Расчёт и назначение посадок




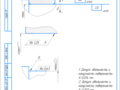
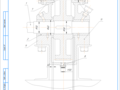
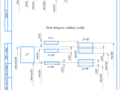
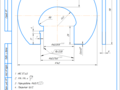
- Добавлен: 24.01.2023
- Размер: 974 KB
- Закачек: 0
Описание
Состав проекта
![]() |
![]() |
![]() ![]() ![]() ![]() |
![]() ![]() ![]() ![]() |
![]() ![]() ![]() |
![]() ![]() ![]() ![]() |
![]() |
![]() ![]() ![]() ![]() |
![]() |
![]() |
![]() |
![]() ![]() ![]() ![]() |
![]() |
![]() ![]() ![]() |
![]() |
![]() ![]() ![]() |
![]() ![]() ![]() ![]() |
![]() ![]() ![]() |
![]() ![]() ![]() ![]() |
![]() |
![]() ![]() ![]() ![]() |
![]() |
![]() ![]() ![]() ![]() |
![]() |
![]() ![]() ![]() ![]() |
![]() ![]() ![]() ![]() |
![]() |
![]() ![]() ![]() ![]() |
![]() |
Дополнительная информация
Подшипник.cdw

Поля допусков резьбового соединения(А3).cdw

натяг.frw

Чертеж 1.cdw

скоба для 2 детали.cdw

резьб соединение.frw

Пояснительная записка 11111.doc
к курсовой работе по курсу
Метрология стандартизация и сертификация
Вариант № 4 Группа: 5ТМ-39
Головачёв С.Ю. Трехгорный: ТТИ НИЯУ МИФИ ТМ 2010 15 л. Библиография литературы – 5 наименований 4 листа формата А4 4 листа формата А3.
В данной курсовой работе произведено назначение посадок для сопрягаемых поверхностей в зависимости от их служебного назначения. Так же произведен расчет соединения с натягом и по данным расчета выбрана посадка с натягом. Произведен расчет одного подшипника и по рекомендациям выбраны посадки для внутреннего и наружного колец подшипника для него построили схему полей допусков.
Так же в курсовой работе построены поля допусков расположения резьбового соединения. Произведены расчеты резьбового калибра-кольца и калибра-пробки по назначенным посадкам. В курсовой работе произведен расчет заданной размерной цепи по методу одного квалитета.
Назначение посадок для всех сопрягаемых деталей 5
Расчет посадки с натягом для соединения 2-9 6
Назначение и расчет подшипника качения 4 7
Расчет исполнительных размеров калибров для соединения 2-9 9
Определяем рабочий калибр для детали 2
Определяем рабочий калибр для детали 9
Расчет рабочих калибров для резьбовой детали 9 соединения 8-9 10
Расчет рабочего калибра-кольца для наружной резьбы детали 8
Расчет рабочего калибра-пробки для внутренней резьбы детали 9
Расчет размерной цепи А 12
Схемы контроля технических требований к детали 6 14
Библиографический список 15
Графическая часть на 4 листах формата А4 4 листах формата А3
Назначение посадок для всех сопрягаемых соединений
- посадка с зазором («скользящая») применяется для подвижных соединений.
– посадка с натягом («прессовая тяжелая») предназначены для соединений на которые воздействуют тяжелые в том числе динамические нагрузки.
- посадка с натягом («прессовая средняя») предназначены для передач в которых применение посадок с большим натягом недопустимо по условиям прочности деталей.
- посадка с зазором. Посадка для наружного кольца подшипника (по расчетам).
– посадка с натягом. Посадка для внутреннего кольца подшипника (по расчетам).
- переходная посадка предназначена для установки втулок в корпуса.
- посадка с зазором. Предпочтительная посадка для среднего класса точности.
Расчет посадки с натягом для соединения 2-9.
Расчетная схема посадки с натягом приведена на рис. 1.
Рисунок 1 – схема посадки с натягом
Расчет посадки с натягом выполняем с целью обеспечения прочности соединения то есть отсутствие смещений сопрягаемых деталей под действием внешних нагрузок и прочности сопрягаемых деталей.
Исходные данные для расчета: внутренний диаметр охватываемой детали 2 d1 = 50 мм наружный диаметр охватываемой и внутренний диаметр охватывающей деталей d = 60 мм наружный диаметр охватывающей детали 9 d2 = 120 мм длина сопрягаемых поверхностей деталей 2-9 L = 50 мм крутящий момент МКР = 500 Н×м.
Материал детали 2 БрОф10-1 с пределом текучести т1= 20·107Нм2 модуль упругости
Е1 = 09·1011 Нм2 коэффициент Пуассона 1=033. Материал детали 9 Сталь 45Л с пределом текучести Нм2 модуль упругости Е1 = 21·1011 Нм2 коэффициент Пуассона коэффициент трения f = 02.
Исходные данные для расчета:
Rad – шероховатость детали 2 RaB=032;
RaD – шероховатость детали 9 RaA=063;
Ad – коэффициент линейного расширения детали 2 Ad=11×10-6 град-1;
AD – коэффициент линейного расширения детали 9 AD=176×10-6 град-1;
Td – рабочая температура детали 2 Td=20°С;
TD – рабочая температура детали 9 TD=20°С;
Gd – предел текучести детали 2 Gd=18·107 Нм2;
GD – предел текучести детали 9 GD=20·107 Нм2;
По дополнительным условиям
определяем посадку 60
Назначение и расчет посадки подшипника качения
Схема расположения полей допусков показана на рисунке 2.
Рисунок 2 – Схема расположения полей допусков
Посадки подшипников качения на вал и в корпус назначаются в зависимости от типа подшипников его размеров условий эксплуатации и характера действующих нагрузок на кольца.
Расчет внутреннего кольца подшипника (циркуляционное нагружение)
d – внутренний диаметр d=80 мм;
D – наружный диаметр D=200 мм;
R – наибольшая радиальная нагрузка на подшипник R=3800Н;
N – коэффициент для средней серии N=2.3;
b – рабочая ширина кольца подшипника b=50 мм;
[N] – расчетный допустимый натяг [N]=221862 мкм;
[dФ] – дополнительный натяг [dФ]=228612 мкм;
Расчет наружного кольца подшипника (местное нагружение)
По таблице назначаю посадку для нормального режима работы;
Расчет исполнительных размеров калибров гладкого цилиндрического соединения
При расчете будут использованы следующие обозначения размеров и допусков (в соответствии с ГОСТ 24853-81):
D – номинальный размер изделия D=60 мм;
Т – допуск изделия (вал – 30 мкм отверстие – 30 мкм);
Н – допуск на изготовление калибров Н= 5 мкм;
Н1 – допуск на изготовление калибров для вала Н1= 5 мкм;
НР – допуск на изготовление контрольного калибра для скобы НР=2 мкм;
Z – отклонение середины поля допуска на изготовление проходного калибра для отверстия относительно наименьшего предельного размера изделия Z=4 мкм;
Z1 – отклонение середины поля допуска на изготовление проходного калибра для вала относительно наибольшего предельного размера изделия Z1= 4 мкм;
Y – допустимый выход размера изношенного проходного калибра для отверстия за границу поля допуска изделия Y= 3 мкм;
Y1 – допустимый выход размера изношенного проходного калибра для вала за границу поля допуска изделия Y1= 3 мкм.
1 Определяем рабочий калибр для отверстия
Проходная сторона новая: размер мм
Проходная сторона изношенная: размер мм
Непроходная сторона: размер мм допуск мкм.
2 Определяем рабочий калибр для вала
Определяем контрольный калибр для вала
Непроходная сторона: размер допуск мкм.
Расчет рабочих калибров для резьбовой детали 9 соединения 8-9
Для резьбового соединения схема расположения полей допусков показана на рисунке 3.
Определяем основные размеры резьбы по ГОСТ 24705-81:
-наружный диаметр d (D) = 30 мм;
-средний диаметр d2(D2) = 27727 мм;
-внутренний диаметр d1(D1) = 27624 мм;
-шаг резьбы Р=35 мм.
Рисунок 3 – Схема расположения полей допусков резьбового соединения
Расчет рабочего калибра-пробки для наружной резьбы детали 9
Определяем предельные отклонения диаметров резьбы по ГОСТ 16093-81
([2] с. 153 табл. 4.29):
-нижнее отклонение D D2 D1 EI = 0 мкм;
-верхнее отклонение D2 ESD2 = -53 мкм;
-верхнее отклонение D1 ESD1 = -478 мкм.
ИCПОЛНИТЕЛЬНЫЕ РАЗМЕРЫ РЕЗЬБОВЫХ КАЛИБРОВ-ПРОБОК (в мм)
Средний диаметр = 27.727
Внутренний диаметр = 26.211
Степень точности основное отклонение 6H
Наружный диаметр = 30.0300
Средний диаметр = 27.7497
Износ рабочего калибра = 27.7217
Внутренний диаметр = 26.2111
Внутренний диаметр по канавке не более 25.7071
Ширина канавки = 0.875
Радиус канавки = 0.504
Наружный диаметр = 28.7277
Средний диаметр = 28.0207
Износ рабочего калибра = 27.9987
Внутренний диаметр по канавке = 25.7071
Ширина канавки = 1.10
Расчет размерной цепи А
На рисунке 4 показана размерная цепь. Для размерной цепи даны номинальные значения составляющих звеньев А1 =5 мм А2 = 211 мм= 5 мм А4 = 200 мм замыкающее звено по служебному назначению устройства требуется чтобы он был выдержан в пределах мм.
Размерную цепь решаем методом одного квалитета ([2] с. 22) по ГОСТ 16320-80.
Рисунок 4 – Схема размерной цепи А
В данной задаче исходным звеном является зазор . Предельные размеры замыкающего звена мм и мм. В схеме размерной цепи уменьшающими звеньями являются звенья и А1 остальные звенья цепи – увеличивающие.
Составляем уравнение размерной цепи (линейная размерная цепь):
Производим вычисления размера
Рассчитываем допуски составляющих звеньев по способу одной степени точности. Определяем среднее число единиц составляющих размеров
где среднее число единиц составляющих размеров;
допуск замыкающего звена ;
i – значение единицы допуска([4] c. 20) мкм.
Находим что такому числу единиц допуска соответствует примерно 13 квалитету в ЕСПД ([1] с. 45 табл. 1.8). Принимаем допуски составляющих звеньев с учетом степени сложности изготовления: Т1 =014 мм Т2 = 072 мм Т3 = 014 мм Т = 012 мм.
Проведем проверку правильности выбора квалитета
Подставляя ранее найденные значения получим
Для обеспечения равенства допусков выбираем в качестве увязочного звена звено А4 и округляем для него отношение:
Таким образом получаем что
Произведем проверку:
Схема контроля технических требований к детали 6
Контроль радиального биения осуществляется при помощи измерительных головок при базировании вала в центрах и повороте его на 3600. На результаты измерения влияет отклонение от круглости проверяемого сечения. Контроль торцевого биения производят на заданном диаметре торцевой поверхности
На рисунке 6 изображена схема контроля торцевого биения и отклонение формы цилиндрических поверхностей в которую входит: 1 – проверяемая деталь 2 –измерительная головка для измерения отклонение формы цилиндрических поверхностей.
В таблице 7.1 приведены приборы для контроля размеров и параметров контролируемой детали.
Рисунок 6 – Схема контроля радиального и торцевого биений
Таблица 7.1-Приборы для контроля размеров и параметров
Контролируемый размер и параметры
СР-50 (ц. д.0002 мм)
Профилограф-профилометр 252
)Полей М.А. Допуски и посадки: Справочник М.А. Полей В.Д. Мягков А.Б. Романов В.А. Брагинский; - Л.: Машиностроение 1982. 573 с. Ч.1.
)Полей М.А. Допуски и посадки: Справочник М.А. Полей В.Д. Мягков А.Б. Романов В.А. Брагинский; - Л.: Машиностроение 1982. 573 с. Ч.2.ГОСТ 24853-81 «Калибры гладкие для размеров до 500 мм. Допуски».
)Якушев А.И. Взаимозаменяемость стандартизация и технические измерения: Учебник для вузов. Якушев А.И. Воронцов Л.И. Федотов И.Н. – М.: Машиностроение 1987. 352 с.
)ГОСТ 24853-81 «Калибры гладкие для размеров до 500 мм. Допуски».
)Бойков Ф.И.Взаимозаменяемость стандартизация и технические измерения: Учеб. пособие для выполнения курсовой работы. Бойков Ф.И. Серадская И.В. и др. – ЧПИ 1987. 93 с.
ПЗ.doc
к курсовой работе по курсу
Метрология стандартизация и сертификация
Вариант № 4 Группа: 5ТМ-39
Головачёв С.Ю. Трехгорный: ТТИ НИЯУ МИФИ ТМ 2010 15 л. Библиография литературы – 5 наименований N листа формата А4 N листа формата А3.
В данной курсовой работе произведено назначение посадок для сопрягаемых поверхностей в зависимости от их служебного назначения. Так же произведен расчет соединения с натягом и по данным расчета выбрана посадка с натягом. Произведен расчет одного подшипника и по рекомендациям выбраны посадки для внутреннего и наружного колец подшипника для него построили схему полей допусков.
Так же в курсовой работе построены поля допусков расположения резьбового соединения. Произведены расчеты резьбового калибра-кольца и калибра-пробки по назначенным посадкам. В курсовой работе произведен расчет заданной размерной цепи по методу одного квалитета.
Назначение посадок для всех сопрягаемых деталей
Расчет посадки с натягом для соединения 2-9
Назначение и расчет подшипника качения 4
Расчет исполнительных размеров калибров для соединения 2-9
1Определяем рабочий калибр для детали 2
2Определяем рабочий калибр для детали 9
Расчет рабочих калибров для резьбовой детали 9 соединения 8-9
1Расчет рабочего калибра-кольца для наружной резьбы детали 8
2Расчет рабочего калибра-пробки для внутренней резьбы детали 9
Расчет размерной цепи А
Схемы контроля технических требований к детали 6
Библиографический список
Графическая часть на N листах формата А4 N листах формата А3
Назначение посадок для всех сопрягаемых соединений
- посадка с зазором («скользящая») применяется для подвижных соединений.
– посадка с натягом («прессовая тяжелая») предназначены для соединений на которые воздействуют тяжелые в том числе динамические нагрузки.
- посадка с натягом («прессовая средняя») предназначены для передач в которых применение посадок с большим натягом недопустимо по условиям прочности деталей.
- посадка с зазором. Посадка для наружного кольца подшипника (по расчетам).
– посадка с натягом. Посадка для внутреннего кольца подшипника (по расчетам).
- переходная посадка предназначена для установки втулок в корпуса.
- посадка с зазором. Предпочтительная посадка для среднего класса точности.
Расчет посадки с натягом для соединения 2-9.
Расчетная схема посадки с натягом приведена на рис. 1.
Рисунок 1 – схема посадки с натягом
Расчет посадки с натягом выполняем с целью обеспечения прочности соединения то есть отсутствие смещений сопрягаемых деталей под действием внешних нагрузок и прочности сопрягаемых деталей.
Исходные данные для расчета: внутренний диаметр охватываемой детали 2 d1 = 50 мм наружный диаметр охватываемой и внутренний диаметр охватывающей деталей d = 60 мм наружный диаметр охватывающей детали 9 d2 = 120 мм длина сопрягаемых поверхностей деталей 2-9 L = 50 мм крутящий момент МКР = 500 Н×м.
Материал детали 2 БрОф10-1 с пределом текучести т1= 20·107Нм2 модуль упругости
Е1 = 09·1011 Нм2 коэффициент Пуассона 1=033. Материал детали 9 Сталь 45Л с пределом текучести Нм2 модуль упругости Е1 = 21·1011 Нм2 коэффициент Пуассона коэффициент трения f = 02.
По известным значениям внешних нагрузок и размерам соединения определяем требуемое минимальное давление на контактных поверхностях соединения:
где Rос – продольная осевая сила Rос=8 кН;
Мk – крутящий момент Мk =0 Нм;
dн.с. – диаметр сопряжения dн.с.=006 м;
f – коэффициент трения f=008.
По полученным значениям p определяем необходимое значение наименьшего расчетного натяга Nmin:
где Е1 и Е2 – модули упругости материалов охватываемой и охватывающей деталей Па;
с1 и с2 – коэффициент Ляме определяемые по формулам:
где и - коэффициенты Пуассона;
Величина минимального допустимого натяга определяем с учетом поправок:
где - поправка учитывающая смятие поверхностей деталей;
- поправка учитывающая различие рабочей температуры деталей и температуры сборки;
- поправка учитывающая ослабление натяга под действием центробежных сил;
- поправка компенсирующая уменьшение натяга при повторных запрессовках.
=5(Ra1+Ra2)=5(125+063)=94 мкм.
=0 так как температура сборки и деталей одинакова.
=0 так как детали не вращаются относительно друг друга.
Принимаем с учетом возможных разборок =5 мкм.
На основе теории наибольших касательных напряжений определяем максимальное допустимое удельное давление [pmax]. В качестве [pmax] берется наименьшее из двух значений:
где и - пределы текучести материалов.
Определяем наибольший расчетный натяг:
Определяем величину максимального допустимого натяга с поправками:
где - коэффициент увеличения давления с торцов =075.
По справочнику допусков и посадок выбираем посадку 60 для которой Nmax=85мкм[Nmax] Nmin=23мкм>[Nmin].
Назначение и расчет посадки подшипника качения
Минимальный натяг определяем через интенсивность радиальной нагрузки.
Определяем интенсивность радиальной нагрузки по формуле:
где b – ширина подшипника (за вычетом фасок) b=23 мм;
FR – радиальная реакция опоры на подшипник FR = 365 кН;
k1 – динамический коэффициент посадки k1=1;
k2 – коэффициент учитывающий степень ослабления посадочного натяга k2=1;
k3 – коэффициент неравномерности распределения радиальной нагрузки k3=1.
В соответствии с [2 т1] заданным условиям соответствует поле допуска k6. Nmin=0002 мкм Nmax=0021 мкм. Таким образом посадка подшипника на вал будет . Посадку для наружного кольца подшипника с корпусом при местном нагружении принимаем по рекомендациям посадку ([4] с. 239 табл. 9.6). Схема расположения полей допусков показана на рисунке 2.
Рисунок 2 – Схема расположения полей допусков
Расчет исполнительных размеров калибров гладкого цилиндрического соединения
При расчете будут использованы следующие обозначения размеров и допусков (в соответствии с ГОСТ 24853-81):
D – номинальный размер изделия D=60 мм;
Т – допуск изделия (вал – 30 мкм отверстие – 30 мкм);
Н – допуск на изготовление калибров Н= 5 мкм;
Н1 – допуск на изготовление калибров для вала Н1= 5 мкм;
НР – допуск на изготовление контрольного калибра для скобы НР=2 мкм;
Z – отклонение середины поля допуска на изготовление проходного калибра для отверстия относительно наименьшего предельного размера изделия Z=4 мкм;
Z1 – отклонение середины поля допуска на изготовление проходного калибра для вала относительно наибольшего предельного размера изделия Z1= 4 мкм;
Y – допустимый выход размера изношенного проходного калибра для отверстия за границу поля допуска изделия Y= 3 мкм;
Y1 – допустимый выход размера изношенного проходного калибра для вала за границу поля допуска изделия Y1= 3 мкм.
1 Определяем рабочий калибр для отверстия
Проходная сторона новая: размер мм
Проходная сторона изношенная: размер мм
Непроходная сторона: размер мм допуск мкм.
2 Определяем рабочий калибр для вала
Определяем контрольный калибр для вала
Непроходная сторона: размер допуск мкм.
Расчет рабочих калибров для резьбовой детали 2 соединения 2-7
Для резьбового соединения схема расположения полей допусков показана на рисунке 3.
Определяем основные размеры резьбы по ГОСТ 24705-81:
-наружный диаметр d (D) = 140 мм;
-средний диаметр d2(D2) = 137402 мм;
-внутренний диаметр d1(D1) = 135670 мм;
Рисунок 3 – Схема расположения полей допусков резьбового соединения
1 Расчет рабочего калибра-кольца для наружной резьбы детали 7
Определяем предельные отклонения диаметров резьбы по ГОСТ 16093-81
([2] с. 153 табл. 4.29):
-верхнее отклонение d d1 d2 es = -60 мкм;
-нижнее отклонение d e
-нижнее отклонение d2 eid2 = -310 мкм.
Расчет проходного калибра-кольца по наружному внутреннему и среднему диаметрам ведется соответственно от наибольших наружного внутреннего и среднего диаметров болта. Расчет непроходного калибра-кольца ведется: по внутреннему диаметру – от размера равного разности наименьшего среднего диаметра болта и удвоенной высоты головки профиля по среднему диаметру – от наименьшего среднего диаметра болта; по наружному диаметру – аналогично проходному калибру от наибольшего наружного диаметра болта.
Для ПР резьбового калибра-кольца.
Определяем наименьший предельный наружный диаметр
TR – допуск внутреннего и среднего диаметров резьбового проходного калибра-кольца TR = 005 мм;
Н – высота исходного треугольника Н12 = 0288 мм.
Определяем наименьший предельный средний диаметр
ZR – расстояние от середины поля TR резьбового проходного калибра-кольца до проходного (верхнего) предела среднего диаметра наружной резьбы ZR = 002 мм.
Определяем наименьший предельный внутренний диаметр
Допуск среднего диаметра ПР резьбового калибра-кольца равен мм допуск внутреннего диаметра ПР резьбового калибра-кольца мм.
Исполнительные размеры ПР резьбового калибра-кольца:
-наружный диаметр 140278 мм m
-средний диаметр 137297+005 мм;
-внутренний диаметр 135635+005 мм.
Определяем размер изношенного ПР резьбового калибра-кольца по среднему диаметру
где D2ПРизн – размер изношенного ПР резьбового калибра-кольца по среднему диаметру мм;
WGO – величина среднедопустимого износа резьбового проходного калибра-кольца
Для НЕ резьбового калибра-кольца.
F1 – расстояние между линией среднего диаметра и вершиной укороченного профиля резьбы F1 = 03 мм.
Допуск среднего диаметра НЕ резьбового калибра-кольца равен мм допуск внутреннего диаметра НЕ резьбового калибра-кольца мм.
Исполнительные размеры НЕ резьбового калибра-кольца:
-средний диаметр 137042+005 мм;
-внутренний диаметр 136417+01 мм.
Определяем размер изношенного НЕ резьбового калибра-кольца по среднему диаметру
где D2НЕизн – размер изношенного НЕ резьбового калибра-кольца по среднему диаметру мм;
WNG – величина среднедопустимого износа резьбового непроходного калибра-кольца
2 Расчет рабочего резьбового калибра-пробки для внутренней резьбы детали 2
-нижнее отклонение D D2 D1 EI = 0 мкм;
-верхнее отклонение D2 ESD2 = +425 мкм;
-верхнее отклонение D1 ESD1 = +750 мкм.
Расчет проходного калибра-пробки по наружному внутреннему и среднему диаметрам ведется соответственно от наименьших наружного внутреннего и среднего диаметров гаек. Расчет непроходного калибра-пробки ведется: по наружному диаметру – от размера равного сумме наибольшего среднего диаметра гайки и удвоенной высоты головки профиля по среднему диаметру – от наибольшего среднего диаметра гайки; по внутреннему – аналогично проходному калибру от наименьшего внутреннего диаметра гайки.
Для ПР резьбового калибра-пробки.
Определяем наибольший предельный наружный диаметр
ZPL –расстояние от середины поля допуска TPL резьбового проходного калибра-пробки до проходного (нижнего) предела диаметра внутренней резьбы ZPL = 007 мм;
TPL – допуск наружного и среднего диаметров резьбового проходного и непроходного калибров-пробок TPL = 003 мм.
Определяем наибольший предельный средний диаметр
Определяем наибольший предельный внутренний диаметр
Допуск среднего диаметра ПР резьбового калибра-пробки равен мм допуск наружного диаметра ПР резьбового калибра-пробки мм.
Исполнительные размеры ПР резьбового калибра-пробки:
наружный диаметр 1401-006 мм;
средний диаметр 137457-003 мм;
внутренний диаметр 135094 мм max по канавке.
Определяем размер изношенного ПР резьбового калибра-пробки по среднему диаметру
где d2ПРизн – размер изношенного ПР резьбового калибра-пробки по среднему диаметру мм;
WGO – величина среднедопустимого износа резьбового проходного калибра-пробки
Для НЕ резьбового калибра-пробки.
Допуск среднего диаметра НЕ резьбового калибра-пробки равен мм допуск наружного диаметра НЕ резьбового калибра-пробки мм.
Исполнительные размеры НЕ резьбового калибра-пробки:
-наружный диаметр 14107-006 ММ
-средний диаметр 137857-003 мм;
-внутренний диаметр 136246 мм max по канавке.
Определяем размер изношенного НЕ резьбового калибра-пробки по среднему диаметру
где d2НЕизн – размер изношенного НЕ резьбового калибра-пробки по среднему диаметру мм;
WNG – величина среднедопустимого износа резьбового непроходного калибра-пробки
Расчет размерной цепи А
На рисунке 4 показана размерная цепь. Для размерной цепи даны номинальные значения составляющих звеньев А1 =5 мм А2 = 211 мм= 5 мм А4 = 200 мм замыкающее звено по служебному назначению устройства требуется чтобы он был выдержан в пределах мм.
Размерную цепь решаем методом одного квалитета ([2] с. 22) по ГОСТ 16320-80.
Рисунок 4 – Схема размерной цепи А
В данной задаче исходным звеном является зазор . Предельные размеры замыкающего звена мм и мм. В схеме размерной цепи уменьшающими звеньями являются звенья и А1 остальные звенья цепи – увеличивающие.
Составляем уравнение размерной цепи (линейная размерная цепь):
Производим вычисления размера
Рассчитываем допуски составляющих звеньев по способу одной степени точности. Определяем среднее число единиц составляющих размеров
где среднее число единиц составляющих размеров;
допуск замыкающего звена ;
i – значение единицы допуска([4] c. 20) мкм.
Находим что такому числу единиц допуска соответствует примерно 13 квалитету в ЕСПД ([1] с. 45 табл. 1.8). Принимаем допуски составляющих звеньев с учетом степени сложности изготовления: Т1 =014 мм Т2 = 072 мм Т3 = 014 мм Т = 012 мм.
Проведем проверку правильности выбора квалитета
Подставляя ранее найденные значения получим
Для обеспечения равенства допусков выбираем в качестве увязочного звена звено А4 и округляем для него отношение:
Таким образом получаем что
Произведем проверку:
Схема контроля технических требований к детали 8
Контроль радиального биения осуществляется при помощи измерительных головок при базировании вала в центрах и повороте его на 3600. На результаты измерения влияет отклонение от круглости проверяемого сечения. Контроль торцевого биения производят на заданном диаметре торцевой поверхности
На рисунке 6 изображена схема контроля торцевого биения и отклонение формы цилиндрических поверхностей в которую входит: 1 – проверяемая деталь 2 – измерительная головка для измерения торцевого биения 3 – измерительная головка для измерения отклонение формы цилиндрических поверхностей.
В таблице 7.1 приведены приборы для контроля размеров и параметров контролируемой детали.
Рисунок 6 – Схема контроля радиального и торцевого биений
Таблица 7.1-Приборы для контроля размеров и параметров
Контролируемый размер и параметры
Измерительная головка рычажно-зубчатая (однооборотная) МИГ2 (цена деления 0002 мм)
Калибр-кольцо резьбовой ПР
калибр-кольцо резьбовой НЕ
Калибр-пробка резьбовой ПР
калибр-пробка резьбовой НЕ
Профилометр мод. 283
)Допуски и посадки: Справочник М.А. Полей В.Д. Мягков А.Б. Романов В.А. Брагинский; Л.: Машиностроение 1982. 573 с. Ч.1.
)Допуски и посадки: Справочник М.А. Полей В.Д. Мягков А.Б. Романов В.А. Брагинский; Л.: Машиностроение 1982. 573 с. Ч.2.ГОСТ 24853-81 «Калибры гладкие для размеров до 500 мм. Допуски».
)Якушев А.И. Воронцов Л.И. Федотов И.Н. Взаимозаменяемость стандартизация и технические измерения: Учебник для вузов. – М.: Машиностроение 1987. 352 с.
)ГОСТ 24853-81 «Калибры гладкие для размеров до 500 мм. Допуски».
)Бойков Ф.И. Серадская И.В. и др. Взаимозаменяемость стандартизация и технические измерения: Учеб. пособие для выполнения курсовой работы. Ф.И. Бойков И.В. Серадская – ЧПИ 1987. 93 с.
задание 4.cdw

Поле допуска гладкой скобы
фрагмент.frw

Схема контроля.cdw

Поля допусков резьбового соединения.cdw

Поля допусков резьбового соединения(А3)1.cdw

зубчатое колесо №7.cdw

Высота до постоянной
Сталь 30Х13 ГОСТ 5632-72
деталь № 6 раб черт зад 10.cdw

задание 2.cdw

Рекомендуемые чертежи
Свободное скачивание на сегодня
- 29.08.2014
- 24.01.2023