Разработка технологического процесса изготовления детали - шток




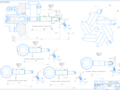
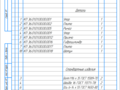
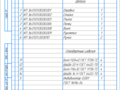
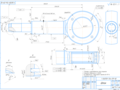
- Добавлен: 24.01.2023
- Размер: 2 MB
- Закачек: 4
Описание
Разработка технологического процесса изготовления детали - шток
Состав проекта
![]() |
![]() |
![]() |
![]() |
![]() ![]() ![]() |
![]() ![]() ![]() |
![]() ![]() ![]() |
![]() ![]() ![]() |
![]() ![]() ![]() |
![]() ![]() ![]() |
![]() ![]() ![]() |
![]() ![]() ![]() |
![]() |
![]() ![]() ![]() |
![]() ![]() ![]() |
![]() ![]() ![]() |
![]() ![]() ![]() |
![]() ![]() ![]() |
![]() |
![]() ![]() ![]() |
![]() ![]() ![]() |
![]() |
![]() ![]() ![]() |
![]() ![]() ![]() |
![]() |
![]() ![]() ![]() ![]() |
![]() |
![]() ![]() ![]() |
![]() ![]() ![]() ![]() |
![]() ![]() ![]() ![]() |
![]() ![]() ![]() ![]() |
![]() ![]() ![]() ![]() |
![]() ![]() ![]() ![]() |
![]() ![]() ![]() ![]() |
![]() |
![]() ![]() ![]() |
![]() ![]() ![]() |
![]() ![]() ![]() |
![]() ![]() ![]() |
![]() ![]() ![]() |
![]() ![]() ![]() |
![]() ![]() ![]() |
![]() ![]() ![]() |
![]() ![]() ![]() |
![]() ![]() ![]() |
![]() ![]() ![]() |
![]() ![]() ![]() |
![]() ![]() ![]() |
![]() ![]() ![]() |
![]() ![]() ![]() |
![]() ![]() ![]() |
![]() ![]() ![]() |
![]() ![]() ![]() |
![]() ![]() ![]() |
![]() ![]() ![]() |
![]() ![]() ![]() |
![]() ![]() ![]() |
Дополнительная информация
ОК040.doc
Оборудование устройство ЧПУ
Обозначение программы
Эмульсон НГЛ ТУ 38-101-547-80
При выполнении операции соблюдать инструкции по технике безопасности
Установить и закрепить заготовку в центрах
Центр 7032-0035 МОРЗЕ 5 ГОСТ 13214-79
Центр 7032-0043 МОРЗЕ 6 ГОСТ 13214-79
Очки О ГОСТ 12.4.013-85
Полировать поверхность под хромирование
Войлочный круг 125 ГОСТ 17620-72
Контролировать размеры: 30 Ra 016
Профилометр 170621 ГОСТ 19300-86
ГОСТ 3.1404-86 Форма 2
ОК1.doc
Оборудование устройство ЧПУ
Обозначение программы
Эмульсон НГЛ ТУ 38-101-547-80
При выполнении операции соблюдать инструкции по технике безопасности
ГОСТ 3.1404-86 Форма 2
ОК015.doc
Горизонтально-фрезерная
Оборудование устройство ЧПУ
Обозначение программы
Эмульсон НГЛ ТУ 38-101-547-80
При выполнении операции соблюдать инструкции по технике безопасности
Установить заготовку в приспособлении
Приспособление Э 250.000
Очки О ГОСТ 12.4.013-85
Фрезеровать поверхность выдерживая размеры 77±13 угол 45°
Фреза 2214-0001 45° ГОСТ 24359-80
Расточить отверстие до 461-062
Насадная расточная оправка 2210-0560
Резец расточной ТУ 2-035-1040-86
ГОСТ 3.1404-86 Форма 2
Зенкеровать начерно отверстие до 4647-025.
Зенкер 621-075 ГОСТ 3231-71 тип 2
Зенкеровать начисто отверстие до 467-01.
Зенкер 621-077 ГОСТ 3231-71 тип 2
Развернуть отверстие начерно выдержав размер 46912-0039.
Развертка машинная насадная 652-029 ГОСТ 1672-80 тип 3
Развернуть отверстие начисто выдержав размер 47012-0025.
Развертка машинная насадная 652-033 ГОСТ 1672-80 тип 3
Фрезеровать канавку 19+01 до 495+025 по контуру выдерживая размер 1075±0215
Фреза дисковая ГОСТ 3755-78
Фрезеровать фаску 06×45° по контуру
Зенковка коническая 2353-0121 ГОСТ 14953-80
Сверлить четыре отверстия 42+013 выдерживая размеры 45±590 62±03 последовательно.
Сверло 2300-7551 42 ГОСТ 10902-77
Зенковать четыре фаски 06×45 в отверстии 42+013 последовательно
Зенковка коническая 2353-0121 ГОСТ 14953-80
Нарезать резьбу в 4 отверстиях М5-6Н выдерживая размер 10+1 последовательно.
Метчик 2620-1123 Н3 ГОСТ 3266-81
Повернуть стол на 180°
Фрезеровать два паза 5+03×12±02 выдерживая размер 6±01 последовательно.
Фреза 2250-0005 Н14 ГОСТ 3964-69
Очистить деталь от стружки
Контролировать размер: 47Js7 495+025 27-052 1075±0215 M592-6Н 215+013 19+014 12±02 Ra 25
Штангенциркуль ШЦ1-160-01 ГОСТ 162-80
Штангенглубиномер ШГ-160 ГОСТ 162-80
Калибр-пробка 8133-0934Js7 ГОСТ 14810-69
Калибр на размер 19+014 ИИ 66.000-04
Нутромер специальный 8146-НА 495+025
Шаблон на размер 215+013
Пробка 8221-0027 6Н ГОСТ 17756-72
Пробка 8221-1027 6Н ГОСТ 17757-72
ОК010.doc
Оборудование устройство ЧПУ
Обозначение программы
Эмульсон НГЛ ТУ 38-101-547-80
При выполнении операции соблюдать инструкции по технике безопасности
Установить и закрепить заготовку в центрах
Очки О ГОСТ 12.4.013-85
Точить ступенчатую поверхность начерно выдерживая размеры 175-043 1985-012 3082+062 5±01
±03 325±015 фаски 2×30° 06×45° угол 45°.
Резец контурный 2525 ГОСТ 20872-80 пластина 02114-100612 Т15К6 ГОСТ 19048-80
Точение получистовое ступенчатой поверхности выдерживая размеры 3024+025 277
ГОСТ 3.1404-86 Форма 2
Точить ступенчатую поверхность начисто выдерживая размеры 3003+01 277
Резец контурный 2525 ГОСТ 20872-80 пластина 02114-100612 Т30К4 ГОСТ 19048-80
Точение тонкое ступенчатой поверхности выдерживая размеры 30 277
Нарезать резьбу М20×15-6g выдерживая размер 30+1
Резец резьбовой 2661-0775 ГОСТ 18885-73
Очистить деталь от стружки
Контролировать размер: 175-043 1985-012 30 5±01 47±03 325±015 М20×15-6g 30+1 Ra 125
Штангенциркуль ШЦ1-160-01 ГОСТ 162-80
Штангенциркуль ШЦ2-400-005 ГОСТ 166-89
Микрометр МК-25-2 ГОСТ 6507-78
Микрометр МК-50-1 ГОСТ 6507-90
Кольцо 8211-0082 6g ГОСТ 17763-72
Кольцо 8211-1082 6g ГОСТ 17764-72
Образец шероховатости Ra 125 ГОСТ 9378-93
ОК005.doc
Фрезерно-центровальная
Оборудование устройство ЧПУ
Обозначение программы
Эмульсон НГЛ ТУ 38-101-547-80
При выполнении операции соблюдать инструкции по технике безопасности
Установить и закрепить исходную заготовку в призме
Очки О ГОСТ 12.4.013-85
Фрезеровать торец выдерживая размер 407±08
Штангенциркуль ШЦ II-400-01 ГОСТ 166-89
Центровать торцы одновременно по форме А 3.15 ГОСТ 14034-74 выдерживая размеры 39+05 307±024
Сверло 2317-0106 ГОСТ 14952-75
ГОСТ 3.1404-86 Форма 2
Очистить деталь от стружки
ОК020.doc
Оборудование устройство ЧПУ
Обозначение программы
Эмульсон НГЛ ТУ 38-101-547-80
При выполнении операции соблюдать инструкции по технике безопасности
Установить и закрепить заготовку в тисках
Тиски 7827-0289 ГОСТ 4045-75
Очки О ГОСТ 12.4.013-85
Зачистить заусенцы и притупить острые кромки на фрезерованных поверхностях
Напильник 2820-0018 ГОСТ 1465-80
Калибровать резьбу М20×15-6G
Плашка 2650-0100 ГОСТ 9740-71
Вороток 6910-0164 ГОСТ 9740-71
ГОСТ 3.1404-86 Форма 2
ОК035.doc
Оборудование устройство ЧПУ
Обозначение программы
Эмульсон НГЛ ТУ 38-101-547-80
При выполнении операции соблюдать инструкции по технике безопасности
Установить и закрепить заготовку в центрах
Центр 7032-0035 МОРЗЕ 5 ГОСТ 13214-79
Центр 7032-0043 МОРЗЕ 6 ГОСТ 13214-79
Очки О ГОСТ 12.4.013-85
Полировать поверхность под хромирование
Войлочный круг 125 ГОСТ 17620-72
Контролировать размеры: 30 Ra 032
Микрометр МК-50-1 ГОСТ 6507-90
Профилометр 170621 ГОСТ 19300-86
ГОСТ 3.1404-86 Форма 2
МК2.doc
Код наименования операции
Обозначение документа
Код наименования оборудования
Наименование детали сб. единицы или материала
МК1.doc
Сталь 45 ГОСТ 1050-88
Код наименования операции
Обозначение документа
Код наименования оборудования
Фрезерно-центровальная
Горизонтально-фрезерная
Введение.docx
Важная роль в ускорении научно-технического прогресса в машиностроении отводится подготовке высоко квалифицированных инженерных кадров освоению ими современных способов изготовления и контроля продукции методик проектирования прогрессивных технологических процессов.
Данный курсовой проект ставит перед собой цель изучение методики разработки технологического процесса изготовления детали - “Диск спиральный” а также проектирования станочного и контрольного приспособлений на базе имеющихся данных. В данном курсовом проекте будут рассмотрены такие вопросы как:
– определение типа производства;
– анализ конструкции и технологичности детали;
– выбор схем базирования и методов обработки поверхностей;
– выбор оборудования;
– расчет и назначение припусков;
– расчет режимов резания и нормирование операций;
– расчет и проектирование технологического оснащения производства и т.д.
Главное условие курсового проекта: обеспечение более высокого уровня изготовления детали по сравнению с существующим на производстве уровнем.
Курсовой проект включает в себя необходимый минимум графического материала по рассмотренным вопросам документацию к чертежам и сам технологический процесс.
КОНТРОЛЬНАЯ.doc
ШЕРОХОВАТОСТЬ ГЛАДКОЙ ЦИЛИНДРИЧЕСКОЙ ПОВЕРХНОСТИ Ф30(-0.020-0.072)- RА0.16
ПРОФИЛОМЕТР 170621 ГОСТ 19300-86
ШЕРОХОВАТОСТЬ ТОРЦОВОЙ ПОВЕРХНОСТИ Ф30(-0.020-0.072)М20*1.5-6G - RА2.5
ОБРАЗЕЦ ШЕРОХОВАТОСТИ RА2.5-ТТ ГОСТ 9378-93
ШЕРОХОВАТОСТЬ ОТВЕРСТИЯ Ф47(+-0.012) - RА2.5
ОБРАЗЕЦ ШЕРОХОВАТОСТИ RА2.5-Р ГОСТ 9378-93
РАЗМЕР ГЛАДКОЙ ЦИЛИНДРИЧЕСКОЙ ПОВЕРХНОСТИ Ф30(-0.020-0.072)
РАЗМЕР РЕЗЬБОВОЙ ПОВЕРХНОСТИ М20*1.5-6G
КОЛЬЦО 8211-0082 6G ГОСТ 17763-72
КОЛЬЦО 8211-1082 6G ГОСТ 17764-72
РАЗМЕР РЕЗЬБОВОЙ ПОВЕРХНОСТИ М5-6Н
ПРОБКА 8221-0027 6Н ГОСТ 17756-72
ПРОБКА 8221-1027 6Н ГОСТ 17757-72
РАЗМЕР ГЛАДКОГО ЦИЛИНДРИЧЕСКОГО ОТВЕРТИЯ Ф47(+-0.012)
КАЛИБР-ПРОБКА 8133-0934 JS7 ГОСТ 14810-69
РАЗМЕРЫ 320(+-0.18) 368(+-0.8)
ШТАНГЕНЦИРКУЛЬ ШЦ II-400-0.05 ГОСТ 166-89
РАЗМЕРЫ КАНАВКИ 1.9(+0.14)
КАЛИБР НА РАЗМЕР 1.9(+0.14) ИИ 66.000-04
НУТРОМЕР СПЕЦ. 8146- НА Ф49.5(+0.25)
ШАБЛОН НА РАЗМЕР 21.5(+0.13)
РАЗМЕРЫ 27(-0.52) 5(+0.3)
ШТАНГЕНЦИРКУЛЬ ШЦ I-160-0.05 ГОСТ 166-89
РАЗМЕРЫ 6(+-0.1) 12(+-0.2) 5(+-0.1)
ШТАНГЕНГЛУБИНОМЕР ШГ-160 ГОСТ 162-90
РАДИАЛЬНОЕ И ТОРЦОВОЕ БИЕНИЕ СОГЛАСНО ЭСКИЗУ
ПРИСПОСОБЛЕНИЕ КОНТРОЛЬНОЕ:
ПРИЗМА II-1-1 ТУ 2-034-812-88
СТОЙКА С-IV ГОСТ 10197-70
ШТАТИВ Ш-III-8 ГОСТ 10197-70
ИНДИКАТОР ИЧ-10 КЛ.Б ГОСТ 577-68
ДОПУСК ПРЯМОЛИНЕЙНОСТИ ПОВЕРХН. Ф30(-0.020-0.072)
ЛИНЕЙКА ЛД 1-125 ГОСТ 8026-75
ЩУП НАБОР №2 ТУ 2-034-225-87
ДОПУСК ПЕРЕСЕЧЕНИЯ ОСЕЙ И ДОПУСК ПЕРПЕНДИКУЛЯРНОСТИ СОГЛАСНО ЭСКИЗУ
ПРИСПОСОБЛЕНИЕ КОНТРОЛЬНОЕ
РАЗНОСТЕННОСТЬ ПРОУШИНЫ Г ПО КОНТУРУ 1 ММ НЕ БОЛЕЕ
МИКРОМЕТР МК-25 ГОСТ 6507-90
КЛЕЙМИТЬ ДЕТАЛЬ СОГЛАСНО ЭСКИЗУ
ЖИДКОСТЬ БЕСКИСЛОТНАЯ
Приспособления для гор-фр. операции.cdw

Приспособление предназначено для обработки штока
Ц63-3405121 на горизонтально-фрезерном станке с ЧПУ.
Остальные Т.Т. по СТБ 1022-96.
Станочное.spw

КП 36.01.01.00.00.002
КП 36.01.01.00.00.005
КП 36.01.01.00.00.009
КП 36.01.01.00.00.0012
КП 36.01.01.00.00.0016
КП 36.01.01.00.00.0017
КП 36.01.01.00.00.0018
Болт М16 х 35 ГОСТ 15589-70
Шайба 16 ГОСТ 11371-78
Ось 6-14 х 55 ГОСТ 9650-80
Винт М12 х 80 ГОСТ 10336-80
Ось 6-8 х 55 ГОСТ 9650-80
Шайба 6 Н ГОСТ 6402-70
Контрольное.spw

перпендикулярности поверхности
отверстия и оси штока
КП 36.01.01.00.00.001
КП 36.01.01.00.00.002
КП 36.01.01.00.00.003
КП 36.01.01.00.00.006
КП 36.01.01.00.00.008
КП 36.01.01.00.00.009
КП 36.01.01..00.0010
Шайба 20 Н ГОСТ 6402-70
Шайба 16 Н ГОСТ 6402-70
Поковка!!.cdw

степень сложности-С2
исходный индекс-12 по ГОСТ 7505-81
Неуказанные штамповочные уклоны-7
Неуказанные радиусы до-2
Допускается частичный срез штамповочных уклонов.
Смещение по поверхности разъёма штампов до 1 мм.
Внешние дефекты согласно ГОСТ 8479-70.
Поковка должна быть очищена от окалины.
Шток.cdw

Покрытие поверхности А-Хтв.30.
На поверхности Г допускаются черноты до 90 %.
Клеймить клеймом ОТК.
Операционные эскизы.cdw

Горизонтально-фрезерная с ЧПУ
отв. центр. А3.15 ГОСТ 14034-74
Карта наладки станка сЧПУ.cdw

Схема движения инструмента ТО1 Установ 1 Переход 1
Схема движения инструмента ТО1 Установ 1 Переход 2
Схема движения инструмента ТО3 Установ 1 Переход 5
Схема движения инструмента ТО1 Установ 1 Переход 4
Схема движения инструмента ТО1 Установ 1 Переход 3
Контрольное приспособление.cdw

Оправку поз. 1 установить в отв.
Разность показаний индикатора на цилиндрических частях
На виде сверху и сбоку магнитная стойка условно не показана.
На виде сверху оправка условно не показана.
Приспособление контрольное
Проверяемые параметры:
Установить изделие в призму поз. 2
Прижать изделие винтом поз. 8.
1,1.doc
Шток Ц63-3405121 входит в состав гидроцилиндра Ц63-3405115 в рулевой трапеции для тракторов МТЗ-252228223022. Выходным звеном является шток который совершает возвратно-поступательные движения. С помощью гидроцилиндра энергия рабочей жидкости преобразуется в механическую энергию перемещения штока относительно корпуса цилиндра. Через шток исполнительный элемент получает поступательное движение. В качестве исполнительного элемента выступает передний мост трактора. Шток предназначен для передачи усилия от поршня на подшипник затем на палец.
Деталь шток состоит из стержня и ушка с отверстием. Деталь имеет несложную конструкцию.
Рассмотрим основные поверхности детали исходя из ее служебного назначения. Для этого пронумеруем все поверхности детали.
Рисунок 1.3- Основные поверхности детали.
Основные конструкторские поверхности применяемые для базирования детали в механизме.
Основными конструкторскими поверхностями являются: поверхность 7.
Вспомогательные конструкторские поверхности применяемые для базирования других деталей в механизме.
Такими поверхностями будут являться: поверхность 45711121316.
Исполнительные поверхности посредством которых деталь выполняет свои функции в механизме: 4712.
Свободные поверхности предназначены для ограничения размера детали и придания ей определённой формы их размер и форма выбирается произвольно. Такими поверхностями являются: 1236891015.
Материал детали - конструкционная углеродистая сталь 45 (ГОСТ 1050-88) широко используется для изготовления различных видов и типоразмеров шестерен коленчатых и распределительных валов шпинделей. работающих в условиях требующих повышенной прочности и износостойкости.
Таблица 1.1 - Химический состав стали 45 (ГОСТ 1050-88).
Таблица 1.2 - Механические свойства стали 45 (ГОСТ 1050-88).
Предел прочнос-ти в МПа
Предел текучес-ти т МПа
Относи-тельное удлинение %
Относи-тельное сужение %
Твердость до термообра-ботки
2.1.1.doc
1 Проектирование станочного приспособления
1.1. Описание конструкции и работы приспособления
Проектируемое приспособление предназначено для фрезерования плоскости штока обработки отверстия 47Js7 сверления четырех отверстий 42 нарезания в них резьбы фрезерования двух пазов. Данное приспособление устанавливается на горизонтально-фрезерный станок с ЧПУ модели 6902ПМФ2.
Приспособление представляет собой плиту на которую устанавливаются: призма стойка с прижимом гидроцилиндр. Для ориентации детали в осевом направлении в конструкции приспособления предусмотрен упор. В качестве упора применена пластина. Для ориентации детали по углу поворота вокруг своей оси в конструкции приспособления предусмотрен откидной упор.
Данный упор необходим для ориентации ушка в вертикальном положении. Второй Закрепление заготовки осуществляется при помощи гидрозажима.
Закрепление заготовки осуществляется следующим образом:
- заготовку устанавливают в призму
- заготовку ориентируют по углу поворота вокруг своей оси с помощью откидного упора ставя уступ в вертикальное положение.
- включают гидроцилиндр который посредством прижима осуществляет зажим заготовки.
1.16.doc
Уточнённый расчёт типа производства производится на основе определения коэффициента закрепления операции:
где n - количество всех различных технологических операций выполняемых в течение года
Р- число рабочих мест необходимых для выполнения производственной программы.
В предыдущем пункте мы определили коэффициенты загрузки оборудования разработанного техпроцесса. Так как на каждой операции он меньше нормативного для среднесерийного производства ( = 08) то станки будем догружать операциями из технологических процессов производства других деталей данного типа. При этом упрощенно считаем что операции из техпроцессов-аналогов загружают станки также как и одноименные операции из проектируемого техпроцесса.
Определим количество операций выполняемых на каждом рабочем месте за год при нормативной загрузке оборудования:
где = 08 – нормативный коэффициент загрузки станков для серийного типа производства;
i – коэффициент загрузки станка на каждой операции.
Операция 005: n1 =08005=17;
Операция 010: n2 =08029=28;
Операция 015: n3 =08063=13;
Операция 035: n4 =0801=8;
Операция 045: n5 =0801=8;
Тогда коэффициент закрепления операций:
Кзо=(17+28+13+8+8)4=101
Для среднесерийного типа производства по нормативам Кзо установлен в пределах 10 20. Так как рассчитанное значение Кзо попадает в этот интервал то можно сделать вывод о том что предварительный выбор среднесерийного типа производства для изготовления требуемого количества деталей в год (20000) верен.
2.2.doc
Данное контрольное приспособление является специальным. Оно предназначено для контроля допуска перпендикулярности поверхности отверстия и оси цилиндрической части штока 30f9.
Контрольное приспособление имеет простую конструкцию. Устанавливать деталь в приспособление удобно. Всё это позволяет правильно и точно производить измерения.
Цилиндрическая часть штока является установочной поверхностью. Деталь устанавливается цилиндрической поверхностью 30f9 в призму позиции 2. Деталь закрепляется в приспособлении при помощи прижатия винтом 8. Оправку 1 устанавливают в отверстие 47Js7 мм. Изделия. К оправке подведен индикатор 5. Измерение производится сначала на левом конце оправки затем на правом после чего показания сравниваются и производится их перерасчет для заданной на чертеже длины.
Для того чтобы контрольное приспособление обеспечивало достаточную точность и правильность контроля требуется чтобы его погрешность была не более 13 допуска на контролируемый параметр.
где i - суммарное значение погрешностей в процессе измерения.
Погрешности в процессе измерения:
б - погрешность базирования;
З - погрешность закрепления;
И - погрешность в результате износа установочных элементов;
пер. мех - погрешность передаточных механизмов;
изм. средства - погрешность средств измерения (индикатора).
Расчет контрольного приспособления на точность
Погрешность базирования самой заготовки будет равна 0 т.к. деталь устанавливается в призму и ось детали будет занимать стабильное положение в процессе всего измерения. Но в нашем приспособлении будет переустанавливаться само измерительное устройство поэтому будем учитывать эту погрешность. Она будет равна допуску прямолинейности плиты на которую устанавливается индикатор который равен 005100;
З = 0 так как в нашем случае не происходит закрепления детали в контрольном приспособлении усилием развиваемым пружиной (2 кг.) можно пренебречь;
И = 0 так как износ оправки не учитывается из-за того что при наладке контрольного приспособления индикатор каждый раз выставляется на «0»;
пер. мех. = 0 так как в конструкции приспособления нет передаточных элементов;
изм. средства = 0001 мм так как в качестве средства измерения используется индикатор многооборотный модели 1МИГП ГОСТ 9696-82 [12] с ценой деления 0001 мм. А так как проводим два измерения то умножаем данное значение погрешности средств измерения на два. В итоге окончательно получаем погрешность средств измерения равную 0002 .
Так как i = 52 мкм ΔПР = 167 мкм то условие выполняется. Значит измерение будет проведено с достаточной точностью.
1,4.doc
Анализ детали на технологичность – комплекс мероприятий по выявлению тех конструктивных факторов которые могут вызвать затруднение при изготовлении или увеличение затрат на изготовление детали.
Основная цель анализа технологичности конструкции обрабатываемой детали - возможное уменьшение трудоемкости и металлоемкости возможность обработки детали высокопроизводительными методами.
Проведём анализ технологичности по следующим критериям:
Оценка технологичности материала детали.
Материал детали – сталь 45 механическая обработка которого не вызывает сложностей при обработке твердым сплавом (коэффициент относительной скорости резания k=10). Эта сталь по сравнению с низкоуглеродистыми имеет более высокую прочность при более низкой пластичности. В связи с этим их следует применять для изготовления небольших деталей или более крупных но не требующих сквозной прокаливаемости.
Доступность всех поверхностей детали для обработки на станках и непосредственного измерения.
Большинство поверхностей детали имеют хороший доступ для обработки на станках и непосредственного измерения. К сложно обрабатываемым поверхностям относится поверхность под подшипник вследствие наличия высокого квалитета.
Простота конструкции наличие поверхностей удобных для базирования и закрепления.
Деталь имеет длинную цилиндрическую поверхность которую удобно базировать в призму. При использовании базирования в призму не соблюдается принцип единства баз.
Жёсткость детали для применения высокопроизводительных методов.
Деталь нежесткая поэтому применение высокопроизводительных методов обработки нецелесообразно. Отношение длины к диаметру превышает 10.
В конструкции штока нет мест резких изменений формы. Убывание диаметральных размеров шеек от середины к концу вала.
Оценка доли обрабатываемых поверхностей в общем количестве поверхностей детали.
Обработке подвергаются все поверхности заготовки кроме наружной поверхности ушка. Отсюда делаем вывод что по данному параметру деталь не технологична.
Унификация размеров с целью исключения специального инструмента.
Все поверхности можно получить путем использования стандартного инструмента кроме поверхности для базирования подшипника для обработки которой используется специальный резец.
Применяемое оборудование.
Для получения детали с требуемой точностью размеров формы взаимного расположения а также величины шероховатости можно применять станки нормального и повышенного класса точности.
С точки зрения получения для неё дешёвой и приближённой по форме и размерам заготовки.
Коэффициент использования металла высок и составляет 81%. По этому параметру деталь технологична.
СОДЕРЖАНИЕ.doc
1 Служебное назначение и конструкция детали
2 Анализ технических условий изготовления детали
3Предварительное определение типа производства (по таблицам)
4Анализ технологичности детали
5Анализ базового технологического процесса
6Выбор метода получения заготовки и разработка её конструкции
7Выбор и обоснование методов обработки поверхностей детали
8Выбор и обоснование технологических баз составление схем базирования
9Выбор и обоснование технологического маршрута
10 Разработка технологических операций(выбор структуры оборудования оснастки)
11 Аналитический расчёт припусков
12 Выявление и расчёт технологической размерной цепи
13 Определение режимов резания по эмпирическим формулам и таблицам
14 Определение норм времени на операции
15Определение необходимого количества оборудования и его загрузка
16 Уточнение типа производства по коэффициенту закрепления операций
Расчёт и проектирование средств технологического оснащения
1 Расчёт и проектирование приспособления для фрезерования плоскости штока
1.1 Описание конструкции приспособления
1.2 Расчёт усилия зажима заготовки
1.3 Расчёт приспособления на точность
1.4 Расчёт приспособления на прочность
2 Расчёт и проектирование контрольного приспособления для измерения перпендикулярности отверстия47 относительно базы А
№ докум. оцонооокуруеркоомрсггааангагндаподокумента
Датаааааааааааааааааааа
1.13.doc
Расчет режимов резания на два перехода производится по эмпирическим формулам по методике [14].
Произведем расчет режимов резания черновой обработки цилиндрической поверхности вала 30f9 на токарной с ЧПУ операции 010.
Глубина резания : t=25мм;
Подача при черновом точении : S=05 ммоб.
Скорость резания при точении:
где Т - период стойкости и показатели степеней находим по таблицам[ ]:
СV = 290; y = 035; m = 02; T = 50 мин.
где KМV – коэффициент учитывающий качество обрабатываемого материала;
KПV – коэффициент учитывающий состояние поверхности заготовки;
KИV – коэффициент учитывающий материал инструмента.
где sB – физический параметр характеризующий обрабатываемый материал;
КГ и nv – коэффициент и показатель степени характеризующие группу стали по обрабатываемости.
KV = 142×08×1 = 1136.
Определяем скорость резания:
Определим частоту вращения:
Принимаем n=1600мин.
Определяем силу резания Рz:
Коэффициенты и показатели степеней определяем по таблицам [ ]:
СР = 300; х = 10; у = 075; n = -015.
где - коэффициенты учитывающие фактические условия резания ().
КМР определяется по формуле:
Определяем мощность затрачиваемую на резание:
Определяем основное время То:
где Sо - оборотная подача обмин;
L – рабочая длина равная сумме длин врезания перебега и рабочего хода.
Произведём расчёт режимов резания чистового развёртывания отверстия в ушке 47Js7 на горизонтально-фрезерной операции с ЧПУ 015.
Глубина резания равная половине припуска на диаметр t=005 мм;
Подача при чистовом развёртывании: при параметре шероховатости поверхности Ra=25 мкм и радиусе при вершине резца 2мм подача sо=105ммоб.
Скорость резанья при развёртывании:
Т – период стойкости инструмента: Т=90мин.
СV=105; q=03; y=065; m=04.
где sB – предел прочности МПа;
Окончательно скорость резания:
Частота вращения развёртки :
Для стандартного диапазона со знаменателем геометрического ряда 126 принимаем n=100 0бмин.
Уточним скорость резания:
Крутящий момент Mкр:
Где -подача на один зуб инструмента равная sz=1056=
Коэффициенты и показатели степеней определяем по таблицам [14]:
СP = 200; у = 075; n = 0;
СР = 200; х = 10; у = 075; n = 0.
Тогда мощность резания:
Произведем расчет основного времени (при сверлении одного отверстия):
l1+l2 =5+7=12 мм - суммарная величина врезания и перебега.
На все остальные операции режимы резания определим по нормативам приводимым в технических справочниках и полученные результаты расчетов режимов резания сведём в таблицу 1.
Таблица 1. - Сводная таблица режимов резания.
Наименование операции или перехода
Фрезерно-центровальная
сверление центровых отверстий
черн. точение 175 мм
черн. точение 315 мм
получист. точение 308 мм
чист. точение 303 мм
тонкое точение 30IT8 мм
нарезание резьбы М2015-6g
Горизонтально-фрезерная
фрезерование плоскости 77±13
Растачивание отверстия 44
Зенкерование черновое 45
Зенкерование чистовое 46
Развёртывание черновое 466
Развёртывание чистовое47
Фрезерование канавку по контуру
Зенкование отверстия
Нарезание резьбы М5-6H
фрезерование паза 5+03
Полирование поверхности 30
1.9.doc
На данном этапе разрабатывается общий план обработки детали определяется содержание операций техпроцесса. При этом заполняются маршрутные карты техпроцесса (приложение).
При составлении маршрута обработки будем пользоваться базовым технологическим процессом а также следует учитывать следующие положения:
-каждая последующая операция должна уменьшить погрешность и улучшить качество поверхности;
-в первую очередь следует обрабатывать те поверхности которые будут служить технологическими базами для следующих операций;
-обработка поверхностей ведётся в последовательности обратной их степени точности;
-не рекомендуется совмещение черновой и чистовой обработки немерным инструментом на одном и том же станке;
-технический контроль намечают после тех этапов обработки где вероятно повышение количества брака перед сложными дорогостоящими операциями а также в конце обработки детали.
Приняв во внимание вышеперечисленное сформулируем особенности технологического маршрута обработки детали “шток”:
-в первую очередь следует обработать искусственные базы так как они будут служить технологическими базами для последующих операций;
-обработка отверстия в ушке штока должна выполняться после точения цилиндрической части штока так как базирование при обработке отверстия осуществляется по поверхностям получаемым на этих операциях;
-обработку ушка будем выполнять перед закалкой ТВЧ так как поверхность ушка располагается вблизи закаливаемой поверхности и образование “частично-закаленных” слоев металла в месте обработки приводит к интенсивному износу и поломке лезвийного инструмента.
На основании вышеперечисленных особенностей можно составить последовательность переходов механической обработки «штока»:
Сверление центровых отверстий с двух сторон.
Обтачивание ступенчатой части штока черновое.
Обтачивание ступенчатой части штока получистовое.
Обтачивание цилиндрической части чистовое.
Обтачивание цилиндрической части тонкое.
Фрезерование плоскости ушка черновое.
Растачивание отверстия ушка черновое.
Зенкерование отверстия ушка черновое.
Зенкерование отверстия ушка чистовое.
Развёртывание отверстия ушка нормальное.
Развёртывание отверстия ушка тонкое.
Фрезерование канавок и фасок черновое.
Сверление четырёх отверстий.
Зенкерование восьми фасок под резьбу.
Нарезание резьбы метчиком.
Фрезерование двух пазов.
Полирование предварительное.
Полирование чистовое.
Учитывая недостатки базового технологического процесса (пункт 1.5) выбранные методы обработки поверхностей (пункт 1.7) и тип производства выберем предварительно тип оборудования:
-точение цилиндрической части штока будем выполнять на токарном станке с ЧПУ что обеспечит высокую производительность и концентрацию операций.
-обработку ушка штока будем производить на горизонтально-фрезерном станке с ЧПУ.
-шлифование цилиндрической поверхности штока будем выполнять на круглошлифовальном станке.
По общим признакам (одинаковое оборудование схемы базирования режущий инструмент и др.) объединим переходы в операции. Выделим следующие операции:
Операция 005 – Фрезерно-центровальная (переход 1-2).
Фрезеровать торец центровать торцы.
Операция 010 – Токарная с ЧПУ (переход 3-6).
Точить ступенчатую поверхность штока нарезать резьбу.
Операция 015 - Горизонтально-фрезерная с ЧПУ (переход 7-17).
Фрезеровать плоскость ушка обработка отверстия ушка сверлить зенкеровать и нарезать резьбу четырёх отверстий. Фрезеровать два паза.
Операция 020 - Слесарная
Зачистить заусенцы и притупить острые кромки на фрезерованных поверхностях.
Операция 025 – Закалка ТВЧ (переход 18).
Закалить цилиндрическую поверхность штока.
Операция 030 - Правка
Править цилиндрическую поверхность штока на прессе.
Операция 035 - Круглошлифовальная (переход 19).
Полировать поверхность под хромирование.
Операция 040 - Хромирование (переход 20).
Хромировать цилиндрическую поверхность штока.
Операция 045 - Круглошлифовальная (переход 21).
Полировать поверхность после хромирования.
Операция 050 - Промывка
Промыть деталь в содовом растворе.
Операция 055 – Контроль приёмочный.
1,5.doc
Получение заготовки методом горячей штамповки в открытых штампах на прессах соответствует предварительно выбранному среднесерийному типу производства по производительности.
В исходном технологическом процессе (ТП) на первой операции 005 выполняется сверление рассверливание и зенкерование отверстия 47±0012 а после неё фрезерование и зацентровка торцов детали что не соответствует принципу однократного использования черновых баз. Чтобы соблюсти данный принцип необходимо изменить последовательность выполнения операций а именно изначально обработать торцы и зацентровать их а затем обработать цилиндрическую ступенчатую поверхность чтобы в будущем можно было базировать деталь в призму или патрон.
Так как предварительно был выбран серийный тип производства то необходимо гидрокопировальные станки на операциях 015 020 заменить на один станок с ЧПУ. При использовании станков с ЧПУ можно спроектировать концентрированные операции за счет объединения отдельных переходов исходного ТП. На токарных операциях при использовании станков с ЧПУ можно сократить номенклатуру используемого инструмента. Так как при использовании станков с ЧПУ можно совмещать черновые и чистовые операции и при том выдержать необходимые размеры шероховатость и допуск формы то на данном станке мы можем совместить следующие операции: 040 045 080 085.
Совместим операции 005 050 065 070 075 на которых обрабатывалось отверстие под подшипник боковая плоскость ушка штока и отверстия под винты в одну которую будем осуществлять на горизонтально-фрезерном станке c ЧПУ за два установа при базировании по длинной цилиндрической поверхности.
В конце ТП полируется цилиндрическая поверхность штока на токарно-винторезном станке 1624М что нецелесообразно так как для осуществления данной операции на этом станке необходима дополнительная техоснастка. Данный станок может применяться в условиях единичного и мелкосерийного производства а в нашем случае мы имеем среднесерийное производство поэтому заменим данный станок на круглошлифовальный.
Результаты анализа сведем в таблицу.
Таблица 1.5 – Результаты анализа исходного техпроцесса.
Содержание операции.
Измерительный инструмент
Вертикально-сверлильная
Сверлить отверстие выдержав размер 25+1;
Рассверлить отверстие выдержав размер 43+025;
Зенкеровать отверстие выдержав размер 44+016;
Патрон 7100-0035 ГОСТ 2675-80
Сверло 2301-0087 25 ГОСТ 10903-77;
Сверло 2301-0146 43 ГОСТ 10903-77;
Нутромер НИ-18-50 ГОСТ 10903-77
Фрезерно-центровальная
Фрезеровать торец выдерживая размер 368±08;
Центровать торцы выдерживая размеры 39+05 307±024;
Сверло 2317-0106 ГОСТ 14952-75
Штангенциркуль ШЦ II-400-01 ГОСТ 166-89
Токарно-копировальная
Точить ступенчатую поверхность выдерживая размеры: 306-016 325±015 225-013 47±03
Резец MWLNR 2525 М10 пластина 02114-100612 Т15К6 ГОСТ 19048-80
Микрометр МК50-1 ГОСТ 6507-90;
Микрометр МК25-2 ГОСТ 6507-78;
Штангенциркуль ШЦ II-400-005 ГОСТ 166-89;
Штангенглубиномер ШГ-160 ГОСТ 162-80
Точить ступенчатую поверхность выдерживая размеры: 1985-012 47±03 175-043 5±01
Фаску 0645 о угол 45 о.
Микрометр МК25-1 ГОСТ 6507-78;
Штангенциркуль ШЦ I-160-005 ГОСТ 166-89;
При биении поверхности А относительно центровых отверстий более 01 мм править поверхность А до биения не более 01 мм
Индикатор ИЧ-10 кл.Б ГОСТ 577-68
Шлифовать поверхность до 303-01
Центр 7032-0029 Морзе 4 ГОСТ 13214-79
Круг ПП 60063305 24А 16-П С2 7 К5 Кл. А ГОСТ 9378-93
Образец шероховатости Ra 125 ГОСТ 9378-93
Нарезать резьбу М2015-6g выдерживая размер 30+1
Вертикально-фрезерная
Фрезеровать поверхности выдерживая размеры: 27-052 77±13
Приспособление фрезерное Э 250.000
Фреза 2214-0001 45 о ГОСТ 24359-80
Горизонтально-фрезерная
Фрезеровать 2 паза 5+0312±02 выдерживая размер 6±01 последовательно.
Головка делительная 7036-0053 ГОСТ 8615-89
Фреза 2250-0005 Н14 ГОСТ 3964-69
Штангенглубиномер ШГ-160 ГОСТ 162-80.
Расточить отверстие 47±0012 до 467+017;
Расточить фаску 07545 о в отверстии47±0012 ;
Расточить вторую фаску 07545 о в отверстии 47±0012 ;
Развернуть отверстие 47±0012;
Расточить 2 канавки 19+014 до 495+025последовательно выдерживая размеры 1075±0215 215+013
Планшайба ПЦ 451.000
Резец 03211-51 Т15К6;
Развёртка ПЦ 683.000;
Нутромер НИ 18-50-1 ГОСТ 868-82;
Калибр-пробка 8133-0934JS7 ГОСТ 14810-69;
Образец шероховатости Ra25 Р ГОСТ 9378-93;
Калибр на размер 19+014 ИИ 66.000-04;
Нутромер специальный 8146 на 495+025; Шаблон на размер 215+013
Сверлить 4 отверстия 42+013 выдерживая размеры 45 о±5 о ; 90 о; 62±03;
Зенкеровать 8 фасок 0645 о в отверстиях 42+013.
Сверло 2300-7551 42 ГОСТ 10902-77
Зенковка 2353-0121 ГОСТ 14953-80
Нутромер НИ6-10 ГОСТ 868-82.
Нарезать резьбу в 4 отверстиях М5-6Н выдерживая размер 10+1
Метчик 2620-1123 Н3 ГОСТ 3266-81
Пробка 8221-0027 6Н ГОСТ 17756-72
Шлифовать поверхность до
Центр 7032-0029 Морзе 6 ГОСТ 13214-79
Образец шероховатости Ra04 ШЦ ГОСТ 9378-93.
Подрезать торец выдерживая размер 320±018;
Точить фаску выдерживая размеры 2 и 30 о на поверхности 30.
Резец 2112-0057 Т15К6 ГОСТ 18880-73;
Резец 2102-0079 Т15К6 ГОСТ 18877-73
Штангенциркуль ШЦ 2-400-005 ГОСТ 166-89;
Образец шероховатости Ra25 ГОСТ 9378-93.
Токарно-винторезная Полировать поверхность под хромирование до 30
Центр 7032-0035 Морзе 5 ГОСТ 13214-79
Шкурка шлифовальная 2 83050 С2 МА ГОСТ 5009-82
Образец шероховатости Ra032 ГОСТ 9378-93.
Полировать поверхность до 30.
Образец шероховатости Ra016 ГОСТ 9378-75;
Окончательный контроль размеров детали
Профилометр 170621 ГОСТ 19300-86;
Образец шероховатости Ra25 –ТТ ГОСТ 9378-93;
Образец шероховатости Ra25 –Р ГОСТ 9378-93;
Пробка 8221-0027 6Н ГОСТ 17756-72;
Нутромер специальный 8146 на 495+025
1.11.doc
Произведём расчёт припусков расчётно-аналитическим методом на две поверхности а так же построим для них схемы расположения припусков и допусков.
–заготовка – поковка материал – Столь 45;
–точность размеров соответствует 17 кв.;
–деталь устанавливается в центрах вращение задаётся поводком;
Необходимо получить размер . Параметры поковки 17 кв. Rz=150 мкм; h = 250 мкм.
Составим технологический маршрут получения поверхности 30f9 с указанием Rz и h по переходам:
-ый переход-обтачивание черновое (IT14 Rz=100 мкм; h=100 мкм);
-ой переход- обтачивание получистовое (IT12 Rz=50 мкм; h=50 мкм);
-ий переход- обтачивание чистовое (IT10 Rz=25 мкм; h=25 мкм);
-ый переход- обтачивание тонкое (IT8 Rz=5 мкм; h=5 мкм).
-ый переход- термообработка (IT9 Rz=5 мкм; h=0 мкм).
-ый переход- полирование предварительное (IT9 Rz=25; h=0 мкм);
-ый переход- полирование чистовое (IT9 Rz=063; h=0 мкм).
где Rz – высота неровностей профиля по 10 точкам (шероховатость поверхности)
Так как размер формируется уже на четвёртом переходе а термообработка и полирование существенно не повлияют на качество поверхности то расчёт будем вести только на первые четыре перехода.
Определим значения пространственных отклонений для заготовки.
где rсм- смещение оси шейки относительно общей оси
rкор – коробление штока; rкор = К× l;
Δк – удельная кривизна заготовки Δк=4мкммм (по табл. П16 [5])
l – длина заготовки (здесь l=L2=4092=2045 мм так как максимальная кривизна возможна посреди штока).
rкор = 4×2045= 818 мкм
Рассчитаем погрешность центрирования:
где sз – допуск на диаметральный размер поверхности используемой в качестве базовой на фрезерно-центровальной операции. В нашем случае sз =2 мм.
Найдём погрешность заготовки:
Остаточное пространственное отклонение по переходам определяем по формуле:
где Ку – коэффициент уточнения формы.
-ый переход-обтачивание черновое ρ1 =006·ρзаг=006·1490=90 мкм;
-ой переход- обтачивание получистовое ρ2 =005·ρ1=005·90=45 мкм;
-ий переход- обтачивание чистовое ρ3 =004·ρ2=004·45=0 мкм;
-ый переход- обтачивание тонкое ρ4 =003·ρ3=003·0=0 мкм.
Погрешность установки eу = 0 т.к. базирование производится по центровому отверстию в центрах с поводком.
Расчёт минимальных припусков.
где i - выполняемый переход.
-й переход (обтачивание черновое)
-й переход (обтачивание получист.)
-й переход (обтачивание чистовое)
-й переход (обтачивание тонкое)
Расчётный размер диаметра вала dР вычислим начиная с конечного минимального чертёжного размера путём последовательного прибавления минимального припуска каждого предыдущего перехода:
-й переход dР тонк. точ..= 29928 мм;
-й переход dР чист. точ..= 29928 +2×005 = 30028 мм;
-й переход dР получист. точ..= 30028 +2×0105 = 30238 мм;
-й переход dР чернов. точ..= 30238 +2×0290 = 30818 мм;
Заготовка dР заг..= 30818+2×189 = 346 мм.
Назначаем допуски на технические переходы по таблице [2 40] а допуски на заготовку по ГОСТ 2590 – 71:
заготовка – 2000 мкм;
-й переход – 620 мкм;
-й переход – 250 мкм;
-й переход – 100 мкм;
-й переход – 39 мкм;
Предельный размер dmin определяем округляя dp до большего значения в пределах допуска на данном переходе а dmax определяем прибавляя к dmin допуски соответствующих переходов:
заготовка: dm dmax.заг = 346+2000 = 366 мм.
Максимальное предельное значение припусков 2×Zmax.ПР. находим как разность наибольших предельных размеров выполняемого и предшествующего переходов а минимальные значения2×Zmin.ПР – как разность наименьших предельных размеров выполняемого и предшествующих переходов.
Общий минимальный припуск находим как сумму минимальных промежуточных припусков а общий максимальный – как сумму максимальных припускав:
Общий номинальный припуск находим по формуле:
где HЗ – нижнее отклонение заготовки по ГОСТ 2590 – 71
HД – нижнее отклонение детали по чертежу.
тогда номинальный диаметр заготовки:
Проверяем правильность произведённых расчётов:
-й переход: 5162-3782 = 138 мкм 20-062 = 138 мкм
-й переход: 095-058= 037 мкм 062-025 = 037 мкм
-й переход: 036-021 = 015 мкм 025-01 = 015 мкм
-й переход: 0161-01 = 0061 мкм 01-0039 = 0061 мкм
Общий припуск: 6633 -4672 = 1961 мкм 20-004 = 196 мкм
Проверка правильна значит расчёты межоперационных припусков произведены правильно. Все расчёты параметров припусков приведём в таблицу.
Таблица 1. – Параметры припусков на размер 30мм
Технологические переходы обработки поверхности 30
Элементы припуска мкм
Расчётный припуск 2Zmin мкм
Расчётный размер dp мм
Допуск на размер d мкм
Предельный размер мм
Предельные значения припусков мм
-й переход (черновое точение)
-й переход (получистовое точение)
-й переход (чистовое точение)
-й переход (тонкое точение)
Рисунок 1. - Схема графического расположения припусков и допусков на обработку поверхности 30 мм.
Выберем технологический маршрут обработки отверстия
и определим величины Rz и h по переходам:
Параметры поковки 17 кв. Rz=150 мкм; h = 250 мкм.
Технологический маршрут состоит из пяти переходов:
Растачивание черновое ( Rz=60 мкм; h=50 мкм);
Зенкерование черновое (IT12 Rz=50 мкм; h=50 мкм);
Зенкерование чистовое (IT10 Rz=40 мкм; h=40 мкм);
Развёртывание нормальное (IT8 Rz=10 мкм; h=20 мкм);
Развёртывание точное (IT7 Rz=5 мкм; h=10 мкм);
Δк – удельная кривизна заготовки Δк=3мкммм (по табл. П16 [5])
l – длина заготовки (здесь l=180 мм так как максимальная кривизна возможна у края штока).
rкор = 3×180= 540 мкм
– отклонение заготовки при базировании которое равно половине допуска на размер от базы. =800 мкм.
-ый переход- растачивание черновое ρ1 =006·ρзаг=006·1190=72 мкм;
-ой переход- зенкерование черновое ρ2 =005·ρ1=005·72=4 мкм;
-ий переход- зенкерование чистовое ρ3 =004·ρ2=004·4 0 мкм;
При нормальном развёртывании и точном развёртывании ρост настолько малы что в расчётах ими можно пренебречь.
Погрешность установки детали на выполняемом переходе определяется по формуле:
где - погрешность базирования которая на всех переходах равна нулю.
- погрешность закрепления заготовки в приспособлении.
=0 так как у нас применяется гидравлическое зажимное устройство обеспечивающее постоянство зажимной силы.
- погрешность позиционирования режущего инструмента на станке которая в нашем случае равна дискретности станка:
Полученные Rzi hi i и ρi-1 заносим в таблицу.
Расчёт минимальных припусков
-й переход (растачивание черновое)
-й переход (зенкерование черновое)
-й переход (зенкерование чистовое)
-й переход (развёрт. нормальное)
-й переход (развёртывание точное)
Расчётные размеры определяем начиная с конечного максимального чертёжного размера последовательным вычитанием 2Zi min каждого технологического перехода:
-5-й переход (развёртывание точное):
DР5 =47012-01 =46912 мм;
-4-й переход (развёртывание нормальное):
DР4 =46912-02=46712 мм;
-3-й переход (зенкерование чистовое):
DР3 =46712-024=46472 мм;
-2-й переход (зенкерование черновое):
DР2 =46472-037=46102 мм;
-1-й переход (растачивание черновое):
DР1 =46102-318=42922 мм.
Предельные размеры Dmaxi определяем округляя DРi до точности допуска в меньшую сторону а Dmini определим вычитанием из Dmaxi допусков соответствующих технологических переходов:
Допуск заготовки определим по ГОСТ 26645-85.
-заготовка: DЗmax=429 мм DЗmin=429-2=409 мм.
Минимальные предельные значения припусков ZiminПР определим как разность наибольших предельных размеров выполняемого и предшествующего переходов а максимальные значения ZimaxПР - как разность наименьших предельных размеров:
-5-й переход: 2Z5minПР=47012-46912=01 мм 2Z5ma
-4-й переход: 2Z4minПР=46912-467=0212мм 2Z4ma
-3-й переход: 2Z3minПР=467-4647=0230 мм 2Z3ma
-2-й переход: 2Z2minПР=4647-461=037 мм 2Z2ma
-1-й переход: 2Z1minПР=461-429=32 мм 2Z1maxПР=4548-409=458 мм.
Предельные значения общих припусков 2Z0minПР и Z0maxПР определим суммируя промежуточные припуски:
Z0min=01+0212+0230+037+32=4112 мм.
Общий номинальный припуск Z0НОМ находим по формуле:
Z0НОМ=2Z0min + ВЗ - ВД= 4112+1400-12=4700 мкм=55 мм
где ВЭ и ВД - соответственно верхние отклонения заготовки и готовой детали мкм.
Зная значение 2Z0НОМ находим номинальный размер заготовки:
Dном ЗАГ= Dном Д - 2Z0НОМ=47-55=415 мм.
Проверим правильность произведённых расчётов по формулам:
ZПРimax- 2ZПРimin=Di-1 – Di
Z0max- 2Z0min=DЗ - DД
Для нашего случая имеем:
-5-й переход: 114-100=39-25 т.е 14=14;
-4-й переход: 273-212=100-39 т.е 61=61;
-3-й переход: 380-230=250-100 т.е 150=150;
-2-й переход: 740-370=620-250 т.е 370=370;
-1-й переход: 4580-3200=2000-620 т.е 1380=1380;
общий припуск: 6087-4112=2000-25 т.е. 1975=1975.
Следовательно расчёты межоперационных припусков произведены правильно.
Все расчёты параметров припусков заносим в таблицу.
Таблица 1. – Параметры припусков на размер 47±0012мм
Технологические переходы обработки поверхности 47±0012
-й переход (растачивание черновое)
-й переход (зенкерование черновое)
-й переход (зенкерование чистовое)
-й переход (развёртывание нормальное)
-й переход (развёртывание точное)
Рисунок 1. – Схема графического расположения припусков и допусков
на обработку отверстия ф47±012 мм.
1.15.doc
Для серийного типа производства необходимое количество станков S определяется по формуле:
Тшт.к.- штучно-калькуляционное время обработки изделия мин;
F -действительный годовой фонд времени работы оборудования час;
Кв = 11 13 – коэффициент выполнения норм времени. Кв = 12.
Коэффициент загрузки оборудования:
где: Sпр—принятое количество станков.
На основании рассчитанных коэффициентов строим график загрузки оборудования.
Рисунок 1. – График загрузки оборудования.
1,3.doc
Годовой объём выпуска деталей «Шток» равен 20000Используя массу как меру трудоемкости изготовления детали по годовому объёму выпуска и ее массе определим предварительно тип производства.
Масса детали – 227кг.
Годовой выпуск - 20000шт.
Тип производства – среднесерийное.
Таблица 1.3 - Тип производства
Предварительный тип производства
В дальнейшем тип производства будет уточнен по коэффициенту закрепления операций (когда последний будет рассчитан).
1,7.doc
При назначении метода обработки следует стремиться к тому чтобы одним и тем же методом обрабатывалось возможно большее количество поверхностей заготовки что дает возможность разработать операции с максимальным совмещением обработки отдельных поверхностей сократить общее количество операций длительность цикла обработки повысить производительность и точность обработки заготовки.
Выбор и обоснование методов обработки проведем для наиболее ответственных поверхностей. Внутреннее отверстие ушка 47±0012 мм что соответствует полю допуска Js7 будем получать растачиванием а окончательную обработку произведем чистовым развёртыванием (обоснование выбранных методов описано ниже). Обоснование выбора методов обработки будем производить на основе требуемых величин уточнения КУ рассчитанных по допускам линейных размеров соответствующих поверхностей.
При выборе методов обработки будем пользоваться справочными таблицами экономической точности обработки в которых содержатся сведения о технических возможностях различных методов обработки.
Выберем методы обработки отверстия 47Js7 ( Ra25):
- растачивание черновое(IT14);
- зенкерование черновое (IT12);
- зенкерование чистовое (IT10);
- развёртывание нормальное (IT8);
- развёртывание точное (IT7);
Так как 47 мм - достаточно небольшой диаметр то для его обработки рационально в условиях серийного производства применить осевой инструмент вместо резцов так как осевой инструмент является более производительным тем более что в дальнейшем в отверстии будем фрезеровать еще две внутренних цилиндрических поверхность 495 мм и шириной 19 мм нарезаются фаски.
Требуемый коэффициент уточнения:
где КУ—требуемая величина уточнения;
dзаг—допуск размера заготовки;
dдет—допуск размера детали.
Расчетная величина уточнения по выбранному маршруту обработки:
где К1 К2 Кn—величины уточнения по каждому переходу или операции при обработке рассматриваемой поверхности.
Точность на черновом переходе обработки сталей обычно повышается на 1 3 квалитета размерной точности. Точность на каждом чистовом и отделочном переходе при обработке сталей повышается на 1 2 квалитета точности. Единая система допусков и посадок ЕСДП построена так что для одного интервала номинальных размеров допуски в соседних квалитетах отличаются в 16 раз. Поэтому расчетные величины уточнений для сталей будут равны:
К = 16 163 = 16 41 – для черновой обработки;
К = 16 162 = 16 256 – для чистовой обработки.
Так как соблюдается условие Ку.расч. ≥ КУ значит требуемая точность будет обеспечиваться выбранными методами обработки.
Выберем методы для обработки цилиндрической поверхности штока. Необходимо получить размер 30f9 мм. (IT9 Ra016):
- обтачивание черновое(IT14);
- обтачивание получистовое (IT12);
- обтачивание чистовое (IT10);
- обтачивание тонкое (IT8).
Выбираем такие методы обработки т.к. точение наиболее дешевый метод обработки не требует специального инструмента и оборудования и позволяет получить требуемый квалитет размерной точности. Окончательно требуемый размер получаем полированием т.к. необходимо обеспечить шероховатость поверхности Ra016 а также высокий допуск прямолинейности поверхности указанный на чертеже детали а тонким точением это сделать невозможно.
Так как соблюдается условие Ку. расч. ≥ Ку значит требуемая точность будет обеспечиваться выбранными методами обработки.
Выбранные методы сведем в таблицу.
Таблица 1. - Выбор методов обработки.
Внутреннее цилиндрическое отверстие ушка 47Js7
Растачивание черновое;
Зенкерование черновое;
Зенкерование чистовое;
Развёртывание нормальное;
Развёртывание точное.
Цилиндрическая поверхность штока
Обтачивание черновое;
Обтачивание получистовое;
Обтачивание чистовое;
Обтачивание черновое.
Фрезерование черновое.
Расстояние от оси ушка до торца штока 320Js11
Обтачивание получистовое.
Расточка отверстия 495H12
Черновое фрезерование
Отверстие с резьбой М592
Зенкерование под резьбу;
Нарезание резьбы метчиком.
1,2.doc
Исходя из служебного назначения детали проведём анализ технических условий её изготовления.
Самая точная поверхность детали выполняется по 7 квалитету - это диаметр отверстия в которое устанавливается подшипник. К нему предъявляются требования по перпендикулярности и пересечению осей а также отверстие развёртывают под подшипник с шероховатостью Ra 25. Данные условия соответствуют правильным техническим требованиям.
Также высокие требования предъявляются к поверхности 30f9 на которую назначается также допуск прямолинейности. Для повышения физических свойств поверхностного слоя эту поверхность детали подвергают закалке ТВЧ на глубину 15 мм до 40 HRCэ. Также её подвергают хромированию которое увеличивает износостойкость трущихся поверхностей защищает их от коррозии а также является способом защитно-декоративной отделки. Для увеличения срока службы уплотнительных элементов поверхность подвергают полировке до хромирования и после в результате чего получаем шероховатость Ra 016.
При работе гидроцилиндра шток испытывает нагрузки различного характера: сжатие растяжение изгиб. Для того чтобы лимитировать эти значения на чертеже проставлены допуски на радиальное биение торца относительно цилиндрической поверхности так как при несоблюдении данного допуска формы может произойти заклинивание штока в гидроцилиндре что вызовет повышенные нагрузки на шток.
Для защиты от загрязнения подшипника на шток устанавливается пыльник который крепится при помощи винтов. Для отверстий под винты назначается позиционный допуск для того чтобы ограничить отклонения в расположении центров крепежных отверстий и обеспечить так называемую «собираемость» резьбового соединения. Этот допуск задают только в том случае когда отверстия для винтов сверлят независимо друг от друга в приспособлениях или на станках с числовым программным управлением.
Заготовка изготавливается из стали 45 методом горячей объёмной штамповки на КГШП в открытых штампах. Класс точности поковки в базовом техпроцессе принят Т5 но для штамповки на КГШП для открытых штампов можно принять T4 что позволит уменьшить припуски на обработку и соответственно увеличить КИМ.
2.1.2.doc
Расчет сил зажима сводится к решению задачи статики на равновесие твердого тела под действием внешних сил. Величина сил зажима определяется из условия равновесия всех сил при полном сохранении контакта технологических баз обрабатываемой заготовки с установочными элементами приспособления и невозможности ее сдвига или поворота в процессе обработки.
В рассчитываемом нами приспособлении выполняется большое количество различного рода видов обработки а для расчета диаметра гидроцилиндра необходимо выбрать метод с самыми большими силами резания и моментами. В нашем случае данным методом является растачивание отверстия так как при этом удаляется наибольшее количество припуска.
Условия установки и закрепления детали в приспособлении дают возможности считать приспособление на условие отрыва. Так же есть возможность проворота заготовки вокруг своей оси. Поэтому будем вести расчет заготовки на проворот вокруг своей оси под действием составляющей силы резания Рx и на условие опрокидывания заготовки под действием составляющей силы резания Рz.
Рисунок 2.1 - Действие силы Pz
Запишем уравнение равновесия моментов (без учета веса заготовки):
где Q—сила зажима Н;
Рz— сила резания при растачивании Рz=950 Н
k - коэффициент запаса ;
а=120 мм - плечо силы зажима Q;
b=75 мм - плечо силы резания Рz
где k0 - гарантированный коэффициент запаса;
k1 - коэффициент учитывающий возрастание сил обработки при затуплении инструмента;
k2 - коэффициент учитывающий неравномерность сил резания из - за непостоянства снимаемого при обработке припуска;
k3 - коэффициент учитывающий изменение сил обработки при прерывистом резании;
k4 - коэффициент учитывающий непостоянство развиваемых приводами сил зажима;
k5 - коэффициент учитывающий непостоянство развиваемых сил зажимных устройств с ручным приводом;
k6 - коэффициент учитывающий неопределенность положения мест контакта заготовки с установочными элементами и изменение в связи с этим моментов трения противодействующих повороту заготовки на базовой плоскости;
k = 19×17×1×1×1×1×1 = 324
Рисунок 2.2- действие силы Рx
r=15-радиус заготовки мм;
f1=f2=015- коэффициенты трения заготовки.
Из приведенных выше расчетов видно что сила зажима необходимая для того что бы избежать проворот заготовки выше силы требуемой для избежания опрокидывания заготовки поэтому последующие расчеты приведем для силы РX = 4290 Н
Рассчитаем диаметр гидроцилиндра необходимого для создания силы зажима Q.
Определяем диаметр цилиндра D:
Т.к. рабочей является безштоковая полость то:
где p=5 МПа-давление эмульсии в гидроцилиндре;
Принимаем следующие параметры гидроцилиндра:
Материал гидроцилиндра – сталь 40;
Диаметр гидроцилиндра dц =40 мм;
Диаметр штока гидроцилиндра dш =10 мм.
2.1.4.doc
Рассчитаем на прочность опасное звено приспособления. Из рассмотрения данного приспособления можно прийти к выводу что наиболее нагруженными деталями является: резьба.
Резьба работает на смятие она изготовлен из стали 40Х.
Расчет на смятие проводим по формуле :
где : F - сила действующая на резьбу винта и гайки F =4290 Н ;
d2 =15026 мм- средний диаметр резьбы винта и гайки мм. ;
h=13 мм- высота резьбы;
z=5- число рабочих витков мм;
[см] – допускаемое напряжение при смятии принимается обычно в 2 — 25 раза больше основного допускаемого напряжения на растяжение и сжатие [см] = 200 Нмм2.
Тогда необходимый размер опасного сечения :
Полученное напряжение смятия полностью удовлетворяет условию износостойкости ходовой резьбы по допустимым напряжениям смятия.
2.1.3.doc
Цель расчета приспособления на точность заключается в определении требуемой точности изготовления приспособления по выбранному точностному параметру и задании допусков размеров деталей и элементов приспособления.
Расчет точности изготовления приспособления из условия обеспечения размера 47±0012 мм.
Определяется погрешность базирования.
Для данного случая погрешность базирования составит:
Определяется погрешность закрепления. Для данного случая:
З = 0 мм так как заготовка находится в призме и сила закрепления направлена перпендикулярно призме;
Определяется погрешность установки приспособления на станке.
Выявляется погрешность от перекоса (смещения) инструмента.
Так как в приспособлении отсутствуют направляющие элементы: П = 002мм;
Определяется погрешность от изнашивания установочных элементов. Изнашивание призмы можно определить по формуле:
где: - постоянная зависящая от вида установочных элементов и условий контакта = 0002 ;
N - количество контактов заготовки с опорой за год
После подстановки получим :
и = 0002×20000 = 40 мкм.;
Погрешность от изнашивания установочных элементов принимаем: = 004 мм
При этом в ТУ на эксплуатацию приспособления указать что проверку приспособления и ремонт (замену) установочных элементов необходимо производить 2 раза в год.
Определяется экономическая точность обработки. Для принятых условий (заготовка из стали растачивание 47 мм точность по IT7 ) находится экономическая точность = 0025 мм.
Принимаются значения коэффициентов и определяется погрешность изготовления приспособления ПР.
Коэффициент учитывающий отклонение рассеяния значений составляющих величин от закона нормального распределения : kт = 1.1.
Коэффициент учитывающий уменьшение предельного значения погрешности базирования при работе на настроенных станках: kт1=08.
Коэффициент учитывающий долю погрешности обработки в суммарной погрешности вызываемой факторами не зависящими от приспособления : kт2 = 06 .
Допуск на изготовление детали = 0024 мм.
Определяем погрешность изготовления приспособления ПР :
ПР = - kт× (kт1*б)2 + З2 + У2 + П2 + И2 + ( kт2 * )2
ПР = 0 24 - 11×(08×0)2 + 0 2 + 0152 + 0022 + 0042 + (06×0025)2 = 0027 мм. ;
Таким образом ПР = 0027 мм.
1,8.doc
Выбор баз для механической обработки производим с учётом достижения требуемой точности взаимного расположения поверхностей детали по линейным и угловым размерам обеспечения доступа инструментов к обрабатываемым поверхностям.
В процессе обработки вала предлагаем использовать следующие схемы базирования:
Чистовыми базами на дальнейших операциях механической обработки будут служить искусственные технологические базы в виде центровых отверстий. Установка детали в центра на токарных и шлифовальных станках позволяет обеспечить доступ к большинству обрабатываемых поверхностей штока. При использовании центровых отверстий можно соблюдать принцип постоянства технологических баз на большинстве операций технологического процесса обработки штока. При токарной шлифовальной обработке наружного контура штока будем базировать его в центрах с поводком (причём передний центр будет плавающий). Такая схема базирования позволяет совместить измерительную и технологическую базы.
Рисунок 1.8.1 - Схема базирования при обработке цилиндрической поверхности штока.
При обработке отверстия ушка его плоскости и отверстий базирование будем осуществлять по начисто обработанной цилиндрической поверхности штока путём устанавливания с помощью двух равномерно-сходящихся призм упора и доработки по торцу посредством упора и по одной из плоскостей ушка. Данная обработка осуществляется при помощи откидного опора. Данный метод базирования будем использовать также для обработки шлифованием длинной цилиндрической поверхности.
Рисунок 1.8.2 - Схема базирования при обработке отверстия ушка плоскости штока и отверстий под винты.
При обработке искусственных баз происходит формирование чистовых баз которые используются затем при дальнейшей обработке других поверхностей детали. Так как обработанных поверхностей на этой стадий еще нет произведем выбор комплекта черновых баз.
Наиболее удобной установочной базой для обработки искусственных баз является поверхность цилиндрическая поверхность штока так как она наиболее развита и позволяет обработать торец штока и чистовые базы принятым методом. Заготовку закреплять будем в две равномерно сходящихся призмы.
Рисунок 1.8.3 - Схема базирования при обработке торца штока и центровых отверстий.
1,6.doc
Выбор методов получения исходной заготовки оказывает большое значение на решение задачи экономии металла. При выборе методов получения исходных заготовок следует учитывать потери металла связанные с этими методами. Так как при выборе метода получения заготовки важнейшими критериями являются стоимость и коэффициент использования материала.
Заготовкой для получения детали в базовом варианте является поковка получаемая штамповкой на кривошипных горячештамповочных прессах в открытых штампах. Этот метод получения заготовки имеет высокую производительность и используется в серийном и массовом производстве. Точность линейных размеров поковки полученной штамповкой на КГШП в открытых штампах соответствует примерно 15-17 квалитету точности. В качестве альтернативного метода получения заготовки будем рассчитывать тот же метод что и в базовом техпроцессе но класс точности поковки примем T4 и изменим конфигурацию получаемой поковки убрав напуск на конце стержневой основы поковки.
Назначим припуски на обработку по ГОСТ 7505-89 .
Штамповочное оборудование – КГШП (штамповка в открытых штампах)
Исходные данные по детали:
1 Материал сталь 45 по ГОСТ1050-88.
Исходные данные для расчета:
1 Класс точности принимаем Т4 (т.к. основное деформирующее оборудование: кривошипный горячештамповочный пресс технологический процесс: открытая штамповка)
2 Группа стали М2 (т.к. сталь поковки среднеуглеродистая)
3 Степень сложности С2 (т.к. отношение массы поковки к массе геометрической фигуры в которую вписывается форма поковки равняется 037)
Конфигурация поверхности разъема – плоская.
Принимаем исходный индекс 12.
Припуски и кузнечные напуски:
1 Основные припуски на размеры мм:
– диаметр 30 мм и чистота поверхности 125;
– диаметр 47 мм и чистота поверхности 125;
– диаметр 78 мм и чистота поверхности 125;
– диаметр 20 мм и чистота поверхности 125;
– длина 320 мм и чистота поверхности 125;
– длина 38 мм и чистота поверхности 125;
– длина 48 мм и чистота поверхности 125;
– толщина 27 мм и чистота поверхности 125.
2 Дополнительные припуски учитывающие:
смещение поверхностей разъема штампа – 03мм;
отклонение от плоскостности – 05мм;
3 Штамповочный уклон:
на наружной поверхности – не более 50 принимается 50;
на внутренней поверхности – не более 70 принимается 70;
Размеры поковки и их допускаемые отклонения:
1 Размеры поковки мм:
диаметр 30 + (13 + 03) · 2 = 332 принимается 335;
диаметр 47 – (14 + 03) · 2 = 436 принимается 44;
диаметр 78 + (14 + 03) · 2 = 814 принимается 815;
диаметр 20 + (13 + 03) · 2 = 232 принимается 235;
длина 368 + (19 + 03) · 2 = 3724 принимается 3725;
длина 38 + (13 + 03) · 2 = 412 принимается 41;
длина 48 + (14 + 03) · 2 = 514 принимается 515;
толщина 27 + (14 + 05) · 2 = 308 принимается 31.
2 Радиус закругления наружных углов – 40мм (минимальный) принимается 40мм.
3 Допускаемые отклонения размеров мм:
4 Неуказные предельные отклонения размеров принимаются равными 15 допуска соответствующего размера поковки с равными допускаемыми отклонениями.
5 Неуказанные допуски радиусов закруглений – 05мм.
6 Допускаемая высота торцового заусенца – 3мм.
7 Допускаемая высота заусенца в плоскости разъёма матриц – 06мм.
8 Допускаемое отклонение по изогнотости от плоскостности и от прямолинейности – 10мм.
9 Допускаемое смещение по поверхности разъема штампа – 04мм.
Теперь можно сравнить базовый и альтернативный методы получения заготовки.
Базовый (КГШП в открытых штампах):
Себестоимость заготовки можно определить по формуле:
Sотх – базовая стоимость одной тонны отходов по ценам 1981г. руб.;
кт - коэффициент зависящий от класса точности;
кс - коэффициент зависящий от группы сложности;
кв - коэффициент зависящий от массы;
км - коэффициент зависящий от марки материала;
кп - коэффициент зависящий от объема производства.
Q-масса заготовки кг;
кт = 1; кс = 1; кв = 1; км = 1; кп = 08
Определим стоимость заготовки получаемой на КГШП штамповкой в открытых штампах (альтернативный метод):
Определим массу заготовки при использовании КГШП в открытых штампах при использовании альтернативного метода:
Определим стоимость поковки по формуле:
кт = 105; кс = 1; кв = 1; км = 1 кп = 08.
Найдём коэффициент использования металла:
На КГШП в открытых штампах:
На КГШП в открытых штампах (альтернативный метод):
Таким образом заготовка получаемая на КГШП в открытых штампах при использовании альтернативного метода имеет выше КИМ но её себестоимость выше чем стоимость заготовки в базовом техпроцессе. В этом случае однозначный выбор сделать невозможно однако при настоящем дефиците сырья принимаем вариант с большим КИМ.
1.14.doc
Расчёт норм времени проводим подробно для токарной операции с ЧПУ 010 по методике [11].
Общее основное время определим как сумму основных времен каждого перехода:
То = (0007+0054+034+029+042+12+001)=232 мин.
Определяем вспомогательное время на обработку цилиндрической части штока токарной операции с ЧПУ 010:
где ТУС – время на установку и снятие детали мин (ТУС = 019 мин – при установке детали в центра при массе детали до 3кг);
ТИЗ – время на измерение детали мин (ТИЗ = 031+021+012+024=088мин – где 031 при измерении штангенциркулем с точностью до 01мм длины заготовки до 500 мм; 021 при измерении штангенциркулем с точностью до 005мм длины заготовки до 100 мм;012 при измерении микрометром; 024 при проверке резьбы кольцом).
ТУП – время на приемы управления мин
ТУП = Tвклоткл + Tподвотв + Tсм.
где Tвклоткл=001мин – время на включениевыключение станка кнопкой;
Tсм.поз=002 время на смену позиции в револьверной головке );
Tподвотв – время на быстрый подвод и отвод режущего инструмента;
Время на подвод инструмента из исходного положения в точку нуля заготовки в начале работы и его отвод в конце:
Тx(подвод-отвод)=(200+200)2400=016мин.
Тz(подвод-отвод)=(Sподвод z+Sотвод z)Vбыстр.перемещ.по z ;
Тz(подвод-отвод)=(100+100)4800=004мин
где скорость быстрого перемещения суппорта станка вдоль оси z:
Vбыстр.перемещ.по z =4800 мммин а скорость быстрого перемещения суппорта станка вдоль оси х: Vбыстр.перемещ.по х =2400мммин.
Общее время быстрых перемещений из исходного положения в точку нуля заготовки в начале работы и его отвод в конце:
Т(подвод-отвод)=Тz(подвод-отвод)+ Тx(подвод-отвод)=016+004=02
Найдём время на быстрое перемещение инструмента в точку начала получистового точения а так как расстояние этого перемещения будет аналогичным для чистового и тонкого точения то время также не поменяется:
Tx1 =Lx1 Vбыстр.перемещ.по х=2852400=012 мин.
Время на быстрое перемещение инструмента в точку начала нарезания резьбы по двум осям:
Tx2 =Lx2 Vбыстр.перемещ.по х=3052400=013 мин.
Tz2 =Lz2 Vбыстр.перемещ.по х=52400=0002 мин.
Tподвотв=02+012+0132=045 мин.
Общее время на приёмы управления при точении наружной цилиндрической поверхности 30f8 равны:
ТУП = 001+045+006=052 мин.
Вспомогательное время на обработку наружной цилиндрической поверхности для токарной операции с ЧПУ 010:
ТИЗ меньше основного времени на обработку цилиндрической поверхности для токарной операции с ЧПУ 010 поэтому совмещаем это время с временем обработки.
Время на обслуживание рабочего места отдых определяется как:
Тоб.от = Топ · Поб.отд.100=303×9100=027 мин
где Поб.отд =9% затраты на обслуживание рабочего места и отдых.
Далее определяем норму штучного времени:
Тшт=То+Твсп+Тоб.от 232+071+027 = 33мин.
Расчёт норм штучно-калькуляционного времени производим по формуле:
Тшт.к. = Тп.з. n + Тшт
где Тп.з - подготовительно-заключительное время мин;
n - количество деталей в партии шт.
Норма подготовительно-заключительного времени состоит из:
Тп.з1 – время на организационную подготовку:
-получить наряд чертёж технологическую документацию программоноситель режущий и вспомогательный инструмент контрольно-измерительный инструмент приспособление заготовки исполнителем и сдать их после окончания обработки партии деталей-13 мин;
- ознакомление с документацией и осмотр заготовки – 4мин;
- на инструктаж мастера – 2мин.
Получаем Тп.з1= 19 мин.
Тп.з2 - время на дополнительные приемы:
- установить и снять патрон поводковый – 65 мин;
- установить исходные режимы станка-025 мин;
- установить программоноситель в считывающее устройство и снять – 1 мин;
- проверить работоспособность считывающего устройства и перфоленты – 09 мин;
- ввести программу в память системы с ЧПУ с программоносителя – 2 мин;
- установить исходные координаты X и Y (настроить нулевое положение)- 20 мин.
- разложить и убрать инструмент – 2мин;
- установить в магазин инструменты: время на смену одного резца в резцедержатель 1мин т.к. необходимо три резца то 3·1=3мин.
Всего Тп.з2 =65+025+1+09+2+2+2+3=1765 мин
Тп.з3 - время на пробную обработку. Т.к. число режущих инструментов три и число измеряемых по диаметру поверхностей три то время на пробную обработку равно 65 мин.
Тп.з =Тп.з1 +Тп.з2 +Тп.з3 =19+1765+65=4315 мин
Рассчитаем размер партии:
где Nгод=20000- объём выпуска в год;
а=10 – периодичность запуска в производство в днях;
Ф = 254 дня - число рабочих дней в году.
Нормы времени на все остальные операции определим без приведения расчётов а все полученные данные сведём в таблицу 1. .
Таблица 1. - Технические нормы времени по операциям мин
Наименование опеации
Фрезерно-центровальная
Горизонтально-фрезерная с ЧПУ
1.12.doc
При разработке технологических процессов механической обработке заготовок деталей машин технологу часто приходится вместо конструкторских размеров устанавливать размеры и определять допуски на эти размеры но так чтобы в результате их выполнения обеспечивались размеры и допуски установленные чертежом детали. Определение технологических размеров и допусков должно производиться на основе выявления и расчёта технологических размерных цепей выражающих связь размеров обрабатываемой детали по мере выполнения технологического процесса.
Схема размерной цепи:
Рисунок 1. – Схема размерной цепи.
На горизонтально-фрезерной операции 015 производим развёртывание отверстия и выдерживаем размер от оси отверстия до ступени цилиндрической части штока равный 320±018. При этом принцип единства баз не соблюдается так как технологическая база (левый торец заготовки) не совпадает с измерительной базой. Размер A2 = 48±03 был получен на предыдущих переходах при обработке заготовки с выдерживанием принципа единства баз.
Необходимо решить проектную задачу то есть по номиналу допуску и предельным отклонениям исходного звена определить аналогичные параметры составляющих звеньев.
Применим способ равноточных допусков.
Замыкающее звено: АD=320±018мм.
Устанавливаем какие составляющие звенья являются увеличивающими размер замыкающего звена какие - уменьшающими.
А1 - увеличивающее А2 - уменьшающее. Общее число звеньев 3.
Номинальные значения составляющих звеньев: А1 =368 мм; А2 =48 мм.
Середина поля допуска ЕDСР=0 мм.
Величина единицы допуска для каждого составляющего звена:
где DС.Г. - среднее геометрическое значение размера.
где Dmin и Dmax - границы интервала размеров в таблице допусков в которые попадает номинальный размер составляющего звена.
Расчёт количества единиц допуска:
ij - единица допуска зависящая от значения номинального размера.
По значению определяем квалитет составляющих звеньев. Принимаем для звена А1=368 10 квалитет а для звена А2=48 10 квалитет.
В качестве корректирующего звена выбираем А2.
Назначим допуски на составляющие звенья:
Назначенные допуски технологически достижимы на выбранном оборудовании при принятых методах обработки поверхностей.
На увеличивающее звено А1 отклонение назначим как на основное отверстие: ES1 =ТА1 =012 мм. EI1=0. Середина поля допуска Е1СР=006 мм.
А1max=А1+ES=368+012=36812 мм.
Можно записать: А1=368 +012 мм.
Для получения замыкающего звена АD=320±018 принимаем уменьшающее звено А2=48 мм корректирующим и найдём для него предельные значения (предельные отклонения на увеличивающие звенья берём как для отверстия - в плюс на уменьшающие звенья - в минус как для вала).
А2min=36818-32018=48 мм.
А2max=368-31982=4818 мм.
Можно записать: А2=48-018 мм.
Следовательно данные технологические переходы и принятая схема базирования обеспечивают требуемую точность замыкающего звена.
1.10.doc
На этом этапе окончательно определяется состав и порядок выполнения переходов в пределах каждой технологической операции производится выбор моделей оборудования станочных приспособлений режущих и измерительных инструментов.
Операция 005 – Фрезерно-центровальная
Установить и закрепить заготовку в призме.
Фрезеровать торец выдерживая размер 368±08.
Центровать торцы одновременно по форме А 3.15 ГОСТ 14034-74 выдерживая размеры 39+05 ; 307±024.
Выбираем последовательность выполнения операции- применим последовательно-параллельный принцип так как при его использовании у нас уменьшится основное время на обработку детали.
Произведем выбор режущего инструмента - обработку торцев осуществляем торцевой фрезой. Для выбора торцевой фрезы рассчитаем наиболее оптимальный её диаметр в зависимости от обрабатываемой поверхности:
Где D-диаметр фрезы;
d-диаметр обрабатываемой поверхности.
Из стандартного ряда фрез выбираем ближайшее наибольшее значение:
Так как минимальным диаметром фрезы из стандартных является 63 то будем использовать именно его. Окончательно выбираем 63 ГОСТ 21461-10-88 со вставными ножами 03305-3А материал – Т15К6. Торцы обрабатываются при помощи сверла 2317-0106 ГОСТ 14952-75 материал - быстрорежущая сталь Р6М5.
Выберем измерительный инструмент. Для контроля размера 368±08 - длины полученной после обработки заготовки применяется штангенциркуль ШЦ II-400-01 ГОСТ 166-89 с ценой деления 01 мм диапазоном измерения 0-400 мм. погрешностью измерения 02 мм. Погрешность измерения инструмента не должна превышать примерно трети допуска контролируемой величины. В нашем случае это требование выполняется а значит измерение может быть выполнено с достаточной точностью.
Заготовка устанавливается в призму Э 91.000.
Используем станок ПРД-02.
Для остальных операций выбор режущего и измерительного инструмента производим аналогично.
Операция 010 – Токарная с ЧПУ
Установить и закрепить заготовку в центрах.
Точить ступенчатую поверхность штока выдерживая размеры:
-первой ступени 175-043 ; фаску 0645; 5±01
-второй ступени 20 ; фаску 1545
-третьей ступени (при черновом 315 IT14 мм при получистовом 308 IT12 мм при чистовом 303 IT10 при тонком 30 IT8); фаску 230.
Нарезать резьбу М2015-6g выдерживая размер 30+1.
Выбираем станок 16К20Ф3. Данный станок имеет 6-позиционную горизонтальную револьверную головку что достаточно для установки необходимого количества режущего инструмента. Станок является нормальной степени точности что достаточно для получения необходимого качества поверхности.
Режущий инструмент – контурные резцы с параллелограммными пластинками и углом для обточки деталей по цилиндру торцу и канавок (ГОСТ 20872-80 тип 1) оснащенные пластинами из сплава Т15К6 (для чернового и получистового точения). На чистовых токарных операциях применяем резцы с твердосплавными пластинами Т30К4 (чистовое и тонкое точение). Инструмент с режущей частью из твердого сплава группы ТК рекомендовано использовать именно для обработки стальных заготовок.
Измерительный инструмент – ШЦ1-160-01 ГОСТ 162-80; ШЦ2-400-005 ГОСТ 166-89; Микрометр МК25-2 ГОСТ 6507-78; Микрометр МК50-1 ГОСТ 6507-90; Кольцо 8211-0082 6g ГОСТ 17763-72; Кольцо 8211-1082 6g ГОСТ 17764-72; Образец шероховатости Ra125 ГОСТ 9378-93.
Установка детали производится в центра (центр передний ПЦ 38.000 центр задний ПЦ 602.000).
Операция 015 - Горизонтально-фрезерная с ЧПУ.
Установить и закрепить заготовку в приспособлении.
Фрезеровать поверхность выдерживая размеры 77±13 ; угол 45.
Расточить отверстие до .
Зенкеровать начерно отверстие до .
Зенкеровать начисто выдержав размер .
Развернуть отверстие выдержав размер .
Фрезеровать канавку 19+014 до 495+025 выдерживая размер 1075±0215.
Фрезеровать фаску 0645.
Сверлить 4 отверстия 42+013 выдерживая размеры 45±590 62±03 последовательно.
Зенковать 4 фаски 0645 в отверстии 42+013 последовательно.
Нарезать резьбу в 4 отверстиях М5-6Н выдерживая размер 10+1 последовательно.
Фрезеровать поверхность выдерживая размеры 27-052 ; 77±13 ; угол 45.
Фрезеровать канавку 19+014 до 495+025 выдерживая размер 1075±0215 215+013.
Переустановить деталь.
Фрезеровать два паза 5+0312±02 выдерживая размер 6±01 последовательно.
Выбираем станок горизонтально-фрезерный 6904ВМФ2 . Размеры рабочей поверхности стола 500400 что достаточно для обработки нашей детали. Ёмкость инструментального магазина 30 едениц что также удовлетворяет условиям. Размеры станка 279020602000.
Режущий инструмент – для фрезерования плоскости штока фреза 2214-0001 45 ГОСТ 24359-80 материал фрезы Р6М5; для обработки отверстия в ушке используем инструмент из материала Р6М5; для фрезерования канавки будем использовать Т-образную фрезу с коническим хвостовиком ГОСТ 7063-72; для нарезания резьбы используем метчик 2620-1123 Н3 ГОСТ 3266-81 материал-Р6М5; для сверления 4 отверстий спиральное сверло 2300-7551 42 ГОСТ 10902-77 материал Р6М5; для зенкования восьми фасок - зенковка 2353-0121 ГОСТ 14953-80; фреза 2250-0005 Н14 ГОСТ 3964-69.
Измерительный инструмент – штангенциркуль ШЦ-1-160-005-1 ГОСТ 166-89; калибр-пробка 8133-0934Js7 ГОСТ 14810-69; калибр на размер 19+014 ИИ 66.000-04; нутромер специальный 8146-НА 495+025; шаблон на размер 215+013; пробка 8221-0027 6Н ГОСТ 17756-72; пробка 8221-1027 6Н ГОСТ 17757-72; штангенглубиномер ШГ-160 ГОСТ 162-80;.
Установку детали осуществляем в специальное приспособление Э 250.000.
Операция 020 – Слесарная
Установить и закрепить заготовку в тисках.
Зачистить заусенцы и притупить острые кромки на фрезерованных поверхностях.
Калибровать резьбу М2015-6G.
Операция 025 – Закалка ТВЧ.
Операция 035 – Круглошлифовальная.
Полировать поверхность под хромирование до .
Для осуществления операции выберем круглошлифовальный станок 3М153. С максимальным диаметром под шлифование 140 мм. максимальной длинной обрабатываемой заготовки 500 мм. что удовлетворяет нашей заготовке. Габаритные размеры станка 270025401950.
Для полировки будем использовать войлочный круг ГОСТ 17620-72 диаметром 125 мм и толщиной 15 мм.
Установка детали производится в центра (центр передний 7032-0035 Морзе 5 ГОСТ 13214-79 центр задний 7032-0043 Морзе 6 ГОСТ 13214-79).
Измерительный инструмент – Микрометр МК50-1 ГОСТ 6507-90; Образец шероховатости Ra032 ГОСТ 9378-93.
Операция 040 – Хромирование
Операция 045 – Круглошлифовальная.
Для осуществления операции выберем круглошлифовальный станок 3М153. С максимальным диаметром под шлифование 140 мм. максимальной длинной обрабатываемой заготовки 500 мм. что удовлетворяет нашей заготовке. Габаритные размеры станка 270025401950.
Для полировки применим войлочный круг ГОСТ 17620-72 диаметром 125 мм и толщиной 15 мм.
Измерительный инструмент – Микрометр МК50-1 ГОСТ 6507-90; Образец шероховатости Ra016 ГОСТ 9378-93; скоба ИИ 1006.000.
Операция 055 – Контроль приёмочный.
Таблица 1. - Ведомость станочного оборудования.
Размер рабочей поверхности стола
Фрезерно-центровальный
Горизонтально-фрезерный
Рекомендуемые чертежи
- 13.12.2022
- 24.01.2023
- 22.05.2023
- 24.01.2023
- 24.01.2023
- 01.07.2014