Проектирование линии для нанесения покрытия Sn-Bi




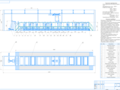
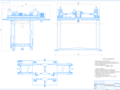
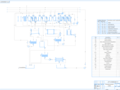
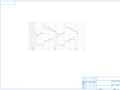
- Добавлен: 24.01.2023
- Размер: 1 MB
- Закачек: 0
Описание
Состав проекта
![]() |
![]() |
![]() ![]() ![]() |
![]() ![]() |
![]() ![]() ![]() ![]() |
![]() ![]() ![]() ![]() |
![]() |
![]() ![]() ![]() ![]() |
![]() ![]() ![]() ![]() |
Дополнительная информация
оборудование.docx
Учреждение образования
«БЕЛОРУССКИЙ ГОСУДАРСТВЕННЫЙ ТЕХНОЛОГИЧЕСКИЙ УНИВЕРСИТЕТ»
Кафедра химии технологии электрохимических производств и материалов электронной техники
по курсу “Оборудование и основы проектирования электрохимических производств”
тема проекта “Линия нанесения сплава олово-висмут на контакты”
Данный курсовой проект содержит стр. табл. рисунка литературных источника.
ЛИНИЯ ЭЛЕКТРОЛИТ ОБЕЗЖИРИВАНИЕ УПЛОТНЕНИЕ НАСОС АВТООПЕРАТОР ВЕНТИЛЯТОР ШИНОПРОВОД ЦИКЛОГРАММА
Объект изучения: линия нанесения покрытия сплавом олово-висмут медные детали (контакты).
Целью курсового проекта является расчет подбор и компоновка оборудования в линии нанесения покрытия рассчитать основное и вспомогательное оборудование построить циклограмму для автооператора подобрать автоматические системы управления параметрами технологического процесса обосновать выбор конструкционных материалов и мероприятий по защите от коррозии.
В проекте предусмотрена комбинированная газожидкостная ванна улавливания которая позволяет уменьшить унос электролита и снизить расход воды на промывку.
Проведена автоматизация автооператорной линии а также локальной схемы очистки сточных вод и регенерации отработанных электролитов.
При разработке проекта используются данные литературно-патентной проработки за 5 лет и материалы производственной практики.
Графическая часть включает:
– общий вид гальванической линии 1 лист формата
Аналитический обзор. . .
1 Характеристика оборудования для подготовки поверхности .
2 Характеристика основного оборудования .
3 Характеристика вспомогательного оборудования
Обоснование выбранного типа гальванического оборудования
Расчет и выбор основного и вспомогательного оборудования .
1 Расчет автоматической линии ..
2 Расчет и построение циклограммы работы линии
3 Расчет и подбор вспомогательного оборудования .. .
3.1 Подбор источника питания .
3.2 Подбор и расчет материала подвески .
3.3 Подбор системы бортовой вентиляции ..
3.5 Подбор насосов для ванн промывок обезжиривания травления
3.6 Подбор электронагревательного оборудования
3.7 Подбор систем очистки и регенерации растворов .
4 Расчет нагрузок на ванну
4.1 Расчет нагрузки на дно ванны
4.2 Расчет нагрузки на стенки ванны
Автоматизация и автоматические системы управления параметрами технологического процесса . ..
Сравнительная характеристика спроектированного оборудования ..
Список использованной литературы ..
Приложение А .. . .
Для придания поверхности деталей специфических свойств (высокой пластичности и паяемости) применяются оловянные покрытия с внедрением различных дополнительных металлов. Внедрение в оловянное покрытие висмута позволяет повысить износостойкость покрытия и его пластичность паяемость. Данные свойства позволяют увеличить срок службы и качество изделий.
Для достижения поставленных целей необходим правильный подбор основного и вспомогательного оборудования и операций. Модификация существующего и разработка нового оборудования позволяет сократить материальные и энергетические затраты производства что положительно сказывается на себестоимости продукции.
Электрохимическое получение покрытий сплавов обладает рядом преимуществ перед остальными методами:
- получение покрытий с определенными физическими свойствами;
- возможность регулирования заданных параметров получения покрытия а именно плотности тока толщины покрытия фазового состава;
- возможность регулирования состава покрытия и его свойств.
1 Характеристика оборудования для подготовки поверхности.
Все недостатки поверхностей деталей поступающих в гальванический цех перед нанесением покрытий устраняют механической химической или химико-механической обработкой.
В соответствии с технологией применяемое оборудование следует разделить на следующие группы:
- оборудование для механической подготовки поверхности;
- оборудование для подготовки поверхности в водных и неводных растворах;
Механическая подготовка предназначена для удаления с поверхности деталей неровностей царапин забоин заусенцев окалины и придания ей требуемой шероховатости. Качество обработки поверхности и ее шероховатость регламентируются ГОСТ 9.301-86.
Шероховатость поверхности — это совокупность неровностей с относительно малыми шагами образующих рельеф поверхности детали в пределах базовой длины. Численное значение шероховатости отсчитывается от средней линии профиля которая проводится так чтобы в пределах базовой длины среднее квадратичное отклонение профиля по этой линии было минимальным. Номенклатуру параметров числовые значения параметров и базовых длин а также типы направлений неровностей устанавливает ГОСТ 2789-73. Термины и определения шероховатости поверхности приведены в ГОСТ 25142-82.
При выборе способа механической подготовки поверхности учитываются следующие обстоятельства:
- требуемое качество обработки поверхности;
- наличие на поверхности дефектов степень загрязненности и коррозионного поражения;
- размеры и конфигурация деталей;
- объем и сроки выполнения работ;
- необходимость максимального ограничения ручного труда.
Оптимальным решением не всегда является использование одного метода обработки поверхности деталей в ряде случаев необходимо применение двух или нескольких дополняющих друг друга процессов. Выбор метода подготовки поверхности или их сочетания должен сопровождаться также расчетом экономической эффективности процессов. Кроме того способ механической подготовки поверхности определяется видом покрытия поскольку например блестящие хромовые никелевые серебряные покрытия снижают шероховатость поверхности матовый никель-хром не изменяет состояния поверхности а цинковые и фосфатные покрытия повышают значение
высот неровностей. При нанесении покрытий на медь или ее сплавы цинковые сплавы или коррозионностойкую сталь требуется блестящая поверхность при обработке углеродистой стали или чугуна поверхности чаще всего придают матовый вид.
К основным видам механической обработки поверхности относят: шлифование полирование крацевание виброобработку струйную абразивную и гидроабразивную обработки.
Для проведения операций шлифования-полирования основное используемое оборудование - шлифовально-полировальные станки (одно- и двухшпиндельные) станки-электродвигатели ленточные ручные и специальные станки. Шпиндель - вращающийся вал станков с устройством для закрепления заготовок и инструмента. Основной рабочий инструмент — шлифовально-полировальные круги или абразивная лента закрепленные на вращающихся шпинделях станков. Мощность привода электродвигателя в зависимости от типа деталей и размеров шлифовально-полировальных кругов колеблется от 06 до 3-5 кВт.
Подготовка поверхности в растворах производится практически непосредственно перед нанесением гальванопокрытий. Основное ее назначение - удаление жировых загрязнений смазок и масел продуктов коррозии окисных слоев остатков шлифовально-полировальных паст. К видам обработки относят: обезжиривание травление активацию химическое и электрохимическое полирование. В качестве рабочих растворов используют органические растворители щелочные моющие растворы кислотные растворы и жидкости.
Выбор способа обработки поверхности деталей зависит от характера количества и природы загрязнений. Если загрязнения имеют химическую природу (термическая окалина продукты коррозии сульфидные или оксидные пленки) т. е. образуются за счет взаимодействия поверхности металла с окружающей средой и связаны химическим сродством то их удаление осуществляется методом травления. Загрязнения которые удерживаются силами адгезии (консервационные смазки остатки полировальных паст абразива охлаждающих эмульсий) удаляются в процессе обезжиривания.
Жировые загрязнения минерального происхождения не растворимые в воде удаляются с помощью органических растворителей в качестве которых могут применяться хлорированные и нехлорированные углеводороды. Предпочтение следует отдавать хлорированным вследствие их большей безопасности в работе. По причине токсичности органических растворителей все работы с ними должны проводиться в специальных установках герметичного исполнения. Существуют два метода обработки: метод погружения в растворитель для отмочки и обработка в парах растворителя. При обработке по первому методу детали в корзинах или на подвесках загружают в сварные ванны прямоугольной либо цилиндрической формы которые для более эффективного разделения загрязнений снабжаются вставным дном различной формы. При обезжиривании в парах растворителя используют двухкамерные установки герметичного исполнения (не применяются для обработки титана и алюминиевых сплавов).
Химическое обезжиривание проводится либо после обезжиривания в органических растворителях либо как первый этап перед последующими операциями более тщательного обычно электрохимического обезжиривания. В первом случае химическое обезжиривание должно удалить следы загрязнений остающихся на деталях после испарения даже кажущейся чистой последней порции растворителя а во втором - в ванну химического обезжиривания поступают детали загрязненные большим количеством минеральных и органических веществ. В связи с этим могут несколько различаться составы растворов используемых при обезжиривании.
Основное оборудование для реализации процессов обезжиривания в водных растворах травления активации электрополирования — стационарные ванны которые снабжаются различными дополнительными устройствами располагаемыми внутри корпуса:
- барботерами (обезжиривание);
- нагревательными устройствами (в основном обезжиривание в некоторых случаях травление);
- устройствами для размещения деталей или приспособлений с деталями.
В зависимости от коррозионной активности среды ванны могут быть изготовлены из углеродистой стали (с футеровкой или без нее) или легированной стали толщиной 3- 5 мм. В нижней части корпуса ванны располагается сливной штуцер. Для уменьшения теплопотерь ванны снабжают теплоизоляцией.
При обезжиривании на поверхности раствора образуется пенный слой содержащий остатки жировых и других загрязнений. При последующем извлечении подвески с деталями будет происходит вынос загрязнений в последующие ванны промывки. По этой причине ванны обезжиривания должны снабжаться устройствами облегчающими удаление пенного продукта после завершения операции обезжиривания. Принцип работы устройства состоит в том что в ванне создают плавное без завихрений движение верхнего слоя жидкости направленное в сторону имеющегося в торцевом конце ванны кармана. Движение жидкости может создаваться путем доливки небольшого количества раствора (около 05 лм 2 поверхности раствора) отбираемого из средней части переливного кармана. Отбор раствора может осуществляться с помощью ручного (типов БКФ-2 БКФ-4 НР-20 НР-40) или электронасоса небольшой производительности. Добавка раствора в ванну обезжиривания поднимает его уровень выше края кармана и вызывает быстрый и полный слив пены и грязи с поверхности раствора в карман. Чтобы грязная пена сливалась в карман ровной сплошной струей по всей ширине ванны не застаиваясь и не взмучиваясь верхняя кромка кармана должна простираться поперек всей ванны от одной боковой стенки до другой и быть совершенно ровной строго горизонтальной. Глубина кармана равна рабочей глубине ванны. Это необходимо для того чтобы пена с раствором в кармане могла отстояться: твердые частицы осесть жиры всплыть а в средней части остаться достаточно чистый раствор. Удаление из кармана жиров и твердых частиц производится с помощью соответствующих штуцеров.
Ускорить проведение операции обезжиривания с одновременным улучшением качества обработки можно при использовании моечных машин или камер в которых реализуется процесс струйного обезжиривания. В таких машинах щелочной раствор нагретый до 70-90 °С непрерывно циркулирует и попадает на детали со всех сторон через специальные сопла под давлением 500-580 кПа. Применение многокамерных машин позволяет одновременно проводить операции обезжиривания промывки и сушки.
1Характеристика основного оборудования
Для нанесения гальванических и химических покрытий применяются следующие виды оборудования: ванны (стационарные колокольные барабанные) и автоматические конвейерные установки.
Различие в конструкции стационарных ванн определяется характером процесса для которого применяется данная ванна составом раствора его рН а также особенностями технологического процесса требующими подогрева или охлаждения электролита перемешивания качания штанг непрерывной фильтрации наложения различных физических факторов (ультразвук магнитное поле проток электролита).
Ванны представляют собой емкости прямоугольной формы которые являются «держателями» гальванических растворов. Они предназначены для проведения процессов нанесения покрытия а также для подготовительных и окончательных операций. Внутренние размеры ванн определяются ГОСТ 23738 – 85. Ванны и агрегаты для щелочных электролитов изготавливают из стали без футеровки. Ванны для щелочных цианистых электролитов рекомендуется футеровать внутри резиной винипластом полифторэтиленом полипропиленом. Ванны в которых находятся кислые и слабокислые электролиты снабжают кислотоупорной футеровкой либо изготавливают из кислотостойких материалов.
Промывочные ванны по количеству позиций обработки делят на одно- и многопозиционные (каскадные). Применение ванн каскадной промывки резко сокращает расход промывочной жидкости без ущерба качеству очистки поверхности изделий. Двухпозиционная ванна каскадной промывки в теплой воде состоит из корпуса с карманом и перегородкой разделяющей ванну на два отсека: левый и правый. В каждом отсеке установлены четыре опоры – ловителя наддонный коллектор нагрева сливной штуцер. Левый отсек кроме того имеет барботер с двумя ветвями а правый – наливную трубу. В нижней зоне кармана установлен сливной штуцер.
Автооператоры предназначены для транспортирования изделий по технологическим позициям автоматических и механизированных линий для химической и электрохимической обработки поверхности основного металла и получения металлических и неметаллических покрытий.
Автоматизированные гальванические линии требуемые современному производству должны сочетать в себе технологическую гибкость высокую производительность и экологичность. Характерный для большинства гальванических производств многономенклатурный входной поток деталей определяет проблему автоматического функционирования таких линий состоящую в необходимости адаптации к потоку подлежащих обработке деталей и систем водосбережения дозировки и очистки. Одним из путей решения этой задачи являются роботизированные гальванические линии.
Реализуемая экологическая концепция роботизированных гальванических линий – это:
Безаварийность достигаемая применением бессточных ванн опорожняемых полипропиленовыми переносными насосами.
Малоотходность за счет программирования времени стекания над каждой ванной обеспечения значительного возврата выносимых растворов.
Снижение концентрации гальваностоков с помощью ванн-уловителей со встроенными электролизерами.
Организация системы дозирования промывок - вливается количество воды пропорциональное площади погружаемых деталей.
В зависимости от видов применяемых автооператоров автоматизированные гальванические линии делятся на два основных типа: с подвесными или портальными автооператорами. В меньшей степени для гибких автоматизированных гальванических линий целесообразно применение консольных автооператоров. Другим важным признаком является тип используемых технологических спутников или кассет: подвески барабаны корзины или их комбинации.
Появление в последние годы гальванических манипуляторов с расширенными функциональными возможностями позволяющими активно участвовать в формировании сточных вод по концентрации и объему в значительной степени способствует созданию и успешному внедрению малоотходных и безотходных технологических процессов нанесения покрытий. Многофункциональные манипуляторы имеют ряд дополнительных механизмов устройств приспособлений позволяющих уменьшить вынос электролитов из гальванических ванн формировать стоки по концентрации и объему. Применение этих манипуляторов позволяет обслуживать узкие вспомогательные ванны что дает возможность уменьшить общую длину гальванической линии уменьшить расход химикатов.
3 Характеристика вспомогательного оборудования
К вспомогательному оборудованию относятся фильтровальные установки насосы для перекачки электролитов различные ёмкости для хранения транспортировки и корректировки растворов а также сушильное оборудование и источники питания ванн.
Фильтровальные установки предназначены для очистки электролитов от различных загрязнений. Электролиты очищают от механических загрязнений при помощи периодической или постоянной фильтрации. Периодическая фильтрация осуществляется через суконный рамочный фильтр. Для фильтрации электролитов применяют аэрофильтры и переносные фильтры. Наиболее тщательная очистка электролита может быть достигнута при помощи фильтр-пресса состоящего из чередующихся рам и плит между которыми проложена фильтровальная ткань.
Как для фильтрации так и для перекачки растворов необходимы насосы. Различают насосы двух основных типов: динамические и объемные. В динамических насосах жидкость перемещается при воздействии сил на незамкнутый объем жидкости который непрерывно сообщается с входом в насос и выходом из него. Динамические насосы по виду сил действующих на жидкость подразделяются на лопастные (центробежные и осевые) и насосы трения (вихревые и струйные). В объемных насосах жидкость перемещается (вытесняется) при изменении замкнутого объема жидкости который периодически сообщается с входом в насос и выходом из него. Группа объемных насосов включает насосы в которых жидкость вытесняется из замкнутого пространства телом движущимся возвратно - поступательно (поршневые плунжерные диафрагменные насосы) или имеющие вращательное движение (шестеренчатые пластинчатые винтовые насосы).
В зависимости от характера перекачиваемого электролита применяют кислотостойкие или щелочестойкие насосы. Наиболее часто применяют насосы – центробежные для химических производств с горизонтальным подводом жидкости по оси центробежные погружные насосы центробежные герметичные насосы насосы – дозаторы.
Центробежные химические насосы применяют для подачи кислот щелочей и солей. Производительность таких насосов 5-100 м3ч допустимая высота всасывания 5-6 м водяного столба.
Насосы центробежные погружные применяют для перекачивания химически активных чистых и загрязненных жидкостей с температурой до 80оС. Содержание абразивных включений в перекачиваемой жидкости должно быть не более 02% по массе и размером частиц до 02 мм. В частности насосы в цехах гальванопокрытий применяют для перекачивания из сборников кислых и щелочных промывных стоков загрязненных шламом и фильтрующими материалами углем асбестом. Производительность таких насосов 5-25 м3ч напор не превышает 25 м водяного столба.
Насосы центробежные герметичные взрывозащищенного исполнения применяют для перекачки электролитов хромирования и концентрированной серной кислоты. Производительность их 10 м3ч допустимый напор 21-55 м водяного столба.
Насосы-дозаторы – одноплунжерные горизонтальные насосы простого действия с подачей регулируемой вручную при остановленном электродвигателе. Насосы-дозаторы применяют для объемного напорного дозирования нейтральных и агрессивных жидкостей эмульсий и суспензий с концентрацией неабразивной твердой фазы до 10% по массе при температуре до 200оС. В гальванических цехах эти насосы применяют для выполнения корректировочных работ по подаче кислых и щелочных растворов. После окончания перекачки жидкостей склонных к выделению солей и кристаллизации необходимо промыть насос что предупреждает преждевременный износ плунжера и уплотнения. Производительность таких насосов 06-25 м3ч максимальное давление нагнетания 1Мпа.
Выбор сушильного оборудования определяется в основном массой габаритными размерами и производительностью линии. Наиболее часто в механизированных и автоматических линиях используют сушильную камеру. При работе на стационарных ваннах сушку деталей производят вне линии рабочих ванн для чего используют сушильные шкафы.
Для подвешивания деталей в электролитическую ванну используют специальные подвески и приспособления. Выбор подвесок зависит от конфигурации деталей размеров ванны типа электролита и т.д. Приспособления для подвешивания деталей в гальванические ванны должны удовлетворять следующим требованиям: обеспечивать хороший контакт с покрываемой деталью и токоподводящей штангой обеспечивать получение равномерного покрытия не допускать циркуляцию электролита к участкам деталям не подлежащих покрытию не допускать экранирования мест подлежащих покрытию.
Для питания гальванических ванн используется постоянный ток получаемый от источников питания – полупроводниковых выпрямителей. От технических характеристик источников питания зависит эффективность технологического процесса: качество гальванопокрытий производительность экономические показатели.
Выпрямитель состоит из трансформатора преобразующего ток высокого напряжения (220 или 380 В) и малой силы в ток низкого напряжения и большой силы и электрических вентилей главным образом на основе тиристоров преобразующих переменный ток в постоянный.
Наиболее распространены выпрямительные агрегаты серии ВАК и ВАКР (В – выпрямительный А – агрегат К – кремниевые вентили Р - реверсивный). Агрегаты имеют ручное плавное регулирование выпрямленного напряжения автоматическую стабилизацию выпрямленного напряжения и тока с точностью стабилизации ±5% плотности тока с точностью стабилизации ±10%. Реверсивные агрегаты серии ВАКР кроме того могут работать в следующих режимах: ручное и автоматическое реверсирование выпрямленного тока длительная работа с любой полярностью выпрямленного тока. Ориентировочный срок службы агрегатов 15-20 лет. Вероятность отказа при работе на протяжении 500 ч не ниже 075.
В связи с возросшими требованиями к качеству гальванопокрытий и с развитием новых комплектующих изделий (сильноточных тиристоров микросхем и т.п.) была разработана и активно внедряется в производство новая серия преобразователей типов: ТЕ ТЕР ТВ ТВР и ТВИ (Т - тиристорный Е - естественное охлаждение В - водяное охлаждение тиристоров Р - реверсивный И — импульсный). В выпрямителях этой серии существенно улучшены технические показатели: повышена точность стабилизации напряжения и тока до ±3 % а плотности тока - до ±6 % снижена пульсация выпрямленного тока предусмотрено дистанционное и программное управление выпрямителями повышен КПД на 1-15 % уменьшены габаритные размеры унифицированы схемные и конструктивные решения агрегатов и их узлов что в свою очередь улучшило их ремонтоспособность. Диапазон ручного регулирования тока и напряжения от 10 до 100%. Реверсивные агрегаты позволяют получать постоянный ток с автоматической и ручной сменой его полярности. В агрегатах предусмотрена раздельная установка значений постоянного тока и напряжения каждого направления с длительностью от 2 до 200 с (дискретность 2 с) прямого тока и от 02 до 20 с обратного тока (дискретность 02 с). Импульсные агрегаты ТВИ обеспечивают на выходе как импульсный ток так и постоянный. Длительность импульсов тока от 001 до 01 с и пауз между ними от 003 до 05 с. Импульсные агрегаты в зависимости от типа комплектуются дополнительными устройствами: пультом дистанционного управления пультом программного управления сглаживающим реактором.
С целью расширения технологических возможностей и повышения эффективности процесса удаления газов аэрозолей и испарений предложен способ для регулирования количества отсасываемого воздуха в бортовых отсосах гальванических ванн и установка для его осуществления. Установка для гальванохимической обработки и горячей промывки содержит ванны бортовые вентиляционные отсосы оснащенные поворотными заслонками и внешними исполнительными органами для фиксированного поворота последних вокруг своих осей. При этом каждый из бортовых отсосов оснащен элементом с термодеформируемой поверхностью в качестве которых используют материалы с термомеханической памятью24.
Промышленные сточные воды после обезвреживание и нейтрализации содержат остатки веществ в виде ила (например гидроокись тяжелых металлов). Для их удаления предназначены установки осветления (седиментации) после чего вода может быть сброшена в канализационную сеть (остаток веществ менее 1 млл) или в природный водоем (остаток веществ менее 03 млл). Преимущества данных установок: небольшая занимаемая площадь высокая производительность непрерывное извлечение жидкого или и невозможность «прорывов» ила в осветленную воду легкая компоновка с предварительными очистными сооружениями. Установка осветления включает в себя два отстойника и «осциллирующую систему отстаивания ила». В первом отстойнике отделяется уже 9% ила второй отстойник нагружается только пылевидным илом. Осциллирующая система подводится непосредственно к месту отсасывания ила что является значительным преимуществом. Выпускаются несколько типов установок различной производительности.
Обоснование выбранного оборудования
Предлагается использовать однорядную линию с подвесным манипулятором тележечного типа для осуществления технологического процесса нанесения покрытия олово-висмут.
Автоматическая линия представляет собой прямолинейный ряд ванн установленных в определенном порядке на металлоконструкции в соответствии с техпроцессом. Над ваннами к потолку крепятся ездовые пути по которым перемещается автооператор.
С одной стороны линии установлена площадка обслуживания. Вся сантехническая обвязка линии технологическими трубопроводами располагается под площадками обслуживания и доступ к ней возможен сбоку линии и через съемный настил.
Линия обслуживается двухрельсовым манипулятором подвесного типа (автооператор тележечный A-200Т2).
Технические характеристики:
Грузоподъемность не более 250 кг.
Горизонтальная рабочая скорость при заводской установке (частота 50 Гц) - (033 ± 005) мc т.е (20 ± 3) м мин.;
горизонтальная в ручном режиме при разгоне и торможении - (007 ± 001) мc т. е. (4 ± 08) м мин.;
Скорость перемещения груза вертикальная - (0116 ± 003) мc т. е. (7 ± 014) м мин.;
Установленная номинальная мощность электродвигателей:
- привода тележки – 037 кВт;
- привода подъемника – 055 кВт.
Входные питающие напряжения:
- переменное трехфазное – 380 В частотой – 50 Гц;
- переменное трехфазное 36 В частотой – 50 Гц;
- постоянное – 24 В;
- переменное однофазное – 24 В частотой – 50 Гц.
Автооператор предназначен для перемещения деталей находящихся на подвесках катодной штанги или в барабанном контейнере.
Преимущества данного манипулятора:
- манипулятор может работать в следующих режимах (ручной режим “от кнопки на позицию” автоматический режим.
- манипулятор обладает устройством для встряхивания подвески с деталями.
- большая грузоподъемность – 250 кг.
- работа от любого промышленного источника питания.
Ванны электрохимического обезжиривания травления нанесения покрытия горячей промывки снабжены бортовыми отсосами с системой фильтрации воздуха на базе волокнистого фильтра ФВГ-М с производительностью 2.5-40 тыс. м3ч.
При этом степень очистки воздуха составит не менее 95%. Все ванны установлены на опорные изоляторы. Ванны изготовлены из полипропилена и имеют поддерживающий каркас из нержавеющей стали.
Трубопроводы подачи электролитов слива концентрированных стоков спроектированы из полипропиленовых труб. Запорная арматура – из чугуна футерованного фторопластом.
Для объемного напорного дозирования нейтральных и агрессивных жидкостей эмульсий суспензий предлагается использовать насос центробежный муфтовый НЦ.М3-4. Предназначен для перекачивания агрессивных и нейтральных жидкостей с плотностью не более 1200 кгм и температурой от +7 до +60°С. Бессальниковая конструкция насоса исключает утечку перекачиваемой жидкости и ее контакт с химически нестойкими материалами.
Также целесообразно применять для нанесения сплава на основе олова выпрямительный агрегат для гальваники который обладает рядом технических преимуществ:
- Возможность работы в агрессивных зонах гальванических производств
- Модульная конструкция
- Микропроцессорный блокконтроля и управления
На гальванической линии установлен источник тока PS 60-PU-R.
Данный источник тока удовлетворяет потребностям линии после модернизации в результате чего его можно использовать для электрохимического обезжиривания и нанесения покрытия.
Технические характеристики:
- Максимальное выходное напряжение. . . . . . . . . . . . . . . . . . . . . . . . .30 В
- Максимальный ток нагрузки . . . . . . . . . . . . . . . . . . . . . . . . . . . . . . . . 60 А
- Точность установки тока в режиме ручного управления . . . . . . . . . ±05 А
- Точность установки тока в режиме управления от компьютера . . .±01 А
- Типичное значение . . . . . . . . . . . . . . . . . . . . . . . . . . . . . . . . . . . . . . . .±01 А
- Пульсации выходного напряжения не более . . . . . . . . . . . . . . . . . . . .20 мВ
- Напряжение питания . . . . . . . . . . . . . . . . . . . . . . . . . . . . . . . . . . . . . . .380 В
- Частота питающей сети . . . . . . . . . . . . . . . . . . . . . . . . . . . . . . . . .50÷60 Гц
- Потребляемая мощность не более . . . . . . . . . . . . . . . . . . . . . . . . . . .18 кВт
- Необходимый расход воды не менее . . . . . . . . . . . . . . . . . . . . . . . .4 лмин
- Вес . . . . . . . . . . . . . . . . . . . . . . . . . . . . . . . . . . . . . . . . . . . . . . . . . . . . . .70 кг
- Размеры . . . . . . . . . . . . . . . . . . . . . . . . . . . . . . . . . . . . . . . . .200×300×210 мм
- Охлаждение блока – водяное и принудительное воздушное.
Особенности прибора:
- Прецизионное линейное регулирование больших токов;
- Низкий уровень пульсаций акустических и электромагнитных помех;
- Возможность аварийного выключения по внешнему управляющему сигналу (например сигналу с датчика потока воды);
- Защита от перегрузки перегрева короткого замыкания и обрыва цепи нагрузки;
- Возможность компьютерного управления по последовательному порту
- Возможность работы в агрессивных зонах гальванических производств;
- Работа на постоянном реверсивном и импульсном токе;
- Модульная конструкция;
- Микропроцессорный блок контроля и управления;
Расчет и выбор основного и вспомогательного оборудования
1 Расчет автоматической линии
Для расчета автоматической линии используются следующие данные:
-производительность линии: Sгод.= 15000 м2год;
-Два типа деталей: S1 = 13210-6 м2 S2 = 10810-6 м2.
-коэффициент исправимого брака: = 2%;
-число праздничных дней в году: tп = 9 дней;
-число выходных дней в году: t0 = 104;
-продолжительность работы оборудования за сутки: = 16 ч;
-число предпраздничных дней в году: tпп = 9 дней;
Номинальный фонд рабочего времени Т0 рассчитывается по формуле [1]:
Т0 = (tг – t0 – tп). t – tпп. t1 (3.1)
где tг - число дней в году;
t0 - число выходных дней в году;
tп - число праздничных дней в году;
t - длительность рабочей смены;
tпп - число предпраздничных дней в году;
t1 - число часов на которые сокращается рабочий день в предпраздничные дни.
Т0 = (365 – 104 – 9) .16 – 2.9 = 4014 ч
Действительный фонд работы оборудования Тд рассчитывается по формуле:
Тд = Т0. (1 - Кп) (3.2)
где Кп – коэффициент простоя оборудования.
Тд = 4014.(1-008) = 369288 ч
Эффективный фонд работы оборудования Тэф рассчитывается по формуле:
Тэф = Тд – (tг – t0 – tп).tтц (3.3)
где tтц – время технологического цикла ч.
Тэф = 369288 – (365 – 104 – 9).1 = 344088 ч
Время электрохимического нанесения покрытия Т мин рассчитывается по формуле:
где = 610-6 - толщина покрытия м;
ρ = 7180 - плотность покрытия (сплава) гм3;
qсп = 219 - электрический эквивалент сплава гА.ч;
ВТ = 099 - выход по току.
Необходимое количество ванн n рассчитывается по формуле:
где tосн - время основной операции мин;
tвсп - вспомогательное время мин;
R - ритм выдачи мин.
Задаемся предполагаемым R и рассчитываем количество ванн. Рассчитанное количество ванн округляем до большего целого числа и определяем коэффициент использования ванн Кисп %
Полученные данные о количестве ванн и коэффициенте использовании ванн сводим в таблицу 3.1.
Таблица 3.1 Зависимость количества ванн от ритма выдачи.
Данные таблицы свидетельствуют о том что при небольшом ритме выдачи достигается наибольший коэффициент использования ванн но при этом число ванн максимально. Это в свою очередь приводит к значительному увеличению длины линии сложности технологической подвязки большому количеству контрольно-измерительных приборов и средств автоматизации к увеличению числа автооператоров обслуживающих линию к возрастанию капитальных затрат по обслуживанию линии. При увеличении ритма выдачи значительно сокращается количество ванн что приводит к снижению длины линии и упрощению ее обслуживания при этом уменьшается коэффициент использования ванн. Для высоких ритмов выдачи высока технико-экологическая опасность – огромны капитальные затраты при замене ванн больших размеров. Необходимо выбирать оптимальное значение ритма выдачи.
Принимаем для процесса нанесения сплава R = 10 мин.
Рассчитаем коэффициент использования ванн для данного ритма выдачи по формуле 3.6:
Поверхность единовременной загрузки Sед.загр м2 определяется по формуле [1]:
где - коэффициент исправимого брака.
На линии покрывается два типа деталей в соотношении по производительности 40:60 то необходимо рассчитать площадь нанесения покрытия на каждый тип деталей:
Количество деталей на подвеске определяется по формуле [1]:
где Sдет – площадь поверхности одной детали (S1 = 13210-6 м2 S2 = 10810-6м2).
Для конструирования и расчета площади подвески необходимо учитывать сложность профиля деталей и РС электролита. Габариты подвески: 1300×1000 мм габариты барабана: 300×1000 мм.
Расчет размеров ванн необходимо вести по большему из технологических спутников.
Определим габариты ванны.
Длина ванны Lв мм рассчитывается по формуле [1]:
где l1 – расстояние от края подвески до торца ванны мм
l - длина подвески мм.
Внутренняя ширина ванны Вв мм электрохимической обработки рассчитывается по формуле [1]:
где в1 - ширина подвески с деталями мм;
в2 - расстояние от центра А до центра края подвески мм;
в3 - расстояние от края анода до торцов стенки мм;
п - количество катодных рядов.
Высота ванны Нв мм рассчитывается по формуле [1]:
где Н1 – высота подвески мм;
H2 - расстояние от нижнего края подвески до уровня электролита мм;
H3 - расстояние от верхнего края подвески до уровня электролита мм
H4 - расстояние от уровня электролита до края ванны мм.
Длина автооператорной линии La мм рассчитывается по формуле:
где Ввн – внутренняя ширина ванны мм;
Вс – ширина воздушной камеры мм;
Взр- ширина стойки загрузки-разгрузки мм;
Всз- расстояние между сушкой и стойкой загрузки мм;
n0 - количество сопряженных ванн без бортотсосов;
n1 - количество сопряженных ванн с односторонними бортотсосами;
n2 - количество сопряженных ванн с двухсторонними бортотсосами;
n – количество ванн одного типа размера.
Ширина линии Вл мм рассчитывается по формуле [1]:
где Lв -длина ванны мм;
В1 - расстояние от края ванны до металлоконструкции мм;
В2- расстояние от края ванны до наружной плоскости площадки обслуживания мм.
Необходимое число автооператоров nа рассчитывается по формуле [1]:
где Т1 – суммарное время горизонтального перемещения с.
n1 – количество позиций в линии;
– скорость горизонтального перемещения автооператора мс (1 = 033 мс).
Т2 – суммарное время на подъем и опускание с:
где Т2 - среднее время подъема и опускания с
n2 – количество позиций с однократным обслуживанием ванны;
n3 – количество позиций с двукратным обслуживанием ванны;
n4 – количество позиций с трехкратным обслуживанием ванны.
где h – геометрическая высота подъема м;
– скорость вертикального перемещения мс (2 = 0116 мс).
Т3 – суммарное время пауз с:
где Т’3 – время паузы с
n1 – число позиций с длительностью менее 60 с;
n2 – число позиций с длительностью более 60 с.
Т’4 – время простоя над позициями с:
Т5 – суммарное время простоя автооператора над позициями с опущенными деталями с:
Принимаем для работы АГЛ 2 автооператора.
2 Построение циклограммы
Циклограмма – это графическое или табличное изображение функциональных перемещений автооператора при выполнении им последовательности переноса технологических спутников по позициям с соблюдением заданной длительности технологических операций.
При построении циклограммы были использованы следующие условные обозначения:
– рабочий ход автооператора – перемещение автооператора с технологическим спутником;
– холостой ход автооператора – перемещение автооператора без технологического спутника;
– позиция разгрузки;
- время выстоя автооператора над позицией.
Цикл работы автооператора состоит из подциклов каждый из которых равен ритму выдачи. Цикл работы автооператора включает время в течение которого автооператор должен выполнить операции по обслуживанию ванн находящихся в зоне его действия и вернуться на исходную позицию.
Построенная циклограмма позволяет определить следующие параметры:
)уточненный ритм выдачи (R = 98 мин.);
)последовательность выполнения транспортных операций;
)фактическую длительность технологических операций (tц = 162 мин)
)время проведения основных операций:
- нанесение покрытия – 99 мин;
- травление – 2 мин;
- улавливание – 40 с;
- горячая промывка – 120 с;
- холодная промывка- 60-90 с;
3Расчет и подбор вспомогательного оборудования
3.1 Подбор источника питания
В качестве источника для ванн электрохимического обезжиривания травления нанесения покрытия выбираем выпрямительный агрегат который обладает рядом технических преимуществ а именно:
- Работа на постоянном реверсивном и импульсном токе
Основные технические характеристики:
- напряжение питания – сеть переменного тока – 220 В 50 Гц
- выходная мощность Вт – до 2400
- диапазон регулирования постоянного тока А – от 0 до 60
- диапазон регулирования выходного напряжения В – от 0до56
- рабочий диапазон температур окружающей среды0С – от +5до + 50
- электромагнитная совместимость по ОСТ 45.183-2001
Для ванн нанесения покрытия необходимо 4 блока с токовой нагрузкой 240 А по 2 блока на каждую ванну соответственно.
Коэффициент запаса регулирования тока составит:
Для ванны электрохимического обезжиривания требуется установить 4 блока с общей токовой нагрузкой 240 А.
Рассчитаем токоподводные шины для гальванических ванн. Шинопровод выполнен из медного пучка проволоки. Шинопровод рассчитывается по большей токовой нагрузке для ванн принимается соответственно расчетному.
Площадь сечения шинопровода [2]:
Кз = 12-13 – поправочный коэффициент запаса токовой нагрузки.
Длина шинопровода определяется расстоянием от ванны да места установки блока источника тока. Максимальная длина шинопрововода составляет 15 метров. Рассчитаем сопротивление и падение напряжения на шинопроводе:
где ρ = 15510-8 Омм2м- удельная электрическая проводимость меди;
Sш = 7510-6 м2 - площадь сечения проводника;
l = 15 м - длина проводника.
Температура свободноподвешенного в воздухе токоподвода [1]:
где tок – температура окружающей среды 0С;
k – коэффициент учитывающий условия теплоотдачи Вт(мм2град).
3.2 Подбор и расчет материала подвески
Материал подвески: медь покрытая прессованным углепластиком который обладает малым весом высокой прочностью и износостойкостью устойчив в агрессивных средах плохо смачивается водой что значительно уменьшает унос электролитов. Расчет толщины токоведущей части необходимо производить с учетом максимально возможной токовой нагрузки на линии т.е 240А.
Определим толщину токоведущей части подвески [1]:
где Sш – площадь сечения проводника.
Толщину токоведущей части подвески 10 мм толщина углепластикового покрытия составит 2 мм. Таким образом толщина подвески составит 14 мм.
3.3 Подбор системы бортовой вентиляции
Удельный объем отсасываемого воздуха определим по формуле (3.23) [2]:
где Ввн Lвн –внутренние ширина и длина ванны м;
Нр – расстояние от зеркала электролита до борта ванны (015м).
Для ванн химической обработки:
Для ванн электрохимической обработки:
Расчет объема воздуха отсасываемого от зеркала ванн производят по формуле [1]:
где KΔt – коэффициент учитывающий разность температур раствора и помещения;
КT – коэффициент учитывающий токсичность и интенсивность выделения вредных веществ;
K1 – коэффициент учитывающий тип отсоса (односторонний – 18; двусторонний – 10);
К2 – коэффициент учитывающий наличие воздушного перемешивания раствора (барботаж – 12; без перемешивания – 1);
Значения всех коэффициентов для бортовых отсосов расположенных у различных ванн сведем в таблицу 3.2.
Таблица 3.2 – Коэффициенты для расчета воздуха удаляемого бортовыми отсосами
Наименование операций
В связи с тем что ванны улавливания и обезжиривания оборудованы закрывающимися экранами способствующими уменьшению объема отсасываемого воздуха от зеркала ванны то рассчитанный по формуле (3.24) объем воздуха умножается на поправочный коэффициент рассчитанный по формуле (3.25):
где – время нахождения ванны без укрытия экраном мин;
R – ритм выдачи мин.
Для ванны нанесения покрытия
Рассчитанный объем воздуха отсасываемого от зеркала ванн сведен в таблице 3.3.
Таблица 3.3 – Расход отсасываемого воздуха
Расположение бортового отсоса
Тип бортового отсоса
Ванна нанесения покрытия
Общий объем воздуха который необходимо отсасывать от гальванической линии составит:
По полученным данным расчета выбираем осевой вентилятор марки OSD-M производительностью 20 м3ч и мощностью 06 и 08 КВтч.
3.4 Подбор насосов для ванн промывок обезжиривания травления.
Для объемного напорного дозирования нейтральных и агрессивных жидкостей эмульсий суспензий предлагается использовать насос центробежный муфтовый НЦ.М3-4. Предназначен для перекачивания агрессивных и нейтральных жидкостей с плотностью не более 1200 кгм и температурой от +7 до +60°С. Бессальниковая конструкция насоса исключает утечку перекачиваемой жидкости и ее контакт с химически нестойкими материалами (характеристики производителя).
- Производительность мах м3ч – 35
- Потребляемая мощность кВт – 1
- Напряжение питающей сети В – 380
- Габариты мм – 390x182x160
3.6 Подбор электронагревательного оборудования.
Для разогрева ванны горячей промывки необходимо 3647171 кДж тепла.
Рассчитаем тепловой поток для разогрева ванны по формуле [3]:
где = 1800 с – время разогрева ванны.
Рассчитаем мощность электронагревателей по формуле [3]:
где k = 102-105 – коэффициент учитывающий потери при преобразовании электрической энергии в тепловую.
Таблица 3.4 – Технические характеристики блока нагревателей (необходимы для определения количества блоков в ванне).
Число элементов в блоке
Ширина блока нагревателей
Ток срабатывания защитного отключения
Длина погружаемой части нагревательного элем.
Диапазон регулирования температуры
Высота блока нагревателей мм
Точность поддержания температуры
рН нагреваемых растворов
Материал корпуса блока электронагревателей
Максимальная мощность блока
Материал корпуса нагревательного элемента
Рассчитаем количество блоков:
Принимаем количество нагревательных элементов в ванне равным 8.
Рассчитаем количество затраченной энергии на нагрев ванны:
3.7 Подбор систем очистки и регенерации растворов.
Расчет установки фильтрации.
Предназначена для удаления из электролитов и растворов механических примесей в процессе работы.
Выберем тканевый фильтр для фильтрации раствора после кристаллизации.
Определим время фильтрации по формуле:
где – вязкость фильтрата 1110-3 Пас;
rв – массовое удельное сопротивление осадка 7861010 мкг;
Δр – перепад давления на фильтре 68104 Па;
hос – высота слоя осадка 0005м;
Rф.п. – сопротивление фильтровальной перегородки 41109 м-1;
Vф – объем фильтрата 107022 л.
Рассчитаем поверхность фильтрования
где V – производительность м3ч;
К – коэффициент учитывающий увеличение поверхности из-за увеличения сопротивления фильтровальной перегородки в ходе работы (К = 08);
vуд – удельный объем фильтрата м3м2.
Эту поверхность может обеспечить фильтр марки Д18-18У с поверхностью фильтрования 18 м2.
Расчет гиперфильтратора
При расчете аппарата гиперфильтрации выбираем фильтровальную мембрану МГА-95 с удельной производительностью G = 250 лм2·сут и селективностью A = 95 %.
Объем фильтрата находим по формуле [1]:
где Ск и Сн – начальная и конечная концентрация компонента в концентрате (Ск Сн = 100).
Определим рабочую поверхность [1]:
Количество блоков исходя из площади 1 блока = 05 м2.
Конструктивно выбираем аппарат с плоскопараллельным расположением мембран.
Расчет электролизера для извлечения олова.
Принимаем время процесса 8 часов за которые концентрация сульфата олова уменьшиться 248 до 001 гл. Vр = 0209 м3 – объем раствора поступающего на очистку;
Определим токовою нагрузку на электролизере по формуле [11]:
где Cн = 248 гл Ск = 001 гл – начальная и конечная концентрация С
V = 209 л – объем раствора;
q = 221 г(Ач) – электрохимический эквивалент;
– время электролиза ч;
ВТ – выход по току (принимаем 95%).
Определим истинную площадь электродов принимая SA = SK.
где i – плотность тока Ам2.
Рассчитаем количество водорода выделившегося на катоде:
Определим напряжение на электролизере по формуле [9]:
К – коэффициент газонаполнения;
– электропроводность раствора Смм.
UM – падение напряжения в мембране В.
Удельные энергозатраты составят:
4 Расчет нагрузок на ванну
Рисунок 1 – Схема нагрузки ванны
Расчет нагрузок га ванну необходимо производить по опасному сечению т.е тем местам где корпус ванны подвержен наибольшим воздействиям. По результатам расчета принимается толщина корпуса уточняется необходимость и вид поддерживающего каркаса. Наиболее опасные места в гальванической ванне это:
) Дно между опорами при максимальном расстоянии между ними (по длине).
) Боковые стенки от середины ванны до его дна по оси.
В данных местах при большой нагрузке и недостаточной прочности материала может наблюдаться деформация или повреждение корпуса что недопустимо.
4.1 Расчет нагрузки на дно ванны:
где S = 054 м2 – площадь занимаемая раствором ограниченная проекцией опор;
Н = 12 м – высота раствора;
ρ = 119411 кгм3 – плотность раствора нанесения покрытия;
g = 981 мс2 – ускорение свободного падения.
Нагрузка на дно ванны у стен:
Решение системы уравнений:
Рисунок 2 – Эпюра сил действующих на дно ванны
Построим эпюру изгибающих моментов:
Рисунок 3 – Эпюра изгибающих моментов
4.2 Расчет нагрузки на стенки ванны
Рисунок 4 – Эпюра сил действующих на стенки ванны
Рисунок 5 – Эпюра изгибающих моментов
5 Обоснование конструкционных материалов и мероприятия по защите от коррозии
ГОСТ 5272-68 определяет коррозию как процесс самопроизвольного окисления (разрушения) металлов вследствие химического или электрохимического взаимодействия их с коррозионной средой. Это взаимодействие ведет к частичному или полному разрушению металла.
Профилактика коррозии начинается уже на этапе производственного проектирования назначением мер по защите от коррозии выбором оптимальных материалов конструктивных форм производственных технологических процессов в соответствии с условиями эксплуатации оборудования.
Основными конструкционными материалами для изготовления оборудования цехов электрохимических покрытий легированные (нержавеющие) стали марок 12х18н9т 12х18н10т полипропилен винилпласт фторопласт углепластик применяют для изготовления ванн нагревателей бортовых отсосов подвесок.
(ГОСТ 613-79) применяют для изготовления шинопроводов различных токопередающихузлов нагревателей. В настоящее время одной из актуальных проблем производства является защита оборудования цехов электрохимических покрытий от коррозии в сильнощелочных сильнокислотных и окислительных средах. При выборе защитных материалов следует учитывать их химическую стойкость к данному виду агрессивного воздействия физико-механические свойства надежность экономичность безопасность эксплуатации.
Известны различные способы защиты оборудования от коррозии включающие использование химически стойких материалов пластмасс лакокрасочных материалов и эмалей.
С учетом практических данных для изготовления и защиты оборудования цехов электрохимических покрытий рекомендуются следующие материалы: кислотоупорная керамика полиэтилен полипропилен фторопласты стеклопласты резины и эбониты.
Для ванн без нагрева используется поливинилхлорид полиэтилен ВД. Для защиты промывных ванн целесообразно применять покрытия из резин и эбонитов герметики. Защита промывных ванн расположенных непосредственно после ванн травления осуществляется по шипу защиты самой травильной ванны. На практике для этой цели служат пластикаты пенопласт полипропилен.
Поливинилхлорид (ПВХ) и его сополимеры относятся к числу наиболее распространенных видов пластмасс. Для футеровки ванн можно использовать винипласт. Недостатки винипласта: невысокая теплостойкость (600С) и низкая ударопрочность. Наибольшее распространение для защиты оборудования получили пластикат прокладочный ПП-К7 (ОСТ 6-19-003-79) и пластикат рецептуры П57-40КЭ (ТУ 6-05-1146-75) толщина 2 мм.
На основании литературной обработки в качестве антикоррозийного материала для защиты ванн электрохимического обезжиривания и цинкования используют пластикат марок ПХ-22 (ТУ-6-19-051-130-90). Он эластичен термостабилен хорошо сваривается и обладает высокой химической стойкостью в горячих (до 400С) средах гальванических ванн стоек в H2SO4 HNO3 HCL щелочах окиси хрома и других средах. Пластикат пулестоек в хлористом железе и азотнокислом натре.
Для ванн пассивирования используют футеровку из пентопласта которую широко используют агрессивных средах при температуре до 120№. По химической стойкости в ряду термопластов он уступает только фторопластам.
В качестве защитного покрытия металлических поверхностей кронштейнов стоек стержней используют пластизоль который обладает более высокой химической и теплостойкостью.
Для изготовления бортотсосов вентиляционных коробов крышек к ваннам для наружной облицовки гальванической линии где неизбежны систематические обливы аппаратуры и коммуникаций агрессивными средствами используют листовой полипропилен (ТУ-6-05-1313-75) который имеет блестящую легко моющую поверхность высокую химическую стойкость обладает высоким сопротивлением ударным нагрузкам. В качестве теплоизоляционного материала используют стекловолокно.
Автоматизация и автоматические системы управления параметрами технологического процесса
Одним из основных направлений решения производственных задач является внедрение средств автоматизации и контрольно-измерительных приборов. Это необходимо для обеспечения необходимого качества покрытия а также для уменьшения доли ручного труда в управлении процессом на ваннах. Автоматизированному контролю подвергаются различные параметры технологического процесса: температура уровень растворов кислотность регулирование расхода и многое другое.
В практике регулирования температуры в гальванических линиях находят применение следующие датчики температуры: термопреобразователи сопротивления и электрические контактные термометры манометрические термометры.
Для контролирования температуры в ванне теплой промывки устанавливаем устройство которое состоит из термометра сопротивления типа ТСМ-0879 измерительного прибора (магнитного пускателя) и исполнительных механизмов (электронагревателей типа ТЭН).
В рабочих ваннах необходимо поддерживать такой уровень электролита чтобы подвеска с деталями всегда была покрыта слоем электролита постоянной толщины так как изменение этого параметра может влиять на распределение электрических полей в объеме электролита. Точность поддержания уровня составляет как правило ± 5 мм. Причины вызывающие изменение уровня следующие: вынос электролита с подвесками вынос электролита в бортовые отсосы и его испарение. Для контроля уровня применяют следующие методы: электроконтактный поплавковый ультразвуковой высокочастотный резонансный емкостной гидростатический.
Для контролирования уровня устанавливаем датчик поплавкового типа. Передача показаний от такого датчика к устройству сигнализации производится через бесконтактный ферромагнитный передатчик. Использование такого способа передачи позволяет избежать утечек тока из ванны.
Регулирование уровня в промывных ваннах по существу отсутствует. Чистая вода подается в ванну для разбавления концентрации электролитов и выливается через сливные отверстия на очистку или регенерацию. Регулирование уровня в промывочных ваннах сводится к регулированию водоиспользования. Для этого предлагаются схемы управления подачей воды позволяющие уменьшить ее расход. Эти схемы предполагают наличие в автоматической линии запорных соленоидных вентилей на подводе воды к промывочным ваннам. По первому решению вода подается на промывочные ванны начиная с момента когда в них загружаются детали
и прекращается подача воды после подъема деталей из ванны промывки. Более экономичной является схема требующая большего числа приборов: установка на выходе из ванн концентратомеров по сигналу которых производится подача воды.
Несвоевременная корректировка значений рН электролита отрицательно сказывается на структуре и качестве осаждаемых покрытий. Требования к точности поддержания рН= ± (005-075). Регулирование рН в гальванических ваннах имеет свои особенности. Измерение рН происходит медленно период между корректировками составляет часы. Выравнивание среднего значения рН в ванне после внесения дозы корректирующего раствора зависит от размеров ванн загрузки способов перемешивания и составляет ~ 10 минут.
Дополнительная погрешность изменения рН в ваннах может быть на порядок больше чем основная допустимая погрешность рН-метра. Учитывая эти особенности для регулирования рН в гальванических ваннах целесообразно применять импульсные системы регулирования функционирующие следующим образом.
Определяется доза корректирующего раствора не вызывающая отклонения за допустимые пределы. Схема регулирования выдает эту дозу через время определенное через определяемое из условий усреднения значения рН в ванне производит измерение рН сравнивает измеренное значение с заданным и выдает если это необходимо следующую дозу.
Для автоматического контроля концентрации электролитов в гальваническом производстве нашли применение следующие способы: потенциометрический магнитометрический кондуктометрический денсиметрический способы способ титрования контроль по ампер-часам. Опыт внедрения в производство автоматических систем корректирующих добавки малыми порциями в интервале 30-200 с при полной нагрузке ванны показал что при этом поддерживается практически постоянный состав концентрации добавок. Экономия добавок колеблется от 30 до 80 % по сравнению с корректировкой ванн вручную.
Сравнительная характеристика спроектированного оборудования
Разработанная автооператорная линия предназначена для осуществления процесса нанесения сплава олово-висмут. Обозначенные решение способствуют сокращению производственных площадей и возможности реализации установки локальных схем очисток что позволяет возвратить в технологический цикл нанесения гальванопокрытия значительное количество ценных компонентов тем самым снизить материалоемкость процесса.
Была проведена установка трехкаскадных ванн промывок что позволило сократить производственные площади упростить сантехническую обвязку трубопроводами. Для сокращения выноса раствора из технологических ванн были установлены козырьки между технологическими и промывными ваннами с наклоном в сторону технологических ванн.
Линия комплектуется современным оборудованием: плунжерными дозировочными насосами центробежными однонаправленными вентиляторами серии RF которые защищены от воздействия влаги снабжены асинхронным двигателем с внешним ротором и уплотненными подшипниками что увеличивает срок их службы.
Список использованной литературы
Смоляг Н.Л. Технология электрохимических производств: учеб.-метод. Пособие для студентов специальности 1-48 01 04. – Минск: БГТУ 2007. – 92 с.
Смоляг Н.Л. Основное оборудование электрохимических производств: учеб.-пособ. – Минск: БГТУ 2004. – 83 с.
Гибкие автоматизированные гальванические линии: справочник В.Л.Зубченко В.И.Захаров В.М.Рогов и др.; под общ. Ред. В.Л.Зубченко. – М.: Машиностроени 1989. – 627 с.
Основные процессы и аппараты химической технологии: учеб. пособие по проектированию Г. С. Борисов [и др.]; под общ. ред. Ю. И. Дытнерского. – 2-е изд. перераб. и доп. – М.: Химия 1991. – 496 с.
линия.cdw

Контакт привода барабана
Двухсторонний бортовой отсос
Трубопровод чистой воды
Трубопровод оборотной воды
Односторонний бортовой отсос
Площадка обслуживания
Техническая характеристика:
Линия предназначена для нанесения покрытия
Производительность линии - 15000 м
Габаритные размеры линии:
Количество манипуляторов - 1
Тип манипулятора - подвесной тележечный
Скорость перемещения:
Грузоподъемность манипулятора - 200 кг
Технические требования:
Отклонение от прямолинейности путей манипулятора
по всей длине не более 20мм
Пульт управления и пульт дистанционного управления
выпрямителями устанавливается в аппаратной
Шкаф локальной автоматики
не связанные с линией жесткими
размерами устанавливаются вдоль стены цеха
Сечение шинопроводов при полной нагрузке должно
обеспечивать падение напряжение в них не более 0
Сопротивление изоляции между корпусами токовых
ванн и шиной заземления должно быть не менее 4 кОм
Нанести порядковый номер на консоли каждого
манипулятора ГОСТ 9754-76
Цех должен иметь заземляющий контур и все
корпуса электрооборудования должны быть
Сопротивление между болтом заземления и корпусом
должно быть не более 0
Датчики положения манипулятора устанавливаются
вдоль линии движения с разделом на зоны
обслуживания каждого манипулятора
циклограмма.cdw

автооператор + схема управления.cdw

Грузоподъемность автооператора 250 кг.
Скорость горизонтального перемещения манипулятора 0
Скорость поднимания-опускания подвески манипулятором 0
автоаператора 250 кг
Мощность электродвигателя движение 0
Технические требования
Установка ограждений в рабочей зоне автооператора
Перед пуском проверить подключение к питающей сети
Обеспечить дуступ к выключателям и блакировочным устройствам
Мероприятия по защите от коррозии автооператора
осуществить согластно ГОСТ 7313 - 35
Смазака движущих узлов периодическая
Цепи и открытые зубчатые передачи смазать солидолом Ж
Тех. схема.cdw

Ванна двухкаскадной промывки
Ванна газожидкостной промывки
Ванна нанесения покрытия
Ванна горячей промывки
Насос высокого давления
Условные обазначения Наименование среды в трубопроводе
Загрязненный электролит
Очищенный электролит
Вентиляционные выбросы
Раствор из газожидкостной промывки
Рекомендуемые чертежи
- 25.01.2023
- 24.01.2023