Разработка технологического процесса изготовления детали



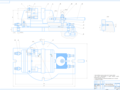
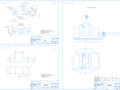
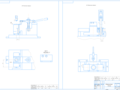
- Добавлен: 24.01.2023
- Размер: 15 MB
- Закачек: 0
Узнать, как скачать этот материал
Подписаться на ежедневные обновления каталога:
Описание
Разработка технологического процесса изготовления детали
Состав проекта
![]() |
![]() ![]() ![]() |
![]() ![]() ![]() |
![]() ![]() ![]() |
![]() ![]() ![]() ![]() |
![]() ![]() ![]() ![]() |
![]() ![]() ![]() |
![]() ![]() ![]() ![]() |
![]() ![]() ![]() |
![]() ![]() ![]() |
Дополнительная информация
Контент чертежей
03_List_Prisposob.cdw

02_list_.cdw

01_list_moy.cdw

Рекомендуемые чертежи
- 13.12.2022
- 24.01.2023
- 24.01.2023
- 24.01.2023
- 01.07.2014
Свободное скачивание на сегодня
Обновление через: 1 час 50 минут