Технологический процесс изготовления детали - гнездо




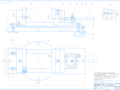
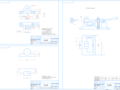
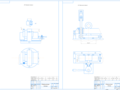
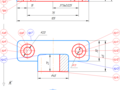
- Добавлен: 24.01.2023
- Размер: 1 MB
- Закачек: 1
Описание
Состав проекта
![]() |
![]() |
![]() |
![]() ![]() ![]() |
![]() ![]() ![]() |
![]() |
![]() ![]() ![]() |
![]() ![]() ![]() |
![]() ![]() ![]() |
![]() ![]() |
![]() ![]() ![]() |
![]() ![]() ![]() |
![]() ![]() ![]() |
![]() ![]() ![]() |
![]() ![]() |
![]() ![]() |
![]() ![]() |
![]() ![]() ![]() |
![]() ![]() ![]() |
![]() ![]() ![]() |
![]() ![]() ![]() ![]() |
![]() |
![]() |
![]() ![]() ![]() |
![]() ![]() ![]() |
![]() ![]() ![]() |
![]() ![]() ![]() |
![]() ![]() |
![]() ![]() |
![]() |
![]() |
![]() |
![]() |
![]() |
![]() |
![]() |
![]() |
![]() |
![]() ![]() ![]() |
![]() ![]() ![]() |
![]() ![]() ![]() |
![]() ![]() ![]() |
![]() ![]() |
![]() ![]() ![]() |
![]() ![]() |
![]() |
![]() ![]() ![]() ![]() |
![]() ![]() ![]() ![]() |
![]() ![]() ![]() ![]() |
![]() ![]() ![]() ![]() |
![]() ![]() ![]() ![]() |
![]() ![]() ![]() ![]() |
![]() ![]() ![]() ![]() |
![]() ![]() ![]() ![]() |
![]() ![]() ![]() ![]() |
![]() ![]() ![]() ![]() |
![]() ![]() ![]() ![]() |
![]() ![]() ![]() ![]() |
![]() ![]() ![]() ![]() |
![]() |
![]() ![]() ![]() ![]() |
![]() ![]() ![]() ![]() |
![]() ![]() ![]() ![]() |
![]() |
![]() ![]() ![]() |
![]() ![]() ![]() |
![]() ![]() ![]() |
![]() ![]() ![]() |
![]() ![]() ![]() |
![]() ![]() ![]() |
![]() ![]() ![]() |
![]() ![]() ![]() |
![]() ![]() ![]() |
![]() ![]() ![]() |
![]() ![]() ![]() |
![]() ![]() ![]() |
![]() ![]() ![]() |
![]() ![]() ![]() |
![]() ![]() ![]() |
![]() ![]() ![]() |
Дополнительная информация
02_Zadanie_02.doc
(дата и подпись студента)
06_Заключение.doc
При проектировании курсового проекта был приобретен опыт проектирования технологического процесса закреплен ранее пройденный теоретический материал.
Проблемы проектирования.
При проектировании возникли следующие сложности: при расчете размерных цепей припуски на обработку по разным осям были не одинаковыми - поэтому необходимо расширить допуски между размерами или применять другие схемы базирования.
01_Part_1_P.doc
Корпусные детали в большинстве случаев являются базовыми деталями на которые монтируют отдельные сборочные единицы и детали соединяемые между собой с требуемой точностью относительного положения. Корпусные детали должны обеспечить постоянство точности относительного положения деталей и механизмов как в статическом состоянии так и в процессе эксплуатации машин. В данном курсовом проекте рассматривается гнездо.
Классификация поверхностей подразумевает следующие их виды:
Основные базы - поверхности детали которые обеспечивают ее ориентацию относительно машины в целом (при помощи этих поверхностей деталь сопрягается с корпусами станинами и т.п.). Конструктивное исполнение этих поверхностей обычно предусматривает регулировку при сборке а следовательно их качество может быть не очень высоким. В моей детали это поверхности Mp6 Кo9 и Kp9 (No9 и Np9) Ko10 и Kp10 (No10 и Np10).
Вспомогательные базы - поверхности детали которые обеспечивают ориентацию присоединяемых деталей. В моей детали это поверхности Mp5 Mp2 и Mо2 и Моо2 Np2 и No2 и Nоо2 Kp8 и Ko8 (No8 и Np8) Kp11 и Ko11 (No11 и Np11). Исполнительные поверхности - поверхности детали выполняющие ее СН. В корпусных деталях ИП часто совпадают с ВБ. У меня это поверхности Мо3 и Mp3 No3 и Np3.
Свободные поверхности - поверхности не принимающие непосредственного участия в выполнении СН но обеспечивающие необходимую прочность жесткость внешний вид и габариты детали. В свою очередь СП подразделяются на обработанные поверхности Кр14 и необработанные поверхности Mp1 Мо1 Мр4 Kp7 Кp12 Кp13 Кp15 Np16 Np1 и No1). В большинстве случаев параметры СП зависит не от СН а от метода получения заготовки и последующей обработки.
Основными параметрами детали являются габаритные размеры - 708855 мм. Деталь получена отливкой в песчано-глинистые смеси. Деталь состоит из основания имеющего в высоту 17 мм; на нем находится цилиндр с отверстием для крепления вала. Материалом детали является КЧ 30-6.
1.2 Форма и материал.
В основании детали лежит прямоугольная призма по краям которой находятся крепежные отверстия. Перпендикулярно основанию по центру располагается цилиндр со сквозным отверстием. Деталь изготовлена из ковкого чугуна КЧ 30-6 ГОСТ 1412-85. Стандартные марки чугунов обозначаются буквами К-ковкий и Ч-чугун. После букв следует число обозначающее предел прочности при растяжении (кгсмм2). В данном случае sв=30 кГсмм2. Химический состав КЧ 30-6: содержание углерода 2.4-2.8% при этом до 0.9% углерода находится в химически связанном состоянии остальная часть углерода содержится в виде графита.
Отливки из ковкого чугуна (по ГОСТу 1215-59).
Содержание элементов в %
Где sв – временное сопротивление (предел прочности при растяжении)
sн – предел прочности при изгибе
НВ – твердость по Бриннелю.
Единая система конструкторской документации представляет собой совокупность правил простановки размеров. Линейные размеры составляют основную долю применяемых в технике числовых характеристик. В подавляющем большинстве случаев взаимозаменяемость по геометрическим параметрам составляет основную долю взаимозаменяемости. Эта геометрическая взаимозаменяемость достигается за счет соответствующих размеров и допусков. Из-за большего удельного веса линейных размеров и их роли в обеспечении взаимозаменяемости оказалось целесообразным самостоятельно регламентировать ряды линейных размеров приняв в качестве базы предпочтительные для них числа.
При выборе размеров рядам с более крупной градации и входящих в них размерам должно отдаваться предпочтение: ряд Ra5 следует предпочитать ряду Ra 10 ряд Ra10 - ряду Ra20 ряд Ra20 – ряду Ra40.
Численное значение допусков формы допусков расположения суммарных допусков формы и расположения поверхностей деталей машин должны применяться в соответствии с ГОСТом 24643-81.Для каждого вида допусков формы или расположения установлено 16 степеней точности.
Шероховатость поверхности является одной из основных геометрических характеристик качества поверхности детали и оказывает влияние на эксплуатационные показатели.
Требования к шероховатости поверхности должны устанавливаться исходя из функционального назначения поверхности для обеспечения заданного качества изделия. Требования к шероховатости поверхности не включают требований к дефектам поверхностей.
Основными параметрами по которым нормируют шероховатость являются Ra Rz tp (мкм и %).
Стандартам устанавливает следующие виды отклонения формы:
-отклонение от прямолинейности; Разновидностями его является отклонения от прямолинейности в плоскости отклонение от прямолинейности выпуклости вогнутости.
-отклонение от плоскостности;
-отклонение от цилиндричности.
Одним из факторов влияющих на характер технологических процессов является технологичность деталей. При разработке конструкции детали необходимо добиваться не только выполнения эксплуатационных требований но и также требований наиболее рационального и экономически обоснованного изготовления детали. Чем меньше трудоемкость и себестоимость изготовления детали тем более она технологична.
Виды и показатели технологичности конструкции приведены в ГОСТ 18831 а правила обработки конструкции изделия и перечень обязательных показателей технологичности в ГОСТ 14201.
Особое внимание необходимо уделять технологичности конструкции заготовки она должна иметь не только простоту изготовления самой детали но и упрощать процесс изготовления самих заготовок.
Анализ исходных графов позволяет выявить недостаточную и ошибочную информацию дополнить и исправит ее.
В связи с наличием избыточной информации – размером между поверхностями Mp3-Mp4-Mp5 убираем размер и оставляем размер с наиболее жестким допуском – размер между поверхностями Мp3-Mp5 (25-1).
В связи с оторванностью размера между комплексом поверхностей вводим недостающий размер 17±05 между поверхностью Np8 и осью Nо5 - также добавляем размеры связывающие комплекс поверхностей Nо4 No1 No6 и No3 с остальными поверхностями размерами: 0±02025 No1 с поверхностью Nо3; No4 и No6 с поверхностью No5- поверхность Nо3 связываем размером 29±025 с поверхностью Nо5-No7.
В связи с оторванностью размера между комплексом поверхностей вводим размеры связывающие комплекс поверхностей Kо4 Ko1 Ko6 и Ko3 с остальными поверхностями размерами: 0±02025 Ko1 с поверхностью Kо3; Ko4 с поверхностью Ko5 и Ko6 с поверхностью поверхность Kо3 связываем размером 30±03 с поверхностью Kо5.
По оси К имеются оторванные поверхности Ко5-Кр5 которые размером 14±0.5 связываем с поверхностью Кр8. Оторванные поверхности Ко2 и Кр8 связываем размером 44±1 с поверхностью Ко5.
После обнаружения недостающей и излишней информации переходим к исправлению ее. По соответствующим осям производим следующие изменения:
Мp1-Мр2 12±0.2 Мp1- Мр2 12±0.2(10) 14 ст.
Мp5-Mр1 55-0.74 Мp5-Мр1 55-0.74 (10) H14
Мр3-Мр5 25-1 Мр3-Мр5 25-1.0 (20)-t3
Мр5-Мp4 Мр5-Мp4 14-0.43 (20) 13 ст.
Ко5Ко7-Кр5Кр7 ±4.5+0.18 Ко5Ко7-Кр5Кр7 ±4.5+0.18 (20) h14
Ко4Ко6-Кр4Кр6 ±7.5+0.215 Ко4Ко6-Кр4Кр6 ±7.5+0.215 (40) h14
Ко1-Ко3 Ко1-Ко3 0±0.2175 (5) 15ст
Ко3-Кр3 ±17.5+0.0125Ко3-Кр3 ±17.5+0.0125 (80) H7
Ко4-Ко5 Ко4-Ко5 0±0.2025(5) 16ст
Ко1-Кр1 ±23+0.31 Ко1-Кр1 ±23+0.31 (80) H14
Ко2-Кр2 ±28.5±0.75 Ко2- Кр2 ±29±0.75(80) 3 ктл
Кp8-Кр9 85±1.5 Кp8-Кр9 88±1.5 (80) 3ктл
Кр8-Ко2 Кр8-Ко2 44±1 (80) 3 ктл
Кр8-Ко5 Кр8-Ко5 14±05 (80) –t3
No1-No3 No1-No3 0±0.2025 (5) 16 ст.
Nо5Nо7-Nр5Nр7 ±4.5+0.18 Nо5Nо7-Nр5Nр7 ±4.5+0.18 (20) h14
Nо4Nо6-Nр4Nр6 ±7.5+0.215 Nо4Nо6-Nр4Nр6 ±7.5+0.215 (40) h14
Nо3-Nр3 ±17.5+0.0125Nо3-Nр3 ±17.5+0.0125 (80) H7
Nо4-Nо5 Ко4-Ко5 0±0.2025(5) 16ст
Nо1-Nр1 ±23+0.31 Nо1-Nр1 ±23+0.31 (80) H14
Nо2-Nр2 ±28.5±0.75 Nо2- Nр2 ±29±0.75(80) 3 ктл
Nр8-Nо2 Nр8-Nо2 41±1 (80) 3 ктл
3 Технологичность детали.
Заготовку отливается из ковкого чугуна КЧ 30-6 он обладает хорошими литейными свойствами. Форма заготовки образована небольшим количеством простых поверхностей легко получаемых при обработке. Параметры поверхностей назначаются в зависимости от служебного назначения.
Отверстия на проход крепежных деталей подошвы станин корпусов лап - имеют шероховатость Rа=80.
Поверхности механически обработанных корпусных деталей с наибольшим размером до100мм Ra=25; с размерами св.100 до 400 мм Rа=20.
Поверхности заготовки выполненной по 2 классу точности литья имеют минимальные требования к шероховатости Ra=100мкм.
Технологичность конструкции отливок характеризуется условиями формовки заливки формы жидким металлом остывание выбивки и обрубки. На выполнение основных операций технологического процесса получения отливок влияют уклоны толщина стенки размерные соотношения и другие условия. Большее влияние на технологию последующей обработки отливок оказывает наличие в них отверстий. При массовом производстве в отливках обычно получают отверстия диаметром свыше 20 мм при серийном - диаметром свыше 30 мм а при единичном – диаметром свыше 50 мм.
При изготовлении отливки отверстие диаметром 35 мм проливается. Уступы шириной более 25 мм и выемки глубиной свыше 6 мм на мелких и средних отливках делают литыми. Если соотношение толщины стенок составляет 1:2 то переходные поверхности формируются в виде галтелей.
Состояние баз и обрабатываемых поверхностей отливок и условий их обработки зависят от способов очистки и обрубки. В технологический процесс изготовления отливок включается и контроль.
4.1 «Важнейшие требования»
Требованиями с помощью которых производится контроль детали являются:
-отклонение от перпендикулярности;
-отклонение от соосности;
-отклонение от параллельности;
Отклонение от параллельности плоскостей определяется как разность показаний измерительной головки в двух положениях на заданной длине нормируемых участков.
Допуски плоскостности прямолинейности и параллельности по относительной геометрической точности А В и С определяется как 60 40 и 25 % соответственно от допуска размера с округлением до ближайшего числа из таблицы.
Контроль производиться с помощью поверочной плиты на которую деталь устанавливается базовой поверхностью и измерительной головки перемещающейся параллельно плоскости плиты.
Выбор допуска перпендикулярности по таблицам в зависимости от точности линейных размеров и согласно СТ СЭВ 302-76 должны соблюдаться для всех прямых углов независимо от наличия ссылок на чертежах на неуказанные допуски.
Если с торцом связано несколько осевых размеров разной точности то неуказанный допуск торцевого биения выбирается по более точному квалитету. За базу к которой относится неуказанный допуск принимается ось поверхности имеющая большую длину при одинаковых длинах – поверхности с допуском диаметра по более точному квалитету при одинаковых квалитетах – поверхность с большим диаметром.
Контроль производиться уголками на «просвет» концевыми мерами длины или по измерительной головке.
Выбор допуска соосности при данной степени точности производиться по диаметру нормируемой поверхности или размеру между поверхностями образующими нормируемой симметричный элемент. Если база не указывается то допуск определяется по элементу с большим размером.
За базу к которой относится неуказанный допуск принимается ось поверхности имеющая большую длину при одинаковых длинах – поверхности с допуском имеющий более точный квалитет при одинаковых квалитетах – элемент с большим размером.
При изготовлении деталь подвергают линейные размеры отклонения от параллельности и перпендикулярности а также шероховатость поверхности. В зависимости от требуемой точности измерения для этих целей можно использовать измерительные столики центра поверочные линейки плиты специальные струны. Контроль линейных размеров осуществляется с помощью штангенциркулей нутрометров микрометров. Для измерения отклонений от круглости предназначены кругломеры. Кругломеры со специальными приспособлениями можно использовать для измерения концентричности поверхностей деталей типа втулки для измерения отклонений от плоскостности. Параметры шероховатости поверхности контролируют либо сравнением с образцами либо определением значений этих параметров с помощью специальных приборов.
Деталь контролируется на параллельности плоскостей с помощью индикаторов. Контроль осуществляется путем перемещения индикатора влево и вправо на контролируемой поверхности. Главное чтобы получаемое при этом отклонение было меньше допускаемого.
5.1 Возможные методы.
Для получения заготовки рассмотрим два возможных метода получения заготовок: литье в песчано-глинистые формы и литье в кокиль.
Область применения того или иного способа литья определяется объемом производства требованиям к геометрической точности и шероховатости поверхности отливки экономической целесообразности и других факторов.
Кокильное литье применяется в массовом и серийном производстве для изготовления отливок из чугуна стали и сплавов цветных металлов с толщиной стенок 3-100 мм и массой от нескольких десятков граммов до нескольких десятков килограммов.
При литье в кокиль сокращается расход формовочной и стержневой смесей. Затвердевание отливок происходит в условиях интенсивного отвода тепла от залитого металла что обеспечивает большую плотность металла и механические свойства чем у отливок полученных в песчано-глинистых формах. Кокильные отливки имеют высокую геометрическую точность размеров и малую шероховатость поверхности что снижает припуск на механическую обработку вдвое по сравнению с литьем в песчано-глинистые формы. Этот способ литья высокопроизводительный.
Недостатками кокильного литья являются: высокая трудоемкость изготовления кокилей их ограниченная стойкость трудность изготовления сложных по конфигурации отливок.
Литье в песчано-глинистые формы позволяет получать заготовки для массового производства. Основными достоинствами литья в песчано-глинистые формы является простота и относительная дешевизна получения заготовок. Методы автоматизации позволяют использовать данный метод для крупносерийного и массового производства. Автоматизация заливки литейных форм обеспечивает высокую точность дозировки металла облегчает труд заливщика и повышает производительность труда.
Отливка 2 класса точности обеспечивается ручной формовкой в песчано-глинистые формы а так же машинной формовкой по координатным плитам с незакрепленными моделями (см. рис. 2 34). Выбираем литью в песчано-глинистые формы как наиболее оптимальный способ получения отливок.
03_Part_2_24.doc
Размерный анализ технологического процесса по оси N:
Размерный анализ технологического процесса по оси K:
02_Part_2_.doc
Разрабатываемый маршрутный технологический процесс устанавливает последовательность обработки поверхности детали с целью получения требуемого качества поверхностей и наименьшей себестоимости.
Тех. требования ITRa
Синтез укрупненных операций.
Укрупненные операции обычно разбивают на более простые чтобы уменьшить трудоемкость переналадок связанную с необходимостью перенастраивать станок при переходе с обработки одной группы поверхностей к другой. Чаще всего это связано с тем что на выбранном типе оборудования невозможно обрабатывать все указанные в этом этапе поверхности с одной установки.
Назначение и характеристика
Получение заготовки и её термообработка
Mp6Mo3No3Mp3Np3Ko9Ko10
No9No10Kp9Kp10Np9Np10Ko8Ko11
No8No11Kp8Np8Np5Kp11Np11Kp14
3.1 Единый комплект технологических баз.
Базовые поверхности обрабатываются в самом начале технологического процесса. При их выборе необходимо учитывать основные принципы базирования: принцип совмещения баз и принцип постоянства баз. Базовые поверхности обеспечивают:
-отсутствие смещения деформации;
-простоту конструкции приспособлений с удобной установкой креплением и снятием обрабатываемой детали.
Базирование – процесс определения поверхностей ОП от которых следует настраивать формообразующий элемент для получения требуемой точности размера.
Разработка единого комплекта технологических баз ЕКТБ разрабатывается с целью упрощения процессов проектирования ТТТ и оснастки.
ЕКТБ обеспечивает ориентацию ОП относительно всех координатных плоскостей. При разработке ЕКТБ применяются единые правила:
- элементом ЕКТБ чаще всего становится поверхность с большим числом размерных связей.
- элементами ЕКТБ являются обработанные поверхности;
- следует учитывать наиболее жесткие абсолютные и средние требования предъявляемые к размерным связям поверхности ОП;
-следует учитывать возможность использования поверхностей в качестве того или иного элементарного типа баз;
В качестве установочной базы выбираем Mp6 как наибольшую обработанная. В качестве направляющей выбираем Ко9 Ко10 т.к. она обработана имеет 2 связи и достаточно жесткие требования. В качестве опорной выбираем Kо5.
3.2 Базирование на первых операциях.
Целью первой операции является обеспечение точности размерной связи между обрабатываемыми и необрабатываемыми поверхностями а также – получение баз для дальнейших операций.
3.3 Дифференциация операций
Схемы базирования для каждой операции с указанием наименования и номера операции.
0_СОДЕРЖАНИЕСТР.doc
1.2 Форма и материал
4.1 Важнейшие требования
5.1 Возможные методы получения заготовки
Технологический процесс
3.1. Единый комплект технологических баз
3.2. Базирование на первых операциях
3.3. Дифференциация операций
4 . Размерный анализ
6. Выбор оборудования
1. Служебное назначение
2. Разработка конструкции
04_Part_2_25.doc
Глубиной резания t называется расстояние между обрабатываемой и обработанной поверхностями заготовки измеренное перпендикулярно к последней.
Подачей s называется путь режущей кромки инструмента относительно заготовки в направлении движения подачи за один оборот либо один ход заготовки или инструмента.
Скорость резания v – расстояние пройденное точкой режущей кромки инструмента относительно заготовки в единицу времени.
Расчет режимов резания для окончательной обработки поверхности будем производить по справочным материалам.
Исходные данные: обрабатываемая поверхность основания
Вид обработки: черновое фрезерование
Глубина резания t=168 мм.
Материал режущей кромки РK8
проведем расчет длины рабочего хода по формуле
где Lрез- длина обрабатываемой поверхности 105 мм.
L1- длина подвода и врезания
L2- длина перебега инструмента L1+L2=20 мм.
Тогда Lрх=105+20=125мм.
определим рекомендуемую подачу на зуб. Подача равна Sz=03 ммзуб
определение стойкости инструмента Tp=KФλ где λ- коэффициент времени резания
λ=Lрез Lрх =105125=084
стойкость фрезы Тр=180 мин
расчет скорости резания частоты вращения и минутной подачи
скорость резания Vтабл=110 ммин
Тогда n= 1000*110 *80=437898 мин-1
Принимаем n=400 мин-1
Тогда V=80**4001000=10048 мм.
Минутную подачу определяем по формуле Sм=Sзуб*Zn*n=03*10*400=1200 мммин.
Принимаем Sм=1120 мммин.
Расчет основного времени tм=LрхSм=1251120=011 мин
Аналогично проводим выбор режимов резания на основные поверхности и переходы
Полученные данные заносим в таблицу:
Номер и наименование
6 Выбор оборудования
Для выбора оборудования оснастки и инструмента пользуемся справочной литературой. Исходными данными влияющими на выбор является тип производства и разработанный технологический процесс.
Выбор средств технологического оснащения производится с учетом:
-точность обрабатываемой поверхности;
-расположение обрабатываемой поверхности относительно технологических баз;
-габаритные размеры и масса заготовки;
-производительность операции;
-возможности группирования операций;
Результаты приведены в таблице
Наименование операции
Наименование и модель станка
Вертикально-фрезерный модели 6Р12
Тиски с эксцентриком
Вертикально-сверлильный
Сверло спиральное ГОСТ 10902-75
Горизонтально-расточной модели 261
Резец расточной ГОСТ 9795-73
Вертикально-фрезерный модели 6Р10
Горизонтально-расточной 262Г
00_Vvedenie_p.doc
–ознакомиться с наиболее общими методами формообразования;
–изучить методы расчета достижимой точности размерных параметров деталей машин;
–изучить теорию базирования;
–изучить формальные методы проектирования технологических процессов.
Целью курсового проектирования является закрепление и обобщение знаний полученных студентами во время лекционных и практических занятий. Курсовое проектирование должно научить студента пользоваться справочной литературой ГОСТами таблицами умело сочетая справочные данные с теоретическими знаниями полученных в процессе изучения курса.
Схема проектирования процесса имеет вид:
Размерный анализ чертежа детали.
Определение типа производства.
Определение методов получения заготовки.
Выбор методов обработки.
Разработка схем базирования.
Синтез маршрута обработки
Синтез структур операций.
Размерный анализ техпроцесса.
Проектирование приспособлений.
Выбор инструментов и режимов резания.
Расчет норм резания.
Расчет технологической себестоимости.
__Tit.doc
УО “Витебский государственный технологический университет”
Контрольная работа №2
По предмету: «Технология машиностроения»
На тему: «Разработка технологического процесса изготовления детали Гнездо №32»
На тему: «Разработка технологического процесса изготовления детали Стойка №37»
07_karti.doc
Оборуд. устройство ЧПУ
Обозначение программы
5 Вертикально-фрезерная
Вертикально-фрезерный 6Р12
Установить деталь в приспособлении закрепить
Приспособление тиски эксцентриковые с двумя неподвижными губками
Фрезеровать поверхность выдерживая размер 1
Фреза торцевая ВК8 100 ГОСТ 24359-80
Открепить снять детальуложить в тару
0 Вертикально-фрезерная
Фреза концевая ВК6 100 ГОСТ 24359-80
Снять детальуложить в тару
Фреза концевая ВК4 20 ГОСТ 20536-75
0 Вертикально-сверлильная
Вертикально-сверлильный 2Н150
Сверлить отверстие выдерживая размеры 1234
Сверлоь спиральное ГОСТ 10993-77
Горизонтально-расточной 261
Растачивать выдерживая размеры 1234
Резец расточной ГОСТ9795-73
Фреза концевая ВК4 63 ГОСТ 20-035-476-76
Фреза концевая ВК4 100 ГОСТ 20536-75
Фрезеровать поверхность выдерживая размеры 1234
Фреза концевая ВК4 100 ГОСТ 22085
5 Вертикально-сверлильная
Сверлить отверстие выдерживая размеры 12
Горизонтально-расточной 262Г
05_part_3_prisp.doc
Приспособление применяется для увеличения производительности труда обеспечения стабильности качества уменьшения трудоёмкости работы. По-своему назначению разрабатываемое приспособление является специальным. Собирают его из нормализованных и стандартизированных узлов и деталей. Достоинством приспособления является несложность сборки и экономичность оснащения. Базой на этой операции является предварительно обработанные поверхности. В качестве приспособления используют тиски с эксцентриковым зажимом.
2 Разработка конструкции
Прототипом приспособления являются тиски эксцентриковые с двумя подвижными губками ГОСТ 4045-75. Опоры постоянные со сферической головкой по ГОСТ 13441-68 для необработанных поверхностей и с насеченной головкой по ГОСТ 13442-68 для обработанных поверхностей. Устройство настройки инструмента: принимаем установ высотный ГОСТ 8925-68. Механизм зажима эксцентриковый. Приспособление оснащено специальными пазами для установки на станке.
Опора постоянная со сферической головкой
Опора постоянная с насеченной головкой
Вертикально-фрезерный станок 6Р12
Эскиз приспособления
Расчет приспособления на точность осуществляется по теории размерных цепей. Схема размерной цепи изображена на рисунке 3.8.
Следовательно условие выполнено.
Размерная схема расчёта приспособления на точность
Требуемое усилие зажима.
Величина сил зажима определяется из условия равновесия сил возникающих в процессе обработки сил зажима и реакций опор. Причем основными силами процесса являются силы резания. Определяется требуемая сила зажима с учетом коэффициента запаса К предусматривающего возможное увеличение силы резания вследствие затупления режущего инструмента неоднородности обрабатываемого материала неравномерности припуска и.т.д.
К=К0× К1× К2× К3× К4× К5;
где: К0 = 15 – гарантированный коэффициент запаса для всех случаев;
К1 – коэффициент учитывающий состояние поверхности заготовок К1=12 (чистовая заготовка);
К2 – коэффициент учитывающий увеличение сил резания от прогрессирующего затупления инструмента К2 = 12;
К3 – коэффициент учитывающий увеличение силы резания при прерывистом резании К3 = 10;
К4 – коэффициент учитывающий постоянство силы зажима развиваемой силовым приводом приспособления К4=13;
К5 – коэффициент учитываемый только при наличии крутящих моментов стремящихся повернуть обрабатываемую деталь К5=10.
К = 15×12×12×10×13×10 = 28.
Рассчитаем требуемое усилие зажима:
Nрез= (Е*V*t*Z)1000*К1*К2=06*(90*35*5)1000*11*10=104 Квт
Р= NрезV=1000*1.0490=11.5 Н
где: Р1 = 115 Н; Р2=03*Р2=346 Н; – силы резания;
f = 025 – коэффициент трения на рабочих поверхностях зажимов (для гладких поверхностей);
К – коэффициент запаса;
a = 80 мм; b=30мм; Z=23мм; Z0=40мм
Возможное усилие зажима.
Усилие зажима круговым эксцентриком определяется по формуле:
где: Q=15 кгс – сила приложенная к рукоятке эксцентрика;
D=32 мм – диметр кругового эксцентрика;
p=10 мм – расстояние от оси вращения эксцентрика до точки соприкосновения его с изделием;
j = 57о – угол трения между изделием и эксцентриком;
j1 = 57о – угол трения на оси эксцентрика;
a - угол подъема кривой эксцентрика.
где l1 = 70 мм – длина рукоятки.
l = 70+0.5×32 = 86 мм.
Определяем угол подъема кривой эксцентрика a.
Допускаемый угол поворота эксцентрика g = 45о.
где: e=1.7 мм – эксцентриситет;
b = 90о- g = 90о – 45о = 45о.
Рисунок 39 – Схема для силового расчета приспособления.
00i_Shema.cdw

kar_055_p_.frw

kar_050_p_.frw

kar_020+.frw

kar_025+.frw

kar_045a_p_.frw

kar_015+.frw

kar_040+.frw

kar_045b_p_.frw

kar_045+.frw

045_p_.frw

040_p_.frw

005_p_.frw

055_p_.frw

015_p_.frw

035_p_.frw

020_p_.frw

045a_p_.frw

030_p_.frw

025_p_.frw

010_p_.frw

050_p_.frw

045b_p_.frw

03_List_Prisposob.cdw

Приспособление красить эмалью НЦ-243 черного цвета
Для смазки приспособления в период хранения солидол
синтетический ГОСТ 4366-76ъ
Смену установленных элементов производить раз в 6 месяцев
Неуказанные предельные отклонения H14
Размеры для справок*
02_list_.cdw

01_list_moy.cdw

Формовочные уклоны по
Литейные радиусы 2-3 мм
Неуказанные предельные отклонения
КЧ 30-6 ГОСТ 1412-85
5 Расточная операция
06_M_ISPR.CDW

01_pr_01_Ishodniy_eskiz_!sd.cdW

09_m_mak_.cdw

03_K_ishGRAF.CDW

00_01_Zadanie.CDW

12_M_proizvGRAF.CDW

10_k_mak_.cdw

13_K_proizvGRAF.CDW

02_M_ishGRAF.CDW

14_Nv_proizvGRAF.CDW

04_N_ishGRAF.CDW

11_n_mak.cdw

07_K_ISPR.CDW

01_pr_01_Ishodniy_sd.cdw

08_N_ISPR.CDW

05_ISPRAVLENY_ESKIZ_2_!.CDW

Рекомендуемые чертежи
- 24.01.2023
- 13.12.2022
Свободное скачивание на сегодня
- 24.01.2023