Проектирование привода по заданной схеме




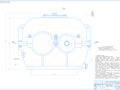
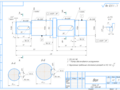
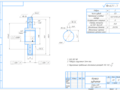
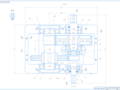
- Добавлен: 24.01.2023
- Размер: 1 MB
- Закачек: 0
Описание
Состав проекта
![]() |
![]() |
![]() ![]() ![]() ![]() |
![]() ![]() ![]() ![]() |
![]() ![]() ![]() |
![]() |
![]() ![]() ![]() ![]() |
![]() ![]() ![]() ![]() |
![]() ![]() ![]() ![]() |
![]() ![]() ![]() ![]() |
Дополнительная информация
Лист3.cdw

Лист1.cdw

Вал.cdw

Колесо.cdw

Крышка.cdw

Шкив.cdw

Рекомендуемые чертежи
- 02.10.2019