Разработка технологического процесса детали ''Зубчатое колесо''




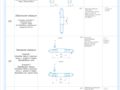
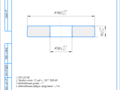
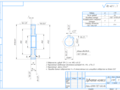
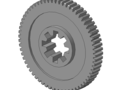
- Добавлен: 24.01.2023
- Размер: 3 MB
- Закачек: 4
Описание
Состав проекта
![]() |
![]() |
![]() ![]() ![]() ![]() |
![]() ![]() ![]() ![]() |
![]() ![]() ![]() |
![]() ![]() ![]() ![]() |
![]() |
![]() |
Дополнительная информация
Чертеж.cdw

Поверхность зубьев ТВЧ 2 4 мм
Неуказанные предельные отклонения размеров
Торцевое биение поверхностей А и Б относительно оси шлицевого отверстия не более 0
Сталь 40ХФА ГОСТ 4543-84
Тех. процесс А1(можно А2).cdw

содержание переходов
Установка заготовки в
цанговую разжимную отправку
Подрезка торца и точение фасок.
Перевернуть заготовку.
цанговую разжимную оправку
Подрезка второго ступенчатого
Сверлильная операция
Установка заготовки в
Рассверливание центрального
Установить детали в станочные
тиски с упором в торец.
Фрезерование паза с другого торца.
Зубофрезерная операция
Установка заготовки в цанговую
разжимную оправку с упором в торец.
Фрезерование зубьев.
ПОСЛЕДОВАТЕЛНОСТЬ ВЫПОЛНЕНИЯ ТЕХНОЛОГИЧЕСКИХ ОПЕРАЦИЙ
ИЗГОТОВЛЕНИЯ ВТУЛКИ КОРПУСА ПОДШИПНИКА
Токарно-винторезный
Цанговая разжимная оправка
Резец подрезной оттогнутый
Резец проходной ГОСТ 18869-73
Резец токарный фасочный
Шлифовальный круг ПП 25х50х5
А 40-П С2 5 К5 35 мс-1 1кл. А
Тиски для точных станочных
Шлицефрезерный полуавтомат
Специальное приспособление
Фреза червячная шлицевая
Вертикально-сверлильный
Сверло спиральное с коническим
Шлицешлифовальный станок
0х60х305 14 А25СМ16К 35 мс
Штангенциркуль 0-250 мм
Шагомер Б8-5070 ГОСТ 3883-81
Набор эталонов для измерения
Зубошлифовальный станок
Шлицешлифовальная операция
Установка в специальное приспособление.
с качеством поверхности
Шлицефрезерная операция
специальное приспособление.
Фрезерование шлицев.
Внутришлифовальная операция
Шлифование внутренней цилиндрической
с шероховатостью Ra 1
Плоскошливовальная операция
Установка заготовки в цанговую
разжимную оправку с упором
Перевернуть заготовку в цанговую
Шлифование другого торца.
Зубошлифовальная операция
Установка детали в цанговую
разжимную оправку с упором
Контрольная операция
Проверка размеров шлиц
и функциональных поверхностей.
шероховатости Ra 1.25 и Ra 0.63
Зубофрезерный горизонтальный
Дисковая модульная фреза
Шлифовальный круг ПП13х23х5
Разработка технологического процесса
изготовления зубчатого колеса
Последовательность выполнения
технологических операций
изготовлениязубчатого колеса
БГТУ им. В.Г. Шухова
Пояснительная записка зубчатого колеса с рамкой.docx
1. Описание конструкции детали.
2. Данные по материалу детали.
3. Данные по массе детали.
Технологическая часть
1. Определение типа производства
2. Выбор метода получения заготовки
Разработка технологического маршрута
1. Назначение технологических баз и выбор способов обработки поверхностей
2. Технологический маршрут обработки детали
3. Выбор оборудования
4. Выбор режущего и вспомогательного инструментов
5. Выбор приспособлений
6. Выбор измерительного инструмента
8. Расчет режимов резания сил и моментов резания
9. Техническое нормирование
Список использованной литературы
Целью курсовой работы является разработка одного из возможных технологических процессов обработки детали «зубчатое колесо».
При его разработке были учтены: тип производства свойства и особенности обрабатываемого материала точность размеров качество поверхности действующие стандарты и нормативы.
Курсовая работа состоит из пояснительной записки операционных карт карт эскизов и чертежей.
Графическая часть работы содержит: чертеж детали заготовки (отливка для получения одной детали и для получения десяти деталей) чертеж технологического маршрута обработки детали с указанием технологических размеров оборудования режущего и вспомогательного инструментов приспособлений и измерительного инструмента.
При оформлении графической части проекта и альбома операционных карт и карт эскизов учитывались требования ЕСКД и ЕСТПП.
Выполнение данной курсовой работы способствует развитию навыков самостоятельного решения инженерных задач в области проектирования технологических процессов в выборе оборудования режущего и вспомогательного инструментов приспособлений и измерительного инструмента для получения годной детали механической обработкой; а также помогает студенту более глубоко освоить изученные ранее дисциплины их практическое применение и значимость.
1.Описание конструкции детали
Зубчатое колесо представляет собой тело вращения относится к типу дисков. Деталь средней сложности цельная. Габаритные размеры: наружный диаметр dmax=1155 мм ширина b = 18 мм (см. рис. 1).
рис. 1. Чертеж зубчатого колеса
Зубчатое колесо с зубчатым венцом наружного зацепления число зубьев z=64 модуль m=175 наружный диаметр do=1155 мм с точностью h11 и качеством поверхности Ra 125 мкм делительный диаметр de=112 мм. Шероховатость зубчатой поверхности - Ra 063 мкм. На торцах имеются шпоночные пазы длиной 175 мм. Посадочное центральное отверстие имеет шлицы размером d8x28 H7x34H7 шероховатость отверстия и шлиц – Ra 25 мкм.
Шероховатость торцев Ra 125 мкм.
Неуказанная шероховатость Rz 40 мкм. Неуказанные пределы отклонений размеров h14 H14 ±IT 142.
2.Данные по материалу детали
Зубчатое колесо выполнено из стали 40ХФА ГОСТ 4543-84. Сталь конструкционная легированная улучшаемая. Плотность ρ=7810 кгм3.
Физико-механические свойства и химический состав которого указаны в таблице 1 и 2 соответственно.
Химический состав стали 40ХФА
Содержание элементов %
Механические свойства стали 40ХФА
сопротивление разрыву В МПа
Относительное удлинение %
Относительное сужение поперечного сечения %
Ударная вязкость аК КДжм2
3.Данные по массе детали
Масса детали составляет 0989 кг.
рис. 2. Модель зубчатого колеса
Тип производства и соответствующая ему форма труда определяют характер технологического процесса и его построение.
В соответствии с массой зубчатого колеса (M=0989 кг) и годовой программой выпуска (N=5000 штгод) определяем тип производства как серийное (см. таблицу 3).
Выбор типа производства по программе выпуска
Тип (вид) производства
Количество обрабатываемых в год деталей одного наименования и типоразмера
Крупных тяжелых большой трудоемкости
Средних размеров и трудоемкости
Небольших легких малотрудоемких
Серийное производство характеризуется ограниченной номенклатурой изделий изготавливаемых или ремонтируемых периодически повторяющимися и сравнительно большим объемом выпуска причем размер партии определяется по формуле:
где a – периодичность запуска (необходимость запаса деталей на складах) дни.
Определяем размер партии n:
Масса детали М(=0989кг) 1кг что классифицируется как мелкая по массе. Для деталей средних по массе a = 12-24 дней принимаем а = 18 дней.
Количество изделий в партии средних по массе деталей находится в интервале 51 500следовательно тип производства можно охарактеризовать как среднесерийный (см. таблицу 4)
Выбор серийности производства
Серийность производства
Количество изделий в серии (партии)
Выбор метода получения заготовки
Обоснование выбора вариантов заготовки
Ориентируясь на свойства материала детали (сталь 40ХФА - не является литейной) принимаем метод обработки металлов давлением. С учетом того что производство массовое целесообразно получить заготовку горячей объемной штамповкой т.к. она характеризуется более высокой производительностью и меньшей трудоемкостью чем свободная ковка. Кроме того горячей объемной штамповкой можно получить поковки более сложной формы.
Для изготовления заготовки детали «Зубчатое колесо» можно применить штамповку на кривошипных горячештамповочных прессах (КГШП). Они применяются в условиях массового производства для штамповки поковок близких по форме и размерам к готовым деталям. КГШП отличаются высокой производительностью небольшими значениями припусков на механическую обработку. Деформация заготовки производится за один удар.
Также можно рассмотреть получение поковки на горизонтально-ковочных машинах (ГКМ) т.к. использовать это оборудование в условиях массового производства довольно рационально. Штамповка на ГКМ характеризуется высокой производительностью возможностью автоматизации процесса и получения заготовок с глубокими полостями и отверстиями а также имеет сравнительно низкие значения припусков напусков и штамповочных уклонов.
Определение припусков на механическую обработку допусков и размеров заготовки
Для решения поставленной задачи по ГОСТ 7505-89 определим исходный индекс для нахождения которого необходимо принять следующие конструктивные характеристики:
Определение класса точности паковки: T2.
Определение приведенной массы паковки:
Мп=к*Мд где к=11. Тогда
Определение группы стали: М2.
Определение степени сложности паковки:
Vф=314*57752*18= 188 498 (мм3)= 1885 (см3)
Мф=105*1885*781=155 кг.
Тогда степень сложности – С3.
Нахождение исходного индекса – 8.
Определение припуска z допуска и предельных отклонений заготовки (приведены в таблице 4):
Шероховатость Ra мкм
Предельные отклонения мм
Определение класса точности паковки: T4.
Нахождение исходного индекса – 12
Определение припуска z допуска и предельных отклонений заготовки (приведены в таблице 5):
Расчет массы заготовок
Объем заготовки получаемой штамповкой на КГШП равен:
V = 314*59252*192-314*1922*192 = 1894 (см3)
Объем заготовки получаемой штамповкой на ГКМ равен:
V = 314*59752*198-314*1982*198 = 1976 (см3)
Масса заготовки получаемой штамповкой на КГШП равен Мз = 1 479 г.
Масса заготовки получаемой штамповкой на ГКМ равна: Мз = 1 543 г.
Определение технико-экономических показателей
Q - масса заготовки;
kT - коэффициент зависящий от точности;
kС - коэффициент зависящий от группы сложности;
kB - коэффициент зависящий от массы;
kM - коэффициент зависящий от марки материала;
kП - коэффициент зависящий от объема производства;
Sотх - себестоимость 1 т отходов.
Ки.м. - коэффициент использования металла
)Для поковок получаемых на КГШП:
СSОТХ=276 рубтонну;q=0989 кг;Q=148 кг;
кТ=1; кС=075;кВ=185; кМ=1; кП=1.
Ки.м.=qQ=0989148=067
)Для поковок получаемых на ГКМ:
С SОТХ=276 рубтонну; q=0989 кг;Q=154 кг;
кТ=102;кС=075;кВ=185; кМ=1; кП=1.
Ки.м.=qQ=0989154=064
Из расчетов видно что себестоимость заготовки и коэффициент использования металла изготовленной на КГШП незначительно ниже чем у заготовки изготовленной на ГКМ поэтому предпочтительным будет считаться изготовление заготовки на КГШП.
Разработка технологического процесса изготовления заготовки.
)Резка прутка на мерные заготовки на пресс ножницах;
)Нагрев исходной заготовки на индукционной установке ТВЧ;
)Штамповка поковки в закрытом штампе на КГШП;
)Пробивка отверстий;
)Калибровка на шарнирно-рычажном чеканном прессе;
)Термообработка - отжиг в обжиговой печи;
)Очистка от окалины на пескоструйной установке;
Чертеж заготовки зубчатого колеса изготовленной штамповкой на КГШП см. в приложениях.
Способы обработки поверхностей и технологические базы удобно свести в таблицу 6. Поверхности пронумерованы и показаны на рис. 1.
Рис.1. Эскиз детали с обозначением поверхностей
Способы обработки поверхностей и технологические базы
Номер и наименование обрабатываемой поверхности
Вид механической обработки
Номер базовой поверхности
Количество лишенных степеней свободы
Точение и шлифование
– зубчатая поверхность
– внутренняя цилиндрическая поверхность
Рассверливание и чистовое шлифование
Фрезерование и чистовое шлифование
Далее рассмотрим последовательность обработки поверхностей.
Точить торец устанавливая заготовку в цанговой разжимной оправке перевернуть заготовку и точить другой ступенчатый торец. Операция выполняется на токарном винторезном станке 16К20.
Сверлильная операция
Рассверливаем отверстие ∅28 зажимая деталь в тисках.
Зубофрезерная операция
Фрезеровать зубья (обеспечивается 11-ая степень точности) зажав деталь в цанговой разжимной оправке. Технологическая база – отверстие и базовый торец (реализуется оправкой и упором в торец). Оборудование – зубофрезерный полуавтомат.
Фрезеруется паз зажимая деталь в станочных тисках концевой фрезой. Оборудование – вертикальный консольно-фрезерный станок 6Р12.
Шлицефрезерная операция
Фрезеруем шлицы зажав заготовку в специальном приспособлении. Операцию выполняем шлицефрезерном полуавтомате 5350А.
Шлицешлифовальная операция
Сверлим сквозное отверстие ∅16 зенкуем фаски.
Внтришлифовальная операция
Выполняем шлифование внутренней цилиндрической поверхности используя мембранный патрон.
Плоскошлифовальная операция
Шлифование торцев зажимая деталь в патроне.
Зубошлифовальная операция
Шлифование зубьев выполняем на зубошлифовальном станке 3У12УА.
Контрольная операция
Наименование и содержание операции
Оборудование приспособление инструмент
Установка заготовки в цанговую разжимную оправку с упором в торец.
Подрезка торца и точение фаски
Перевернуть заготовку.
Подрезка второго ступенчатого торца точение фаски.
Установ I Установ II
Токарно-винторезный станок 16К20
Цанговая разжимная оправка
Резец подрезной оттогнутый
Резец токарный фасочный
Установка детали в станочные тиски с упором в торец.
Рассверливание центрального отверстия ∅28 мм.
Вертикально-сверлильный станок 2Н150
Тиски для точных станочных работ
Сверло спиральное с коническим хвостовиком ∅28 мм
Установить детали в станочные тиски с упором в торец.
Фрезеровать паз с другого торца.
Вертикальный консольно-фрезерный станок 6Р12
Зубофрезерный горизонтальный станок мод 5В370
Дисковая модульная фреза диаметром
Установка детали в специальное приспособление.
Шлицефрезернай полуавтомат 5350А
Специальное приспособление
Фреза червячная шлицевая прямобочная Р6М5
Установка в специальное приспособление.
Шлифование шлиц с качеством поверхности Ra 25 мкм.
Шлицешлифовальный станок 3451
Круг шлифовальный профильный ПП 600х60х305 14А25СМ16К 35 мс ГОСТ 2424-83
Внутришлифовальная операция
Установка детали в мембранный патрон.
Обработка внутренней цилиндрической поверхности ∅28 мм с шероховатостью Ra 125 мкм.
Внутришлифовальный станок 3К225В
А 40-П С2 5 К5 35мс-1 1кл. А.
Подрезка второго торца.
Плоскошлифовальный станок 3Е711В
Установка детали в цанговую разжимную оправку с упором в торец.
Зубошлифовальный станок мод. 3У12УА
Круг шлифовальный тарельчатый ГОСТ 5392 – 80
Проверка размеров шлицев шага зубьев и функциональных поверхностей.
Проверка качества шероховатости Ra125 и Ra063.
Штангенциркуль 0-250 мм (005 мм) ШЦ-II (ЧИЗ) ГОСТ 166-89
Микрометр МК 50-1 ГОСТ 6507-90
Шагомер Б8 – 5070 ГОСТ 3883 – 81
Набор эталонов для измерения шероховатости
Выбор оборудования для механической обработки зубчатого колеса будем производить в соответствии со следующими принципами:
- оборудование должно иметь возможность достигать требуемую точность обрабатываемых поверхностей;
- оборудование должно соответствовать типу производства;
- рабочая зона станка должна вмещать в себя обрабатываемую деталь но не быть чрезмерно просторной что ведет к недогруженности станка;
- станок должен обеспечивать требуемую жесткость закрепления детали и инструмента при обработке и кинематические возможности;
- желательно по возможности сократить номенклатуру станков и подобрать их таким образом чтобы была возможность производить обработку за наименьшее количество операций.
Проведем подбор оборудования для операции 005 – токарной. На данной операции производится точение торцев и фасок. Исходными данными для выбора оборудования являются:
- габаритные размеры детали
(наибольший диаметр - ∅1155 мм ширина – 18 мм);
- тип производства – серийный.
Для данной операции выберем токарно-винторезный станок 16К20. Предназначены для выполнения разнообразных токарных работ: обтачивания и растачивания цилиндрических и конических поверхностей нарезания наружных и внутренних метрических дюймовых модульных и питчевых резьб а также сверления зенкерования развертывания и т.п. Отклонение от цилиндричности 7 мкм конусности 20 мкм на длине 300 мм отклонение от прямолинейности торцевой поверхности на диаметре 300 мм - 16 мкм.
Станки оснащены механическим фрикционом приводом быстрых перемещений суппорта задняя бабка имеет аэростатическую разгрузку направляющие станины закалены HRCэ 49 57
Основные технические характеристики станка 16К20 представлены в таблице 7.
Технические характеристики станка 16К20
Наибольшая длина обрабатываемого изделия мм
Высота оси центров над плоскими направляющими станины мм
Пределы оборотов обмин
Мощность электродвигателя главного привода кВт
Наибольший диаметр изделия устанавливаемого над станиной мм
Наибольший диаметр обработки над поперечными салазками суппорта мм
Наибольший диаметр прутка проходящего через отверстие в шпинделе мм
Габаритный размеры станка мм
Проведем подбор оборудования для операции 010 – сверлильной. На данной операции будет производиться рассверливание отверстия. Исходными данными для выбора оборудования являются:
Для данной операции выберем вертикально-сверлильный станок 2Н150. Предназначен для сверления рассверливания зенкования зенкерованияразвертывания и подрезки торцев ножами. Наличие на станке механической подачи шпинделя при ручном управлении циклами работы допускает обработку деталей в широком диапазоне размеров из различных материалов с использованием инструмента из высокоуглеродистых и быстрорежущих сталей и твердых сплавов. Установленное на станке электрическое устройство реверсирования двигателя главного движения позволяет производить нарезание резьбы машинными метчиками при ручной подаче шпинделя.
Основные технические характеристики станка 2Н150 представлены в таблице 9.
Технические характеристики станка 2Н150
Наибольший диаметр сверления в стали 45 ГОСТ 1050- 74 мм
Размеры конуса шпинделя по СТ СЭВ 147-75
Расстояние оси шпинделя до направляющих колонны мм
Наибольший ход шпинделя мм
Расстояние от торца шпинделя мм:
Наибольшие (установочное) перемещение сверлильной головки мм
Перемещение шпинделя за один оборот штурвала мм
Рабочая поверхность стола мм
Наибольший ход стола мм
Количество скоростей шпинделя
Мощность электродвигателя главного движения кВт
Габарит станка: длина ширина высота мм
Проведем подбор оборудования для операции 015 –фрезерной. На данной операции производится фрезерование пазов. Исходными данными для выбора оборудования являются:
Для данной операции выберем вертикальный консольно-фрезерный станок 6Р12.Предназначен для фрезерования всевозможных деталей из стали чугуна и цветных металлов торцовыми концевыми цилиндрическими радиусными и другими фрезами.
Основные технические характеристики станка 6Р12 указаны в таблице 10.
Технические характеристики станка 6Р12
Наименование параметров
Размеры рабочей поверхности стола мм:
Число Т-образных пазов
Наибольшее перемещение стола мм:
Продольное механическое
Поперечное механическое
Вертикальное механическое
Вертикальное вручную
Расстояния от торца шпинделя до стола при ручном перемещении (наименьшее – наибольшее) мм
Расстояние от оси шпинделя до вертикальных направляющих станины мм
Наибольшая масса обрабатываемой детали кг
Наибольшее осевое перемещение пиноли шпинделя мм
Наибольший угол поворота шпиндельной головки град.
Двигатель привода главного движения:
Частота вращения обмин
Всего двигателей шт.
Габаритные размеры станка мм (длина х ширина х высота)
Проведем подбор оборудования для операции 020 – зубофрезерной. На данной операции производится фрезерование зубьев. Исходными данными для выбора оборудования являются:
Для данной операции выберем зубофрезерный горизонтальный станок 5В370. Предназначен для фрезерования зубьев цилиндрических зубчатых колес методом радиального врезания. Основные технические характеристики станка 5В370 указаны в таблице 8.
Технические характеристики станка 5В370
Класс точности станка по ГОСТ 8-82 (НПВАС)
Диаметр обрабатываемой детали мм
Длина зуба нарезаемого колеса мм
Габариты станка Длинна Ширина Высота (мм)
Мощность двигателя кВт
Пределы частоты вращения шпинделя MinMax обмин
Проведем подбор оборудования для операции 025 – шлицефрезерной. На данной операции будет производиться фрезерование шлиц. Исходными данными для выбора оборудования являются:
Для данной операции выберем шлицефрезерный полуавтомат 5350А. Предназначен для фрезерования на валах прямых прямобочных и эвольвентных шлицев а также зубъев шестерен выполненных заодно с валом.
Основные технические характеристики станка 5350А представлены в таблице 11.
Технические характеристики станка 5350А
Длина нарезаемых шлицев мм
Число инструментов в магазине
Проведем подбор оборудования для операции 030 – шлицешлифовальной. На данной операции будет производиться шлифование шлиц. Исходными данными для выбора оборудования являются:
Для данной операции выберем станок шлицешлифовальный станок 3451. Предназначен для шлифования прямобочных треугольных шлицевых валов а также для шлифования боковых сторон эвольвентных шлицевых валов по радиусу приближенному к эвольвенте.
Основные технические характеристики станка 3451 представлены в таблице 12.
Технические характеристики станка 3451
макс. скорость шпинделя
мин. скорость шпинделя
Наибольшая длина обрабатываемой детали мм
Наибольший диаметр обрабатываемой детали мм
Проведем подбор оборудования для операции 035 – внутришлифовальной. На данной операции будет производиться шлифование внутренней цилиндрической поверхности. Исходными данными для выбора оборудования являются:
Для данной операции выберем станок внутришлифовальный станок 3К225В. Предназначен для шлифования цилиндрических конических глухих и сквозных отверстий. Станок имеет торцешлифовальный шпиндель позволяющий шлифовать наружный торец детали за один установ с обработкой отверстия. Передняя бабка может поворачиваться на угол 45° для шлифования конических поверхностей.
Основные технические характеристики станка 3К225В представлены в таблице 10.
Технические характеристики станка 3К225В
Диаметр обрабатываемого отверстия d мм
Проведем подбор оборудования для операции 040 – плоскошлифовальной. На данной операции будет производиться шлифование зубьев. Исходными данными для выбора оборудования являются:
Для данной операции выберем станок плоскошлифовальный станок 3Е711В. Предназначен для обработки в цикле или вне цикла периферией абразивного или алмазного круга плоских поверхностей деталей из стали чугуна и других материалов закрепленных на зеркале стола или во вспомогательных приспособлениях. В пределах допустимых кожухом шлифовального круга на станках возможна обработка торцом круга а с применением приспособлений для фасонной правки абразивных кругов механизмов деления и крепления деталей которыми комплектуются станки по особому заказу возможна обработка пазов и фасонных профилей методом многопроходного врезного шлифования. Станки используются на предприятиях с серийным и массовом производством.
Основные технические характеристики станка 3Е711В представлены в таблице 14.
Технические характеристики станка 3Е711В
Длина (диаметр) рабочей поверхности стола мм
Размеры шлифовального кругамм
Проведем подбор оборудования для операции 045 – зубошлифовальной. На данной операции будет производиться шлифование зубьев. Исходными данными для выбора оборудования являются:
Для данной операции выберем станок зубошлифовальный станок 3У12УА. Предназначен для наружного и внутреннего шлифования цилиндрических конических и торцевых поверхностей деталей при установке их в центрах кулачковых патронах и на планшайбе в условиях единичного и мелкосерийного производства
Основные технические характеристики станка 3У12УА представлены в таблице 13.
Технические характеристики станка 3У12УА
Анализируя данные выбранных станков можно сделать следующие выводы:
станки подходят по назначению для выполнения требуемых операций;
габариты рабочей зоны станков обладают достаточными размерами для размещения в ней приспособления и детали;
применение станков в среднесерийном производстве приемлемо;
точность обработки на станках обеспечивает требуемую точность получаемых поверхностей.
Следовательно выбранные станки подходят для выполнения соответствующих заданных операций.
Проведем выбор режущего инструмента для операции 005 – токарной. Исходными данными для этой операции будут:
- материал детали – Сталь 40ХФА ГОСТ 4543-84;
- диаметр детали – ∅1155 мм (Rz40 мкм 11-й квалитет точности);
- содержание операции – точение торцев и фасок;
- оборудование – токарно-винторезный станок 16К20.
Для подрезки торца примем материал режущей части инструмента твердый сплав – ВК8. Данный материал обладает следующими свойствами: предел прочности на изгиб ; плотность ; твердость HRC≥875 который подходит для обработки стали твердостью НВ не более 241.
В качестве инструмента выберем резец подрезной 2112-0057 (25х16х140) ВК8 ГОСТ 18880-82 проходной резец 2100-0003 ГОСТ 18878-73 с пластинами из твердого сплава ВК8 (сечения державки ВxH=20х20) и токарный фасочный резец 2136-0709 ГОСТ 18875-73 с пластинами из твердого сплава ВК8 (сечения державки ВxH=16х16).
Резец будет закрепляться в резцедержателе 1-30 ОСТ 2 П15-7-84.
Проведем выбор режущего инструмента для операции 010 –сверлильной. Исходными данными для этой операции будут:
- диаметр отверстия – ∅28 мм (Rz40 мкм 7-й квалитет точности);
- содержание операции – рассверливание отверстия;
- оборудование – вертикально-сверлильный станок 2Н150.
Для сверления выберем материал режущей части инструмента - твердый сплав ВК8.
Данный материал обладает следующими свойствами: предел прочности на изгиб ; плотность ; твердость HRC≥875 который подходит для обработки чугунов твердостью НВ 240.
В качестве инструмента выберем сверло спиральное с коническим хвостовиком 2301-3665 ГОСТ 10903-77 (диаметр - ∅28 мм длина рабочей части – 170 мм длина сверла – 291 конус Морзе 3).
Проведем выбор режущего инструмента для операции 015 – фрезерной. Исходными данными для этой операции будут:
- ширина паза – 17 мм (Rz40 мкм 14-й квалитет точности);
- содержание операции – фрезерование паза;
- оборудование – фрезерный станок 6Р12.
Для обработки паза примем материал режущей части инструмента быстрорежущей стали ВК8. Данный материал обладает следующими свойствами: предел прочности на изгиб ; плотность ; твердость HRC≥875 который подходит для обработки чугунов твердостью НВ 240.
В качестве инструмента выберем концевую фрезу диметром ∅175 мм ГОСТ 18372-73 (длина рабочей части - 40 мм длина фрезы – 100 мм).
Проведем выбор режущего инструмента для операции 020 – зубофрезерной. Исходными данными для этой операции будут:
- содержание операции – фрезерование зубьев;
- оборудование – зубофрезерный станок 5В370.
Для обработки зубчатой поверхности примем материал режущей части инструмента быстрорежущей стали Р6М5. Данный материал обладает следующими свойствами: предел прочности на изгиб ; твердость HRC≥63 который подходит для обработки стали твердостью НВ не более 241.
В качестве инструмента выберем дисковую модульную фрезу с модулем 175 шириной В = 6 мм диаметром ∅55 мм количеством зубьев – 14.
Проведем выбор режущего инструмента для операции 025 – шлицефрезерной. Исходными данными для этой операции будут:
- длина шлицы – 7 мм (Rz20 мкм 14-й квалитет точности);
- содержание операции – фрезерование шлиц;
- оборудование – шлицефрезерный полуавтомат 5350А.
В качестве инструмента выберем червячную шлицевую прямобочную фрезу 2520-0701 с длиной L = 63 мм диаметром ∅26 мм количеством зубьев – 6.
Проведем выбор режущего инструмента для операции 030 – шлицешлифовальной. Исходными данными для этой операции будут:
- длина шлицы – 7 мм (Ra 25 мкм 7-й квалитет точности);
- содержание операции – шлифование шлиц;
- оборудование – шлицешлифовальный станок 3451.
Для шлифования шлиц в качестве инструмента выберем шлифовальный круг шлифовальный профильный ПП 600х60х305 14А25СМ16К 35 мс ГОСТ 2424-83.
Проведем выбор режущего инструмента для операции 035 – внутришлифовальной. Исходными данными для этой операции будут:
- диаметр отверстия – ∅28 мм (Rа 125 мкм 7-й квалитет точности);
- содержание операции – шлифование отверстия;
- оборудование – внутришлифовальный станок 3К225В.
Для шлифования внутренней цилиндрической поверхности в качестве инструмента выберем шлифовальный круг ПП 13235 9А 40-П С2 5 К5 35мс-1 1кл. А. ГОСТ 2424-82.
Проведем выбор режущего инструмента для операции 040 – плоскошлифовальной. Исходными данными для этой операции будут:
- диаметр детали – ∅1155 мм (Ra125 мкм 11-й квалитет точности);
- содержание операции – шлифование торца;
- оборудование – плоскошлифовальный станок 3Е711В.
Для шлифования наружной цилиндрической поверхности в качестве инструмента выберем шлифовальный круг ПП 25505 9А 40-П С2 5 К5 35мс-1 1кл. А. ГОСТ 2424-82.
Проведем выбор режущего инструмента для операции 045 – зубошлифовальной. Исходными данными для этой операции будут:
- диаметр детали – ∅112 мм (Ra 063 мкм 14-й квалитет точности);
- содержание операции – шлифование зубьев;
- оборудование – зубошлифовальный станок 3У12УА.
Для шлифования зубчатой поверхности в качестве инструмента выберем шлифовальный круг шлифовальный тарельчатый ГОСТ 5392-80.
Анализируя полученные сведения можно сделать вывод о том что выбранный режущий и вспомогательный инструмент подходит для соответствующих операций выполняемых при механической обработке детали.
Выберем приспособление для выполнения операции 005 – токарной. Исходными данными для выбора приспособления являются:
-габаритные размеры детали (наибольший диаметр - ∅1155 мм ширина – 18 мм)
-тип производства – среднесерийный
-габариты рабочей зоны станка (наибольшая длина обрабатываемой детали – 1000 мм наибольший диаметр детали – 400 мм)
-принятая схема базирования (внутренняя цилиндрическая поверхность с упором в торец).
Для осуществления данной схемы базирования и обеспечения остальных требований наиболее приемлемым приспособлением является цанговая разжимная оправка.
Выберем приспособление для выполнения операции 010 –сверлильной.
Исходными данными для выбора приспособления являются:
-габариты рабочей зоны станка (наибольший диаметр сверления – 50 мм наибольшее установочное перемещение сверлильной головки – 250 мм)
-принятая схема базирования (наружная цилиндрическая поверхность и торец).
Для осуществления данной схемы базирования и обеспечения остальных требований наиболее приемлемым приспособлением являются тиски для точных станочных работ с пневмозажимом ГОСТ 20746-84.
По габаритным размерам детали и станка подбираем модель тисков 7033-0035.
Данная модель обладает следующими характеристиками:
- размеры зажимной детали – 25 175 мм
Приспособление для выполнения операции 015 – фрезерной аналогично тому которое использовалось в операции 010.
Приспособление для выполнения операции 020 – зубофрезерной аналогично тому которое использовалось в операции 005.
Выберем приспособление для выполнения операции 025 - шлицефрезерной. Исходными данными для выбора приспособления являются:
-габариты рабочей зоны станка (длина нарезаемых шлиц – 925 мм длина детали – 500 мм)
-принятая схема базирования (наружная цилиндрическая поверхность).
Для осуществления данной схемы базирования и обеспечения остальных требований наиболее приемлемым приспособлением является специальное приспособление
Приспособление для выполнения операции 030 – шлицешлифовальной аналогично тому которое использовалось в операции 025.
Выберем приспособление для выполнения операции 035 - внутришлифовальной. Исходными данными для выбора приспособления являются:
-габариты рабочей зоны станка (диаметр обрабатываемого отверстия – 150 мм длина детали – 125 мм)
Для осуществления данной схемы базирования и обеспечения остальных требований наиболее приемлемым приспособлением является мембранный патрон (для толстостенных колец и втулок).
Приспособление для выполнения операции 040 – плоскошлифовальной аналогично тому которое использовалось в операции 005.
Выберем приспособление для выполнения операции 045 - зубошлифовальной. Исходными данными для выбора приспособления являются:
-габариты рабочей зоны станка (длина шлифования – 320 мм длина детали – 500 мм)
Для осуществления данной схемы базирования и обеспечения остальных требований наиболее приемлемым приспособлением является разжимная оправка.
Из перечисленных выше характеристик приспособлений следует что соответствующие приспособления подходят для выполнения операций
механической обработки детали.
6. Выбор измерительного инструмента.
Измерительный инструмент - это техническое устройство используемое при измерениях и имеющее нормированные метрологические свойства. При выборе измерительного инструмента учитываются формы контроля (сплошной или выборочный масштаб производства конструктивные характеристики детали точность её изготовления).
В соответствии с габаритными размерами детали (наибольший диаметр - ∅1155 мм ширина – 18 мм) в качестве основного измерительного инструмента выбираем: штангенциркуль ШЦ – II (ЧИЗ) (0-250) ГОСТ 166-89 с ценой делений 005 мм и микрометр МК 50-1 ГОСТ 6507-90.
Для контроля зубьев применим шагомер Б8-5070 ГОСТ 3883-81.
Для проверки шероховатости поверхностей с качеством поверхности Ra 25 Ra 125 и Ra 063 используем набор эталонов шероховатости ГОСТ 9378-93.
Рассчитаем припуски на обработку функциональной поверхности – наружной поверхности ∅1155h11 (табл. 14).
Технологический маршрут обработки поверхности ∅1155h11 состоит из обтачивания чистового и предварительного и шлифования чистового.
Припуски на обработку наружной цилиндрической поверхности ∅115
Необходимо определить операционные припуски на обработку поверхности ∅1155детали "Зубчатое колесо" длина обработки L=18 мм параметр шероховатости Ra1.25 последовательным обтачиванием и шлифованием. Исходная заготовка – штамповка на КГШП.
Используя справочные данные осуществляем расчет.
Исходная заготовка – штамповка на КГШП: ES=0; EI=-022; (Rz+h)=275 мкм где h – толщина дефектного поверхностного слоя.
Пространственная погрешность - погрешность связанная с пространственными отклонениями расположения поверхности и в некоторых случаях отклонения формы поверхности.
Суммарное значение пространственных отклонений:
где - удельная кривизна заготовок на 1 мм длины; L – длина заготовки.
Пространственная погрешность
Величина смещения оси заготовки в результате погрешности зацентровки:
где т – допуск на диаметр базовой поверхности заготовки использованной при центровании мм.
Суммарная погрешность:
Заготовка после точения: задаем по справочникам погрешность по h11 поле допуска Т=016 мм; Rz = 20 мкм h = 30 мкм (толщина дефектного слоя после предыдущей операции); биение 01 мм = (в зависимости от станка). Сводим в табл. 13.
Расчет припусков и операционных размеров ведут в направлении от обрабатываемой поверхности к исходной заготовке:
Выбираем по справочнику ρ Rz h тогда припуск:
Расчетный (номинальный) припуск:
где - допуск на предшествующей операции.
Максимальный припуск:
где - допуск на следующей операции.
Исходные данные для расчёта
Предельные отклонения выдерживаемого размера
Горячий прокат (исходная заготовка)
Номинальный (наибольший) операционный размер на обтачивание:
Окончательно с допуском: мм
где -016 мм - предельное отклонение на обтачивание из табл. 13.
Минимальный припуск на обтачивание:
Номинальный (расчётный) припуск на обтачивание:
Расчётный диаметр заготовки:
По ГОСТ 2590-87 принимаем диаметр прутка мм.
Фактические размеры припуска на обтачивание:
Расчет режимов резания сил и моментов резания для операции 005 Токарная
Черновое точение торцев.
Глубина резания при черновом точении и отсутствии ограничений принимается максимально возможной t = 2 мм.
Подача определяется по таблице. При диаметре детали ∅1155 мм подача равна . Принимаем сопоставив табличное значение подачи с техническими характеристиками станка 16К20.
Скорость резания определяется по формуле
где - стойкость режущего инструмента принимается в пределах 30-60мин примем .
Значения коэффициента и показателей степени смотрим по таблице:
- период стойкости его определяем по таблице ;
- общий поправочный коэффициент на скорость резания учитывающий фактические условия резания
где - коэффициент учитывающий качество обрабатываемого материала : .
- коэффициент учитывающий состояние поверхности заготовки (без корки) .
- коэффициент на инструментальный материал .
Рассчитываем скорость резания.
Частота вращения. Определяем по формуле:
Сравнивая с техническими характеристиками станка 16К20 выбираем ближайшее меньшее значение частоты вращения - .
Фактическая скорость резания определяется по формуле:
Сила резания. Силу резания принято раскладывать на составляющие силы направленные по осям координат станка (тангенциальную радиальную и осевую ). Эти составляющие рассчитываются по формуле:
гдезначения коэффициента и показателей степени смотрим по таблице для составляющей : .
Поправочный коэффициент представляет собой произведение ряда коэффициентов: учитывающих фактические условия резания. Численные значения этих коэффициентов берём из таблиц:
; ; - передний угол ; - угол наклона главного лезвия ; - радиус при вершине .
Таким образом сила резания будет равна:
Мощность резания определяют по формуле:
По техническим характеристикам станка 16К20 его максимальная мощность . Так как то рассчитанные режимы резания подходят.
Расчет режимов резания сил и моментов резания для операции 010 - Сверлильная
Рассверливание отверстия ∅28 мм l = 18 мм.
Глубина резания. При сверлении глубина резания определяется по формуле:
Режущий инструмент: сверло спиральное Р6М5 d = 28 мм.
Подача. При сверлении отверстий глубиной подачу определяют по табличному значению. Табличное значение подачи для сверла диаметром - 3.
Сравнив табличное значение подачи с техническими характеристиками станка выбираем .
Скорость резания. Скорость резания при сверлении определяется по формуле:
гдезначения коэффициента и показателей степени смотрим по таблице:;
где - коэффициент на обрабатываемый материал
- коэффициент учитывающий глубину сверления .
Сравнивая с техническими характеристиками станка выбираем ближайшее меньшее значение частоты вращения - .
Крутящий момент и осевая сила. Они рассчитываются по формулам:
где и и показатели степени и определяем по таблице:
- для крутящего момента;
- коэффициент учитывающий фактические условия обработки в данном случае зависит только от материала обрабатываемой заготовки и определяется выражением .
Значение коэффициента приведено в таблице: .
Таким образом получаем .
Тогда крутящий момент .
Мощность резания определяют по формуле т.е..
По техническим характеристикам станка 2Н118 его максимальная мощность . Так как то рассчитанные режимы резания подходят.
Расчет режимов резания сил и моментов резания для операции 015 Фрезерная
Глубина фрезерования
На этой операции фрезеруется паз врезаясь в заготовку поэтому принимаем глубину резания 4 мм при ширине фрезерования 14мм.
Режущий инструмент: Фреза концевая ∅140 Z=5 КМ5 кхв Р6М5 ГОСТ1092-85 ширина фрезерования .
Подача. При фрезеровании различают подачу на один зуб подачу на один оборот фрезы и подачу минутную которые находятся в следующем соотношении:
где - частота вращения фрезы
- число зубьев фрезы.
Подача на зуб фрезы при фрезеровании торцовыми фрезами с пластинами из твёрдого сплава Р6М5 при мощности станка 6Р13 равной 34 кВт равна: сравнив с техническими характеристиками станка 6Р13 принимаем тогда .
Скорость резания – окружная скорость фрезы определяется по формуле
гдезначения коэффициента и показателей степени смотрим по таблице:
Рассчитываем скорость резания
Определяем по формуле:
Сравнивая с техническими характеристиками станка 6Р13 выбираем ближайшее меньшее значение частоты вращения - .
Сила резания. Главная составляющая силы резания при фрезеровании – окружная сила она рассчитывается по формуле:
гдезначения коэффициента и показателей степени смотрим по таблице: ; .
Значение коэффициента приведено в таблице .
Рассчитываем силу резания
Крутящий момент на шпинделе определяем по формуле:
По техническим характеристикам станка 6Р13 его максимальная мощность . Так как то рассчитанные режимы резания подходят.
Расчет режимов резания сил и моментов резания для операции 020 зубофрезерная
Глубина фрезерования рассчитывается по формуле:
где - припуск на обработку двух торцевых поверхностей заготовки.
Подача на зуб фрезы равна: сравнив с техническими характеристиками станка 5В370 принимаем тогда .
Сравнивая с техническими характеристиками станка 5В370 выбираем ближайшее меньшее значение частоты вращения - .
По техническим характеристикам станка 5В370 его максимальная мощность . Так как то рассчитанные режимы резания подходят.
Определение режимов резания по остальным операциям ведём по следующей схеме:
)Определяем глубину резания по разработанному технологическому процессу.
)По картам справочника режимов резания определяем подачу в соответствии с группой станка и типом обработки. Затем сравниваем табличное значение подачи с техническими характеристиками станка и выбираем подходящее значение.
)Определяем скорость резания по картам справочника режимов резания.
)Рассчитываем частоту вращения по формул: сравнивая с техническими характеристиками станков1 выбираем ближайшее меньшее значение частоты вращения.
)По рассчитанным данным определяем фактическую скорость резания по формуле:
)Определяем мощность по картам и техническим характеристикам станка.
Для остальных операций все вышеперечисленные параметры определяем по справочнику технолога-машиностроителя.
Расчет режимов резания сил и моментов резания для операции 025 шлицефрезерная
Фрезерование шлицев.
Расчет режимов резания сил и моментов резания для операции 030 шлицешлифовальная
Расчет режимов резания сил и моментов резания для операции 035 внутришлифовальная
Чистовое шлифование внутренней цилиндрической поверхности диаметром ∅40 l=42 мм.
Расчет режимов резания сил и моментов резания для операции 040 плоскошлифовальная
Расчет режимов резания сил и моментов резания для операции 045 зубошлифовальная
Режимы резания силы и моменты резания сводятся в таблицу 16.
- глубина резания мм;
- подача (продольная при шлифовании) мм;
- подача на один зуб фрезы при фрезеровании ммзуб;
- поперечная подача при шлифовании мммин;
- скорость резания ммин;
- скорость круга при шлифовании ммин;
- скорость заготовки при шлифовании ммин.
- тангенциальная составляющая силы резания (окружная сила при сверлении) Н;
- мощность резания кВт.
Произведем расчет технического нормирования операций 005 и 010 для остальных операций устанавливаем по нормативам.
Нормирование для операции 010 токарная
Основное (технологическое) время для подрезки торцов на токарном станке определится как
где - расчетная длина пути резца имеющего наибольшую длину обтачивания; - число проходов; n - число оборотов шпинделя в минуту; s - подача резца за один оборот шпинделя в мм.
Число оборотов шпинделя
где - скорость резания; d - диаметр подрезаемого торца.
где - длина поверхности обтачиваемой резцом; - величина врезания резца включая путь на подход резца; - величина перебега резца.
Величина врезания поперечным перемещением продольного суппорта определяется по формуле
где - глубина резания; - главный угол резца в плане.
Величина перебега резца
Количество проходов .
Определим состав подготовительно-заключительного времени : установка заготовки в патроне – 7 мин; установка резца в многорезцовой державке – 2 мин; получение инструмента и приспособлений до начала работы и сдачи их после завершения работы – 7 мин. Т.о. .
Время на установку и снятие детали закрепление ее и открепление (самоцентрирующийся патрон) .
Время на приемы управления : включить и выключить станок кнопкой – 001 мин; переместить каретку суппорта в продольном направлении – 006 мин. Тогда .
Время затраченное на измерение детали равно 012 мин; при 20% контролируемых деталей получим .
Поправочный коэффициент на вспомогательное время при среднесерийном производстве .
Вспомогательное время .
Время на обслуживание рабочего места и отдых составляет 7% оперативного времени тогда
Основное (технологическое) время для обтачивания наружной поверхности определится как
где - скорость резания; d - диаметр наружной поверхности.
Время затраченное на измерение детали равно 016 мин; при 20% контролируемых деталей получим .
Время на обслуживание рабочего места и отдых составляет 8% оперативного времени тогда
Штучно-калькуляционное время определим по формуле:
где n – количество изделий в партии.
Нормирование для операции 010 зубофрезерная
Основное (технологическое) время для фрезерования определится как
где - расчетная длина обработки фрезой; - число проходов; - минутная подача в мммин.
Длина обработки фрезой
где - длина фрезеруемой поверхности; - длина врезания фрезы; - величина перебега фрезы.
Для торцового фрезерования величина врезания фрезы определяется по формуле:
где - диаметр фрезы; - ширина фрезерования; - главный угол фрезы в плане.
При ; ; длина врезания определится
Определим состав подготовительно-заключительного времени : установка заготовки в цанговой оправке – 18 мин; установка фрезы – 2 мин; получение инструмента и приспособлений до начала работы и сдачи их после завершения работы – 7 мин. Т.о. .
Время на установку и снятие детали закрепление ее и открепление (цанговая разжимная оправка) .
Время на приемы управления : включить и выключить станок кнопкой – 001 мин; подвести или отвести фрезу к детали при обработке – 004 мин; переместить шпиндель в вертикальном направлении – 001 мин; переместить стол – 005 мин. Тогда .
Расчеты норм времени сводятся в таблицу 17.
Общее время изготовления одной детали
При выполнении данной курсовой работы был разработан один из возможных вариантов технологического процесса обработки детали «Втулка».
Было подобрано соответствующее оборудование и станочные приспособления с установлением рациональных режимов резания и технологически обоснованных норм времени режущий вспомогательный и измерительный инструмент. Произведен расчет припусков на обрабатываемые поверхности детали составлен комплект операционных карт и карт эскизов.
Проделанная работа позволила закрепить и применить полученные знания по курсам: Технология машиностроения; Метрология стандартизация сертификация.
Выполнение данной курсовой работы способствовало более подробному ознакомлению с принятой в машиностроении терминологией с общей последовательностью выполнения проектных работ; получению навыков оценки степени технологичности изделия и способам ее повышения. а также получению первичных знаний и навыков варианта технологического процесса обеспечивающего получение заданного качества изделия наиболее производительными и рентабельными способами.
Ансеров М.А. Приспособления для металлорежущих станков. Расчеты и конструкции. - изд. 3-е стереотип. - М.: изд-во "Машиностроение" 1966. - 652 с. ил.
Анурьев В.И. Справочник конструктора-машиностроителя: В 3 т. Т.1. - 8-е изд. перераб. и доп. Под ред И.Н. Жестковой. - М.: Машиностроение 2001. - 920 с. ил.
Допуски и посадки: Справочник в 2-х ч. Ч.1Под ред. В.Д. Мягкова. - 5-е изд. перераб. и доп. - Л.: Машиностроение. Ленингр. отд-ние 1979. - 544 с. ил.
Допуски и посадки: Справочник в 2-х ч. Ч.2Под ред. В.Д. Мягкова. - 5-е изд. перераб. и доп. - Л.: Машиностроение. Ленингр. отд-ние 1979. - 544 с. ил.
Егоров М.Е. Технология машиностроения: Учебник для вузовМ.Е. Егоров В.И. Дементьев В.Л. Дмитриев. - М.: Высш. школа 1976. - 534 с. ил.
Кожевников Д.В. Гречишников В.А. Кирсанов С.В. Кокарев В.И. Схиртладзе А.Г. Режущий инструмент: Учебник для вузов [Текст] Под редакцией С.В. Кирсанова. М.: Машиностроение 2004. - 512 с. ил.
Лебедев Л.В. Шрубченко И.В. Погонин А.А. Схиртладзе А.Г. Основы технологии машиностроения: учеб. пособие Л.В. Лебедев И.В. Шрубченко А.А. Погонин А.Г. Схиртладзе. - 3-изд. перераб. и доп. - Белгород: Изд-во БГТУ им. В.Г. Шухова 2005. - 264 с. ил.
Маталин А.А. Технология машиностроения: Учебник для машиностроительных вузов по специальности "Технология машиностроения металлорежущие станки и инструменты". - Л.: Машиностроение Ленингр. отд-ние 1985. - 496 с. ил.
Металлорежущие станки (альбом общих видов кинематических схем и узлов). Кучер А.М. Киватицкий М.М. Покровский А.А. Изд-во "Машиностроение" 1972. - 308 с. ил.
Оборудование машиностроительных предприятий: Учебник А.Г. Схиртладзе В.И. Выходец Н.И. Никифоров Я.Н. Отений ВолгГТУ Волгоград 2005. - 128 с.
Справочник инструментальщика И.А. Ординарцев Г.В. Филиппов А.Н. Шевченко и др.; Под общ. ред. И.А. Ординарцева. - Л.: Машиностроение. Ленингр. отд-ние 1987. - 846 с. ил.
Справочник технолога-машиностроителя. В 2-х т. Т.1Под ред А.Г. Косиловой и Р.К. Мещерякова. - 4-е изд. перераб и доп. - М.: Машиностроение 1985. - 656 с. ил.
Справочник технолога-машиностроителя. В 2-х т. Т.2Под ред А.Г. Косиловой и Р.К. Мещерякова. - 4-е изд. перераб и доп. - М.: Машиностроение 1986. - 496 с. ил.
ГОСТ 3.1118-82 Единая система технологической документации. Формы и правила оформления маршрутных карт.
ГОСТ 3.1125-88 Правила графического выполнения элементов литейных форм и отливок.
ГОСТ 3.1404 Формы и правила оформления документов на технологические процессы и операции обработки резанием.
ГОСТ 2675-80 Патроны самоцентрирующиеся трехкулачковые.
ГОСТ 17123-79 Круги эльборовые шлифовальные. Типы и основные размеры.
ГОСТ 18868-73 Резцы токарные проходные отогнутые с пластинками из быстрорежущей стали. Конструкция и размеры.
ГОСТ 18880-93 Резцы токарные подрезные отогнутые с пластинами из твердого сплава. Конструкция и размеры.
ГОСТ 26645-85 Отливки из металлов и сплавов. Допуски размеров массы и припуски на механическую обработку.
Чертеж заготовки.cdw

Штамповочные уклоны - 1
Штамповочные радиусы закругления - 2 мм
Сталь 40ХФА ГОСТ 4543-84
БГТУ им. В.Г. Шухова
Рекомендуемые чертежи
- 24.01.2023
- 24.01.2023
- 24.01.2023
- 13.12.2022
- 24.01.2023
Свободное скачивание на сегодня
Другие проекты
- 16.05.2019