Разработка технологического процесса изготовления детали Цилиндр




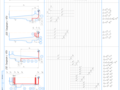
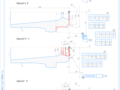
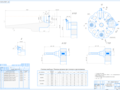
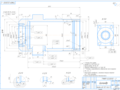
- Добавлен: 24.01.2023
- Размер: 2 MB
- Закачек: 1
Описание
Состав проекта
![]() |
![]() |
![]() ![]() ![]() ![]() |
![]() ![]() ![]() |
![]() ![]() ![]() ![]() |
![]() ![]() ![]() ![]() |
![]() ![]() ![]() ![]() |
![]() ![]() ![]() ![]() |
Дополнительная информация
А1 №4 Карта операционных эскизов.cdw

А2 Чертеж цилиндра 711И09 32.20.012 - 2.cdw

А1 №3 Размерные цепи (Лист 1 Линейные).cdw

А1 №2 Наладка ЧПУ.cdw

Нумерация поверхностей (Чертеж цилиндра).cdw

Рекомендуемые чертежи
- 13.12.2022
- 24.01.2023
- 24.01.2023
- 24.01.2023
- 01.07.2014
Свободное скачивание на сегодня
- 22.08.2014
- 29.08.2014