Привод ленточного транспортёра с одноступенчатым цилиндрическим редуктором с косозубой передачей внутреннего зацепления




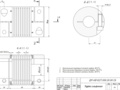

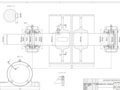
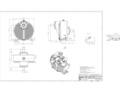
- Добавлен: 04.11.2022
- Размер: 13 MB
- Закачек: 1
Описание
Состав проекта
![]() |
![]() ![]() ![]() ![]() |
![]() ![]() ![]() |
![]() |
![]() ![]() ![]() ![]() |
![]() ![]() ![]() ![]() |
![]() |
![]() ![]() ![]() ![]() |
![]() ![]() ![]() ![]() |
![]() ![]() ![]() ![]() |
![]() ![]() ![]() |
![]() ![]() ![]() ![]() |
Дополнительная информация
Приводной вал.dwg

Приводной вал с барабаном
ДМ АВЧ227.000.50.00 СБ
АВЧ227 РПЗ.docx
Факультет «Робототехника и комплексная автоматизация»
Кафедра «Основы конструирования машин»
Пояснительная записка
к курсовому проекту на тему:
«Привод ленточного транспортёра с одноступенчатым цилиндрическим редуктором с косозубой передачей внутреннего зацепления»
ДМ АВЧ227.01.00.00 ПЗ
Студент: Терентьев Ю. А. Э5-61 ФИО и номер группы
Консультант проекта: Чиркин А. В.
Подпись консультанта
Техническое задание4
Кинематический расчет привода5
1 Подбор электродвигателя5
2 Уточнение передаточных чисел привода7
Расчет зубчатой передачи на ЭВМ7
1 Приближенные значения диаметров валов10
2 Расстояния между деталями передач11
3 Выбор типа подшипников11
4 Конструирование зубчатого колеса внешнего зацепления быстроходной ступени12
5 Конструирование корпуса13
6 Расчет собственных колебаний корпуса редуктора13
Уточненные расчеты узлов редуктора16
1.1 Уточненный расчет подшипников16
2 Расчет валов на прочность20
3 Расчет шпоночных соединений23
Расчет сконструированной муфты24
Выбор смазки редуктора24
Список использованных источников26
Целью курсового проекта является проектирование привода ленточного транспортера. Составными частями привода являются электродвигатель одноступенчатый цилиндрический редуктор две сильфонные муфты приводной вал с барабаном.
Принцип действия привода следующий: вращающий момент передается с электродвигателя на входной вал редуктора через сильфонную муфту; с выходного вала редуктора на приводной вал с барабаном присоединенного к приводу через еще одну сильфонную муфту.
Требуется выполнить необходимые расчеты выбрать наилучшие параметры схемы редуктора и разработать конструкторскую документацию предназначенную для изготовления привода:
- чертеж общего вида привода;
- сборочный чертеж редуктора;
- чертежи деталей редуктора;
- сборочный чертеж упругой муфты;
- чертеж приводного вала;
- расчетно-пояснительную записку и спецификации;
Кинематический расчет привода
1 Подбор электродвигателя
Для выбора электродвигателя определяю требуемую мощность. Для этого находим общий КПД:
Где – КПД цилиндрической передачи – КПД муфты – КПД опор приводного вала (см. [1] табл. 1.1)
Находим потребляемую мощность привода:
Где Н – окружная сила; мc – скорость ленты. (техническое задание).
Мощность электродвигателя:
Частота вращения приводного вала:
Где мм – диаметр барабана. (техническое задание)
Предварительные значения частот вращения вала электродвигателя:
– передаточное число цилиндрической передачи (см. [1] табл. 1.2)
Выбираем частоту вращения вала электродвигателя
По полученным значениям требуемых мощности и частоты электродвигателя выбираем двигатель АИР160S8727 с номинальной мощностью 75 кВт. (Рис. 1.)
Рис. 1. Электродвигатель АИР 160S8 исполнение IM1081
Таблица 1. Габаритные установочные и присоединительные размеры электродвигателя АИР 160S8
2 Уточнение передаточных чисел привода
Общее передаточное число редуктора:
Вращающий момент на тихоходной ступени редуктора:
Расчет зубчатой передачи на ЭВМ
Данные необходимые для расчета зубчатой передачи на ЭВМ (рис 2.1):
Вращающий момент на тихоходном валу:
Частота вращения тихоходного вала:
Ресурс: (техническое задание)
Режим нагружения: II (техническое задание)
Передаточное отношение редуктора:
Рис. 2.1 Исходные данные механизма для расчета на ЭВМ
На основе произведённого расчёта и технических требований в пакете прикладных программ ПДМ (проектирование деталей машин) был произведён проектный расчёт:
- цилиндрического одноступенчатого редуктора с внутренним косозубым зацеплением.
Расчёт проводился в два этапа:
На первом определялись возможные проектные решения и определялись основные показатели качества необходимые для выбора рационального варианта: твёрдость рабочих поверхностей зубьев колёс межосевое расстояние (необходимо меньшее в связи с ограничениями по габаритам редуктора) масса механизма и колёс.
На втором этапе для выбранного варианта были получены все расчётные параметры требуемые для дальнейших этапов проектирования.
Для цилиндрического одноступенчатого редуктора с внутренним косозубым зацеплением был выбран вариант со II-ым способом термической обработки (улучшение и закалка ТВЧ шестерни и улучшение колеса) и наименьшими для этого способа термической обработки межосевым расстоянием - 95 мм и массой механизма - 31 кг (вариант 6).
Характеристики передаточных механизмов вынесены в приложение 1.
Определим материал шестерни и колеса. Так как был выбран вариант со II-ым способом термической обработки (улучшение и закалка ТВЧ шестерни и улучшение колеса) и исходя из того что на поверхностях шестерни и колеса были получены твёрдости 49 и 285 HRCэ соответственно по таблице 2.1 [1 стр. 15] (предельные размеры заготовки) а также по марочнику сталей В.Г. Сорокина [3] была определена марка стали: 40ХН.
Результаты полученные в ходе вычисления на ЭВМ (рис. 2.2):
Рис 2.2 Результаты расчёта механизма
1 Приближенные значения диаметров валов
Вращающие моменты на валах:
Предварительные значения диаметров различных участков стальных валов редуктора с 45 [2].
Принимаем согласно нормальным линейным размерам (ГОСТ 6636-69).
Для быстроходного вала: высота заплечика ; координата фаски ; размер фаски .
Для тихоходного вала: высота заплечика ; координата фаски ; размер фаски .
2 Расстояния между деталями передач
Чтобы поверхности вращающихся колёс не задевали за внутренние поверхности стенки корпуса между ними оставляют зазор а мм
Тогда расстояние между внешними поверхностями деталей передач:
Минимальный зазор между поверхностями вращающихся колёс и внутренними поверхностями стенки корпуса [1 стр. 56]:
Минимальное расстояние между дном корпуса и поверхностью колеса:
3 Выбор типа подшипников
Цилиндрические колеса должны быть зафиксированы в осевом направлении. Для опор валов применяют шариковые подшипники.
Предварительно назначаю шариковые радиальные однорядные подшипники с двусторонним уплотнением (рис. 3.1) для валов редуктора
Для быстроходного вала – подшипник 180208 ГОСТ 8882-75.
Для тихоходного вала – подшипник 180209 ГОСТ 8882-75.
Рис. 3.1 Подшипник шариковый радиальный однорядный с двусторонним уплотнением ГОСТ 8882-75
Таблица 3.3 Размеры и характеристика шарикового однорядного подшипника с двусторонним уплотнением (см. табл. 20.1.6 [2])
4 Конструирование зубчатого колеса внешнего зацепления быстроходной ступени
При серийном производстве заготовки колес получают из прутка свободной ковкой а также ковкой в штампе. При годовом объеме выпуска более 50экономически оправдана ковка в простейших односторонних прокладных штампах.
Так как в технических требованиях указан объем выпуска в 1000в год то целесообразно применить двусторонние штампы.
Расчёт геометрических параметров колеса (см. гл.5.2 [1]). Ширина зубчатого венца без канавки из условия Длина ступицы считается по следующей формуле:
Ширина торцов зубчатого венца:
Размер паза под шпону:
Размер фасок принимаем . Размер штамповочного уклона Примем
Материал колеса Сталь 40ХН.
5 Конструирование корпуса
Корпусная деталь состоит из стенок ребер бобышек фланцев и других элементов соединенных в единое целое. При конструировании корпусной литой детали стенки рекомендуется по возможности выполнять одинаковой толщины. Толщину стенок литых деталей уменьшают до величины определяемой условиями хорошего заполнения формы жидким металлом. Поэтому чем больше размеры корпуса тем толще должны быть его стенки. Материал корпуса – серый чугун. Толщина стенки для чугунных отливок отвечающая требованиям технологии литья необходимой прочности и жесткости корпуса рассчитывается по следующей формуле (см. стр. 289 [1]):
Принимая во внимание рекомендуемую толщину стенки корпуса от приведённого габарита принимаем толщину стенки корпуса .
При проектировании редуктора следует все выступающие элементы устранить с наружных поверхностей и ввести внутрь корпуса. Это обеспечит большую жесткость и лучшие вибро-акустические свойства.
6 Расчет собственных колебаний корпуса редуктора
Теоретические и экспериментальные исследования приводов и в частности тяговых редукторов показывают что главной причиной этих разрушений являются резонансные колебания элементов привода.
Возмущающими факторами являются периодические воздействия от
работы изношенного зубчатого зацепления дисбалансы вращающихся частей. Функции распределения скоростей движения по участкам обращения
показывает что имеются зоны наиболее вероятных скоростей движения в
которых нежелательны резонансные явления в узлах привода.
Элементами наиболее подверженными резонансным колебаниям
(вибрациям) являются корпус редуктора. Тонкостенная конструкция с малым
внутренним демпфированием имеет большое количество собственных частот
колебаний с зонами их «сгущений» которые как показывает практика
сосредоточены в зонах эксплуатационных скоростей движения.
Собственную частоту корпуса можно найти по известной формуле:
Чтобы найти прогиб корпуса зададим нагрузку в 1000Н закрепим лапы корпуса и установим датчик на дне цилиндрического корпуса. В результате моделирования датчик покажет прогиб корпуса под воздействием нагрузки. Результат моделирования представлен на рис. 3.6. Прогиб корпуса редуктора под воздействием силы в 1000Н составил =005567 мм.
Рис. 3.6 Прогиб (смещение по оси Y) корпуса редуктора под воздействием силы в 1000Н
Частота электродвигателя равна:
Так как то такая конструкция корпуса не подвержена резонансным колебаниям. Следовательно такая конструкция корпуса вполне удовлетворяет нашим требованиям.
Уточненные расчеты узлов редуктора
1.1 Уточненный расчет подшипников
Основными нагрузками на валы являются силы от передач. Силы на валы передают через насаженные на них детали: зубчатые или червячные колес шкивы звездочки и тд. Силы в зацеплении пкосозубой цилиндрической передачи изображены на рисунке 4.1.
Рис. 4.1 Силы в зацеплении косозубой цилиндрической передачи
Для опор валов косозубых колес редукторов применяют чаще всего шариковые радиальные подшипники. Первоначально назначают подшипники серии диаметров 2. Если при последующем расчете грузоподъемность подшипника окажется недостаточной то используют подшипники серии 3.
Рис. 4.4 Силы и реакции на приводном валу.
Сила натяжения ленты:
Номинальный крутящий момент муфты:
Подшипник 53510 ГОСТ 24696-81:
Найдем реакции в опорах от действия сил в зацеплении:
Суммарные реакции опор в плоскости перпендикулярной валу:
Найдем реакции опор от действия муфты:
Радиальная жесткость сильфонной муфты:
Радиальная сила на валу от упругой муфты:
где - радиальное смещение вала.
Максимальные реакции опор (при совпадении векторов и ):
Для типового режима нагружения II коэффициент эквивалентной нагрузки:
Вычисляем эквивалентные нагрузки:
Очевидно что первый подшипник более нагружен поэтому дальнейший расчет будем вести для него.
Предварительно назначим роликовые радиальные двухрядные подшипники второй серии диаметров.
Найдем коэффициент осевого нагружения:
Так как отношение где коэффициент вращения (равен 1 при вращении внутреннего кольца) принимаем
Принимаем (коэффициент безопасности) (коэффициент температуры)
Эквивалентная динамическая осевая нагрузка:
Расчетный скорректированный ресурс подшипника при (обычные условия применения) k=103 (роликовый подшипник)
Найдем максимальную эквивалентную динамическую нагрузку:
Так как расчетный ресурс больше требуемого и выполнено условие 05то предварительно назначенный подшипник 53510 пригоден.
2 Расчет валов на прочность
Рис. 4.6Эпюры внутренних силовых факторов.
Воспользуемся значениями сил и реакций полученными в пункте 4.1.4:
Опасными сечениями являются I II III так как в них максимальны силовые факторы. I сечение дополнительно ослаблено зубьями шестерни. III сечение ослаблено шпоночным пазом.
Определим внутренние силовые факторы в опасных сечениях:
Суммарный изгибающий момент:
Изгибающие моменты:
Определение геометрических характеристик сечений:
Момент сопротивления при изгибе:
Момент сопротивления при кручении:
Расчет вала на статическую прочность:
Найдем напряжения изгиба и кручения:
Частные коэффициенты запаса прочности:
Общий предел запаса прочности по пределу текучести:
Найдем напряжения кручения:
коэффициенты запаса прочности:
Статическая прочность вала обеспечена во всех опасных сечениях
3 Расчет шпоночных соединений
Рис. 4.6. Шпонка призматическая (ГОСТ 23360-78)
Тихоходный вал (соединение вала и зубчатого колеса):
Размеры призматической шпонки (ГОСТ 23360-78) для диаметра вала: Для стальной неподвижной шпонки принимаем: .
Глубина врезания шпонки в ступицу:
Определим рабочую длину шпонки:
где - вращающий момент на тихоходном валу.
Полная длина шпонки:
По ряду длин шпонок выбираем
Расчет сконструированной муфты
Сильфонную муфту на быстроходном и тихоходном валу выбираем по вращающим моментам на валах. Для быстроходного вала выбрана сильфонная муфта с номинальным моментом 80 Н*м с максимальным моментом 160 Н*м. Для тихоходного вала выбрана сильфонная муфта WK-4Е с номинальным вращающим моментом 500 Н*м с максимальным вращающим моментом 900 Н*м.
Выбор смазки редуктора
Для уменьшения потерь мощности на трение и снижения интенсивности износа трущихся поверхностей а также для предохранения их от заедания коррозии и лучшего отвода теплоты трущиеся поверхности деталей должны иметь надежную смазку. Для смазывания передач широко применяют картерную систему. В корпус редуктора заливают масло так чтобы венцы колес были в него погружены. Колеса при вращении увлекают масло разбрызгивая его внутри корпуса. Масло попадает на внутренние стенки корпуса откуда стекает в нижнюю его часть. Внутри корпуса образуется взвесь частиц масла в воздухе которая покрывает поверхность расположенных внутри корпуса деталей. Принцип назначения сорта масла следующий: чем выше окружная скорость колеса тем меньше должна быть вязкость масла и чем выше контактные давления в зацеплении тем большей вязкостью должно обладать масло. Поэтому требуемую вязкость масла определяют в зависимости от контактного напряжения и окружной скорости колес. Важно обеспечить надежную смазку тихоходной ступени поэтому расчет ведется по большему из напряжений.
для данных параметров рекомендуемая кинематическая вязкость масла (см. [1] табл. 11.1 ): 34
Подшипники самосмазывающиеся.
Выбираем марку масла: И-Г-А-32 ГОСТ 20799-88.
Г – для гидравлических систем
А – масло без присадок
– класс кинематической вязкости
Список использованных источников
Дунаев П.Ф. Конструирование узлов и деталей машин : учеб. пособие для студ. высш. учеб. заведений П.Ф. Дунаев О.П. Леликов. 13-е изд. испр. и доп. М.: Издательство МГТУ им. Н.Э. Баумана 2017. 564 с.
Атлас конструкций узлов и деталей машин : учеб. пособие [Б. А. Байков и др.] ; под ред. О. А. Ряховского О. П. Леликова. 2-е изд. перераб. и доп. М. : Изд-во МГТУ им. Н. Э. Баумана 2009. 400 с. : ил.
Муфта.dwg

Максимальный крутящий момент муфты: 160 Н*м
Максимальный момент затяжки винта: 28 Н*м
МГТУ им. Н. Э. Баумана
ДМ АВЧ227.000.20.00 СБ
Общий вид редуктора.dwg

внутреннего зацепления
Цилиндрический редуктор с
ДМ АВЧ227.000.30.00СБ
Loctite 510 при окончательной сборке
Плоскость разъема покрыть тонким слоем герметика
Технические требования
Коэффициент полезного действия: 0
Общее передаточное число: 4
Частота вращения выходного вала: 145
Вращающий момент на выходном валу: 357
Техническая характеристика
Тихоходный вал.dwg

Сталь 45Х ГОСТ 8479-70
Общие допуски по ГОСТ 30893.2-mK
кроме места указанного особо
Редуктор.dwg

Привод ленточного транспортёра.dwg

на приводном валу: 2362
на тихоходном валу: 2362
на быстроходном валу: 745
Радиальная консольная сила:
Допустимые смещения валов:
Номинальная частота вращения электродвигателя 750 обмин
Номинальная мощность электродвигателя 7
Общее передаточное число привода: 4
Скорость движения ленты 2
Окружная сила на барабане 2
Техническая характеристика
МГТУ им. Н. Э. Баумана
ДМ АВЧ227.000.00.00 ВО
Технические требования
Схема расположения опорных поверхностей привода
Крышка привертная правая.dwg
Неуказанные радиусы 2 мм max.
Неуказанные литейные уклоны 1°.
МГТУ им. Н. Э. Баумана
Колесо зубчатое.dwg

Сталь 40ХН ГОСТ 8479-70
Общие допуски по ГОСТ 30893.2-mk
Радиусы округлений 1 мм max.
Коэффициент смещения
Нормальный исходный
Направление линии зуба
Рекомендуемые чертежи
- 24.01.2023
- 18.04.2023
- 18.02.2025
- 25.10.2022
- 15.02.2021