Проектирование режущего инструмента




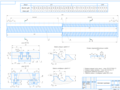
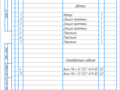
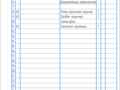
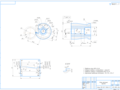
- Добавлен: 04.11.2022
- Размер: 1 MB
- Закачек: 0
Описание
Курсовая работа - Проектирование режущего инструмента
Состав проекта
![]() |
![]() ![]() ![]() ![]() |
![]() ![]() ![]() ![]() |
![]() ![]() ![]() ![]() |
![]() ![]() ![]() |
![]() ![]() ![]() ![]() |
![]() |
![]() ![]() ![]() ![]() |
Дополнительная информация
Долбяк чашечный.cdw

Класс точности по ГОСТ 9323-79
Сталь Р18 ГОСТ 19265-73
Класс точности долбяка АА.
Твердость режущей части долбяка HRCэ 63 66.
Неуказанные предельные отклонения
Комплект протяжек.spw

Резец круглый.cdw

Твёрдость резца НRСэ 63 66
Материал шаблона и контршаблона - стальХ12
Твёрдость шаблона и контршаблона НRСэ 62 65
Неуказанные предельные отклонения : Н14;
расчёт33.doc
Расчет и конструирование чашечного долбяка для нарезания
прямозубых зубчатых колес 10
Расчет и конструирование комплекта протяжек для обработки
наружных поверхностей 17
Список использованных источников 23
От качества надежности и работоспособности режущих инструментов применяемых в машиностроении в значительной степени зависят качество и точность получаемых изделий производительность и эффективность процесса обработки в особенности при автоматизированном производстве в условиях гибких производственных систем (ГПС).
При проектировании режущих инструментов необходимы знания теоретических основ конструирования и расчета инструментов с использованием систем автоматизированного проектирования (САПР) нужно уметь правильно определить наилучшие для данных условий обработки конструктивные элементы инструментов и создавать оптимальную их конструкцию учитывая условия эксплуатации знать основные направления их совершенствования пути повышения надежности и эффективности представлять себе возможные направления и перспективы развития режущего инструмента.
Целью данной курсовой работы является проектирование круглого фасонного резца чашечного долбяка для нарезания прямозубых колес и комплекта протяжек для обработки фасонной поверхности.
Расчет и конструирование круглого фасонного резца
Исходные данные для расчета представлены в таблице 1.
Таблица 1 – Исходные данные
Шероховатость по контуру мкм
Эскиз обрабатываемой поверхности детали представлен на рисунке 1.
Рисунок 1 – Эскиз поверхности детали
Определяем передний и задний углы резца
задний угол α = 12º; передний угол γ = 20º
Размеры дополнительных режущих кромок под отрезание и подрезание
b1 = 1 мм b = 5 мм a = 1 мм φ = 15º
Общая ширина резца вдоль оси заготовки
Lр = Lд + b1 + b + а = 85 + 1 + 5 + 1 = 92 мм.
Наибольшая глубина профиля детали
tmax = (60 – 48) 2 = 6 мм.
Габаритные и конструктивные размеры резца
Размеры резца: D = 75 мм d (H8) = 22 мм d1 = 34 мм b = 15 мм K = 4 мм r = 2 мм D1 = 42 мм d2 = 5 мм.
Высота заточки резца Н = R sin(α + γ) = 375 · 053 = 19875 мм
Высота установки резца hр = R sinα = 375 · 0208 = 78 мм
Определим по эскизу детали радиусы окружностей узловых точек профиля детали и осевые расстояния до этих точек от торца детали.
r1 = r2 = 24 мм; l1-2 = 25 мм
r3 = r4 = 30 мм; l1-3 = 65 мм
r5 = r6 = 25 мм; l1-45 = 77 мм
tg = r3 - r1 l1-3 - l1-2 = 30 – 24 65 – 25 = 015 (1)
tgλ = tg · s λ = 2°56 (2)
Определяем постоянные величины
l = r1 cosγ + R cos = 24 · 094 + 375 · 0848 = 5436 мм (3)
n = r1 sinγ + R sin = 24 · 0342 + 375 · 053 = 2808 мм (4)
Определяем радиус резца R2
r2 = r1 + y2 tg = 24 + 25 · 015 = 2775 мм (5)
m2 = r2 sinγ = 2775 · 0342 = 949 мм (6)
Н2 = n – m2 = 2808 – 949 = 1859 мм (7)
М2 = r2 cosγ2 = 24 · 0918 = 22032 мм (9)
N2 = l – М2 = 5436 – 22032 = 32328 мм (10)
tg2 = Н2 N2 = 1859 32328 = 0575; 2 = 29º54 (11)
R2 = Н2 sin2 = 1859 0499 = 37254 мм (12)
Определяем радиус резца R3
r3 = r1 + y3 tg = 24 + 65 · 015 = 3375 мм
m3 = r3 sinγ = 3375 · 0342 = 1154 мм
Н3 = n – m3 = 2808 – 1154 = 1654 мм
М3 = r3 cosγ3 = 30 · 0923 = 27686 мм
N3 = l – М3 = 5436 – 27686 = 26674 мм
tg3 = Н3 N3 = 1654 26674 = 062; 3 = 31º48
R3 = Н3 sin3 = 1654 0527 = 31385 мм
Определяем радиус резца R4
r4 = r1 + y4 tg = 24 + 77 · 015 = 3555 мм
m4 = r4 sinγ = 3555 · 0342 = 1216 мм
Н4 = n – m4 = 2808 – 1216 = 1592 мм
М4 = r4 cosγ4 = 30 · 0914 = 2743 мм
N4 = l – М4 = 5436 – 2743 = 2693 мм
tg4 = Н4 N4 = 1592 2693 = 0591; 4 = 30º36
R4 = Н4 sin4 = 1592 0509 = 31277 мм
Определяем радиус резца R5
r5 = r1 + y5 tg = 24 + 77 · 015 = 3555 мм
m5 = r5 sinγ = 3555 · 0342 = 1216 мм
Н5 = n – m5 = 2808 – 1216 = 1592 мм
М5 = r5 cosγ5 = 25 · 0874 = 21844 мм
N5 = l – М5 = 5436 – 21844 = 32516 мм
tg5 = Н5 N5 = 1592 32516 = 049; 5 = 26º6
R5 = Н5 sin5 = 1592 044 = 36182 мм
Определяем радиус резца R6
r6 = r1 + y6 tg = 24 + 85 · 015 = 3675 мм
m6 = r6 sinγ = 3675 · 0342 = 1257 мм
Н6 = n – m6 = 2808 – 1257 = 1551 мм
М6 = r6 cosγ6 = 25 · 0864 = 2161 мм
N6 = l – М6 = 5436 – 2161 = 3275 мм
tg6 = Н6 N6 = 1551 3275 = 0474; 6 = 25º21
R6 = Н6 sin6 = 1551 0428 = 36238 мм
Определяем координатные расстояния
P2 = R – R2 = 375 – 37254 = 0246 мм
P3 = R – R3 = 375 – 31385 = 6115 мм
P4 = R – R4 = 375 – 31277 = 6223 мм
P5 = R – R5 = 375 – 36182 = 1318 мм
P6 = R – R6 = 375 – 36238 = 1262 мм
прямозубых зубчатых колес
Исходные данные для расчета приведены в таблице 2.
Таблица 2 – Исходные данные
Модуль нарезаемого колеса мм
Число зубьев нарезаемого колеса
Число зубьев сопрягаемого колеса
Степень точности колеса
Определяем геометрические параметры нарезаемого колеса.
mt = m cos = 225 1 = 225 мм (13)
Делительные диаметры.
d1 = mt z1 = 225 30 = 675 мм (14)
d2 = mt z2 = 225 58 = 1305 мм
Профильный угол в торцевом сечении.
tg αt = tg α cos = 0364 1 = 0364; αt = 20° (15)
Диаметры основных окружностей.
db1 = d1 cos αt = 675 094 = 6345 мм (16)
db2 = d2 cos αt = 1305 094 = 12267 мм
Угол зацепления в передаче.
inv αt12 = inv αt + [2 (x1 + x2) (z1 + z2)] tg α =
= 00149 + [2 (0 + 0) (32 + 58)] 036 = 00149; αt12 = 20° (17)
где - x1 и x2 – коэффициенты смещения выбираемые по ГОСТ 16532-70.
Межосевое расстояние.
А12 = [m (z1 + z2) 2] · [cosαt cosαt12 cos] =
= [225 (32 + 58) 2] · [094 094 1] = 10125 мм (18)
Диаметры вершин зубьев.
da1 = d1 + 2ha1 = 675 + 2 18 = 711 мм (19)
da2 = d2 + 2ha2 = 1305 + 2 18 = 1341 мм
ha1 = ha2 = fm = 0 (20)
Диаметры впадин зубьев.
df1 = d1 - 2hf1 = 675 - 2 236 = 6278 мм (21)
df2 = d2 - 2hf2 = 1305 - 2 236 = 12578 мм
hf1 = hf2 = (f + 025) m = (08 + 025) 225 = 236 мм (22)
Sn1 = 05 m + 2x1 tg α = 05 314 225 + 2 0 0364 = 353 мм (23)
Sn2 = 05 m + 2x2 tg α = 05 314 225 + 2 0 0364 = 353 мм
Наибольший радиус кривизны профиля зуба колеса.
ρ1max = 2 = 2 = 321 мм (24)
Радиус кривизны в точке начала активной части профиля зуба колеса.
ρ1 = А12 sinαt12 – 2 = 10125 0342 – 2 = 754 мм
Определяем число зубьев долбяка
где d0 – номинальный диаметр чашечного долбяка мм;
m – модуль колеса мм;
Определяем высоту головки и ножки зуба в исходном сечении.
haОисх = haFисх = (ha’+c’)m (26)
где ha’ – коэффициент высоты;
c’ - коэффициент радиального зазора;
haОисх = haFисх = (08 + 03) 225 = 2475 мм
Диаметр окружности выступов в исходном сечении.
dA0исх = dо+2 haОисх (27)
dA0исх = 80 + 2 · 2475 = 8495 мм
Диаметр окружности впадин в исходном сечении.
dF0исх = dо-2 hFОисх (28)
dF0исх = 80 – 2 · 2475 = 7505 мм
Толщина зуба по дуге делительной окружности в исходном сечении.
Sоисх = m2 + ΔS (29)
где ΔS – утолщение зуба рейки мм.
Sоисх = 314 · 225 2 + 014 = 3673 мм
Минимальная толщина зуба на окружности выступов.
Принимаем по ГОСТ 9323-79 значение заднего угла при вершине в осевом сечении αв = 6°; γв = 5°
Определяем толщину зуба на окружности выступов в исходном сечении.
Sаоисх = 2rАОисх(Sоисх2rО + invαO - invαAОисх) (31)
где rАоисх – радиус окружности выступов мм;
Sаоисх = 2 · 42475 (3673 2 · 40 + 00149 – 00418) = 16 мм
cosαAОисх = rво rAОисх (32)
где rво – радиус основного цилиндра долбяка мм
cosαAОисх = 37588 42475 = 0885; αAОисх = 27°45
Радиус основного цилиндра долбяка.
где αo - угол наклона зуба нарезаемого колеса.
rво = 40 · cos20° = 37588 мм
Определяем расстояние от торца долбяка до исходного сечения.
Определяем диаметр окружности выступов в плоскости переднего торца.
dao = daoисх + 2А tgαв (35)
dao = 8495 + 2 · 137 · 0105 = 8783 мм
Определяем диаметр окружности впадин в плоскости переднего торца.
dFo = dFoисх + 2А tgαв (36)
dFo = 7505 + 2 · 137 · 0105 = 7793 мм
Конструктивные параметры чашечного долбяка принимаем по ГОСТ 9323-79.
- высота долбяка В = 30 мм;
- диаметр посадочного отверстия d = 3175 мм;
- ширина ступицы b1 = 10 мм;
- диаметр ступицы d3 = 60 мм;
- диаметр выточки d2 = 50 мм.
Производим проверку принятой величины А.
Проверка отсутствия cрезания головки зубьев колеса.
ρl = а10 sinα010 – 05 (37)
Межосевое расстояние долбяка и нарезаемого колеса.
а 10 = (d1 + d0) cos αt 2 cos αt10 = (675 + 80) 094 2 094 = 7375 мм
ρl = 7375 0342 – 05 088 = 1265 мм
ρаl = 05dа1 sinαа1 = 05 711 0342 = 1216 мм
ρl > ρаl – условие выполняется
наружных поверхностей
Исходные данные для расчета приведены в таблице 3.
Таблица 3 – Исходные данные
Длина обработки L мм
Эскиз обрабатываемой поверхности детали представлен на рисунке 2.
Рисунок 2 – Эскиз поверхности детали
1 Определяем подъем на зуб протяжки [3 стр.287].
2 Определяем профиль стружечной канавки:
Определим объемный коэффициент заполнения впадины по [3 стр.277 табл.107]..
Площадь сечения впадины между зубьями должна отвечать условию
k = Fв Fc = 2 5 (38)
где Fв – площадь сечения впадины мм;
Fс – площадь сечения металла снимаемого одним зубом мм
Определим площадь сечения металла снимаемого одним зубом.
Fс = 120 · 005 = 6 мм2
Определим площадь сечения впадины.
Fв = 35 · 6 = 21 мм2
Пользуясь справочной литературой [3 стр.276 табл.106] выбираем ближайшее большее значение Fв для криволинейной формы впадины зуба Fв = 2825 мм.
Исходя из полученного значения Fв принимаем параметры впадины зубьев протяжки.
Шаг протяжки t = 14 мм;
Глубина впадины h = 6 мм;
Длина задней поверхности b = 4 мм;
Радиус закругления дна впадины r = 30 мм;
Радиус закругления задней поверхности зубьев R = 10 мм.
3 Определим максимальное число одновременно работающих зубьев.
zmax = 120 14 + 1 10
4 Определим параметры режущих зубьев протяжки.
Передний угол γ = 10º;
Задние углы режущих и калибрующих зубьев αр = 10º; αк = 5º;
Угол наклона зубьев к оси протяжки = 75º.
5 Определим коэффициенты длины и ширины.
где В – ширина протягивания мм
Определим Кв для первой секции протяжки:
Кв = 50 14 · 3732 = 096
Определим Кв для второй секции протяжки:
Кв = 20 14 · 3732 = 038
Определим Кв для третьей секции протяжки:
Кв = 30 14 · 3732 = 057
6 Определим силу резания
Т.к. оба коэффициента найденные выше не являются целыми числами то для нахождения силы резания необходимо определить общую наибольшую длину режущих кромок одновременно находящихся в работе для каждой секции протяжки.
Для всех секций секции:
Сила резания определяется по формуле.
Pzmax = Р Σbmax (45)
где Р – сила резания на 1 мм длины лезвия Н
Pzmax1 = 235 · 445 = 104575 Н 1046 кН
Pzmax2 = 235 · 197 = 46295 Н 463 кН
Pzmax3 = 235 · 280 = 65800 Н 658 кН
7 Высоту первого зуба принимаем равной 20 мм.
Высоту каждого последующего зуба определяем путем прибавления к высоте предшествующего зуба величины Sz.
Количество и размеры режущих зубьев заносим в таблицу на чертеже протяжки.
Принимаем число калибрующих зубьев равным zк = 5.
Определяю длину секций протяжки.
L = t (zр – 1 + zк) + 12t + B ctg (46)
L1 = 14 (31 – 1 + 5) + 12 · 14 + 50 · 0268 = 520 мм
L2 = 14 (31 – 1 + 5) + 12 · 14 + 20 · 0268 = 512 мм
L3 = 14 (31 – 1 + 5) + 12 · 14 + 30 · 0268 = 515 мм
Общая длина протяжки Lo = L1 + L3 = 520 + 515 = 1035 мм
9 Исходя из длины протяжки и силы резания определяем модель станка на котором возможна обработка данной протяжкой.
Выбираем станок горизонтально – протяжной модели 7А510.
Номинальная тяговая сила станка Р = 105 кН;
Наибольшая длина хода L = 1250 мм.
По данным расчета строим чертеж протяжки.
При выполнении данной курсовой работы я научился проектировать круглый фасонный резец чашечный долбяк для нарезания прямозубых колес и комплект протяжек для обработки фасонной поверхности а также закрепил навыки применения специальной литературы.
Проектирование металлорежущего инструмента является одной из основных дисциплин при подготовке инженеров по специальностям «Технология машиностроения» и «Металлорежущие станки и инструмент».
Ее изучение должно дать нам сведения необходимые при разработке современных технологических процессов и проектировании станков и инструментов.
Список использованных источников
Справочник технолога машиностроителя. В 2 т. Т.2. Под ред. А.Г. Косиловой и Р.К. Мещерякова. - М.: Машиностроение 1986. - 496с.
Руководство по курсовому проектированию металлорежущих инструментов. Под ред. Г.Н. Кирсанова - М.: Машиностроение 1986 - 288 с.
Нефедов Н.А. Осипов К.А. Сборник задач по резанию металлов и режущему инструменту. - М.: Машиностроение 1990.- 448с.
Основы резания материалов и режущий инструмент. П.И.Ящерицын М.Л.Еременко Н.И.Жигалко. – 2-е изд. доп. и перераб. – Мн.: Выш.школа 1981. – 560с.
Ведомость.cdw

режущих инструментов
Ведомость курсовой работы
КР-02069964-151002-33-11
Пояснительная записка
Резец фасонный круглый
Документация текстовая
Документация графическая
Комплект протяжек.cdw

Материал режущей части секций - сталь Р18 ГОСТ19265-73
Материал корпуса протяжки - сталь 40Х ГОСТ4543-71
Неуказанные предельные отклонения :
Твердость режщих и калибрующих зубьев НRСэ 61 66
Профиль режущих зубьев (4:1)
Профиль калибрующих зубьев (4:1)