Проект гальванического участка нанесения блестящего никелевого покрытия в барабане, производительность 8000 квадратных метров в год


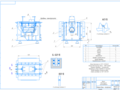
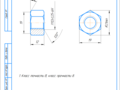
- Добавлен: 25.01.2023
- Размер: 555 KB
- Закачек: 1
Получить бесплатный доступ добавив свой материал или получить скидку оплатив сразу нескольких материалов
- ВКонтакте
- РћРТвЂВВВВВнокласснРСвЂВВВВВРєРСвЂВВВВВ
- Telegram
Подписаться на ежедневные обновления каталога:
Описание
Проект гальванического участка нанесения блестящего никелевого покрытия в барабане, производительность 8000 квадратных метров в год
Состав проекта
![]() |
![]() |
![]() ![]() ![]() ![]() |
![]() ![]() ![]() ![]() |
![]() ![]() ![]() |
Дополнительная информация
Контент чертежей
ванна.cdw

Полная вместимость ванны - 1008 литров
Материал барабана - полипропилен
Перфорация стенок барабана не показана
Привод барабана показан условно
Аноды никелевые по ГОСТ 2132-90
Барабан гальванический
Нагревательный элемент
Материал ванны - полипропилен
К источнику питания (-)
К источнику питания (+)
гайка.cdw

расчеты.docx
высшего образования
(технический университет)»
УГС (код наименование) 18.00.00 Химические технологии .
Направление 18.03.01 Химическая технология
Направленность Химическая технология неорганических веществ
(модуль - Технология электрохимических производств)
Факультет Химии веществ и материалов
Кафедра Технологии электрохимических производств
Учебная дисциплина Технологическое оборудование электрохимических производств
Тема Проект гальванического участка нанесения блестящего никелевого покрытия в барабане производительность 8000 м2 в год
Студент А.Р. Кузнецова
(подпись дата) (инициалы фамилия)
должность Н.В.Евреинова
(подпись дата)(инициалы фамилия)
федеральное государственное бюджетное образовательное учреждение
ЗАДАНИЕ НА КУРСОВОЙ ПРОЕКТ
Студент Кузнецова Арина Романовна
Тема: Проект гальванического участка нанесения блестящего никелевого покрытия производительность 8000 м2 в год
Исходные данные по проекту (источники)
Варыпаев В.Н. Введение в проектирование электролизеров: Учебное пособие. – Л.:ЛТИ им Ленсовета 1981 – 93 с.
Виноградов С.С. Организация гальванического производства. Оборудование расчет производства нормирование. Изд.2-е перераб. и доп.Под ред. В.Н.Кудрявцева. – М.: «Глобус» 2005. – 240 с.
ГОСТ 7.32-2001. СИБИД. Отчет о научно-исследовательской работе. Структура и правила оформления.
Перечень вопросов подлежащих разработке
Провести анализ научно-технической литературы по нанесению гальванических блестящих никелевых покрытий
Произвести выбор основного технологического оборудования
Выбор технологической схемы процесса
Определение номинального и эффективного фонда времени
Расчет и выбор оборудования
Расчет материального баланса электролизера и определение условий корректировки
Расчет баланса напряжения
Расчет теплового баланса. Выбор энергоносителей и теплообменников
Перечень графического материала
Технологическая схема процесса
Эскизный чертеж детали
Эскизный чертеж электролизера
Требования к аппаратному и программному обеспечению
Операционная система Microsoft Windows текстовый редактор Microsoft Office Word табличный редактор Microsoft Office Excel
Дата выдачи задания 30.09.2018
Срок представления работы к защите декабрь 2018 г
Заведующий кафедрой Агафонов Д.В.
к выполнению Кузнецова А.Р.
Аналитический обзор6
1 Электролиты никелирования и режимы электролиза .. .7
2 Очистка электролита11
3 Особенности нанесения покрытия в барабанах14
4 Оборудование для нанесения гальванических покрытий .. .16
5 Подготовка поверхности18
6 Выбор электролита и режима электролиза20
Технологическая часть22
Инженерные расчеты24
1 Определение фондов рабочего времени и режим работы цеха24
2 Определение толщины покрытия и времени электролиза25
3 Расчёт оборудования26
4 Материальный баланс31
5 Баланс напряжения электролизёра и выбор источника питания37
Никель – пластичный металл серебристо-белого цветам с желтоватым оттенком. Плотность никеля составляет – 89 гсм3 температура плавления 1455 о С. Никель обладает высокой коррозионной стойкостью в самых различных средах. Скорость коррозии никеля при эксплуатации в условиях умеренно холодного климата (УХЛ-4 УХЛ-3) очень низка и составляет менее 10–3 ммгод.
В растворах щелочей любых концентраций и даже в их расплавах при температурах вплоть до 350 о С никель коррозионностоек. Серная и соляная кислоты растворяют никель очень медленно многие органические кислоты действуют на никель лишь после длительного контакта с ним. В концентрированной азотной кислоте никель пассивируется. Никель довольно легко растворяется только в разбавленной азотной кислоте. Твёрдость никелевых покрытий достигает 4 МПа что выше чем у кадмиевых цинковых и оловянных покрытий. Никель является довольно сильным аллергеном. По этой причине не рекомендуется наносить никелевые покрытия на изделия которые могут соприкасаться с кожей человека.[7]
В гальванической паре с железом никель является катодом и способен надежно защищать железо от коррозии лишь при условии полной беспористости покрытия поэтому никелирование как защитно–декоративное покрытие применяют обычно с подслоем меди.[11]
Чрезвычайно высокая распространённость гальванического способа нанесения никеля обусловлена следующими достоинствами:
возможность задавать и регулировать толщину покрытий;
возможность получения покрытий с высокой степенью блеска;
наличие большого количества совершенных технологических разработок (высокая технологичность процесса нанесения покрытий);
высокий уровень автоматизации гальванического производства;
довольно высокая скорость нанесения покрытий ( 1 мкммин и более);
возможность нанесения покрытий только на отдельные участки изделия;
высокая чистота металла наносимого покрытия;
возможность осаждения никелевых сплавов заданного и регулируемого состава;
более низкая себестоимость никелевых покрытий по сравнению с никелированием другими методами.
Вместе с тем гальванический способ имеет и существенные недостатки:
большое количество жидких отходов сложность их нейтрализации и как следствие высокая экологическая опасность гальванического производства;
трудности нанесения покрытий толщиной более 24 мкм без ухудшения их механических свойств;
сложности нанесения никелевого покрытия на детали из высокопрочных термообработанных сталей из-за их высокой наводороживаемости и сильного охрупчивания приводящего к разрушению ответственных деталей в процессе их эксплуатации.
1 Электролиты никелирования и режимы электролиза
Основным достоинством никелевых покрытий является способность никеля к глубокой пассивации с образованием на своей поверхности очень тонкой прозрачной беспористой плёнки защищающей никель при обычных условиях в течение длительного времени. Основным недостатком никелевых покрытий является их высокая пористость резко снижающая защитные свойства никелевых покрытий особенно в кислых средах. В зависимости от функционального назначения никелевые покрытия бывают однослойными и многослойными матовыми полублестящими и блестящими а также обладающими другими специфическими функциональными или декоративными свойствами.
Однослойные никелевые покрытия из-за их высокой пористости и как следствие невысокой защитной способности как правило наносят на детали эксплуатируемые в лёгких условиях. При эксплуатации изделий в более жёстких условиях никелевые покрытия наносят не индивидуально а в составе многослойных покрытий.[7]
При никелировании имеющем своей целью защитно-декоративную отделку изделий никель должен иметь зеркально-блестящую поверхность.
Механическая полировка применяемая для этого является трудоемкой операцией и требует высокой квалификации рабочих. Кроме того при полировке никелевых покрытий безвозвратно теряется слой никеля толщиной 2-4 мк.
Поэтому широкое применение получили электролиты блестящего никелирования содержащие различные блескообразователи. [11]
Так например борфтористые электролиты отличаются высокой производительностью и электропроводностью.
Состав и режим работы одного из них приводятся ниже:
Рисунок 1 - состав борфтористого электролита никелирования
Никелевые покрытия получаются блестящие или полублестящие легко полирующиеся обладают высокой эластичностью и твердостью . Электролит пригоден для использования в колокольных и барабанных ваннах.
Большой практический интерес представляют также сульфаминовые электролиты составляемые на основе сульфаминовой кислоты SО3OH·NH2. Эта кислота представляет собой бесцветные ромбические кристаллы она безвредна нелетуча и негигроскопична. Никелевые соли сульфаминовой кислоты имеют практически неограниченную растворимость. Ниже приводятся состав и режим работы одного из сульфаминовых электролитов:
Рисунок 2 – состав сульфаминового электролита никелирования
Необходимо перемешивание и фильтрование электролита. Следует упомянуть также об аммиачном электролите дающем блестящие покрытия.
Для него приняты следующие состав и режим эксплуатации:
Рисунок 3 – состав аммиачного электролита никелирования
Отмечаются высокая прочность сцепления никелевых покрытий со сталью хорошая эластичность и блеск их при толщине до 30 мк. Повышение концентрации солей кадмия или цинка приводит к полосатости покрытий.
В настоящее время разработано большое количество составов сернокислых электролитов позволяющих получать осадки с различными физикохимическими свойствами. Практически все современные электролиты для никелирования представляют собой разновидность электролита Уоттса. Введение в электролит Уоттса блескообразующих и выравнивающих добавок позволяет получать блестящие и даже зеркальноблестящие никелевые покрытия. Классическим примером сернокислого электролита блестящего никелирования является электролит следующего состава:[7]
Таблица 1 – состав электролита блестящего никелирования
Необходимо отметить что в настоящее время на рынке химикатов для гальванического производства предлагается очень большое количество различных электролитов никелирования отличающихся как правило только добавками которые по механизму действия являются весьма схожими и взаимозаменяемыми.
Все компоненты электролита и рабочие режимы оказывают большое влияние на физико-механические свойства. Рассмотрим один из таких готовых электролитов:
Таблица 2 – состав электролита блестящего никелирования с добавкой Likonda Ni
Рабочая концентрация с0 гл
Минимальный предел концентрации с0min гл
Добавка Likonda Ni-Aмлл
Добавка Likonda Ni-Bмлл
Анодная плотность токаАдм2
Катодная плотность тока Адм2
Процесс предназначен для нанесения высококачественного никелевого покрытия с повышенной степенью блеска и выравнивания на изделия простого и сложного профиля из различных типов металла на подвесках и в барабане.
Высокая выравнивающая способностьдаже при малой толщине покрытия.
Повышенная рассеивающая способностьи как следствие хороший декоративный вид и коррозионная стойкость покрытия деталей сложного профиля.
Пластичность покрытияпри высокой степени блеска.
Пониженное содержание продуктов разложенияорганических добавок в растворе и в покрытии – высокая стойкость покрытий к старению уменьшение затрат на очистку электролита.
Активность никелевого покрытияпозволяющая высококачественное хромирование.
Включениеантипиттинговых компонентовв составблескообразователей.
Стабильностьтехнологического процессапростота корректирования(используются только две добавки).
Как видно этот электролит более удобен поскольку все концентрации предоставляются производителем а готовые добавки обеспечивают равномерное покрытие. Поэтому выбираем его для дальнейших расчетов.
2 Очистка электролита
Примеси меди и цинка удаляются из раствора путем селективной очистки т. е. проработкой постоянным током (ik = 01 02 Адм2) при интенсивном перемешивании. Для этого на катодные штанги завешиваются гофрированные стальные катоды имеющие большую поверхность чем плоские катоды. С целью снижения вероятности совместного выделения никеля электролит иногда подкисляют до рН = 3. Проработку проводят до тех пор пока на катоде не начнет выделяться светлый осадок никеля.
Для удаления железа в раствор при рабочем рН вводят пероксид водорода который окисляет ионы двухвалентного железа до трехвалентного в результате чего последние выпадают в осадок в виде Fe(OH)3. Выпавший гидроксид отфильтровывается. Процесс гидратообразования проходит довольно медленно поэтому после введения окислителя (H2О2 KMnO4) фильтрацию следует проводить не ранее чем через сутки.
Органические примеси вызывающие питтинг и пористость удаляют путем окисления их пероксидом водорода или перманганатом калия с последующей обработкой активированным углем. При интенсивной эксплуатации ванны никелирования необходимо осуществлять непрерывную фильтрацию электролита так как залогом качественного никелевого покрытия является чистота электролита его идеальная прозрачность и соответствие рН норме.
Анализ электролита на присутствие примесей проводиться либо аналитическими методами в центральной заводской лаборатории либо с помощью ячейки Хулла в цеховых лабораториях. Ячейку Хулла можно использовать для определения достаточности блескообразующих добавок при корректировке электролита. Для обеспечения нормальной работы ванны рН электролита замеряют не реже одного раза в смену.
Наличие в электролите железа и механических примесей можно определить по внешнему виду электролита. Для этого достаточно налить электролит в прозрачный стакан и посмотреть на свет. Качественный электролит должен быть абсолютно прозрачным и иметь изумрудно-зеленый цвет. Если цвет электролита с оттенком болотной зелени то это свидетельствует о наличии значительного количества примеси железа. Если электролит недостаточно прозрачен то это указывает на наличие гидроксидов или механических примесей в виде взвешенных частичек пыли. Прежде чем приступать к фильтрации электролита необходимо довести рН до нормы и выдержать сутки чтоб гидроксиды никеля растворились в противном случае на фильтре остается значительное количество дорогостоящих соединений никеля.
Если загрязнение электролита всё-таки произошло то очистку следует проводить по следующей схеме: полная (комплексная) очистка электролита никелирования проводится в несколько этапов. [7]
Первый этап: предварительно перед селективной очисткой проводят очистку электролита от железа путём окисления его до 3-х валентного состояния пероксидом водорода. Для этого в раствор вводят 30 % раствор пероксида водорода из расчёта 1 мл на 1 литр раствора. При рабочем рН ионы 3-х валентного железа гидролизуются и выпадают в осадок в виде Fe(OH)3. Для более полного осаждения железа электролит подщелачивают до рН = 60 добавкой кальцинированной соды или углекислого никеля. Электролит интенсивно перемешивают 1–3 часа и дают отстояться. Процесс окисления и гидролиза железа происходит не мгновенно поэтому фильтрацию необходимо проводить не ранее чем через 8–16 часов после введения пероксида водорода. Это необходимо ещё и для того чтобы избыток пероксида успел разложиться. Введение в электролит пероксида водорода позволяет совместно с железом произвести очистку от хрома. При наличии шестивалентного хрома пероксид водорода действует на шестивалентный хром не как окислитель а как восстановитель. При этом сам пероксид водорода восстанавливая шестивалентный хром окисляется до кислорода по реакции:
H2O2+ Cr2O72- 2Cr(OH)3+ 3O2+H2O
Для ускорения процесса желательно электролит подкислить до рН=3. После этого с помощью углекислого никеля доводят рН = 60 и ванну прогревают до 70 С в течение 30 минут для удаления излишка пероксида. Далее ванну фильтруют. При наличии в электролите алюминия последний при рН = 60 будет гидролизоваться и отфильтровываться совместно с железом и восстановленным хромом. После фильтрации рН электролита доводят до рабочего значения а при необходимости селективной очистки – до рН 3.
Необходимо отметить что при обработке раствора пероксидом водорода возможно частичное окисление органических примесей и блескообразующих добавок. Окисление органических примесей желательно т. к. некоторые органические загрязнения лучше удаляются активированным углем. Окисление добавок нежелательно поэтому после очистки электролита требуется корректировка по добавкам.
Второй этап: после фильтрации и удаления гидроксидов железа и хрома электролит подкисляют до рН 3. Подкисление проводится для того чтобы в процессе дальнейшей селективной очистки от ионов меди и цинка выход по току никеля на гофрированном катоде был как можно ниже что необходимо для снижения потерь никеля при очистке. Подкисление практически никак не повлияет на выход по току меди и цинка так как и тот и другой металл выделяются на катоде из кислых растворов с довольно высоким выходом по току. Плотность тока выбирается в зависимости от степени загрязнения электролита и как правило не превышает 0102 Адм. Увеличение плотности тока не приводит к увеличению скорости очистки
т. к. скорость осаждения примесей на катоде из-за их малой концентрации зависит только от скорости подвода ионов примеси к катоду. Поэтому для увеличения скорости очистки необходимо создавать условия для более быстрого подвода ионов примеси из глубины раствора к поверхности катода (интенсивное перемешивание нагрев увеличение поверхности катода). Для увеличения поверхности катод делают гофрированным (гармошкой). Желательно гофры делать более крупные с таким расчётом чтобы по ширине гофрированный катод занимал как можно больше пространства между анодами. Угол перегиба нужно сделать не менее 90 градусов лучше 60 или даже 45. При такой конструкции катода он будет напоминать катод в ячейке Хулла. На выступающих частях катода (ближних к аноду) плотность тока будет наибольшей и здесь может быть достигнут потенциал восстановления всех примесей включая потенциал электроотрицательного цинка. Во впадинах плотность тока минимальна – там возможно восстановление только ионов меди. Первоначально на гофрированном катоде осадок имеет грязносерый цвет и содержит большое количество примесей. По мере очистки электролита осадок светлеет. Процесс очистки нужно проводить до получения светлых осадков на всей поверхности гофрированного катода. В зависимости от степени загрязненности электролита очистка может длиться от нескольких часов до нескольких суток. Перемешивание обязательно! [6]
Третий этап: после окончания селективной очистки рН электролита необходимо довести до нормы. Подщелачивание электролита растворами щелочей сопряжено с опасностью выпадения гидроксидов никеля и их потерей при последующем фильтровании. Лучше подщелачивание проводить углекислым никелем или кальцинированной содой. Для снижения гидратообразования раствор нужно вливать тонкой струйкой при интенсивном перемешивании. Тем не менее даже при таком способе подщелачивания электролита вероятность гидратообразования не исключается и раствор может потерять свою прозрачность. Нужно помнить что при последующей выдержке электролита образовавшиеся гидроксиды частично растворяются что приведёт к увеличению рН. Поэтому в случае помутнения раствора в процессе подщелачивания необходимо заканчивать подщелачивание до значения рН на 0102 единицы меньше оптимального значения т. е. при рН 41. Растворение выпадающих гидроксидов никеля в очень малом избытке кислоты происходит очень медленно поэтому перед фильтрацией необходимо выдержать электролит в течение нескольких часов. Иногда для того чтобы снять проблемы связанные с доведением рН раствора перед селективной очисткой раствор не подкисляют но в этом случае потеря никеля за счёт соосаждения его на гофрированном катоде совместно с примесями неизбежна.
Четвёртый этап: Очистка электролита от органических примесей. Проводится путём обработки активированным углем. Обработку лучше проводить в отдельной ванне так как рабочую ванну потом очень трудно отмыть от мелкой угольной пыли. Обычно электролит перекачивают в запасную ванну через фильтр с насосанным активированным углем на фильтрующую поверхность фильтровальной установки. Перед применением свежего активированного угля его необходимо обработать 01 Н раствором HCl. Дело в том что уголь имеет щелочную реакцию вследствие чего при контакте с электролитом никелирования происходит моментальное заполнение пор активированного угля гидроксидами никеля. В результате уголь полностью теряет адсорбционную способность. Как уже было сказано чистый электролит должен быть идеально прозрачен и иметь изумрудно-зелёный цвет. Никелевые электролиты наиболее чувствительны к загрязнениям и поэтому требования к их чистоте предъявляются очень жесткие.[6]
3 Особенности нанесения покрытия в барабанах
Условия формирования покрытия на деталях во вращающихся барабанах существенно отличаются от условий электроосаждения на подвесках. Основное отличие заключается в том что при покрытии деталей насыпью в барабанах или колоколах большая доля тока приходится на детали находящиеся на поверхности загрузки и на те которые находятся вблизи перфорированных стенок. На детали находящиеся в глубине загрузки ток практически не попадает так как они экранированы поверхностными деталями. Нетрудно представить что чем больше загрузка тем меньше доля деталей находящихся на поверхности и тем выше плотность тока приходящаяся на поверхностные детали. В барабанах средняя расчетная плотность тока значительно ниже чем плотность тока рекомендуемая для покрытия деталей на подвесках. Как правило плотности тока в барабанах ниже чем на подвесках в 2–3 раза. Расчетная плотность тока в барабанах обычно не превышает 115 Адм 2 . Но даже при таких низких средних плотностях тока реальная плотность тока на поверхностных деталях может превышать 10 Адм 2 . При покрытии деталей в барабанах вследствие их пересыпания для каждой конкретной детали имеет место как бы импульсный режим тока. Частота пульсации тока зависит от скорости вращения барабана а интенсивность импульсов тока зависит от величины загрузки и плотности тока.[2]
Состав электролита используемый в барабанных ваннах идентичен составу электролита в подвесочных ваннах но концентрация ионов металла может быть ниже чем в подвесочных ваннах. Низкие концентрации основной соли в барабанных ваннах вполне допустимы так как при интенсивном перемешивании и коротких импульсах тока низкая концентрация разряжающихся ионов не приводит к диффузионным ограничениям в то время как эффект от снижения уноса солей металла с деталями из разбавленных растворов получается довольно существенный. А вот концентрацию компонентов обеспечивающих высокую электропроводность (H2SO4 NaCl) при составлении электролитов для барабанных ванн стараются увеличить. Это делается с целью снижения падения напряжения в электролите и в перфорации барабана. Еще одной особенностью покрытия деталей в барабанах является истирание наносимого на детали покрытия вследствие трения их друг о друга.
Для учёта этого явления при расчете времени покрытия вводится коэффициент увеличивающий расчетное время на 530 %. Коэффициент истирания зависит не только от износостойкости покрытия но и от массы загрузки определяющей прижим деталей друг к другу. Кроме того истирание зависит от наличия острых кромок способствующих истиранию. По этой причине величина коэффициента истирания принимается различной в каждом конкретном случае и на практике может быть определена по фактической толщине покрытия.
Обычно эффект истирания рассматривается как нежелательное явление но в нём есть и положительная сторона. Дело в том что истирание покрытия происходит только на выступающих частях деталей т. е. как раз там где толщина покрытия за счёт низкой рассеивающей способности электролитов получается наибольшая. Таким образом истирание способствует выравниванию покрытия по толщине. Кроме того при трении деталей происходит галтовка в результате которой покрытие становится более гладким и плотным. Вместе с тем необходимо отметить что истирание металла деталей приводит к ускоренному загрязнению электролита ионами металла покрываемых деталей.
Следующей особенностью покрытия деталей в барабанах является трудность покрытия тонкостенных плоских деталей и деталей типа витых пружин. Тонкостенные плоские детали нередко слипаются и в результате этого внутренняя поверхность слипшихся деталей не покрывается. Иногда для разбивки слипшихся деталей к ним добавляют более тяжелые детали другой формы. Витые пружины и детали имеющие отверстия крючки или другие зацепы сцепляются межу собой в единый комок в котором внутренние детали не покрываются. Кроме того после покрытия их бывает очень трудно расцепить.[2]
4 Оборудование для нанесения гальванических покрытий
Ванны изготавливаем из полипропилена - это наиболее перспективный материал обладающий высокой химической стойкостью износостойкостью термостойкостью высоким сопротивлением ударным нагрузкам и удовлетворительной механической прочностью. Высокая химическая стойкость полипропилена в электролитах для нанесения типовых покрытий дополняется тем что он не оказывает влияния на электропроводимость растворов и обладает высокой прочностью.
Электродные штанги предназначены для крепления подвесок с обрабатываемыми деталями и анодов. Применяют штанги круглого и прямоугольного сечения длиной не более 2 м. Диаметр штанг круглого сечения 25 – 40 мм.
Крупные детали загружаются в ванну индивидуально или партиями на специальных подвесках служащих одновременно и контактами. К ним относятся подвески крючки крепление на проволоку. Самый трудоёмкий способ – навязывание деталей на проволоку.
Для нанесения покрытий на мелкие детали в массовом производстве обычно применяют вращающиеся колокола и барабаны.
Барабан погружают в ванну с электролитом и поднимают из нее с помощью специального подъемника. Во время работы барабан вращается вокруг горизонтальной оси от электродвигателя через редуктор.
Анодные пластины подвешивают на штанги расположенные в ванне снаружи барабана. Благодаря этому плотность тока на аноде в барабанных ваннах может быть такой же как и в стационарных. Для уменьшения межэлектродного пространства рекомендуется изогнуть аноды полукольцом вокруг барабана. Подвод тока к покрываемым деталям осуществляется через специальные контактные кнопки расположенные с внутренней стороны барабана.
Загрузка и разгрузка барабана производятся обычно через одну из открывающихся граней. Барабаны больших размеров опускают и поднимают с помощью электрического или пневматического тельфера.[5]
На риcунке 4 показана конструкция ручного переносного барабана. Их изготовляют из органического стекла и снабжают небольшим приводным механизмом. Ручные барабаны могут быть использованы для покрытия мелких деталей в любой стационарной ванне как с кислым так и со щелочным электролитом. Эти барабаны обычно имеют диаметр 100—280 мм длину 160—500 мм массу — до 50 кг.
Для циркуляции электролита и прохождения тока необходима перфорация стенок барабанов. Размер отверстий обычно от 3 до 8 мм промежутки между ними 25 – 6мм. Отверстия в перфорированной стенке почти всегда делают в шахматном порядке так как теоретически при этом на единице площади стенки умещается большее количество отверстий.
Барабанный электролизер (рис.5) состоит из сварной рамы 5 с цапфами 2 для укладки в ловители ванн и захватов 6 взаимодействующих с грузозахватами автооператора. К раме крепятся: несущие щеки 11 (неметаллические или металлические с антикоррозионной изоляцией) с фторопластовыми подшипниками 12 в которых устанавливается вращающаяся шестигранная перфорированная обечайка 13 с крышкой 14; привод электролизера 4; катодный токоподвод 1 для передачи технологического тока обрабатываемым изделиям; автомат 7 для защиты электродвигателя; контактное устройство 8 для передачи переменного трехфазного тока напряжением 36В электродвигателю барабанного электролизера; защитный кожух 3. Постоянный ток подводится к катодным токоподводам через пластины 10 и втулки 9 на цапфах электролизера контактирующих с обкладками опор-ловителей ванн соединенных с источником постоянного тока.[5]
Рисунок 4 – ручной переносной барабан
Рисунок 5 – Барабанный электролизер для нанесения электрохимических покрытий
5 Подготовка поверхности
Предварительная подготовка поверхности металла перед покрытием необходима для того чтобы обеспечить прочное сцепление покрытия с основным металлом создать условия снижения пористости и улучшения внешнего вида.[9]
На деталях поступающих в гальванических цех всегда имеются различные загрязнения – жировые оксидные и др. Эти загрязнения должны быть тщательно удалены так как они препятствуют прочному сцеплению с основным металлом. Если детали плохо очищены покрытие будет частично или полностью отслаиваться и со временем темнеть.
Для нанесения покрытий допускаются детали на поверхности которых нет раковин окалины заусенцев и других дефектов поскольку их наличие вызывает увеличение пористости покрытия ухудшает внешний вид покрытия и снижает его коррозионную стойкость. Шероховатость покрываемой поверхности деталей должна быть не ниже 4 класса точности (по ГОСТ 2789-73).[9]
Для подготовки изделий применяют механические химические и электрохимические способы обработки поверхности.
Механическую очистку проводят в том случае когда наряду с очисткой поверхности от продуктов коррозии необходимо получить поверхность более высокой чистоты. Механической обработке относят шлифование полирование крацевание пескоструйная гидроабразивная вибрационная обработка деталей и т.д.
Химическая и электрохимическая обработка поверхности включает химические и электрохимические процессы обезжиривания поверхности т.е. удаления следов минеральногоо масла полирововчных паст и т.д.
Жировые загрязнения хорошо растворяются в органических растворителях щелочных растворах и синтетических ПАВах. Обезжиривание осуществляют путем погружения детали в жидкость струйным способом или обработкой в паровой фазе. Щелочные растворы применяемые для обезжиривания стали различных марок содержат 5-15 гл едкого натра или кали 15-35гл тринатрийфосфата 15-35 гл кальцинированной соды и 3-10 гл эмульгатора.
Химическое обезжиривание щелочными растворами и моющими средствами быстрее протекает при повышенной температуре (60-80С). Продолжительность обезжиривания от 5 до 20 минут.
Применяется также обезжиривание с применением ультразвука этот способ наиболее эффективен при обезжиривании в слабощелочных растворах очень мелких или сложнопрофильных деталей.
Электрохимическое обезжиривание – способ обезжиривания металлов на катоде или аноде в щелочном растворе под действием электрического тока. Состав раствора применяемого для электрохимического обезжиривания приблизительно такой же как и для химического обезжиривания но без добавления эмульгаторов. Процесс ведут при температуре раствора 60 – 80 С и плотности тока 02 – 1 кАм2.
Электрохимическое обезжиривание более эффективно за счет того что газы выделяющиеся на электродах выполняют роль эмульгаторов и ослаблять связь жировых капель с поверхностью металла и тем самым ускоряют их удаление. [9]
6 Выбор электролита и режима электролиза
На основании проведенного аналитического обзора были выбраны электролит и режим электролиза.
Таблица 3 – Выбранный электролит
Основной целью курсового проекта является проектирование гальванического участка нанесения блестящего никелирования производительностью 8000 м2год.
Задачами курсового проекта являются:
Выбор электролита и режима электролиза;
Проведение инженерных расчетов;
Выбор гальванического оборудования на основании расчетов;
Составление технологической схемы процесса.
Таким образом в ходе курсового проекта необходимо подобрать наиболее рациональные условия для проведения процесса.
Технологическая часть
Таблица – Порядок технологических операций
Ультразвуковое обезжиривание поверхности
Промывка горячей проточной водой
Электрохимическое обезжиривание поверхности
Промывка проточной горячей водой
Травление поверхности
Промывка проточной холодной водой
Промывка горячей водой
Блестящее никелирование
Промывка холодной проточной водой
1 Определение фондов рабочего времени и режим работы цеха
Определение номинального времени работы гальванической линии работающей в 1 (одну) смену с учетом выходных праздничных и предпраздничных дней:
Следовательно номинальное время работы линии:
Рассчитаем эффективное время работы :
где – номинальное время работы гальванической линии;
– коэффициент простоя для гальванической линии.
Площадь детали рассчитывается по формуле (3):
где - площадь большого круга мм;
– площадь отверстия детали мм;
b – высота детали мм;
– коэффициент учитывающий что покрытие детали осуществляется с 2-х сторон;
- количество граней;
R – радиус окружности проходящей по ребрам детали мм
Производительность с учетом брака Р’год (м2год) (4):
где -105 – коэффициент брака;
– годовая производительность линии (8000м2год по заданию).
Рассчитаем часовую производительность Рчас (м2час) по формуле:
Рассчитаем производительность в смену Pсмена1 (м2смена) и Pсмена2 (детсмена) по формулам (6) и (7):
где – рабочее время одной смены
S – площадь детали определенная по формуле (3).
2 Определение толщины покрытия и времени электролиза
Согласно ГОСТ 9.303-84 «Единая система защиты от коррозии и старения. Покрытия металлические и неметаллические неорганические. Общие требования к выбору» выбираем толщину покрытия блестящим никелем в 9 мкм.[4]
Для определения времени электролиза нам необходимо знать электрохимический эквивалент никеля:
n = 2– число переносимых электронов;
F = 268 А*чмоль эл-нов – число Фарадея А*чмоль эл-нов.
Из закона Фарадея определяем продолжительность электролиза с учетом выбранной толщины покрытия и плотности тока.
где эл-за - продолжительность электролиза мин;
d - толщина покрытия мкм ( = 9мкм=9*10-5дм);
ρ - плотность никеля гсм3 (ρ = 891 гсм3=8910 гдм3);
– коэффициент перевода часов в минуты;
q - электрохимический эквивалент никеля (q = 11 г(А·ч));
Втк - катодный выход по току в % (Втк = 96 %);
Кист – коэффициент истирания (Кист = 120).
3 Расчёт оборудования
Определим время цикла по формуле :
Количество циклов z в полном рабочем дне определяется по формуле (12):
где (т.к. принимаем односменный график работы);
Производительность цикла за сутки Pцикла1 (м2цикл) и производительность по деталям в одном цикле Pцикла2 (детцикл) определяем по формулам (13) и (14):
Однако производительность цикла должна быть численно больше или равна часовой производительности поэтому необходимо проверить неравенство отношения В случае если проведенные выше расчеты выполнены корректны.
Необходимо учесть что для проверки неравенства определенное по формуле (10) нужно перевести в часы.
Следовательно расчеты выполнены корректно.
Определение количества деталей за один цикл:
где Sдет – покрываемая площадь детали Sдет = 00011 м2.
Масса одной детали( по чертежу):
mдет = ρ * Sдет*hдет (16)
Где ρ – плотность никеля гсм3 (ρ = 891 гсм3);
Sдет – площадь детали (рассчитанная по формуле (3))см2
hдет – толщина детали см
mдет = 891* 11*12 = 118г
Рассчитаем массу одной загрузки:
Мзагрузки = mдет * nдет = 118 * 1300 = 153400г =154 кг
Насыпной объем деталей:
Vдет = Мзагрузки*Кнасγ(17)
Где: Мзагрузки – масса одной загрузки кг;
γ – плотность материала детали ( γ Ст3 =7850) кгм3
Кнас – коэффициент насыпного объема
Кнас = 3 10 примем Кнас = 6
Vдет = 154 *67850 = 0118 м3
Рассчитаем объем барабана
Примем что детали занимают 30% от всего барабана т.е. коэффициент заполнения Кз=03. Тогда:
Vбар = VдетКз =011803=0393 м3= 393 л
Поскольку объем барабана слишком большой возьмем 5 барабанов с объемом 80л.
Где: R – радиус описанной окружности дм;
l – длина барабана дм.
Примем что l = 4R тогда:
Рассчитаем высоту барабана:
Где: r – радиус вписанной окружности см.
r = Н2=352=175 cм (22)
l = 4R=4*20= 80 см (23)
Найдем высоту слоя деталей в барабане:
Из методических указаний [2] находим:
Т.к. Кз = Vдет Vбар = 03 = 30% то
hH=034 и h = 059*R (24)
Сведем все рассчитанные данные:
Рисунок 6 – Параметры барабана
Переход от внутренних размеров барабана к наружным (все размеры в см):
Длина барабана (примем lперех= 20 см)
L нар = l внутр + lперех = 80 + 20 = 100 см (25)
Наружный диаметр (примем dперех =5 см)
Dнар = H + dперех = 35 + 5 = 40 см (26)
Рассчитаем габариты ванны:
Lвн = lнар + 2*lт (28)
Где lт – расстояние от барабана до торца ванны см (lт = 10 20 см).
Lвн = 100+ (10 20 см) = 110 120 см = 1000 1200 мм
Bвн = Dнар+2*(b1 + b2 + ba) (29)
Где b1 – расстояние от барабана до анода см (b1 = 10 20 см);
b2 – расстояние от анода до борта ванны см (b2 = 5 10 см);
ba – толщина анодов см (bа = 1 см).
Bвн = 40+2*((10 20) + (5 10) + 1) = 72 102 см = 720 1020 мм
Hвн = h1 + h2 + h3 (30)
Где h1 – расстояние от дна до барабана (по касательной) см (h1 = 10 30 см);
h2 – глубина погружения барабана см;
h3 – расстояние от электролита до края ванны см (h3 = 15 30 см).
Нвн = (10 30) + 492 + (15 30) =792 1092 см = 792 1092 мм.
Сведем все габариты ванны:
Выбор ванны по ГОСТу:
Выберем стандартную ванну по ГОСТ 23738 – 85 «Ванны автооператорных линий для химической электрохимической обработки поверхности и получения покрытий. Основные параметры и размеры». Выбираем ванну из полипропилена ванна без кармана исполнение 3 (штуцер для слива в дне ванны). Выбираем габариты ванны по ГОСТу в пределах рассчитаных значений:
Lвн = 1120мм = 112см = 112дм
Bвн=900мм = 90см = 9 дм
Hвн=1000мм = 100см = 10дм
Полная вместимость ванны 1008 литров.
Выбираем аноды по ГОСТ 2132-90 «Аноды никелевые» исходя из размеров ванны и анодной плотности тока iа:
Возьмем аноды прямоугольного сечения толщиной 1 см(10 мм). Ширина анодов(La) от 100мм до 300мм. Длина может быть: 40050060070080090010002000 мм. Аноды прямоугольного сечения изготавливают из никеля марки НПА1 НПА2.
Примем размеры анодов: 10х300х600
Найдем максимальное количество анодов на штанге:
na0 = LвнLa =1120300= 3 (31)
Так как анодных штанг в ванне две то всего количество анодов:
Na = na0 *2 = 2*3 = 6 анодов в ванне. (32)
Суммарная площадь анодов:
Sa = Na * sa = 6*600*300 = 1 080000мм2=108 дм2 (33)
Пересчёт плотности тока:
ia*Sa=2*(ik*Sk) (35)
ia = 2(ik* Sk) Sa (36)
Sk – площадь катода за одну загрузку(15 от площади загрузки одного цикла т.к. 5 ванн) м2 (Sk = 1435=0286 м2 = 286 дм2)
Sа – суммарная площадь анодов м2 (Sа = 108 дм2)
ia =2*( 2*286 ) 108 1 Адм2
Исходя из режима электролиза ia = 1-3 Адм2 т.е. анодная плотность тока является допустимой.
Таким образом выбираем аноды марки НПА2 размером 10*300*600.
4 Материальный баланс
) Рабочий объем электролита найдем по формуле (37):
0 – расстояние от борта ванны до уровня технологического раствора (зеркала электролита).
Определим массу электролита:
где ρ – плотность электролита гсм3 (примем ρэл-та = ρр-раN
– рабочий объём электролита см3;
Определим массу компонентов:
где – рабочая концентрация компонента гл (Таблица 1)примем что 1мл добавки равен 1грамму.
Коэффициент пересчета кристаллогидрата:
Тогда начальная масса хлорида никеля:
Масса воды в электролите рассчитывается как масса электролита за вычетом массы всех остальных компонентов:
Приход Ni за счет растворения анодов:
mNi = I z э q Bта (40)
где I – ток на ванне A
z – число загрузок за сутки
э – время электролиза ч
q – электрохимический эквивалент г(А·ч)
Bта – анодный выход по току (Bта = 100%)
Ток на ванне за 1 цикл:
где: I – ток на ванне А
ik – катодная тока Адм2 (ik = 2 Адм2)
Sпокр – площадь покрытия за один цикл дм2 (Sпокр = 286 м2 =0286 дм2)
I = ik Sпокр = 2 286 = 572 А
mNi = 572 24 (1860) 11 100 = 44396 г = 045кг
Расход никеля на покрытие рассчитываем по закону Фарадея:
Mпокр. = I z э q Bтк (42)
где Втк-катодный выход по току
mпокр=572*24*(1860)*11*096=044кг
Унос электролита поверхностью деталей и барабаном:
Vунэл-та = Ну Sпокр z Квн Кбар (43)
где Ну – норма уноса электролита (Ну = 036 лм2)
Sпокр – площадь покрываемой поверхности м2 (Sпокр= 189 м2)
z – число загрузок за сутки (z = 28 загрузок)
Квн – коэффициент ванны уноса. Квн = 05 (т.к. две ванны уноса)
Кбар – коэффициент при обработке деталей в барабане (Кбар = 15)
Vунэл-та = 036 189 28 05 15 = 142 лсмена
Масса уносящихся компонентовпримемчто 1 мл добавки равен 1 ее грамму :
= Vунэл-та ρэл-та (44)
= 1420 см3 12 гсм3 = 1704 г = 174кг
Определим потери на испарение.испарившейся воды:
где 456 – коэффициент пропорциональности кг*м-2*ч-1
Kв – коэффициент вентиляции для спокойной вентиляции принимаем равным 056
F– поверхность зеркала испарения м2 F=112*09= 10м2
р1 – давление насыщенного водяного пара при температуре электролита мм.рт.ст. р1=1495 мм.рт.ст. (при температуре 60°С).
р2 – парциальное давление водяного пара при данной влажности и температуре воздуха мм.рт.ст
ц – время работы ванны за цикл ч ц = 1860=03 ч.
zц – количество загрузок за смену zц =24 цикл
В – барометрическое давление мм.рт.ст В = 760 мм.рт. ст
Парциальное давление водяного пара при данной влажности и температуре воздуха:
где – давление насыщенного водяного пара при температуре воздуха мм.рт.ст
φ – влажность воздуха %. Примем влажность воздуха 75%.
Корректировка воды осуществляется по мере убыли уровня электролита (по фактическому состоянию на заводе).
Расчет ориентировочного времени корректировки электролита
где: кор – количество смен через которое необходимо корректировать состав электролита по какому-либо из компонентовсмен
сдоп – допустимое изменение концентрации компонента в электролите гл
ссут – изменение концентрации компонента в электролите за 1 смену гл
ссут = mуносаVэлектролита (47)
Для удобства сведем расчеты в таблицу где:
схраб - рабочая концентрация компонента гл
сх min – минимально допустимая рабочая концентрация компонента гл
Таблица 3 – Ориентировочное время корректировки электролита
Сводная таблица материального состава:
Таблица 4 – Материальный баланс электролизёра
Количество компонентов необходимое для корректировки:
Определим объём одного анода:
где N – количество анодов шт.
Теоретическая масса загружаемых анодов будет определяться следующим образом:
Масса скрапа составляет 5% от начальной массы анодов:
Mскрап= 005· moанод (51)
Масса шлама составляет 1% от начальной массы анодов:
Mшлам= 001· moанод (52)
Рассчитаем время растворения анодов то есть время через которое необходимо менять аноды:
раст.ан. = ( moанод- mскрап- mшлам)(q*I*Вта) (53)
раст.ан=(9800-49-096)=9212
Количество смен через которое необходимо заменять аноды:
раст.ан. смен. =92128 = 11 смен (54)
5Баланс напряжения электролизёра и выбор источника питания
При выборе источников постоянного тока для питания гальванических ванн необходимо знать напряжение которое он должен подавать на ванну. Для этого составляем полное уравнение баланса напряжения.
где Uг – напряжение на генераторе В
Ea и Ek – потенциалы анодной и катодной реакций В
ΔUЭл-т – падение напряжения в электролите В
ΔUч – падение напряжения в чехлах В
– падение напряжения в перфорацииВ
ΔUКонт – падение напряжения в контактах токоподводах и на других участках внешней цепи В
ΔUан– падение напряжения на анодах В
ΔUшин – падение напряжения в шинопроводе В
Запишем реакции происходящие на электродах:
К: Ni2++2eNi0 Вт = 96%
A: Ni0 -2eNi2+ Вт=100%
Потенциалы под током определим из поляризационных кривых которые приведены на рисунках 7 и 8 [6].
Для этого при рабочей плотности тока (ik = 02 Адм2 ia = 1 Адм2) находим значение потенциала под током.
Рисунок 7 – Поляризационные кривые при осаждении никеля из сернокислого электролитарН = 40 при различных температурах: 1 – температура 60С 2- 50С 3 – 25С.
Рисунок 8 – Поляризационные кривые при электроосаждении никеля из сернокислого электролита рН = 54 при температурах: 1 – в присутствии хлоридов 2 – в отсутствии хлоридов.
Из поляризационных кривых получаем что:
ΔЕ = + 030 – (-08) = + 11 В
Электрические составляющие баланса:
А) Падение напряжения в электролите находим по формуле:
ΔUэлектролита = i · l ·Кг
- удельная электропроводность электролита См см;
Найдем i [виноградов]:
l – расстояние в электролите между анодом и катодом т.к. у нас барабан то найдем ее как :
lд – расстояние от анода до середины барабана см (lд = 30 см).
l = 05(10 + 30) = 20 см
- удельная электропроводность электролита ( = 015 Смсм)
ΔUэлектролита = 002 20 015 100 26 В
Падение напряжения на перфорации барабана:
ΔUпер = ( iрасч ) р (58)
где – толщина стенки барабана см (примем 05 см)
р – степень перфорации (020-025 примем 025)
iрасч = Iв Sпрох (59)
Sпрох= 23 Sбок = 23 *a*l* 6
где: а- ширина грани барабана см;
l- длина барабана см.
Sпрох = 23 20 80 6 = 6400 см2
iрасч = 572 6400 = 001 Асм2
ΔUпер = (001 05) (025 015) = 013 В
Падение напряжения в чехлах рассчитываем как диафрагму. Уравнение для расчёта имеет вид:
– толщина хлориновой ткани м = 1 мм = 10-2 дм;
К = 35 - коэффициент показывающий во сколько раз сопротивление чехла пропитанного электролитом больше чем сопротивление слоя электролита
- удельная электропроводность электролита ( = 015 Смдм)
Падение напряжения в насыпной массе катода:
Падение напряжения на анодах ΔUан принимается 01 - 02 В поэтому принимаем:
Напряжение на ванне UВ определяется уравнением:
Uв = 11 + 26 + 013 + 005 + 02 + 4 = 808 В
Падение напряжения на шинопроводе ΔUш принимаем:
Падение напряжения в контактах ΔUконт составляет 7% от напряжения на ванне.
Таким образом напряжение на генераторе равно:
Сведём результаты расчёта баланса напряжений в таблицу 5 .
Таблица 5 – Баланс напряжения ванны и генератора
Составляющие баланса
Падение напряжения В
Таблица 6 – Параметры выпрямителя
Номин.выходной ток А
Номин. выходное напряжение В
Необходимо рассчитать насколько изменится температура электролита при непрерывной работе электролизера за смену и на основании этого значения сделать выводы о необходимости подогревания или охлаждения.
Рассчитаем джоулево тепло т.е. количество теплоты выделяющееся в результате работы ванны за смену:
QДж= I Егр эл z Кпер (73)
где: I – ток на ванне (I = 572 А)
эл - время электролиза (эл = 03 ч)
Eгр – греющее напряжение на ваннеВ
Греющее напряжение на ванне складывается из напряжения электролизера и падения напряжения в электролите:
Eгр = ΔЕ + Uэлетролита (74)
Eгр = 11 + 26 = 37 В
z – число циклов за смену (z = 24 цикла)
Кпер- коэффициент перевода в кДж (Кпер = 36)
QДж= 572 * 37* 03 24 36 = 54857 кДжч
Qпот = 01 54857 = 54857 кДжч
Джоулево тепло с учетом потерь в окружающую среду составляет:
QДж’ - Qпот = 54857 – 54857 = 493713 кДжч
Необходимо рассчитать изменение температуры в процессе электролиза:
QДж= Сэл-та mэл-та (tизм – tраб) (76)
где Сэл-та – теплоемкость электролита кДжкгК
mэл-та – масса электролита кг
tизм – температура электролита после электролиза ºС
tраб – рабочая температура электролиза ºС
Примем комнатную температуру tраб = 200С
Рассчитаем теплоемкость электролита:
Сэл-та = С NiSO4 · α NiSO4 + CNiCl2 · α NiCl2 + CH3BO3 · α H3BO3 + CH2O · α H2O (77)
где αi – массовая доля компонента электролита
Сi – удельная теплоемкость компонента электролита
Рассчитаем массовые доли компонентов:
α = mком-та mэл-та (78)
α (NiSO4) = m (NiSO4) mэл-та = 286 =025 = 25 %
α (NiCl2) = m (NiCl2) mэл-та = 477 =004 = 4 %
α (H3BO3) = m (H3BO3) mэл-та = 381 = 003 = 3 %
α (Н2O) = 100 – Σ = 100 – (25+4+3) = 68%
Теплоёмкости веществ в кДж(кгград):
Cp (NiSO4)=35кДж(кг*град)
Cp (NiCl2)=308 кДж(кг*град)
Cp (H3BO3)=23 кДж(кг*град)
Cp (Н2O)=418 кДж(кг*град)
Сэл-та = 35 * 025 + 308 * 004 + 23*003 + 418 068 = 39 кДж(кг*град)
За смену непрерывной работы электролизера температура электролита повышается на 11 ºС необходим принудительный нагрев т.к. процесс необходимо вести в интервале температур от 50 ºС до 65 ºС.
Тепловой баланс ванны электролиза можно посчитать по формуле:
где – теплота на разогрев электролита до рабочей температуры кДж;
– теплота на разогрев ванны до рабочей температуры кДж;
– теплота на разогрев анодов до рабочей температуры кДж;
– теплота на разогрев деталей до рабочей температуры кДж;
Теплотой на разогрев деталей можем пренебречь так как детали будут разогреты до рабочей температуры в предыдущем этапе .
Рассчитаем теплоту необходимую на разогрев электролита до 60 С по формуле (81):
где – теплоемкость электролита кДжкг*град;
– масса электролита кг;
– рабочая температура электролита К;
– температура в цеху на начало разогрева К.
Рассчитаем теплоту необходимую на разогрев анодов до 60 С по формуле (82):
где – теплоемкость анодов равная теплоемкости никеля кДжкг*К;
Рассчитаем теплоту необходимую на разогрев ванны до 50 С по формуле (45):
где – теплоемкость материала ванны (полипропилен) кДжкг*К;
Массу ванны рассчитаем исходя из формулы:
где – площадь длинной стенки ванны м2;
– площадь короткой стенки ванны м2;
– площадь дна ванны м2;
d – толщина стенок ванны м;
– плотность винипласта кгм3.
Общее тепло на разогрев ванны:
Выберем электронагреватель по теплоте которую нужно сообщить системе:
7 кВт*ч = 1853052 кДж
В данной курсовой работе был проведён расчёт гальванического участка блестящего никелирования стальных деталей производительностью 8000 м2год. Определены размеры ванны и барабана ванна выбрана по ГОСТу рассчитаны:
материальный баланс гальванической ванны
баланс напряжения на основании которого выбран источник питания
тепловой баланс электролизёра
время корректировки электролита.
Предложена технологическая схема покрытия никелем в барабане выбраны аноды
Для никелирования деталей выбран сульфатный электролит с готовыми добавками. Прежде всего он наиболее удобен обладает хорошей рассеивающей способностью имеет высокий выход по току равный 94-98% на катоде.
Виноградов С.С. Организация гальванического производства. Оборудование расчет производства нормирование. Изд.2-е перераб. и доп.Под ред. Кудрявцев – М.: «Глобус» 2005. – 240 с.
ГОСТ 7.32-2001. СИБИД. Отчет о научно-исследовательской работе. Структура и правила оформления.
ГОСТ 9.303-84 «Единая система защиты от коррозии и старения. Покрытия металлические и неметаллические неорганические. Общие требования к выбору»
Истомина Н.В. Оборудование электрохимических производств: Учебное пособие. – 2-е изд. перераб. – Ангарск: АГТА2010 – 100с.
Кудрявцев Н.Т. Прикладная электрохимия. Изд. 2-еперераб. и доп.под ред. Н.Т. Кудрявцева - М.: «Химия»1975 – 552с.
Мамаев В.И. Функциональная гальванотехника: Учебное пособие. - Киров: ВятГУ2013 – 208с.
Зинченко А.В. Новый справочник химика и технолога.Химическое равновесие.свойства растворов. под ред. Симанова С.А. – СПБ.: АНО НПО «Профессионал»2004.-998с.
Томилов А.П. Прикладная электрохимия. А.П. Томилов.- Л.: Химия 1984.-520с.: ил.
Ямпольский А.М. Краткий справочник гальванотехника. А.М. Ямпольский В.А. Ильин - Л.: Машиностроение Ленинградское отделение. 1981.-244с.
Ямпольский А.М. 'Меднение и никелирование' Издание 2-е дополненное и переработанное - Москва: Государственное научно-техническое издательство машиностроительной литературы 1961 - с.60
Рекомендуемые чертежи
Свободное скачивание на сегодня
Обновление через: 18 часов 8 минут