Реконструкция цеха по производству газированного напитка в ООО Пивоваренная компания НАШЕ ПИВО с модернизацией сатуратора ОКА2.12М2/1




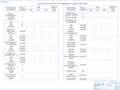

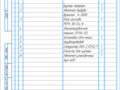
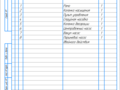
- Добавлен: 24.01.2023
- Размер: 2 MB
- Закачек: 0
Описание
Реконструкция цеха по производству газированного напитка в ООО Пивоваренная компания НАШЕ ПИВО с модернизацией сатуратора ОКА2.12М2/1
Состав проекта
![]() |
![]() |
![]() ![]() ![]() ![]() |
![]() ![]() ![]() ![]() |
![]() |
![]() ![]() ![]() ![]() |
![]() ![]() ![]() ![]() |
![]() ![]() ![]() ![]() |
![]() ![]() ![]() ![]() |
![]() ![]() ![]() ![]() |
![]() |
![]() ![]() ![]() ![]() |
![]() ![]() ![]() ![]() |
![]() ![]() ![]() ![]() |
![]() ![]() ![]() ![]() |
![]() ![]() ![]() ![]() |
![]() ![]() ![]() ![]() |
![]() ![]() ![]() ![]() |
![]() ![]() ![]() ![]() |
![]() ![]() ![]() ![]() |
![]() ![]() ![]() ![]() |
![]() ![]() ![]() ![]() |
![]() ![]() ![]() |
![]() ![]() ![]() |
![]() ![]() ![]() |
![]() ![]() |
![]() ![]() ![]() |
Дополнительная информация
09_А1_План_график_ТО.cdw

06_А1_Сборочный_чертеж_поршневого насоса.cdw

07_03_А1_Деталировка.cdw

07_01_А1_Деталировка.cdw

07_04_А1_Деталировка.cdw

07_02_А1_Деталировка.cdw

01_А1_Анализ_производственно-хозяйственной_деятельности.cdw

03_А4_План цеха с рассановкой оборудования _ ДП 110303.65.57.003.cdw

06_А4_Сборочный_чертеж_поршневого_насоса.cdw

05_А4_Общий_вид _сатуратора _ОКА_2.12М.cdw

10_А1_Технико-экономические_показатели_ реконструкции_цеха.cdw

11_А1_Технологическая_карта_на_изготовление_крышки_насоса.cdw

08_А1_Выбор_приспособлений_для_монтажа_оборудования.cdw

04_А1_Кинематическая_схема.cdw

02_А1_Машино-аппаратурная_схема_производства_газированных_напитков.cdw

03_А1_План_цеха_с_растановкой_оборудования.cdw

05_А1_Общий_вид _сатуратора _ОКА_2.12М.cdw

12_А1_Результаты_патентного_иследования.cdw

Рекомендуемые чертежи
- 29.07.2014
- 24.01.2023
- 29.07.2014
- 25.01.2023
- 28.02.2014
- 13.04.2022