Разработка технологического процесса механической обработки детали Втулка



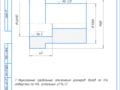
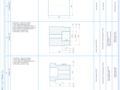
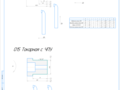
- Добавлен: 24.01.2023
- Размер: 242 KB
- Закачек: 0
Описание
Состав проекта
![]() |
![]() |
![]() ![]() ![]() ![]() |
![]() ![]() ![]() |
![]() |
![]() |
![]() ![]() ![]() |
![]() ![]() ![]() ![]() |
![]() ![]() ![]() ![]() |
![]() |
Дополнительная информация
Тп.cdw

выдерживая размер 105
Установить и закрепить заготовку.
Точить торец выдерживая размер3.
Точить поверхность выдерживая размеры 1
Сверлить поверхность выдерживая размеры 3
Точить поверхность выдерживая размеры 5
Острые кромки притупить R0
Точить торец выдерживая размер2.
Резец проходной упорный ВК8
Резец расточной упорный ВК8
Разработка технологического процесса
механической обработки детали "Втулка
Информационно-технологическая
карта обработки детали "Втулка
Наименование операции
Мерительный инструмент
Установить и закрепить
Трехкулачковый самоцентрирущийся патрон
Информационно-технологическая карта обработки детали "Втулка
Станок токарный 16К20Ф3
Министерство образования и науки Российской Федерации тит лист.docx
Государственное образовательное учреждение
высшего профессионального образования
«ВОРОНЕЖСКИЙ ГОСУДАРСТВЕННЫЙ ТЕХНИЧЕСКИЙ УНИВЕРСИТЕТ»
Кафедра «Технология машиностроения»
по дисциплине «Технология машиностроения»
Тема: «Разработка технологического процесса механической обработки детали Втулка»
курсовой.docx
Описание типа производства и формы организации работ6
Обоснование выбора базирующих поверхностей.13
Определение и обоснование метода получения заготовки.16
Разработка маршрута обработки отдельных поверхностей и полной маршрутной технологии.17
Аналитический расчет припусков на поверхность 70h8.19
Основные принципы и обоснование выбора технологического оборудования приспособлений и мерительного инструмента.22
Расчет режимов резания и техническое нормирование.24
2 Техническое нормирование.26
Развитию и формированию учебной дисциплины «технология машиностроения» как прикладной науки предшествовал непрерывный прогресс машиностроения на протяжении последних двух столетий. Степень прогресса определяла интенсивность изучения производственных процессов а следовательно и научное их обобщение с установлением закономерностей в технологии механической обработки и сборки.
Машиностроительная промышленность является ведущей отраслью так как это главный потребитель сырья и рабочей силы. От нее зависит материально техническая база и обороноспособность страны. Именно в машиностроении материализуются научно-технические идеи создаются новые системы машин определяющие прогресс в других отраслях.
Современный уровень технического прогресса создание совершенных высокопроизводительных автоматизированных и высокоточных машин основанных на использовании новейших достижений науки требует подготовки высокообразованных инженеров обладающих глубокими знаниями и хорошо владеющих новой техникой и технологией производства.
Эффективность производства его технический прогресс качество выпускаемой продукции во многом зависят от опережающего развития нового оборудования машин станков и аппаратов от внедрения методов технико-экономического анализа обеспечивающего решение технических вопросов экономическую эффективность технологических и конструкторских разработок.
Курсовой проект является одним из основных этапов подготовки студентов к дипломному проектированию. Основной задачей курсового проекта является разработка технологического процесса механической обработки заготовки на стадии технического проекта для различных видов и типов производства с выполнением ряда технических расчетных работ и технико-экономическим обоснованием принятых решений.
Описание назначения детали качественно-точностные характеристики ее основных поверхностей химический и физико-механические свойства материала детали.
Классификация:Латунь обрабатываемая давлением
Применение:очень хорошо деформируется в холодном состоянии (холодной высадкой)
Таблица 1 - Механические свойства при Т=20 °С материала Л68
Твердость материала Л68 сплав мягкий HB 10 -1 = 55 - 65 МПа
Твердость материала Л68 сплав твердыйHB 10 -1 = 145-155 МПа
Таблица 2 - Физические свойства материала Л68
Литейно-технологические свойства материала Л68
Температура плавления °C :938
Температура горячей обработки °C :700 - 850
Температура отжига °C :550 - 650
Таблица 3 - Химический состав в % материала Л68
Примечание: Zn - основа; процентное содержание Zn дано приблизительно
Механические свойства:
sв- Предел кратковременной прочности [МПа]
sT- Предел пропорциональности (предел текучести для остаточной деформации) [МПа]
d5- Относительное удлинение при разрыве [ % ]
y- Относительное сужение [ % ]
KCU- Ударная вязкость [ кДж м2]
HB- Твердость по Бринеллю [МПа]
Физические свойства :
T - Температура при которой получены данные свойства [Град]
E- Модуль упругости первого рода [МПа]
a - Коэффициент температурного (линейного) расширения (диапазон 20° - T ) [1Град]
l- Коэффициент теплопроводности (теплоемкость материала) [Вт(м·град)]
r- Плотность материала [кгм3]
C - Удельная теплоемкость материала (диапазон 20° - T ) [Дж(кг·град)]
R - Удельное электросопротивление [Ом·м]
Магнитные свойства :
Hc- Коэрцитивная сила (не более) [ Ам ]
Umax- Магнитная проницаемость (не более) [ МГнм ]
P1.050- Удельные потери (не более) при магнитной индукции 1.0 Тл и частоте 50 Гц [ Вткг ]
B100- Магнитная индукция Tл (не менее) в магнитных полях при напряженности магнитного поля 100 [ Ам ]. [7]
Описание типа производства и формы организации работ
Гибким автоматизированным производствам могут соответствовать различные формы и методы организации процессов производства в зависимости от степени автоматизации (комплекс и производство) и уровня организационной структуры (модуль линия участок).
Гибкая производственная система представляет собой совокупность или отдельную единицу технологического оборудования и системы обеспечения его функционирования в автоматическом режиме обладающую свойствами автоматизированной переналадки на производство изделий произвольной номенклатуры в установленных пределах значений их характеристик. Ее использование позволяет распространить преимущества автоматизации на мелко - и среднесерийное производство обеспечить выпуск продукции малыми партиями и чрезвычайно высокую адаптацию к требованиям рынка способностью быстро реагировать на спрос потребителя. Следует иметь в виду что внедрение гибких автоматизированных производств на базе ГПС сопровождается немалыми единовременными затратами. Экономическая целесообразность принятия решения об их использовании требует тщательного обоснования и расчета эффективности внедрения.
В гибких автоматизированных производствах реализуются такие фундаментальные принципы научной организации производства как концентрация специализация и универсализация пропорциональность непрерывность ритмичность параллельность прямоточность и др. Однако их роль и методы осуществления в новых условиях изменяются.
Резко повышается роль принципа пропорциональности поскольку в ГПС должна быть тщательно увязана пропускная способность не только всех основных производственных подразделений предприятия но и сопряженных с ними вспомогательных. Возрастает роль принципа универсализации. В ГПС отходят от принципов традиционной узкой специализации работающих возникает потребность в рабочих широкого профиля в определенной мере теряет значение принцип прямоточности.
Могут быть названы новые принципы необходимость соблюдения которых при построении ГПС проявляется во все большей степени. К ним относятся:
В процессе проектирования ГПС должны решаться следующие организационные задачи:
) Подбор номенклатуры деталей подлежащих обработке на участках гибкой автоматизации и определение характера специализации производственных подразделений;
) Разработка проекта организации труда всех категорий исполнения и процедур реализации или функций управления и обслуживания.
Функциональная система организации производства ГАП охватывает организацию подготовки производства эксплуатации гибкой автоматической системы оперативного управления производством и организацию непосредственных процессов труда исполнителей.
Гибкие производственные системы (ГПС) отличаются пространственной структурой и методами организации (для гибкого модуля - точечная организация для гибкой линии - принцип жесткой и гибкой передачи предмета труда) временной структурой (той или иной степенью свободы формирования номенклатуры запускаемых в производство деталей) а также степенью интеграции основных вспомогательных и обслуживающих процессов в единый производственный процесс.
Техническую базу гибкой автоматизированной системы составляют оборудование с ЧПУ промышленные роботы специальные транспортные средства и автоматизированные системы управления технологическими процессами. Высокая эффективность использования этих дорогостоящих технических средств обеспечивается надлежащей организацией производства. При этом формы и методы организации производственных процессов должны быть приведены в соответствие с технико-экономическими требованиями.
Основными направлениями совершенствования процессов в гибких производственных системах являются:
Производственный процесс в ГПС следует рассматривать как единый комплекс включающий технологические транспортные погрузочно-разгрузочные контрольные и наладочные операции. В качестве основного документа определяющего содержание процессов и работ их последовательность при изготовлении продукции в ГПС и смежных с нею подразделениях используется «Карта производственного процесса». В ней для технологических и других машинных процессов выполняемых в автоматическом режиме указывается шифр оборудования и шифр управляющей программы; для производственных операций выполняемых с участием человека приводится подробное описание работ нормы времени. «Карта производственного процесса» сопровождается оперограммой или сетевым графиком в которых указывается последовательность работ время их опережения и сроки выполнения.
Организация оперативного управления в условиях гибкой автоматизации базируется на календарной регламентации взаимной увязке частичных производственных процессов и ресурсных возможностей каждого подразделения ГПС.
Главной целью автоматизированной системы оперативного управления (АСОУ) является обеспечение согласованного во времени и маршрутно-технологически ориентированном пространстве (цехи участки рабочие места) движения и их частей в данном ГПС. АСОУ должна обеспечить своевременность принятия мер по предупреждению и ликвидации сбоев в ходе производственного процесса.
В соответствии с этими целями в подсистеме оперативного планирования АСОУ решается три блока задач:
В блоке объемного планирования осуществляется построение производственной программы цеха участка и обосновывается объемными расчетами загрузка этих подразделений;
В блоке календарного планирования разрабатываются календарные планы-графики а в блоке оперативного планирования - пятидневные (недельные) и сменно-суточные задания.
При планировании хода производства за основу могут быть приняты интегрированные планы-графики работы производственной системы на различные периоды (месяц декада пятидневка). На их основе составляются пятидневные и сменно-суточные задания по гибким производственным модулям.
Работа подразделений подготовки и обслуживания регламентируется соответствующими графиками обеспечения месячных декадных и пятидневных планов и сменно-суточных заданий. Организация выполнения запланированных работ контроль и регулирование хода производственного процесса оперативный учет и анализ выполнения заданий строятся с ориентацией на выполнение интегрированных планов-графиков обеспечения.
На качественно новом уровне организуется в ГПС система технического и организационного обслуживания. Вся совокупность работ по обслуживанию должна выполняться в рамках автоматизированной системы комплексного регламентированного обслуживания (АСКРО).
В основе построения и функционирования АСКРО лежат следующие принципы: комплексность профилактичность регламентированность автоматичность гибкость (мобильность) оптимальность.
Каждый гибкий производственный модуль обеспечивается комплексом оснастки и инструмента наладкой ремонтом управляющими программами плановой информацией техническим контролем перемещением предметов труда и удалением отходов.
Все виды обслуживания выполняются в строго установленное время в соответствии с графиком обеспечения и обслуживания рабочих мест. Организация непрерывного и предупредительного обслуживания осуществляется с помощью внедрения многоступенчатой подготовки работ по всем функциям обслуживания для обеспечения выполнения конкретных производственных планов (квартальных месячных и декадных планов пятидневных и сменно-суточных заданий). Контроль за ходом работ проводится с помощью подсистемы проверки готовности ГПС входящей в систему оперативного управления. При создании регламентированного обслуживания согласовывается и оптимизируется пропускная способность комплекса технологического оборудования и обслуживающих подразделений определяется состав и размер резервов потребные людские ресурсы.[6]
Анализ технологичности детали.
Под технологичностью конструкции изделия понимается совокупность свойств конструкции изделия проявляемых в возможности оптимальных затрат труда средств материалов и времени при технической подготовке производства изготовлении эксплуатации и ремонте по сравнению с соответствующими показателями однотипных конструкций изделий того же назначения при обеспечении установленных значений показателей качества и принятых условий изготовления эксплуатации и ремонта.
Обработка конструкции на технологичность представляет собой комплекс мероприятий по обеспечению необходимого уровня технологичности конструкции по установленным показателям направлена на повышение производительности труда снижение затрат и сокращение времени на изготовление изделия при обеспечении необходимого его качества. Виды и показатели технологичности приведены в ГОСТ 18831-73 а правила отработки конструкции изделия и перечень обязательных показателей технологичности в ГОСТ 14.201-73. Оценка технологичности конструкции может быть двух видов: качественной и количественной. Качественная оценка характеризует технологичность конструкции обобщенно на основании опыта исполнителя и допускается на всех стадиях проектирования как предварительная. Количественная оценка технологичности конструкции изделия выражается числовым показателем и рациональна в том случае если эти показатели существенно влияют на технологичность рассматриваемой конструкции.[5. Стр. 6]
Качественная оценка технологичности конструкции детали:
- технологический контроль чертежа детали «втулка» дает полное представление о ее конструкции. На чертеже проставлены размеры с допусками и шероховатостью необходимыми для изготовления детали
- деталь имеет удобные и надежные технологические базы в процессе обработки;
- предусмотрена возможность непосредственного измерения большинства заданных на чертеже размеров;
- деталь по форме несложная;
- все поверхности можно обработать универсальными инструментами;
Исходя из вышесказанного данную деталь можно считать технологичной.
Обоснование выбора базирующих поверхностей.
Проектирование любой технологической операции входящей в технологический процесс предполагает разработку теоретической схемы базирования (ТСБ). ТСБ представляет собой расположение опорных точек на базах заготовки. Под базой понимают поверхность (ось точку) принадлежащую заготовке и используемую для базирования. Базы имеют ряд классификаций которые установлены ГОСТ 21495-76: по функциональному назначению (конструкторская технологическая измерительная) по лишаемым степеням свободы (установочная направляющая опорная двойная направляющая двойная опорная) и по характеру проявления (явная скрытая).
Обоснование последовательности обработки поверхностей детали и выбор технологических баз между собой тесно взаимосвязаны и поэтому решаются комплексно .
Для установления последовательности обработки поверхностей детали целесообразно выявить размерные связи с помощью которых определяется относительное положение поверхностей детали и выявить те поверхности относительно которых наиболее строго задано положение большинства других поверхностей детали. Эти поверхности и рекомендуется использовать в качестве технологических баз на большинстве операций технологического процесса если они отвечают требованиям предъявленным к технологическим базам и позволяют полностью обрабатывать деталь с одной установки. При выборе технологических баз необходимо учитывать:
возможность совмещения технологических и конструкторских баз;
возможность сохранения на всех операциях обработки принципа единства баз обеспечивающих заданную чертежом точность детали;
возможность подхода инструмента для обработки поверхностей с наибольшего количества сторон.
Выбрав комплект технологических баз для большинства операций технологического процесса необходимо выбрать технологические базы для обработки детали на первой или первых операциях на которых создаются технологические базы для последующих операций. Эта задача решается несколькими вариантами. Поэтому путем анализа различных вариантов базирования детали выбирается наиболее предпочтительнее с точки зрения обеспечения точности детали при обработке от выбранных баз. Следует помнить что для подобного анализа необходимо прежде всего выявить и четко сформулировать задачи которые решаются при обработке детали. Если несколько вариантов базирования в равной степени обеспечивают решение поставленных задач то выбирают такой при котором технологический процесс проще и экономичнее.
На заготовке детали представляющей собой тело вращения длина которого меньше диаметра шесть опорных точек располагаются следующим образом: три- на торцевой поверхности лишающей заготовку детали 2 степеней свободы вследствие чего эта поверхность является двойной опорной базой.
На рисунке 1 представлена схема базирования заготовки:
Рисунок 1 – Схема базирования заготовки
Плоскость YOZ – установочная база
Т1 а – смещение по оси х
Т2 => – поворот вокруг оси у
Т3γ – поворот вокруг оси z
Центр О – двойная опорная база
Т4 => с – смещение по оси z
Т5 В – смещение по оси у
Плоскость XOZ – опорная база
Т6 λ – поворот вокруг оси х
Так как метод получения заготовки – прокат то есть заготовкой является пруток диаметром 95 мм единственным вариантом базирования заготовки на первых операциях является базирование по цилиндрической поверхности и по торцу. Зажим производится в трехкулачковом патроне. На первых операциях необходимо осуществлять подрезку торца и обработку участка цилиндрической поверхности.
Определение и обоснование метода получения заготовки.
Метод выполнения заготовок деталей машин определяется назначением конструкции детали материалом техническими требованиями масштабом и серийностью выпуска а также экономичностью изготовления. Выбрать заготовку - значит установить способ ее получения наметить припуски на обработку каждой поверхности рассчитать размеры и указать допуски на неточность изготовления. От правильного выбора заготовки зависит трудоемкость и себестоимость обработки.
Для данной детали можно использовать следующие методы получения заготовок: горячая объемная штамповка на молотах и прессах горячая объемная штамповка на горизонтально-ковочных машинах а также получение заготовки из проката.
Наиболее рациональными методами получения заготовки из вышеперечисленных для данной детали с учетом материала массы конфигурации габаритов детали и годовой программы выпуска является метод получения заготовок из проката так как он не требует изготовления штампов пресс-форм и т.п.
Разработка маршрута обработки отдельных поверхностей и полной маршрутной технологии.
Обоснование последовательности обработки поверхностей заготовки ведут с учетом конструктивных особенностей детали и требований к ее качеству состава переходов по обработке поверхностей заготовки и ее базирования в технологическом процессе необходимости термической обработки. Условий организации производственного процесса и других.
В начале технологического процесса с заготовки удаляем наибольшие припуски что способствует перераспределению остаточных напряжений в материале заготовки.
Высокие требования к точности формы относительного положения и размеров поверхностей детали вынуждают обрабатывать заготовку в несколько этапов с применением различных способов обработки. В нашем случае предварительную и окончательную обработку удается выполнить последовательно при одной установке что значительно уменьшает погрешность обработки а также время на обработку.
В конце технологического процесса выполняем промывку и контроль.
Намеченная последовательность обработки поверхностей заготовки позволяет составить маршрут технологического процесса изготовления детали в виде списка переходов с соблюдением последовательности их выполнения.
Технологический маршрут обработки втулки состоит из следующих основных операций:
Установить и закрепить заготовку.
Отрезать заготовку от прутка выдерживая размер 105±1.
Точить торец выдерживая размер3.
Точить поверхность выдерживая размеры 1 6.
Сверлить поверхность выдерживая размеры 34.
Точить поверхность выдерживая размеры 52.
Острые кромки притупить R03.
Снять деталь уложить в тару.
Точить торец выдерживая размер2.
Точить поверхность выдерживая размеры 1 3.
Снять деталь уложить в тару..
Аналитический расчет припусков на поверхность 70h8.
Припуск – слой материала удаляемый с поверхности заготовки в целях достижения заданных свойств обрабатываемой поверхности детали.
Расчетной величиной является минимальный припуск на обработку достаточный для устранения на выполняемом переходе погрешностей обработки и дефектов поверхностного слоя полученных на предшествующем переходе и компенсации погрешностей возникающих на выполняемом переходе.
Промежуточные размеры определяющие положение обрабатываемой поверхности и размеры заготовки рассчитывают с использованием минимального припуска.
Исходные данные. Деталь «Втулка». Технические требования – диаметр 70h8 шероховатость Ra = 125 мкм. Материал детали – Л 68. Общая длина детали – 100 мм. Длина обрабатываемой поверхности – 72 мм. Метод получения заготовки – прокат. Обработка производится в патроне на токарном станке 16К20. Требуется определить межоперационный и общий припуски и диаметральный размер заданной поверхности заготовки.
В графу 2 таблицы 4 записывают элементарную поверхность детали и технологические переходы в порядке последовательности их выполнения.
Заполняем графы 3 4 и 9 по всем технологическим переходам. Данные для заполнения граф 3 4 и 9 взяты из таблиц. [5 П 1.11 и П 1.18 ]
Суммарное значение пространственных погрешностей при отработке наружной поверхности:
где оп – общее отклонение оси от прямолинейности;
к – кривизна профиля сортового проката;
Lз – длина заготовки.
Таблица 4- Расчет припусков на размер
Маршрут обработки поверхности
Допуск по переходам мкм
Предельные размеры мм
Предельные припуски мм
Находим коэффициенты уточнения для:
- чернового точения Ку = 006
- чистового точения Ку = 005
ρ1 = 150 · 006 = 9мкм;
ρ2 = 9 · 005 = 045 мкм.
Данные заносим в графу 5.
Погрешность установки заготовок (графа 6) в трехкулачковом самоцентрирующем патроне при черновом обтачивании у1 =200мкм; при чистовом обтачивании без переустановки – у2 = 0 мкм.
На переходе шлифования обработка производится в центрах т.е. у3 = 0мкм.
Расчет минимального припуска (графа 7) при обработке наружной поверхности проката в патроне производится по формуле:
- при черновом точении:
- при чистовом точении:
В графу 11 записываются размеры по всем технологическим переходам округляя их увеличением до того же знака десятичной дроби с каким задан допуск на размер для каждого перехода.
Наибольшие предельные размеры (графа 10) определяются путем прибавления допуска к округленному минимальному предельному размеру.
Предельные размеры припусков Zi max (графа 12) определяются как разность предельных максимальных размеров и Zi min (графа 13) – как разность предельных минимальных размеров предшествующего и выполняемого переходов.
Для определения общих припусков Z0 min и Z0 max суммируются соответствующие промежуточные припуски на обработку. [5 стр. 15-17]
Основные принципы и обоснование выбора технологического оборудования приспособлений и мерительного инструмента.
Выбор металлорежущего станка для операции определяется методом обработки габаритными размерами заготовок с учетом их конфигурации мощностью необходимой на резание техническими требованиями определяющими точность и шероховатость обработанных поверхностей; производительностью и себестоимостью в соответствии с типом производства. При выборе конкретной модели станка необходимо обязательно учитывать его технические характеристики основные из которых размерные скоростные и силовые.
В связи с этим целесообразно применить в процессе обработки нашей заготовки следующее оборудование:
Пила ленточная- для заготовительной операции.
Токарный станок с ЧПУ 16К20Ф3 – для двух токарных операций.
Моечная машина – для промывки детали
В соответствии с выполнением требуемых операций необходима следующая оснастка:
Трехкулачковый самоцентрирующийся патрон.
На выбор режущего инструмента влияют следующие параметры:
-требования к качеству детали;
-свойства материала обрабатываемой заготовки;
-выполняемая операция или переход;
-возможности и состояние используемого технологического оборудования;
-экономические показатели.
Для обработки латуни предпочтительно применять резцы с пластинками из твердых сплавов серии ВК в соответствии для обработки необходим следующий режущий инструмент:
Резец проходной упорный ВК8
Резец расточной упорный ВК8
В качестве мерительного инструмента при изготовлении детали используется:
Штангенциркуль ШЦ-I
Калибр пробка ∅46Н10
Расчет режимов резания и техническое нормирование.
Расчет режимов резания на наружную цилиндрическую поверхность диаметром 70h8. Шероховатость Ra = 125 мкм. Материал детали – Л 68. Общая длина детали – 100 мм. Длина обрабатываемой поверхности – 72 мм. Метод получения заготовки – прокат. Обработка производится в патроне на токарном станке 16К20Ф3. Режущий инструмент – резец с пластинами из твердого сплава ВК8.
Операция «Токарная».
Переход 1. Точить поверхность 1 предварительно.
Глубина резания – t мм
t = 18 мм (данные берутся из расчета припусков).
S = 10 ммоб. [5 табл. П 2.7)]
Рассчитываем скорость резания – V ммин
Выписываем значения С и показатели степеней х у m. [ 5 табл. П 2.11]
Σв = 750 Мпа С = 182 х = 012 у = 030 m = 023.
Период стойкости инструмента – T = 120 мин.
Находим поправочные коэффициенты
Км – поправочный коэффициент на скорость резания зависящий от материала заготовки;
Кп – поправочный коэффициент на скорость резания зависящий от состояния обрабатываемой поверхности;
Ки – поправочный коэффициент на скорость резания зависящий от режущего инструмента;
Определяем частоту вращения шпинделя – n обмин
Уточняем частоту вращения шпинделя по паспорту и корректируем ее в ближайшую меньшую сторону.
Принимаем n = 250 обмин.
Пересчитываем скорость резания Vф.
Vф – фактическая скорость резания ммин:
Переход 2. Точить поверхность 1 окончательно.
t = 03 мм (данные берутся из расчета припусков).
Назначаем подачу – S ммоб
Выписываем значения С и показатели степеней х у m: [5 табл. П 2.11]
С =182 ; х =012; у = 025; m = 023.
Период стойкости инструмента – Т = 120 мин
Находим поправочные коэффициенты:
Принимаем n = 350 обмин.
Vф – фактическая скорость резания:
2 Техническое нормирование.
Переход 1. Точить наружную поверхность 1 предварительно.
Резец проходной. Угол резца в плане φ = 45.
lр.х = 72 мм – длина рабочего хода инструмента. [5 табл. П 3.17. ]
Lврпер = 18 мм – величина врезания и перебега инструмента.
N = 250 обмин – частота вращения (по расчету режимов резания).
Sоб = 1 ммоб – подача на оборот (по расчету режимов резания).
Вспомогательное время связанное с переходом
Твсп1 = 009 мин [5 табл. П 3.9.]
Переход 2. Точить наружную поверхность 1 окончательно.
lр.х = 72 мм – длина рабочего хода инструмента.
Lврпер = 03 мм – величина врезания и перебега инструмента.
N = 350 обмин – частота вращения (по расчету режимов резания).
Sоб = 07 ммоб – подача на оборот (по расчету режимов резания).
Тосн=0288+0293=0581.
Вспомогательное время связанное с переходом:
Время на обслуживание рабочего места:
В результате выполнения КП по Технологии машиностроения был разработан технологический процесс механической обработки детали «Втулка» который включает в себя: операции токарной обработки. На наиболее точную поверхность осуществлен расчет межоперационных припусков в результате выполненного расчета спроектирована заготовка для данной детали. На часть операций механической обработки определены режимы резания путем аналитического расчета а на остальные – назначены по общим машиностроительным нормативам. Проведено технологическое нормирование операции механической обработки.
В конструкторской части курсового проекта рассмотрено устройство и принцип работы установочного приспособления мерительного инструмента режущего инструмента для токарной операции.
В приложении курсового проекта представлен комплект технологической документации который включает в себя: 1) комплект технологической документации (технологический процесс механической обработки детали «Втулка»); 2) графическая часть (чертеж детали технологической наладки режущего инструмента).
Маталин А.А. Основы технологии машиностроения. М. 1986г.
Горбацевич А.Ф. Курсовое проектирование по технологии машиностроения. Минск. «Высшая школа» 1975г. 288с. с ил.
Нефедов Н.А. Осипов К.А. Сборник задач и примеров по резанию металлов и режущему инструменту. Изд. 3-е перераб. и доп. М Машиностроение 1977г. 288с. с ил.
Гелин Ф.Д. Металлические материалы справ. – Мн.: Высш. шк. 1987. – 368с.
Пачевский В.М. Курсовое проектирование по технологии машиностроения: Учеб. пособие. Воронеж: Воронеж. гос. техн. ун-т 2003. 180 с.
Чертеж.cdw

механической обработки детали "Втулка
Неуказанные предельные отклонения размеров: валов по h14
Наладки.cdw

Расточной упорный резец ВК8
Разработка технологического процесса
механической обработки детали "Втулка
Технологические наладки
Рекомендуемые чертежи
- 24.01.2023
- 24.01.2023
- 28.05.2016
- 23.04.2016