Расчет коробки подач токарно-револьверного станка




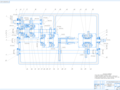
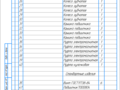
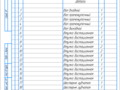
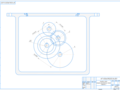
- Добавлен: 25.01.2023
- Размер: 1 MB
- Закачек: 1
Описание
Расчет коробки подач токарно-револьверного станка
Состав проекта
![]() |
![]() ![]() ![]() |
![]() |
![]() ![]() ![]() ![]() |
![]() |
![]() ![]() ![]() ![]() |
![]() ![]() ![]() ![]() |
![]() |
![]() ![]() ![]() ![]() |
![]() ![]() ![]() ![]() |
![]() ![]() ![]() ![]() |
Дополнительная информация
Курсовой пороект по МО.doc
ДОНЕЦКИЙ НАЦИОНАЛЬНИЙ ТЕХНИЧЕСКИЙ УНИВЕРСИТЕТ
Факультет инженерной механики и машиностроения
Кафедра «Металлорежущие станки и системы»
по дисциплине: «Металлообрабатывающее оборудование»
на тему: «Расчет коробки подач токарно-револьверного станка»
студент гр. МС – 06б Ященко А.Ю
Консультант Мирошниченко А.В
Нормоконтролер Мирошниченко А.В
Курсовой проект: . табл. рис. источников приложения.
Объект исследования – коробка подач токарно-револьверного станка.
В курсовом проекте выбран электродвигатель определены передаточные отношения каждой ступени коробки а также мощности крутящие моменты частоты вращения каждого вала. Рассчитаны модули для каждой передачи. Определены основные размеры зубчатых колес. Спроектированы передачи и проведен расчет наиболее нагруженного вала. Выбрана система смазки. Выбраны электромагнитные муфты и подшипники качения а также выбраны и рассчитаны шлицевые соединения. Выполнены чертежи развертки коробки подач свертки общего вида токарно-револьверного станка (прототипа) кинематическая схема структурная сетка и график частот вращения.
СТАНОК ВАЛ ПОДШИПНИК КОРОБКА СКОРОСТЕЙ ЭЛЕКТРОМАГНИТНАЯ МУФТА ЗУБЧАТОЕ КОЛЕСО ПЕРЕДАТОЧНОЕ ОТНОШЕНИЕ МОДУЛЬ
ЗАДАНИЕ НА ПРОЕКТИРОВАНИЕ
Спроектировать коробку подач токарно-револьверного станка имея такие исходные данные:
Основной размер: d = 25 мм;
Предельные значения подач : S = 005 - 20 ммоб;
Знаменатель геометрической прогрессии: φ=141;
Вес подвижных частей 500 кг.
Общая характеристика станка и его назначение
Обоснование выбора предельных режимов резания
Определение диапазона регулирования подач
Выбор структурной формулы коробки подач
Выбор чисел зубьев зубчатых колес коробки подач
Расчет эффективной мощности коробки подач
Расчет модулей зубчатых колес
Определение параметров зубчатых колес
Определение параметров валов
1 Выбор материала для валов
2 Уточненный расчёт валов
3 Расчет вала на усталость
Выбор элементов передающих крутящий момент
Определение системы смазки которая обеспечивает заданную точность обработки
Расчет динамических характеристик проектируемой коробки подач
1 Расчет критической скорости скольжения по характеристикам трения
2 Расчет критической скорости скольжения по жесткости привода
Список использованных источников
Приложение А: Общий вид станка и кинематическая схема коробки подач
Приложение Б: Сборочный чертеж коробки подач
Приложение В: Спецификация
В настоящее время наблюдается тенденция на повышение уровня автоматизации производственных процессов. В производство все более внедряется автоматизированное оборудование работающее без непосредственного участия человека или значительно облегчающее труд рабочего. Это позволяет значительно сократить трудоемкость производственного процесса снизить себестоимость выпускаемой продукции увеличить производительность труда. Поэтому главная задача инженеров—разработка автоматизированного оборудования расчет его основных узлов и агрегатов выявление наиболее оптимальных технических решений и внедрение их в производство.
Целью данного курсового проекта является разработка автоматической коробки подач токарно-винторезного станка переключение передач в которой осуществляется при помощи электромагнитных фрикционных муфт.
Привод подач предназначен для сообщения рабочего движения инструменту при обработке и изменения скорости его движения при неизменной частоте вращения шпинделя. Крутящий момент передается коробке подач от электродвигателя через коробку скоростей и механизм гитары за счет чего обеспечивается жесткая кинематическая связь с частотой вращения шпинделя. После прохождения через коробку подач крутящий момент передается ходовому валу а от ходового вала – фартуку в котором крутящий момент и частота вращения окончательно преобразуются до требуемых значений зубчатой шестерни реечной передачи обеспечивающей требуемую скорость движения суппорта.
Расчет коробки подач включает определение диапазона регулирования подач. Построение структурной сетки и в соответствии с ней графика подач и кинематической схемы определение чисел зубьев зубчатых колес коробки Определения передаточного отношения постоянной передачи фартука требуемой эффективной мощности коробки подач модулей и параметров зубчатых колес параметров валов и уточненный расчет на усталость самого нагруженного вала выбор шпоночных или шлицевых соединений передающих крутящий момент. Выбор электромагнитных муфт выбор подшипников опор валов выбор системы смазки расчет динамических характеристик обеспечивающих заданную точность обработки.
Револьверные ( токарно –револьверные )станки предназначены для обработки заготовок деталей сложной конфигурации в серийном производстве . Наружные поверхности обрабатывающих резцами различных типов центральное отверстие детали – резцами сверлами метчиками и пр.
Основной особенностью револьверных станков является наличие продольного суппорта несущего многопозиционную поворотную револьверную головку на которой закрепляют различные инструменты.
При поворотах револьверной головки последовательно вводятся в действие заранее настроенные на размер инструменты благодаря чему значительно сокращается вспомогательное время.
Кроме продольного суппорта эти станки в большинстве случаев имеют суппорт на котором крепят инструменты для обработки наружных поверхностей.
Основными размерами револьверных станков являются наибольший диаметр обработки над станиной.
В револьверных станках главным движением является вращение шпинделя несущего заготовку ; движениями подачи – продольное и поперечное перемещение суппортов несущих режущий инструмент. Иногда поперечная подача осуществляется медленным вращением револьверной головки или перемещением салазок с револьверной головки или перемещением салазок с револьверной головкой в поперечном направлении .
Вспомогательным движениями в револьверных станках являются:
а) повороты револьверной головки для последовательного ввода в работу инструментов;
б) подача и зажим материала;
в) быстрый подвод и отвод револьверного поперечного суппортов и др.
Определяем предельные значения размеров обрабатываемой заготовки.
Принимаем 8 видов операций возможных на данном станке и для них в соответствии с рекомендацией выберем значения режимов обработки в соответствии с видом обработки и материалом режущего инструмента. Полученные данные заносим в таблицу 1.
Таблица 1 – Режимы резания при различных способах обработки
Сталь конструкционная углеродистая и легированная
Черновое продольное точение и подрезание торцов (получение 14 квалитета)
Получистовое продольное точение и подрезание торцов (получение 12 квалитета)
Чистовое продольное точение и подрезание торцов (получение 10 квалитета)
Черновое растачивание (получение 14 квалитета )
Получистовое растачивание (получение 12 квалитета )
Чистовое растачивание (получение 10 квалитета )
Определяем диапазон регулирования подач по формуле:
Определяем число ступеней коробки подач:
По числу ступеней коробки подач и знаменателю геометрической прогрессии φ=141 из таблицы [2. стр.26] выбираем вид структуры АII-4. При этом структурная формула имеет вид:
По рисунку [2 с. 26] выбираем типовую кинематическую схему привода:
Рисунок1 - Кинематическая схема привода
Выбираем следующие параметры коробки подач:
КШ = 14 – число шестерен коробки;
КВ = 5 – количество валов коробки подач;
Zкц=4 – количество ступеней подачи передаваемых по короткой кинематической цепи;
КБ = 3 – количество блоков – шестерен;
КМ = 1 – количество муфт;
- максимальное значение знаменателя прогрессии.
В соответствии со знаменателем прогрессии φ=141 выбираем стандартный ряд подач: 0056;008;0112;016;0224;0315;045;063;09;125;18;25.
Строим структурную сетку и график подач по полученным данным.
Рисунок 2 – Структурная сетка коробки подач
Рисунок 3 – График подач токарно-винторезного станка
Исходя из найденных по графику подач передаточных отношений а также из кинематической схемы коробки определяем числа зубьев зубчатых колес по таблице 6 [2 стр.102 - 103]
Таблица 2 – Числа зубьев зубчатых колес.
Направление передачи (валы)
Расчёт эффективной мощности коробки подач
Определение мощности электродвигателя главного движения определяется по формуле :
Эффективная мощность коробки подач определяется по формуле:
Q - тяговое усилие на рейке Н
S - максимальная подача ммоб
Значение Q для комбинированных направляющих определяем по формуле:
G – масса передвижных частей кг;
F – коэффициент трения между поверхностями пиноли и корпуса. На шлицах или на шпонках шпинделя;
F» - приведенный коэффициент трения на направляющих;
Pz – составляющая сила резания что прижимает каретку суппорта или стола к направляющим Н. Определяем по формуле:
Для определения усилия резания выбираем наиболее тяжелые условия резания – ВК8диаметр обрабатываемый 400 мм при t=4 мм подаче s= 25 ммоб и период стойкости Т = 30 мин.
Скорость резания определяем по формуле:
При этом необходимо вычислить необходимые поправочные коэффициенты:
где nV = 1.25; НВ = 170.
Определяем значение коэффициента и показателей степени в формулах скорости резания при обработке резцами :
СV = 215 ; y = 045 ;m = 020 [1 стр.269 таб.17]
Коэффициент КV является произведением коэффициентов учитывающих влияние материала заготовки KMV (1 стр.260-266 таб.1-4) состояние поверхности KПV (1 стр.260-266 таб.5) материала инструмента KИV (1 стр.260-266 таб.6):
KV = KMV·· KПV ·KИV (10)
KMV – коэффициент влияния обрабатываемого материала 115;
KПV - коэффициент учитывающий состояние поверхности заготовки 10;
KИV - коэффициент учитывающий влияние материала инструмента 115 (
при обработке конструкционной стали резцом ВК8.
Подставляем все значения в формулу (..):
Определяем составляющую силу резания:
Определяем поправочный коэффициент для чугуна учитывающий влияние качества обрабатываемого материала на силовые зависимости KMP:
Определяем значение коэффициента СP и показателей степени в формулах силы резания для составляющей Рz при точении:
СР = 92; y = 075; n = 0 [1 стр.273 таб. 22]
Определяем поправочный коэффициент для составляющей Рz учитывающий влияние геометрических параметров режущей части инструмента на составляющие силы резания при обработке чугуна:
Кφр = 094; Кγр = 10; Кλр = 10; Кrр = 10 [1 стр.275 таб. 23]
Составляющая сила Рz составляет:
Определяем значение коэффициента СP и показателей степени в формулах силы резания для составляющей Рy при точении:
СР = 54; y = 075; n = 0 [1 стр.273 таб. 22]
Кφр = 077; Кγр = 10; Кλр = 125; Кrр = 10 [1 стр.275 таб. 23]
Определяем значение коэффициента СP и показателей степени в формулах силы резания для составляющей Рx при точении:
СР = 46; y = 04; n = 0 [1 стр.273 таб. 22]
Кφр = 111; Кγр = 10; Кλр = 085; Кrр = 10 [1 стр.275 таб. 23]
G – сила тяжести подвижных частей суппорта Н
G = m·g =500 981= 4900 Н (12)
Определяем тяговое усилие :
Частот вращения шпинделя определяем по формуле:
Имея необходимые расчёты можем определить эффективную мощность коробки подач:
Тогда мощность электродвигателя главного движения будет равна:
Расчёт модулей зубчатых колёс
При расчёте зубчатых колёс коробки подач модуль рассчитывается для каждой из передач в отдельности исходя из прочности зубьев на изгиб и прочности зубьев на контакт.
Для стальных прямозубых колес формулы для определения модуля имеют вид:
где – допускаемые напряжения на изгиб;
– коэффициент формы зуба выбирается из (3 стр.79 таб.3.19)
– число зубьев меньшего колеса;
– момент на валу меньшего колеса;
– коэффициент ширины зубчатого колеса (рекомендуется принимать );
– коэффициент нагрузки который учитывает изменение нагрузки по сравнению с номинальной от действия различных факторов. Данный коэффициент выбирается из (3 стр.80 таб.3.20)
а) Расчет модуля передач с первого на второй валы.
Для данной передачи: количество зубьев шестерни составляет z = 40; крутящий момент на валу Н·м; материал – сталь 40Х.
Для расчета модуля по изгибным напряжениям принимаем: ;YF1=39.
Определяем значения необходимые для нахождения KF=13-15.
Модуль зубчатой передачи:
Принимаем модуль зубчатого колеса m=15.
а) Расчет модуля передач со второго на третий валы.
Для данной передачи: количество зубьев шестерни составляет z=33; крутящий момент на валу Н·м; материал – сталь 40Х.
Определяем значения необходимые для нахождения KF=13-15
б) Расчет модуля передач с третьего на четвернтые валы.
Для данной передачи: количество зубьев шестерни составляет z=20; крутящий момент на валу Н·м; материал – сталь 40Х.
в) Расчет модуля передач с четвёртого н6а пятый валы.
Определение параметров зубчатых колёс
К основным параметрам зубчатых колес относятся модуль межосевое расстояние ширина зубчатых колес диаметр делительной окружности диаметр вершин зубьев и диаметр впадин зубьев .
Диаметр делительной окружности
Диаметр окружности вершин
Диаметр окружности впадин
Межосевое расстояние
Ширина зубчатого венца
Таблица 3 -Основные размеры зацепления
Делитель-ный диаметр
Межцентровое расстояние аw
Назначаем для всех валов в качестве материала сталь 45 с термической обработкой нормализация.
Механические свойства стали 35 выбираем из таблицы [4]:
2 Уточненный расчет вала
Определяем крутящие моменты на всех валах по формуле:
- передаточное отношение коробки подач
Проектирование валов осуществляется путем определения диаметра валов. Расчет ведется на кручение по формуле :
где – крутящий момент;
– допустимое напряжение кручения
Полученные значения округляем до ближайшего из стандартных значений
Принимаем стандартный диаметр валов12 мм.
Уточненный расчет выполняем для четвертого вала так как он является наиболее нагруженным на пятом валу наибольшее значение крутящего момента.
Определяем окружную силу в зацеплении по формуле:
Для 10-го зубчатого колеса:
Для 13-го зубчатого колеса:
Определяем радиальную силу:
Fr = Ft ··tgα Н (24)
где α – угол профиля зубьев α=200
Для -го зубчатого колеса:
Рассмотрим данную расчетную схему вала в двух плоскостях: горизонтальной и вертикальной в которых действуют радиальная и окружная силы.
Рисунок 4 – Схема нагружения и эпюры крутящих и изгибающих моментов расчитуемого вала.
Составим уравнение равновесия вала в вертикальной плоскости.
По найденным реакциям строим эпюру изгибающих моментов в вертикальной плоскости.
Составим уравнение равновесия в горизонтальной плоскости.
По найденным реакциям строим эпюру изгибающих моментов в горизонтальной плоскости.
Полная нагрузка на опоры вала
Суммарные изгибающие моменты :
Приведенный момент в опасном сечении вала:
Приведенный момент в первом сечении вала
3Расчет вала на усталость
Усталостный расчет вала выполняется как проверочный. Он заключается в определении расчетных коэффициентов запаса прочности в предположительно опасных сечениях.
При расчете принимаем что напряжения изгиба изменяются по симметричному циклу а напряжения кручения – от нулевому циклу.
Амплитудные значения напряжений изгиба и кручения определяются по формулам:
где М – изгибающий момент в сечении;
Wнетто – момент сопротивления сечения изгибу
Wкнетто – момент сопротивления сечения кручению;
Момент сопротивления сечения изгибу для сечения со шпоночным пазом определяется по формуле:
Момент сопротивления сечения кручению определяется по формуле:
Шлицевые соединения по сравнению со шпоночными обладают более высокой нагрузочной способностью создают меньшую концентрацию напряжений в валах а следовательно обеспечивают более высокую выносливость последних создают лучшую центровку деталей на валах более удобны для массового и серийного производства.
Расчёт шлицевых соединений выполняется обычно как проверочный по напряжениям смятия:
Рисунок 5-Шлицевое соединение
φ- коэффициент что учитывает неравномерное распределение нагрузки между шлицами ( обычно принимают 075);
D d z – размеры разреза соединения ( внешний внутренний диаметр и количество шлицёв);
f – размер фаски по длине шлица мм;
- рабочая часть шлица мм;
- напряжения смятия что допускаются. Определяются в зависимости от условий эксплуатации принимаем = 40 МПа
Также в коробке подач присутствуют шпоночные соединения которые необходимо проверить на смятие. Которая проводится по формуле:
Рисунок 6- Шпоночное соединение
гдеМкр –крутящий момент на валу Нм;
d – диаметр вала = 20 мм;
h – высота шпонки = 5мм;
[sсм] – допускаемые напряжения смятия для материала шпонки 45.
Рабочая длина шпонки определяется по формуле:
lр = lшп – b мм (46)
Подставляем в формулу () получаем:
Условие выполняется.
Для выбора подшипников опор валов определяем диаметры шипов валов которые определяются по формуле:
dш=(08 09) dв мм (47)
dш= (08 09)·20=16 18мм
Учитывая элементы расположенные на валах а также по полученным диаметрам шипов выбираем подшипники параметры которых указаны в таблице 4
Рисунок 7 – Подшипник шариковый радиальный
Таблица 4- Параметры подшипников на валах коробки подач.
Внутренний диаметр d мм
Наружный диаметр D мм
Статическая грузоподъемностьC0кН
Динамическая грузоподъемностьCкН
Смазочная система станка служит для подачи смазочного материала ко всем трущимся поверхностям.
Существует несколько схем подвода смазочного материала к трущимся поверхностям.
Индивидуальная схема служит для подвода смазочного материала к одной смазочной точке централизованная к нескольким точкам. В нераздельной схеме нагнетательное устройство присоединено к смазочной точке постоянно в раздельной оно подключается только на время подачи смазочного материала. В проточной системе жидкий или пластичный материал используется один раз. В циркуляционной системе жидкий материал подается повторно. В системах дроссельного дозирования объем смазочного материала подаваемого к смазочной точке регулируется дросселем. В системах объемного дозирования могут регулироваться не только доза но и частота подачи. В комбинированных системах могут быть предусмотрены объемное и дроссельное регулирование одно- и двухматериальные питатели. Системы с жидким смазочным материалом в зависимости от способа его подачи к поверхностям трения могут быть разбрызгивающими струйными капельными аэрозольными. Для смазки данного станка принимаем импульсную смазочную систему в которой смазочный материал ко всем поверхностям трения подается одновременно. Схема импульсной системы приведена на рисунке 13.1 где 1 – указатель уровня смазочного материала; 2 – приемный фильтр; 3 – насос; 4 – фильтр напорной магистрали; 5 – манометр; 6 – смазочный дроссельный блок с ротаметрическими указателями; 7 – реле расхода смазочного материала; 8 – точки смазывания; 9 – указатель потока; 10 – точки смазывания с форсункой; 11 – точки смазывания; 12 – смазочный дроссельный блок; 13 – сливной магнитосетчатый фильтр; 14 – предохранительный клапан;15 – реле уровня; 16 – фильтр; 17 – резервуар.
Рисунок 8 – Схема импульсной централизованной смазочной системы
1 Расчёт критической скорости скольжения по характеристикам трения
Точность изготовления и качество обработанной поверхности в значительной степени зависит от устойчивости медленных перемещений узлов станка несущих инструмент или заготовку. Появление неравномерного скачкообразного движения объясняемое возникновением фрикционных автоколебаний стола при недостаточной жесткости привода подач и различием коэффициентов трения покоя и движения приводит к резкому ухудшению шероховатости а в некоторых случаях – точности обработки.
В зависимости от величины подачи и геометрии режущего инструмента высота микронеровностей определяется по формуле:
где φ1 и φ – главный и вспомогательный углы в плане. Для рассматриваемого вида обработки принимаем φ1=φ=450.
S – величина подачи ммоб. S=25 ммоб.
Подача определенная по заданной высоте микронеровностей является имитирующей.
По этой подаче определяем скорость перемещения суппорта:Vs=Sn.
где n – частота вращения шпинделя при режиме резания соответствующем лимитирующей подаче обмин.
Лимитирующее значение подачи для данного станка при котором можно получить шероховатость Ra 25 мкм составляет 01 мкм. При этом частота вращения шпинделя при обработке заготовки диаметром 400 мм принимаем 45 обмин.
Vs=12545=5625мммин= 0056ммин.Для получения равномерного движения скорость перемещения суппорта должна быть большей или равной критической скорости скольжения вычисленной по характеристикам трения и направляющих и критической скорости скольжения определяемой жесткостью привода подач.
Одной из основных причин скачкообразного движения суппорта является малая жесткость привода а также нелинейная зависимость коэффициента трения от скорости.
На основе теории скольжения тел с периодическими остановками получена формула для получения критической скорости скольжения которая является границей равномерного и неравномерного движения при заданной величине демпфирования в системе.
где N– нормальная направляющая нагрузка на суппорт кг
fп fд - коэффициенты трения покоя и движения соответственно. По таблице (5 стр.11) определяем fп=0.28 fд=0.2.
– коэффициент относительного рассеивания энергии колебаний. По таблице (5 стр.11) для направляющих скольжения определяем =09
m – приведенная масса перемещаемых частей кг. m=64286кг.
С0 – приведенная жесткость привода кгсмм.
Считая что приведенная жесткость привода определяется жесткостью ходового винта как стержня работающего на растяжение можно записать:
где Е – модуль упругости материала винта кгмм2
для материала винта Е=2105кгмм2.
dср - средний диаметр винта мм; dср=12мм.
l – длина участка винта работающего на растяжение мм. Принимаем l=500мм.
Условие Vкр Vs выполняется.
В результате проделанной работы был произведен расчет коробки подач выбор и расчет параметров отдельных ее элементов: электромагнитных муфт обеспечивающих автоматическое переключение передач коробки подач; подшипников качения служащих опорами валов; системы смазки и смазочного материала обеспечивающих непрерывный подвод смазочного материала ко всем механизмам станка. Был произведен расчет критической скорости скольжения по характеристикам трения и по жесткости привода значения которой меньше скорости движения суппорта что обеспечивает равномерность его движения. Были разработаны компоновочная схема и чертеж коробки подач с указанием ее основных элементов.
В приложении А пояснительной записки выполнен чертеж общего вида токарно-винторезного станка где указаны его основные элементы и габаритные размеры а также схематически показаны структурная сетка и график подач данного станка.
Список использованной литературы:
Справочник технолога-машиностроителя. 2 том. Под редакцией А. Г. Косиловой и Р.К. Мещерякова. 4-е издание переработанное и дополненное. – М.: Машиностроение 1985. – 496 с.
Методические указания к курсовому проекту по курсу «Металлорежущие станки и промышленные роботы» Составили: Ю.А. Сапронов В.Г. Кочергин Н.В. ВяльцевА. Е. Гаркуша. – Донецк. ДПИ 1987г. – 48 с.
А. С. Пронников. Расчет и конструирование металлорежущих станков. Изд. 2-е.М.: «Высшая школа» 1968. 431 с.
Методические указания по курсовому проектированию деталей машин. Раздел 3: расчет и конструирование валов. Сост. Симонов А.Л. Ващенко В.Ф. Матеко П.М. – Донецк ДПИ 1981. – 51с.
Решетов Д. Н. Атлас деталей и узлов машин. М: «Машиностроение»
Подшипники качения: Расчет проектирование и обслуживание опор: Справочник. Л.Я. Перель. – М.: Машиностроение 1983. – 543 с. ил.
В.И. Анурьев. Справочник конструктора машиностроителя: В 3-х т. Т.1 Т.3. – 5-е изд. перераб. и доп. – М.: машиностроение 1978.
Методические указания к самостоятельной работе над курсовым проектом по даталям машин. Раздел III. Этапы «Эскизный проект» и «Технический проект». Проектирование зубчатых и червячных передач.- Донецк: ДПИ 1992.-84 с.
Детали и механизмы металлорежущих станков Под ред. Д.Н. Решетова.- М.:Машиностроение1972-т.2-250с.
В.И. Анурьев. Справочник конструктора машиностроителя: В 3-х т. Т.2 Т.3. – 5-е изд. перераб. и доп. – М.: машиностроение 1978.
Батурин А.Т. Детали машин. М.: Машиностроение1971.-467с.
Спецификация 1.cdw

Спецификация 2.cdw

Спецификацмя3.cdw

Свётрка.cdw

Общий вид станка.cdw

быстрого поворота револьверной головки; 5 - кнопка "Аварийный стоп"; 6 - штурвал ручного продольного перемещения
револьверного суппорта; 7 - рукоятка пуска и осановка шпинделя; 8 - рукоятка переключения диапазона скоростей; 9 -
рукоятка преключения подач.
Техническая характеристика станка
Наибольший диаметр обрабатываемой заготовки D
Число ступеней подач Z=12
Предельные значения подач:
Токарно - револьверный станок
кинематическая схема
график подач токарно - револьверного
КП 10.06.090203.34.001
График подач токарно-револьверного станка
Структурная сетка коробки подач
Кинематическая схема
Курсовой прект на новый ладcdw.cdw

После сборки обкатать в течении 6 часов
Заедания при работе и преключении передач не добускается.
Осевая игра валов: выходного - 0
Регулировать осевую игру валов набором прокладок.
токарно - револьверного станка
КП 10.06.090203.34.002