Разработка автоматизированного склада для пакетированных грузов




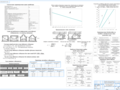
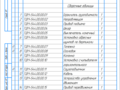
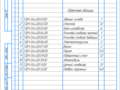
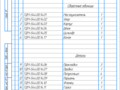
- Добавлен: 25.01.2023
- Размер: 123 MB
- Закачек: 1
Описание
Разработка автоматизированного склада для пакетированных грузов
Состав проекта
![]() |
![]() |
![]() ![]() ![]() |
![]() |
![]() ![]() ![]() |
![]() ![]() ![]() |
![]() ![]() ![]() |
![]() ![]() ![]() |
![]() ![]() ![]() |
![]() ![]() ![]() |
![]() ![]() ![]() |
![]() ![]() ![]() |
![]() ![]() ![]() |
![]() ![]() ![]() |
![]() ![]() ![]() |
![]() ![]() ![]() |
![]() ![]() ![]() |
![]() ![]() ![]() |
![]() ![]() ![]() |
![]() ![]() ![]() |
![]() ![]() ![]() |
![]() ![]() ![]() |
![]() ![]() ![]() |
![]() ![]() ![]() |
![]() ![]() ![]() |
![]() ![]() ![]() |
![]() ![]() |
![]() ![]() ![]() |
![]() ![]() ![]() |
![]() ![]() ![]() |
![]() |
![]() ![]() ![]() ![]() |
![]() ![]() ![]() ![]() |
![]() |
![]() |
![]() ![]() ![]() |
![]() |
![]() |
![]() ![]() ![]() ![]() |
![]() |
![]() |
![]() ![]() ![]() ![]() |
![]() ![]() ![]() ![]() |
![]() ![]() ![]() ![]() |
![]() |
![]() |
![]() |
![]() |
![]() ![]() ![]() ![]() |
![]() |
![]() |
![]() ![]() ![]() ![]() |
![]() |
![]() |
![]() |
![]() |
![]() ![]() ![]() ![]() |
![]() |
![]() |
![]() |
![]() |
![]() |
![]() |
![]() |
![]() ![]() ![]() ![]() |
![]() ![]() ![]() ![]() |
![]() ![]() ![]() ![]() |
![]() |
![]() ![]() ![]() |
![]() ![]() ![]() |
![]() |
![]() |
![]() ![]() ![]() ![]() |
![]() |
![]() ![]() ![]() ![]() |
![]() |
![]() ![]() ![]() ![]() |
![]() |
![]() |
![]() |
![]() |
![]() |
![]() |
![]() |
![]() |
![]() |
![]() |
![]() |
![]() |
![]() |
![]() |
![]() |
![]() |
![]() |
![]() |
![]() |
![]() |
Дополнительная информация
Содержание.docx
1.Общая компоновка16
2.1.Механизм подъема19
2.2.Механизм передвижения20
2.3.Телескопический захват21
2.4.Система управления23
Анализ различных вариантов конструктивного исполнения и основных расчетов крана-штабелера24
1.Назначение специфика и нормативные основы24
3.Расчет стеллажных кранов-штабелеров33
Описание конструкции и предварительная разработка общего вида крана-штабелера39
1.Техническое описание41
3.Устройство и работа изделия43
Конструкторская часть46
1.Конструктивная разработка отдельных механизмов и узлов46
1.1.Расчет механизма передвижения тележки46
1.2.Расчет механизма подъема62
1.3.Расчет механизма передвижения вил79
1.4.Расчет гидравлического буфера85
1.Условия работы складов на железнодорожном транспорте90
2.Организация работ92
Технологическая часть103
1.Разработка технологического процесса штока гидробуфера103
1.1.Анализ технологических требований изделия детали103
1.2.Выбор вида финишной обработки конструктивных элементов детали104
1.3.Выбор способа установки заготовки для ее обработки105
1.4.Выбор вида определение размеров заготовки типа и типоразмера центровых отверстий105
1.5.Составление укрупнённого маршрута изготовления детали106
2.Разработка операций по формированию контура детали107
2.1.Расчет числа стадий обработки по каждому конструктивному элементу107
2.2.Расчет точности промежуточных размеров заготовки по стадиям обработки108
2.3. Определение промежуточных размеров по стадии механической обработки109
3.Составление плана токарной и шлифовальной обработок детали114
3.1.Расчет предельно-допустимых глубин резания при черновом обтачивании115
4.Выбор и расчет режимов резания117
4.1.Токарная обработка117
4.2.Расчет режимов шлифования118
4.3.Расчет режимов предварительного шлифования119
4.4.Расчет режимов окончательного шлифования120
Технико-экономические расчеты124
1.Описание сравниваемых результатов. Исходные данные для расчетов124
2.Определение барьерной ставки126
3.Расчет инвестиций и расходов127
4.Изменение расходов132
5.Чистая текущая стоимость (NPV)135
Безопасность жизнедеятельности138
1.Безопасность персонала при обслуживании проектируемого склада138
1.1.Эксплуатационно-технические характеристики138
1.2.Требования к персоналу режимы работ квалификация138
1.3.Основные опасности и вредности при работе персонала139
1.4.Технические и организационные мероприятия по обеспечению персонала при работе на складе140
1.5.Техника безопасности при обслуживании склада151
2.Безопасность персонала в чрезвычайных ситуациях152
2.1.Пожарная безопасность на складах152
Список используемой литературы161
Экономическая часть.docx
1. Описание сравниваемых результатов.
Исходные данные для расчёта.
Вилочный захват крана-штабелера включает в себя электромеханический привод в котором движение передаётся от электродвигателя к исполнительному механизму через карданный вал. Комплекс обслуживают 3 человека.
Вилочный захват крана-штабелера включает в себя гидравлический привод в котором движение исполнительного механизма происходит от электродвигателя соединённого непосредственно с рабочим органом. Комплекс обслуживает 2 человека.
Исходные данные Таблица 8.1.
Количество элементов ппривода:
- гидрораспределитель
- гидроклапан давления
Продолжение таблицы 8.1.
2. Определение барьерной ставки.
Барьерная ставка определяет ту финансовую отдачу которую инвесторы ожидают от своих капвложений и включает в себя два компонента – свободную от риска ставку СРС и страховую премию СП.
Стоимость капитала – это средневзвешенная цена (в процентах) которую предприятие уплатило за денежные средства использованные для формирования своего капитала. Эта величина определяется соотношением заемного и собственного капиталов в пассивной части баланса и может быть определена следующим образом:
СК = БС = ДД · СД + ДСК · ССК
где СК – стоимость капитала %;
ДСК – доля собственного капитала;
ССК – стоимость собственного капитала %.
Так как выплаты процентов по займам уменьшают величину налогооблагаемой прибыли то собственно уменьшается и величина налоговых выплат. Экономия на налогах частично компенсирует выплаты по долгам. Поэтому процент выплат по займам с учётом этой экономии составит:
СД = (1 – СН) · СРССД
где СН – ставка налога на прибыль;
СРССД – уровень процентной ставки.
Доля долга и доля собственных средств:
Эффективные ставки то есть ставки с учётом реинвестиций по месяцам:
НСД = ((Нкб р) + 1)р – 1
где НСД – номинальная банковская ставка;
р – число периодов начисления процентов внутри года.
Ставка процента СРС:
НСК = ((НД р) + 1)р + 1
НСД = ((035 2) + 1)2 – 1 = 038
СРССД = (038 – 012) (1 + 012) = 023
НСК = ((024 2) + 1)2 – 1 = 025
СРССК = (025 – 012) (1 + 012) = 0116
СД = (1 – 024) · 023 = 0175
БС = 024 · 0175 + 076 · 0116 = 013 13%
3. Расчёт инвестиций и расходов.
К1 = Кдв + Кт + Кр + Кк.в. + Кмах + Кмуфт + Крем
где Кдв – капитальные вложения на закупку
Кт – капитальные вложения на закупку
Кр – капитальные вложения на закупку
Кк.в. – капитальные вложения на закупку карданных
Кмах – капитальные вложения на закупку маховиков;
Кмуфт – капитальные вложения на закупку муфт
Крем – капитальные вложения на закупку ремней.
Кдв = Zдв · Цдв · (1 + γм)
где Цдв – стоимость одного электродвигателя
Zдв – число электродвигателей
γм – коэффициент учитывающий затраты на доставку и
Кдв = 1 · 4690 · (1 + 012) = 5253 (руб.)
Кт. = Zт. · Цт. · (1 + γм)
где Цт. – стоимость одного тормоза
Кт. = 1 · 2050 · (1 + 012) = 2296 (руб.)
Кр. = Zр. · Цр. · (1 + γм)
где Цр. – стоимость одного редуктора
Zр. – число редукторов
Кр. = 1 · 1800 · (1 + 012) = 2016 (руб.)
Кк.в. = Zк.в. · Цк.в. · (1 + γм.)
где Цк.в. – стоимость одного карданного вала
Zк.в. – число карданных валов
Кк.в. = 2 · 2140 · (1 + 012) = 4794 (руб.)
Кмах = Zмах · Цмах · (1 + γм)
где Цмах – стоимость одного маховика
Zмах – число маховиков
Кмах = 1 · 1130 · (1 + 012) = 1266 (руб.)
Кмуфт = Zмуфт · Цмуфт · (1 + γм)
где Цмуфт – стоимость одной муфты шарнирной
Цмуфт = 2030 (руб.);
Zмуфт – число муфт шарнирных
Кмуфт = 2 · 2030 · (1 + 012) = 4547 (руб.)
Крем = Zрем · Црем · (1 + γм)
где Црем – стоимость одного ремня
Крем = 2 · 280 · (1 + 012) = 466 (руб.)
К1 = 5253 + 2296 + 2016 + 4794 + 1266 + 4547 + 466 =
К2 = Кдв + Кн + Кц + Краспр + Кж.т. + Ккл.дав. + Кф + Кб + Кв
Кн – капитальные вложения на закупку гидронасосов;
Кц – капитальные вложения на закупку
Краспр – капитальные вложения на закупку
гидрораспределителей;
Кж.т. – капитальные вложения на закупку жёстких трубопроводов;
Ккл.дав. – капитальные вложения на закупку клапанов
Кф – капитальные вложения на закупку фильтров;
Кб - капитальные вложения на закупку бака;
Кв - капитальные вложения на закупку вентиля.
Кдв = 1 · 16750 · (1 + 012) = 18760 (руб.)
Кн = Zн · Цн · (1 + γм)
где Цн – стоимость одного гидронасоса
Zн – число гидронасосов
Кн = 1 · 3558 · (1 + 012) = 3985 (руб.)
Кц = Zц · Цц · (1 + γц)
где Цц – стоимость одного гидроцилиндра
Zц – число гидроцилиндров
Кц = 2 · 2000 · (1 + 012) = 4480 (руб.)
Краспр = Zраспр · Цраспр · (1 + γм)
где Цраспр – стоимость одного гидрораспределителя
Цраспр = 2297 (руб.);
Zраспр – число гидрораспределителей
Краспр = 1 · 2297 · (1 + 012) = 2573 (руб.)
Кж.т. = Lж.т. · Цж.т · (1 + γм)
где Цж.т. – стоимость одного метра жёсткого трубопровода
Lж.т. – длина жёсткого трубопровода
Кж.т. = 3 · 110 · (1 + 012) = 370 (руб.)
Ккл.дав = Zкл.дав · Цкл.дав. · (1 + γм)
где Цкл.дав. – стоимость одного клапана давления
Цкл.дав. = 1200 (руб.);
Zкл.дав. – число обратных клапанов
Ккл.дав. = 1 · 1200 · (1 + 012) = 1344 (руб.)
Кф = Zф · Цф · (1 + γм)
где Цф – стоимость одного фильтра
Кф = 1 · 1040 · (1 + 012) = 1165 (руб.)
Кб = Zб · Цб · (1 + γб)
где Цб. – стоимость одного бака
Кб = 1 · 1500 · (1 + 012) = 1680 (руб.)
Кв = Zв · Цв. · (1 + γв)
где Цв – стоимость одного вентиля
Цкл.дав. = 1598 (руб.);
Zкл.дав. – число вентилей
Ккл.дав. = 1 · 1598 · (1 + 012) = 1790 (руб.)
К2 = 18760 + 3985 + 4480 + 2573 + 370 + 1344 + 1165 + 1680 + 1790 = 36147 (руб.)
4. Расчёт приращения доходов и расходов.
С1 = Сзаробщ + Сотч + Снакл + Срем т.о. + Сэл + Саморт
где Сзаробщ – расходы на заработную плату
обслуживающего персонала;
Сотч – отчисления на социальные нужды;
Снакл – накладные расходы (расходы на содержание административно-управленческого персонала);
Срем т.о. – расходы на ремонт и техническое
Сэл - расходы на электроэнергию за год;
Саморт – амортизационные отчисления на реновацию.
Сзаробщ = Стар.зар. + Сдоплаты + Сдоп.зар.
где Стар.зар. – тарифная заработная плата
Стар.зар. = Σ Кr · Tст · 12
где Кr – количество обслуживающего персонала;
Тст – тарифная ставка по должностям.
Сдоплаты – доплата к заработной плате.
Кr = 3 (чел.) Тст = 2100 (руб.)
Стар.зар. = 3 · 2100 · 12 = 75600 (руб.)
Сдоплаты = Стар.зар. · 04
Сдоплаты = 75600 · 04 = 30240 (руб.)
Сдоп.зар. – дополнительная заработная плата;
Сдоп.зар. = (Стар.зар. + Сдоплаты) · 01
Сдоп.зар. = (75600 + 30240) · 01 = 10584 (руб.)
Сзаробщ = 75600 + 30240 + 10584 = 116424 (руб.)
Сотч = 0385 · Сзаробщ
Сотч = 0385 · 116424 = 44824 (руб.)
Снакл = 02 · Сзаробщ
Снакл = 02 · 116424 = 23285 (руб.)
Сэл = Цэл*Ки* Ci*Pi*Fэф
Цэл- тариф на электроэнергию : Цэл=059 ркВт*ч ;
Ки- коэффициент использования оборудования по времени 07
Fэф – эффективный годовой фонд времени работы оборудования
Fэф =(365–n(праздники)-n(выходные))*n(смен)*8*0.85=(365-11-104)*2*8*0.85=3400 час
Сэл = 059*07*1*065*3 400 = 913 (руб.)
Срем т.о. = 012 · К1
Срем т.о. = 012 · 143272 = 17193 (руб.)
где Q – срок службы машины Q = 12 лет.
Самор. = 20638 12 = 1720 (руб.)
С1 = 116424 + 44824 + 23285 + 17193 + 913 + 1720 = 204358 (руб.)
С2 = Сзаробщ + Сотч + Снакл + Срем т.о. + Сэл + Саморт
Стар.зар. = Σ Кr · Tст · 12
Кr = 2 (чел.) Тст = 2100 (руб.)
Стар.зар. = 2 · 2100 · 12 = 50400 (руб.)
Сдоплаты = 50400 · 04 = 20160 (руб.)
Сдоп.зар. = (50400 + 20160) · 01 = 7056 (руб.)
Сзаробщ = 50400 + 20160 + 7056 = 77616 (руб.)
Сотч = 0385 · 77616 = 29882 (руб.)
Снакл = 02 · 77616 = 15524 (руб.)
Сэл = 059*07*1*044*3 400 = 618 руб
Срем т.о. = 012 · К2
Срем т.о. = 012 · 218839 = 26207 (руб.)
Самор. = 36147 12 = 3013 (руб.)
С2 = 77616 + 29882 + 15524 + 26207 + 618 + 3013 = 152860 (руб.)
Расчёт чистых денежных потоков приведён в таблице 8.2.
Расчёт чистых денежных потоков
Приращение доходов и расходов:
- экономия заработной платы
- отчисления на социальные
- расходы по содержанию и
эксплуатации оборудования
- расходы на электроэнергию
- Приращение доходов
Чистые денежные потоки
5. Чистая текущая стоимость (NPV).
Чистая текущая стоимость является суммой дисконтированных чистых денежных потоков порождённых капиталовложениями и определяется следующим образом:
где ЧДП – чистый денежный поток руб.;
HR – барьерная ставка;
n – число лет функционирования проекта.
ЧДП берётся со знаком соответствующим оттоку или притоку денежных средств.
Положительное значение чистой текущей стоимости (NPV) говорит об эффективности рассматриваемого варианта.
Рассчитаем значения чистой текущей стоимости. Данные занесем в таблицу 8.3.
По полученным значениям чистой текущей стоимости (NVP) построим график зависимости её от числа годов срока службы машины (рис. 8.1.).
Внедрение и использование модернизированного захвата увеличивает производительность погрузочно-разгрузочных работ позволяет увеличить грузопоток что является основной экономической характеристикой склада и получить экономический эффект.
Курсовая по экономике только 5-е задание.doc
Капитал предприятия формируется из двух источников: собственного и заёмного. Для привлечения капитала из этих источников предприятию необходимо платить. Это либо процент по кредитам (заёмный капитал) либо дивиденды ( акционерный капитал). Чем более рисковый проект тем более высоких дивидендов будут ожидать акционеры а кредиторы будут предлагать кредиты под более высокие проценты. И акции предприятий и кредиты реализуются на финансовых рынках. И именно силы свободного рынка определяют степень риска инвестиций.
Поэтому можно сказать что стоимость капитала предприятия представляет собой рыночную оценку уровня риска по операциям предприятия. Предприятия принимают эту оценку в качестве среднего значения барьерного коэффициента HR так как у них нет более объективного показателя.
В общем случае стоимость капитала - это средневзвешенная цена (в процентах) которую предприятие уплатило за денежные средства используемые для формирования своего капитала. Эта величина определяется соотношением заемного и собственного капиталов:
БС=CK=ДД*СД + ДСК*ССК
где: СК-стоимость капитала % ;
СД-стоимость долга%;
ДСК-доля собственного капитала;
ССК-стоимость собственного капитала%.
Так как выплаты процентов уменьшают величину налогооблагаемой прибыли то соответственно уменьшается и величина налоговых выплат. Экономия на налогах частично компенсирует выплаты по долгам. Поэтому реальный процент выплат по долгам с учетом экономии составит
СД=(1 - СН) * Nе(СД)
где: СН - ставка налога на прибыль;
Nе(СД) - уровень эф. процентной ставки.
Доля долга и собственных средств в сумме равны единице. Поэтому определив одну из составляющих можно определить и другую:
Стоимость собственного капитала при отсутствии развитого фондового рынка в России для Государственных предприятий можно взять на уровне альтернативного размещения средств ( депозитные банковские ставки проценты по государственным облигациям и т.д.).
В условиях высокой инфляции ставки ссудного процента и депозитные ставки рассчитываются с учетом внутригодовых реинвестиций и очищаются от инфляции по следующей методике.
Берутся номинальные ( т.е. с учетом инфляции) годовые ставки коммерческих банков. На их основе рассчитываются эффективные ставки (т.е. с учетом реинвестиций по периодам внутри года):
Ne(СД ) = ( 1 + ———— ) ^p - 1
Ne( ССК) = ( 1 + ———— ) ^p - 1
где: Ne(СД ССК) - номинальная эффективная ставка (кредитная
и депозитная соответственно)
N(кб дб) - номинальная банковская ставка (кредит-
ная и депозитная соответсвенно)
p-число периодов начисления процентов внутри года.
Полученное значение Nе(СД) подставляется в формулу расчета СД а значение Nе(ССК) является искомым значением ССК.
Определение экономических результатов (денежных пото-
ков) по вариантам инвестиций.
Хотя в рыночных условиях предприятие старается максимизировать свою прибыль но при определении эффективности инвестиций используют не результаты изменения прибыли а так называемые чистые денежные потоки ЧДП. Это связано с тем что прибыль определяется в соответствии с бухгалтерскими правилами и она измеряется как разница между доходами предприятия и его расходами за определенный период времени. Так как некоторые виды доходов и расходов не оказывают влияния на денежную наличность то величины прибыли и денежных потоков могут различаться. Чистые денежные потоки могут выступать в виде притока (+) или оттока (-).Графически это изображено на рис.3.
- Срок эксплуатации проекта
Рисунок 3. Движение денежных потоков.
Расчет денежных потоков обычно оформляется в виде таблицы 7 где денежные потоки разделены на три части.
Приращения доходов и расходов.
Корректировка денежных потоков.
Прогноз чистых денежных потоков
Приращения доходов и расходов
Корректировка денежных потоков
Чистые денежные потоки
В части “Инвестиции” представлены все существенные и связанные с инвестицией расходы. Они включают стоимость новых активов и сопутствующие им расходы. Обычно считается что инвестиции проводятся в нулевой период.
В части “Приращения доходов и расходов” определяются экономические результаты получающиеся в результате осуществления инвестиций. Здесь рассматриваются только те денежные потоки которые изменяют сложившееся состояние производства и могут быть объяснены именно действием новых инвестиций. В этой части определяются изменения расходов по заработной плате материалам топливу эл. энергии амортизации налогам и т. д. Алгебраическая сумма притоков и оттоков денежных средств в этой части дает величину приращения доходов от инвестиций.
В части “Корректировка денежных потоков” содержатся статьи которые прибавляются или вычитаются из доходов части 2. Эти корректировки включают те статьи которые не входят в отчет о доходах но которые связаны с приходом или расходом наличности а также статьи которые появляются в отчете о доходах но не связаны с движением наличных денег. Из всех корректировок денежных потоков самые важные связаны с амортизационными отчислениями и остаточной стоимостью.
Амортизация является важной составляющей при определение денежных потоков по следующим причинам.
Амортизация часто является одной из самых крупных статей расходов.
Поскольку амортизацию можно исключить из налогооблажения ее учет уменьшает налоговые обязательства.
В силу того что амортизация представляет собой неденежный расход и деньги не покидают предприятие в качестве платы за нее то предприятие получает возможность использовать эти деньги.
В части 2 (табл. 7) амортизация рассматривается как расход который может быть использован для уменьшения налоговых платежей. Но раз деньги не уходят с предприятия то они могут использоваться то есть их можно рассматривать как доход. Поэтому необходимо сделать корректировку то есть в части 3 поместить величину амортизации с знаком плюс. В результате рассматривая амортизацию как отток в части 2 и как приток в части 3 получаем нулевое значение. Единственным результатом будет уменьшение выплат налогов на прибыль.
Остаточная стоимость имеет отношение к стоимости активов в конце инвестиционного периода если есть возможность их реализовать.
Пример расчета чистых денежных потоков.
Предположим что новое оборудование стоит 250 тыс. руб. Использование данного оборудования приведет к следующим экономическим результатам: экономия заработной платы - 60 тыс. руб. увеличение расходов на эл. энергию - 8 тыс. руб. увеличение расходов по содержанию и эксплуатации оборудования - 2 тыс. руб. Инвестиционный период составляет 7 лет. Остаточная стоимость оборудования - 60 тыс. руб. Расчет проводится в табл. 8 ( в скобках показаны оттоки денежных средств) Норма амортизации - 143
Пример расчета чистых денежных потоков (тыс. руб.)
-стоимость оборудования
-экономия зар. платы
-расходы по содержанию и эксплуатации оборудования
-остаточная стоимость
Чистые денежные потоки (ЧДП)
Показатели эффективности инвестиций.
Основными показателями эффективности инвестиций являются:
Чистая текущая стоимость (NPV).
Внутренняя норма рентабельности (IRR).
Чистая текущая стоимость ( NPV ) представляет сумму дисконтированных чистых денежных потоков порожденных инвестициями и определяется следующим образом:
ЧДП0 ЧДП1 ЧДП2 ЧДПn
NPV = ————— + ————— + —————— + + —————
( 1 + БС)^0 ( 1 + БС)^1 ( 1 + БС)^2 ( 1 + БС)^n
где: ЧДП - чистый денежный поток руб.;
БС - барьерная ставка;
n - число лет функционирования объекта.
Чистый денежный поток берется с знаком соответствующим оттоку или притоку денежных средств. Положительное значение NPV говорит об эффективности рассматриваемого варианта.
Внутренняя норма рентабельности (IRR) представляет собой ставку дисконтирования при которой NPV равно нулю. В этом случае барьерная ставка HR называется внутренней нормой рентабельности IRR. Если величина IRR оказывается больше барьерной ставки HR то такой вариант является эффективным.
В курсовой работе предлагается определить эффективность применения чугунных клиньев и планок вместо стальных в клиновых гасителях колебаний тележек грузовых вагонов. Более высокая износостойкость чугунных клиньев позволяет повысить срок их службы по сравнению со стальными. Но чугунные клинья не поддаются восстановлению в то время как часть стальных восстанавливается наплавкой что в свою очередь требует дополнительного оборудования и соответственно дополнительных капитальных вложений и текущих расходов при ремонте. Выбор эффективного варианта проводится по рассмотренной выше методике.
Титул техников диплома.doc
ЖЕЛЕЗНОДОРОЖНОГО ТРАНСПОРТА
ГОСУДАРСТВЕННОЕ ОБРАЗОВАТЕЛЬНОЕ УЧРЕЖДЕНИЕ ВЫСШЕГО
ПРОФЕССИОНАЛЬНОГО ОБРАЗОВАНИЯ
«МОСКОВСКИЙ ГОСУДАРСТВЕННЫЙ УНИВЕРСИТЕТ
ПУТЕЙ СООБЩЕНИЯ» (МИИТ)
Зав. кафедрой «ПСМ и РК»
Руководитель проекта ( )
Консультант по экономическим вопросам ( )
Консультант по технологическим вопросам ( )
Консультант по вопросам безопасности
жизнедеятельности ( )
Методичка по экономической части дипломных проектов (СДМ).doc
РОССИЙСКОЙ ФЕДЕРАЦИИ
МОСКОВСКИЙ ГОСУДАРСТВЕННЫЙ УНИВЕРСИТЕТ ПУТЕЙ СООБЩЕНИЯ (МИИТ)
Кафедра «Экономика организация и управление производством»
МЕТОДИЧЕСКИЕ УКАЗАНИЯ
К экономической части дипломных проектов
для студентов специальности
“Строительно-дорожные машины и оборудование ”
Основные требования и порядок обоснования решений принимаемых в дипломных проектах
Дипломное проектирование — заключительный этап подготовки специалиста в высшем учебном заведении. Оно закрепляет знание теории и дает практические навыки самостоятельной работы в области технических и экономических расчетов выбора оптимальных вариантов производства работ организации труда использования техники и т. д.
В экономической части дипломных проектов по погрузочно-разгрузочным строительным и путевым работам дипломник должен выполнить технико-экономические расчеты по выбранным вариантам сделать стоимостной и качественный анализ вариантов и рассчитать эффективность внедрения проектируемой (модернизируемой) машины.
Расчету экономической эффективности предлагаемого варианта с использованием проектируемой машины должно предшествовать:
-определение условий использования проектируемой машины;
-обоснование принятой технологии выполнения работ;
-выбор базы сравнения т. е. определение преимуществ и недостатков действующей в данных условиях или ранее проектируемой технологии производства работ;
- расчет производительности машин эффективного времени работы каждой машины в часах или машино-сменах за год годового объема работ.
Эффективность инвестиционного проекта - категория отражающая соответствие инвестиционного проекта целям н интересам его участников. Для разных участников проекта его эффективность может быть различной.
Эффективносчь инвестиционных проектов может оцениваться как количественными так и качественными характеристиками. .
При анализе инвестиционных проектов в зависимости от их характера и целей используются показатели обшей иили сравнительной эффективности.
Показатели общей эффективности позволяют оценить эффективность инвестиций по конкретному проекту при учете всех затрат и результатов.
Показатели сравнительной эффективности дают возможность выбрать наиболее рациональные решения из числа анализируемых вариантов при учете только изменяющихся но вариантам частей затрат и результатов что снижает трудоемкость оптимизации решения.
Как показатели общей так и сравнительной эффективности могут иметь форму:
показатели общественной (социально-экономической) эффективности которые применяются как правило для народнохозяйственных и крупномасштабных проектов и учитывают затраты и результаты допускающие стоимостное измерение последствия осуществления инвестиционного проекта для общества в целом в том числе непосредственные результаты и затраты проекта затраты и результаты в смежных секторах экономики а также экологические социальные и иные внеэкономические эффекты выходящие за пределы прямых финансовых интересов участников инвестиционного проекта;
показатели коммерческой (отраслевой или объектовой) эффективности которые используются для обоснования большинства инвестиционных проектов на железнодорожном транспорте и учитывающие финансовые последствия в предположении что участник реализующий инвестиционный проект производит все необходимые для реализации проекта затраты и пользуется всеми его результатами. В дипломной работе используются показатели коммерческой эффективности.
Денежные потоки по видам деятельности
При оценке инвестиционного проекта необходимо учесть что каждое предприятие осуществляет в ходе проекта разные виды деятельности. Выделяют три вида деятельности: инвестиционная операционная и финансовая. Инвестиционная деятельность охватывает процесс создания основных средств — сюда включаются капитальное строительство а также создание или наращивание оборотного капитала. Под операционной деятельностью понимается производственная деятельность. Другой термин используется здесь потому что основной деятельностью предприятия может быть не только промышленная (производство какой-либо промышленной продукции) но и строительная транспортная торговая а также оказание каких-либо услуг. В подобных ситуациях говорить о "производстве" не корректно. К финансовой деятельности относятся операции привлечения и возврата заемных средств.
С каждым видом деятельности связаны свои денежные потоки. Этот термин в общем случае охватывает три элемента:
приток реальных денег (денежные поступления);
отток реальных денег (расходы);
сальдо реальных денег (активный баланс эффект) — разность между притоком и оттоком реальных денег
Структура денежных потоков
В результате инвестиционной деятельности обычно растут долгосрочные активы предприятия (основные средства) что связано главным образом с затратами (оттоками реальных денег). В составе этих затрат можно выделить:
первоначальные инвестиции;
предпроизводственные расходы;
ликвидационные затраты.
К первоначальным инвестициям относятся;
инвестиции (вложения) в создание или прирост основных средств осуществляемые до начала операционной деятельности (затраты на проведение изыскательских конструкторских и опытных работ
затраты на приобретение и аренду земельных участков включая стоимость подготовки к освоению; затраты на приобретение и доставку машин и оборудования; затраты на приобретение или строительство зданий сооружений и передаточных устройств; затраты на приобретение патентов лицензий ноу-хау технологий и других нематериальных активов; расходы на подготовку кадров для вводимых в действие объектов; прочие единовременные расходы).
налог на имущество плата за земельный участок (земельный налог) и иные аналогичные платежи осуществляемые до начала операционной деятельности;
отчисления на строительство объектов региональной инженерной или социальной инфраструктуры установленные региональной администрацией в зависимости от стоимости строительства проектируемых объектов (инвестиционный налог);
оплата процентов по инвестиционному кредиту полученному для реализации проекта а также оплата других банковских услуг связанных с получением этого кредита произведенная до начала операционной деятельности;
затраты на создание оборотного капитала необходимого для начала операционной деятельности (создание производственных запасов предоплата сырья материалов и комплектующих изделий которые должны быть поставлены в начале операционной деятельности).
Помимо первоначальных инвестиций до начала производства могут предусматриваться также предпроизводственные расходы.
расходы возникающие при образовании и регистрации фирмы (оплата юридических услуг по составлению уставных документов расходы по регистрации фирмы и оформлению прав собственности на земельный участок расходы на эмиссию ценных бумаг и т. п.);
плата за земельный участок (земельный налог) используемый в период строительства объекта;
расходы на предпроизводственные маркетинговые исследования и создание сбытовой сети;
расходы на страхование в период строительства объекта.
В отношении предпроизводственных расходов важно учитывать следующее обстоятельство. Подобные расходы в соответствии с действующим порядком не включаются в сметную стоимость объекта не относятся к капитальным вложениям и потому не амортизируются. С другой стороны они носят явно единовременный характер. В бухгалтерском учете эти расходы считаются текущими и учитываются как расходы будущих периодов. Поэтому они относятся на себестоимость продукции в течение определенного учетной политикой предприятия срока который обычно короче срока службы основного технологического оборудования. В этой связи в расчетах эффективности удобно рассматривать предпроизводственные расходы как особый вид инвестиций (но не капиталовложений') с "индивидуальным" сроком амортизации.
К текущим инвестициям относятся осуществляемые после ввода предприятия в эксплуатацию:
затраты по приобретению основных средств в целях предусмотренного проектом расширения или модернизации производства а также взамен выбывающих в связи с их физическим или моральным износом;
затраты по приобретению нематериальных активов необходимых для продолжения расширения или изменения характера операционной деятельности;
расходы по созданию объектов социальной инфраструктуры для работников предприятия; отчисления в региональные фонды или затраты на строительство объектов региональной инженерной или социальной инфраструктуры (если требование по осуществлению таких затрат предъявлено региональной администрацией при согласовании или утверждении проекта);
В составе ликвидационных затрат учитываются все осуществляемые после ввода предприятия в эксплуатацию затраты связанные с ликвидацией или реализацией на сторону имущества участника (например затраты па демонтаж и разборку зданий сооружений и оборудования отделение предметов пригодных для дальнейшего использования в производстве оплата транспортных и иных услуг сторонних организаций связанных с реализацией иили утилизацией отходов и металлолома).
Операционная деятельность.
Основным притоком реальных денег от операционной деятельности является выручка от реализации продукции. Исходная информация для ее определения задается по шагам расчетного периода для каждого вида продукции отдельно для реализации на внутреннем и внешнем рынках.
В оттоке реальных денег от операционной деятельности учитываются текущие (операционные) затраты т.е. себестоимость продукции рассчитываемая по статьям калькуляции.
Финансовая деятельность.
Финансовая деятельность отличается от операционной и инвестиционной тем что к ней относятся операции со средствами внешними по отношению к проекту а не со средствами генерируемыми проектом. Денежные потоки по финансовой деятельности в расчетах дипломной работы не учитываются.
Дисконтирование денежных потоков
Один из основных принципов оценки эффективности инвестиционных проектов требует сопоставления связанных с проектом результатов и затрат на протяжении всего периода его реализации. Для этого результаты и затраты относящиеся к разным моментам времени (разновременные) должны быть предварительно приведены в сопоставимый вид.
Наиболее распространенный способ приведения сводится к тому что эффекты относящиеся к другим годам умножаются на некоторые коэффициенты отражающие относительную ценность эффектов этих лет по сравнению с эффектами в году приведения. Такие коэффициенты называются коэффициентами дисконтирования. Значение коэффициента относящееся к n шагу обозначим через a Тогда эффект на этом шаге равный Ф после приведения станет равным a Ф . Эту величину будем называть дисконтированным эффектом или (в тех случаях когда речь идет о денежных потоках) дисконтированным денежным потоком. Коэффициент дисконтирования рассчитывается
Входящий сюда показатель Е играет роль специфического экономического норматива и носит название нормы дисконта (в экономической литературе советского периода этот показатель именовался нормативом эффективности капитальных вложений).
Определение величины нормы дисконта.
Капитал предприятия формируется из двух источников: собственного и заёмного. В общем случае стоимость капитала - это средневзвешенная цена (в процентах) которую предприятие уплатило за денежные средства используемые для формирования своего капитала. Эта величина определяется соотношением заемного и собственного капиталов:
Е=CK=ДД*СД + ДСК*ССК
где: СК-стоимость капитала % ;
СД-стоимость долга%;
ДСК-доля собственного капитала;
ССК-стоимость собственного капитала%.
Так как выплаты процентов уменьшают величину налогооблагаемой прибыли то соответственно уменьшается и величина налоговых выплат. Экономия на налогах частично компенсирует выплаты по долгам. Поэтому реальный процент выплат по долгам с учетом экономии составит
где: СН - ставка налога на прибыль;
ПС - уровень процентной ставки.
Доля долга и собственных средств в сумме равны единице. Поэтому определив одну из составляющих можно определить и другую:
Стоимость собственного капитала при отсутствии развитого фондового рынка в России для предприятий можно взять на уровне альтернативного размещения средств (депозитные банковские ставки. Стоимость долга принимается на уровне кредитных банковских ставок.
Cтавки ссудного процента и депозитные ставки рассчитываются с учетом внутрегодовых реинвестиций. Берутся номинальные годовые ставки коммерческих банков. На их основе рассчитываются эффективные ставки (т.е. с учетом реинвестиций по периодам внутри года):
Ne = ( 1 +----------- ) ^p - 1
где: Ne - номинальная эффективная ставка;
N.б - номинальная банковская ставка;
p-число периодов начисления процентов внутри года.
Показатели эффективности инвестиционных проектов.
В качестве основных показателей используемых для расчетов эффективности инвестиционных проектов применяются:
чистый дисконтированный доход (ЧДД)
внутренняя норма доходности (ВНД)
индексы доходности затрат и инвестиций;
Чистым доходом называется накопленный эффект (сальдо денежного потока) за расчетный период:
где суммирование распространяется на все шаги расчетного периода.
Важнейшим показателем эффективности проекта является чистый дисконтированный доход ЧДД — накопленный дисконтированный эффект за расчетный период. ЧДД рассчитывается по формуле:
Для признания проекта эффективным с точки зрения инвестора необходимо чтобы ЧДД проекта был положительным; при сравнении альтернативных проектов предпочтение должно отдаваться проекту с большим значением ЧДД .
Внутренней нормой доходности называется такое положительное число Ев что при норме дисконта Е = Ев чистый дисконтированный доход проекта обращается в 0 при всех больших значениях Е — отрицателен при всех меньших значениях Е — положителен. Если не выполнено хотя бы одно из этих условий считается что ВНД не существует.
Для оценки эффективности ИП значение ВНД необходимо сопоставлять с нормой дисконта Е. Инвестиционные проекты у которых ВНД > Е имеют положительный ЧДД и поэтому эффективны. Проекты у которых ВНД Е имеют отрицательный ЧДД и потому неэффективны.
Сроком окупаемости называется продолжительность периода от начального момента до момента окупаемости. Моментом окупаемости называется тот наиболее ранний момент времени в расчетном периоде после которого текущий чистый доход ЧД(k) становится и в дальнейшем остается неотрицательным.
При оценке эффективности срок окупаемости как правило выступает только в качестве ограничения.
Сроком окупаемости с учетом дисконтирования называется продолжительность периода от начального момента до "момента окупаемости с учетом дисконтирования". Моментом окупаемости с учетом дисконтирования называется тот наиболее ранний момент времени в расчетном периоде после которого текущий чистый дисконтированный доход ЧДД(k) становится и в дальнейшем остается неотрицательным.
Индексы доходности характеризуют (относительную) "отдачу проекта" на вложенные в него средства. Они могут рассчитываться как для дисконтированных так и для не дисконтированных денежных потоков. При оценке эффективности часто используются:
Индекс доходности затрат — отношение суммы денежных притоков (накопленных поступлений) к сумме денежных оттоков (накопленным платежам).
Индекс доходности дисконтированных затрат — отношение суммы дисконтированных денежных притоков к сумме дисконтированных денежных оттоков.
Индекс доходности инвестиций (ИД) — отношение суммы элементов денежного потока от операционной деятельности к абсолютной величине суммы элементов денежного потока от инвестиционной деятельности. Он равен увеличенному на единицу отношению ЧД к накопленному объему инвестиций;
Индекс доходности дисконтированных инвестиций (ИДД) — отношение суммы дисконтированных элементов денежного потока от операционной деятельности к абсолютной величине дисконтированной суммы элементов денежного потока от инвестиционной деятельности. ИДД равен увеличенному на единицу отношению ЧДД к накопленному дисконтированному объему инвестиций.
При расчете ИД и ИДД могут учитываться либо все капиталовложения за расчетный период включая вложения в замещение выбывающих основных фондов либо только первоначальные капиталовложения осуществляемые до ввода предприятия в эксплуатацию (соответствующие показатели будут конечно иметь различные значения).
Индексы доходности затрат и инвестиций превышают 1 если и только если для этого потока ЧД положителен
Индексы доходности дисконтированных затратой инвестиций превышают 1 если и только если для этого потока ЧДД положителен.
Расчет стоимости машино-смен путевых машин механизмов и оборудования.
Стоимость машино-смен путевых машин механизмов и оборудования может быть определена по формуле:
М = П + Гр + Эр + Гд + И + Зр + Зд + Ф (руб.)
где М - стоимость машино-смены при работе путевых машин механизмов и оборудования руб.;
П -постоянные расходы на полное восстановление первоначальной
стоимости путевых машин механизмов и оборудования за машино- смену руб.;
Гр Эр - стоимость горючего или электроэнергии (потребляемой от внешних источников электроснабжения) моторного масла и смазки израсходованных на работу в течение необходимого времени в пределах машино- смены путевых машин механизмов и оборудования руб.;
Гд - стоимость горючего и моторного масла израсходованных самоходными путевыми машинами по пути следования от базы до места работ и обратно руб.;
И - стоимость быстроизнашиваемых деталей за машино- смену отдельных
путевых машин механизмов и оборудования руб.;
Зр - заработная плата обслуживающего производственного персонала
путевых машин кранов и оборудования за смену руб.;
Зд - заработная плата персонала сопровождающего самоходные машины от базы до места работ я обратно руб.;
Ф - средства необходимые на создание ремонтного фонда обеспечивающего все виды текущего ремонта и обслуживание путевых машин механизмов и оборудования в межремонтном цикле за смену руб.;
Постоянные расходы на полное восстановление первоначальной стоимости путевых машин механизмов и оборудования за машино- смену следует определять по формуле:
где: С - балансовая стоимость путевой машины механизмов и оборудования руб.;
А - норма амортизационных отчислений на полное восстановление %;
Н - число смен работы за год путевой машины механизма и оборудования.
Расходы на работу путевых машин механизмов и оборудования.
1 Стоимость горючего моторного масла и смазки израсходованных при работе на перегоне в течение необходимого времени в пределах машино-смены путевых машин с автономным двигателем следует определять по формуле
Гр=Wp*tp*Cг +mp*tp*Cm + (h1*tp*C1 + + hn*tp*Cn (руб.)
где; Wp - расход горючего в час при использовании номиналь ной мощности двигателя кгч;
tp - необходимое время для выполнения данной работы на перегоне^ ч;
Сг- стоимость одного килограмма моторного масла руб.;
mp - расход моторного масла в час кг ч;
Сm - стоимость одного килограмма моторного масла руб.;
H1..n - расход каждого вида смазки в час кг ч ;
С1-п - стоимость одного килограмма каждого вида смазки руб.
2. Стоимость электрической энергии израсходованной при работе на базе путевой машиной станции в течение необходимого времени в пределах мапшно-смены кранами и оборудованием следует определять по формуле:
Эр=Ээ*tp*Сэ + (h1*tp*C1 + .+hn*tp*Cn) (руб.);
где: Ээ - расход электроэнергии (потребляемой от внешних источников электроснабжения) в час кВт ч;
tр - необходимое время для выполнения данной работы на базе ч.;
Сэ - стоимость одного кВт электроэнергии руб.;
h1-n - расход каждого вида смазки в час кгч;
С1-n - стоимость одного килограмма каждого вида смазки руб.
3. Стоимость электрической энергии израсходованной при работе на перегоне оборудованием и механизмами не учитывается так как они потребляют энергию собственных передвижных электростанций. Стоимость горючего масла и смазки передвижных электростанций следует определять по п.2.1.
Стоимость смазки израсходованной при работе на перегоне оборудованием
механизмами следует определять также по п.2.1.
Стоимость горючего и моторного масла израсходованных самоходными
путевыми машинами по пути следования от базы до места работ и обратно.
следует определять по формуле:
Гд=Кдм*Wр*tд*Сг+mp*tд*Сm (руб.);
где: Кдм - коэффициент использования двигателя по номинальной
мощности при движении самоходных путевых машин от базы
до места работ и обратно. Коэффициент Кдм принимается рав
tд - время движения самоходных путевых машин от базы до места
работ и обратно. tд принимается равным 2 часам;
Wр Сг mp Сm - обозначены в п.2.1.
Стоимость быстроизнашиваемых деталей и материалов за время
выполнения работы в машнно-смену отдельных путевых машин механизмов и оборудования следует определять по формуле:
где: Сд - стоимость быстроизнашиваемых деталей или материалов руб.;
h количество быстроизнашиваемых деталей;
Т - число лет за которое быстроизнашиваемые детали или материалы приходят в негодность;
Н - число смен работы за год путевой машины механизма и оборудования
Расходы на заработную плату.
1 Расходы по .заработной плате обслуживающего персонала путевых машин кранов и оборудования за смену определяются по нормативам и квалификации членов персонала и действующим тарифным ставкам.
2 Расходы по заработной плате персонала сопровождающего самоходные путевые машины от базы до места работ и обратно относящиеся на смену определяются из расчета:
- Заработная плата сопровождения оплачивается одному члену по средней тарифной ставке всего персонала путевой машины;
- Время сопровождения путевой машины установлено в размере 16 часов на каждую смену ее работы на перегоне с учетом простоев станциях в ожидании возможности проезда к месту работ и предоставления «окна».
3 При определении стоимости машино-смен электрофицированных или гидравлических механизмов (инструментов) расходы на заработную плату обслуживающего персонала не учитываются.
Средства необходимые на создание ремонтного фонда обеспечивающего все вида текущего ремонта и обслуживание путевых машин механизмов и оборудования определяются на основании фактических расходов относимых на число рабочих машино-смен вырабатываемых путевой машиной механизмом или оборудованием в межремонтном цикле. Средства следует определять по формуле:
Ф = ————————- (руб.)
где: Ф1-n - расходы на все виды текущих ремонтов и обслуживание в межремонтном цикле в соответствии с ППР руб.;
Тф - число лет в межремонтом цикле;
H- число смен работы за год путевой машины механизма и оборудования
При расчете стоимости машино- смен путевых машин механизмов и оборудования следует руководствоваться следующими рекомендациями:
Балансовая стоимость путевых машин механизмов и оборудования стоимость горюче- смазочных материалов и электроэнергии быстроизнашиваемых деталей и материалов тарифные ставки обслуживающего производственного персонала принимаются по факту на момент производства расчета стоимости машино- смен.
Нормы амортизационных отчислений на полное восстановление путевых машин механизмов и оборудования могут быть приняты по «Указателю инвентарных объектов основных фондов железнодорожного транспорта» утвержденному МПС Российской Федерации в 1993 г.
Расходы топлива и моторного масла при работе двигателей путовых машин следует определять по их техническим паспортам где приведены расходы та 1 кВт (1 л. с.) номинальной мощности в час при нормативной загрузке.
Виды и расходы смазок при работе путевых машин механизмов и оборудования следует определять по их техническим паспортам.
В стоимость машино- смен путевых машин передвижение которых
осуществляется локомотивом дополнительно включается арецдная плата за использование локомотива. .
В стоимость машино- смен путевых машин и оборудования следует включать основную заработную плату обслуживающего персонала с повышающим коэффициентом на вредность работы.
Продолжительность машино-смен при расчете их стоимости должна быть принята равной 8 час.
Экономическая эффективность модернизации электропогрузчика ЭП-1013.
Характеристика конструкции разрабатываемого погрузчика
Настоящий раздел представляет собой расчет экономической эффективности применения разрабатываемого в данном дипломном проекте электропогрузчика грузоподъемностью 1 т. Указанный электропогрузчик представляет собой модернизированную модель электропогрузчика ЭП-1013 выпускаемого Машиностроительным заводом им. Калинина.
Модернизация электропогрузчика ЭП-1013 продиктована необходимостью повышения его производительности при работе на погрузке - разгрузке крытых железнодорожных вагонов чего можно достичь путем уменьшения времени его рабочего цикла и заключается в следующем
Указанные усовершенствования привели к увеличению средней затраты электроэнергии за один рабочий цикл. Замена аккумуляторной батареи позволила увеличить продолжительность работы электропогрузчика в течение рабочей смены
Электропогрузчик грузоподъемностью 1т разрабатываемый в настоящем дипломном проекте предназначен для погрузочно-разгрузочных работ внутри крытых железнодорожных вагонов штабелирования и транспортирования грузов в крытых помещениях и на открытых площадках с твердым и ровным покрытием при температуре окружающей среды от +40° до -40° С и высоте над уровнем моря не более 1200 м.
Основным рабочим органом разрабатываемого электропогрузчика является вилочный. Конструкция электропогрузчика обеспечивает возможность монтажа дополнительных сменных грузозахватных приспособлений.
Учет фактора времени в расчетах осуществлялся с помощью дисконтирования т.е. приведения будущих результатов применения погрузчика в стоимостном выражении к нулевому году.
Сравнительная технико-экономическая характеристика электропогрузчиков.
Определение количества погрузчиков ЭП-1013 для выполнения заданного годового объема работ в железнодорожном складе. Исходные данные:
Рабочее плечо S = 50 м;
Высота подъема груза Н= 28 м;
Максимальная скорость передвижения
без груза V"= 10 кмч
Скорость подъема вил
с грузом V п.в = 9 ммин
без груза V" п.в = 12 ммин;
Скорость опускания вил
с грузом V о.в = 24 ммин
без груза V" о.в. == 16 ммин
Рабочий цикл рассчитывается по формуле:
Тц.расч. = Т1 + Т2 + + Т11 = 1239 с
где: Т1 - время наклона грузоподъемника вперед заводки вил под груз наклона назад подъема груза на вилах до 300 мм Т1=15(с);
Т2 - время разворота электропогрузчика на 180° Т2=15(с);
ТЗ - время передвижения с грузом
Т3=S*3600V*1000=50*36009*1000 =20 с
Т4 - время подъезда к штабелю Т4=29(с);
Т5 - время поднятия вил
Т5=Н*60(Vn.B.+V"n.B.)2=28*60(9+12)2=138 с.
Т6 - время укладки груза Тб = 8 (с);
Т7 - время наклона грузоподъемника назад без груза Т7=17(с);
Т8 - время опускания вил
Т8=Н*60(vo.b.+v'o.b.)2=28*60(24+16 )2= 75 с
Т9 - время разворота без груза Т9=15(с);
Т 10 - время передвижения без груза
Т10=S*3600 V"*1000=50*360010*1000=18 с
T11- дополнительное время на переключение рычагов
Расчетный цикл с учетом увеличения чистого цикла на 25% для соблюдения режима работы электродвигателей:
Техническая производительность погрузчика рассчитывается
Пт == 3600Тц* Gm = 36001549== 2324 тчас
где: gm - грузоподъемность машины G'м = 1 (т).
Эксплуатационную производительность погрузчиков рассчитываем по формуле :
Пэ = Пт * Кв * Кг = 2324 * 075 * 08 = 1487 тчас
где: Кв=075 - коэффициент использования машины по времени
Кг=QпGм=081=08 - коэффициент использования машины по грузоподъемности:
где: Qn - масса груза перемещаемого за цикл т.е. в данном случае масса пакета.
Сменную производительность погрузчика рассчитываем
Псм = Пэ * Тем = 1487 * 8 = 11899 тсм
где: Тем=8 час - продолжительность смены.
Объем механизированной переработки груза на складе рассчитываем
Количество погрузчиков рассчитываем по формуле:
Мм = Qмех*365Псм*т*(365-Тр)=1860*365118.99*2*(365-278)=94610
где: Тр=27.8 дней - время нахождения погрузчиков в ремонте в течение года.
Расчет списочного числа рабочих для обслуживания погрузчиков ЭП-1013.
Списочное число механизаторов для обслуживания машин и оборудования определяют учитывая следующие потребности:
водитель на каждый погрузчик;
ремонтник на каждый погрузчик;
аккумуляторщик на 5 погрузчиков.
Списочное число рабочих рассчитываем по формуле:
R=α*Qv*365*mПсм*Траб= 112*1680*365*211899*305=378=38 чел
где: a - коэффициент подмены α = 112;
m - количество рабочих смен m = 2.
Расчет энергоемкости батареи разрабатываемого погрузчика и времени его работы без перезарядки батареи.
Средняя затрата электроэнергии от батареи на один цикл погрузчика:
Wц=(Qr*hr1+(Qn+Qr)**l”2+Qп**1”2=8*1305 + (21+8)*02*25075 + 2517*02*25075= 01 кВтч
где: Qr=8 кН - средний вес груза перемещаемого за один цикл
hr=13- средняя высота подъема груза высота пакета
=05 - общий коэффициент полезного действия системы грузоподъемника включая электродвигатель
=075 - то же механизма передвижения включая электродвигатель
=02 коэффициент сопротивления передвижению по горизонтальной поверхности с асфальтобетонным покрытием
и 1" - среднее передвижение электропогрузчика за один цикл соответственно с грузом и порожняком 1=
Количество циклов разрабатываемого погрузчика в смену при заданном режиме работы (Тем == 8 час)
Nц=Тсм*Кв*3600 Тц= 8*075*360012164= 1775 циклов
Энергоемкость батареи:
W6 == Wu * Nn = 01 * 1775 = 1775кВтч=18 кВтч.
Время работы погрузчика без перезарядки батареи:
Тр=Tц*W63600*Wц=12164*183600*01=6 час
По величине энергоемкости выберем аккумуляторную батарею 36 ТЖН-4ОО емкость А=400Ач напряжение U= 45 В.
Учитывая использование погрузчика по времени ( Кв = 075) энергоемкости выбранной батареи хватит для работы в течение смены.
Для зарядки выбранной батареи необходимо автоматическое зарядное устройство для тяговых аккумуляторных батарей УЗА-150-80 ( мощность Nз=12).
Технике - экономические показатели разрабатываемого погрузчика и погрузчика ЭП -1013 приведены в таблице 1.
Таблица 1 Сравнительная технико-экономическая характеристика погрузчиков.
БАЗОВЫЙ ВАРИАНТ ЭП-1013
РАЗРАБАТЫВАЕМЫЙ ВАРИАНТ
Высота подъема груза М
Максимальная скорость передвижения кмч с грузом без груза
Скорость подъема вил ммин с грузом без груза
Скорость опускания вил ммин с грузом без груза
Энергия аккумуляторной батареи кВт*ч
Время работы погрузчика без перезарядки батареи час
Нормативный срок службы лет
Продолжительность рабочего цикла сек
Эксплуатационная производительность тчас
Мощность потребляемая зарядным устройством. кВт
Продолжительность нормального заряда батарей час
Обслуживающий персонал чел
Цена батареи. руб. за банку
Цена зарядного устройства руб
Количество погрузчиков для выполнения заданного объема работ шт
Основные вложения на организацию механизированной погрузки-разгрузки грузов на складе представляют собой расходы на приобретение:
комплекта сменных тяговых батарей;
зарядного устройства для тяговых батарей.
Обозначения со знаком (") относятся к разрабатываемому погрузчику. Денежные потоки со знаком (-) представляют собой оттоки денежных средств.
Ип = (Nп*Цп- ( Nn" *Цп" )=(10* 172608)-(8*203000)=102080 руб.
где:Цп" = Цп * ( 1+ (Qkc Qn)) + ΔЦб * 36 = 148800 * (1-(2002250)) - 284 * 36 = 172250 руб.
где: Qkc=200 кГ - масса каретки смещения
ΔЦб=284 руб - разница цены батареи разрабатываемого погрузчика и цены батареи установленной на базовом погрузчике
- количество банок в батарее установленной на разрабатываемом погрузчике.
Сменные аккумуляторные батареи:
Иб =Nn * Цб * 34 - Nn" * Цб" * 36 =10 * 816 * 34 - 8 * 1100 * 36 = -39360 руб.
3.3 Зарядное устройство:
Изу = Цзу - Цзу" = 10600 - 9500 = - 1100 ( руб.).
Общий объем инвестиций:
Поскольку для выполнения заданного объема погрузочно-разгрузочных работ требуется меньшее количество разрабатываемых погрузчиков (по сравнению с базовым вариантом) то величина И войдет в расчет чистых денежных потоков со знаком плюс т.е. имеет место приток денежных средств. Эти инвестиции осуществляются в нулевой год.
И=Ип + Иб + Изу=10080-39360-1100=61620 руб.
Расходы на заработную плату:
= Згод - R - Згод" * R" = 1966272*30-1966272*34 =78655088 руб. где: Згод - годовой размер заработной платы
Згод = Змее * 12 = 163856 * 12 = 1966272 руб.
Змее - месячный размер заработной платы
Змее = Зтариф "+ Д + Здоп = 11704+351.12-11704=163856 руб.
где: Зтарпф – тарифная ставка обслуживающего персонала
Зтарнф = 616 * 19 = 11704 руб.
Д - размер доплаты ( 30% размера тарифа)
Д=11704*0.3=35112 (руб.);
Здоп - размер дополнительной заработной платы (10% размера тарифа) Здоп=11704*O.1 =11704 руб.
Таким образом общее снижение расходов на заработную плату составит 78655088 руб.
Расходы на электроэнергию:
Э = (Тзар * Nзу * пб * Nп) * Драб.п * Цэл - (Тзар" * Nзу" * пб" * Nn") * Драб.п*Цэл =(7*52*8*10)*278*05-(7*12*8 *2)*278*05 = -163464 руб.
где: по - количество заряжаемых в день аккумуляторных батарей
Цэл=05 руб- цена 1 кВт-час электроэнергии
Драб.п - число дней работы погрузчика в году с учетом простоев связанных с ремонтом
Драб.п = Драб. - Др = 305-278 = 278 дней.
Затраты на ремонт погрузчиков.
Затраты на ремонт погрузчиков рассчитываются укрупненно и составляют 12 % от стоимости погрузчиков.
Р = Ип * 012 =102080 * 012 = 122496 руб.
Затраты на вспомогательные материалы.
Затраты на вспомогательные материалы определяются в размере 15% от стоимости электроэнергии.
Мвсп=Э*015=-163464* 015 =-245196 руб.
Амортизационные отчисления:
А= An + Азу +А6 = - 170474 - 9540 - 8064 =-273938 руб.
где: An - амортизационные отчисления по погрузчикам
Ал = Ип * Nal = 102080*0167= -170474 руб.
где: Nal =167% -норма амортизации по погрузчикам
Азу - амортизационные отчисления по зарядным устройствам
Азу = Изу * Na2 = 10600* 09 = -9540 руб.
где: Na2 = 90 %- норма амортизации по зарядным устройствам
Аб - амортизационные отчисления по батареям
Аб = Иб * Na3 - 4032 * 02 = -8064 руб.
где: Na3 = 20 %- норма амортизации по батареям.
Корректировка денежных потоков проводится по амортизации и остаточной стоимости оборудования.
Остаточная стоимость оборудования:
Со = Con + Соб = 203000 + 1760 = 204760 руб.
где: Con - остаточная стоимость погрузчиков
Con =Цn"*Nn* No = 203000*2*01=162400 руб.
где: No == 10 %. - норма остаточной стоимости.
Соб - остаточная стоимость батарей
Соб = Цб" * (2*Nn) * No =1100* 2*8* 01 =1760 (руб.)
Расчет чистых денежных потоков.
Расчет чистых денежных потоков приведен в таблице 2. Чистые денежные потоки представляют собой разность результатов достигнутых в i-том году и затрат осуществленных в том же году. В качестве результатов выступает годовая величина чистой прибыли а в последнем году - также чистая выручка от ликвидации оборудования..
Таблица 2. Расчет чистых денежных потоков (тыс. руб).
Приращение доходов и расходов:
-Вспомогательные материалы
-остаточная стоимость
Оценка эффективности инвестиций.
Определение чистой текущей стоимости.
Показателем эффективности инвестиций является чистый дисконтированный доход (ЧДД) представляющая собой сумму дисконтированных чистых денежных потоков от инвестиций за весь расчетный период.
Если значение ЧДД положительно то инвестиционный проект является эффективным и может рассматриваться вопрос о его осуществлении. Чем большеЧДД тем эффективней проект.
ЧДД=ЧДПО(1+i)0+ЧДП1(1+i)1+ ЧДПn(1+i)n=61.62+5643(1+0.0516) +5643(1+0.0516)2 +5643(1+0.0516)3 +5643(1+0.0516)4 +5643(1+0.0516)5 +5643(1+0.0516)6 +5643(1+0.0516)7 +5643(1+0.0516)8 +5643(1+0.0516)9 +5643(1+0.0516)10 +5643(1+0.0516)11+7439(1+0.0516)12= 541 тыс.руб.
Положительное значение чистой текущей стоимости (ЧДД) говорит об эффективности рассматриваемого варианта применения разрабатываемого погрузчика (при работе в две смены по 8 часов с одним выходным в неделю).
Расчет экономической эффективности щебнеочистительной машины ЩОМ-850ПУ по сравнению с машиной RM-80UHR.
Характеристика машины ЩОМ-850ПУ
Щебнеочистительная машина ЩОМ-850ПУ предназначена для очистки от засорителей щебеночного балласта на перегонах и станционных путях с отбором засорителей в сторону от пути или в специальный состав и укладкой очищенного балласта под путевую решетку послойно с уплотнением нижнего слоя. Машина ЩОМ-850ПУ состоит из двух модулей - щебнеочистительного и энергетического.
Преимущества машины ЩОМ-850ПУ по сравнению с ее аналогами:
Уплотнение поверхности среза перед укладкой геотекстиля
послойное распределение очищенного щебня с разравниванием и уплотнением его нижнего слоя
регулирование качества очистки щебня путем изменения угла наклона грохота
подбивка возвращаемого в путь верхнего слоя очищенного щебня.
Определение цены машины ЩОМ-850ПУ.
Аналогом для расчета цены машины ЩОМ-850ПУ принята машина RM-80UHR российского производства:
Ц = 70000 * (120 + 89) 91 * 033 = 53000 тыс.руб
где 70000 - цена машины RM-80UHR совместного производства (25-29 млн) тыс.руб.
0+89 - масса щебнеочистительного и энергетического модулей машины ЩОМ-850ПУ т
- масса машины RM-80UHR т
3 - коэффициент сложности изготовления машины ЩОМ-850ПУ по сравнению с машиной RM-80UHR.
Цена щебнеочистительного модуля:
Цш = 53000 * 120(120+89) = 30430 тыс.руб.
Цена энергетического модуля::
Цэ = 53000 * 89(120+89) = 22570 тыс.руб.
Таблица 1. Исходные данные
А. Техническая характеристика.
Эксплуатационная производительность
Глубина вырезки балласта ниже подошвы шпал
Ширина вырезаемого балласта
Диапазон рабочей скорости машины
Установленная мощность
Максимальный подъем путевой решетки
Минимальный радиус кривых
Врем перевода машины в рабочее положение из транспортного и обратно
Средство транспортирования машины
Численность обслуживающего персонала
Качество очистки щебня
Технологические возможности:
- послойное распределение чистого щебня
- очистка стрелочных переводов
- очистка ж.д. путей у высоких платформ
- очистка горловин станций
- укладка гидроизоляционных материалов
- создание основой площадки земляного полотна с поперечным уклоном
- удаление щебня загрязненного из шпального ящика
- погрузка засорителей в спец состав
- отбор очищенного щебня в спец состав
- вырезка загрязненного балласта и погрузка в спец состав
- исключение просыпания загрязненного балласта за выгребное устройство
- распределение балласта внутри и снаружи ж.д. колеи за счет поворота разгрузочных конвейеров
- возможность восстановления балластной призмы
- понижение(подъем) ж.д. пути
- устройство обеспечивающее горизонтальное положение выгребной цепи при работе на кривых участках пути
- контроль за наклоном выгребной цепи
Б. Технико-экономические показатели расчета экономической эффективности.
Толщина слоя очищаемого щебня ниже подошвы шпал
Ширина вырезаемого слоя балласта
Объем щебня на 1 км пути
Средняя степень засоренности щебня
Количество рабочих смен в году
Техническая норма времени на очистку 1 км пути
Скорость рабочая при очистке щебня расчетная
Средняя продолжительность работы в «окне»
Фронт работы в «окне»
Объем ожидаемого щебня в «окно»
Протяженность очищенного за год путей (с учетом времени простоев-40%)
Стоимость выгребной цепи
Стойкость выгребной цепи
Стоимость быстро изнашиваемых изделий
Стойкость быстро изнашиваемых изделий
Зарплата обслуживающего персонала
Коэффициент начисления на зарплату с учетом доплат за подвижной характер работы
Расход эксплуатационных материалов
Стоимость 1 кг эксплуатационных материалов
Цена одного м3 щебня
Отчисление в % на полное восстановление
Отчисление в % на капитальный ремонт машины
Отчисление в % на текущей ремонт машины
1 Определение ставки дисконтирования
Е =015*019175+085*0169 =0262
СД -стоимость долга%;
ДСК -доля собственного капитала;
ССК -стоимость собственного капитала%;
Процент выплат по долгам с учетом экономии:
СД=(1-035)*0295 = 019175
где: СН =035 ставка налога на прибыль;
Nр(СД) -уровень реальной процентной ставки
Nе(СДССК) = (1 + N(кбдб) р L p -1
Nе(СДССК) -номинальная эффективная ставка
N(кбдб) - номинальная банковская ставка
p =3 число периодов начисления процентов внутри года.
Nе(ССК) = (1+ 0163) L 3 -1 = 0169
Nе(СД) = (1+ 0273) L 3 -1 = 0295
Nр(СД) = Nе(СД) =0295
Годовые объемы работ по глубокой очистке щебня:
а) ЩОМ-850ПУ : В1 = 0.60*2795*128*5.253.29 =342720 м3
б) RM-80UHR : В2 = 0.60*2795*128*5.254.30 = 262080 м3
2.2 Соотношение годовых объемов работ по глубокой очистке щебня :
Амортизационные отчисления :
для ЩОМ-850ПУ : И1вос = Кц *Кот = 53000*0.056 = 2968 тыс.руб
для RM-80UHR : И2вос = Кц *Кот = 1.308*70000*0.056 = 5126154 тыс.руб
Ивос = И2вос -И1вос = 5126 -2968=2158154тыс.руб
Кц - Оптовая цена машины
Кот -Отчисление в % на полное
Издержки годовые на зплату (с начислениями ) :
для ЩОМ-850ПУ : И1зар = К1 *К2 *К3 *Кн *Кг *Кр = =0.0713*128*2.92*5*1.14*1.054 = 160 тыс.руб
для RM-80UHR : И2зар = К1 *К2 *К3 *Кн *Кг *Кр = =1.308*0.0713*2.92*3*1.14*1.054 = 125.538 тыс.руб
Изар = И2зар - И1зар = 125.538 -160 = -34.462тыс.руб
К1 -зарплата обслуживающего персонала
К2 -Количество рабочих смен в году
К3 -коэффициент начисления на зарплату с учетом доплат за подвижный характер работы
Годовые издержки от стоимости ГСМ
для ЩОМ-850ПУ : И1гсм=0.60*(К4 +К5)*К6*К2*(К7 *К9 +К8 *К10) = =0.60(5.25+1.6)*830*128*1*(0.240*0.0040+0.00127*0.0060) =422.508 тыс.руб
И2гсм =0.60*Ипр(К4 +К5)*К6*К2*(К7 *К9 +К8 *К10) = =0.60*1.308*(5.25+1.6)*666*128*(0.240*0.0040+0.00127*0.0060) = =443.339тыс.руб
Игсм = И2гсм -И1гсм= 443.339 -422.508 =443.339 тыс.руб
К4 -Средняя продолжительность работы в «окне»;
К5 -Фронт работы в «окне»;
К6 -Установленная мощность;
К7 -Расход дизтоплива;
К9 - Стоимость 1кг дизтоплива;
К10- Стоимость 1кг масла;
Годовые издержки потребителя на ремонты (капитальный и текущий)
для ЩОМ-850ПУ : И1рем= Кц *(К11 +К12)= 53000*(0.052+0.020)= 3816 тыс.руб
для RM-80UHR : И2рем = Ипр *Кц *(К11 +К12)= 1.308*70000*(0.052+0.020) = 6590.769 тыс.руб
Ирем = И2рем - И1рем= 6590.769 - 3816 =2774.769 тыс.руб
К11 -Отчисление в % на капитальный ремонт машины;
К12 - Отчисление в % на капитальный ремонт машины;
Годовые издержки от стоимости быстроизнашивающихся изделий
для ЩОМ-850ПУ : И1изн= (215.81030+25.0005.0)*122.6 = 1495.175 тыс.руб
для RM-80UHR : И2изн = 1.308*(215.81030+25.0005.0)*93.8 = 1495.175 тыс.руб
Годовые издержки потребителя от налога на имущество :
для ЩОМ-850ПУ : И1нал= Кц*Н= 53000*0.020 = 1060 тыс.руб
для RM-80UHR : И2нал = Ипр* Кц*Н= 1.308*70000*0.20 = 1830.769 тыс.руб
Инал = И2нал -И1нал= 1830.769 -1060=770.769тыс.руб
Издержки от внесения дополнительного количества нового щебня равнозначны т.к. показатели качества очистки у щебнеочистительных машин равны.
Годовые эксплуатационные издержки потребителя
для ЩОМ-850ПУ : И1общ=И1вос +И1зар +И1гсм +И1рем +И1изн +И1нал = =2968+160+422.508+3816+1495.175+1060=9921.682тыс.руб
И2общ = И2вос +И2зар +И2гсм +И2рем +И2изн +И2нал = =5126.154+125.538+443.339+6590.769+1495.175+1830.769=
Годовые эксплуатационные издержки без учета зплаты:
для ЩОМ-850ПУ : И1экс= И1общ -И1зар= 9921.682 - 160 = 9761.682 тыс.руб
для RM-80UHR : И2экс = И2общ -И2зар= 15611.745- 125.538 = 15486.206 тыс.руб
Иэкс = И2экс -И1экс=15486.206 -9761.682 = 5724.527тыс.руб
Стоимость работы 1 машино-смены:
для ЩОМ-850ПУ : С1м-с = И1общ К2 =9921.682128 = 77513 тыс.руб
для RM-80UHR : С2м-с = И2общ К2 =15611.7451.308128 = 93.269 тыс.руб
Экономические показатели сведены в таблицу 2
стоимость оборудования
Приращение доходов и расходов.
Зплата (с начислениями)
Ремонт (капитальный и текущий)
Корректировка денежных потоков
Чистые денежные потоки
ЧДД = –––––– + –––––– + –––––– + ––––– + –––––– + –––––– + ––––––
+ –––––– + –––––– + –––––– + ––––– + –––––– +–––––––– = 26млн.р
Выполняя возврат очищенного щебня с послойным уплотнением нижнего слоя машина ЩОМ-850ПУ дает новое качество ремонта железнодорожного пути позволяя с одной стороны уменьшить объем удаляемого с загрязнителями щебня а с другой увеличить межремонтный период эксплуатации пути т.к. послойное уплотнение обеспечивает уменьшение его расстройства.
Кроме того в результате более высокой производительности и меньшей первоначальной стоимости ЧДД от снижения издержек у потребителя при использовании машины ЩОМ-850ПУ по сравнению с машиной RM-80UHR составит 267млн.руб.
Преображенская клад с краном штабелером.doc
1. Описание сравниваемых результатов.
Выгрузка пачек плит вспененных полистирольных из полувагона осуществляется в ручную. Четыре человека находится в самом полувагоне и подают от туда пачки а 6-еть человека поочередно подвое принимают и складируют пачки. Комплекс обслуживают 10-еть человек.
Выгрузка пачек плит вспененных полистирольных из полувагона осуществляется полукозловым краном электрическим управляемым с пола с вакуумным захватом. Процесс выгрузки пачек осуществляет оператор находясь на возвышенной эстакаде а контролирует процесс - стропальщик. Комплекс обслуживают 2 человека.
2 Определение барьерной ставки.
Капитал предприятия формируется из двух источников: собственного и заемного. Для привлечения капитала из этих источников предприятию необходимо платить. Это либо процент по кредитам (заемный капитал) либо дивиденды (акционерный капитал). Чем более рискованный проект тем более высоких дивидендов будут ожидать акционеры а кредиторы будут предлагать кредиты под более высокий процент. И акции предприятий и кредиты реализуются на финансовых рынках. И именно силы свободного рынка определяют степень риска инвестиций.
Поэтому можно сказать что стоимость капитала предприятия представляет собой рыночную оценку уровня риска по операциям предприятия. Предприятия принимают эту оценку в качестве среднего значения барьерного коэффициента HR так как у них нет более объективного показателя.
В общем случае стоимость капитала – это средневзвешенная цена (в процентах) которую предприятие уплатило за денежные средства используемые для формирования капитала. Эта величина определяется соотношением заемного и собственного капиталов:
где : CK – стоимость капитала %;
CD – стоимость долга %
DCK – доля собственного капитала;
CCK – стоимость собственного капитала %
Так как выплаты процентов уменьшают величину налогооблагаемой прибыли то соответственно уменьшается и величина налоговых выплат. Экономия на налогах частично компенсирует выплаты по долгам. Поэтому реальный процент выплат по долгам с учетом экономии составит:
где CH=0.2 – ставка налога на прибыль;
Стоимость собственного капитала при отсутствии развитого фондового рынка в России для государственных предприятий можно взять на уровне альтернативного размещения средств (депозитные банковские ставки проценты по государственным облигациям и т.д.).
В условиях высокой инфляции ставки ссудного процента и депозитные ставки рассчитываются с учетом внутригодовых реинвестиций и очищаются от инфляции по следующей методике.
Берутся номинальные (т.е. с учетом инфляции) годовые ставки коммерческих банков. На их основе рассчитываются эффективные ставки (т.е. с учетом реинвестиций по периодам внутри года):
Ne(CDCCK) – номинальная эффективная ставка (кредитная и депозитная соответственно)
N(кбдб) – номинальная банковская ставка (кредитная и депозитная соответственно); Nкб=0.21 Nдб=0.11;
p=2 – число периодов начисления процентов внутри года.
Рассчитанная барьерная ставка является для предприятия средним значением
3 Экономическая эффективность инвестиций.
Основной целью внедрения полукозлового крана с вакуумным захватом в складское помещение было увеличение производительности склада за счет снижения доли ручного труда и повышение скорости выгрузки одной единицы груза.
Увеличение экономической эффективности складского помещения после внедрения туда полукозлового крана с вакуумным захватом будет наиболее заметно после сравнения производительности операции по выгрузке груза на складе до и после инновации.
Производительность операции по выгрузке груза в ручную определим по формуле:
где Gгр = 40 – вес пакета Gгр = 40 кг
С – число циклов которое машина делает за 1 час
где γ – коэфициэнт совмещения операций γ = 1
Тц – время цикла сек
где: - время затрачиваемое на снятие груза с полувагона с
-время затрачиваемое машиной на продольные и поперечные передвижения по складу с грузом и без груза с
-время затрачиваемое на вспомогательные операции c
-время затрачиваемое на отдых рабочих с
Определим для полукозлового крана техническую производительность по формуле (8.4) число циклов по формуле (8.5):
где: -время затрачиваемое машиной на продольные и поперечные передвижения по складу с грузом и без груза с
- время затрачиваемое на подъем грузоподъемного захвата с грузом и без груза с
-время затрачиваемое на опускание грузоподъемного захвата с грузом и без груза с
-время затрачиваемое на повороты машины с
Определим -время затрачиваемое машиной на продольные и поперечные передвижения по складу с грузом и без груза. Т.к. скорости передвижения с грузом и без груза полукозлового крана одинаковы то
Определим - время затрачиваемое на подъем грузоподъемного захвата с грузом и без груза и -время затрачиваемое на опускание грузоподъемного захвата с грузом и без груза . Т.к. у полукозлового крана скорость подъема и скорость опускания грузоподъемного захвата одинаковы и равны не зависят от наличия груза или нет то
Определим эксплутационную производительность:
где - коэффициент использования крана по времени
4. Определение эксплуатационных расходов
В составе текущих издержек учитываются основная и дополнительная заработная плата рабочих занятых управлением краном техническим его обслуживанием и ремонтом затраты на материалы электроэнергию.
4.1. Определим расходы по заработной плате
Заработная плата работника
где т = 1 – количество смен;
Т – годовой фонд рабочего времени Т = 2750 ч;
кп – коэффициент учитывающий дополнительную заработную плату прими и доплаты кп = 25 – для монтеров пути кп = 2 – для крановщика и стропольщика;
rм – часовая тарифная ставка работника;
i – количество работников i – того разряда.
Разгрузка груза в ручную.
При разгрузки полувагонов в ручную необходимо четыре монтера пути четвертого разряда и шесть монтеров пути третьего разряда.
Заработная плата монтера пути четвертого разряда
где rр =428– часовая тарифная ставка монтера пути четвертого разряда.
Заработная плата монтера пути третьего разряда
где rр =354 – часовая тарифная ставка монтера пути третьего разряда.
Разгрузка груза полукозловым краном.
Для обслуживания нового крана необходим один крановщик четвертого разряда и один стропальщик третьего разряда:
Заработная плата машиниста
где rр =428– часовая тарифная ставка машиниста четвертого разряда.
где rр = 354 – часовая тарифная ставка стропольщика третьего разряда.
4.2. Определим расходы на электроэнергию
Разгрузка груза в ручную.
Т.к. при разгрузки полувагонов в ручную электроэнергия не потребляется то
где -цена одного кВт в час силовой электроэнергии =205 руб;
-суммарная установочная мощность электродвигателей всех механизмов;
-коэффициент по мощности =08;
-коэффициент учитывающий потери электроэнергии в сети =105;
-коэффициент полезного действия =085;
ПВ- средняя продолжительность включения двигателей отдельных механизмов процессе работы крана 25%.
4.3.Определим расходы на вспомогательные материалы
где квсп = 015 – коэффициент учитывающий стоимость вспомогательных материалов от стоимости электроэнергии.
4.4. Определим расходы на техническое обслуживание и ремонт кранов
где км – коэффициент учитывающий стоимость материалов на проведение технических обслуживаний и ремонтов доля единиц от стоимости крана
4.5. Определим расходы на социальные нужды
где ксн – коэффициент учитывающий социальные нужды в долях единиц от заработной платы ксн = 026.
Суммарные эксплуатационные расходы
5. Денежные потоки и инвестиции
Экономия на заработной плате при использовании нового крана составит
Экономия на электроэнергии
Экономия на вспомогательных материалах
Затраты на материалы на ремонт
Экономия на социальных нуждах
6. Определение капитальных вложений
Капитальные вложения определяются по формуле
где - цена базового оборудования руб;
- цена нового оборудования руб.
Но т.к. базовая технология по выгрузке груза не включает в себя никакого оборудования то капитальные вложения будут равны стоимости полукозлового крана.
где С - цена оборудования руб;
qa – норма амортизации qa = 005.
Затраты на амортизацию
Результаты расчета чистых денежных потоков капитальные вложения и амортизация записаны в табл. 8.1.
Приращение доходов и расходов.
Экономия на ремонт и тех. обслуживание
Экономия на социальные нужды
Экономия на вспомогательные материалы
Корректировка денежных потоков
Чистые денежные потоки
8. Расчет чистой текущей стоимости
Чистая текущая стоимость (NVR) представляет собой сумму дисконтированных чистых денежных потоков порожденных инвестициями и определяется следующим образом:
где ЧДП – чистый денежный поток руб;
HR – барьерная ставка;
n – число лет функционирования объекта.
Положительное значение чистой текущей стоимости (NPV) говорит об эффективности рассматриваемого варианта применения разрабатываемого склада.
По полученным значениям чистой текущей стоимости (NVP) построим график зависимости её от числа годов срока службы машины (рис. 8.1.).
Внедрение и использование склада с применением полукозлового крана при разгрузке плит вспененных полистирольных позволяет увеличивать производительность погрузочно-разгрузочных работ снизить количество занятых рабочих на данной операции что является основной экономической характеристикой склада и получить экономический эффект.
Рис. 8.1. График зависимости NVP от числа срока службы машины
Задание ПТМ техники на диплом.doc
робототехнические комплексы
Специальность "Подъемно-транспортные строительные
дорожные машины и оборудование
по дипломному проекту (работе) студента
(фамилия имя отчество)
Срок сдачи студентом законченного проекта (работы)
Исходные данные к проекту (работе)
Содержание расчетно-пояснительной записки
(перечень подлежащих разработке вопросов)
Согласно календарному плану
Перечень графического материала
(с точным указанием обязательных чертежей)
Количество чертежей указано в пунктах календарного плана
по каждому разделу проекта
Консультанты по проекту (работе)
с указанием относящихся к ним разделов проекта
Безопасность жизнедеятельности
выдачи задания07 января 2012 года
Задание принял к исполнению
дипломного проекта (работы)
Обзор существующих конструкций
и выбор рациональной схемы машины
Анализ различных вариантов конструктивного исполнения и проведение основных кинематических и прочностных расчетов 5 – 10 стр. 1 лист
Описание конструкции и предварительная разработка общего вида машины
Конструктивная разработка отдельных механизмов и узлов с проведением расчетов на прочность долговечность надежность
Технологическая часть
Технико-экономические расчеты
Обеспечение безопасности жизнедеятельности
Окончательное оформление чертежей
и расчетно-пояснительной записки
Список литературы с отечественными и
зарубежными источниками
Экскаватор_эконом.doc
ОТ ВНЕДРЕНИЯ НОВОГО РАБОЧЕГО ОБОРУДОВАНИЯ
К БАЗОВОМУ ЭКСКАВАТОРУ МТП-71
Цель расчета - экономическое обоснование внедрения нового рабочего оборудования к базовому экскаватору.
Экономическая эффективность может определяться показателями: увеличением производительности труда фондоотдачи удельной металлоемкости удельного расхода топлива и т.д..
Так как темой проекта является модернизация торфяного одноковшового универсального экскаватора с гидравлическим приводом на уширенно-удлиненном гусеничном ходу то базовой машиной будем считать экскаватор МТП-71.
Модернизация машины заключается в разработке нового рабочего оборудования - драглайна которое требуется для выполнения земляных работ.
Основной задачей раздела является определение полезного эффекта который определяется по формуле:
Эп = Цб*[(ккор*1(Тб + Еп)(1(Тн + Еп)))–1]+[Uб*ккор –Uн (1(Тн + Еп))]
где Цб - инвентарно-расчетная стоимость экскаватора МТП-71
по данным ВНИИДормаша составляет 61242000 руб.;
ккор - коэффициент корректировки производства;
Еп - нормативный коэффициент эффективности новой
Тб Тн - сроки службы базовой и новой техники;
Uб Uн - годовые текущие затраты на базовую и новую технику.
Как показали расчеты коэффициент использования машины до модернизации кВБ =031 после модернизации кВН =075.
Расчет ведем для выполнения земляных работ в слабонесущем грунте Ш категории ёмкость ковша q = 10 м3 время работы в течение смены Тсм = 8 ч. время работы в течение года Тгод =250 см.
Определение производительности машины
Пэсм = 60 * q * n * Тсм * кв
где n - количество циклов в минуту.
Пэсмб = 60 * 10 * 3 * 8 * 031=4464 м3
Пэсмн = 60 * 10 * 2 * 8 * 075 =720 м3
Пэб = 4464 * 250 = 111600 м3
Пэн = 720 * 250 = 180000 м3
Модернизация ведет к увеличению веса машины на 2500 кг (стрела 1000 кг ковш 1500 кг).
По данным ВНИИДормаша вес базового экскаватора МТП-71 составляет 18500 кг ± 2%
Определение капитальных затрат:
кн = кб + (кб *1078625)* 405 = 61242000+(61242000*1078625)*
*405 = 64320000 руб.
Расчет удельных капиталовложений
Кудб = 61242000111600 = 54876 руб м3
Кудн = 64320000180000 = 3573 руб м3
Текущие затраты определяются по формуле
U = Sзп + Sкр + Sэр + Sм + Sт + Sпб
где Sзп - заработная плата рабочих занятых управлением машины;
Sкр - затраты на капитальный ремонт;
Sэр - затраты на техническое обслуживание;
Sм - затраты на смазочные материалы;
Sт - затраты на топливо;
Sпб - затраты на перебазировку.
Текущие затраты по отдельным статьям определяются с учетом накладных расходов. Накладные расходы принимаются в размере 30% от суммы основной заработной платы экскаваторщика.
И 10% от суммы остальных статей затрат на эксплуатацию техники.
Заработная плата рабочих занятых управлением машиной определяются по формуле
Sзп = кнз * кр * l * ТГ * Gi
где кр - поправочный коэффициент к тарифной ставке
Б - количество рабочих занятых управлением техники;
Gi - часовая тарифная ставка i -ого разряда.
SзпБ = 13 1105 125 2000 1200=4309500 руб.
Примем что заработная плата рабочих занятых управлением машины после модернизации экскаватора не изменилась т.е.
Затраты на капитальный ремонт определяем по формуле
Sкр = кнп * Np * Зк 100
где Np - отчисления на реновацию (%)
Затраты на техническое обслуживание и текущий ремонт состоит из затрат на заработную плату ремонтных рабочих и затрат на материалы и запасные части.
Затраты на заработную плату рабочих определяется по формуле:
Sэрз = ТГ * кнз * lр * Ср * аi * ri ТЦ
где ТЦ - продолжительность межремонтного цикла техники
lр - коэффициент учитывающий премии ремонтных рабочих
Ср - средняя тарифная ставка рабочих по ремонту машин
m - количество видов ТО и ТР;
ri - трудоемкость i -х видов ТО и ТР (чел.час).
Затраты на материалы и запасные части определяются по формуле:
Sэрм = кнп * Sэрз * кэр кнз
где кэр - коэффициент перехода от заработной платы к затра-
там на материалы и запасные части кэр = 117.
SэрБ =241280+238867 = 480147 руб.
Затраты на топливо для техники определяются по формуле:
Sт = кнп * ЦТi * Wтi * Ттi
m - количество видов топлива.
Wтi = 103 * 10-3 * Nном * gсм * кN * кдв * кдм
где Nном - номинальная мощность двигателя;
gсм - удельный расход топлива;
кдв - коэффициент использования двигателя по времени;
кдм - коэффициент использования двигателя по мощности;
кN - коэффициент учитывающий изменение расхода топлива в
зависимости от степени использования двигателя по
WтiБ = 103 * 10 * 130 * 200 * 053 * 1015 = 14 кг
SтБ = 11 1000 14 200 =30800000 руб.
Затраты на смазочные материалы для техники
где e -коэффициент перехода от годовых затрат на топливо
к затратам на смазочные материалы e =022.
SсмБ = 022 * 30800000=6776000 руб.
Затраты на масло для гидросистемы определяется по формуле
Sмг = кнп * Vг * gм * Цм * кд * ТГ tмг
где Vг - емкость гидроситемы дм3;
gм - объемная масса масла для гидросистемы кг дм3
Цм - оптовая цена масла рубкг Цм =900 рубкг;
кд - коэффициенты добавок масла в гидроситему кд =15;
tмг - периодичность смены масла в гидросистеме.
SмгБ =11* 400 * 0885 * 900 * 15 *20002000 =525690 руб.
Затраты на перебазировку техники с объекта на объект
Экскаватор МТП-71 имеет гусеничный ход поэтому перебази-ровка осуществляется на трейлере. Затраты на перебазировку включают в себя затраты на заработную плату рабочих и затраты на эксплуатацию оборудования транспортных и монтажных средств.
Затраты на заработную плату рабочих занятых на перевозке техники на трейлере.
Sпзт = кнз * (Sз + (zT – zH) * Sдз)
Sпзт = 13(13200+(50-25)* 3000) = 269100 руб.
Эксплуатационные затраты
Sпэт = кнп * (Sз + (zT – zH) * Sдз)
Sпэт = 11(153000+(50-25)*4800) = 300300 руб.
SперБ = 269100+300300 = 569400 руб.
Затраты на перебазировку в течение года:
Sпб = 2000*56940020 = 56940000 руб.
Результаты сведем в таблицу.
Годовые текущие затраты
Статьи затрат Условные Един. Значения показателей
Зарплата рабочих Sзп т.руб. 43095 43095
ремонтный фонд Sкр т.руб. 5995592 990528
ремонт Sэр т.руб. 480147 480147
Затраты на топливо Sт т.руб. 30800 30800
ные материалы Sсм т.руб. 6776 6776
для гидросистем Sмг т.руб. 52569 52569
базировку Sпб т.руб. 56940 56940
текущих затрат U т.руб. 105826929 109736617
Определение годового экономического эффекта
Эп = 61242(16*1(6+015)(1(6+015)))+(105826929*16 -109736617(1(6+015))) = 2249129 тыс.руб.
Цд = Цб * 09 + Эп * 07
Цд = 61242 * 09+2249120 * 07=21255683 тыс.руб.
Себестоимость разработки 1 м3 грунта
Цена разработки 1 м3 грунта
Цр =62712(1+035)=846612 руб м3
Прибыль от внедрения новой машины
ПБ =(846612-62712) * 270000 =59262840 руб.
ПН =(846612-40643) * 270000 =118849140 руб.
DП =118849140 - 59262840 = 59586300 руб.
Результаты расчетов сведем в таблицу.
Показатели экономической эффективности
Наименование Усл. Един. Значение показателей БТ %
показателей обоз. изм. БТ НТ НТ
Капитальные затраты кз руб. 61242000 64320000 105
Годовые текущие затраты U руб. 105826929 109736617 104
Годовая эксплуатацион-
ная производительность Пэг руб. 111600 270000 242
Цена договорная Цд руб. 212556830
Цена оптовая Цо руб. 61242000
Полезный эффект Эп руб. 224912900
работки 1 м3 грунта Ср рубм3 62712 40643 65
м3 грунта Цр рубм3 846612 846612
Хозрасчетный эффект DП руб. 59586300
Определение барьерной ставки
HR = CK = ДД * СД + ДСК * ССК
где СК – стоимость капитала% ;
СД – стоимость долга % ;
ДСК – доля собственного капитала ;
CCК – стоимость собственного капитала % .
CД = (1 – СН ) * NPСД
где СН – ставка налога на прибыль;
NPСД – реальная ставка.
Рассчитаем эффективные ставки:
NeСД = (1 + (Nк.б p))p – 1
NeССК = (1 + (Nд.б p))p – 1
где Ne – номинальная эффективная ставка;
Nд.б – номинальная банковская ставка по депозитам;
p – число периодов начисления процентов внутри года.
Определяем реальную ставку
NрСД = ( NeСД – Nин )( 1+ Nин )
NрССК = ( NeССК – Nин )( 1+ Nин )
где Nин – годовой уровень инфляции.
Кран штабелер(Хараб ТДМ 512).doc
1. Технико-экономическое обоснование внедрение робокара грузоподъемностью 05 тонн для обслуживания склада тарно-штучных грузов.
Для обоснования экономической эффективности внедрения робокара на складе тарно- штучных грузов рассмотрим два варианта :
штабельное хранение груза
стелажное хранение груза
1.1. Штабельное хранение груза
Вариант штабельного хранения грузов предусматривает поперечное хранение грузов в крытом складе по высоте складирования в 3 рада и с учетом ширины проезда электропогрузчика . Все погрузочно-разгрузочные операции выполняются электропогрузчиком ЭП-103 грузоподъемностью 05 тонн . Расчет параметров склада и количества погрузочно-разгрузочных средств.
Количество пакетов по высоте :
Количество пакетов по ширине склада :
.z в = В - 4в пр. - 2 в без. l п = 30 - 12 – 2 08 = 20 (пакетов)
в пр. = 3 (м) - ширина проезда электропогрузчика ЭП-103
в без. = 1 (м) - дополнительная ширина склада для обеспечения противопожарной безопасности .
l п. = 08 (м) - длина пакета
В = 30 (м) - ширина склада
Количество пакетов в одном ряду:
Количество блок секций :
.z б.с = V z h * z l * z в
V =16028 (пакетов) - емкость склада
.z б.с = 16028 2 * 3 * 20 = 134 (шт.)
L скл. = z б.с ( z l * в п. + в пр. ) + 2 в без. + l доп.
В п = 12 (м) - ширина пакета
.l доп. = 10 (м) - дополнительная длина склада необходимая для размещения бытовых и технических помещений .
L скл. = 134 ( 2 * 12 + 3 ) + 2 + 10 = 736 (м)
Площадь зоны хранения :
F хр. = L * B = 30 * 736 = 22080 (м2)
Объем зоны хранения :
V хр. = F хр. * Н = 22080 * 5 = 110400 (м3)
Н = 5 (м) - высота склада
Площадь зоны погрузки - выгрузки :
F п-в = 05 * F хр. = 11040 (м2)
Объем зоны погрузки - выгрузки :
V п-в = F п-в * Н п-в = 11040 * 35 = 38640 (м3)
Н п-в = 35 (м) - высота зоны погрузки - выгрузки .
Необходимое количество электропогрузчиков :
.z эп. = Q г. * К н 365 * Т * q эп.
Q г. = 1000000 (тонн) - годовой грузопоток на складе
К н = 14 - коэффициент учитывающий дополнительные операции на складе
Т = 16 (ч) - время работы электропогрузчиков в сутки.
q эп. - часовая производительность электропогрузчика ЭП – 103
q эп. = 60 Т ц * φ * q эп. п
Т ц = 112 (мин.) - время цикла электропогрузчика ЭП-103
.φ = 16 24 = 067 - коэффициент учитывающий использование электропогрузчика по времени .
q эп. п. = 05 (тонн) - грузоподъемность электропогрузчика
q эп. = 60 * 05 112 * 067 = 3 995 (тоннчас)
z эп. = 1000000 * 14 365 * 16 * 3995 = 60 (шт.)
1.2. Стеллажное хранение груза
Стеллажное хранение грузов предусматривает хранение грузов в ячейках стеллажей обслуживаемых робокаром грузоподъемностью 05 тонн работающем в автоматическом режиме . Из вагона робокары с низкой загрузкой подают грузы в наземный склад на конвейер а в подземный склад в лифты . Далее в наземном складе робокары устанавливают груз в свободные ячейки а в подземном складе робокары устанавливают грузы в свободные ячейки после того как груз прибывает на лифте нижний этаж .
Переработка грузов с наземного склада в автомобиль происходит по следующем пути : робокар достает груз из нужной ячейки и перегружает его в автомобиль .
Из подземного склада - с точностью наоборот.
Организацию работ на складе тарно-штучных грузов со стеллажным хранением показана на чертеже за номером.
1. 2.1. Параметры склада и количество погрузочно-разгрузочных средств.
Расчеты параметров склада и количества погрузочно-разгрузочных средств приведены в дипломном проекте в разделе “ Организация работ на складе тарно-штучных грузов”
1.3. Параметры склада и количества технических средств по вариантам представлены в таблице 4.1.
Параметры склада и количество технических средств по вариантам.
Показатели и размерность
2. Экономические расчеты
Нацеленность предприятия в рыночных условиях на максимальную прибыль а также наличие конкуренции заставляет предприятие систематически обновлять основные фонды (капитал) то есть делать инвестиции . На рынке факторов производства капитал является ресурсом который имеет особенности .
Во первых он в отличие от других факторов является ресурсом длительного пользования и участвует в производстве на протяжении многих лет с момента приобретения . Поэтому здесь появляется фактор времени . Когда предприятие принимает решение о приобретении капитала (построить новый цех купить новое оборудование и т.д. ) оно должно сравнить капиталовложения которые ему предстоит сделать сегодня с прибылью которую принесет этот капитал в будущем . Потому предприятию необходимо ответить на вопрос : сколько будущие прибыли стоят сегодня ?
Во-вторых капитал как фактор производства т.е. как физический капитал имеет высокую стоимость . Поэтому предприятию прежде чем приобретать капитал-фактор надо приобрести необходимую сумму денег т.е. инвестиционный капитал требующийся для его покупки . Приобретение инвестиционного капитала осуществляется на финансовых рынках . При этом возможны два способа :
Прямое ивестиционирование путем реализации акций и за счет перераспределения прибыли .
Займы через финансовых посредников (банки инвестиционные фонды и т.д.)
Во втором случае предприятие берет взаймы в кредит за который следует платить . Величина платы определяются ссудным процентом который имеет различную величину для различных сделок и зависит в основном от степени риска конкретной сделки .
Таким образом предприятие решая приобрести капитал должно исходить из следующего :
Если используются заемные средства то прибыль получаемая за весь срок функционирования капитала должна быть не меньше суммы быть не меньше суммы займа с процентами за него (с учетом фактора времени ).
Если используются собственные средства то прибыль должна давать ежегодные проценты не меньше величины выплачиваемой по акциям . Учет фактора времени осуществляется с помощью так называемого дисконтирования т.е. приведения будущих результатов в стоимостном выражении к нулевому году .
Тогда текущая стоимость результата n – го года А составит РV : РV = A (1 + .i )n где
.i - ставка дисконтирования .
Так как ставка дисконтирования является для различных проектов и разных предприятий различной то ее величина для конкретного проекта называется барьерной ставкой НR.
2.1. Определение барьерной ставки.
НR = СК = ДД * СД + ДСК * ССК где
СК - стоимость капитала
СД - стоимость долга
ДСК - доля собственного капитала
ССК - стоимость собственного капитала
Так как выплаты процентов уменьшают величину налогооблагаемой прибыли то соответственно уменьшается и величина налоговых выплат . Экономия на налогах частично компенсирует выплаты по долгам . Поэтому реальный процент выплат по долгам с учетом экономии составит :
СД = ( 1 - СН ) * ПС где
СН = 035 - ставка налога на прибыль
ПС - уровень процентной ставки
Стоимость собственного капитала при отсутствии развитого фондового рынка России для Государственных предприятий можно взять на уровне размещения альтернативного размещения средств (депозитные ставки проценты по ГКО и т.д. )
В условиях высокой инфляции ставки ссудного процента и депозитные ставки рассчитываются с учетом внутригодовых реинвестиций и очищаются от инфляции по следующей методике .
Берутся номинальные (т.е. с учетом инфляции) годовые ставки коммерческих банков . На их основании рассчитываются эффективные ставки ( т.е. с учетом реинвестиций по периодам внутри года ) .
N с(ссн) = ( 1 + N ДБ р )р - 1
N с(дк) = ( 1 + N КБ р )р - 1 где
N ДБ N КБ - номинальные банковские ставки по депозитам и кредитам соответственно
р = 3 - число периодов начисления процентов внутри год
N инф. = 02 - годовой уровень инфляции.
N ДБ = 019 N КБ = 028
N с(ссн) = ( 1 + N ДБ р )р - 1 = ( 1 + 019 3 )3 - 1 = 0202
N с(сд) = ( 1 + N КБ р )р - 1 = ( 1 + 028 3 )3 - 1 = 03
N рк. = N ек. - N инф. 1 + N инф. = 03 - 02 1 + 02 = 0083
СД = ( 1 – СН ) * ПС = ( 1 - 035 ) * 03 = 0195
НR = ДД * СД + ДСК * ССК = 035 * 0195 + 065 + 0202 = 019
3. Расчет инвестиций по вариантам .
К 1 = К скл. + К тер. + К ж.д . + К авт. + К ком. + К эп. где
К скл - капитальное вложение на сооружение склада
К тер. - стоимость земли при размещении склада
К ж.д. + К авт. + К ком. - капитальные вложения на сооружение железнодорожного погрузочно-разгрузочного пути автодороги и комуникаций.
К эп. - капитальные вложения на закупку электропогрузчиков.
К скл. = ( V хр. * Ц хр. + V п-в * Ц п-в ) где
Ц хр. - стоимость одного м3 зоны хранения
Ц хр. = 440 ( руб. м3)
Ц п-в - стоимость одного м3 зоны погрузки- выгрузки
К тер. = ( F хр. + F п-в ) * пр. * Ц тер. где
. пр. - коэффициент учитывающий дополнительную площадь на проезды
Ц тер. - стоимость 1 м2 земли
Ц тер. = 360 ( рубм2)
К ж.д. = L ж.д. * Ц ж.д где
Ц ж.д. - стоимость одного погонного метра железнодорожного погрузочно-разгрузочного пути
Ц ж.д. = 13200 ( руб п.м.)
К авт. = L * В авт. * Ц авт. где
В авт. - ширина автопогрузки
Ц авт. - стоимость сооружений одного квадратного метра автомобильной дороги .
Ц авт. = 600 (рубм2)
К ком. = L * Ц ком. где
Ц ком - стоимость одного погонного метра коммуникаций
Ц ком. = 1800 ( руб. п.м.)
К эп. = z эп. * Ц эп. * ( 1 + γ м. ) * ( 1 + з.у. ) где
Ц эп. - стоимость одного электропогрузчика
Ц эп. = 120000 (руб.)
.γ м. - коэффициент учитывающий затраты на доставку и монтаж
з.у. - коэффициент учитывающий затраты на подзарядную станцию.
К ЭВМ К к.с. - капитальные вложения на приобретение ЭВМ каналов связи и периферийных устройств.
К скл. Подз = L скл. Подз * Ц скл. Подз. где
Ц скл. Подз = 72 900 (рубм)
К роб. = z роб. * Ц роб. * ( 1 + γ м. ) * ( 1 + з.у. )
Ц роб. = 420 000 (руб)
К роб. Низк. = z роб. Низк * Ц роб. Низк * ( 1+ γ м.) * ( 1 + з.у. ) где
Ц роб. Низк. = 300000 (руб)
К лифта = z лифт * Ц лифт * ( 1 + γ м. ) где
Ц лифт = 48000 (руб.)
К ПТС = L ПТС * Ц ПТС * ( 1 + γ м. ) где
Ц ПТС = 1800 (руб. п.м.)
.q яч. = 0154 (тонн)
q ст. - масса металлоконструкции в килограммах на 1 м2 площади
Ц яч. - стоимость одной тонны металла
Ц яч. = 3840 (руб. тонна)
К ЭВМ = n ЭВМ * Ц ЭВМ где
К к.с. = 06 * К ЭВМ
4. Расчет приращения доходов и расходов по вариантам.
С = С зар. Общ. + С отч. + С элэн осв. + С элэн силов. + С мат. + С накл. + С рем. Т.о. + С аморт. + С 2 ЭВМ где
С зар. Общ. - расходы на заработную плату обслуживающего персонала склада
С отч. - отчисление на социальные нужды
С элэн осв. - расходы на освещение территории склада
С элэн силов. - расходы на силовую электроэнергию погрузочно-разгрузочных машин лифтов и ПТС.
С мат. - расходы на материалы (смазочно-обтирочные)
С накл. - накладные расходы (содержание административно-управленческого аппарата )
С рем. Т.о. - расходы на ремонт и техническое обслуживание
С аморт. - амортизационные отчисления на реновацию.
С зар. Общ. = С тар. Зар. + С доплаты + С доплаты + С доп. Зар. где
С тар. Зар - тарифная заработная плата
С тар. Зар. = Σ К r * Т ст. * 12
К r - количество обслуживающего персонала
Т ст. - тарифная ставка по должностям
С доплаты - доплаты к заработной плате
С доплаты = С тар.зар. * 04
С доп. Зар. - дополнительная заработная плата
С доп. Зар = ( С тар.зар. + С доплаты ) * 01
С отч. = 037 С зар.общ.
С элэн осв. = ( F хр. * t осв. * w + F п-в * t осв * w ) * 10-3 * Ц элэн
где t осв. t осв. - время освещения зоны хранения и погрузки выгрузки в течении года
t осв. = 365 * Т * 07
t осв. = 365 * Т * 05
w w - удельная освещенность на 1 м2 площади
w = 5 (Втм2) 2. w = 2 (Вт м2)
w = 6 (Втм2) w = 6 (Вт м2)
Ц элэн = 059 (р кВт час )
С элэн силов1 = Т раб. Эп. * N эп. *γ 1 * γ 2 * γ 3 * γ 4 * Ц элэн
Т раб. Эп. - суммарное время работы электропогрузчика в течении года
N - суммарная мощность в расчете на один электропогрузчик
.γ 1 = 08 - коэффициент учитывающий использование двигателей по времени
γ 2 = 05 - коэффициент учитывающий неодновременность работы электродвигателей.
.γ 3 = 08 - коэффициент учитывающий
γ 4 = 105 - коэффициент учитывающий потери энергии в элекрораспределительной сети
С 2 сил. Элэн = ( Σ n .i =1 * Т раб i * N .i ) * γ 1 * γ 2 * γ 3 * γ 4 * Ц элэн
С мат. = 02 * С элэн силов.
С накл. = 037 * С зар. Об.
С рем т.о. = 015 * К
С аморт. = Σ n i = 1 * К i * .i где
. i - нормы амортизационных отчислений на полное восстановление
С 2 ЭВМ = 42 (рубчас) * Т раб. ЭВМ
К скл. = (110400 * 440 + 38640 * 240) = 578496 * 103 (руб)
К тер. = (22080 + 11040 ) * 15 * 360 = 178848 * 103 (руб)
К ж.д. = 200 * 13200 = 2640 * 103 (руб.)
К авт. = 450 * 20 * 600 = 5400 * 103 (руб)
К ком. = 1532 * 1800 = 27576 * 103 (руб)
К эп. = 60 * 120000 * 11 * 115 = 9108 * 103 (руб)
К 1 = 578496 * 103 + 178848 * 103 + 2640 * 103 + 5400 * 103 + 27576 * 103 + 9108 * 103 = 95640 * 103 (руб)
С зар.общ. = С тар.зар. + С доплаты + С доп.зар
С тар.зар. = Σ n .i =1 * K r .i * T cт .i * 12
К r воз. = 365 * 16 * 60 * 115 2080 = 194 (чел)
К r груз = 365 * 16 * 120 * 115 2080 = 388 (чел)
К r рем = 365 * 16 * 2 * 115 2080 = 7 (чел)
Т ст.воз = 2200 (руб)
Т ст. груз = 2000 (руб.)
Т ст.рем = 1600 (руб)
С тар.зар = (2200 * 194 + 2000 * 388 + 1600 * 7 ) * 12 = 14568 * 103 (руб)
С доплаты = С тар.зар * 04 = 14568 * 103 * 04 = 58272 * 103 (руб)
С доп. зар = ( С тар. Зар. + С доплаты ) * 01 = (14568 * 103 + 58272 * 103) * 01 = 203952 * 103 (руб)
С зар. Общ = 14568 * 103 + 58272 * 103 + 203952 * 103 = 2243472 * 103 (руб)
С отч. = 037 * 2243472 * 103 = 83008464 * 103 (руб)
С элэн осв. = (F хр. * t осв. * w + F п-в * t осв. * w ) * 10-3 * 059
.t осв. = 365 * 16 * 07 = 4088 (кВт)
t осв.= 365 * 16 * 05 = 2920 (кВт)
С элэн осв = ( 22080 * 4088 * 5 + 11040 * 2920 * 6 ) * 103 * 059 = 380394 * 103
С элэн силов = Т раб. Эп. * N эп. * γ1 * γ2 * γ3 * γ4 * 059
Т эп. Раб. = Q г. ( 1- α n.) q эп.
Q г. = 1000000 (тонн)
q эп. = 3995 (тоннчас)
Т эп. Раб. = 1000000 * ( 1 - 02) 3995 ) = 2002503129 (час)
С эл.эн сил. = 2002503129 * 8 * 08 * 05 * 08 * 105 * 059 = 317580 * 103 (руб)
С накл. = 037 * 2243472 * 103 = 83008464 * 103 (руб)
С мат. = 02 * 968891 * 103 = 19378 * 103 (руб)
С рем. Т.о = 015 * 52374 * 103 = 78561 * 103 (руб)
С аморт. = ( 289248 * 01 + 1320 * 005 + 2700 * 01 + 13788 * 02 + 9108 * 0165 ) * 103 = 500706 * 103 (руб)
С 1 = 2243472 * 103 + 83008464 * 103 + 380394 * 103 + 317580 * 103 + 19378 * 103 + 83008464 * 103 + 78561 * 103 + 500706 * 103 = 526168248 * 103
К скл. Наз. = 38400 * 440 + 4200 * 240 = 17904 * 103
К скл. Подз. = 75 * 72900 = 54675 * 103 (руб)
К тер = 3600 * 15 * 360 = 1944 * 103 (руб)
К ж.д. = 120 * 13200 = 1584 * 103 (руб)
К авт. = 115 * 20 * 600 = 1380 * 103 (руб.)
К ком. = 470 * 1800 = 846 * 103
К роб. = 14 * 420000 * 11 * 115 = 7438 2 * 103
К роб. Низк. = 5 * 300000 * 11 * 115 = 18975 * 103 *руб)
К лифта = 3 * 48000 * 15 = 216 * 103 (руб)
К ПТС = 10 * 1800 * 12 = 216 * 103 (руб)
К ЭВМ = 1* 40000 = 40 * 103 (руб)
К к.с = 06 * 40 * 103 = 24 * 103 (руб)
К 2 = 17904 * 103 + 54675 * 103 + 1944 * 103 + 1584 * 103 + 1380 * 103 + 846 * 103 + 74382 * 103 + 18975 * 103 + 216 * 103 + 216 * 103 + 129288 * 103 + 40 * 103 + 24 * 103 = 516916 * 103 (руб)
С зар . общ. = С тар. Зар. + С доп. зар.
С тар зар. = Σ n .i = 1 К r .i * T cт .i * 12
К r опер ЭВМ = 365 * 24 * 2 * 115 2080 = 10 (чел)
К r рем = 365 * 24 * 4 * 115 2080 = 20 (чел)
Т ст.опер. = 2000 (руб)
Т ст. рем. = 1600 (руб)
С зар.тар. = ( 10 * 2000 + 20 * 1600 ) * 12 = 624 * 103 (руб)
С доплаты = 624 * 103 * 04 = 2496 * 103 (руб)
С доп. зар. = (624 * 103 + 2496 * 103 ) * 01 = 8736 * 103 (руб)
С зар. Общ. = 96096 * 103 (руб)
С отч. = 037 * 96096 * 103 = 3555552 * 103
С элэн осв = (F хр. * t осв. * w + Fп-в * t осв * w ) * 10-3 * 059
.t осв = 365 * 24 * 07
t осв = 365 * 168 * 05
С осв элэн = ( 3900 * 6132 * 2 + 1200 * 3066 * 6 ) * 10-3 * 059 = 412438 * 103 (руб)
С элэн силов. = ( Т роб.раб * N роб + Т роб. Нижн. Раб. * N роб. Нижн. + Т раб. Роб * N ПТС * t ПТС + Т раб.лифта * N лифта ) * 08 * 05 * 08 * 105 * 059
Т наземн. Роб. Раб = 600000 (1-02) 12 = 40000 (час)
Наземн. Т роб.нижн. раб. = 600000 ( 1- 02) 30 = 16000 (час.)
Подз. Т раб. Роб = 400000 (1- 02) 12 = 2666667 (час)
Подз. Т роб. Нижн. Раб = 400000 (1-02) 30 = 1066667 (час)
Т лифт раб. = 400000 ( 1- 02 ) 33875 = 9446494 (час)
С силов элэн = (40000 * 23.5 + 16000 * 8 + 2666667 * 235 + 1066667 * 8 + 40000 * 035 * 10 +9446494 * 70 ) * 08 * 05 * 08 * 105 * 059 = 5117079 * 103 (руб)
С мат = 02 * 156 1143 * 103 = 31223 * 103 (руб)
С накл = 037 * 96096 * 103 = 3555552 * 103 (руб)
С рем. Т.о = 0.15 * 39819 * 103 = 597297 * 103 ( руб)
С аморт. = (( 8952 + 54675) * 01 + 792 * 105 + (74382 + 18975 + 216 ) * 0165 + 690 * 01 + 423 * 02 + 108 * 0094 + 129288 * 015 + 12 * 05) * 103 = 51533157 * 103 (руб)
С ЭВМ = 42 * 365 * 24 = 36792 * 103 (руб)
С 2 = 96096 * 103 + 3555552 * 103 + 41 2438 * 103 + 5117079 * 103 + 31223 * 103 + 3555552 * 103 + 597297 *103 + 51533157 * 103 + 36792 * 103 = 252322917 * 103
Расчеты чистых денежных потоков приведены в таблице 4.2.
5. Показатели эффективности инвестиций.
Основными показателями эффективности инвестиций являются:
Чистая текущая стоимость (NPV)
Внутренняя норма рентабельности (IRR)
Чистая текущяя стоимость (NPV) представляет сумму дисконтированных чистых денежных потоков порожденных инвестициями и определяется следующим образом:
NPV = ЧДПi (1 + HR)^i где
ЧДПi – чистый денежный поток тыс. руб.
HR – барьерная ставка
n – число лет функционирования объекта.
NPV = (439484 + 25759(1+019)^1 + + 25759(1 + 019)^8) * 10^3= 1458088 * 10^3
При изменении барьерной ставки HR будет меняться
Зависимость NPV от HR показана на графике на рис
Вывод: В результате расчетов получили что строительство подземного склада и применение робокаров с высотой подъема груза 135 м выгодно не только по капитальным вложениям но и позволило высвободить 559 человек в год сокротить эксплуатационные расходы и получить величину чистой текущей стоимости NPV равной 1458088 * 10^3 руб.
Положительная величина NPV говорит о целесообразности применения данной разработки.
Козловой кран Щекланов.doc
1. Характеристика конструкции разрабатываемой траверсы
Настоящий раздел представляет собой расчет экономической эффективности применения разрабатываемого в данном дипломном проекте траверсы грузоподъемностью 10 т.
Траверса предназначен для непосредственного бесперебойного захвата звеньев массой до 9.9т. Траверса может быть применена на кранах любой конструкции с электроприводом имеющих грузоподъемность не менее 10 т на канатах.
За базовый вариант сравнения в расчете экономической эффективности принята схема работы крана с крюковыми захватами.
Учет фактора времени в расчетах осуществлялся с помощью дисконтирования т. е. приведения будущих результатов применения траверсы в стоимостном выражении к нулевому году.
2. Расчет экономической эффективности
2.1. Определение количества кранов при использовании базового и нового вариантов
Находим время рабочего цикла козлового крана
где tз – время застроповки звена tз = 15 с;
tо – время отстроповки звена tо = 10 с;
у – коэффициент совмещения операций для козловых кранов у = 08;
Нср – средняя высота подъема (опускания) груза за один цикл Нср = 4 м;
tТ – средний путь передвижения тележки за цикл tТ = 125 м;
tКР – средний путь передвижения крана за цикл tКР = 71 м;
–номинальные скорости подъема груза передвижения тележки
и передвижения крана мс;
Техническая производительность козлового крана
где а - число грузовых единиц (звеньев) за один цикл для
Эксплуатационная производительность козлового крана
где кв – коэффициент использования погрузочно-разгрузочных машин по
Сменная производительность козлового крана
где tсм – продолжительность смены tсм = 8 часов;
Годовая производительность козлового крана
где nр – число рабочих дней в году nр = 230 дней;
Для базового варианта
Суточный объем механизированных работ при перегрузке звеньев по прямому варианту (звеносборочная база-вагон)
где – суточный звенопоток по изготовлению и пребытию;
кп – коэффициент перегрузки звеньев по прямому варианту кп = 03;
у1 у2 – число операций выполняемых со звеном при различных
вариантах перегрузки у1 = 1 у2 = 2;
Суточный объем механизированных работ при перегрузке звеньев по варианту: звеносборочная база-штабель-вагон
Число козловых кранов определяем по формуле
где m – число рабочих смен за сутки m = 1;
– суточный объем механизированных работ при перегрузке
звеньев по прямому варианту (звеносборочная база-вагон) звен;
– то же но при перегрузке звеньев по варианту: звеносборочная база-штабель-вагон звен;
П – сменная производительность машин при перегрузке звеньев
по соответствующему варианту звенсмена;
nвых – число выходных дней в году nвых = 106;
nпр – число праздничных дней в году nпр = 12;
nрем – регламентированное время простоя каждой машины в ремонте в
течение года nрем =17 суток;
Т.к краны работают в паре то потребность звеносборочной базы в козловых кранах составляет М=2
2.2. Расчет списочного числа рабочих для обслуживания крана
Списочное число механизаторов для обслуживания кранов и оборудования определяют учитывая следующие потребности
крановщик на каждый кран;
механик-ремонтник на каждый кран;
стропальщика на каждый кран.
Списочное число рабочих рассчитываем по формуле
где a – коэффициент подмены α = 12;
m – количество рабочих смен m = 1.
График работы: 5дней по 8 часов 2 выходных дня
Необходимо R = 10 человек.
Необходимо R = 5 человек.
Сравнительная технико-экономическая характеристика
разрабатываемый вариант с траверсами
Масса навесного оборудования кг
Высота подъема груза м
Техническая производительность
Эксплуатационная производительность звенчас
продолжение таблицы 7.1
Сменная производительность
Годовая производительность
Обслуживающий персонал чел
Цена навесного оборудования руб
3. Общий объем инвестиций
В связи с приобретением нового навесного оборудования – траверса величина И войдет в расчет чистых денежных потоков со знаком минус т.е. имеет место отток денежных средств. Эти инвестиции осуществляются в нулевой год.
4. Определение эксплуатационных расходов
В составе текущих издержек учитываются основная и дополнительная заработная плата рабочих занятых управлением краном техническим его обслуживанием и ремонтом затраты на материалы электроэнергию.
4.1 Расходы на заработную плату
Для обслуживания базового варианта необходимы два крановщика пятого разряда четыре стропальщика четвертого разряда два механика четвертого разряда и два вспомогательных рабочих. Для обслуживания нового варианта необходимы два крановщика пятого разряда два механика четвертого разряда и один вспомогательный рабочий.
где - расходы на заработную плату за год для базового варианта;
- расходы на заработную плату за год для нового варианта;
где - расходы на заработную плату в месяц для базового варианта;
- расходы на заработную плату в месяц для нового варианта;
- размер доплаты 30% от тарифа;
- размер дополнительной заработной платы10% размера тарифа;
4.2. Расходы на электроэнергию
где - затраты на электроэнергию для базового варианта;
- затраты на электроэнергию для нового варианта;
где Сэл - цена одного кВтчас электроэнергии Сэл = 308 руб.;
N - суммарная установочная мощность электродвигателей всех
Тф – годовой фонд рабочего времени Тф = 1840 ч;
kn - коэффициент по мощности kn = 08;
kпот - коэффициент учитывающий потери электроэнергии в сети
КПД - коэффициент полезного действия КПД = 085;
ПВ - средняя продолжительность включения двигателей отдельных
механизмов в процессе работы крана ПВ = 25%;
4.3. Затраты на вспомогательные материалы
Затраты на вспомогательные материалы определяются в размере 15%
стоимости электроэнергии
4.4. Затраты на ремонт траверсы
Затраты на ремонт траверсы рассчитываются укрупнено и составляют 12 % от стоимости траверсы
4.5. Амортизационные отчисления
где NА – норма амортизации NА = 167%;
5. Корректировка денежных потоков
Корректировка денежных потоков проводится по амортизационым отчислениям.
6. Расчет чистых денежных потоков
Расчет чистых денежных потоков приведен в таблице 7.2. Чистые денежные потоки представляют собой разность результатов достигнутых в
i-том году и затрат осуществленных в том же году. В качестве результатов выступает годовая величина чистой прибыли.
- вспомогательные материалы
- приращение доходов
Корректировка денежных потоков (амортизация)
Чистые денежные потоки (ЧДП)
Расчет чистых денежных потоков
7. Оценка эффективности инвестиций
Показателем эффективности инвестиций является чистая текущая стоимость (NPV) представляющая собой сумму дисконтированных чистых денежных потоков от инвестиций за весь расчетный период. Дисконтирование (т.е. учет фактора времени) осуществляется следующим образом
где БС – барьерная ставка
где ДД – доля долга ДД = 03%;
ДСК – доля собственного капитала ДСК = 07 %;
СД – стоимость долга %;
CCК – стоимость собственного капитала %;
где СН – ставка налога на прибыль СН = 02%;
NC(CД) – номинальная процентная ставка
где NКБ – номинальная кредитная банковская ставка NКБ = 023%;
Р – число периодов начисления процентов внутри года Р = 2;
где NДБ – номинальная депозитная банковская ставка NДБ = 01%.
Значение номинальной банковской ставки рассчитывается как среднее по десяти банкам.
Значение NPV положительно инвестиционный проект является эффективным и может рассматриваться вопрос о его осуществлении.
Положительное значение чистой текущей стоимости (NPV) говорит об эффективности рассматриваемого варианта замены крюковых захватов на полуавтоматические траверсы.
Рассмотрим зависимость чистой текущей стоимости от величины барьерной ставки для варианта работы предприятия в одну смену по 8 часов (по данным таблицы 7.3) т.е. NPV = (БС).
Зависимость NVP = f(БС)
Зависимость NPV = f(БС)
Вывод: В ходе расчета экономической эффективности использования козлового крана с траверсой. По сравнению с вариантом работы крана с крюковыми захватами увеличилась производительность крана. Так как NPV > 0 (3011068085 руб.) и IRR > БС то это говорит об эффективности проекта. Экономический эффект достигнут сокращением численности обслуживающего персонала.
ПФМ Юскаев.docx
При современном производстве для внедрения новых технологий требуется прежде всего экономическое обоснование новшеств. Для этого проведем экономический расчет эффективности применения на железной дороге гидравлической насосной станции для выполнения путевых работ в сравнении с электрической генераторной станцией.
1 Определение чистой текущей стоимости (NPV).
Чистая текущая стоимость (NPV) представляет сумму дисконтирования чистых денежных потоков порожденных инвестициями определяется следующим образом.
где: ЧДП - чистый денежный поток руб;
БС - барьерная ставка;
n - число лет функционирования объекта.
Чистый денежный поток берется со знаком соответствующим оттоку или притоку денежных средств. Положительное значение ЧДП говорит об эффективности рассматриваемого варианта.
Определение барьерной ставки.
где: ДД = 03 - доля долга;
СД - стоимость долга%;
ДСК - доля собственного капитала;
ССК – стоимость собственного капитала%.
Так как выплаты процентов уменьшают величину налогооблагаемой прибыли то соответственно уменьшается и величина налоговых выплат. Экономия на налогах частично компенсирует выплаты по долгам. Поэтому реальный процент выплат по долгам с учетом экономии составит
где: СН=02 – ставка налога на прибыль;
Ne(СД) – уровень реальной процентной ставки.
Доля долга и собственных средств в сумме равны единице. Поэтому определив одну из составляющих можно определить и другую:
Стоимость собственного капитала при отсутствии развитого фондового рынка в России для Государственных предприятий можно взять на уровне альтернативного размещения средств (депозитные банковские ставки проценты по государственным облигациям и т.д.).
В условиях высокой инфляции ставки ссудного процента и депозитные ставки рассчитываются с учетом внутригодовых реинвестиций и очищаются от инфляции по следующей методике.
Берутся номинальные (т.е. с учетом инфляции) годовые ставки коммерческих банков. На их основе рассчитываются эффективные ставки (т.е. с учетом реинвестиций по периодам внутри года):
где: Ne (СД ССК) - номинальная эффективная ставка (кредитная и депозитная соответственно);
Ne (кбдб) - номинальная банковская ставка (кредитная и депозитная соответственно);
р=2 - число периодов начисления процентов внутри года.
Ne (кб) =02-03. Согласно исходным данным принимаем Ne(кб) =023.
Сравнение характеристик ПФМ и ручного труда.
Наименование характеристик для сравнения
Механизированный (разрабатываемый вариант)
Ручной труд (бригады из 6-х рабочих)
Заработная плата руб.
Расход электроэнергии кВтчас.
2 Расчет чистых денежных потоков.
Все полученные результаты расчётов сведены в таблицу 2.
Расчет заработной платы грузчика.
Тарифная ставка рабочего первого разряда составляет 5230 рублей. Тарифный коэффициент рабочего 4-го разряда составляет 144.
Доплата составляет 30%.
Основная заработная плата: тарифная ставка + доплата.
Дополнительная заработная плата составляет 10% от основной заработной платы.
Получаем 97905601= 979056 рубля
Расходы на социальные нужды составляют 26% от основной и дополнительной заработной платы и доплаты.
Получаем (979056+979056 )026=28001 рублей.
Расчет заработной платы машиниста.
Ставка машиниста первого разряда составляет 5230 рублей. Коэффициент начисления на заработную плату ставки рабочего составляет 176.
Получаем 5230 176=92048 рублей.
Получаем 9204803= 276144 рубля.
Основная заработная плата: тарифная ставка + доплата.
Получаем 92048+276144=1196624 рубля.
Получаем 119662401= 1196624 рубля.
Расходы на социальные нужды составляют 26% от основной заработной платы и доплаты.
Получаем (1196624+1196624)026= 3422345 рубля.
Рассчитаем время работы пакетоформирующей машины. Число рабочих дней в году принимаем равным 200 дням. Будем считать что машина будет работать 24 часа в день. Получаем что машина используется 20024=4800 часов в год.
Вычисления ведутся по разнице между показателям ручного труда и механизированного (нового).
Как видно из таблицы стоимость ПФМ составляет 1450000 рублей.
Второй и последующие годы.
Нет никаких инвестиций.
Приращения доходов и расходов.
Согласно таблице число работников при базовом варианте составляет 6 человек а при новом 1. Получаем приращение доходов при экономии на выплате заработной платы используя ранее полученные данные.
Заработная плата грузчика
При выплате основной заработной платы в месяц:
79056 - 11196624= 4677712 рубля
При выплате основной заработной платы в год:
7771212=56132544 рублей.
При выплате дополнительных выплат в месяц:
79056- 11196624=4677712 рубля.
При выплате дополнительных выплат в год:
7771212= 56132544 рубля.
При расходах на социальные нужды в месяц:
8001 - 13422345=13378255 рубля.
При трате на социальные нужды в год:
37825512= 16053906 рубля.
Расход электроэнергии ПФМ составляет 191 кВтчас с учетом коэффициента использования электродвигателя по мощности. Стоимость кВтчас 3 рубля.
Найдем расходы на электроэнергию ПФМ за год 275040 рублей.
Расход электроэнергии грузчиками составляет 1 кВтчас.
Найдем расходы на электроэнергию затрачиваемую грузчиками за год 14400 рублей.
Разница между показателями ручным и механическим трудом составляет
400 – 275040 = - 260640 руб.год.
Расходные материалы.
Расходные материалы составляют 2 % от стоимости машин. Получаем выплаты на расходные материалы для ПФМ 1450000002=29000 рублей. Для грузчиков расходы на два комплекта спец. одежды в год приходящиеся на одного человека 1500 рублей. Разница составляет 61500-29000= -20000 рублей.
Расходы на ремонт составляют 5 % от стоимости машин.
Получаем выплаты на ремонт для ПФМ 1450000005=72500 рублей. Разница составляет - 72500 рублей.
Амортизация ПФМ составляет 666% от стоимости машины при работе в течении 15 лет.
Поэтому отчисления на амортизацию для ПФМ получаются:
5000000666 = 96570 рублей.
Разница составляет – 96570 рублей.
Эти пункты одинаковы для всех лет наблюдения.
Сложим все пункты приращения прибыли. Получаем:
Основная заработная плата + дополнительные выплаты + отчисления на социальные нужды + расходы на электроэнергию + отчисления на расходные материалы + расходы на ремонт + отчисления на амортизацию =
132544+56132544+16053906 - 260640 – 20000 - 72500 – 96570=328287044 руб.
Занесем в графу таблицы «Всего».
Налог составляет 20%.Вычислим отчисления на прибыль:
-328287044 02= -6565741 рубля.
Корректировка по амортизации.
Т. к. мы не получаем нигде денег за амортизацию чтобы более точно рассчитать налоги. Перенесем данные из графы «Амортизация» в графу «Корректировка по амортизации» со знаком «+».
Вычислим чистую прибыль с учетом корректировки по амортизации и без налогов. Из графы «Всего» вычтем графу «Налог на прибыль» и прибавим графу «Корректировка по амортизации». Получаем: 328287044 – 6565741=262629634 рубля.
Занесем результат в графу «Итого».
Чистая текущая стоимость (NVP) представляет сумму дисконтирования чистых денежных потоков порожденных инвестициями определяется следующим образом.
Барьерная ставка рассчитана ранее.
Чистая текущая стоимость (NPV)
Налог на прибыль (20%)
Корректировка по амортизации
Чистые денежные потоки
Проведенный расчет эффективности применения пакетоформирующей машины показывает что использование новой машины целесообразно и экономически обосновано так как значение NPV=7863796 > 0.
Миронов ПФМ для гранулированных хим удобрений.doc
При современном производстве для внедрения новых технологий требуется прежде всего экономическое обоснование новшеств. Для этого проведем экономический расчет эффективности применения пакетоформирующей машины в сравнении с ручным трудом бригады рабочих.
Определение чистой текущей стоимости (NPV)
Чистая текущая стоимость (NPV) представляет сумму дисконтирования чистых денежных потоков порожденных инвестициями определяется следующим образом.
где: ЧДП - чистый денежный поток руб.;
БС - барьерная ставка;
n - число лет функционирования объекта.
Чистый денежный поток берется с знаком соответствующим оттоку или притоку денежных средств. Положительное значение ЧДП говорит об эффективности рассматриваемого варианта.
Определение барьерной ставки
где ДД = 025 - доля долга;
СД- стоимость долга %;
ДСК- доля собственного капитала;
ССК – стоимость собственного капитала %.
Так как выплаты процентов уменьшают величину налогооблагаемой прибыли то соответственно уменьшается и величина налоговых выплат. Экономия на налогах частично компенсирует выплаты по долгам. Поэтому реальный процент выплат по долгам с учетом экономии составит
где СН=02 – ставка налога на прибыль;
Ne(СД) – уровень реальной процентной ставки.
Доля долга и собственных средств в сумме равны единице. Поэтому определив одну из составляющих можно определить и другую:
Стоимость собственного капитала при отсутствии развитого фондового рынка в России для Государственных предприятий можно взять на уровне альтернативного размещения средств ( депозитные банковские ставки проценты по государственным облигациям и т.д.).
В условиях высокой инфляции ставки ссудного процента и депозитные ставки рассчитываются с учетом внутригодовых реинвестиций и очищаются от инфляции по следующей методике.
Берутся номинальные (т.е. с учетом инфляции) годовые ставки коммерческих банков. На их основе рассчитываются эффективные ставки (т.е. с учетом реинвестиций по периодам внутри года):
где Ne (СД ССК)- номинальная эффективная ставка (кредитная и депозитная соответственно);
Ne (кбдб) - номинальная банковская ставка (кредитная и депозитная соответственно);
р=2 - число периодов начисления процентов внутри года.
Ne (кб) =02-03 принимаем Ne (кб) =02
Сравнение характеристик пакетоформирующей машины и ручного труда бригады рабочих.
Наименование характеристик для сравнения
Механизированный (разрабатываемый вариант)
Ручной труд (бригады из 6-х рабочих)
Заработная плата руб.
Расход электроэнергии
Расчет чистых денежных потоков.
Все результаты сведены в таблицу 2.
Расчет заработной платы грузчика.
Тарифная ставка рабочего первого разряда составляет 3773 рублей. Тарифный коэффициент рабочего 4-го разряда составляет 182.
Доплата составляет 50%. Получаем рубль.
Основная заработная плата: тарифная ставка + доплата.
Дополнительная заработная плата составляет 15% от основной заработной платы. Получаем рубля.
Расходы на социальные нужды составляют 26% от основной и дополнительной заработной платы и доплаты.
Расчет заработной платы машиниста.
Ставка машиниста первого разряда составляет 3773 рублей. Коэффициент начисления на заработную плату ставки рабочего составляет 24.
Доплата составляет 50%. Получаем рубля.
Дополнительная заработная плата составляет 15% от основной заработной платы.
Расходы на социальные нужды составляют 26% от основной заработной платы и доплаты.
Рассчитаем время работы пакетоформирующей машины. Число рабочих дней в году принимаем равным 200 дням. Будем считать что машина будет работать 8 часов в день. Получаем что машина используется 200*8=1600 часов в год.
Вычисления ведутся по разнице между показателем ручного труда и механизированного (нового).
Как видно из таблицы стоимость ПФМ составляет 448000 рублей.
Второй и последующие годы.
Нет никаких инвестиций.
Приращения доходов и расходов.
Согласно таблице число работников при базовом варианте составляет 6 человек а при новом 1. Получаем приращение доходов при экономии на выплате заработной платы используя ранее полученные данные.
Заработная плата грузчика
При выплате основной заработной платы в месяц.
При выплате основной заработной платы в год.
При выплате дополнительных выплат в месяц.
При выплате дополнительных выплат в год.
При расходах на социальные нужды в месяц.
При трате на социальные нужды в год.
Расход электроэнергии ПФМ составляет 3465 кВтчас с учетом коэффициента использования электродвигателя по мощности. Стоимость кВтчас 22 рубля.
Найдем расходы на электроэнергию ПФМ за год:
Расход электроэнергии грузчиками составляет 1 кВтчас.
Найдем расходы на электроэнергию затрачиваемую грузчиками за год рублей.
Разница между показателями ручным и механическим трудом составляет
Расходные материалы.
Расходные материалы составляют 2 % от стоимости машин. Получаем выплаты на расходные материалы для ПФМ рублей. Для грузчиков расходы на два комплекта спец. одежды в год приходящиеся на одного человека 800 рублей.
Разница составляет рублей.
Расходы на ремонт составляют 5 % от стоимости машин. Получаем выплаты на ремонт для ПФМ рублей.
Разница составляет -22400 рублей.
Амортизация ПФМ составляет 666% от стоимости машины при работе в течении 15 лет. Поэтому отчисления на амортизацию для ПФМ получаются рублей.
Разница составляет -29568 рублей.
Эти пункты одинаковы для всех лет наблюдения.
Сложим все пункты приращения прибыли. Получаем:
Основная заработная плата + дополнительные выплаты + отчисления на социальные нужды + расходы на электроэнергию + отчисления на расходные материалы + расходы на ремонт + отчисления на амортизацию=
Занесем в графу таблицы «Итого».
Налог составляет 20% . Вычислим отчисления на прибыль - рублей.
Корректировка по амортизации.
Т. к. мы не получаем нигде денег за амортизацию чтобы более точно рассчитать налоги. Перенесем данные из графы «Амортизация» в графу «Корректировка по амортизации» со знаком «+».
Вычислим чистую прибыль с учетом корректировки по амортизации и без налогов. Из графы «Всего» вычтем графу «Налог на прибыль» и прибавим графу «Корректировка по амортизации».
Занесем результат в графу «Итого».
Чистые денежные потоки (ЧДП).
Для того чтобы вычислить ЧДП требуется сложить инвестиции и прибыль без налогов из графы «Итого».
Чистая текущая стоимость (NVP) представляет сумму дисконтирования чистых денежных потоков порожденных инвестициями определяется следующим образом.
где: ЧДП - чистый денежный поток руб;
НR - барьерная ставка;
Барьерная ставка рассчитана ранее.
Чистая текущая стоимость (NPV)
Налог на прибыль (20%)
Корректировка по амортизация
Чистые денежные потоки
Проведенный расчет эффективности применения пакетоформирующей машины показывает что использование новой машины целесообразно и экономически обосновано. ПФМ принесет прибыль в размере 1842342 рублей к концу своей эксплуатации.
Мост кран Гулевич ТДМ441.doc
1.Определение барьерной ставки
Капитал предприятия формируется из двух источников: собственного и заемного. Для привлечения капитала из этих источников предприятию необходимо платить. Это либо процент по кредитам (заемный капитал) либо дивиденды (акционерный капитал). Чем более рискованный проект тем более высоких дивидендов будут ожидать акционеры а кредиторы будут предлагать кредиты под более высокие проценты. Акции предприятий и кредиты реализуются на финансовых рынках. И именно силы свободного рынка определяют степень риска инвестиций.
Поэтому можно сказать что стоимость капитала предприятия представляет собой рыночную оценку уровня риска по операциям предприятия. Предприятия принимают эту оценку в качестве среднего значения барьерного коэффициента HR так как у них нет более объективного показателя.
В общем случае стоимость капитала – это средневзвешенная цена (в процентах) которую предприятие уплатило за денежные средства используемые для формирования своего капитала. Эта величина определяется соотношением заемного и собственного капитала:
где СК – стоимость капитала %;
СД – стоимость долга %;
ДСК=075 – доля собственного капитала;
ССК – стоимость собственного капитала %.
Так как выплаты процентов уменьшают величину налогооблагаемой прибыли то соответственно уменьшается и величина налоговых выплат. Экономия на налогах частично компенсирует выплаты по долгам. Поэтому реальный процент выплат по долгам с учетом экономии составит
где – ставка налога на прибыль;
уровень реальной процентной ставки.
Доля долга и собственных средств в сумме равна единице.
ДД + ДСК = 1 ДД = 1 – ДСК;
В условиях высокой инфляции ставки ссудного процента и депозитные ставки рассчитываются с учетом внутригодовых реинвестиций и очищаются от инфляции по следующей методике.
Берутся номинальные (т.е. с учетом инфляции) годовые ставки коммерческих банков. На их основе рассчитываются эффективные ставки (т.е. с учетом реинвестиций по периодам внутри года):
где номинальная и эффективная ставка (кредитная и депозитная соответственно);
номинальная банковская ставка (кредитная и депозитная соответственно);
р – число периодов начисления процентов внутри года.
2. Расчет экономической эффективности
2.1. Характеристика и сферы применения нового крана с траверсой
Развитие и повышение эффективности складских работ неразрывно связаны с совершенствованием конструкций средств механизации погрузочно-разгрузочных работ.
Задачи дальнейшего совершенствования и интенсификации промышленного производства пути повышения уровня его механизации и автоматизации могут выть успешно решены посредством комплексного совершенствования всех звеньев производственного процесса в том числе и складского хозяйства предприятий.
Складирование грузов необходимо в связи с имеющимися неравномерностями циклов производства транспортировок и потребления материальных ценностей. Склады различных типов создаются вначале и конце транспортных грузопотоков и производственных процессов для временного накопления грузов и своевременного снабжения материалами в нужных количествах.
Склады на промышленных предприятиях играют важную роль в общем процессе производства. Поэтому от уровня технологической оснащенности и организации работ на этих складах зависит организованность общий ритм и эффективность производственного процесса.
Для производства погрузочно-разгрузочных и складских работ на открытых площадках хранения сортового листового и различных других металлоизделий проводим модернизирование и усовершенствование мостового крана общего назначения с клещевым захватом.
Годовой грузопотоктыс.т.
Количество смен в суткиm.
Количество работников обслуживающих кран:
- вспомогательного подъема
двигателей работающих
одновременно Nдв кВт:
2.2. Определение годовой производительности крана.
Расчет годового объема грузопереработки крана выполнен по данным Единых норм выработки и времени на вагонные автотранспортные и складские погрузочно-разгрузочные работы .
2.2.1. Эксплуатационная производительность
где Q = 20 т – номинальная грузоподъемность;
ТЦ = 449 с – продолжительность одного цикла – для нового крана;
ТЦ = 3155 с – продолжительность одного цикла – для базоого крана ( с учетом времени затраченного на замену грузозахватного приспособления).
КВ = 08 – коэффициент использования машины по времени;
Кгр= 08 – коэффициент использования по грузоподъемности.
Произведем расчет по формулам:
2.2.2. Суточная производительность
где Пэ – эксплуатационная производительность тчас;
tсм = 11 часов – время смены.
2.2.3. Годовая производительность крана
где 250 – количество рабочих дней в году.
2.3. Определение эксплуатационных расходов
В составе текущих издержек учитываются основная и дополнительная заработная плата рабочих занятых управлением краном техническим его обслуживанием и ремонтом затраты на материалы электроэнергию.
2.3.1. Определим расходы по заработной плате
Для обслуживания базового крана необходим 1 крановщик четвертого разряда три стропальщика третьего разряда
Заработная плата машинистов
где т = 2 – количество смен;
Т – годовой фонд рабочего времени Т = 2750 ч;
кп – коэффициент учитывающий дополнительную заработную плату прими и доплаты кп = 2;
rм – часовая тарифная ставка машиниста;
i – количество работников i – того разряда.
где kм = 162 руб – тарифная ставка для машинистов четвертого разряда.
Заработная плата стропальщиков
где rр – часовая тарифная ставка машиниста;
где kР = 144 руб – тарифная ставка для стропальщиков третьего разряда.
Для обслуживания нового крана необходим 1 крановщик четвертого разряда и два стропальщик третьего разряда:
2.3.2. Определим расходы на электроэнергию
где -цена одного кВт в час силовой электроэнергии =13 [рубль];
N-суммарная установочная мощность электродвигателей всех механизмов;
-коэффициент по мощности =08;
-коэффициент учитывающий потери электроэнергии в сети =105;
-коэффициент полезного действия =085;
ПВ- средняя продолжительность включения двигателей отдельных механизмов процессе работы крана 25%.
2.3.3.Определим расходы на вспомогательные материалы
где квсп = 015 – коэффициент учитывающий стоимость вспомогательных материалов от стоимости электроэнергии.
2.3.4. Определим расходы на техническое обслуживание и ремонт кранов
где км – коэффициент учитывающий стоимость материалов на проведение технических обслуживаний и ремонтов доля единиц от стоимости крана
2.3.4.Определим расходы на социальные нужды
где ксн – коэффициент учитывающий социальные нужды в долях единиц от заработной платы ксн = 026.
Суммарные эксплуатационные расходы
2.4. Денежные потоки и инвестиции
Экономия на заработной плате при использовании нового крана составит
Экономия на электроэнергии
Экономия на вспомогательных материалах
Затраты на материалы на ремонт
Экономия на социальных нуждах
2.5. Определение капитальных вложений
2.6. Определим амортизацию
где qa – норма амортизации qa = 005.
Затраты на амортизацию
Расчет чистых денежных потоков ( руб.)
Приращение доходов и расходов.
Экономия на ремонт и техническое обслуживание
Экономия на социальные нужды
Экономия на вспомогательные материалы
Корректировка денежных потоков
Чистые денежные потоки
3. Расчет чистой текущей стоимости
Чистая текущая стоимость (NVR) представляет собой сумму дисконтированных чистых денежных потоков порожденных инвестициями и определяется следующим образом:
где ЧДП – чистый денежный поток руб;
HR – барьерная ставка;
n – число лет функционирования объекта.
Положительное значение чистой текущей стоимости (NPV) и IRR>БС говорят об эффективности модернизации мостового крана общего назначения 205.
Введение.docx
В народном хозяйстве нет предприятий не имеющих в своем составе складов. А в такой отрасли как материально-техническое снабжение склады являются основными производственными подразделениями.
Склады в системе материально-технического снабжения должны обеспечивать в установленном ритме основное производство материально-техническими ресурсами в потребных количествах и ассортименте. Причем поставка продукции должна осуществляться в объемах менее транзитных норм отгрузки чтобы не создавать излишних производственных запасов на промышленных предприятиях. Наиболее распространенной складской продукцией являются тарно-штучные грузы к которым обычно относят грузы любых видов упакованные в тару и хранимые на поддонах в ящичной таре или в контейнерах.
На грузовых фронтах всех складов выполняют погрузочно-разгрузочные операции которые отличаются высокой интенсивностью особенно в пунктах стыка различных видов транспорта. Под влиянием технического прогресса и прежде всего развития вычислительной и подъемно-транспортной техники крупные складские системы превращаются в современные предприятия с четко организованным автоматизированным технологическим процессом — транспортно-складские (грузовые) комплексы (ТСК). Четкий ритм их функционирования обеспечивают сложные автоматизированные поточно-транспортные системы (ПТС) которые по структуре и масштабам напоминают автоматизированные поточные технологические линии современных промышленных предприятий. ПТС состоят из конвейеров упаковочных пакетоформирующих и пакеторазборочных агрегатов автоматизированных складских и погрузочно-разгрузочных машин накопителей и др. Классификация ТСК по функциональному принципу дана на рис. 1. Могут быть также предложены в зависимости от потребностей практики другие частные признаки классификации например тип подъемно-транспортного оборудования вариант объемно-планировочного решения взаимное расположение погрузочно-разгрузочных путей и автопроездов и др.
Рис.1 . Классификация транспортно-складских комплексов
Склады представляют собой сложное хозяйство оснащенное высокопроизводительным специальным оборудованием. До недавнего времени основными средствами механизации работ на складах тарно-штучных грузов служили мостовые краны напольные погрузчики и штабелеры. Однако по мере роста потребности в складских помещениях все более очевидными стали недостатки напольных погрузочно-разгрузочных машин – необходимость в устройстве широких проходов для движения погрузчиков и штабелеров и ограниченная высота подъема груза.
Поиски оборудования обеспечивающего максимальное использование складских помещений удобство доступа к грузам и высокую производительность привели к созданию различных систем складирования грузов. Наибольшее распространение получили системы с кранами-штабелерами укладывающими грузы в стеллаж с помощью грузозахватных устройств.
Краны-штабелеры позволяют рационализировать складское хозяйство экономить площади высвободить значительное количество вспомогательных рабочих и открывают широкие возможности для автоматизации складирования.
Краны-штабелеры применяют в самых различных отраслях промышленности но особенно эффективно – в машиностроении металлургической промышленности материально-техническом снабжении.
Краны-штабелеры применяют в таких отраслях в которых ранее использовали лишь традиционные подъемно-транспортные машины.
Основным видом подъемно-транспортного оборудования складов стеллажного типа являются мостовые краны-штабелеры и стеллажные штабелеры(рис. 2). Практика и исследования показывают что мостовые краны-штабелеры целесообразно применять при высоте стеллажей до 10-12 м; при более высоких стеллажах более экономичными являются стеллажные штабелеры.
Рис. 2. Схема стеллажного крапа-штабслера установленного на складе: 1 — подающие роликовые конвейеры; 2 — поворотная секция роликового конвеера; 3 — контроль размерен пакетов; 4- распределительный конвейер: 5 — площадка для установки грузов. 6 — стеллажный кран
Мостовой кран-штабелер имеет вертикальную колонну 5 подвешенную к грузовой тележке 4 перемещающейся по мосту 3 передвигающемуся по крановым рельсам 1 (рис. 3 а). По колонне перемещается грузозахватное устройство в виде вил 6 а нередко и кабина крановщика. Подъем
(и опускание) кабины может осуществляться тем же механизмом что и подъем груза. Находят применение раздельные механизмы подъема кабины и груза. Один такой кран-штабелер может обслуживать группу стеллажей и даже весь склад.
Стеллажный кран-штабелер имеет вертикальную колонну перемещающуюся между стеллажами (рис. 3 б). В этих кранах тележка передвигается по рельсам уложенным на стеллажах. Грузоподъемное устройство перемещающееся по колонне должно обслуживать оба стеллажа (правый и левый). Если колонна будет выполнена поворотной то требуется увеличить расстояние между стеллажами. Грузозахватное устройство выполнено выдвижным.
Стеллажные краны могут перемещаться по напольному рельсовому пути.
По способу опирания на рельсовый путь краны-штабелеры бывают опорными или подвесными (рис. 4 и 5). Это деление является условным. Подвесной кран-штабелер подвешен к ходовым тележкам.
Рис. 3. Краны-штабелеры: а – мостовой; б – стеллажный
Рис. 4. Краны-штабелеры мостового типа: а – опорный ; б — подвесной
Грузоподъемность кранов-штабелеров обычно не превышает 5 т но находят применение краны-штабелеры грузоподъемностью более 10 т.
Высота подъема отечественных кранов составляет 10 м. Скорость подъема 8—12 ммин. Скорость передвижения моста 50 ммин (при управлении с пола только 36 ммин) скорость передвижения тележки 12—20 ммин. Частота вращения колонны 4 обмин. Одной из особенностей кранов-штабелеров по сравнению с обычными крюковыми кранами является точная остановка всех механизмов. Поэтому при достаточно высоких рабочих скоростях предусматривается возможность движения с пониженными (доводочными) скоростями. В отечественных кранах доводочные скорости: подъема 4 ммин передвижения моста 10 ммин передвижения тележки 5 ммин.
Рис. 5. Стеллажные краны-штабелеры:
а -- подвесной; б — опорный велосипедного типа; в — опорный с опорой на стеллажи
Обзор существующих конструкций кранов-штабелеров
Стеллажные краны-штабелеры представляют собой широкую группу кранов-штабелеров которые могут устанавливать грузы в один стеллаж расположенный вдоль крановых путей или в два стеллажа расположенные по обе стороны крановых путей. Стеллажным называется кран-штабелер с вертикальной колонной перемещающейся в проходе между стеллажами.
Стеллажные краны-штабелеры являются наиболее эффективным складским оборудованием и интерес к ним проявляемый со стороны потребителей и поставщиков предопределил интенсивное развитие производства этих кранов-штабелеров.
Краны-штабелеры грузоподъемностью 1 т. представляют собой двухколонную раму передвигающуюся по подвесному пути укрепленному на стеллажах. По раме вертикально перемещается грузоподъемник. В нижней части рамы установлены ролики которые катятся по направляющим рельсам и удерживают кран-штабелер в вертикальном положении. Рама подвешена на двух приводных каретках. Каждая каретка имеет два электродвигателя мощностью 018 и 08 кВт оборудованных электромагнитными тормозами дифференциальный редуктор и две пары ходовых колес причем одна пара – приводная.
Приводные каретки сообщают крану-штабелеру скорость 60 ммин при одновременной работе двух электродвигателей и скорость 10 ммин при работе одного (малого) электродвигателя. На верхней балке рамы установлен привод механизма подъема состоящий из электротали оборудованной двухскоростным электродвигателем мощностью 50 кВт.
Грузоподъемник движется вдоль рамы крана-штабелера по направляющим рельсам с помощью четырех пар роликов охватывающих эти рельсы. На верхней поперечной балке грузоподъемника установлен подпружиненный канатный блок соединенный тягами с клиновыми ловителями охватывающими направляющие рельсы. При обрыве несущего каната или поломке механизма подъема происходит заклинивание ловителей и посадка грузоподъемника на раму крана.
Кабины кранов-штабелеров изготовляли двух исполнений: полуоткрытой применяемой в отапливаемых складах с температурой не ниже +50 и закрытой используемой в не отапливаемых складах. Закрытая кабина имела теплоизоляцию и была оборудована приборами отопления.
Конструкция описанного крана-штабелера характерна для всех подвесных кранов-штабелеров. Преимущества их предопределившие достаточно широкое применение заключались в следующем: простая и технологичная конструкция рамы; удобство установки и крепления ходовых механизмов и механизма подъема; возможность использования узлов и механизмов монорельсового транспорта.
Однако длительная эксплуатация стеллажных подвесных кранов-штабелеров различных конструкций изготовленных многими фирмами выявила ряд общих для них недостатков:
во-первых интенсивное изнашивание ходовых колес и монорельсовых путей особенно при увеличившихся до 100-120 ммин скоростях передвижения;
во-вторых значительное недоиспользование высоты склада обусловленное необходимостью разместить под монорельсом верхнюю несущую балку рамы привод механизма подъема и другие механизмы;
в-третьих неудобство эксплуатации связано с размещением основных механизмов в верхней части крана-штабелера и трудностью доступа к ним обслуживающего персонала.
В связи с этим выпуск подвесных стеллажных кранов-штабелеров был прекращен. Их заменили более совершенными опорными.
Рис.2. Одноколонный стеллажный кран-штабелер передвигающийся по рельсовым путям уложенным на стеллажи:
– телескопические захваты; 2 – грузоподъемник; 3 – кабина; 4 – колонна; 5 – тележка крана; 6 – привод передвижения; 7 – привод подъема; 8 – рельсы передаточной тележки; 9 – передаточная тележка; 10 – крановый рельс; 11 – стеллаж; 12 – направляющие рельсы.
Как одно из направлений в дальнейшем развитии конструкции стеллажных кранов-штабелеров можно рассматривать появление кранов-штабелеров опирающихся на рельсы уложенные в стеллажи. Например одноколонный кран-штабелер (рис.2.). Рельсы для него укладывают на верхние планки стеллажей и крепят к ним болтами. При этом должна быть обеспечена высокая точность их монтажа ( отклонение – не более 2мм). Колея рельсовых путей в зависимости от размеров перерабатываемого груза и прохода между стеллажами составляет 15 – 25 м. По крановым рельсам передвигается тележка крана-штабелера несущая на себе основные механизмы: приводы подъема и передвижения шкаф с электроаппаратурой. К тележке крепят колонну или сплошного сечения ( на кранах-штабелерах малой грузоподъемности) или решетчатую (на кранах-штабелерах большой грузоподъемности).
Опирающиеся на стеллаж краны-штабелеры имеют лучшие чем подвесные краны-штабалеры условия работы благодаря катанию ходовых колес по крановым рельсам а также возможности увеличить их диаметры. Однако их конструкции присущи серьезные недостатки:
во-первых это верхнее расположение механизмов (недостаток подвесных кранов-штабелеров)
во-вторых - высокие требования предъявляемые к монтажу направляющих путей.
Действительно при большой высоте подъема груза небольшая разность установки крановых путей по вертикали приводит к значительному отклонению нижнего конца колонны от среднего положения. При установке направляющего пути в этом случае могут появляться нежелательные нагрузки от перекоса металлоконструкции крана-штабелера.
Основным преимуществом опирающихся на стеллажах кранов-штабелеров является относительно простая конструкция передаточных тележек которые предназначены для перемещения кранов-штабелеров из одного межстеллажного прохода в другой.
Передаточные тележки обычно изготовляют в виде четырехколесной платформы перемещающейся по двум рельсам проходящим поперек фронта стеллажей под перекрытием склада. Один из рельсов устанавливают на стеллаж а другой крепят непосредственно к перекрытию склада. На передаточных тележках направляющие рельсы не предусматривают так как возможный перекос колонны крана-штабелера установленного на тележке не имеет существенного значения. От рамы тележки вниз опускаются короткие кронштейны несущие участок крановых путей который стыкуется с крановыми путями расположенными на стеллажах.
Передаточная тележка с краном-штабелером грузоподъемностью 1 т. изготовлена в виде сварной рамы передвигающейся по двум крановым путям один из которых установлен на стеллажах другой на специальных металлоконструкциях. Рама тележки несет на себе участок крановых рельсов для передвижения крана-штабелера оканчивающихся стыковыми замками запирающими кран-штабелер при передвижении на передаточной тележке.
В настоящее время большинство фирм перешло к выпуску стеллажных кранов-штабелеров перемещающихся по одному крановому пути установленному на полу склада. В верхней части кранов-штабелеров устанавливают направляющие ролики которые перемещаются по направляющему пути и удерживают кран-штабелер в вертикальном положении. Опорные (на пол) стеллажные краны-штабелеры по компоновке представляют собой одноколонную или двухколонную конструкцию имеющую нижнюю ходовую балку с двумя безребордными колесами одно из которых – приводное. К балке крепят одну или две вертикальные колонны заканчивающиеся направляющими роликами охватывающими с двух сторон направляющий путь углового или чаще двутаврового профиля. При двух колоннах краны-штабелеры имеют в верхней части продольную балку которая связывает их и образует таким образом замкнутую прямоугольную конструкцию. На нижней балке или на нижней части колонны устанавливают канатный или цепной механизм подъема с помощью которого осуществляется вертикальное перемещение грузоподъемника совместно с кабиной оператора. Подобная конструкция ставшая классической имеет несомненные преимущества перед описанными выше подвесными и опирающимися на стеллаж кранами-штабелерами.
При перемещении крана-штабелера по специальному крановому рельсу с помощью двух безребордных колес оборудованных горизонтальными роликами катящимися по боковым граням рельса изнашивание как ходовой части крана-штабелера так и рельса в том числе и при высоких (120 – 160 ммин) скоростях перемещения минимально. Причем возможно применение ходовых колес достаточно большого диаметра что в свою очередь позволяет уменьшить сопротивление перемещению и улучшить энергетические показатели механизма передвижения. При расположении в нижней части крана-штабелера всех механизмов и электрооборудования улучшаются условия доступа к этим механизмам при эксплуатации. Крановый путь установленный на полу склада (в межстеллажном проходе) позволяет создать более благоприятные условия для монтажа данного типа крана-штабелера (по сравнению с другими типами). чч Монтаж кранов-штабелеров сводится к установке на крановый путь опорной балки со смонтированными на ней механизмами и установке на эту балку колонны с помощью стрелового автомобильного крана или с помощью электрической или ручной тали подвешиваемой к направляющему пути.
Однако главным преимуществом опирающихся на пол стеллажных кранов-штабелеров является более высокая степень использования высоты помещения чем при применении стеллажных подвесных и опирающихся на стеллаж кранов-штабелеров достигающая своего максимального значения в одноколонных кранах-штабелерах.
Претерпели значительное изменение и некоторые узлы кранов-штабелеров среди которых прежде всего следует отметить грузозахватные устройства. На первых конструкциях стеллажных кранов-штабелеров преимущественно использовали роликовые столы с помощью которых пакетированные грузы устанавливались на кран-штабелер и в стеллаж а также выдвижные и поворотные вилочные захваты. Применение кранов-штабелеров с роликовыми столами на складах с интенсивной работой оказалось неприемлемым прежде всего в результате тяжелых условий труда операторов.
Применение выдвижных (и поворотных) вилочных захватов подобных используемым на автопогрузчиках позволило полностью исключить ручной труд при пакетной переработке груза. Однако это влечет за собой увеличение прохода между стеллажами так как необходимо оставлять определенное место для крепления вилочных захватов. Поэтому получили распространение выдвижные телескопические захваты технологически более сложные чем вилочные но позволяющие создать проход между стеллажами минимальной ширины равной практически сумме ширины перерабатываемого груза и зазоров (по 50 – 100 мм на сторону) между грузом и стеллажом.
Телескопические захваты представляют собой три секции одинаковой длины из которых одна неподвижная а две другие подвижные. Причем секция которая несет на себе груз движется с увеличенной вдвое скоростью по отношению к промежуточной. Телескопические захваты могут выдвигаться в обе стороны поперек прохода.
Значительные изменения претерпела система управления кранов-штабелеров начиная от ручного управления оператором из кабины на первых кранах-штабелерах и кончая полностью автоматизированным управлением применяемым на стеллажных кранах-штабелерах последних поколений. Изменился принципиальный подход к конструированию приводных механизмов. Переход от ручного к автоматическому управлению и возросшие скорости перемещения обусловили переход от применения асинхронных электродвигателей к электродвигателям постоянного и переменного тока с тиристорным регулированием скорости а также к электродвигателям с микроприводом. Более широко стали применяться редукторы специально предназначенные для использования на кранах-штабелерах вместо редукторов общепромышленного применения.
Изменения в конструкции кабин операторов направлены в основном на улучшение условий труда создание комфортных условий и обеспечение безопасности в работе.
В настоящее время стеллажные краны-штабелеры являются высокопроизводительным надежным оборудованием которое отличает отработанность конструкции ее высокая технологичность тщательность отделки. Таким образом поиски наиболее оптимальных конструктивных решений завершились созданием современных стеллажных кранов-штабелеров имеющих много общего в конструкции но отличающихся один от другого техническим исполнением отдельных узлов деталей систем управления. Можно сделать предположение что дальнейшие конструктивные поиски будут направлены в основном на повышение надежности технологичности расширение функциональных возможностей системы управления.
Стеллажные краны-штабелеры изготовляют в настоящее время в различных странах. Конструктивные их решения обусловлены традициями технологическими возможностями наличием освоенного производства узлов подъемно-транспортных машин систем управления. В принципе компоновки стеллажных кранов-штабелеров однотипны.
Современный стеллажный кран-штабелер выполнен в виде нижней ходовой балки оборудованной двумя безребордными колесами к которой крепят одну или две колонны имеющие сверху горизонтально расположенные направляющие ролики. Если устанавливают две колонны то верхние их концы соединяют горизонтальной балкой. По колонне с помощью канатного или реже цепного привода механизма подъема перемещается консольно установленный грузоподъемник несущий кабину управления и выдвижной телескопический захват. На стеллажных кранах-штабелерах предназначенных для поштучного отбора грузов так называемых комплектовочных кранах-штабелерах вместо выдвижных телескопических захватов можно устанавливать гладкие или роликовые столы а также другие приспособления для укладки в стеллажи и отбора из стеллажей грузов.
Одноколонный стеллажный кран-штабелер имеет нижнюю ходовую балку на которой установлены приводное и холостое колеса. К балке крепят колонну на верхней части которой установлены горизонтальные ролики удерживающие кран-штабелер в вертикальном положении.
По колонне перемещается консольный грузоподъемник с кабиной оператора. Кабина оператора имеет небольшой свободный ход относительно грузоподъемника для того чтобы полностью использовать высоту склада. На два телескопических захвата грузоподъемника устанавливается груз. грузоподъемник по колонне перемещается с помощью канатного механизма подъема . шкаф с электрооборудованием соединен с колонной кронштейном.
Двухколонные стеллажные краны-штабелеры применяют при больших высоте подъема и грузоподъемности. Кран-штабелер имеет нижнюю опорную балку на которой установлены приводное и холостое колеса. К опорной балке крепят две колонны и соединенные верхними концами продольной балки. На этой балке установлены две пары горизонтальных роликов и механизм синхронизации применяемый для уменьшения амплитуды перемещения верхней части колонны относительно ее нижней части.
Между колонн перемещается грузоподъемник представляющий собой платформу с двух сторон оборудованную каретками ролики которых обкатываются по направляющим колонн. На грузоподъемнике установлена кабина оператора и выдвижные телескопические захваты служащие для установки в стеллажи пакетированного груза. грузоподъемник поднимается с помощью канатного механизма подъема который установлен на одной колонне а на второй – шкаф с электрооборудованием. Для обслуживания механизма подъема и механизма синхронизации на одной из колонн крепят рабочие площадки к которым по лестнице поднимается обслуживающий персонал.
Сравнивая схемы этих кранов нетрудно увидеть что использование полезной высоты склада при применении двухколонных кранов-штабелеров хуже чем в одноколонных. Во-первых из-за наличия верхней балки соединяющей колонны и во-вторых из-за того что кабина не может вертикально перемещаться относительно грузоподъемника.
Одноколонную или двухколонную схему крана-штабелера выбирают прежде всего из условий обеспечения фиксированного положения груза на грузоподъемнике. При выдвижении груза инерционные силы приводят к поперечному перемещению рамы грузоподъемника в результате зазоров направляющих роликов грузоподъемника и закручивания колонн в поперечной плоскости. Очевидно что это поперечное перемещение консольного грузоподъемника существенно больше чем перемещение грузоподъемника имеющего направляющие ролики расположенные с обеих сторон по направлению движения крана-штабелера. Поэтому при грузах массой более 2 т при грузах длина которых более 2 – 25 м и при большой высоте подъема (свыше 20 м) применяют двухколонные краны-штабелеры.
Одноколонные краны-штабелеры по сравнению с двухколонными имеют минимальные собственные массу и размеры; позволяют лучше использовать высоту помещения и более удобны при монтаже. Недостатками одноколонных стеллажных кранов-штабелеров являются относительно большое поперечное перемещение грузоподъемника и увеличенные нагрузки на направляющие катки грузоподъемника в результате его консольного расположения и как следствие этого - большой износ катков и направляющих колонны.
Эти недостатки не оказывают существенного влияния при грузоподъемности кранов-штабелеров до 20 – 25 т. Однако при грузоподъемности свыше 2 т и при больших (свыше 25 м) размерах груза устранение этих отрицательных влияний путем увеличения прочности и жесткости металлоконструкций увеличения диаметров направляющих катков грузоподъемника и расстояния между ними приводит к неоправданному увеличению массы и размеров крана-штабелера. В этих случаях предпочтение следует отдать двухколонной схеме при которой кран-штабелер работает в значительно более благоприятных условиях.
1.1.Механизм подъема
Механизмы подъема стеллажных кранов-штабелеров принципиально мало отличаются от соответствующих механизмов других грузоподъемных машин. В подавляющем большинстве на стеллажных кранах-штабелерах применяют канатные механизмы подъема. Механизм подъема как правило состоит из электродвигателя тормоза редуктора и канатного барабана. Эти механизмы имеют определенные ширину ограниченную шириной межстеллажного прохода и длину непосредственно зависящую от длины крана-штабелера. Поэтому наибольшее распространение получила вертикальная компоновка механизма подъема. Основой механизма является вертикальный конусно-цилиндрический редуктор который крепят к задней стенке колонны. Канатные барабаны устанавливают или на двух концах выходного вала по обе стороны редуктора (в этом случае используют канат без полиспаста) или на одном конце вала тогда груз поднимают с помощью полиспаста а свободный конец каната через блоки крепят к ограничителю грузоподъемности. На редуктор сверху помещают фланцевый вертикальный электродвигатель. Тормоз устанавливают на тормозной муфте соединяющей редуктор с электродвигателем.
Стеллажные краны-штабелеры могут иметь иную компоновку механизма подъема. На них используют стандартные червячные или цилиндрические крановые редукторы и тормозы вертикального исполнения. Редуктор и электродвигатель установлены горизонтально по продольной оси крана-штабелера. Канатный барабан установлен или на выходном валу редуктора или соединен с редуктором зубчатой передачей. Длина подобного механизма больше чем механизма при вертикальной компоновке. Однако на размерах крана-штабелера такая компоновка механизма подъема не сказывается так как его встраивают внутрь решетчатой колонны.
Описанная компоновка механизма подъема выгодна тем что при ее использовании не требуются специальные конусно-цилиндрические редукторы стоимость которых больше чем червячных или цилиндрических.
1.2.Механизм передвижения
Механизм передвижения принципиально не отличается от механизмов передвижения других грузоподъемных устройств. Они состоят из электродвигателя тормоза и редуктора соединенного с ходовым колесом. Подобно механизмам подъема механизмы передвижения как правило имеют вертикальную компоновку. Механизмы передвижения большинства зарубежных фирм выполнены в виде вертикального конусноцилиндрического или червячного редуктора установленного на валу приводного колеса или соединяемого с ним открытой зубчатой передачей. На редукторы вертикально устанавливают фланцевые электродвигатели со встроенным тормозом. Широко применяют электродвигатели с микроприводом обеспечивающие большой диапазон регулирования скоростей при постоянном крутящем моменте.
На многих типах кранов-штабелеров в том числе на стеллажных кранах-штабелерах отечественного производства механизм передвижения выполнен в виде вертикального цилиндрического редуктора с полым выходным валом насаженного на вал приводного колеса. Выходной вал редуктора соединен с электродвигателем с помощью тормозной муфты. Электродвигатель расположен горизонтально над ходовой балкой крана-штабелера. Такая компоновка более эффективна так как этот механизм лучше вписывается в габариты крана. С целью сокращения длины кранов-штабелеров механизм подъема как правило расположен над механизмом передвижения. При большой высоте механизма передвижения механизм подъема приходится устанавливать достаточно высоко что усложняет его обслуживание.
Механизм передвижения всегда выполняют на одном из ходовых колес расположенном для двухколонных кранов-штабелеров со стороны более нагруженной колонны и для одноколонных – со стороны колонны.
1.3.Телескопический захват
Выдвижные телескопические захваты разного конструктивного исполнения в настоящее время применяют на всех стеллажных кранах-штабелерах предназначенных для пакетной переработки грузов.
Телескопические захваты независимо от конструктивного исполнения выполнены по единой схеме. Они обычно состоят из трех секций: неподвижной промежуточной и выдвижной. Последняя служит опорной площадкой для установки груза. Она расположена несколько выше остальных секций чтобы при выдвижении груз не задевал за неподвижную и промежуточную секции. Промежуточная секция имеет ролики благодаря которым она может передвигаться по направляющим неподвижной секции. В свою очередь выдвижная секция с помощью роликов движется по промежуточной секции. Ширина всех секций одинакова и равна максимальной ширине перевозимого груза.
Рис.2.2. Схемы выдвижных телескопических захватов с расположением секций:
а – вертикальным; б – горизонтальным
Промежуточная секция выдвигается примерно на половину ее длины; выдвижная секция выступает из промежуточной на ту же величину. Обе секции выдвигаются одновременно с помощью привода. Захват может выдвигаться в обе стороны прохода. Таким образом взятый из загрузочного устройства груз может быть установлен в любую сторону без какого-либо поворота грузового захвата. Благодаря этому ширина прохода между стеллажами может быть снижена до минимального размера определяемого шириной перевозимого груза с учетом необходимых зазоров между грузом и стеллажами (от 50 до 100 мм на сторону).
Выдвижной телескопический захват с вертикальным расположением секций (рис. 2.2 а) состоит из выдвижной площадки 3 с закрепленной на ней роликовых батарей 5 и 6 промежуточной секции 2 неподвижных роликовых батарей 1 и 7 и приводного вала с шестернями 8. на верхней выдвижной площадке 3 промежуточной секции 2 и на неподвижной секции закреплены зубчатые рейки 4 длина которых равна длине секции.
Работа телескопического захвата происходит следующим образом. При вращении вала 8 установленные на нем шестерни входящие в зацепление с рейками на средней секции 2 сообщают средней секции некоторую скорость. На оси закрепленной в средней секции свободно вращается шестерня входящая в зацепление одновременно с рейкой закрепленной на неподвижной секции и с рейкой закрепленной на верхней выдвижной площадке. При перемещении средней секции со скоростью v1 шестерня входящая в зацепление с неподвижной рейкой сообщает верхней секции скорость v2 = 2*v1. Таким образом при включении привода захвата одновременно перемещаются на одинаковую величину: средняя секция по неподвижной со скоростью выдвижная площадка по средней секции с удвоенной скоростью v2.
После взятия груза привод захвата переключает и обе секции одновременно перемещаются и приходят в среднее положение. Выдвижной телескопический захват (рис.2.2.б) другого типа имеет горизонтальное расположение секций. На неподвижной секции его установленной на грузоподъемнике крепят ролики 9 по которым перемещается промежуточная секция 2 с роликами 8 служащими для передвижения выдвижной площадки 3. На валу промежуточного элемента смонтирована шестерня входящая одновременно в зацепление с зубчатой рейкой закрепленной на неподвижной секции захвата.
Привод захвата состоит из электродвигателя редуктора и тормоза. На выходном валу редуктора размещена шестерня входящая в зацепление с шестерней приводного вала захвата имеющего также две шестерни 10 сопряженные с зубчатыми рейками установленными на промежуточной секции захвата.
Работает захват таким образом. При включении привода шестерни посредством зубчатых реек сообщают поступательное движение промежуточной секции 2. Шестерня промежуточной секции движущаяся вместе с ней входит в зацепление с неподвижной зубчатой рейкой и передает движение с удвоенной скоростью зубчатой рейке установленной на выдвижной площадке захвата. Промежуточный и выдвижной элементы захвата движутся одновременно но выдвижной элемент перемещается вдвое быстрее первого.
Захваты с горизонтальным расположением секций имеют меньшую высоту что позволяет лучше использовать вместимость склада. К недостаткам следует отнести сложность конструкции и относительно высокую ее стоимость.
1.4.Система управления
Рабочие скорости механизмов – подъема передвижения выдвижения телескопических захватов достаточно высоки. Работа механизмов при таких скоростях возможна только при большом диапазоне регулирования скоростей механизмов. Для остановки крана-штабелера (грузоподъемника) точно против требуемой ячейки (позиционирование) необходимо чтобы кран-штабелер и грузоподъемник подходили к ячейке на низких установочных скоростях. При ручном управлении эти скорости не должны превышать 6 – 8 ммин при автоматическом –2 – 4 ммин. При этих скоростях можно с точностью до нескольких миллиметров останавливать соответствующий механизм. Для приводов подъема и передвижения наиболее часто применяют тиристорные преобразователи постоянного или переменного тока. За рубежом находят применение специальные электродвигатели с микроприводами позволяющие получить низкие установочные скорости (08 – 12 ммин) при сохранении необходимого крутящего момента. Эти приводы значительно дороже чем приводы с обычными электродвигателями однако позволяют достигать высокой точности позиционирования.
Краны-штабелеры оборудованы тиристорными преобразователями и электродвигателями постоянного тока с диапазоном регулирования 50 : 1. недостатком применения тиристорных приводов является уменьшение крутящего момента на валу электродвигателя (приводного колеса) и отсюда – повышение требований к качеству монтажа кранового пути.
Краны-штабелеры с относительно низкими скоростями механизмов (подъема – 8 – 12 ммин передвижения – 60 – 80 ммин) с ручным управлением оборудуют двух или многоскоростными асинхронными электродвигателями. Стоимость таких приводов значительно меньше стоимости тиристорных приводов равно как и стоимость обслуживания и ремонта. Двухскоростные электродвигатели с соотношением скоростей 8:1 широко применяют на стеллажных кранах-штабелерах производства НРБ.
Анализ расчета кранов-штабелеров.
1.Назначение специфика и нормативные основы
Все вновь проектируемые или модернизируемые краны-штабелеры подвергаются тщательному расчету. Оформленный расчет является обязательным документом технического проекта крана-штабелера; расчеты элементов или узлов размеры которых становятся известными на стадии рабочего проектирования или корректируются по результатам испытаний опытного образца оформляют затем в виде дополнительных частей или разделов.
Такое внимание к расчетам обусловлено тем что краны-штабелеры являются объектами повышенной ответственности. Прежде всего кран-штабелер – это подъемно-транспортная машина разрушение или повреждение которой представляет опасность для жизни обслуживающего персонала. Во-вторых кран-штабелер в большинстве случаев является единственным средством доступа к грузам находящимся в обслуживаемом им хранилище. Поэтому даже рядовые отказы крана-штабелера нарушают работу склада что особенно чувствительно для складов интенсивных производств и технологических линий.
Таким образом основным назначением расчетов является проверка безопасности и надежности крана-штабелера в работе.
Безопасность крана-штабелера должна быть проверена также и для процесса его испытаний поскольку этот процесс характеризуется увеличенной массой применяемых грузов повышенной вероятностью возникновения отказов искусственным созданием отказов некоторых видов а также значительной численностью персонала испытателей безопасность которых должна быть гарантирована.
Другим назначением расчетов является проверка соответствия технических параметров проекта крана-штабелера требованиям технического задания и нормативно-технических документов. Некоторые из перечисленных параметров например расчетный ресурс запасы прочности жесткость элементов конструкции крана-штабелера имеют прямое отношение к вопросам безопасности и надежности крана-штабелера. Другие параметры – скорость ускорения и замедления обеспечиваемые механизмами характеризуют производительность крана-штабелера.
Очевидно что сравнение различных образцов кранов-штабелеров может быть правильно выполнено только в том случае если расчеты выполнены по одной и той же методике на основании одинаковых нормативов. Этим определяется первая предпосылка необходимости стандартизации норм расчета кранов-штабелеров. Другая и не менее важная предпосылка вытекает из самой ответственности разработки стандарта как официального и обязательного документа; из широкой гласности при обсуждении проекта стандарта заинтересованными и специализированными организациями в результате чего стандарт как правило отражает передовой научный технический и проектно-конструкторский опыт.
В результате специального изучения условий эксплуатации и нормирования расчетов кранов-штабелеров разработаны и введены в действие ОСТ 24.090.68-82 «Краны-штабелеры стеллажные. Нормы расчета» и ОСТ 24.091.14-85 «Краны-штабелеры мостовые. Нормы расчета». Излагаемые ниже основные положения расчета кранов-штабелеров даны в полном соответствии с упомянутыми стандартами.
Оба стандарта предназначаются для кранов-штабелеров по ГОСТ 16553-82. однако основные принципы и нормы расчета этих стандартов могут быть использованы для кранов-штабелеров других типов и параметров например для подвесных мостовых и стеллажных кранов-штабелеров для кранов-штабелеров с облегченным режимом работы. Для того чтобы конструктор мог в таких случаях самостоятельно внести в нормативы необходимые изменения здесь даются пояснения о происхождении тех или иных нормативных требований.
Наконец следует сказать что отчетный расчет как документ проекта представляет собой итоговую часть расчетной работы которой предшествует большое число предварительных и вариантных расчетов. Последние особенно важны так как представляют собой в большинстве случаев единственный инструмент для получения конструкции необходимого технического уровня. Вариантные расчеты в настоящее время с успехом выполняются на ЭВМ принимая форму так называемых оптимизационных расчетов. В качестве критерия оптимизации для крана-штабелера обычно выбирают его массу которую следует минимизировать. Возможно применение и стоимостного или смешанного критерия.
Известно что для расчетов с помощью ЭВМ необходима четкая формализация расчетных схем и требований. И в этом отношении стандартизованные нормы расчета кранов-штабелеров дают необходимый материал.
Исходные данные для предварительных расчетов принимают в соответствии с техническим заданием и схемами предварительных конструктивных проработок крана-штабелера. Исходные данные оформляемого расчета должны полностью соответствовать параметрам указанным в конструкторской и эксплуатационной документации на кран-штабелер; отдельные несоответствия должны оговариваться в отношении их причин и следствий.
В конструкции крана-штабелера обычно используют материалы и комплектующие изделия выпускаемые промышленностью для общего потребления. К ним относятся металлический прокат электродвигатели стандартные редукторы подшипники муфты тормоза и т.п. Их технические параметры приводимые в сортаментах и каталогах также являются исходными данными для расчета в результате которого должны быть выявлены минимально необходимые типоразмеры материалов и комплектующих изделий (с учетом возможностей поставки которые учитываются в расчете как ограничители сортаментов).
Желательно чтобы полученные расчетом скорости механизмов крана-штабелера составляли от 09 до 11 их номинальных значений. Следует отметить что согласно ГОСТ 16553-82 допускаемое отклонение фактических скоростей от номинальных составляет 15%. Сужать поле допуска расчетных скоростей целесообразно для компенсации возможного расхождения расчетных и фактических скоростей.
Расчетное ускорение (замедление) обеспечиваемое механизмом передвижения крана-штабелера должно составлять 03 – 06 мс2. Это объясняется тем что при ускорениях (замедлениях) меньших чем 03 мс2 процессы разгона или торможения чрезмерно затягиваются. Например при ускорении 02 мс2 и номинальной скорости 20 мс разгон будет длиться 10 с; увеличение ускорения до 04 мс2 сокращает время разгона до 5 с а общая экономия времени за цикл работы крана-штабелера составит 20 с что равносильно увеличению производительности крана-штабелера не менее чем на 20%. Ускорение большее чем 06 мс2 во многих случаях недостижимо по условию необходимого запаса сцепления приводных колес с рельсами. Однако и тогда когда имеется избыточный запас сцепления (например у кранов-штабелеров с малой высотой подъема) увеличение ускорения свыше 06 мс2 нецелесообразно: увеличение производительности получается несущественным а габарит электродвигателя может возрасти так как требуется повышенный пусковой момент.
Расчетное ускорение грузозахватного органа должно быть не более 10 мс2. ускорения большие чем указанное не применяют потому что скорость подъема обычно не превышает 05 мс и сокращать время разгона по сравнению с величиной 05 с не только не имеет смысла но и невыгодно во всех отношениях.
Нижняя граница ускорения при подъеме не регламентируется. Дело в том что электродвигатель механизма подъема подбирают таким образом чтобы требуемый момент установившегося движения на валу электродвигателя был близок к его номинальному моменту. Пусковой момент электродвигателя в 2 – 3 раза больше номинального поэтому ускорение разгона обычно получается не менее 04 – 05 мс2 что вполне приемлемо так как время разгона не превышает 10 – 15 с.
Верхняя граница замедления торможения при опускании грузозахватного органа также равна 10 мс2 а нижняя не ограничивается по причинам аналогичным вышеизложенным так как основной процесс торможения обеспечивается электродвигателем.
Расчетное ускорение (замедление) при выдвижении телескопических захватов должно быть не более 10 мс2. Такое ограничение необходимо для предотвращения смещения груза относительно захвата под действием инерционных сил. Поэтому указанное ограничение проверяется для случаев пуска и торможения захвата на котором установлена порожняя тара так как при этом ускорение (замедление) получается наибольшим. Вследствие того что скорость выдвижения захватов сравнительно невелика (до 025 мс) инерционная доля массы порожней тары в приведенном моменте инерции привода захвата также невелика и можно рассчитывать ускорение для захвата без груза. Этим объясняется то что в ОСТ 24.090.68-82 не оговаривается для какого случая нагружения захватов следует проверять ускорение поскольку очевидно что наибольшее его значение будет в случае порожних захватов.
Нижний предел расчетного ускорения (замедления) захвотов не регламентируется ввиду того что скорость выдвижения как уже отмечалось сравнительно невелика и время разгона практически никогда не превышает 1 с даже в наиболее тяжелом случае – при взятии номинального груза из ячейки стеллажа.
Расчетный срок службы кранов-штабелеров принимается равным 20 годам при односменной работе. В течение этого срока металлоконструкции кранов-штабелеров должны проработать безотказно и такое требование практически выполнимо.
Календарный срок службы крана-штабелера и его узлов удобен для эксплуатационника. Между этой величиной и долговечностью существует определенная связь зависящая от продолжительности цикла крана-штабелера и от соотношения продолжительностей включения различных механизмов в течение цикла.
При индивидуальном проектировании крана-штабелера предназначенного для склада с определенными заданными параметрами – длиной высотой числом ячеек грузооборотом - характеристики цикла можно определить однозначно путем их осреднения по складу с учетом принятых приоритетов загрузки и выгрузки.
Для крана-штабелера серийного производства условия работы заранее не известны. Поэтому приходится задаваться некоторым условным складом параметры которого были бы представительны по частоте практической применяемости и создавали бы в то же время достаточно напряженный режим работы крана-штабелера. При этом для определения характеристики цикла стеллажного крана-штабелера практически достаточно задаться длиной склада. Для мостового крана-штабелера существует некоторое множество пар значений длины и ширины склада при которых может быть обеспечен заданный грузооборот. Этому множеству соответствует множество возможных циклов из которых следует выбрать наиболее характерные принимаемые в качестве нормативных.
Такая работа выполнена при разработке ОСТ 24.090.68-82 и ОСТ 24.091.14-85. Отметим что выбор нормативного цикла работы крана-штабелера позволяет помимо ресурса установить и другие важные характеристики режима работы механизмов крана-штабелера. К ним относятся число включений в час и продолжительность включения (ПВ %) необходимые для выбора электродвигателей.
К ним также относятся циклограммы работы механизмов показывающие изменение нагрузки механизмов в течение цикла и необходимые для расчета всех звеньев механизмов в том числе и электродвигателей. Для получения циклограмм приходится рассматривать процессы установившегося движения а также разгона и торможения механизмов и кроме того учитывать статистическую изменчивость массы складируемых грузов.
Методической основой для установления расчетных характеристик режима работы механизмов является ГОСТ 25835-83 «Краны грузоподъемные. Классификация механизмов по режимам работы» а также стандартные значения ПВ и числа включений в час применяемые в отечественной промышленности.
Согласно ГОСТ 25835-83 найденные с помощью нормативного цикла значения чистого времени работы каждого из механизмов за срок службы округляются до стандартных ближайших значений. Таким образом устанавливается класс использования механизма по времени. По циклограммам работы механизмов вычисляют коэффициент нагружения равный сумме произведений относительной длительности нагрузки на куб относительной нагрузки взятой по всем элементарным прямоугольникам циклограммы. По коэффициенту нагружения устанавливают класс нагружения который в сочетании с классом использования определяет группу режима работы механизма крана-штабелера.
Как показали исследования для стеллажных кранов-штабелеров по ГОСТ 16553-82 все механизмы должны быть отнесены к группе режима работы 5М по ГОСТ 25835-83 что соответствует тяжелому режиму работы по классификации Госгортехнадзора.
Элементы механизмов должны быть проверены на прочность по наибольшим нагрузкам пусковых и тормозных режимов а также на выносливость с учетом требуемого ресурса и циклограмм нагружения элементов получаемых путем образмеривания исходных циклограмм по данным о величинах нагрузки передаточных чисел и коэффициентов полезного действия звеньев передачи.
При этом расчет цилиндрических эвольвентных зубчатых передач внешнего зацепления следует выполнять по ГОСТ 21354-75 подшипников качения – по ГОСТ 18854-82 и ГОСТ 18855-82. ходовые колеса кранов-штабелеров следует проверять по ОСТ 24.090.44-82 «Колеса крановые. Выбор и расчет» с учетом изложенных ниже рекомендаций. Для расчета поворотных опор колонн мостовых кранов-штабелеров следует применять ОСТ 22-1401-79 «Опоры поворотные роликовые однорядные с зубьями внутреннего зацепления». Прочие элементы механизмов рекомендуется рассчитывать по соответствующим РТМ ВНИИПТмаша. Для стандартных редукторов подлежащих согласованию следует применять РТМ 2-056-80 «Редукторы общего назначения. Методика выбора редукторов и моторов-редукторов».
Электродвигатели механизмов должны быть проверены по наибольшим нагрузкам пусковых и тормозных режимов а также на нагрев с учетом их расчетных характеристик и соответствующих циклограмм.
При расчете металлоконструкций кранов-штабелеров проверяют прочность устойчивость жесткость и выносливость конструкций в целом и их отдельных элементов. Для стеллажных кранов-штабелеров выполняют также расчет затухания колебаний колонны при остановке крана-штабелера.
Стальные конструкции рассчитывают по методике СНиП II-23-81 «Нормы проектирования. Стальные конструкции» а алюминиевые конструкции – по методике СНиП II-24-74 «Нормы проектирования. Алюминиевые конструкции» с учетом излагаемых здесь специфических требований.
При формировании исходных данных для расчета следует убедиться что принятые в проекте крана-штабелера материалы металлоконструкций и сварочные материалы соответствуют требованиям обязательного РТМ 24.090.52-79 «Краны грузоподъемные. Материалы для сварных металлических конструкций» а примененные для болтовых соединений стальные болты гайки и шайбы соответствуют требованиям СНиП II-23-81. следует также проверить что кран-штабелер оборудован всеми устройствами безопасности в соответствии с требованиями ОСТ 24.090.38-83 и ОСТ 24.090.39-83.
В заключение следует указать что в расчетах выполняемых на группу исполнении крана-штабелера отличающихся пролетом высотой грузоподъемностью и скоростями механизмов должны быть рассмотрены все исполнения группы а не только исполнения с наибольшими характеристиками.
Краны-штабелеры рассчитанные в соответствии с настоящими рекомендациями могут быть использованы для эксплуатации в сейсмических районах без ограничений так как применяемые здесь экстремальные расчетные нагрузки превосходят наибольшие сейсмические нагрузки по СНиП II-7-81.
3.Расчет стеллажных кранов-штабелеров
Расчетные характеристики режима работы механизмов стеллажных кранов-штабелеров соответствующие ГОСТ 25835-83 приведены в табл.3.1
Значения показателя для механизма
Группа режима работы
Общее время работы тыс.ч
Коэффициент нагружения (стеллажных кранов-штабелеров)
Число включений в час
Продолжительность включения ПВ %
В расчетных циклограммах загрузки механизмов (рис.3.1) по оси абсцисс отложено относительное число циклов или относительная продолжительность действия нагрузки. Строго говоря число циклов нагрузки не пропорционально времени ее действия ввиду наличия периодов разгона и торможения и следовало бы давать отдельные циклограммы по числу циклов и по времени в качестве аргументов. Однако для механизмов подъема и выдвижения относительная продолжительность неустановившихся режимов движения всегда невелика – менее 3 %. Для механизма передвижения при нормировании режима работы принят стеллаж длиной 100 м. При этом средний путь передвижения крана-штабелера за простой цикл составит также 100 м. Можно показать что например при скорости передвижения 20 мс и ускорении (замедлении) 05 мс2 погрешность в вычислении числа циклов если не учитывать неустановившиеся режимы движения составит 8 % в сторону увеличения т.е. в запас. Такая погрешность находится в пределах точности исходных предпосылок поэтому и в данном случае достаточно ограничиваться одной циклограммой.
Рисунок 3.1. Расчетные циклограммы загрузки механизмов стеллажных кранов-штабелеров: а б в – соответственно передвижения подъема и выдвижения захватов
Переход к абсолютному времени для элементов рассчитываемых на полный срок службы крана-штабелера производится по общему времени работы (см. табл. 3). Для прочих элементов это время уменьшается в 2 раза или более.
Для нахождения полного числа циклов нагружения какого-либо элемента механизма необходимо общее время работы разделить на длительность одного цикла. Для вращающихся элементов – валов шестерен подшипников и т.д. – циклом является один оборот (особенности существуют только для планетарных редукторов). При этом частоту их вращения следует брать для установившегося режима движения. Например для вала механизма подъема вращающегося с частотой 1000 обмин и рассчитываемого на полный срок службы получим полное расчетное число циклов 1000*60*12500 = 75*108.
В расчетных циклограммах (см. рис. 3.1) по оси ординат отложена относительная нагрузка. Абсолютная величина наибольшей ординаты нагрузки для механизма передвижения соответствует моменту при разгоне с расчетным ускорением; для механизма подъема – моменту при установившемся движении подъема с номинальным грузом; для механизма выдвижения – при взятии номинального груза из ячейки стеллажа т.е. на наибольшем вылете захвата но без учета сил инерции.
При установлении характеристик режима работы (см. табл.3.1 и рис.3.1 ) рассматривали краны-штабелеры обслуживающие стеллажи длиной 100 м высотой 16 м и глубиной 12 м со скоростями передвижения от 16 до 25 мс подъема – 04 мс и выдвижения захватов – 02 мс. ускорения при разгоне механизмов принимали равным 04 мс2. Относительное число простых и сложных циклов 06 и 04 соответственно. Процесс подъема считали как совмещенный по времени с процессом передвижения. Изменчивость массы Q грузов оценивали по гистограмме (рис.3.1) полученной по результатам обследования действующих складов; средняя масса груза по этой гистограмме составляет 06 от номинальной Qном.
Рис.3.2 Расчетная гистограммараспределения массы брутто
складируемых грузов;ρ – плотность вероятности
Для расчета опорных одноколонных стеллажных кранов-штабелеров рекомендуется использовать схемы представленные на рис. 3.2
В кране-штабелере выделяют шесть укрупненных конструктивных узлов со следующей закрепленной за ними индексацией: ходовая балка 1 в сборе с установленным на ней механизмом передвижения и ходовыми колесами; механизм подъема 2 (включая канаты); колонна 3(или две колонны у двухколонных кранов-штабелеров рамной конструкции рис. 3.2; при шарнирно-сочлененной конструкции по рис. 3.3 правая и левая колонны и их ходовые балки должны рассматриваться отдельно дополнительным элементом является сцепка); оголовок колонны 4 в сборе с грузовыми блоками и боковыми роликами (или верхняя балка у двухколонных кранов-штабелеров); грузоподъемник 5 в сборе с каретками грузовыми подвесками и грузовыми захватами; кабина 6 (при определении ее массы учитывается масса оператора).
Шкаф электрооборудования относят к ходовой балке или к колонне в зависимости от того на чем он установлен.
Отдельным элементом является транспортируемый груз номинальная масса которого обозначена через Q.
Для каждого из этих узлов предварительно определяют номинальные значения масс m zi) в прямоугольной системе координат начало которой расположено в середине площадки контакта приводного ходового колеса с наземным крановым рельсом.
Для расчета металлоконструкций подготавливают геометрические характеристики сечений ходовой балки колонн верхней балки а также расчетные сопротивления и модуль упругости материала.
Рис. 3.3 Стержневые схемы конструкций двухколонных стеллажных кранов-штабелеров:
а – рамной; б – шарнирно-сочлененной; 1 1’ – ходовые балки; 2 – механизм подъема; 3 3’ – колонны; 4 – верхняя балка; 5 – рама грузоподъемника; К – каретка подъемника; ГК – грузовые канаты; С – сцепка
Сопротивление передвижению крана-штабелера определяется как сила необходимая для преодоления трения качения ходовых колес и подшипников умноженная на коэффициент 11 учитывающий трение в боковых роликах. Уклон пути не учитывается так как согласно ОСТ 24.090.39-83 уклон ограничен очень малой величиной – 0001.
Сопротивление передвижению необходимо знать для определения скорости ускорения и замедления крана-штабелера обеспечиваемых используемым электродвигателем и передаточным механизмом.
Однако методически удобней начинать расчет механизма передвижения с анализа запаса сцепления приводных колес а затем и устойчивости крана-штабелера в режимах разгона и торможения.
Физический смысл необходимости запаса сцепления – предотвращение пробуксовки приводного колеса приводящей к ускоренному изнашиванию колеса и рельса. Для крана-штабелера такое изнашивание особенно нежелательно так как помимо прочего уменьшение диаметра колеса нарушает вертикальное положение колонны от которого непосредственно зависит возможность правильного позиционирования грузового захвата во все ячейки по высоте стеллажа.
Для кранов-штабелеров с гибким токоподводом следует дополнительно учесть воздействие усилий статического натяжения и сопротивления передвижению кабельной подвески если эти усилия вызывают разгрузку приводного колеса. При этом кабельную подвеску следует рассматривать в наиболее растянутом положении т.е. на полной длине стеллажа которую принимают равной 100 м если в техническом задании нет других указаний.
Составив уравнения для коэффициента запаса сцепления в соответствии с приведенными указаниями легко увидеть что в них входят только геометрические и массовые параметры крана-штабелера и ускорения (замедления). Таким образом получим предельно допускаемое ускорение и замедление крана-штабелера всего четыре значения (ускорение и замедление для крана-штабелера с грузом и без груза) каждое из которых должно быть не менее 03 мс2.
По допускаемому ускорению с помощью известных формул определяют соответствующий среднепусковой момент электродвигателя который должен уравновесить сопротивление передвижению и силы инерции масс крана-штабелера а также инерционные моменты вращающихся масс ротора муфты тормозного шкива и т.п. с учетом КПД механизма.
Расчет выполняют для крана-штабелера с грузом и без груза; из двух полученных значений среднепускового момента выбирают наименьшее которое для перехода к номинальному моменту следует разделить на коэффициент кратности пускового момента и коэффициент использования пускового момента значения которого приведены в табл.3.2
Система упраления приводом
Коэффициент использования пускового момента
Релейно-контроллерная
Асинхронный с фазовым ротором
Асинхронный короткозамкнутый
Преобразователь или регулятор
Переменного или постоянного тока
Полученное значение номинального момента электродвигателя является предельно допустимым поэтому из рассматриваемой упорядоченной номенклатуры следует выбирать тот наибольший электродвигатель номинальный момент которого при ПВ = 60 % не превышает предельно допустимый.
Отсюда начинается проверочная часть расчета механизма передвижения. Сначала с помощью механической характеристики электродвигателя определяют расчетную скорость установившегося движения крана-штабелера которая должна удовлетворять требованиям изложенным выше. Если результат не достигнут то следует изменить передаточное число редуктора а возможно и рассмотреть другую номенклатуру редукторов и (или) электродвигателей.
Описание конструкции
Краны-штабелеры стеллажные автоматические грузоподъемностью 1 т предназначены для механизации процессов укладки в стеллажи и выдачи из стеллажей на загрузочные устройства грузов уложенных в стандартную ящичную тару по ГОСТ 14861-74 или на специальные поддоны и тару с размерами в плане 1200*800 мм для кранов-штабелеров грузоподъемностью 1 т.
Краны-штабелеры предназначены для применения в автоматизированных транспортно-складских системах функционирующих как самостоятельно так и в составе автоматизированных технологических комплексах а также для использования в цеховых складах машиностроительных заводов.
Климатическое использование кранов-штабелеров УХЛ4 по ГОСТ 15150-69.
Краны-штабелеры не предназначены для применения во взрыво и пожароопасных помещениях (за исключением П-IIа) в помещениях с парами кислот и щелочей концентрации которых вызывают разрушение электрической изоляции и металлических конструкций а также в помещениях в которых возможно выделение вредных веществ в воздух рабочей среды.
Кран-штабелер транспортируется и поступает потребителю упакованным в деревянные ящики кроме колонны следующими частями:
тележка в сборе с приводом передвижения направляющими роликами подхватами и конечными выключателями;
грузоподъемник в сборе с электрооборудованием;
направляющие для установки шунтов и направляющие кабельного блока;
считыватели конечные выключатели шунты линейки;
кабельные изделия детали и узлы креплений кабелей кабельный блок клеммные коробки кабельные тележки и другие узлы;
электрошкаф с реакторами;
устройство управления движением в сборе с кронштейном для его установки на кране-штабелере;
командное устройство управления;
1.Техническое описание
1.1.Технические характеристики кранов-штабелеров стеллажных автоматических грузоподъемностью 1 т представлены в таблице 4.1.1
Наименование параметров
Режим работы крана-штабелера
Режим работы механизмов по
привод выдвижения грузозахватного органа
Максимальное расстояние от головки рельса до подвесного пути Нр м
Максимальная высота подъема грузозахватного органа Нп м
Габариты перерабатываемых грузов:
Минимальная высота опор ящичной тары мин м
Скорость подъема грузозахватного органа мс
Скорость передвижения крана-штабелера мс
Скорость выдвижения грузозахватного органа мс
Тип грузозахватного органа
Величина выдвижения грузозахватного органа
Высота выдвигаемых элементов грузозахватного органа м
Ширина крана-штабелера В м
Длина крана-штабелера (вдоль пути)м
Ширина прохода для штабелирования А м
Максимальное количество адресов:
Двутавр №12 ГОСТ 8239-72
Продолжение табл. стр18
Тип нижнего рельсового пути
Суммарная мощность установленных электродвигателей кВт
Коэффициент установленной мощности
Подвод электропитания
Максимальная масса крана-штабелера т
Удельная металлоемкость ттыс.т.
Рельс Р24 ГОСТ6368-82
В состав изделия входят:
комплект монтажных частей;
эксплуатационная документация.
Кран-штабелер состоит из следующих составных частей
– электрооборудование.
В комплект монтажных частей поставляемых с краном-штабелером входят:
установка информационных каналов связи;
устройство командное;
буферы гидравлические;
детали для крепления рельсового и подвесного путей;
кабель подвесной для электропитания крана-штабелера;
линейки кронштейны и т.п.
1.3.Устройство и работа изделия
Привод передвижения установлен на тележке имеющей два колеса:
одно приводное и одно холостое диаметром 200мм.
На торцах тележки установлено по паре катков удерживающих кран-штабелер от бокового смещения.
Катки установлены на прокладках служащих для регулировки зазоров между катками и боковой поверхностью рельса.
К тележки при помощи болтов крепится колонна.
По направляющим на колонне перемещается грузоподъемник.
На грузоподъемнике установлен грузозахватный орган а также фотоэлементы для контроля положения груза датчики контроля занятости ячеек стеллажа и считыватель адреса по вертикали.
Подвод электропитания к грузоподъемнику осуществляется при помощи гибких кабелей. Натяжение кабелей осуществляется блоком перемещающимся по направляющим закрепленным на колонне на половине ее высоты.
Привод подъема расположен на нижней части колонны. Натяжение грузового каната контролируется ограничителем грузоподъемности.
В верхней части колонны установлен оголовок на котором имеются 4 отводных блока и пара направляющих катков служащих для удержания крана-штабелера в вертикальном положении.
Кран-штабклкр перемещается между стеллажами по рельсу уложенному вдоль продольной оси межстеллажного прохода. В верхней части межстеллажного прохода уложен подвесной путь из двутавра №12 по которому обкатываются катки установленные на оголовке крана-штабелера.
Подвод электропитания крана-штабелера осуществляется при помощи гибких кабелей подвешенных на специальных тележках перемещающихся по подвесному пути.
Управление краном-штабелером:
-автоматическое – от командного устройства;
-ручное – с наладочного пульта.
Система автоматического управления предусматривает возможность непосредственного управления от ЭВМ верхнего уровня.
Кран-штабелер выполняет следующие работы:
-берет груз с загрузочного устройства и устанавливает его в ячейку стеллажа;
-берет груз из ячейки стеллажа и устанавливает его на загрузочное устройство;
-берет груз из любой ячейки стеллажа или любого загрузочного устройства работающего на загрузку стеллажей и устанавливает его в другую ячейку стеллажа или на другое загрузочное устройство работающее на выгрузку.
Любая из указанных выше работ выполняется краном-штабелером по команде от ЭВМ или с командного устройства включающей адрес ячейки из которой кран-штабелер должен взять груз и адрес ячейки в которую кран-шлтабелер должен установить груз.
После получения команды кран-штабелер выполняет работу в следующей последовательности:
-включается привод подъема и передвижения кран-штабелер подходит и останавливается у ячейки откуда надо взять груз;
-включается привод выдвижения грузозахватного органа захваты выдвигаются и устанавливаются под грузом в ячейке стеллажа;
-включается привод подъема груз приподнимается привод подъема выключается;
-включается привод грузозахватного органа захваты с грузом возвращаются в среднее положение;
-включается привод подъема и передвижения кран-штабелер подходит и останавливается у ячейки в которую надо установить груз;
-путем последовательного включения привода грузозахватного органа и привода подъема груз устанавливается в заданную ячейку;
-после возвращения грузозахватного органа в среднее положение кран-штабелер остается на месте до получения следующей команды.
Экономика.docx
Вилочный захват крана-штабелера включает в себя электромеханический привод в котором движение передается от электродвигателя к исполнительному механизму через карданный вал. Комплекс обслуживают 3 человека.
Вилочный захват крана-штабелера включает в себя гидравлический привод в котором движение исполнительного механизма происходит от электородвигателя соединённого непосредственно с рабочим органом а также механизмы передвижения и подъема в которых движение исполнительного механизма происходит от мотор-редуктора. Комплекс обслуживает 1 человек.
Исходные данныеТаблица 8.1.
Количество элементов привода:
гидроклапан давления
Определение барьерной ставки.
Барьерная ставка определяет ту финансовую отдачу которую инвесторы ожидают от своих капитальных вложений и включает в себя два компонента – свободную от риска ставку СРС и страховую премию СП.
Поэтому можно сказать что стоимость капитала предприятия представляет собой рыночную оценку уровня риска по операциям предприятия. Предприятия принимают эту оценку в качестве среднего значения барьерного коэффициента HR так как у них нет более объективного показателя.
Стоимость капитала – это средневзвешенная цена (в процентах) которую предприятие уплатило за денежные средства использованные для формирования своего капитала. Эта величина определяется соотношением заемного и собственного капиталов в пассивной части баланса и может быть определена следующим образом:
СК – стоимость капитала %;
СД – стоимость долга %;
ДСК – доля собственного капитала;
ССК – стоимость собственного капитала %.
Так как выплаты процентов по займам уменьшают величину налогооблагаемой прибыли то собственно уменьшается и величина налоговых выплат. Экономия на налогах частично компенсирует выплаты по долгам. Поэтому процент выплат по займам с учётом этой экономии составит:
СН – ставка налога на прибыль;
NE(СД) – уровень эффекта процентной ставки;
В условиях высокой инфляции ставки ссудного процента и депозитные ставки рассчитываются с учетом внутригодовых реинвестиций и очищаются от инфляции.
Берутся номинальные (т.е. с учетом инфляции) годовые ставки коммерческих банков. На их основе рассчитываются эффективные ставки (т.е. с учетом реинвестиций по периодам внутри года):
NE(СД ССК) – номинальная эффектная ставка (кредитная и депозитная соответственно)
N(кб дб) – номинальная банковская ставка (кредитная и депозитная соответственно)
p – число периодов начисления процентов внутри года.
Расчет инвестиций и расходов.
Кдв – капитальные вложения на закупку электродвигателей;
Кт – капитальные вложения на закупку тормозов;
Кр – капитальные вложения на закупку редукторов;
Кк.в. – капитальные вложения на закупку карданных валов;
Кмах – капитальные вложения на закупку маховиков;
Кмуфт – капитальные вложения на закупку муфт шарнирных;
Крем – капитальные вложения на закупку ремней.
Цдв – стоимость одного электродвигателя
Zдв – количество электродвигателей
γм – коэффициент учитывающий затраты на доставку и монтаж
Цт – стоимость одного тормоза
Zт – количество тормозов
Цр – стоимость одного редуктора
Zр – количество редукторов
Цк.в – стоимость одного карданного вала
Zк.в – количество карданных валов
Цмах – стоимость одного маховика
Zмах – количество маховиков
Цмуфт – стоимость одной муфты шарнирной
Цмуфт = 4060 (руб.);
Zмуфт – количество муфт шарнирных
Црем – стоимость одного ремня
Zрем – количество муфт шарнирных
Км.р. – капитальные вложения на закупку мотор-редукторов;
Кц – капитальные вложения на закупку гидроцилиндров;
Кн – капитальные вложения на закупку гидронасосов;
Краспр – капитальные вложения на закупку гидрораспределителей;
Кт.ж. – капитальные вложения на закупку жестких трубопроводов;
Ккл.дав. – капитальные вложения на закупку клапанов давления.
Кф – капитальные вложения на закупку фильтров;
Кб – капитальные вложения на закупку гидробака;
Кв – капитальные вложения на закупку вентиля.
Цм.т. – стоимость одного мотор-редуктора
Цм.т. = 25200 (руб.);
Zм.т. – количество мотор-редукторов
Цц – стоимость одного гидроцилиндра
Zц – количество редукторов
Цн – стоимость одного гидронасоса
Zн – количество гидронасосов
Цраспр – стоимость одного гидрораспределителя
Цраспр = 4594 (руб.);
Zраспр – количество гидрораспределителей
Цт.ж. – стоимость одного метра жесткой трубы
Lт.ж. – длина жесткой трубы
Цкл.давл. – стоимость одного гидроклапана давления
Цкл.давл. = 2400 (руб.);
Zкл.давл. – количество гидроклапанов давления
Zкл.давл. = 1 (шт.);
Цф – стоимость одного фильтра
Zф – количество фильтров
Цб – стоимость одного гидробака
Zб – количество гидробаков
Цв – стоимость одного вентиля
Zв – количество вентилей
Сзаробщ – расходы на заработную плату обслуживающего персонала;
Сотч – отчисления на социальные нужды;
Снакл – накладные расходы (расходы на содержание административно-управленческого персонала);
Срем. – расходы на ремонт и техническое обслуживание;
Сэл – расходы на электроэнергию за год;
Саморт – амортизационные отчисления на реновацию.
Стар.зар. – тарифная заработная плата
Кп = 3 (чел) – количество обслуживающего персонала;
Тст = 6200 (руб) – тарифная ставка по должностям.
Сдоп. – доплата к заработной плате.
Сдоп.зар. – дополнительная заработная плата;
Цэл – тариф на электроэнергию : Цэл = 35 ркВтч ;
Ки – коэффициент использования оборудования по времени 07
Fэф – эффективный годовой фонд времени работы оборудования
Q – срок службы машины Q = 12 лет.
Кп = 1 (чел) – количество обслуживающего персонала;
Расчет чистых денежных потоков приведен в таблице 8.2.
Расчет чистых денежных потоков.
Приращение доходов и расходов
экономия заработной платы
отчисления на социальные нужды
расходы по содержанию и эксплуатации оборудования
расходы на электроэнергию
Корректировка денежных потоков:
Чистые денежные потоки
Чистая текущая стоимость (NPV)
Чистая текущая стоимость является суммой дисконтированных чистых денежных потоков порождённых капиталовложениями и определяется следующим образом:
ЧДП – чистый денежный поток руб.;
HR – барьерная ставка;
n – число лет функционирования проекта.
ЧДП берётся со знаком соответствующим оттоку или притоку денежных средств.
Положительное значение чистой текущей стоимости (NPV) говорит об эффективности рассматриваемого варианта.
Рассчитаем значения чистой текущей стоимости.
Внедрение и использование модернизированного захвата увеличивает производительность погрузочно-разгрузочных работ позволяет увеличить грузопоток что является основной экономической характеристикой склада и получить экономический эффект.
БЖД.docx
1.Безопасность персонала при обслуживании проектируемого склада
1.1.Эксплуатационно-технические характеристики.
Режим работы по ГОСТ 25546-827К
Габариты перерабатываемого груза м:
Высота выдвигаемых элементов грузозахватного органа мм70
Величина выдвижения грузозахватного органа мм920
Скорость передвижения крана мс25
Скорость подъема грузозахватного органа мс2
Скорость выдвижения грузозахватного органа мс025
Техническая производительность тч178
Суммарная мощность двигателей кВт253
Тип нижнего путиР24 ГОСТ 6368-82
Тип верхнего путидвутавр 12 ГОСТ 8239-72
Подвод электропитаниякабельный
Управлениеавтоматическое
Климатическое исполнениеУХЛ4 ГОСТ 15150-69
Класс пожароопасностиП-2а
1.1.Требования к персоналу режимы работ квалификация
К управлению электропогрузчиком допускаются лица не моложе 18 лет прошедшие теоретическое и практическое обучение сдавшие экзамен и получившие удостоверение на право управления электропогрузчиком.
Перед допуском к работе водителю электропогрузчика необходимо пройти медицинское освидетельствование получить вводный инструктаж по охране труда первичный инструктаж на рабочем месте освоить безопасные приемы эксплуатации электропогрузчика; пройти проверку знаний в объеме II группы по электробезопасности теоретических знаний и приобретенных практических навыков безопасного выполнения работ по управлению электропогрузчика при подъеме транспортировке и укладке грузов.
Водитель электропогрузчика должен:
перед началом работы проверить техническое состояние погрузчика;
обладать навыками требующимися для управления всеми механизмами погрузчика и ухода за ним;
знать правила безопасного перемещения грузов;
соблюдать действующие в организации правила внутреннего трудового распорядка график работы режим труда и отдыха.
извещать своего непосредственного руководителя о происшедшем с ним или по его вине несчастном случае а также о любом несчастном случае происшедшем на производстве об ухудшении состояния своего здоровья в том числе о проявлении признаков острого заболевания.
Режим работ водителей электрпогрузчиков по 12 часов в 1 смену.
1.2.Основные опасности и вредности при работе персонала
Во время работы персонала на складе могут воздействовать следующие опасные и вредные производственные факторы:
столкновение или наезд на людей или другим транспортным средством;
падение перевозимого груза.
удар электрическим током
неустойчивые штабели перемещаемых и складируемых товаров; повышенная запыленность воздуха рабочей зоны;
недостаточная освещенность места проведения работ;
острые кромки заусенцы и шероховатости на поверхностях деталей инструмента;
опасный уровень напряжения в электрической цепи.
движущиеся и вращающиеся детали и узлы крана-штабелера;
При работе с различными грузами возможно влияние таких опасных и вредных производственных факторов как токсические раздражающие сенсибилизирующие канцерогенные мутагенные влияющие на репродуктивную функцию.
1.1.Технические и организационные мероприятия по обеспечению персонала при работе на складе.
Поскольку персонал работает на складе то рассмотрим проблему освещения рабочего места.
Требования к освещению.
Оборудование электрического освещения производственных и бытовых помещений сборочно-сварочных цехов и участков должно соответствовать нормам установленным в СН 245-71 и СНиП 23-05-95.
В зависимости от вида источника света производственное освещение подразделяется:
на естественное которое создается излучением поступающим непосредственно от Солнца без изменения направления распространения и диффузным (отраженным и рассеянным атмосферой) солнечным светом;
искусственное обеспечиваемое электрическими светильниками.
Естественный (солнечный) свет по спектральному составу значительно отличается от излучения электрических источников.
В солнечном спектре гораздо больше необходимых человеку ультрафиолетовых лучей. Для естественного освещения характерна высокая степень рассеяния света благоприятная для зрительной работы.
Рис. 5.4. Схемы распределения коэффициента естественной освещенности е по разрезу помещения:
а - одностороннее боковое освещение; б - двустороннее боковое освещение; в - верхнее освещение; г - комбинированное освещение; 1 - уровень рабочей плоскости; еmin и еср - минимальное и среднее значения коэффициента естественной освещенности
В соответствии с конструктивными особенностями помещения естественное освещение может быть (рис. 5.4):
боковым (осуществляется через окна в наружных стенах);
верхним (производится через аэрационные и зенитные фонари проемы в покрытиях и световые проемы в местах перепада высоты смежных пролетов зданий);
комбинированным (к верхнему освещению добавляется боковое).
Искусственное освещение предусматривается в тех случаях когда естественного света недостаточно или он отсутствует.
По конструктивному исполнению осветительной системы искусственное освещение может быть:
местным создающим световой поток непосредственно на рабочем месте;
общим (освещается все помещение);
комбинированным (к общему освещению добавляется местное).
Общее освещение подразделяется на равномерное и локализованное создаваемое с учетом расположения рабочих мест.
Ряд единиц необходимых для расчета искусственного освещения вытекает из задач данного мероприятия. Эти единицы нормированы и поддержание их обеспечивает оптимальное распределение световой энергии а значит позволяет выполнить поставленные задачи. Основные параметры которые учитываются при расчете искусственного освещения таковы:
Световой поток. Данная величина измеряемая в люменах (лм) существенна для расчета искусственного освещения поскольку характеризует мощность лучистой энергии в 1 Вт.
Освещенность. Эта характеристика измеряемая в люксах (лк) важна для расчета искусственного освещения поскольку определяет отношение светового потока к площади освещаемой поверхности.
Сила света измеряется в канделах (кд) и учитывается при расчете искусственного освещения потому что характеризует плотность светового потока.
Светимость важна для расчета искусственного освещения в силу того что определяет отношения светового потока к источнику освещения. Принятая единица измерения – лмм2.
Яркость. Эта величина принципиальна для расчета искусственного освещения потому что определяет отношение силы света к освещаемой поверхности.
Для расчета искусственного освещения специалисты прибегают к различным методам: точечному методу методу удельных мощностей и методу коэффициента использования светового потока.
Точечный метод расчета искусственного освещения
Его особенность состоит в том что учитывается отраженная световая энергия. Расчет искусственного освещения производится опираясь на показатели силы света (I кд) высоты подвеса осветительного прибора (H м) а также коэффициент запаса (11 5 - 18).
Для расчета искусственного освещения данным методом используются отдельные формулы для горизонтальной и вертикальной плоскости:
Ег=I*cos3αН 2 *К3 - для горизонтальной плоскости
Ев= I*cos3 (90-α) Н 2 *К3 - для вертикальной плоскости
При расчете искусственного освещения помещения или пространства несколькими светильниками освещенность определяется от каждого источника а затем показатели суммируются.
Следовательно формула для расчета искусственного освещения в данном случае усложняется ведь необходимо учесть и количество ламп (n) и коэффициент дополнительной освещенности точки ( 11 - 12) и световой поток лампы (Фл лм) и сумму условных освещенностей от светильников которые светят в данную точку (ΣЕг) и условный световой поток (1000 лм). Поэтому при расчете искусственного освещения для нескольких светильников используется формула:
Расчет искусственного освещения методом удельных мощностей
Достоинство данного метода расчета искусственного освещения состоит в простоте а слабая сторона – в недостаточной точности. Потому эта техника применяется при первичных расчетах. Суть подобного расчета искусственного освещения сводится к определению количества светильников того или иного типа с помощью таблиц удельных мощностей.
В подобных специальных таблицах указаны удельные мощности источников освещения в зависимости от площади освещаемой поверхности типов светильников высоты их подвеса необходимой освещенности. При этом в ходе расчета искусственного освещения используют формулу удельной мощности:
где n - число ламп в светильниках
Рл - мощность лампы Вт;
S - площадь освещаемого помещения м2.
Таком образом с помощью данной формулы расчета искусственного освещения можно определить количество светильников которое необходимо для освещения данной площади и электрическую мощность приборов.
Расчет искусственного освещения методом коэффициента использования светового потока
Данный метод расчета искусственного освещения считается самым популярным. Его сущность состоит в определении светового потока необходимого для достижения заданных показателей освещенности. При расчете искусственного освещения таким способом учитывается отраженный свет и необходимость в равномерном распределении светового потока. Формулы которые используются для расчета искусственного освещения зависят от вида источника освещения.
Расчет искусственного освещения для ламп накаливания и ламп типов ДРЛ ДРИ и ДНат:
где F—световой поток одной лампы лм;
Е—нормированная освещенность лк;
S—площадь помещения м2;
z—коэффициент неравномерности светильника (для стандартных светильников 11—13);
Kз — коэффициент запаса;
n - число светильников;
u —коэффициент использования зависящий от типа (055—060)
Расчет искусственного освещения для люминесцентных ламп:
F=( E*S*z*Kз)(n*Фл* )
где Фл - световой поток лампы лм;
- коэффициент использования светового потока осветительной установки.
1.4.2 Защитное заземление.
Одним из основных опасных факторов при обслуживании ПФМ является возможность поражения электрическим током. Для защиты применяют защитное заземление.
Заземление электроустановки — преднамеренное электрическое соединение ее корпуса с заземляющим устройством.
Заземление электроустановок бывает двух типов: защитное заземление и зануление которые имеют одно и тоже назначение - защитить человека от поражения электрическим током если он прикоснулся к корпусу электроприбора который из-за нарушения изоляции оказался под напряжением.
Защитное заземление - преднамеренное соединение с землей частей электроустановки.
Принцип действия защитного заземления – снижение до безопасных значений напряжений прикосновения и шага обусловленных замыканием на корпус. Это достигается уменьшением потенциала заземленного оборудования а также выравниванием потенциалов за счет подъема потенциала основания на котором стоит человек до потенциала близкого по значению к потенциалу заземленного оборудования. Область применения защитного заземления – трехфазные трехпроводные сети напряжением до 1000 В с изолированной нейтралью и выше 1000 В с любым режимом нейтрали (рис. 9.2.1.).
Рис. 9.2.1. Принципиальные схемы защитного заземления
В случае возникновения пробоя изоляции между фазой и корпусом электроустановки корпус ее может оказаться под напряжением. Если к корпусу в это время прикоснулся человек - ток проходящий через человека не представляет опасности потому что его основная часть потечет по защитному заземлению которое обладает очень низким сопротивлением. Защитное заземление состоит из заземлителя и заземляющих проводников.
Есть два вида заземлителей – естественные и искусственные.
К естественным заземлителям относятся металлические конструкции зданий надежно соединенные с землей.
В качестве искусственных заземлителей используют стальные трубы стержни или уголок длиной не менее 25 м забитых в землю и соединенных друг с другом стальными полосами или приваренной проволокой. В качестве заземляющих проводников соединяющих заземлитель с заземляющими приборами обычно используют стальные или медные шины которые либо приваривают к корпусам машин либо соединяют с ними болтами. Защитному заземлению подлежат металлические корпуса электрических машин трансформаторов щиты шкафы.
Защитное заземление значительно снижает напряжение под которое может попасть человек. Это объясняется тем что проводники заземления сам заземлитель и земля имеют некоторое сопротивление. При повреждении изоляции ток замыкания протекает по корпусу электроустановки заземлителю и далее по земле к нейтрали трансформатора вызывая на их сопротивлении падение напряжения которое хотя и меньше 220 В но может быть ощутимо для человека. Для уменьшения этого напряжения необходимо принять меры к снижению сопротивления заземлителя относительно земли например увеличить количество искусственных заземлителей.
При замыкании одной из токоведущих крана выполненный из проводящего материала (металл) он оказывается под напряжением.
Прикосновение к корпусу крана человека (так называемое косвенное прикосновение) приводит к возникновению тока через него Iч который может привести к электротравме.
В целях электробезопасности необходимо проводящий корпус электроустановки заземлить т.е. выполнить электрическое соединение проводящих частей электроустановки (нормально не находящихся под напряжением) с проводящими частями находящимися в электрическом контакте с землёй и называемыми заземлителем.
Совокупность заземлитея и проводников соединяющих заземлитель с проводящим корпусом электроустановки называют заземляющим устройством.
Откуда видно что при электрическом соединение корпуса электроустановки с заземлителем Rзу происходит параллельное соединение сопротивлений человека Rч и заземлителя Rзy
Тогда величина тока через человека составит:
где: Iз – ток замыкания на землю.
Если поставить условие Rзу « Rч то
т.е. защитное заземление уменьшает величину тока через человека в соотношение
раз. При отсутствии заземляющего устройства (Rзу = Iч = Iз.
А так как электрическое сопротивление человека принимается величиной постоянной равной 1000 Ом то необходимые условия электробезопасности (допустимый ток через человека Iчдоп) при установленном значении тока замыкания Iз могут быть достигнуты только при определенном значении Rзу.
Величина тока замыкания в общем случае определяется напряжением и схемой электрической сети к которой подключена электроустановка.
Характеристика воздействия на человека электрического тока различной силы
Переменный ток 50-60 Гц
Лёгкое дрожание пальцев рук
Сильное дрожание пальцев рук
Руки с трудом но ещё можно оторвать от электродов. Сильные боли в руках особенно в кистях и пальцах.
Руки парализуются оторвать их от электродов не возможно. Очень сильные боли. Затрудняется дыхание.
Ещё большее уселение нагревания незначительное сокращение мышц рук.
Паралич дыхания. Начало трепетания желудочков сердца.
Сильное ощущение нагревания. Сокращение мышц рук. Судороги. Затруднение дыхания.
Паралич дыхания и сердца при воздействии более 01с
На рисунке приведены результаты экспериментального исследования зависимости значений «опускающего» тока от индивидуальных качеств человека.
На рисунке графически представлена область предельно допустимых значений тока и длительность его протекания через человека с вероятностью 995 % не вызывающих фибрилляцию сердца (А – область недопустимых значений).
По Дальцилу граница областей допустимых значений тока через человека и длительности его протекания определяется выражением:
где: I – предельно допустимый ток через человека мА;
Т – длительность протекания тока через тело человека с.
Предельно допустимые уровни напряжений прикосновения.
Неощутимое напряжение В для t ≤ 10 мин
Отпускающее напряжение В t ≤ 30 c
Нефибрилляционное напряжение В t = 10 с
Предельная величина Uпр
Предельно допустимые уровни токов прикосновения.
Неощутимый ток мА t ≤ 10 мин
Отпускающий ток А t ≤ 30 c
Нефибрилляционный ток А t = 10 с
Главным средством для обеспечения безопасности обслуживании стенда обкатки редуктора является заземление.
Предполагается сооружение заземлителя с внешней стороны участка с расположением вертикальных электродов в один ряд длиной 20 м; материал - круглая сталь диаметром 20 мм метод погружения - ввертывание; верхние концы вертикальных стержней погруженные на глубину 07 м приварены к горизонтальному электроду из той же стали.
Требуемое сопротивление заземления:
1.2.Техника безопасности при обслуживании склада
Т.к. на складах основной опасностью для работников является транспорт который перемещается внутри склада т.е. электропогрузчики.
Все операции связанные с техническим обслуживанием устранением неисправностей очисткой двигателя и машины q.t грязи и подготовкой машины к работе выполняют при остановленном двигателе.
Работы ведут в соответствии с паспортом и инструкцией по эксплуатации завода-изготовителя. Запрещается выполнять операции не соответствующие назначению и технической характеристике сменного рабочего оборудования.
Работа погрузчика допускается только на освещенных площадках и внутриобъектных дорогах с твердым и ровным покрытием с уклоном не более 5°. Запрещается работать на захламленных имеющих выбоины и рытвины площадках. Зимой площадки и дороги должны быть очищены от снега и льда и посыпаны песком золой или шлаком.
Контейнеры поддоны и штучные грузы допускается штабелировать на площадках с уклоном не более 1°. Запрещается работать с неисправными контейнерами поддонами и другими пакетирующими приспособлениями.
Строповочные приспособления ежедневно осматривают и проверяют соответствуют ли они нормативным документам. Не допускается работа с приспособлениями имеющими дефекты.
Груз поднимают при отклоненном назад грузоподъемнике и за торможенном погрузчике. Груз распределяют равномерно по ширине вил а при работе со стрелой — по продольной оси машины. Запрещается поднимать груз масса которого превышает норму указанную в технической характеристике а также примерзший или защемленный какими-нибудь предметами. Если груз выходит за габариты вилочный подхватов его закрепляют.
При движении погрузчика запрещается поднимать или опускать груз менять наклон грузоподъемника. Груз закрывающие обзор пути движения перевозят в сопровождении помощника который следит за дорогой. Запрещается на погрузчике перевозить людей.
На автомобильные дороги общего назначения погрузчики выезжай в исключительных случаях соблюдая при этом Правила дорожного движения. При езде по дороге ночью погрузчик должен быть оснащен средствами световой сигнализации и освещения.
После окончания работы и при длительных перерывах в работе грузоподъемник с грузом опускают в крайнее нижнее положение.
При проведении технического обслуживания и ремонта соблюдают следующие правила техники обслуживания и ремонта. Запрещается находиться под погрузчиком и под грузоподъемником при работающем двигателе.
Все работники должны соблюдать технику безопасности складского хозяйства стеллажного хранения груза:
работники должны ходить по тому маршруту в котором указан в маршрутной карте;
запрещается находиться под стеллажами и в межстеллажном пространстве если не связанно с его обязанностью.
запрещается находиться в местах работающего крана-штабелера т.к. это может привести к травматизму.
2.Безопасность персонала в чрезвычайных ситуациях
2.1.Пожарная безопасность на складах.
Организация работ по пожарной безопасности должна включать:
разработку и внедрение системы управления пожарной безопасностью согласно требованиям руководящих документов;
общее руководство и контроль за состоянием пожарной безопасности на предприятии контроль за соблюдением законодательных и иных нормативных правовых актов требований правил и инструкций по пожарной безопасности. Контроль за выполнением служебных обязанностей подчиненными;
обеспечение пожарной безопасности при проведении технологических процессов эксплуатации оборудовании производстве пожароопасных работ;
установка и контроль за состоянием средств контроля оповещения и пожаротушения;
организацию разработки и обеспечение выделения финансовых средств на реализацию мероприятий по обеспечению пожарной безопасности;
проведение обучения и инструктажа работников предприятия по пожарной безопасности;
обеспечение электробезопасности предприятия.
Установка и контроль за состоянием средств контроля оповещения и пожаротушения.
Обучение по пожарной безопасности специалистов служащих и рабочих включает:
- проведение вводного первичного повторного внепланового и целевого инструктажей;
- организация занятий по пожарно-техническому минимуму;
- проведение учений и противопожарных тренировок.
Система пожарной сигнализации склада выполняет задачу обнаружения места возгорания и оповещения об этом соответствующих служб. Кроме того она должная быть связана с системами автоматического пожаротушения и дымоудаления которые локализуют очаги возгорания ещё до приезда пожарных служб. Установка на складе охранной и пожарной сигнализации значительно повышает безопасность склада и материальных ценностей а также обеспечивает своевременное оповещение пожарных служб.
Система охранной сигнализации - одна из составляющих комплексной системы безопасности склада представляет собой совокупность совместно действующих технических средств охранной сигнализации устанавливаемых на охраняемом объекте и объединенных системой инженерных сетей и коммуникаций. Системы охранной сигнализации не зависят от человеческого фактора и своевременно оповещают службы охраны о проникновении или попытке проникновения на склад с фиксацией факта места и времени нарушения рубежа охраны.
Последние две системы безопасности для складов можно объединить в одну что и предлагают многие российские и зарубежные производители оборудования. Современная охранно-пожарная сигнализация (ОПС) склада - представляет собой комплекс оборудования обеспечивающего пожарную безопасность склада и своевременное обнаружение проникновения в охраняемую зону а также оповещение о месте возникновения пожара на объекте.
Установки пожарной автоматики (УПА) занимают ведущее место в обеспечении пожарной безопасности различных объектов включая производственные складские административные здания и подвижной состав железнодорожного транспорта.
Действующие сегодня законодательные и иные нормативные правовые акты по пожарной Согласно ГОСТ 12.1.004-91 "Пожарная безопасность. Общие требования" противопожарная защита должна достигаться в первую очередь применением автоматических установок пожарной сигнализации и пожаротушения.
Широкое внедрение средств пожарной автоматики позволят значительно сократить количество крупных пожаров и ущерб от них.
В целом по стране число пожаров и ущерб от них на объектах оборудованных УПА соответственно в 30 и 40 раза меньше в сравнениями с показателями пожаров на объектах на которых средства пожарной автоматики отсутствуют.
Очень важную роль в предотвращении пожаров и обнаружении очага возгорания играет своевременная информация о месте возникновения пожара. Для этой цели служит автоматическая пожарная сигнализация. Системы пожарной сигнализации включают в себя пожарные извещатели линейные сооружения линии связи и приемные пульты станций.
Рассмотрим виды пожарных извещателей:
Тепловые извещатели реагируют на изменение температуры в помещении. Выпускаются тепловые извещатели максимальной температуры и максимально-дифференциальные. Детекторы максимальной температуры имеют некоторый фиксированный порог и срабатывают; когда температура окружающей среды в помещении достигнет порогового значения. Максимально- дифференциальные извещатели реагируют не только на величину температуры но и на скорость ее нарастания т.е. на производную температуры по времени. Отсюда и их название. В большинстве случаев максимально-дифференциальные извещатели раньше обнаруживают возгорание чем детекторы максимальной температуры.
Площадь контролируемая одним точечным тепловым пожарным извещателем а также максимальное расстояние между извещателями извещателем и стеной необходимо определять по таблице 8 но не превышая величин указанных в технических условиях и паспортах на извещатели.
Наиболее распространены оптические дымовые извещатели. Их принцип действия заключается в следующем. В дымовой камере под углом 120 градусов установлены излучатель и фотоприемник. Конструкция камеры выполнена таким образом что в дежурном режиме ИК-излучение от светодиода не попадает на фотоприемник. При поступлении дыма в камеру его частицы рассеивают ИК-излучение и оно достигает фотоприемника. При определенной концентрации дыма и следовательно достаточном количестве отраженного излучения происходит срабатывание извещателя.
Площадь контролируемая одним точечным дымовым пожарным извещателем а также максимальное расстояние между извещателями извещателем и стеной за исключением случаев оговоренных в п. 12.20 необходимо определять по таблице 5 но не превышая величин указанных в технических условиях и паспортах на извещатели.
Ручные извещатели являются обязательным компонентом любой системы пожарной сигнализации. Их назначение - подача сигнала о пожаре при его обнаружении персоналом здания. Ручные пожарные извещатели устанавливают на стенах и конструкциях на высоте 15 м от уровня пола или земли. Максимальное расстояние между двумя ближайшими ручными извещателями внутри помещений – не более 50 м а вне помещения – 150 м; ввод проводов в корпус извещателя – трубный. В случае неисправности на извещатель следует повесить табличку с соответствующей надписью.
Выносная сигнализация пожарной безопасности складов служит для подачи сигнала тревоги и выполняется в соответствии с требованиями НПБ 104-2003 «Системы оповещения и управления эвакуацией людей при пожарах в зданиях и сооружениях». В качестве прибора оптической сигнализации пожарной безопасности складов используются лампы накаливания мощностью 25 Вт для защиты которых служит светосигнальная арматура со стеклянным плафоном окрашенным в красный цвет защищенная металлической сеткой. Система сигнализации пожарной безопасности складов монтируется с помощью арматуры установленной с фасадной стороны здания на высоте не менее 275 м от земли и крепится к стене здания или на металлическом кронштейне. В качестве арматуры допускается использовать светильники типа НПП05 ПСХ НСП (исполнение полностью пылезащищенное).
В качестве акустического сигнализатора пожарной безопасности складов применяют сирены ревуны звонки мощностью до 20 Вт. Приборы звуковой сигнализации устанавливают на наружной стене здания с фасадной стороны на высоте 275 м от земли и выполняются в металлическом корпусе.
Инструкция по противопожарной защите высотного стеллажного склада
I. Следует использовать автоматическую систему пожарной сигнализации
с применением датчиков реагирующих на присутствие газов и дымов (например ионных датчиков) или иных устройств которые при возникновении пожара обеспечивают оповещение пожарных служб на предприятии или в населенном пункте. Датчики следует размещать в горизонтальных плоскостях на расстоянии около 8 м друг от друга. Такая их расстановка не оказывает принципиального влияния на решение строительной части здания.
В крыше здания должны быть предусмотрены отверстия для отвода
газов дыма и горячего воздуха. Эти отверстия должны быть оборудованы клапанами с автоматическим открыванием. Отверстия должны занимать
—5% поверхности крыши (поскольку наличие дыма и газов затрудняет
операцию тушения и. кроме того может быть причиной взрыва).
На расстоянии не более 50 м друг от друга следует предусмотреть
устройство поперечных (относительно пролетов) переходов через весь склад.
Такие переходы должны иметь ширину не менее 0.8 м и высоту не менее
9 м В железобетонных складах эти переходы должны быть снабжены
противопожарными дверями имеющими такую же огнестойкость что и сте-
на. разделяющая отдельные камеры. В каждом переходе следует разместить
два гидранта со шлангами и брандспойтами. подача воды к которым осуществляется из двух независимых источников.
Следует предусмотреть необходимую систему аварийных выходов и
лестниц оборудованную соответствующими указателями и аварийным освещением. Эти коммуникационные пути должны быть всегда доступными.
Выводы: в данном разделе был проведен расчет заземления крана-штабелера выбраны средства заземления предложено определенное количество стержней заземления для хорошего отведения тока а так же рассмотрена техника безопасности при пожаре приведена инструкция по противопожарной защите высотного стеллажного склада.
Практическое обеспечение безопасности жизнедеятельности при проведении технологических процессов и эксплуатации технических систем во многом определяется решениями и действиями инженеров и техников. Руководитель производственного процесса обязан:
-обеспечивать оптимальные (допустимые) условия деятельности на рабочих местах подчиненных ему сотрудников;
-идентифицировать травмирующие и вредные факторы сопутствующие реализации производственного процесса;
-обеспечивать применение и правильную эксплуатацию средств защиты работающих и окружающей среды;
-постоянно (периодически) осуществлять контроль условий деятельности уровня воздействия травмирующих и вредных факторов на работающих;
-организовывать инструктаж или обучение работающих безопасным приемам деятельности;
-лично соблюдать правила безопасности и контролировать их соблюдение подчиненными;
-при возникновении аварий организовывать спасение людей локализацию огня воздействия электрического тока химических и других опасных воздействий.
Технология.docx
Разработка технологического процесса штока гидробуфера
В конструкторском разделе диплома выполнен основной расчет параметров гидробуфера.
Рассчитаны на прочность его основные детали в том числе и шток как наиболее ответственный элемент.
По заданию в технологической части необходимо разработать технологический процесс изготовления штока. а именно выбрать заготовку составить маршрут изготовления подробно разработать токарную и шлифовальную операции составить на них эскизы.
Анализ технологических требований изготовления детали
Шток является оригинальной деталью что обосновывает целесообразность составления технологической карты его изготовления.
Деталь изготавливается в условиях единичного производства из стали 45 ГОСТ 1050-88 твердостью НВ 190 - 230 термообработка – нормализация. Она представляет собой 6-ти ступенчатый вал длиной 390 мм. Относится к группе цилиндрических изделий. Внутри - сплошной.
Первая ступень диаметром 20 мм и длиной 30 мм служит для нарезания резьбы обрабатывается с допуском h9 шероховатостью Rа = 08 мкм.
Вторая ступень диаметром 24 мм и длиной 15 мм служит для фрезерования на ней четырёхгранника обрабатывается с допуском h11 шероховатостью Rz40.
Третья ступень диаметром 45 мм и длиной 248 мм служит опорой для посадки уплотнения с допуском f9 шероховатостью Rа = 032 мкм.
Четвёртая ступень диаметром 61 мм и длиной 10 мм служит упорным буртиком специально не обрабатывается.
Пятая ступень диаметром 45 мм и длиной 52 мм является переходной ступенью специально не обрабатывается.
Шестая ступень диаметром 18 мм и длиной 38 мм служит для нарезания резьбы обрабатывается с допуском h9 шероховатостью Rа = 08 мкм.
Для удобства монтажа делаем фаски на ступенях: 1 2356 которые подрезаются на токарном станке при помощи проходного резца. Фаски не являются рабочими поэтому точность и шероховатость обеспечивается инструментом.
На поверхностях 1 и 6 необходимо нарезать резьбу после черновой и чистовой обработки. Поверхность 2 необходимо фрезеровать под четырёхгранник.
При изготовлении детали необходимо выдерживать допуски формы и расположения.
Допуск цилиндричности (табл. 24.2 [1]);
- для поверхностей 3 (45 f9 )
Тo = 05 .62 = 31 мкм. Принимаем Тo = 003 мм;
- для поверхности 6 (18 h9)
Тo = 05 .52 = 26 мкм. Принимаем Тo=003 мм;
- для поверхности 1 (20 h9)
Тo = 05 .52= 26 мкм. Принимаем Тo=003 мм;
Допуск перпендикулярности упорного буртика под поршень.
– степень точности допуска 7 (табл. 22.4 [9]);
Т = 0016 мм (табл. 22.8 [9]); Принимаем Т = 001мм
Выбор вида финишной обработки конструктивных элементов детали.
Для обрезки заготовки в размер сверления центровых отверстий и формирования профиля вала применим токарный станок 16К20.
Для поверхности 2 (24h12) 4 (61h14) 5 (45h14) с шероховатостью Rz 80 назначаем только черновое точение.
Для поверхности 2 (24h11) с шероховатостью Rz 40 назначаем получистовое точение.
Для поверхностей 1(20h9) 6 (18h9) с шероховатостью Ra 08 назначаем окончательное шлифование.
Для поверхностей 3 (45f9) для участка под манжетное уплотнение с Ra 032 назначаем полирование.
Фаски галтели и центровые отверстия получаем на токарном станке при закреплении заготовки в патрон.
Для получения резьбы используем резьбовой резец.
Выбор способа установки заготовки для её обработки.
Рассчитаем средний диаметр заготовки как:
где:n – число конструктивных элементов;
– диаметр и длина конструктивного элемента;
Определим коэффициент жесткости:
Т.к. Кж>12 то применяем установку в центрах с люнетом.
Выбор вида определение размеров заготовки типа и типоразмера центровых отверстий.
Для условий единичного или мелкосерийного производства и при несущественном перепаде диаметров для детали типа вал применяется в качестве заготовки круглый горячекатаный сортовой прокат.
При максимальном диаметре детали 61 мм и при К = рекомендуемый диаметр заготовки 65 мм.
Из номенклатуры круглого сортового проката выбираем сталь горячекатаную круглую ГОСТ 2590 – 88 обычной степени точности (В) 65 мм с предельными отклонениями +05; -11 допуск на заготовку составляет 16мм (Т = 16мм) что соответствует 16 квалитету.
Определим длину заготовки:
где Zто – припуск на торцевую обработку. При номинальном диаметре проката свыше 50 до 50 мм Zто = 3мм(по табл. П7 [10])
Центровые отверстия для токарной и шлифовальной обработки выбираем согласно ГОСТ 14034-74. Для детали 65 мм рекомендовано центровое отверстие В 63.
Выбираем: отверстие центровое В 63. ГОСТ 14034-74.
Составление укрупнённого маршрута изготовления детали.
Отрезать заготовку от проката круглого сечения обычной степени точности 65мм длиной 396мм.
Заготовку подвергнуть термообработке – нормализации до НВ 280.
Выполнить обработку торцов в размер 390 h14 и сверлить два центровых отверстия В 63. ГОСТ 14034-74.. За несколько технологических переходов выполнить обработку по формированию контура детали. Точить фаски канавки.
0 Кругло-шлифовальная
Выполнить предварительную и окончательную обработку шеек детали.
Фрезеровать многогранник.
Подвергнуть ТВЧ шейку вала 45f9под манжету.
Очистить детали от загрязнений;
Выполнить контроль детали по условиям чертежа;
Разработка операций по формированию контура детали.
1. Расчёт числа стадий обработки по каждому конструктивному элементу.
Ужесточение точности:
Число стадий обработки:
2. Расчёт точности промежуточных размеров заготовки по стадиям обработки.
Определим точность заготовки по каждой стадии механической обработки для каждой поверхности. При расчете шаг уменьшения квалитетов по стадиям механической обработки должен изменяться по закону убывающей арифметической прогрессии. Расчет ведём в табличной форме.
Таблица 2. Расчет точности промежуточных размеров
– ой 20h9 и 6 – ой 18h9
Обтачивание черновое
Обтачивание чистовое
Шлифование окончательное
Таблица 3. Расчет точности промежуточных размеров 3 – ей поверхности вала: 45f9
Для получения размера 24 и 5-ой поверхности с 45h14 61h14 и 24h12 используем только обтачивание черновое.
3. Определение промежуточных размеров по стадии механической обработки
Расчет ведем в табличной форме используя следующие формулы:
где: - припуск на обработку поверхности принимается из ;
d - текущий диаметр;
d() - диаметр предшествующей обработки;
- исходный размер ступени вала;
– максимальный размер ступени вала.
Таблица 6. Расчет припусков на промежуточные размеры 3 - ей ступени вала 45f9
Расчёт промежуточных размеров
Характеристика размера
Точение получистовое
Таблица 6. Расчет припусков на промежуточные размеры 1 - oй ступени вала 20h9
Таблица 6. Расчет припусков на промежуточные размеры 6 - oй ступени вала 18h9
Таблица 8. Расчет припусков на промежуточные размер 2-ой ступени
Таблица 8. Расчет припусков на промежуточные размер 4-ой ступени
Таблица 8. Расчет припусков на промежуточные размер 5-ой ступени
Окончательно выбираем из сортамента прокат 65мм
Составление плана токарной и шлифовальной обработок детали
Расчёт выполняем из условия применения станка 16К20 имеющего следующие характеристики:
- допустимая мощность резания N = 75 кВт;
- максимальный диаметр заготовки до 400 мм;
- максимальная длина заготовки 1400 мм;
- частота вращения шпинделя 125 1600 обмин (регулирование ступенчатое);
- продольная подача суппорта 005 28 ммоб (регулирование ступенчатое).
1. Расчет предельно-допустимых глубин резания при черновом обтачивании.
Глубину резания для технологического перехода рассчитываем по формуле:
и сравниваем полученное значение с предельно допустимым для данного диаметра:
если обработка осуществляется за один переход
если обработка осуществляется за несколько технологических переходов.
Применим формулу с коэффициентом «005» т.к. Кж = 98>12.
При этом назначаем подачу инструмента и сравниваем мощность резания с допустимой мощностью на шпинделе (75 кВт).
Третья ступень: 4553
следовательно обработка по диаметрам возможна за 2 прохода.
Выполняем анализ по мощности:
При подаче инструмента S = 03 ммоб и глубине резания t = 487 мм мощность N = 72 кВт что меньше 75кВт (по табл. П13 [10]).
следовательно обработка по диаметрам возможна за 5 проходов.
При подаче инструмента S = 06 ммоб и глубине резания t = 21 мм мощность N = 71 кВт что меньше 75кВт (по табл. П13 [10]).
Первая ступень: 2056
следовательно обработка по диаметрам возможна за 1 проход.
При подаче инструмента S = 06 ммоб и глубине резания t = 197 мм мощность N = 71 кВт что меньше 75кВт (по табл. П13 [10]).
Четвёртая ступень: 61
При подаче инструмента S = 06 ммоб и глубине резания t = 2 мм мощность N = 72 кВт что меньше 75кВт (по табл. П13 [10]).
При подаче инструмента S = 04 ммоб и глубине резания t = 4 мм мощность N = 71 кВт что меньше 75кВт (по табл. П13 [10]).
Шестая ступень: 1856
следовательно обработка по диаметрам возможна за 8 проходов.
При подаче инструмента S = 06 ммоб и глубине резания t = 165 мм мощность N = 71 кВт что меньше 75кВт (по табл. П13 [10]).
Выбор и расчёт режимов резания.
1. Токарная обработка.
При черновом обтачивании применяем проходной резец с главным углом в плане φ = 450 стойкостью Т = 60 мин из материала Т15К6.
-для чернового обтачивания принимаем значение подачи из пункта 7.1.
-для получистового обтачивания:
. SТАБЛ = 087 при Rz = 40. (по табл. П11 [10])
где К3 = 045 (по табл. П11 [10])
Из нормального ряда продольных подач суппорта станка принимаем значение S = 04 ммоб.
Cv - коэффициент скорости зависящий от значения величины подачи.
Принимаем согласно (по табл. П14 [10]);
Т – расчётная стойкость резца в минуту. Принимаем согласно (по табл. П13 [10]);
t – глубина резания;
Коэффициент корректировки.
КMV – коэффициент учёта влияния материала заготовки на скорость резания; КПV – коэффициент учёта влияния состояния поверхности на скорость резания (по табл. П18 [10]);
КИV – коэффициент учёта влияния инструментального материала на скорость резания для материала Т15К6 (по табл. П19 [10]);
КφV – коэффициент учёта влияния главного угла в плане резца на скорость резания (по табл. П20 [10]).
КГ - коэффициент характеризующий группу стали по обрабатываемости.
Принимаем согласно (по табл. П17 [10]);
- предел выносливости. Принимаем согласно [4 табл.2] =600 МПа
nv – показатель степени. Принимаем согласно (по табл. П16 [10]).
Результаты вычислений сведены в таблицу 9.
3. Расчёт режимов шлифования.
Шлифование выполняем на шлифовальном станке 3Б151 который имеет следующие характеристики:
-наибольший диаметр и длина шлифуемой заготовки: 180 х 630(800) мм;
-диаметр и ширина шлифовального круга: 600 х 63 мм;
-частота вращения детали: 63 400 обмин (бесступенчатое регулирование);
-скорость продольного перемещения рабочего стола: 01 06 ммин (бесступенчатое регулирование);
-поперечная подача шлифовального круга (глубина шлифования): 00025 005 мм на один ход рабочего стола с шагом 00025 мм;
-непрерывная подача шлифовального круга при врезном шлифовании: 01 2 мммин;
-мощность электродвигателя привода шлифовального круга: 7 кВт.
3.1. Расчёт режимов предварительного шлифования.
Согласно [32] с. 302 для предварительного шлифования принимаем:
-скорость вращения шлифовального круга: vШЛ.КР. = 30 мс;
-скорость вращения заготовки: vЗАГ. = 20 ммин;
-продольная подача шлифовального круга: S = (03 07)ВШЛ.КР. = 189 441 ммоб. Принимаем S = 30 ммоб;
-глубина шлифования tШЛИФ = 001 мм;
-количество проходов шлифовального круга:
Частота вращения шлифовального круга:
Частота вращения заготовки:
Результаты вычислений сведены в таблицу 10.
3.2. Расчёт режимов окончательного шлифования.
Согласно [32] с. 302 для окончательного шлифования принимаем:
-скорость вращения шлифовального круга: vШЛ.КР. = 35 мс;
-скорость вращения заготовки: vЗАГ. = 35 ммин;
-продольная подача шлифовального круга: S=(02 04)ВШЛ.КР.=126 256 моб. Принимаем S = 20 ммоб;
-глубина шлифования tШЛИФ = 0005 мм;
В ходе расчетно-пояснительной записки был разработан технологический процесс на изготовление детали – шток для единичного условия производства. В работе были применены технологические оборудования и инструменты: токарный станок 16К20 шлифовальный станок 3Б151 и резец Т15К6.
Оформлена технологическая документация на операции и переходы применяемые в ходе получения детали. Установлены и применены в ходе разработки техпроцесса основные принципы и приемы используемые при обработке металлов резанием.
Список литературы.docx
М.: «Высшая школа» 1983
Справочник технолога-машиностроителя: 3-е издание в 2-х т. под ред. Косиловой А.Г. Мещерякова Р.К. -М. “Машиностроение” 1972.
Справочник технолога-машиностроителя: 4-е издание в 2-х т. под ред. Косиловой А.Г. Мещерякова Р.К. -М. “Машиностроение” 1985.
Краткий справочник металлиста 3-е издание под ред. Орлова П.Н. Скороходова Е.А. -М.: «Машиностроение» 1987.
Панов А.А. Обработка металлов резанием. Справочник технолога -М.: «Машиностроение» 1988.
Дальский А.М. Справочник технолога-машиностроителя: в 2-х т. -М.: «Машиностроение» 2004.
Технология машиностроения: в 2-х т. т. 1. Основы технологии машиностроения Бурцев В.М. Васильев А.С. Дальский А.М. и др. – М.: МГТУ им. Н.Э. Баумана 1999.
Конструирование узлов и деталей машин под ред. Дунаева П.Ф. Леликова О.П. М.: Издательский центр “Академия” 2003.
Справочник технолога авторемонтного производства. – М.: «Транспорт» 1977.
Проектирование технологических процессов изготовления деталей подъёмно-транспортных строительных и дорожных машин. 2-я часть В.И. Фомин – М: «МИИТ» 2009.
таблица.docx
Диаметр поверхности мм
Расчётное значение n мин-1
Принятое значение n мин-1
- Установ В (черновое обтачивание)
- Установ Г (черновое обтачивание)
- Установ Г (получистовое обтачивание)
- Установ Д (получистовое обтачивание)
Режимы шлифовальной обработки вала.
Расчётная мощность N кВт
- Установ А (шлифование окончательное)
- Установ Б (шлифование окончательное)
Конструкторская часть.docx
Расчет сопротивлений передвижению тележки крана-штабелера с грузом.
Приведенная ниже методика и нормы расчета применяются для механизмов передвижения кранов и грузовых тележек перемещающихся по рельсовому пути.
Полное сопротивление передвижению крана:
Wртр – сопротивление трения при движении крана с учетом трения роликов;
Wтр – сопротивление трения при движении крана без учета трения реборд
kр – коэффициент учитывающий сопротивление трения реборд ходовых колес крана о головку рельсов (при подшипниках скольжения – трения торцов ступиц колеса) при движении крана (табл.5.1.1.) т.к. колесо безребордное то kр = 1.
Wук – сопротивление от уклона подкрановых путей;
Wв – сопротивление от действия ветровой нагрузки.
Качения и скольжения
Передвижения тележки
Сопротивление трения определяется по формуле:
Q = 1000 – вес номинального груза кг;
G= 3250 – собственный вес крана кг;
Dх.к.= 200 – диаметр ходового колеса мм;
d = 45 – диаметр цапфы вала ходового колеса мм;
dр = 150 – диаметр ролика мм
= 003 – коэффициент трения качения (табл.5.1.2.стр134)
f = 0015 – коэффициент трения в подшипниковых опорах ходовых колес; значения f принимают:
Для подшипников скольжения открытого типа010
Для букс с жидкой смазкой008
Для шариковых и роликовых подшипников0015
Для конических подшипников качения002
Определим сопротивление трения:
Определим силу трения ролика:
Диаметр ходового колеса мм
для стальных колес см
для чугунных колес см
Сопротивление от уклона подкрановых путей:
Расчетные уклоны подкрановых путей α принимают:
Для путей с железобетонным фундаментом на металлических балках0001
Для путей с щебеночным основанием и деревянными шпалами0002
Для подтележечных путей на мосту крана0002
Так как наш кран-штабелер работает в помещении то Wв = 0
Найдем полное сопротивление передвижению крана:
Расчет сопротивлений передвижению тележки крана-штабелера без груза.
Так как кран-штабелер работает в помещении то Wв = 0
Полное сопротивление передвижению крана без груза:
Выбор мотор-редуктора.
Выбор мотор-редуктора для механизма передвижения крановых тележек производят по максимально допустимому пусковому моменту двигателя при котором обеспечивается надлежащий запас сцепления ходового колеса с рельсом исключающий возможность буксования при передвижении тележки без груза в процессе пуска.
Допустимое значение ускорения тележки:
φ = 02 – коэффициент сцепления ходового колеса с рельсом;
Рв= 0 – ветровая нагрузка на кран в рабочем состоянии;
g – ускорение силы тяжести;
nпр – число приводных ходовых колес;
nк – общее число ходовых колес.
Определим мощность двигателя по статическому сопротивлению при перемещении тележки с номинальным грузом:
vт = 25 мс = 150 ммин – скорость передвижения тележки;
= 09 – К.П.Д. передачи при установке ходовых колес на подшипниках качения.
Число оборотов ходовых колес:
Конический мотор-редуктор
BK20-54VUDHE09XA4C-TF-SESX027A9HAS40
Скорость ведущего вала
Направление клеммной коробки
Вес нетто (базовая сборка) 1 шт
Конструкцияисполнение
Исполнение редуктора
Конический редуктор BK20
моментный рычаг спереди вниз
полый вал с пазом под шпонку ø 40.00 mm
с установленным сапуном
Доп. спец. исполнение
Резиновые буферы для моментного рычага
Исполнение двигателя
Трехфазный электродвигатель DHE09XA4C
Напряжениесоединение
Номинальная скорость
Класс защиты по IP в соотв. с EN 60529
Коэффициент мощности (cosphi)
охлаждение EN 60034-6
IE_CODE_NACH_EN60034-30
Конструкция во соответствии с DIN VDE 0530-1EN 60034-1
Однодисковый тормоз с пружинами ESX027A9
Номинальный тормозной момент
Класс защиты по IP в соотв. с EN 60 529
с Стандарт -Выпрямитель (встроенный в клеммную коробку двигателя)
Напряжение питания AC 50Hz
HA ручной отпуск с блокировкой
Основные параметры электродвигателя
Номинальная мощность (PN): 22 кВт
Номинальная частота вращения вала ротора (n): 1440 обмин
Номинальный вращающий момент вала ротора (MN): 145 Нм
Момент инерции массы ротора (Jrot): 00053 кгм2
Режим работы: продолжительный S1
Основные параметры мотор-редуктора
Тип редуктора: BK2(конический редуктор)
Скорость ведущего вала: 240 обмин
Крутящий момент (Mк): 80 Нм
Передаточное число (i): 602
Масса мотор-редуктора (m): 556 кг
Основные параметры тормоза
Тип тормоза: ESX027A9 (однодисковый тормоз с пружинами)
Тормозной момент: 22 Нм
Момент инерции масс тормозного диска: 0000172 кгм2
Фактическая скорость передвижения тележки:
Требуемая при этом мощность двигателя:
что соответствует мощности выбранного двигателя.
Время пуска при максимально допустимом ускорении:
Что находиться в допустимых пределах от 05 сек. до 5 сек.
Момент сопротивления при передвижении тележки без груза:
Маховой момент двигателя
Маховой момент диска тормоза
Маховой момент вращающихся движущихся масс
Маховой момент поступательно движущихся масс
Общий маховой момент
Необходимый пусковой момент:
Номинальный момент двигателя
Фактическое время пуска
Тормозной момент механизма передвижения определяют при обеспечении надлежащего сцепления ходового колеса с рельсом которое исключило бы возможность юза при торможении тележки движущейся с номинальной скоростью без груза.
Максимально допустимое замедление при котором обеспечивается заданный запас сцепления ходовых колес с рельсом:
Уравнение моментов при торможении
Мтсо – момент сопротивления передвижению тележки без груза при торможении
Сопротивление передвижению при торможении
Момент сопротивления приведенный к валу тормоза:
Инерционный момент при торможении вращающихся и поступательно движущихся масс:
Тогда тормозной момент:
При снижении скорости перед остановкой крана-штабелера для увеличения его точности относительно ячейки устанавливаем преобразователь на число оборотов двигателя в доводовом режиме 350 обмин.
То инерционный момент при торможении вращающихся и поступательно движущихся масс:
Т.к. тормоз ESX027A9 имеет номинальный тормозной момент 22 Нм то найдем скорость передвижения тележки с номинальным тормозным моментом.
Применим уравнение моментов при торможении
То инерционный момент торможения будет равен:
Определим время торможения через инерционный момент при торможении
Определим максимальное замедление тележки при tт = 295 с
Номинальный тормозной момент механизма передвижения не исключает возможность юза при максимальном замедлении тележки. Для исключения возможности юза требуется уменьшить скорость передвижения тележки.
Расчет механизма подъема.
Для расчета механизма подъема кроме его основных параметров (грузоподъемности Q скорости v подъема груза высоты подъема груза) должны быть заданы режим работы механизма и его кинематическая и конструктивная схемы.
Определение усилий в канате
Принципиальная схема полиспаста механизма подъема приведена на рис.5.1.2
Рис. 5.1.2. Схема полиспаста
Натяжение каната при подъеме каретки с грузом:
Qкар = 558 – вес каретки кг;
Qгр = 1000 – вес груза кг;
m = 1 – число полиспастов;
бл- К.П.Д. блока полиспаста учитывающий потери в опорах блока а также потери вызываемые жесткостью каната.
кар = 09 – К.П.Д. каретки;
Z = 3 – число направляющих блоков.
Натяжение каната при подъеме каретки без груза:
Расчет каната по Правилам Госгортехнадзора проводим по формуле:
k – запас прочности принимаемый по Правилам Госгортехнадзора в зависимости от назначения каната и режима работы механизма; для грузовых канатов при тяжелом режиме работы k=6;
Рраз – разрывное усилие каната в целом принимаемое по таблицам ГОСТа.
При выборе каната нужно соблюдать условие:
Pст – разрывное усилие по стандарту
По таблицам на канаты ГОСТа 2688-69 выбираем канат типа ЛК-Р 6×19 = 114 диаметром 15 мм имеющий при расчетном пределе прочности проволоки при растяжении равном 160 кгмм2 разрывное усилие Рст = 11700 кг.
После выбора каната проверяют фактический запас его прочности
Фактический запас прочности:
Определение основных размеров и числа оборотов барабана
Минимально допустимый диаметр барабана измеренный по дну канавки для каната определяется по формуле:
e – коэффициент принимаемый по Правилам Госгортехнадзора в зависимости от типа грузоподъемной машины и режима ее работы. Для нашего случая e = 30;
dк = 15 – диаметр каната мм.
Так как увеличение диаметра барабана приводит к повышению долговечности каната то примем диаметр барабана Dб = 560 мм.
Число витков нарезки на барабан:
H = 12 – высота подъема груза м;
Uп= 2 – кратность полиспаста.
Длина нарезки на барабан:
Оставляем на закрепление каната с одной стороны барабана расстояние s равное длине не менее четырех шагов нарезки. При tб = 17 мм примем s = 68 мм.
Тогда общая длина барабана:
Скорость каната навиваемого на барабан при скорости груза 120 ммин
Число оборотов барабана в минуту:
Определяем статическую мощность двигателя при подъеме номинального груза:
= 09 – общее значение К.П.Д.
Проверка барабана на прочность
В барабанах при соотношении параметров напряжения изгиба и кручения незначительны.
В этих условиях проверке подлежат лишь напряжения сжатия:
- толщина оболочки стального барабана.
Плоский цилиндрический мотор-редуктор
BF70-04DHE18XA4-TF-SZSX500A9HAK70
Плоский цилиндрический редуктор BF70
полый вал с пазом под шпонку ø 70.00 mm
Трехфазный электродвигатель DHE18XA4
Двухдисковый тормоз с пружинами ZSX500A9
Номинальная частота вращения вала ротора (n): 1470 обмин
Номинальный вращающий момент вала ротора (MN): 142Нм
Момент инерции массы ротора (Jrot): 0195кгм2
Тип редуктора: BF70-04(цилиндрический редуктор)
Скорость ведущего вала: 143обмин
Крутящий момент (Mк): 1460Нм
Передаточное число (i): 1032
Масса мотор-редуктора (m): 449 кг
Тип тормоза: ZSX500A9 (двухдисковый тормоз с пружинами)
Тормозной момент: 400 Нм
Момент инерции масс тормозного диска: 00133 кгм2
Проверка электродвигателя по времени пуска
Фактическая скорость подъема груза:
Правила Гостехнадзора регламентируют максимальные ускорения для кранов в пределах
Предполагая процесс пуска равноускоренным при заданной скорости подъема 120 ммин допустимое время пуска:
Определяем средний пусковой момент выбранного двигателя:
ср – средняя перегрузочная способность электродвигателя в период разгона с учетом нормального падения напряжения
max – максимальная перегрузочная способность электродвигателя
Определим статический момент от сил тяжести масс груза и каретки приведенный к валу мотор-редуктора:
Определяем маховой момент двигателя
Определяем маховой момент диска тормоза
Определяем маховой момент вращающихся масс
Определяем условный маховой момент поступательно движущихся масс
Определяем фактическое время пуска:
Проверка тормозного момента
где k – коэффициент запаса торможения принимаемый согласно Правилам Госгортехнадзора для тяжелого режима работы равным 2;
Мтс– статический крутящий момент на тормозном валу при торможении определенный в предположении равномерного распределения нагрузки между всеми ветвями полиспаста с учетом потерь в механизме способствующих удержанию груза;
Минимально допустимый диаметр блока:
Нагрузка на один подшипник при максимальном грузе:
- динамический коэффициент; - число блоков; - коэффициент вращения (при вращении наружного кольца подшипника )
Расчет механизма передвижения вил.
рис. 5.1.3. Схема привода передвижения вил
Оптимизация энергозатрат при гидроприводе должна производиться по двум параметрам: рабочему давлению и расходу рабочего тела раздельно. Привод телескопического захвата крана-штабелера осуществляется от нерегулируемого насоса (1) имеющего постоянную частоту вращения рабочего вала. В результате оптимизации показателя необходимо добиться выполнения условия наиболее полной загрузки электродвигателя насосной станции по мощности. Здесь необходимо сделать следующие предпосылки:
Установочная мощность приводной станции минимальна при минимуме рабочего давления и расхода рабочего тела т.е. p m
Энергозатраты минимальны при постоянстве минимальных значений давления и расхода в течение цикла т.е. при pmin= const Qmin= const.
Выбор гидроцилиндра.
Установлено что устойчивость движения горизонтально расположенных гидроцилиндров может быть обеспечена лишь при соотношении:
Dц – диаметр цилиндра;
S – ход штока цилиндра.
L – перемещение вил;
U = 2 – передаточное число.
Перемещение вил складывается из длины поддона и зазора между концом вил и стеллажом.
Рекомендуемая скорость поршня должна быть не более 05 мс поэтому время выполнения операции имеет ограничение:
Принимаем Dц = 32 мм. При данном захвате зазор между концом вил и стеллажом 006 м.
Сопротивление при выдвижении вил и нагнетании в штоковую полость без прогиба:
Gз = 25 – собственный вес захвата кг;
dр= 4 – диаметр роликов см;
= 003 – коэффициент трения качения.
Сопротивление при возврате вил с учетом уклона и с нагнетанием в поршневую полость:
Давление страгивания и холостого хода при максимальном сопротивлении передвижению вил:
Площадь поршня со стороны штоковой полости:
φ = 165 – коэффициент отношения площадей со стороны поршневой и штоковой плоскостей.
Расход рабочего тела при параллельной работе цилиндров:
V – объем рабочего тела потребляемый в течение времени Т находим как произведение площади поршня на ход поршня:
Рабочий объем штоковой полости:
Максимальный расход штока:
Давление в штоковой полости:
Давление в поршневой полости:
В каталоге выберем гидроцилиндр типа ЦРГ32*16*s:
номинальное давлением 16 МПа;
максимальное давление 20 МПа;
давление страгивания 1 МПа;
Номинальная мощность на валу насоса:
Из каталога по номинальной подаче и мощности выберем насос типа НПл 4063:
рабочий объем 40 см3;
номинальная подача 357 лмин;
номинальное давление на выходе 63 МПа;
номинальная частота вращения 950 обмин;
максимальная частота вращения 1500 обмин;
минимальная частота вращения 600 обмин;
номинальная мощность 43 кВт;
Выбор электродвигателя.
Мощность электродвигателя в зависимости от подачи насоса определяется по формуле:
Q – подача насоса лмин;
P – давление в напорной линии МПа;
п – полный КПД насоса.
N = 146*357 60*085 = 102 кВт
По каталогу на электродвигатели выберем электродвигатель типа 4А80А4 с номинальной мощностью 11 кВт.
Выбор гидрораспределителя.
Из каталога выберем (Р1) гидрораспределитель В6:
диаметр условного прохода 6 мм;
номинальное давление 6 МПа;
максимальное усилие управления на рукоятке 45 Н.
Из каталога выберем (Р2) гидрораспределитель ВЕ6 схема 574.В220.УХЛ.4
Для пластинчатого нерегулируемого насоса с давлением
до 63МПа выберем приемный (сетчатый) фильтр с номинальной тонкостью фильтрации 40 мкм.
Выбор клапана давления.
Выберем гадроклапан давления Г54-32М:
-номинальный расход масла 32 лмин;
-номинальный перепад давлений 02 МПа;
-максимальное давление на входе 20 МПа.
Т.к. система передвижения вил – это система низкого давления (до 25 МПа) то используем аллюминивые трубы по ГОСТ 18475-82 длинной 3м.
Исходя из расхода гидроцилиндров и рабочего объема насоса выберем бак вместимостью 200 л.
Расчет гидравлического буфера
Буферное устройство предназначено для ограничения перемещения крана-штабелера вдоль стеллажей путем поглощения кинетической энергии крана-штабелера.
Задачей расчета является определение необходимого количества отверстий их диаметра и координат по длине цилиндра обеспечивающих постоянное заданное значение среднего замедления 4 мс2 в процессе торможения при амплитуде пульсаций тормозного усилия не более 20%.
Рассмотрим наиболее неблагоприятный случай: кран-штабелер с номинальным грузом движется на полной скорости двигатель привода передвижения при заезде крана-штабелера на конечный упор продолжает работать.
Определение расчетного количества отверстий вдоль образующей цилиндра
с учетом обозначений
v = 25 мс – расчетная скорость движения крана-штабелера;
m = 4250 кг – масса крана-штабелера номинальная с грузомноминальным;
= 4 мс2 – расчетное замедление;
R = 342 Н – сопротивление передвижениюкрана-штабелера;
с = 2 Нм – жесткость возвратной пружины;
λ = 0012 м – предварительное поджатие пружины;
= 085 кгм3 – плотность рабочей жидкости;
= 06 – коэффициент расхода; для конусообразного диффузора с углом при вершине 90;
D = 008 м – диаметр поршня;
d = 0004 м– диаметр отверстия;
z = 1 – количество одновременно работающих буферов;
P = 325 Н – усилие привода передвижения;
k – коэффициент сцепления
Дробная часть n1 числа n реализуется как отверстие диаметром:
которое располагается вблизи днища цилиндра.
Координату центра i-го отверстия отсчитываемую от торца поршня в его начальном положении вычисляют по формуле:
i – порядковый номер отверстия.
Определение скорости поршня при прохождении i-го отверстия
Si – координата центра i-го отверстия
Определение усилия на штоке непосредственно перед i-м отверстием
Определение усилия на штоке сразу же после прохождения i-го отверстия
Определение среднего значения усилия на штоке
Определение коэффициента пульсации усилия на i-ом отверстии
Определение допускаемого усилия на штоке из условия прочности цилиндра
D1 = 0093 м – наружный диаметр цилиндра;
– коэффициент учитывающий концентрацию напряжений у отверстий; рекомендуемое значение равно 08;
т = 360106 Па – предел текучести материала цилиндра;
φ – коэффициент запаса прочности; рекомендуемое значение равно 15.
Для отверстий отстоящих от днища цилиндра более чем на величину диаметра поршня должно выполняться условие:
Сравнив усилие на штоке сразу же после прохождения отверстия (max) и допускаемое усилие 1302 144820 мы видим что условие выполняется.
Пояснительная записка.docx
В народном хозяйстве нет предприятий не имеющих в своем составе складов. А в такой отрасли как материально-техническое снабжение склады являются основными производственными подразделениями.
Склады в системе материально-технического снабжения должны обеспечивать в установленном ритме основное производство материально-техническими ресурсами в потребных количествах и ассортименте. Причем поставка продукции должна осуществляться в объемах менее транзитных норм отгрузки чтобы не создавать излишних производственных запасов на промышленных предприятиях. Наиболее распространенной складской продукцией являются тарно-штучные грузы к которым обычно относят грузы любых видов упакованные в тару и хранимые на поддонах в ящичной таре или в контейнерах.
На грузовых фронтах всех складов выполняют погрузочно-разгрузочные операции которые отличаются высокой интенсивностью особенно в пунктах стыка различных видов транспорта. Под влиянием технического прогресса и прежде всего развития вычислительной и подъемно-транспортной техники крупные складские системы превращаются в современные предприятия с четко организованным автоматизированным технологическим процессом – транспортно-складские (грузовые) комплексы (ТСК). Четкий ритм их функционирования обеспечивают сложные автоматизированные поточно-транспортные системы (ПТС) которые по структуре и масштабам напоминают автоматизированные поточные технологические линии современных промышленных предприятий. ПТС состоят из конвейеров упаковочных пакетоформирующих и пакеторазборочных агрегатов автоматизированных складских и погрузочно-разгрузочных машин накопителей и др. Классификация ТСК по функциональному принципу дана на рис. 1. Могут быть также предложены в зависимости от потребностей практики другие частные признаки классификации например тип подъемно-транспортного оборудования вариант объемно-планировочного решения взаимное расположение погрузочно-разгрузочных путей и автопроездов и др.
Рис.1 . Классификация транспортно-складских комплексов
Склады представляют собой сложное хозяйство оснащенное высокопроизводительным специальным оборудованием. До недавнего времени основными средствами механизации работ на складах тарно-штучных грузов служили мостовые краны напольные погрузчики и штабелеры. Однако по мере роста потребности в складских помещениях все более очевидными стали недостатки напольных погрузочно-разгрузочных машин – необходимость в устройстве широких проходов для движения погрузчиков и штабелеров и ограниченная высота подъема груза.
Поиски оборудования обеспечивающего максимальное использование складских помещений удобство доступа к грузам и высокую производительность привели к созданию различных систем складирования грузов. Наибольшее распространение получили системы с кранами-штабелерами укладывающими грузы в стеллаж с помощью грузозахватных устройств.
Краны-штабелеры позволяют рационализировать складское хозяйство экономить площади высвободить значительное количество вспомогательных рабочих и открывают широкие возможности для автоматизации складирования.
Краны-штабелеры применяют в самых различных отраслях промышленности но особенно эффективно – в машиностроении металлургической промышленности материально-техническом снабжении.
Краны-штабелеры применяют в таких отраслях в которых ранее использовали лишь традиционные подъемно-транспортные машины.
Основным видом подъемно-транспортного оборудования складов стеллажного типа являются мостовые краны-штабелеры и стеллажные штабелеры(рис. 2). Практика и исследования показывают что мостовые краны-штабелеры целесообразно применять при высоте стеллажей до 10-12 м; при более высоких стеллажах более экономичными являются стеллажные штабелеры.
Рис. 2. Схема стеллажного крана-штабелера установленного на складе: 1 – подающие роликовые конвейеры; 2 – поворотная секция роликового конвейера; 3 – контроль размера пакетов; 4 – распределительный конвейер; 5 – площадка для установки грузов; 6 – стеллажный кран
Мостовой кран-штабелер имеет вертикальную колонну 5 подвешенную к грузовой тележке 4 перемещающейся по мосту 3 передвигающемуся по крановым рельсам 1 (рис. 3 а). По колонне перемещается грузозахватное устройство в виде вил 6 а нередко и кабина крановщика. Подъем (и опускание) кабины может осуществляться тем же механизмом что и подъем груза. Находят применение раздельные механизмы подъема кабины и груза. Один такой кран-штабелер может обслуживать группу стеллажей и даже весь склад.
Стеллажный кран-штабелер имеет вертикальную колонну перемещающуюся между стеллажами (рис. 3 б). В этих кранах тележка передвигается по рельсам уложенным на стеллажах. Грузоподъемное устройство перемещающееся по колонне должно обслуживать оба стеллажа (правый и левый). Если колонна будет выполнена поворотной то требуется увеличить расстояние между стеллажами. Грузозахватное устройство выполнено выдвижным.
Стеллажные краны могут перемещаться по напольному рельсовому пути.
По способу опирания на рельсовый путь краны-штабелеры бывают опорными или подвесными (рис. 4 и 5). Это деление является условным. Подвесной кран-штабелер подвешен к ходовым тележкам.
Рис. 3. Краны-штабелеры: а – мостовой; б – стеллажный
Рис. 4. Краны-штабелеры мостового типа: а – опорный; б — подвесной
Грузоподъемность кранов-штабелеров обычно не превышает 5 т но находят применение краны-штабелеры грузоподъемностью более 10 т.
Высота подъема отечественных кранов составляет 10 м. Скорость подъема 8—12 ммин. Скорость передвижения моста 50 ммин (при управлении с пола только 36 ммин) скорость передвижения тележки 12—20 ммин. Частота вращения колонны 4 обмин. Одной из особенностей кранов-штабелеров по сравнению с обычными крюковыми кранами является точная остановка всех механизмов. Поэтому при достаточно высоких рабочих скоростях предусматривается возможность движения с пониженными (доводочными) скоростями. В отечественных кранах доводочные скорости: подъема 4 ммин передвижения моста 10 ммин передвижения тележки 5 ммин.
Рис. 5. Стеллажные краны-штабелеры:
а -- подвесной; б — опорный велосипедного типа; в — опорный с опорой на стеллажи
Обзор существующих конструкций и выбор рациональной схемы крана-штабелера.
Стеллажные краны-штабелеры представляют собой широкую группу кранов-штабелеров которые могут устанавливать грузы в один стеллаж расположенный вдоль крановых путей или в два стеллажа расположенные по обе стороны крановых путей. Стеллажным называется кран-штабелер с вертикальной колонной перемещающейся в проходе между стеллажами.
Стеллажные краны-штабелеры являются наиболее эффективным складским оборудованием и интерес к ним проявляемый со стороны потребителей и поставщиков предопределил интенсивное развитие производства этих кранов-штабелеров.
Краны-штабелеры грузоподъемностью 1 т. представляют собой двухколонную раму передвигающуюся по подвесному пути укрепленному на стеллажах. По раме вертикально перемещается грузоподъемник. В нижней части рамы установлены ролики которые катятся по направляющим рельсам и удерживают кран-штабелер в вертикальном положении. Рама подвешена на двух приводных каретках. Каждая каретка имеет два электродвигателя мощностью 018 и 08 кВт оборудованных электромагнитными тормозами дифференциальный редуктор и две пары ходовых колес причем одна пара – приводная.
Приводные каретки сообщают крану-штабелеру скорость 60 ммин при одновременной работе двух электродвигателей и скорость 10 ммин при работе одного (малого) электродвигателя. На верхней балке рамы установлен привод механизма подъема состоящий из электротали оборудованной двухскоростным электродвигателем мощностью 50 кВт.
Грузоподъемник движется вдоль рамы крана-штабелера по направляющим рельсам с помощью четырех пар роликов охватывающих эти рельсы. На верхней поперечной балке грузоподъемника установлен подпружиненный канатный блок соединенный тягами с клиновыми ловителями охватывающими направляющие рельсы. При обрыве несущего каната или поломке механизма подъема происходит заклинивание ловителей и посадка грузоподъемника на раму крана.
Кабины кранов-штабелеров изготовляли двух исполнений: полуоткрытой применяемой в отапливаемых складах с температурой не ниже +50 и закрытой используемой в не отапливаемых складах. Закрытая кабина имела теплоизоляцию и была оборудована приборами отопления.
Конструкция описанного крана-штабелера характерна для всех подвесных кранов-штабелеров. Преимущества их предопределившие достаточно широкое применение заключались в следующем: простая и технологичная конструкция рамы; удобство установки и крепления ходовых механизмов и механизма подъема; возможность использования узлов и механизмов монорельсового транспорта.
Однако длительная эксплуатация стеллажных подвесных кранов-штабелеров различных конструкций изготовленных многими фирмами выявила ряд общих для них недостатков:
во-первых интенсивное изнашивание ходовых колес и монорельсовых путей особенно при увеличившихся до 100-120 ммин скоростях передвижения;
во-вторых значительное недоиспользование высоты склада обусловленное необходимостью разместить под монорельсом верхнюю несущую балку рамы привод механизма подъема и другие механизмы;
в-третьих неудобство эксплуатации связано с размещением основных механизмов в верхней части крана-штабелера и трудностью доступа к ним обслуживающего персонала.
В связи с этим выпуск подвесных стеллажных кранов-штабелеров был прекращен. Их заменили более совершенными опорными.
Рис.2. Одноколонный стеллажный кран-штабелер передвигающийся по рельсовым путям уложенным на стеллажи:
– телескопические захваты; 2 – грузоподъемник; 3 – кабина; 4 – колонна; 5 – тележка крана; 6 – привод передвижения; 7 – привод подъема; 8 – рельсы передаточной тележки; 9 – передаточная тележка; 10 – крановый рельс; 11 – стеллаж; 12 – направляющие рельсы.
Как одно из направлений в дальнейшем развитии конструкции стеллажных кранов-штабелеров можно рассматривать появление кранов-штабелеров опирающихся на рельсы уложенные в стеллажи. Например одноколонный кран-штабелер (рис.2.). Рельсы для него укладывают на верхние планки стеллажей и крепят к ним болтами. При этом должна быть обеспечена высокая точность их монтажа ( отклонение – не более 2мм). Колея рельсовых путей в зависимости от размеров перерабатываемого груза и прохода между стеллажами составляет 15 – 25 м. По крановым рельсам передвигается тележка крана-штабелера несущая на себе основные механизмы: приводы подъема и передвижения шкаф с электроаппаратурой. К тележке крепят колонну или сплошного сечения ( на кранах-штабелерах малой грузоподъемности) или решетчатую (на кранах-штабелерах большой грузоподъемности).
Опирающиеся на стеллаж краны-штабелеры имеют лучшие чем подвесные краны-штабалеры условия работы благодаря катанию ходовых колес по крановым рельсам а также возможности увеличить их диаметры. Однако их конструкции присущи серьезные недостатки:
во-первых это верхнее расположение механизмов (недостаток подвесных кранов-штабелеров)
во-вторых - высокие требования предъявляемые к монтажу направляющих путей.
Действительно при большой высоте подъема груза небольшая разность установки крановых путей по вертикали приводит к значительному отклонению нижнего конца колонны от среднего положения. При установке направляющего пути в этом случае могут появляться нежелательные нагрузки от перекоса металлоконструкции крана-штабелера.
Основным преимуществом опирающихся на стеллажах кранов-штабелеров является относительно простая конструкция передаточных тележек которые предназначены для перемещения кранов-штабелеров из одного межстеллажного прохода в другой.
Передаточные тележки обычно изготовляют в виде четырехколесной платформы перемещающейся по двум рельсам проходящим поперек фронта стеллажей под перекрытием склада. Один из рельсов устанавливают на стеллаж а другой крепят непосредственно к перекрытию склада. На передаточных тележках направляющие рельсы не предусматривают так как возможный перекос колонны крана-штабелера установленного на тележке не имеет существенного значения. От рамы тележки вниз опускаются короткие кронштейны несущие участок крановых путей который стыкуется с крановыми путями расположенными на стеллажах.
Передаточная тележка с краном-штабелером грузоподъемностью 1 т. изготовлена в виде сварной рамы передвигающейся по двум крановым путям один из которых установлен на стеллажах другой на специальных металлоконструкциях. Рама тележки несет на себе участок крановых рельсов для передвижения крана-штабелера оканчивающихся стыковыми замками запирающими кран-штабелер при передвижении на передаточной тележке.
В настоящее время большинство фирм перешло к выпуску стеллажных кранов-штабелеров перемещающихся по одному крановому пути установленному на полу склада. В верхней части кранов-штабелеров устанавливают направляющие ролики которые перемещаются по направляющему пути и удерживают кран-штабелер в вертикальном положении. Опорные (на пол) стеллажные краны-штабелеры по компоновке представляют собой одноколонную или двухколонную конструкцию имеющую нижнюю ходовую балку с двумя безребордными колесами одно из которых – приводное. К балке крепят одну или две вертикальные колонны заканчивающиеся направляющими роликами охватывающими с двух сторон направляющий путь углового или чаще двутаврового профиля. При двух колоннах краны-штабелеры имеют в верхней части продольную балку которая связывает их и образует таким образом замкнутую прямоугольную конструкцию. На нижней балке или на нижней части колонны устанавливают канатный или цепной механизм подъема с помощью которого осуществляется вертикальное перемещение грузоподъемника совместно с кабиной оператора. Подобная конструкция ставшая классической имеет несомненные преимущества перед описанными выше подвесными и опирающимися на стеллаж кранами-штабелерами.
При перемещении крана-штабелера по специальному крановому рельсу с помощью двух безребордных колес оборудованных горизонтальными роликами катящимися по боковым граням рельса изнашивание как ходовой части крана-штабелера так и рельса в том числе и при высоких (120 – 160 ммин) скоростях перемещения минимально. Причем возможно применение ходовых колес достаточно большого диаметра что в свою очередь позволяет уменьшить сопротивление перемещению и улучшить энергетические показатели механизма передвижения. При расположении в нижней части крана-штабелера всех механизмов и электрооборудования улучшаются условия доступа к этим механизмам при эксплуатации. Крановый путь установленный на полу склада (в межстеллажном проходе) позволяет создать более благоприятные условия для монтажа данного типа крана-штабелера (по сравнению с другими типами). чч Монтаж кранов-штабелеров сводится к установке на крановый путь опорной балки со смонтированными на ней механизмами и установке на эту балку колонны с помощью стрелового автомобильного крана или с помощью электрической или ручной тали подвешиваемой к направляющему пути.
Однако главным преимуществом опирающихся на пол стеллажных кранов-штабелеров является более высокая степень использования высоты помещения чем при применении стеллажных подвесных и опирающихся на стеллаж кранов-штабелеров достигающая своего максимального значения в одноколонных кранах-штабелерах.
Претерпели значительное изменение и некоторые узлы кранов-штабелеров среди которых прежде всего следует отметить грузозахватные устройства. На первых конструкциях стеллажных кранов-штабелеров преимущественно использовали роликовые столы с помощью которых пакетированные грузы устанавливались на кран-штабелер и в стеллаж а также выдвижные и поворотные вилочные захваты. Применение кранов-штабелеров с роликовыми столами на складах с интенсивной работой оказалось неприемлемым прежде всего в результате тяжелых условий труда операторов.
Применение выдвижных (и поворотных) вилочных захватов подобных используемым на автопогрузчиках позволило полностью исключить ручной труд при пакетной переработке груза. Однако это влечет за собой увеличение прохода между стеллажами так как необходимо оставлять определенное место для крепления вилочных захватов. Поэтому получили распространение выдвижные телескопические захваты технологически более сложные чем вилочные но позволяющие создать проход между стеллажами минимальной ширины равной практически сумме ширины перерабатываемого груза и зазоров (по 50 – 100 мм на сторону) между грузом и стеллажом.
Телескопические захваты представляют собой три секции одинаковой длины из которых одна неподвижная а две другие подвижные. Причем секция которая несет на себе груз движется с увеличенной вдвое скоростью по отношению к промежуточной. Телескопические захваты могут выдвигаться в обе стороны поперек прохода.
Значительные изменения претерпела система управления кранов-штабелеров начиная от ручного управления оператором из кабины на первых кранах-штабелерах и кончая полностью автоматизированным управлением применяемым на стеллажных кранах-штабелерах последних поколений. Изменился принципиальный подход к конструированию приводных механизмов. Переход от ручного к автоматическому управлению и возросшие скорости перемещения обусловили переход от применения асинхронных электродвигателей к электродвигателям постоянного и переменного тока с тиристорным регулированием скорости а также к электродвигателям с микроприводом. Более широко стали применяться редукторы специально предназначенные для использования на кранах-штабелерах вместо редукторов общепромышленного применения.
Изменения в конструкции кабин операторов направлены в основном на улучшение условий труда создание комфортных условий и обеспечение безопасности в работе.
В настоящее время стеллажные краны-штабелеры являются высокопроизводительным надежным оборудованием которое отличает отработанность конструкции ее высокая технологичность тщательность отделки. Таким образом поиски наиболее оптимальных конструктивных решений завершились созданием современных стеллажных кранов-штабелеров имеющих много общего в конструкции но отличающихся один от другого техническим исполнением отдельных узлов деталей систем управления. Можно сделать предположение что дальнейшие конструктивные поиски будут направлены в основном на повышение надежности технологичности расширение функциональных возможностей системы управления.
Стеллажные краны-штабелеры изготовляют в настоящее время в различных странах. Конструктивные их решения обусловлены традициями технологическими возможностями наличием освоенного производства узлов подъемно-транспортных машин систем управления. В принципе компоновки стеллажных кранов-штабелеров однотипны.
Современный стеллажный кран-штабелер выполнен в виде нижней ходовой балки оборудованной двумя безребордными колесами к которой крепят одну или две колонны имеющие сверху горизонтально расположенные направляющие ролики. Если устанавливают две колонны то верхние их концы соединяют горизонтальной балкой. По колонне с помощью канатного или реже цепного привода механизма подъема перемещается консольно установленный грузоподъемник несущий кабину управления и выдвижной телескопический захват. На стеллажных кранах-штабелерах предназначенных для поштучного отбора грузов так называемых комплектовочных кранах-штабелерах вместо выдвижных телескопических захватов можно устанавливать гладкие или роликовые столы а также другие приспособления для укладки в стеллажи и отбора из стеллажей грузов.
Одноколонный стеллажный кран-штабелер имеет нижнюю ходовую балку на которой установлены приводное и холостое колеса. К балке крепят колонну на верхней части которой установлены горизонтальные ролики удерживающие кран-штабелер в вертикальном положении.
По колонне перемещается консольный грузоподъемник с кабиной оператора. Кабина оператора имеет небольшой свободный ход относительно грузоподъемника для того чтобы полностью использовать высоту склада. На два телескопических захвата грузоподъемника устанавливается груз. грузоподъемник по колонне перемещается с помощью канатного механизма подъема . шкаф с электрооборудованием соединен с колонной кронштейном.
Двухколонные стеллажные краны-штабелеры применяют при больших высоте подъема и грузоподъемности. Кран-штабелер имеет нижнюю опорную балку на которой установлены приводное и холостое колеса. К опорной балке крепят две колонны и соединенные верхними концами продольной балки. На этой балке установлены две пары горизонтальных роликов и механизм синхронизации применяемый для уменьшения амплитуды перемещения верхней части колонны относительно ее нижней части.
Между колонн перемещается грузоподъемник представляющий собой платформу с двух сторон оборудованную каретками ролики которых обкатываются по направляющим колонн. На грузоподъемнике установлена кабина оператора и выдвижные телескопические захваты служащие для установки в стеллажи пакетированного груза. грузоподъемник поднимается с помощью канатного механизма подъема который установлен на одной колонне а на второй – шкаф с электрооборудованием. Для обслуживания механизма подъема и механизма синхронизации на одной из колонн крепят рабочие площадки к которым по лестнице поднимается обслуживающий персонал.
Сравнивая схемы этих кранов нетрудно увидеть что использование полезной высоты склада при применении двухколонных кранов-штабелеров хуже чем в одноколонных. Во-первых из-за наличия верхней балки соединяющей колонны и во-вторых из-за того что кабина не может вертикально перемещаться относительно грузоподъемника.
Одноколонную или двухколонную схему крана-штабелера выбирают прежде всего из условий обеспечения фиксированного положения груза на грузоподъемнике. При выдвижении груза инерционные силы приводят к поперечному перемещению рамы грузоподъемника в результате зазоров направляющих роликов грузоподъемника и закручивания колонн в поперечной плоскости. Очевидно что это поперечное перемещение консольного грузоподъемника существенно больше чем перемещение грузоподъемника имеющего направляющие ролики расположенные с обеих сторон по направлению движения крана-штабелера. Поэтому при грузах массой более 2 т при грузах длина которых более 2 – 25 м и при большой высоте подъема (свыше 20 м) применяют двухколонные краны-штабелеры.
Одноколонные краны-штабелеры по сравнению с двухколонными имеют минимальные собственные массу и размеры; позволяют лучше использовать высоту помещения и более удобны при монтаже. Недостатками одноколонных стеллажных кранов-штабелеров являются относительно большое поперечное перемещение грузоподъемника и увеличенные нагрузки на направляющие катки грузоподъемника в результате его консольного расположения и как следствие этого - большой износ катков и направляющих колонны.
Эти недостатки не оказывают существенного влияния при грузоподъемности кранов-штабелеров до 20 – 25 т. Однако при грузоподъемности свыше 2 т и при больших (свыше 25 м) размерах груза устранение этих отрицательных влияний путем увеличения прочности и жесткости металлоконструкций увеличения диаметров направляющих катков грузоподъемника и расстояния между ними приводит к неоправданному увеличению массы и размеров крана-штабелера. В этих случаях предпочтение следует отдать двухколонной схеме при которой кран-штабелер работает в значительно более благоприятных условиях.
2.1.Механизм подъема.
Механизмы подъема стеллажных кранов-штабелеров принципиально мало отличаются от соответствующих механизмов других грузоподъемных машин. В подавляющем большинстве на стеллажных кранах-штабелерах применяют канатные механизмы подъема. Механизм подъема как правило состоит из электродвигателя тормоза редуктора и канатного барабана. Эти механизмы имеют определенные ширину ограниченную шириной межстеллажного прохода и длину непосредственно зависящую от длины крана-штабелера. Поэтому наибольшее распространение получила вертикальная компоновка механизма подъема. Основой механизма является вертикальный конусно-цилиндрический редуктор который крепят к задней стенке колонны. Канатные барабаны устанавливают или на двух концах выходного вала по обе стороны редуктора (в этом случае используют канат без полиспаста) или на одном конце вала тогда груз поднимают с помощью полиспаста а свободный конец каната через блоки крепят к ограничителю грузоподъемности. На редуктор сверху помещают фланцевый вертикальный электродвигатель. Тормоз устанавливают на тормозной муфте соединяющей редуктор с электродвигателем.
Стеллажные краны-штабелеры могут иметь иную компоновку механизма подъема. На них используют стандартные червячные или цилиндрические крановые редукторы и тормозы вертикального исполнения. Редуктор и электродвигатель установлены горизонтально по продольной оси крана-штабелера. Канатный барабан установлен или на выходном валу редуктора или соединен с редуктором зубчатой передачей. Длина подобного механизма больше чем механизма при вертикальной компоновке. Однако на размерах крана-штабелера такая компоновка механизма подъема не сказывается так как его встраивают внутрь решетчатой колонны.
Описанная компоновка механизма подъема выгодна тем что при ее использовании не требуются специальные конусно-цилиндрические редукторы стоимость которых больше чем червячных или цилиндрических.
1.1.Механизм передвижения.
Механизм передвижения принципиально не отличается от механизмов передвижения других грузоподъемных устройств. Они состоят из электродвигателя тормоза и редуктора соединенного с ходовым колесом. Подобно механизмам подъема механизмы передвижения как правило имеют вертикальную компоновку. Механизмы передвижения большинства зарубежных фирм выполнены в виде вертикального конусноцилиндрического или червячного редуктора установленного на валу приводного колеса или соединяемого с ним открытой зубчатой передачей. На редукторы вертикально устанавливают фланцевые электродвигатели со встроенным тормозом. Широко применяют электродвигатели с микроприводом обеспечивающие большой диапазон регулирования скоростей при постоянном крутящем моменте.
На многих типах кранов-штабелеров в том числе на стеллажных кранах-штабелерах отечественного производства механизм передвижения выполнен в виде вертикального цилиндрического редуктора с полым выходным валом насаженного на вал приводного колеса. Выходной вал редуктора соединен с электродвигателем с помощью тормозной муфты. Электродвигатель расположен горизонтально над ходовой балкой крана-штабелера. Такая компоновка более эффективна так как этот механизм лучше вписывается в габариты крана. С целью сокращения длины кранов-штабелеров механизм подъема как правило расположен над механизмом передвижения. При большой высоте механизма передвижения механизм подъема приходится устанавливать достаточно высоко что усложняет его обслуживание.
Механизм передвижения всегда выполняют на одном из ходовых колес расположенном для двухколонных кранов-штабелеров со стороны более нагруженной колонны и для одноколонных – со стороны колонны.
1.2.Телескопический захват.
Выдвижные телескопические захваты разного конструктивного исполнения в настоящее время применяют на всех стеллажных кранах-штабелерах предназначенных для пакетной переработки грузов.
Телескопические захваты независимо от конструктивного исполнения выполнены по единой схеме. Они обычно состоят из трех секций: неподвижной промежуточной и выдвижной. Последняя служит опорной площадкой для установки груза. Она расположена несколько выше остальных секций чтобы при выдвижении груз не задевал за неподвижную и промежуточную секции. Промежуточная секция имеет ролики благодаря которым она может передвигаться по направляющим неподвижной секции. В свою очередь выдвижная секция с помощью роликов движется по промежуточной секции. Ширина всех секций одинакова и равна максимальной ширине перевозимого груза.
Рис.2.2. Схемы выдвижных телескопических захватов с расположением секций:
а – вертикальным; б – горизонтальным
Промежуточная секция выдвигается примерно на половину ее длины; выдвижная секция выступает из промежуточной на ту же величину. Обе секции выдвигаются одновременно с помощью привода. Захват может выдвигаться в обе стороны прохода. Таким образом взятый из загрузочного устройства груз может быть установлен в любую сторону без какого-либо поворота грузового захвата. Благодаря этому ширина прохода между стеллажами может быть снижена до минимального размера определяемого шириной перевозимого груза с учетом необходимых зазоров между грузом и стеллажами (от 50 до 100 мм на сторону).
Выдвижной телескопический захват с вертикальным расположением секций (рис. 2.2 а) состоит из выдвижной площадки 3 с закрепленной на ней роликовых батарей 5 и 6 промежуточной секции 2 неподвижных роликовых батарей 1 и 7 и приводного вала с шестернями 8. на верхней выдвижной площадке 3 промежуточной секции 2 и на неподвижной секции закреплены зубчатые рейки 4 длина которых равна длине секции.
Работа телескопического захвата происходит следующим образом. При вращении вала 8 установленные на нем шестерни входящие в зацепление с рейками на средней секции 2 сообщают средней секции некоторую скорость. На оси закрепленной в средней секции свободно вращается шестерня входящая в зацепление одновременно с рейкой закрепленной на неподвижной секции и с рейкой закрепленной на верхней выдвижной площадке. При перемещении средней секции со скоростью v1 шестерня входящая в зацепление с неподвижной рейкой сообщает верхней секции скорость v2 = 2*v1. Таким образом при включении привода захвата одновременно перемещаются на одинаковую величину: средняя секция по неподвижной со скоростью выдвижная площадка по средней секции с удвоенной скоростью v2.
После взятия груза привод захвата переключает и обе секции одновременно перемещаются и приходят в среднее положение. Выдвижной телескопический захват (рис.2.2.б) другого типа имеет горизонтальное расположение секций. На неподвижной секции его установленной на грузоподъемнике крепят ролики 9 по которым перемещается промежуточная секция 2 с роликами 8 служащими для передвижения выдвижной площадки 3. На валу промежуточного элемента смонтирована шестерня входящая одновременно в зацепление с зубчатой рейкой закрепленной на неподвижной секции захвата.
Привод захвата состоит из электродвигателя редуктора и тормоза. На выходном валу редуктора размещена шестерня входящая в зацепление с шестерней приводного вала захвата имеющего также две шестерни 10 сопряженные с зубчатыми рейками установленными на промежуточной секции захвата.
Работает захват таким образом. При включении привода шестерни посредством зубчатых реек сообщают поступательное движение промежуточной секции 2. Шестерня промежуточной секции движущаяся вместе с ней входит в зацепление с неподвижной зубчатой рейкой и передает движение с удвоенной скоростью зубчатой рейке установленной на выдвижной площадке захвата. Промежуточный и выдвижной элементы захвата движутся одновременно но выдвижной элемент перемещается вдвое быстрее первого.
Захваты с горизонтальным расположением секций имеют меньшую высоту что позволяет лучше использовать вместимость склада. К недостаткам следует отнести сложность конструкции и относительно высокую ее стоимость.
1.3.Система управления.
Рабочие скорости механизмов – подъема передвижения выдвижения телескопических захватов достаточно высоки. Работа механизмов при таких скоростях возможна только при большом диапазоне регулирования скоростей механизмов. Для остановки крана-штабелера (грузоподъемника) точно против требуемой ячейки (позиционирование) необходимо чтобы кран-штабелер и грузоподъемник подходили к ячейке на низких установочных скоростях. При ручном управлении эти скорости не должны превышать 6 – 8 ммин при автоматическом –2 – 4 ммин. При этих скоростях можно с точностью до нескольких миллиметров останавливать соответствующий механизм. Для приводов подъема и передвижения наиболее часто применяют тиристорные преобразователи постоянного или переменного тока. За рубежом находят применение специальные электродвигатели с микроприводами позволяющие получить низкие установочные скорости (08 – 12 ммин) при сохранении необходимого крутящего момента. Эти приводы значительно дороже чем приводы с обычными электродвигателями однако позволяют достигать высокой точности позиционирования.
Краны-штабелеры оборудованы тиристорными преобразователями и электродвигателями постоянного тока с диапазоном регулирования 50 : 1. недостатком применения тиристорных приводов является уменьшение крутящего момента на валу электродвигателя (приводного колеса) и отсюда – повышение требований к качеству монтажа кранового пути.
Краны-штабелеры с относительно низкими скоростями механизмов (подъема – 8 – 12 ммин передвижения – 60 – 80 ммин) с ручным управлением оборудуют двух или многоскоростными асинхронными электродвигателями. Стоимость таких приводов значительно меньше стоимости тиристорных приводов равно как и стоимость обслуживания и ремонта. Двухскоростные электродвигатели с соотношением скоростей 8:1 широко применяют на стеллажных кранах-штабелерах производства НРБ.
Анализ различных вариантов конструктивного исполнения и основных расчетов крана-штабелера.
1.Назначение специфика и нормативные основы.
Все вновь проектируемые или модернизируемые краны-штабелеры подвергаются тщательному расчету. Оформленный расчет является обязательным документом технического проекта крана-штабелера; расчеты элементов или узлов размеры которых становятся известными на стадии рабочего проектирования или корректируются по результатам испытаний опытного образца оформляют затем в виде дополнительных частей или разделов.
Такое внимание к расчетам обусловлено тем что краны-штабелеры являются объектами повышенной ответственности. Прежде всего кран-штабелер – это подъемно-транспортная машина разрушение или повреждение которой представляет опасность для жизни обслуживающего персонала. Во-вторых кран-штабелер в большинстве случаев является единственным средством доступа к грузам находящимся в обслуживаемом им хранилище. Поэтому даже рядовые отказы крана-штабелера нарушают работу склада что особенно чувствительно для складов интенсивных производств и технологических линий.
Таким образом основным назначением расчетов является проверка безопасности и надежности крана-штабелера в работе.
Безопасность крана-штабелера должна быть проверена также и для процесса его испытаний поскольку этот процесс характеризуется увеличенной массой применяемых грузов повышенной вероятностью возникновения отказов искусственным созданием отказов некоторых видов а также значительной численностью персонала испытателей безопасность которых должна быть гарантирована.
Другим назначением расчетов является проверка соответствия технических параметров проекта крана-штабелера требованиям технического задания и нормативно-технических документов. Некоторые из перечисленных параметров например расчетный ресурс запасы прочности жесткость элементов конструкции крана-штабелера имеют прямое отношение к вопросам безопасности и надежности крана-штабелера. Другие параметры – скорость ускорения и замедления обеспечиваемые механизмами характеризуют производительность крана-штабелера.
Очевидно что сравнение различных образцов кранов-штабелеров может быть правильно выполнено только в том случае если расчеты выполнены по одной и той же методике на основании одинаковых нормативов. Этим определяется первая предпосылка необходимости стандартизации норм расчета кранов-штабелеров. Другая и не менее важная предпосылка вытекает из самой ответственности разработки стандарта как официального и обязательного документа; из широкой гласности при обсуждении проекта стандарта заинтересованными и специализированными организациями в результате чего стандарт как правило отражает передовой научный технический и проектно-конструкторский опыт.
В результате специального изучения условий эксплуатации и нормирования расчетов кранов-штабелеров разработаны и введены в действие ОСТ 24.090.68-82 «Краны-штабелеры стеллажные. Нормы расчета» и ОСТ 24.091.14-85 «Краны-штабелеры мостовые. Нормы расчета». Излагаемые ниже основные положения расчета кранов-штабелеров даны в полном соответствии с упомянутыми стандартами.
Оба стандарта предназначаются для кранов-штабелеров по ГОСТ 16553-82. однако основные принципы и нормы расчета этих стандартов могут быть использованы для кранов-штабелеров других типов и параметров например для подвесных мостовых и стеллажных кранов-штабелеров для кранов-штабелеров с облегченным режимом работы. Для того чтобы конструктор мог в таких случаях самостоятельно внести в нормативы необходимые изменения здесь даются пояснения о происхождении тех или иных нормативных требований.
Наконец следует сказать что отчетный расчет как документ проекта представляет собой итоговую часть расчетной работы которой предшествует большое число предварительных и вариантных расчетов. Последние особенно важны так как представляют собой в большинстве случаев единственный инструмент для получения конструкции необходимого технического уровня. Вариантные расчеты в настоящее время с успехом выполняются на ЭВМ принимая форму так называемых оптимизационных расчетов. В качестве критерия оптимизации для крана-штабелера обычно выбирают его массу которую следует минимизировать. Возможно применение и стоимостного или смешанного критерия.
Известно что для расчетов с помощью ЭВМ необходима четкая формализация расчетных схем и требований. И в этом отношении стандартизованные нормы расчета кранов-штабелеров дают необходимый материал.
Исходные данные для предварительных расчетов принимают в соответствии с техническим заданием и схемами предварительных конструктивных проработок крана-штабелера. Исходные данные оформляемого расчета должны полностью соответствовать параметрам указанным в конструкторской и эксплуатационной документации на кран-штабелер; отдельные несоответствия должны оговариваться в отношении их причин и следствий.
В конструкции крана-штабелера обычно используют материалы и комплектующие изделия выпускаемые промышленностью для общего потребления. К ним относятся металлический прокат электродвигатели стандартные редукторы подшипники муфты тормоза и т.п. Их технические параметры приводимые в сортаментах и каталогах также являются исходными данными для расчета в результате которого должны быть выявлены минимально необходимые типоразмеры материалов и комплектующих изделий (с учетом возможностей поставки которые учитываются в расчете как ограничители сортаментов).
Желательно чтобы полученные расчетом скорости механизмов крана-штабелера составляли от 09 до 11 их номинальных значений. Следует отметить что согласно ГОСТ 16553-82 допускаемое отклонение фактических скоростей от номинальных составляет 15%. Сужать поле допуска расчетных скоростей целесообразно для компенсации возможного расхождения расчетных и фактических скоростей.
Расчетное ускорение (замедление) обеспечиваемое механизмом передвижения крана-штабелера должно составлять 03 – 06 мс2. Это объясняется тем что при ускорениях (замедлениях) меньших чем 03 мс2 процессы разгона или торможения чрезмерно затягиваются. Например при ускорении 02 мс2 и номинальной скорости 20 мс разгон будет длиться 10 с; увеличение ускорения до 04 мс2 сокращает время разгона до 5 с а общая экономия времени за цикл работы крана-штабелера составит 20 с что равносильно увеличению производительности крана-штабелера не менее чем на 20%. Ускорение большее чем 06 мс2 во многих случаях недостижимо по условию необходимого запаса сцепления приводных колес с рельсами. Однако и тогда когда имеется избыточный запас сцепления (например у кранов-штабелеров с малой высотой подъема) увеличение ускорения свыше 06 мс2 нецелесообразно: увеличение производительности получается несущественным а габарит электродвигателя может возрасти так как требуется повышенный пусковой момент.
Расчетное ускорение грузозахватного органа должно быть не более 10 мс2. ускорения большие чем указанное не применяют потому что скорость подъема обычно не превышает 05 мс и сокращать время разгона по сравнению с величиной 05 с не только не имеет смысла но и невыгодно во всех отношениях.
Нижняя граница ускорения при подъеме не регламентируется. Дело в том что электродвигатель механизма подъема подбирают таким образом чтобы требуемый момент установившегося движения на валу электродвигателя был близок к его номинальному моменту. Пусковой момент электродвигателя в 2 – 3 раза больше номинального поэтому ускорение разгона обычно получается не менее 04 – 05 мс2 что вполне приемлемо так как время разгона не превышает 10 – 15 с.
Верхняя граница замедления торможения при опускании грузозахватного органа также равна 10 мс2 а нижняя не ограничивается по причинам аналогичным вышеизложенным так как основной процесс торможения обеспечивается электродвигателем.
Расчетное ускорение (замедление) при выдвижении телескопических захватов должно быть не более 10 мс2. Такое ограничение необходимо для предотвращения смещения груза относительно захвата под действием инерционных сил. Поэтому указанное ограничение проверяется для случаев пуска и торможения захвата на котором установлена порожняя тара так как при этом ускорение (замедление) получается наибольшим. Вследствие того что скорость выдвижения захватов сравнительно невелика (до 025 мс) инерционная доля массы порожней тары в приведенном моменте инерции привода захвата также невелика и можно рассчитывать ускорение для захвата без груза. Этим объясняется то что в ОСТ 24.090.68-82 не оговаривается для какого случая нагружения захватов следует проверять ускорение поскольку очевидно что наибольшее его значение будет в случае порожних захватов.
Нижний предел расчетного ускорения (замедления) захватов не регламентируется ввиду того что скорость выдвижения как уже отмечалось сравнительно невелика и время разгона практически никогда не превышает 1 с даже в наиболее тяжелом случае – при взятии номинального груза из ячейки стеллажа.
Расчетный срок службы кранов-штабелеров принимается равным 20 годам при односменной работе. В течение этого срока металлоконструкции кранов-штабелеров должны проработать безотказно и такое требование практически выполнимо.
Календарный срок службы крана-штабелера и его узлов удобен для эксплуатационника. Между этой величиной и долговечностью существует определенная связь зависящая от продолжительности цикла крана-штабелера и от соотношения продолжительностей включения различных механизмов в течение цикла.
При индивидуальном проектировании крана-штабелера предназначенного для склада с определенными заданными параметрами – длиной высотой числом ячеек грузооборотом - характеристики цикла можно определить однозначно путем их осреднения по складу с учетом принятых приоритетов загрузки и выгрузки.
Для крана-штабелера серийного производства условия работы заранее не известны. Поэтому приходится задаваться некоторым условным складом параметры которого были бы представительны по частоте практической применяемости и создавали бы в то же время достаточно напряженный режим работы крана-штабелера. При этом для определения характеристики цикла стеллажного крана-штабелера практически достаточно задаться длиной склада. Для мостового крана-штабелера существует некоторое множество пар значений длины и ширины склада при которых может быть обеспечен заданный грузооборот. Этому множеству соответствует множество возможных циклов из которых следует выбрать наиболее характерные принимаемые в качестве нормативных.
Такая работа выполнена при разработке ОСТ 24.090.68-82 и ОСТ 24.091.14-85. Отметим что выбор нормативного цикла работы крана-штабелера позволяет помимо ресурса установить и другие важные характеристики режима работы механизмов крана-штабелера. К ним относятся число включений в час и продолжительность включения (ПВ %) необходимые для выбора электродвигателей.
К ним также относятся циклограммы работы механизмов показывающие изменение нагрузки механизмов в течение цикла и необходимые для расчета всех звеньев механизмов в том числе и электродвигателей. Для получения циклограмм приходится рассматривать процессы установившегося движения а также разгона и торможения механизмов и кроме того учитывать статистическую изменчивость массы складируемых грузов.
Методической основой для установления расчетных характеристик режима работы механизмов является ГОСТ 25835-83 «Краны грузоподъемные. Классификация механизмов по режимам работы» а также стандартные значения ПВ и числа включений в час применяемые в отечественной промышленности.
Согласно ГОСТ 25835-83 найденные с помощью нормативного цикла значения чистого времени работы каждого из механизмов за срок службы округляются до стандартных ближайших значений. Таким образом устанавливается класс использования механизма по времени. По циклограммам работы механизмов вычисляют коэффициент нагружения равный сумме произведений относительной длительности нагрузки на куб относительной нагрузки взятой по всем элементарным прямоугольникам циклограммы. По коэффициенту нагружения устанавливают класс нагружения который в сочетании с классом использования определяет группу режима работы механизма крана-штабелера.
Как показали исследования для стеллажных кранов-штабелеров по ГОСТ 16553-82 все механизмы должны быть отнесены к группе режима работы 5М по ГОСТ 25835-83 что соответствует тяжелому режиму работы по классификации Госгортехнадзора.
Элементы механизмов должны быть проверены на прочность по наибольшим нагрузкам пусковых и тормозных режимов а также на выносливость с учетом требуемого ресурса и циклограмм нагружения элементов получаемых путем образмеривания исходных циклограмм по данным о величинах нагрузки передаточных чисел и коэффициентов полезного действия звеньев передачи.
При этом расчет цилиндрических эвольвентных зубчатых передач внешнего зацепления следует выполнять по ГОСТ 21354-75 подшипников качения – по ГОСТ 18854-82 и ГОСТ 18855-82. ходовые колеса кранов-штабелеров следует проверять по ОСТ 24.090.44-82 «Колеса крановые. Выбор и расчет» с учетом изложенных ниже рекомендаций. Для расчета поворотных опор колонн мостовых кранов-штабелеров следует применять ОСТ 22-1401-79 «Опоры поворотные роликовые однорядные с зубьями внутреннего зацепления». Прочие элементы механизмов рекомендуется рассчитывать по соответствующим РТМ ВНИИПТмаша. Для стандартных редукторов подлежащих согласованию следует применять РТМ 2-056-80 «Редукторы общего назначения. Методика выбора редукторов и моторов-редукторов».
Электродвигатели механизмов должны быть проверены по наибольшим нагрузкам пусковых и тормозных режимов а также на нагрев с учетом их расчетных характеристик и соответствующих циклограмм.
При расчете металлоконструкций кранов-штабелеров проверяют прочность устойчивость жесткость и выносливость конструкций в целом и их отдельных элементов. Для стеллажных кранов-штабелеров выполняют также расчет затухания колебаний колонны при остановке крана-штабелера.
Стальные конструкции рассчитывают по методике СНиП II-23-81 «Нормы проектирования. Стальные конструкции» а алюминиевые конструкции – по методике СНиП II-24-74 «Нормы проектирования. Алюминиевые конструкции» с учетом излагаемых здесь специфических требований.
При формировании исходных данных для расчета следует убедиться что принятые в проекте крана-штабелера материалы металлоконструкций и сварочные материалы соответствуют требованиям обязательного РТМ 24.090.52-79 «Краны грузоподъемные. Материалы для сварных металлических конструкций» а примененные для болтовых соединений стальные болты гайки и шайбы соответствуют требованиям СНиП II-23-81. следует также проверить что кран-штабелер оборудован всеми устройствами безопасности в соответствии с требованиями ОСТ 24.090.38-83 и ОСТ 24.090.39-83.
В заключение следует указать что в расчетах выполняемых на группу исполнении крана-штабелера отличающихся пролетом высотой грузоподъемностью и скоростями механизмов должны быть рассмотрены все исполнения группы а не только исполнения с наибольшими характеристиками.
Краны-штабелеры рассчитанные в соответствии с настоящими рекомендациями могут быть использованы для эксплуатации в сейсмических районах без ограничений так как применяемые здесь экстремальные расчетные нагрузки превосходят наибольшие сейсмические нагрузки по СНиП II-7-81.
2.Расчет стеллажных кранов-штабелеров.
Расчетные характеристики режима работы механизмов стеллажных кранов-штабелеров соответствующие ГОСТ 25835-83 приведены в табл.3.3
Значения показателя для механизма
Группа режима работы
Общее время работы тыс.ч
Коэффициент нагружения (стеллажных кранов-штабелеров)
Число включений в час
Продолжительность включения ПВ %
В расчетных циклограммах загрузки механизмов (рис.3.1) по оси абсцисс отложено относительное число циклов или относительная продолжительность действия нагрузки. Строго говоря число циклов нагрузки не пропорционально времени ее действия ввиду наличия периодов разгона и торможения и следовало бы давать отдельные циклограммы по числу циклов и по времени в качестве аргументов. Однако для механизмов подъема и выдвижения относительная продолжительность неустановившихся режимов движения всегда невелика – менее 3 %. Для механизма передвижения при нормировании режима работы принят стеллаж длиной 100 м. При этом средний путь передвижения крана-штабелера за простой цикл составит также 100 м. Можно показать что например при скорости передвижения 20 мс и ускорении (замедлении) 05 мс2 погрешность в вычислении числа циклов если не учитывать неустановившиеся режимы движения составит 8 % в сторону увеличения т.е. в запас. Такая погрешность находится в пределах точности исходных предпосылок поэтому и в данном случае достаточно ограничиваться одной циклограммой.
Рисунок 3.1. Расчетные циклограммы загрузки механизмов стеллажных кранов-штабелеров: а б в – соответственно передвижения подъема и выдвижения захватов
Переход к абсолютному времени для элементов рассчитываемых на полный срок службы крана-штабелера производится по общему времени работы (см. табл. 3). Для прочих элементов это время уменьшается в 2 раза или более.
Для нахождения полного числа циклов нагружения какого-либо элемента механизма необходимо общее время работы разделить на длительность одного цикла. Для вращающихся элементов – валов шестерен подшипников и т.д. – циклом является один оборот (особенности существуют только для планетарных редукторов). При этом частоту их вращения следует брать для установившегося режима движения. Например для вала механизма подъема вращающегося с частотой 1000 обмин и рассчитываемого на полный срок службы получим полное расчетное число циклов 1000*60*12500 = 75*108.
В расчетных циклограммах (см. рис. 3.1) по оси ординат отложена относительная нагрузка. Абсолютная величина наибольшей ординаты нагрузки для механизма передвижения соответствует моменту при разгоне с расчетным ускорением; для механизма подъема – моменту при установившемся движении подъема с номинальным грузом; для механизма выдвижения – при взятии номинального груза из ячейки стеллажа т.е. на наибольшем вылете захвата но без учета сил инерции.
При установлении характеристик режима работы (см. табл.3.1 и рис.3.1 ) рассматривали краны-штабелеры обслуживающие стеллажи длиной 100 м высотой 16 м и глубиной 12 м со скоростями передвижения от 16 до 25 мс подъема – 04 мс и выдвижения захватов – 02 мс. ускорения при разгоне механизмов принимали равным 04 мс2. Относительное число простых и сложных циклов 06 и 04 соответственно. Процесс подъема считали как совмещенный по времени с процессом передвижения. Изменчивость массы Q грузов оценивали по гистограмме (рис.3.1) полученной по результатам обследования действующих складов; средняя масса груза по этой гистограмме составляет 06 от номинальной Qном.
Рис.3.2 Расчетная гистограммараспределения массы брутто
складируемых грузов;ρ – плотность вероятности
Для расчета опорных одноколонных стеллажных кранов-штабелеров рекомендуется использовать схемы представленные на рис. 3.2
В кране-штабелере выделяют шесть укрупненных конструктивных узлов со следующей закрепленной за ними индексацией: ходовая балка 1 в сборе с установленным на ней механизмом передвижения и ходовыми колесами; механизм подъема 2 (включая канаты); колонна 3(или две колонны у двухколонных кранов-штабелеров рамной конструкции рис. 3.2; при шарнирно-сочлененной конструкции по рис. 3.3 правая и левая колонны и их ходовые балки должны рассматриваться отдельно дополнительным элементом является сцепка); оголовок колонны 4 в сборе с грузовыми блоками и боковыми роликами (или верхняя балка у двухколонных кранов-штабелеров); грузоподъемник 5 в сборе с каретками грузовыми подвесками и грузовыми захватами; кабина 6 (при определении ее массы учитывается масса оператора).
Шкаф электрооборудования относят к ходовой балке или к колонне в зависимости от того на чем он установлен.
Отдельным элементом является транспортируемый груз номинальная масса которого обозначена через Q.
Для каждого из этих узлов предварительно определяют номинальные значения масс m zi) в прямоугольной системе координат начало которой расположено в середине площадки контакта приводного ходового колеса с наземным крановым рельсом.
Для расчета металлоконструкций подготавливают геометрические характеристики сечений ходовой балки колонн верхней балки а также расчетные сопротивления и модуль упругости материала.
Рис. 3.3 Стержневые схемы конструкций двухколонных стеллажных кранов-штабелеров:
а – рамной; б – шарнирно-сочлененной; 1 1’ – ходовые балки; 2 – механизм подъема; 3 3’ – колонны; 4 – верхняя балка; 5 – рама грузоподъемника; К – каретка подъемника; ГК – грузовые канаты; С – сцепка
Сопротивление передвижению крана-штабелера определяется как сила необходимая для преодоления трения качения ходовых колес и подшипников умноженная на коэффициент 11 учитывающий трение в боковых роликах. Уклон пути не учитывается так как согласно ОСТ 24.090.39-83 уклон ограничен очень малой величиной – 0001.
Сопротивление передвижению необходимо знать для определения скорости ускорения и замедления крана-штабелера обеспечиваемых используемым электродвигателем и передаточным механизмом.
Однако методически удобней начинать расчет механизма передвижения с анализа запаса сцепления приводных колес а затем и устойчивости крана-штабелера в режимах разгона и торможения.
Физический смысл необходимости запаса сцепления – предотвращение пробуксовки приводного колеса приводящей к ускоренному изнашиванию колеса и рельса. Для крана-штабелера такое изнашивание особенно нежелательно так как помимо прочего уменьшение диаметра колеса нарушает вертикальное положение колонны от которого непосредственно зависит возможность правильного позиционирования грузового захвата во все ячейки по высоте стеллажа.
Для кранов-штабелеров с гибким токоподводом следует дополнительно учесть воздействие усилий статического натяжения и сопротивления передвижению кабельной подвески если эти усилия вызывают разгрузку приводного колеса. При этом кабельную подвеску следует рассматривать в наиболее растянутом положении т.е. на полной длине стеллажа которую принимают равной 100 м если в техническом задании нет других указаний.
Составив уравнения для коэффициента запаса сцепления в соответствии с приведенными указаниями легко увидеть что в них входят только геометрические и массовые параметры крана-штабелера и ускорения (замедления). Таким образом получим предельно допускаемое ускорение и замедление крана-штабелера всего четыре значения (ускорение и замедление для крана-штабелера с грузом и без груза) каждое из которых должно быть не менее 03 мс2.
По допускаемому ускорению с помощью известных формул определяют соответствующий среднепусковой момент электродвигателя который должен уравновесить сопротивление передвижению и силы инерции масс крана-штабелера а также инерционные моменты вращающихся масс ротора муфты тормозного шкива и т.п. с учетом КПД механизма.
Расчет выполняют для крана-штабелера с грузом и без груза; из двух полученных значений среднепускового момента выбирают наименьшее которое для перехода к номинальному моменту следует разделить на коэффициент кратности пускового момента и коэффициент использования пускового момента значения которого приведены в табл.3.2
Система упраления приводом
Коэффициент использования пускового момента
Релейно-контроллерная
Асинхронный с фазовым ротором
Асинхронный короткозамкнутый
Преобразователь или регулятор
Переменного или постоянного тока
Полученное значение номинального момента электродвигателя является предельно допустимым поэтому из рассматриваемой упорядоченной номенклатуры следует выбирать тот наибольший электродвигатель номинальный момент которого при ПВ = 60 % не превышает предельно допустимый.
Отсюда начинается проверочная часть расчета механизма передвижения. Сначала с помощью механической характеристики электродвигателя определяют расчетную скорость установившегося движения крана-штабелера которая должна удовлетворять требованиям изложенным выше. Если результат не достигнут то следует изменить передаточное число редуктора а возможно и рассмотреть другую номенклатуру редукторов и (или) электродвигателей.
Описание конструкции и предварительная разработка общего вида крана-штабелера.
Краны-штабелеры стеллажные автоматические грузоподъемностью 1 т предназначены для механизации процессов укладки в стеллажи и выдачи из стеллажей на загрузочные устройства грузов уложенных в стандартную ящичную тару по ГОСТ 14861-74 или на специальные поддоны и тару с размерами в плане 1200*800 мм для кранов-штабелеров грузоподъемностью 1 т.
Краны-штабелеры предназначены для применения в автоматизированных транспортно-складских системах функционирующих как самостоятельно так и в составе автоматизированных технологических комплексах а также для использования в цеховых складах машиностроительных заводов.
Климатическое использование кранов-штабелеров УХЛ4 по ГОСТ 15150-69.
Краны-штабелеры не предназначены для применения во взрыво- и пожароопасных помещениях (за исключением П-IIа) в помещениях с парами кислот и щелочей концентрации которых вызывают разрушение электрической изоляции и металлических конструкций а также в помещениях в которых возможно выделение вредных веществ в воздух рабочей среды.
Кран-штабелер транспортируется и поступает потребителю упакованным в деревянные ящики кроме колонны следующими частями:
тележка в сборе с приводом передвижения направляющими роликами подхватами и конечными выключателями;
грузоподъемник в сборе с электрооборудованием;
направляющие для установки шунтов и направляющие кабельного блока;
считыватели конечные выключатели шунты линейки;
кабельные изделия детали и узлы креплений кабелей кабельный блок клеммные коробки кабельные тележки и другие узлы;
электрошкаф с реакторами;
устройство управления движением в сборе с кронштейном для его установки на кране-штабелере;
командное устройство управления;
1.Техническое описание.
Технические характеристики кранов-штабелеров стеллажных автоматических грузоподъемностью 1 т представлены в таблице 4.1.
Наименование параметров
Режим работы крана-штабелера
Режим работы механизмов по
привод выдвижения грузозахватного органа
Максимальное расстояние от головки рельса до подвесного пути Нр м
Максимальная высота подъема грузозахватного органа Нп м
Габариты перерабатываемых грузов:
Минимальная высота опор ящичной тары мин м
Скорость подъема грузозахватного органа мс
Скорость передвижения крана-штабелера мс
Скорость выдвижения грузозахватного органа мс
Тип грузозахватного органа
Величина выдвижения грузозахватного органа
Высота выдвигаемых элементов грузозахватного органа м
Ширина крана-штабелера В м
Длина крана-штабелера (вдоль пути)м
Ширина прохода для штабелирования А м
Максимальное количество адресов:
Тип нижнего рельсового пути
Суммарная мощность установленных электродвигателей кВт
Коэффициент установленной мощности
Подвод электропитания
Максимальная масса крана-штабелера т
Удельная металлоемкость ттыс.т.
Двутавр №12 ГОСТ 8239-72
Рельс Р24 ГОСТ6368-82
В состав изделия входят:
комплект монтажных частей;
эксплуатационная документация.
Кран-штабелер состоит из следующих составных частей
– электрооборудование.
В комплект монтажных частей поставляемых с краном-штабелером входят:
установка информационных каналов связи;
устройство командное;
буферы гидравлические;
детали для крепления рельсового и подвесного путей;
кабель подвесной для электропитания крана-штабелера;
линейки кронштейны и т.п.
3.Устройство и работа изделия
Привод передвижения установлен на тележке имеющей два колеса:
одно приводное и одно холостое диаметром 200мм.
На торцах тележки установлено по паре катков удерживающих кран-штабелер от бокового смещения.
Катки установлены на прокладках служащих для регулировки зазоров между катками и боковой поверхностью рельса.
К тележке при помощи болтов крепится колонна.
По направляющим на колонне перемещается грузоподъемник.
На грузоподъемнике установлен грузозахватный орган а также фотоэлементы для контроля положения груза датчики контроля занятости ячеек стеллажа и считыватель адреса по вертикали.
Подвод электропитания к грузоподъемнику осуществляется при помощи гибких кабелей. Натяжение кабелей осуществляется блоком перемещающимся по направляющим закрепленным на колонне на половине ее высоты.
Привод подъема расположен на нижней части колонны. Натяжение грузового каната контролируется ограничителем грузоподъемности.
В верхней части колонны установлен оголовок на котором имеются 4 отводных блока и пара направляющих катков служащих для удержания крана-штабелера в вертикальном положении.
Кран-штабелер перемещается между стеллажами по рельсу уложенному вдоль продольной оси межстеллажного прохода. В верхней части межстеллажного прохода уложен подвесной путь из двутавра №12 по которому обкатываются катки установленные на оголовке крана-штабелера.
Подвод электропитания крана-штабелера осуществляется при помощи гибких кабелей подвешенных на специальных тележках перемещающихся по подвесному пути.
Управление краном-штабелером:
-автоматическое – от командного устройства;
-ручное – с наладочного пульта.
Система автоматического управления предусматривает возможность непосредственного управления от ЭВМ верхнего уровня.
Кран-штабелер выполняет следующие работы:
-берет груз с загрузочного устройства и устанавливает его в ячейку стеллажа;
-берет груз из ячейки стеллажа и устанавливает его на загрузочное устройство;
-берет груз из любой ячейки стеллажа или любого загрузочного устройства работающего на загрузку стеллажей и устанавливает его в другую ячейку стеллажа или на другое загрузочное устройство работающее на выгрузку.
Любая из указанных выше работ выполняется краном-штабелером по команде от ЭВМ или с командного устройства включающей адрес ячейки из которой кран-штабелер должен взять груз и адрес ячейки в которую кран-штабелер должен установить груз.
После получения команды кран-штабелер выполняет работу в следующей последовательности:
-включается привод подъема и передвижения кран-штабелер подходит и останавливается у ячейки откуда надо взять груз;
-включается привод выдвижения грузозахватного органа захваты выдвигаются и устанавливаются под грузом в ячейке стеллажа;
-включается привод подъема груз приподнимается привод подъема выключается;
-включается привод грузозахватного органа захваты с грузом возвращаются в среднее положение;
-включается привод подъема и передвижения кран-штабелер подходит и останавливается у ячейки в которую надо установить груз;
-путем последовательного включения привода грузозахватного органа и привода подъема груз устанавливается в заданную ячейку;
-после возвращения грузозахватного органа в среднее положение кран-штабелер остается на месте до получения следующей команды.
Конструкторская часть.
1.Конструктивная разработка отдельных механизмов и узлов.
1.1.Расчет механизма передвижения тележки.
Расчет сопротивлений передвижению тележки крана-штабелера с грузом.
Приведенная ниже методика и нормы расчета применяются для механизмов передвижения кранов и грузовых тележек перемещающихся по рельсовому пути.
Полное сопротивление передвижению крана:
Wртр – сопротивление трения при движении крана с учетом трения роликов;
Wтр – сопротивление трения при движении крана без учета трения реборд
kр – коэффициент учитывающий сопротивление трения реборд ходовых колес крана о головку рельсов (при подшипниках скольжения – трения торцов ступиц колеса) при движении крана (табл.5.1.1.) т.к. колесо безребордное то kр = 1.
Wук – сопротивление от уклона подкрановых путей;
Wв – сопротивление от действия ветровой нагрузки.
Качения и скольжения
Передвижения тележки
Сопротивление трения определяется по формуле:
Q = 1000 – вес номинального груза кг;
G= 3250 – собственный вес крана кг;
Dх.к.= 200 – диаметр ходового колеса мм;
d = 45 – диаметр цапфы вала ходового колеса мм;
dр = 150 – диаметр ролика мм
= 003 – коэффициент трения качения (табл.5.1.2.стр134)
f = 0015 – коэффициент трения в подшипниковых опорах ходовых колес; значения f принимают:
Для подшипников скольжения открытого типа010
Для букс с жидкой смазкой008
Для шариковых и роликовых подшипников0015
Для конических подшипников качения002
Определим сопротивление трения:
Определим силу трения ролика:
Диаметр ходового колеса мм
для стальных колес см
для чугунных колес см
Сопротивление от уклона подкрановых путей:
Расчетные уклоны подкрановых путей α принимают:
Для путей с железобетонным фундаментом на металлических балках0001
Для путей с щебеночным основанием и деревянными шпалами0002
Для подтележечных путей на мосту крана0002
Так как наш кран-штабелер работает в помещении то Wв = 0
Найдем полное сопротивление передвижению крана:
Расчет сопротивлений передвижению тележки крана-штабелера без груза.
Так как кран-штабелер работает в помещении то Wв = 0
Полное сопротивление передвижению крана без груза:
Выбор мотор-редуктора.
Выбор мотор-редуктора для механизма передвижения крановых тележек производят по максимально допустимому пусковому моменту двигателя при котором обеспечивается надлежащий запас сцепления ходового колеса с рельсом исключающий возможность буксования при передвижении тележки без груза в процессе пуска.
Допустимое значение ускорения тележки:
φ = 02 – коэффициент сцепления ходового колеса с рельсом;
Рв= 0 – ветровая нагрузка на кран в рабочем состоянии;
g – ускорение силы тяжести;
nпр – число приводных ходовых колес;
nк – общее число ходовых колес.
Определим мощность двигателя по статическому сопротивлению при перемещении тележки с номинальным грузом:
vт = 25 мс = 150 ммин – скорость передвижения тележки;
= 09 – К.П.Д. передачи при установке ходовых колес на подшипниках качения.
Число оборотов ходовых колес:
Конический мотор-редуктор
BK20-54VUDHE09XA4C-TF-SESX027A9HAS40
Скорость ведущего вала
Направление клеммной коробки
Вес нетто (базовая сборка) 1 шт
Конструкцияисполнение
Исполнение редуктора
Конический редуктор BK20
моментный рычаг спереди вниз
полый вал с пазом под шпонку ø 40.00 mm
с установленным сапуном
Доп. спец. исполнение
Резиновые буферы для моментного рычага
Исполнение двигателя
Трехфазный электродвигатель DHE09XA4C
Напряжениесоединение
Номинальная скорость
Класс защиты по IP в соотв. с EN 60529
Коэффициент мощности (cosphi)
охлаждение EN 60034-6
IE_CODE_NACH_EN60034-30
Конструкция во соответствии с DIN VDE 0530-1EN 60034-1
Однодисковый тормоз с пружинами ESX027A9
Номинальный тормозной момент
Класс защиты по IP в соотв. с EN 60 529
с Стандарт -Выпрямитель (встроенный в клеммную коробку двигателя)
Напряжение питания AC 50Hz
HA ручной отпуск с блокировкой
Основные параметры электродвигателя
Номинальная мощность (PN): 22 кВт
Номинальная частота вращения вала ротора (n): 1440 обмин
Номинальный вращающий момент вала ротора (MN): 145 Нм
Момент инерции массы ротора (Jrot): 00053 кгм2
Режим работы: продолжительный S1
Основные параметры мотор-редуктора
Тип редуктора: BK2(конический редуктор)
Скорость ведущего вала: 240 обмин
Крутящий момент (Mк): 80 Нм
Передаточное число (i): 602
Масса мотор-редуктора (m): 556 кг
Основные параметры тормоза
Тип тормоза: ESX027A9 (однодисковый тормоз с пружинами)
Тормозной момент: 22 Нм
Момент инерции масс тормозного диска: 0000172 кгм2
Фактическая скорость передвижения тележки:
Требуемая при этом мощность двигателя:
что соответствует мощности выбранного двигателя.
Время пуска при максимально допустимом ускорении:
Что находиться в допустимых пределах от 05 сек. до 5 сек.
Момент сопротивления при передвижении тележки без груза:
Маховой момент двигателя
Маховой момент диска тормоза
Маховой момент вращающихся движущихся масс
Маховой момент поступательно движущихся масс
Общий маховой момент
Необходимый пусковой момент:
Номинальный момент двигателя
Фактическое время пуска
Тормозной момент механизма передвижения определяют при обеспечении надлежащего сцепления ходового колеса с рельсом которое исключило бы возможность юза при торможении тележки движущейся с номинальной скоростью без груза.
Максимально допустимое замедление при котором обеспечивается заданный запас сцепления ходовых колес с рельсом:
Уравнение моментов при торможении
Мтсо – момент сопротивления передвижению тележки без груза при торможении
Сопротивление передвижению при торможении
Момент сопротивления приведенный к валу тормоза:
Инерционный момент при торможении вращающихся и поступательно движущихся масс:
Тогда тормозной момент:
При снижении скорости перед остановкой крана-штабелера для увеличения его точности относительно ячейки устанавливаем преобразователь на число оборотов двигателя в доводовом режиме 350 обмин.
То инерционный момент при торможении вращающихся и поступательно движущихся масс:
Т.к. тормоз ESX027A9 имеет номинальный тормозной момент 22 Нм то найдем скорость передвижения тележки с номинальным тормозным моментом.
Применим уравнение моментов при торможении
То инерционный момент торможения будет равен:
Определим время торможения через инерционный момент при торможении
Определим максимальное замедление тележки при tт = 295 с
Номинальный тормозной момент механизма передвижения не исключает возможность юза при максимальном замедлении тележки. Для исключения возможности юза требуется уменьшить скорость передвижения тележки.
1.1.Расчет механизма подъема.
Для расчета механизма подъема кроме его основных параметров (грузоподъемности Q скорости v подъема груза высоты подъема груза) должны быть заданы режим работы механизма и его кинематическая и конструктивная схемы.
Определение усилий в канате
Принципиальная схема полиспаста механизма подъема приведена на рис.5.1.2
Рис. 5.1.2. Схема полиспаста
Натяжение каната при подъеме каретки с грузом:
Qкар = 558 – вес каретки кг;
Qгр = 1000 – вес груза кг;
m = 1 – число полиспастов;
бл – К.П.Д. блока полиспаста учитывающий потери в опорах блока а также потери вызываемые жесткостью каната.
кар = 09 – К.П.Д. каретки;
Z = 3 – число направляющих блоков.
Натяжение каната при подъеме каретки без груза:
Расчет каната по Правилам Госгортехнадзора проводим по формуле:
k – запас прочности принимаемый по Правилам Госгортехнадзора в зависимости от назначения каната и режима работы механизма; для грузовых канатов при тяжелом режиме работы k=6;
Рраз – разрывное усилие каната в целом принимаемое по таблицам ГОСТа.
При выборе каната нужно соблюдать условие:
Pст – разрывное усилие по стандарту
По таблицам на канаты ГОСТа 2688-69 выбираем канат типа ЛК-Р 6×19 = 114 диаметром 15 мм имеющий при расчетном пределе прочности проволоки при растяжении равном 160 кгмм2 разрывное усилие Рст = 11700 кг.
После выбора каната проверяют фактический запас его прочности
Фактический запас прочности:
Определение основных размеров и числа оборотов барабана
Минимально допустимый диаметр барабана измеренный по дну канавки для каната определяется по формуле:
e – коэффициент принимаемый по Правилам Госгортехнадзора в зависимости от типа грузоподъемной машины и режима ее работы. Для нашего случая e = 30;
dк = 15 – диаметр каната мм.
Так как увеличение диаметра барабана приводит к повышению долговечности каната то примем диаметр барабана Dб = 560 мм.
Число витков нарезки на барабан:
H = 12 – высота подъема груза м;
Uп= 2 – кратность полиспаста.
Длина нарезки на барабан:
Оставляем на закрепление каната с одной стороны барабана расстояние s равное длине не менее четырех шагов нарезки. При tб = 17 мм примем s = 68 мм.
Тогда общая длина барабана:
Скорость каната навиваемого на барабан при скорости груза 120 ммин
Число оборотов барабана в минуту:
Определяем статическую мощность двигателя при подъеме номинального груза:
= 09 – общее значение К.П.Д.
Проверка барабана на прочность
В барабанах при соотношении параметров напряжения изгиба и кручения незначительны.
В этих условиях проверке подлежат лишь напряжения сжатия:
- толщина оболочки стального барабана.
Плоский цилиндрический мотор-редуктор
BF70-04DHE18XA4-TF-SZSX500A9HAK70
Плоский цилиндрический редуктор BF70
полый вал с пазом под шпонку ø 70.00 mm
Трехфазный электродвигатель DHE18XA4
Двухдисковый тормоз с пружинами ZSX500A9
Номинальная частота вращения вала ротора (n): 1470 обмин
Номинальный вращающий момент вала ротора (MN): 142Нм
Момент инерции массы ротора (Jrot): 0195кгм2
Тип редуктора: BF70-04(цилиндрический редуктор)
Скорость ведущего вала: 143обмин
Крутящий момент (Mк): 1460Нм
Передаточное число (i): 1032
Масса мотор-редуктора (m): 449 кг
Тип тормоза: ZSX500A9 (двухдисковый тормоз с пружинами)
Тормозной момент: 400 Нм
Момент инерции масс тормозного диска: 00133 кгм2
Проверка электродвигателя по времени пуска
Фактическая скорость подъема груза:
Правила Гостехнадзора регламентируют максимальные ускорения для кранов в пределах
Предполагая процесс пуска равноускоренным при заданной скорости подъема 120 ммин допустимое время пуска:
Определяем средний пусковой момент выбранного двигателя:
ср – средняя перегрузочная способность электродвигателя в период разгона с учетом нормального падения напряжения
max – максимальная перегрузочная способность электродвигателя
Определим статический момент от сил тяжести масс груза и каретки приведенный к валу мотор-редуктора:
Определяем маховой момент двигателя
Определяем маховой момент диска тормоза
Определяем маховой момент вращающихся масс
Определяем условный маховой момент поступательно движущихся масс
Определяем фактическое время пуска:
Проверка тормозного момента
где k – коэффициент запаса торможения принимаемый согласно Правилам Госгортехнадзора для тяжелого режима работы равным 2;
Мтс– статический крутящий момент на тормозном валу при торможении определенный в предположении равномерного распределения нагрузки между всеми ветвями полиспаста с учетом потерь в механизме способствующих удержанию груза;
Минимально допустимый диаметр блока:
Нагрузка на один подшипник при максимальном грузе:
- динамический коэффициент; - число блоков; - коэффициент вращения (при вращении наружного кольца подшипника )
1.2.Расчет механизма передвижения вил.
рис. 5.1.3. Схема привода передвижения вил
Оптимизация энергозатрат при гидроприводе должна производиться по двум параметрам: рабочему давлению и расходу рабочего тела раздельно. Привод телескопического захвата крана-штабелера осуществляется от нерегулируемого насоса (1) имеющего постоянную частоту вращения рабочего вала. В результате оптимизации показателя необходимо добиться выполнения условия наиболее полной загрузки электродвигателя насосной станции по мощности. Здесь необходимо сделать следующие предпосылки:
Установочная мощность приводной станции минимальна при минимуме рабочего давления и расхода рабочего тела т.е. p m
Энергозатраты минимальны при постоянстве минимальных значений давления и расхода в течение цикла т.е. при pmin= const Qmin= const.
Выбор гидроцилиндра.
Установлено что устойчивость движения горизонтально расположенных гидроцилиндров может быть обеспечена лишь при соотношении:
Dц – диаметр цилиндра;
S – ход штока цилиндра.
L – перемещение вил;
U = 2 – передаточное число.
Перемещение вил складывается из длины поддона и зазора между концом вил и стеллажом.
Рекомендуемая скорость поршня должна быть не более 05 мс поэтому время выполнения операции имеет ограничение:
Принимаем Dц = 32 мм. При данном захвате зазор между концом вил и стеллажом 006 м.
Сопротивление при выдвижении вил и нагнетании в штоковую полость без прогиба:
Gз = 25 – собственный вес захвата кг;
dр= 4 – диаметр роликов см;
= 003 – коэффициент трения качения.
Сопротивление при возврате вил с учетом уклона и с нагнетанием в поршневую полость:
Давление страгивания и холостого хода при максимальном сопротивлении передвижению вил:
Площадь поршня со стороны штоковой полости:
φ = 165 – коэффициент отношения площадей со стороны поршневой и штоковой плоскостей.
Расход рабочего тела при параллельной работе цилиндров:
V – объем рабочего тела потребляемый в течение времени Т находим как произведение площади поршня на ход поршня:
Рабочий объем штоковой полости:
Максимальный расход штока:
Давление в штоковой полости:
Давление в поршневой полости:
В каталоге выберем гидроцилиндр типа ЦРГ32*16*s:
номинальное давлением 16 МПа;
максимальное давление 20 МПа;
давление страгивания 1 МПа;
Номинальная мощность на валу насоса:
Из каталога по номинальной подаче и мощности выберем насос типа НПл 4063:
рабочий объем 40 см3;
номинальная подача 357 лмин;
номинальное давление на выходе 63 МПа;
номинальная частота вращения 950 обмин;
максимальная частота вращения 1500 обмин;
минимальная частота вращения 600 обмин;
номинальная мощность 43 кВт;
Выбор электродвигателя.
Мощность электродвигателя в зависимости от подачи насоса определяется по формуле:
Q – подача насоса лмин;
P – давление в напорной линии МПа;
п – полный КПД насоса.
N = 146*357 60*085 = 102 кВт
По каталогу на электродвигатели выберем электродвигатель типа 4А80А4 с номинальной мощностью 11 кВт.
Выбор гидрораспределителя.
Из каталога выберем (Р1) гидрораспределитель В6:
диаметр условного прохода 6 мм;
номинальное давление 6 МПа;
максимальное усилие управления на рукоятке 45 Н.
Из каталога выберем (Р2) гидрораспределитель ВЕ6 схема 574.В220.УХЛ.4
Для пластинчатого нерегулируемого насоса с давлением
до 63МПа выберем приемный (сетчатый) фильтр с номинальной тонкостью фильтрации 40 мкм.
Выбор клапана давления.
Выберем гадроклапан давления Г54-32М:
-номинальный расход масла 32 лмин;
-номинальный перепад давлений 02 МПа;
-максимальное давление на входе 20 МПа.
Т.к. система передвижения вил – это система низкого давления (до 25 МПа) то используем аллюминивые трубы по ГОСТ 18475-82 длинной 3м.
Исходя из расхода гидроцилиндров и рабочего объема насоса выберем бак вместимостью 200 л.
1.3.Расчет гидравлического буфера.
Буферное устройство предназначено для ограничения перемещения крана-штабелера вдоль стеллажей путем поглощения кинетической энергии крана-штабелера.
Задачей расчета является определение необходимого количества отверстий их диаметра и координат по длине цилиндра обеспечивающих постоянное заданное значение среднего замедления 4 мс2 в процессе торможения при амплитуде пульсаций тормозного усилия не более 20%.
Рассмотрим наиболее неблагоприятный случай: кран-штабелер с номинальным грузом движется на полной скорости двигатель привода передвижения при заезде крана-штабелера на конечный упор продолжает работать.
Определение расчетного количества отверстий вдоль образующей цилиндра
с учетом обозначений
v = 25 мс – расчетная скорость движения крана-штабелера;
m = 4250 кг – масса крана-штабелера номинальная с грузомноминальным;
= 4 мс2 – расчетное замедление;
R = 342 Н – сопротивление передвижениюкрана-штабелера;
с = 2 Нм – жесткость возвратной пружины;
λ = 0012 м – предварительное поджатие пружины;
= 085 кгм3 – плотность рабочей жидкости;
= 06 – коэффициент расхода; для конусообразного диффузора с углом при вершине 90;
D = 008 м – диаметр поршня;
d = 0004 м– диаметр отверстия;
z = 1 – количество одновременно работающих буферов;
P = 325 Н – усилие привода передвижения;
k – коэффициент сцепления
Дробная часть n1 числа n реализуется как отверстие диаметром:
которое располагается вблизи днища цилиндра.
Координату центра i-го отверстия отсчитываемую от торца поршня в его начальном положении вычисляют по формуле:
i – порядковый номер отверстия.
Определение скорости поршня при прохождении i-го отверстия
Si – координата центра i-го отверстия
Определение усилия на штоке непосредственно перед i-м отверстием
Определение усилия на штоке сразу же после прохождения i-го отверстия
Определение среднего значения усилия на штоке
Определение коэффициента пульсации усилия на i-ом отверстии
Определение допускаемого усилия на штоке из условия прочности цилиндра
D1 = 0093 м – наружный диаметр цилиндра;
– коэффициент учитывающий концентрацию напряжений у отверстий; рекомендуемое значение равно 08;
т = 360106 Па – предел текучести материала цилиндра;
φ – коэффициент запаса прочности; рекомендуемое значение равно 15.
Для отверстий отстоящих от днища цилиндра более чем на величину диаметра поршня должно выполняться условие:
Сравнив усилие на штоке сразу же после прохождения отверстия (max) и допускаемое усилие 1302 144820 мы видим что условие выполняется.
1.Условия работы складов на железнодорожном транспорте.
По причине высокой производительности высотный стеллажный склад (особенно с автоматизированным управлением) требует очень четкой организации. В таком складе каждая операция каждое прохождение груза пли документа работа каждой машины и каждое рабочее место человека должны быть тщательно описаны проанализированы и учтены в общем балансе работы системы. Многие функции склада особенно периферийных его частей (в отличие от стеллажной складской части) являются спонтанными например подвоз грузов по железной дороге. Поэтому к проекту организации работ предъявляются необычайно высокие требования.
Основной задачей при проектировании организации работ в складе является обеспечение стабилизации стеллажной структуры — самого дорогостоящего элемента в системе склада — и обеспечение непрерывной работы этой структуры с максимальной производительностью на протяжении смены или суток. Такой принцип позволяет ограничить до минимума расходы на стеллажную часть склада и обеспечивают быструю амортизацию.
Приведенные требования к проекту организации работ вызывают радикальное изменение прежнего понятия «проекта организации работ» который на практике обычно складывался из описания операций определения количества рабочей силы и схемы зависимостей между отдельными звеньями управления складом.
Проект организации работ высотного стеллажного склада должен на основе количественного анализа складского процесса давать инструкции по обслуживанию прохождения грузов и информации (документов) в любой момент прохождения (пиковый или средний) в тесной связи с окружением («вход» и «выход») и расчетом необходимых для обеспечения заданной производительности средств (люди и машины). В этом проекте на основе анализа различных случает должны быть также приведены инструкции по осуществлению операций и необходимые средства на случай аварии отдельных элементов этой сложной системы.
В традиционном проекте организация работ в высотном стеллажном складе разрабатывается на заключительной стадии проектирования но в получаемом результате содержатся все прежние технические и технологические решения.
В современных складских системах ориентированных на функции и связи организационные проблемы в одинаковой степени влияют как на технические так и на технологические решения. По этой причине проект организации работ следует начинать уже на стадии разработки концепции и продолжать вместе со всеми последующими стадиями проектирования. Установление четкой границы между организацией и так называемой технологией складирования является весьма затруднительным. Здесь отсутствуют какие-либо нормативные указания. Поэтому в настоящей работе принят следующий ход рассуждений.
Для установленного процесса складирования обусловленного функцией склада подбираются технические средства и проектируется организация обеспечивающая осуществление этого процесса с определенной производительностью. Складские процессы вместе с техническими средствами определяют ту или иную технологию складирования. Проект организации работ рассматривает эту технологию в количественных категориях с учетом производительности людей и машин а также определяет способ управления прохождением грузов и информации во всей системе. Достигнутое в проекте организации соответствие заданной и найденной производительности замыкает цикл проектирования склада в то время как в случае несоответствия этих показателей требуется либо вносить изменения в технологию либо возвращаться к предшествующим стадиям проектирования.
1.Организация работ.
Определим количество средств механизации погрузочно-разгрузочных работ требуемых для перерабатывания однотипного пакетного груза на складе МЧ железной дороги.
Масса груза (пакета) – 1 т
Емкость склада – 1200 т
Срок хранения – 10 сут.
Груз расположен на стандартном поддоне мм –
Высота груза с поддоном – 1350 мм
Определим суточный грузооборот склада:
- коэффициент неравномерности прибытия отправления груза
Определим суточный грузооборот в пакетах:
Определим среднюю загрузку вагона:
Vв – внутренний объем крытого вагона м3
kу = 085-09 – коэффициент учитывающий плотность укладки
Vп – объем одного пакета м3
Внутренний объем крытого вагона выбираем
Для перевозки тарно-штучных грузов принимаем крытый четырехосный вагон грузоподъемностью 65 т.
В вагоне умещается 83 пакета по объему но учитывая тот факт что грузоподъемность вагона составляет 65 т а масса одного пакета 1 т то принимаем количество пакетов в вагоне равным 65 шт.
Определим число железнодорожных вагонов (суточный вагонопоток) в которых поступает груз:
Т.к. в вагон вмещается 65 пакетов следовательно в два вагона вмещается 130 пакетов а оставшиеся 14 пакетов отправим автотранспортом.
Определим число вагонов в одной подаче:
z – число подач вагонов на грузовой пункт за сутки ( z = 2 5 ) z = 1
Вычислим необходимое количество поддонов на складе:
- коэффициент учитывающий время нахождения поддонов в ремонте
- время оборота поддонов (время перевозки и хранения груза на складе).
Определим количество автотранспорта:
Tц – продолжительность транспортного цикла автомобиля
- дальность перевозки км (для внутригородских поставок )
- среднетехническая скорость автомобиля
- коэффициент пробега автомашины
Tпр = 01 – время простоя под грузовыми операциями
qа = 5 т – фактическая загрузка автомобиля
T = 8 ч – количество рабочих часов автомобиля в сутки
kt = 07 – коэффициент использования автомобиля по времени
Длина фронта подачи вагонов:
lв – длина ж.д. вагона по автосцепке l = 1473 м
aм – удлинение фронта подачи вагонов для выполнения маневровых работ aм = (15 2)
Длина фронта погрузки-выгрузки:
zс – число смен (перестановок) вагонов на грузовом фронте (zс = 1 2)
При установке автомобиля к рампе склада торцом:
k – число погрузочно-разгрузочных постов образующих фронт погрузки выгрузки (равно числу дверных проемов со стороны автотранспорта); k = 2
bа = габаритная ширина автомобиля м; bа = 25 м
Sт – расстояние между смежными автомобилями обеспечивающее выезд автомобиля при торцевой расстановке м; Sт = 1 м
Вместимость склада с учетом хранения
Определим общее количество порожних поддонов.
На складе 1440 поддонов загружены а 10% - порожние поддоны.
Определим количество пачек.
В одной пачке сложено 10 поддонов следовательно:
Определим геометрические размеры элементарной площадки под поддоны:
– длина элементарной площадки
– ширина элементарной площадки
– площадь элементарной площадки
Вместимость одного стеллажа
Zl Zh – количество ячеек по длине и ширине (Zl = 15 Zh = 8)
Определим количество стеллажей
Определим размеры стеллажа
Т.к. максимальный размер пакета составляет 1200 мм то длина ячейки Az = 1500 мм ширина ячейки Bz = 900 мм; высота пакета с поддоном составляет 1350 мм то высота ячейки Hz = 1500 мм.
Определим площадь площадки занятой стеллажами
r = 1000 мм – ширина проезда между стеллажами
nпр = 6 – количество проездов между стеллажами
Высота склада – 128 м
Ширина склада – 32 м
Высота рампы для ж.д. вагонов – 125 м
Высота рампы для автомобилей – 125 м
Ширина погрузочно-разгрузочной платформы для обслуживания ж.д. подвижного состава и автомобилей – 4 м
Расстояние от края платформы до оси ж.д. пути – 165 м
Расстояние от оси пути ж.д. пути до стены склада – 566 м
Размеры одного стеллажа м (Д х Ш х В) – 225 х 09 х 12
Расстояние между стеллажами – 1 м
Количество стеллажей – 12 шт
Выбор типа и количества погрузочно-разгрузочных машин
Электропогрузчик грузоподъемностью 1 т.
Технические характеристики электоропогрузчика:
Грузоподъемность – 1 т
Высота подъема груза – 2 м
Скорость подъема вил:
Скорость опускания вил:
Наибольшая скорость передвижения:
Дорожный просвет – 100 мм
Внешний радиус поворота – 1600 мм
Наименьшая ширина проездов под углом 90 - 2950 мм
Техническая производительность машин используемых при переработке тарно-штучных грузов находиться по формуле:
Gм – грузоподъемность машины т
Tц – продолжительность времени цикла с
Для погрузчика время цикла:
tдв t’дв – время затрачиваемое погрузчиком на продольные и поперечные передвижения по складу с грузом и без груза с
tпод t’под – время затрачиваемое на подъем каретки погрузчика с грузом и без груза с
tоп t'оп – время затрачиваемое на опускание каретки с грузом и без груза с
tпов – время затрачиваемое на повороты погрузчика с
tвсп – время затрачиваемое на вспомогательные операции
l – длина рабочего плеча м
v – скорость движения погрузчика мс
a – ускорение погрузчика мс2
Средняя высота подъема:
H – высота подъема груза погрузчиком
Определение эксплуатационной и сменной производительности
Эксплуатационная производительность погрузчика:
kв = 08 – коэффициент использования по времени
Сменная производительность:
Объем механизированной переработки груза:
mсм = 1 – количество смен
Tр – время нахождения машины в ремонте и смены батареи в течение года
Принимаем Мм = 2 машину с учетом одновременной разгрузки-погрузки автомобиля и одной ж.д. подачи.
Определение производительности крана-штабелера на складе базового варианта
Техническую производительность крана-штабелера в базовом варианте определим по формуле:
Gгр = 1000 кг – вес пакета
C – число циклов которое машина делает за 1 час
tц – время цикла сек
lp = 1185 м– средняя длина перемещения крана-штабелера
lv = 1 м – длина выдвижения грузозахватного органа
lk = 5 м – средняя высота подъема пакета
vp = 1 мс – скорость передвижения крана
vv = 025 мс – скорость выдвижения грузозахватного органа
vk = 1 мс – скорость подъема грузозахватного органа
Эксплуатационная и сменная производительность:
kв = 09 – коэффициент использования крана по времени
Определение производительности крана-штабелера на складе нового варианта
vp = 25 мс – скорость передвижения крана
vk = 2 мс – скорость подъема грузозахватного органа
Эксплуатационная производительность:
В результате анализируя полученные результаты можно сделать вывод о том что склад с новым вариантом крана-штабелера более предпочтителен с точки зрения производительности перед складом с базовым вариантом крана-штабелера так как эксплуатационная производительность нового крана-штабелера больше чем у базового крана-штабелера.
Определение количество кранов-штабелеров на складе
Т. к. на складе имеется 12 стеллажей: 2 стеллажа расположены раздельно (по краям склада) а 10 стеллажей расположены по парно т.е. пять пар стеллажей между стеллажами имеются проезды для кранов-штабелеров.
Для обслуживания 12 стеллажей требуется 6 кранов-штабелеров.
Технологическая часть
1.Разработка технологического процесса штока гидробуфера
В конструкторском разделе диплома выполнен основной расчет параметров гидробуфера.
Рассчитаны на прочность его основные детали в том числе и шток как наиболее ответственный элемент.
По заданию в технологической части необходимо разработать технологический процесс изготовления штока а именно выбрать заготовку составить маршрут изготовления подробно разработать токарную и шлифовальную операции составить на них эскизы.
1.1.Анализ технологических требований изготовления детали
Шток является оригинальной деталью что обосновывает целесообразность составления технологической карты его изготовления.
Деталь изготавливается в условиях единичного производства из стали 45 ГОСТ 1050-88 твердостью НВ 190 - 230 термообработка – нормализация. Она представляет собой 6-ти ступенчатый вал длиной 390 мм. Относится к группе цилиндрических изделий. Внутри - сплошной.
Первая ступень диаметром 20 мм и длиной 30 мм служит для нарезания резьбы обрабатывается с допуском h9 шероховатостью Rа = 08 мкм.
Вторая ступень диаметром 24 мм и длиной 15 мм служит для фрезерования на ней четырёхгранника обрабатывается с допуском h11 шероховатостью Rz40.
Третья ступень диаметром 45 мм и длиной 248 мм служит опорой для посадки уплотнения с допуском f9 шероховатостью Rа = 032 мкм.
Четвёртая ступень диаметром 61 мм и длиной 10 мм служит упорным буртиком специально не обрабатывается.
Пятая ступень диаметром 45 мм и длиной 52 мм является переходной ступенью специально не обрабатывается.
Шестая ступень диаметром 18 мм и длиной 38 мм служит для нарезания резьбы обрабатывается с допуском h9 шероховатостью Rа = 08 мкм.
Для удобства монтажа делаем фаски на ступенях: 1 2356 которые подрезаются на токарном станке при помощи проходного резца. Фаски не являются рабочими поэтому точность и шероховатость обеспечивается инструментом.
На поверхностях 1 и 6 необходимо нарезать резьбу после черновой и чистовой обработки. Поверхность 2 необходимо фрезеровать под четырёхгранник.
При изготовлении детали необходимо выдерживать допуски формы и расположения.
Допуск цилиндричности (табл. 24.2 [1]);
- для поверхностей 3 (45 f9 )
Тo = 05 .62 = 31 мкм. Принимаем Тo = 003 мм;
- для поверхности 6 (18 h9)
Тo = 05 .52 = 26 мкм. Принимаем Тo=003 мм;
- для поверхности 1 (20 h9)
Тo = 05 .52= 26 мкм. Принимаем Тo=003 мм;
Допуск перпендикулярности упорного буртика под поршень.
– степень точности допуска 7 (табл. 22.4 [9]);
Т = 0016 мм (табл. 22.8 [9]); Принимаем Т = 001мм
1.2.Выбор вида финишной обработки конструктивных элементов детали.
Для обрезки заготовки в размер сверления центровых отверстий и формирования профиля вала применим токарный станок 16К20.
Для поверхности 2 (24h12) 4 (61h14) 5 (45h14) с шероховатостью Rz 80 назначаем только черновое точение.
Для поверхности 2 (24h11) с шероховатостью Rz 40 назначаем получистовое точение.
Для поверхностей 1(20h9) 6 (18h9) с шероховатостью Ra 08 назначаем окончательное шлифование.
Для поверхностей 3 (45f9) для участка под манжетное уплотнение с Ra 032 назначаем полирование.
Фаски галтели и центровые отверстия получаем на токарном станке при закреплении заготовки в патрон.
Для получения резьбы используем резьбовой резец.
1.3.Выбор способа установки заготовки для её обработки.
Рассчитаем средний диаметр заготовки как:
где:n – число конструктивных элементов;
– диаметр и длина конструктивного элемента;
Определим коэффициент жесткости:
Т.к. Кж>12 то применяем установку в центрах с люнетом.
1.4.Выбор вида определение размеров заготовки типа и типоразмера центровых отверстий.
Для условий единичного или мелкосерийного производства и при несущественном перепаде диаметров для детали типа вал применяется в качестве заготовки круглый горячекатаный сортовой прокат.
При максимальном диаметре детали 61 мм и при К = рекомендуемый диаметр заготовки 65 мм.
Из номенклатуры круглого сортового проката выбираем сталь горячекатаную круглую ГОСТ 2590 – 88 обычной степени точности (В) 65 мм с предельными отклонениями +05; -11 допуск на заготовку составляет 16мм (Т = 16мм) что соответствует 16 квалитету.
Определим длину заготовки:
где Zто – припуск на торцевую обработку. При номинальном диаметре проката свыше 50 до 50 мм Zто = 3мм(по табл. П7 [10])
Центровые отверстия для токарной и шлифовальной обработки выбираем согласно ГОСТ 14034-74. Для детали 65 мм рекомендовано центровое отверстие В 63.
Выбираем: отверстие центровое В 63. ГОСТ 14034-74.
1.5.Составление укрупнённого маршрута изготовления детали.
Отрезать заготовку от проката круглого сечения обычной степени точности 65мм длиной 396мм.
Заготовку подвергнуть термообработке – нормализации до НВ 280.
Выполнить обработку торцов в размер 390 h14 и сверлить два центровых отверстия В 63. ГОСТ 14034-74.. За несколько технологических переходов выполнить обработку по формированию контура детали. Точить фаски канавки.
0 Кругло-шлифовальная
Выполнить предварительную и окончательную обработку шеек детали.
Фрезеровать многогранник.
Подвергнуть ТВЧ шейку вала 45f9под манжету.
Очистить детали от загрязнений;
Выполнить контроль детали по условиям чертежа;
2.Разработка операций по формированию контура детали.
2.1.Расчёт числа стадий обработки по каждому конструктивному элементу.
Ужесточение точности:
Число стадий обработки:
1.1.Расчёт точности промежуточных размеров заготовки по стадиям обработки.
Определим точность заготовки по каждой стадии механической обработки для каждой поверхности. При расчете шаг уменьшения квалитетов по стадиям механической обработки должен изменяться по закону убывающей арифметической прогрессии. Расчет ведём в табличной форме.
Таблица 1. Расчет точности промежуточных размеров
– ой 20h9 и 6 – ой 18h9
Обтачивание черновое
Обтачивание чистовое
Шлифование окончательное
Таблица 2. Расчет точности промежуточных размеров
Таблица 3. Расчет точности промежуточных размеров 3 – ей поверхности вала: 45f9
Для получения размера 24 и 5-ой поверхности с 45h14 61h14 и 24h12 используем только обтачивание черновое.
1.2.Определение промежуточных размеров по стадии механической обработки
Расчет ведем в табличной форме используя следующие формулы:
где: - припуск на обработку поверхности принимается из ;
d - текущий диаметр;
d() - диаметр предшествующей обработки;
- исходный размер ступени вала;
– максимальный размер ступени вала.
Таблица 4. Расчет припусков на промежуточные размеры 3 - ей ступени вала 45f9
Расчёт промежуточных размеров
Характеристика размера
Точение получистовое
Таблица 5. Расчет припусков на промежуточные размеры 1 - oй ступени вала 20h9
Таблица6. Расчет припусков на промежуточные размеры 6 - oй ступени вала 18h9
Таблица 7. Расчет припусков на промежуточные размер 2-ой ступени
Таблица 8. Расчет припусков на промежуточные размер 4-ой ступени
Таблица 9. Расчет припусков на промежуточные размер 5-ой ступени
Окончательно выбираем из сортамента прокат 65мм
2.Составление плана токарной и шлифовальной обработок детали
Расчёт выполняем из условия применения станка 16К20 имеющего следующие характеристики:
- допустимая мощность резания N = 75 кВт;
- максимальный диаметр заготовки до 400 мм;
- максимальная длина заготовки 1400 мм;
- частота вращения шпинделя 125 1600 обмин (регулирование ступенчатое);
- продольная подача суппорта 005 28 ммоб (регулирование ступенчатое).
2.1.Расчет предельно-допустимых глубин резания при черновом обтачивании.
Глубину резания для технологического перехода рассчитываем по формуле:
и сравниваем полученное значение с предельно допустимым для данного диаметра:
если обработка осуществляется за один переход
если обработка осуществляется за несколько технологических переходов.
Применим формулу с коэффициентом «005» т.к. Кж = 98>12.
При этом назначаем подачу инструмента и сравниваем мощность резания с допустимой мощностью на шпинделе (75 кВт).
Третья ступень: 4553
следовательно обработка по диаметрам возможна за 2 прохода.
Выполняем анализ по мощности:
При подаче инструмента S = 03 ммоб и глубине резания t = 487 мм мощность N = 72 кВт что меньше 75кВт (по табл. П13 [10]).
следовательно обработка по диаметрам возможна за 5 проходов.
При подаче инструмента S = 06 ммоб и глубине резания t = 21 мм мощность N = 71 кВт что меньше 75кВт (по табл. П13 [10]).
Первая ступень: 2056
следовательно обработка по диаметрам возможна за 1 проход.
При подаче инструмента S = 06 ммоб и глубине резания t = 197 мм мощность N = 71 кВт что меньше 75кВт (по табл. П13 [10]).
Четвёртая ступень: 61
При подаче инструмента S = 06 ммоб и глубине резания t = 2 мм мощность N = 72 кВт что меньше 75кВт (по табл. П13 [10]).
При подаче инструмента S = 04 ммоб и глубине резания t = 4 мм мощность N = 71 кВт что меньше 75кВт (по табл. П13 [10]).
Шестая ступень: 1856
следовательно обработка по диаметрам возможна за 8 проходов.
При подаче инструмента S = 06 ммоб и глубине резания t = 165 мм мощность N = 71 кВт что меньше 75кВт (по табл. П13 [10]).
3.Выбор и расчёт режимов резания.
3.1.Токарная обработка.
При черновом обтачивании применяем проходной резец с главным углом в плане φ = 450 стойкостью Т = 60 мин из материала Т15К6.
-для чернового обтачивания принимаем значение подачи из пункта 7.1.
-для получистового обтачивания:
. SТАБЛ = 087 при Rz = 40. (по табл. П11 [10])
где К3 = 045 (по табл. П11 [10])
Из нормального ряда продольных подач суппорта станка принимаем значение S = 04 ммоб.
Cv - коэффициент скорости зависящий от значения величины подачи.
Принимаем согласно (по табл. П14 [10]);
Т – расчётная стойкость резца в минуту. Принимаем согласно (по табл. П13 [10]);
t – глубина резания;
Коэффициент корректировки.
КMV – коэффициент учёта влияния материала заготовки на скорость резания; КПV – коэффициент учёта влияния состояния поверхности на скорость резания (по табл. П18 [10]);
КИV – коэффициент учёта влияния инструментального материала на скорость резания для материала Т15К6 (по табл. П19 [10]);
КφV – коэффициент учёта влияния главного угла в плане резца на скорость резания (по табл. П20 [10]).
КГ - коэффициент характеризующий группу стали по обрабатываемости.
Принимаем согласно (по табл. П17 [10]);
- предел выносливости. Принимаем согласно [4 табл.2] =600 МПа
nv – показатель степени. Принимаем согласно (по табл. П16 [10]).
Результаты вычислений сведены в таблицу 9.
1.1.Расчёт режимов шлифования.
Шлифование выполняем на шлифовальном станке 3Б151 который имеет следующие характеристики:
-наибольший диаметр и длина шлифуемой заготовки: 180 х 630(800) мм;
-диаметр и ширина шлифовального круга: 600 х 63 мм;
-частота вращения детали: 63 400 обмин (бесступенчатое регулирование);
-скорость продольного перемещения рабочего стола: 01 06 ммин (бесступенчатое регулирование);
-поперечная подача шлифовального круга (глубина шлифования): 00025 005 мм на один ход рабочего стола с шагом 00025 мм;
-непрерывная подача шлифовального круга при врезном шлифовании: 01 2 мммин;
-мощность электродвигателя привода шлифовального круга: 7 кВт.
1.2.Расчёт режимов предварительного шлифования.
Согласно [32] с. 302 для предварительного шлифования принимаем:
-скорость вращения шлифовального круга: vШЛ.КР. = 30 мс;
-скорость вращения заготовки: vЗАГ. = 20 ммин;
-продольная подача шлифовального круга: S = (03 07)ВШЛ.КР. = 189 441 ммоб. Принимаем S = 30 ммоб;
-глубина шлифования tШЛИФ = 001 мм;
-количество проходов шлифовального круга:
Частота вращения шлифовального круга:
Частота вращения заготовки:
Результаты вычислений сведены в таблицу 10.
1.3.Расчёт режимов окончательного шлифования.
Согласно [32] с. 302 для окончательного шлифования принимаем:
-скорость вращения шлифовального круга: vШЛ.КР. = 35 мс;
-скорость вращения заготовки: vЗАГ. = 35 ммин;
-продольная подача шлифовального круга: S=(02 04)ВШЛ.КР.=126 256 моб. Принимаем S = 20 ммоб;
-глубина шлифования tШЛИФ = 0005 мм;
Режимы токарной обработки вала.
Диаметр поверхности мм
Расчётное значение n мин-1
Принятое значение n мин-1
- Установ В (черновое обтачивание)
- Установ Г (черновое обтачивание)
- Установ Г (получистовое обтачивание)
- Установ Д (получистовое обтачивание)
Режимы шлифовальной обработки вала.
Расчётная мощность N кВт
- Установ А (шлифование окончательное)
- Установ Б (шлифование окончательное)
В ходе расчетно-пояснительной записки был разработан технологический процесс на изготовление детали – шток для единичного условия производства. В работе были применены технологические оборудования и инструменты: токарный станок 16К20 шлифовальный станок 3Б151 и резец Т15К6.
Оформлена технологическая документация на операции и переходы применяемые в ходе получения детали. Установлены и применены в ходе разработки техпроцесса основные принципы и приемы используемые при обработке металлов резанием.
Технико-экономические расчеты
1.Описание сравниваемых результатов. Исходные данные для расчетов.
Вилочный захват крана-штабелера включает в себя электромеханический привод в котором движение передается от электродвигателя к исполнительному механизму через карданный вал. Комплекс обслуживают 3 человека.
Вилочный захват крана-штабелера включает в себя гидравлический привод в котором движение исполнительного механизма происходит от электородвигателя соединённого непосредственно с рабочим органом а также механизмы передвижения и подъема в которых движение исполнительного механизма происходит от мотор-редуктора. Комплекс обслуживает 1 человек.
Исходные данныеТаблица 8.1.
Количество элементов привода:
гидроклапан давления
1.Определение барьерной ставки.
Барьерная ставка определяет ту финансовую отдачу которую инвесторы ожидают от своих капитальных вложений и включает в себя два компонента – свободную от риска ставку СРС и страховую премию СП.
Поэтому можно сказать что стоимость капитала предприятия представляет собой рыночную оценку уровня риска по операциям предприятия. Предприятия принимают эту оценку в качестве среднего значения барьерного коэффициента HR так как у них нет более объективного показателя.
Стоимость капитала – это средневзвешенная цена (в процентах) которую предприятие уплатило за денежные средства использованные для формирования своего капитала. Эта величина определяется соотношением заемного и собственного капиталов в пассивной части баланса и может быть определена следующим образом:
СК – стоимость капитала %;
СД – стоимость долга %;
ДСК – доля собственного капитала;
ССК – стоимость собственного капитала %.
Так как выплаты процентов по займам уменьшают величину налогооблагаемой прибыли то собственно уменьшается и величина налоговых выплат. Экономия на налогах частично компенсирует выплаты по долгам. Поэтому процент выплат по займам с учётом этой экономии составит:
СН – ставка налога на прибыль;
NE(СД) – уровень эффекта процентной ставки;
В условиях высокой инфляции ставки ссудного процента и депозитные ставки рассчитываются с учетом внутригодовых реинвестиций и очищаются от инфляции.
Берутся номинальные (т.е. с учетом инфляции) годовые ставки коммерческих банков. На их основе рассчитываются эффективные ставки (т.е. с учетом реинвестиций по периодам внутри года):
NE(СД ССК) – номинальная эффектная ставка (кредитная и депозитная соответственно)
N(кб дб) – номинальная банковская ставка (кредитная и депозитная соответственно)
p – число периодов начисления процентов внутри года.
2.Расчет инвестиций и расходов.
Кдв – капитальные вложения на закупку электродвигателей;
Кт – капитальные вложения на закупку тормозов;
Кр – капитальные вложения на закупку редукторов;
Кк.в. – капитальные вложения на закупку карданных валов;
Кмах – капитальные вложения на закупку маховиков;
Кмуфт – капитальные вложения на закупку муфт шарнирных;
Крем – капитальные вложения на закупку ремней.
Цдв – стоимость одного электродвигателя
Zдв – количество электродвигателей
γм – коэффициент учитывающий затраты на доставку и монтаж
Цт – стоимость одного тормоза
Zт – количество тормозов
Цр – стоимость одного редуктора
Zр – количество редукторов
Цк.в – стоимость одного карданного вала
Zк.в – количество карданных валов
Цмах – стоимость одного маховика
Zмах – количество маховиков
Цмуфт – стоимость одной муфты шарнирной
Цмуфт = 4060 (руб.);
Zмуфт – количество муфт шарнирных
Црем – стоимость одного ремня
Zрем – количество муфт шарнирных
Км.р. – капитальные вложения на закупку мотор-редукторов;
Кц – капитальные вложения на закупку гидроцилиндров;
Кн – капитальные вложения на закупку гидронасосов;
Краспр – капитальные вложения на закупку гидрораспределителей;
Кт.ж. – капитальные вложения на закупку жестких трубопроводов;
Ккл.дав. – капитальные вложения на закупку клапанов давления.
Кф – капитальные вложения на закупку фильтров;
Кб – капитальные вложения на закупку гидробака;
Кв – капитальные вложения на закупку вентиля.
Цм.т. – стоимость одного мотор-редуктора
Цм.т. = 25200 (руб.);
Zм.т. – количество мотор-редукторов
Цц – стоимость одного гидроцилиндра
Zц – количество редукторов
Цн – стоимость одного гидронасоса
Zн – количество гидронасосов
Цраспр – стоимость одного гидрораспределителя
Цраспр = 4594 (руб.);
Zраспр – количество гидрораспределителей
Цт.ж. – стоимость одного метра жесткой трубы
Lт.ж. – длина жесткой трубы
Цкл.давл. – стоимость одного гидроклапана давления
Цкл.давл. = 2400 (руб.);
Zкл.давл. – количество гидроклапанов давления
Zкл.давл. = 1 (шт.);
Цф – стоимость одного фильтра
Zф – количество фильтров
Цб – стоимость одного гидробака
Zб – количество гидробаков
Цв – стоимость одного вентиля
Zв – количество вентилей
3.Изменение расходов.
Сзаробщ – расходы на заработную плату обслуживающего персонала;
Сотч – отчисления на социальные нужды;
Снакл – накладные расходы (расходы на содержание административно-управленческого персонала);
Срем. – расходы на ремонт и техническое обслуживание;
Сэл – расходы на электроэнергию за год;
Саморт – амортизационные отчисления на реновацию.
Стар.зар. – тарифная заработная плата
Кп = 3 (чел) – количество обслуживающего персонала;
Тст = 6200 (руб) – тарифная ставка по должностям.
Сдоп. – доплата к заработной плате.
Сдоп.зар. – дополнительная заработная плата;
Цэл – тариф на электроэнергию : Цэл = 35 ркВтч ;
Ки – коэффициент использования оборудования по времени 07
Fэф – эффективный годовой фонд времени работы оборудования
Q – срок службы машины Q = 12 лет.
Кп = 1 (чел) – количество обслуживающего персонала;
Расчет чистых денежных потоков приведен в таблице 8.2.
Расчет чистых денежных потоков.
Приращение доходов и расходов
экономия заработной платы
отчисления на социальные нужды
расходы по содержанию и эксплуатации оборудования
расходы на электроэнергию
Корректировка денежных потоков:
Чистые денежные потоки
4.Чистая текущая стоимость (NPV)
Чистая текущая стоимость является суммой дисконтированных чистых денежных потоков порождённых капиталовложениями и определяется следующим образом:
ЧДП – чистый денежный поток руб.;
HR – барьерная ставка;
n – число лет функционирования проекта.
ЧДП берётся со знаком соответствующим оттоку или притоку денежных средств.
Положительное значение чистой текущей стоимости (NPV) говорит об эффективности рассматриваемого варианта.
Рассчитаем значения чистой текущей стоимости.
Внедрение и использование модернизированного захвата увеличивает производительность погрузочно-разгрузочных работ позволяет увеличить грузопоток что является основной экономической характеристикой склада и получить экономический эффект.
Безопасность жизнедеятельности.
1.Безопасность персонала при обслуживании проектируемого склада
1.1.Эксплуатационно-технические характеристики.
Режим работы по ГОСТ 25546-827К
Габариты перерабатываемого груза м:
Высота выдвигаемых элементов грузозахватного органа мм70
Величина выдвижения грузозахватного органа мм920
Скорость передвижения крана мс25
Скорость подъема грузозахватного органа мс2
Скорость выдвижения грузозахватного органа мс025
Техническая производительность тч178
Суммарная мощность двигателей кВт253
Тип нижнего путиР24 ГОСТ 6368-82
Тип верхнего путидвутавр 12 ГОСТ 8239-72
Подвод электропитаниякабельный
Управлениеавтоматическое
Климатическое исполнениеУХЛ4 ГОСТ 15150-69
Класс пожароопасностиП-2а
1.1.Требования к персоналу режимы работ квалификация
К управлению электропогрузчиком допускаются лица не моложе 18 лет прошедшие теоретическое и практическое обучение сдавшие экзамен и получившие удостоверение на право управления электропогрузчиком.
Перед допуском к работе водителю электропогрузчика необходимо пройти медицинское освидетельствование получить вводный инструктаж по охране труда первичный инструктаж на рабочем месте освоить безопасные приемы эксплуатации электропогрузчика; пройти проверку знаний в объеме II группы по электробезопасности теоретических знаний и приобретенных практических навыков безопасного выполнения работ по управлению электропогрузчика при подъеме транспортировке и укладке грузов.
Водитель электропогрузчика должен:
перед началом работы проверить техническое состояние погрузчика;
обладать навыками требующимися для управления всеми механизмами погрузчика и ухода за ним;
знать правила безопасного перемещения грузов;
соблюдать действующие в организации правила внутреннего трудового распорядка график работы режим труда и отдыха.
извещать своего непосредственного руководителя о происшедшем с ним или по его вине несчастном случае а также о любом несчастном случае происшедшем на производстве об ухудшении состояния своего здоровья в том числе о проявлении признаков острого заболевания.
Режим работ водителей электрпогрузчиков по 12 часов в 1 смену.
1.2.Основные опасности и вредности при работе персонала
Во время работы персонала на складе могут воздействовать следующие опасные и вредные производственные факторы:
столкновение или наезд на людей или другим транспортным средством;
падение перевозимого груза.
удар электрическим током
неустойчивые штабели перемещаемых и складируемых товаров; повышенная запыленность воздуха рабочей зоны;
недостаточная освещенность места проведения работ;
острые кромки заусенцы и шероховатости на поверхностях деталей инструмента;
опасный уровень напряжения в электрической цепи.
движущиеся и вращающиеся детали и узлы крана-штабелера;
При работе с различными грузами возможно влияние таких опасных и вредных производственных факторов как токсические раздражающие сенсибилизирующие канцерогенные мутагенные влияющие на репродуктивную функцию.
1.1.Технические и организационные мероприятия по обеспечению персонала при работе на складе.
Поскольку персонал работает на складе то рассмотрим проблему освещения рабочего места.
Требования к освещению.
Оборудование электрического освещения производственных и бытовых помещений сборочно-сварочных цехов и участков должно соответствовать нормам установленным в СН 245-71 и СНиП 23-05-95.
В зависимости от вида источника света производственное освещение подразделяется:
на естественное которое создается излучением поступающим непосредственно от Солнца без изменения направления распространения и диффузным (отраженным и рассеянным атмосферой) солнечным светом;
искусственное обеспечиваемое электрическими светильниками.
Естественный (солнечный) свет по спектральному составу значительно отличается от излучения электрических источников.
В солнечном спектре гораздо больше необходимых человеку ультрафиолетовых лучей. Для естественного освещения характерна высокая степень рассеяния света благоприятная для зрительной работы.
Рис. 5.4. Схемы распределения коэффициента естественной освещенности е по разрезу помещения:
а - одностороннее боковое освещение; б - двустороннее боковое освещение; в - верхнее освещение; г - комбинированное освещение; 1 - уровень рабочей плоскости; еmin и еср - минимальное и среднее значения коэффициента естественной освещенности
В соответствии с конструктивными особенностями помещения естественное освещение может быть (рис. 5.4):
боковым (осуществляется через окна в наружных стенах);
верхним (производится через аэрационные и зенитные фонари проемы в покрытиях и световые проемы в местах перепада высоты смежных пролетов зданий);
комбинированным (к верхнему освещению добавляется боковое).
Искусственное освещение предусматривается в тех случаях когда естественного света недостаточно или он отсутствует.
По конструктивному исполнению осветительной системы искусственное освещение может быть:
местным создающим световой поток непосредственно на рабочем месте;
общим (освещается все помещение);
комбинированным (к общему освещению добавляется местное).
Общее освещение подразделяется на равномерное и локализованное создаваемое с учетом расположения рабочих мест.
Ряд единиц необходимых для расчета искусственного освещения вытекает из задач данного мероприятия. Эти единицы нормированы и поддержание их обеспечивает оптимальное распределение световой энергии а значит позволяет выполнить поставленные задачи. Основные параметры которые учитываются при расчете искусственного освещения таковы:
Световой поток. Данная величина измеряемая в люменах (лм) существенна для расчета искусственного освещения поскольку характеризует мощность лучистой энергии в 1 Вт.
Освещенность. Эта характеристика измеряемая в люксах (лк) важна для расчета искусственного освещения поскольку определяет отношение светового потока к площади освещаемой поверхности.
Сила света измеряется в канделах (кд) и учитывается при расчете искусственного освещения потому что характеризует плотность светового потока.
Светимость важна для расчета искусственного освещения в силу того что определяет отношения светового потока к источнику освещения. Принятая единица измерения – лмм2.
Яркость. Эта величина принципиальна для расчета искусственного освещения потому что определяет отношение силы света к освещаемой поверхности.
Для расчета искусственного освещения специалисты прибегают к различным методам: точечному методу методу удельных мощностей и методу коэффициента использования светового потока.
Точечный метод расчета искусственного освещения
Его особенность состоит в том что учитывается отраженная световая энергия. Расчет искусственного освещения производится опираясь на показатели силы света (I кд) высоты подвеса осветительного прибора (H м) а также коэффициент запаса (11 5 - 18).
Для расчета искусственного освещения данным методом используются отдельные формулы для горизонтальной и вертикальной плоскости:
Ег=I*cos3αН 2 *К3 - для горизонтальной плоскости
Ев= I*cos3 (90-α) Н 2 *К3 - для вертикальной плоскости
При расчете искусственного освещения помещения или пространства несколькими светильниками освещенность определяется от каждого источника а затем показатели суммируются.
Следовательно формула для расчета искусственного освещения в данном случае усложняется ведь необходимо учесть и количество ламп (n) и коэффициент дополнительной освещенности точки ( 11 - 12) и световой поток лампы (Фл лм) и сумму условных освещенностей от светильников которые светят в данную точку (ΣЕг) и условный световой поток (1000 лм). Поэтому при расчете искусственного освещения для нескольких светильников используется формула:
Расчет искусственного освещения методом удельных мощностей
Достоинство данного метода расчета искусственного освещения состоит в простоте а слабая сторона – в недостаточной точности. Потому эта техника применяется при первичных расчетах. Суть подобного расчета искусственного освещения сводится к определению количества светильников того или иного типа с помощью таблиц удельных мощностей.
В подобных специальных таблицах указаны удельные мощности источников освещения в зависимости от площади освещаемой поверхности типов светильников высоты их подвеса необходимой освещенности. При этом в ходе расчета искусственного освещения используют формулу удельной мощности:
где n - число ламп в светильниках
Рл - мощность лампы Вт;
S - площадь освещаемого помещения м2.
Таком образом с помощью данной формулы расчета искусственного освещения можно определить количество светильников которое необходимо для освещения данной площади и электрическую мощность приборов.
Расчет искусственного освещения методом коэффициента использования светового потока
Данный метод расчета искусственного освещения считается самым популярным. Его сущность состоит в определении светового потока необходимого для достижения заданных показателей освещенности. При расчете искусственного освещения таким способом учитывается отраженный свет и необходимость в равномерном распределении светового потока. Формулы которые используются для расчета искусственного освещения зависят от вида источника освещения.
Расчет искусственного освещения для ламп накаливания и ламп типов ДРЛ ДРИ и ДНат:
где F—световой поток одной лампы лм;
Е—нормированная освещенность лк;
S—площадь помещения м2;
z—коэффициент неравномерности светильника (для стандартных светильников 11—13);
Kз — коэффициент запаса;
n - число светильников;
u —коэффициент использования зависящий от типа (055—060)
Расчет искусственного освещения для люминесцентных ламп:
F=( E*S*z*Kз)(n*Фл* )
где Фл - световой поток лампы лм;
- коэффициент использования светового потока осветительной установки.
Защитное заземление.
Одним из основных опасных факторов при обслуживании ПФМ является возможность поражения электрическим током. Для защиты применяют защитное заземление.
Заземление электроустановки — преднамеренное электрическое соединение ее корпуса с заземляющим устройством.
Заземление электроустановок бывает двух типов: защитное заземление и зануление которые имеют одно и тоже назначение - защитить человека от поражения электрическим током если он прикоснулся к корпусу электроприбора который из-за нарушения изоляции оказался под напряжением.
Защитное заземление - преднамеренное соединение с землей частей электроустановки.
Принцип действия защитного заземления – снижение до безопасных значений напряжений прикосновения и шага обусловленных замыканием на корпус. Это достигается уменьшением потенциала заземленного оборудования а также выравниванием потенциалов за счет подъема потенциала основания на котором стоит человек до потенциала близкого по значению к потенциалу заземленного оборудования. Область применения защитного заземления – трехфазные трехпроводные сети напряжением до 1000 В с изолированной нейтралью и выше 1000 В с любым режимом нейтрали (рис. 9.2.1.).
Рис. 9.2.1. Принципиальные схемы защитного заземления
В случае возникновения пробоя изоляции между фазой и корпусом электроустановки корпус ее может оказаться под напряжением. Если к корпусу в это время прикоснулся человек - ток проходящий через человека не представляет опасности потому что его основная часть потечет по защитному заземлению которое обладает очень низким сопротивлением. Защитное заземление состоит из заземлителя и заземляющих проводников.
Есть два вида заземлителей – естественные и искусственные.
К естественным заземлителям относятся металлические конструкции зданий надежно соединенные с землей.
В качестве искусственных заземлителей используют стальные трубы стержни или уголок длиной не менее 25 м забитых в землю и соединенных друг с другом стальными полосами или приваренной проволокой. В качестве заземляющих проводников соединяющих заземлитель с заземляющими приборами обычно используют стальные или медные шины которые либо приваривают к корпусам машин либо соединяют с ними болтами. Защитному заземлению подлежат металлические корпуса электрических машин трансформаторов щиты шкафы.
Защитное заземление значительно снижает напряжение под которое может попасть человек. Это объясняется тем что проводники заземления сам заземлитель и земля имеют некоторое сопротивление. При повреждении изоляции ток замыкания протекает по корпусу электроустановки заземлителю и далее по земле к нейтрали трансформатора вызывая на их сопротивлении падение напряжения которое хотя и меньше 220 В но может быть ощутимо для человека. Для уменьшения этого напряжения необходимо принять меры к снижению сопротивления заземлителя относительно земли например увеличить количество искусственных заземлителей.
При замыкании одной из токоведущих крана выполненный из проводящего материала (металл) он оказывается под напряжением.
Прикосновение к корпусу крана человека (так называемое косвенное прикосновение) приводит к возникновению тока через него Iч который может привести к электротравме.
В целях электробезопасности необходимо проводящий корпус электроустановки заземлить т.е. выполнить электрическое соединение проводящих частей электроустановки (нормально не находящихся под напряжением) с проводящими частями находящимися в электрическом контакте с землёй и называемыми заземлителем.
Совокупность заземлителя и проводников соединяющих заземлитель с проводящим корпусом электроустановки называют заземляющим устройством.
Откуда видно что при электрическом соединение корпуса электроустановки с заземлителем Rзу происходит параллельное соединение сопротивлений человека Rч и заземлителя Rзy.
Тогда величина тока через человека составит:
где: Iз – ток замыкания на землю.
Если поставить условие Rзу « Rч то
т.е. защитное заземление уменьшает величину тока через человека в соотношение
раз. При отсутствии заземляющего устройства (Rзу = Iч = Iз.
А так как электрическое сопротивление человека принимается величиной постоянной равной 1000 Ом то необходимые условия электробезопасности (допустимый ток через человека Iчдоп) при установленном значении тока замыкания Iз могут быть достигнуты только при определенном значении Rзу.
Величина тока замыкания в общем случае определяется напряжением и схемой электрической сети к которой подключена электроустановка.
Характеристика воздействия на человека электрического тока различной силы
Переменный ток 50-60 Гц
Лёгкое дрожание пальцев рук
Сильное дрожание пальцев рук
Руки с трудом но ещё можно оторвать от электродов. Сильные боли в руках особенно в кистях и пальцах.
Руки парализуются оторвать их от электродов не возможно. Очень сильные боли. Затрудняется дыхание.
Ещё большее уселение нагревания незначительное сокращение мышц рук.
Паралич дыхания. Начало трепетания желудочков сердца.
Сильное ощущение нагревания. Сокращение мышц рук. Судороги. Затруднение дыхания.
Паралич дыхания и сердца при воздействии более 01с
На рисунке приведены результаты экспериментального исследования зависимости значений «опускающего» тока от индивидуальных качеств человека.
На рисунке графически представлена область предельно допустимых значений тока и длительность его протекания через человека с вероятностью 995 % не вызывающих фибрилляцию сердца (А – область недопустимых значений).
По Дальцилу граница областей допустимых значений тока через человека и длительности его протекания определяется выражением:
где: I – предельно допустимый ток через человека мА;
Т – длительность протекания тока через тело человека с.
Предельно допустимые уровни напряжений прикосновения.
Неощутимое напряжение В для t ≤ 10 мин
Отпускающее напряжение В t ≤ 30 c
Нефибрилляционное напряжение В t = 10 с
Предельная величина Uпр
Предельно допустимые уровни токов прикосновения.
Неощутимый ток мА t ≤ 10 мин
Отпускающий ток А t ≤ 30 c
Нефибрилляционный ток А t = 10 с
Главным средством для обеспечения безопасности обслуживании стенда обкатки редуктора является заземление.
Предполагается сооружение заземлителя с внешней стороны участка с расположением вертикальных электродов в один ряд длиной 20 м; материал - круглая сталь диаметром 20 мм метод погружения - ввертывание; верхние концы вертикальных стержней погруженные на глубину 07 м приварены к горизонтальному электроду из той же стали.
Требуемое сопротивление заземления:
1.1.Техника безопасности при обслуживании склада
Т.к. на складах основной опасностью для работников является транспорт который перемещается внутри склада т.е. электропогрузчики.
Все операции связанные с техническим обслуживанием устранением неисправностей очисткой двигателя и машины q.t грязи и подготовкой машины к работе выполняют при остановленном двигателе.
Работы ведут в соответствии с паспортом и инструкцией по эксплуатации завода-изготовителя. Запрещается выполнять операции не соответствующие назначению и технической характеристике сменного рабочего оборудования.
Работа погрузчика допускается только на освещенных площадках и внутриобъектных дорогах с твердым и ровным покрытием с уклоном не более 5°. Запрещается работать на захламленных имеющих выбоины и рытвины площадках. Зимой площадки и дороги должны быть очищены от снега и льда и посыпаны песком золой или шлаком.
Контейнеры поддоны и штучные грузы допускается штабелировать на площадках с уклоном не более 1°. Запрещается работать с неисправными контейнерами поддонами и другими пакетирующими приспособлениями.
Строповочные приспособления ежедневно осматривают и проверяют соответствуют ли они нормативным документам. Не допускается работа с приспособлениями имеющими дефекты.
Груз поднимают при отклоненном назад грузоподъемнике и за торможенном погрузчике. Груз распределяют равномерно по ширине вил а при работе со стрелой — по продольной оси машины. Запрещается поднимать груз масса которого превышает норму указанную в технической характеристике а также примерзший или защемленный какими-нибудь предметами. Если груз выходит за габариты вилочный подхватов его закрепляют.
При движении погрузчика запрещается поднимать или опускать груз менять наклон грузоподъемника. Груз закрывающие обзор пути движения перевозят в сопровождении помощника который следит за дорогой. Запрещается на погрузчике перевозить людей.
На автомобильные дороги общего назначения погрузчики выезжай в исключительных случаях соблюдая при этом Правила дорожного движения. При езде по дороге ночью погрузчик должен быть оснащен средствами световой сигнализации и освещения.
После окончания работы и при длительных перерывах в работе грузоподъемник с грузом опускают в крайнее нижнее положение.
При проведении технического обслуживания и ремонта соблюдают следующие правила техники обслуживания и ремонта. Запрещается находиться под погрузчиком и под грузоподъемником при работающем двигателе.
Все работники должны соблюдать технику безопасности складского хозяйства стеллажного хранения груза:
работники должны ходить по тому маршруту в котором указан в маршрутной карте;
запрещается находиться под стеллажами и в межстеллажном пространстве если не связанно с его обязанностью.
запрещается находиться в местах работающего крана-штабелера т.к. это может привести к травматизму.
2.Безопасность персонала в чрезвычайных ситуациях
2.1.Пожарная безопасность на складах.
Организация работ по пожарной безопасности должна включать:
разработку и внедрение системы управления пожарной безопасностью согласно требованиям руководящих документов;
общее руководство и контроль за состоянием пожарной безопасности на предприятии контроль за соблюдением законодательных и иных нормативных правовых актов требований правил и инструкций по пожарной безопасности. Контроль за выполнением служебных обязанностей подчиненными;
обеспечение пожарной безопасности при проведении технологических процессов эксплуатации оборудовании производстве пожароопасных работ;
установка и контроль за состоянием средств контроля оповещения и пожаротушения;
организацию разработки и обеспечение выделения финансовых средств на реализацию мероприятий по обеспечению пожарной безопасности;
проведение обучения и инструктажа работников предприятия по пожарной безопасности;
обеспечение электробезопасности предприятия.
Установка и контроль за состоянием средств контроля оповещения и пожаротушения.
Обучение по пожарной безопасности специалистов служащих и рабочих включает:
- проведение вводного первичного повторного внепланового и целевого инструктажей;
- организация занятий по пожарно-техническому минимуму;
- проведение учений и противопожарных тренировок.
Система пожарной сигнализации склада выполняет задачу обнаружения места возгорания и оповещения об этом соответствующих служб. Кроме того она должная быть связана с системами автоматического пожаротушения и дымоудаления которые локализуют очаги возгорания ещё до приезда пожарных служб. Установка на складе охранной и пожарной сигнализации значительно повышает безопасность склада и материальных ценностей а также обеспечивает своевременное оповещение пожарных служб.
Система охранной сигнализации - одна из составляющих комплексной системы безопасности склада представляет собой совокупность совместно действующих технических средств охранной сигнализации устанавливаемых на охраняемом объекте и объединенных системой инженерных сетей и коммуникаций. Системы охранной сигнализации не зависят от человеческого фактора и своевременно оповещают службы охраны о проникновении или попытке проникновения на склад с фиксацией факта места и времени нарушения рубежа охраны.
Последние две системы безопасности для складов можно объединить в одну что и предлагают многие российские и зарубежные производители оборудования. Современная охранно-пожарная сигнализация (ОПС) склада - представляет собой комплекс оборудования обеспечивающего пожарную безопасность склада и своевременное обнаружение проникновения в охраняемую зону а также оповещение о месте возникновения пожара на объекте.
Установки пожарной автоматики (УПА) занимают ведущее место в обеспечении пожарной безопасности различных объектов включая производственные складские административные здания и подвижной состав железнодорожного транспорта.
Действующие сегодня законодательные и иные нормативные правовые акты по пожарной Согласно ГОСТ 12.1.004-91 "Пожарная безопасность. Общие требования" противопожарная защита должна достигаться в первую очередь применением автоматических установок пожарной сигнализации и пожаротушения.
Широкое внедрение средств пожарной автоматики позволят значительно сократить количество крупных пожаров и ущерб от них.
В целом по стране число пожаров и ущерб от них на объектах оборудованных УПА соответственно в 30 и 40 раза меньше в сравнениями с показателями пожаров на объектах на которых средства пожарной автоматики отсутствуют.
Очень важную роль в предотвращении пожаров и обнаружении очага возгорания играет своевременная информация о месте возникновения пожара. Для этой цели служит автоматическая пожарная сигнализация. Системы пожарной сигнализации включают в себя пожарные извещатели линейные сооружения линии связи и приемные пульты станций.
Рассмотрим виды пожарных извещателей:
Тепловые извещатели реагируют на изменение температуры в помещении. Выпускаются тепловые извещатели максимальной температуры и максимально-дифференциальные. Детекторы максимальной температуры имеют некоторый фиксированный порог и срабатывают; когда температура окружающей среды в помещении достигнет порогового значения. Максимально- дифференциальные извещатели реагируют не только на величину температуры но и на скорость ее нарастания т.е. на производную температуры по времени. Отсюда и их название. В большинстве случаев максимально-дифференциальные извещатели раньше обнаруживают возгорание чем детекторы максимальной температуры.
Площадь контролируемая одним точечным тепловым пожарным извещателем а также максимальное расстояние между извещателями извещателем и стеной необходимо определять по таблице 8 но не превышая величин указанных в технических условиях и паспортах на извещатели.
Наиболее распространены оптические дымовые извещатели. Их принцип действия заключается в следующем. В дымовой камере под углом 120 градусов установлены излучатель и фотоприемник. Конструкция камеры выполнена таким образом что в дежурном режиме ИК-излучение от светодиода не попадает на фотоприемник. При поступлении дыма в камеру его частицы рассеивают ИК-излучение и оно достигает фотоприемника. При определенной концентрации дыма и следовательно достаточном количестве отраженного излучения происходит срабатывание извещателя.
Площадь контролируемая одним точечным дымовым пожарным извещателем а также максимальное расстояние между извещателями извещателем и стеной за исключением случаев оговоренных в п. 12.20 необходимо определять по таблице 5 но не превышая величин указанных в технических условиях и паспортах на извещатели.
Ручные извещатели являются обязательным компонентом любой системы пожарной сигнализации. Их назначение - подача сигнала о пожаре при его обнаружении персоналом здания. Ручные пожарные извещатели устанавливают на стенах и конструкциях на высоте 15 м от уровня пола или земли. Максимальное расстояние между двумя ближайшими ручными извещателями внутри помещений – не более 50 м а вне помещения – 150 м; ввод проводов в корпус извещателя – трубный. В случае неисправности на извещатель следует повесить табличку с соответствующей надписью.
Выносная сигнализация пожарной безопасности складов служит для подачи сигнала тревоги и выполняется в соответствии с требованиями НПБ 104-2003 «Системы оповещения и управления эвакуацией людей при пожарах в зданиях и сооружениях». В качестве прибора оптической сигнализации пожарной безопасности складов используются лампы накаливания мощностью 25 Вт для защиты которых служит светосигнальная арматура со стеклянным плафоном окрашенным в красный цвет защищенная металлической сеткой. Система сигнализации пожарной безопасности складов монтируется с помощью арматуры установленной с фасадной стороны здания на высоте не менее 275 м от земли и крепится к стене здания или на металлическом кронштейне. В качестве арматуры допускается использовать светильники типа НПП05 ПСХ НСП (исполнение полностью пылезащищенное).
В качестве акустического сигнализатора пожарной безопасности складов применяют сирены ревуны звонки мощностью до 20 Вт. Приборы звуковой сигнализации устанавливают на наружной стене здания с фасадной стороны на высоте 275 м от земли и выполняются в металлическом корпусе.
Инструкция по противопожарной защите высотного стеллажного склада
I. Следует использовать автоматическую систему пожарной сигнализации
с применением датчиков реагирующих на присутствие газов и дымов (например ионных датчиков) или иных устройств которые при возникновении пожара обеспечивают оповещение пожарных служб на предприятии или в населенном пункте. Датчики следует размещать в горизонтальных плоскостях на расстоянии около 8 м друг от друга. Такая их расстановка не оказывает принципиального влияния на решение строительной части здания.
В крыше здания должны быть предусмотрены отверстия для отвода
газов дыма и горячего воздуха. Эти отверстия должны быть оборудованы клапанами с автоматическим открыванием. Отверстия должны занимать
—5% поверхности крыши (поскольку наличие дыма и газов затрудняет
операцию тушения и. кроме того может быть причиной взрыва).
На расстоянии не более 50 м друг от друга следует предусмотреть
устройство поперечных (относительно пролетов) переходов через весь склад.
Такие переходы должны иметь ширину не менее 0.8 м и высоту не менее
9 м В железобетонных складах эти переходы должны быть снабжены
противопожарными дверями имеющими такую же огнестойкость что и сте-
на. разделяющая отдельные камеры. В каждом переходе следует разместить
два гидранта со шлангами и брандспойтами. подача воды к которым осуществляется из двух независимых источников.
Следует предусмотреть необходимую систему аварийных выходов и
лестниц оборудованную соответствующими указателями и аварийным освещением. Эти коммуникационные пути должны быть всегда доступными.
1.Выводы: в данном разделе был проведен расчет заземления крана-штабелера выбраны средства заземления предложено определенное количество стержней заземления для хорошего отведения тока а так же рассмотрена техника безопасности при пожаре приведена инструкция по противопожарной защите высотного стеллажного склада.
Практическое обеспечение безопасности жизнедеятельности при проведении технологических процессов и эксплуатации технических систем во многом определяется решениями и действиями инженеров и техников. Руководитель производственного процесса обязан:
-обеспечивать оптимальные (допустимые) условия деятельности на рабочих местах подчиненных ему сотрудников;
-идентифицировать травмирующие и вредные факторы сопутствующие реализации производственного процесса;
-обеспечивать применение и правильную эксплуатацию средств защиты работающих и окружающей среды;
-постоянно (периодически) осуществлять контроль условий деятельности уровня воздействия травмирующих и вредных факторов на работающих;
-организовывать инструктаж или обучение работающих безопасным приемам деятельности;
-лично соблюдать правила безопасности и контролировать их соблюдение подчиненными;
-при возникновении аварий организовывать спасение людей локализацию огня воздействия электрического тока химических и других опасных воздействий.
В данном дипломном проекте был выполнен анализ существующих конструкций стеллажных кранов-штабелеров. Были отмечены их недостатки и были предложены варианты усовершенствования их конструкции.
Была разработана конструкция одноколонного стеллажного крана-штабелера с гидравлическим приводом телескопического захвата. Произведена разработка отдельных узлов с соответствующими расчетами.
Выполнена разработка организации работ с применением стеллажного крана-штабелера.
Так же был разработан технологический процесс изготовления штока гидравлического буфера. Были применены в ходе разработки технологического процесса основные принципы и приемы изготовления штока.
Внедрение и использование в стеллажном кране-штабелере гидравлического привода захвата а также были заменены приводы передвижения и подъема которые позволяют получить экономический эффект что и было доказано в экономической части.
Также были рассмотрены вопросы техники безопасности при использовании стеллажных кранов-штабелеров. Затронута тема пожарной безопасности.
Список используемой литературы
Зерцалов А.И. Певзнер Б.И. Бененсон И.И. Краны-штабелеры. – М.: Машиностроение 1986. – 320 с. ил.
Анурьев В.И. Справочник конструктора- машиностроителя – М.: Машиностроение 1988. – 557 с.
Свешников В.К. Усов А.А. Станочные гидроприводы – М.: Машиностроение 1988. – 510 с.
Жуков В. И. Федосов В. Д. Пономарев В. М. Автоматические средства пожарной безопасности на железнодорожном транспорте: Методические указания. – М: МИИТ. 2010. – 186 с
Юдин Е.Я. Охрана труда в машиностроении – М.: Машиностроение 1983. – 423 с.
Руденко Н.Ф. Александров М.П. Лысяков А.Г. Курсовое проектирование грузоподъемных машин – М.: Машиностроение 1971. – 457 с.
Маликов О.Б. Проектирование автоматизированных складов штучных грузов. Л.: Машиностроение 1981. – 240 с.
Смехов А.А. Автоматизированные склады. 3-е изд. М.: Машиностроение 1979. – 288 с.
Аверкин В.А. Зиновен Н.А.Задание и методические указания к курсовой работе по дисциплине «Экономика производства» М. МИИТ 2000г.
Дунаев П.Ф. Леликов О.П. Конструирование узлов и деталей машин М. “Высшая школа” 1985г.
Справочник технолога-машиностроителя: 4-е издание в 2-х т. под ред. Косиловой А.Г. Мещерякова Р.К. -М. “Машиностроение” 1985.
Краткий справочник металлиста 3-е издание под ред. Орлова П.Н. Скороходова Е.А. -М.: «Машиностроение» 1987.
Проектирование технологических процессов изготовления деталей подъёмно-транспортных строительных и дорожных машин. 2-я часть В.И. Фомин – М: «МИИТ» 2009.
Рецензия Лавриненко.docx
« Разработка автоматизированного склада для пакетированных грузов».
Дипломный проект выполнен в объеме 161 страницы расчетно-пояснительной записки графическая часть 9 листов конструкторско-технической документации. Работа проведена по актуальной тематике в области автоматизации складских работ с пакетированными грузами.
Графическая часть и расчетно-пояснительная записка выполнена с соблюдением требований ЕСКД аккуратно и включает в себя разработку организации ПРТС работ конструкторской и технологической части разработана технологическая безопасность и проведен технико-экономический расчет.
При разработке проекта автор показал что он владеет инженерными методами расчета анализирует полученные результаты и выполняет графическую часть с помощью программ «Компас» и «Word».
Расчетно-пояснительная записка выполнена с помощью программ «Word» «MC-Cat» и «АРМ Winmachine».
Это определило достижение поставленной цели в дипломной работе – создание автоматизированного склада с краном-штабелером имеющего повышенную производительность при складировании пакетов при сроке хранении 10 суток на стеллажах высотой 12 метров.
В качестве замечаний необходимо отметить:
В дипломном проекте отсутствует схема автоматики поэтому не ясно как осуществляется регулирование скорости приводов для реализации заданной программы при разгоне и торможении рабочих органов;
Не везде даны ссылки на используемую литературу.
В целом дипломант Лавриненко Р. А. показал что он в достаточной степени владеет инженерными методами работы выполненный им проект соответствует предъявленным требованиям и заслуживает положительной оценки а Лавриненко Р. А. присвоения ему квалификации инженера.
Главный специалист к.т.н
на дипломную работу «Разработка автоматизированного склада для пакетированных грузов».
студента группы ТДМ-544 Лавриненко Р. А.
За время проектирования Лавриненко Р. А. показал хорошие знания по специальным дисциплинам. Способен самостоятельно решать инженерные задачи.
Основным направлением выбрал: разработку автоматизированного склада с краном-штабелером автоматического управления.
Достаточно полно использовал нормативно техническую документацию и новую техническую литературу. Расчетно-пояснительная записка и чертежи выполнены с помощью программ «Бауэр мотор-редуктор» «APM Winmachine» «Компас» «MS Word» с соблюдением требований ЕСКД. Все это определило достижение поставленной цели в дипломной работе – разработки автоматизированного высотного склада с кранами-штабелерами обслуживающими высотные стеллажи и снабженными автоматическими приводами.
Вполне заслуживает положительной оценки и присвоения квалификации инженер-механик по специальности «Подъемно-транспортные строительные дорожные машины и оборудование».
Руководитель дипломного
проектирования к. т. н.
Титульный лист.doc
ЖЕЛЕЗНОДОРОЖНОГО ТРАНСПОРТА
ГОСУДАРСТВЕННОЕ ОБРАЗОВАТЕЛЬНОЕ УЧРЕЖДЕНИЕ ВЫСШЕГО
ПРОФЕССИОНАЛЬНОГО ОБРАЗОВАНИЯ
«МОСКОВСКИЙ ГОСУДАРСТВЕННЫЙ УНИВЕРСИТЕТ
ПУТЕЙ СООБЩЕНИЯ» (МИИТ)
Зав. кафедрой «ПСМ и РК»
Руководитель проекта ( )
Консультант по экономическим вопросам ( )
Консультант по технологическим вопросам ( )
Консультант по вопросам безопасности
жизнедеятельности ( )
Пояснительная записка.doc
В народном хозяйстве нет предприятий не имеющих в своем составе складов. А в такой отрасли как материально-техническое снабжение склады являются основными производственными подразделениями.
Склады в системе материально-технического снабжения должны обеспечивать в установленном ритме основное производство материально-техническими ресурсами в потребных количествах и ассортименте. Причем поставка продукции должна осуществляться в объемах менее транзитных норм отгрузки чтобы не создавать излишних производственных запасов на промышленных предприятиях. Наиболее распространенной складской продукцией являются тарно-штучные грузы к которым обычно относят грузы любых видов упакованные в тару и хранимые на поддонах в ящичной таре или в контейнерах.
На грузовых фронтах всех складов выполняют погрузочно-разгрузочные операции которые отличаются высокой интенсивностью особенно в пунктах стыка различных видов транспорта. Под влиянием технического прогресса и прежде всего развития вычислительной и подъемно-транспортной техники крупные складские системы превращаются в современные предприятия с четко организованным автоматизированным технологическим процессом – транспортно-складские (грузовые) комплексы (ТСК). Четкий ритм их функционирования обеспечивают сложные автоматизированные поточно-транспортные системы (ПТС) которые по структуре и масштабам напоминают автоматизированные поточные технологические линии современных промышленных предприятий. ПТС состоят из конвейеров упаковочных пакетоформирующих и пакеторазборочных агрегатов автоматизированных складских и погрузочно-разгрузочных машин накопителей и др. Классификация ТСК по функциональному принципу дана на рис. 1. Могут быть также предложены в зависимости от потребностей практики другие частные признаки классификации например тип подъемно-транспортного оборудования вариант объемно-планировочного решения взаимное расположение погрузочно-разгрузочных путей и автопроездов и др.
Рис.1 . Классификация транспортно-складских комплексов
Склады представляют собой сложное хозяйство оснащенное высокопроизводительным специальным оборудованием. До недавнего времени основными средствами механизации работ на складах тарно-штучных грузов служили мостовые краны напольные погрузчики и штабелеры. Однако по мере роста потребности в складских помещениях все более очевидными стали недостатки напольных погрузочно-разгрузочных машин – необходимость в устройстве широких проходов для движения погрузчиков и штабелеров и ограниченная высота подъема груза.
Поиски оборудования обеспечивающего максимальное использование складских помещений удобство доступа к грузам и высокую производительность привели к созданию различных систем складирования грузов. Наибольшее распространение получили системы с кранами-штабелерами укладывающими грузы в стеллаж с помощью грузозахватных устройств.
Краны-штабелеры позволяют рационализировать складское хозяйство экономить площади высвободить значительное количество вспомогательных рабочих и открывают широкие возможности для автоматизации складирования.
Краны-штабелеры применяют в самых различных отраслях промышленности но особенно эффективно – в машиностроении металлургической промышленности материально-техническом снабжении.
Краны-штабелеры применяют в таких отраслях в которых ранее использовали лишь традиционные подъемно-транспортные машины.
Основным видом подъемно-транспортного оборудования складов стеллажного типа являются мостовые краны-штабелеры и стеллажные штабелеры(рис. 2). Практика и исследования показывают что мостовые краны-штабелеры целесообразно применять при высоте стеллажей до 10-12 м; при более высоких стеллажах более экономичными являются стеллажные штабелеры.
Рис. 2. Схема стеллажного крана-штабелера установленного на складе: 1 – подающие роликовые конвейеры; 2 – поворотная секция роликового конвейера; 3 – контроль размера пакетов; 4 – распределительный конвейер; 5 – площадка для установки грузов; 6 – стеллажный кран
Мостовой кран-штабелер имеет вертикальную колонну 5 подвешенную к грузовой тележке 4 перемещающейся по мосту 3 передвигающемуся по крановым рельсам 1 (рис. 3 а). По колонне перемещается грузозахватное устройство в виде вил 6 а нередко и кабина крановщика. Подъем (и опускание) кабины может осуществляться тем же механизмом что и подъем груза. Находят применение раздельные механизмы подъема кабины и груза. Один такой кран-штабелер может обслуживать группу стеллажей и даже весь склад.
Стеллажный кран-штабелер имеет вертикальную колонну перемещающуюся между стеллажами (рис. 3 б). В этих кранах тележка передвигается по рельсам уложенным на стеллажах. Грузоподъемное устройство перемещающееся по колонне должно обслуживать оба стеллажа (правый и левый). Если колонна будет выполнена поворотной то требуется увеличить расстояние между стеллажами. Грузозахватное устройство выполнено выдвижным.
Стеллажные краны могут перемещаться по напольному рельсовому пути.
По способу опирания на рельсовый путь краны-штабелеры бывают опорными или подвесными (рис. 4 и 5). Это деление является условным. Подвесной кран-штабелер подвешен к ходовым тележкам.
Рис. 3. Краны-штабелеры: а – мостовой; б – стеллажный
Рис. 4. Краны-штабелеры мостового типа: а – опорный; б — подвесной
Грузоподъемность кранов-штабелеров обычно не превышает 5 т но находят применение краны-штабелеры грузоподъемностью более 10 т.
Высота подъема отечественных кранов составляет 10 м. Скорость подъема 8—12 ммин. Скорость передвижения моста 50 ммин (при управлении с пола только 36 ммин) скорость передвижения тележки 12—20 ммин. Частота вращения колонны 4 обмин. Одной из особенностей кранов-штабелеров по сравнению с обычными крюковыми кранами является точная остановка всех механизмов. Поэтому при достаточно высоких рабочих скоростях предусматривается возможность движения с пониженными (доводочными) скоростями. В отечественных кранах доводочные скорости: подъема 4 ммин передвижения моста 10 ммин передвижения тележки 5 ммин.
Рис. 5. Стеллажные краны-штабелеры:
а -- подвесной; б — опорный велосипедного типа; в — опорный с опорой на стеллажи
Обзор существующих конструкций и выбор рациональной схемы крана-штабелера.
Стеллажные краны-штабелеры представляют собой широкую группу кранов-штабелеров которые могут устанавливать грузы в один стеллаж расположенный вдоль крановых путей или в два стеллажа расположенные по обе стороны крановых путей. Стеллажным называется кран-штабелер с вертикальной колонной перемещающейся в проходе между стеллажами.
Стеллажные краны-штабелеры являются наиболее эффективным складским оборудованием и интерес к ним проявляемый со стороны потребителей и поставщиков предопределил интенсивное развитие производства этих кранов-штабелеров.
Краны-штабелеры грузоподъемностью 1 т. представляют собой двухколонную раму передвигающуюся по подвесному пути укрепленному на стеллажах. По раме вертикально перемещается грузоподъемник. В нижней части рамы установлены ролики которые катятся по направляющим рельсам и удерживают кран-штабелер в вертикальном положении. Рама подвешена на двух приводных каретках. Каждая каретка имеет два электродвигателя мощностью 018 и 08 кВт оборудованных электромагнитными тормозами дифференциальный редуктор и две пары ходовых колес причем одна пара – приводная.
Приводные каретки сообщают крану-штабелеру скорость 60 ммин при одновременной работе двух электродвигателей и скорость 10 ммин при работе одного (малого) электродвигателя. На верхней балке рамы установлен привод механизма подъема состоящий из электротали оборудованной двухскоростным электродвигателем мощностью 50 кВт.
Грузоподъемник движется вдоль рамы крана-штабелера по направляющим рельсам с помощью четырех пар роликов охватывающих эти рельсы. На верхней поперечной балке грузоподъемника установлен подпружиненный канатный блок соединенный тягами с клиновыми ловителями охватывающими направляющие рельсы. При обрыве несущего каната или поломке механизма подъема происходит заклинивание ловителей и посадка грузоподъемника на раму крана.
Кабины кранов-штабелеров изготовляли двух исполнений: полуоткрытой применяемой в отапливаемых складах с температурой не ниже +50 и закрытой используемой в не отапливаемых складах. Закрытая кабина имела теплоизоляцию и была оборудована приборами отопления.
Конструкция описанного крана-штабелера характерна для всех подвесных кранов-штабелеров. Преимущества их предопределившие достаточно широкое применение заключались в следующем: простая и технологичная конструкция рамы; удобство установки и крепления ходовых механизмов и механизма подъема; возможность использования узлов и механизмов монорельсового транспорта.
Однако длительная эксплуатация стеллажных подвесных кранов-штабелеров различных конструкций изготовленных многими фирмами выявила ряд общих для них недостатков:
во-первых интенсивное изнашивание ходовых колес и монорельсовых путей особенно при увеличившихся до 100-120 ммин скоростях передвижения;
во-вторых значительное недоиспользование высоты склада обусловленное необходимостью разместить под монорельсом верхнюю несущую балку рамы привод механизма подъема и другие механизмы;
в-третьих неудобство эксплуатации связано с размещением основных механизмов в верхней части крана-штабелера и трудностью доступа к ним обслуживающего персонала.
В связи с этим выпуск подвесных стеллажных кранов-штабелеров был прекращен. Их заменили более совершенными опорными.
Рис.2. Одноколонный стеллажный кран-штабелер передвигающийся по рельсовым путям уложенным на стеллажи:
– телескопические захваты; 2 – грузоподъемник; 3 – кабина; 4 – колонна; 5 – тележка крана; 6 – привод передвижения; 7 – привод подъема; 8 – рельсы передаточной тележки; 9 – передаточная тележка; 10 – крановый рельс; 11 – стеллаж; 12 – направляющие рельсы.
Как одно из направлений в дальнейшем развитии конструкции стеллажных кранов-штабелеров можно рассматривать появление кранов-штабелеров опирающихся на рельсы уложенные в стеллажи. Например одноколонный кран-штабелер (рис.2.). Рельсы для него укладывают на верхние планки стеллажей и крепят к ним болтами. При этом должна быть обеспечена высокая точность их монтажа ( отклонение – не более 2мм). Колея рельсовых путей в зависимости от размеров перерабатываемого груза и прохода между стеллажами составляет 15 – 25 м. По крановым рельсам передвигается тележка крана-штабелера несущая на себе основные механизмы: приводы подъема и передвижения шкаф с электроаппаратурой. К тележке крепят колонну или сплошного сечения ( на кранах-штабелерах малой грузоподъемности) или решетчатую (на кранах-штабелерах большой грузоподъемности).
Опирающиеся на стеллаж краны-штабелеры имеют лучшие чем подвесные краны-штабалеры условия работы благодаря катанию ходовых колес по крановым рельсам а также возможности увеличить их диаметры. Однако их конструкции присущи серьезные недостатки:
во-первых это верхнее расположение механизмов (недостаток подвесных кранов-штабелеров)
во-вторых - высокие требования предъявляемые к монтажу направляющих путей.
Действительно при большой высоте подъема груза небольшая разность установки крановых путей по вертикали приводит к значительному отклонению нижнего конца колонны от среднего положения. При установке направляющего пути в этом случае могут появляться нежелательные нагрузки от перекоса металлоконструкции крана-штабелера.
Основным преимуществом опирающихся на стеллажах кранов-штабелеров является относительно простая конструкция передаточных тележек которые предназначены для перемещения кранов-штабелеров из одного межстеллажного прохода в другой.
Передаточные тележки обычно изготовляют в виде четырехколесной платформы перемещающейся по двум рельсам проходящим поперек фронта стеллажей под перекрытием склада. Один из рельсов устанавливают на стеллаж а другой крепят непосредственно к перекрытию склада. На передаточных тележках направляющие рельсы не предусматривают так как возможный перекос колонны крана-штабелера установленного на тележке не имеет существенного значения. От рамы тележки вниз опускаются короткие кронштейны несущие участок крановых путей который стыкуется с крановыми путями расположенными на стеллажах.
Передаточная тележка с краном-штабелером грузоподъемностью 1 т. изготовлена в виде сварной рамы передвигающейся по двум крановым путям один из которых установлен на стеллажах другой на специальных металлоконструкциях. Рама тележки несет на себе участок крановых рельсов для передвижения крана-штабелера оканчивающихся стыковыми замками запирающими кран-штабелер при передвижении на передаточной тележке.
В настоящее время большинство фирм перешло к выпуску стеллажных кранов-штабелеров перемещающихся по одному крановому пути установленному на полу склада. В верхней части кранов-штабелеров устанавливают направляющие ролики которые перемещаются по направляющему пути и удерживают кран-штабелер в вертикальном положении. Опорные (на пол) стеллажные краны-штабелеры по компоновке представляют собой одноколонную или двухколонную конструкцию имеющую нижнюю ходовую балку с двумя безребордными колесами одно из которых – приводное. К балке крепят одну или две вертикальные колонны заканчивающиеся направляющими роликами охватывающими с двух сторон направляющий путь углового или чаще двутаврового профиля. При двух колоннах краны-штабелеры имеют в верхней части продольную балку которая связывает их и образует таким образом замкнутую прямоугольную конструкцию. На нижней балке или на нижней части колонны устанавливают канатный или цепной механизм подъема с помощью которого осуществляется вертикальное перемещение грузоподъемника совместно с кабиной оператора. Подобная конструкция ставшая классической имеет несомненные преимущества перед описанными выше подвесными и опирающимися на стеллаж кранами-штабелерами.
При перемещении крана-штабелера по специальному крановому рельсу с помощью двух безребордных колес оборудованных горизонтальными роликами катящимися по боковым граням рельса изнашивание как ходовой части крана-штабелера так и рельса в том числе и при высоких (120 – 160 ммин) скоростях перемещения минимально. Причем возможно применение ходовых колес достаточно большого диаметра что в свою очередь позволяет уменьшить сопротивление перемещению и улучшить энергетические показатели механизма передвижения. При расположении в нижней части крана-штабелера всех механизмов и электрооборудования улучшаются условия доступа к этим механизмам при эксплуатации. Крановый путь установленный на полу склада (в межстеллажном проходе) позволяет создать более благоприятные условия для монтажа данного типа крана-штабелера (по сравнению с другими типами). чч Монтаж кранов-штабелеров сводится к установке на крановый путь опорной балки со смонтированными на ней механизмами и установке на эту балку колонны с помощью стрелового автомобильного крана или с помощью электрической или ручной тали подвешиваемой к направляющему пути.
Однако главным преимуществом опирающихся на пол стеллажных кранов-штабелеров является более высокая степень использования высоты помещения чем при применении стеллажных подвесных и опирающихся на стеллаж кранов-штабелеров достигающая своего максимального значения в одноколонных кранах-штабелерах.
Претерпели значительное изменение и некоторые узлы кранов-штабелеров среди которых прежде всего следует отметить грузозахватные устройства. На первых конструкциях стеллажных кранов-штабелеров преимущественно использовали роликовые столы с помощью которых пакетированные грузы устанавливались на кран-штабелер и в стеллаж а также выдвижные и поворотные вилочные захваты. Применение кранов-штабелеров с роликовыми столами на складах с интенсивной работой оказалось неприемлемым прежде всего в результате тяжелых условий труда операторов.
Применение выдвижных (и поворотных) вилочных захватов подобных используемым на автопогрузчиках позволило полностью исключить ручной труд при пакетной переработке груза. Однако это влечет за собой увеличение прохода между стеллажами так как необходимо оставлять определенное место для крепления вилочных захватов. Поэтому получили распространение выдвижные телескопические захваты технологически более сложные чем вилочные но позволяющие создать проход между стеллажами минимальной ширины равной практически сумме ширины перерабатываемого груза и зазоров (по 50 – 100 мм на сторону) между грузом и стеллажом.
Телескопические захваты представляют собой три секции одинаковой длины из которых одна неподвижная а две другие подвижные. Причем секция которая несет на себе груз движется с увеличенной вдвое скоростью по отношению к промежуточной. Телескопические захваты могут выдвигаться в обе стороны поперек прохода.
Значительные изменения претерпела система управления кранов-штабелеров начиная от ручного управления оператором из кабины на первых кранах-штабелерах и кончая полностью автоматизированным управлением применяемым на стеллажных кранах-штабелерах последних поколений. Изменился принципиальный подход к конструированию приводных механизмов. Переход от ручного к автоматическому управлению и возросшие скорости перемещения обусловили переход от применения асинхронных электродвигателей к электродвигателям постоянного и переменного тока с тиристорным регулированием скорости а также к электродвигателям с микроприводом. Более широко стали применяться редукторы специально предназначенные для использования на кранах-штабелерах вместо редукторов общепромышленного применения.
Изменения в конструкции кабин операторов направлены в основном на улучшение условий труда создание комфортных условий и обеспечение безопасности в работе.
В настоящее время стеллажные краны-штабелеры являются высокопроизводительным надежным оборудованием которое отличает отработанность конструкции ее высокая технологичность тщательность отделки. Таким образом поиски наиболее оптимальных конструктивных решений завершились созданием современных стеллажных кранов-штабелеров имеющих много общего в конструкции но отличающихся один от другого техническим исполнением отдельных узлов деталей систем управления. Можно сделать предположение что дальнейшие конструктивные поиски будут направлены в основном на повышение надежности технологичности расширение функциональных возможностей системы управления.
Стеллажные краны-штабелеры изготовляют в настоящее время в различных странах. Конструктивные их решения обусловлены традициями технологическими возможностями наличием освоенного производства узлов подъемно-транспортных машин систем управления. В принципе компоновки стеллажных кранов-штабелеров однотипны.
Современный стеллажный кран-штабелер выполнен в виде нижней ходовой балки оборудованной двумя безребордными колесами к которой крепят одну или две колонны имеющие сверху горизонтально расположенные направляющие ролики. Если устанавливают две колонны то верхние их концы соединяют горизонтальной балкой. По колонне с помощью канатного или реже цепного привода механизма подъема перемещается консольно установленный грузоподъемник несущий кабину управления и выдвижной телескопический захват. На стеллажных кранах-штабелерах предназначенных для поштучного отбора грузов так называемых комплектовочных кранах-штабелерах вместо выдвижных телескопических захватов можно устанавливать гладкие или роликовые столы а также другие приспособления для укладки в стеллажи и отбора из стеллажей грузов.
Одноколонный стеллажный кран-штабелер имеет нижнюю ходовую балку на которой установлены приводное и холостое колеса. К балке крепят колонну на верхней части которой установлены горизонтальные ролики удерживающие кран-штабелер в вертикальном положении.
По колонне перемещается консольный грузоподъемник с кабиной оператора. Кабина оператора имеет небольшой свободный ход относительно грузоподъемника для того чтобы полностью использовать высоту склада. На два телескопических захвата грузоподъемника устанавливается груз. грузоподъемник по колонне перемещается с помощью канатного механизма подъема . шкаф с электрооборудованием соединен с колонной кронштейном.
Двухколонные стеллажные краны-штабелеры применяют при больших высоте подъема и грузоподъемности. Кран-штабелер имеет нижнюю опорную балку на которой установлены приводное и холостое колеса. К опорной балке крепят две колонны и соединенные верхними концами продольной балки. На этой балке установлены две пары горизонтальных роликов и механизм синхронизации применяемый для уменьшения амплитуды перемещения верхней части колонны относительно ее нижней части.
Между колонн перемещается грузоподъемник представляющий собой платформу с двух сторон оборудованную каретками ролики которых обкатываются по направляющим колонн. На грузоподъемнике установлена кабина оператора и выдвижные телескопические захваты служащие для установки в стеллажи пакетированного груза. грузоподъемник поднимается с помощью канатного механизма подъема который установлен на одной колонне а на второй – шкаф с электрооборудованием. Для обслуживания механизма подъема и механизма синхронизации на одной из колонн крепят рабочие площадки к которым по лестнице поднимается обслуживающий персонал.
Сравнивая схемы этих кранов нетрудно увидеть что использование полезной высоты склада при применении двухколонных кранов-штабелеров хуже чем в одноколонных. Во-первых из-за наличия верхней балки соединяющей колонны и во-вторых из-за того что кабина не может вертикально перемещаться относительно грузоподъемника.
Одноколонную или двухколонную схему крана-штабелера выбирают прежде всего из условий обеспечения фиксированного положения груза на грузоподъемнике. При выдвижении груза инерционные силы приводят к поперечному перемещению рамы грузоподъемника в результате зазоров направляющих роликов грузоподъемника и закручивания колонн в поперечной плоскости. Очевидно что это поперечное перемещение консольного грузоподъемника существенно больше чем перемещение грузоподъемника имеющего направляющие ролики расположенные с обеих сторон по направлению движения крана-штабелера. Поэтому при грузах массой более 2 т при грузах длина которых более 2 – 25 м и при большой высоте подъема (свыше 20 м) применяют двухколонные краны-штабелеры.
Одноколонные краны-штабелеры по сравнению с двухколонными имеют минимальные собственные массу и размеры; позволяют лучше использовать высоту помещения и более удобны при монтаже. Недостатками одноколонных стеллажных кранов-штабелеров являются относительно большое поперечное перемещение грузоподъемника и увеличенные нагрузки на направляющие катки грузоподъемника в результате его консольного расположения и как следствие этого - большой износ катков и направляющих колонны.
Эти недостатки не оказывают существенного влияния при грузоподъемности кранов-штабелеров до 20 – 25 т. Однако при грузоподъемности свыше 2 т и при больших (свыше 25 м) размерах груза устранение этих отрицательных влияний путем увеличения прочности и жесткости металлоконструкций увеличения диаметров направляющих катков грузоподъемника и расстояния между ними приводит к неоправданному увеличению массы и размеров крана-штабелера. В этих случаях предпочтение следует отдать двухколонной схеме при которой кран-штабелер работает в значительно более благоприятных условиях.
2.1.Механизм подъема.
Механизмы подъема стеллажных кранов-штабелеров принципиально мало отличаются от соответствующих механизмов других грузоподъемных машин. В подавляющем большинстве на стеллажных кранах-штабелерах применяют канатные механизмы подъема. Механизм подъема как правило состоит из электродвигателя тормоза редуктора и канатного барабана. Эти механизмы имеют определенные ширину ограниченную шириной межстеллажного прохода и длину непосредственно зависящую от длины крана-штабелера. Поэтому наибольшее распространение получила вертикальная компоновка механизма подъема. Основой механизма является вертикальный конусно-цилиндрический редуктор который крепят к задней стенке колонны. Канатные барабаны устанавливают или на двух концах выходного вала по обе стороны редуктора (в этом случае используют канат без полиспаста) или на одном конце вала тогда груз поднимают с помощью полиспаста а свободный конец каната через блоки крепят к ограничителю грузоподъемности. На редуктор сверху помещают фланцевый вертикальный электродвигатель. Тормоз устанавливают на тормозной муфте соединяющей редуктор с электродвигателем.
Стеллажные краны-штабелеры могут иметь иную компоновку механизма подъема. На них используют стандартные червячные или цилиндрические крановые редукторы и тормозы вертикального исполнения. Редуктор и электродвигатель установлены горизонтально по продольной оси крана-штабелера. Канатный барабан установлен или на выходном валу редуктора или соединен с редуктором зубчатой передачей. Длина подобного механизма больше чем механизма при вертикальной компоновке. Однако на размерах крана-штабелера такая компоновка механизма подъема не сказывается так как его встраивают внутрь решетчатой колонны.
Описанная компоновка механизма подъема выгодна тем что при ее использовании не требуются специальные конусно-цилиндрические редукторы стоимость которых больше чем червячных или цилиндрических.
1.1.Механизм передвижения.
Механизм передвижения принципиально не отличается от механизмов передвижения других грузоподъемных устройств. Они состоят из электродвигателя тормоза и редуктора соединенного с ходовым колесом. Подобно механизмам подъема механизмы передвижения как правило имеют вертикальную компоновку. Механизмы передвижения большинства зарубежных фирм выполнены в виде вертикального конусноцилиндрического или червячного редуктора установленного на валу приводного колеса или соединяемого с ним открытой зубчатой передачей. На редукторы вертикально устанавливают фланцевые электродвигатели со встроенным тормозом. Широко применяют электродвигатели с микроприводом обеспечивающие большой диапазон регулирования скоростей при постоянном крутящем моменте.
На многих типах кранов-штабелеров в том числе на стеллажных кранах-штабелерах отечественного производства механизм передвижения выполнен в виде вертикального цилиндрического редуктора с полым выходным валом насаженного на вал приводного колеса. Выходной вал редуктора соединен с электродвигателем с помощью тормозной муфты. Электродвигатель расположен горизонтально над ходовой балкой крана-штабелера. Такая компоновка более эффективна так как этот механизм лучше вписывается в габариты крана. С целью сокращения длины кранов-штабелеров механизм подъема как правило расположен над механизмом передвижения. При большой высоте механизма передвижения механизм подъема приходится устанавливать достаточно высоко что усложняет его обслуживание.
Механизм передвижения всегда выполняют на одном из ходовых колес расположенном для двухколонных кранов-штабелеров со стороны более нагруженной колонны и для одноколонных – со стороны колонны.
1.2.Телескопический захват.
Выдвижные телескопические захваты разного конструктивного исполнения в настоящее время применяют на всех стеллажных кранах-штабелерах предназначенных для пакетной переработки грузов.
Телескопические захваты независимо от конструктивного исполнения выполнены по единой схеме. Они обычно состоят из трех секций: неподвижной промежуточной и выдвижной. Последняя служит опорной площадкой для установки груза. Она расположена несколько выше остальных секций чтобы при выдвижении груз не задевал за неподвижную и промежуточную секции. Промежуточная секция имеет ролики благодаря которым она может передвигаться по направляющим неподвижной секции. В свою очередь выдвижная секция с помощью роликов движется по промежуточной секции. Ширина всех секций одинакова и равна максимальной ширине перевозимого груза.
Рис.2.2. Схемы выдвижных телескопических захватов с расположением секций:
а – вертикальным; б – горизонтальным
Промежуточная секция выдвигается примерно на половину ее длины; выдвижная секция выступает из промежуточной на ту же величину. Обе секции выдвигаются одновременно с помощью привода. Захват может выдвигаться в обе стороны прохода. Таким образом взятый из загрузочного устройства груз может быть установлен в любую сторону без какого-либо поворота грузового захвата. Благодаря этому ширина прохода между стеллажами может быть снижена до минимального размера определяемого шириной перевозимого груза с учетом необходимых зазоров между грузом и стеллажами (от 50 до 100 мм на сторону).
Выдвижной телескопический захват с вертикальным расположением секций (рис. 2.2 а) состоит из выдвижной площадки 3 с закрепленной на ней роликовых батарей 5 и 6 промежуточной секции 2 неподвижных роликовых батарей 1 и 7 и приводного вала с шестернями 8. на верхней выдвижной площадке 3 промежуточной секции 2 и на неподвижной секции закреплены зубчатые рейки 4 длина которых равна длине секции.
Работа телескопического захвата происходит следующим образом. При вращении вала 8 установленные на нем шестерни входящие в зацепление с рейками на средней секции 2 сообщают средней секции некоторую скорость. На оси закрепленной в средней секции свободно вращается шестерня входящая в зацепление одновременно с рейкой закрепленной на неподвижной секции и с рейкой закрепленной на верхней выдвижной площадке. При перемещении средней секции со скоростью v1 шестерня входящая в зацепление с неподвижной рейкой сообщает верхней секции скорость v2 = 2*v1. Таким образом при включении привода захвата одновременно перемещаются на одинаковую величину: средняя секция по неподвижной со скоростью выдвижная площадка по средней секции с удвоенной скоростью v2.
После взятия груза привод захвата переключает и обе секции одновременно перемещаются и приходят в среднее положение. Выдвижной телескопический захват (рис.2.2.б) другого типа имеет горизонтальное расположение секций. На неподвижной секции его установленной на грузоподъемнике крепят ролики 9 по которым перемещается промежуточная секция 2 с роликами 8 служащими для передвижения выдвижной площадки 3. На валу промежуточного элемента смонтирована шестерня входящая одновременно в зацепление с зубчатой рейкой закрепленной на неподвижной секции захвата.
Привод захвата состоит из электродвигателя редуктора и тормоза. На выходном валу редуктора размещена шестерня входящая в зацепление с шестерней приводного вала захвата имеющего также две шестерни 10 сопряженные с зубчатыми рейками установленными на промежуточной секции захвата.
Работает захват таким образом. При включении привода шестерни посредством зубчатых реек сообщают поступательное движение промежуточной секции 2. Шестерня промежуточной секции движущаяся вместе с ней входит в зацепление с неподвижной зубчатой рейкой и передает движение с удвоенной скоростью зубчатой рейке установленной на выдвижной площадке захвата. Промежуточный и выдвижной элементы захвата движутся одновременно но выдвижной элемент перемещается вдвое быстрее первого.
Захваты с горизонтальным расположением секций имеют меньшую высоту что позволяет лучше использовать вместимость склада. К недостаткам следует отнести сложность конструкции и относительно высокую ее стоимость.
1.3.Система управления.
Рабочие скорости механизмов – подъема передвижения выдвижения телескопических захватов достаточно высоки. Работа механизмов при таких скоростях возможна только при большом диапазоне регулирования скоростей механизмов. Для остановки крана-штабелера (грузоподъемника) точно против требуемой ячейки (позиционирование) необходимо чтобы кран-штабелер и грузоподъемник подходили к ячейке на низких установочных скоростях. При ручном управлении эти скорости не должны превышать 6 – 8 ммин при автоматическом –2 – 4 ммин. При этих скоростях можно с точностью до нескольких миллиметров останавливать соответствующий механизм. Для приводов подъема и передвижения наиболее часто применяют тиристорные преобразователи постоянного или переменного тока. За рубежом находят применение специальные электродвигатели с микроприводами позволяющие получить низкие установочные скорости (08 – 12 ммин) при сохранении необходимого крутящего момента. Эти приводы значительно дороже чем приводы с обычными электродвигателями однако позволяют достигать высокой точности позиционирования.
Краны-штабелеры оборудованы тиристорными преобразователями и электродвигателями постоянного тока с диапазоном регулирования 50 : 1. недостатком применения тиристорных приводов является уменьшение крутящего момента на валу электродвигателя (приводного колеса) и отсюда – повышение требований к качеству монтажа кранового пути.
Краны-штабелеры с относительно низкими скоростями механизмов (подъема – 8 – 12 ммин передвижения – 60 – 80 ммин) с ручным управлением оборудуют двух или многоскоростными асинхронными электродвигателями. Стоимость таких приводов значительно меньше стоимости тиристорных приводов равно как и стоимость обслуживания и ремонта. Двухскоростные электродвигатели с соотношением скоростей 8:1 широко применяют на стеллажных кранах-штабелерах производства НРБ.
Анализ различных вариантов конструктивного исполнения и основных расчетов крана-штабелера.
1.Назначение специфика и нормативные основы.
Все вновь проектируемые или модернизируемые краны-штабелеры подвергаются тщательному расчету. Оформленный расчет является обязательным документом технического проекта крана-штабелера; расчеты элементов или узлов размеры которых становятся известными на стадии рабочего проектирования или корректируются по результатам испытаний опытного образца оформляют затем в виде дополнительных частей или разделов.
Такое внимание к расчетам обусловлено тем что краны-штабелеры являются объектами повышенной ответственности. Прежде всего кран-штабелер – это подъемно-транспортная машина разрушение или повреждение которой представляет опасность для жизни обслуживающего персонала. Во-вторых кран-штабелер в большинстве случаев является единственным средством доступа к грузам находящимся в обслуживаемом им хранилище. Поэтому даже рядовые отказы крана-штабелера нарушают работу склада что особенно чувствительно для складов интенсивных производств и технологических линий.
Таким образом основным назначением расчетов является проверка безопасности и надежности крана-штабелера в работе.
Безопасность крана-штабелера должна быть проверена также и для процесса его испытаний поскольку этот процесс характеризуется увеличенной массой применяемых грузов повышенной вероятностью возникновения отказов искусственным созданием отказов некоторых видов а также значительной численностью персонала испытателей безопасность которых должна быть гарантирована.
Другим назначением расчетов является проверка соответствия технических параметров проекта крана-штабелера требованиям технического задания и нормативно-технических документов. Некоторые из перечисленных параметров например расчетный ресурс запасы прочности жесткость элементов конструкции крана-штабелера имеют прямое отношение к вопросам безопасности и надежности крана-штабелера. Другие параметры – скорость ускорения и замедления обеспечиваемые механизмами характеризуют производительность крана-штабелера.
Очевидно что сравнение различных образцов кранов-штабелеров может быть правильно выполнено только в том случае если расчеты выполнены по одной и той же методике на основании одинаковых нормативов. Этим определяется первая предпосылка необходимости стандартизации норм расчета кранов-штабелеров. Другая и не менее важная предпосылка вытекает из самой ответственности разработки стандарта как официального и обязательного документа; из широкой гласности при обсуждении проекта стандарта заинтересованными и специализированными организациями в результате чего стандарт как правило отражает передовой научный технический и проектно-конструкторский опыт.
В результате специального изучения условий эксплуатации и нормирования расчетов кранов-штабелеров разработаны и введены в действие ОСТ 24.090.68-82 «Краны-штабелеры стеллажные. Нормы расчета» и ОСТ 24.091.14-85 «Краны-штабелеры мостовые. Нормы расчета». Излагаемые ниже основные положения расчета кранов-штабелеров даны в полном соответствии с упомянутыми стандартами.
Оба стандарта предназначаются для кранов-штабелеров по ГОСТ 16553-82. однако основные принципы и нормы расчета этих стандартов могут быть использованы для кранов-штабелеров других типов и параметров например для подвесных мостовых и стеллажных кранов-штабелеров для кранов-штабелеров с облегченным режимом работы. Для того чтобы конструктор мог в таких случаях самостоятельно внести в нормативы необходимые изменения здесь даются пояснения о происхождении тех или иных нормативных требований.
Наконец следует сказать что отчетный расчет как документ проекта представляет собой итоговую часть расчетной работы которой предшествует большое число предварительных и вариантных расчетов. Последние особенно важны так как представляют собой в большинстве случаев единственный инструмент для получения конструкции необходимого технического уровня. Вариантные расчеты в настоящее время с успехом выполняются на ЭВМ принимая форму так называемых оптимизационных расчетов. В качестве критерия оптимизации для крана-штабелера обычно выбирают его массу которую следует минимизировать. Возможно применение и стоимостного или смешанного критерия.
Известно что для расчетов с помощью ЭВМ необходима четкая формализация расчетных схем и требований. И в этом отношении стандартизованные нормы расчета кранов-штабелеров дают необходимый материал.
Исходные данные для предварительных расчетов принимают в соответствии с техническим заданием и схемами предварительных конструктивных проработок крана-штабелера. Исходные данные оформляемого расчета должны полностью соответствовать параметрам указанным в конструкторской и эксплуатационной документации на кран-штабелер; отдельные несоответствия должны оговариваться в отношении их причин и следствий.
В конструкции крана-штабелера обычно используют материалы и комплектующие изделия выпускаемые промышленностью для общего потребления. К ним относятся металлический прокат электродвигатели стандартные редукторы подшипники муфты тормоза и т.п. Их технические параметры приводимые в сортаментах и каталогах также являются исходными данными для расчета в результате которого должны быть выявлены минимально необходимые типоразмеры материалов и комплектующих изделий (с учетом возможностей поставки которые учитываются в расчете как ограничители сортаментов).
Желательно чтобы полученные расчетом скорости механизмов крана-штабелера составляли от 09 до 11 их номинальных значений. Следует отметить что согласно ГОСТ 16553-82 допускаемое отклонение фактических скоростей от номинальных составляет 15%. Сужать поле допуска расчетных скоростей целесообразно для компенсации возможного расхождения расчетных и фактических скоростей.
Расчетное ускорение (замедление) обеспечиваемое механизмом передвижения крана-штабелера должно составлять 03 – 06 мс2. Это объясняется тем что при ускорениях (замедлениях) меньших чем 03 мс2 процессы разгона или торможения чрезмерно затягиваются. Например при ускорении 02 мс2 и номинальной скорости 20 мс разгон будет длиться 10 с; увеличение ускорения до 04 мс2 сокращает время разгона до 5 с а общая экономия времени за цикл работы крана-штабелера составит 20 с что равносильно увеличению производительности крана-штабелера не менее чем на 20%. Ускорение большее чем 06 мс2 во многих случаях недостижимо по условию необходимого запаса сцепления приводных колес с рельсами. Однако и тогда когда имеется избыточный запас сцепления (например у кранов-штабелеров с малой высотой подъема) увеличение ускорения свыше 06 мс2 нецелесообразно: увеличение производительности получается несущественным а габарит электродвигателя может возрасти так как требуется повышенный пусковой момент.
Расчетное ускорение грузозахватного органа должно быть не более 10 мс2. ускорения большие чем указанное не применяют потому что скорость подъема обычно не превышает 05 мс и сокращать время разгона по сравнению с величиной 05 с не только не имеет смысла но и невыгодно во всех отношениях.
Нижняя граница ускорения при подъеме не регламентируется. Дело в том что электродвигатель механизма подъема подбирают таким образом чтобы требуемый момент установившегося движения на валу электродвигателя был близок к его номинальному моменту. Пусковой момент электродвигателя в 2 – 3 раза больше номинального поэтому ускорение разгона обычно получается не менее 04 – 05 мс2 что вполне приемлемо так как время разгона не превышает 10 – 15 с.
Верхняя граница замедления торможения при опускании грузозахватного органа также равна 10 мс2 а нижняя не ограничивается по причинам аналогичным вышеизложенным так как основной процесс торможения обеспечивается электродвигателем.
Расчетное ускорение (замедление) при выдвижении телескопических захватов должно быть не более 10 мс2. Такое ограничение необходимо для предотвращения смещения груза относительно захвата под действием инерционных сил. Поэтому указанное ограничение проверяется для случаев пуска и торможения захвата на котором установлена порожняя тара так как при этом ускорение (замедление) получается наибольшим. Вследствие того что скорость выдвижения захватов сравнительно невелика (до 025 мс) инерционная доля массы порожней тары в приведенном моменте инерции привода захвата также невелика и можно рассчитывать ускорение для захвата без груза. Этим объясняется то что в ОСТ 24.090.68-82 не оговаривается для какого случая нагружения захватов следует проверять ускорение поскольку очевидно что наибольшее его значение будет в случае порожних захватов.
Нижний предел расчетного ускорения (замедления) захватов не регламентируется ввиду того что скорость выдвижения как уже отмечалось сравнительно невелика и время разгона практически никогда не превышает 1 с даже в наиболее тяжелом случае – при взятии номинального груза из ячейки стеллажа.
Расчетный срок службы кранов-штабелеров принимается равным 20 годам при односменной работе. В течение этого срока металлоконструкции кранов-штабелеров должны проработать безотказно и такое требование практически выполнимо.
Календарный срок службы крана-штабелера и его узлов удобен для эксплуатационника. Между этой величиной и долговечностью существует определенная связь зависящая от продолжительности цикла крана-штабелера и от соотношения продолжительностей включения различных механизмов в течение цикла.
При индивидуальном проектировании крана-штабелера предназначенного для склада с определенными заданными параметрами – длиной высотой числом ячеек грузооборотом - характеристики цикла можно определить однозначно путем их осреднения по складу с учетом принятых приоритетов загрузки и выгрузки.
Для крана-штабелера серийного производства условия работы заранее не известны. Поэтому приходится задаваться некоторым условным складом параметры которого были бы представительны по частоте практической применяемости и создавали бы в то же время достаточно напряженный режим работы крана-штабелера. При этом для определения характеристики цикла стеллажного крана-штабелера практически достаточно задаться длиной склада. Для мостового крана-штабелера существует некоторое множество пар значений длины и ширины склада при которых может быть обеспечен заданный грузооборот. Этому множеству соответствует множество возможных циклов из которых следует выбрать наиболее характерные принимаемые в качестве нормативных.
Такая работа выполнена при разработке ОСТ 24.090.68-82 и ОСТ 24.091.14-85. Отметим что выбор нормативного цикла работы крана-штабелера позволяет помимо ресурса установить и другие важные характеристики режима работы механизмов крана-штабелера. К ним относятся число включений в час и продолжительность включения (ПВ %) необходимые для выбора электродвигателей.
К ним также относятся циклограммы работы механизмов показывающие изменение нагрузки механизмов в течение цикла и необходимые для расчета всех звеньев механизмов в том числе и электродвигателей. Для получения циклограмм приходится рассматривать процессы установившегося движения а также разгона и торможения механизмов и кроме того учитывать статистическую изменчивость массы складируемых грузов.
Методической основой для установления расчетных характеристик режима работы механизмов является ГОСТ 25835-83 «Краны грузоподъемные. Классификация механизмов по режимам работы» а также стандартные значения ПВ и числа включений в час применяемые в отечественной промышленности.
Согласно ГОСТ 25835-83 найденные с помощью нормативного цикла значения чистого времени работы каждого из механизмов за срок службы округляются до стандартных ближайших значений. Таким образом устанавливается класс использования механизма по времени. По циклограммам работы механизмов вычисляют коэффициент нагружения равный сумме произведений относительной длительности нагрузки на куб относительной нагрузки взятой по всем элементарным прямоугольникам циклограммы. По коэффициенту нагружения устанавливают класс нагружения который в сочетании с классом использования определяет группу режима работы механизма крана-штабелера.
Как показали исследования для стеллажных кранов-штабелеров по ГОСТ 16553-82 все механизмы должны быть отнесены к группе режима работы 5М по ГОСТ 25835-83 что соответствует тяжелому режиму работы по классификации Госгортехнадзора.
Элементы механизмов должны быть проверены на прочность по наибольшим нагрузкам пусковых и тормозных режимов а также на выносливость с учетом требуемого ресурса и циклограмм нагружения элементов получаемых путем образмеривания исходных циклограмм по данным о величинах нагрузки передаточных чисел и коэффициентов полезного действия звеньев передачи.
При этом расчет цилиндрических эвольвентных зубчатых передач внешнего зацепления следует выполнять по ГОСТ 21354-75 подшипников качения – по ГОСТ 18854-82 и ГОСТ 18855-82. ходовые колеса кранов-штабелеров следует проверять по ОСТ 24.090.44-82 «Колеса крановые. Выбор и расчет» с учетом изложенных ниже рекомендаций. Для расчета поворотных опор колонн мостовых кранов-штабелеров следует применять ОСТ 22-1401-79 «Опоры поворотные роликовые однорядные с зубьями внутреннего зацепления». Прочие элементы механизмов рекомендуется рассчитывать по соответствующим РТМ ВНИИПТмаша. Для стандартных редукторов подлежащих согласованию следует применять РТМ 2-056-80 «Редукторы общего назначения. Методика выбора редукторов и моторов-редукторов».
Электродвигатели механизмов должны быть проверены по наибольшим нагрузкам пусковых и тормозных режимов а также на нагрев с учетом их расчетных характеристик и соответствующих циклограмм.
При расчете металлоконструкций кранов-штабелеров проверяют прочность устойчивость жесткость и выносливость конструкций в целом и их отдельных элементов. Для стеллажных кранов-штабелеров выполняют также расчет затухания колебаний колонны при остановке крана-штабелера.
Стальные конструкции рассчитывают по методике СНиП II-23-81 «Нормы проектирования. Стальные конструкции» а алюминиевые конструкции – по методике СНиП II-24-74 «Нормы проектирования. Алюминиевые конструкции» с учетом излагаемых здесь специфических требований.
При формировании исходных данных для расчета следует убедиться что принятые в проекте крана-штабелера материалы металлоконструкций и сварочные материалы соответствуют требованиям обязательного РТМ 24.090.52-79 «Краны грузоподъемные. Материалы для сварных металлических конструкций» а примененные для болтовых соединений стальные болты гайки и шайбы соответствуют требованиям СНиП II-23-81. следует также проверить что кран-штабелер оборудован всеми устройствами безопасности в соответствии с требованиями ОСТ 24.090.38-83 и ОСТ 24.090.39-83.
В заключение следует указать что в расчетах выполняемых на группу исполнении крана-штабелера отличающихся пролетом высотой грузоподъемностью и скоростями механизмов должны быть рассмотрены все исполнения группы а не только исполнения с наибольшими характеристиками.
Краны-штабелеры рассчитанные в соответствии с настоящими рекомендациями могут быть использованы для эксплуатации в сейсмических районах без ограничений так как применяемые здесь экстремальные расчетные нагрузки превосходят наибольшие сейсмические нагрузки по СНиП II-7-81.
2.Расчет стеллажных кранов-штабелеров.
Расчетные характеристики режима работы механизмов стеллажных кранов-штабелеров соответствующие ГОСТ 25835-83 приведены в табл.3.3
Значения показателя для механизма
Группа режима работы
Общее время работы тыс.ч
Коэффициент нагружения (стеллажных кранов-штабелеров)
Число включений в час
Продолжительность включения ПВ %
В расчетных циклограммах загрузки механизмов (рис.3.1) по оси абсцисс отложено относительное число циклов или относительная продолжительность действия нагрузки. Строго говоря число циклов нагрузки не пропорционально времени ее действия ввиду наличия периодов разгона и торможения и следовало бы давать отдельные циклограммы по числу циклов и по времени в качестве аргументов. Однако для механизмов подъема и выдвижения относительная продолжительность неустановившихся режимов движения всегда невелика – менее 3 %. Для механизма передвижения при нормировании режима работы принят стеллаж длиной 100 м. При этом средний путь передвижения крана-штабелера за простой цикл составит также 100 м. Можно показать что например при скорости передвижения 20 мс и ускорении (замедлении) 05 мс2 погрешность в вычислении числа циклов если не учитывать неустановившиеся режимы движения составит 8 % в сторону увеличения т.е. в запас. Такая погрешность находится в пределах точности исходных предпосылок поэтому и в данном случае достаточно ограничиваться одной циклограммой.
Рисунок 3.1. Расчетные циклограммы загрузки механизмов стеллажных кранов-штабелеров: а б в – соответственно передвижения подъема и выдвижения захватов
Переход к абсолютному времени для элементов рассчитываемых на полный срок службы крана-штабелера производится по общему времени работы (см. табл. 3). Для прочих элементов это время уменьшается в 2 раза или более.
Для нахождения полного числа циклов нагружения какого-либо элемента механизма необходимо общее время работы разделить на длительность одного цикла. Для вращающихся элементов – валов шестерен подшипников и т.д. – циклом является один оборот (особенности существуют только для планетарных редукторов). При этом частоту их вращения следует брать для установившегося режима движения. Например для вала механизма подъема вращающегося с частотой 1000 обмин и рассчитываемого на полный срок службы получим полное расчетное число циклов 1000*60*12500 = 75*108.
В расчетных циклограммах (см. рис. 3.1) по оси ординат отложена относительная нагрузка. Абсолютная величина наибольшей ординаты нагрузки для механизма передвижения соответствует моменту при разгоне с расчетным ускорением; для механизма подъема – моменту при установившемся движении подъема с номинальным грузом; для механизма выдвижения – при взятии номинального груза из ячейки стеллажа т.е. на наибольшем вылете захвата но без учета сил инерции.
При установлении характеристик режима работы (см. табл.3.1 и рис.3.1 ) рассматривали краны-штабелеры обслуживающие стеллажи длиной 100 м высотой 16 м и глубиной 12 м со скоростями передвижения от 16 до 25 мс подъема – 04 мс и выдвижения захватов – 02 мс. ускорения при разгоне механизмов принимали равным 04 мс2. Относительное число простых и сложных циклов 06 и 04 соответственно. Процесс подъема считали как совмещенный по времени с процессом передвижения. Изменчивость массы Q грузов оценивали по гистограмме (рис.3.1) полученной по результатам обследования действующих складов; средняя масса груза по этой гистограмме составляет 06 от номинальной Qном.
Рис.3.2 Расчетная гистограммараспределения массы брутто
складируемых грузов;ρ – плотность вероятности
Для расчета опорных одноколонных стеллажных кранов-штабелеров рекомендуется использовать схемы представленные на рис. 3.2
В кране-штабелере выделяют шесть укрупненных конструктивных узлов со следующей закрепленной за ними индексацией: ходовая балка 1 в сборе с установленным на ней механизмом передвижения и ходовыми колесами; механизм подъема 2 (включая канаты); колонна 3(или две колонны у двухколонных кранов-штабелеров рамной конструкции рис. 3.2; при шарнирно-сочлененной конструкции по рис. 3.3 правая и левая колонны и их ходовые балки должны рассматриваться отдельно дополнительным элементом является сцепка); оголовок колонны 4 в сборе с грузовыми блоками и боковыми роликами (или верхняя балка у двухколонных кранов-штабелеров); грузоподъемник 5 в сборе с каретками грузовыми подвесками и грузовыми захватами; кабина 6 (при определении ее массы учитывается масса оператора).
Шкаф электрооборудования относят к ходовой балке или к колонне в зависимости от того на чем он установлен.
Отдельным элементом является транспортируемый груз номинальная масса которого обозначена через Q.
Для каждого из этих узлов предварительно определяют номинальные значения масс m zi) в прямоугольной системе координат начало которой расположено в середине площадки контакта приводного ходового колеса с наземным крановым рельсом.
Для расчета металлоконструкций подготавливают геометрические характеристики сечений ходовой балки колонн верхней балки а также расчетные сопротивления и модуль упругости материала.
Рис. 3.3 Стержневые схемы конструкций двухколонных стеллажных кранов-штабелеров:
а – рамной; б – шарнирно-сочлененной; 1 1’ – ходовые балки; 2 – механизм подъема; 3 3’ – колонны; 4 – верхняя балка; 5 – рама грузоподъемника; К – каретка подъемника; ГК – грузовые канаты; С – сцепка
Сопротивление передвижению крана-штабелера определяется как сила необходимая для преодоления трения качения ходовых колес и подшипников умноженная на коэффициент 11 учитывающий трение в боковых роликах. Уклон пути не учитывается так как согласно ОСТ 24.090.39-83 уклон ограничен очень малой величиной – 0001.
Сопротивление передвижению необходимо знать для определения скорости ускорения и замедления крана-штабелера обеспечиваемых используемым электродвигателем и передаточным механизмом.
Однако методически удобней начинать расчет механизма передвижения с анализа запаса сцепления приводных колес а затем и устойчивости крана-штабелера в режимах разгона и торможения.
Физический смысл необходимости запаса сцепления – предотвращение пробуксовки приводного колеса приводящей к ускоренному изнашиванию колеса и рельса. Для крана-штабелера такое изнашивание особенно нежелательно так как помимо прочего уменьшение диаметра колеса нарушает вертикальное положение колонны от которого непосредственно зависит возможность правильного позиционирования грузового захвата во все ячейки по высоте стеллажа.
Для кранов-штабелеров с гибким токоподводом следует дополнительно учесть воздействие усилий статического натяжения и сопротивления передвижению кабельной подвески если эти усилия вызывают разгрузку приводного колеса. При этом кабельную подвеску следует рассматривать в наиболее растянутом положении т.е. на полной длине стеллажа которую принимают равной 100 м если в техническом задании нет других указаний.
Составив уравнения для коэффициента запаса сцепления в соответствии с приведенными указаниями легко увидеть что в них входят только геометрические и массовые параметры крана-штабелера и ускорения (замедления). Таким образом получим предельно допускаемое ускорение и замедление крана-штабелера всего четыре значения (ускорение и замедление для крана-штабелера с грузом и без груза) каждое из которых должно быть не менее 03 мс2.
По допускаемому ускорению с помощью известных формул определяют соответствующий среднепусковой момент электродвигателя который должен уравновесить сопротивление передвижению и силы инерции масс крана-штабелера а также инерционные моменты вращающихся масс ротора муфты тормозного шкива и т.п. с учетом КПД механизма.
Расчет выполняют для крана-штабелера с грузом и без груза; из двух полученных значений среднепускового момента выбирают наименьшее которое для перехода к номинальному моменту следует разделить на коэффициент кратности пускового момента и коэффициент использования пускового момента значения которого приведены в табл.3.2
Система упраления приводом
Коэффициент использования пускового момента
Релейно-контроллерная
Асинхронный с фазовым ротором
Асинхронный короткозамкнутый
Преобразователь или регулятор
Переменного или постоянного тока
Полученное значение номинального момента электродвигателя является предельно допустимым поэтому из рассматриваемой упорядоченной номенклатуры следует выбирать тот наибольший электродвигатель номинальный момент которого при ПВ = 60 % не превышает предельно допустимый.
Отсюда начинается проверочная часть расчета механизма передвижения. Сначала с помощью механической характеристики электродвигателя определяют расчетную скорость установившегося движения крана-штабелера которая должна удовлетворять требованиям изложенным выше. Если результат не достигнут то следует изменить передаточное число редуктора а возможно и рассмотреть другую номенклатуру редукторов и (или) электродвигателей.
Описание конструкции и предварительная разработка общего вида крана-штабелера.
Краны-штабелеры стеллажные автоматические грузоподъемностью 1 т предназначены для механизации процессов укладки в стеллажи и выдачи из стеллажей на загрузочные устройства грузов уложенных в стандартную ящичную тару по ГОСТ 14861-74 или на специальные поддоны и тару с размерами в плане 1200*800 мм для кранов-штабелеров грузоподъемностью 1 т.
Краны-штабелеры предназначены для применения в автоматизированных транспортно-складских системах функционирующих как самостоятельно так и в составе автоматизированных технологических комплексах а также для использования в цеховых складах машиностроительных заводов.
Климатическое использование кранов-штабелеров УХЛ4 по ГОСТ 15150-69.
Краны-штабелеры не предназначены для применения во взрыво- и пожароопасных помещениях (за исключением П-IIа) в помещениях с парами кислот и щелочей концентрации которых вызывают разрушение электрической изоляции и металлических конструкций а также в помещениях в которых возможно выделение вредных веществ в воздух рабочей среды.
Кран-штабелер транспортируется и поступает потребителю упакованным в деревянные ящики кроме колонны следующими частями:
тележка в сборе с приводом передвижения направляющими роликами подхватами и конечными выключателями;
грузоподъемник в сборе с электрооборудованием;
направляющие для установки шунтов и направляющие кабельного блока;
считыватели конечные выключатели шунты линейки;
кабельные изделия детали и узлы креплений кабелей кабельный блок клеммные коробки кабельные тележки и другие узлы;
электрошкаф с реакторами;
устройство управления движением в сборе с кронштейном для его установки на кране-штабелере;
командное устройство управления;
1.Техническое описание.
Технические характеристики кранов-штабелеров стеллажных автоматических грузоподъемностью 1 т представлены в таблице 4.1.
Наименование параметров
Режим работы крана-штабелера
Режим работы механизмов по
привод выдвижения грузозахватного органа
Максимальное расстояние от головки рельса до подвесного пути Нр м
Максимальная высота подъема грузозахватного органа Нп м
Габариты перерабатываемых грузов:
Минимальная высота опор ящичной тары мин м
Скорость подъема грузозахватного органа мс
Скорость передвижения крана-штабелера мс
Скорость выдвижения грузозахватного органа мс
Тип грузозахватного органа
Величина выдвижения грузозахватного органа
Высота выдвигаемых элементов грузозахватного органа м
Ширина крана-штабелера В м
Длина крана-штабелера (вдоль пути)м
Ширина прохода для штабелирования А м
Максимальное количество адресов:
Тип нижнего рельсового пути
Суммарная мощность установленных электродвигателей кВт
Коэффициент установленной мощности
Подвод электропитания
Максимальная масса крана-штабелера т
Удельная металлоемкость ттыс.т.
Двутавр №12 ГОСТ 8239-72
Рельс Р24 ГОСТ6368-82
В состав изделия входят:
комплект монтажных частей;
эксплуатационная документация.
Кран-штабелер состоит из следующих составных частей
– электрооборудование.
В комплект монтажных частей поставляемых с краном-штабелером входят:
установка информационных каналов связи;
устройство командное;
буферы гидравлические;
детали для крепления рельсового и подвесного путей;
кабель подвесной для электропитания крана-штабелера;
линейки кронштейны и т.п.
3.Устройство и работа изделия
Привод передвижения установлен на тележке имеющей два колеса:
одно приводное и одно холостое диаметром 200мм.
На торцах тележки установлено по паре катков удерживающих кран-штабелер от бокового смещения.
Катки установлены на прокладках служащих для регулировки зазоров между катками и боковой поверхностью рельса.
К тележке при помощи болтов крепится колонна.
По направляющим на колонне перемещается грузоподъемник.
На грузоподъемнике установлен грузозахватный орган а также фотоэлементы для контроля положения груза датчики контроля занятости ячеек стеллажа и считыватель адреса по вертикали.
Подвод электропитания к грузоподъемнику осуществляется при помощи гибких кабелей. Натяжение кабелей осуществляется блоком перемещающимся по направляющим закрепленным на колонне на половине ее высоты.
Привод подъема расположен на нижней части колонны. Натяжение грузового каната контролируется ограничителем грузоподъемности.
В верхней части колонны установлен оголовок на котором имеются 4 отводных блока и пара направляющих катков служащих для удержания крана-штабелера в вертикальном положении.
Кран-штабелер перемещается между стеллажами по рельсу уложенному вдоль продольной оси межстеллажного прохода. В верхней части межстеллажного прохода уложен подвесной путь из двутавра №12 по которому обкатываются катки установленные на оголовке крана-штабелера.
Подвод электропитания крана-штабелера осуществляется при помощи гибких кабелей подвешенных на специальных тележках перемещающихся по подвесному пути.
Управление краном-штабелером:
-автоматическое – от командного устройства;
-ручное – с наладочного пульта.
Система автоматического управления предусматривает возможность непосредственного управления от ЭВМ верхнего уровня.
Кран-штабелер выполняет следующие работы:
-берет груз с загрузочного устройства и устанавливает его в ячейку стеллажа;
-берет груз из ячейки стеллажа и устанавливает его на загрузочное устройство;
-берет груз из любой ячейки стеллажа или любого загрузочного устройства работающего на загрузку стеллажей и устанавливает его в другую ячейку стеллажа или на другое загрузочное устройство работающее на выгрузку.
Любая из указанных выше работ выполняется краном-штабелером по команде от ЭВМ или с командного устройства включающей адрес ячейки из которой кран-штабелер должен взять груз и адрес ячейки в которую кран-штабелер должен установить груз.
После получения команды кран-штабелер выполняет работу в следующей последовательности:
-включается привод подъема и передвижения кран-штабелер подходит и останавливается у ячейки откуда надо взять груз;
-включается привод выдвижения грузозахватного органа захваты выдвигаются и устанавливаются под грузом в ячейке стеллажа;
-включается привод подъема груз приподнимается привод подъема выключается;
-включается привод грузозахватного органа захваты с грузом возвращаются в среднее положение;
-включается привод подъема и передвижения кран-штабелер подходит и останавливается у ячейки в которую надо установить груз;
-путем последовательного включения привода грузозахватного органа и привода подъема груз устанавливается в заданную ячейку;
-после возвращения грузозахватного органа в среднее положение кран-штабелер остается на месте до получения следующей команды.
Конструкторская часть.
1.Конструктивная разработка отдельных механизмов и узлов.
1.1.Расчет механизма передвижения тележки.
Расчет сопротивлений передвижению тележки крана-штабелера с грузом.
Приведенная ниже методика и нормы расчета применяются для механизмов передвижения кранов и грузовых тележек перемещающихся по рельсовому пути.
Полное сопротивление передвижению крана:
Wртр – сопротивление трения при движении крана с учетом трения роликов;
Wтр – сопротивление трения при движении крана без учета трения реборд
kр – коэффициент учитывающий сопротивление трения реборд ходовых колес крана о головку рельсов (при подшипниках скольжения – трения торцов ступиц колеса) при движении крана (табл.5.1.1.) т.к. колесо безребордное то kр = 1.
Wук – сопротивление от уклона подкрановых путей;
Wв – сопротивление от действия ветровой нагрузки.
Качения и скольжения
Передвижения тележки
Сопротивление трения определяется по формуле:
Q = 1000 – вес номинального груза кг;
G= 3250 – собственный вес крана кг;
Dх.к.= 200 – диаметр ходового колеса мм;
d = 45 – диаметр цапфы вала ходового колеса мм;
dр = 150 – диаметр ролика мм
= 003 – коэффициент трения качения (табл.5.1.2.стр134)
f = 0015 – коэффициент трения в подшипниковых опорах ходовых колес; значения f принимают:
Для подшипников скольжения открытого типа010
Для букс с жидкой смазкой008
Для шариковых и роликовых подшипников0015
Для конических подшипников качения002
Определим сопротивление трения:
Определим силу трения ролика:
Диаметр ходового колеса мм
m для стальных колес см
m для чугунных колес см
Сопротивление от уклона подкрановых путей:
Расчетные уклоны подкрановых путей α принимают:
Для путей с железобетонным фундаментом на металлических балках0001
Для путей с щебеночным основанием и деревянными шпалами0002
Для подтележечных путей на мосту крана0002
Так как наш кран-штабелер работает в помещении то Wв = 0
Найдем полное сопротивление передвижению крана:
Расчет сопротивлений передвижению тележки крана-штабелера без груза.
Так как кран-штабелер работает в помещении то Wв = 0
Полное сопротивление передвижению крана без груза:
Выбор мотор-редуктора.
Выбор мотор-редуктора для механизма передвижения крановых тележек производят по максимально допустимому пусковому моменту двигателя при котором обеспечивается надлежащий запас сцепления ходового колеса с рельсом исключающий возможность буксования при передвижении тележки без груза в процессе пуска.
Допустимое значение ускорения тележки:
φ = 02 – коэффициент сцепления ходового колеса с рельсом;
Рв= 0 – ветровая нагрузка на кран в рабочем состоянии;
g – ускорение силы тяжести;
nпр – число приводных ходовых колес;
nк – общее число ходовых колес.
Определим мощность двигателя по статическому сопротивлению при перемещении тележки с номинальным грузом:
vт = 25 мс = 150 ммин – скорость передвижения тележки;
= 09 – К.П.Д. передачи при установке ходовых колес на подшипниках качения.
Число оборотов ходовых колес:
Конический мотор-редуктор
BK20-54VUDHE09XA4C-TF-SESX027A9HAS40
Скорость ведущего вала
Направление клеммной коробки
Вес нетто (базовая сборка) 1 шт
Конструкцияисполнение
Исполнение редуктора
Конический редуктор BK20
моментный рычаг спереди вниз
полый вал с пазом под шпонку ø 40.00 mm
с установленным сапуном
Доп. спец. исполнение
Резиновые буферы для моментного рычага
Исполнение двигателя
Трехфазный электродвигатель DHE09XA4C
Напряжениесоединение
Номинальная скорость
Класс защиты по IP в соотв. с EN 60529
Коэффициент мощности (cosphi)
охлаждение EN 60034-6
IE_CODE_NACH_EN60034-30
Конструкция во соответствии с DIN VDE 0530-1EN 60034-1
Однодисковый тормоз с пружинами ESX027A9
Номинальный тормозной момент
Класс защиты по IP в соотв. с EN 60 529
с Стандарт -Выпрямитель (встроенный в клеммную коробку двигателя)
Напряжение питания AC 50Hz
HA ручной отпуск с блокировкой
Основные параметры электродвигателя
Номинальная мощность (PN): 22 кВт
Номинальная частота вращения вала ротора (n): 1440 обмин
Номинальный вращающий момент вала ротора (MN): 145 Нм
Момент инерции массы ротора (Jrot): 00053 кгм2
Режим работы: продолжительный S1
Основные параметры мотор-редуктора
Тип редуктора: BK2(конический редуктор)
Скорость ведущего вала: 240 обмин
Крутящий момент (Mк): 80 Нм
Передаточное число (i): 602
Масса мотор-редуктора (m): 556 кг
Основные параметры тормоза
Тип тормоза: ESX027A9 (однодисковый тормоз с пружинами)
Тормозной момент: 22 Нм
Момент инерции масс тормозного диска: 0000172 кгм2
Фактическая скорость передвижения тележки:
Требуемая при этом мощность двигателя:
что соответствует мощности выбранного двигателя.
Время пуска при максимально допустимом ускорении:
Что находиться в допустимых пределах от 05 сек. до 5 сек.
Момент сопротивления при передвижении тележки без груза:
Маховой момент двигателя
Маховой момент диска тормоза
Маховой момент вращающихся движущихся масс
Маховой момент поступательно движущихся масс
Общий маховой момент
Необходимый пусковой момент:
Номинальный момент двигателя
Фактическое время пуска
Тормозной момент механизма передвижения определяют при обеспечении надлежащего сцепления ходового колеса с рельсом которое исключило бы возможность юза при торможении тележки движущейся с номинальной скоростью без груза.
Максимально допустимое замедление при котором обеспечивается заданный запас сцепления ходовых колес с рельсом:
Уравнение моментов при торможении
Мтсо – момент сопротивления передвижению тележки без груза при торможении
Сопротивление передвижению при торможении
Момент сопротивления приведенный к валу тормоза:
Инерционный момент при торможении вращающихся и поступательно движущихся масс:
Тогда тормозной момент:
При снижении скорости перед остановкой крана-штабелера для увеличения его точности относительно ячейки устанавливаем преобразователь на число оборотов двигателя в доводовом режиме 350 обмин.
То инерционный момент при торможении вращающихся и поступательно движущихся масс:
Т.к. тормоз ESX027A9 имеет номинальный тормозной момент 22 Нм то найдем скорость передвижения тележки с номинальным тормозным моментом.
Применим уравнение моментов при торможении
То инерционный момент торможения будет равен:
Определим время торможения через инерционный момент при торможении
Определим максимальное замедление тележки при tт = 295 с
Номинальный тормозной момент механизма передвижения не исключает возможность юза при максимальном замедлении тележки. Для исключения возможности юза требуется уменьшить скорость передвижения тележки.
1.1.Расчет механизма подъема.
Для расчета механизма подъема кроме его основных параметров (грузоподъемности Q скорости v подъема груза высоты подъема груза) должны быть заданы режим работы механизма и его кинематическая и конструктивная схемы.
Определение усилий в канате
Принципиальная схема полиспаста механизма подъема приведена на рис.5.1.2
Рис. 5.1.2. Схема полиспаста
Натяжение каната при подъеме каретки с грузом:
Qкар = 558 – вес каретки кг;
Qгр = 1000 – вес груза кг;
m = 1 – число полиспастов;
бл – К.П.Д. блока полиспаста учитывающий потери в опорах блока а также потери вызываемые жесткостью каната.
кар = 09 – К.П.Д. каретки;
Z = 3 – число направляющих блоков.
Натяжение каната при подъеме каретки без груза:
Расчет каната по Правилам Госгортехнадзора проводим по формуле:
k – запас прочности принимаемый по Правилам Госгортехнадзора в зависимости от назначения каната и режима работы механизма; для грузовых канатов при тяжелом режиме работы k=6;
Рраз – разрывное усилие каната в целом принимаемое по таблицам ГОСТа.
При выборе каната нужно соблюдать условие:
Pст – разрывное усилие по стандарту
По таблицам на канаты ГОСТа 2688-69 выбираем канат типа ЛК-Р 6×19 = 114 диаметром 15 мм имеющий при расчетном пределе прочности проволоки при растяжении равном 160 кгмм2 разрывное усилие Рст = 11700 кг.
После выбора каната проверяют фактический запас его прочности
Фактический запас прочности:
Определение основных размеров и числа оборотов барабана
Минимально допустимый диаметр барабана измеренный по дну канавки для каната определяется по формуле:
e – коэффициент принимаемый по Правилам Госгортехнадзора в зависимости от типа грузоподъемной машины и режима ее работы. Для нашего случая e = 30;
dк = 15 – диаметр каната мм.
Так как увеличение диаметра барабана приводит к повышению долговечности каната то примем диаметр барабана Dб = 560 мм.
Число витков нарезки на барабан:
H = 12 – высота подъема груза м;
Uп= 2 – кратность полиспаста.
Длина нарезки на барабан:
Оставляем на закрепление каната с одной стороны барабана расстояние s равное длине не менее четырех шагов нарезки. При tб = 17 мм примем s = 68 мм.
Тогда общая длина барабана:
Скорость каната навиваемого на барабан при скорости груза 120 ммин
Число оборотов барабана в минуту:
Определяем статическую мощность двигателя при подъеме номинального груза:
= 09 – общее значение К.П.Д.
Проверка барабана на прочность
В барабанах при соотношении параметров напряжения изгиба и кручения незначительны.
В этих условиях проверке подлежат лишь напряжения сжатия:
d - толщина оболочки стального барабана.
Плоский цилиндрический мотор-редуктор
BF70-04DHE18XA4-TF-SZSX500A9HAK70
Плоский цилиндрический редуктор BF70
полый вал с пазом под шпонку ø 70.00 mm
Трехфазный электродвигатель DHE18XA4
Двухдисковый тормоз с пружинами ZSX500A9
Номинальная частота вращения вала ротора (n): 1470 обмин
Номинальный вращающий момент вала ротора (MN): 142Нм
Момент инерции массы ротора (Jrot): 0195кгм2
Тип редуктора: BF70-04(цилиндрический редуктор)
Скорость ведущего вала: 143обмин
Крутящий момент (Mк): 1460Нм
Передаточное число (i): 1032
Масса мотор-редуктора (m): 449 кг
Тип тормоза: ZSX500A9 (двухдисковый тормоз с пружинами)
Тормозной момент: 400 Нм
Момент инерции масс тормозного диска: 00133 кгм2
Проверка электродвигателя по времени пуска
Фактическая скорость подъема груза:
Правила Гостехнадзора регламентируют максимальные ускорения для кранов в пределах
Предполагая процесс пуска равноускоренным при заданной скорости подъема 120 ммин допустимое время пуска:
Определяем средний пусковой момент выбранного двигателя:
Yср – средняя перегрузочная способность электродвигателя в период разгона с учетом нормального падения напряжения
Ymax – максимальная перегрузочная способность электродвигателя
Определим статический момент от сил тяжести масс груза и каретки приведенный к валу мотор-редуктора:
Определяем маховой момент двигателя
Определяем маховой момент диска тормоза
Определяем маховой момент вращающихся масс
Определяем условный маховой момент поступательно движущихся масс
Определяем фактическое время пуска:
Проверка тормозного момента
где k – коэффициент запаса торможения принимаемый согласно Правилам Госгортехнадзора для тяжелого режима работы равным 2;
Мтс– статический крутящий момент на тормозном валу при торможении определенный в предположении равномерного распределения нагрузки между всеми ветвями полиспаста с учетом потерь в механизме способствующих удержанию груза;
Минимально допустимый диаметр блока:
Нагрузка на один подшипник при максимальном грузе:
- динамический коэффициент; - число блоков; - коэффициент вращения (при вращении наружного кольца подшипника )
1.2.Расчет механизма передвижения вил.
рис. 5.1.3. Схема привода передвижения вил
Оптимизация энергозатрат при гидроприводе должна производиться по двум параметрам: рабочему давлению и расходу рабочего тела раздельно. Привод телескопического захвата крана-штабелера осуществляется от нерегулируемого насоса (1) имеющего постоянную частоту вращения рабочего вала. В результате оптимизации показателя необходимо добиться выполнения условия наиболее полной загрузки электродвигателя насосной станции по мощности. Здесь необходимо сделать следующие предпосылки:
Установочная мощность приводной станции минимальна при минимуме рабочего давления и расхода рабочего тела т.е. p m
Энергозатраты минимальны при постоянстве минимальных значений давления и расхода в течение цикла т.е. при pmin= const Qmin= const.
Выбор гидроцилиндра.
Установлено что устойчивость движения горизонтально расположенных гидроцилиндров может быть обеспечена лишь при соотношении:
Dц – диаметр цилиндра;
S – ход штока цилиндра.
L – перемещение вил;
U = 2 – передаточное число.
Перемещение вил складывается из длины поддона и зазора между концом вил и стеллажом.
Рекомендуемая скорость поршня должна быть не более 05 мс поэтому время выполнения операции имеет ограничение:
Принимаем Dц = 32 мм. При данном захвате зазор между концом вил и стеллажом 006 м.
Сопротивление при выдвижении вил и нагнетании в штоковую полость без прогиба:
Gз = 25 – собственный вес захвата кг;
dр= 4 – диаметр роликов см;
= 003 – коэффициент трения качения.
Сопротивление при возврате вил с учетом уклона и с нагнетанием в поршневую полость:
Давление страгивания и холостого хода при максимальном сопротивлении передвижению вил:
Площадь поршня со стороны штоковой полости:
φ = 165 – коэффициент отношения площадей со стороны поршневой и штоковой плоскостей.
Расход рабочего тела при параллельной работе цилиндров:
V – объем рабочего тела потребляемый в течение времени Т находим как произведение площади поршня на ход поршня:
Рабочий объем штоковой полости:
Максимальный расход штока:
Давление в штоковой полости:
Давление в поршневой полости:
В каталоге выберем гидроцилиндр типа ЦРГ32*16*s:
номинальное давлением 16 МПа;
максимальное давление 20 МПа;
давление страгивания 1 МПа;
Номинальная мощность на валу насоса:
Из каталога по номинальной подаче и мощности выберем насос типа НПл 4063:
рабочий объем 40 см3;
номинальная подача 357 лмин;
номинальное давление на выходе 63 МПа;
номинальная частота вращения 950 обмин;
максимальная частота вращения 1500 обмин;
минимальная частота вращения 600 обмин;
номинальная мощность 43 кВт;
Выбор электродвигателя.
Мощность электродвигателя в зависимости от подачи насоса определяется по формуле:
Q – подача насоса лмин;
P – давление в напорной линии МПа;
п – полный КПД насоса.
N = 146*357 60*085 = 102 кВт
По каталогу на электродвигатели выберем электродвигатель типа 4А80А4 с номинальной мощностью 11 кВт.
Выбор гидрораспределителя.
Из каталога выберем (Р1) гидрораспределитель В6:
диаметр условного прохода 6 мм;
номинальное давление 6 МПа;
максимальное усилие управления на рукоятке 45 Н.
Из каталога выберем (Р2) гидрораспределитель ВЕ6 схема 574.В220.УХЛ.4
Для пластинчатого нерегулируемого насоса с давлением
до 63МПа выберем приемный (сетчатый) фильтр с номинальной тонкостью фильтрации 40 мкм.
Выбор клапана давления.
Выберем гадроклапан давления Г54-32М:
-номинальный расход масла 32 лмин;
-номинальный перепад давлений 02 МПа;
-максимальное давление на входе 20 МПа.
Т.к. система передвижения вил – это система низкого давления (до 25 МПа) то используем аллюминивые трубы по ГОСТ 18475-82 длинной 3м.
Исходя из расхода гидроцилиндров и рабочего объема насоса выберем бак вместимостью 200 л.
1.3.Расчет гидравлического буфера.
Буферное устройство предназначено для ограничения перемещения крана-штабелера вдоль стеллажей путем поглощения кинетической энергии крана-штабелера.
Задачей расчета является определение необходимого количества отверстий их диаметра и координат по длине цилиндра обеспечивающих постоянное заданное значение среднего замедления 4 мс2 в процессе торможения при амплитуде пульсаций тормозного усилия не более 20%.
Рассмотрим наиболее неблагоприятный случай: кран-штабелер с номинальным грузом движется на полной скорости двигатель привода передвижения при заезде крана-штабелера на конечный упор продолжает работать.
Определение расчетного количества отверстий вдоль образующей цилиндра
с учетом обозначений
v = 25 мс – расчетная скорость движения крана-штабелера;
m = 4250 кг – масса крана-штабелера номинальная с грузомноминальным;
= 4 мс2 – расчетное замедление;
R = 342 Н – сопротивление передвижениюкрана-штабелера;
с = 2 Нм – жесткость возвратной пружины;
λ = 0012 м – предварительное поджатие пружины;
r = 085 кгм3 – плотность рабочей жидкости;
= 06 – коэффициент расхода; для конусообразного диффузора с углом при вершине 90°;
D = 008 м – диаметр поршня;
d = 0004 м– диаметр отверстия;
z = 1 – количество одновременно работающих буферов;
P = 325 Н – усилие привода передвижения;
k – коэффициент сцепления
Дробная часть n1 числа n реализуется как отверстие диаметром:
которое располагается вблизи днища цилиндра.
Координату центра i-го отверстия отсчитываемую от торца поршня в его начальном положении вычисляют по формуле:
i – порядковый номер отверстия.
Определение скорости поршня при прохождении i-го отверстия
Si – координата центра i-го отверстия
Определение усилия на штоке непосредственно перед i-м отверстием
Определение усилия на штоке сразу же после прохождения i-го отверстия
Определение среднего значения усилия на штоке
Определение коэффициента пульсации усилия на i-ом отверстии
Определение допускаемого усилия на штоке из условия прочности цилиндра
D1 = 0093 м – наружный диаметр цилиндра;
– коэффициент учитывающий концентрацию напряжений у отверстий; рекомендуемое значение равно 08;
т = 360106 Па – предел текучести материала цилиндра;
φ – коэффициент запаса прочности; рекомендуемое значение равно 15.
Для отверстий отстоящих от днища цилиндра более чем на величину диаметра поршня должно выполняться условие:
Сравнив усилие на штоке сразу же после прохождения отверстия (max) и допускаемое усилие 1302 144820 мы видим что условие выполняется.
1.Условия работы складов на железнодорожном транспорте.
По причине высокой производительности высотный стеллажный склад (особенно с автоматизированным управлением) требует очень четкой организации. В таком складе каждая операция каждое прохождение груза пли документа работа каждой машины и каждое рабочее место человека должны быть тщательно описаны проанализированы и учтены в общем балансе работы системы. Многие функции склада особенно периферийных его частей (в отличие от стеллажной складской части) являются спонтанными например подвоз грузов по железной дороге. Поэтому к проекту организации работ предъявляются необычайно высокие требования.
Основной задачей при проектировании организации работ в складе является обеспечение стабилизации стеллажной структуры — самого дорогостоящего элемента в системе склада — и обеспечение непрерывной работы этой структуры с максимальной производительностью на протяжении смены или суток. Такой принцип позволяет ограничить до минимума расходы на стеллажную часть склада и обеспечивают быструю амортизацию.
Приведенные требования к проекту организации работ вызывают радикальное изменение прежнего понятия «проекта организации работ» который на практике обычно складывался из описания операций определения количества рабочей силы и схемы зависимостей между отдельными звеньями управления складом.
Проект организации работ высотного стеллажного склада должен на основе количественного анализа складского процесса давать инструкции по обслуживанию прохождения грузов и информации (документов) в любой момент прохождения (пиковый или средний) в тесной связи с окружением («вход» и «выход») и расчетом необходимых для обеспечения заданной производительности средств (люди и машины). В этом проекте на основе анализа различных случает должны быть также приведены инструкции по осуществлению операций и необходимые средства на случай аварии отдельных элементов этой сложной системы.
В традиционном проекте организация работ в высотном стеллажном складе разрабатывается на заключительной стадии проектирования но в получаемом результате содержатся все прежние технические и технологические решения.
В современных складских системах ориентированных на функции и связи организационные проблемы в одинаковой степени влияют как на технические так и на технологические решения. По этой причине проект организации работ следует начинать уже на стадии разработки концепции и продолжать вместе со всеми последующими стадиями проектирования. Установление четкой границы между организацией и так называемой технологией складирования является весьма затруднительным. Здесь отсутствуют какие-либо нормативные указания. Поэтому в настоящей работе принят следующий ход рассуждений.
Для установленного процесса складирования обусловленного функцией склада подбираются технические средства и проектируется организация обеспечивающая осуществление этого процесса с определенной производительностью. Складские процессы вместе с техническими средствами определяют ту или иную технологию складирования. Проект организации работ рассматривает эту технологию в количественных категориях с учетом производительности людей и машин а также определяет способ управления прохождением грузов и информации во всей системе. Достигнутое в проекте организации соответствие заданной и найденной производительности замыкает цикл проектирования склада в то время как в случае несоответствия этих показателей требуется либо вносить изменения в технологию либо возвращаться к предшествующим стадиям проектирования.
1.Организация работ.
Определим количество средств механизации погрузочно-разгрузочных работ требуемых для перерабатывания однотипного пакетного груза на складе МЧ железной дороги.
Масса груза (пакета) – 1 т
Емкость склада – 1200 т
Срок хранения – 10 сут.
Груз расположен на стандартном поддоне мм –
Высота груза с поддоном – 1350 мм
Определим суточный грузооборот склада:
- коэффициент неравномерности прибытия отправления груза
Определим суточный грузооборот в пакетах:
Определим среднюю загрузку вагона:
Vв – внутренний объем крытого вагона м3
kу = 085-09 – коэффициент учитывающий плотность укладки
Vп – объем одного пакета м3
Внутренний объем крытого вагона выбираем
Для перевозки тарно-штучных грузов принимаем крытый четырехосный вагон грузоподъемностью 65 т.
В вагоне умещается 83 пакета по объему но учитывая тот факт что грузоподъемность вагона составляет 65 т а масса одного пакета 1 т то принимаем количество пакетов в вагоне равным 65 шт.
Определим число железнодорожных вагонов (суточный вагонопоток) в которых поступает груз:
Т.к. в вагон вмещается 65 пакетов следовательно в два вагона вмещается 130 пакетов а оставшиеся 14 пакетов отправим автотранспортом.
Определим число вагонов в одной подаче:
z – число подач вагонов на грузовой пункт за сутки ( z = 2 5 ) z = 1
Вычислим необходимое количество поддонов на складе:
- коэффициент учитывающий время нахождения поддонов в ремонте
- время оборота поддонов (время перевозки и хранения груза на складе).
Определим количество автотранспорта:
Tц – продолжительность транспортного цикла автомобиля
- дальность перевозки км (для внутригородских поставок )
- среднетехническая скорость автомобиля
- коэффициент пробега автомашины
Tпр = 01 – время простоя под грузовыми операциями
qа = 5 т – фактическая загрузка автомобиля
T = 8 ч – количество рабочих часов автомобиля в сутки
kt = 07 – коэффициент использования автомобиля по времени
Длина фронта подачи вагонов:
lв – длина ж.д. вагона по автосцепке l = 1473 м
aм – удлинение фронта подачи вагонов для выполнения маневровых работ aм = (15 2)
Длина фронта погрузки-выгрузки:
zс – число смен (перестановок) вагонов на грузовом фронте (zс = 1 2)
При установке автомобиля к рампе склада торцом:
k – число погрузочно-разгрузочных постов образующих фронт погрузки выгрузки (равно числу дверных проемов со стороны автотранспорта); k = 2
bа = габаритная ширина автомобиля м; bа = 25 м
Sт – расстояние между смежными автомобилями обеспечивающее выезд автомобиля при торцевой расстановке м; Sт = 1 м
Вместимость склада с учетом хранения
Определим общее количество порожних поддонов.
На складе 1440 поддонов загружены а 10% - порожние поддоны.
Определим количество пачек.
В одной пачке сложено 10 поддонов следовательно:
Определим геометрические размеры элементарной площадки под поддоны:
– длина элементарной площадки
– ширина элементарной площадки
– площадь элементарной площадки
Вместимость одного стеллажа
Zl Zh – количество ячеек по длине и ширине (Zl = 15 Zh = 8)
Определим количество стеллажей
Определим размеры стеллажа
Т.к. максимальный размер пакета составляет 1200 мм то длина ячейки Az = 1500 мм ширина ячейки Bz = 900 мм; высота пакета с поддоном составляет 1350 мм то высота ячейки Hz = 1500 мм.
Определим площадь площадки занятой стеллажами
r = 1000 мм – ширина проезда между стеллажами
nпр = 6 – количество проездов между стеллажами
Высота склада – 128 м
Ширина склада – 32 м
Высота рампы для ж.д. вагонов – 125 м
Высота рампы для автомобилей – 125 м
Ширина погрузочно-разгрузочной платформы для обслуживания ж.д. подвижного состава и автомобилей – 4 м
Расстояние от края платформы до оси ж.д. пути – 165 м
Расстояние от оси пути ж.д. пути до стены склада – 566 м
Размеры одного стеллажа м (Д х Ш х В) – 225 х 09 х 12
Расстояние между стеллажами – 1 м
Количество стеллажей – 12 шт
Выбор типа и количества погрузочно-разгрузочных машин
Электропогрузчик грузоподъемностью 1 т.
Технические характеристики электоропогрузчика:
Грузоподъемность – 1 т
Высота подъема груза – 2 м
Скорость подъема вил:
Скорость опускания вил:
Наибольшая скорость передвижения:
Дорожный просвет – 100 мм
Внешний радиус поворота – 1600 мм
Наименьшая ширина проездов под углом 90° - 2950 мм
Техническая производительность машин используемых при переработке тарно-штучных грузов находиться по формуле:
Gм – грузоподъемность машины т
Tц – продолжительность времени цикла с
Для погрузчика время цикла:
tдв t’дв – время затрачиваемое погрузчиком на продольные и поперечные передвижения по складу с грузом и без груза с
tпод t’под – время затрачиваемое на подъем каретки погрузчика с грузом и без груза с
tоп t'оп – время затрачиваемое на опускание каретки с грузом и без груза с
tпов – время затрачиваемое на повороты погрузчика с
tвсп – время затрачиваемое на вспомогательные операции
l – длина рабочего плеча м
v – скорость движения погрузчика мс
a – ускорение погрузчика мс2
Средняя высота подъема:
H – высота подъема груза погрузчиком
Определение эксплуатационной и сменной производительности
Эксплуатационная производительность погрузчика:
kв = 08 – коэффициент использования по времени
Сменная производительность:
Объем механизированной переработки груза:
mсм = 1 – количество смен
Tр – время нахождения машины в ремонте и смены батареи в течение года
Принимаем Мм = 2 машину с учетом одновременной разгрузки-погрузки автомобиля и одной ж.д. подачи.
Определение производительности крана-штабелера на складе базового варианта
Техническую производительность крана-штабелера в базовом варианте определим по формуле:
Gгр = 1000 кг – вес пакета
C – число циклов которое машина делает за 1 час
tц – время цикла сек
lp = 1185 м– средняя длина перемещения крана-штабелера
lv = 1 м – длина выдвижения грузозахватного органа
lk = 5 м – средняя высота подъема пакета
vp = 1 мс – скорость передвижения крана
vv = 025 мс – скорость выдвижения грузозахватного органа
vk = 1 мс – скорость подъема грузозахватного органа
Эксплуатационная и сменная производительность:
kв = 09 – коэффициент использования крана по времени
Определение производительности крана-штабелера на складе нового варианта
vp = 25 мс – скорость передвижения крана
vk = 2 мс – скорость подъема грузозахватного органа
Эксплуатационная производительность:
В результате анализируя полученные результаты можно сделать вывод о том что склад с новым вариантом крана-штабелера более предпочтителен с точки зрения производительности перед складом с базовым вариантом крана-штабелера так как эксплуатационная производительность нового крана-штабелера больше чем у базового крана-штабелера.
Определение количество кранов-штабелеров на складе
Т. к. на складе имеется 12 стеллажей: 2 стеллажа расположены раздельно (по краям склада) а 10 стеллажей расположены по парно т.е. пять пар стеллажей между стеллажами имеются проезды для кранов-штабелеров.
Для обслуживания 12 стеллажей требуется 6 кранов-штабелеров.
Технологическая часть
1.Разработка технологического процесса штока гидробуфера
В конструкторском разделе диплома выполнен основной расчет параметров гидробуфера.
Рассчитаны на прочность его основные детали в том числе и шток как наиболее ответственный элемент.
По заданию в технологической части необходимо разработать технологический процесс изготовления штока а именно выбрать заготовку составить маршрут изготовления подробно разработать токарную и шлифовальную операции составить на них эскизы.
1.1.Анализ технологических требований изготовления детали
Шток является оригинальной деталью что обосновывает целесообразность составления технологической карты его изготовления.
Деталь изготавливается в условиях единичного производства из стали 45 ГОСТ 1050-88 твердостью НВ 190 - 230 термообработка – нормализация. Она представляет собой 6-ти ступенчатый вал длиной 390 мм. Относится к группе цилиндрических изделий. Внутри - сплошной.
Первая ступень диаметром 20 мм и длиной 30 мм служит для нарезания резьбы обрабатывается с допуском h9 шероховатостью Rа = 08 мкм.
Вторая ступень диаметром 24 мм и длиной 15 мм служит для фрезерования на ней четырёхгранника обрабатывается с допуском h11 шероховатостью Rz40.
Третья ступень диаметром 45 мм и длиной 248 мм служит опорой для посадки уплотнения с допуском f9 шероховатостью Rа = 032 мкм.
Четвёртая ступень диаметром 61 мм и длиной 10 мм служит упорным буртиком специально не обрабатывается.
Пятая ступень диаметром 45 мм и длиной 52 мм является переходной ступенью специально не обрабатывается.
Шестая ступень диаметром 18 мм и длиной 38 мм служит для нарезания резьбы обрабатывается с допуском h9 шероховатостью Rа = 08 мкм.
Для удобства монтажа делаем фаски на ступенях: 1 2356 которые подрезаются на токарном станке при помощи проходного резца. Фаски не являются рабочими поэтому точность и шероховатость обеспечивается инструментом.
На поверхностях 1 и 6 необходимо нарезать резьбу после черновой и чистовой обработки. Поверхность 2 необходимо фрезеровать под четырёхгранник.
При изготовлении детали необходимо выдерживать допуски формы и расположения.
Допуск цилиндричности (табл. 24.2 [1]);
- для поверхностей 3 (45 f9 )
Тo = 05 .62 = 31 мкм. Принимаем Тo = 003 мм;
- для поверхности 6 (18 h9)
Тo = 05 .52 = 26 мкм. Принимаем Тo=003 мм;
- для поверхности 1 (20 h9)
Тo = 05 .52= 26 мкм. Принимаем Тo=003 мм;
Допуск перпендикулярности упорного буртика под поршень.
– степень точности допуска 7 (табл. 22.4 [9]);
Т = 0016 мм (табл. 22.8 [9]); Принимаем Т = 001мм
1.2.Выбор вида финишной обработки конструктивных элементов детали.
Для обрезки заготовки в размер сверления центровых отверстий и формирования профиля вала применим токарный станок 16К20.
Для поверхности 2 (24h12) 4 (61h14) 5 (45h14) с шероховатостью Rz 80 назначаем только черновое точение.
Для поверхности 2 (24h11) с шероховатостью Rz 40 назначаем получистовое точение.
Для поверхностей 1(20h9) 6 (18h9) с шероховатостью Ra 08 назначаем окончательное шлифование.
Для поверхностей 3 (45f9) для участка под манжетное уплотнение с Ra 032 назначаем полирование.
Фаски галтели и центровые отверстия получаем на токарном станке при закреплении заготовки в патрон.
Для получения резьбы используем резьбовой резец.
1.3.Выбор способа установки заготовки для её обработки.
Рассчитаем средний диаметр заготовки как:
где:n – число конструктивных элементов;
– диаметр и длина конструктивного элемента;
Определим коэффициент жесткости:
Т.к. Кж>12 то применяем установку в центрах с люнетом.
1.4.Выбор вида определение размеров заготовки типа и типоразмера центровых отверстий.
Для условий единичного или мелкосерийного производства и при несущественном перепаде диаметров для детали типа вал применяется в качестве заготовки круглый горячекатаный сортовой прокат.
При максимальном диаметре детали 61 мм и при К = рекомендуемый диаметр заготовки 65 мм.
Из номенклатуры круглого сортового проката выбираем сталь горячекатаную круглую ГОСТ 2590 – 88 обычной степени точности (В) 65 мм с предельными отклонениями +05; -11 допуск на заготовку составляет 16мм (Т = 16мм) что соответствует 16 квалитету.
Определим длину заготовки:
где Zто – припуск на торцевую обработку. При номинальном диаметре проката свыше 50 до 50 мм Zто = 3мм(по табл. П7 [10])
Центровые отверстия для токарной и шлифовальной обработки выбираем согласно ГОСТ 14034-74. Для детали 65 мм рекомендовано центровое отверстие В 63.
Выбираем: отверстие центровое В 63. ГОСТ 14034-74.
1.5.Составление укрупнённого маршрута изготовления детали.
Отрезать заготовку от проката круглого сечения обычной степени точности 65мм длиной 396мм.
Заготовку подвергнуть термообработке – нормализации до НВ 280.
Выполнить обработку торцов в размер 390 h14 и сверлить два центровых отверстия В 63. ГОСТ 14034-74.. За несколько технологических переходов выполнить обработку по формированию контура детали. Точить фаски канавки.
0 Кругло-шлифовальная
Выполнить предварительную и окончательную обработку шеек детали.
Фрезеровать многогранник.
Подвергнуть ТВЧ шейку вала 45f9под манжету.
Очистить детали от загрязнений;
Выполнить контроль детали по условиям чертежа;
2.Разработка операций по формированию контура детали.
2.1.Расчёт числа стадий обработки по каждому конструктивному элементу.
Ужесточение точности:
Число стадий обработки:
1.1.Расчёт точности промежуточных размеров заготовки по стадиям обработки.
Определим точность заготовки по каждой стадии механической обработки для каждой поверхности. При расчете шаг уменьшения квалитетов по стадиям механической обработки должен изменяться по закону убывающей арифметической прогрессии. Расчет ведём в табличной форме.
Таблица 1. Расчет точности промежуточных размеров
– ой 20h9 и 6 – ой 18h9
Обтачивание черновое
Обтачивание чистовое
Шлифование окончательное
Таблица 2. Расчет точности промежуточных размеров
Таблица 3. Расчет точности промежуточных размеров 3 – ей поверхности вала: 45f9
Для получения размера 24 и 5-ой поверхности с 45h14 61h14 и 24h12 используем только обтачивание черновое.
1.2.Определение промежуточных размеров по стадии механической обработки
Расчет ведем в табличной форме используя следующие формулы:
где: - припуск на обработку поверхности принимается из ;
d - текущий диаметр;
d() - диаметр предшествующей обработки;
- исходный размер ступени вала;
– максимальный размер ступени вала.
Таблица 4. Расчет припусков на промежуточные размеры 3 - ей ступени вала 45f9
Расчёт промежуточных размеров
Характеристика размера
Точение получистовое
Таблица 5. Расчет припусков на промежуточные размеры 1 - oй ступени вала 20h9
Таблица6. Расчет припусков на промежуточные размеры 6 - oй ступени вала 18h9
Таблица 7. Расчет припусков на промежуточные размер 2-ой ступени
Таблица 8. Расчет припусков на промежуточные размер 4-ой ступени
Таблица 9. Расчет припусков на промежуточные размер 5-ой ступени
Окончательно выбираем из сортамента прокат 65мм
2.Составление плана токарной и шлифовальной обработок детали
Расчёт выполняем из условия применения станка 16К20 имеющего следующие характеристики:
- допустимая мощность резания N = 75 кВт;
- максимальный диаметр заготовки до 400 мм;
- максимальная длина заготовки 1400 мм;
- частота вращения шпинделя 125 1600 обмин (регулирование ступенчатое);
- продольная подача суппорта 005 28 ммоб (регулирование ступенчатое).
2.1.Расчет предельно-допустимых глубин резания при черновом обтачивании.
Глубину резания для технологического перехода рассчитываем по формуле:
и сравниваем полученное значение с предельно допустимым для данного диаметра:
если обработка осуществляется за один переход
если обработка осуществляется за несколько технологических переходов.
Применим формулу с коэффициентом «005» т.к. Кж = 98>12.
При этом назначаем подачу инструмента и сравниваем мощность резания с допустимой мощностью на шпинделе (75 кВт).
Третья ступень: 4553
следовательно обработка по диаметрам возможна за 2 прохода.
Выполняем анализ по мощности:
При подаче инструмента S = 03 ммоб и глубине резания t = 487 мм мощность N = 72 кВт что меньше 75кВт (по табл. П13 [10]).
следовательно обработка по диаметрам возможна за 5 проходов.
При подаче инструмента S = 06 ммоб и глубине резания t = 21 мм мощность N = 71 кВт что меньше 75кВт (по табл. П13 [10]).
Первая ступень: 2056
следовательно обработка по диаметрам возможна за 1 проход.
При подаче инструмента S = 06 ммоб и глубине резания t = 197 мм мощность N = 71 кВт что меньше 75кВт (по табл. П13 [10]).
Четвёртая ступень: 61
При подаче инструмента S = 06 ммоб и глубине резания t = 2 мм мощность N = 72 кВт что меньше 75кВт (по табл. П13 [10]).
При подаче инструмента S = 04 ммоб и глубине резания t = 4 мм мощность N = 71 кВт что меньше 75кВт (по табл. П13 [10]).
Шестая ступень: 1856
следовательно обработка по диаметрам возможна за 8 проходов.
При подаче инструмента S = 06 ммоб и глубине резания t = 165 мм мощность N = 71 кВт что меньше 75кВт (по табл. П13 [10]).
3.Выбор и расчёт режимов резания.
3.1.Токарная обработка.
При черновом обтачивании применяем проходной резец с главным углом в плане φ = 450 стойкостью Т = 60 мин из материала Т15К6.
-для чернового обтачивания принимаем значение подачи из пункта 7.1.
-для получистового обтачивания:
. SТАБЛ = 087 при Rz = 40. (по табл. П11 [10])
где К3 = 045 (по табл. П11 [10])
Из нормального ряда продольных подач суппорта станка принимаем значение S = 04 ммоб.
Cv - коэффициент скорости зависящий от значения величины подачи.
Принимаем согласно (по табл. П14 [10]);
Т – расчётная стойкость резца в минуту. Принимаем согласно (по табл. П13 [10]);
t – глубина резания;
Коэффициент корректировки.
КMV – коэффициент учёта влияния материала заготовки на скорость резания; КПV – коэффициент учёта влияния состояния поверхности на скорость резания (по табл. П18 [10]);
КИV – коэффициент учёта влияния инструментального материала на скорость резания для материала Т15К6 (по табл. П19 [10]);
КφV – коэффициент учёта влияния главного угла в плане резца на скорость резания (по табл. П20 [10]).
КГ - коэффициент характеризующий группу стали по обрабатываемости.
Принимаем согласно (по табл. П17 [10]);
- предел выносливости. Принимаем согласно [4 табл.2] =600 МПа
nv – показатель степени. Принимаем согласно (по табл. П16 [10]).
Результаты вычислений сведены в таблицу 9.
1.1.Расчёт режимов шлифования.
Шлифование выполняем на шлифовальном станке 3Б151 который имеет следующие характеристики:
-наибольший диаметр и длина шлифуемой заготовки: 180 х 630(800) мм;
-диаметр и ширина шлифовального круга: 600 х 63 мм;
-частота вращения детали: 63 400 обмин (бесступенчатое регулирование);
-скорость продольного перемещения рабочего стола: 01 06 ммин (бесступенчатое регулирование);
-поперечная подача шлифовального круга (глубина шлифования): 00025 005 мм на один ход рабочего стола с шагом 00025 мм;
-непрерывная подача шлифовального круга при врезном шлифовании: 01 2 мммин;
-мощность электродвигателя привода шлифовального круга: 7 кВт.
1.2.Расчёт режимов предварительного шлифования.
Согласно [32] с. 302 для предварительного шлифования принимаем:
-скорость вращения шлифовального круга: vШЛ.КР. = 30 мс;
-скорость вращения заготовки: vЗАГ. = 20 ммин;
-продольная подача шлифовального круга: S = (03 07)ВШЛ.КР. = 189 441 ммоб. Принимаем S = 30 ммоб;
-глубина шлифования tШЛИФ = 001 мм;
-количество проходов шлифовального круга:
Частота вращения шлифовального круга:
Частота вращения заготовки:
Результаты вычислений сведены в таблицу 10.
1.3.Расчёт режимов окончательного шлифования.
Согласно [32] с. 302 для окончательного шлифования принимаем:
-скорость вращения шлифовального круга: vШЛ.КР. = 35 мс;
-скорость вращения заготовки: vЗАГ. = 35 ммин;
-продольная подача шлифовального круга: S=(02 04)ВШЛ.КР.=126 256 моб. Принимаем S = 20 ммоб;
-глубина шлифования tШЛИФ = 0005 мм;
Режимы токарной обработки вала.
Диаметр поверхности мм
Расчётное значение n мин-1
Принятое значение n мин-1
- Установ В (черновое обтачивание)
- Установ Г (черновое обтачивание)
- Установ Г (получистовое обтачивание)
- Установ Д (получистовое обтачивание)
Режимы шлифовальной обработки вала.
Расчётная мощность N кВт
- Установ А (шлифование окончательное)
- Установ Б (шлифование окончательное)
В ходе расчетно-пояснительной записки был разработан технологический процесс на изготовление детали – шток для единичного условия производства. В работе были применены технологические оборудования и инструменты: токарный станок 16К20 шлифовальный станок 3Б151 и резец Т15К6.
Оформлена технологическая документация на операции и переходы применяемые в ходе получения детали. Установлены и применены в ходе разработки техпроцесса основные принципы и приемы используемые при обработке металлов резанием.
Технико-экономические расчеты
1.Описание сравниваемых результатов. Исходные данные для расчетов.
Вилочный захват крана-штабелера включает в себя электромеханический привод в котором движение передается от электродвигателя к исполнительному механизму через карданный вал. Комплекс обслуживают 3 человека.
Вилочный захват крана-штабелера включает в себя гидравлический привод в котором движение исполнительного механизма происходит от электородвигателя соединённого непосредственно с рабочим органом а также механизмы передвижения и подъема в которых движение исполнительного механизма происходит от мотор-редуктора. Комплекс обслуживает 1 человек.
Исходные данныеТаблица 8.1.
Количество элементов привода:
гидроклапан давления
1.Определение барьерной ставки.
Барьерная ставка определяет ту финансовую отдачу которую инвесторы ожидают от своих капитальных вложений и включает в себя два компонента – свободную от риска ставку СРС и страховую премию СП.
Поэтому можно сказать что стоимость капитала предприятия представляет собой рыночную оценку уровня риска по операциям предприятия. Предприятия принимают эту оценку в качестве среднего значения барьерного коэффициента HR так как у них нет более объективного показателя.
Стоимость капитала – это средневзвешенная цена (в процентах) которую предприятие уплатило за денежные средства использованные для формирования своего капитала. Эта величина определяется соотношением заемного и собственного капиталов в пассивной части баланса и может быть определена следующим образом:
СК – стоимость капитала %;
СД – стоимость долга %;
ДСК – доля собственного капитала;
ССК – стоимость собственного капитала %.
Так как выплаты процентов по займам уменьшают величину налогооблагаемой прибыли то собственно уменьшается и величина налоговых выплат. Экономия на налогах частично компенсирует выплаты по долгам. Поэтому процент выплат по займам с учётом этой экономии составит:
СН – ставка налога на прибыль;
NE(СД) – уровень эффекта процентной ставки;
В условиях высокой инфляции ставки ссудного процента и депозитные ставки рассчитываются с учетом внутригодовых реинвестиций и очищаются от инфляции.
Берутся номинальные (т.е. с учетом инфляции) годовые ставки коммерческих банков. На их основе рассчитываются эффективные ставки (т.е. с учетом реинвестиций по периодам внутри года):
NE(СД ССК) – номинальная эффектная ставка (кредитная и депозитная соответственно)
N(кб дб) – номинальная банковская ставка (кредитная и депозитная соответственно)
p – число периодов начисления процентов внутри года.
2.Расчет инвестиций и расходов.
Кдв – капитальные вложения на закупку электродвигателей;
Кт – капитальные вложения на закупку тормозов;
Кр – капитальные вложения на закупку редукторов;
Кк.в. – капитальные вложения на закупку карданных валов;
Кмах – капитальные вложения на закупку маховиков;
Кмуфт – капитальные вложения на закупку муфт шарнирных;
Крем – капитальные вложения на закупку ремней.
Цдв – стоимость одного электродвигателя
Zдв – количество электродвигателей
γм – коэффициент учитывающий затраты на доставку и монтаж
Цт – стоимость одного тормоза
Zт – количество тормозов
Цр – стоимость одного редуктора
Zр – количество редукторов
Цк.в – стоимость одного карданного вала
Zк.в – количество карданных валов
Цмах – стоимость одного маховика
Zмах – количество маховиков
Цмуфт – стоимость одной муфты шарнирной
Цмуфт = 4060 (руб.);
Zмуфт – количество муфт шарнирных
Црем – стоимость одного ремня
Zрем – количество муфт шарнирных
Км.р. – капитальные вложения на закупку мотор-редукторов;
Кц – капитальные вложения на закупку гидроцилиндров;
Кн – капитальные вложения на закупку гидронасосов;
Краспр – капитальные вложения на закупку гидрораспределителей;
Кт.ж. – капитальные вложения на закупку жестких трубопроводов;
Ккл.дав. – капитальные вложения на закупку клапанов давления.
Кф – капитальные вложения на закупку фильтров;
Кб – капитальные вложения на закупку гидробака;
Кв – капитальные вложения на закупку вентиля.
Цм.т. – стоимость одного мотор-редуктора
Цм.т. = 25200 (руб.);
Zм.т. – количество мотор-редукторов
Цц – стоимость одного гидроцилиндра
Zц – количество редукторов
Цн – стоимость одного гидронасоса
Zн – количество гидронасосов
Цраспр – стоимость одного гидрораспределителя
Цраспр = 4594 (руб.);
Zраспр – количество гидрораспределителей
Цт.ж. – стоимость одного метра жесткой трубы
Lт.ж. – длина жесткой трубы
Цкл.давл. – стоимость одного гидроклапана давления
Цкл.давл. = 2400 (руб.);
Zкл.давл. – количество гидроклапанов давления
Zкл.давл. = 1 (шт.);
Цф – стоимость одного фильтра
Zф – количество фильтров
Цб – стоимость одного гидробака
Zб – количество гидробаков
Цв – стоимость одного вентиля
Zв – количество вентилей
3.Изменение расходов.
Сзаробщ – расходы на заработную плату обслуживающего персонала;
Сотч – отчисления на социальные нужды;
Снакл – накладные расходы (расходы на содержание административно-управленческого персонала);
Срем. – расходы на ремонт и техническое обслуживание;
Сэл – расходы на электроэнергию за год;
Саморт – амортизационные отчисления на реновацию.
Стар.зар. – тарифная заработная плата
Кп = 3 (чел) – количество обслуживающего персонала;
Тст = 6200 (руб) – тарифная ставка по должностям.
Сдоп. – доплата к заработной плате.
Сдоп.зар. – дополнительная заработная плата;
Цэл – тариф на электроэнергию : Цэл = 35 ркВт×ч ;
Ки – коэффициент использования оборудования по времени 07
Fэф – эффективный годовой фонд времени работы оборудования
Q – срок службы машины Q = 12 лет.
Кп = 1 (чел) – количество обслуживающего персонала;
Расчет чистых денежных потоков приведен в таблице 8.2.
Расчет чистых денежных потоков.
Приращение доходов и расходов
экономия заработной платы
отчисления на социальные нужды
расходы по содержанию и эксплуатации оборудования
расходы на электроэнергию
Корректировка денежных потоков:
Чистые денежные потоки
4.Чистая текущая стоимость (NPV)
Чистая текущая стоимость является суммой дисконтированных чистых денежных потоков порождённых капиталовложениями и определяется следующим образом:
ЧДП – чистый денежный поток руб.;
HR – барьерная ставка;
n – число лет функционирования проекта.
ЧДП берётся со знаком соответствующим оттоку или притоку денежных средств.
Положительное значение чистой текущей стоимости (NPV) говорит об эффективности рассматриваемого варианта.
Рассчитаем значения чистой текущей стоимости.
Внедрение и использование модернизированного захвата увеличивает производительность погрузочно-разгрузочных работ позволяет увеличить грузопоток что является основной экономической характеристикой склада и получить экономический эффект.
Безопасность жизнедеятельности.
1.Безопасность персонала при обслуживании проектируемого склада
1.1.Эксплуатационно-технические характеристики.
Режим работы по ГОСТ 25546-827К
Габариты перерабатываемого груза м:
Высота выдвигаемых элементов грузозахватного органа мм70
Величина выдвижения грузозахватного органа мм920
Скорость передвижения крана мс25
Скорость подъема грузозахватного органа мс2
Скорость выдвижения грузозахватного органа мс025
Техническая производительность тч178
Суммарная мощность двигателей кВт253
Тип нижнего путиР24 ГОСТ 6368-82
Тип верхнего путидвутавр 12 ГОСТ 8239-72
Подвод электропитаниякабельный
Управлениеавтоматическое
Климатическое исполнениеУХЛ4 ГОСТ 15150-69
Класс пожароопасностиП-2а
1.1.Требования к персоналу режимы работ квалификация
К управлению электропогрузчиком допускаются лица не моложе 18 лет прошедшие теоретическое и практическое обучение сдавшие экзамен и получившие удостоверение на право управления электропогрузчиком.
Перед допуском к работе водителю электропогрузчика необходимо пройти медицинское освидетельствование получить вводный инструктаж по охране труда первичный инструктаж на рабочем месте освоить безопасные приемы эксплуатации электропогрузчика; пройти проверку знаний в объеме II группы по электробезопасности теоретических знаний и приобретенных практических навыков безопасного выполнения работ по управлению электропогрузчика при подъеме транспортировке и укладке грузов.
Водитель электропогрузчика должен:
перед началом работы проверить техническое состояние погрузчика;
обладать навыками требующимися для управления всеми механизмами погрузчика и ухода за ним;
знать правила безопасного перемещения грузов;
соблюдать действующие в организации правила внутреннего трудового распорядка график работы режим труда и отдыха.
извещать своего непосредственного руководителя о происшедшем с ним или по его вине несчастном случае а также о любом несчастном случае происшедшем на производстве об ухудшении состояния своего здоровья в том числе о проявлении признаков острого заболевания.
Режим работ водителей электрпогрузчиков по 12 часов в 1 смену.
1.2.Основные опасности и вредности при работе персонала
Во время работы персонала на складе могут воздействовать следующие опасные и вредные производственные факторы:
столкновение или наезд на людей или другим транспортным средством;
падение перевозимого груза.
удар электрическим током
неустойчивые штабели перемещаемых и складируемых товаров; повышенная запыленность воздуха рабочей зоны;
недостаточная освещенность места проведения работ;
острые кромки заусенцы и шероховатости на поверхностях деталей инструмента;
опасный уровень напряжения в электрической цепи.
движущиеся и вращающиеся детали и узлы крана-штабелера;
При работе с различными грузами возможно влияние таких опасных и вредных производственных факторов как токсические раздражающие сенсибилизирующие канцерогенные мутагенные влияющие на репродуктивную функцию.
1.1.Технические и организационные мероприятия по обеспечению персонала при работе на складе.
Поскольку персонал работает на складе то рассмотрим проблему освещения рабочего места.
Требования к освещению.
Оборудование электрического освещения производственных и бытовых помещений сборочно-сварочных цехов и участков должно соответствовать нормам установленным в СН 245-71 и СНиП 23-05-95.
В зависимости от вида источника света производственное освещение подразделяется:
на естественное которое создается излучением поступающим непосредственно от Солнца без изменения направления распространения и диффузным (отраженным и рассеянным атмосферой) солнечным светом;
искусственное обеспечиваемое электрическими светильниками.
Естественный (солнечный) свет по спектральному составу значительно отличается от излучения электрических источников.
В солнечном спектре гораздо больше необходимых человеку ультрафиолетовых лучей. Для естественного освещения характерна высокая степень рассеяния света благоприятная для зрительной работы.
Рис. 5.4. Схемы распределения коэффициента естественной освещенности е по разрезу помещения:
а - одностороннее боковое освещение; б - двустороннее боковое освещение; в - верхнее освещение; г - комбинированное освещение; 1 - уровень рабочей плоскости; еmin и еср - минимальное и среднее значения коэффициента естественной освещенности
В соответствии с конструктивными особенностями помещения естественное освещение может быть (рис. 5.4):
боковым (осуществляется через окна в наружных стенах);
верхним (производится через аэрационные и зенитные фонари проемы в покрытиях и световые проемы в местах перепада высоты смежных пролетов зданий);
комбинированным (к верхнему освещению добавляется боковое).
Искусственное освещение предусматривается в тех случаях когда естественного света недостаточно или он отсутствует.
По конструктивному исполнению осветительной системы искусственное освещение может быть:
местным создающим световой поток непосредственно на рабочем месте;
общим (освещается все помещение);
комбинированным (к общему освещению добавляется местное).
Общее освещение подразделяется на равномерное и локализованное создаваемое с учетом расположения рабочих мест.
Ряд единиц необходимых для расчета искусственного освещения вытекает из задач данного мероприятия. Эти единицы нормированы и поддержание их обеспечивает оптимальное распределение световой энергии а значит позволяет выполнить поставленные задачи. Основные параметры которые учитываются при расчете искусственного освещения таковы:
Световой поток. Данная величина измеряемая в люменах (лм) существенна для расчета искусственного освещения поскольку характеризует мощность лучистой энергии в 1 Вт.
Освещенность. Эта характеристика измеряемая в люксах (лк) важна для расчета искусственного освещения поскольку определяет отношение светового потока к площади освещаемой поверхности.
Сила света измеряется в канделах (кд) и учитывается при расчете искусственного освещения потому что характеризует плотность светового потока.
Светимость важна для расчета искусственного освещения в силу того что определяет отношения светового потока к источнику освещения. Принятая единица измерения – лмм2.
Яркость. Эта величина принципиальна для расчета искусственного освещения потому что определяет отношение силы света к освещаемой поверхности.
Для расчета искусственного освещения специалисты прибегают к различным методам: точечному методу методу удельных мощностей и методу коэффициента использования светового потока.
Точечный метод расчета искусственного освещения
Его особенность состоит в том что учитывается отраженная световая энергия. Расчет искусственного освещения производится опираясь на показатели силы света (I кд) высоты подвеса осветительного прибора (H м) а также коэффициент запаса (11 5 - 18).
Для расчета искусственного освещения данным методом используются отдельные формулы для горизонтальной и вертикальной плоскости:
Ег=I*cos3αН 2 *К3 - для горизонтальной плоскости
Ев= I*cos3 (90-α) Н 2 *К3 - для вертикальной плоскости
При расчете искусственного освещения помещения или пространства несколькими светильниками освещенность определяется от каждого источника а затем показатели суммируются.
Следовательно формула для расчета искусственного освещения в данном случае усложняется ведь необходимо учесть и количество ламп (n) и коэффициент дополнительной освещенности точки ( 11 - 12) и световой поток лампы (Фл лм) и сумму условных освещенностей от светильников которые светят в данную точку (ΣЕг) и условный световой поток (1000 лм). Поэтому при расчете искусственного освещения для нескольких светильников используется формула:
Расчет искусственного освещения методом удельных мощностей
Достоинство данного метода расчета искусственного освещения состоит в простоте а слабая сторона – в недостаточной точности. Потому эта техника применяется при первичных расчетах. Суть подобного расчета искусственного освещения сводится к определению количества светильников того или иного типа с помощью таблиц удельных мощностей.
В подобных специальных таблицах указаны удельные мощности источников освещения в зависимости от площади освещаемой поверхности типов светильников высоты их подвеса необходимой освещенности. При этом в ходе расчета искусственного освещения используют формулу удельной мощности:
где n - число ламп в светильниках
Рл - мощность лампы Вт;
S - площадь освещаемого помещения м2.
Таком образом с помощью данной формулы расчета искусственного освещения можно определить количество светильников которое необходимо для освещения данной площади и электрическую мощность приборов.
Расчет искусственного освещения методом коэффициента использования светового потока
Данный метод расчета искусственного освещения считается самым популярным. Его сущность состоит в определении светового потока необходимого для достижения заданных показателей освещенности. При расчете искусственного освещения таким способом учитывается отраженный свет и необходимость в равномерном распределении светового потока. Формулы которые используются для расчета искусственного освещения зависят от вида источника освещения.
Расчет искусственного освещения для ламп накаливания и ламп типов ДРЛ ДРИ и ДНат:
где F—световой поток одной лампы лм;
Е—нормированная освещенность лк;
S—площадь помещения м2;
z—коэффициент неравномерности светильника (для стандартных светильников 11—13);
Kз — коэффициент запаса;
n - число светильников;
u —коэффициент использования зависящий от типа (055—060)
Расчет искусственного освещения для люминесцентных ламп:
F=( E*S*z*Kз)(n*Фл* )
где Фл - световой поток лампы лм;
- коэффициент использования светового потока осветительной установки.
Защитное заземление.
Одним из основных опасных факторов при обслуживании ПФМ является возможность поражения электрическим током. Для защиты применяют защитное заземление.
Заземление электроустановки — преднамеренное электрическое соединение ее корпуса с заземляющим устройством.
Заземление электроустановок бывает двух типов: защитное заземление и зануление которые имеют одно и тоже назначение - защитить человека от поражения электрическим током если он прикоснулся к корпусу электроприбора который из-за нарушения изоляции оказался под напряжением.
Защитное заземление - преднамеренное соединение с землей частей электроустановки.
Принцип действия защитного заземления – снижение до безопасных значений напряжений прикосновения и шага обусловленных замыканием на корпус. Это достигается уменьшением потенциала заземленного оборудования а также выравниванием потенциалов за счет подъема потенциала основания на котором стоит человек до потенциала близкого по значению к потенциалу заземленного оборудования. Область применения защитного заземления – трехфазные трехпроводные сети напряжением до 1000 В с изолированной нейтралью и выше 1000 В с любым режимом нейтрали (рис. 9.2.1.).
Рис. 9.2.1. Принципиальные схемы защитного заземления
В случае возникновения пробоя изоляции между фазой и корпусом электроустановки корпус ее может оказаться под напряжением. Если к корпусу в это время прикоснулся человек - ток проходящий через человека не представляет опасности потому что его основная часть потечет по защитному заземлению которое обладает очень низким сопротивлением. Защитное заземление состоит из заземлителя и заземляющих проводников.
Есть два вида заземлителей – естественные и искусственные.
К естественным заземлителям относятся металлические конструкции зданий надежно соединенные с землей.
В качестве искусственных заземлителей используют стальные трубы стержни или уголок длиной не менее 25 м забитых в землю и соединенных друг с другом стальными полосами или приваренной проволокой. В качестве заземляющих проводников соединяющих заземлитель с заземляющими приборами обычно используют стальные или медные шины которые либо приваривают к корпусам машин либо соединяют с ними болтами. Защитному заземлению подлежат металлические корпуса электрических машин трансформаторов щиты шкафы.
Защитное заземление значительно снижает напряжение под которое может попасть человек. Это объясняется тем что проводники заземления сам заземлитель и земля имеют некоторое сопротивление. При повреждении изоляции ток замыкания протекает по корпусу электроустановки заземлителю и далее по земле к нейтрали трансформатора вызывая на их сопротивлении падение напряжения которое хотя и меньше 220 В но может быть ощутимо для человека. Для уменьшения этого напряжения необходимо принять меры к снижению сопротивления заземлителя относительно земли например увеличить количество искусственных заземлителей.
При замыкании одной из токоведущих крана выполненный из проводящего материала (металл) он оказывается под напряжением.
Прикосновение к корпусу крана человека (так называемое косвенное прикосновение) приводит к возникновению тока через него Iч который может привести к электротравме.
В целях электробезопасности необходимо проводящий корпус электроустановки заземлить т.е. выполнить электрическое соединение проводящих частей электроустановки (нормально не находящихся под напряжением) с проводящими частями находящимися в электрическом контакте с землёй и называемыми заземлителем.
Совокупность заземлителя и проводников соединяющих заземлитель с проводящим корпусом электроустановки называют заземляющим устройством.
Откуда видно что при электрическом соединение корпуса электроустановки с заземлителем Rзу происходит параллельное соединение сопротивлений человека Rч и заземлителя Rзy.
Тогда величина тока через человека составит:
где: Iз – ток замыкания на землю.
Если поставить условие Rзу « Rч то
т.е. защитное заземление уменьшает величину тока через человека в соотношение
раз. При отсутствии заземляющего устройства (Rзу = Iч = Iз.
А так как электрическое сопротивление человека принимается величиной постоянной равной 1000 Ом то необходимые условия электробезопасности (допустимый ток через человека Iчдоп) при установленном значении тока замыкания Iз могут быть достигнуты только при определенном значении Rзу.
Величина тока замыкания в общем случае определяется напряжением и схемой электрической сети к которой подключена электроустановка.
Характеристика воздействия на человека электрического тока различной силы
Переменный ток 50-60 Гц
Лёгкое дрожание пальцев рук
Сильное дрожание пальцев рук
Руки с трудом но ещё можно оторвать от электродов. Сильные боли в руках особенно в кистях и пальцах.
Руки парализуются оторвать их от электродов не возможно. Очень сильные боли. Затрудняется дыхание.
Ещё большее уселение нагревания незначительное сокращение мышц рук.
Паралич дыхания. Начало трепетания желудочков сердца.
Сильное ощущение нагревания. Сокращение мышц рук. Судороги. Затруднение дыхания.
Паралич дыхания и сердца при воздействии более 01с
На рисунке приведены результаты экспериментального исследования зависимости значений «опускающего» тока от индивидуальных качеств человека.
На рисунке графически представлена область предельно допустимых значений тока и длительность его протекания через человека с вероятностью 995 % не вызывающих фибрилляцию сердца (А – область недопустимых значений).
По Дальцилу граница областей допустимых значений тока через человека и длительности его протекания определяется выражением:
где: I – предельно допустимый ток через человека мА;
Т – длительность протекания тока через тело человека с.
Предельно допустимые уровни напряжений прикосновения.
Неощутимое напряжение В для t ≤ 10 мин
Отпускающее напряжение В t ≤ 30 c
Нефибрилляционное напряжение В t = 10 с
Предельная величина Uпр
Предельно допустимые уровни токов прикосновения.
Неощутимый ток мА t ≤ 10 мин
Отпускающий ток А t ≤ 30 c
Нефибрилляционный ток А t = 10 с
Главным средством для обеспечения безопасности обслуживании стенда обкатки редуктора является заземление.
Предполагается сооружение заземлителя с внешней стороны участка с расположением вертикальных электродов в один ряд длиной 20 м; материал - круглая сталь диаметром 20 мм метод погружения - ввертывание; верхние концы вертикальных стержней погруженные на глубину 07 м приварены к горизонтальному электроду из той же стали.
Требуемое сопротивление заземления:
1.1.Техника безопасности при обслуживании склада
Т.к. на складах основной опасностью для работников является транспорт который перемещается внутри склада т.е. электропогрузчики.
Все операции связанные с техническим обслуживанием устранением неисправностей очисткой двигателя и машины q.t грязи и подготовкой машины к работе выполняют при остановленном двигателе.
Работы ведут в соответствии с паспортом и инструкцией по эксплуатации завода-изготовителя. Запрещается выполнять операции не соответствующие назначению и технической характеристике сменного рабочего оборудования.
Работа погрузчика допускается только на освещенных площадках и внутриобъектных дорогах с твердым и ровным покрытием с уклоном не более 5°. Запрещается работать на захламленных имеющих выбоины и рытвины площадках. Зимой площадки и дороги должны быть очищены от снега и льда и посыпаны песком золой или шлаком.
Контейнеры поддоны и штучные грузы допускается штабелировать на площадках с уклоном не более 1°. Запрещается работать с неисправными контейнерами поддонами и другими пакетирующими приспособлениями.
Строповочные приспособления ежедневно осматривают и проверяют соответствуют ли они нормативным документам. Не допускается работа с приспособлениями имеющими дефекты.
Груз поднимают при отклоненном назад грузоподъемнике и за торможенном погрузчике. Груз распределяют равномерно по ширине вил а при работе со стрелой — по продольной оси машины. Запрещается поднимать груз масса которого превышает норму указанную в технической характеристике а также примерзший или защемленный какими-нибудь предметами. Если груз выходит за габариты вилочный подхватов его закрепляют.
При движении погрузчика запрещается поднимать или опускать груз менять наклон грузоподъемника. Груз закрывающие обзор пути движения перевозят в сопровождении помощника который следит за дорогой. Запрещается на погрузчике перевозить людей.
На автомобильные дороги общего назначения погрузчики выезжай в исключительных случаях соблюдая при этом Правила дорожного движения. При езде по дороге ночью погрузчик должен быть оснащен средствами световой сигнализации и освещения.
После окончания работы и при длительных перерывах в работе грузоподъемник с грузом опускают в крайнее нижнее положение.
При проведении технического обслуживания и ремонта соблюдают следующие правила техники обслуживания и ремонта. Запрещается находиться под погрузчиком и под грузоподъемником при работающем двигателе.
Все работники должны соблюдать технику безопасности складского хозяйства стеллажного хранения груза:
работники должны ходить по тому маршруту в котором указан в маршрутной карте;
запрещается находиться под стеллажами и в межстеллажном пространстве если не связанно с его обязанностью.
запрещается находиться в местах работающего крана-штабелера т.к. это может привести к травматизму.
2.Безопасность персонала в чрезвычайных ситуациях
2.1.Пожарная безопасность на складах.
Организация работ по пожарной безопасности должна включать:
разработку и внедрение системы управления пожарной безопасностью согласно требованиям руководящих документов;
общее руководство и контроль за состоянием пожарной безопасности на предприятии контроль за соблюдением законодательных и иных нормативных правовых актов требований правил и инструкций по пожарной безопасности. Контроль за выполнением служебных обязанностей подчиненными;
обеспечение пожарной безопасности при проведении технологических процессов эксплуатации оборудовании производстве пожароопасных работ;
установка и контроль за состоянием средств контроля оповещения и пожаротушения;
организацию разработки и обеспечение выделения финансовых средств на реализацию мероприятий по обеспечению пожарной безопасности;
проведение обучения и инструктажа работников предприятия по пожарной безопасности;
обеспечение электробезопасности предприятия.
Установка и контроль за состоянием средств контроля оповещения и пожаротушения.
Обучение по пожарной безопасности специалистов служащих и рабочих включает:
- проведение вводного первичного повторного внепланового и целевого инструктажей;
- организация занятий по пожарно-техническому минимуму;
- проведение учений и противопожарных тренировок.
Система пожарной сигнализации склада выполняет задачу обнаружения места возгорания и оповещения об этом соответствующих служб. Кроме того она должная быть связана с системами автоматического пожаротушения и дымоудаления которые локализуют очаги возгорания ещё до приезда пожарных служб. Установка на складе охранной и пожарной сигнализации значительно повышает безопасность склада и материальных ценностей а также обеспечивает своевременное оповещение пожарных служб.
Система охранной сигнализации - одна из составляющих комплексной системы безопасности склада представляет собой совокупность совместно действующих технических средств охранной сигнализации устанавливаемых на охраняемом объекте и объединенных системой инженерных сетей и коммуникаций. Системы охранной сигнализации не зависят от человеческого фактора и своевременно оповещают службы охраны о проникновении или попытке проникновения на склад с фиксацией факта места и времени нарушения рубежа охраны.
Последние две системы безопасности для складов можно объединить в одну что и предлагают многие российские и зарубежные производители оборудования. Современная охранно-пожарная сигнализация (ОПС) склада - представляет собой комплекс оборудования обеспечивающего пожарную безопасность склада и своевременное обнаружение проникновения в охраняемую зону а также оповещение о месте возникновения пожара на объекте.
Установки пожарной автоматики (УПА) занимают ведущее место в обеспечении пожарной безопасности различных объектов включая производственные складские административные здания и подвижной состав железнодорожного транспорта.
Действующие сегодня законодательные и иные нормативные правовые акты по пожарной Согласно ГОСТ 12.1.004-91 "Пожарная безопасность. Общие требования" противопожарная защита должна достигаться в первую очередь применением автоматических установок пожарной сигнализации и пожаротушения.
Широкое внедрение средств пожарной автоматики позволят значительно сократить количество крупных пожаров и ущерб от них.
В целом по стране число пожаров и ущерб от них на объектах оборудованных УПА соответственно в 30 и 40 раза меньше в сравнениями с показателями пожаров на объектах на которых средства пожарной автоматики отсутствуют.
Очень важную роль в предотвращении пожаров и обнаружении очага возгорания играет своевременная информация о месте возникновения пожара. Для этой цели служит автоматическая пожарная сигнализация. Системы пожарной сигнализации включают в себя пожарные извещатели линейные сооружения линии связи и приемные пульты станций.
Рассмотрим виды пожарных извещателей:
Тепловые извещатели реагируют на изменение температуры в помещении. Выпускаются тепловые извещатели максимальной температуры и максимально-дифференциальные. Детекторы максимальной температуры имеют некоторый фиксированный порог и срабатывают; когда температура окружающей среды в помещении достигнет порогового значения. Максимально- дифференциальные извещатели реагируют не только на величину температуры но и на скорость ее нарастания т.е. на производную температуры по времени. Отсюда и их название. В большинстве случаев максимально-дифференциальные извещатели раньше обнаруживают возгорание чем детекторы максимальной температуры.
Площадь контролируемая одним точечным тепловым пожарным извещателем а также максимальное расстояние между извещателями извещателем и стеной необходимо определять по таблице 8 но не превышая величин указанных в технических условиях и паспортах на извещатели.
Наиболее распространены оптические дымовые извещатели. Их принцип действия заключается в следующем. В дымовой камере под углом 120 градусов установлены излучатель и фотоприемник. Конструкция камеры выполнена таким образом что в дежурном режиме ИК-излучение от светодиода не попадает на фотоприемник. При поступлении дыма в камеру его частицы рассеивают ИК-излучение и оно достигает фотоприемника. При определенной концентрации дыма и следовательно достаточном количестве отраженного излучения происходит срабатывание извещателя.
Площадь контролируемая одним точечным дымовым пожарным извещателем а также максимальное расстояние между извещателями извещателем и стеной за исключением случаев оговоренных в п. 12.20 необходимо определять по таблице 5 но не превышая величин указанных в технических условиях и паспортах на извещатели.
Ручные извещатели являются обязательным компонентом любой системы пожарной сигнализации. Их назначение - подача сигнала о пожаре при его обнаружении персоналом здания. Ручные пожарные извещатели устанавливают на стенах и конструкциях на высоте 15 м от уровня пола или земли. Максимальное расстояние между двумя ближайшими ручными извещателями внутри помещений – не более 50 м а вне помещения – 150 м; ввод проводов в корпус извещателя – трубный. В случае неисправности на извещатель следует повесить табличку с соответствующей надписью.
Выносная сигнализация пожарной безопасности складов служит для подачи сигнала тревоги и выполняется в соответствии с требованиями НПБ 104-2003 «Системы оповещения и управления эвакуацией людей при пожарах в зданиях и сооружениях». В качестве прибора оптической сигнализации пожарной безопасности складов используются лампы накаливания мощностью 25 Вт для защиты которых служит светосигнальная арматура со стеклянным плафоном окрашенным в красный цвет защищенная металлической сеткой. Система сигнализации пожарной безопасности складов монтируется с помощью арматуры установленной с фасадной стороны здания на высоте не менее 275 м от земли и крепится к стене здания или на металлическом кронштейне. В качестве арматуры допускается использовать светильники типа НПП05 ПСХ НСП (исполнение полностью пылезащищенное).
В качестве акустического сигнализатора пожарной безопасности складов применяют сирены ревуны звонки мощностью до 20 Вт. Приборы звуковой сигнализации устанавливают на наружной стене здания с фасадной стороны на высоте 275 м от земли и выполняются в металлическом корпусе.
Инструкция по противопожарной защите высотного стеллажного склада
I. Следует использовать автоматическую систему пожарной сигнализации
с применением датчиков реагирующих на присутствие газов и дымов (например ионных датчиков) или иных устройств которые при возникновении пожара обеспечивают оповещение пожарных служб на предприятии или в населенном пункте. Датчики следует размещать в горизонтальных плоскостях на расстоянии около 8 м друг от друга. Такая их расстановка не оказывает принципиального влияния на решение строительной части здания.
В крыше здания должны быть предусмотрены отверстия для отвода
газов дыма и горячего воздуха. Эти отверстия должны быть оборудованы клапанами с автоматическим открыванием. Отверстия должны занимать
—5% поверхности крыши (поскольку наличие дыма и газов затрудняет
операцию тушения и. кроме того может быть причиной взрыва).
На расстоянии не более 50 м друг от друга следует предусмотреть
устройство поперечных (относительно пролетов) переходов через весь склад.
Такие переходы должны иметь ширину не менее 0.8 м и высоту не менее
9 м В железобетонных складах эти переходы должны быть снабжены
противопожарными дверями имеющими такую же огнестойкость что и сте-
на. разделяющая отдельные камеры. В каждом переходе следует разместить
два гидранта со шлангами и брандспойтами. подача воды к которым осуществляется из двух независимых источников.
Следует предусмотреть необходимую систему аварийных выходов и
лестниц оборудованную соответствующими указателями и аварийным освещением. Эти коммуникационные пути должны быть всегда доступными.
1.Выводы: в данном разделе был проведен расчет заземления крана-штабелера выбраны средства заземления предложено определенное количество стержней заземления для хорошего отведения тока а так же рассмотрена техника безопасности при пожаре приведена инструкция по противопожарной защите высотного стеллажного склада.
Практическое обеспечение безопасности жизнедеятельности при проведении технологических процессов и эксплуатации технических систем во многом определяется решениями и действиями инженеров и техников. Руководитель производственного процесса обязан:
-обеспечивать оптимальные (допустимые) условия деятельности на рабочих местах подчиненных ему сотрудников;
-идентифицировать травмирующие и вредные факторы сопутствующие реализации производственного процесса;
-обеспечивать применение и правильную эксплуатацию средств защиты работающих и окружающей среды;
-постоянно (периодически) осуществлять контроль условий деятельности уровня воздействия травмирующих и вредных факторов на работающих;
-организовывать инструктаж или обучение работающих безопасным приемам деятельности;
-лично соблюдать правила безопасности и контролировать их соблюдение подчиненными;
-при возникновении аварий организовывать спасение людей локализацию огня воздействия электрического тока химических и других опасных воздействий.
В данном дипломном проекте был выполнен анализ существующих конструкций стеллажных кранов-штабелеров. Были отмечены их недостатки и были предложены варианты усовершенствования их конструкции.
Была разработана конструкция одноколонного стеллажного крана-штабелера с гидравлическим приводом телескопического захвата. Произведена разработка отдельных узлов с соответствующими расчетами.
Выполнена разработка организации работ с применением стеллажного крана-штабелера.
Так же был разработан технологический процесс изготовления штока гидравлического буфера. Были применены в ходе разработки технологического процесса основные принципы и приемы изготовления штока.
Внедрение и использование в стеллажном кране-штабелере гидравлического привода захвата а также были заменены приводы передвижения и подъема которые позволяют получить экономический эффект что и было доказано в экономической части.
Также были рассмотрены вопросы техники безопасности при использовании стеллажных кранов-штабелеров. Затронута тема пожарной безопасности.
Список используемой литературы
Зерцалов А.И. Певзнер Б.И. Бененсон И.И. Краны-штабелеры. – М.: Машиностроение 1986. – 320 с. ил.
Анурьев В.И. Справочник конструктора- машиностроителя – М.: Машиностроение 1988. – 557 с.
Свешников В.К. Усов А.А. Станочные гидроприводы – М.: Машиностроение 1988. – 510 с.
Жуков В. И. Федосов В. Д. Пономарев В. М. Автоматические средства пожарной безопасности на железнодорожном транспорте: Методические указания. – М: МИИТ. 2010. – 186 с
Юдин Е.Я. Охрана труда в машиностроении – М.: Машиностроение 1983. – 423 с.
Руденко Н.Ф. Александров М.П. Лысяков А.Г. Курсовое проектирование грузоподъемных машин – М.: Машиностроение 1971. – 457 с.
Маликов О.Б. Проектирование автоматизированных складов штучных грузов. Л.: Машиностроение 1981. – 240 с.
Смехов А.А. Автоматизированные склады. 3-е изд. М.: Машиностроение 1979. – 288 с.
Аверкин В.А. Зиновен Н.А.Задание и методические указания к курсовой работе по дисциплине «Экономика производства» М. МИИТ 2000г.
Дунаев П.Ф. Леликов О.П. Конструирование узлов и деталей машин М. “Высшая школа” 1985г.
Справочник технолога-машиностроителя: 4-е издание в 2-х т. под ред. Косиловой А.Г. Мещерякова Р.К. -М. “Машиностроение” 1985.
Краткий справочник металлиста 3-е издание под ред. Орлова П.Н. Скороходова Е.А. -М.: «Машиностроение» 1987.
Проектирование технологических процессов изготовления деталей подъёмно-транспортных строительных и дорожных машин. 2-я часть В.И. Фомин – М: «МИИТ» 2009.
Первый лист.docx
Графическое приложение на 9 листах.
Организация.docx
По причине высокой производительности высотный стеллажный склад (особенно с автоматизированным управлением) требует очень четкой организации. В таком складе каждая операция каждое прохождение груза пли документа работа каждой машины и каждое рабочее место человека должны быть тщательно описаны проанализированы и учтены в общем балансе работы системы. Многие функции склада особенно периферийных его частей (в отличие от стеллажной складской части) являются спонтанными например подвоз грузов по железной дороге. Поэтому к проекту организации работ предъявляются необычайно высокие требования.
Основной задачей при проектировании организации работ в складе является обеспечение стабилизации стеллажной структуры — самого дорогостоящего элемента в системе склада — и обеспечение непрерывной работы этой структуры с максимальной производительностью на протяжении смены или суток. Такой принцип позволяет ограничить до минимума расходы на стеллажную часть склада и обеспечивают быструю амортизацию.
Приведенные требования к проекту организации работ вызывают радикальное изменение прежнего понятия «проекта организации работ» который на практике обычно складывался из описания операций определения количества рабочей силы и схемы зависимостей между отдельными звеньями управления складом.
Проект организации работ высотного стеллажного склада должен на основе количественного анализа складского процесса давать инструкции по обслуживанию прохождения грузов и информации (документов) в любой момент прохождения (пиковый или средний) в тесной связи с окружением («вход» и «выход») и расчетом необходимых для обеспечения заданной производительности средств (люди и машины). В этом проекте на основе анализа различных случает должны быть также приведены инструкции по осуществлению операций и необходимые средства на случай аварии отдельных элементов этой сложной системы.
В традиционном проекте организация работ в высотном стеллажном складе разрабатывается на заключительной стадии проектирования но в получаемом результате содержатся все прежние технические и технологические решения.
В современных складских системах ориентированных на функции и связи организационные проблемы в одинаковой степени влияют как на технические так и на технологические решения. По этой причине проект организации работ следует начинать уже на стадии разработки концепции и продолжать вместе со всеми последующими стадиями проектирования. Установление четкой границы между организацией и так называемой технологией складирования является весьма затруднительным. Здесь отсутствуют какие-либо нормативные указания. Поэтому в настоящей работе принят следующий ход рассуждений.
Для установленного процесса складирования обусловленного функцией склада подбираются технические средства и проектируется организация обеспечивающая осуществление этого процесса с определенной производительностью. Складские процессы вместе с техническими средствами определяют ту или иную технологию складирования. Проект организации работ рассматривает эту технологию в количественных категориях с учетом производительности людей и машин а также определяет способ
Управления прохождением грузов и информации во всей системе. Достигнутое в проекте организации соответствие заданной и найденной производительности замыкает цикл проектирования склада в то время как в случае несоответствия этих показателей требуется либо вносить изменения в технологию либо возвращаться к предшествующим стадиям проектирования.
Определим количество средств механизации погрузочно-разгрузочных работ требуемых для перерабатывания однотипного пакетного груза на складе МЧ железной дороги .
Масса груза (пакета) – 1 т
Емкость склада – 1200 т
Срок хранения – 10 сут.
Груз расположен на стандартном поддоне мм –
Высота груза с поддоном – 1350 мм
Определим суточный грузооборот склада:
- коэффициент неравномерности прибытия отправления груза
Определим суточный грузооборот в пакетах:
Определим среднюю загрузку вагона:
Vв – внутренний объем крытого вагона м3
kу = 085-09 – коэффициент учитывающий плотность укладки
Vп – объем одного пакета м3
Внутренний объем крытого вагона выбираем
Для перевозки тарно-штучных грузов принимаем крытый четырехосный вагон грузоподъемностью 65 т.
В вагоне умещается 83 пакета по объему но учитывая тот факт что грузоподъемность вагона составляет 65 т а масса одного пакета 1 т то принимаем количество пакетов в вагоне равным 65 шт.
Определим число железнодорожных вагонов (суточный вагонопоток) в которых поступает груз:
Т.к. в вагон вмещается 65 пакетов следовательно в два вагона вмещается 130 пакетов а оставшиеся 14 пакетов отправим автотранспортом.
Определим число вагонов в одной подаче:
z – число подач вагонов на грузовой пункт за сутки ( z = 2 5 ) z = 1
Вычислим необходимое количество поддонов на складе:
- коэффициент учитывающий время нахождения поддонов в ремонте
- время оборота поддонов (время перевозки и хранения груза на складе).
Определим количество автотранспорта:
Tц – продолжительность транспортного цикла автомобиля
- дальность перевозки км (для внутригородских поставок )
- среднетехническая скорость автомобиля
- коэффициент пробега автомашины
Tпр = 01 – время простоя под грузовыми операциями
qа = 5 т – фактическая загрузка автомобиля
T = 8 ч – количество рабочих часов автомобиля в сутки
kt = 07 – коэффициент использования автомобиля по времени
Длина фронта подачи вагонов:
lв – длина ж.д. вагона по автосцепке l = 1473 м
aм – удлинение фронта подачи вагонов для выполнения маневровых работ aм = (15 2)
Длина фронта погрузки-выгрузки:
zс – число смен (перестановок) вагонов на грузовом фронте (zс = 1 2)
При установке автомобиля к рампе склада торцом:
k – число погрузочно-разгрузочных постов образующих фронт погрузки выгрузки (равно числу дверных проемов со стороны автотранспорта); k = 2
bа = габаритная ширина автомобиля м; bа = 25 м
Sт – расстояние между смежными автомобилями обеспечивающее выезд автомобиля при торцевой расстановке м; Sт = 1 м
Вместимость склада с учетом хранения
Определим общее количество порожних поддонов.
На складе 1440 поддонов загружены а 10% - порожние поддоны.
Определим количество пачек.
В одной пачке сложено 10 поддонов следовательно:
Определим геометрические размеры элементарной площадки под поддоны:
– длина элементарной площадки
– ширина элементарной площадки
– площадь элементарной площадки
Вместимость одного стеллажа
Zl Zh – количество ячеек по длине и ширине (Zl = 15 Zh = 8)
Определим количество стеллажей
Определим размеры стеллажа
Т.к. максимальный размер пакета составляет 1200 мм то длина ячейки Az = 1500 мм ширина ячейки Bz = 900 мм; высота пакета с поддоном составляет 1350 мм то высота ячейки Hz = 1500 мм.
Определим площадь площадки занятой стеллажами
r = 1000 мм – ширина проезда между стеллажами
nпр = 6 – количество проездов между стеллажами
Высота склада – 128 м
Ширина склада – 32 м
Высота рампы для ж.д. вагонов – 125 м
Высота рампы для автомобилей – 125 м
Ширина погрузочно-разгрузочной платформы для обслуживания ж.д. подвижного состава и автомобилей – 4 м
Расстояние от края платформы до оси ж.д. пути – 165 м
Расстояние от оси пути ж.д. пути до стены склада – 566 м
Размеры одного стеллажа м (Д х Ш х В) – 225 х 09 х 12
Расстояние между стеллажами – 1 м
Количество стеллажей – 12 шт
Выбор типа и количества погрузочно-разгрузочных машин
Электропогрузчик грузоподъемностью 1 т.
Технические характеристики электоропогрузчика:
Грузоподъемность – 1 т
Высота подъема груза – 2 м
Скорость подъема вил:
Скорость опускания вил:
Наибольшая скорость передвижения:
Дорожный просвет – 100 мм
Внешний радиус поворота – 1600 мм
Наименьшая ширина проездов под углом 90 - 2950 мм
Техническая производительность машин используемых при переработке тарно-штучных грузов находиться по формуле:
Gм – грузоподъемность машины т
Tц – продолжительность времени цикла с
Для погрузчика время цикла:
tдв t’дв – время затрачиваемое погрузчиком на продольные и поперечные передвижения по складу с грузом и без груза с
tпод t’под – время затрачиваемое на подъем каретки погрузчика с грузом и без груза с
tоп t'оп – время затрачиваемое на опускание каретки с грузом и без груза с
tпов – время затрачиваемое на повороты погрузчика с
tвсп – время затрачиваемое на вспомогательные операции
l – длина рабочего плеча м
v – скорость движения погрузчика мс
a – ускорение погрузчика мс2
Средняя высота подъема:
H – высота подъема груза погрузчиком
Определение эксплуатационной и сменной производительности
Эксплуатационная производительность погрузчика:
kв = 08 – коэффициент использования по времени
Сменная производительность:
Объем механизированной переработки груза:
mсм = 1 – количество смен
Tр – время нахождения машины в ремонте и смены батареи в течение года
Принимаем Мм = 2 машину с учетом одновременной разгрузки-погрузки автомобиля и одной ж.д. подачи.
Определение производительности крана-штабелера на складе базового варианта
Техническую производительность крана-штабелера в базовом варианте определим по формуле:
Gгр = 1000 кг – вес пакета
C – число циклов которое машина делает за 1 час
tц – время цикла сек
lp = 1185 м– средняя длина перемещения крана-штабелера
lv = 1 м – длина выдвижения грузозахватного органа
lk = 5 м – средняя высота подъема пакета
vp = 1 мс – скорость передвижения крана
vv = 025 мс – скорость выдвижения грузозахватного органа
vk = 1 мс – скорость подъема грузозахватного органа
Эксплуатационная и сменная производительность:
kв = 09 – коэффициент использования крана по времени
Определение производительности крана-штабелера на складе нового варианта
vp = 25 мс – скорость передвижения крана
vk = 2 мс – скорость подъема грузозахватного органа
Эксплуатационная производительность:
В результате анализируя полученные результаты можно сделать вывод о том что склад с новым вариантом крана-штабелера более предпочтителен с точки зрения производительности перед складом с базовым вариантом крана-штабелера так как эксплуатационная производительность нового крана-штабелера больше чем у базового крана-штабелера.
Определение количество кранов-штабелеров на складе
Т. к. на складе имеется 12 стеллажей: 2 стеллажа расположены раздельно (по краям склада) а 10 стеллажей расположены по парно т.е. пять пар стеллажей между стеллажами имеются проезды для кранов-штабелеров.
Для обслуживания 12 стеллажей требуется 6 кранов-штабелеров.
Общий вид.cdw

Режим работы по ГОСТ 25546-82
Габариты перерабатываемого груза
Высота выдвигаемых элементов
грузозахватного органа
Величина выдвижения грузозахватного
Скорость передвижения крана
Скорость подъема грузозахватного
Скорость выдвижения грзозахватного
Суммарная мощность двигателей
двутавр 12 ГОСТ 8239-72
Подвод электропитания
Климатическое исполнение
Класс пожароопасности
Разработка автоматизированного
склада для пакетированных грузов
не ограниченные допусками
Отклонение колонны крана штабелера от вертикали (по
направляющим для перемещения грузоподъемника) не более 5 мм
Негоризонтальность опорных поверхностей телескопических
захватов не более 2:1000
Неперпендикулярность осей телескопических захватов к
продолной оси межстеллажного прохода не более 2:1000
Суммарные зазоры между направляющими и контактами (оголовка
Зазоры отрегулировать при помощи прокладок (оголовок
тележка. боковые катки грузоподъемника) в соответствии с
указаниями руководства по эксплуатации
Смазку механизмов произвести в соответствии с указаниями
рукаводства по эксплуатации
Остальные технические требования по ТУ 24 09 636-86
Грузоподъемник.spw

Мотор-редуктор (подъем).frw

Оголовок.spw

Болт М12 ГОСТ 7798-70
Гайка М30 ГОСТ 11871-80
Шайба 30 ГОСТ 11872-80
Шайба 10 ГОСТ 13463-77
Шайба 12 ГОСТ 13463-77
Кольцо ГОСТ 13943-68
Масленка ГОСТ 19853-74
Оголовок.cdw

склада для пакетированных грузов
*Размеры для справок
Подшипники заполнить смазкой литол 24 ГОСТ 21150-75
План склада.cdw

Технические характеристики
Количество стеллажей
Количество кранов-штабелеров
Количество погрузчиков
Организация складских
Разработка автоматизированного
склада для пакетированных грузов
Буфер гидравлический.cdw

склада для пакетированных грузов
*Размеры для справок
При сборке проверить отверстия в цилиндре поз. 5 и их
положение относительно корпуса поз. 5
Залить масло АМГ 10 ГОСТ 6794-75. Уровень масла в бачке
должен находиться в пределах рисок маслоуказателя
Прокачку воздуха из полости цилиндров буфера производить при
снятом маслоуказателе
Кольцо поз. 22 пропитать маслом МВП ГОСТ 1805-76 резиновые
уплотнения смазать смазкой солидол Ж-ЖСКА 216-2 ГОСТ 1033-79
Деталь поз. 15 приклеить клеем 88НП ТУ 38-105540-73
Маркировать исполнение сборки
БЖД.cdw

Габариты перерабатываемого груза
Высота выдвигаемых элементов грузозахватного органа
Величина выдвижения грузозахватного органа
Скорость передвижения крана
Скорость подъема грузозахватного органа
Скорость выдвижения грузозахватного органа
Техническая производительность
Суммарная мощность двигателей
двутавр 12 ГОСТ 8239-72
Подвод электропитания
Климатическое исполнение
Класс пожароопасности
Схемы распределения коэффициента естественной
освещенности е по разрезу помещения:
Точечный метод расчета искусственного освещения
Ег=I*cos3бН 2 *К3 - для горизонтальной плоскости
Ев= I*cos3 (90-б) Н 2 *К3 - для вертикальной плоскости
Расчет искусственного освещения методом удельных мощностей
Расчет искусственного освещения для ламп типов ДРЛ
Расчет искусственного освещения для люминесцентных ламп:
F=( E*S*z*Kз)(n*Фл*
Результаты исследования зависимости значений "отпускающего
тока от индивидуальных качеств человека.
- группа из 28 женщин - среднее значение тока 10
-группа из 134 мужчин - среднее значение тока 16 мА
Предельно допустимый ток через
Предельно допустимые уровни
напряжений прикосновения
Расстояние от извещателя
Характеристика пожарных
Область предельно допустимых значений тока и длительность его протекания
% не вызывающих фибрилляцию сердца
(А - область недопустимых значений)
Характеристика воздействия на
человека электрического тока
Разработка автоматизированного
склада для пакетированных грузов
Безопасность персонала
автоматизированного склада
ТДМ-544.00.00.00 БЖД
Техническакя характеристика крана-штабелера
8 10 12 14 16 18 20 22 24 I
Величина тока через тело человека
Требуемое сопротивление заземления
Принципиальная схема заземления
Типы пожарных извещателей
Параметры теплового извещателя
Параметры дымового извещателя
Тележка.spw

Болт М12 ГОСТ 7798-70
Шайба 12 ГОСТ 7798-70
Болт М16 ГОСТ 7805-70
Гайка М16 ГОСТ 5927-70
Винт М8 ГОСТ 1491-80
Шайба 8 ГОСТ 6402-70
Шайба 8 ГОСТ 11371-78
Болт М10 ГОСТ 7798-70
Болт М16 ГОСТ 7798-70
Общий вид.spw

Выключатель конечный
Установка считывателя
Устройство управления
Грузоподъемник.cdw

склада для пакетированных грузов
* Размеры для справок
Допуск перпендикулярности поверхности Я при полностью
выдвинутой платформы захвата относительно вертикальной оси И
грузоподъемника не более 5 мм
Допуск симметричности расположения направляющих катков
относительно вертикальной оси грузоподъемника не более 5 мм
Телескопический захват испытать при работе от привода с
номинальным грузом в течении 30 мин с реверсированием
направления движения платформы
Допустимый уровень звукового давления 60 дБ
Неточность останова платформы телескопического захвата
отдействия конечных выключателей в нейтральном и крайних
Срабатывание устройства занятости ячейки должно
происходить при установке препятствия на пути перемещения
платформы захвата на расстоянии не менее 150 мм от исходного
На поверхности В1 и В2 нанести полосы эмаль НЦ-132П черная
Смазку механизмов производить в соответствии с указаниями в
руководстве по эксплуатации
Тележка.cdw

При сборке подшипника поз. 15 и 26 заполнить смазкой литол 24
Тормоз отрегулировать на М
Привод обкатать в течении 30 мин с реверсированием через
Экономика.cdw

Грузоподъемность крана-штабелера
Масса перерабатываемого груза
Средняя высота подъема
Скорость передвижения крана
Скорость подъема грузозахватного органа
Скорость выдвижения грузозахватного органа
Техническая производительность
Количество обслуживающего персо
Сравнительная технико-экономическая характеристика базового и нового варианта
Приращение доходов и расходов:
- экономия заработной платы
- отчисления на социальные нужды
-расходы по содержанию и эксплуатации оборудования
-расходы на электроэнергию
- приращение доходов
Корректировка денежных потоков:
Чистые денежные потоки
ЧДП - чистый денежный поток;
HR - барьерная ставка;
n - число лет функционирования проекта
Разработка автоматизированного
склада для пакетированных грузов
Экономическая эффективность
модернизации крана-штабелера
Экономическая эффективность модернизации крана-штабелера
Расчет чистых денежных потоков
Зависимость чистой текущей стоимомти (NPV) от ставки дисконтирования (HR)
Мотор-редуктор (передвижение).frw

Сечение.frw

Гидробуфер.spw

Гайка М18 ГОСТ 5916-70
Манжета ГОСТ 6969-54
Шайба 8 ГОСТ 6402-70
Шайба 18 ГОСТ 10450-78
План склада.spw

Роликовый конвейер приемный
Роликовый конвейер выдающий
Технология.cdw

Сверлить центровое отверстие
*- размеры для справок.
Общие допуски по ГОСТ 30893
Переустановить заготовку.
Подрезать торец справа с соблюдением
Точить начерно в размер 1 на длине 6
Точить начерно в размер 2 на длине 5
Точить начерно в размер 3 на длине 4
Точить начерно в размер 1 на проход.
Точить получисто в размер 7 обеспечивая
размер 8 с образованием галтели 9
Шлифовать окончательно
в размер 1 на длине 2.
Сталь 40Х ГОСТ 1050-88
Общие допуски по ГОСТ 30893.1; Н14
в размер 2 на длине 3.
в размер 1 на длине 4.
Точить получисто в размер 3 обеспечивая
Точить канивку по размерам 9
Точить получисто в размер 2 обеспечивая
размер 12 с образованием галтели 6
Точить получисто в размер 1 обеспечивая
размер 8 с образованием галтели 7
Центровое отверстие B6
Разработка автоматизированного
склада для пакетированных грузов
Операционные эскизы на токарную и шлифовальную обработку штока гидробуфера
5 Токарная операция: торцевание заготовки
5 Токарная операция: черновое обтачивание
5 Токарная операция: получистовое обтачивание
0 Шлифовальная операция: предворительное
окончательное шлифование
Рекомендуемые чертежи
- 24.01.2023
- 25.01.2023