
Операция 040 Калить и отпустить очистить заготовки от окалины
Операция 045 Шлифовать конусное отверстие
Операция 050 Заточить зубья по передней поверхности
Операция 055 Шлифовать рабочую часть предварительно
Операция 060 Шлифовать заборный конус под углом 15°
Операция 065 Шлифовать заборную фаску под углом 45°
Операция 070 Шлифовать рабочую часть с обратным конусом
Операция 075 Шлифовать рабочую часть по цилиндру начисто
Операция 080 Заточить задние углы 100 с оставлением ленточки
Операция 085 Заточить задние углы 10° наостро на заборной фаске 45°
Операция 090 Заточить задние углы 10° наостро на заборной части 15°
Одним из наиболее сложных и принципиальных разделов проектирования техпроцессов механической обработки является назначение технологических баз. От правильного решения данного вопроса в значительной степени зависят:
фактическая точность выполнения размеров заданных конструктором;
правильность взаимного расположения обрабатываемых поверхностей;
степень сложности и конструкция необходимых приспособлений режущих и мерительных инструментов.
Основные принципы базирования - принцип постоянства и совмещения баз принцип последовательной смены баз.
Принцип постоянства баз заключается в том что при разработке техпроцесса необходимо стремиться к использованию одной и той же технологической базы не допуская без особой необходимости смены баз не считая смены черновой базы. Для насадного режущего инструмента это - центральное отверстие.
Принцип совмещения баз предусматривает чтобы в качестве технологической базы по возможности использовать поверхность являющуюся измерительной базой и конструкторской. Для насадного инструмента - это центральное посадочное отверстие.
Принцип последовательной смены баз заключается в том что при смене баз следует переходить от менее точной к более точной.
Исходя из основных принципов базирования выбираем технологические базы:
черновую базу используем только при обработке базового конусного отверстия; на всех последующих базой является отверстие конусное т. е. заготовка крепится на оправке;
после термообработки первой операцией будет шлифование базового отверстия а затем все шлифовальные и заточные операции производим на оправке.
Выбранные базы оборудование и оснастку сводим в таблицу 2.2.
Паспортные данные станков
Токарно - винторезный станок мод. 16К20
Наибольшие размеры обрабатываемой заготовки мм
Частота вращения шпинделя мин"1 125 1600
Наибольшее перемещение суппорта мм
Подача суппорта мм об
Габаритные размеры мм 2505х1190
Горизонтально - фрезерный станок мод. 6Р80
Размеры рабочей поверхности стола мм 200 800
Наибольшее перемещение стола мм
Частота вращения шпинделя мин -1 50 2240
вертикальная 125 560
Габаритные размеры мм 1525 х1875
Внутришлифовальный станок мод.ЗК225В
Наибольший диаметр устанавливаемой заготовки мм 200
Диаметр шлифуемых отверстий мм 3 25
Наибольший ход стола мм 320
Наибольший угол поворота бабки заготовки град 45
Скорость движения стола м мин
при правке шлифовального круга 01 2
Частота вращения шпинделя мин-1
внутришлифовального 20000 100000
бабки заготовки 280 2000
торцешлифовального приспособления 11500
Габаритные размеры мм 2225х1775
Универсально — заточной станок мод. ЗД642Е
Наибольшие размеры заготовки мм
Наибольший диаметр круга мм 200
Частота вращения шпинделя мин"1 2240..6300
Скорость продольного перемещения стола м мин 02 80
Габаритные размеры мм 1800х1470
Таблица 2.2. Технологические базы оборудование и оснастка
Наименование операции
Режущий и измерительный инструмент
Токарно-револьверная
Патрон трехкулачковый с пневмозажимом
Державки для резцов; втулки переходные; резец подрезной; резец проходной; сверло спиральное; зенкер конусный 1:30; развертка конусная 1:30; резец расточной; шт.-циркуль; калибр конусный 1:30; кронциркуль
Отверстие конусное 1:30
оправка 1:30 спец.; патрон трехкулачковый с пневмозажимом
Резец проходной Т15К6 φ=45°; шт.-циркуль
Приспособление (при станке)
Горизонтально-фрезерная
Приспособление спец. с пневмозажимом
Оправка; фреза дисковая пазовая Р6М5; шт.-циркуль; калибр на симметричность; калибр пазовый
Головка делительная; бабка задняя; оправка 1:30 спец.;центра;
Оправка; фреза угловая; шаблон угловой
Оправка; фреза пазовая; штангенциркуль ШЦ
Термопечь; ванна зак.
Диаметр рабочей части
Патрон трехкулачковый
Оправка для круга; круг шлифовальный; калибр конусный 1:30
Универсально- заточная
Приспособление делительное при станке; центра; хомутик спец.; оправка 1:30
Круг эльборовый тарельчатой формы; образцы шероховатости
Центра; хомутик; оправка 1:30 спец.
Круг ЭБ формы ПП; микрометр
Круг шлифовальный ЭБ формы ПП; угломер
Круг шлифовальный ЭБ формы ПП; скоба индикаторная
Центра; хомутик; оправка 1:30 спец
Круг шлифовальный эльборовый формы ПП; скоба
Приспособление делительное при станке; центра; хомутик спец. оправка 1:30 спец.
Круг эльборовый формы ЧК; угломер; лупа
Приспособление делительное (при станке); центра; хомутик спец.; оправка 1:30 спец.
Приспособление делительное при станке; центра; хомутик спец.; оправка 1:30 спец.
5. РАСЧЁТ ПРИПУСКОВ НА ЗАГОТОВКУ
Заготовка – сталь горячекатаная круглая обычной точности (В) без правки.
Метод базирования при обработке – переход 1 – в патроне;
переходы 2 и 3 – на оправке центровой.
По таблице 3.12 [1 с. 40] назначаем припуск на подрезку торцов: zT = 06 мм.
Определяем осевые размеры заготовки:
LЗАГ = 55 + 2 zT = 55 + 2 06 = 562 мм.
Принимаем LЗАГ = 57 мм.
LК = 05 LЗАГ = 05 57 = 285 мм.
Определяем припуски аналитическим методом для рабочей части
Минимальный припуск при обработке наружных поверхностей вращения определим по формуле:
Где Rz – высота микронеровностей оставшихся при выполнении предшествующего технологического перехода мкм
Т – глубина дефектного поверхностного слоя при выполнении предшествующего перехода мкм
rо - суммарное отклонение расположения возникшее на предшествующем переходе мкм
ey - величина погрешности установки заготовки на выполняемом переходе мкм.
Производим расчёты заполняя таблицу 2.3.
Определяем значение Rz и Т:
Заготовка Rz = 150 мкм; Т = 250 мкм [1.с.63]
Переход 1Rz = 30 мкм; Т = 30 мкм
Переход 2Rz = 10 мкм; Т = 20 мкм
Переход 3Rz = 6 мкм;Т = 12 мкм [1с.63 таб.3.21]
Определяем значение rо.
Местную кривизну заготовки определяем по формуле:
где Dy – удельное отклонение мкммм
D y = 130 [1c.64 табл. 3.22]
Величина смещения оси заготовки в результате погрешности зацентровки:
где d3 - допуск на диаметр заготовки d3=11 мм [ с.43 табл. 3.14]
Суммарное отклонение расположения заготовки:
Для перехода 1 определяем остальное отклонение.
где Ку – коэффициент уточнения
Ку = 006[1.с.61 табл. 3.19]
После перехода 1 производится термообработка поэтому дополнительно определяем rт:
где - удельное отклонение после термообработки
Определяем суммарное отклонение после перехода 1 и термообработки:
Для перехода 2 значение rо определяем по формуле (2.4):
Кy = 006 [1с.61 табл. 3.19]
Для перехода 3 значение rо можно не учитывать ввиду малой величины.
Определяем погрешность установки на выполняемом переходе
где - погрешность базирования
- погрешность закрепления.
Для перехода 1: = 0 мкм [2 с.76 табл. 36] – при установке в патроне
= 320 мкм [2 с.76 табл. 37]
Для переходов 2 и 3 – при установке на конической центровой оправке:
= 0 мкм = 0 мкм [2 с.76 табл. 37 прим. 1].
По формуле (2.1) определяем расчётные припуски:
Определяем наименьший предельный размер окончательно обработанной повенрхности (по чертежу):
dmin = dном + НО = 57016 + (-0005) = 57011 мм
Последовательно заполняем графу 8 суммируя данные граф 8 и 7:
В графу 9 записываем значения допусков используя данные граф 2 и 8:
dзаг = 11 мм [1 с.43 табл. 3.14]
d1 = 02 мм – 12 квалитет
d2 = 006 мм – 9 квалитет d3 = 0025 мм – 7 квалитет
Заполняем графу 10 округляя данные графы 8 в сторону увеличения до того знака что в графе 9.
Запролняем графу 11 суммируя данные граф 10 и 9:
011 + 0005 = 57016 мм
Заполняем графу 12 используя данные графы 10:
09 – 57011 = 0079 мм
Заполняем графу 13 используя данные графы 11:
15 – 57016 = 0134 мм
Определяем общие припуски в графах 12 и 13:
Производим проверку правильности расчетов используя данные граф 12 13 и 9:
Определяем номинальный диаметр заготовки – прутка:
Dзаг = dminзаг - HOзаг (2.7)
где HOзаг – нижнее отклонение диаметра прутка:
HOзаг = -07 мм [1 с. 43 табл. 3.14]
dminзаг = 591 (по расчету)
Dзаг = 591 - ( -07 ) = 598 мм.
Принимаем по сортаменту пруток ближайшего большего диаметра:
Dзаг = [1 с. 43 табл. 3.14]
Назначаем окончательно межоперационные размеры и допуски:
Шлифование предварительное до
Шлифование чистовое до .
5.3. Отверстие конусное 1:30 .
Припуски на обработку хвостовой части назначаем табличным методом. Ранее была назначена технологическая схема обработки хвостовика:
)Сверление – 12 квалитет;
)Зенкерование – 11 квалитет;
)Развертывание – 9 квалитет;
)Шлифование – 7 квалитет.
Определяем межоперационные припуски табличным методом с целью определения диаметра сверла. При конусности 1:30 и длине отверстия 4 мм:
D = 27016 – 15 = 25516 мм.
Табличный припуск [3 т.1]
На шлифование z4 = 03 мм.
На развертывание z3 = 04 мм.
На зенкерование z2 = 05 мм.
Производим расчеты для заполняя таблицу 2.4.
Dmax = 25516 – 0005 = 25511 мм.
Dmax = 25511 – 03 = 25211 мм » 252 мм.
Dmax = 252 – 04 = 248 мм.
Dmax = 248 – 05 = 243 мм.
Dном = 243 – 02 = 241 мм.
Dном = 248 – 01 = 247 мм.
Dном = 252 – 004 = 2516 мм.
Окончательная схема обработки конусного отверстия (расчетные размеры конусного отверстия пропорционально переводим на контролируемый размер отверстия ):
Таблица 2.4 Табличный метод расчета припусков
Технологические переходы
Расчётный размер Dmin мм
Допуск или предельное отклонение мм
Номинальный размер Domm
Аналитический расчет припусков
Технологические переходы обработки поверхности
Элементы припуска мкм
Расчетный припуск 2Zmin мм
Расчетный диаметр dр мм
Предельный размер мм
Предельные значения припусков мм
Точение однократное
Шлифование предварительное
* Из расчета исключается в связи с последующей термообработкой
6. Конструирование заготовки определение ее массы коэффициента использования материала и стоимости.
Эскиз заготовки развертки с основными размерами приведен на рис. 2.3.
Определяем массу заготовки:
где ρ = 785 10-6 кгмм3 – плотность стали 40Х.
Определяем общую массу материала с учетом отходов при отрезке от прутка:
где b – ширина отрезного инструмента при отрезке мм
b = 2 мм – при отрезке абразивным кругом.
Определяем коэффициент использования материала:
где Мизд – масса готового изделия кг.
По предварительным расчетам Мизд = 0637 кг. .
Масса отходов при изготовлении развертки: Мотх = Мм – Мизд = 13 – 0637 = 0663 кг.
Определяем стоимость заготовки исходя из цен на материалы и сдаваемые отходы (стружку): Sзаг (2.11)
где Ц – цена одной тонны стали 40Х руб;
Цотх – цена одной тонны стружки руб.
По ценам действующим на 1.02.2002 г.
7. Расчет режимов резания и основного времени.
7.1. Операция 010 Токарно-винторезная
Снять установить и закрепить заготовку.
Точить поверхность 1.
Материал заготовки – сталь 40Х В = 920 МПа.
Режущий инструмент – резец проходной Т15К6 φ = 45О радиус при вершине r = 08 мм.
Станок – токарно-винторезный мод. 16К20.
Рассчитанные параметры обработки.
Диаметр до обработки D = Dзаг = 60 мм.
Диаметр после обработки d = 575 мм.
Число проходов i = 1.
Дальнейшие расчеты производим по справочнику [3 т.2].
Табличная подача ST = 033 ммоб [с. 268 табл. 14].
Принимаем по паспорту станка S = 040 ммоб.
Назначаем стойкость резца Т = 60 мин [с. 268].
Скорость резания определяем по формуле
где Cv – коэффициент скорости резания
m x y – показатели степени
Kv – общий поправочный коэффициент Kv = Kmv * Knv * Kuv [с. 265] (30).
[с. 261 табл. 1] (2.14)
где Kr – коэффициент характеризующий группу стали по обрабатываемости
nV – показатель степени.
Kr = 07; nv = 10 [с. 262 табл. 2]
По формуле (2.14) определяем:
Из таблицы 17 [с. 269] Cv = 350 x = 015 y = 035 m = 020.
Расчетный диаметр D = 60 мм.
Расчетная частота вращения станка
Принимаем по паспорту станка n = 630 обмин.
Действительная скорость резания
Длина резания (по эскизу) lp = 40 мм.
Величина подвода и врезания:
lпод = t * ctg φ + (05 20) = 175 * ctg 45 + 2 = 4 мм.
Величина перебега: lпер = 1 3 = 2 мм.
Расчетная длина обработки: L = lp + lпод + lпер = 40 + 4 + 2 = 46 мм.
Число рабочих ходов i = 1.
Диаметр до обработки D = Dзаг = 55 мм.
Диаметр после обработки d = 2518 мм.
Глубина резания t = h = 10 мм.
Подачу принимаем поо переходу 2: S = 04 ммоб.
Дальнейшие расчеты производим по нрмативам [5].
Kv = 10 vP = 117 1 = 117 ммин
Длина резания при поперечном точении
Величина врезания и перебега: l1 = 2 мм.
Расчетная длина обработки: L = 15 + 2 = 17 мм.
При точении фаски режимы резания принимаем по переходу 3:
t = 10 мм – ширина фаски.
Основное время: То = SТоi = 018 + 007 + 0012 = 0262 мин.
7.2 Операция 025. Горизонтально – фрезерная.
Фрезеровать десять стружечных канавок по последовательно 1 последвательно.
Материал заготовки – сталь 40Х В = 920 Мпа; 255НВ.
Режущий инструмент – фреза дисковая Р6М5 zФ = 22.
Станок горизонтально-фрезерный мод. 6Р80.
Число проходов на каждую канавку i = 1.
Глубина и ширина фрезерования (по эскизу) t = 63 мм B = 13 мм.
Расчет режимов резания производим по нормативам [5].
Табличная подача на 1 зуб фрезы: Sz = 007 005 ммзуб [карта 194].
Поправочный коэффициент на подачу: Ksz = 10 [с. 190 табл. 13 схема I].
Принимаем для расчета Sz = 006 ммзуб.
Табличная скорость резания Vт = 44 ммин [карта 196].
Поправочные коэффициенты:
Kmv = 055 [карта 120]
Kzv = 10 [карта 199]
Kv = 10 [c. 190 табл. 13.II]
Расчетная скорость резания: Vр = 44 055 10 10 = 242 ммин.
Расчетный диаметр D = D ф = 75 мм.
Расчетная частота вращения фрезы:
Принимаем по паспорту станка n = 100 обмин.
Фактическая скорость резания:
Расчетная минутная подача
Принимаем по паспорту станка .
Уточняем подачу на зуб фрезы
Длина резания l = 32 мм (по эскизу).
Длина подвода и врезания
Величина перебега lпер = 1 5 мм принимаем lпер = 3 мм.
Расчетная длина обработки L = lр + lпод + lпер = 40 + 23 + 3 = 66 мм.
Число рабочих ходов на одну канавку: i = 1.
Основное время на обработку одной канавки: .
Общее основное время на операцию To = z . TO1 = 10 . 0528 = 528 мин.
7.3. Операция 045 Внутришлифовальная
Шлифовать отверстие 1.
Материал заготовки – сталь 40Х 60 64 HRCЭ
Диаметр до обработки: d = 2666 мм.
После обработки D = 27016 мм (минимальный диаметр конусного отверстия
Параметр шероховасти Rа = 08 мкм.
Станок – внутришлифовальный мод. 3К225В.
Выбираем размеры круга и устанавливаем его характеристику: при внутренем шлифовании рекомендуется [6 с.312].
Принимаем отноошение равным 09:
Dk = 09 175 = 1575 мм. Принимаем по стандарту Dk = 16 мм высота круга Вк = 40 мм диаметр отверстия круга dk = 6 мм.
Материал круга – 24А (электрокорунд белый) [3 т. 2 с. 242]
Характеристика круга: [3 т. 2 с. 247 249]
Полное обозначение круга: ПП 16406 24А 25 Н С1 7 К5 35 мс 1кл. А
Допустимая кружная скорость круга vk = 35 мс.
Расчетная частота вращения шпинделя шлифовального круга:
обмин в паспортных пределах станка (20000 100000 мин-1).
Табличная скорость вращения заготовки Vзт:
Vзт = 20 40 ммин [3 т. 2 с. 301].
Принимаем Vзт = 40 ммин = 067 мс.
Расчетный диаметр заготовки: Dз = 27мм.
Расчетная частота оборотов вращения заготовки (регулируется бесступенчато):
Табличная глубина шлифования:
t = 00025 001 [3 т. 2 с. 301].
Принимаем t = 00025 мм.
Радиальная подача на каждый ход численно равна глубине шлифования:
Sp = t = 00025 ммход.
Табличная продольная подача на один оборот заготовки:
Sпр.т = (025 04)×Bк [3 т. 2 с. 301].
Принимаем Sпр.т = 025 40 = 10 ммоб.
Скорость продольной минутной пдачи стола (регулируется бесступенчато)
Sм = nз Sпр = 472 10 =4720 мммин.
Принятые значения nз Sпр Sм находятся в паспортных пределах станка.
Расчетная длина обработки L = Lш + Lп = 55 + 40 = 95 мм
при перебеге круга на каждую сторону равном 05Вк.
Припуск на шлифование на сторону:
Коэффициент учитывающий время на выхаживание:
Число рабочих ходов:
Основное время на операцию:
7.4. Операция 045. Заточная
Заточить десять зубьев по передней поверхности 1 последовательно.
Материал заготовки – сталь 40Х В = 780 МПа.
Метод заготовки – с прерывистым контактом изделия и круга.
Припуск снимаемый при заточке h = 005 мм.
Станок универсально-заточной мод. 3Д642Е.
При заданных величинах припуска и шероховатости при затачивании инструмента из быстрорежущей стали рекомендуется заточка кругами из эльбора[6 с. 373 табл. 149].
Форма круга – тарельчатая 12А2-200 (ЛЗТ).
Размеры круга: Dк = 150 мм d = 32 мм H = 16 мм.
Характеристика круга [6 с. 373 табл. 149]:
марка алмаза – ЛО связка – БИ1- бакелитовая
концентрация 100% (4) зернистость – 10080 [4 т. 2 с. 245 250].
Полное обозначение круга
А2 - 200 150321610 ГОСТ 17123–79 ЛО 10080 БИ1 100% (4).
Расчетный диаметр D = Dк = 150 мм.
Табличная окружная скорость круга vK = 20 30 мс [3 т. 2 с. 302].
Принимаем vK = 25 мс.
Расчетная частота вращения круга
Принимаем по паспорту станка nK = 3150 обмин.
Фактическая скорость резания:
Табличная продольная подача стола: Snp = 15 ммин = 1500 мммин.
Принимаем Snp = 2 ммин. Это значение находится в паспортных пределах станка.
Табличная подача на глубину шлифования: St = 001 002 ммдв. ход.
Глубина резания в данном случае численно равна поперечной подаче:
Длина затачиваемой поверхности lр = 40 мм (по эскизу).
Высота зуба Н = 6 мм.
Величина перебега lпер = 1 3 мм
принимаем lпер = 3 мм.
Расчетная длина обработки L = lр + lпод + lпер = 40 + 32 + 3 = 75 мм.
Коэффициент учитывающий время на выхаживание: K = 12 15
Число рабочих ходов: i = 16 где h – припуск на заточку и h = 01 мм.
Основное время на заточку одного зуба:
Общее основное время на операцию:
Приспособление фрезерное предназначено для закрепления заготовок на операции 025 - горизонтально - фрезерной.
Основными узлами приспособления являются: основание поз. 1 с корпусом поз. 11; опора поз. 13 с упорной призмой поз. 15; механизированный привод состоящий из пневмоцилиндра с поршнем поз. 19 и
зажимной клиноплунжерный механизм состоящий из прижима поз. 14
ползуна поз.5 и клина поз. 10.
Приспособление устанавливается на столе горизонтально - фрезерного станка мод.6Р80 по направляющим шпонкам поз.Зб прикрепленных к основанию поз. 1 винтами поз.24 и закрепляется с помощью станочных болтов входящих в пазы основания.
К корпусу поз. 11 прикреплен пневмоцилиндр двустороннего действия с поршнем поз.19 и штоком поз.21. Шток соединяется с толкателем поз.16. Головка толкателя расположена в пазу клина поз. 10. Клин поз. 10 имеет опору в виде двух роликов поз.9 на осях поз. 8. Третий ролик на оси поз.6 скользит по наклонной поверхности клина. Ролик расположен в пазу ползуна поз.5левый конец которого входит в наклонный паз клина. Правый конец ползуна через винт поз. 12 соединен с прижимом поз. 14; прижим закреплен на пальце поз.4.
Обрабатываемая заготовка устанавливается на опору поз.13 до упора в неподвижную призму поз. 15. При подаче воздуха в нижнюю полость цилиндра шток движется вверх; вверх движется и клин а ползун с прижимом будут перемещаться вправо и зажимать заготовку.
При переключении пневмокрана и подаче воздуха в верхнюю полость пневмоцилиндра поршень со штоком движется вниз; вниз движется и клин с наклонным пазом и левым концом ползуна в нем .Ползун перемещается влево и отводит прижим от обрабатываемой заготовки. Происходит освобождение заготовки.
Рисунок 3.1 Расчетная схема приспособления
3. Расчёт измерительного инструмента
Для контроля изделий на операции 030 (шлифование цилиндрических поверхностей) используется калибр - скоба.
Производим расчёт проходного и непроходного размеров скобы.
Контролируемый диаметр: D = 45 h6.
Наименьший предельный диаметр:
Dmin = D + HO = 45 + (-0016) = 44984 мм.
Допуск размера изделия: d = ВО – НО = (+0000) - (-0016) = 0016мм.
Для 8 квалитета (по таблице допусков и квалитетов) отклонение середины поля допуска проходного размера скобы относительно наибольшего предельного размера изделия равно: z1 = 3 мкм = 0003 мм.
Допуск на измерительные размеры скобы: НК = 7 мкм = 0007 мм.
Наименьший проходной размер скобы определяем по формуле:
ПРmin = Dmax – z1 - Нк2 (3.3)
Исполнительного размера проходной части скобы с учётом допуска Нк:
ПРmin = 45000 – 0003 – 0007 05 = 449935 мм.
Наименьший проходной размер скобы равны :
НЕ = 44984 - 0007 05 = 449805 мм.
Используемый непроходной размер скобы с допуском Нк проставляемый на чертеже НЕ = 449805+0.007.
Схема расположение допуска на размеры изделия и скобы приведена на рис. 3.2.
Рисунок 3.2. Схема расположения полей допусков на изделие
Библиографический список
Нефедов Н.А. «Дипломное проектирование в машиностроительных техникумах» М. «Высшая школа» 1986.
Добрыднев И. С. Курсовое проектирование по предмету «Технология машиностроения» М. «Машиностроение» 1985.
Курсовое проектирование по технологии машиностроения Под ред. А. Ф. Горбацевича. Минск. «Высшая школа» 1975.
Справочник технолога-машиностроителя т. 1 и 2. Под ред. А. Г. Косиловой и Р. К. Мешерякова. М. «Машиностроение» 1986.
Общемашиностроительные нормативы режимов резания для технического нормирования работ на металлорежущих станках (ч.1). М. «Машиностроение» 1994.
Нефедов Н. А. Осипов К. А. Сборник задач и примеров по резанию металлов и режущему инструменту. М. «Машиностроение" 1994.
Общемашиностроительные нормативы времени вспомогательного на обслуживание рабочего места и подготовительно-заключительного для технического нормирования М. «Машиностроение» 1990.
Белоусов А. П. Проектирование станочных приспособлений. М. «Высшая школа» 1974.
Волков О.ИСкляренко В.К. «Экономика предприятия» М. ИНФРА-М2002.
Шипунов В.Г. «Управление предприятием» М.«Высшая школа» 1999.
Мельников Т.Н. Вороненко В.П. «Проектирование механосборочных цехов» М. «Машиностроение» 1990.
Гамрат-Курек Л. «Экономическое обоснование дипломных проектов» М. «Высшая школа» 1986.
«Расчеты экономической эффективности в дипломных и курсовых проектах» М. «Высшая школа» 1984.
фрезер паз.cdw

Операция 40.cdw

Наладка технологическая 2.CDW

Развертка.cdw

Маркировать обозначение и марку твердого сплава..
Остальные технические требования по ГОСТ 5735-81Е.
техпроцесс.cdw

Технологические базы
Режущий и измерительный инструмент
Токарно-револьверная
Патрон трехкулачковый
Державки для резцов; втулки переходные;
резец подрезной; резец проходной;
сверло сприральное; зенкер конусный 1:30;
развертка конусная 1:30; резец расточной;
штангенциркуль; калибр конусный 1:30
Резец проходной Т15К6;
Горизонтально-фрезерная
Наружняя поверхность
Приспособление спец.
Оправка; фреза дисковая пазовая Р6М5;
штангенциркуль; калибр на симметричность;
Головка делительная;
Оправка; фреза угловая;
Оправка для круга; круг шлифоваллный;
калибр конусный 1:30
Универсально-заточная
Приспособление делительное
образцы шероховатости
Круг ЭБ формы ПП; микрометр
при станке; центра; хомутик
Технологический процесс
изготовления развертки 2323-1111
Рекомендуемые чертежи
- 24.01.2023