Проектирование привода с двухступенчатым редуктором




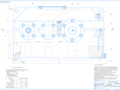
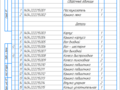
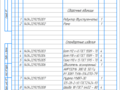
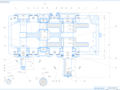
- Добавлен: 24.01.2023
- Размер: 1 MB
- Закачек: 0
Описание
Проектирование привода с двухступенчатым редуктором
Состав проекта
![]() |
![]() |
![]() ![]() ![]() ![]() |
![]() |
![]() |
![]() |
![]() |
![]() ![]() ![]() ![]() |
![]() ![]() ![]() ![]() |
![]() ![]() ![]() ![]() |
![]() |
![]() ![]() ![]() |
![]() ![]() ![]() |
![]() ![]() ![]() ![]() |
![]() ![]() ![]() ![]() |
![]() |
![]() |
![]() ![]() ![]() |
![]() ![]() ![]() ![]() |
Дополнительная информация
сборка спереди.cdw

приводная станция.cdw

колесо мое.cdw

Копия Редуктор22222.spw

сборка сверху.cdw

вал мой.cdw

приводная.spw

Рекомендуемые чертежи
- 02.10.2019
- 25.10.2022
- 24.01.2023
- 24.01.2023
- 20.04.2023
- 10.03.2024