Технологическая оснастка для сборки. Разработка сборочного приспособления для запрессовки втулки во фланец



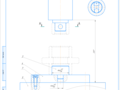
- Добавлен: 25.01.2023
- Размер: 295 KB
- Закачек: 0
Узнать, как скачать этот материал
Подписаться на ежедневные обновления каталога:
Описание
Технологическая оснастка для сборки. Разработка сборочного приспособления для запрессовки втулки во фланец
Состав проекта
![]() |
![]() ![]() ![]() |
![]() ![]() ![]() ![]() |
![]() ![]() ![]() ![]() |
Дополнительная информация
Контент чертежей
МАТЕМАТИЧЕСКИЙ РАСЧЕТ ПРИСПОСОБЛЕНИЯ.cdw

СБОРОЧНОЕ ПРИСПОСОБЛЕНИЕ.cdw

Рекомендуемые чертежи
- 11.06.2017
- 25.01.2023
Свободное скачивание на сегодня
Обновление через: 15 часов 5 минут