Проектирование 2х ступенчатого соосного цилиндрического редуктора




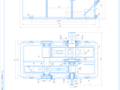
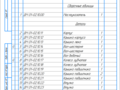
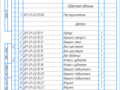
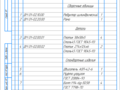
- Добавлен: 24.01.2023
- Размер: 506 KB
- Закачек: 0
Описание
Проектирование 2х ступенчатого соосного цилиндрического редуктора
Состав проекта
![]() |
![]() |
![]() ![]() ![]() ![]() |
![]() ![]() ![]() |
![]() ![]() ![]() ![]() |
![]() ![]() ![]() ![]() |
![]() ![]() ![]() ![]() |
![]() ![]() ![]() ![]() |
![]() ![]() ![]() ![]() |
![]() ![]() ![]() ![]() |
Дополнительная информация
Спецификация CБ+.spw

поясн.зап.ДМ новая.doc
Выбор электродвигателя и кинематический расчет ..
Определение требуемой мощности двигателя .
Определение передаточных отношений
Определение вращающихся моментов на валах .. .
Расчет зубчатых колес редуктора ..
Определение допускаемых контактных напряжений.
Расчет тихоходной передачи ..
Определение межосевого расстояния из условия контактной выносливости поверхностей зубьев
Определение нормального модуля
Определение основных размеров шестерни и колеса ..
Определение окружной скорости колес тихоходной ступени ..
Проверка контактных напряжений
Определение сил действующих в зацеплении тихоходной ступени ..
Проверка зубьев тихоходной ступени по напряжению изгиба.. .. .
Расчет быстроходной передачи
Определение межосевого расстояния.
Определение основных размеров шестерни и колеса
Определение окружной скорости колес быстроходной ступени ..
Проверка контактных напряжений ..
Определение сил действующих в зацеплении быстроходной ступени ..
Проверка зубьев быстроходной ступени по напряжению изгиба.. .. .
Предварительный расчет валов .
Промежуточный вал ..
Конструктивные размеры шестерни и колеса
Быстроходная ступень .
Тихоходная ступень .
Конструктивные размеры корпуса редуктора
Первый этап компоновки редуктора
Проверка долговечности подшипника .
Промежуточный вал .. ..
Проверка прочности шпоночных соединений .
Промежуточный вал .. .. ..
Уточненный расчет валов .
Выбор сорта масла .
Сборка редуктора.. .
Список используемой литературы
Техническое задание.
Рассчитать редуктор если заданы:
требуемая мощность Nт = 35 кВт;
частота вращения nт = 30 обмин.
Рис.1. Двухступенчатый горизонтальный цилиндрический
соосный косозубый редуктор
Выбор электродвигателя и кинематический расчет.
По таблице 2.1 [1] выбираем КПД механических передач.
КПД закрытой зубчатой передачи с цилиндрическими колесами 1 = 098. Потери на трение в подшипниках на обе пары каждого вала 2 = 099.
2.Определение требуемой мощности двигателя.
По таблице 2.2 [1] по требуемой мощности подбираем двигатель серии
АОП2-42-6 с Nном = 4кВт n = 955обмин.
По таблице 2.3 [1] подбираем диаметр вала ротора dдв = 32 мм.
3. Определение передаточных отношений.
Общее передаточное отношение привода:
Намечаем частные передаточные отношения редуктора.
По формулам из таблицы 1.3 [3] имеем:
Отклонение что меньше допускаемого .
Частоты вращения и угловые скорости валов редуктора:
ведущего вала редуктора
промежуточного вала редуктора
ведомого вала редуктора
4. Определение вращающихся моментов на валах.
Вращающийся момент на валу электродвигателя (на входном валу редуктора): .
Вращающийся момент на промежуточном валу редуктора: .
Вращающийся момент на выходном валу редуктора:
Расчет зубчатых колес редуктора.
Рис.2. Кинематическая схема цилиндрического двухступенчатого соосного редуктора
Так как в задании нет особых требований в отношении габаритов передачи выбираем материалы со средними механическими характеристиками. По таблице 3.3 [2] принимаем для шестерен сталь 45 улучшенную с твердостью НВ 230; для колес сталь 45 улучшенную с твердостью НВ 200.
Редуктор нереверсивный предназначен для длительной эксплуатации; работа односменная; валы установлены на подшипниках качения.
1. Определение допускаемых контактных напряжений.
Допускаемые контактные напряжения на поверхности зубьев цилиндрических колес при проектном расчете
здесь – предел контактной выносливости при базовом числе циклов (принимаем по таблице 3.2 [2]):
Коэффициент долговечности при длительной эксплуатации редуктора KHL = 1. Коэффициент запаса прочности выбирается в пределах 11÷12 принимаем = 115.
Принимаем значения коэффициента нагрузки для случая несимметричного расположения колес КН = 125 (таблица 3.1 [2]).
Коэффициенты ширины венцов по межосевому расстоянию для быстроходной ступени и для тихоходной ступени (так сделано потому что тихоходная ступень более нагружена чем быстроходная).
2. Расчет тихоходной передачи.
2.1. Определение межосевого расстояния из условия контактной выносливости поверхностей зубьев.
В соосном редукторе межосевые расстояния быстроходной и тихоходной ступеней равны: аwБ = аwТ.
Межосевое расстояние из условия контактной выносливости активных поверхностей зубьев определяется по формуле:
Округляем межосевое расстояние до ближайшего значения по стандарту СТ СЭВ 229-75 (мм): по первому ряду выбираем а = 250 мм.
2.2. Определение нормального модуля.
По стандарту СТ СЭВ 310-76 (мм) по первому ряду выбираем mnТ = 4.
2.3. Определение основных размеров шестерни и колеса.
Принимаем предварительно угол наклона зубьев = 10и определяем число зубьев шестерни:
= . Принимаем z3 = 20.
Тогда число зубьев колеса: .
Проверим межосевое расстояние.
Для косозубых колес со стандартным модулем:
При проверке обнаружилось несоответствие полученного результата с ранее принятым значением аТ = 250 мм по стандарту. В этом случае надо устранить расхождение изменением угла по формуле:
Теперь проверяем расчеты определив диаметры делительных окружностей:
Диаметры вершин зубьев:
Ширина колеса и шестерни:
Определяем коэффициент ширины шестерни по диаметру: .
2.4. Определение окружной скорости колес тихоходной ступени.
При скорости до 5 мс назначаем 8-ю степень точности.
2.5. Проверка контактных напряжений.
Назначаем коэффициенты для проверки контактных напряжений:
где - коэффициент учитывающий неравномерность распределения нагрузки по ширине венца который определяется по таблице 3.5[2]. При твердости НВ 350 и =128 = 1058;
- коэффициент учитывающий неравномерность распределения нагрузки между зубьями который определяется по таблице 3.4 [2]. = 106;
- коэффициент учитывающий динамическую нагрузку который определяется по таблице 3.6 [2]. = 100.
Тогда = 1058·106·100 = 112.
Условие прочности зубчатой передачи по контактным напряжениям:
т.е. условие прочности по контактным напряжениям выполнено.
2.6. Определение сил действующих в зацеплении тихоходной ступени.
2.7. Проверка зубьев тихоходной ступени по напряжению изгиба.
Для косозубых колес проверка проводится по формуле:
Определяем коэффициент нагрузки
где - коэффициент учитывающий неравномерность распределения нагрузки по длине зубьев; выбираем по таблице 3.7[2]. При и твердости ≤ НВ 350 =1154;
- коэффициент учитывающий динамическое действие нагрузки; выбираем по таблице 3.8 [2]. Принимаем при 8-ой степени точности твердости ≤ НВ 350 и скорости V до 3 мс =11.
Таким образом =1154·11=127.
Подбор коэффициента формы зуба YF проводится в зависимости от эквивалентных чисел зубьев.
Для шестерни: =; 398.
Определение допускаемого напряжения проводим по формуле:
По таблице 3.9 [2] для стали 45 улучшенной предел выносливости при нулевом цикле =18 НВ.
Коэффициент запаса прочности
где - коэффициент учитывающий нестабильность свойств материала зубчатых колес; по таблице 3.9 [2] = 175;
- коэффициент учитывающий способ получения заготовки зубчатого колеса. Для поковок и штамповок =10.
Определяем допускаемые напряжения и отношения :
Найденное отношение меньше для колеса следовательно дальнейшую проверку проводим для зубьев колеса. Определяем коэффициент Y учитывающий повышение прочности косых зубьев по сравнению с прямыми:
Для средних значений коэффициента торцового перекрытия α = 15 и 8-ой степени точности КFα = 075.
= что значительно меньше []F4 = 206Нмм2.
Следовательно условие прочности по напряжениям изгиба также выполнено.
3. Расчет быстроходной передачи.
Допускаемое контактное напряжение для материала колеса такое же как в тихоходной ступени: []Н = 408Нмм2.
3.1. Определение межосевого расстояния.
Из условия соосности аwБ = аwТ = 250 мм.
3.2. Определение нормального модуля.
Нормальный модуль для быстроходной ступени в целях увеличения плавности и бесшумности передачи принимают несколько меньше чем в тихоходной. Принимаем mnБ = 25.
3.3. Определение основных размеров шестерни и колеса.
Принимаем предварительно угол наклона зубьев = 10.
Определяем число зубьев шестерни:
Тогда число зубьев колеса: = 27·63 = 1701. Принимаем z2 = 170.
Теперь проверяем расчеты определив диаметры делительных окружностей: ;
Определяем коэффициент ширины шестерни по диаметру:
3.4. Определение окружной скорости колес быстроходной ступени.
3.5. Проверка контактных напряжений.
где - коэффициент учитывающий неравномерность распределения нагрузки по ширине венца который определяется по таблице 3.5 [2].
При твердости ≤ НВ 350 и = 101 = 104;
- коэффициент учитывающий неравномерность распределения нагрузки между зубьями который определяется по таблице 3.4 [2]. = 108;
- коэффициент учитывающий динамическую нагрузку который определяется по таблице 3.6 [2]. = 10.
Тогда = 104·108·10 = 112.
I ступени 2-х ступенчатых редукторов.
Условие прочности по контактным напряжениям выполнено.
3.6. Определение сил действующих в зацеплении быстроходной ступени.
3.7. Проверка зубьев быстроходной ступени по напряжению изгиба.
Коэффициент нагрузки
где - коэффициент учитывающий неравномерность распределения нагрузки по длине зубьев; выбираем по таблице 3.7 [2]. При и твердости НВ 350 =110;
- коэффициент учитывающий динамическое действие нагрузки; выбираем по таблице 3.8 [2]. Принимаем при 8-ой степени точности твердости НВ 350 и скорости V от 3 мс до 8 мс =13.
Таким образом =11·13=143.
Для шестерни: =; 384.
Определение допускаемого напряжения проводим по формуле: .
По таблице 3.9 [2] для стали 45 улучшенной предел выносливости при нулевом цикле =18НВ:
Для колеса принимаем = .
Найденное отношение меньше для колеса следовательно дальнейшую проверку проводим для зубьев колеса. Повышение прочности косых зубьев учитываем коэффициентом Y:
= 282Нмм2 = 206Нмм2 следовательно условие прочности по напряжениям изгиба также выполнено.
Предварительный расчет валов.
Проектирование вала начинаем с ориентировочного определения диаметра выходного конца его из расчета на чистое кручение по пониженным допускаемым напряжениям без учета влияния изгиба:
где МК – крутящий момент Н·мм;
[t]К – допускаемые напряжения на кручение Нмм2.
Крутящие моменты в поперечных сечениях валов:
ведущего М1 = 40·103 Н·мм;
промежуточного М2 = М3 =252·103 Н·мм;
ведомого М4 = 1260·103 Н·мм.
Диаметр выходного конца ведущего вала при [t]К =25 Нмм2:
Т.к. вал редуктора соединен муфтой с валом электродвигателя то необходимо согласовать диаметры ротора dB1 и dдв .
У подобранного электродвигателя dдв= 32мм.
Выбираем МУВП по ГОСТ 21424-75 с расточками полумуфт под dдв=32мм и dB1 = 25мм.
Диаметр следующей ступени определим по формуле
где с – фаска соответствующая диаметру dB1.
Принимаем диаметр шеек под подшипники dП1 = 30мм.
Шестерню выполняем за одно целое с валом.
2. Промежуточный вал.
У промежуточного вала определяем диаметр под колесом z2 по пониженным допускаемым напряжениям [t]К =15 Нмм2:
Принимаем диаметр вала под колесом dK2 = 45мм.
Диаметр шеек под подшипники dП2 = 40мм.
Расчет ведется при [t]К =25 Нмм2.
Диаметр выходного конца вала:
Принимаем dB4 = 65мм.
Диаметр шеек под подшипники dП4 = 70мм.
Диаметр вала под колесом dK4 = 75мм.
Конструктивные размеры шестерни и колеса.
1. Быстроходная ступень.
делительный диаметр d1 = 69мм;
диаметр вершин зуба dа1 = 74мм;
ширина венца зуба b1 = 70мм;
шестерню изготавливаем заодно целое с валом.
делительный диаметр d2 = 431мм;
диаметр вершин зуба dа2 = 436мм;
ширина венца зуба b2 = 63мм.
Диаметр ступицы колеса:
Длина ступицы колеса:
принимаем = = 63мм.
2. Тихоходная ступень.
делительный диаметр d3 = 83мм;
диаметр вершин зуба dа3 = 91мм;
ширина венца зуба b3 = 106мм;
делительный диаметр d4 = 417мм;
диаметр вершин зуба dа4 = 425мм;
ширина венца зуба b4 = 100мм.
Конструктивные размеры корпуса редуктора.
Для вычерчивания общего вида редуктора рассчитываем необходимые размеры для элементов корпуса и крепежных деталей:
Ориентировочные соотношения
Толщина стенки корпуса редуктора
Толщина стенки крышки редуктора
Толщина верхнего пояса (фланца) корпуса и крышки
Толщина нижнего пояса (фланца) корпуса
Толщина нижнего пояса корпуса без бобышки
Толщина ребер основания корпуса
Толщина ребер крышки
Диаметр фундаментальных болтов
Диаметр болтов у подшипников
Диаметр болтов соединяющих основание корпуса с крышкой
Диаметр болтов крепления крышки подшипников
Расстояние между центром болта крепления крышки подшипника и болтом крепления фланца крышки к фланцу корпуса
Расстояние от центра болта для крепления крышки подшипника до наружного торца крышки
Расстояние от центра болта для крепления крышки подшипника до наружной поверхности гнезда под подшипник
Первый этап компоновки редуктора.
Первый этап служит для приближенного определения положения зубчатых колес и шестерен относительно опор для последующего определения опорных реакций и подбора подшипников.
Последовательность выполнения компоновки.
Проводим две вертикальные осевые линии на расстоянии аБ = 250 мм и
Вычерчиваем в виде прямоугольников упрощенно шестерню за одно целое с валом и колесо.
Ориентировочно намечаем для валов радиальные шарикоподшипники легкой серии.
Габариты подшипников выбираем по диаметру вала в месте посадки используя данные из таблицы 8.1 [1].
Получаем следующие подшипники:
Условное обозначение подшипника
Динамическая грузоподъемность С кН
Статическая грузоподъемность
Наименьший зазор между наружной поверхностью колеса и внутренней стенкой корпуса:
по диаметру А = (1 12)· = (1 12)·10 = 10 12мм принимаем 10мм;
по торцам А1 А = 10мм.
Вычерчиваем зубчатые колеса в виде прямоугольников и очерчиваем внутреннюю стенку корпуса отступая от наиболее выступающих элементов зубчатых колес на расчетное расстояние А = 10мм.
Размещаем подшипники в корпусе редуктора углубив их от внутренней стенки корпуса на расстояние у = 5мм.
Определяем замером расстояния: на ведущем валу на промежуточном валу на ведомом валу
Проверка долговечности подшипника.
Из предыдущих расчетов имеем: окружная сила РБ = 1159 Н;
радиальная сила РrБ = 428 Н;
осевая сила РаБ = 203 Н.
Из первого этапа компоновки имеем: l1 = 58мм d1 = 69мм
Находим реакции опор:
Определяем суммарные реакции:
Подбираем подшипники по наиболее нагруженной опоре 1. Намечаем подшипники радиальные однорядные по ГОСТ 8338-75 легкая серия. Обозначение подшипника 206:
d = 30мм; D = 62мм; В = 16мм; С =15кН; С0 = 10кН.
Эквивалентная нагрузка необходимая для определения расчетной долговечности рассчитывается по формуле:
где радиальная нагрузка = = 641 Н;
осевая нагрузка 203 Н;
(вращается внутреннее кольцо); = 1 (по таблице 7.1 [2]);= 1(по таблице 7.2 [2]).
Для подбора X и Y вычислим отношение . Этой величине (по таблице 7.3 [2]) соответствует е = 021.
Расчетная долговечность млн.об.:
Расчетная долговечность ч.:
Для построения эпюр действующих моментов определяем значения изгибающих моментов.
Рис.3. Расчетная схема ведущего вала.
Из предыдущих расчетов имеем: окружная сила РБ = 1159Н;
радиальная сила РrБ = 428Н;
осевая сила РаБ = 203Н;
Из первого этапа компоновки имеем: l4 = 77мм.
d2 = 431мм; d3 = 83мм.
n2 = 1516 обмин.; Мкр2 = 252·103 Н×мм.
Составляем уравнение равновесия относительно точки 3:
Составляем уравнение равновесия относительно точки 4:
Подбираем подшипники по наиболее нагруженной опоре 4. Намечаем подшипники радиальные однорядные по ГОСТ 8338-75 легкая серия. Обозначение подшипника 208:
d= 40мм; D = 80мм; В = 18мм; С =251 кН; С0 = 178 кН.
где радиальная нагрузка ==4634Н;
осевая нагрузка 1770 - 203 = 1567Н;
Для подбора X и Y вычислим отношение
Этой величине соответствует е 0283.
Рис.4. Расчетная схема промежуточного вала
Из предыдущих расчетов имеем: окружная сила РТ = 6072Н;
радиальная сила РrТ = 2302Н;
осевая сила РаТ = 1770Н.
Из первого этапа компоновки имеем: d4 = 417мм.
n3 = 303обмин.; Мкр3 = 1260·103Н×мм.
Составляем уравнение равновесия относительно точки 6:
Составляем уравнение равновесия относительно точки 5:
Подбираем подшипники по наиболее нагруженной опоре 6. Намечаем подшипники радиальные однорядные по ГОСТ 8338-75 легкая серия.
Обозначение подшипника 214:
d= 70мм; D = 125мм; В = 24мм; С =479кН; С0 = 374кН.
где радиальная нагрузка 46013Н;
осевая нагрузка =1770Н;
Для подбора X и Y вычислим отношение .
Этой величине соответствует е 043.
Рис.4. Расчетная схема ведомого вала
Проверка прочности шпоночных соединений.
Шпонки выбираем призматические со скругленными торцами. Размеры сечений шпонок пазов и длины по ТССЭВ 189-75. Материал шпонок – сталь 45 нормализованная. Проверка прочности шпоночных соединений проводится по формуле:
Допускаемое напряжение на смятие при чугунной ступице стальной ступице . Длину шпонки выбираем так чтобы она была несколько меньше длины ступицы на (5 10 мм). Параметры призматических шпонок выбираем по таблице 10.1.[1].
На ведущем валу проверяем шпонку под полумуфтой. Ее параметры:
Длина шпонки (при длине ступицы полумуфты МУВП 60мм). Момент на ведущем валу .
(полумуфты МУВП изготавливают из чугуна марки СЧ 21).
Условие смятия выполнено.
На смятие будем проверять шпонку под колесом быстроходной ступени поскольку шестерню изготавливаем заодно целое с валом. Параметры:
Длина шпонки (при длине ступицы колеса ). Момент на промежуточном валу .
На смятие проверяем шпонку под колесом тихоходной ступени. Параметры:
Длина шпонки (при длине ступицы колеса ). Момент на ведомом валу .
Уточненный расчет валов.
Принимаем что нормальные напряжения от изгиба изменяются по симметричному циклу а касательные от кручения – по отнулевому (пульсирующему). Уточненный расчет состоит в определении коэффициентов запаса прочности п для опасных сечений и сравнении их с требуемыми значениями [п]. Прочность соблюдается при При п > 25 требуется расчет на жесткость.
Материал вала тот же что и для шестерни (шестерня выполнена заодно с валом) – сталь 45 термообработка – улучшение.
По таблице 3.3 [2] при диаметре заготовки вала до 90мм () среднее значение .
Предел выносливости при симметричном цикле изгиба .
Предел выносливости при симметричном цикле касательных напряжений .
В этом сечении при передаче вращающего момента от электродвигателя через муфту возникают только касательные напряжения. Концентрацию напряжений вызывает наличие шпоночной канавки.
Коэффициент запаса прочности определяется по следующей зависимости:
где амплитуда и среднее напряжение отнулевого цикла
Для углеродистых и легированных сталей . Значение выбираем по таблице 11.2 [1]. Принимаем = 168. Значение выбираем по таблице 11.3 [1]. Принимаем тогда
Такой большой коэффициент запаса прочности объясняется тем что диаметр вала был увеличен при конструировании для соединения его муфтой с валом электродвигателя.
Материал вала – сталь 45 термообработка – улучшение (т.к. на промежуточном валу находится шестерня изготавливаемая заодно с валом из стали 45 улучшенной). По таблице 3.3 [2] при диаметре заготовки вала от 90мм до 120мм () среднее значение .
Принимаем что нормальные напряжения от изгиба изменяются по симметричному циклу а касательные от кручения – по отнулевому (пульсирующему). Определяем коэффициент запаса прочности для наиболее опасного сечения которым является сечение А–А под колесом быстроходной ступени. Концентрация напряжений обусловлена наличием шпоночной канавки.
По данным расчета изгибающие моменты:
Результирующий изгибающий момент:
Моменты сопротивления нетто:
Амплитуда нормальных напряжений изгиба:
Амплитуда и среднее напряжение цикла касательных напряжений:
По таблицам 11.2 и 11.3 [1] принимаем:
Коэффициенты запаса прочности:
Общий коэффициент запаса прочности:
Такой большой коэффициент запаса прочности позволяет не проверять сечение с галтелью в месте перехода от посадочного диаметра колеса к диаметру буртика вала в которое упирается колесо при установке.
Материал вала – сталь 45 нормализованная .
Принимаем что нормальные напряжения от изгиба изменяются по симметричному циклу а касательные от кручения – по отнулевому (пульсирующему). Определяем коэффициент запаса прочности для сечения в котором возникает наибольший изгибающий момент. Это сечение А–А под колесом тихоходной ступени. И в этом случае концентрация напряжения обусловлена наличием шпоночной канавки.
Из предыдущих расчетов имеем изгибающие моменты:
По таблицам 11.2 и 11.3 [1] принимаем:
Смазка зубчатых зацеплений производится окунанием зубчатых колес в масло заливаемое внутрь корпуса до уровня обеспечивающего погружение колеса примерно на 10мм.
Объем масляной ванны определяется из расчета 025дм3 на 1кВт передаваемой мощности: .
Подшипники смазываются тем же маслом засчет разбрызгивания. По таблице 12.1 [1] устанавливаем вязкость масла.
В быстроходной паре V=345мс рекомендуется вязкость . В тихоходной паре V=066мс рекомендуется вязкость .
По таблице 12.1 [1] выбираем индустриальное масло И-100А с вязкостью . Уровень масла контролируется трубчатым маслоуказателем.
Перед сборкой внутреннюю полость корпуса редуктора тщательно очищают и покрывают маслостойкой краской. Сборку производят в соответствии с чертежом общего вида редуктора начиная с узлов валов.
На ведущий вал насаживают шарикоподшипники предварительно нагретые в масле до 80 – 100 0С. В промежуточный вал закладывают шпонки и напрессовывают зубчатое колесо плотно до упора в бурт вала; затем надевают распорную втулку и устанавливают шарикоподшипники предварительно нагретые в масле. В ведомый вал закладывают шпонки и напрессовывают зубчатое колесо до упора в бурт вала; затем надевают распорную втулку и устанавливают шарикоподшипники предварительно нагретые в масле.
Собранный ведомый вал укладывают в основание картера редуктора и надевают корпус редуктора покрывая предварительно поверхности стыка крышки и корпуса спиртовым лаком. Для центровки корпус устанавливают на картер с помощью двух конических штифтов затягивают болты крепления корпуса к картеру. В той же последовательности производят установку промежуточного и ведущего валов.
После этого на ведущий вал надевают распорные кольца ставят крышки подшипников с комплектом металлических прокладок. Перед установкой сквозных крышек в проточки закладывают войлочные соединения пропитанные горячим маслом.
Проверяют проворачиванием валов отсутствие заклинивания подшипников (валы должны проворачиваться от руки) и закрепляют крышки винтами. Затем ввертывают пробку маслосливного отверстия с прокладкой и трубчатый маслоуказатель. Заливают в картер масло и закрывают заливное отверстие.
Собранный редуктор обкатывают и подвергают испытанию на стенде по программе устанавливаемой техническими условиями.
Список используемой литературы.
Детали машин. Учеб. пособ.В.И. Мигненко А.П. Осипов; Самар. гос. техн. ун-т филиал в г.Сызрани. Самара 2002.– 68 с.
Чернавский С.А. Курсовое проектирование деталей машин. Учеб. пособ. для техникумов. – М.: Машиностроение 1979. – 351с.
Дунаев П.Ф. Леликов О.П. Конструирование узлов и деталей машин: Учеб. пособие для техн. спец. вузов. – 5-е изд. перераб. и доп. – М.: Высш. шк. 1998. – 447с. ил.
Чернилевский Д.В. Детали машин. Проектирование приводов технологического оборудования: Учеб. пособие для студентов вузов. – 3-е изд. исправл. – М.: Машиностроение 2004. – 560 с. ил.
В. И. Анурьев. Справочник конструктора–машиностроителя: В 3-х томах. 6-ое изд. перераб. и доп. – М.: Машиностроение 1982.
Детали машин. Атлас конструкций. 4-е изд.Под ред. Д.Н. Решетова. –М.: Машиностроение 1970. – 360 с.
Допуски и посадки. Справочник в 2-х частях. 6-е изд. .Под ред. В.Д. Мягкова М.А. Палей. – Л.: Машиностроение 1982. – 543 с.
Спецификация CБ++.spw

Спецификация привод+.spw

Редуктор цилиндрический
Сталь45 ГОСТ 9045-93
вал-шестерня +.cdw

Нормальный исходный контур
Коэффициент смещения
улучшение 220 240 НВ
Размер обеспечить инструментом.
Неуказанные предельные отклонения размеров: валов - t
t2 по ГОСТ 25670-83.
Сталь 45 ГОСТ 1050-74
колесо+.cdw

Неуазанные предельные размеров: валов - t
t2 по ГОСТ 25670-83.
Направление линии зуба
Нормальный исходный контур
Коэффециент смещения
Сталь 45 ГОСТ 1050-74
рама+.cdw

Сварные швы выполнить по ГОСТ 5264-80 электродом Э-42А
Покрытие рамы - грунтовка ГФ-021 ГОСТ 25129-82 и эмаль
ПФ-115 серая ГОСТ 6465-76.
Неуказанные предельные отклонения размеров: отверстий +t
остальных + t2 по ГОСТ 25670-83.
СБ+.cdw

Частота вращения тихоходного вала редуктора n=30обмин
Мощность электродвигателя 3
Передаточное отношение редуктора 31
Степень точности изготовления зубчатой передачи 8.
Коэффициент полезного действия 0
Редуктор двухступенчатый
цилиндрический соосный
Необработанные поверхности деталей
находящихся в маслянной
красить маслостойкой красной эмалью.
Наружные поверхности корпуса красить серой эмалью ПФ-115
Плоскость разъема покрыть тонким слоем герметика УТ-34
ГОСТ 24285-85 при окончательной сборке.
Технические требования
Техническая характеристика
Рекомендуемые чертежи
- 20.12.2022
- 25.10.2022
Свободное скачивание на сегодня
- 24.01.2023
Другие проекты
- 18.03.2024
- 20.08.2014