Проектирование линии для нанесения покрытия Zn-Co




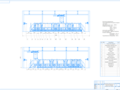
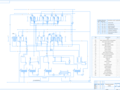
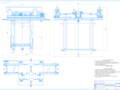
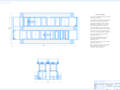
- Добавлен: 24.01.2023
- Размер: 2 MB
- Закачек: 2
Описание
Состав проекта
![]() |
![]() |
![]() ![]() ![]() ![]() |
![]() ![]() |
![]() ![]() ![]() ![]() |
![]() ![]() ![]() ![]() |
![]() ![]() ![]() |
![]() ![]() ![]() ![]() |
![]() |
![]() ![]() ![]() ![]() |
![]() ![]() ![]() |
Дополнительная информация
автооператор.cdw

Грузоподъемность автооператора 500 кг.
Скорость горизонтального перемещения манипулятора 0
Скорость поднимания-опускания подвески манипулятором 0
автоаператора 250 кг
Мощность электродвигателя движение 1
Технические требования
Установка ограждений в рабочей зоне автооператора
Перед пуском проверить подключение к питающей сети
Обеспечить дуступ к выключателям и блакировочным устройствам
Мероприятия по защите от коррозии автооператора
осуществить согластно ГОСТ 7313 - 35
Смазака движущих узлов периодическая
Цепи и открытые зубчатые передачи смазать солидолом Ж
Линия вид сверху.cdw

Отклонение от прямолинейности путей манипулятора
по всей длине не более 20мм
Пульт управления и пульт дистанционного управления
выпрямителями устанавливается в аппаратной
Шкаф локальной автоматики
не связанные с линией жесткими
размерами устанавливаются вдоль стены цеха
Сечение шинопроводов при полной нагрузке должно
обеспечивать падение напряжение в них не более 0
Сопротивление изоляции между корпусами токовых
ванн и шиной заземления должно быть не менее 4 кОм
Нанести порядковый номер на консоли каждого
манипулятора ГОСТ 9754-76
Цех должен иметь заземляющий контур и все
корпуса электрооборудования должны быть
Сопротивление между болтом заземления и корпусом
должно быть не более 0
Датчики положения манипулятора устанавливаются
вдоль линии движения с разделом на зоны
обслуживания каждого манипулятора
Гальваническая линия
для нанесения покрытия
циклограмма.cdw

Приложение к оборудованию.docx
Рисунок 2 – Эскизы покрываемых деталей
Линия вид сбоку.cdw

Односторонний бортовой отсос
Площадка обслуживания
Контактный пускатель
Бортовой отсос двухсторонний
Бортовой отсос односторонний
Техническая характеристика:
Линия предназначена для нанесения покрытия
Производительность линии - 25000 м
Габаритные размеры линии:
Количество манипуляторов - 2
Тип манипулятора - подвесной тележечный
Скорость перемещения:
Грузоподъемность манипулятора - 250 кг
Двухрядная автоматическая
линия для нанесения
покрытия цинк-кобальт
Тех. схема.cdw

Ванна трехкаскадной промывки
Ванна двухкаскадной промывки
Ванна нанесения покрытия
Ванна газожидкостной промывки
Ванна хромитирования
Ванна горячей промывки
Насос высокого давления
Условные обазначения Наименование среды в трубопроводе
Загрязненный электролит
Очищенный электролит
Вентиляционные выбросы
Оборудование.docx
Предлагается использовать однорядную линию с подвесным манипулятором тележечного типа для осуществления технологического процесса нанесения цинкового покрытия.
Автоматическая линия представляет собой прямолинейный ряд ванн установленных в определенном порядке на металлоконструкции в соответствии с техпроцессом. Над ваннами к потолку крепятся ездовые пути по которым перемещается автооператор.
С одной стороны линии установлена площадка обслуживания. Вся сантехническая обвязка линии технологическими трубопроводами располагается под площадками обслуживания и доступ к ней возможен сбоку линии и через съемный настил.
Линия обслуживается двухрельсовым манипулятором подвесного типа (автооператор тележечный A-200Т2).
Технические характеристики:
Грузоподъемность не более 250 кг.
Горизонтальная рабочая скорость при заводской установке (частота 50 Гц) - (033 ± 005) мc т.е (20 ± 3) м мин.;
горизонтальная в ручном режиме при разгоне и торможении - (007 ± 001) мc т. е. (4 ± 08) м мин.;
Скорость перемещения груза вертикальная - (0116 ± 003) мc т. е. (7 ± 014) м мин.;
Установленная номинальная мощность электродвигателей:
- привода тележки – 037 кВт;
- привода подъемника – 055 кВт.
Входные питающие напряжения:
- переменное трехфазное – 380 В частотой – 50 Гц;
- переменное трехфазное 36 В частотой – 50 Гц;
- постоянное – 24 В;
- переменное однофазное – 24 В частотой – 50 Гц.
Автооператор предназначен для перемещения деталей находящихся на подвесках катодной штанги или в барабанном контейнере.
Преимущества данного манипулятора:
- манипулятор может работать в следующих режимах (ручной режим “от кнопки на позицию” автоматический режим.
- манипулятор обладает устройством для встряхивания подвески с деталями.
- большая грузоподъемность – 250 кг.
- работа от любого промышленного источника питания.
Ванны электрохимического обезжиривания травления цинкования горячей промывки снабжены бортовыми отсосами с системой фильтрации воздуха на базе волокнистого фильтра ФВГ-М с производительностью 2.5-40 тыс. м3ч.
При этом степень очистки воздуха составит не менее 95%. Все ванны установлены на опорные изоляторы. Ванны изготовлены из полипропилена и имеют поддерживающий каркас из нержавеющей стали.
Трубопроводы подачи электролитов слива концентрированных стоков спроектированы из полипропиленовых труб. Запорная арматура – из чугуна футерованного фторопластом.
Для объемного напорного дозирования нейтральных и агрессивных жидкостей эмульсий суспензий предлагается использовать насос центробежный муфтовый НЦ.М3-4. Предназначен для перекачивания агрессивных и нейтральных жидкостей с плотностью не более 1200 кгм и температурой от +7 до +60°С. Бессальниковая конструкция насоса исключает утечку перекачиваемой жидкости и ее контакт с химически нестойкими материалами.
Также целесообразно применять для нанесения сплавов на основе цинка выпрямительный агрегат для гальваники который обладает рядом технических преимуществ:
- Возможность работы в агрессивных зонах гальванических производств
- Модульная конструкция
- Микропроцессорный блокконтроля и управления
Агрегат выпрямительный содержит две последовательно соединенные аккумуляторные батареи емкостью 26Ач с суммарным напряжением 24В для бесперебойного питания гальванической линии в случае внезапного отключения электроэнергии в основной сети. Микропроцессорный блокконтроля и управления измеряет параметры входного и выходного напряжения токи каждого модуля преобразователятемпературные параметры.Блок контроля управляет величинами выходного тока и напряжения отображает текущие значения основных параметров.
Расчет и выбор основного и вспомогательного оборудования
1 Расчет автоматической линии
Для расчета автоматической линии используются следующие данные:
-производительность линии: Sгод.= 25000 м2год;
-Два типа деталей: S1 = 00063 м2 S2 = 00150 м2.
-коэффициент исправимого брака: = 2%;
-число праздничных дней в году: tп = 9 дней;
-число выходных дней в году: t0 = 104;
-продолжительность работы оборудования за сутки: = 16 ч;
-число предпраздничных дней в году: tпп = 9 дней;
Габаритные размеры ванн представлены на рисунке 3.13.2:
Рисунок 3.1 – Ванна полипропиленовая для химических операций.
Рисунок 3.2 – Ванна полипропиленовая для гальванических операций.
Номинальный фонд рабочего времени Т0 рассчитывается по формуле [1]:
Т0 = (tг – t0 – tп). t – tпп. t1 (3.1)
где tг - число дней в году;
t0 - число выходных дней в году;
tп - число праздничных дней в году;
t - длительность рабочей смены;
tпп - число предпраздничных дней в году;
t1 - число часов на которые сокращается рабочий день в предпраздничные дни.
Т0 = (365 – 104 – 9) .16 – 2.9 = 4014 ч
Действительный фонд работы оборудования Тд рассчитывается по формуле:
Тд = Т0. (1 - Кп) (3.2)
где Кп – коэффициент простоя оборудования.
Тд = 4014.(1-008) = 369288 ч
Эффективный фонд работы оборудования Тэф рассчитывается по формуле:
Тэф = Тд – (tг – t0 – tп).tтц (3.3)
где tтц – время технологического цикла ч.
Тэф = 369288 – (365 – 104 – 9).1 = 344088 ч
Время электрохимического цинкования Т мин рассчитывается по формуле:
где = 910-6 - толщина покрытия м;
ρ = 7292 - плотность покрытия Zn- Co с содержанием 9% N
ВТ = 093 - выход по току[5].
где wZnwCo – процентное соотношение компонентов в сплаве;
qZnqCo – электрохимический эквивалент цинка и кобальта гА·ч[9].
Необходимое количество ванн n рассчитывается по формуле[10]:
где tосн - время основной операции мин;
tвсп - вспомогательное время мин;
R - ритм выдачи мин.
Задаемся предполагаемым R и рассчитываем количество ванн. Рассчитанное количество ванн округляем до большего целого числа и определяем коэффициент использования ванн Кисп %
Полученные данные о количестве ванн и коэффициенте использовании ванн сводим в таблицу 3.1.
Таблица 3.1 Зависимость количества ванн от ритма выдачи.
Данные таблицы свидетельствуют о том что при небольшом ритме выдачи достигается наибольший коэффициент использования ванн но при этом число ванн максимально. Это в свою очередь приводит к значительному увеличению длины линии сложности технологической подвязки большому количеству контрольно-измерительных приборов и средств автоматизации к увеличению числа автооператоров обслуживающих линию к возрастанию капитальных затрат по обслуживанию линии. При увеличении ритма выдачи значительно сокращается количество ванн что приводит к снижению длины линии и упрощению ее обслуживания при этом уменьшается коэффициент использования ванн. Для высоких ритмов выдачи высока технико-экологическая опасность – огромны капитальные затраты при замене ванн больших размеров. Необходимо выбирать оптимальное значение ритма выдачи.
Принимаем для процесса нанесения сплава цинк-кобальт R = 10 мин.
Рассчитаем коэффициент использования ванн для данного ритма выдачи по формуле 3.6:
Поверхность единовременной загрузки Sед.загр м2 определяется по формуле [1]:
где - коэффициент исправимого брака.
Количество деталей на подвеске определяется по формуле [1]:
где Sдет – площадь поверхности одной детали (S1 = 00091 м2 S2=00015м2).
Для конструирования и расчета площади подвески необходимо учитывать сложность профиля деталей и РС электролита. Габариты подвески 2100×700 мм
Расчет размеров ванн необходимо вести по большей из подвесок.
Определим габариты ванны.
Длина ванны Lв мм рассчитывается по формуле [1]:
где l1 = 75 мм – расстояние от края подвески до торца ванны мм
l - длина подвески мм.
Внутренняя ширина ванны Вв мм электрохимической обработки рассчитывается по формуле [1]:
где в1 - ширина подвески с деталями мм;
в2 - расстояние от центра А до центра края подвески мм;
в3 - расстояние от края анода до торцов стенки мм;
п - количество катодных рядов.
Высота ванны Нв мм рассчитывается по формуле [1]:
где Н1 – высота подвески мм;
H2 - расстояние от нижнего края подвески до уровня электролита мм;
H3 - расстояние от верхнего края подвески до уровня электролита мм
H4 - расстояние от уровня электролита до края ванны мм.
Ширина линии Вл мм рассчитывается по формуле [1]:
где Lв -длина ванны мм;
В1 - расстояние от края ванны до металлоконструкции мм;
В2- расстояние от края ванны до наружной плоскости площадки обслуживания мм.
Необходимое число автооператоров nа рассчитывается по формуле [1]:
где Т1 – суммарное время горизонтального перемещения с.
n1 – количество позиций в линии;
– скорость горизонтального перемещения автооператора мс (1 = 036 мс).
Т2 – суммарное время на подъем и опускание с:
где Т2 - среднее время подъема и опускания с
n2 – количество позиций с однократным обслуживанием ванны;
n3 – количество позиций с двукратным обслуживанием ванны;
n4 – количество позиций с трехкратным обслуживанием ванны.
где h – геометрическая высота подъема м;
– скорость вертикального перемещения мс (2 = 02 мс).
Т3 – суммарное время пауз с:
где Т’3 – время паузы с
n1 – число позиций с длительностью менее 60 с;
n2 – число позиций с длительностью более 60 с.
Т’4 – время простоя над позициями с:
Т5 – суммарное время простоя автооператора над позициями с опущенными деталями с:
Принимаем для работы АГЛ 2 автооператора.
2 Построение циклограммы
Циклограмма – это графическое или табличное изображение функциональных перемещений автооператора при выполнении им последовательности переноса технологических спутников по позициям с соблюдением заданной длительности технологических операций.
При построении циклограммы были использованы следующие условные обозначения:
– рабочий ход автооператора – перемещение автооператора с технологическим спутником;
– холостой ход автооператора – перемещение автооператора без технологического спутника;
– позиция разгрузки;
- время выстоя автооператора над позицией.
Цикл работы автооператора состоит из подциклов каждый из которых равен ритму выдачи. Цикл работы автооператора включает время в течение которого автооператор должен выполнить операции по обслуживанию ванн находящихся в зоне его действия и вернуться на исходную позицию.
Построенная циклограмма позволяет определить следующие параметры:
)уточненный ритм выдачи (R = 10 мин.);
)последовательность выполнения транспортных операций;
)фактическую длительность технологических операций (tц = 194 мин)
)время проведения основных операций:
- Нанесение сплава – 10 мин;
- травление – 35 мин;
- улавливание – 30 с;
- горячая промывка – 60 с;
- холодная промывка- 30-40 с;
3Расчет и подбор вспомогательного оборудования
3.1 Подбор источника питания
В качестве источника для ванн электрохимического обезжиривания травления нанесения покрытия выбираем выпрямительный агрегат PS 800-PU который обладает рядом технических преимуществ а именно:
- Максимальное выходное напряжение. . . . . . . . . . . . . . . . . . . . . . . . .30 В
- Максимальный ток нагрузки . . . . . . . . . . . . . . . . . . . . . . . . . . . . . . . . 800 А
- Точность установки тока в режиме ручного управления . . . . . . . . . ±05 А
- Точность установки тока в режиме управления от компьютера . . .±01 А
- Типичное значение . . . . . . . . . . . . . . . . . . . . . . . . . . . . . . . . . . . . . . . .±01 А
- Пульсации выходного напряжения не более . . . . . . . . . . . . . . . . . . . .20 мВ
- Напряжение питания . . . . . . . . . . . . . . . . . . . . . . . . . . . . . . . . . . . . . . .3×380 В
- Частота питающей сети . . . . . . . . . . . . . . . . . . . . . . . . . . . . . . . . .50÷60 Гц
- Потребляемая мощность не более . . . . . . . . . . . . . . . . . . . . . . . . . . .30 кВт
- Необходимый расход воды не менее . . . . . . . . . . . . . . . . . . . . . . . .4 лмин
- Вес . . . . . . . . . . . . . . . . . . . . . . . . . . . . . . . . . . . . . . . . . . . . . . . . . . . . . .360 кг
- Размеры . . . . . . . . . . . . . . . . . . . . . . . . . . . . . . . . . . . . . . . . .600×800×1700 мм
- Охлаждение блока – водяное и принудительное воздушное.
Для ванн нанесения покрытия необходимо 1 блок с токовой нагрузкой 800 А. Коэффициент запаса регулирования тока составит:
Для ванны электрохимического обезжиривания требуется установить 1 блок с общей токовой нагрузкой 800 А.
Коэффициент запаса регулирования тока составит:
Рассчитаем токоподводные шины для гальванических ванн. Шинопровод выполнен из медного пучка проволоки. Шинопровод рассчитывается по большей токовой нагрузке для ванн принимается соответственно расчетному.
Площадь сечения шинопровода [2]:
Кз = 12-13 – поправочный коэффициент запаса токовой нагрузки.
Длина шинопровода определяется расстоянием от ванны да места установки блока источника тока. Максимальная длина шинопрововода составляет 10 метров. Рассчитаем сопротивление и падение напряжения на шинопроводе:
где ρ = 15510-8 Омм2м- удельная электрическая проводимость меди;
Sш = 7510-6 м2 - площадь сечения проводника;
l = 15 м - длина проводника.
Температура свободноподвешенного в воздухе токоподвода [1]:
где tок – температура окружающей среды 0С;
k – коэффициент учитывающий условия теплоотдачи Вт(мм2град).
3.2 Подбор и расчет материала подвески
Материал подвески: медь покрытая прессованным углепластиком который обладает малым весом высокой прочностью и износостойкостью устойчив в агрессивных средах плохо смачивается водой что значительно уменьшает унос электролитов. Расчет толщины токоведущей части необходимо производить с учетом максимально возможной токовой нагрузки на линии т.е 600А.
Определим толщину токоведущей части подвески [1]:
где Sш – площадь сечения проводника.
Толщину токоведущей части подвески 115 мм толщина углепластикового покрытия составит 2 мм. Таким образом толщина подвески составит 135 мм.
3.3 Подбор системы бортовой вентиляции
На ваннах электрохимического химического обезжиривания травления активации нанесения покрытия и горячей промывки устанавливаются горизонтальные бортовые отсосы. Ширина щели составляет 5 см. Размер бортовых отсосов определяется шириной ванн.
Удельный объем отсасываемого воздуха определим по формуле [20]:
где Ввн Lвн –внутренние ширина и длина ванны м;
Нр – расстояние от зеркала электролита до борта ванны (015 м).
Для ванн химической обработки:
Для ванн электрохимической обработки:
Расчет объема воздуха отсасываемого от зеркала ванн производят по формуле [20]:
где KΔt – коэффициент учитывающий разность температур раствора и помещения при разности 0 – 10 при разности 10 – 116 при разности 20 – 131[20];
КT – коэффициент учитывающий токсичность и интенсивность выделения вредных веществ. Для ванн нанесения покрытия 08 для ванн травления 09 для ванн химического и электрохимического обезжиривания 08 для ванны активации 07 для ванн хромитирования 08 [20];
K1 – коэффициент учитывающий тип отсоса (односторонний – 18; двусторонний – 10)[20];
К2 – коэффициент учитывающий наличие воздушного перемешивания раствора (барботаж – 12; без перемешивания – 1) [20];
Значения всех коэффициентов для бортовых отсосов расположенных у различных ванн сведем в таблицу 2.20.
Таблица 2.20 – Коэффициенты для расчета воздуха удаляемого бортовыми отсосами
Наименование операций
Электрохимическое обезжиривание
Общий объем воздуха который необходимо отсасывать от гальванической линии составит:
По полученным данным расчета выбираем центробежный вентилятор с одним входом Systemair CE 280-4. Характеристики: CE 280-4 2895 м3час 60 dB(A) 1270 Вт 27.3 кг 455x233x547 мм.
3.5 Подбор насосов для ванн промывок обезжиривания травления.
- Производительность мах м3ч – 35
- Потребляемая мощность кВт – 1
- Напряжение питающей сети В – 380
- Габариты мм – 390x182x160
3.6 Подбор электронагревательного оборудования.
Для разогрева ванн можно использовать нагреватели USV-115 R.
Таблица 2.21 – Технические характеристики блока нагревателей.
Число элементов в блоке
Ширина блока нагревателей
Максимальная мощность блока
Диапазон регулирования температуры
Материал корпуса нагревательного элемента
Точность поддержания температуры
Высота блока нагревателей мм
рН нагреваемых растворов
Для разогрева ванны горячей промывки необходимо затратить 339460 кДж тепловой энергии.
Рассчитаем тепловой поток для разогрева ванны по формуле [16]:
где = 1800 с – время разогрева ванны.
Рассчитаем мощность электронагревателей по формуле [16]:
где k = 102-105 – коэффициент учитывающий потери при преобразовании электрической энергии в тепловую [16].
Рассчитаем количество блоков по формуле [16]:
Принимаем количество нагревательных элементов в ванне равным 7.
Рассчитаем количество затраченной энергии на нагрев ванны[5]:
3.7 Подбор систем очистки и регенерации растворов.
Расчет установки фильтрации.
Предназначена для удаления из электролитов и растворов механических примесей в процессе работы.
Выберем тканевый фильтр для фильтрации раствора после кристаллизации.
Определим время фильтрации по формуле:
где – вязкость фильтрата 1110-3 Пас;
rв – массовое удельное сопротивление осадка 7861010 мкг;
Δр – перепад давления на фильтре 68104 Па;
hос – высота слоя осадка 0005м;
Rф.п. – сопротивление фильтровальной перегородки 41109 м-1;
Vф – объем фильтрата 107022 л.
Рассчитаем поверхность фильтрования
где V – производительность м3ч;
К – коэффициент учитывающий увеличение поверхности из-за увеличения сопротивления фильтровальной перегородки в ходе работы (К = 08);
vуд – удельный объем фильтрата м3м2.
Эту поверхность может обеспечить фильтр марки Д18-18У с поверхностью фильтрования 18 м2.
Расчет гиперфильтратора
При расчете аппарата гиперфильтрации выбираем фильтровальную мембрану МГА-95 с удельной производительностью G = 250 лм2·сут и селективностью A = 95 %.
Объем фильтрата находим по формуле [1]:
где Ск и Сн – начальная и конечная концентрация компонента в концентрате (Ск Сн = 100).
Определим рабочую поверхность [1]:
Количество блоков исходя из площади 1 блока = 05 м2.
Конструктивно выбираем аппарат с плоскопараллельным расположением мембран.
Расчет электролизера для извлечения цинка и кобальта.
Принимаем время процесса 8 часов за которые концентрация сульфата никеля уменьшиться 6394 до 05 гл. Vр = 0209 м3 – объем раствора поступающего на очистку;
Определим токовою нагрузку на электролизере по формуле [1]:
где Cн = 6394 гл Ск = 05 гл – начальная и конечная концентрация N
V = 209 л – объем раствора;
q = 1085 г(Ач) – электрохимический эквивалент;
– время электролиза ч;
ВТ – выход по току (принимаем 95).
Определим истинную площадь электродов принимая SA = SK.
где i – плотность тока Ам2.
Рассчитаем количество водорода выделившегося на катоде:
Определим напряжение на электролизере по формуле [1]:
К – коэффициент газонаполнения;
– электропроводность раствора Смм.
UM – падение напряжения в мембране В.
Удельные энергозатраты составят [1]:
4 Расчет нагрузок на ванну
Рисунок 1 – Схема нагрузки ванны
Расчет нагрузок га ванну необходимо производить по опасному сечению т.е тем местам где корпус ванны подвержен наибольшим воздействиям. По результатам расчета принимается толщина корпуса уточняется необходимость и вид поддерживающего каркаса. Наиболее опасные места в гальванической ванне это:
) Дно между опорами при максимальном расстоянии между ними (по длине).
) Боковые стенки от середины ванны до его дна по оси.
В данных местах при большой нагрузке и недостаточной прочности материала может наблюдаться деформация или повреждение корпуса что недопустимо.
4.1 Расчет нагрузки на дно ванны:
где S = 054 м2 – площадь занимаемая раствором ограниченная проекцией опор;
Н = 12 м – высота раствора;
ρ = 119411 кгм3 – плотность раствора нанесения покрытия;
g = 981 мс2 – ускорение свободного падения.
Нагрузка на дно ванны у стен:
Решение системы уравнений:
Рисунок 2 – Эпюра сил действующих на дно ванны
Построим эпюру изгибающих моментов:
Рисунок 3 – Эпюра изгибающих моментов
4.2 Расчет нагрузки на стенки ванны
Рисунок 4 – Эпюра сил действующих на стенки ванны
Рисунок 5 – Эпюра изгибающих моментов
5 Обоснование конструкционных материалов и мероприятия по защите от коррозии
ГОСТ 5272-68 определяет коррозию как процесс самопроизвольного окисления (разрушения) металлов вследствие химического или электрохимического взаимодействия их с коррозионной средой. Это взаимодействие ведет к частичному или полному разрушению металла.
Профилактика коррозии начинается уже на этапе производственного проектирования назначением мер по защите от коррозии выбором оптимальных материалов конструктивных форм производственных технологических процессов в соответствии с условиями эксплуатации оборудования.
Основными конструкционными материалами для изготовления оборудования цехов электрохимических покрытий легированные (нержавеющие) стали марок 12х18н9т 12х18н10т полипропилен винилпласт фторопласт углепластик применяют для изготовления ванн нагревателей бортовых отсосов подвесок.
(ГОСТ 613-79) применяют для изготовления шинопроводов различных токопередающихузлов нагревателей. В настоящее время одной из актуальных проблем производства является защита оборудования цехов электрохимических покрытий от коррозии в сильнощелочных сильнокислотных и окислительных средах. При выборе защитных материалов следует учитывать их химическую стойкость к данному виду агрессивного воздействия физико-механические свойства надежность экономичность безопасность эксплуатации.
Известны различные способы защиты оборудования от коррозии включающие использование химически стойких материалов пластмасс лакокрасочных материалов и эмалей.
С учетом практических данных для изготовления и защиты оборудования цехов электрохимических покрытий рекомендуются следующие материалы: кислотоупорная керамика полиэтилен полипропилен фторопласты стеклопласты резины и эбониты.
Для ванн без нагрева используется поливинилхлорид полиэтилен ВД. Для защиты промывных ванн целесообразно применять покрытия из резин и эбонитов герметики. Защита промывных ванн расположенных непосредственно после ванн травления осуществляется по шипу защиты самой травильной ванны. На практике для этой цели служат пластикаты пенопласт полипропилен.
Поливинилхлорид (ПВХ) и его сополимеры относятся к числу наиболее распространенных видов пластмасс. Для футеровки ванн можно использовать винипласт. Недостатки винипласта: невысокая теплостойкость (600С) и низкая ударопрочность. Наибольшее распространение для защиты оборудования получили пластикат прокладочный ПП-К7 (ОСТ 6-19-003-79) и пластикат рецептуры П57-40КЭ (ТУ 6-05-1146-75) толщина 2 мм.
На основании литературной обработки в качестве антикоррозийного материала для защиты ванн электрохимического обезжиривания и цинкования используют пластикат марок ПХ-22 (ТУ-6-19-051-130-90). Он эластичен термостабилен хорошо сваривается и обладает высокой химической стойкостью в горячих (до 400С) средах гальванических ванн стоек в H2SO4 HNO3 HCL щелочах окиси хрома и других средах. Пластикат пулестоек в хлористом железе и азотнокислом натре.
Для ванн пассивирования используют футеровку из пентопласта которую широко используют агрессивных средах при температуре до 120№. По химической стойкости в ряду термопластов он уступает только фторопластам.
В качестве защитного покрытия металлических поверхностей кронштейнов стоек стержней используют пластизоль который обладает более высокой химической и теплостойкостью.
Для изготовления бортотсосов вентиляционных коробов крышек к ваннам для наружной облицовки гальванической линии где неизбежны систематические обливы аппаратуры и коммуникаций агрессивными средствами используют листовой полипропилен (ТУ-6-05-1313-75) который имеет блестящую легко моющую поверхность высокую химическую стойкость обладает высоким сопротивлением ударным нагрузкам. В качестве теплоизоляционного материала используют стекловолокно.
Автоматизация и автоматические системы управления параметрами технологического процесса
Одним из основных направлений решения производственных задач является внедрение средств автоматизации и контрольно-измерительных приборов. Это необходимо для обеспечения необходимого качества покрытия а также для уменьшения доли ручного труда в управлении процессом на ваннах. Автоматизированному контролю подвергаются различные параметры технологического процесса: температура уровень растворов кислотность регулирование расхода и многое другое.
В практике регулирования температуры в гальванических линиях находят применение следующие датчики температуры: термопреобразователи сопротивления и электрические контактные термометры манометрические термометры.
Для контролирования температуры в ванне теплой промывки устанавливаем устройство которое состоит из термометра сопротивления типа ТСМ-0879 измерительного прибора (магнитного пускателя) и исполнительных механизмов (электронагревателей типа ТЭН).
В рабочих ваннах необходимо поддерживать такой уровень электролита чтобы подвеска с деталями всегда была покрыта слоем электролита постоянной толщины так как изменение этого параметра может влиять на распределение электрических полей в объеме электролита. Точность поддержания уровня составляет как правило ± 5 мм. Причины вызывающие изменение уровня следующие: вынос электролита с подвесками вынос электролита в бортовые отсосы и его испарение. Для контроля уровня применяют следующие методы: электроконтактный поплавковый ультразвуковой высокочастотный резонансный емкостной гидростатический.
Для контролирования уровня устанавливаем датчик поплавкового типа. Передача показаний от такого датчика к устройству сигнализации производится через бесконтактный ферромагнитный передатчик. Использование такого способа передачи позволяет избежать утечек тока из ванны.
Регулирование уровня в промывных ваннах по существу отсутствует. Чистая вода подается в ванну для разбавления концентрации электролитов и выливается через сливные отверстия на очистку или регенерацию. Регулирование уровня в промывочных ваннах сводится к регулированию водоиспользования. Для этого предлагаются схемы управления подачей воды позволяющие уменьшить ее расход. Эти схемы предполагают наличие в автоматической линии запорных соленоидных вентилей на подводе воды к промывочным ваннам. По первому решению вода подается на промывочные ванны начиная с момента когда в них загружаются детали
и прекращается подача воды после подъема деталей из ванны промывки. Более экономичной является схема требующая большего числа приборов: установка на выходе из ванн концентратомеров по сигналу которых производится подача воды.
Несвоевременная корректировка значений рН электролита отрицательно сказывается на структуре и качестве осаждаемых покрытий. Требования к точности поддержания рН= ± (005-075). Регулирование рН в гальванических ваннах имеет свои особенности. Измерение рН происходит медленно период между корректировками составляет часы. Выравнивание среднего значения рН в ванне после внесения дозы корректирующего раствора зависит от размеров ванн загрузки способов перемешивания и составляет ~ 10 минут.
Дополнительная погрешность изменения рН в ваннах может быть на порядок больше чем основная допустимая погрешность рН-метра. Учитывая эти особенности для регулирования рН в гальванических ваннах целесообразно применять импульсные системы регулирования функционирующие следующим образом.
Определяется доза корректирующего раствора не вызывающая отклонения за допустимые пределы. Схема регулирования выдает эту дозу через время определенное через определяемое из условий усреднения значения рН в ванне производит измерение рН сравнивает измеренное значение с заданным и выдает если это необходимо следующую дозу.
Для автоматического контроля концентрации электролитов в гальваническом производстве нашли применение следующие способы: потенциометрический магнитометрический кондуктометрический денсиметрический способы способ титрования контроль по ампер-часам. Опыт внедрения в производство автоматических систем корректирующих добавки малыми порциями в интервале 30-200 с при полной нагрузке ванны показал что при этом поддерживается практически постоянный состав концентрации добавок. Экономия добавок колеблется от 30 до 80 % по сравнению с корректировкой ванн вручную.
Сравнительная характеристика спроектированного оборудования
Разработанная автооператорная линия предназначена для осуществления процесса нанесения сплава цинк-кобальт. Обозначенные решение способствуют сокращению производственных площадей и возможности реализации установки локальных схем очисток что позволяет возвратить в технологический цикл нанесения гальванопокрытия значительное количество ценных компонентов тем самым снизить материалоемкость процесса.
Была проведена установка трехкаскадных ванн промывок что позволило сократить производственные площади упростить сантехническую обвязку трубопроводами. Для сокращения выноса раствора из технологических ванн были установлены козырьки между технологическими и промывными ваннами с наклоном в сторону технологических ванн.
Линия комплектуется современным оборудованием: плунжерными дозировочными насосами центробежными однонаправленными вентиляторами серии RF которые защищены от воздействия влаги снабжены асинхронным двигателем с внешним ротором и уплотненными подшипниками что увеличивает срок их службы.
Список использованной литературы
Смоляг Н.Л. Технология электрохимических производств: учеб.-метод. Пособие для студентов специальности 1-48 01 04. – Минск: БГТУ 2007. – 92 с.
Смоляг Н.Л. Основное оборудование электрохимических производств: учеб.-пособ. – Минск: БГТУ 2004. – 83 с.
Гибкие автоматизированные гальванические линии: справочник В.Л.Зубченко В.И.Захаров В.М.Рогов и др.; под общ. Ред. В.Л.Зубченко. – М.: Машиностроени 1989. – 627 с.
Основные процессы и аппараты химической технологии: учеб. пособие по проектированию Г. С. Борисов [и др.]; под общ. ред. Ю. И. Дытнерского. – 2-е изд. перераб. и доп. – М.: Химия 1991. – 496 с.
Рекомендуемые чертежи
- 25.01.2023
- 24.01.2023