Разработка технологического процесса изготовления и упрочнения передней рубашки




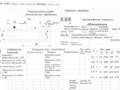
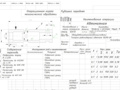
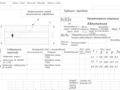
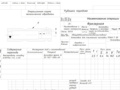
- Добавлен: 24.01.2023
- Размер: 1 MB
- Закачек: 1
Описание
Состав проекта
![]() |
![]() ![]() ![]() ![]() |
![]() ![]() ![]() ![]() |
![]() ![]() ![]() ![]() |
![]() ![]() ![]() ![]() |
![]() ![]() ![]() ![]() |
![]() ![]() ![]() ![]() |
![]() ![]() ![]() |
![]() ![]() ![]() ![]() |
![]() ![]() ![]() ![]() |
![]() ![]() ![]() ![]() |
![]() ![]() ![]() |
Дополнительная информация
Рубашка передняя(О.В.).dwg

лист 4).dwg

лист 7).dwg

лист 5).dwg

лист 3!.dwg

спецификация СБ.dwg

Рубашка передняя (1).dwg

лист 1!.dwg

лист 6).dwg

Рекомендуемые чертежи
- 24.01.2023
- 24.01.2023