Проектирование и изучение механизмов зубодолбежного станка




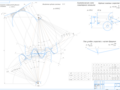
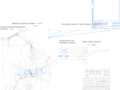
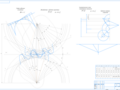
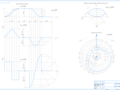
- Добавлен: 24.01.2023
- Размер: 7 MB
- Закачек: 0
Описание
Состав проекта
![]() |
![]() |
![]() |
![]() |
![]() ![]() ![]() |
![]() ![]() ![]() ![]() |
![]() |
![]() ![]() ![]() ![]() |
![]() ![]() ![]() |
![]() |
![]() |
![]() ![]() ![]() ![]() |
![]() ![]() ![]() |
![]() |
![]() ![]() ![]() |
![]() ![]() ![]() |
![]() ![]() ![]() |
![]() ![]() ![]() ![]() |
![]() ![]() ![]() |
![]() |
![]() ![]() ![]() |
![]() ![]() ![]() |
![]() |
![]() ![]() ![]() ![]() |
![]() ![]() |
![]() ![]() ![]() |
![]() ![]() ![]() |
Дополнительная информация
Схема привода исполнительного механизма.frw

Пример 1 (неготов, для Ирины).cdw

Чертеж Олега (пример 3, не моя работа, сырой).cdw

ЧертежКурсовойОлег (пример 2, не моя работа, сырая).cdw

Чертеж Графики(печать).cdw

Чертеж(печать).cdw

Рекомендуемые чертежи
- 10.08.2016
Свободное скачивание на сегодня
Другие проекты
- 22.08.2014