Технологический процесс изготовления червячного колеса




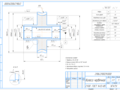
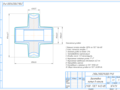
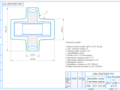
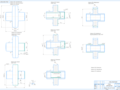
- Добавлен: 24.01.2023
- Размер: 1 MB
- Закачек: 4
Описание
Состав проекта
![]() |
![]() |
![]() ![]() ![]() |
![]() |
![]() |
![]() ![]() ![]() |
![]() ![]() ![]() |
![]() |
![]() ![]() ![]() ![]() |
![]() ![]() ![]() ![]() |
![]() ![]() ![]() ![]() |
![]() ![]() ![]() ![]() |
Дополнительная информация
СОДЕРЖАНИЕ.doc
химического состава материала детали и его механических свойств. 4
Анализ ее технологичности. 7
Анализ и обоснование выбора способа получения заготовки. 12
1 Выбор заготовки литье в земляные формы 12
2 Литье в металлические формы (кокиль) 14
Технико-экономическое обоснование способа получения
заготовки (общая методика заготовка из проката или листа;
прогрессивная заготовка выбранная в проекте). 17
Разработка маршрутного технологического процесса и его
1 Разработка плана обработки и его описание. 20
Разработка операционного технологического процесса и его обоснование: 22
1 Расчет операционных технологических размеров (при помощи комплекса расчета операционных размеров и отклонений расположения
APROPOS 1995-2003 редакция 7.71 УГАТУ каф. ТиТМ лаб. САПР ТП). 22
2 Расчет режимов обработки; 22
3 Нормирование операций технологического процесса (расчет
основного вспомогательного штучного и штучно-калькуляцион-
Список используемой литературы. 39
Содержание графической части:
Пояснительная записка.doc
Целью данного курсового проекта является ознакомление непосредственно с процессом производства а также оценка и сравнение его эффективности не только с экономической но и с технологической точек зрения.
В данной работе разработана операционная технология механической обработки детали «Колесо червячное» для серийного производства. На начальной стадии разработки техпроцесса проектируется заготовка отвечающая требованиям данного вида производства. Размеры заготовки определяются предварительно по виду изготовления в данном случае литье в кокиль. Далее разрабатывается технологический процесс который должен обеспечивать выполнение всех требований чертежа. Также в проекте производится анализ технологичности конструкции детали по качественным и количественным характеристикам. Производится подробный расчет режимов резания и норм времени на три операции. На все остальные операции режимы резания и расчет норм времени назначается табличным методом по справочникам.
Производство изделия его сущность и методы оказывают наиболее весомое влияние на технологические эксплуатационные эргономические и конечно функциональные характеристики этой продукции а следовательно на его себестоимость от которой в прямой зависимости находятся цена изделия спрос на него со стороны потребителей объемы продаж прибыль от реализации а следовательно все экономические показатели которые и определяют финансовую устойчивость предприятия его рентабельность долю рынка и т.д. Таким образом то как изготовляется продукция оказывает влияние на весь жизненный цикл товара.
Итак проектирование технологического процесса является важнейшим этапом производства продукции который влияет на весь жизненный цикл товара и способен стать определяющим при принятии решения о производстве того или иного продукта.
Назначение детали описание работы детали в узле анализ химического состава материала детали и его механических свойств.
Червячная передача — это зубчато-винтовая передача элементы которой скользят относительно друг друга.
Состоит передача из червяка и червячного колеса. Ведущим звеном обычно является червяк. Рис. 1.
Червячные передачи применяют при необходимости передачи движения между перекрещивающимися (как правило взаимно перпендикулярными) валами. При вращении червяка (он является ведущим) его витки плавно входят в зацепление с зубьями колеса (ведомым) и приводят его во вращение. Червячные передачи используют в станках автомобилях подъемно-транспортных и других машинах.
Сравнительно низкий КПД.
Большие потери на трение (тепловыделение).
Повышенный износ и склонность к заеданию.
Повышенные требования к точности сборки необходимость регулировки
Большое передаточное отношение в одной паре.
Изготовление и червяка и колеса из твердых материалов не обеспечивает достаточной износостойкости и сопротивления заеданию. Поэтому одну из деталей передачи выполняют из антифрикционного материала хорошо сопротивляющегося заеданию. Для червяка характерны относительно малый диаметр и значительное расстояние между опорами его жесткость и прочность обеспечивают за счет изготовления его из стали. Поскольку при приработке на червяк возлагается роль формообразующего элемента его прочность и твердость поверхности должны быть выше соответствующих свойств колеса.
Наиболее применяемый материал червяка – сталь 18ХГТ твердость поверхности после цементации и закалки 56 63 HRC. Используют также стали 40Х 40ХН 35ХГСА с поверхностной закалкой до твердости 45 55HRCэ. Во всех этих случаях необходимы шлифование и полирование червяка. Применение азотируемых сталей 38Х2МЮА 38Х2Ю позволяет исключить шлифование червяка.
Червячное колесо обычно выполняют составным: венец – из антифрикционных относительно дорогих материалов центр – из стали при небольших нагрузках – из чугуна.
Так как это учебная работа и задание было обговорено с преподавателем мы не будем уделять конструктивным особенностям червячного колеса. Поэтому колесо будет выполнено цельным.
Далее в нашей курсовой работе все данные и расчеты будут касаться только червячного колеса.
Допускается изготовление червячных колес из серого чугуна марок СЧ 20 СЧ 25 и др. при скорости скольжения до 2 мс. Лит 8
Материал для колеса выбираем СЧ 30 по ГОСТ 1412-85. ЧУГУН С ПЛАСТИНЧАТЫМ ГРАФИТОМ ДЛЯ ОТЛИВОК.
Ниже приведена таблица 1 в которой отображаются общие сведения для стали СЧ 30.
Таблица 1. Физические свойства чугуна с пластинчатым графитом
Модуль упругости при растяжении Е×10-2 МПа
Удельная теплоемкость при температуре от 20 до 200°С G Дж(кг×К)
Коэффициент линейного расширения при температуре от 20 до 200°С a 1°С
Теплопроводность при 20°С l Вт(м×К)
Таблица 2. Химический состав серого чугуна СЧ30.
Массовая доля элементов %
Примечание. Допускается низкое легирование чугуна различными элементами (хромом никелем медью фосфором и др.).
Анализ ее технологичности.
В соответствии с ГОСТ 14.205-83 технологичность – это совокупность свойств конструкции изделия определяющих ее приспособленность к достижению оптимальных затрат при производстве эксплуатации и ремонте при заданных показателях качества объема выпуска и условиях выполнения работ.
Производственная технологичность конструкции детали – это степень ее соответствия требованиям наиболее производительного и экономичного изготовления. Чем меньше трудоемкость и себестоимость изготовления тем более технологичной является конструкция детали.
Оценка технологичности конструкции бывает двух видов: качественная и количественная.
Качественная оценка технологичности является предварительной обобщенной и характеризуется показаниями: лучше – хуже’ технологично-нетехнологично’ и т.д. Технологичной при качественной оценке следует считать такую геометрическую конфигурацию детали и отдельных ее элементов при которой учтены возможности минимального расхода материала и использование наиболее производительных и экономичных для определенного типа производства методов изготовления.
Количественная оценка технологичности выражается показателем численное значение которого характеризует степень удовлетворения требований к технологичности. Согласно ГОСТ 14.202-73 номенклатура показателей технологичности изделия содержит четыре основных и 31 дополнительный показатель.
К основным показателям относятся:
- коэффициент унификации конструктивных элементов КУЭ;
- коэффициент точности Кт;
- коэффициент шероховатости Кш;
- коэффициент использования материалов Ким.
Проведем оценку конструкции детали на ТКИ по ГОСТ 14.201-204 – 83.
Качественная оценка.
Деталь состоит из стандартных и унифицированных конструктивных элементов: отверстий фасок канавок и т.д.
Деталь имеет точность и шероховатость которые можно получить стандартными унифицированными инструментами.
Деталь простой формы конструкция которой позволяет свободный подвод режущего инструмента при обработке.
Материал детали СЧ 30 по ГОСТ 1412 – 85 хорошо обрабатывается резанием и имеет хорошие литейные свойства например текучесть.
По вышеизложенным результатам можно считать деталь технологичной.
Количественная оценка.
Так как в задании при курсовом проектировании используется одна деталь то в качестве количественных показателей технологичности могут рассматриваться: масса детали; коэффициент использования материала (КИМ); коэффициент точности обработки; коэффициент шероховатости поверхностей; уровень технологичности конструкции по технологической себестоимости.
Масса детали составляет 337 кг. что говорит о небольших габаритных размерах.
Коэффициент использования материала
Для исходной заготовки литье в кокиль КИМ составляет 057.
В нашем случае неплохой показатель но в современном машиностроении этот показатель нужно стремиться доводить как можно ближе к 1.
Коэффициент точности обработки Кт.
Расчетная формула коэффициента точности имеет вид
где Тср – средний квалитет точности обработки поверхности изделия определяется по формуле:
Тср – среднее значение этого параметра;
ni – число размеров или поверхностей для каждого квалитета.
Подставив эти данные в вышестоящие формулы получим коэффициент точности КТ = 0913.
ВЫВОД: коэффициент точности удовлетворяет нормативному т.к. Кт = 0913 > 085 (Кт.норм ≥ 085).
Коэффициент шероховатости поверхностей Кш.
Рассчитываем коэффициент шероховатости для колеса. Коэффициент шероховатости Кш определяется по ГОСТ 14202 – 73 и принимается в пределах от 0 до 1.
Raср – среднее значение;
ni – число размеров или поверхностей для каждого значения шероховатости.
Подставив эти данные в вышестоящие формулы получим коэффициент шероховатости Кш = 0199.
ВЫВОД: коэффициент точности удовлетворяет нормативному (Кш.норм 027) т.к. Кш > Кш.норм.
Таким образом чертеж детали крышка не подвергается изменениям и пересмотру. В этом случае уровень технологичности конструкции по этим показателям равен 1. Это решение принято исходя из анализа технологичности конструкции по точности обработки и коэффициенту шероховатости.
Уровень технологичности конструкции по технологической себестоимости.
Деталь – колесо червячное (рис 2) – изготовлена литьем в металлические формы из серого чугуна СЧ 30 и после проходит термическую обработку что имеет большое значение в отношении короблений возможных в процессе литья. Зубчатые колеса в плане обработки можно считать не совсем технологичны так как нарезание зубьев производиться малопроизводительными методами. А применение специнструмента ведет к удорожанию детали. Поэтому при проектировании таких деталей нужно учитывать повышения производительности зубообработки.
Конструкция колеса предусматривает наличие ступиц с двух сторон что не добавляет технологичности детали (наиболее технологичными являются зубчатые колеса плоской формы без выступающих ступиц) и это в свою очередь не позволяет обрабатывать одновременно несколько колес что ведет к увеличению количества станков. Этот факт явно не в пользу технологичности колеса.
Симметричное расположение перемычки между ступицей и венцом положительно сказывается на термообработке так как не приводит к искажению формы колеса.
В целом деталь можно признать достаточно технологичной потому что позволяет применять высокопроизводительные режимы механической обработки. Простая по конструкции и имеет простые базовые поверхности.
Анализ и обоснование выбора способа получения заготовки.
При выборе метода получения заготовки нужно придерживаться таких вариантов при которых изготовление детали было бы целесообразно и экономически выгодно т. е. уменьшить время на механическую обработку а так же снижение материальных затрат.
Оптимальный метод получения заготовки выбирают анализируя ряд фактов:
-технические требования на ее изготовление
-объем и серийность выпуска
-форму поверхностей и размеры детали.
Все эти показатели сводятся к одному получение детали с наименьшей себестоимостью.
Далее мы подробнее рассмотрим на примере изготовления детали «колесо червячное» выбор заготовок.
В машиностроении применяют заготовки полученные различными способами: прокат литье поковки.
В нашем случае мы рассмотрим два варианта – 1 литье в земляные формы 2 – литье в кокиль. Нашей задачей будет выбрать такую заготовку которая удовлетворяла тем требованиям которые мы описывали выше.
1 Выбор заготовки литье в земляные формы
Итак рассмотрим 1 вариант заготовки литье в земляные формы чугун СЧ30 по ГОСТ 1412-85. Рисунок 3.
Общие исходные данные:
Материал детали чугун СЧ30.
Масса детали МД = 337 кг.
Масса заготовки МЗ = 804 кг.
Годовая программа N = 2000шт.
Производство серийное.
Рисунок 3 литье в земляные формы.
Определим коэффициент использования материала (КИМ)
При таком варианте видно что КИМ = 043 не удовлетворяет требованиям при которых должно достигаться условие КИМ ³ 06.
2 Выбор заготовки литье в кокиль
В машиностроении применяются различные способы литья заготовок. Поэтому при выборе получения заготовки необходимо оценивать все преимущества и недостатки каждого рассматриваемого сопоставляемого варианта. Без такой оценки невозможно принять правильное решение об использовании того или иного способа невозможен выбор оптимального варианта.
Для сравнения экономичности применения различных способов литья также следует учитывать трудоемкость которая зависит от массы и сложности отливок технических требований предъявляемых к отливкам характера производства и его организации а также от степени механизации и автоматизации технологического процесса. С увеличением объема производства трудоемкость и себестоимость литья уменьшаются. В табл. 5 приведена средняя себестоимость 1 т литья в зависимости от способа.
Как видно из таблицы самый оптимальный вариант литье в металлические формы (кокиль). Его и выбираем для изготовления заготовки.
2 Литье в металлические формы (кокиль)
Является одним из прогрессивных способов получения отливок из чугуна стали и цветных сплавов массой от нескольких граммов до десятков тонн.
Сущность процесса заключается в многократном применении металлической формы имеющей гораздо более высокую стойкость чем обычная песчано-глинистая. Полости в отливке выполняют при помощи металлических или песчаных стержней которые извлекают из отливки после ее затвердевания и охлаждения до заданной температуры. Экономическая целесообразность литья в металлические формы во многом зависит от стойкости форм их долговечности и стоимости.
Итак рассмотрим 2 вариант заготовки литье в кокиль чугун СЧ30 по ГОСТ 1412-85. Рисунок 4.
Масса заготовки МЗ = 59 кг.
При таком варианте видно что КИМ = 057 не удовлетворяет требованиям при которых должно достигаться условие КИМ ³ 06 но в нашем случае это не плохой показатель.
Рисунок 5 литье в кокиль.
Технико-экономическое обоснование способа получения заготовки
Метод получения заготовки выбирают учитывая ряд факторов: материал детали технические требования на ее изготовление объем и серийность выпуска форму поверхностей и размеры деталей. Оптимальным считается метод получения заготовки обеспечивающий технологичность и минимальную себестоимость.
Для выбора оптимальной заготовки выполнен сравнительный анализ двух типов заготовок: литье в кокиль и литье в песчаные формы.
Определение коэффициента использования материала и себестоимости заготовки - литье в кокиль.
Себестоимость заготовки:
Qз – масса заготовки кг;
Qд – масса детали кг
Sотх – стоимость одной тонны стружки (Sотх = 248 руб.);
КТ – коэф-т учитывающий класс точности заготовки (КТ = 105)
КС – коэф-т учитывающий степень сложности заготовки (КС= 083);
КМ – коэф-т учитывающий материал заготовки (КМ = 104);
КВ – коэф-т учитывающий массу заготовки (КВ = 091);
КП – коэф-т учитывающий тип производства (КП = 1).
Масса детали и заготовки найдены в системе твердотельного проектирования КОМПАС 3D V9.
Данные необходимые для сравнительного анализа сведены в таблицу.
Определение коэффициента использования материала и себестоимости заготовки – литье в земляные формы.
Учитывая параметры детали подобран по:
Qд – массса детали кг
Sотх – стоимость одной тонны стружки ( Sотх = 248 руб. );
КС – коэф-т учитывающий степень сложности заготовки (КС = 1);
КП – коэф-т учитывающий тип производства (КП = 1);
Данные необходимые для сравнительного анализа сведены в таблицу 6.
Таблица 6. Сравнение типов заготовок
Наименование показателей
Литье в песчаные формы
Стоимость 1т. заготовок руб.
Стоимость 1т. стружки руб.
Себестоимость одной заготовки руб.
С индексирующим коэффициентом
По таблице видно что заготовка – литье в кокиль является оптимальной для производства детали «колесо червячное» так как она легче и дешевле литья в земляные формы а коэффициент использования материала на порядок выше чем у литья в земляные формы.
Разработка маршрутного технологического процесса и его обоснование
Маршрутную технологию разрабатывают выбирая технологические базы и схемы базирования для всего технологического процесса.
Всю механическую обработку распределяют по операциям и таким образом выявляют последовательность выполнения операций и их число для каждой операции выбирают оборудование и определяют конструктивную схему приспособления.
При разработке технологического процесса руководствуются следующими принципами:
- в первую очередь обрабатывают те поверхности которые являются базовыми при дальнейшей обработке;
- после этого обрабатывают поверхности с наибольшим припуском;
- далее выполняют обработку поверхностей снятие металла с которых в наименьшей степени влияет на жесткость заготовки;
- в начало технологического процесса следует относить те операции на которых можно ожидать появление брака из-за скрытых дефектов металла;
- поверхности обработка которых связана с точностью и допусками относительного расположения поверхностей изготавливают при одной установке;
- совмещение черновой (предварительной) и чистовой (окончательной) обработок в одной операции и на одном и том же оборудовании нежелательно – такое совмещение допускается при обработке жестких заготовок с небольшими припусками;
Разработка плана обработки и его описание
Литейное оборудование
Продолжение таблицы 7
Дробеструйная установка
Штангенциркуль ШЦ-I-125-005 ГОСТ 166 – 89 микрометр.
Токарно-винторезный станок 16К20
Резец 2112-0035 ГОСТ 18871 – 73 резец 2102-0005 ГОСТ 18877 – 73.
Резец 2112-0035 ГОСТ 18871 – 73 резец 2102-0005 ГОСТ 18877 – 73 резец 2130-0255 ГОСТ 18884 – 73.
(Включает в себя центрование сверление растачивание)
Резец 2112-0035 ГОСТ 18871 – 73 резец 2102-0005 ГОСТ 18877 – 73 резец 2130-0255 ГОСТ 18884 – 73. Сверло центровочное ГОСТ 14952 – 75 сверло 2301-4113 ГОСТ 2092 – 77 резец 2140-0508 ГОСТ 18872 – 73.
Резец 2140-0508 ГОСТ 18872 – 73.
Вертикальный протяжный станок 7Б65
Протяжка 2403-0676 ГОСТ 25158 – 82 шлицы ГОСТ 6033 – 80 шаблон для зубьев калибр-пробка ГОСТ 24969 – 81.
Зубофрезерный полуавтомат 5К301П
Фреза 2510-4023 ГОСТ 9324 – 80 прибор ГОСТ 9776 – 82.
Круглошлифовальный станок 3М151
Круг 250×32×76 ГОСТ 2424 – 83 микрометр МК 50-1 ГОСТ 6507 – 90.
Штангенциркуль ШЦ-I-125-005 ГОСТ 166 – 89 микрометр микрометр МК 50-1 ГОСТ 6507 – 90. прибор ГОСТ 9776 – 82 калибр-пробка ГОСТ 24969 – 81.
К этому разделу прилагается чертеж «ПЛАН ОБРАБОТКИ» см. графическую часть.
Разработка операционного технологического процесса и его обоснование
1 Расчет операционных технологических размеров
(при помощи комплекса расчета операционных размеров и отклонений расположения APROPOS 1995-2003 редакция 7.71 УГАТУ каф. ТиТМ лаб. САПР ТП)
2 Расчет режимов обработки
Операция 035 Токарная (центровка и сверление)
Инструмент: сверло центровочное ø10 ГОСТ 14952 – 75 и сверло спиральное ø20 мм ГОСТ 2092 – 77.
Переход 1: зацентровать отверстие центровочным сверлом ø10 мм на глубину 8 мм.
Подача: принимаем S = 03 ммоб;
Скорость резания рассчитываем по эмпирической формуле:
где Т – среднее значение стойкости; принимаем Т = 35 мин.
где Кмv – коэффициент учитывающий качество обрабатываемого материала.
KИv – коэффициент учитывающий инструментальный материал;
Кv = Кмv Киv Кlv = 083 083 1 = 0689
Определим частоту вращения шпинделя:
Крутящий момент и осевая сила определяются по формулам
Мкр = 10·CM·Dq·sy·Kp Нм;
РO = 10·Ср Dq·sy·Kp Н;
Cм = 0012; q = 22; y = 08
Ср = 42; q = 12; y = 075
Кр – поправочный коэффициент.
где Кмр = (HB190)n =(190220)06 = 0916
Мкр = 10·0012·1022·0308·0916 = 664 Н·м;
РО = 10·42·1012·03075·0916 = 246945 Н.
Мощность резания рассчитываем по формуле:
где Nшп – мощность шпинделя станка кВт.
где Nдв – мощность двигателя станка кВт;
Nшп = 11 · 075 = 825 кВт.
Переход 2. сверление.
где Т – среднее значение стойкости; принимаем Т = 60 мин.
Кv = Кмv Киv Кlv = 083 083 07 = 0482
Крутящий момент и осевая сила определяются по формулам
Cм = 0021; q = 20; y = 08
Ср = 427; q = 10; y = 08
где Кмр = (HB190)n =(190220)06 = 0916.
Мкр = 10·0021·202·0508·0916 = 4424 Н·м;
РО = 10·427·201·0508·0916 = 4498 Н.
Мощность резания рассчитываем по формуле
где Nшп – мощность шпинделя станка кВт
где Nдв – мощность двигателя станка кВт
Операция 35 токарная (растачивание).
Расточить отверстие 20 мм. в 33 мм.
Резец: по ГОСТ 18872 – 73.
Глубина резания t при черновом точении принимается равной припуску на обработку.
Подачу принимаем s = 04 ммоб при глубине резания t = 2 мм. 3 прохода.
Скорость резания при наружном продольном и поперечном точении и растачивании рассчитываем по эмпирической формуле:
где Т = 30 – 60 мин – среднее значение стойкости при одноинструментной обработке; принимаем Т = 60 мин.
t – глубина резания 2 мм;
где Кмv – коэффициент учитывающий влияние материала заготовки
Кпv – коэффициент учитывающий влияние состояния поверхности;
Киv – коэффициент учитывающий влияние материал инструмента;
Кv = 083 08 1 = 0664
При растачивании применяется поправочный коэффициент 09 табл. 17 стр. 270 том 2.
Корректируем частоту вращения по паспорту станка n = 800 обмин. Действительная скорость резания определяется по формуле:
Сила резания: Силу резания Р принято раскладывать на составляющие силы направленные по осям координат станка (тангенциальную Рz радиальную Рy и осевую Рx).
Рzyx = 10 × Ср ×tx × sy × vn × Кр
где Ср x y n – коэффициент и показатели степени для конкретных условий обработки для каждой из составляющих силы резания.
В таблице 8 приведены численное значение коэффициентов и показателей степени по всем силам.
Кр – поправочный коэффициент
Кр = Кмр Кφр Кγр Кλр Кrр
где Кмр – поправочный коэффициент учитывающий влияние качества обрабатываемого материала на силовые зависимости
Кмр = (HB190)n = (190220)04 = 0943
где Кφр Кγр Кλр Кrр – поправочный коэффициент учитывающий влияние геометрических параметров режущей части инструмента на составляющие силы резания
В таблице 9 указаны численные значения всех коэффициентов учитывающие влияние геометрических параметров режущей части инструмента.
Таким образом имеем:
Крz = 0943 1 1 1 094 = 089
Крy = 0943 077 1 17 1 = 123
Крx = 0943 111 1 165 1 = 173
Эти значения подставим в уравнение для определения сил:
Значение сил для цилиндрического размера d1:
Рy = 10 542090407582890 123 = 6234 Н;
Pz = 10 92 21 040782890 173 = 16871 Н;
Nшп = 11·075 = 825 кВт.
Операция 045 протяжная
Станок протяжный горизонтальный 7Б65 протяжка по ГОСТ 25158 – 82
Подача Sz – принимаем 012 мм
где Т – период стойкости протяжки мин (принимается в пределах 105 – 500 мин);
Сv – коэффициент зависящий от качества обрабатываемого материала;
Р – сила резания приходящаяся на 1 мм длины режущей кромки зуба протяжки Н.
- наибольшая суммарная длина кромок всех одновременно режущих зубьев мм;
где В – периметр резания мм;
Zp – наибольшее число одновременно режущих зубьев;
t – шаг режущих зубьев протяжки мм;
К – поправочный коэффициент учитывающий влияние геометрии протяжки износ режущей части условия резания
К = Кα × Кγ × Кh × КО
где Кα Кγ – коэффициенты учитывающие влияние переднего и заднего углов протяжки;
Кh – коэффициент учитывающий влияние износа зубьев протяжки;
КО – коэффициент учитывающий охлаждение зоны резания;
КО = 134 (без охлаждения).
К = 1 × 113 × 115 × 134 = 174.
Мощность протягивания. Эффективная мощность:
Потребляемая мощность
3 Нормирование операций технологического процесса
Операция 35 токарная (центрование и сверление)
Основное машинное время:
l1 + l2 – величина врезания и перебега мм
l – длина обработки мм
Общее время на центрование и сверление ТО = 058 мин.
Вспомогательное время определяется по формуле
Тв = Туст + Топ + Тизм
где Туст – вспомогательное время на установку и снятие детали
Туст = 03 + 03 мин – установка инструмента; (Приложение9 стр. 348)
Топ1 = 014 + 055 мин – проверить приход инструмента в заданную точку после обработки;
Топ2 = 003 мин. – установить и снять щиток от забрызгивания эмульсией;
Тизм = 013 мин. – время на измерение штангенциркулем. (Карта 87)
Тв = 06 + 069 + 003 + 013 = 145 мин.
атех аорг аотл – время на техническое и организационное обслуживание рабочего места на отдых и личные потребности;
атех + аорг + аотл = 4 %
Штучное время определяется по формуле
Тпз = Тпз1+ Тпз2+ Тпз
где Тпз1 – подготовительно-заключительное время на организационную подготовку;
Тпз1 = 4 мин. (Приложение9 стр. 348).
Тпз2 – подготовительно-заключительное время на наладку станка приспособлений инструмента устройств;
Тпз2 = 14 мин (Приложение9 стр. 348).
Тпз = 14 + 4 = 18 мин.
Штучно – калькуляционное время определяется по формуле
где n – количество деталей в год.
Операция 35 токарная (растачивание)
Основное время на обработку рассчитывается по формуле
Основное время 118 мин.
где Туст – вспомогательное время на установку и снятие детали
Туст = 085 мин – установка в трехкулачковом патроне
Топ1 = 03 мин – проверить приход инструмента в заданную точку после обработки (Карта 20 стр. 64).
Топ2 = 003 мин – установить и снять щиток от забрызгивания эмульсией;
Тизм = 012 мин – время на измерение штангенциркулем. (Карта 87 стр. 184)
Тв = 085 + 03 + 003 + 012 = 13 мин.
Тпз = Тпз1 + Тпз2 + Тпз мин.
Тпз1 = 4 мин (Приложение9 стр. 348).
Тпз2 – подготовительно-заключительное время на наладку станка приспособлений инструмента программных устройств;
Тпз2 = 16 мин (Карта 21 стр. 70)
Тпз = 16 + 4 = 20 мин.
Основное машинное время
где L – длина рабочего хода протяжки мм;
L = l + lp + lk + l1
где h – припуск на обработку мм;
tр – шаг режущих зубьев протяжки мм;
l1 – длина перебега протяжки (10 20 мм).
L = 66 + 45 + 70 + 10 = 191 мм.
Туст = 027 мин – установка детали (Карта 80 стр. 168).
Топ1 = 02 мин – переместить ползун в рабочее положение (Приложение 9 стр. 379).
Топ2 = 003 мин – установить и снять щиток.
Тизм = 02 мин – время на измерение калибром-пробкой. (Карта 87 поз. 103 стр. 181).
Тв = 027 + 02 + 003 + 02 = 07 мин.
атех +аорг + аотл = 35 %
где Тпз1 – подготовительно – заключительное время на организационную подготовку;
Тпз2 – подготовительно – заключительное время на наладку станка приспособлений инструмента программных устройств;
Тпз = 5 + 7 = 12 мин.
В результате выполнения работы был разработан технологический процесс механической обработки детали "Колесо червячное" в условиях серийного производства. Произведена качественная и количественная оценка технологичности детали. Спроектирована и обоснована выбранная заготовка обеспечивающая минимальные припуски на механическую обработку. На несколько технологических операций приведен подробный расчет режимов резания и норм времени. Заполнена маршрутная операционная карты а так же карта эскизов и карта контроля.
Справочник технолога – машиностроителя. В 2-х т. Т.2 Под ред. А. Г. Косиловой и Р. К. Мещерякова. – 4-е изд. перераб. и доп. – М.: Машиностроение 1986. – 496 с.
Режимы резания металлов: Справочник Под ред. Ю. В. Барановского. Изд. 3-е – М.: Машиностроение 1972. – 407 с.
Расчеты деталей машин И. М. Чернин А. В. Кузьмин Г. М. Ицкович. – 2-е изд. перераб. и доп. – Мн.: Выш.школа 1978. – 472 с. ил.
Горбацевич А. Ф. Шкред В. А. Курсовое проектирование по технологии машиностроения: (Учеб. Пособие для машиностроит. спец. вузов). – 4-е изд. перераб. и доп. – Мн.: Выш. школа 1983. – 256 с. ил.
Анурьев В.И. Справочник конструктора- машиностроителя. В 3-х т. Т. 2.-5-е изд. перераб. и доп. - М: Машиностроение 1979. –559 с. ил.
Липницкий А. М. Морозов И. В. Справочник рабочего-литейщика. Л. «Машиностроение» (Ленинград. отд-ние) 1976. 344 с. ил.
Маталин А. А. Технология машиностроения. – М.: Машиностроение 1985 - 496 с.
Общемашиностроительные нормативы времени вспомогательного на обслуживание рабочего места и подготовительно-заключительного для технического нормирования станочных работ. – М.: Машиностроение 1967. – 396с.
Приложение к ПЗ п 6.1.doc
Шифp: Дата: Разpаб.:
Начало Конец Вид Напр. Номинал Верхнее Нижнее
размера размера элемента коорд размера отклон. отклон.
¦ ¦ 1 ¦ лв ¦ 0 ¦ ¦ ¦ ¦
¦ 1 ¦ 2 ¦ лв ¦ 0 ¦ 45 ¦ ¦ -0.62 ¦
¦ 1 ¦ 3 ¦ лв ¦ 0 ¦ 28 ¦ ¦ -0.52 ¦
¦ 1 ¦ 6 ¦ пр ¦ 0 ¦ 122 ¦ ¦ -1 ¦
¦ 6 ¦ 4 ¦ пр ¦ 0 ¦ -45 ¦ ¦ -0.62 ¦
¦ 6 ¦ 5 ¦ пр ¦ 0 ¦ -28 ¦ ¦ -0.52 ¦
¦ ¦ 7 ¦ ось ¦ 1 ¦ ¦ ¦ ¦
¦ 7 ¦ 8 ¦ отв ¦ 1 ¦ D40 ¦ +0.062 ¦ ¦
¦ 7 ¦ 10 ¦ вал ¦ 1 ¦ D50 ¦ +0.018 ¦ +0.002 ¦
¦ 7 ¦ 11 ¦ вал ¦ 1 ¦ D136 ¦ ¦ -0.25 ¦
¦ 7 ¦ 9 ¦ отв ¦ 1 ¦ D34 ¦ +0.025 ¦ ¦
¦ 7 ¦ 12 ¦ вал ¦ 1 ¦ D50 ¦ +0.018 ¦ +0.002 ¦
¦ 7 ¦ 13 ¦ отв ¦ 1 ¦ D40 ¦ +0.062 ¦ ¦
* 7 ¦ 10 ¦ РБ ¦ ¦ 0.05 ¦ ¦ ¦
* 7 ¦ 12 ¦ РБ ¦ ¦ 0.05 ¦ ¦ ¦
Шифp: Цех: Проектно-поверочный расчет
Ном.Техн Допуск Нач.Кон.Напр Номинал ВерхнееНижнее Кв. Миним.
оп. база располож.р-рар-ракоор размера отклон.отклон.р-ра припуск
¦ 025 ¦ ¦ ¦ 1 ¦ 6 ¦ 0 ¦ ¦ ¦ ¦ ¦ 3 ¦
¦ 025 ¦ ¦ ¦ 7 ¦ 10 ¦ 1 ¦ D ¦ ¦ ¦ ¦ 2 ¦
¦ 025 ¦ 6 ¦ ¦ 6 ¦ 4 ¦ 0 ¦ ¦ ¦ ¦ ¦ 4 ¦
¦ 030 ¦ 1 ¦ ¦ 1 ¦ 6 ¦ 0 ¦ ¦ ¦ ¦ ¦ 3 ¦
¦ 030 ¦1 ¦ ¦ 7 ¦ 12 ¦ 1 ¦ D ¦ ¦ ¦ ¦ 2 ¦
¦ 030 ¦ 1 ¦ ¦ 1 ¦ 2 ¦ 0 ¦ ¦ ¦ ¦ ¦ 4 ¦
¦ 030 ¦1 ¦ ¦ 7 ¦ 11 ¦ 1 ¦ ¦ ¦ ¦ ¦ 4 ¦
¦ 035 ¦1 ¦ ¦ 7 ¦ 9 ¦ 1 ¦ D ¦ ¦ ¦ ¦ 1.5 ¦
¦ 035 ¦ 1 ¦ ¦ 7 ¦ 8 ¦ 1 ¦ D ¦ ¦ ¦ ¦ 2 ¦
¦ 035 ¦ 6 ¦ ¦ 6 ¦ 5 ¦ 0 ¦ ¦ ¦ ¦ ¦ 2 ¦
¦ 040 ¦1 ¦ ¦ 7 ¦ 13 ¦ 1 ¦ D ¦ ¦ ¦ ¦ 2 ¦
¦ 040 ¦ 1 ¦ ¦ 1 ¦ 3 ¦ 0 ¦ ¦ ¦ ¦ ¦ 2 ¦
* 055 ¦ ¦ ¦ 7 ¦ 10 ¦ 1 ¦ ¦ ¦ ¦ ¦ 0.5 ¦
* 055 ¦ ¦ ¦ 7 ¦ 12 ¦ ¦ ¦ ¦ ¦ ¦ ¦
¦ ¦ ¦ ¦ ¦ ¦ ¦ ¦ ¦ ¦ ¦ ¦
ТМ (R) Комплекс расчета операционных размеров и отклонений расположения
APROPOS (c) 1995-2003 редакция 7.71 УГАТУ кафедра ТМ лаб. САПР ТП
Управляющие параметры проекта:
Учет биений в расчетах Нет Номер направления координат -1
ИСО(Да)OCT(Нет) Да Оптимизация разм. связей Да
Неуказанные пред.отклонения 13 Печать данных Да
Число составляющих Р.Ц. 5 Печать графической схемы Да
Погрешность расчетов(%) .50 Печать уравнений Р.Ц. Да
Коэффициент расш. допуска 1.00 Печать поверочных расчетов Да
Округление допусков Да
РАСЧЕТ РАЗМЕРОВ ПО НАПРАВЛЕНИЮ 0
ДАННЫЕ ЧЕРТЕЖА ДЕТАЛИ
Начало Конец Вид Номинал Верхнее Нижнее
разм. разм. элемента размера отклон. отклон.
6 ПР 122.000 -1.0000
4 ПР -45.000 -0.6200
5 ПР -28.000 -0.5200
ДАННЫЕ ТЕХНОЛОГИЧЕСКОГО ПРОЦЕССА
Номер Начало Конец. Минимальный Квалит. Номинал Верхнее Нижнее Идент.
опер. разм. разм. припуск (класс) размера отклон. отклон. размера
Констр. размеров - 5
Технол. размеров - 6
ГРАФИЧЕСКАЯ СХЕМА РАЗМЕРНЫХ СВЯЗЕЙ
оп. 25 ¦-------------------------------------------------------->¦ L1
¦ ¦ ¦ ¦-------------------¦ L2
оп. 30 ¦--------------------------------------------------------> L3
¦------------------->¦ ¦ ¦ ¦ L4
оп. 35 ¦ ¦ ¦ ¦ ¦-----------¦ L5
оп. 40 ¦----------->¦ ¦ ¦ ¦ ¦ L6
¦------------------->¦ ¦ ¦ ¦ 45.00
¦----------->¦ ¦ ¦ ¦ ¦ 28.00
¦-------------------------------------------------------->¦ 122.00
¦ ¦ ¦ ¦-------------------¦ 45.00
¦ ¦ ¦ ¦ ¦-----------¦ 28.00
СИСТЕМА УРАВНЕНИЙ РАЗМЕРНЫХ ЦЕПЕЙ Кол-во технол. р-ров
K( 6 - 4)= -L1 +L2 +L3 3
Z( 6 30)= +L1 -L3 2
Условные имена размеров в уравнениях обозначают:
K - размер чертежа (начало-конец)
Z - операционный припуск (обрабатываемая пов. операция)
L - линейный технологический размер
D - диаметральный технологический размер
R - радиальный технологический размер
T - симметричный технологический размер
C - технологическая глубина цементации
P - технологическая толщина покрытия
Расчет производился методом MINMAX
РАСЧЕТНЫЕ ЗНАЧЕНИЯ ОПЕРАЦИОННЫХ РАЗМЕРОВ И ПРИПУСКОВ
Номер Начало Конец Идент. Номинал Верхн. Нижн. Квалит. Снимаемый
опер. р-ра р-ра р-ра р-ра откл. откл. (класс) припуск
1 6 L1 124.800 -0.1600 10(13)
6 4 L2 48.000 -0.1600 11(13)
1 6 L3 121.600 -0.2500 11(13) 3.040 +0.410
1 2 L4 44.800 -0.3900 13(13)
6 5 L5 27.900 -0.3300 13(13)
1 3 L6 27.900 -0.3300 13(13)
КОНТРОЛЬНОЕ СУММИРОВАНИЕ ГРАНИЧНЫХ ЗНАЧЕНИЙ РАЗМЕРОВ И ПРИПУСКОВ
Для контрольной проверки не зависимо от примененного метода расчета
допусков всегда используется метод предельных отклонений (MINMAX).
Обозначение Расчетные границы Заданные границы Предупрежд.
K( 1 - 3) 27.5700 .. 27.9000 27.4800 .. 28.0000
K( 1 - 2) 44.4100 .. 44.8000 44.3800 .. 45.0000
K( 1 - 6) 121.3500 .. 121.6000 121.0000 .. 122.0000
K( 6 - 4) 44.3900 .. 44.9600 44.3800 .. 45.0000
K( 6 - 5) 27.5700 .. 27.9000 27.4800 .. 28.0000
Z( 6 30) 3.0400 .. 3.4500 3.0000 .. ? z+
***************** Конец расчета по направлению 0 *******************
РАСЧЕТ РАЗМЕРОВ ПО НАПРАВЛЕНИЮ 1
8 ОТВ D 40.000 +0.0620
10 ВАЛ D 50.000 +0.0180 +0.0020
11 ВАЛ D 136.000 -0.2500
9 ОТВ D 34.000 +0.0250
12 ВАЛ D 50.000 +0.0180 +0.0020
13 ОТВ D 40.000 +0.0620
Констр. размеров - 6
оп. 25 ¦------------------->¦ ¦ ¦ D1
оп. 30 ¦--------------------->¦ ¦ D2
¦-------------------------------------------------------->¦ L3
оп. 35 ¦------------->¦ ¦ ¦ ¦ ¦ ¦ D4
¦--------------->¦ ¦ ¦ ¦ ¦ D5
оп. 40 ¦----------------->¦ ¦ ¦ ¦ D6
¦--------------->¦ ¦ ¦ ¦ ¦ 20.00
¦------------------->¦ ¦ ¦ 25.00
¦-------------------------------------------------------->¦ 68.00
¦------------->¦ ¦ ¦ ¦ ¦ ¦ 17.00
¦--------------------->¦ ¦ 25.00
¦----------------->¦ ¦ ¦ ¦ 20.00
7 10 D1 50.018 -0.0160 5 (13)
7 12 D2 50.018 -0.0160 5 (13)
7 11 L3 68.000 -0.1250 10(13)
7 9 D4 34.000 +0.0250 7 (13)
7 8 D5 40.000 +0.0620 9 (13)
7 13 D6 40.000 +0.0620 9 (13)
K( 7 - 9) 17.0000 .. 17.0125 17.0000 .. 17.0125
K( 7 - 8) 20.0000 .. 20.0310 20.0000 .. 20.0310
K( 7 - 13) 20.0000 .. 20.0310 20.0000 .. 20.0310
K( 7 - 10) 25.0010 .. 25.0090 25.0010 .. 25.0090
K( 7 - 12) 25.0010 .. 25.0090 25.0010 .. 25.0090
K( 7 - 11) 67.8750 .. 68.0000 67.8750 .. 68.0000
***************** Конец расчета по направлению 1 *******************
Дата: 22. 1.2009 Время: 19: 4:46.25
Заготовка в землю.cdw

Класс точности отливки 12.
Линейная усадка не более 1
Термообработка отжиг.
Отливки после ТО пескоструить.
Неуказанные литейные уклоны 1
Неуказанные предельные отклонения
Маркировать краской.
Консервация и хранение по ГОСТ 15150-69.
Общие технические условия по ГОСТ 26358-84.
План обработки.cdw

Операция 030. Токарная
Операция 035. Токарная
Операция 050. Зубофрезерная
Операция 040. Токарная
Операция 045. Протяжная
Операция 055. Шлифовальная
Круглошлифовальный станок 3М151
Материал СЧ30 по ГОСТ 1412-85
Операция 005. Заготовительная
Операция 060. Контрольная
Операция 010. Термическая (отжиг)
Операция 015. Очистная
Операция 020. Контрольная
Операция 065. Маркировочная
Операция 070. Упаковочная
Заготовка литье.cdw

Класс точности отливки 7.
Линейная усадка не более 1
Термообработка нормализация.
Отливки после ТО пескоструить.
Неуказанные литейные уклоны 1
Неуказанные предельные отклонения
Маркировать краской.
Консервация и хранение по ГОСТ 15150-69.
Общие технические условия по ГОСТ 26358-84.
Колесо червячное чертеж.cdw

Делительный угол подьема
Межосевое расстояние
сопряженного червяка
Твердость 210 220 НВ.
Внешний осмотр 100% по ГОСТ 166-80.
Неуказанные радиусы скруглений 1
Маркировать краской.
Рекомендуемые чертежи
- 24.01.2023
- 24.01.2023
- 24.01.2023