Спроектировать привод конвейера по схеме




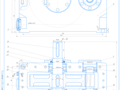
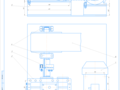
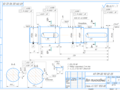
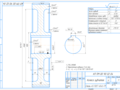
- Добавлен: 24.01.2023
- Размер: 452 KB
- Закачек: 0
Описание
Состав проекта
![]() |
![]() ![]() ![]() ![]() |
![]() ![]() ![]() |
![]() ![]() ![]() ![]() |
![]() ![]() ![]() ![]() |
![]() ![]() ![]() ![]() |
![]() ![]() ![]() ![]() |
![]() ![]() ![]() ![]() |
Дополнительная информация
крышка глухая28900.cdw

3_курс_курсовой_прикладная_механика.doc
«БЕЛОРУССКИЙ ГОСУДАРСТВЕННЫЙ
ТЕХНОЛОГИЧЕСКИЙ УНИВЕРСИТЕТ»
кафедрамеханика материалов и конструкций
ПОЯСНИТЕЛЬНАЯ ЗАПИСКА
по дисциплине прикладная механика
Темапривод конвейера
подпись дата инициалы и фамилия
должность ученая степень ученое звание подпись дата инициалы и фамилия
(подпись) (инициалы и фамилия)
Спроектировать привод конвейера по заданной схеме
– рама; 2 – электродвигатель; 3 – муфта упругая; 4 – редуктор; 5 – клиноременная передача; 6 –конвейер ленточный
Исходные данные для расчета:
Мощность на выходе Pв = 55 кВт;
Частота вращения на выходе nв = 100 мин-1;
Угол наклона α = 15º;
Срок службы Lh =10500 часов.
Расчетно-пояснительная записка к курсовому проекту содержит: 32 страницы; 3 рисунка; 1 таблицу; 2 литературных источника; 3 приложения; 3 листа формата А1 (иллюстративного материала)
РЕДУКТОР ЗУБЧАТАЯ ПЕРЕДАЧА КЛИНОРЕМЕННАЯ ПЕРЕДАЧА ЦИЛИНДРИЧЕСКАЯ КОСОЗУБАЯ ПЕРЕДАЧА МУФТА ВАЛ ЭЛЕКТРОДВИГАТЕЛЬ ШЕСТЕРНЯ КОЛЕСО ЗУБЧАТОЕ ПОДШИПНИК ШПОНКА ДОПУСКАЕМОЕ НАПРЯЖЕНИЕ СМАЗКА
Цель проекта – спроектировать привод к конвейеру с заданной мощностью на выходном валу частотой вращения этого вала углом наклона клиноременной передачи и сроком службы привода.
Выполнение проекта включает: выбор электродвигателя и кинематический расчет привода; проектировочный и проверочный расчет зубчатой передачи редуктора; проектировочный и проверочный расчет клиноременной передачи; проектировочный расчет валов подшипников и элементов корпуса; выбор муфты; составление расчетных схем валов определение реакций в опорах и построение эпюр изгибающих и крутящих моментов; проверочные расчеты подшипников валов и шпонок; выбор способа смазки и смазочных материалов; описание последовательности сборки и разборки редуктора; выбор норм точности изготовления деталей и их сопряжений; разработку графической части проекта.
Выбор электродвигателя и кинематический расчет привода6
Расчет зубчатой передачи9
Расчет клиноременной передачи12
Проектный расчет валов. Эскизная компоновка14
Основные элементы корпуса редуктора15
Расчетные схемы валов редуктора17
Проверочные расчеты22
1 Проверочный расчет подшипников22
2 Проверочный расчет шпонок23
3 Проверочный расчет валов24
Нормирование точности геометрических размеров28
Список использованной литературы30
Приложение А. Компоновка . .29
Приложение Б. Спецификация .. 30
Приложение В. Спецификация .. 31
Привод – устройство предназначенное для приведения в движение подвижных элементов рабочих машин. Энергия необходимая для приведения в движение машины может быть передана от вала электродвигателя подвижной части машины с помощью различных дополнительных устройств т.к. в большинстве случаев режим работы двигателя не совпадает с режимом работы рабочей машины. Механическая энергия от двигателя машине может передаваться и преобразовываться при помощи различных видов передач таких как зубчатые передачи (цилиндрические конические планетарные) червячные передачи ременные передачи цепные передачи фрикционные передачи.
Привод обычно представляет собой совокупность передач передающих механическую энергию. Передачи обычно выполняют следующие функции: понижают (повышают) угловую скорость; повышают (понижают) вращающий момент; преобразуют один вид движения в другой; реверсируют движение; распределяют энергию двигателя между исполнительными механизмами. Привод конвейера состоит из следующих элементов: электродвигатель клиноременная передача редуктор муфта; барабан конвейера.
Редуктор является одним из ключевых элементов привода. Его выполняют в виде отдельного агрегата в закрытом корпусе которого размещается одна или несколько передач. Расчет и проектирование редукторов включает в себя следующие этапы: выбор материалов; проектировочный расчет передач; проектировочные расчеты остальных элементов редуктора; проверочные расчеты передач; проверочные расчеты остальных элементов редуктора; выбор способа смазки и смазочных материалов; разработка сборочного чертежа редуктора и рабочих чертежей деталей.
Редуктор в приводе предназначен для понижения угловой скорости и увеличения крутящего момента. Зубчатые передачи обладают рядом преимуществ перед ременными или цепными а именно: малыми габаритными размерами высоким коэффициентом полезного действия высокой надежностью и долговечностью работы постоянным передаточным числом возможностью применения в широком диапазоне крутящих моментов и окружных скоростей.
Расчет зубчатых передач производится в соответствии с ГОСТ 21354-75. Основными видами расчетов являются расчеты на контактную выносливость активных поверхностей зубьев и расчеты зубьев при изгибе. Так как основной причиной выхода из строя закрытых зубчатых передач является усталостное контактное выкрашивание то проектный расчет зубчатых передач выполняют на контактную выносливость и выносливость при изгибе.
Выбор электродвигателя и кинематический расчет привода
Требуемая мощность на выходе Pв = 55 кВт; частота вращения на выходе
nв = 100 мин-1; угол наклона α = 15º; срок службы Lh = 10500 часов.
Рисунок 1.1 – Кинематическая схема привода конвейера
– рама; 2 – электродвигатель; 3 – муфта упругая; 4 – редуктор;
– клиноременная передача; 6 – конвейер ленточный
Коэффициент полезного действия привода определим по формуле:
где зп - к.п.д. закрытой цилиндрической зубчатой передачи (зп = 096);
оп - к.п.д. открытой клиноременной передачи (оп = 096);
м - к.п.д. муфты (м = 098;
пк - к.п.д. пары подшипников (пк = 099) (табл. 2.1 1)
Определим требуемую мощность электродвигателя с учетом потерь возникающих в приводе (кВт)
Определим Uор ориентировочное значение общего передаточного числа привода приняв ориентировочное значение передаточного числа зубчатой передачи Uзп = 63 клиноременной передачи Uоп = 2 (табл. 2.3 1)
Определим ориентировочное значение частоты вращения вала двигателя
По табл. К9 1 выберем электродвигатель 4А132М6У3 с мощностью
Pном = 75кВт и частотой вращения вала nном =1455 мин-1.
Двигатель 4А132М6У3 с мощностью Pном = 75кВт будет работать с недогрузкой
Определим общее передаточное число привода:
Уточним передаточное число открытой передачи
Вычислим частоты вращения валов привода
Вычислим численные значения мощностей на каждом из трех валов.
Вычислим численные значения крутящих моментов на каждом из валов.
Результаты расчетов кинематических параметров привода приведены в таблице 1.1
Таблица 1.1 - Результаты расчетов кинематических параметров привода
Расчет зубчатой передачи
По таблице 3.1 1 выберем материал зубчатых колес. Принимаем материал - сталь 45 и термообработка:
шестерня – улучшение: HB 269 302
колесо – улучшение: HB 269 302
Определим допускаемые контактные напряжения [c.33 2]
[s]H = (18HBср+67)KHL (2.1)
где KHL=1–коэффициент долговечности при длительной эксплуатации
[s]H1 =(18×300+67)1=607 МПа
[s]H2 =(18×280+67)1=571 МПа
Определим допускаемые напряжения изгиба
[s]F1 = 103·300 = 309 МПа
[s]F2 = 103·280 = 2884 МПа
Определим межосевое расстояние
где Kа = 43 – для косозубых передач
yа = 036 – коэффициент ширины венца
Принимаем по ГОСТ 6636–69; aw = 160 мм
Определим модуль зацепления:
d2 – делительный диаметр колеса
b2 –ширина венца колеса
b2=036·160=576 принимаем b2=58 мм
По ГОСТ 9563-60 принимаем m = 2 мм
Определим угол наклона линии зуба min
min=arcsin(35·m b2) (2.7)
min=arcsin(35·2 58)=69319º
Определим числа зубьев цилиндрической передачи.
Число зубьев шестерни тогда число зубьев колеса
z2= ZΣ -z1 = 159-22 = 137
Фактическое передаточное число Uф = 13722=623 отклонение 11%
Уточним величину угла наклона
=arccos(ZΣ·m 2·aw) (2.9)
=arccos(159·2 2·160)=64092º
Определим основные геометрические параметры передачи
Делительные диаметры
d1=m·z1cos = 2·220993=4428мм
d2=m·z2cos = 2·1370966=27572мм
Диаметры вершин зубьев
dа1=d1+2m = 4428+2·2=4828мм
dа2=d2+2m = 27572+2·2=27972мм
df1=d1-24m=4428-24·2=3948мм
df2=d2-24m=27572-24·2=27092мм
Определим расчетное контактное напряжение
где К – вспомогательный коэффициент К = 376
Ft – окружная сила в зацеплении
Ft =(2·T2·103) d2 (2.14)
Ft =(2·5415·103) 27572 = 3928 Н
КHv = 101 в зависимости от окружной скорости
Назначаем 9-ую степень точности
Передача недогружена недогрузка составляет что допустимо
Проверим напряжения изгиба зубьев шестерни и колеса:
где КFα = 1; КFv = 104; КF = 1
YF1 иYF2–коэффициент формы зуба
При эквивалентном числе зубьев
Определим силы действующие в зацеплении:
Ft1= Ft2=2T2d2 = 2×5415×10327572 = 3928 Н
Fr = Ft×tgacos (2.20)
Fr1 = Fr2 = Ft×tgacos = 3928· tg 20cos64092 =1439 Н
где α - угол зацепления (α = 20o)
Fа1 = Fа2 =Ft×tg=3928×0112=440 Н
Расчет клиноременной передачи
По рис. 5.2.1 выберем ремень сечения Б и минимально допустимый диаметр ведущего шкива dmin=125мм Ввиду отсутствия жестких требований к габаритам для увеличения тяговой способности и КПД передачи а также долговечности ремней принимаем стандартный расчетный диаметр малого шкива
Определим диаметр большого шкива:
d2=231·140(1-001)=32016мм
принимаем стандартное значение по табл.К40 1 d2=315мм
Уточняем передаточное отношение:
u = d2d1(1–e) (3.2)
u = 315140×(1–001) = 227.
Отклонение от принятого передаточного 17% что допустимо
Найдем предварительно межосевое расстояние:
a = 055(d1+d2) +h(3.3)
где h = 105 мм высота профиля ремня сечения Б
a = 055×(140+315) +105= 26075 мм.
Определим расчетную длину ремня:
L = 2a+05p(d1+d2)+(d2–d1)2(4a) (3.4)
L = 2×26075+05p(140+315)+(315-140)2(4×26075) = 1265 мм.
принимаем L = 1400 мм.
Уточним значение межосевого расстояния
а=18(2L-(d1+d2)+((( 2L-(d1+d2))2-8(d2-d1)2)0.5)(3.5)
а=18(2·1400-(140+315)+((( 2·1400-(140+315))2-8(315-140)2)0.5)=3313 мм
Угол обхвата малого шкива:
a1 = 180–57(d2–d1)a (3.6)
a1= 180–57×(315–140)3313 = 150°> 120°
V = pd1n160000 (3.7)
V = p×0140×145560 = 1067 мс.
Определим частоту пробегов
U = 106714=76515 с-1
Определим окружную силу:
Ft = 6279×1031067 = 589 Н.
Определим допускаемую мощность передаваемую одним клиновым
[Рп] = [Р0] СpCαСlСz (3.10)
где Cα=089; Сp=1; С Сz=095 табл. 52 1
[Рп] = 28×089·1×091×095 = 215 кВт.
Определим количество клиновых ремней
Предварительное натяжение одного ремня:
F0 = 850 Pном Сl (z·v Cα Сp)(3.12)
F0 = 850×6279 0.91(3·1067 089 1 )= 171 Н
Fоп = 2zF0sina12(3.13)
Fоп = 2·3·171sin150°2 =991 Н.
Проверочный расчет по максимальным напряжениям в сечении ведущей ветки
max= 1+ и+ v []p(3.14)
А =138мм2 – площадь сечения клинового ремня
Еи=80 100МПа – модуль продольной упругости
ρ=1250кгмм3- плотность материала ремня
v=1250·10672 10-6=014 МПа
max= 195+ 6+ 014=81 []p
Проектный расчет валов. Эскизная компоновка
В проектном расчете выберем заниженные допускаемые напряжения на кручение при этом меньшее значение []к = 20 МПа - для быстроходного вала а большее значение []к = 30 МПа - для тихоходного вала. Определим геометрические параметры ступеней валов.
Диаметры выходных участков вала определяют по формуле;
где Т - крутящий момент на валу Нмм;
[]к - пониженные допускаемые напряжения кручения МПа.
Полученное значение диаметра вала округляют по ГОСТ 6639-69. Быстроходный вал: мм
Примем диаметры валов под подшипники.
Быстроходный вал: d1п = 35 мм; тихоходный вал: d2п = 50 мм. На быстроходном валу шестерню будем выполнять заодно с валом. Примем диаметр для посадки зубчатого колеса на тихоходный вал d2к = 55 мм. Остальные элементы валов определим графически при разработке компоновки.
В зацеплении присутствуют осевые силы сил и согласно рекомендациям табл. 7.2.1 предварительно выберем подшипники шариковые однорядные по ГОСТ 8338-75. Для быстроходного вала - подшипники легкой серии 207: d = 35 мм; D = 72 мм; В = 17 мм; Сr = 255 кН Сor = 137 кН. Для тихоходного вала - подшипники легкой серии 210: d = 50 мм; D = 90 мм; В = 20 мм; Сr = 351 кН
На основании расчетов на миллиметровой бумаге вычертим эскизную компоновку редуктора которая позволит определить расстояния между точками приложения усилий в зацеплении и реактивными усилиями в подшипниках необходимые для их построения эпюр изгибающих моментов (приложение А).
Основные элементы корпуса редуктора
Корпус редуктора предназначен для размещения в нем деталей передачи обеспечения смазки восприятия усилий возникающих при работе а также предохранения деталей передачи от повреждений и загрязнений. Наиболее распространенным материалом для литых корпусов является серый чугун СЧ 15 ГОСТ 1214-85. Редукторы общего назначения для удобства сборки и разборки конструируют разъемными. Плоскость разъема обычно проходит через оси валов параллельно плоскости основания.
В крышке корпуса для заливки масла контроля сборки и осмотра редуктора при эксплуатации предусматривается смотровое окно. В нижней части основания корпуса предусматривается маслосливное отверстие закрываемое резьбовой пробкой и отверстие для установки маслоуказателя. Для подъема и транспортировки крышки основания корпуса или редуктора в целом предусматривают крючья проушины или рым-болты.
Определим толщину стенок редуктора по формуле:
Примем значение толщины стенок корпуса и крышки редуктора = 8 мм.
Определим диаметры болтов (винтов) редуктора по табл. 10.17.1: примем для фундамента болты с резьбой М14 для болтов соединяющих крышку корпуса с основанием редуктора
а)у подшипников примем болты М 12.
б)прочие болты примем М 10.
Болты крепящие крышку подшипников с корпусом примем М 8 крепящих смотровую крышку с корпусом примем М 6
По таблице 10.18 1 определим размеры фланцев корпуса с учетом того что для соединения будут использоваться болты:
-- у подшипниковых узлов: ширина фланца К = 32 мм; расстояние от оси болта до стенки С = 16 мм; диаметр отверстия do = 13 мм; диаметр планировки D0 = 20 мм
- у прочих: ширина фланца К = 30 мм; расстояние от оси болта до стенки С = 16 мм; диаметр отверстия do = 11 мм; диаметр планировки Do = 18 мм.
Зазор между наиболее выступающими элементами передач и стенками корпуса или другими деталями редуктора: X = (11 - 12) = 88 - 96 мм. Толщина лап 235 = 20 мм.
Для соединения выходного тихоходного вала редуктора и приводного вала барабана ленточного конвейера установленных как правило на общей раме обычно применяют упругие втулочно-пальцевые муфты. Эти муфты обладают достаточными упругими свойствами и малым моментом инерции для уменьшения пусковых нагрузок на соединяемые валы. Выберем упругую втулочно-пальцевую муфту которая получила большое распространение благодаря простоте конструкции и удобству замены упругих элементов.
Основной характеристикой для выбора муфты является номинальный вращающий момент (Т) установленный стандартом. Муфты выбирают по расчетному моменту (Тр) который должен быть в пределах номинального:
где Т1 - вращающий момент на соответствующем валу редуктора;
К = 13 - коэффициент учитывающий режим работы.
Тр = 5415·13 = 704 Нм.
В соответствии с полученным значением а также с учетом диаметров соединяемых валов выберем муфту 710-45-1.1-45-П.2-УЗ ГОСТ 21424-93 с моментом Т = 710 Нм.
Радиальная сила вызванная радиальным смещением определяется по соотношению:
где Δr - радиальное смещение составляющее для выбранной муфты 03 мм;
СΔr - радиальная жесткость муфты которая составляет 6140 Нмм
FM = 6140·04 = 2456 Н.
Расчетные схемы валов редуктора
Составим расчетные схемы валов редуктора определим опорные реакции и построим эпюры изгибающих и крутящих моментов по правилам сопротивления материалов.
Расчетная схема быстроходного вала приведена на рис. 7.1.
Исходные данные Fr1 = 1439 Н; Ft1 = 3928 Н Fа1 = 440 Н d1 = 44 мм Fоп =991Н;
Fопу =Fоп ·sin 15=256Н Fопx =Fоп ·cos 15=957Н расстояния между характерными точками указаны на схеме в миллиметрах.
Рис. 7.1. Расчетная схема быстроходного вала
Вертикальная плоскость ZY.
Определим опорные реакции
RDy·116+Fr1·58 +Fа1·22 +Fопу· 199=0
RDy=(-1439·58-440·22-256·199)116 = -1242Н
-RCy·116-Fr1·58+Fа1·22+Fопу ·83=0
RCy=(440·22-1439·58+256·83)116=-453Н
RCy+RDy+Fr1+ Fопу= 0
-453-1242+1439+256=0
Построим эпюру изгибающих моментов относительно оси Х в точках 1 – 4:
Мх2 = RCy 0058= -263 Н·м;
Мх2 = RDy ·0058+ Fопу ·0141= -359 Н·м;
Мх3 = Fопу· 0083= 213 Н·м
Горизонтальная плоскость ZХ.
Fопх ·199+ RDх·116 - Ft1· 58 = 0;
RDх=(-957·199+3928·58)116= 322Н
Fопх ·83-RCх·116+ Ft1· 58 = 0;
RCх =(957·83 + 3928·58)116=2649 Н
Fопх +RCх+ RDх - Ft1= 0;
Построим эпюру изгибающих моментов относительно оси Y в точках 1 – 4:
Мy3 = Fопх ·0083=794 Н·м
Построим эпюру крутящих моментов относительно оси Z :
Определим суммарные радиальные реакции
Определим максимальный суммарный изгибающий момент в опасных сечениях
Расчетная схема тихоходного вала приведена на рис. 7.2.
Исходные данные Fм =2456 Н; Fr2 = 1439 Н; Ft2 = 3928 Н Fа2 = 440 Н
d2 = 276мм расстояния между характерными точками указаны на схеме в миллиметрах.
Вертикальная плоскость ZY
RAy ·118-Fr2·59 + Fа2·138 = 0
RAy = (1439·59-440·138)118= 205Н
-RBy ·118+Fr2·59 +Fа2·138 = 0
RBy = ( 1439·59+ 440·138)118= 1234Н
Мх2 = RAy ·0059 = 121 Н·м;
Мх2 = RВy ·0059 = 728 Н·м;
-Fм ·133+ RАх·118 + Ft2 ·59 = 0;
RAх=(2456·133-3928·59)118=804Н
Рис. 7.2. Расчетная схема тихоходного вала
- Fм ·241- RBх·118- Ft2 ·64= 0;
RBх=(-2456·251-3928·59)118=-7188Н
Fм +RBх+ RAх + Ft2= 0;
Му2 = RАх ·0059 =474 Н м;
Му3 = Fм ·0133 =327 Н·м
Мкр =Мz =Т2=5415 Н·м
1 Проверочный расчет подшипников
Проверим пригодность подшипников 207 быстроходного вала Сr = 255 кН Сor = 137 кН. Реакции в подшипниках: R1 = 2688 Н; R2 = 1283 Н. Частота вращения вала n = 630 мин-1. Требуемая долговечность Lh = 10500 часов.
Определим соотношение RаVR и сравним с коэффициентом е (V - коэффициент вращения который равен 1 при вращении внутреннего кольца подшипника). Ra – осевая сила в зацеплении по табл. 9.6 1 Ra= Fa=440Н
Определим отношение RаС0r=44013700=0032 по таблице 9.2 1 находим коэффициент е = 023. По соотношению RаVR1е выбираем формулу и определяем эквивалентную нагрузку для более нагруженного подшипника
где Кб - коэффициент безопасности который примем равным 12;
Кт - температурный коэффициент который при температуре менее 100°С равен 1.
RE = 2688·1·12·1 = 3226 Н.
Определим динамическую грузоподъемность:
Сгр Сг следовательно подшипник пригоден.
Определим долговечность подшипника
Долговечность обеспечена.
Проверим пригодность подшипников 210 тихоходного вала Сr = 351 кН
Сor = 198 кН. Реакции в подшипниках: R1 = 830 Н; R2 = 7293 Н. Частота вращения вала n = 100 мин-1. Требуемая долговечность Lh = 10500 часов.
Определим соотношение RаVR и сравним с коэффициентом е (V - коэффициент вращения который равен 1 при вращении внутреннего кольца подшипника). Ra – осевая сила в зацеплении по табл. 9.6 1 Ra= Fa=440Н RаVR2=4407293=006
Определим отношение RаС0r=44019800=0022 по таблице 9.2 1 находим коэффициент е = 02. По соотношению RаVR1е выбираем формулу и определяем эквивалентную нагрузку для более нагруженного подшипника
RE = 7293·1·12·1 = 8752 Н
2 Проверочный расчет шпонок
Призматические шпонки проверяют по напряжениям смятия по формуле:
где Т - крутящий момент на валу Н·мм;
d - диаметр вала в месте посадки шпонки мм;
Р - рабочая длина шпонки (1Р = 1 - b) мм;
[см] - допускаемое напряжение смятия.
При стальной ступице [см] = 160 МПа; при чугунной [см] = 90 МПа
b h и t1 - стандартные размеры шпонки.
Проверим шпонку на выходном конце быстроходного вала (d = 30 мм;
b = 8 мм; h = 7мм; t1 = 4 мм; 1 = 40 мм).
Проверим шпонки на тихоходном валу:
- под ступицей зубчатого колеса (d = 55 мм; b= 16 мм; h= 10 мм; t1 =6 мм; 1 = 56 мм)
- на выходном конце вала (d = 45 мм; b = 14 мм; h = 9 мм; t1 = 55 мм; 1 = 70 мм)
3 Проверочный расчет валов
Проверочный расчет валов на усталостную прочность осуществляют на совместное действие изгиба и кручения путем определения коэффициентов запаса прочности в опасных сечениях вала и сравнения их с допускаемым значением которое принимают [s] = 13-15. Коэффициент запаса прочности определяют по формуле:
где s и s коэффициенты запаса прочности соответственно по изгибу и кручению.
Поскольку шестерня выполняется заодно с валом то материал вала - сталь 40Х с твердостью 269-302 НВ имеющая высокие значения пределов выносливости при изгибе и кручении и коэффициенты запаса прочности в сечениях вала будут обеспечены поэтому наиболее целесообразно в первую очередь провести проверку тихоходного вала выполненного из менее прочной стали 45 твердостью 210 НВ в = 780 МПа -1 = 335 МПа у которого опасным является сечение 3 где действует максимальный изгибающий момент (M3 = 327 МПа). Концентрация напряжений обусловлена посадкой с натягом внутреннего кольца подшипника на вал.
Нормальные напряжения в сечении:
где W – осевой момент сопротивления сечения вала
Касательные напряжения в сечении:
где W – полярный момент инерции сечения вала
Определим коэффициенты концентрации напряжений
где К и К – эффективные коэффициенты концентрации;
Кd – коэффициент влияния абсолютных размеров;
Кf – коэффициент учета влияния шероховатости; Кf=11
По табл. 11.2 2 и табл. 11.3 2
Определим пределы выносливости в сечении:
где -1=058·-1 = 058·335=194 МПа
Определим коэффициенты запаса прочности
Определим общий коэффициент запаса прочности
Смазка зубчатых зацеплений и подшипников уменьшает потери на трение износ и нагрев деталей. По способу смазки зацеплений различают картерную и циркуляционную смазки.
Картерная смазка осуществляется путем окунания венцов зубчатых колес в масло заливаемое внутрь корпуса. Данный тип смазки применяют при окружных скоростях в зацеплениях до 12-15 мс. При смазывании окунанием в масляную ванну объем масла заливаемого в картер определяют из расчета 04-08 л масла на 1 кВт передаваемой мощности. В конических редукторах должны быть полностью погружены в масляную ванну зубья конического колеса.
По табл. 10.29 1 выберем сорт масла: индустриальное И-Г-А-46 ГОСТ 17479.4-87 с кинематической вязкостью 41 51 мм2с. Уровень масла будет контролироваться с использованием прозрачного круглого маслоуказателя.
Смазка подшипников может осуществляться двумя способами - разбрызгиванием из картера и пластичными мазями. Первый способ является более предпочтительным т.к. обеспечивает высокую стабильность смазывания меньшее сопротивление вращению способность отводить теплоту и очищать подшипники от продуктов износа.
Данный способ эффективен при окружных скоростях колес более 2-3 мс. В нашем случае окружная скорость (13 мс) не удовлетворяет этому условию по этому для смазки подшипников применяем пластичные смазки. Для защиты подшипников от попадания в них жидкого масла устанавливают специальные мазеудерживающие кольца на валах рядом с подшипниками. Для предотвращения вытекания смазочного материала из подшипниковых узлов и попадания в них пыли влаги в крышках подшипников устанавливают манжетные уплотнения.
Сборка редуктора после изготовления всех деталей осуществляется в следующей последовательности.
Шпонка под зубчатое колесо помещается в шпоночную канавку с использованием запрессовки после чего колесо напрессовывается на предусмотренный для его расположения участок тихоходного вала.
Подшипники перед установкой на валы предварительно нагревают в масляной ванне до температуры 80 - 100°С после чего немедленно одевают на предусмотренные под них участки валов предварительно таким же образом одевают распорную втулку на тихоходный вал. Далее запрессовывают шпонки в шпоночные канавки на выходных концах валов. После сборки валы размещают в соответствующие отверстия основания корпуса редуктора расположенные в его бобышках.
Перед сборкой корпуса его плоскость разъема обычно покрывают специальным герметиком а внутреннюю поверхность корпуса покрывают маслостойкой краской. После одевания крышки корпуса в предусмотренные отверстия забивают два конических штифта что позволяет центрировать все отверстия под соединительные болты. После этого крышку и основание корпуса стягивают винтами. Затем вставляют сквозные и глухие крышки с прокладками (с помощью прокладок путем подбора их толщины осуществляют регулировку зацепления) и распорными кольцами в отверстия бобышек корпуса и все крышки подшипников фиксируют винтами.
Для проверки правильности сборки механизма после сборки необходимо прокрутить быстроходный вал вручную несколько оборотов и при свободном вращении валов сборка считается выполненной правильно. В редуктор заливают масло через отверстие люка в крышке корпуса предварительно ввинтив в основание корпуса пробку и маслоуказатель. После заливки редуктора маслом привинчивают крышку люка в которую ввинчивают отдушину производят внешнюю покраску редуктора.
После полностью завершенной сборки редуктор подвергают обкатке на испытательном стенде согласно техническим условиям и после этого редуктор монтируют в привод. Разборка редуктора производится в последовательности обратной сборке.
Нормирование точности геометрических размеров
Одним из принципов конструирования и производства независимо изготовленных деталей и узлов обеспечивающих правильную сборку работоспособность и замену при ремонте без дополнительной обработки с соблюдением требований качества и экономичности является взаимозаменяемость. Для обеспечения взаимозаменяемости деталей и упорядочения их производства должны выполняться определенные требования предъявляемые к точности геометрических и других параметров качества устанавливаемых соответствующими стандартами.
Точность геометрических параметров оценивается точностью размеров форм и шероховатостью поверхностей и должна быть соответствующим образом задана в технической документации.
Экономически целесообразные предельные отклонения и допуски размеров деталей определяются единой системой допусков и посадок установленной ГОСТ25347-82 и ГОСТ 25346-82 и указываются на чертежах для всех размеров.
Посадки сопряженных поверхностей деталей обычно назначаются на основании расчетов или накопленного в промышленности опыта по методу аналогов. Согласно рекомендациям табл. 14.1 3 по методу аналогов примем следующие посадки:
-кольца подшипников на вал
-кольца подшипников в корпус Н7
-ступица колеса на вал Н7
-крышки подшипников в корпус
-полумуфта на вал Н7
-допуск вала под манжету d9.
При изготовлении деталей неизбежно возникают погрешности не только линейных размеров но и геометрической формы а также в относительном расположении осей поверхностей и конструктивных элементов деталей. Эти погрешности могут оказывать вредное влияние на работоспособность машин. Чтобы ограничить подобные отклонения на чертежах задают допуски формы и взаимного расположения поверхностей.
Примем согласно ГОСТ 2.308 - 77 для поверхностей деталей редуктора следующие предельные отклонения формы и расположения поверхностей.
Допуск перпендикулярности торца ступицы 0025 мм допуск параллельности шпоночного паза 002 мм допуск симметричности шпоночного паза 008 мм допуск цилиндричности отверстия ступицы колеса 0008 мм
(по 7-му квалитету табл. 13.10 - 13.12 2).
Для тихоходного вала в качестве базовых поверхностей примем участки вала для посадки подшипников.
Примем относительно базовых поверхностей допуски соосности этих участков а также участка для посадки зубчатого колеса 0002 мм допуски перпендикулярности буртика вала 0025 мм допуски параллельности шпоночных пазов 0002 мм допуски симметричности шпоночных пазов 0008 мм допуски цилиндричности посадочных участков вала 0008 мм под колесо подшипники и полумуфту (по 7-му квалитету табл. 13.10 - 13.12 1).
Для крышки подшипника в качестве базовой поверхности примем посадочную поверхность в корпус редуктора относительно которой примем допуск соосности отверстия под манжету 003 мм допуск перпендикулярности торцевых поверхностей крышки 004 мм (по 7-му квалитету табл. 13.11 - 13.12 1).
Действительные поверхности деталей отличаются от номинальных наличием неровностей образовавшихся при обработке поверхности и обусловленных колебанием инструмента и детали в процессе обработки дефектами обработки и другими причинами. Неровности у которых отношение шага к их высоте менее 50 называют шероховатостью. Шероховатость существенно влияет на эксплуатационные свойства деталей.
Параметры характеризующие шероховатость поверхности установлены ГОСТ 25142 - 82. Наибольшее применение в промышленности получил Ra - среднее арифметическое отклонение профиля в мкм определяемое на базовой длине. Отсчет ведется от средней линии имеющей форму номинального профиля поверхности.
Требования по шероховатости должны быть указаны для всех поверхностей однако если часть участков поверхности детали должны иметь одинаковую шероховатость ее указывают в правом верхнем углу. Знак шероховатости в скобках означает что все остальные поверхности детали кроме тех шероховатость которых обозначена имеют шероховатость указанную перед скобкой.
Согласно рекомендациям табл. 14.4 2 примем следующие шероховатости поверхностей деталей по Ra: посадочных участков тихоходного вала под подшипники колесо и полумуфту 08 мкм; отверстия крышки подшипника под манжету 08 мкм; отверстия ступицы зубчатого колеса 08 мкм торцов ступицы колеса и буртика вала 16 мкм; рабочих поверхностей шпоночных пазов контактных поверхностей крышки подшипника поверхности профиля зубьев колеса 16 мкм; поверхности вала под манжету 04 мкм; шероховатости прочих поверхностей деталей 63 мкм.
Список использованной литературы
Шейнблит А.Е. Курсовое проектирование деталей машин. -М.: Высшая школа 1991.
Дулевич А.Ф. Новиков С.А. Сурус А.И. Царук Ф.Ф. Курсовое проектирование. Учебно-методическое пособие. -Мн.: БГТУ 1997.
редуктор цилиндрический28900.cdw

Передаточное число редуктора u=6
Вращающий момент на тихоходном валу Т
Частота вращения быстроходного вала п
Технические требования
*Размеры для справок.
Редуктор залит маслом: индустриальное И-Г-А-46 ГОСТ 17479. 4-87.
Допускается эксплуатировать редуктор с отклонением от
горизонтального положения на угол до 5
. При этом должен быть
обеспечен уровень масла
достаточный для смазки зацепления.
колесо зубчатое28900.cdw

Нормальный исходный контур
Коэффициент смещения
Степень точности по ГОСТ 1643-81
Обозначение чертежа сопряженного
Сталь 45 ГОСТ 4543-71
Неуказанные радиусы 5 мм max.
привод28900.cdw

Мощность на выходе Р
Частота вращения на выходе n
Передаточное число привода u=14
*Размер для справок.
Привод обкатать без нагрузки в течение 1 часа
шум не допускается.
Натяжение ремней поз.15 регулировать с помощью болтов поз. 9.
Вал28900.cdw

крышка сквозная28900.cdw

Рекомендуемые чертежи
- 08.12.2021
- 24.01.2023