Проектирование механизма зубодолбежного станка




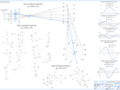
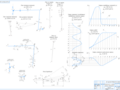
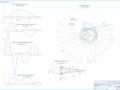
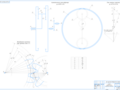
- Добавлен: 24.01.2023
- Размер: 476 KB
- Закачек: 1
Описание
Состав проекта
![]() |
![]() ![]() ![]() ![]() |
![]() ![]() ![]() ![]() |
![]() ![]() ![]() |
![]() ![]() ![]() ![]() |
![]() ![]() ![]() ![]() |
Дополнительная информация
Синтез кулачкового механизма.cdw

Кинематический анализ механизма.cdw

Динамический.cdw

Синтез передаточного зубчатого механизма.cdw
