Проектирование режущего инструмента




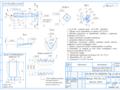
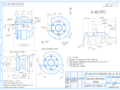
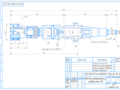
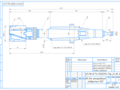
- Добавлен: 24.01.2023
- Размер: 4 MB
- Закачек: 0
Описание
Состав проекта
![]() |
![]() |
![]() |
![]() |
![]() |
![]() |
![]() ![]() |
![]() |
![]() |
![]() |
![]() ![]() ![]() |
![]() |
![]() |
![]() |
![]() ![]() ![]() |
![]() |
![]() ![]() ![]() |
![]() |
![]() |
![]() |
![]() |
![]() |
![]() ![]() ![]() |
![]() ![]() ![]() |
![]() ![]() |
![]() ![]() ![]() |
![]() |
![]() ![]() ![]() ![]() |
![]() ![]() ![]() ![]() |
![]() ![]() ![]() ![]() |
![]() ![]() ![]() ![]() |
![]() ![]() ![]() ![]() |
![]() ![]() ![]() ![]() |
![]() |
![]() ![]() ![]() ![]() |
![]() |
![]() |
![]() ![]() ![]() |
![]() ![]() ![]() |
![]() ![]() ![]() |
![]() |
![]() ![]() |
![]() |
![]() |
![]() ![]() ![]() ![]() |
![]() ![]() ![]() |
![]() |
![]() ![]() ![]() ![]() |
![]() ![]() |
![]() |
Дополнительная информация
рисунок 1.4.frw

рисунок 1.3.frw

рисунок 1.2.frw

Титульный лист.docx
Кафедра «Технология и оборудование машиностроения»
Пояснительная записка
по режущему инструменту
Нижний Новгород 2012
2.1.frw

рисунок 1.1.frw

Зенкерование D2-28.cdw

Конус морзе 4 АТ-7 ГОСТ 25557-90
КП-РИ-НГТУ-151001(10-ТМу-2)-28-12
Оправка для насадных зенкеров и разверток
Втулка переходная 191831064
Сверление D4-28.cdw

Конус морзе 3 АТ-7 ГОСТ 25557-90
КП-РИ-НГТУ-151001(10-ТМу-2)-28-12
Втулка переходная 191831064
Рассверливание D3-28.cdw

Конус морзе 4 АТ-7 ГОСТ 25557-90
КП-РИ-НГТУ-151001(10-ТМу-2)-28-12
ИБ для расверливания
Втулка переходная 191831064
Растачивание D1-28.cdw

КП-РИ-НГТУ-151001(10-ТМу-2)-28-12
Оправка расточная 191421244
Развётывание D-28.cdw

Конус 40 АТ-4 ГОСТ 15945-82
КП-РИ-НГТУ-151001(10-ТМу-2)-28-12
ИБ для развёртывания
Оправка для насадных разверток
Втулка переходная 191834064
Фрезерование канавки-28.cdw

КП-РИ-НГТУ-151001(10-ТМу-2)-28-12
Фреза фасонная дисковая
Патрон цанговый 191113040
резец фас.cdw

Допуски на свободные размеры IT122
Шероховатость обработки фасонной поверхности - Ra 3.2
Характер опоры заготовки - без ролика
КП-РИ-НГТУ-151001(10-ТМу-2)-79-12
Покрыть TiN толщиной 0
Неуказанные предельные отклонения h12
*Размеры для справок.
Схема установки резца
Данные о детали и заготовки
Фрагмент 1.9.frw

рисунок 1.7.frw

Пояснительная записка.doc
1 Подготовка исходных данных для расчета профиля резца
Характер опоры заготовки – без ролика.
Допуски на свободные размеры – по 5 классу точности (система отверстия).
Шероховатость обработки фасонной поверхности – 5 (Ra32)
Производство деталей – массовое
Производство инструмента – мелкосерийное
Материал заготовки – сталь 45
Модель станка – 1265М
Эскиз детали и ее размеры приведены на рисунке 1.1
Рисунок 1.1 Эскиз детали
1.2 Подготовка исходных размеров детали к профилированию
Профиль детали рекомендуется описывать в системе координат Х – Y таким образом чтобы ось Х совпадала с осью детали а начало координат совпадала с правой торцевой линей.
Рабочий чертёж детали может иметь различную простановку размеров но их нужно пересчитать из цепной в координатную.
На чертеже детали не все размеры указаны с отклонениями а имеются так называемые свободные размеры на них необходимо назначить допуски.
Рекомендуется для диаметральных свободных размеров назначить отклонения по 12 квалитету со знаком «-» а для линейных принять симметричные отклонения по 12 квалитету со знаком «±».
Переведём квалитет из старой системы допусков и посадок в новую.
Эскиз детали с переведёнными посадками и проставленными допусками приведён на рисунке 1.2
Рисунок 1.2 Эскиз детали с переведенными посадками и проставленными отклонениями всех размеров.
Длинновые размеры детали как видно из рисунка 1.2 составляют одну размерную цепь.
В этой цепи размеры 25±005 не удовлетворяет требованию координатной простановки длинновых размеров от одной базы – правого торца детали.
Рассмотрим размерную цепь состоящую из размеров 35±0125 25±005.
±005– размер уменьшающий;
±0125 – размер увеличивающий;
А0- замыкающий размер.
Для удобства расчёта профиля все остальные размеры с ассиметричными отклонениями пересчитываем на размеры с симметричными отклонениями.
Определённые размеры представлены на рисунке 1.3
Рисунок 1.3 Эскиз детали с координатной простановкой размеров.
1.3 Выбор узловых точек на профиле детали
Для проведения коррекционных расчётов профиля резца необходимо на профиле детали выбрать ряд узловых точек и определить их координаты Х и Y. В качестве узловых обычно выбираются точки пересечения соседних участков профиля.
На рисунке 1.4 показан эскиз детали с координатами узловых точек вдоль оси Х.
Рисунок 1.4 Эскиз детали с координатами узловых точек
Определяем координаты узловых точек. Полученные при определении
координаты точек профиля величины сводим в таблицу1.1.
Таблица 1.1 Расположение узловых точек профиля детали
Наименьший радиус детали ri принимаем при расчёте профиля резца в качестве базового rб = 149475 мм
На рисунке 1.5 представлена схема обработки детали фасонным резцом когда ширина резца точно соответствует ширине детали. Участок лезвия резца у правого конца будет интенсивно нагреваться и изнашиваться. Резец часто придётся перетачивать нести значительные потери производительности и средств на эксплуатационный расход. Тоже самое можно заметить и у левого конца лезвия резца. Во избежание описанных потерь такие слабые участки лезвия усиливают вводя дополнительные режущие кромки. На правой стороне лезвия введен участок “а” а на левой “в” и “в”. Величину “а” принимают равной 2÷5 мм.
Рисунок 1.5 Дополнительные лезвия фасонного резца
Размеры и формы левого дополнительного участка лезвия принимаются из соображений облегчения работы отрезного резца которым деталь будет отрезаться от прутка из которого она изготовляется. При этом в = 70 мм.
Величина « в1+в» должна превышать протяжённость участка под отрезку на заготовке 1÷15 мм.
Выберем дополнительные узловые точки и покажем их на рисунке 1.6
Рисунок 1.6 Дополнительная узловая точка
Координаты дополнительной узловой точки
2Материал габаритные размеры и геометрические параметры резца
2.1Материал для изготовления резца
В качестве инструментально режущего материала примем быстрорежущую сталь Р6М5 ГОСТ 19265-73 [16с.75табл.29].
2.2Габаритные размеры резца
Определяем наибольшую глубину обрабатываемого профиля.
где – наибольший и наименьший диаметры обрабатываемых поверхностей.
Определяем ширину резца
- длина дополнительного левого участка лезвия
а- длина дополнительного правого участка лезвия.
Размеры круглого фасонного резца.
2.3 Геометрические параметры резца
Задний угол и передний угол назначаются в зависимости от условий отработки для базовой точки резца наиболее удалённый у круглого от его центра.
Задний угол [2с.15табл.2.3]
Передний угол [2с.15табл.2.3]
При наружной обработки фасонными резцами с передними углами во избежание вибраций не следует допускать чрезмерного снижения режущих кромок по отношению к оси обрабатываемой детали. Это снижение не должно превышать (01÷02)наибольшего обрабатываемого радиуса детали.
Проверим допустимость выбранного угла
где - передний угол в град.;
- наибольший обрабатываемый радиус детали;
- наибольшая глубина обрабатываемого профиля.
Проверяем выбранный угол
– условие выполняется.
где - передний угол резца;
– минимальный радиус детали при наружной обработке;
– радиус детали в рассматриваемой точке.
где - угол заострения резца (в различных точках профиля принимает разные значения).
где - расчётная величина равная расстоянию от оси резца до продолжения его передней поверхности;
- радиус резца в произвольно выбранной точки i профиля.
Углы фасонного резца в сечении
Для создания условий резания .
Расстояние от центра резца по плоскости передней грани.
где - наибольший радиус фасонного резца.
где - задний угол резца
- передний угол резца
Расстояние от оси круглого резца до плоскости П0.
Проверим расчёт углов лезвия в любой точке рабочего профиля фасонного резца.
- условие резания выполняется.
3Коррекционный расчет профиля резца
3.1Схема и алгоритм расчёта
Наличие передних и задних углов фасонных резцов приводит к несовпадению глубин профилей изменяемых у круглых резцов в радиальном сечении с глубинами профиля обрабатываемой детали.
На рисунке 1.7 приведена схема коррекционного расчёта резца.
Рисунок 1.7 Схема коррекционного расчёта фасонного резца
Схемы расчёта и расчётные формулы сведены в таблицу 1.2.
Таблица 1.2 Расчет профиля круглого фасонного резца
Формулы и обозначения
Номера узловых точек
Суммарный угол в базовой точке
Расстояние от центра детали до плоскости передней грани
Передний угол в текущей
Расстояние от текущей точки
Промежуточная величина
Глубина профиля резца на
Вспомогательная величина
Продолжение таблицы 1.2
Расстояние от центра резца до
до плоскости передней грани
Суммарный угол в текущей
Радиус резца в текущей точке
Глубина профиля в радиальном
Задний угол в текущей точке
3.2 Расчёт угловых размеров профиля фасонного резца для обработки конических участков детали
Угловые размеры профиля резца определяем по формуле:
где угол профиля резца
измеренное перпендикулярно боковым плоскостям расстояние между узловыми точками обозначающими начало и конец наклонного участка профиля резца.
Рисунок 1.8 Схема к определению углового размера профиля фасонного резца.
3.3 Погрешности конических участков деталей обработанных фасонными резцами
Точно очерченные конические участки профиля детали при их обработке фасонными резцами образуются когда соответствующие режущие кромки полностью совпадают с прямолинейными образующими создаваемых конусов. У круглых резцов сами режущие кромки конических участков всегда имеют выпуклость возрастающую с увеличением угла их заточки . Образующие конических участков деталей обрабатываемых круглыми фасонными резцами искажаются как при нулевом переднем угле (только под влиянием выпуклости режущей кромки) так и при (под влиянием вогнутости режущей кромки и её расположение на различном уровне по отношению к оси детали). Возникающие искажения могли быть компенсированы путём изготовления резцов с соответствующим образом искажёнными на конических участках режущими кромками. Изготовление таких резцов представляет большие трудности и практического применения не получило. При обработки круглыми фасонными резцами в силу указанных выше причин эти искажения значительно больше и могут достигать величин . Оценку возникающих погрешностей при обработке круглыми резцами конических участков детали можно производить аналитически.
где - фактический и теоретический радиусы средней точки конуса детали мм.
Рисунок 1.9 Схема к определению погрешности обработки конического участка детали
4Разработка рабочего чертежа
Допуски на основные конструкционные элементы резца.
Резец круглый как и любая деталь машины изготавливается на металлорежущих станках. Точность изготовления профиля фасонного резца имеет определённые границы. Величины допусков приемлемые для производственных условий составляют:
а) на диаметральные размеры - (004 005) мм;
б) на осевые размеры – (002 003) мм.
Профильно-шлифовальные станки при изготовлении фасонных резцов позволяют достичь точности в 002 мм. Дальнейшее превышение точности представляет определённые трудности.
Допуски на осевые размеры рекомендуется принимать в пределах 13 – 12 допуска наименьшего осевого размера. Для больших размеров разрешается увеличивать допуски против вычисленных значений исходя из величины исходных допусков.
В нашем примере длинновой размер с наименьшим допуском . Взяв 13 допуска этого размера получим:
Для размера мм величину допуска расширяют:
или в виде отклонений (±004)
Таким образом длинновые размеры с отклонениями имеют значения:
Допуск по наружному диаметру круглого фасонного резца принятому за исходный при расчётах должен назначаться исходя из условий взаимозаменяемости фасонных резцов.
Диаметр D6 круглых резцов выдерживают с допуском равным удвоенному допуску настроечного размера. Требование к точности различных участков неодинаково а элементарные лезвия образующие фасонный профиль могут совершать движение подачи только одновременно. При точных расчётах за основу принимают ступень детали с наименьшим допуском.
В качестве настроечного размера принимаем ступень:
Определим глубины профиля детали относительно настроечной поверхности
Величины допусков на размеры профиля передаваемые резцом на деталь определятся из выражений:
Или в виде отклонения ±00125мм.
Или в виде отклонения ±0 мм.
Разделив наименьшую величину допуска 02 получаем 0- неприемлемое значение допуска для размера . Для расширения полей допусков на глубины профиля резца ужесточим допуск настроечного размера например 004.
Или в виде отклонения ±00425мм.
Или в виде отклонения ±003 мм.
Разделив наименьшую величину допуска 0062 получаем 003- приемлемое значение допуска для размера .
Рациональна следующая простановка размеров:
Допуски на заточку и установку резца устанавливают в зависимости от принятой точности размеров глубины профиля резца. На угол принимают ориентировочно допуск в минутах равным выраженному в микрометрах наименьшему допуску на изготовление глубины профиля резца со знаком минус.
В нашем примере наименьший допуск на изготовление глубины профиля резца равен 30 мкм погрешности углов составят:
где - погрешность расстояния от центра резца до плоскости передней грани;
- погрешность угла заточки резца в градусах;
- погрешность в превышении оси резца над осью детали.
Величина погрешности от установки резца определяется по формуле:
Для случая когда смещение вершины резца происходит в направлении перпендикулярной к основной плоскости:
В случае когда смещение происходит под углом в основной плоскости или по дуге окружности радиуса :
где - погрешность обрабатываемого резцом диаметра;
- погрешность положения вершины резца в направлении перпендикулярном к основной плоскости.
5 Условия рациональной эксплуатации фасонного резца
Станок 1265М-полуавтомат токарный многошпиндельный горизонтальный прутковый.
На рисунке 1.10 приведена двухопорная державка для работы на автоматах и полуавтоматах. Одна из опор может перемещаться по направляющей шпонке 4 укреплённой на подвижной опоре 3 с помощью штифта [17с.245].
Рисунок 1.10 Державка для круглых фасонных резцов
-корпус; 2-опорный болт; 3-подвижная опора; 4-шпонка;
-регулировочный сектор; 6-регулировочный винт.
При установке фасонного резца в рабочее положение (см. рисунок 1.11) основная точка его профиля Оп располагается в плоскости П0. Резец должен быть повёрнут в сечении С0 вокруг точки Оп на величину запроектированного заднего угла α0 измеряемого между плоскостью резания и задней поверхностью резца. Необходимый для создания α0 поворот резца достигается соответствующим расположением резца в державке перемещением оси резца Ор в положение Ор2 на расстояние h0 от его оси до плоскости П0. После соответствующей установки резца для образования заднего угла на нём образуется одновременно и требуемый передний угол.
Задний угол фасонного резца зависит только от его установки в рабочее положение а передний угол зависит как от заточки так и от установки резца.
Непосредственная установка круглых фасонных резцов для их заточки под углом 0 а также изменение у них углов 0 представляет некоторые трудности: поэтому используется вспомогательная величина H0 равная расстоянию от оси резца до положения его передней плоскости.
Величины 0 0 и H0 связаны между собой зависимостями:
Рисунок 1.11 Схема установки фасонного резца в рабочее положение
При обработке детали с шириной резания 49мм диаметром прутка 50мм подача составит 002 ммоб а скорость резания 73 ммин. [6с.61]
Обработка фасонным резцом выполняется при вращении детали и поперечной подачи резца обработка производительна и точна кроме того допускает большое количество переточек.
В процессе резания металлов фасонным резцом в результате затраченной работы возникает тепло. Основным источником тепла при резании является работа: затраченная на пластические деформации в срезаемом слое и в слоях прилегающих к обработанной поверхности и поверхности резания; затрачиваемая на преодоление трения по передней и задней поверхности резца.
Тепло переходящее в резец размягчает его и делает менее износостойким. В местах контакта стружки с резцом и резца с заготовкой тепло оказывает большое влияние на состояние трущихся поверхностей на точность обработки. Для отвода тепла от режущего инструмента и заготовки применяется смазочные охлаждающие жидкости: МР-1 МР-2у МР-4 при подаче 8-12 лмин.
При переточке фасонного резца необходимо восстановить остроту режущей кромки и воспроизвести геометрические параметры режущей части и обеспечить получение при обработке переточенным резцом заданной поверхности детали. Переточка производится по передней поверхности.
Проектирование машинного метчика
Таблица 2.1 Исходные технологические данные операции резьбонарезания
Условные обозначения принятые в таблице 2.1:
Тип участка детали с резьбовым отверстием - см. рисунок 2.1
ОМ – обрабатываемый материал
МС – тип металлорежущего станка
МЦ – многоцелевой фрезерно-сверлильно-расточной центр
Для всех вариантов исходных данных машинные метчики ММ проектируются для нарезания резьбы в заготовках в условиях крупносерийного или мелкосерийного автоматизированного производства.
Рисунок 2.1. Эскиз детали
2 Конструктивная разновидность машинного метчика
При нарезании точных резьб (4Н 5Н) используются метчики с винтовыми стружечными канавками с углом наклона =100 150. При нарезании правой резьбы в сквозных отверстиях применяются метчики – с левым направлением канавок. По сравнению с прямыми канавками обеспечивается более надёжный вывод стружки из зоны резания повышает плавность работы метчика и улучшает качество резьбы. Принимаем =100.
Рисунок 2.2 Эскиз метчика
Схема срезания припуска – генераторная .
Рисунок 2.3 Схема срезания припуска
3 Выбор марки инструментального режущего материала
По заданию обрабатываемый материал легированная конструкционная сталь – 38ХС. По рекомендациям [4с.14табл.1] в качестве инструментального материала берём Р6М5. На режущую и калибрующую часть метчика наносим износостойкое покрытие нитрида титана TiN толщиной 0003 0005 мм с целью увеличения стойкости инструмента в 15-2 раза.
4 Выбор конструктивных и геометрических параметров метчика
4.1 Выбор числа зубьев метчика
Число зубьев метчика выбирается в зависимости от обрабатываемого материала и диаметра нарезаемой резьбы. [4с.15табл.2]
Для принимаем Z = 3.
4.2 Выбор формы и размеров канавки
Форма канавки должна отвечать следующим требованиям:
а) обеспечивать свободное размещение стружки образующейся при нарезании особенно при нарезание резьб в глухих отверстиях;
б) содействовать лёгкому отводу стружки;
в) не допускать налипание и спрессовывания стружки в канавке.
Для выбираем профиль канавок трёхперых метчиков №5. [6с.17табл.4]
Рисунок 2.4 Профиль канавок трёхпёрого метчика
4.3 Определение длины заборной части l2 и угла в плане φ
а = 005 [7с.26табл.2]
Угол заборной части (4 с.20):
Длина заборной части (4 с.20):
– диаметр переднего торца метчика (4 с.19);
где – диаметр сверла под резьбу (4 с.53)
С целью сокращения номенклатуры инструмента принимаем
4.4 Определение длины калибрующей части l1 и обратной конусности
Длина калибрующей части:
где l3 =28мм [4с.21табл.8]– длина рабочей части
Для уменьшения трения калибрующей часть должна иметь обратную конусность по всему профилю резьбы величина которой выбирается по таблице 9 [4с.21]
При обработке стали 38ХС обратная конусность на 100 мм длины равна 008 мм.
4.5 Выбор переднего угла заднего угла и величины затылования К
Учитывая тяжёлые условия работы метчика передний угол как правило берут положительным. Для обработки 38ХС рекомендуется брать угол
Задний угол =. [7с.27табл.3]
Величина падения затылка измеряемая на радиусе проведённом в вершину соседнего зуба
Метчики со шлифованным профилем резьбы могут быть изготовлены всех классов точности. Шлифование профиля резьбы повышает качество режущих лезвий уменьшает вероятность налипания металла на боковые поверхности резьбы метчика и способствует повышению стойкости машиного метчика. У метчиков со шлифованным профилем резьбы целесообразно производить также затылование по калибрующей части с К=0015 002 при затылование по всей ширине зуба.
4.6 Назначение степени точности метчика
Степень точности метчика выбирается в зависимости от точности нарезаемой резьбы по данным таблицы [3с.14табл.4]. Для данной степени точности резьбы 5Н принимаем 2 класс точности метчика-К2.
4.7 Определение размеров профиля резьбы метчика
Рисунок 2.5 Исполнительные размеры метчика
Для степени точности К2 принимаем исполнительные размеры метчика согласно [4с.55].
Предельные отклонения угла профиля
Так как по исходным данным после нарезания резьбы наносится покрытие то исполнительные размеры корректируем в соответствии с p =0008 мм.
4.8 Определение размеров хвостовика
Размеры хвостовика следует определять по таблице 10 [4с.22]. Хвостовики метчиков предназначены для быстросменных патронов делают в исполнении 2.
Рисунок 2.6 Эскиз хвостовика
Для экономии инструментального материала хвостовик делаем из стали 40Х ГОСТ4543 – 73 с последующей сваркой с рабочей частью.
Расстояние l4 от переднего торца заборной части метчика до места сварки с хвостовиком равно:
4.9 Определение общей длины метчика
Общая длина метчика рассчитывается по формуле
где – величина выхода калибрующей части метчика из изделия
– длина нарезаемой резьбы с полной глубиной профиля
– расстояние от вспомогательного инструмента до изделия;
– длина вхождения метчика во вспомогательный инструмент
Рисунок 2.7 Размеры метчика
4.10 Рациональные условия эксплуатации машинного метчика
На рисунке 2.8а показана конструкция патрона предназначенного для нарезания резьбы метчиками М6-М16 в сквозных и глухих отверстиях.
В корпусе 1 размещено устройство осевой компенсации состоящие из муфты 2 шариков 3 пружин 4 и 5.
Корпус 1 муфта 2 и хвостовик 6 с гайкой 13 крепится при помощи пальца 7. Шарики 3 служат для передачи крутящего момента и являются направляющими качения осевого перемещения муфты в корпусе. Для предохранения шариков от выпадания на корпус 1 установлена обойма 9 зафиксированная при помощи кольца 8.
На конце муфты 2 имеется замковое устройство для метчикодержателя 14 состоящее из замка 10 шариков 11 и пружины 12.
Осевая компенсация «растяжения» реализуется в патроне тогда когда шаг нарезаемой метчиком резьбы больше чем рабочая подача станка. В этом случае метчик вместе с метчикодержателем 14 и муфтой 2 выдвигается из корпуса 1 скользя по шарикам 3.
При выводе метчика из резьбового отверстия пружина 4 осуществляет возврат муфты 2 в исходное положение. При осевом перемещении шарики 3 перекатываются по пазам корпуса 1.
Осевая компенсация «сжатия» реализуется в патроне тогда когда прекращается перемещение (осевое и вращательное) метчика а рабочая подача и вращение патрона продолжаются. В этом случае метчик вместе с метчикодержателем 14 и муфтой 2 вдвигаются внутрь корпуса 1 скользя по шарикам 3.
Предохранение метчиков от поломок при повышении допустимой величины крутящего момента осуществляется с помощью муфты размещённой в сменном метчикодержателе.
Сменный метчикодержатель (рисунок 2.8б) состоит из корпуса 1 и предохранительного устройства которое состоит из сепаратора 2 сухаря 3 шариков 4 упругого элемента 5 и резьбовой пробки 6.
При помощи винта 6 пробка фиксируется от самоотвинчивания в процессе работы. Пробкой 10 регулируется крутящий момент при котором срабатывает предохранительное устройство метчикодержателя.
В корпусе 1 метчикодержателя смонтировано замковое устройство для крепления метчиков состоящее из замка 7 шариков 8 и пружин 9.
Выступы служат для передачи крутящего момента от патрона к сепаратору 2 метчикодержателя [5 с.131].
Рисунок 2.8 –а) Патрон с цилиндрическим регулируемым хвостовиком; б) Сменный метчикодержатель
Скорость резания при нарезании резьбы метчиками должна быть небольшой; это удлиняет срок службы метчика и предотвращает заклинивание стружки. Рекомендуются следующие скорости резания: для стали — 3—15ммин для чугуна бронзы и алюминия — 6—22ммин.
Охлаждение должно быть обильным. В качестве смазочно-охлаждающих жидкостей рекомендуются: для нарезания деталей из стали — сульфофрезол для деталей из чугуна бронзы и алюминия — эмульсия или керосин.
Проектирование инструментальной наладки
Рисунок 3.1. Конструктивные параметры участка детали
Таблица 3.1 Исходные технологические данные операции обработки круглого отверстия на многоцелевом станке
Условные обозначения принятые в таблице 3.1:
D-номинальный диаметр обрабатываемого отверстия;
IT-обозначение квалитета точности отверстия диаметром D;
ОМ- марка обрабатываемого материала;
НВ – твёрдость обрабатываемого материала;
Δ- точность позиционирования просверленного отверстия;
D1- номинальный диаметр предварительно обработанного отверстия после выполнения перехода растачивания отверстия;
IT1- обозначение квалитета точности отверстия диаметром
D2- номинальный диаметр предварительно обработанного отверстия после выполнения перехода зенкерования отверстия;
D3 - номинальный диаметр предварительно обработанного отверстия после выполнения перехода рассверливания отверстия;
D4 - номинальный диаметр предварительно обработанного отверстия после выполнения перехода сверления отверстия;
ТХ – тип хвостовика спирального сверла для предварительного сверления отверстия диаметром
НК – номер конуса конического отверстия с конусностью 7:24 по ГОСТ15945-82 в шпинделе станка.
2 Проектирование технологического процесса для инструментальной наладки
Сформируем набор ТП для обработки заданного отверстия:
Так как допуск на координату Δ> 015 мм и длина вылета спирального сверла из инструментодержателя 8 10D отверстие сверлим без предварительного центрования специальным центровочным сверлом.
Значит 1 переходом будет сверление отверстия D4H12=24Н12. В качестве РИ выбираем сверло спиральное с коническим хвостовиком [8 с.225-228 табл.74]:
d=24мм общая длина L=280 мм длина стружечной канавки Lk=160 мм. Форма режущей кромки сверла – двухплоскостная с плоской подточкой поперечной кромки. Так как обрабатываемый материал СЧ21 с НВ=180 угол 2φ=1180 [13с.108табл.3.3]. Хвостовик – конус Морзе 3. Вспомогательным инструментом будет втулка переходная с хвостовиком конусностью 7:24 и внутренним конусом Морзе 3[10 c.334 табл.29].
переходом будет рассверливание отверстия D3Н12=45Н12. РИ будет сверло спиральное с коническим хвостовиком. Форма режущей кромки сверла – двухплоскостная с плоской подточкой поперечной кромки и двойной заточкой с прямолинейной переходной режущей кромкой. Так как обрабатываемый материал СЧ21 с НВ=180 угол 2φ=1180 [13с.108табл.3.3]. Рассчитаем длину сверла [12 с.8]:
где Lk- длина стружечной канавки мм
LД- длина участка сверла от стружечной канавки до шейки мм
Lш- длина участка шейки мм
L1-выбирают по ГОСТ2557-82 для принятого конуса Морзе хвостовика.
Длина стружечной канавки рассчитывается по формуле:
где L- длина обрабатываемого отверстия мм. L=98мм.
L - дополнительная длина рабочей части сверла с учетом переточекмм:
L з=15D0 – для свёрл точного исполнения класса А и А1мм.
Lп- величина перебега сверла мм:
Lн- величина недобега максимально сточенного сверла для обеспечения выхода стружки из стружечной канавки мм.
Lн=05 D0=05*45=225 мм.
С целью обеспечения наибольшей жесткости сверла принимают наименьшую стандартную длину стружечной канавки с учетом расчетной длины стружечной канавки по таблице 5.2 [9 с.216]. Определяем -средняя серия.
В зависимости от диаметра сверла выбираем номер конуса Морзе 4 [14 с.372 табл.10.10]. По ГОСТ 25557-82 для конуса Морзе 4:
L1=124 мм D1=316 мм. Тогда
Вспомогательным инструментом будет втулка переходная с хвостовиком конусностью 7:24 и внутренним конусом Морзе 4.
переходом будет зенкерование отверстия D2H11=52H11.В качестве РИ выбираем зенкер 52h8 с L=55мм и d=22мм. [8 с.241 табл.85]. Вспомогательным инструментом будут оправка для насадных зенкеров и развёрток и переходная втулка с хвостовиком конусностью 7:24 и внутренним конусом Морзе 4.
и 5 переходом будет фрезерование кольцевой канавки и фаски 1×45º на наружном торце круглого отверстия в качестве РИ выбираем фрезу фасонную дисковую трёхстороннюю с цилиндрическим хвостовиком специальную.
Ширина срезаемого слоя:
Принимаем длину угловых режущих кромок на 25 мм больше чем ширина фаски канавки внутри отверстия 5+25=7.5 мм.
Вспомогательным инструментом будет патрон цанговый.
переходом будет расточка отверстия диаметром D1 с полем допуска Н9.
В качестве РИ выбираем резец державочный расточной с СМП. а=10мм.
Вспомогательным инструментом будет оправка расточная с микрорегулировкой резца для чистового растачивания [10 с.337табл. 34].
переходом будет развёртывание отверстия диаметром D=54Н8. В качестве РИ выбираем развёртку сборную насадную с привёрнутыми ножами оснащенная пластинами из твёрдого сплава по ГОСТ11176-80[11с.202-203 табл.3.112]. Вспомогательным инструментом будут оправка качающаяся для насадных развёрток с коническим хвостовиком и переходная втулка с хвостовиком конусностью 7:24 и внутренним конусом Морзе 4 [10 с.334табл. 29].
Полученные переходы занесём в таблицу 3.2.
Таблица 3.2. Технологические переходы обработки круглого отверстия на многоцелевом станке
Элементы инструментального блока
Вспомогательный инструмент
Сверлить отверстие диаметром D4H12 предварительно
Сверло спиральное с коническим хвостовиком
Рассверлить отверстие диаметром D3H12 предварительно.
Втулка переходная с хвостовиком конусностью 7:24 и внутренним конусом Морзе
Зенкеровать отверстие диаметром D2H11
Зенкер насадной оснащённый пластинами из твёрдого сплава
Оправка для насадных зенкеров и развёрток. Втулка переходная с хвостовиком конусностью 7:24 и внутренним конусом Морзе
Продолжение таблицы 3.2
Фрезеровать кольцевую канавку и образовать фаску на наружном торце отверстия с размерами 1х45 относительно диаметра D
Фреза фасонная дисковая с цилиндрическим хвостовиком специальная
Расточить отверстие диаметром D1 с полем допуска Н9
Резец державочный расточной с СМП
Оправка расточная с микрорегулировкой резца для чистового растачивания.
Развернуть отверстие диаметром D с полем допуска Н8
Развёртка сборная насадная с привёрнутыми ножами оснащенная пластинами из твёрдого сплава по ГОСТ11176-80
Оправка качающаяся для насадных развёрток с коническим хвостовиком и переходная втулка с хвостовиком конусностью 7:24 и внутренним конусом Морзе
Сборник заданий на курсовую работу по металлорежущим инструментам. Под редакцией Максимова М.А. Учебное пособие. – Горький: ГПИ 1971
Проектирование фасонных резцов. Методическое пособие для студентов. НГТУ. Составитель– Ю.Ю.Немцов Н.Новгород 2008.
Проектирование машинных метчиков. Методические рекомендации и задание на проектирования. Ю.Ю Немцов. – Н.Новгород: НГТУ 2007.
Зотов Ю.Н. Проектирование резьбообразующих инструментов. Горький: ГГУ 1978.
Маслов А. Р. Приспособления для металлорежущего инструмента: Справочник. 2-е изд. исправ. и доп. Библиотека инструментальщика – М.: Машиностроение 2002.
Режимы резания металлов. Справочник. Изд.3-е переработанное и дополненное. Под редакцией Ю.В. Барановского М. «Машиностроение» 1972.
Режущий инструмент. Метод. материалы по выполнению курсового проекта для студентов спец. 151001 очно-заочной и заочной форм обучения Авт. Немцов Ю. Ю. – Н.Новгород: НГТУ 2011. 18 с.
Кузнецов Ю.И. Оснастка для станков с ЧПУ: справочник – 2-е изд. перераб. и доп. Ю.И. Кузнецов А.Р. Маслов А.Н. Байков – М.:Машиностроение 1990.
Справочник конструктора – инструментальщикапод ред. В.И. Баранчикова - М.:Машиностроение 1994.
Обработка материалов резанием: справочник технолога А.А. Панов В.В. Аникин Н.Г.Бойм и др.; под общ. ред. А.А. Панова- М.:Машиностроение 1988.
Металлообрабатывающий твёрдосплавный инструмент: справочник В.С. Самойлов Э.Ф. Эйхманс И.А.Фальковский и др.;- М.:Машиностроение 1988.
Исследование и проектирование спиральных сверл. Методические
указания и задания к лабораторной работе по дисциплине “Инструментальное обеспечение машиностроительного производства” для студентов спец. 120200 и 120100 НГТУ Ю.Ю.Немцов. – Н.Новгород 1998.
Инструмент для станков с ЧПУ многоцелевых станков и ГПСИ.Л.Фадюшин Я.А.Музыкант А.И.Мещеряков и др. – М.: Машиностроение 1990.
Справочник инструментальщика И.А.Ординарцев Г.В.Филиппов
А.Н.Шевченко и др.; Под общ. ред. И.А.Ординарцева.–Л.: Машиностроение 1987.
Проектирование инструментальной наладки для обработки круглого отверстия на многоцелевом станке: методические указания и задания на проектирование для студентов обучающихся по направлению 657800 (151000) «Конструкторско-технологическое обеспечение машиностроительных производств»НГТУ; сост. Ю.Ю. Немцов.-Н.Новгород2006.-12с.
Юликов М.И. Горбунов Б.И. Колесов Н.В. Проектирование и производство режущего инструмента. - М.: Машиностроение 1987
Грановский Г.И Панченко К.П Фасонные резцы. М. «Мащиностроение» 1975. 309с.
Проектирование фасонного резца4
1 Подготовка исходных данных для расчета профиля резца4
1.1 Исходные данные4
1.2 Подготовка исходных размеров детали к профилированию4
1.3 Выбор узловых точек на профиле детали6
2Материал габаритные размеры и геометрические параметры резца8
2.1Материал для изготовления резца8
2.2Габаритные размеры резца8
2.3 Геометрические параметры резца9
3Коррекционный расчет профиля резца11
3.1Схема и алгоритм расчёта11
3.2 Расчёт угловых размеров профиля фасонного резца для обработки конических участков детали15
3.3 Погрешности конических участков деталей обработанных фасонными резцами15
4Разработка рабочего чертежа17
5 Условия рациональной эксплуатации фасонного резца20
Проектирование машинного метчика23
2 Конструктивная разновидность машинного метчика23
3 Выбор марки инструментального режущего материала24
4 Выбор конструктивных и геометрических параметров метчика24
4.1 Выбор числа зубьев метчика24
4.2 Выбор формы и размеров канавки24
4.3 Определение длины заборной части l2 и угла в плане φ25
4.4 Определение длины калибрующей части l1 и обратной конусности26
4.5 Выбор переднего угла заднего угла и величины затылования К26
4.6 Назначение степени точности метчика26
4.7 Определение размеров профиля резьбы метчика27
4.8 Определение размеров хвостовика27
4.9 Определение общей длины метчика28
4.10 Рациональные условия эксплуатации машинного метчика29
Проектирование инструментальной наладки32
2 Проектирование технологического процесса для инструментальной наладки33
Список литературы:37
метчик.cdw

2 Предельное отклонение
шага резьбы относится к
расстоянию между двумя любыми
витками на длине до 25 мм.
КП-РИ-НГТУ-151001(10-ТМу-2)-28-12
65 HRC - режущая часть
Рабочую часть цианировать на глубину 0
Обратная конусность по внутреннему
среднему и наружному
Сварка контактная стыковая оплавлением
Центровые отверстия притереть
Предельные отклонения среднего диаметра резьбы метчика
проверять в начале калибрующей части
Профиль стружечной канавки контролировать по шаблону
Затыловать по профилю на всей длине калибрующей части
величина затылования 0
Неуказанные предельные отклонения H14
Маркировать М12 кл.2
Остальные ТТ по ГОСТ 3449-84
Рабочая часть Р6М5 ГОСТ19265-73
Хвостовик 40Х ГОСТ4543-73
Профиль резьбы (5:1)
Фрезерование фаски-28.cdw

Рекомендуемые чертежи
Свободное скачивание на сегодня
- 24.01.2023