Проектирование режущего инструмента (фасонный резец, протяжка, долбяк)



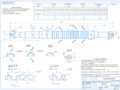
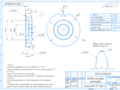
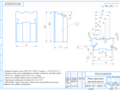
- Добавлен: 24.01.2023
- Размер: 568 KB
- Закачек: 1
Узнать, как скачать этот материал
Подписаться на ежедневные обновления каталога:
Описание
Проектирование режущего инструмента (фасонный резец, протяжка, долбяк)
Состав проекта
![]() |
![]() |
![]() ![]() ![]() |
![]() ![]() ![]() ![]() |
![]() ![]() ![]() ![]() |
![]() ![]() ![]() |
![]() ![]() ![]() ![]() |
Дополнительная информация
Контент чертежей
Долбяк мой 17 вариант.cdw

протяжка вариант 77.cdw

Резец фасонный призматический _ 1510.12.528.00.00..cdw

Рекомендуемые чертежи
Свободное скачивание на сегодня
Обновление через: 8 часов 45 минут
Другие проекты
- 14.04.2020