Технологический процесс изготовления детали Крышка




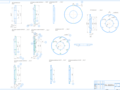
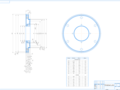
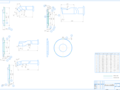

- Добавлен: 24.01.2023
- Размер: 462 KB
- Закачек: 1
Описание
Состав проекта
![]() |
![]() ![]() ![]() ![]() |
![]() ![]() ![]() ![]() |
![]() ![]() ![]() |
![]() |
![]() ![]() ![]() ![]() |
![]() ![]() ![]() ![]() |
Дополнительная информация
Чертеж Размерные цепи.cdw

Чертеж План обработки.cdw

0 Токарно-черновая 16К20Ф3С32
5 Токарно-чистовая 16К20Ф3с32
0 Токарно-чистовая 16К20ф3С32
5 Внутришлифовальная 3К227В
0 Круглошлифовальная 3У143МВ
ПЗ ВМ.doc
РАСЧЕТНО-ПОЯСНИТЕЛЬНАЯ
к курсовому проекту
По дисциплине «Технологические процессы в машиностроении»
ТЕМА КУРСОВОГО ПРОЕКТА
Технологический процесс изготовления детали «Крышка»
Назначение детали и условия её работы характеристики материала детали4
Анализ технологичности детали5
Анализ типа производства7
Технологическое оборудование8
Расчёт операционных размеров 12
Расчёт режимов механообработки 15
Нормирование операций 24
Список использованной литературы 27
Цель курсового проектирования по технологии машиностроения - научится правильно применять теоретические знания полученные в процессе учебы использовать свой практический опыт работы на машиностроительных предприятиях для решения профессиональных технологических и конструкторских задач.
К мероприятиям по разработке новых прогрессивных технологических процессов относится и автоматизация на ее основе проектируется высокопроизводительное технологическое оборудование осуществляющее рабочие и вспомогательные процессы без непосредственного участия человека.
В соответствии с этим решаются следующие задачи: Расширение углубление систематизация и закрепление теоретических знаний и применение их для проектирования прогрессивных технологических процессов сборки изделий и изготовления деталей включая проектирование средств технологического оснащения. Развитие и закрепление навыков ведения самостоятельной творческой инженерной работы. Овладение методикой теоретико-экспериментальных исследований технологических процессов механосборочного производства.
В курсовом проекте должна отображаться экономия затрат труда материала энергии. Решение этих вопросов возможно на основе наиболее полного использования возможностей прогрессивного технологического оборудования и оснастки создания гибких технологий.
Назначение детали и условия её работы характеристики материала детали
Деталь крышка служит для ограничения осевого перемещения вала расположенного на подшипниках в изделии (машине) за счет создания определенного натяга или гарантированного осевого зазора между торцом наружного кольца подшипника и торцом крышки. Крышки кроме того используются для плотного закрытия различных отверстий и пространств с целью их изоляции от окружающей среды. Деталь выполняется из чугуна СЧ15 ГОСТ 1412-85.
Крышка представляет собой деталь в форме тела вращения с габаритными размерами 22*240. Деталь имеет пазы.
Поверхности детали выполняется по 14 квалитету. После обработки деталь подвергают контролю.
Характеристики материала детали
Чугун – наиболее распространенный материал для изготовления отливок благодаря хорошим технологическим свойствам и относительной дешевизне. У серых чугунов хорошие технологические и прочностные свойства.
Химический состав чугуна СЧ15 для отливки должен соответствовать требованиям указанным в таблицах.
Таблица №1.1. Химический состав %
Таблица №1.2. Механические свойства
Анализ технологичности детали
Технологичность - комплекс требований и показателей характеризующие технологическую рациональность конструктивных решений в зависимости от вида изделий и стадии разработки конструкторской документации.
Размеры детали соответствуют нормальному ряду чисел допустимые отклонения размеров соответствуют ГОСТ 25347-82.
Деталь жесткая имеет поверхности удовлетворяющие требованиям достаточной точности установки. Простановка размеров технологична так как их легко можно измерить на обрабатывающих и контрольных операциях.
При изготовлении детали используют нормализованные и специализированные измерительные и режущие инструменты.
Конструкция детали технологична по следующим параметрам:
oконструкция детали состоит из стандартных и унифицированных конструктивных элементов;
oдеталь изготовляется из стандартной заготовки (круг);
oразмеры и поверхности детали имеют соответственно оптимальные точность и шероховатость;
oфизико-химические и механические свойства материала форма и размеры соответствуют требованиям технологии изготовления;
oконструкция детали обеспечивает возможность применения типовых и стандартных технологических процессов её изготовления.
Исходными данными для проектирования технологического маршрута обработки детали являются: рабочий чертеж детали и производственная программа.
При этом предлагается придерживаться следующих рекомендаций:
В зависимости от шероховатости точности и специальных требований чертежа детали назначают окончательные методы обработки.
Назначают методы предшествующей обработки поверхностей т.е. определяются этапы: черновой чистовой и отделочный.
При наличии операций термической обработки и гальванопокрытий определяют их место в технологическом процессе изготовления детали.
Устанавливают поверхности детали подлежащие обработке на каждой операции т.е. формируется примерное их содержание.
План обработки см. на чертеже ТМ.2010.31401.26.КП
Перечислим последовательность технологических операций получения детали:
0 - заготовка - литье
5 - токарно-черновая с ЧПУ
0 - токарно-чистовая с ЧПУ
5 - токарно-черновая с ЧПУ
5 - внутришлифовальная
0 - круглошлифовальная
Комплект технологической документации прилагается.
Анализ типа производства
Характер технологического процесса в значительной мере зависит от типа производства деталей (единичного серийного массового). Это обусловлено тем что в различных типах производств экономически целесообразно использование различного по степени универсальности механизации и автоматизации оборудования приспособлений различного по сложности и универсальности режущего и измерительного инструмента. В зависимости от вида производства существенно изменяются и организационные структуры цеха: расстановка оборудования системы обслуживания рабочих мест номенклатура деталей и т.д.
Сведения перед разработкой технологического процесса отсутствуют. В этих условиях поступаю следующим образом. По табл.1 устанавливаю предварительно тип производства в зависимости от веса и количества деталей подлежащих изготовлении в течение года.
Таблица №4.1. Выбор типа производства по программе выпуска
Количество обрабатываемых деталей (изделий)
одного наименования и типоразмера в год
Таким образом определив предварительный тип производства разрабатываю для него технологический процесс с нормированием операций.
При среднесерийном типе производства используется универсальное и специализированное оборудование станки с ЧПУ и гибкие модули. В качестве оснастки используются сборно-разборные и специализированные наладочные приспособления.
В промышленности используются две основные формы организации производства: поточная и групповая. Первое используется в крупносерийном и массовом производстве. В нашем способе целесообразно применить групповую форму организации.
Группирование станочного оборудования и рабочих мест производится либо по видам технологической обработки изделий либо по виду технологических процессов. При втором способе группировки специализированные участки создаются по конструкторско-технологическому признаку.
В нашем случае воспользуемся группированием станочного оборудования по видам обработки. Он заключается в формировании участков станков одного наименования.
В результате группировки получается восемь участков: 2 токарно-черновых с ЧПУ 2 токарно-чистовых с ЧПУ фрезерный сверлильный внутришлифовальный круглошлифовальный.
Технологическое оборудование
Выбор модели станка прежде всего определяется его возможностью обеспечить точность размеров и форм а также качество поверхности изготовляемой детали. Если эти требования можно обеспечить обработкой на различных станках определенную модель выбирают из следующих соображений:
Соответствие основных размеров станка габаритам обрабатываемых деталей устанавливаемых по принятой схеме обработки;
Соответствие станка по производительности заданному масштабу производства;
Возможность работы на оптимальных режимах резания;
Соответствие станка по мощности;
Возможность механизации и автоматизации выполняемой обработки;
Наименьшая себестоимость обработки;
Реальная возможность приобретения станка;
Необходимость использования имеющихся станков.
Токарный станок с ЧПУ 16К20Ф3С32
Наибольший диаметр устанавливаемого изделия над станиной - 500 мм
Наибольший диаметр обрабатываемого изделия над суппортом - 220 мм
Высота резца устанавливаемого в резцедержателе – 25 мм
Наибольшая длина обработки 905 мм
Наибольшая длина устанавливаемого изделия 1000 мм
Внутренний конус в шпинделе по ГОСТ 13214-79 - МОРЗЕ БАТБ
Конец шпинделя фланцевого по ГОСТ 12593-72 – БК
Диаметр цилиндрического отверстия в шпинделе – 55 мм
Центр в пиноли с конусом по ГОСТ 13214-79 - МОРЗЕ БАТБ
Частота вращения шпинделя – 20-2240 обмин
Пределы частоты вращения шпинделя устанавливаемые вручную
I диапазон – 20-325 обмин
II диапазон – 63-900 обмин
III диапазон – 160-2240 обмин
Пределы программируемых подач
продольное – 001-40 ммоб
поперечное – 0005-20 ммоб
Максимальная скорость рабочей подачи
продольной – 2000 мммин
поперечной – 1000 мммин
Скорость быстрых ходов не менее
продольных – 7500 мммин
поперечных – 5000 мммин
Дискретность перемещений
поперечных – 0005 мм
Количество позиций поворотной головки – Б
Наибольший крутящий момент на шпинделе – 1000 Н*м
Предельные диаметры сверления
Габариты станка - 3250*1700*2145 мм
Масса станка – 3800 кг
Консольно-фрезерный станок 6Р82Г
Наибольшее перемещение стола мм
Наименьшее и наибольшее расстояние от оси шпинделя до рабочей поверхности стола – 30-450 мм;
Перемещение тола на одно деление лимба – 005 мм
Перемещение тола на один оборот лимба мм
продольное поперечное – 5
Число оборотов шпинделя – 1460 мин
Число оборотов подачи шпинделя – 1430 обмин
Вертикально-сверлильный станок 2Н125
Наибольший ход шпинделя – 200 мм
Расстояние от торца шпинделя до стола – 60-700 мм
до плиты – 690-1060 мм
Наибольшее перемещение сверлильной головки - 170 мм.
Перемещение за 1 оборот шпинделя 12246 мм
Наибольший ход стола - 270 мм
Количество скоростей шпинделя – 12
Частота вращения шпинделя – 45-2000 обмин.
Число подач шпинделя - 9.
Подача шпинделя - 01-16 ммоб.
Мощность эд главного привода - 22 кВт.
Внутришлифовальный 273К2В
Диаметры шлифуемых отверстий – 20-1000 мм
Наибольшая длина шлифования при наибольшем диаметре отверстия – 125 мм
Наибольший диаметр устанавливаемого изделия – 400 мм
Расстояние от оси шпинделя изделия до подошвы станины – 1200 мм
Наибольший диаметр устанавливаемого изделия в кожухе 250 мм
Наибольший угол поворота бабки изделия 45 град
Поперечное перемещение шлифовальной бабки
За 1 оборот маховика:
грубое (наладочное) - 25 мм
на одно деление лимба – 0001 мм
Величина поперечной подачи 0002; 0004; 0006 ммдв. ход
Число оборотов шпинделя изделия – 140-1000 обмин
Число оборотов внутришлифовальных шпинделей – 9000; 12000; 18000; 24000обмин
Число оборотов торцевого шпинделя - 5600 обмин
Наибольший ход стола - 450 мм
Перемещение стола за 1 оборот маховика – 19 мм
Размеры устанавливаемых внутришлифовальных кругов по ГОСТ 2424-75
диаметр – ПП20-80 мм
Круглошлифовальный 3У143МВ
Класс точности по ГОСТ 11654-84 - В
Наибольшая длина устанавливаемого изделия – 1400 мм
Наибольший диаметр шлифования – 400 мм
Наибольшая длина шлифования – 1400 мм
Высота центров над столом – 240 мм
Наибольшая масса устанавливаемого изделия
при незажатой пинали – 100 кг
при зажатой пинали – 500 кг
Наибольшая длина перемещения стола – 1395 мм
Пределы скоростей врезных подач – 001-45 мммин
Толчковая подача – 001 мм
Частота вращения изделия – 25-300 обмин
Наибольший диаметр устанавливаемого изделия в патроне – 250 мм
Диаметр шлифуемого изделия
Скорость перемещения стола от гидросистемы - 005- 5ммин
Шлифовальный круг по ГОСТ 2424-75 – ПП600*80*305
Частота вращения шпинделя шлифовальной бабки – 1590 обмин
Скорость резания - 50 мс
Величина быстрого подвода шлифовальной бабки - 50±2 мм
Время быстрого подвода шлифовальной бабки – 25 с
Расчёт операционных размеров
Расчет диаметральных размерных цепей
Расчёт линейных размерных цепей
Выбор оснастки является одним из важнейших задач при разработке технологического процесса механической обработки заготовки от правильного его выбора зависит производительность изготовления детали экономическое использование производственных площадей электроэнергии и в итоге себестоимости изделия.
Оборудование на проектируемом участке должно быть по возможности универсальным.
Используемые измерительный вспомогательный инструмент и приспособления:
Штангенциркуль ШЦ II-250-01 ГОСТ 166-80;
Калибр-пробка 8140-0001 H12 ГОСТ 14820-69;
Калибр-пробка 8140-0051 H12 ГОСТ 14821-69;
Калибр-скоба 8113-0311 ГОСТ 18364-73;
Калибр для контроля пазов;
Калибр-пробка 8133-0928 H14 ГОСТ 14810-69;
Калибр-пробка 8133-0913 H14 ГОСТ 14810-69;
Калибр-пробка 8140-0008 H9 ГОСТ 14820-69;
Калибр-пробка 8140-0058 H9ГОСТ 14821-69;
Калибр-скоба 8113-0219 h9 ГОСТ 18363-73.
Выбор режущего инструмента обуславливается материалом обрабатываемой детали твёрдостью конфигурацией видом обработки (черновая чистовая) универсальностью конструкцией детали выбором оборудования и по возможности из стандартного режущего инструмента.
Используемый режущий инструмент:
Резец подрезной 2112-0015 ВК8 ГОСТ18880-73;
Резец проходной отогнутый 2102-0029 ВК8 ГОСТ18877-73;
Резец расточной 2140-0058 ВК8 ГОСТ18882-73;
Резец проходной упорный 2101-0011 ВК8 ГОСТ18879-73;
Резец расточной 2141-0058 ВК8 ГОСТ18883-73;
Фреза дисковая 2241-0022 ВК8 ГОСТ 5348-69;
Сверло спиральное 2301-0046 ГОСТ 10903-77;
Сверло спиральное 2300-0181 ГОСТ 10902-77;
Круг шлифовальный по ГОСТ 2424-80.
Расчёт режимов механообработки.
Выполняемые переходы:
точить торец на длину 266 мм
точить наружную поверхность на длину 266 мм выдерживая диаметр 2418 мм;
расточить отверстие на длину 266 мм выдерживая диаметр 988 мм;
точить торец на длину 241 мм
точить наружную поверхность на длину 105мм выдерживая диаметр 1818 мм;
расточить отверстие на длину 161 мм выдерживая диаметр 120 мм;
точить торец на длину 229 мм
точить наружную поверхность на длину 229мм выдерживая диаметр 240 мм
расточить отверстие на длину 229 мм выдерживая диаметр 102 мм;
точить торец на длину 22мм
точить наружную поверхность на длину 10мм выдерживая диаметр 1808 мм
расточить отверстие на длину 16 мм выдерживая диаметр 124 мм;
расточить отверстие на длину 4 мм выдерживая диаметр 160 мм;
Приспособление: Трёх - кулачковый патрон.
Станок токарный модели 16К20Ф3С32
Выбор инструментального материала.
Для условий чернового точения чугуна используем твёрдый сплав Т5К10 для чистового – Т15К6
.6. Выбор геометрии режущего инструмента.
Рекомендуемую геометрию выбираем из табл. 1 стр. 211 [1]. Параметры запишем в итоговую таблицу 8.2.1.
Таблица 8.2.1. Основные параметры операции 010.
Выбор смазочно-охлаждающих технических средств (СОТЦ)
Детали из серого чугуна обрабатываются без СОЖ т.к. чугунная стружка вредно влияет на износ станков
Назначение глубины резания t.
Согласно операционным размерам и размерам заготовки определяем глубину резания и заносим в сводную табл. 8.2.1:
Назначение подачи S.
Считаем что станок располагает такими подачами. Полученные значения подач S заносим в табл. 8.2.1.
Выбор стойкости резца Т.
Согласно табл. 18 стр.227 [1] при обработке материалов 8 группы твердосплавным инструментом рекомендуются соответствующие для каждого перехода износ и стойкость инструмента. Их значения заносим в итоговую табл. 8.2.1.
Назначение скорости резания V.
Расчет частоты вращения заготовки n.
Частота определяется по известной зависимости:
где Dз - диаметр обрабатываемой поверхности заготовки.
Так как станок с ЧПУ имеет бесступенчатое регулирование то корректировку частот выполнять не обязательно.
Выбранные значения nст и соответствующее ей V заносим в табл. 8.2.1.
Расчёт основного времени t0.
Формулы для расчета t0 для различных видов обработки приведены на стр. 609 [3]. Для токарных переходов:
гдеL1 L2 - соответственно величины врезания и перебега резца мм;
Значения L1 и L2 приведены на табл. 2 стр.620 [3]. Значения t0 заносим в табл. 8.2.1.
Расчет силы резания Pz.
Рассчитаем значение Pz. Полученные значения занесём в табл. 8.2.1.
Расчет эффективной мощности резания.
Выполняется для сравнения эффективной мощности резания Nе с мощностью станка Nст. Расчёт выполняется по формуле на стр.271 [2].
Полученные значения и заносим в табл. 8.2.1.
фрезеровать паз размерами 26Х2.
Деталь базируется в цилиндрической оправке
В качестве оборудования выбран горизонтально-фрезерный станок 6Р82Г
Операции фрезерования выполняем за один ход т.е. .
Выбор материала режущей части инструмента.
Согласно табл. 14 стр. 57 [1] для фрезерования чугуна рекомендуется твердый сплав ВК6
Выбор конструкции и геометрии инструмента.
Согласно табл. 17 стр. 225 [1] и стр. 174 [2] выбираем конструкцию и геометрию дисковой фрезы с числом зубьев D=160 B=25мм
Согласно табл. 24 стр. 233 [1] при фрезеровании чугуна рекомендуется 5-10% раствор Аквол-10М.
Назначение глубины фрезерования t.
Дисковая фреза работает с глубиной резания t=2 мм.
Значения глубины резания заносим в сводную табл. 8.1.3.
Для дисковой фрезы согласно табл. 113стр. 305 [1] для сталей 8 группы и :
Выбор стойкости фрезы Т.
Рекомендуемые значения допустимого износа hз и стойкости Т фрезы выбираем из табл. 22 стр. 231 [1] и заносим в соответствующие графы табл. 8.1.3
Расчёт частот вращения инструмента n.
При фрезерной обработке:
где DФ - диаметр фрезы мм.
Расчетное значение n должно быть скорректировано по nст:
Рассчитаем фактическую скорость резания:
Выбранные значения ncт и V заносим в табл. 8.1.3.
Согласно с.613 [3] основное время для различных видов фрезерования определяется выражением:
Значения величин врезания L1 и перебега L2 приведены в табл. 6 стр. 622 [3].
В нашем случае согласно табл. 3.4 получаем:
На фрезерование одного паза
Значение t0 заносим в табл. 8.1.3.
Расчёт силы резания Рz.
Согласно стр. 282 [2]:
Выбирая значения постоянных и показателей степеней для различных видов фрезерования из табл.41 стр.291 [2] и выполняя вычисления получим:
Расчёт крутящего момента Мк.
Согласно стр. 270 [2]:
Расчёт мощности резания.
Полученные значения Рz МK и Ne заносятся в соответствующие графы табл. 8.1.3.
Таблица 8.1.3. Основные параметры фрезерной операции.
сверлить 6 отверстий диаметром 14 мм Н13 и ;
сверлить 4 отверстия диаметр 6 мм Н14 и ;
В качестве оборудования выбран вертикально-сверлильный одношпиндельный станок 2Н125.
Выбор числа ходов z при сверлении отверстия.
Согласно табл. 62 стр. 265 [1] отверстия диаметром 6 мм и 14мм в чугунной детали просверливаются за один ход т.е. .
Выбор длины участков L сверления между выводами свёрл.
Согласно табл. 63 стр. 265 [1] в сплошном материале 8 группы сверлом диаметром 78 мм можно сверлить отверстие на длину без его вывода для удаления стружки. Поскольку заданная длина сверления 52 > 312 то обработка выполняется в два этапа по 26 мм с выводом сверла.
Согласно табл. 63 стр. 265 [1] в сплошном материале 8 группы сверлом диаметром 2 мм можно сверлить отверстие на длину без его вывода для удаления стружки. Поскольку заданная длина сверления 142 > 10 то обработка выполняется в два этапа по 71 мм с выводом сверла.
Согласно табл. 5 стр. 42 [1] для обработки материалов 8 группы сверлением рекомендуется быстрорежущая сталь Р6М5
Выбор конструкции и геометрии осевого инструмента.
Согласно стр. 103 [1] выбираем стандартную конструкцию и геометрию осевых инструментов.
Согласно операционным размерам и параметрам заготовки определяем глубину резания результаты заносим в сводную табл. 8.3.1.
Таблица 8.3.1. Основные параметры операции осевой обработки.
Согласно стр.266 [1] условия сверления определяют 1-ю группу подач.
Выполним корректировку рассчитанной подачи по набору подач Sст станка. Рассчитанную подачу корректируем до станочных значений:
Полученное значение подачи заносим в табл. 8.3.1.
Выбор стойкости инструментов Т.
Рекомендуемые значения допустимого износа hз и стойкости Т осевых инструментов
выбираем соответственно из табл. 19 стр. 228 и табл. 20 стр. 229 [1] 5и заносим в сводную табл. 8.3.1.
Расчет частоты вращения инструмента n.
Для осевой обработки
где Dи - диаметр инструмента мм.
Расчетное значение n должно быть скорректировано по nст.
Выбранные значения ncт и соответствующие им V заносим в табл. 8.3.1.
Расчет основного времени t0.
Формула для расчета t0 при сверлении приведена на стр. 611 [3]:
Расчет осевого усилия Р0.
При сверлении согласно стр. 281 [2]:
Расчет крутящего момента Мк.
При сверлении согласно стр.277 [2]:
Согласно табл. 32 стр. 281 [2]:
Расчет мощности резания.
Согласно с.280 [2] эффективная мощность резания:
Полученные значения Р0 Mk и Ne заносим в табл. 8.3.1.
шлифовать диаметр 125мм H9 и ;
шлифовать диаметр 180 мм h9 и ;
Деталь зажимается в 3х кулачковом пневматическом патроне
Деталь устанавливается в центрах
В качестве оборудования выбран внутришлифовальный станок 273К2В
В качестве оборудования выбран круглошлифовальный станок 3У143МВ
Выбор шлифовального круга
КЗ9 25 СМ2-СА 6-7К D=100 В=13
КЗ9 25-40 С1-С2 5К D=100 В=13
Назначение припусков на шлифование h
Припуск на диаметр 2h=05
Припуск на торец h=02 припуск на диаметр 2h=04
Результаты заносим в сводную табл. 8.3.1.
Выбор скорости движения детали
Выбор скорости шлифовального круга
Назначение продольной подачи Sпр.
азначение поперечной подачи Sпп.
При Dд=125 Vд=35 Sпр=1105 Sпп=00093ммдв.х.
Нормирование операций
Расчет операционного времени по каждой операции.
где - вспомогательное время связанное с переходом
- количество переходов в операции
- дополнительное время
- дополнительное время на обслуживание рабочего места
- дополнительное время на отдых и личные надобности.
Расчет штучно-калькуляционного времени.
Станкоёмкость обработки годовой программы по каждой операции.
где - годовая программа выпуска шт.
Расчет потребного количества станков.
где - эффективный годовой фонд времени часа.
4 - количество рабочих дней в году
- количество часов в смену
Определение коэффициента загрузки.
Для групповой операции применяем линейную компоновку.
Штучно-калькуляционное
Годовая программа шт
Станкоёмкость обработки годовой программы штчас
Коэффициент загрузки
Список использованной литературы
«Прогрессивные режущие инструменты и режимы резания металлов» СправочникПод общей ред. В.И. Баранчикова. М.: Машиностроение 1990 г.
«Справочник технолога-машиностроителя». Под ред. А.Г. Косиловой и Р.К. Мещерякова. М.: Машиностроение 1985 г. Т1Т2.
Е.М. Коровин и В.Ю. Зыков. «Расчет режимов резания конструкционных материалов». Учебное пособие. Казань 2002 г.
Н.А. Дунин и В.Д. Толпегин. «Проектирование процессов механической обработки деталей авиадвигателей». КГТУ им. А.Н. Туполева 1989 г.
«Абразивная и алмазная обработка материалов». СправочникПод Ред. А.Н. Резникова. М.: Машиностроение 1977 г.
«Машиностроительные стали». Справочник. Под ред. В.Н.Журавлева и О.И.Николаевой. М.: Машиностроение 1990 г.
«Резание конструкционных материалов режущие инструменты и станки»Под общей ред. П.Г. Петрухи. М.: Машиностроение 1974 г.
«Обработка металлов резанием». Справочник технологаПод ред. Г.А. Монахова. М.: Машиностроение 1974 г.
А.А. Панов и др. «Обработка металлов резанием». М.: Машиностроение 1988 г.
«Технология машиностроения».Под общей ред. А.М. Дальского. М.: Издательства МГТУ им. Н.Э. Баумана 2001 г. Т1 Т2.
В.Д. Толпегин. «Типовые примеры назначение размеров технологических переходов операций механической обработки деталей». КГТУ им. А.Н. Туполева 1982 г.
«Режимы резания металлов». Под ред. Ю.В.Барановского М.: Машиностроение 1972 г.
Чуртеж детали 1.cdw

Чертеж Эскиз наладок.cdw

Рекомендуемые чертежи
- 24.01.2023
- 13.12.2022
Свободное скачивание на сегодня
- 24.01.2023