Расчет коробки скоростей токарно-револьверного станка




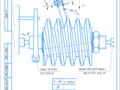
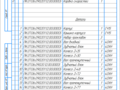

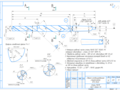
- Добавлен: 25.01.2023
- Размер: 465 KB
- Закачек: 0
Описание
Расчет коробки скоростей токарно-револьверного станка
Состав проекта
![]() |
![]() |
![]() ![]() ![]() |
![]() ![]() ![]() ![]() |
![]() ![]() ![]() ![]() |
![]() ![]() ![]() ![]() |
![]() ![]() ![]() ![]() |
![]() |
![]() ![]() ![]() ![]() |
![]() ![]() ![]() ![]() |
Дополнительная информация
Спецификация.spw

Фреза РИ.cdw

Кинематическая схема коробки скоростей.cdw

Коробка скоростей токарно-револьверного станка.cdw

Карта наладки РИ.cdw

Сверло РИ.cdw
