Разработка технологического процесса механической обработки детали втулка глухая




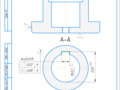
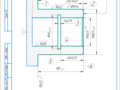
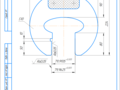
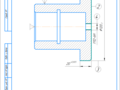
- Добавлен: 24.01.2023
- Размер: 470 KB
- Закачек: 6
Описание
Состав проекта
![]() |
![]() |
![]() ![]() ![]() |
![]() |
![]() ![]() ![]() ![]() |
![]() ![]() ![]() ![]() |
![]() ![]() ![]() ![]() |
![]() ![]() ![]() ![]() |
![]() ![]() ![]() ![]() |
![]() ![]() ![]() ![]() |
![]() ![]() ![]() ![]() |
![]() ![]() ![]() ![]() |
![]() ![]() ![]() ![]() |
![]() ![]() ![]() ![]() |
![]() ![]() ![]() ![]() |
![]() ![]() ![]() ![]() |
Дополнительная информация
КР Технология отраслевого машиностроения.doc
1. Установление конструкторского кода детали7
2. Определение типа производства8
Анализ исходных данных для разработки технологического
процесса изготовления детали10
1. Анализ технологичности конструкции10
Расчет подетальной размерной цепи15
Анализ технологических процессов17
1. Выбор заготовки17
2. Расчет припусков на обработку резанием19
3. Выбор металлорежущих станков и приспособлений к ним27
Расчет режимов резания32
Расчет предельного калибра44
Охрана труда и окружающей среды46
Список использованной литературы48
Машиностроение является ведущей отраслью всей промышленности. Продукция предприятий машиностроения играет решающую роль в реализации достижений научно-технического прогресса во всех областях хозяйства.
Машиностроение как самостоятельная отрасль общественного производства возникло в конце XVIII — начале XIX вв. на текстильных мануфактурах Англии где зарождались первые производственные участки по созданию и изготовлению прядильных и ткацких станков окрасочных и отбелочных машин паровых машин. Однако производство этих машин постепенно пришло в противоречие с низкой технической базой. С ростом потребности фабрик и заводов в текстильных и паровых машинах производство их из сферы текстильной отрасли промышленности выделяется на отдельные предприятия и в связи с охватом сельского хозяйства промышленности и транспорта машинным производством вскоре становится самостоятельной отраслью промышленности.
В России первые металлообрабатывающие заводы мануфактурного типа возникли в начале XVIII в. в первую очередь для удовлетворения военных нужд (например судостроительная Адмиралтейская верфь в Петербурге 1704 г.; Тульский оружейный завод 1712 г.; Сестрорецкий оружейный завод 1724 г.). До 1790 г. существовали только государственные механические заводы. К концу XVIII в. появились частнокапиталистические металлообрабатывающие предприятия. Всего в первой половине XIX в. в России было построено около 20 металлообрабатывающих предприятий. Среди них чугунолитейный завод Огарева в Петербурге Ижорский орудийный и сталелитейный завод Александровский чугунолитейный и Механический заводы под Петербургом. Однако объем металлообрабатывающего производства был весьма незначительным. С развитием капитализма возрастают масштабы и темпы производства машиностроения и металлообработки. Развивается промышленность расширяется внутренний рынок развертываются железнодорожное строительство и судоходство. Создаются крупные машиностроительные и металлообрабатывающие заводы. В 1857 г. основывается Семянниковский литейный завод; в 1849 г. — Сормовский завод; в 1856г. — Балтийский завод; в 1859 г. — завод братьев Бромлей.
После поражения России в Крымской войне (1853 — 1856 гг.) и крестьянской реформы 1861 г. начался период бурного развития капитализма в промышленности и сельском хозяйстве. Возникают паровозо- и вагоностроительные заводы строятся новые судостроительные верфи увеличивается производство сельскохозяйственных машин оборудования для текстильной пищевой и легкой промышленности.
Гражданская война разразившаяся после Октябрьской революции нанесла значительный урон всем отраслям машиностроения поэтому после завершения войны потребовались огромные усилия для восстановления всей экономики страны.
К началу Великой Отечественной войны существовало мощное машиностроение по объему машиностроительного производства Советский Союз занимал второе место в мире после США.
В годы войны машиностроительные отрасли производили в основном продукцию военного назначения.
После окончания Великой Отечественной войны машиностроительная промышленность значительно повысила темпы и уровень производства. Вообще машиностроение за годы Советской власти развивалось более быстрыми темпами чем народное хозяйство в целом. Средств производства производилось больше чем товаров народного потребления.
Несмотря на высокие темпы развития уже в конце 70-х и в середине 80-х годов машиностроение не обеспечивало в полной мере потребности народного хозяйства ни по количеству ни по качеству своей продукции.
В зависимости от особенностей размещения в машиностроении условно можно выделить несколько групп отраслей в том числе:
Тяжелое машиностроение (67 % продукции).
Общее машиностроение (18% продукции).
Среднее машиностроение (15 % продукции).
Общее машиностроение — эта группа машиностроительных отраслей характеризующаяся средними нормами потребления металла энергии невысокой трудоемкостью. Предприятия общего машиностроения производят технологическое оборудование для нефтеперерабатывающей химической бумажной лесной строительной промышленности дорожные и простейшие сельскохозяйственные машины. Преобладают специализированные предприятия связанные с изготовлением заготовок и сборкой конструкций агрегатов и деталей поставляемых в порядке кооперации. Ряд предприятий выпускающих оборудование для отраслей промышленности с химической технологией нуждается в специальных видах сталей цветных металлов и пластмасс.
Общее машиностроение отличается широким развитием межотраслевых и внутриотраслевых связей основанных в значительной мере на производственном кооперировании. Его связи с другими межотраслевыми комплексами служит одним из важнейших условий функционирования единого народнохозяйственного комплекса страны. Выпуская орудия труда для разных отраслей народного хозяйства оно реализует достижения научно-технического прогресса обеспечивает комплексную механизацию и автоматизацию производства.
Для развития транспорта торговли и сельского хозяйства особую важность имеет именно группа отраслей общего машиностроения т.к. она поставляет наибольшее количество техники (локомотивостроение судостроение сельскохозяйственное машиностроение и т.д.). Огромное влияние оказывает она и на другие отрасли народного хозяйства.
СЛУЖЕБНОЕ НАЗНАЧЕКИЕ ДЕТАЛИ
1. Установление конструкторского кода детали
Технологический процесс разрабатывают на основе имеющегося типового или группового ТП. Для этого по технологическому классификатору деталей формируют технологический код. По коду изделие относят к определенной классификационной группе и действующему для нее типовому или групповому ТП. Типовой или групповой технологический процесс является информационной основой при разработке рабочего технологического процесса. При отсутствии соответствующей классификационной группы ТП разрабатывают как единичный с учетом ранее принятых прогрессивных решений в действующих единичных ТП.
Технологический код разрабатывают на основе технологического классификатора.
Детали кодируются буквенно-цифровым алфавитом кода. В структуре кода за каждым признаком закреплены определенные разряд (позиция) и число знаков. Система буквенно-цифрового кодирования однозначная. Она включает цифры от 1 до 9 и прописные буквы русского алфавита от А до Я кроме буквы 3.
Классификатор ЕСКД включает 100 классов из которых 51 класс составляют резерв в котором могут быть размещены новые виды изделий.
На все детали машиностроения и приборостроения установлены шесть классов: 71 76. Основным признаком деления (кроме класса 76) является геометрическая форма.
Классы 71 76 охватывают детали всех отраслей промышленности основного и вспомогательного производства:
—класс 71: детали — тела вращения типа колес дисков шкивов блоков стержней втулок стаканов колонок валов осей штоков шпинделей и др.;
—класс 72: детали — тела вращения с элементами зубчатого зацепления; трубы шланги проволочки разрезные секторы сегменты; изогнутые из листов полос и лент; аэрогидродинамические; корпусные опорные емкостные подшипники;
—класс 73: детали — не тела вращения: корпусные опорные емкостные;
—класс 74: детали — не тела вращения: плоскостные; рычажные грузовые тяговые; аэрогидродинамические; изогнутые из листов полос и лент; профильные; трубы;
—класс 75: детали — тела вращения и (или) не тела вращения кулачковые карданные с элементами зацепления арматуры санитарно-технические разветвленные пружинные ручки посуды оптические электрорадиоэлектронные крепежные;
—класс 76: детали технологической оснастки инструмента (сверла метчики пластины режущие матрицы пуансоны и т.д.).
Установим конструкторский код детали: код организации разработчика – ПГТУ втулка относиться к классу 71.
Следовательно полный код ПГТУ 710000-003.
2. Определение типа производства
Тип производства согласно ГОСТ 3.1108-74 характеризуется коэффициентом закрепления операций за одним рабочим местом или единицей оборудования. Тип производства определяется коэффициентом:
где Q – число различных операций;
P – число рабочих мест на которых выполняются данные операции.
Определим коэффициент закрепленных операций если О = 21 P = 31:
Так как определенный коэффициента закрепленных операций меньше 1 значит он соответствует массовому типу производства.
Массовое производство характеризуются узкой номенклатурой и большим объемом выпуска изделий непрерывно изготавливаемых в течение продолжительного периода времени. При массовом производстве технологические процессы разрабатываются подробно и хорошо оснащаются что позволяет обеспечить высокую точность и взаимозаменяемость деталей малую трудоемкость и следовательно более низкую чем при серийном производстве себестоимость изделий.
При массовом производстве более широко применяется механизация и автоматизация производственных процессов используется дифференцирование технологического процесса на элементарные операции применяются быстродействующие специальные приспособления специальный режущий и измерительный инструмент.
Рабочая сила низкой квалификации при наличии настройщиков полная взаимозаменяемость при производстве.
АНАЛИЗ ИСХОДНЫХ ДАННЫХ ДЛЯ РАЗРАБОТКИ ТЕХНОЛОГИЧЕСКОГО ПРОЦЕССА ИЗГОТОВЛЕНИЯ ДЕТАЛИ
1. Анализ технологичности конструкции
Втулка конструктивно представляет собой вал с отверстием.
Втулка — тело вращения. Из требований предъявляемых к шероховатости обрабатываемых поверхностей можно сделать вывод что поверхности обрабатываемые по 7-ому классу точности являются основными то есть по ним происходит соединение втулки с другими деталями.
Втулку в основном изготавливают из конструкционных и легированных сталей отвечающих требованиям высокой точности хорошей обрабатываемости малой чувствительности к конструкционным напряжениям повышенной износостойкостью.
Втулка работает без смазки; нагрузки действующие на неё передаются через три отверстия диаметром 6 мм. При помощи этих отверстий втулка крепится к корпусу а отверстие диаметром 50мм используется для вала который передаёт вращательное движение.
Деталь достаточно технологична допускает применение высокопроизводительных режимов обработки имеет хорошие базовые поверхности и проста по конструкции. Расположение крепёжных отверстий допускает много инструментальную обработку. Поверхности вращения могут быть обработаны на многошпиндельных станках.
Произведем анализ всех поверхностей детали.
Поверхность (1) резьба размером М12-6H D = 12 мм шаг резьбы крупный P = 175 мм сверлить сверлом D = 102 мм поле допуска H степень точности по наружному и среднему диаметру 6 шероховатость Ra = 63. Обработка: сверление и нарезание резьбы машинным метчиком.
Поверхность (2) цилиндрическая поверхность номинальный размер D = 12 мм точность размера по квалитету IT14 основное отклонение H поверхность под подтай. Шероховатость Ra = 63. По справочнику допуск размера 12(+043). Обработка резанием получистовое обтачивание.
Поверхность (3) фаска размер 3×450 согласно технического условия предельные отклонения ширины фаски по ±IT 142 равны ±IT 142=±0.22=±0.1 т.е. размер фаски 2±0.1×450. Качество поверхностного слоя: Ra=63мкм. Обработка резаньем получистовое обтачивание.
Поверхность (4) цилиндрическая поверхность номинальный размер D = 120 мм точность размера по квалитету IT14 основное отклонение h. Шероховатость Ra = 63. По справочнику допуск размера 120(+087). Обработка резанием получистовое обтачивание.
Поверхность (5) цилиндрическая поверхность номинальный размер D = 6H7 мм точность размера по квалитету IT7 основное отклонение H. Шероховатость Ra = 16. Определим допуск Td = 15 мкм = 0015 мм предельное допустимое отклонение EI = 0 ES = Td + EI = (+0015) + (0) = +0015 мм; размер 6H7(+0015). Обработка: лезвийным инструментом развертывание тонкое.
Поверхность (6) цилиндрическая поверхность номинальный размер D = 80h7 мм точность размера по квалитету IT7 основное отклонение h. Шероховатость Ra = 08. Определим допуск Td = 35 мкм = 0035 мм предельное допустимое отклонение e размер 80h7(+0035). Обработка: шлифование чистовое.
Поверхность (7) фаска размер 2×450 согласно технического условия предельные отклонения ширины фаски по ±IT 142 равны ±IT 142=±0.22=±0.1 т.е. размер фаски 3±0.1×450. Качество поверхностного слоя: Ra=63мкм. Обработка резаньем получистовое обтачивание.
Поверхность (8) шпоночный паз номинальный размер 14Js9 точность размера по квалитету IT9 основное отклонение Js посадка по шпонку. Шероховатость Ra = 32. Определим допуск Td = 43 мкм = 0043 мм предельное допустимое отклонение EI = -00215 ES = +00215 мм; размер . Обработка: долбление тонкое.
Поверхность (9) цилиндрический паз номинальный размер D = 60 мм точность размера по квалитету IT14 основное отклонение H технологически по изготовление шпоночного паза. Шероховатость Ra = 63. По справочнику допуск размера 60(-074). Обработка резанием получистовое обтачивание.
Поверхность (10) цилиндрическая поверхность номинальный размер D = 50H7 мм точность размера по квалитету IT7 основное отклонение H посадка под вал. Шероховатость Ra = 32. Определим допуск Td = 30 мкм = 003 мм предельное допустимое отклонение EI = 0 ES = Td + EI = (+003) + (0) = +003 мм; размер 50H7(+003). Обработка: шлифование чистовое.
Поверхность (11) торец точность размера ±IT 142. Шероховатость Ra = 32. Обработка резанием получистовое обтачивание.
Поверхность (12) торец точность размера ±IT 142. Шероховатость Ra = 32. Обработка резанием получистовое обтачивание.
Поверхность (13) торец точность размера ±IT 142. Шероховатость Ra = 63. Обработка резанием получистовое обтачивание.
Поверхность (14) лыска точность размера ±IT 142. Шероховатость Ra = 32. Обработка фрезерование получистовое.
Анализ технологичности конструкции производится по дополнительным показателям технологичности конструкции: коэффициенту унификации конструктивных элементов коэффициенту точности обработки коэффициенту шероховатости поверхности.
Для этого составляем таблицу данных конструкторского анализа детали по поверхностям.
Наименование поверхности
Кол-во унифицированных поверхностей
Параметр шероховатости
Поверхность d=12 (2)
Поверхность d=120 (4)
Поверхность d=6H7 (5)
Поверхность d=80h7 (6)
Поверхность d=50H7(10)
Коэффициент унификации конструктивных элементов детали определим по формуле:
где Qу.э – количество унифицированный поверхностей;
Qэ – количество поверхностей шт.
По этому показателю деталь технологична так как Kу.э ≥ 06.
Коэффициент точности обработки определяется по формуле:
где Aср – средний квалитет точности.
Найдем средний квалитет точности:
где ni – число поверхностей детали точностью соответственно по 1-19 – квалитетам.
Так как Kт.ч > 08 то деталь по этому показателю является технологичной.
Коэффициент шероховатости поверхности определяется по формуле:
где Бср – средняя шероховатость поверхности мкм.
Рассчитаем среднюю шероховатость поверхности:
где ; n14 – количество поверхностей имеющих шероховатость соответствующую данному числовому значению параметра Ra. В нашем случае
Поскольку Кш 032 по этому показателю деталь технологична.
РАСЧЕТ ПОДЕТАЛЬНОЙ РАЗМЕРНОЙ ЦЕПИ
Номинальную величину А определим по формуле:
Определим предельные отклонение составляющих размеров исходное из технических требований что неуказанные предельные отклонение равные для увеличивающих размеров по +Н142 для уменьшающих по –Н142.
Отклонение составляющих размеров равно:
Допуск замыкающего размера звена определим по формуле:
Координаты середины поля допуска замыкающего размера определим по формуле:
Тогда верхнее и нижнее отклонение замыкающего звена равно:
Размер замыкающего звена равен:
АНАЛИЗ ТЕХНОЛОГИЧЕСКИХ ПРОЦЕССОВ
Материал детали сталь 45Х.
Заменитель — стали: 40Х 50Х 45ХЦ 40ХГТ 40ХФ 40Х2АФЕ.
Назначение: валы шестерни оси болты шатуны втулки и другие детали к которым предъявляются требования повышенной твёрдости износостойкости прочности и работающие при незначительных ударных нагрузках.
Химический состав (ГОСТ 4543-71) %:
Механические свойства:
Предел прочности в МПа
Предел текучести т МПа
Относительное удлинение %
Плотность: ρ = 7820 кгм3.
Свариваемость: трудносвариваемая. Способы сваривания: РДС необходимы подогрев и последующая термообработка. Обрабатываемость резанием — в горячекатаном состоянии при НВ 163-168sВ=610МПа Кvтв.спл.=1.20 Кv б.ст.=0.95
Флокеночувствительность: есть.
Склонность к отпускной хрупкости: есть.
Руководствуясь конструкцией детали материалом техническими требованиями - масштабом производства и задачами в целях экономии металла принимаем метод изготовления заготовки - ковка.
Данным способом получают весьма разнообразные по форме и размерам изделия из металла и других материалов с различными степенью точности размеров механическими и другими характеристиками и качеством поверхности. Поэтому ковочно-штамповочное производство находит широкое применение в машиностроении и приборостроении в производстве предметов народного потребления и других отраслях народного хозяйства. Получение изделий ковкой и штамповкой позволяет максимально приблизить исходную форму заготовки к форме и размерам готовой детали и тем самым уменьшить или полностью исключить дорогостоящие операции с потерей металла в стружку.
Данная деталь — втулка — изготовим штамповкой на горизонтально-ковочных машинах (ГКМ). Штамповка на ГКМ является одним из самых производительных способов и рентабельна для заготовки данной детали. Производительность до 400 поковок в час.
Разработаем эскиз заготовка и определяем припуски на обработку.
2 Расчет припусков на обработку резанием
Припуск на обработку определяем из справочной литературы а для двух размеров рассчитываем двумя методами.
Данные о размерах заготовки
Диаметр или длина ступени вала
Шероховатость поверхности мкм
Общий припуск на диаметр 2Zобщ мм
Диаметр ступени на поковке мм
Допуск размера поковки штампован-
Рассчитаем припуск на обработку количество технических переходов допустимые отклонения для размера каждого перехода и шероховатость поверхностей для поверхности с шероховатостью поверхности Ra = 32 мкм.
Исходной заготовки имеет диаметр шероховатость . Общий припуск обработки
Определим точность промежуточных размеров: допуск размера диаметра исходной заготовки 55 и допуск диаметра детали 50H7 .
Теперь определим общий коэффициент ужесточения точности размера равен:
Найдем количество потребных технологических переходов:
Допуск размера диаметра заготовки соответствует 17 квалитету точности допуск размера детали 7 квалитету т.е. точность повышается на 17 – 7 =10 квалитетов. По принятым четырем технологическим переходам (п=4) распределяем точность по закону прогрессивного убывания 10=4+3+2+1. Тогда точность промежуточных размеров заготовки в процессе механической обработки будет соответствовать
Заготовки по 17 квалитету
после 1 перехода 17 – 4 = 13 (IТ13)
после 2 перехода 13 - 3= 10 (IТ10)
после 3 перехода 10 - 2= 8 (IТ8)
после 4 перехода 8 - 1= 7 (IТ7)
Припуски на каждый переход определяем из расчета:
- до этого при выборе заготовки определен общий припуск .
- припуск (на диаметр) под шлифование выбран по таблице и он равен 05 мм; распределяем его на предварительное и окончательное шлифование (примерно в соотношении 3:1)
Припуск под чистовое точение (перед шлифованием): мм.
Определим припуск под черновое точение:
Последовательность обработки поверхностей детали
Промежуточ-ный припуск
Допустимое отклонение размера
Шерохова-тость поверхности
Точить поверхность предварительно
Шлифовать поверхность предварительно
(черновое шлифование)
Шлифовать поверхность окончательно
(чистовое шлифование)
Промежуточные размеры с допуском
Содержание переходы после рассматриваемого перехода
Промежуточный размер с допуском мм
Шлифовать поверхность окончательно диаметр готовой поверхности ступени исходной расчетный размер
(для наружных поверхностей наибольший предельный)
Точить поверхность начисто
Точить поверхность начисто
Диаметр поверхности исходной заготовки (поковки)
Аналитический метод определения припусков
Определить промежуточные припуски и промежуточные размеры при обработке поверхности вала диаметром 80h7 согласно рабочему чертежу.
Суммарные отклонения расположения заготовки при обработке в патроне определяется по формуле:
где: rом – отклонения расположения заготовки штампуемой в различных половинах штампа мм;
ρдеф – деформация заготовки мм.
Отклонение расположения заготовки при консольном закреплении:
где: y - величина удельного отклонения расположения мкммм (y = 006 мкммм);
Lк - расстояние от сечения для которого определяют величину отклонения расположения до места крепления заготовки мм.
Расстояние от сечения для которого определяется кривизна до места опоры при консольной обработки заготовки определяется из отношения:
где L – общая длина заготовки мм (L = 100 мм) тогда принимаем Lк = 100 мм.
Следовательно отклонение расположения заготовки равно:
Найдем деформация кованных заготовок:
где деф – величина удельной деформации поковки мкммм (деф = 08 мкммм).
Рассчитаем суммарное отклонение расположения на черновую обработку:
Погрешность установки на заготовку определим по формуле:
где: б – погрешность базирования мкм;
зк – погрешность закрепления заготовки мкм.
При закреплении заготовки в приспособлениях тисочного типа погрешность закрепления равна:
где: Kз - коэффициент зависящий от характеристики поверхностей воспринимающих силу зажима для поверхностей до обработки Кз = 175;
b – ширина поверхности заготовки мм (b = 120 мм).
При совмещении технологической и измерительной баз погрешность базирования б = 0.
Найдём минимальный припуск на черновую обработку:
Качество поверхности заготовки: Rz =240 мкм h = 250 мкм.
Максимальный припуск на черновую обработку поверхности детали определим по формуле:
Величину остаточного суммарного отклонения расположения заготовки после выполнения черновой обработки поверхности определяем по формуле:
Найдем величина погрешности установки при чистовой обработке поверхности заготовки:
При последующей обработке поверхности детали погрешности установки из-за малости ее величины в расчет не принимаем.
Расчетный минимальный и максимальный припуски на чистовую обработку поверхности детали определим по формулам:
Найдем минимальный и максимальный припуски на шлифовальную обработку поверхности:
Промежуточные расчетные размеры по обрабатываемым поверхности определяем по формуле:
для чистовой токарной обработки
Dmin = Dmin + 2zmin шл
Dmin = 80 + 004 = 8004 мм
для черновой токарной обработки
Dр.черн = Dр.чист + 2zmin чист
Dр.черн = 8004 + 0452 = 80492 мм
для заготовки детали
Dр.з = Dр.черн + 2zmin
Dр.з = 80492 + 5183 = 85675 мм.
Промежуточные размеры определяем методом прибавления (для валов) значений припусков по максимальным и минимальным значениям начиная действия с размеров детали.
Dчист = Dд + 2zmin шл
Dчист = 79965 + 004 = 80 мм
Dmin чист = Dчист + 2zmin чист
Dmin чист = 80 + 0452 = 8045 мм
Dmin 3 = Dчерн + 2zmin черн
Dmin 3 = 8045 + 5183 = 8563 мм.
Максимальные предельные промежуточные размеры:
Dmax чист = Dmax + 2z max шл
Dmax чист = 80 + 0075 = 80075 мм
Dmax черн. = Dmax + 2zmax чист
Dmax черн. = 80075 + 0842 =8092 мм
Dmax 3. = Dmax +2zmax черн
Dmax 3. = 8092 + 672 = 8764 мм.
3. Выбор металлорежущих станков и приспособлений к ним
Выбор станочного оборудования является одной из важнейших задач при разработке технологического процесса механической обработки. От правильного его выбора зависит производительность изготовления детали экономное использование производственных площадей механизации и автоматизации ручного труда электроэнергии и в итоге себестоимость изделия.
В связи с объемом выпуска изделий выбираем станки по степени специализации и высокой производительности а также станки с числовым программным управлением (ЧПУ).
Токарно-винторезный станок с ЧПУ 16Б16Т1.
Наибольший диаметр обрабатываемой заготовки мм:
Наибольшая длина обрабатываемой заготовки мм750
Частота вращения шпинделя обмин40-2000
Число скоростей шпинделя18
Подача суппорта мммин:
Число ступеней подачиБс
Мощность электродвигателя главного привода кВт71
Габаритные размеры мм
Радиально-сверлильный станок 2Р53.
Наибольший условный диаметр сверления в стали мм 50
Расстояние от оси шпинделя до образующей (направляющей)
Расстояние от нижнего торца шпинделя до рабочей поверхности
Наибольшее перемещение:
вертикальное рукава на колонне мм1050
горизонтальное сверлильной головки по рукаву мм-
Наибольшее вертикальное перемещение шпинделя мм400
Число скоростей шпинделя21
Число вращения шпинделя обмин20-2000
Число подач шпинделя12
Подача шпинделя ммоб 0056-25
Наименьшая сила подачи МН16
Мощность электродвигателя привода главного двигателя кВт55
Долбежный станка 7А430.
Длина хода долбяка мм120-320
Расстояние от наружной плоскости резцедержателя до стойки мм615
Расстояние от плоскости стола до нижнего конца направляющих
Диаметр рабочей поверхности мм-
Наибольшее перемещение стола мм:
Угол наклона долбежной головки °±10
Наибольшее сечение резца мм20×32
Число двойных ходов долбяка в минуту-
Скорость долбяка на рабочем ходу ммин3-38
Подача стола за один двойной ход долбяка ммоб:
Мощность электродвигателя привода главного двигателя кВт10
Вертикально-фрезерный станка 6Р11.
Размеры рабочей поверхности стола (ширина × длина) мм 250×1000
Перемещение гильзы со шпинделем мм60
Наибольший угол поворота шпиндельной головки °±45
Число скоростей шпинделя16
Частота вращения шпинделя обмин50-1600
продольная и поперечная35-1020
Скорость быстрого перемещения стола мммин:
продольного и поперечного2900
Шлифовальный станок 3П451.
Наружный диаметр шлицевого вала мм35-100
Длина шлицевой заготовки мм200-710
Наибольшая длина шлифуемых шлицев мм60-380
Число шлицевых шлицев3-98
Размеры рабочей поверхности стола мм 250-1500
Скорость продольного перемещения стола ммин2-10
Наибольшее вертикальное перемещение шлицевой головки мм100
Частота вращения шлифовального круга обмин 2880; 4550;
Мощность электродвигателя привода главного двигателя кВт3
Приспособлениями называются дополнительные устройства к станку предназначенные для закрепления обрабатываемых деталей или расширения технологических возможностей станка.
Приспособления применяемые для изготовления втулки: трехкулачковый пневматический патрон и универсальная делительная головка
РАСЧЕТ РЕЖИМОВ РЕЗАНИЯ
Рассчитаем режим резания для обтачивания вала при следующих данных: Диаметр заготовки D = 8568 мм диаметр детали d = 80-0035 мм длина обрабатываемой поверхности L = 80 мм шероховатость Ra = 08 мкм установка в патроне и заднем центре.
Станок токарно-винторезный с ЧПУ 16Б16Е1; резец – проходной упорный с пластиной из твердого сплава Т15К6. Геометрия резца: γ = 12° α = 10° φ = 90° r = 1 мм; форма передней поверхности – плоская с положительным передним углом.
Данные припусков для черновой и чистовой обработки возьмем из аналитический метода определения припусков.
Назначим режим резания для чернового перехода.
Определим глубину резания:
где D и d – диаметр обрабатываемой и обработанной поверхностей.
По справочнику выбираем подачу S = 06 ммоб так как станок имеет бесступенчатое регулирование значит оставляем это значение.
Следовательно эталонная скорость резания равна Vэт = 157 ммин.
Найдем абсолютное значение скорости резания при 60-минутной стойкости:
где kv – коэффициент обрабатываемости (для обработки стали 45Х резцом из твердосплавного сплава kv = 08).
Рассчитаем действительную скорость резания:
где k1 – коэффициент на стойкость резания (выбираем стойкость резания 90 мин тогда k1 = 092);
k2 – коэффициент обрабатываемости материала (предел прочности стали 45Х в = 570 МПа следовательно k2 = 135);
k3 – коэффициент обрабатываемости поверхности (поверхность без коробления k3 = 1);
k4 – коэффициент материала резца (материал резца сплав Т15К6 тогда k4 = 1);
k5 – коэффициент главного угла резца (при φ = 90° k5 = 08).
По уточненной скорости определяем необходимую частоту вращения заготовки:
Из определения геометрической прогрессии следует что
По таблице справочника находим φ17 = 5056 что соответствует φ= 126.
В графе таблицы соответствующей находим ближайшее меньшее значение .
Уточняем действительную скорость резания.
Проверим режим резания по мощности на шпинделе станка для этого определим усилие резания:
где k – коэффициент резания МПа (k = 1600 МПа).
Найдем мощность необходимую на резание:
Необходимая мощность электродвигателя:
где - кпд кинематической цепи станка ( = 08).
Для осуществления процесса резания необходимо чтобы выполнялось условие
где Nст – мощность электродвигателя главного привода станка (Nст = 71 кВт)
Что вполне достаточно для осуществления выбранного режима резания.
Назначаем режим резания для чистового перехода.
Найдем подачу с учетом поправочного коэффициента:
Скорость резания по справочнику составляет 270 обмин.
Уточняем скорость резания соответственного измененным условиям работы:
Определим необходимую частоту вращения заготовки:
Уточняем частоту вращения заготовки в соответствии с параметрами станка:
Уточняем действительную скорость резания:
Работа при резании затрачиваемая на деформацию срезаемого слоя металла скалывание элементов стружки и преодоление сил трения превращается в теплоту.
Теплота выделяющаяся при точении распределяется примерно в следующих соотношениях: 70—80 % уносится стружкой 20—25 поступает в резец 4—9 в деталь и около 1 % — в окружающее пространство.
Нагрев инструмента и обрабатываемой детали отрицательно влияет на условия работы. Разогретый инструмент теряя твердость быстрее изнашивается а тепловое расширение обрабатываемой детали усложняет получение точных размеров.
При обработке определенного материала температура инструмента зависит от его геометрии применяемого режима резания свойств смазывающе-охлаждающей жидкости и способа охлаждения.
Из элементов режима резания на температуру режущей кромки инструмента наибольшее влияние оказывает скорость резания меньшее - подача и наименьшее — глубина резания. Эта закономерность является исходным положением для выбора оптимальных режимов резания.
Смазывающе-охлаждающая жидкость уменьшая трение снижает нагрев и изнашивание инструмента. Применяемые жидкости характеризуются различными смазывающими и охлаждающими свойствами. Наибольшую охлаждающую и. слабую смазывающую способность имеет раствор кальцинированной соды в воде. Им рекомендуется пользоваться преимущественно при обдирочном точении когда прежде всего необходимо интенсивно охлаждать режущий инструмент. При получистовом и чистовом точении сверлении и зенкеровании универсальной смазывающе-охлаждающей жидкостью является 5 %-ная эмульсия которая представляет собой раствор эмульсола в воде. Основу эмульсола составляет минеральное масло в смеси с раствором едкого натра вследствие этого эмульсия наряду с хорошим охлаждением оказывает и смазывающее действие.
Для чистовых работ с невысокой скоростью резания (развертывание нарезание резьб) целесообразно применять жидкости с большей смазывающей способностью. К ним относятся высококонцентрированные 10—15 %-ные эмульсии сульфофрезолы керосин веретенные масла и их смеси.
Обычный способ охлаждения осуществляется направлением струи жидкости в зону резания со стороны передней поверхности резца.
Более эффективным является способ охлаждения распыленной жидкостью мельчайшие частицы которой хорошо смазывают трущиеся поверхности и производят интенсивное охлаждение за счет ускоренного испарения. Распыление осуществляется потоком сжатого воздуха направляемого в смесительную форсунку куда поступает жидкость от охладительной системы станка.
Технологическая документация.
Разработка технологического процесса механической обработки детали заканчиваем составлением и оформлением комплекта документов технологического процесса.
По степени детализации информации каждый из указанных видов технологических процессов предусматривает различное изложение содержания операции и комплектность документов.
В маршрутно-операционном технологическом процессе предусматриваем краткое описание содержания отдельных операций в маршрутной карте а остальные операции оформляем на операционных картах.
Наименование операции
Трехкулачковый пневматический патрон
Резец проходной упорный отогнутый с углом φ=90° Т15К6
Резец прорезной канавочный Т15К6
Резец проходной прямой с углом φ=45° Т15К6
Сверло спиральное быстрорежущее d = 102 мм
Резбовая калибр-пробка М12-6H
Трехкулачковый патрон
Рабиально-сверлильная
Универсальная делительная головка
Сверло-зенкер-развертка d=6 мм
Сверло спиральное быстрорежущее d = 12 мм
Калибр-пробка d=50H7
Содержание установов и переходов
Установить и закрепить заготовку
трехкулачковый пневматический патрон
резец проходной упорный отогнутый с углом φ=90° ТК15К6
Точить поверхность 5
Точить поверхность 3
резец проходной прямой с углом φ=45° ТК15К6
резец прорезной канавочный
Просверлить и нарезать резьбу 4
сверло спиральное быстрорежущее d = 102 мм
резбовая калибр-пробка М12-6H
трехкулачковый патрон
универсальная делительная головка
Сверлить отверстия 1
сверло-зенкер-развертка d=6 мм
сверло спиральное быстрорежущее d = 12 мм
Шлифовать поверхность 1
Шлифовать поверхность 2
калибр-пробка d=50H7
РАСЧЕТ ПРЕДЕЛЬНОГО КАЛИБРА
Рассчитаем калибр-скоба для размера 80h7.
Определим предельные допустимые отклонения:
Точность размера по квалитету IT7 основное отклонение h. Определим допуск Td = 35 мкм = 0035 мм предельные допустимые отклонения e es = Td + e размер 80h7(-0035) .
Определим предельные размеры проходной и непроходной стороны калибра:
Z1 = 4 мкм = 0004 мм
H1 = 5 мкм = 0005 мм
y1 = 3 мкм = 0003 мм.
Наибольший допустимый размер:
Наименьший допустимый размер
Наибольший изношенный размер
Исполнительный размер
Наибольший допустимый размер
Схема расположения полей допусков
ОХРАНА ТРУДА И ОКРУЖАЮЩЕЙ СРЕДЫ
Под охраной труда следует понимать комплекс технических санитарно-гигиенических и правовых мероприятий направленных на создание безопасных и здоровых условий труда.
Техника безопасности промышленная санитария определяют такие условия в производственной обстановке которые не могут прямо или косвенно привести к несчастным случаям профессиональным заболеваниям. Поэтому рабочие обязаны строго выполнять все требования техники безопасности и промышленной санитарии.
При разработке и внедрении мер по созданию безопасных и здоровых условий труда важно соблюдать последовательность и комплексность. Сначала необходимо устранить факторы вредно воздействующие на организм человека - шум неблагоприятный микроклимат загрязненность воздуха в производственных помещениях и т.п. а затем приступать к эстетизации производственной среды.
Для соблюдения допустимых микроклиамтических условий в рабочей зоне помещения необходимо: летом - естественное проветривание кондиционирование воздуха; зимой - тепловые воздушные завесы и шлюзы в проемах дверей производственных помещений. Для чистоты воздуха на участке должна применяться приточно-вытяжная вентиляция.
Мероприятия по борьбе с шумом и вибрацией - применение звукоизолирующих материалов для облицовки стен применение индивидуальных средств защиты и т.д.
Во избежание травматизма при работе на металлорежущих станках должны строго соблюдаться правила ТБ. Движущиеся и вращающиеся части станков должны быть закрыты надежными ограждениями. Предусматривают защитные средства (экраны из оргстекла очки) от вылетающей стружки. Заготовка и инструмент должны быть надежно закреплены.
Организационные мероприятия: качественное и своевременное проведение инструктажей по ТБ организация общественной инспекции труда усиление наглядной агитации вывешивание плакатов по ТБ создание уголка ТБ назначение дежурных (поочередно) по технике безопасности в каждой смене.
Во избежание пожаров следует соблюдать правила пожарной безопасности. На территории цеха проходы проезды люки колодцев должны быть свободными и не загромождаться материалами заготовками деталями и отходами производства. Промасленная ветошь должна собираться в определенном месте постоянно убираться из цеха.
Обязательно должен быть план эвакуации при пожаре ящик с песком пожарный инвентарь на щитах в нужном количестве и быть легко доступным. Необходимо иметь запасный выход на случай пожара. Также должна быть блокировка электрооборудования.
Для каждого работающего должно быть обеспечено удобное место не стесняющее его действия во время работы. Рабочее место должно быть обеспечено площадью для размещения оснастки заготовок.
Стеллажи для хранения заготовок и деталей должны быть такой высоты чтобы рабочему было удобно и безопасно укладывать заготовки и детали. Запрещается хранение инструмента в станинах станка.
Тумбочки для инструмента и оснастки должны соответствовать количеству рабочих мест и форме предметов для хранения которых они предназначены.
Уборка стружки со станков и автоматических линий должна быть максимально механизирована.
СПИСОК ИСПОЛЬЗОВАННОЙ ЛИТЕРАТУРЫ
Колесов И.М. Основы технологии машиностроения. – М.: Высшая школа 2001.-591с.
Бергер И.И. Справочник молодого токаря.-Мн.; Высш. шк. 1998.-366 с.
Гельфгат Ю.И. Сборник задач и упражнений по технологии машиностроения.-М.: Высш. шк. 2004г.
Технологический классификатор деталей машиностроение. М. 1998 г.
Технология конструкционных материалов. Под. ред. Шатерина М.А. – М.: Политехника 2005. -597с.
Справочник технолога-машиностроителя. В 2-х т. Т.1 под ред. А.Г.Косиловой и Р.К. Мещерикова- М. Машиностроение 1998г. -496с.
Справочник технолога-машиностроителя. В 2-х т. Т.1 под ред. А.Г.Косиловой и Р.К. Мещерикова- М. Машиностроение 1998г. -656с.
Журавлев В.Н. Николаева О.И. Машиностроительные отрасли. Справочник-М.: Машиностроение. 1981.- 391с.
Обработка металлов резанием. Справочник
технолога А.А. Панов и др.-М.: Машиностроение. 1999.-736с.
Технология машиностроения: В 2 кн. Кн 2. Производство деталей машин: Учеб. пособие для вузов Э.Л. Жуков И.И. Козарь С.Л. Мурашкин и др.; Под ред. С.Л. Мурашкина. - М.: Высшая школа 2003. -295с.
Операция 035.cdw

Операция 010.cdw

Заготовка втулка.cdw

Операция 015.cdw

Резец.cdw

Операция 025.cdw

Втулка глухая.cdw

Операция 030.cdw

Эскиз детали для технологического анализа.cdw

Операция 020.cdw

Операция 045.cdw

Калибр-скоба.cdw

Рекомендуемые чертежи
- 24.01.2023
- 24.01.2023
- 28.05.2016
- 23.04.2016