Проектирование АТП на 280 автомобилей ЗИЛ-131




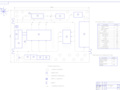
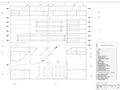
- Добавлен: 25.01.2023
- Размер: 1 MB
- Закачек: 2
Узнать, как скачать этот материал
Подписаться на ежедневные обновления каталога:
Описание
Проектирование АТП на 280 автомобилей ЗИЛ-131
Состав проекта
![]() |
![]() |
![]() ![]() ![]() ![]() |
![]() ![]() ![]() ![]() |
![]() ![]() ![]() ![]() |
![]() ![]() ![]() |
Дополнительная информация
Контент чертежей
Ген План АТП (готовое).dwg

Производственный корпус АТП.(готовое)dwg.dwg

Слесарно-механическое (готовое).dwg

Рекомендуемые чертежи
- 25.01.2023
- 25.01.2023
Свободное скачивание на сегодня
Обновление через: 4 часа 29 минут