Привод цепного транспортёра с одноступенчатым червячным редуктором



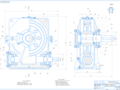
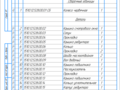
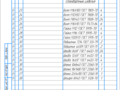
- Добавлен: 24.01.2023
- Размер: 740 KB
- Закачек: 0
Описание
Привод цепного транспортёра с одноступенчатым червячным редуктором
Состав проекта
![]() |
![]() |
![]() ![]() ![]() ![]() |
![]() ![]() ![]() ![]() |
![]() |
![]() ![]() ![]() ![]() |
![]() ![]() ![]() |
![]() |
![]() |
Дополнительная информация
спецификация 1л.cdw

Крышка смотрового окна
Кольцо уплотнительное
спецификация 2 л.cdw

Болт М12Х50 ГОСТ 7808-70
Винт М8Х40 ГОСТ 7808-70
Винт М16Х10 ГОСТ 17473-84
Гайка М12 ГОСТ 5915-70
Гайка М16 ГОСТ 5915-70
Гайка М20Х1.5 ГОСТ 5915-70
Подшипник 7214 ГОСТ 333-79
Подшипник 46309 ГОСТ 831-75
Шайба 8.65Г ГОСТ 6402-70
Шайба 12.65Г ГОСТ 6402-70
Шайба 16.65Г ГОСТ 6402-70
Шпонка 10х8х40 ГОСТ 23360-78
Шпонка 18х11х80 ГОСТ 23360-78
Шпонка 22х14х100 ГОСТ 23360-78
Штифт 8Х40 ГОСТ 3128-70
Редуктор червячный Сборочный чертёж _ 151001.12.528.04.01. СБ.cdw

Вращающий момент на тихоходном валу Т =964
Передаточное число редуктора U=25
Техническая характеристика
достаточный для смазки зацепления.
на угол до 5 . При этом должен быть обеспечен
отклонением от горизонтального положения
Допускается эксплуатировать редуктор с
Редуктор залить маслом И-Т-Д-68 ГОСТ 17479.4-87
Технические требования
ПЗ Головачёв.doc
Детали машин и основы конструирования
на тему "Червячный редуктор. Привод цепного транспортера
Нормоконтроль: Группа: 5ТМ - 39
Головачёв С.Ю. Проектирование привода цепного транспортера. Трехгорный: ТТИ НИЯУ МИФИ ТМ 2012 33л. Библиография литературы – 4 наименования.
В курсовом проекте произведен расчет привода для цепного транспортера который эксплуатируется в загрязненной среде.
Курсовой проект включает в себя выбор электродвигателя выбор материала для зубчатых колес и шестерен а так же расчет допускаемых контактных напряжений и напряжений изгиба определения частот вращения и вращающих моментов на валах редуктора. Так же произведен проектный и проверочный расчет червячной зубчатой передачи проектный расчет валов редуктора и выбор подшипников качения на расчетный ресурс привода.
В курсовом проекте произведено конструирование зубчатых колес расчет шпоночных соединений конструирование корпуса редуктора и крышек подшипников.
Затем сделан выбор смазочных материалов и систем смазывания редуктора подбор и расчет муфт. Произведено описание порядка сборки редуктора и назначение посадок.
Назначение и краткое описание привода 5
Выбор электродвигателя 6
Расчет на прочность и определение параметров передачи 8
Определение сил в зацеплении 12
Проектный и проверочный расчет валов редуктора 14
1 Определение размеров ступеней валов 14
2 Расчетная схема червяка 13
3 Расчетная схема колеса 17
Подбор и расчет подшипников 19
1 Подбор и расчет подшипников червяка 19
2 Подбор и расчет подшипников вала колеса 20
Проверочный расчет валов 21
1 Проверочный расчет вала – червяка 21
2 Проверочный расчет тихоходного вала 24
Проверочный расчет шпоночных соединений 26
1 Проверочный расчет шпонки под колесом 27
2 Проверочный расчет шпонки на тихоходном валу 27
3 Проверочный расчет шпонки на быстроходном валу 28
Тепловой расчет червячного редуктора 28
Назначение квалитетов точности шероховатости поверхности
отклонений формы и взаимного расположения поверхностей 29
Определение размеров основных элементов редуктора 30
Выбор системы назначения сорта и количества смазки и зацепления подшипников 31
Описание технологии сборки и регулирование его основных узлов 32
Список использованной литературы 33
)Графическая часть на 1 листе формата А1
Назначение и краткое описание привода
Транспортирующие машины предназначены для перемещения массового груза непрерывным потоком без остановок для загрузки и разгрузки. Под массовыми грузами следует понимать грузы состоящие из большого числа частиц или кусков перемещаемые в большом количестве.
Транспортные операции по перемещению одинаковых массовых грузов отличаются однотипностью поэтому транспортирующие машины легко поддаются автоматизации. Промышленные предприятия производящие однородные массовые грузы доведены при помощи транспортирующих машин до высокой степени автоматизации.
Цепного транспортеры относятся к группе транспортирующих машин с тяговым органом. Цепной транспортер имеет тяговый орган выполненный в виде бесконечной ленты являющийся одновременно и несущим элементом транспортера приводную станцию с натяжным хвостовым барабаном и натяжным устройствам поддерживающих роликов на рабочей ветви ленты и на холостой ветви ленты загрузочное устройство и разгрузочное устройство отклоняющий барабан и устройство для очистки ленты. Все элементы транспортера смонтированы на металлической раме. Ленточные транспортеры являются наиболее распространенными транспортирующими машинами применяемыми в самых различных областях народного хозяйства для перемещения разнообразных штучных и насыпных грузов.
Основной характеристикой транспортеров является их производительность. Производительность выражается в виде объема материала переносимого транспортером в единицу времени. Диапазон производительности ленточных транспортеров чрезвычайно велик и максимальные значения производительности достигают 20000 тчас. Длина ленточных транспортеров (то есть расстояние между центрами приводного и хвостового барабанов) достигают 45 км.
В данной работе произведен проект привода для цепного транспортера который используется в цехе деревообработки для транспортировки полученной в ходе производства стружки.
Выбор электродвигателя
Для выбора электродвигателя определяем требуемую его мощность и частоту вращения.
Определяем потребляемую мощность привода по формуле:
где - номинальная мощность привода Вт; ;
Находим общий КПД по табл. 01.
Определяем общий КПД привода:
где - общий КПД привода;
- КПД подшипников качения ;
- КПД червячного редуктора .
- КПД клиноременной передачи =096
По формуле (1.2) вычисляем:
Определяем требуемую мощность электродвигателя по (1.1):
Предварительно определяем частоту вращения привода вала:
где nрм – частота вращения приводного вала обмин;
z- число зубьев ведущей звездочки тягового органа z=6;
t- шаг тяговой цепи t=60 мм;
V- скорость конвейера V= 02 мс
С данной номинальной мощностью есть ряд двигателей:
АМ100S2Y3 - nном = 2880 обмин;
АМ100L4Y3 - nном = 1430 обмин;
АМ112MB6Y3 - nном = 950 обмин;
АМ132S8Y3 - nном = 720 обмин.
Из этого ряда электродвигателей выбираем двигатель с устраивающим нас общим передаточным числом.
Определяем для каждого двигателя общее передаточное число по формуле:
где U - общее передаточное число;
nном – номинальная частота вращения двигателя;
nрм – частота вращения приводного вала.
По формуле (1.4) получаем:
Из данного ряда передаточных чисел выбираем второе: U = 36; nном =1430 обмин. Здесь передаточное число червячного редуктора можно подсчитать:
(из табл.12 с.7 в “Курсовом проектировании деталей машин” С.А. Чернавский)
Приняв эти передаточные числа продолжим дальнейший расчет отыскания числа оборотов тихоходного вала:
где n1 –число оборотов входного быстроходного вала равное оборотам двигателя;
n2 – число оборотов тихоходного вала;
Выбранный двигатель 4АМ100L4У3 (Nном. = 4 кВт; nном. = 1430 обмин).
Структура обозначения двигателя:
– порядковый номер серии;
А – вид двигателя – асинхронный;
М – модернизированный;
0 – высота оси вращения ротора;
L – установочный размер по длине станины;
У3 – кинематическое исполнение и категория размещения.
Основные размеры двигателя мм приведены в таблице 2 (стр. 386 [1] табл. К10).
Таблица 2.1 – Основные размеры двигателя мм
Рисунок 1 – Эскиз электродвигателя
Расчет на прочность и определение геометрических параметров передачи
где 1 - угловая скорость на входном валу с-1;
P1- номинальная мощность P1=3000Вт;
Определяем угловую скорость тихоходного вала:
Определяем требуемый крутящий момент на валу электродвигателя:
Определяем крутящий момент на червячном колесе:
где T1 - крутящий момент на быстроходном валу Нм;
=0.8 (при Z1=2 рекомендуется =075..082);
Для этого нужно определить еще передаточное отношение передачи i=n1n2=143079.4=18
По формуле (3.3) вычисляем:
Определяем скорость скольжения:
Предварительное число зубьев колеса:
Z2=Z1*i=2*18=36 (3.5)
При червячное колесо изготавливается составным способом (рис.2 а): венец – бронзовый центр – чугунный. Венец соединен с центром посадкой с натягом. На наружной поверхности центра предусматривается буртик. Во избежание смещения венца относительно центра на стыке установлены 4 винта (рис. 2б).
Рисунок 2 - Червячное колесо
Для червяка по табл. 31(с. 49) выбираем сталь 40Х с твердостью HRC червяк со шлифованными и полированными витками.
Определение допускаемого контактного напряжения :
где KНL – коэффициент долговечности при расчете на контактную прочность;
N- число циклов нагружения зубьев червячного колеса за весь срок службы если то N принять равным 25*107
где - угловая скорость соответствующего вала1с
Lh- срок службы привода
где Lг- срок службы привода лет;
tc- продолжительность смены;
Подставив в (3.6) получим:
Определяем допускаемое напряжение при кратковременной нагрузке:
Определяем коэффициент диаметра червяка:
Приведенный модуль упругости:
Определяем предварительное межосевое расстояние по формуле:
Подставляем значения в формулу (3.9) получаем:
Межцентровое расстояние принимаем aw = 280 мм.
Находим осевой модуль зацепления:
Находим необходимый коэффициент смещения для червячного колеса чтобы вписаться в принятое межосевое расстояние:
По условию не подрезания и не заострения X=+-0.7
Определяем начальные диаметры червяка и колеса:
Проверяем выбранное значение скорости скольжения Vs :
Было принято Vs=6.3 мс- материал БрО10Ф1- сохраняем. Сохраняем и т.к. разность значений Vs мала.
Основные размеры червяка:
m=12.5 мм dа1=d1+2m=125+2*12.5=150 мм
q=10 df1=d1-2.4m=125-2.4*12.5=95 мм
Основные размеры червячного колеса:
X=-0.6 мм da2=(Z2+2+2X)m=(36+2-2*0.6)12.5=460 мм
Z2=36 df2=(Z2-2.4+2X)m=(36-2.4-2*0.6)12.5=405 мм
dfМ1 da2+1.5m=460+1.5*12.5=478.75 мм
Принимаем daM1=479 мм
b 2 0.75da1=0.75*150=112.5 мм
По табл. 6 назначаем 8-ю степень точности (в зависимости от Vs=6.3 мс)
По табл.7 =1022 (среднее значение при Vs=7 мс)
Проверяем прочность по контактным напряжениям:
При этом Кv=1.15 (при Vs3 мс) и Кв=1 (при постоянной нагрузке)
Прочность соблюдается отклонение 9 % считается допустимым т.к. при стандартных m и q не всегда можно получить близкие и .
Определение сил в зацеплении
Окружная сила определяется по формуле:
Радиальная сила находится по формуле:
Консольные силы на муфте червяка находим по формуле:
Консольные силы на муфте колеса находим по формуле:
Проектный и проверочный расчет
1 Определение размеров ступеней валов
Таблица 5.1 – Размеры ступеней валов
где dдв. – диаметр выходного конца вала ротора двигателя
где []k – допустимое касательное напряжение []k=20 Нмм2 (стр. 107 [1])
где l1 – длина конца вала под полумуфту
где t – высота буртика t =3.5 для
где r – фаска подшипника r = 3.5 .
где r = 35 при . Принимаем d3 = 85мм
Определяем графически мм
Определяем графически
определяем графически
2 Расчетная схема червяка
Червяк изготавливаем из стали 40Х азотированной с МПа и МПа.
Определение реакций в местах посадки подшипников.
Рисунок 3 – Эпюры изгибающих и крутящих моментов вала-червяка
Вертикальная плоскость (ось у).
Определяем опорные реакции:
-1260+154368-283.68=0
Строим эпюру изгибающих моментов относительно оси х: .
Горизонтальная плоскость (ось х).
Строим эпюру изгибающих моментов относительно оси у:
Строим эпюру крутящих моментов.
Строим эпюру изгибающих моментов.
Во втором сечении: .
В третьем сечении: .
В первом и четвертом сечении: .
3 Расчетная схема колеса
Вал изготовлен из Стали45 улучшенной с МПа и МПа.
Рисунок 4 – Эпюры изгибающих и крутящих моментов вала колеса
Строим эпюру изгибающих моментов относительно оси х: ; ; ; ; ;
80-4288-12067+7775=0
Строим эпюру изгибающих моментов относительно оси у: ; ; ; ; ;
Строим эпюру крутящих моментов (ЭТ2).
во втором сечении в третьем сечении определяем по формуле (5.13):
Подбор и расчет подшипников
1 Подбор и расчет подшипников червяка
Дано: d = 60 мм Н 1 = 150 с-1.
Пригодность подшипников определяется сопоставлением расчетной динамической грузоподъемности СГР Н и базовой СГ Н по условию СГР СГ.
Расчетная динамическая грузоподъемность определяется по формуле:
где FE – эквивалентная динамическая нагрузка;
Ln – требуемая долговечность подшипника Ln = 12000 ч (табл. 9.4 [1]);
m – показатель степени m = 3.33 – для шариковых радиально-упорных подшипников;
– угловая скорость вращения вала.
Эквивалентная динамическая нагрузка определяется:
где Fa – осевая нагрузка подшипника;
Fr – радиальная нагрузка подшипника;
е – коэффициент влияния осевого нагружения е = 0.30;
V k kT – постоянные составляющие k = 1.2 (табл. 9.4 [1]) v = 1 – при вращающемся внутреннем кольце (табл. 9.1 [1]) kT = 1.1 при рабочей температуре до 150 С (табл. 9.5 [1]);
Y – коэффициент осевой нагрузки Y = 1.97;
Х – коэффициент радиальной нагрузки = 0.4 (табл. 9.1 [1]).
Предварительно выбираем подшипник роликовый конический однорядный №7312 у которого d = 60 мм D = 130 мм В = 31 мм r = 3 мм r1 = 12 мм СГ = 118 кН
Определяем осевые составляющие радиальной нагрузки и .
Определяем осевые нагрузки подшипников из условия равновесия (тал. 9.6 [1]).
Пользуясь формулами (6.2) и (6.3) находим и соответственно:
На обоих концах вала ставим подшипники №7312 враспор.
2 Подбор и расчет подшипников тихоходного вала
Дано: d = 70 мм Н 2 = 6 с-1.
Расчетную грузоподъемность определяем по формуле (6.1). Ln = 12000 ч.
Предварительно выбираем подшипник роликовый конический однорядный №7215 у которого d = 70 мм D = 125 мм Т = 265 мм b = 26 мм c = 21 мм r = 2.5 мм r1 = 0.8 мм СГ = 959 кН Сor = 821 кН е = 0.37 Y = 1.62 Y0 = 0.89.
Пользуясь формулами (6.2) и (6.3) находим и :
Определяем динамическую грузоподъемность по большему значению эквивалентной нагрузки:
На обоих концах тихоходного вала ставим подшипники №7215 враспор.
Проверочный расчет валов
1 Проверочный расчет вала-червяка
Определяем запасы сопротивления усталости в опасных сечениях. Во втором сечении.
Дано: ; d = 60 мм; Tk = 67000 .
Напряжение изгиба находим по формуле:
где WИ – осевой момент сопротивления сечения вала мм3.
Касательные напряжения:
где Тk – крутящий момент на валу;
Wр – полярный момент сопротивления сечения вала мм3.
Запас усталости сопротивления по изгибу:
Запас сопротивления усталости по кручению:
где - пределы выносливости МПа МПа
- амплитуды переменных составляющих циклов нагружений;
- постоянные составляющие ;
- коэффициенты корректирующие влияние постоянной составляющей цикла напряжений на сопротивление усталости и для среднеуглеродистой стали;
- эффективные коэффициенты концентрации напряжений при изгибе и кручении определяются по табл. 11.3 [1] (табл. 11.4 [1]);
- составляющие коэффициенты находим по (табл.15.1[2]) .
Запас сопротивления усталости находим по формуле:
где [S] – допускаемое значение запаса прочности. [S] = 1.3 2. Принимаем [S] = 2.
Во втором сечении прочность на усталость обеспечена.
В третьем сечении запас сопротивления усталости находим как и для второго сечения.
Дано: ; d = 72 мм; Tk = 67000 .
По формуле (7.8) находим = 377 МПа.
По формуле (7.7) находим МПа = .
Используя (7.5) и (7.6) находим и .
Запас сопротивления усталости находим по формуле (7.9):
В третьем сечении прочность на усталость обеспечена.
Проверка статической прочности при перегрузках.
МПа МПа. Тогда по (7.15) находим:
По формулам (7.14) и (7.15) находим и
Проверка показала что прочность вала в опасных сечениях обеспечена.
2 Проверочный расчет червячного ведомого вала
Находим запас сопротивления усталости во втором сечении.
Дано: ; d2 = 70 мм; Tk = .
Напряжение изгиба находим по формуле (7.1) используя (7.2) для определения WИ.
Касательные напряжения находим по формуле (7.3) используя (7.4) для нахождения Wр.
По формуле (7.8) находим = 2856 МПа.
Во втором сечении ведомого колеса прочность на усталость обеспечена.
Находим запас сопротивления усталости в третьем сечении.
Дано: ; d3 = 64.6 мм; Tk = 448900 .
По формуле (7.8) находим = = 16.5 МПа.
Запас сопротивления усталости в третьем сечении обеспечен.
Прверка статической прочности при перегрузках в опасных сечениях:
По формулам (7.10) и (7.11) находим и зная что и .
Проверка показала что прочность тихоходного вала в опасных сечениях обеспечена.
Проверочный расчет шпоночных соединений
Запишем условие прочности:
где Ft – окружная сила на червяке или колесе;
Асм – площадь смятия;
см – допускаемое напряжение смятия см = 150 Нмм2.
h t1 – стандартные размеры шпонки.
где l – полная длина шпонки
Рисунок 5 – Эскиз шпоночного соединения
1 Проверочный расчет шпонки под колесом
По формуле (8.3) находим lp заранее находя параметры h t1 l и b (табл. К42 [1]) h=11мм b = 18 мм t1 = 7мм l = 67 мм. Ширину шпонки для обеих ступней вала принимаем одинаковой исходя из меньшего диаметра для удобства обработки.
lp = 67 – 18 = 49 мм
По формуле (8.2) находим площадь смятия:
Прочность шпонки обеспечена.
2 Проверочный расчет шпонки на тихоходном валу
Используя формулы (8.1) (8.2) и (8.3) ведем расчет шпонки заранее определив (табл. К42 [1]) h = 9 мм b = 12 мм t1 = 55 мм l = 39 мм.
Прочность шпонки обеспечена
3 Проверочный расчет шпонки на быстроходном валу
Используя формулы (8.1) (8.2) и (8.3) ведем расчет шпонки заранее определив (табл. К42 [1]) h = 7 мм b = 8 мм t1 = 4 мм l = 22 мм = 1600 Н.
Тепловой расчет редуктора
При работе редуктора потери мощности вызванные трением в зацеплении и в подшипниках перемешиванием и разбрызгиванием масла приводят к нагреву деталей редуктора и масла. При нагреве вязкость масла резко падает что приводит к нарушению режима смазывания. Нормальная работа редуктора будет обеспечена если температура масла не превысит допускаемой.
Температура масла в редукторе при работе находится по формуле:
где tB – температура окружающей среды tB = 20° С;
Р1 – мощность на быстроходном валу редуктора Р1 = 4 кВт;
– КПД редуктора = 082;
А – площадь теплоотдачи поверхности корпуса редуктора А = 04 (таблица 11.6 );
kt – коэффициент теплоотдачи kt = 9 17 Втм2 град.
Температура масла в работающем редукторе не превышает допускаемого значения перепад температур между маслом и окружающим воздухом не превышает допустимый.
Увеличивать теплоотдающую поверхность охлаждающими ребрами не требуется.
Назначение квалитетов точности шероховатости поверхности отклонений формы и взаимного расположения поверхностей
Выбор допусков посадок и шероховатости поверхности проводим приняв что детали редуктора изготавливаются по нормальной относительной точности размеров [3]. При выборе руководствуемся стандартным рядом параметров шероховатости. Выбираем посадку червячного колеса на вал прессованную (H7r 6). Выбранные значения параметров приведены в таблица 5.
Таблица 10.1 - Параметры точности и шероховатости
Наименование соединения поверхности
Соединение зубчатого колеса с валом
Поверхность вала под подшипниками
Поверхность корпуса для посадки подшипников
Поверхность заплечиков вала
Поверхность выходного конца вала
Посадочная поверхность торцевых крышек
Поверхность червяка под подшипниками
Поверхность выходного конца быстроходного вала
Все остальные обрабатываемые поверхности
Поверхности получаемые литьем
Определение размеров основных элементов редуктора
Корпус редуктора служит для размещения и координации деталей передачи защиты их от загрязнения организации системы смазки а также восприятия сил возникающих в зацеплении редуктора пары подшипниках. Способ изготовления корпуса – литье из серого чугуна (СЧ15СЧ20).
Корпуса червячных редукторов с aw > 140 мм. может быть выполнен разъемным.
Форма корпуса определяется в основном технологическими эксплуатационными и эстетическими условиями с учетом его прочности и жесткости. Этим требованиям удовлетворяют корпуса прямоугольной формы с гладкими наружными стенками без выступающих конструктивных элементов подшипниковые бобышки и ребра внутри стяжные болты только по продольной стороне корпуса в нишах крышки подшипниковых узлов преимущественно врезные фундаментные лапы не выступают за габариты корпуса
В проектируемом редукторе толщины стенок крышки и основания корпуса принимаем одинаковыми:
Фланцы предназначены для соединения корпусных деталей редуктора.
Фундаментальный фланец основания корпуса предназначен для крепления редуктора к фундаментальной раме. Опорную поверхность фланца выполняем в виде двух длинных параллельно расположенных платиков. Ширина опорной поверхности платиков находится по формуле
где d01 – диаметр крепежного болта принимаем d01 = 18 мм;
- толщина стенок корпуса редуктора.
Фланец подшипниковой бобышки крышки и основания корпуса предназначен для соединения крышки и основания разъемных корпусов. Фланец расположен в месте установки стяжных подшипниковых винтов на продольных сторонах корпуса: в крышке наружу от ее стенки в основании – внутрь от стенки.
Подшипниковые стяжные винты выбираем диаметром мм (табл. 10.17 ). Количество стяжных винтов вбираем по конструктивным соображениям в зависимости от размеров продольной стороны редуктора.
Фланец для крышки смотрового окна. Размеры сторон фланца количество винтов и расстояние между ними устанавливаем конструктивно в зависимости от места расположения окна высоту фланца принимаем равной 3 мм.
Установочные штифты предназначены для фиксации крышки и основания корпуса при их совместной обработке. Диаметр шрифтов выбираем из соотношения:
dшт. = 0.7 d3 (11.3)
где d3 – диаметр стержня соединительных винтов d3 = d2 = 8 мм.
Опорные платики. Для прикрепления к корпусу сливных пробок на основании корпуса выполяем опорные платики высоту платиков принимаем равной 7 мм.
Выбираем винты для разъединения крышки и основания корпуса после длительного срока эксплуатации т.к. уплотняющее покрытие склеивает их. В качестве отжимных винтов выбираем винты М8.
Для подъема и транспортировки крышки корпуса и собранного редуктора выполняем проушины в виде ребра с отверстием отливая их заодно с крышкой. Диаметры проушин выбираем конструктивно.
Выбор системы назначение сорта и количества смазки зацепления и подшипников
Для данного редуктора с окружными скоростями 10 мс выбираем смазывание жидким маслом картерным непроточным способом (окунанием). По табл. 10.29 выбираем сорт масла И–Т–Д–100 где И – индустриальное; Т – для тяжелых нагруженных узлов; Д – масло с антиокислительными антикоррозионными противоизносными и противозадирными присадками 100 – класс кинематической вязкости.
Для одноступенчатых редукторов при смазывании окунанием объем масляной ванны определяют из расчета 04 08 л масла на 1 кВт передаваемой мощности. Выбираем объем масла:
где h – высота уровня масла h = 33 мм;
а – длина редуктора а = 200 мм;
b – ширина редуктора b = 128 мм.
При вращении червяка масло будет увлекаться парой маслоразбрызгивателей установленными на нём и разбрызгиваться попадая на внутренние стенки корпуса откуда будет стекать в нижнюю его часть. Внутри корпуса образуется взвесь частиц масла в воздухе которым покрываются поверхности расположенных внутри корпуса деталей в том числе и подшипники.
Контроль уровня масла производится жезловым маслоуказателем. Для слива масла предусмотрена сливная пробка. Заливка масла в редуктор производится через съемную крышку.
Для вала-червяка и для вала червячного колеса выберем манжетные уплотнения по ГОСТ 8752-79. Установим их рабочей кромкой внутрь корпуса так чтобы обеспечить к ней хороший доступ масла.
Описание технологии сборки редуктора и регулировки его основных узлов
Перед сборкой внутреннюю полость редуктора покрыть маслостойкой краской МЛ-158. Сборку производят в соответствии со сборочным чертежом редуктора.
Стаканы устанавливают в крышку корпуса. На червячный вал со стороны противоположной концу вала под муфту устанавливают первый подшипник. Червяк устанавливают в корпус и запрессовывают подшипник. С обоих концов вала-червяка ставятся регулировочно-торцовые крышки и фиксируются к корпусу винтами соблюдая нужную регулировку подшипников. Далее на вал-червяк устанавливают шпонку. Закручивают винт и надевают кольцо.
В тихоходный вал закладывают шпонку и насаживают червячное колесо. Затем с одной стороны вала устанавливают распорное кольцо и с обоих концов вала запрессовывают подшипники качения. Со стороны муфты устанавливают регулировочную шайбу и регулировочный винт вкрученный предварительно во врезную крышку. Вал с регулировочной шайбой и врезной крышкой с вкрученным в нее регулировочным винтом устанавливают в основание корпуса редуктора. Далее устанавливают крышку редуктора предварительно покрыв место контакта крышки и основания корпуса редуктора герметиком В20-1. Для центровки крышки устанавливают штифты. Затягивают винты крепящие крышку корпуса редуктора к основанию. Выполняют регулировку подшипников и зацепления редуктора. Для этого колесо смазывают специальной черной краской прокручивают валы и по пятну контакта определяют характер сцепления червяка с колесом. Производят регулировку зацепления путем смещения колеса в осевом направлении. В основание корпуса вворачивают пробку и вставляют жезловый маслоуказатель. Заливают масло в корпус и устанавливают крышку-отдушину.
Список использованной литературы
) Шейнблит А.Е. Курсовое проектирование деталей машин: Учеб. пособие для техникумов.- М.: Высш. школа. 1991 – 432 с. ил.
) Иванов М.Н. Детали машин: Учебник для машиностр. спец. вузов. – 4-е изд. перераб. – М.: Высш. школа 1984 – 336 с. ил.
) Дунаев П.Ф. Леликов О.П. Конструирование узлов и деталей машин: Учеб. пособие для техн. спец. вузов. - М.: Высш. шк. 2000 – 447 с. ил.
) Беляев В.Н. Богатырев И.С. Буланже А.В. и др. Под ред. Решетова Д.Н. Детали машин: Атлас конструкций. Уч. пособие для машиностроительных вузов. - М.: Машиностроение 1979 – 367 с. ил.