Разработка технологического процесса для изготовления детали Вал вертолетный




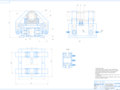
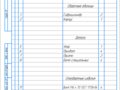
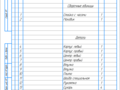
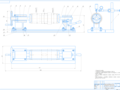
- Добавлен: 24.01.2023
- Размер: 4 MB
- Закачек: 0
Описание
Разработка технологического процесса для изготовления детали Вал вертолетный
Состав проекта
![]() |
![]() |
![]() |
![]() ![]() ![]() ![]() |
![]() |
![]() |
![]() |
![]() ![]() ![]() ![]() |
![]() ![]() ![]() ![]() |
![]() |
![]() ![]() ![]() ![]() |
![]() |
![]() |
![]() ![]() ![]() |
Дополнительная информация
приспособление контрольное.cdw

Погрешность измерения приспособления 0
.Обеспечить плавное вращения центра 16 во втулке 2 и 3 без
Все не рабочие поверхности покрыть эмалью ПФ-115 ГОСТ
Все посадочные и резьбовые соединения смазать смаской
ЦИАТИМ-221 ГОСТ 9433-60.
Спецификация приспособление.spw

Гайка М24 ГОСТ 5929-70
Палец 7030-0906 11f9 ГОСТ 12209-66
Палец 7030-0926 11f9 ГОСТ 12210-66
Штифт 12 х 55 ГОСТ 3128-70
Штифт 20 х 55 ГОСТ 3128-70
Спецификация контрольное.spw

Винт М5 х 12 ГОСТ 1491-80
Винт М6 х 20 ГОСТ 17475-80
Гайка М12-6H ГОСТ 5929-70
Шайба C. 12.37 ГОСТ 11371-78
Штифт 6 х 20 ГОСТ 3128-70
Штифт 8 х 30 ГОСТ 3128-70
Штифт 10 х 50 ГОСТ 3128-70
приспособление.cdw

Перед сборкой полости цилиндра и каналы подвода рабочей
жидкости должны быть тщательно очищены от грязи и стружки.
При сборке все поверхности трения
уплотнительные кольца смазать смазкой ЦИАТИМ-201
Резьбовые соединения уплотнить лентой ФУМ-1
Поршень гидроцилиндра должен перемещаться плавно по всей
без рывков и заеданий.
poyasnitelnaya_val_reduktora_nachalo.doc
Проектно-конструкторская часть
1 Конструктивно-технологический анализ узла составной частью которого является выбранная для проектирования деталь
2 Назначение и краткое техническое описание детали
3 Разработка параметрической твердотельной модели объекта для проектирования технологичной конструкции детали
4 Расчет силовых и деформационных параметров детали в процессе ее эксплуатации или изготовления с использованием САЕ
Производственно – технологическая часть
1 Оценка технологичности детали
2 Установление типа производства
3 Анализ базового технологического процесса
4 Обоснование и разработка мероприятий по оптимизации базового технологического процесса обработки детали
5 Выбор типа заготовки и предварительное назначение припусков
6 Назначение технологических баз и оценка точности базирования
7 Разработка плана обработки и маршрута операций технологического процесса обработки детали
8 Обоснование выбора моделей оборудования
9 Обоснование конструкции и расчет специальных средств технологического оснащения
10 Аналитический расчет технологических параметров (припусков и режимов резания)
11 Автоматизированное проектирование технологического процесса изготовления детали и средств технологического оснащения
11.1 Обоснование выбора программных средств для проектирования технологической подготовки производства
11.2 Использование прикладных библиотек САПР при проектировании технологии изготовления детали
11.3 Проектирование операционной технологии с разработкой управляющих программ и виртуальным моделированием обработки для станков с ЧПУ в САПР
12 Технологическое проектирование производственного подразделения
12.1 Расчет количества технологического оборудования и графика загрузки станков
12.2 Определение производственной площади
12.3 Расчет численности персонала
12.4 Разработка технологической планировки
Эксплуатационная часть
Научно-исследовательская часть
Экономическая и организационно-управленческая часть
1 Экономическое обоснование проекта участка
1.1 Определение потребности в инвестициях для организации
спроектированного участка
1 2 Организация оплаты труда на участке
1.3 Расчет текущих затрат (Расчет себестоимости продукции)
2 Расчёт показателей экономической эффективности проекта
3 Организация ремонтного хозяйства на машиностроительном предприятии в условиях серийного выпуска продукции
Безопасность и экологичность
Приложение А. Графическая часть проекта
Приложение Б. Спецификации к графической части проекта
Приложение В. Комплект технологической документации
Сущностью технологии машиностроения является учение о способах и процессах промышленного производства продукции заданного качества и в требуемом количестве. Современное развитие технологии машиностроения представляет собой совокупность взаимосвязанных процессов совершенствования прежде всего методов обработки материалов технологического оборудования обрабатывающего и измерительного инструментов а также теоретических и практических основ процессов обработки. Оно стимулируется усложнением конструкции изделий повышением требований к качеству их изготовления и стремлением снизить себестоимость продукции а также частой сменой объектов производства. Использование много инструментальных станков с ЧПУ оснащенных средствами механизации и автоматизации позволяет проектировать технологические процессы обработки деталей с укрупненными насыщенными переходами операциями уменьшить трудоемкость их изготовления и существенно сократить время технологической подготовки производства при частой смене номенклатуры выпускаемых изделий.
В современном производстве еще достаточно высока доля технологических процессов не в полной мере удовлетворяющих выше перечисленным требованиям. Поэтому внедрение прогрессивных методов размерной обработки деталей экономически обоснованное применение высокопроизводительного оборудования износостойкого комбинированного режущего инструмента механизированной оснастки и средств автоматизации производственных процессов в механических цехах современных машиностроительных заводов становится весьма актуальным.
Целью настоящего дипломного проектирования является совершенствование операционной технологии изготовления детали из высокопрочных материалов (Сталь 12ХН3А) и достижение наилучших технико-экономических показателей по сравнению с базовым вариантом заводской технологии.
Для достижения указанной цели необходимо решение целого ряда технологических задач:
Совершенствование маршрутного технологического процесса путем замены традиционных способов получения заготовки (прокат) современными высокопроизводительными способами – штамповкой на горизонтально – ковочной машине.
Совершенствование операционного технологического процесса за счет концентрации операций с применением специального режущего инструмента специальной оснастки и много инструментальных станков с ЧПУ.
Оснащение металлорежущего оборудования специальными высокоточными установочными и контрольными приспособлениями.
Проведение организационно-технических мероприятий по перепланировке производственного участка предназначенного для выпуска деталей типа «вал» из высокопрочных материалов.
Для практической реализации поставленных целей и задач дипломного проектирования целесообразно на основе проведения патентно-информационного поиска выявить новые технические решения в области способов и устройств для обработки деталей оснастки и металлорежущего инструмента провести их конструкторскую проработку и воспользоваться известными расчетно-аналитическими или экспериментально-статистическими методами расчета и назначения технологических режимов обработки а также провести технико-экономический анализ целесообразности организации специализированного предметного участка в составе механического цеха.
Проектно-конструкторская часть
1Служебное назначение и техническая характеристика узла составной частью которого является выбранная деталь.
Вал является составной частью редуктора. Назначение редуктора - обеспечение механической загрузки выходных валов испытуемого вертолетного редуктора крутящими моментами с использованием гидроприводных загрузочных шестерен а также наряду с технологическим и испытуемым редукторами соединительными муфтам и быстроходными валами создание кинематической цепи стенда по механически замкнутой схеме.
Редуктор является двухконтурным и представляет собой два независимых одноступенчатых цилиндрических редуктора с передаточным отношением 1:1 объединенных в единый корпус.
Главные зубчатые колеса редуктора (верхнего и нижнего контуров) установлены в подшипниках на полых валах. Верхние и нижние зубчатые колеса попарно соосны. Вращение соосных главных зубчатых колес верхнего и нижнего контуров - разнонаправленное что обусловлено требованиями к направлению вращения выходных валов испытуемого редуктора. Полые валы верхних главных зубчатых колес имеют внутренние шлицы с помощью которых на эти зубчатые колеса передаются крутящие моменты с валов. Валы сцепляются с грибками устанавливаются в редуктор сверху проходят насквозь через полые валы нижних главных зубчатых колес и опираются буртами грибков на верхние торцы полых валов верхних главных зубчатых колес. Передача крутящего момента между главными зубчатыми колесами в каждом контуре осуществляется посредством промежуточной паразитной шестерни установленной в подвижном корпусе. Перемещение загрузочных шестерен осуществляется с помощью гидравлических приводов. Управление приводом осуществляется от гидросистемы нагружения выходных валов испытуемого редуктора ВР226.010.
2. Назначение и краткое техническое описание детали
Вал предназначен для передачи крутящего момента с зубчатых колес на выходные валы редуктора.
Детали редуктора эксплуатируются в условиях знакопеременной нагрузки. К деталям предъявляются повышенные требования по качеству прочности точности обрабатываемых поверхностей.
Вал – деталь цилиндрической формы имеет внутреннюю полость со шлицами. Имеет поверхности для установки на них подшипников крепежную резьбу и 6 шпоночных пазов..
Требования к форме и взаимному расположению поверхностей детали составляют: для радиального биения шеек под подшипники 130n6 и 128g6 – 004 мм торцевое биение – 008 мм.
Конструкция детали в целом является достаточно технологичной.
Деталь Вал имеет следующие габариты: 150×835×370 мм.
Материал Вала – сталь 12ХН3А ГОСТ 4543-71.
Сталь 12ХН3А применяется: для изготовления шестерней валов червяков кулачковых муфт поршневых пальцев и других цементируемых деталей к которым предъявляются требования высокой прочности пластичности и вязкости сердцевины и высокой поверхностной твердости работающие под действием ударных нагрузок и при отрицательных температурах до -100 °С.
Химический состав и технологические свойства стали указаны в таблицах 1.2.1 и 1.2.2.
Таблица 1.2.1 - Химический состав в % материала 12ХН3А ГОСТ 4543– 71
Таблица 1.2.2 - Технологические свойства стали 12ХН3А
Начала 1220 конца 800. Сечения до 100 мм охлаждаются на воздухе 101-300 мм
ограниченная. РДС АДС под флюсом.
Обрабатываемость резанием
В горячекатаном состоянии при НВ183-187
K тв.спл. = 1.26 K б.ст. = 0.95
Склонность к отпускной способности
Флокеночувствительность
Технические требования к детали содержат всю необходимую информацию касающеюся служебного назначения детали и сведения относящиеся непосредственно к чертежу. Это позволяет сделать вывод что технические условия к детали были основательно проработаны конструктором и соответствуют требованиям предъявляемым к детали.
3 Разработка твердотельной 3D модели детали
Построение твердотельной модели детали ведем в программе КОМПАС-3D V13 компании АСКОН.
Подсистема КОМПАС-3D предназначена для создания трехмерных параметрических моделей деталей с целью передачи геометрии в расчетные пакеты и в пакеты разработки управляющих программ для оборудования с ЧПУ а также расчета их геометрических и массо-центровочных характеристик.
В запущенной программе выбираем команду файл создать деталь.
В дереве модели выбираем плоскость XY. На панели «Текущее состояние» выбираем пиктограмму эскиз и в поле чертежа с помощью графических примитивов строим контур сечения детали (рисунок 1.3.1).
Рисунок 1.3.1. – Контур сечения детали
С помощью операции вращения строим твердотельную модель являющуюся основой для дальнейшего проектирования (рисунок 1.3.2.)
Рисунок 1.3.2.– Основа твердотельной модели
Создаем «Эскиз2» элемента шпоночного паза и с помощью операции выдавливания строим профиль паза (рисунок 1.3.3.).
Рисунок 1.3.3 – Построение шпоночного паза
Строим смещенную плоскость. Используя операцию “зеркальный массив” строим противоположный шпоночный паз (рисунок 1.3.4).
Рисунок 1.3.4 – Построение шпоночных пазов
Строим эскиз зубчатого венца и с помощью операции выдавливания строим профиль зубчатого венца (рисунок 1.3.5).
Рисунок 1.3.5– Построение зубчатого венца
С помощью операций условного изображения резьбы строют окончательный контур детали и получают твердотельную 3D-модель детали (рисунок 1.3.6).
Рисунок 1.3.6 – Твердотельная 3D-модель детали
Разработка параметрической 2D модели детали
Однажды созданная параметрическая модель детали может быть быстро перестроена простым изменением значений размеров.
Выбираем в меню: Файл Создать Чертеж. Затем выбираем меню: Вставка Вид с модели Произвольный. (Масштаб 1:1)
Рисунок 1.3.7 – Создание произвольного вида с модели
Выбираем необходимые нам виды (рисунок 1.3.8).
Рисунок 1.3.8.– Выбор необходимых видов
Создаем дополнительные виды разрезы выноски образмериваем чертёж проставляем шероховатости и базы (рисунок 1.3.9).
Рисунок 1.3.9 – Формирование чертежа детали
4 Расчёт силовых и деформационных параметров детали в процессе её эксплуатации или изготовления с использованием САЕ
SolidWorks имеет простой в использовании новый инструмент анализа напряжений для пользователей COSMOSXpress. COSMOSXpress может помочь снизить стоимость и сократить время от начального замысла проекта до его внедрения на рынок выполняя тестирование проектов с помощью компьютера вместо проведения дорогостоящих и долговременных производственных испытаний. Точность результатов анализа зависит от свойств материала ограничений и нагрузок. Чтобы получить надежные результаты указанные свойства материала должны точно представлять материал детали а ограничения и нагрузки должны точно представлять условия эксплуатации детали.
Реакция детали зависит от того из какого материала она сделана. Программе COSMOSXpress необходимо знать упругие свойства материала из которого сделана деталь. Материал назначается для детали путем его выбора из библиотеки материалов. Для материалов в SolidWorks существует два набора свойств: видимые и физические. COSMOSXpress использует только физический набор свойств. Библиотека материалов SolidWorks содержит уже заданные свойства материалов.
На вкладке ограничения определяются ограничения. Каждое ограничение может содержать несколько граней. Для ограниченных граней сохраняются взаимосвязи во всех направлениях. Во избежание сбоя анализа из-за движения твердого тела необходимо указать ограничение хотя бы для одной грани детали.
На вкладке нагрузка к граням модели применяется сила и давление. Несколько сил можно приложить к одной или к нескольким граням.
В процессе анализа напряжений или статического анализа на основе материала ограничений и нагрузок рассчитываются перемещения нагрузки и напряжения в детали. Материал разрушается когда напряжение достигнет определенного уровня. Разные материалы разрушаются при различных уровнях напряжения. Для расчета напряжений COSMOSXpress использует линейный статический анализ на основе метода конечных элементов. Чтобы рассчитать напряжения в детали при линейном статическом анализе делается несколько допущений.
Таблица 1.4.1- Информация о сетке
Сетка на твердом теле
Используемое разбиение:
Автоматическое уплотнение сетки:
Сглаживание поверхности:
Количество элементов:
Время для завершения сетки (часы; минуты; секунды):
В данном случае целью анализа будет определение максимальной величины момента который способен передать вал.
Исходя из этого будем задавать нагрузку на вал. Расчет ведем в следующей последовательности:
)создаем новое упражнение;
)задаем материал детали(рисунок 1.4.1);
)накладываем ограничения на деталь (рисунок 1.4.2);
)прикладываем момент (рисунок 1.4.3);
)Выбираем команду «Выполнить расчет».
Система автоматически формирует сетку на поверхности детали и производит расчеты (рисунок 1.4.4.). В результате расчета было выяснено что при заданной геометрии и моменте 3000 Н*м запас прочности будет равным 995.
По результатам анализа можно увидеть распределение напряжений под данной нагрузкой (рисунок 1.4.5.).
Из рисунка видно что наибольшие напряжения будут на границах шлицов вала (окрашены в зеленый цвет).
Анализ статического напряжения (рисунок 1.4.6.) показывает что наибольшее смещение под нагрузкой будет на зубчатом венце со стороны шпоночных пазов вала.
COSMOSXpress результаты анализа проектирования базируются на линейном статическом анализе и предполагается изотропный материал. Линейный статический анализ предполагает что: 1) поведение материала является линейным согласно закону Гука 2) вызванные нагрузкой смещения являются достаточно небольшими чтобы не учитывать изменения жесткости в результате нагрузки и 3) нагрузки прикладываются медленно чтобы не учитывать динамические эффекты.
COSMOSXpress помогает уменьшить время проектирования и внедрения изделий путем снижения испытаний в условиях эксплуатации.
Производственно-технологическая часть
1. Оценка технологичности детали
Технологичность конструкции детали имеет прямую связь с производительностью труда затратами времени на технологическую подготовку производства и изготовление изделия. Поэтому перед проектированием технологического процесса изготовления детали необходимо провести анализ технологичности ее конструкции. Цель такого анализа – выявление недостатков конструкции по сведениям содержащимся в чертежах и технических требованиях а также возможностей улучшения технологичности рассматриваемой конструкции.
Чертёж детали содержит достаточное количество размеров а так же необходимых видов и сечений позволяющих представить деталь.
Проведём анализ технологичности вала:
Вал имеет небольшой перепад размеров диаметров что исключает повышение трудоёмкости и расход материала что соответствует технологическим требованиям.
Вал имеет тонкостенную конструкцию что может увеличить трудоёмкость изготовления данной детали за счет разбиения операций обработки для предотвращения поводок детали после снятия ее со станка.
Вал имеет внутреннюю нитроцементируемую шлицевую поверхность что может увеличить количество выполняемых финишных операций и соответственно увеличит трудоемкость его изготовления.
Исходя из выше сказанного можно сказать что деталь вал достаточно технологичная в изготовлении. Материал изделия подобран верно с точки зрения его физико-механических и эксплуатационных свойств.
Анализ чертежа показывает что вал имеет обрабатываемые поверхности позволяющие осуществлять свободный подвод и отвод режущих инструментов при выполнении операций.
При обработке Вала на большинстве операций применяется стандартный инструмент и универсальная оснастка.
Поверхность Эв.80х25х32 S4 в вале подвергаются нитроцементации для повышения износостойкости и прочности детали.
Для нарезания зубчатого венца и фрезерования шпоночных пазов на валу необходимо использовать специальные приспособления.
Количественная оценка технологичности конструкции детали по ГОСТ 14.201-83:
Допустимые коэффициенты по ГОСТ 14.201-83 должны находится в пределах от 06 до 09.
Количественная оценка технологичности конструкции детали:
)Коэффициент унификации конструктивных элементов детали
где Qуэ – число унифицированных элементов детали;
Q – общее число элементов.
Коэффициент в пределах допуска.
)Коэффициент использования материалов
где МГ – масса готовой детали;
МЗ – масса заготовки с неизбежными технологическими потерями.
)Коэффициент точности обрабатываемых поверхностей
где Kср – среднее числовое значение параметра точности.
где pi – число поверхностей с соответствующими числовыми значениями параметров точности.
)Коэффициент шероховатости обрабатываемых поверхностей
где Raср - среднее числовое значение параметра шероховатости.
П – общее число поверхностей подлежащих обработке.
Коэффициент незначительно меньше допуска.
)Коэффициент применения типовых технологических процессов
где QТ.П. – число типовых технологических процессов (операций) изготовления контроля испытаний;
QП – общее число применяемых технологических процессов.
Результат проведенного качественного и количественного анализа технологичности конструкции вала показали что деталь достаточно технологична коэффициент шероховатости немного меньше нормативных что может сказаться на увеличении трудоемкости изготовления детали к надёжности ее работы предъявляются высокие требования поэтому упрощение конструкции детали и замена материала невозможны.
2 Установление типа производства
Классификационной категорией производственного процесса является тип производства. Он определяется широтой номенклатуры регулярностью стабильностью и объёмом выпуска продукции. Для участка изготовления детали «Вал» установлен крупносерийный тип производства которому свойственны: ограниченная номенклатура изделий изготовляемых периодически повторяющимися сериями и сравнительно большой объём выпуска.
Под типом производства понимают совокупность признаков определяющих организационно-технологическую характеристику производственного процесса. Тип производства во многом предопределяет формы организации производственного процесса и в соответствии с ГОСТ 3.1108-74 характеризуется коэффициентом закрепления операций:
где – число операций выполняемое на
– количество рабочих мест на участке.
Для разных типов производства величины имеют различное значение:
= 1 – массовое производство;
10 – крупносерийное производство;
20 – среднесерийное производство;
40 – мелкосерийное производство;
> 40 – единичное производство.
Тип производства зависит от двух факторов: от заданной программы выпуска деталей и трудоемкости их изготовления.
Коэффициент закрепления операций в нашем случае соответствует крупносерийному производству. Именно для условий такого производства в дальнейшем будем проектировать технологический процесс.
На основании заданной программы рассчитывается такт выпуска изделия миншт. по формуле:
где – действительное годовое число часов работы одного станка;
N – годовая программа выпуска деталей шт.
FД = D·m·t·() (2.2.3)
где D – число рабочих дней в году;
m– число смен в сутки;
t– продолжительность рабочей смены ч;
kп – плановые потери времени на ремонт % .
Fэ = 247 · 1· 8 · (1 –) = 18772 (ч)
Подставляя численные значения в формулу находим:
= 60 × 18772 2000 = 5632 (миншт.)
Трудоёмкость изготовления детали вал определяется средним штучным временем (Tшт.ср.) по операциям действующего на производстве технологического процесса. Формула для расчета среднего штучного времени имеет следующий вид:
где – суммарная трудоемкость изготовления детали;
n – количество технологических операций.
Подставляя численные значения в формулу находим
Tшт.ср. = 4944512 =412 (мин.).
Отношение величины такта выпуска к среднему значению штучного времени называют коэффициентом серийности:
Kc = Tшт.ср. (2.2.5)
Полученное значение коэффициента серийности находится в диапазоне Кс = 1 ÷ 10 из чего следует что процесс изготовления вала при программе выпуска N =2000 штук в год соответствует крупносерийному типу производства. Именно для условий такого производства в дальнейшем будем проектировать технологический процесс.
Для крупносерийного производства величину партии деталей определяют по формуле:
где N – годовая программа деталей с учётом изготовления запасных частей шт.;
t – число дней на которое необходимо иметь запас деталей на складе. Принимаем t = 5 дней;
Ф – число рабочих дней в году; для определения размера партии деталей принимаем Ф = 247 дней.
n = 2000 × 5 247 = 40 (шт.).
3Анализ базового технологического процесса
Тщательный анализ заводского технологического процесса позволяет выявить недостатки и преимуществ присущие данному технологическому процессу.
Базовый технологический процесс ориентированный на выпуск продукции в условиях мелкосерийного производства. При этом обработку валов ведут на универсальном оборудовании с применением специальных приспособлений и использованием стандартного и специального режущего и мерительного инструментов. При увеличении программы выпуска изделий базовый технологический процесс перестает удовлетворять технико-экономическим требованиям современного производства и нуждается в усовершенствовании.
Технологический процесс изготовления детали должен выполняться с наиболее полным использованием технических возможностей средств производства при наименьшей себестоимости изделий. Оптимизация технологического процесса заключается в том что в установленный промежуток времени необходимо обеспечить выпуск потребного количества изделий заданного качества при возможно минимальной себестоимости их изготовления.
В базовом технологическом процессе для изготовления вала заготовкой служит прокат пруток. Коэффициент использования металла при этом равен 037 что не удовлетворяет условиям крупносерийного производства.
В результате при разработке технологического процесса обработки детали необходимо произвести выбор более приемлемого способа получения заготовки с тем чтобы повысить коэффициент использования металла. Возможно применение более эффективного способа получения заготовок методом штамповки или проката- трубы.
В базовом ТП припуски на механическую обработку являются завышенными из-за износа оборудования на котором производится обработка. Это связано с тем что применяемое технологическое оборудование на предприятии уже выработало свой ресурс. Следует заметить что базовый ТП проектировался в расчете на использование уже имеющегося на предприятии оборудования которое имеет конкретные точностные характеристики.
Маршрутный технологический процесс обработки детали на базовом участке представлен в таблице 2.3.1.
Таблица 2.3.1 – Маршрутный технологический процесс обработки вала
Наименование операции
Термообработка(нитроцементация)
Термообработка(закалка)
Окончание таблицы 2.3.1
В сложившихся условиях базовый ТП является наиболее оптимальным способом изготовления рассматриваемого изделия.
4 Обоснование и разработка мероприятий по оптимизации базового технологического процесса.
Режимы резания применяемые в базовом ТП являются оптимальными для оборудования применяемого на базовом предприятии и соответствуют требованиям получения готовой детали но не являются прогрессивными в новых условиях крупносерийного выпуска деталей с применением прогрессивного оборудования и оснащения.
Технологический процесс будет более эффективным по сравнению с базовым если сократить количество операций заменяя их переходами сократив токарные и шлифовальные операции заменяя введением высокопроизводительных станков с ЧПУ. Необходимо обратить особое внимание на уровень механизации и автоматизации производственного процесса что значительно сократит трудоёмкость изготовления детали и увеличит производительность.
Трудоемкость и себестоимость механической обработки детали в значительной степени зависит от метода и способа получения заготовки. При выборе заготовки необходимо учитывать конфигурацию размеры и вес детали. Материал заготовки должен соответствовать определенному набору требований. Следует также учитывать точность и качество заготовки.
Выбрать заготовку – это значит установить способ её получения рассчитать размеры назначить припуски на обработку каждой поверхности и указать допуски на неточность изготовления.
В качестве метода получения заготовки выбираем обработку давлением. Процесс обработки металла давлением отличаются высокой производительностью относительно малой трудоемкостью обеспечивают экономное расходование металла. К обработке металлов давлением относят прокатку прессование волочение свободную ковку горячую и холодную объемную штамповку листовую штамповку и другие.
Наиболее рациональным способом получения заготовки для вала является горячая объемная штамповка на горизонтально-ковочной машине. Она широко используется в серийном производстве. Этим способом получают заготовки разных форм и размеров из сталей на прессах. Форму и размеры заготовки получаем исходя из маршрута обработки и назначения припусков (таблица 2.5.1).
Таблица 2.5.1. – Маршрут обработки элементарных поверхностей
Черновое обтачивание
Чистовое обтачивание
Черновое растачивание
Чистовое растачивание
Тонкое растачивание-
Черновое фрезерование
Чистовое фрезерование
Зубчатый венец Ж Эв80×25×32S4
Большое значение при выборе заготовок имеет правильное назначение припусков на обработку. На основании выше сказанного маршрута обработки поверхностей можно назначить припуски [ ГОСТ 7505-74 ] которые приведены в таблице 2.5.2
Таблица 2.5.2– Межоперационные и общие припуски на обработку
Окончательное решение принимают на основании экономического расчета с учетом стоимости способа получения заготовки. Сравним стоимость заготовок полученных тремя способами: штамповкой и прокатом – пруток и труба.
Стоимость заготовок получаемых штамповкой можно с достаточной точностью определить по формуле [3 с. 330]:
КТ – коэффициент зависящий от класса точности заготовки [3 с. 337];
КМ – коэффициент зависящий от марки материала [3 с. 337];
КС – коэффициент зависящий от группы сложности заготовки [3 с. 338 табл.14];
КВ – коэффициент зависящий от массы заготовки [3 с. 338 табл. 14];
КП – коэффициент зависящий от объёма производства [3 с. 338 табл.14];
Q – масса заготовки кг;
q – масса готовой детали кг;
Sотх – стоимость одной тонны отходов р.т. [3 с. 333 табл. 10].
Стоимость заготовки полученной прокатом можно с достаточной точностью определить по формуле [3 с. 31]:
Данные необходимые для расчёта стоимости заготовок полученных различными способами сводим в таблице 4.
Таблица 4 – Исходные данные для расчета стоимости заготовки
Себестоимость заготовки выполняемой штамповкой:
Себестоимость заготовки выполняемой из проката:
Себестоимость заготовки выполняемой из проката трубы:
Наиболее рациональным способом получения заготовки для вала является штамповка так как он обеспечивает меньшую технологическую себестоимость детали и более высокий коэффициент использования материала.
Для детали вал выбираем заготовку - штамповку на горизонтально - ковочной машине. Штамповка на горизонтально - ковочных машинах является одной из производительных способов и рентабельна для нашего вида заготовки. Штамповка имеет минимальные припуски на обработку и по форме максимально приближена к форме готовой детали.
Эскиз заготовки показан на рисунке 2.5.1
Рис. 2.5.1-Заготовка вала
6 Назначение технологических баз и оценка точности базирования.
При проектировании технологических процессов большое значение имеет выбор баз. Обработка заготовки обычно начинается с обработки технологических баз.
Базирование – это придание заготовке или изделию требуемое положение относительно выбранной системы координат.
Применительно к механической обработке на станках при базировании заготовок производится придание заготовке требуемого положения относительно элементов станка которое определяет траекторию движения подачи обрабатывающего инструмента.
Выбор технологической базы начинается с выбора технологической базы с первой операции. База на первой операции называется черновой и ее можно использовать только один раз.
Базы различаются по назначению:
Конструкторская – база используемая для определения положения детали или сборочной единицы в изделии;
Технологическая – база используемая для определения положения заготовки или изделия в процессе изготовления или ремонта.
Выбор базовых поверхностей для обработки детали является важным этапом проектирования технологического процесса.
Первой операцией механической обработки является токарная на которой в качестве баз используются торец детали и поверхность вращения. Так как данные поверхности – необработанные то они могут использоваться в качестве базовых только один раз. Деталь обрабатывается с разных сторон поэтому в качестве черновой базы используется поверхность имеющая наименьший припуск.
В последующих операциях в качестве баз используются предварительно обработанные наружные внутренние и торцовые поверхности.
В нашем случае за черновую базу мы принимаем наружную поверхность и упираем заготовку в не обработанный торец.
На следующей операции мы производим захват за обработанную поверхность и упираем в обработанный торец. На шлифованных операциях обработка ведется в центрах с базированием на внутренние торцовые поверхности. На протяжной операции деталь закрепляется за обработанные наружную поверхность и торец. В последующих операциях деталь базируем на шлифованных внутренних и наружных поверхностях.
7 Разработка маршрута операций технологического процесса обработки детали Вал в САПР ТП
7.1 Использование информационных технологий и технических средств при разработке технологического процесса
В основу работы САПР ТП «КОМПАС–АВТОПРОЕКТ» положен принцип заимствования ранее принятых технологических решений. В процессе эксплуатации системы накапливаются типовые групповые единичные технологии унифицированные операции планы обработки конструктивных элементов и поверхностей. При формировании технологического процесса пользователю предоставляется доступ к архивам и библиотекам хранящим накопленные решения.
Разработка технологических процессов осуществляется в следующих режимах:
- проектирование на основе технологического процесса-аналога (автоматический выбор соответствующего ТП из базы данных с последующей его доработкой в диалоговом режиме);
- формирование ТП из отдельных блоков хранящихся в библиотеке типовых технологических операций и переходов;
- объединение отдельных операций архивных технологий;
- автоматическая доработка типовой технологии на основе данных переданных с параметризированного чертежа КОМПАС–ГРАФИК (чертежно-конструкторского редактора);
- разработка ТП в режиме прямого документирования в диалоговом режиме с помощью специальных процедур к справочным базам данных.
В системе реализована процедура позволяющая проектировать сквозные технологии включающие одновременно операции механообработки штамповки термообработки сборки сварки и т.д.
В комплект разрабатываемой документации входят: титульный лист карта эскизов маршрутная маршрутно-операционная операционная карты ТП ведомость оснастки материалов и другие документы в соответствии с ГОСТ. В базовую поставку системы включены более 60 видов технологических карт. Они выполнены в среде MS Excel. Распечатывать их можно как в горизонтальном так и вертикальном исполнении. При необходимости пользователь может разрабатывать новые карты а также вносить изменения в существующие образцы. Эскизы и графическая часть технологических карт выполняются в среде КОМПАС–ГРАФИК и вставляются в листы MS Excel как OLE – объекты.
Для разработки документов произвольной формы используется специальный генератор отчетов также формирующий технологические карты в среде MS Excel.
Технологические процессы разработанные в КОМПАС–АВТОПРОЕКТ помещаются в архив системы в сжатом виде. Оглавление такого архива доступно для ручного просмотра и корректировки. Автоматический поиск ТП в архиве производится либо по коду геометрической формы детали либо по отдельным характеристикам: тип детали принадлежность к изделию вид заготовки габаритные размеры и т.д. По заданным критериям поиска система находит несколько ТП оставляя окончательный выбор за технологом.
Результатом является комплект документов технологического процесса обработки резанием представленный приложением к выпускной квалификационной работе.
Маршрутный технологический процесс представлен ниже.
Операция 005 – заготовительная
Заготовка – штамповка
Операция 010 – токарная
Операция 015 – токарная
Операция 020 – долбежная
Операция 025 – термическая(нитроцементация)
Операция 030 – токарная
Операция 035 – токарная
Операция 040 – термическая (закалка)
Операция 045 – дробеструйная
Операция 050 – протяжная
Операция 055 – токарная
Операция 060 – токарная
Операция 065 – фрезерная
Операция 070 – фрезерная
Операция 075 - слесарная
Операция 080 – шлифовальная
Операция 085 – шлифовальная
Операция 090 – маркировочная
Операция 095 – покрытие
Операция 100 – контрольная
Выбор типов и моделей оборудования рассматривается на различных стадиях технологической подготовки производства. Предварительный выбор оборудования производится при назначении метода обработки поверхностей обеспечивающего выполнение технических требований к обрабатываемым поверхностям. Затем при обработке технологического маршрута обработки и его технико-экономическое обоснование производится выбор конкретной модели станка на основании минимума проведенных затрат на рабочем месте. Выбор модели станка прежде всего определяется его возможностью обеспечить точность размеров и формы а также качество поверхности изготавливаемой детали. Если эти требования можно обеспечить обработкой на различных станках определенную модель выбирают из следующих соображений:
-соответствие основных размеров станка габаритам обрабатываемой детали;
-соответствие станка по производительности заданному масштабу производства;
-возможность работы на оптимальных режимах резания;
-соответствие станка по мощности;
-возможность механизации и автоматизации выполняемых работ;
-наименьшая себестоимость обработки;
-реальная возможность приобрести станок;
-необходимость использования имеющихся станков.
С учетом всех этих требований мы выбираем токарные станки с ЧПУ ROMI GL 170G шлифовальные станки ЗУ131М И ШУ321 зубодолбежные станки 5122 протяжные станки 7А523 вертикально-фрезерный станок с ЧПУ 6Р13Ф3.
Станочные приспособления (оснастка) применяют для установки заготовок на металлорежущих станках. Обоснованное применение станочного приспособления позволяет получать высокое технико-экономические показатели. Трудоемкость и длительность цикла технологической подготовки производства себестоимость продукции можно уменьшить за счет применения стандартных систем станочного приспособления сократив трудоемкость сроки и затраты на проектирование и изготовление станочного приспособления. В условиях серийного производства выгодна система универсального станочного приспособления. Производительность труда значительно возрастает за счет применения станочного приспособления: быстродействующих с механизированным приводом многоместных автоматизированных предназначенных для работы в сочетании с автооператором или технологическим роботом.
При разработке технологического процесса механической обработки заготовки необходимо правильно выбрать и спроектировать приспособления которые должны способствовать повышению производительности труда точности обработки улучшению условий труда ликвидации предварительной разметки заготовки и выверки ее при установке на станке. Применение станочных приспособлений при обработке заготовок дает ряд преимуществ:
а) повышается качество и точность обработки детали;
б) сокращается трудоемкость обработки заготовок за счет уменьшения времени затрачиваемого на установку выверку и закрепление заготовки;
в) расширяются технологические возможности станков.
Для закрепления заготовки при обработке используется специальное фрезерное приспособление с гидроприводом (рисунок 2.9.1) чертёж которого приведен в графической части дипломного проекта.
Приспособление устанавливается на столе станка и крепится к нему болтами. Деталь в приспособлении укладывается на опорные призмы и зажимается прихватами. При фрезеровании сила резания F направлена перпендикулярно усилию зажима Pз и прижимает деталь к упору.
Приспособление представляет собой корпус поз.2 внутри которого закреплены два гидроцилиндра поз.1.На корпусе установлены две призмы поз. 7. На призмах базируется заготовка по диаметру 130. Подается давление в полости гидроцилиндров и прихваты поз. 6 под действием поршней гидроцилиндров зажимают заготовку. Фрезеруем шпоночный паз и пазы для стопорных шайб. Даем противодавление в полости гидроцилиндров переворачиваем заготовку и фрезеруем второй шпоночный паз. Для ориентации детали (шпоночные пазы выполняются через 180 градусов) на установочные пальцы поз. 13 14 устанавливаем упор поз. 5.
Рисунок 2.9.1 – Схема закрепления «Вала» в приспособлении
9.1 Расчет установочного приспособления на прочность и точность
Одним из важнейших параметров при конструировании зажимных механизмов является сила закрепления РЗ.
Силу закрепления РЗ находят из условия равновесия заготовки под действием сил резания тяжести инерции трения и реакций в опорах. Составляющая силы резания создает крутящий момент который стремится провернуть заготовку вокруг оси. Сдвигу заготовки под действием сил резания препятствуют силы трения возникающие в местах контактов заготовки с опорами и зажимным механизмом.
Рассчитаем усилие зажима необходимое для надежного закрепления обрабатываемой детали в приспособлении. Сила зажима Pз Н определяется по формуле:
где К – коэффициент запаса;
f1 f2– коэффициенты трения соответственно в местах контакта заготовки с опорами и с зажимным механизмом;
Коэффициент запаса определяется по формуле:
где Ко – коэффициент гарантированного запаса Ко = 15;
К1 – коэффициент учитывающий увеличение сил резания из-за случайных неровностей на обрабатываемых поверхностях для черновой обработки К1=12;
К2 – коэффициент учитывающий увеличение сил резания вследствие затупления режущего инструмента К2 = 16;
К3 – коэффициент учитывающий увеличение сил резания при прерывистом резании К3 = 1;
К4 – коэффициент характеризующий постоянство сил резания для пневмоцилиндров двойного действия К4 = 1;
К5 – коэффициент характеризующий эргономику ручных зажимных механизмов К5 = 1;
К6 – коэффициент учитываемый при наличии моментов стремящихся повернуть заготовку установленную на постоянные опоры К6 = 15.
Сила резания определяется по формуле
Где z-число зубьев фрезы; n- частота вращения фрезы обмин.
В- ширина фрезерования t- глубина фрезерования s – подача
Диаметр поршня определяется по формуле:
где р – давление масла в гидроцилиндре МПа р = 2 МПа;
В приспособлении установлены два гидроцилиндра со штоками диаметром 100 мм.
Погрешность приспособления определяется по формуле:
где – допуск на соответствующий размер расположения обрабатываемых поверхностей заготовки мм = 04 мм;
k – коэффициент учитывающий возможное отступление от нормального распределения отдельных составляющих k = 12;
k1 – поправочный коэффициент погрешности базирования k1 = 085;
б – погрешность базирования мм б = 0093 мм;
з – погрешность закрепления возникающая в результате деформации заготовки и приспособления при закреплении мм з = 009 мм;
уст – погрешность установки приспособления на станке мм уст = 003 мм;
изн – погрешности возникающие в результате износа деталей приспособления мм изн = 0;
п – погрешность установки и смещения режущего и вспомогательного инструмента на станке вызываемая неточностью изготовления направляющих элементов приспособления мм п=0 так как отсутствуют направляющие элементы приспособления;
k2 – поправочный коэффициент на среднюю экономическую точность обработки k2 = 08;
– значение погрешности обработки исходя из экономической точности для данного метода = 025.
9.2 Проектирование специального контрольного приспособления
Основной задачей технического контроля является установление и последующее устранение влияния на обрабатываемый размер различных факторов действующих в системе станок-приспособление-инструмент-деталь (СПИД) систематическим и случайным образом: износ режущего инструмента; температурные деформации; упругие силовые деформации возникающие из-за нестабильности припуска механических свойств обрабатываемых материалов притупления режущего инструмента и т.д.
В данном дипломном проекте разработана конструкция специального приспособления для контроля радиального биения вала чертёж которого представлен в графической части.(рисунок 2.9.2)
Рисунок 2.9.2 - Контрольное приспособление
Приспособление представляет собой плиту поз. 1 с двумя точными пазами по которым перемещаются корпус левый поз.4 и корпус правый поз.5 с центрами поз. 67. Корпуса с центрами предварительно устанавливаются на нужное расстояние затем при помощи маховика поз. 2 осуществляется необходимый зажим детали. При помощи рукоятки поз. 12 происходит быстрая смена и установка контролируемой детали. На данном приспособлении можно контролировать несоосность и радиальное биение на деталях типа валов
Рекомендуемые чертежи
- 24.01.2023
- 04.06.2017
Свободное скачивание на сегодня
Другие проекты
- 02.06.2024