Проектирование оборудования гибкого промышленного модуля на базе многооперационного станка с ЧПУ модели 2А622МФ2




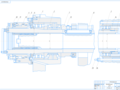
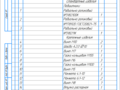
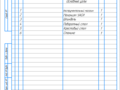
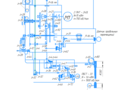
- Добавлен: 25.01.2023
- Размер: 14 MB
- Закачек: 0
Описание
Проектирование оборудования гибкого промышленного модуля на базе многооперационного станка с ЧПУ модели 2А622МФ2
Состав проекта
![]() |
![]() |
![]() |
![]() ![]() ![]() ![]() |
![]() ![]() ![]() ![]() |
![]() ![]() ![]() ![]() |
![]() ![]() ![]() |
![]() ![]() ![]() ![]() |
![]() ![]() ![]() |
![]() ![]() ![]() ![]() |
![]() ![]() ![]() |
![]() ![]() ![]() ![]() |
![]() ![]() ![]() ![]() |
![]() ![]() ![]() ![]() |
![]() ![]() ![]() |
![]() |
![]() ![]() ![]() |
![]() ![]() ![]() ![]() |
![]() ![]() ![]() |
![]() |
![]() ![]() ![]() |
![]() ![]() ![]() |
![]() ![]() ![]() |
![]() ![]() ![]() |
![]() ![]() ![]() |
![]() ![]() ![]() |
![]() ![]() ![]() |
![]() ![]() ![]() |
![]() ![]() ![]() |
![]() ![]() ![]() |
![]() ![]() ![]() |
![]() ![]() ![]() |
![]() ![]() ![]() |
![]() ![]() ![]() |
![]() ![]() ![]() |
![]() ![]() ![]() |
![]() ![]() ![]() |
![]() ![]() ![]() |
![]() |
![]() ![]() ![]() |
![]() ![]() ![]() |
![]() ![]() |
Дополнительная информация
4. ГПМ.cdw

Подъемно-транспортное устройство;
Ячейки для хранения заготовок
инструментальной и станочной оснастки;
Многооперационный станок;
Промежуточный транспортер для подачи стружки
на центральный транспортер 11
который заканчивается
Отделение переработки стружки и удаления СОЖ и стружки;
Наименование выполняемой
Время на выполнение операции
Снятие заготовки со стелажа
и транспортировка ее в
фрезерно-шлифовальный
фрезерный консольный
Шлифовальная операция
Транспортировка заготовки
до приставного стола ГПМ
Загрузка заготовки на
перемещение ее в рабочую
Обработка заготовки на
многоцелевом станке
Выгрузка заготовки на
из рабочей зоны станка
Погрузка детали на робокару
Транспортировка детали на
автоматизированный склад
1. Общий вид станка и техническая характеристика +3D +компановка.cdw

Рекомендованные параметры обработки
растачиваемых выдвижным шпинделем
наибольший диаметр сверла
Автоматически сменяемый инструмент:
Диаметр усиленного выдвижного шпинделя
Внутренний конус выдвижного шпинделя по ГОСТ 15945
Размеры рабочей поверхности
Наибольшие перемещения
Скорость быстрого перемещения:
наибольшее продольное перемещение
скорость быстрого перемещения
наибольшее усилие подачи
сила затяжки инструмента в шпинделе
Частота вращения шпинделя
Число ступеней регулирования
наибольшее вертикальное перемещение
Наибольшая масса обрабатываемой детали
Инструментальный магазин .
Число инструментов в магазине
Масса станка (без электрооборудования)
Шпиндельный узел.frw

№178920 ГОСТ20821-75
Гайка кольцевая М155
Гайка кольцевая М100
станок 3д 2.frw

Станок. спецификация.frw

Пояснительная записка
Инструментальный магазин
Фрагмент планировки ГПМ.frw

Фрагмент кинемат схемы стола.frw

Фрагмент общего вида станка.frw

0. Кронштейн А3.cdw

3. Шпиндельный узел 1 в 1.cdw

2. Кинематическая схема станка.cdw

Кинематическая схема стола
Кинематическая схема механизма АСИ
схема шпинеделя.frw

Фрагмент шпинделя с позициями.frw

Фрагмент кинемат схемы.frw

Фрагмент для структурной формулы.frw

000. Титульный лист.docx
Днепродзержинский государственный технический университет
Кафедра Технологии Машиностроения
по дисциплине металлообратывающие оборудование
на тему: «Проектирование оборудования гибкого промышленного модуля на базе многооперационного станка с ЧПУ модели 2А622МФ2»
1.Общие сведения ГПС 1.1.docx
1 СТРУКТУРА И ПРИНЦИПЫ СОЗДАНИЯ ГПС.
Гибкие производственные системы являются прогрессивной формой организации производства на основе высокоавтоматизированного технологического оборудования обеспечивающего эффективную работу при ограниченном количестве производственного персонала. В соответствии с ГОСТ 26228—85 «Системы производственные гибкие. Термины и определения» гибкая производственная система — это совокупность в разных сочетаниях оборудования с ЧПУ роботизированных технологических комплексов (РТК) гибких производственных модулей (ГПМ) отдельных единиц технологического оборудования и систем обеспечения их функционирования в автоматическом режиме в течение заданного интервала времени обладающая свойством автоматизированной переналадки при производстве изделий произвольной номенклатуры в установленных пределах их характеристик [11].
В систему обеспечения функционирования технологического оборудования ГПС входят:
автоматизированная транспортная и транспортно-складская система (АТСС) состоящая из взаимосвязанных автоматизированных транспортных и складских устройств предназначенных для укладки хранения временного накопления разгрузки и доставки предметов труда и технологической оснастки;
автоматизированная система инструментального обеспечения (АСИО) включающая участки подготовки инструмента его транспортирования накопления устройства смены и контроля качества инструмента обеспечивающая его подготовку хранение автоматическую установку и замену;
система автоматизированного контроля (САК); автоматизированная система удаления отходов (АСУО); автоматизированная система управления технологическими процессами (АСУ ТП);
автоматизированная система научных исследований (АСНИ); система автоматизированного проектирования (САПР); автоматизированная система технологической подготовки производства (АСТПП);
автоматизированная система управления ГПС (АСУ ГПС) и т. д. Производственная структура ГПС включает два комплекса: производственный (ПК) и управляющий вычислительный (УВК).
Производственный комплекс состоит из производственной системы и системы обеспечения функционирования технологического оборудования. Управляющий вычислительный комплекс включает технические средства программное обеспечение необходимое для управления технологическими процессами и соответствующие базы данных.
Комплексы строятся на основе системного подхода к организации и управлению производством т. е. каждый вид их функционирования или обеспечения производства рассматривается как система включающая необходимые технические и программные средства механизации и автоматизации физического и умственного труда и определенный порядок их взаимодействия. Организационной основой ГПС механической обработки является групповая технология в соответствии с принципа ми которой создаются ГПС для обработки деталей корпусных (корпуса коробок скоростей передач станины основания пространственные крон штейны и т. п.) плоскостных (планки крышки панели рейки плоские рычаги и т. п.) типа тел вращения (валы втулки фланцы гильзы зубчатые колеса и т. п.) смешанной группы деталей включающей комбинации из выше приведенных групп и прочих деталей.
Гибкие производственные системы должны организовываться в основном для комплектной обработки обеспечивающей выпуск полностью обработанных деталей или комплектов деталей для узловой сборки. При этом должны быть учтены следующие особенности мелкосерийного производства: большая номенклатура обрабатываемых дета лей разнообразие форм и размеров меняющихся через короткие периоды времени; непостоянство и разнообразие видов заготовок для изготовления од них и тех же или же подобных деталей; широкая номенклатура видов и марок обрабатываемых материалов; меняющееся во времени соотношение трудоемкости выполнения различных видов операций; большие внеочередные заказы не предусмотренные календарным планированием.
Идентифицировать ГПС и ее компоненты как объекты исследования раз работки внедрения и эксплуатации позволяют следующие принципы [22; 31; 39]:
Принцип совмещения высокой производительности и универсальности. В традиционном производстве наибольшая производительность достигается на автоматических линиях а наибольшая универсальность — на технологическом оборудовании с ручным управлением. При этом производительность такого оборудования недопустимо мала. Применение ГПС использующих программно-управляемое и программно перестраиваемое оборудование позволяет совместить высокую производительность с универсальностью на оптимальном уровне возможном при современном развитии техники.
Принцип технологической гибкости. Способность ГПС в короткие сроки и с минимальными затратами переходить к изготовлению новых объектов производства (деталей узлов изделий) характеризует гибкость системы. Различаются следующие виды гибкости ГПС [39]: операционная (технологическая) обеспечиваемая возможностью быстрой смены комплектов приспособлений инструментов и управляющих программ; маршрутная проявляющаяся в возможности изменения маршрута детали по станкам внутри системы в соответствии с программой ее обработки; морфологическая (функциональная) направленная на обеспечение оптимального распределения материальных по токов (деталей инструментов и т. д.) внутри системы путем соответствующей ее перенастройки или перестройки.
Принцип модульности. ГПС строится на базе модулей *. Модуль являясь компонентом ГПС также может состоять из компонентов. Не только модуль но и его компонент может быть самостоятельно разработан изготовлен и внедрен однако присущие ему функции он может выполнять только в составе модуля.
Принцип иерархичности. ГПС представляет собой многоуровневую структуру: на самом нижнем уровне находятся гибкие производственные модули на самом высоком — гибкий автоматизированный цех (ГАЦ) или завод (ГАЗ). Каждый более высокий уровень ГПС имеет в своем составе два или более элементов нижнего уровня. Модульность и иерархичность позволяют разрабатывать проекты ГПС для самого высокого уровня и реализовывать их с учетом специфики конкретно го предприятия.
Принцип обеспечения максимальной предметной замкнутости на возможно более низком уровне. Соблюдение этого принципа позволяет свести к минимуму затраты на межоперационное перемещение деталей сократить число деталеопераций. Наиболее эффективно достижение предметной замкнутости на уровне модуля. Однако при современном развитии техники это не всегда достижимо а в некоторых случаях экономически нецелесообразно.
Принцип функционирования при ограниченном количестве производственного персонала (принцип безлюдности). В соответствии с этим принципом решается задача максимального сокращения численности обслуживающего персонала за счет повышения уровня автоматизации выполняемых системой функций и автоматического контроля за ходом технологического процесса. Другим аспектом этой задачи является возможное продление срока функционирования системы без вмешательства человека.
Принцип интефации ГПС с САПР изделия САПР технологической подготовки производства и АСУП. Этот принцип определяет возможность создания сквозного цикла проектирование — изготовление на основе полной совместимости технических и программных средств систем автоматизации проектирования изделий технологической под готовки производства систем управления предприятий ГПС и единой автоматизированной базы данных.
Принципы системной организации ГПС. Под этими методологическими для поискового проектирования ГПС [39] принципами подразумеваются принцип технологической универсальности и принцип самоорганизации в свою очередь базирующийся на принципах приспособительной деятельности живучести самовосстановления саморазвития эволюционно адаптированного проектирования и внедрения системы. Принцип универсальности выражает тенденцию к расширению технологических возможностей системы и соответственно номенклатуры обрабатываемых деталей уменьшению числа установив сокращению технологических маршрутов протяженности транспортных путей увеличению производительности системы степени завершенности обработки детали. Принцип приспособительной деятельности проявляется в адаптации системы к условиям внешней (технологи ческой) среды. В результате реакции системы ее технологические возможности приводятся в соответствие с технологическими потребностями запускаемых в производство изделий путем соответствующих переналадок элементов и связей внутри системы. Принцип живучести характеризует свойство ГПС активно противостоять вредным воздействиям внешней среды и в случае помех выполнять свои функции путем перестройки структуры или перераспределения функций между нормально работающими элементами.
Принцип самовосстановления направлен на поддержание и сохранение технологического потенциала системы на заданном (проектном) уровне что достигается обеспечением системы средствами самодиагностики и самовосстановления отказавших элементов или их автоматической замены. В основу принципа саморазвития положено свойство системы развиваться и эволюционизировать как путем замены элементов более эффективными и прогрессивными так и путем трансформации морфологической структуры с целью расширения технологического потенциала.
Принцип эволюционного проектирования и внедрения ГПС выражается в продолжении проектирования после того как она создана корректировке проектных решений в процессе отладки и ступенчатом (поэтапном) наращивании мощности технологического потенциала и степени автоматизации ГПС в процессе внедрения.
2 МОДУЛЬНОСТЬ ПОСТРОЕНИЯ ГПС И УРОВНИ УПРАВЛЕНИЯ
Построение ГПС отличающихся большим разнообразием функциональных и параметрических характеристик осуществляется из ограниченного технически и экономически целесообразного функционально полного набора типовых унифицированных модулей. Взаимозаменяемость модулей позволяет при этом обеспечить гибкость и универсальность агрегатно-модульных структур. Поскольку ГПС строится из отдельных модулей различных типов
(аппаратных программных) [14] использование модульного принципа построения позволяет формировать состав технологического оборудования технических и программных средств в соответствии с фактическими потребностями производства.
Эффективная реализация модульного принципа требует комплексного и иерархического подходов к построению модульных структур самих модулей и их компонентов. Это означает необходимость модульного построения на всех уровнях иерархии (нижний уровень — технологическое транспортное и вспомогательное оборудование; средний - структура линий участков подсистем ГПС; верхний уровень — ГАЦ и ГАЗ в целом — как совокупность подсистем модулей) и по всем компонентам (вспомогательные устройства модульного исполнения технические средства математическое и программное обеспечение и т. д.).
Реализация модульного принципа по строения ГПС позволяет сократить сроки и трудоемкости разработки и внедрения ГПС; создавать ГПС силами пред приятий-потребителей с минимальным участием специалистов-разработчиков формировать состав технических и программных средств в соответствии с фактическими потребностями производства без избыточности обеспечить гиб кость структуры ГПС т. е. возможность ее быстрой перестройки при изменении объекта производства наращивать технологические возможности системы и повышать уровень ее автоматизации путем замены или дополнительного подключения соответствующих модулей. В настоящее время выпускаются технологическое складское транспортное оборудование и средства автоматизации гибкие производственные модули и модульные системы которые могут найти применение при разработке ГПС. Теоретические основы модульного принципа конструирования и практические рекомендации по созданию ГПС на его базе освещены в специальной литературе [2; 11].
Типовая модульная структура ГПС механической обработки показана на рис.
Производственный комплекс ГПС представляет собой совокупность гибких производственных модулей и моду лей обеспечения функционирования технологического оборудования: меж операционного транспортирования и складирования инструментального обеспечения автоматического контроля и удаления отходов. ГПМ является основной структурной частью производственного комплекса ГПС Имеющееся в модуле технологическое оборудование взаимодействует со средствами специального технологического оснащения представляющими со бой устройства модульного исполнения и обеспечивающими автоматическую подачу заготовок и инструмента их накопление и хранение соответственно в накопителе или магазине установку загрузку-выгрузку инструмента и заготовок контроль инструмента и детали техническую диагностику оборудования охлаждение и смазку инструмента удаление стружки из зоны резания и выдачу обработанных деталей в пристаночный накопитель или приемное устройство транспортной системы. Схема модульной компоновки ГПМ (на примере многоцелевого сверлильно фрезерно-расточного станка ИР 500МФ-4) типовой перечень входящих в модуль вспомогательных устройств модульного исполнения основные этапы функционирования и состав ГПМ приведены на рис. 2 С помощью устройства загрузки-разгрузки модуля 15 спутник с закрепленной заготовкой 16 помещается в накопитель спутников 9. являющийся составной частью ГПМ. По команде программы приспособление-спутник с заготовкой подается к устройству смены спутников 10 и с помощью гидромеханического поворотного устройства для загрузки-разгрузки ориентируется и фиксируется на столе 27 станка 4. Подача спутников на стол станка и шифр заготовки контролируется автоматически с помощью датчиков 13. Устройство замены режущего инструмента в магазине станка 14 посредством которого обновляется запас инструментов находящихся в магазине и устройство смены инструмента в шпинделе станка 5 являются самостоятельными модульными устройствами.
8. Описание способа удаления стружки.docx
1. ТЕХНОЛОГИЧЕСКИЕ ПРОБЛЕМЫ УДАЛЕНИЯ СТРУЖКИ
В условиях автоматического режима обработки удаление стружки из зоны резания является одним из важных условий надежной качественной и высокопроизводительной обработки изделий на металлорежущем оборудовании ГПС. Наличие стружки может привести к появлению дефектов на обрабатываемой поверхности вызвать преждевременный износ режущего инструмента его затупление и поломку.
Для удаления стружки используются системы состоящие из следующих основных элементов: пылестружкоотводчиков осуществляющих удаление пыли и стружки из зоны резания; устройств транспортирования стружки за пределы станка или участка; циклонов и фильтров обеспечивающих отделение стружки от воздуха и СОЖ; системы магистрального транспортирования стружки к устройствам переработки; системы переработки стружки осуществляющей обезжиривание дробление и брикетирование стружки.
Для надежной работы системы удаления и переработки стружки должна быть обеспечена требуемая однородная фракция стружки (обычно длиной 1 — 2 см). Многообразие режущих инструментов форм и материалов обрабатываемых заготовок приводит к образованию стружки различных форм и размеров (сливная спирально-трубчатая полукольцевая пластинчатая призматическая коническо-спиральная крупообразная хлопьеобразная и т. д.) зависящих от вида режимов обработки и физико-механических свойств обрабатываемого материала. В связи с этим одной из важных задач связанных с удалением стружки является ее формирование.
Наибольшую помеху в режиме автоматической работы оборудования при токарной обработке создают различные виды сливной и спиральной стружки.
Рекомендации ЭНИМС по отводу стружки на токарных станках с ЧПУ входящих в состав модулей обработки определяют следующие технологические методы формирования (дробления) стружки:
Выбор геометрии режущей части инструмента при котором используются стружколоматели в виде лунокуступов или канавок выполняемых на гранях режущей кромки резца. Применяются также накладные стружколоматели закрепленные на верхней грани режущих пластинок.
Выбор режимов резания т. е. нахождение такого соотношения глубины резания и подачи при котором имеет место эффект стружколомания.
Выбор схем перемещения инструмента короткими ходами например при обработке канавок или черновой расточке.
Формирование стружкоразделительных спиральных канавок осуществляемое для чистовых проходов. Прорезка канавок производится на глубину (005—006 мм) меньшую припуска на чистовую обработку с шагом угол подъема которого меньше 6о.
Дополнительные относительные перемещения инструмента (прерывание с выстоем ускоренное врезание с выстоем местное врезание отвод инструмента с выстоем и т. д.).
Рекомендуемые области применения каждого из перечисленных методов в зависимости от видов обработки и материалов приведены в табл. 8.1. Реализация методов 3 4 5 6 может быть выполнена путем программирования или путем включения специальных электронных модулей обеспечивающих формирование стружки по любой схеме независимо от заданной программы перемещения суппорта.
Переход токарной обработки
Конструкционные стали
Высоко углеродистые стали
Метод формирования стружки
Сверление рассверливание
Растачивание черновое
Точение канавок выточек
Растачивание чистовое
Рассмотренные методы формирования стружки могут быть применены и для станков сверлильно-фрезерно-расточной группы при выполнении переходов сверления рассверления растачивания некоторых переходов при фрезеровании пазов уступов криволинейного контура и пр.
При фрезеровании концевыми цилиндрическими и фасонными фрезами дробление стружки может быть осуществлено применением инструмента с так называемыми «кукурузными» зубьями сегментированными по режущим кромкам.
2. УСТРОЙСТВО УДАЛЕНИЯ СТРУЖКИ ИЗ ЗОНЫ РЕЗАНИЯ И ОТ СТАНКА
В практике эксплуатации ГПС получила наибольшее распространение автоматизированная система удаления стружки когда стружка от отдельных станков (ГПМ) или линий (ГАЛ) подается транспортерами на расположенные под полом участковые или магистральные конвейеры которые транспортируют ее за пределы цеха для последующей переработки.
Так как в разрабатываемой ГПС число станков невелико мы должны выбрать небольшое устройство для отвода стружки что существенно сократит затраты для построения данного модуля. Поэтому нужно внедрять небольшие механизмы отвода стружки. В тех задании указан способ отвода стружки – механический. Поэтому как вариант мы можем рассомотреть скребковый транспортер схема которого обозначена на рис. 8.1
На рис. 8.1 показана схема расположенного внутри станины станка скребкового транспортера обеспечивающего вывод стружки с боковой стороны. Скребковый транспортер 3 с приводом от электродвигателя 2 и специального редуктора размещается в корыте 4. Угол установки корыта с транспортером по отношению к основанию станка составляет около 20°. Из зоны резания стружка смывается СОЖ и перемещается по желобу 5. Движущиеся сребки транспортера забирают ее и передают вверх откуда она попадает в желоб конвейера 1. При перемещении стружка освобождается от СОЖ которая через отверстия в дне корыта стекает в резервуар 6.
Данный механизм подходит для нашего ГПМ выбираем его.
4.3 Разработка компоновки станка.docx
3.1. ИСХОДНЫЕ ДАННЫЕ К ВЫБОРУ КОМПОНОВКИ
Компоновка станка должна прежде всего обеспечивать заданный набор исполнительных движений необходимых для формообразования детали в процессе ее обработки на станке. Относительные движения инструмента и заготовки необходимые для формообразования реализуются обычно совокупностью определенного числа прямолинейных и вращательных движений. Таким образом главным исходным условием для компоновки станка является его кинематическая структура.
Совокупность движений инструмента и заготовки осуществляется в результате относительного перемещения одних узлов станка относительно других его узлов по соответствующим направляющим. Последовательность расположения подвижных узлов станка относительно инструмента заготовки и неподвижного узла предопределяет основу компоновки. Изменение последовательности расположения подвижных узлов путем их перестановки приводит к некоторому множеству вариантов компоновки (рис. 4.3.1) Задача конструктора сводится к анализу различных вариантов и выбору оптимального варианта для данных конкретных условий. Помимо основных движений в станке необходимых по условиям формообразования на компоновку станка влияют также установочные перемещения необходимые для настройки станка и осуществления различных вспомогательных операций.
Совокупность всего набора движений предопределяет множество принципиальных компоновок станка. Однако на базе выбранной принципиальной компоновки возможны дополнительные варианты оформления связанные со следующими факторами»
Обеспечение технике-экономических показателей в значительной степени зависит от выбора компоновки станка.
Компоновка станка влияет на возможные резервы в повышении производительности вследствие повышения степени автоматизации. В большинстве случаев при выборе компоновки целесообразно обеспечивать возможность встраивания станка в автоматическую линию или автоматическое производство с обеспечением потока
обрабатываемых деталей и с автоматизацией смены инструмента Автоматизация вспомогательных операций облегчается при удачной компоновке по отводу стружки и охлаждающей жидкости.
Точность обработки существенно зависит от выбора компоновки станка так как последняя влияет на жесткость несущей системы(рис 4.2) на тепловой баланс и соответствующие температурные деформации (Рис. 4.3 ).
От компоновки станка зависит схема нагружения несущей системы силами резания и массой подвижных и неподвижных узлов а это в сильной степени влияет на величину и характер упругих перемещений. Особое значение имеют узлы связанные с массивными обрабатываемыми деталями. Перемещение этих узлов вместе с заготовками в процессе обработки может сильно повлиять на перераспределение упругих деформаций и вызвать соответствующие погрешности обработки.
Рис. 4.2. Влияние компоновки на жесткость несущей системы станка на примере консольного () и бесконсольного () фрезерных станков:
— деформация колонны; 2 — деформации станины или консоли; 3 — смещения в горизонтальных направляющих; 4 — смещения в вертикальных направляющих fx fy fz — упругие перемещения инструмента относительно заготовки соответственно по осям x y z
Рис. 4.3. Влияние компоновки на характер температурных деформаций
Универсальность станка также сильно влияет на окончательный выбор компоновки станка. При компоновке необходимо учитывать массу габариты транспортабельность способы закрепления обрабатываемых деталей на данном станке для всего их множества. Кроме того от компоновки станка зависит и его переналаживаемость. Для станков с ручным управлением очень важным фактором влияющим на выбор компоновки является удобство обслуживания.
Компоновка станка оказывает сильное влияние на экономическую эффективность станка так как от выбора компоновки зависят металлоемкость трудоемкость изготовления и сборки занимаемая станком площадь и многие другие виды затрат как при изготовлении станка так и в процессе его эксплуатации
4Составление структурной формулы компоновки
Исходя из заданных движений инструмента относительно обрабатываемой детали можно рассмотреть всю совокупность возможных базовых компоновок пользуясь методом Ю. Д. Вра-гова. Если выбрать прямоугольную систему координат ориентированную в неподвижном пространстве то минимальное число подвижных узлов должно соответствовать числу заданных элементарных движений. Обозначим неподвижный узел символом О а подвижные узлы символами X V I если они перемещаются прямолинейно по соответствующим осям координат и буквами А В С — вращательные движения относительно тех же осей. Последовательность расположения узлов станка которая и определяет базовую его компоновку можно тогда записать структурной формулой в которой запись будет начинаться с узла несущего заготовку а кончаться узлом несущим режущий инструмент.
Тогда структурная формула станка записывается в виде:
3.1 Разработка операций маршрутной технологии.docx
1 Разработка операций маршрутной технологии
Маршрутная технология приведена в табл. 3.1
Табл 3.1. Маршрутная технология обработки детали
Содержание или наименование операции
Обрубка и очистка отливки
Навесить бирку с номером детали
Фрезеровать поверхность прилегания предварительно
Фрезерный полуавтомат
Фрезеровать торец отверстия 35Н7 предварительно расточить отверстие 35Н7 предварительно
Многооперационный станок с ЧПУ 2А622-МФ2
Наладка УСПО двухместная
Притупить острые кромки
Термическая обработка
Фрезеровать торец отверстия 35Н7 окончательно расточить и развернуть отверстие 35Н7 окончательно сверлить расточить и развернуть отверстие 8Н7 окончательно
В первой позиции: фрезеровать поверхность прилегания и паз В=35(15+20) окончательно сверлить четыре отверстия 7 два отверстия 6 сверлить и нарезать резьбу в двух отверстиях М6-7Н. Во второй позиции: зенковать четыре. Во второй позиции: зенковать четыре отверстия 7 до 11 окончательно рассверлить два отверстия 6 до 11 окончательно зацентровать сверлить и нарезать резьбу М10-7Н.
Наладка УСПО двухпозиционная
Технический контроль
Неуказанные предельные отклонения: валов h14 отверстий H14
Деталь – представитель типа кронштейн предоставлена в общем виде на рис 3.1
Чертеж детали находиться в приложении к курсовому проекту.
4.2 Использование при построении компоновки станка агрегатно-модульного принципа.docx
Унификация — использование в разных станках одинаковых деталей и узлов. Степень унификации можно оценить коэффициентом унификации
где — число унифицированных деталей (узлов) из общего количества деталей (узлов) станка.
Иногда коэффициент унификации подсчитывают по отношению массы или трудоемкости унифицированных деталей к общей массе или общей трудоемкости деталей станка. Унификация существенно снижает затраты на изготовление станков и повышает их надежность однако при излишне большой унификации ухудшаются технологические характеристики станков. Таким образом в каждых конкретных условиях существует оптимальное значение коэффициента унификации по критерию минимума приведенных затрат.
Унифицированные узлы гаммы тяжелых зубофрезерных станков
Диаметр обработки мм
Особые преимущества дает унификация однотипных станков выпускаемых одним производством. За счет снижения трудоемкости изготовления при этом снижаются общие затраты на производство всего размерного ряда. Снижение трудоемкости изготовления базовых деталей и узлов привода тяжелых станков намного перекрывают некоторые дополнительные затраты металла при унификации.
Унификацию станков размерного ряда широко используют как в тяжелых так и в средних станках. В качестве примера поясняющего широкие возможности внутрирядовой унификации станков можно привести унификацию гаммы тяжелых зубофрезерных. станков Коломенского завода тяжелого станкостроения (КЗТС). В табл. 4.2.1 пояснено какие узлы и в каких моделях станков унифицированы.
В более ограниченных масштабах возможна унификация и в станках различных типов. Некоторые базовые детали и узлы привода целесообразно использовать для станков самого различного назначения. Например в последние годы в советском станкостроении получили широкое распространение автоматические коробки скоростей (AKQ с электромагнитными муфтами. При широкой унификации возможно централизованное изготовление отдельных узлов и деталей станков со значительным увеличением серийности производства.
Агрегатирование является дальнейшим развитием унификации и сводится к тому что станки собирают в основном из стандартных узлов — агрегатов Наиболее успешно принцип агрегатирования используют в станках и автоматических линиях для крупносерийного и массового производства. Использование принципов агрегатирования не только удешевляет изготовление станков но и способствует сокращению сроков освоения и выпуска так как производство заранее ориентируется на выпуск стандартных узлов-агрегатов. На рис. 84 приведены схемы компоновки агрегатного станка предназначенного для встраивания в автоматическую линию в крупносерийном и массовом производстве.
Рис 4.2.1 Типовые схемы компоновки агрегатных станков из унифицированных узлов (заштрихованы): а – вертикальный с поворотным столом; б – вертикальный одностоечный в – горизонтальный односторонний; г – горизонтальный двухсторонний; д – горизонтальный барабанного типа.
Принцип агрегатирования является весьма перспективным и при конструировании многооперационных станков а также автоматических участков и автоматических производств с ЧПУ. На рис. 4.2.2. дана схема различных вариантов компоновки многооперационных станков на основе агрегатированной конструкции базовых деталей несущей системы и различных исполнений шпиндельной бабки с инструментальным магазином а также различных исполнений стола станка.
Агрегатирование целесообразно для различных вспомогательных устройств в автоматических станочных системах: транс-лортно-загрузочных и других манипулирующих устройств средств контроля и измерения устройств для автоматической смены ин-струмента5 систем охлаждения и смазки и т. п.
Основы агрегатирования могут быть заложены и при. компоновке обрабатывающих станочных систем из однотипных исходных элементов — так называемых технологических ячеек которые включают станок и загрузочно-транспортные устройства. На рис. 86 приведен пример компоновки автоматических обрабатывающих систем из различного числа станков для обработки зубчатых колес.
Набор технологических узлов снабжают транспортным устройством или роботом для передачи деталей от одного технологического узла к другому Из набора технологических узлов компонуют обрабатывающие системы различного технологического назначения и разной степени автоматизации. По такому агрегатному принципу осуществляют проектирование автоматических участков для обработки зубчатых колес и некоторых других видов деталей машиностроительного производства.
1.Общие сведения ГПС 1.2.docx
электрофизикохимические
автоматизированных складов
перегрузочных и загрузочно-разгрузочных устройств
транспортных роботов
автономных транспортных средств (робокар)
конвейеров транспортеров подвесных дорог
вспомогательного и режущего инструмента
настройки инструмента вне станка
автоматической смены инструмента
станочных приспособлений
контроля работоспособности и готовности оборудования к работе
контроля состояния положения и идентификации технологических объектов
Контроля параметров технологического процесса
Контроля качества продукции
отвода стружки из зоны резания
очистки установочных поверхностей
магистрального стружкоудаления
учета состояния и хода производства
оперативного управления
технологической подготовки производства
контроля и диагностики
ввод - вывода информации
решения задач управления
отображения информации
подготовки и передачи данных
Связи с ЭВМ и объектами
3.2 Определение режимов резания.docx
1 Фрезеровать поверхность прилегания предварительно
Для фрезерования поверхности с размером 86 принимаем фрезу торцевую насадную со вставными ножами из быстрорежущей стали
(по ГОСТ 1092-80) [6]
Глубина фрезеровании t = 15 мм [7]
Подача Sz = 02 мм; [7]
Стойкость фрезы Тм = 150 мин; [7]
К1 – коэффициент зависящий от размеров обработки;
К2 – от обрабатываемого материала;
К3 – от стойкости и материала инструмента;
Vтабл. = 33 ммин; К1=10; К2=09; К3=09 [7]
Е – табличная величина;
V – скорость резания в ммин;
t – глубина резания в мм;
z – число зубьев фрезы;
К1 – коэффициент зависящий от обрабатываемого материала;
К2 – от типа фрезы и скорости резания (для твердосплавных фрез)
bmax. – максимальная ширина фрезерования
Е= 23; К1 = 10; К2 = 10[7]
Мощность электродвигателя главного движения станка 8 кВт.
Расчетная мощность резания меньше мощности привода станка что позволяет вести обработку с заданными режимами резания.
Рассчитаем максимальный крутящий момент на шпинделе
Мшп.max при заданных режимах резания
С1Ф – коэффициент учитывающий значение удельного крутящего момента Нммм² ;
K1Ф – коэффициент динамичности нагрузки при фрезеровании;
С1Ф = 50 Нммм² ; K1Ф =12 [5]
Эффективная мощность резания
Pz – тангенциальная составляющая силы резания Н
Cр = 825; y = 08; u = 11; q = 11; w =0 [6]
Фрезеровать торец отверстия 35Н7 предварительно
Для фрезерования поверхности в размер 52 принимаем фрезу торцевую из быстрорежущей стали (по ГОСТ 9304-69) [6]
Материал пластин Т5К10
Глубина фрезерования t = 15 мм; [7]
Подача Sz = 02 мм;[7]
Стойкость фрезы Тм = 130 мин;[7]
К3 – от стойкости и материала инструмента
Vтабл. = 35 ммин; К1 = 10; К2 = 10; К3 = 1[7]
Е= 23; К1 = 1; К2 = 1 [7]
Мощность электродвигателя главного движения станка 8 кВт. Расчетная мощность резания меньше мощности привода станка что позволяет вести обработку с заданными режимами резания.
Мшп. max при заданных режимах резания
С1Ф = 40 Нммм² ; K1Ф =12 [5]
Cр = 825; y = 075; u = 11; q = 13; w =02 [6]
Расточить отверстие 35Н7 предварительно
Инструмент: расточной резец с пластинами из быстрорежущей стали.
Подача Sо=010 ммоб[7]
Фрезеровать торец отверстия 35Н7 окончательно
Е= 23; К1 = 1; К2 = 1[7]
Расточить отверстие 35Н7 окончательно
Инструмент: зенкер с коническим хвостовиком оснащенный пластинами из твердого сплава 35 мм ГОСТ 3231-71.
Подача Sо=065 ммоб[7]
Vтабл. = 24 ммин; К1 = 10; К2 = 12; К3 = 1 [7]
Определим осевую силу резания и крутящий момент и крутящий момент
где: Ср=68; q=10; y=07 [6]
где: См=0035; q=20; y=08; КрКмр=09[6]
Развернуть отверстие 35Н7 окончательно
Выбираем развертку машинную насадную с пластинами из твердого сплава с коническим хвостовиком ГОСТ 11175-80.
Подача Sz = 10 мм;[7]
Стойкость фрезы Тм = 60 мин;[7]
Vтабл. = 20 ммин; К1 = 13; К2 = 12; К3 = 10[7]
Определим осевую силу резания и крутящий момент
где: Ср=68; q=10; y=07
где: См=0035; q=20; y=08; КрКмр=09.
Сверлить отверстие 8Н7
Сверло спиральное из быстрорежущей стали с коническим хвостовиком (по ГОСТ 10903-77)
Vтабл. = 19 ммин; К1 = 10; К2 = 125; К3 = 1 [7]
Развернуть отверстие 8Н7
Выбираем развертку машинную цельную с коническим хвостовиком (по ГОСТ 1672-80)
Vтабл. = 15 ммин; К1 = 10; К2 = 115; К3 =10 [7]
Фрезеровать поверхность прилегания
Для фрезерования поверхности с размером 86 принимаем фрезу торцевую насадную со вставными ножами из быстрорежущей стали
Vтабл. = 33 ммин; К1 = 10; К2 = 09; К3 = 09 [7]
Фрезеровать паз B=35 (15+20)
Выбираем концевую фрезу с коническим хвостовиком по ГОСТ 17026-71
Глубина фрезерования t = 2 мм; [7]
Vтабл. = 24 ммин; К1 = 10; К2 = 09; К3 = 115[7]
С1Ф – коэффициент учитывающий значение удельного крутящего
Сверлить четыре отверстия 7
Выбираем сверло спиральное из быстрорежущей стали с коническим хвостовиком (по ГОСТ 2092-77) [6]
Vтабл. = 27 ммин; К1 = 09; К2 = 115; К3 = 08 [7]
Сверлить два отверстия 6
Vтабл. = 24 ммин; К1 = 09; К2 = 115; К3 = 08 [7]
Нарезать резьбу в двух отверстиях М6-7Н
Выбираем машинный метчик с коническим хвостовиком по ГОСТ 32266-81
Vтабл. = 8 ммин; Кv = 1; [7]
Зенковать 4 отверстия 7мм до 11мм
Выбираем зенковку цилиндрическую 11 мм
Подача Sо=006 ммоб [7]
Vтабл. = 22 ммин; К1 = 10; К2 = 125; К3 = 10 [7]
где: Ср=67; q=12; y=065[6]
Рассверлить два отверстия 6 до 11 окончательно
Vтабл. = 22 ммин; К1 = 10; К2 = 115; К3 = 10 [7]
Выбираем сверло центровочное спиральное с цилиндрическим хвостовиком для зацентровки под сверление (по ОСТ 2N20-5-80)
Сверлить отверстие 10
Нарезать резьбу М10-7Н
Vтабл. = 9 ммин; Кv = 1; [7]
где: См=0035; q=20; y=08; Кр=Кмр=09.
2. ОПИСАНИЕ РАБОТЫ И УСТРОЙСТВА МНОГООПЕРАЦИОННОГО СТАНКА МОДЕЛИ 2А622-МФ2.docx
Многооперационный станок 2А622-МФ2 служит главным образом обработки в корпусных деталях отверстий инструмент том закрепленным консольно. На станке осуществляют сверление зенкерование растачивание развертывание нарезание резьбы и фрезерование. Обработку можно вести как в автоматическом цикле с помощью системы ПУ так и с ручным управлением.
На станке с горизонтальными направляющими установлена передвижная стойка по которой в вертикальном направлении подвигается шпиндельная бабка с горизонтальным выдвижным расточным шпинделем. Стол станка может совершать продольные и поперечные перемещения кроме того имеется встроенный поворотный стол. Станок имеет инструментальный магазин цепного типа который установлен рядом со станком.
Техническая характеристика
Рекомендованные параметры обработки мм:
диаметр отверстий растачиваемых выдвижным шпинделем300
наибольший диаметр сверла50
Автоматически сменяемый инструмент:
наибольшая масса кг30
наибольший диаметр мм150
(при длине 550 мм без конусной части)
(при длине 300 мм без конусной части)
Диаметр усиленного выдвижного шпинделя мм 110
Внутренний конус выдвижного шпинделя по ГОСТ 15945—70№ 50; 7 :24
Размеры рабочей поверхности мм:
Наибольшие перемещения мм:
Рабочая подача мммин:
Скорость быстрого перемещения:
поперечная мммин8000
продольная мммин8000
наибольшее продольное перемещение мм710
скорость быстрого перемещения мммин5000
наибольшее усилие подачи Н11 000
сила затяжки инструмента в шпинделе Н20 000
Частота вращения шпинделя обмин 4—1250
Число ступеней регулирования26
наибольшее вертикальное перемещение мм1000
скорость быстрого перемещения мммин8000
Наибольшая масса обрабатываемой детали кг4000
Инструментальный магазин . Цепной
Число инструментов в магазине 100
Габаритные размеры станка мм:
Масса станка (без электрооборудования) кг20000
На рис. 1.1 представлен общий вид станка
На рис. 1.2 представлена кинематическая схема станка на рис. 1.3 — структурная схема привода главного движения и на рис. 1.4 — график частоты вращения шпинделя (а) зависимость мощности и крутящего момента от частоты вращения шпинделя (б) и структурная схема передач (в) станка 2А622МФ2. Шпиндель (рис. 1.2) приводится во вращение от регулируемого двигателя Ml постоянного тока. Для расширения диапазона регулирования используют механические ступени регулирования переключение которых осуществляется с помощью гидравлических устройств. Шпиндельная бабка перемещается в вертикальном направлении от винта 2. В полом шпинделе станка размещен расточный шпиндель который перемещается в осевом направлении от винта 3. Стол станка получает продольное и поперечное перемещения соответственно от винтов 4 и 5. Встроенный поворотный стол на вертикальной оси получает вращение от зубчатой передачи 13188. Каждый из подвижных органов получает быстрые и медленные перемещения от индивидуальных приводов (регулируемых двигателей постоянного тока).
Рис. 1.2. Кинематическая схема станка 2А622МФ2
рис. 1.3 — структурная схема привода главного движения
В передачах от двигателей к исполнительным органам имеются редукторы с двумя ступенями скоростей управление которыми осуществляется с помощью электромагнитных муфт. Одну из ступеней используют для быстрых перемещений.
Шпиндельный узел. Основной шпиндель 1 станка (рис. 1.5) сделан полым. Радиальные силы действующие на шпиндель воспринимаются и в передней и в задней опорах регулируемыми цилиндрическими роликовыми подшипниками 3182000. Осевые силы воспринимаются передней опорой. Для этой цели имеется два варианта подшипников: упорные подшипники для первого и упорно-радиальные для второго вариантов. Зазор — натяг в передней опоре регулируется кольцевой гайкой 3 а в задней опоре - кольцевой гайкой 4. Внутри основного полого шпинделя имеется подвижной расточной шпиндель 2. Каждый из шпинделей имеет свое устройство для закрепления инструментальных оправок.
Рис. 1.5. Шпиндельный узел станка 2А622-МФ2
Механизм зажима инструмента в расточном шпинделе (рис. 1.6) имеет дистанционное управление и расположен внутри выдвижного расточного шпинделя. Затяжка оправки 1 в шпинделе 2 осуществляется с помощью осевых сил приложенных к заднему концу штока 6 и создаваемых пакетом тарельчатых пружин 7. На переднем конце штока имеется замок который в момент зажатия оправки сцепляется с переходником они закрепляются во всех зажимных оправках. Три симметрично расположенных сухаря 4 могут перемешаться радиально в пазах на конце штока 6 ограничительного кольца 10 прижатого пружинной 5 к торцовой поверхности внутри шпинделя.
Отжатие оправки осуществляется с помощью гидроцилиндра 9. Масло давит на поршень 8 и перемещает шомпол 6 вперед преодолевая сопротивление пакета пружин 7 и пружины 5. При этом пазы с сухарями 4 на конце шомпола переместятся в зону выточки 3 ограничительного кольца сухари могут радиально перемещаться от центра до упора в поверхность выточки 3. При дальнейшем перемещении шомпол своим торцом коснется бурта переходника и переместит его вместе с оправкой на 2 мм сам находясь в положении «Отжато». После этого оправку можно вынимать из шпинделя манипулятором или вручную. Коническая поверхность переходника раздвинет сухари 4 переместив их от центра в выточку ограничительного кольца.
Оправка зажимается при установлении ее в шпиндель до упора вдоль оси. Цилиндр 9 соединяется со сливом. Пружины 7 перемещают шомпол 6 и поршень 8 назад. Сухари сближаются к центру ограничительным кольцом 10 и после этого скрепляются с конической поверхностью переходника оправки.
При автоматическом действии механизмов перед зажатием инструмента по отверстию внутри шомпола подается сжатый воздух для дополнительной очистки конусов шпинделя и оправки.
Механизм закрепления инструмента в полом шпинделе (рис. 1.7) расположен на переднем торце бабки на выступающем конце полого шпинделя. На переднем конце полый шпиндель имеет точный опорный торец и коническое отверстие
конусностью 7 :24. Приблизительно посредине конусного гнезда в подом шпинделе имеются три паза расположенные равномерно по окружности. В этих пазах могут перемещаться сухари 2 имеющие конические поверхности а на нижних концах. Оправка 1 имеет канавку с точной конической поверхностью с которой прилегают конические поверхности а сухарей. Сила направленная вдоль оси шпинделя и необходимая для затягивании оправки создается при одновременном сближении трех сухарей к центру шпинделя. Это осуществляется кольцом 3 с внутренней фонической поверхностью с которое при перемещении от бабки надвигается на наружную коническую поверхность b сухарей 2. Кольцо 3 получает движение от поршня 6 днухполостного гидроцилиндра 5. Длительное сохранение сжатого положения при отсутствии давления масла обеспечивается наличием самотормозящих конических поверхностей конуса b на кольце 3 и сухарях 2. После окончания зажатия оправки автоматически подается небольшое количество масла в полость отжима. При этом поршень отводится на наибольшую величину в сторону отжима образуя зазор А в замке между кольцами и поршнем. Кольцо получает возможность вращаться вместе со шпинделем без трения о поршень который остается неподвижным. О нахождении механизма в отжатом положении сигнализирует выключатель 4.1
13. Список литературы.docx
Гжиров Р.И. Серебряницкий П.П. Программирование обработки на станках с ЧПУ - Л.: Машиностроение 1990г - 588с.
Проников А.С. Расчет и конструирование металлорежущих станков –М.: Высш. шк. 1967г.;
Дунаев П.Ф. О.П. Леликов Конструирование узлов и деталей машин - М.: Выс. шк. 1985г.
Чернин И.М. Кузьмин А.В. Расчеты деталей машин – Минск: Выс. шк. 1978г.
Барановский Ю.В. Режимы резания металлов - М.: Машиностроение 1972г.
Кузнецов Ю.Н. Агрегатные станки – К.: Вища школа 1987г;
Ачеркан Н.С. Металлорежущие станки - М.: Машиностроение 1965г.;
Тепинкичиева В.К. Металлорежущие станки - М.: Машиностроение 1973г.
Сафраган Р.Э. Модульное оборудование для гибких производственных систем механической обработки - К.: Техника 1989.- 175 с.
Решетов Д.Н. Детали и механизмы металлорежущих станков. Т. 2. - М.: Машиностроение 1972.- 520 с.
Косилова А. Г. Справочник технолога-машиностроителя. В 2-х т. Т. 2. – М. : Машиностроение 1985г. 496 с.
Анурьев В.И. Справочник конструктора-машиностроителя. -В 3-х т. - Т.2. - 5-е изд. – М. : Машиностроение 1977г. 496 с.
1.Общие сведения ГПС 1.3.docx
Дальнейшая обработка измерений и выдача коррекции осуществляется с помощью устройства управления ЧПУ 10. Измерительная го ловка 1 для контроля состояния инструмента закреплена на стойке. Посредством устройства уборки стружки 12 стружка удаляется из зоны резания поступает в магистральный стружкопровод затем брикетируется. Устройства охлаждения и смазки инструмента включаются и выключаются по сигналам программы. Кроме этого ГПМ оснащен следующими контрольно-измерительными устройствами контроля работоспособности 7 готовности оборудования к работе 6 контролирующими наличие инструмента нахождение его в исходной точке наличие заготовки и надежность ее закрепления контроля состояния инструмента в процессе обработки и усилия резания. Обработанная деталь перемещается вместе с спутником в накопитель 9 затем перегружается на транспортную систему направляется на склад. Рассмотренные этапы функционирования ГПМ иллюстрируют взаимодействие станка с модульными устройствами подсистем обеспечения функционирования оборудования АТСС АСИО АСУО и САК.
Управляющий вычислительный комплекс ГПС представляет собой совокупность двух модульных подсистем программного обеспечения и технических средств системы управления ГПС (см. рис. 1) [14]. ГПС осуществляет календарное и оперативное планирование управление исполнительными системами ГЛМ учет продукции и использования технологического оборудования контроль работы оборудования и диагностику комплектацию производства материалами заготовками инструментом управляющими программами и пр. выдачу оперативной информации о состоянии производства.
Типовая иерархическая многоуровневая структурная схема управления ГПС показана на рис. 1.1.
Количество уровней управления зависит от сложности ГПС. Для более простых ГПС типа гибких автоматизированных линий (ТАЛ) или участков (ГАУ) не требующих автоматизированного решения задач САПР АСТПП и АСУП структура управления может быть ограничена двумя уровнями и содержать одну центральную ЭВМ управления ГАУ или ГАЛ. Такая структура показана на рис. 3 красной линией.
Модульное оборудование для ГПС механической обработки
Рис.1.1 Схема модульной компоновки ГПМ на примере многоцелевого станка ИР-500МФ4
— щуповая головка для контроля состояния инструмента; 2 — магазин инструментов; 3 — щуповал головка для измерения размеров заготовки детали; 4 — станок; 5 — устройство замены инструмента в шпинделе станка; 6 — блок устройства контроля готовности модуля к работе; 7— блок устройства контроля работоспособности станка; 8- устройство ЧПУ; 9 - накопитель спутников; 10 — устройство смены спутников: 11 — автоматическое устройство закрепления спутника; 12 — устройство цдаления стружки: 13 — датчики контроля поступления спутника и идентификации заготовки: 14 — устройство замены режущего инструмента в магазине станка; 15 — устройство загрузки-разгрузки модуля; 16 — приспособление-спутник; 17 — стол станка.
Рис 1.2 Функциональная схема управления ГПС
В процессе развития простой ГПС может быть реализована трехуровневая структура обусловленная расширением и автоматизацией функций АСУП или АСТПП В этом случае реализуется связь центральной ЭВМ ГАУ (ГАЛ) с верхним уровнем (на рис. 3 показана красной пунктирной линией). Для более сложных ГПС содержащих несколько простых систем и осуществляющих управление на уровне ГАЦ с использованием автоматизированных систем АСУП и АСТПП верх него уровня система может быть четырехуровневой и содержать центральную ЭВМ управления ГАЦ работающую в сети центральных ЭВМ управляющих ГАЛ или ГАУ. В перспективе при создании более сложных ГПС типа ГАЗ возможна реализация еще одного промежуточного уровня управления (на рис. 3 показан черной пунктирной линией).
Во всех случаях на первом уровне осуществляется непосредственное внутримодульное оперативное управление технологическим процессом. Микро ЭВМ первого уровня управляющие ГПС могут взаимодействовать между собой обеспечивая только локальные функции связи между модулями. На втором уровне центральной ЭВМ ГАЛ ГАУ решаются задачи управления внутри ГАЛ или ГАУ т. е. задачи координации работы локальных систем ЭВМ и управляемых ими модулей.
Центральная ЭВМ второго уровня может быть связана с ЭВМ обеспечивающими решение задач САПР АСУП и АСТПП на верхнем уровне управления. Кроме того на этом уровне с помощью модулей программного обеспечения по казанных на схеме (см- рис- 1) выполняется месячное и сменно-суточное планирование осуществляется учет состояния и хода производства производится отображение соответствующей информации для человека-оператора.
На третьем уровне (при четырехуровневой структуре) центральной ЭВМ ГАУ осуществляется координация работы ГАЛ или ГАУ входящих в ГАЦ.
На четвертом уровне (при пятиуровневой структуре) координируется работа ГАЦ входящих в ГАЗ. Комплекс ЭВМ СУ ГПС реализует функции управления с помощью специальных программных модулей.
Указанные модули так же как и элементы локальной вычислительной сети ГПС и модули взаимодействия с САПР АСУП и АСТПП являются общими для различных ГПС и могут быть использованы как типовые в качестве типовых элементов вычислительной сети могут применяться и модули технических средств имеющие аппаратную и программную совместимость и используемые для решения задач управления хранения данных отображения информации ввода-вывода связи с УВК и объектами подготовки и передачи данных и пр.
3ГПМ. Обзор основных технических характеристик.
В соответствии с классификацией видов станочного оборудования ГПМ механической обработки являются дальнейшим развитием станков с ЧПУ и обрабатывающих центров [17] К ГПМ которые являются автоматизированным программно-управляемым и программно-переналаживаемым оборудованием способным работать в течение нескольких смен с участием ограниченного количества обслуживающего персонала предъявляются те же требования что и к металлорежущим станкам. В ГПМ входят станок с ЧПУ автоматическое загрузочно-разгрузочное устройство автоматическое устройство для закрепления детали или приспособления с деталью автоматическое устройство для смены инструмента накопитель для заготовок и обработанных деталей устройство для автоматического удаления стружки и другие устройства.
В настоящее время серийно выпускаются следующие ГПМ: токарно-прутковые патронно-прутковые патронные и патронно-центровые карусельные сверлильно – фрезерно - расточные (для обработки корпусных и плоских деталей) вертикального и горизонтального исполнений; шлифовальные — универсальные круглошлифовальные (центровые и бесцентровые) внутришлифовальные плоскошлифовальные шлицешлифовальные хонинговальные и заточные; зубообрабатывающие; фрезерные и протяжные; электро-физико-химические [40]. По степени автоматизации различают шесть групп ГПМ (табл. 1). Для каждого уровня автоматизации и категорий модулей приняты кодовые обозначения (табл. 2).
Размерные ряды главных параметров для ГПМ основных технологических групп определяются потребностями отраслей промышленности и прогнозами их развития.
ТЕХНИЧЕСКИЕ ХАРАКТЕРИСТИКИ ГПМ
В состав ГПМ входят токарные сверлильно-фрезерно-расточные и шлифовальные зубообрабатывающие фрезерные протяжные и электрофизико - химические станки. Номенклатура станков вошедших в состав ГПМ обработки определена исходя из следующих критериев:
распространенности и перспективности моделей станков выпускаемых серийно и планируемых к выпуску а также моделей станков на базе которых возможно и целесообразно создание ГПС;
возможности реализации заданного технологического процесса обработки типовых деталей в условиях разной серийности и размерных параметров станков.
Номенклатура включает в себя станки с ЧПУ и полуавтоматы предназначенные для обработки деталей из штучных заготовок следующих типов: токарные патронные и центровые ГПС предполагается создавать в основном из станков средней размерной группы предназначаемых для обработки изделий массой до 500 кг. Основным критерием определяющим возможность включения станков в состав модуля обработки является степень автоматизации станков позволяющая без серьезных конструктивных переделок перевести их на работу в автоматическом режиме а также достаточно быстрая переналаживаемость станка.3
Исходя из этого при создании ГПМ отбираются станки имеющие автоматизированный цикл работы включая переключение скоростей и подач автоматизированный либо механизированный зажим изделия.
Должна учитываться также степень автоматизации вспомогательных операций (контроль деталей отвод и подвод заграждений вывод стружки и пр.). Станки включаемые в состав ГПМ должны обеспечивать [4]:
автоматический зажим и открепление детали на станке; точное и надежное базирование детали в установочном приспособлении станка;
отделение отходов от детали в процессе резания и удаление их из зоны обработки;
автоматизацию контроля отдельных пара метров детали и контроля состояния инструмента в цикле обработки;
автоматическую смену инструмента внутри цикла обработки; связь систем управления ГПМ и станка обеспечивающую автоматический цикл работы ГПМ;
возможность безопасного для обслуживающего персонала функционирования ПР и его доступа в рабочую зону станка;
автоматизацию перемещения ограждения;
высокую надежность обеспечивающую длительную автоматическую работу ГПМ.
Промышленные роботы (ПР) включаемые в состав ГПМ должны отвечать следующим требованиям [4]:
конструктивно-технологические параметры (грузоподъемность скорость перемещения рабочих органов точность позиционирования размеры рабочей зоны тип СПУ) должны соответствовать техническим параметрам и технологическим требованиям станков для обслуживания которых они предназначены;
использование ПР должно улучшать технико-экономические показатели станков т.е. повышать их производительность не менее чем на 20 % увеличивать коэффициент загрузки в 2—25 раза и во столько же раз снижать количество трудозатрат на единицу продукции.
ПР должны иметь минимальное количество степеней подвижности для обеспечения требуемого объема станочных операций и использования вспомогательного оборудования необходимого для нормальной работы комплекса до статочную степень универсальности для перехода оборудования с обработки одного изделия на другое с минимальным циклом работ по переналадке высокую надежность (наработка на отказ ПР должна быть не менее 100 ч) зону обеспечивающую возможность наблюдения за процессом резания и вмешательства в процесс в случае аварийной ситуации. При этом должны быть гарантированы условия техники безопасности для обслуживающего персонала.
4.1 Разработка планировки ГПМ.docx
1 Разработка планировки ГПМ
Для выбора плана ГПС нам потребуется выбор транспортных механизмов которые выбираются относительно массы детали. Так как масса детали в техзадании не указа нам следует ее расчитать.
Ручной метод определения массы детали.
Для нахождения массы нужно рассчитать объем детали. Для нахождения объема разбиваем деталь на отдельные простые тела типа паралелограм и цилиндр:
Ручной метод вычесления массы детали не точен так как не учитывает ответрстий штамповочных уклонов и скруглений. Поэтому следует произвести компьютерный расчет массы детали.
Компьютерный расчет массы детали:
Массовые характеристики КРОНШТЕЙНА:
Плотность = 0.0087 грмм3
Объем = 187426.65 мм3
Площадь поверхности = 41836.32 мм2
Структура типовых компоновок ГПС обусловленная особенностями применяемого модульного оборудования АТСС включает компоновку линейного типа на базе кранов-штабелеров и другого напольного оборудования (см. рис. 4.1 а б и в);компоновку многорядного типа на базе напольного оборудования (см. рис. 4.1 г и д); компоновку кольцевого типа на базе конвейерного оборудования (рис. 4.1 е); компоновку многорядного типа (рис. 4.2 а) и кольцевого типа (рис. 4.2 б) на базе подвесного транспорта.
С использованием типовых компоновок разработаны и применяются при проектировании и внедрении ГПС компоновочные решения учитывающие различные модификациии и сочетания транспортных накопительных складских систем варианты расположения технологического оборудования и пр.
На рис. 4.1 показаны принципиальные схемы компоновочных решений ГПС для применения цикличных видов рельсового транспорта.
На площади занимаемой ГПС могут размещаться от 4 до 100 ГПМ вдоль трассы транспортного робота с одной или двух сторон. Расположение ГПМ — линейное (в одну или две линии) параллельно транспортной трассе перпендикулярно к ней или группам под углом к ней. По схемам приведенным на рис. 4.1 о—е организуются ГАУ и ГАП. При этом система обеспечения функционирования производства выносится за пределы участка (линии) накопители размещаются на территории участка. При организации ГАЦ по схеме показанной на рис. 4.1 ж и з — на площадях занимаемых ГПС размещаются технологическое оборудование и все системы обеспечения производства (СОП).
Технические решения (рис. 4.1 а б и ж) применяются для одностороннего (а) и двустороннего (б и ж) расположения ГПМ. Для перемещения и складирования заготовок деталей инструмента и приспособлений (а) применяются транспортные роботы позволяющие устанавливать тару поддоны и приспособления-спутники на приемные устройства (накопители) рабочих мест и в многоярусные участковые накопители. По схеме приведенной на рис. 4.1 б и ж загрузка пристаночных накопителей производится из ячеек участковых накопителей.
Организация ГПС с централизованным накопителем по схемам виг рекомендуется для одностороннего (в) и двухстороннего (г) расположения ГПМ. Транспортные роботы обеспечивают перемещение и накопление деталей на одном высотном уровне. Автоматические накопители используются для размещения оборотных заделов инструмента и приспособлений.
Схема показанная на рис. 4.1 д целесообразна для организации ГПС в которых для хранения заготовок деталей в таре и спутников предусмотрен общий склад-накопитель с роботом-штабелером. Для загрузки ГПМ транспортный робот захватывает тару или спутник из ячеек склада и устанавливает на пристаночный накопитель или приемное устройство ГПМ.
Характерной особенностью схемы приведенной на рис. 4.1 е является применение в одном транспортном блоке двухуровневого перемещения.
На верхнем уровне перемещается транспортный робот цикличного действия транспортирующий тару поддоны и спутники к станкам. На нижнем уровне служащем для возврата тары поддонов и спутников с рабочих мест в качестве транспортного средства применяется роликовый приводной конвейер. После каждой технологической операции полуфабрикаты и готовые детали на поддонах возвращаются на приемные устройства системы обеспечения функционирования производства.
Принципиальные схемы компоновок ГПС с применением роликовых конвейеров в комплексе с поворотными и подъемными устройствами и цепными конвейерами дины на рис. 4.2.
На площади занимаемой ГПС вдоль линейной или замкнутой «трассы конвейеров могут разместиться до 25 ГПМ и участковые накопители. Система обеспечения функционирования производства вынесена за пределы участка. В зависимости от номенклатуры находящихся в производстве деталей на ГПС могут быть обеспечены постоянная последовательность прохождения технологических позиций (рис. 4.2 а в и г) переменная последовательность прохождения позиций при постоянной направленности перемещения деталей с пропуском технологических позиций (рис. 4.2 б д з) и переменная последовательность прохождения технологических позиций при переменной направленности прохождения деталей по участку (схема ж).
При организации ГПС по схеме приведенной на рис. 4.2 а перемещение деталей осуществляется на приспособлениях-спутниках в основном роликовыми конвейерами с последовательной или выборочной загрузкой рабочих позиций. Накопление заделов у станка производится на ответвлениях конвейера или на загрузочно-разгрузочных устройствах станка. Для установки заготовок на спутники и снятия готовых деталей в составе системы обеспечения функционирования производства организуется специальный пункт (УС) с накопителем спутников заготовок и готовых деталей.
Установка заготовок на спутники выполняется операторами. Снабжение УС заготовками производится со склада-накопителя заготовок системы обеспечения функционирования производства. Готовые детали направляются на цеховой склад готовых деталей. Согласно рис. 4.2 а межоперационное перемещение деталей осуществляется также в таре и на поддонах или на спутниках по схеме (рис. 4.2 б). Для обгонных операций используются вспомогательные конвейеры (роликовые или цепные). В производстве может находиться число партий деталей равное количеству ГПМ.
По схемам приведенным на рис. 4.2 в и г осуществляется двустороннее и одностороннее обслуживание ГПМ в стесненных условиях производства при переменной последовательности обслуживания. Для межоперационных перемещений используются роликовые двухъярусные конвейеры с подъемниками для перемещения спутников между другими конвейерами.
На рис. 4.2 д и е показаны схемы одностороннего и двустороннего обслуживания ГПМ при переменной последовательности обслуживания малой емкости накопителей ГПМ или их отсутствии. Обгонные операции и накопления спутников производятся на одном из конвейеров. В качестве межоперационного транспорта используются роликовые конвейеры для перемещения спутников между роликовыми конвейерами — цепные конвейеры.
На рис. 4.2 ж и з приведены схемы одностороннего и двустороннего обслуживания ГПМ при переменной последовательности обслуживания станков и переменном направлении движения спутников. В качестве межоперационного транспорта используются роликовые конвейеры с подъемными и поворотными устройствами цепные конвейеры и конвейеры на воздушной подушке.
Принципиальные схемы организации ГПС с использованием для межоперационных перемещений деталей напольных безрельсовых машин (робокар) перемещающихся по проездам приведены на рис. 4.3 а и б. Количество станков определяется заданным объемом производства. Реализация этих схем целесообразна для участков где станки устанавливаются группами различной конфигурации в плане и требуется создание криволинейных трасс а также в тех случаях когда склады и участки подготовки располагаются в отдалении от технологического оборудования. Как правило транспортные трассы должны быть закольцованы. Наращивание требуемой производительности средств транспорта по обеспечению рабочих мест производится увеличением числа робокар обслуживающих ГПС. Обе схемы применяются для организации как Г АЛ ГАУ так и ГАЦ. Участки могут иметь квадратную вытянутую прямоугольную или угловую компоновку.
Схемы организации ГПС с применением грузонесущих напольных тележечных конвейеров представленные на рис. 4.3 виг могут быть рекомендованы для ГАЛ ГАУ и ГАЦ при применении грузовых единиц приспособленных для транспортирования на тележечных конвейерах. Организация ГПС аналогична организации по схемам а и б. В зависимости от условий эксплуатации могут применяться грузонесущие тележки конвейеры с подпольным и подвесным размещением тягового элемента (цепи). Трасса конвейера может быть однокольцевой или многокольцевой.
Схемы организации ГПС с использованием для межоперационных и межучастковых перемещений подвесных грузонесущих конвейеров (рис. 4.3 д е и ж) рекомендуются для сложных трасс.
Учитывая рассмотренные планировки ГПС а также с учетом технического задания и в соответствии разработанным техпроцессом детали разрабатываем планировку гибкой производственной системы на основе многооперационного станка 2А622-МФ2 вид которой представлен на рис 4.4
Шлифовальный станок;
Подъемно-транспортное устройство;
Ячейки для хранения заготовок готовых
деталей инструментальной и
7. Расчет шпиндельного узла.docx
Шпиндельный узел наиболее ответственная часть любого станка так как он предназначен для осуществления точного вращения инструмента или обрабатываемой детали. Он входит в несущую систему станка и в значительной мере определяет ее жесткость и виброустойчивость.
К шпиндельным узлам станков предъявляют следующие основные требования:
) точность вращения измеряемая биением на переднем конце шпинделя в радиальном или осевом направлениях; отклонения от идеального вращения являются одной из основных причин погрешностей обработки на многих станках;
) жесткость шпиндельного узла определяемая по упругим перемещениям переднего конца шпинделя обусловленным податливостью собственно шпинделя и его опор; радиальная и осевая жесткость шпиндельного узла существенно влияет на точность обработки;
) виброустойчивость шпиндельного узла существенно влияющая на общую устойчивость несущей системы и всего станка; демпфирующие свойства опор и амплитудно-частотные характеристики шпиндельного узла влияют на шероховатость поверхности и предельно допустимые режимы обработки (для быстроходных шпинделей станков опасность могут представлять резонансные явления);
) долговечность шпиндельных узлов которая связана с долговечностью опор шпинделя в смысле сохранения первоначальной точности вращения; это требование имеет особое значение для шпиндельных опор качения;
) ограничение тепловыделения и температурных деформаций шпиндельного узла которые сильно влияют на точность обработки; опоры шпинделей при значительной частоте вращения являются интенсивным источником выделения тепла в непосредственной близости к зоне обработки;
) быстрое и надежное закрепление инструмента приспособления или детали обеспечивающее их точное центрирование и соответственно точное вращение; в современных станках возрастают
требования к автоматизации закрепления инструмента приспособления или обрабатываемой детали.
Выполнение совокупности сложных требований предъявляемых к шпиндельным узлам станков осуществляется при правильном подборе материала и конструкции шпинделя а главным образом при обоснованном выборе типа и конструкции его опор.
Особенностью многих станков является то что указанные требования должны выполняться при изменяемых в широких пределах нагрузках и частотах вращения.
1 Расчет шпинделя на жесткость
Расчет шпинделя на жесткость сводиться к определению деформаций изгиба и в отдельных случаях- деформаций кручений.
При составлении расчетной схемы шпиндель обычно заменяют балкой на шарнирных опорах. Такое допущение справедливо при наличии в опорах по одному подшипнику качения. Несколько подшипников в одной опоре при уточненных расчетах следует рассматривать как упругую опору.
Рис 7.1 Расчетная схема шпинделя
Смещения конца шпинделя находим по следующим формулам []:
где -условная жесткость консольной части шпинделя;
- относительная длина пролета; P-сила действующая на консоли шпинделя; jA jB – жесткости соответственно передней и задней опор.
Е-модуль упругости (модуль Юнга); I1I2 – моменты инерции консольной и межопорной частей балки соответственно а – размер вылета консоли шпинделя;
b – расстояние между опорами.
Определим момент инерции на консоли балки
где d2=100 мм; d0=170 мм; c1- соотношение внутреннего и наружного диаметров шпинделя консольной части балки;
Определим момент инерции в пролете балки
где d1=150 мм; d0=100 мм; c1- соотношение внутреннего и наружного диаметров шпинделя пролетной части балки;
Определим условную жесткость шпинделя в пролете между опорами:
Определим условную жесткость консольной части шпинделя:
Определим нагрузку передаваемую колесом на шпиндель пользуясь таблицей Анурьева [14] :
Определяем реакции опор:
Приняв и находим значение суммарного прогиба шпинделя [12]:
Пронников приводит формулу для проверки суммарного перемещения консоли шпинделя:
- т.е условие выполняется и жесткость шпинделя данного станка обеспечивается.
Определим для него оптимальную величину межопорного расстояния lопт исходя из необходимости получения максимальной жесткости (т.е. минимума суммарной податливости) из формулы [1]:
тоесть оптимальной величиной межопорного расстояния является 590 мм
2 Рассчитаем виброустойчивость шпинделя.
Уровень колебаний переднего конца шпинделя определяют по амплитудно-фазочастотным характеристикам которые целесообразно расчитывать по заранее подготовленным программам средствами вычислительной техники.
Приближенный расчет собственной частоты шпинделя не имеющего больших сосредоточенных масс можно проводить по формуле [1]
где m – масса шпинделя кг; - относительное расстояние между опорами; -коэффициент который для лежит в пределах 23-24
Масса шпинделя нам неизвестна поэтому мы можем примерно ее рассчитать проанализировав грубую модель шпинделя (рис. 7.2):
Плотность = 0.007850
Масса = 34184.35 гр.
Площадь поверхности = 587439.06
Что лежит в пределах нормальных значений 500-600 Гц
3 Выбор подшипников [12]
В передней опоре радиальные нагрузки воспринимает двухрядный роликовый подшипник серии 3182100К
динамическая: 400 кН
статистическая: 425 кН
В задней опоре радиальные нагрузки воспринимает двухрядный роликовый подшипник серии 318211К
динамическая: 290 кН
статистическая: 300 кН
Радиальные нагрузки воспринимает шариковые упорно-радиальные двухрядные подшипники с углом контакта 60о 178920 (ГОСТ 20821-75)
динамическая: 132000 кН
статистическая: 310000 кН
00 Содержание.docx
Описание работы и устройства многошпиндельного станка модели 2А622-МФ2 .21
Разработка маршрутной технологии обработки детали-представителя
1 Разработка операций маршрутной технологии 28
2 Определение режимов резания . . 29
Выбор и обоснование компоновочной схемы станка и гибкого производственного модуля (ГПМ)
1 Разработка планировки ГПМ . .. . 45
2 Использование при построении компоновки станка агрегатно-модульного принципа . 50
3 Разработка компоновки станка . . .53
4Составление структурной формулы компоновки 55
Выбор и обоснование необходимого количества режущих инструментов и соответствующего им вспомогательного инструмента .. 56
1 Выбор необходимого количества режущих инструментов 56
2 Выбор вспомогательного инструмента ..58
Расчет и конструирование двух механизмов устройства автоматической смены инструмента (УАСИ) и устройства автоматической смены заготовки (УАСЗ) . 63
Расчет и конструирование шпиндельного узла станка модели 2А622-МФ2 . 70
Описание способа удаления стружки .. .. 76
Смазка станка модели 2А622-МФ2 .. 79
Обоснование и выбор системы охраны труда и техники безопасности .80
Разработка и обоснование систем управления ГПМ . . 82
Список литературы .. 86
5. Выбор и обоснование необходимого количества режущих инструментов и соответствующего им вспомогательного инструмента.docx
В разделе 3.2 (Определение режимов резания) для обработки детали были выбраны следующие инструменты:
Фреза торцевая насадная со вставными ножами из быстрорежущей стали (по ГОСТ 1092-80)
Фреза торцевая из быстрорежущей стали (по ГОСТ 9304-69)
Материал пластин Т5К10
Расточной резец с пластинами из быстрорежущей стали.
Зенкер с коническим хвостовиком с пластинами из твердого сплава 35 мм ГОСТ 3231-71.
Развертку машинную насадную с пластинами из твердого сплава ГОСТ 11175-80.
Сверло спиральное из быстрорежущей стали с коническим хвостовиком (по ГОСТ 10903-77)
Концевая фреза с коническим хвостовиком по ГОСТ 17026-71
Сверло спиральное из быстрорежущей стали с коническим хвостовиком (по ГОСТ 2092-77)
Машинный метчик с коническим хвостовиком по ГОСТ 32266-81
Зенковка цилиндрическая 11 мм
2ВЫБОР ВСПОМОГАТЕЛЬНОГО ИНСТРУМЕНТА
ГПМ предназначенные для встраивания в ГПС поставляются с расширенными комплектами режущего и вспомогательного инструмента состав которых согласуется поставщиками модулей и потребителем поскольку номенклатура режущего инструмента определяется на основе анализа типовых деталеопераций выполнение которых предусматривается в ГПС.
Обработка деталей в ГПС требует высокопроизводительного инструмента рассчитанного на высокую надежность работы в автоматическом режиме. Наиболее эффективна ГПС при использовании систем инструмента блочно-модульной конструкции.
Такой инструмент состоит из отдельных элементов (модулей) которые могут компоноваться в оптимальные конструкции инструмента. Блочно-модульные инструменты подразделяются на следующие модули: базовые хвостовики устанавливаемые в шпиндели станков; собственно держатели инструментов предназначенные для непосредственной установки (базирования и закрепления) режущих инструментов резцедержатели резцовые головки борштанги элементы предназначенные для установки насадного или концевого осевого инструмента с цилиндрическим или коническим хвостовиком— кулачковые и цанговые патроны державки оправки патроны для метчиков а также центроискатели измерительные щупы и др.; переходники (адаптеры) устанавливаемые между хвостовиками и держателями инструмента предназначенные для увеличения расстояния между ними уменьшения или увеличения диаметра обработки. В хвостовиках держателях и переходниках имеются специальные посадочные и присоединительные поверхности обеспечивающие точное базирование и закрепление сочленяемых модулей.
Путем замены одного или нескольких модулей модульные вспомогательные инструменты без их съема могут быть использованы многократно для разных операций. При затуплении инструмента замене подлежит не весь инструмент а только один модуль — непосредственно держатель или инструмент. При подготовке производства модульные инструменты собираются и разбираются для компоновки большого количества конструкций инструментов для различных станков. Элементы блочно-модульных инструментов обладают высокой унификацией. Инструменты компонуемые из модульных элементов (что резко сокращает сроки изготовления инструментов) могут' использоваться взамен специальных. Модульные инструменты значительно дешевле (в особенности при централизованном изготовлении) цельных инструментов применяемых для конкретных операций.
Вспомогательный инструмент предназначенный для установки базирования и закрепления режущих инструментов составляет основу существующих модульных инструментальных систем. Его технический уровень существенно влияет на точность производительность длительность простоев металлорежущих станков входящих в модули обработки.
Вспомогательный инструмент должен обеспечивать достаточную жесткость высокую точность и стабильность установки (базирования и крепления) режущего инструмента возможность выполнения всех технологических переходов предусмотренных технической характеристикой станка быстросменность межразмерную унификацию настройку инструмента вне станка.
Разработанная ЭНИМС и ВНИИ система вспомогательного инструмента устанавливает три подсистемы инструмента: инструмент с цилиндрическим базирующим хвостовиком (для крепления на токарных станках) инструмент с базирующей призмой (для крепления на токарных станках); инструмент с коническим и цилиндрическим хвостовиком (для крепления на сверлильно-фрезерно-расточных станках).
рис. 5.1. Модульная система вспомогательного инструмента для сверлильно-фрезерно-расточных ГПМ.
Система вспомогательного инструмента для модулей обработки сверлильно-фрезерно-расточной группы (рис. 5.1) состоит из следующих элементов:
1. — оправка с конусом 7 : 24 для насадных фрез с поперечной шпонкой;
2— оправка с конусом 7:24 для насадных цилиндрических фрез с продольной шпонкой;
3— оправка с конусом 7:24 для насадных торцовых фрез с поперечной шпонкой;
4— патрон с конусом 7:24 цанговый с диапазоном зажима деталей диаметром 20—40 мм.
5— втулка с конусом 7:24 переходная для концевых фрез.
6— патрон с конусом 7:24 цанговый с диапазоном зажима деталей диаметром 5—20 мм;
7— втулка с конусом 7:24 переходная для инструмента с конусом Морзе с лапкой;
8— втулка с конусом 7:24 переходная для инструмента с конусом Морзе с резьбовым отверстием;
9— державка с конусом 7:24 для регулирования патронов втулок и оправок;
10— оправка с конусом 7:24 расточная для получистового растачивания;
11— оправка с конусом 7:24 расточная для чистового растачивания;
12— оправка с конусом 7:24 для чистового растачивания сборная;
13— оправка с конусом 7:24 для подрезания пластин;
14— головка с конусом 7:24 рас точная двузубая;
15— головка с конусом 7:24 расточная универсальная;
16— регулируемый цанговый патрон с диапазоном зажима 5—25 мм;
17— регулируемая втулка с внутренним конусом Морзе универсальная;
18— регулируемая втулка длинная с внутренним конусом Морзе;
19— регулируемая оправка для насадных зенкеров и разверток;
20— регулируемый резьбонарезной патрон;
21— регулируемая оправка для чистового растачивания;
22— регулируемая расточная двузубая оправка;
23— регулируемая оправка для крепления пластин перовых сверл;
24— регулируемая оправка для дисковых фрез;
25 — регулируемый расточный патрон;
26— патрон с конусом Морзе сверлильный трехкулачковый без ключа;
27— то же резьбонарезной;
28— то же расточный;
29— оправка с конусом Морзе для насадных зенкеров и разверток.
Модульная система инструмента для комплектования станков с ЧПУ входящих в состав модулей обработки сверлильно-фрезерно-расточной группы разработана и выпускается Ивановским СПО им. 50-летия СССР (рис. 5.2).
рис. 5.2. Модульная система инструмента для сверлильно-фрезерно-расточных ГПМ.
Базовым инструментом в системе служит универсальная оправка с двумя посадочными диаметрами (d=32 50 d2=50 70 мм) и переходные державки в которые в зависимости от технологических переходов устанавливаются и закрепляются различные инструментальные оправки. В комплекте предусматривается поставка трех типоразмеров оправок с основными посадочными Диаметрами d=22 32 и 50 м. С переднего торца каждой оправки имеется внутреннее отверстие в которое вставляется подпружиненный толкатель для удаления высверленной сердцевины отверстия полученные трепанацией с помощью коронок девяти типоразмеров. Диаметр обрабатываемого трепанацией отверстия й=36 178 мм.
Последующая обработка отверстий (d=32 180 мм) осуществляется одно- и двухрезцовыми расточными головками которые устанавливаются и закрепляются на передней части универсальных оправок.
Чистовая обработка отверстий диаметром до 50 мм выполняется однолезвийными развертками и расточными патронами с микрометрической вставкой отверстий диаметром 50—180 мм — микрометрическими головками.
В комплекте также предусмотрена следующая оснастка: оправки для торцовых фрез с торцовыми и продольными шпонками; переходные втулки с внутренним конусом Морзе № 1 — 5 крепления стандартного инструмента; цанговые патроны для крепления инструмента с цилиндрическими хвостовиками (d=5 40 мм); резьбонарезные патроны для нарезания резьб М4-М36; оправки для крепления концевых фрез; головки для насадных зенкеров и разверток.
В ВНИИинструмента разработана модульная система расточного инструмента для растачивания отверстий 0 40—160 мм. Инструмент (рис. 5.3) состоит из пяти элементов (модулей): хвостовика (конус ИСО 50) трех присоединительных диаметров переходника четырех типоразмеров удлинителей четырех типоразмеров однозубых и двузубых расточных головок оснащенных многогранными неперетачиваемыми твердосплавными пластинами (МНТП) соответственно пяти и шести типоразмеров.
Все модули соединяются между собой посредством резьбовых соединений. Комплект инструмента включает 22 типоразмера модулей позволяющих скомпоновать свыше 100 вариантов инструментов различных диаметров и длин. Модульный расточный инструмент изготовляется Оршанским инструментальным заводом.
Расточные модульные оправки состоят из 24 унифицированных элементов из которых можно скомпоновать по принципу агрегатирования свыше 70 раз личных вариантов инструмента.
Вспомогательный инструмент используемый для комплектации гибких производственных модулей сверлильно-фрезерно-расточной группы и станков с ЧПУ с целью снижения затрат и повышения эффективности унифицирован и стандартизирован. На основе системного подхода разработана элементарная база комплектации станков с концами шпинделей по ГОСТ 2644— 81 и ГОСТ 13876—76.
Компоновка модульного режущего и вспомогательного инструмента по схеме приведенной на рис. 5.3. обеспечивает полное использование технологических возможностей станков.
Оправки модели 191 431 058 с концом 7:24 для насадных фрез с поперечной и продольной шпонками с коническими и цилиндрическими посадочными отверстиями диаметром 22 27 32 40 и 50 мм в нормальном и удлиненном исполнениях выпускаются Кулябским опытным заводом технологической оснастки.
рис. 5.3. Унифицированная система модульного инструмента для сверлильно-фрезерно-расточной обработки.
Патроны цанговые моделей 191 113 040 (191 113 050) и 191 132 050 для крепления концевых фрез сверл и других режущих инструментов с цилиндрическим хвостовиком диаметром 5—20 и 20—40 мм изготовляются Рижским опытным заводом технологической оснастки и Новосибирским инструментальным заводом.
Режущий инструмент рекомендуемый для модулей обработки сверлильно-фрезерно-расточной группы включает торцовые концевые ротационные и специальные фрезы зенкеры и зенковки расточные резцы и головки сверла развертки метчики и другой стандартный и специальный инструмент.
Торцовые и ротационные фрезы расточные резцы и головки а также некоторые типы концевых фрез комплектуются вставными ножами оснащенными пластинами из твердого сплава как напайными так и неперетачиваемыми с механическим креплением (изготовляются Томским заводом режущих инструментов Сестрорецким инструментальным заводом им. С. И. Воскова заводом «Фрезер» Запорожским инструментальным заводом им. П. Л. Войкова и др.) многогранными металлокерамическими пластинами (выпускаются заводом «Фрезер» Московским инструментальным заводом ПО «Урал-маш» и др.) пластинами с механическим креплением из СТМ (композитов) 01 05 10Д (изготовители — Сестрорецкий инструментальный завод им. С.И. Воскова Московский инструментальный завод «Фрезер» им. М.И. Калинина НПО «Спецтехоснастка» Московский опытный инструментальный завод»
Учитывая выбранный инструмент необходимый для обработки детали и принимая к вниманию конструкцию шпиндельного узла в котором может закрепляться оправка с метрическим конусом 7:24 мы можем выбрать необходимые для обработки оправки.
Выбираем из унифицированных оправок предназначенных для сверлильно-фрезерно-расточной группы станков:
Для обработки торцевыми фрезами:
Для обработки сверлами и развертками небольших размеров принимаем оправку:
с переходниками под инструмент:
Для обработки метчиком принимаем оправку:
9. Подбор масла.docx
Принимаем смазку вязкостью 120 мм7с;
Температура рабочей среды 50°С.
Для зубчатых передач принимаем ИРП-40
10. Обоснование и выбор системы охраны труда и техники безопасности.docx
Необходимо решить следующие задачи:
наличие надежного и автоматически действующего ограждения зоны
компоновку станка нужно разрабатывать беспрепятствия удалению стружки
количество подвижных деталей станка должно быть минимальным
значительно сбалансированным регулировка узлов должна быть легкой и доступной;
одной из причин неблагоприятных условий труда является уровень шума его причиной могут быть недостаточно высокая точность изготовления деталей станка износ. Уровень шума регламентируется по ГОСТ 121003-83;
предусмотреть удаление пыли и грязи следует использовать газоотводы
необходимо хорошее освещение станка рабочей зоны по ГОСТ 122009-80;
использование быстродействующих механизмов гидравлических и пневматических устройств обеспечивающих надежное удержание обрабатываемой заготовки или инструмента;
автоматическая блокировка всех звеньев входящих в комплекс начиная с
движущихся узлов станка и заканчивая ограждением;
правильное устройство и размещение органов управления;
обеспечение высокой ремонтопригодности и безопасности.
Безопасность работы на станке обеспечивается не только конструктивными мероприятиями но и монтажем организацией рабочего места. На участке не должны находиться посторонние предметы. Станок должен быть заземлен в соответствии с существующими нормами.
К основным тенденциям развития современного машиностроения следует отнести:
Максимальную концентрацию технологических операций в одном
станке что позволяет повысить коэффициент использования и обработать
заготовку с одной установки;
Максимальное использование агрегатно-модульного построения
технологических машин;
Максимальное использование современных вычислительных систем
12. Заключение.docx
Внедрение ГПМ и ГПС являются передовыми технологиями и успешно применяются во всех отраслях машиностроения. Задача же инженеров – конструкторов это рассчитывать новые и улучшать изобретенные ГПС для решения все новых задач в машиностроении.
11. Разработка и обоснование систем управления ГПМ.docx
Автоматическую взаимосвязанную работу всех компонентов ГПС обеспечивает управление на базе вычислительных машин соединенных в единую многоуровневую иерархическую систему. Нижний уровень предназначен для непосредственного управления ГПМ транспортной системой автоматизированным складом моечной машиной и другими элементами ГПС. Техническими средствами нижнего уровня могут явиться различные устройства ЧПУ программируемые контроллеры и микро ЭВМ. Они выдают информацию непосредственно в момент совершения события (в реальном режиме времени) в параллельном коде. Это обстоятельство в частности является одной из причин появления между нижним и верхним уровнями управления промежуточного среднего уровня так как ЭВМ верхнего уровня может не иметь достаточного числа входов для параллельного приема информации. В этом случае средний уровень управления концентрирует и преобразовывает параллельную информацию нижнего уровня в последовательную и передает ее в ЭВМ верхнего уровня. Работая в реальном режиме времени средний уровень решает задачи диспетчерского управления включая ввод и вывод УП и корректоров инструментов. В настоящее время для этой цели используют микро ЭВМ СМ-1800 с набором периферийных устройств.
Верхний уровень управления использует более мощные вычислительные машины например мини-ЭВМ типа СМ-1420. Совместно с комплектом дополнительных устройств верхний уровень реализует решение задач оперативно-календарного планирования учета хода производства формирования сопроводительных технологических документов (карт наладок ведомостей инструментов и приспособлений) хранения управляющих программ. В ряде случаев на верхний уровень управления ГПС возлагается решение задач САПР АСУП АСУ ТП. При более высокой степени организации АСУ ГПС входит составной частью в АСУ предприятия стыкуется с ней физически как с более высоким уровнем управления. При такой организации решение задач проектирования планирования в масштабах предприятия и разработки УП целесообразно передать на этот уровень предприятия оснащенный более мощной вычислительной техникой и координирующий работу всех ГПС предприятия.
Подсистему управления ГПС (АСУ ГПС) можно расчленить на ряд составных подсистем.
Подсистема планирования реализует месячное недельное и сменно-суточное планирование; формирует и корректирует соответствующую информацию которую выдает в виде документов для пользования персоналом ГПС и в пакетном режиме по кабелям связи из машин верхнего уровня в ЭВМ среднего уровня.
Подсистема оперативного управления воспринимает информацию о вводе в работу новой партии деталей координирует работу технологического оборудования ГПС.
Подсистема технологической подготовки производства выдает задания на своевременную доставку заготовок на склад ГПС подготовку крепежных приспособлений режущих и вспомогательных инструментов; передает управляющие программы.
Рис 11.1 Схема подготовки программы при управлением станком с ЧПУ от ЭВМ
Подсистема учета обобщает сведения о ходе производства работе оборудования наличии в ГПС необходимых ресурсов.
Подсистема диагностики выполняет диагностирование технического состояния оборудования и средств обеспечения ГПС.
Подсистема контроля занята контролем качества продукции техническими средствами ГПС (контрольно-измерительными машинами измерительными головками ГПМ) и управления качеством путем принятия соответствующих решений.
АСУ ГПС образована средствами технического программного информационного и организационного обеспечения
Техническое обеспечение реализуют комплексом технических средств (КТС) который состоит из устройств вычислительной и организационной техники средств передачи и отображения данных: устройств ЧПУ; программируемых контроллеров; процессоров ЭВМ; оперативно-запоминающих и передающих информацию устройств; устройств внешней памяти на жестких и гибких магнитных дисках а также на магнитной ленте; устройств печати; расширителей интерфейса; алфавитно-цифровых терминалов; устройств связи ЭВМ с объектами и др.
Программное обеспечение определяется программами работы всех компонентов ГПС на машинных носителях и текстами этих программ.
Информационное обеспечение образуется во-первых базой данных отраженных в документах и на машинных носителях включающих в себя описание заготовок готовых деталей технологической оснастки маршрутов обработки трудозатрат и во-вторых программно-математическим обеспечением работ вычислительной техники. Организационное обеспечение определяется методическими и руководящими материалами положениями штатным расписанием инструкциями и квалификационными требованиями к обслуживающему персоналу.
0. Введение.docx
Одной из подотраслей машиностроения испытавших на себе наиболее глубокий кризис в перестроечный период является станкостроительная промышленность ориентированная в основном на обеспечение потребности отраслей народного
хозяйства в основных средствах. В настоящее время наблюдаются следующие негативные тенденции:
ухудшение научного обеспечения производства сокращение численности персонала НИИ и КБ и объема работ по стандартизации;
- резкое уменьшение инвестиций и как следствие старение и выход из строя технологического оборудования;
распад кооперации и специализации производства комплектующих изделий что снижает качество продукции.
В 1990 г. СССР занимал второе и третье место соответственно по потреблению и производству металлообрабатывающего оборудования. А уже в 1997 г. Россия как основной центр станкостроения бывшего СССР занимает 20-е место по производству металлообрабатывающего оборудования из 35 стран-производителей; по потреблению станков на душу населения объективному показателю уровня промышленного развития страны в 5 раз с лишним ниже среднемирового уровня. Ситуация в Украине еще печальней. Украина и Россия в ближайшем будущем могут стать полностью зависимыми от импорта станков что создаст угрозу технологических и экономических безопасностям стран. В то же время российская станкоинструментальная промышленность как основная фондообразующая отрасль является базой научно-технического прогресса и роста конкурентоспособности промышленной продукции. Мировой опыт свидетельствует о том что все промышленно развитые страны на различных этапах формирования экономики одним из важнейших приоритетов считали и считают развитие собственного станкостроения являясь как правило основными производителями и потребителями металлообрабатывающего оборудования.
Стратегически важно своевременное поступление наукоемких технологий на базе современных станков и другого оборудования и инструмента в те отрасли которые производят технически сложные потребительские товары и
обеспечивают доминирующие позиции отечественного производства на внутреннем и внешнем рынках.
Совершенствование методов управления предприятием включая планирование производства управление организационной структурой управление инновациями совершенствование структуры управления на базе научных методов позволит повысить эффективность управления
предприятием выйти из кризиса и стать основой для успешного развития станкостроительной промышленности являющейся основой для экономики страны в целом.
В условиях начавшегося оживления в отечественной промышленности и в связи с достижением станочным парком критического износа (средний возраст оборудования достиг 20 лет) перед станкостроительными предприятиями стоит задача обновления активной части производственных фондов машиностроительных заводов что может быть достигнуто благодаря увеличению объёмов выпуска станочной продукции. В условиях ограниченного платежеспособного спроса и дефицита инвестиций в станкостроение наиболее рациональным способом решения этой задачи является более полное использование имеющегося потенциала предприятия (в настоящее время производственные мощности станкозаводов РФ загружены только на 17-20%) ориентация его на освоение выпуска наукоёмкой конкурентоспособной продукции. В общем случае потенциал можно определить как возможность предприятия адаптироваться к изменяющимся внешним условиям за счёт внутренних резервов. Многие станкостроительные заводы продолжают производить оборудование которое не находит платежеспособного спроса на рынках металлорежущего оборудования (МРО).
Одной из причин кризисного состояния отечественных станкостроительных предприятий является неконкурентоспособность производимой продукции. Положение «на грани банкротства» вынуждает предприятия подменять стратегические цели (долгосрочные) и ориентиры деятельности на тактические (краткосрочные). В таких условиях трудно проводить работу по повышению конкурентоспособности станков тем более что отечественным предприятиям сейчас приходится конкурировать с зарубежными компаниями и на внешнем и на внутреннем российском рынке. Выход из сложившейся ситуации возможен лишь в случае выпуска заводами конкурентоспособных станков которые будут востребованы на российском и международном рынке. Однако методик выбора металлорежущих станков (МРС) с конкурентоспособными технико-экономическими характеристиками (ТЭХ) до сих пор нет.
Мировая ситуация в станкостроении
Последние несколько лет наблюдается спад мирового производства МОО. С 1990 г. мировое производство МОО уменьшилось более чем на 30%. Сокращение мирового производства МОО в 2002 г. стало результатом падения объемов производства станков во всех ведущих станкостроительных странах Европы в США и Японии (табл. 1.1.1).
В разделе приведены данные в целом по МОО т.к. в международной статистике МРС и КПО не всегда разделены.
Таблица 1.1.1 Изменение объема производства МОО в мире.
Зап. Европа «CECIMO»
Объем производства в 2000 г. млн.
Объем производства в 2001 г. млн.
Страны Европейского комитета сотрудничества в станкостроении - «CECIMO» второй год подряд превышают отметку половины мирового производства МОО. Хотя и в этой группе стран наблюдался спад производства станков составивший 92%.
«CECIMO» - европейский комитет по кооперации станкостроения имеет свою штаб-квартиру в г. Брюсселе. Он объединяет 15 стран: Австрия Бельгия Великобритания Германия Дания Испания Италия Нидерланды Португалия Турция Финляндия Франция Чехия Швейцария Швеция которые обеспечили 52% мирового производства МОО в 2002 г.
Представленные данные показывают изменения позиций стран в мировом производстве МОО за последние 27 лет: крупнейшая индустриальная страна США переместились с 1-го места в 1980 г. на 5-е место в 2002 г. Германия наконец смогла восстановить лидирующее место удерживавшееся два десятилетия Японией б. СССР в лице правопреемника России скатился с 3-го места в середине 80-х годов на 21-е место в 2002 г. В первую десятку теперь входят бывшие аутсайдеры такие как: Испания Китай Тайвань и Республика Корея. Одновременно перешли в разряд отстающих стран Франция и Великобритания.
В 2003 г. спад мирового производства металлорежущих станков (МРС) и кузнечно-прессового оборудования (КПО) составил 14% в том числе в США - 33% Японии - 30% Германии - 12%. В целом производство металлообрабатывающего оборудования (МОО) в мире сократилось в 2003 г. до 312 млрд. долл. (в 1990 г. - 463 млрд. долл.).
В тоже время значительно увеличилась конкуренция: требования к качеству и стоимости оборудования.
Международная торговля.
Состав крупнейших стран-экспортеров остался неизменным хотя объемы вывоза МОО каждой из них претерпели изменения: сократили экспорт Германия (на 9%) Япония (на 28%) Италия (на 7%) Швейцария (на 16%) США (на 11%) Великобритания (на 25%) Франция (на 12%) Бельгия (на 26%). Из первой десятки стран-экспортеров увеличили вывоз МОО только Тайвань (на 6%) и Испания (на 5%). Среди стран-экспортеров МОО Россия находится только на 26 месте.
Основные страны-импортеры МОО: США КНР Германия Италия Франция. Среди импортеров МОО Россия находится на 20 месте.
Таблица 1.1.3 Торговый баланс МОО по основным странам.
Положительный торговый баланс по МОО имеют лишь 8 стран. Крупное положительное сальдо в 2002 г. имеют Япония Германия Швейцария а также Италия и Тайвань. Обращает на себя внимание значительное сокращение положительного сальдо у крупнейшей страны-экспортера МОО - Японии. В 2002 г. сальдо Японии уменьшилось почти на 30% по сравнению с 2001 г. Значительное отрицательное сальдо имеют Китай США Канада а также Республика Корея Франция Бразилия и Турция (более 100 млн. у 12 каждой страны). Хотя в 2002 г. у США произошло снижение отрицательного сальдо на 40%.
Как видно из вышесказанного доля России в мировом товарообороте невелика. Следовательно вопросы конкурентоспособности российских МРС являются особенно актуальными.
Видимое потребление рассчитываемое как сумма собственного производства и импорта МОО за вычетом экспорта существенно изменилось в 2002 г. Видимое потребление МОО в странах-продуцентах станков представлены в табл. 1.1.4.
Таблица 1.1.4 Потребления МОО.
Потребление 2001 г. млн.
Потребление 2002 г. млн.
Душевое потребление
Среднедушевое потребление МОО отражающее уровень индустриального развития и инвестиционной активности в машиностроении стран варьируется в широких пределах: от самого высокого показателя 7758 долл. на человека в Швейцарии до самого низкого 019 долл. в Индии. В среднем по основным странам участвующем в товарообороте МОО он составляет 850 долл. на человека. Россия с показателем 131 долл. оказалась на 25 месте в мире пропустив вперед такие развивающиеся страны как Турция (500 долл.) Бразилия (330 долл.) и даже Китай (441 долл.) с населением 13 млрд. человек.
В частности в России снижение потребление МРО в значительной степени связано с уменьшением производства на которое в свою очередь существенное влияние оказывает нехватка информации о платежеспособном спросе на отечественное станочное оборудование. [4]
Как мы видим состояние отечественного станкостроения на настоящее время можно охарактеризовать как плачевное. Так как машиностроение которое влияет на большую часть всей экономики страны и ее развитие и благополучие в будущем нужно целеустремленно заниматься развитием все новых видов и методов обработки материалов а также использовать передовые технологии и инструменты для их выполнения и разрабатывать новые. Самые высокие технологии позволяют весьма удешевить деталь сделать ее конкурентно способной на всемирном рынке.
Данный курсовой проект основан на методе системного подхода к проблеме самого оптимального способа изготовления детали использован один из лучших многоцелевых станков что дает положительный экономический эффект на изготовлении приведенной в техническом задании детали.
Рекомендуемые чертежи
- 25.01.2023
- 29.05.2022
- 25.01.2023