Расчет коробки подач токарно-винторезного станка




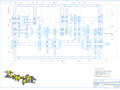
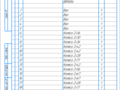

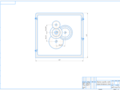
- Добавлен: 25.01.2023
- Размер: 728 KB
- Закачек: 1
Описание
Расчет коробки подач токарно-винторезного станка
Состав проекта
![]() |
![]() ![]() ![]() ![]() |
![]() ![]() ![]() ![]() |
![]() ![]() ![]() ![]() |
![]() ![]() ![]() |
![]() ![]() ![]() ![]() |
Дополнительная информация
Лист 2 - Развертка КП.cdw

Лист 3 - Свертка КП 511.cdw

Лист 1 - Общий вид.cdw

Спецификация.cdw

Рекомендуемые чертежи
- 29.05.2022
- 26.10.2020
Свободное скачивание на сегодня
- 22.08.2014
- 29.08.2014