Спроектировать привод малой мощности по заданной схеме



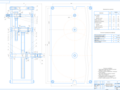
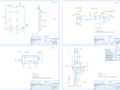

- Добавлен: 24.01.2023
- Размер: 449 KB
- Закачек: 0
Узнать, как скачать этот материал
Подписаться на ежедневные обновления каталога:
Описание
Спроектировать привод малой мощности по заданной схеме
Состав проекта
![]() |
![]() ![]() ![]() ![]() |
![]() ![]() ![]() |
![]() ![]() ![]() |
![]() ![]() ![]() ![]() |
Дополнительная информация
Контент чертежей
детали.frw

B14_3.CDW

эскиз 13_4.cdw

Рекомендуемые чертежи
- 23.08.2014
- 23.08.2014
- 23.08.2014
- 23.08.2014
- 23.08.2014
Свободное скачивание на сегодня
Обновление через: 8 часов 59 минут
Другие проекты
- 29.08.2014