Привод ленточного конвейера с цилиндрическим соосным редуктором и цепной передачей




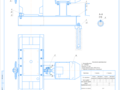
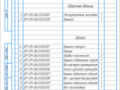
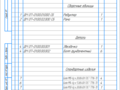
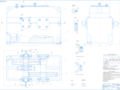
- Добавлен: 24.01.2023
- Размер: 3 MB
- Закачек: 0
Описание
Привод ленточного конвейера с цилиндрическим соосным редуктором и цепной передачей
Состав проекта
![]() |
![]() |
![]() ![]() ![]() ![]() |
![]() ![]() ![]() ![]() |
![]() ![]() ![]() |
![]() ![]() ![]() ![]() |
![]() ![]() ![]() ![]() |
![]() ![]() ![]() ![]() |
Дополнительная информация
Редуктор.cdw

едуктор цилиндрический
Техническая характеристика
Редуктор цилиндрический двухступенчатый соосный:
Способ смазки зацепплений - картерный
Общее передаточное число редуктора - 20
Частота вращения выходного вала редуктора - 126
Вращающий момент на выходном валу редуктора - 114
Технические требования
В редуктор залить масло И-Г-А-32 в объёме 3 литров.
Редуктор подвергнуть обкатке в течении 2 часов до получения
необходимого пятна контакта
- В первой ступени по высоте не менее 40
по длине не менее 50
- Во второй ступени по высоте не менее 40
по длине не менее 50.
Во время обработки не должно быть течи масла через
уплотнения и разъём редуктора.
Редуктор должен работать плавно
должен превышать 80 дБ (ГОСТ12.1.003-83).
Нагрев подшипников свыше 70
Боковые зазоры в передачах
Подшипник условно не показан
Вал.cdw

Неуказанные редельные отклонения размеров: валов- h12
Пояснительная записка.docx
высшего профессионального образования
«Сибирский Федеральный Университет»
Кафедра: «Проектирование и экспериментальная механика машин»
по дисциплине «Детали машин и основы конструирования»
тема: «Проектирование привода ленточного транспортера»
ПОЯСНИТЕЛЬНАЯ ЗАПИСКА
Кинематический расчет .
1 Выбор электродвигателя ..
2 Расчет передаточного числа привода и разбивка по ступеням
3 Расчет крутящих моментов на всех валах привода
Расчет ступеней соосного цилиндрического зубчатого редуктора..
Расчет цепной передачи .
Определение геометрических параметров валов
2 Промежуточный вал .
Конструирование зубчатого колеса внешнего зацепления
Расчет посадки с натягом для колеса выходного вала
Проверочный расчет быстроходного вала по запасу выносливости
Проверочный расчет шпонки
Расчет болтов крепления цилиндрического редуктора к раме ..
1 Расчет болтов по условию не раскрытия стыка ..
2 Расчет болтов крепления по условию отсутствия сдвига ..
Расчет конструктивных элементов редуктора .
1 Конструирование крышки подшипника ..
2 Расчет стенок корпуса
3 Конструктивное оформление внутреннего контура редуктора .
4 Конструктивное оформление приливов для подшипниковых гнезд .
5 Крепление крышки редуктора к корпусу .
6 Фиксирование крышки относительно корпуса
7 Конструктивное оформление опорной части корпуса
8 Оформление сливных отверстий ..
9 Оформление прочих конструктивных элементов корпусных деталей .
Конструирование рамы ..
Смазывание зубчатых зацеплений и подшипников
Библиографический список
Целью данного курсового проекта является освоение навыков расчёта и конструирования основных видов механизмов предназначенных для передачи и преобразования крутящего момента.
Выполнение курсового проекта по деталям машин способствует закреплению знаний полученных при изучении общетехнических дисциплин. Тематика курсового проекта должна иметь вид комплексной инженерной задачи включающей кинематические и силовые расчёты выбор материалов и расчёты на прочность вопросы конструирования и выполнения конструкторской документации в виде габаритных сборочных и рабочих чертежей а также давление спецификации.
В данном курсовом проекте приведён пример проектирования привода транспортёра. В него входят подбор электродвигателя проектирование и расчёт цилиндрического двухступенчатого редуктора а так же проектирование самого привода в сборе.
Привод – устройство приводящее в движение машину или механизм; состоит из источника энергии передаточного механизма и аппаратуры управления.
Соединение вала машины с валом электродвигателя возможно лишь в относительно редких случаях когда частоты вращения этих валов одинаковы. Если это условие не соблюдается то для привода машины необходима установка повышающей или понижающей передачи. Оптимальный тип передачи определяют с учетом ряда факторов: эксплуатационных условий характера изменения нагрузки в процессе работы.
В зависимости от конкретных условий конструктор проектирующий механическое приводное устройство рассматривает варианты применения передач различных типов – зубчатых червячных ременных цепных фрикционных и их целесообразных сочетаний. Проектирование приводных устройств следует начинать с кинематического расчета. Исходными данными необходимыми для расчета могут быть такие показатели: номинальный вращающий момент T на валу приводимой в движение машины его угловая скорость (или частота вращения n) график изменения нагрузки и частоты вращения за определенный период. По этим данным определяются значения момента и частоты вращения. Далее вычисляют значения передаточных отношений для нескольких вариантов приводов.
Для выбора электродвигателя должны быть известны условия эксплуатации требуемая мощность и частота вращения вала. В соответствии с этими данными выбирают по каталогу электродвигатель и проверяют его на нагрев при установившемся и переходных режимах и при кратковременной перегрузке.
Кинематический расчет привода
1. Выбор электродвигателя
Для выбора электродвигателя определяется требуемая мощность и частота вращения. Потребляемую мощность (Вт) привода (мощность на выходе) берут из условия
(1.1) где где рем цил - КПД соответственно ременной цилиндрической передачи.
Ориентировочные значения которых принять.
Тогда и следовательно (кВт).
Далее из справочника электродвигателей подобрать электродвигатель с мощностью P кВт ближайшего к учитывая при этом
Следовательно принять электродвигатель мощностью 22 кВт.
Найденные марки электродвигателей занести в таблицу 1.
Таблица 1 – Марки электродвигателей мощностью 22 кВт
Марка электродвигателя
В справочнике электродвигателей дана синхронная частота (частота без нагрузки) определить асинхронную частоту (частота под нагрузкой) вращения вала электродвигателя по формуле
(1.2) где - S – коэффициент скольжения ротора зависящий от марки электродвигателя.
Чем меньше обороты вала электродвигателя тем больше его масса габариты и стоимость.
Следовательно электродвигатель АИР90LB8 в дальнейший расчет не включать.
2. Расчет передаточного числа привода и разбивка его по ступеням
Определить общее передаточное число привода:
(1.3) где -- выходная угловая скорость данная техническим заданием;
определить по формуле;
(1.4) где n – асинхронная частота вращения вычисленная по формуле (1.2).
Определить передаточное число редуктора:
(1.11) где - передаточное число гибкой связи.
Рекомендуемое число гибкой связи . Принять . Следовательно
Редуцирующие возможности двух ступенчатого цилиндрического редуктора 3с.58
Минимальное передаточное отношение двух ступенчатого цилиндрического редуктора равно 8. Следовательно расчет третьего электродвигателя исключить так как
Разбивка передаточного числа редуктора по ступеням.
Передаточное отношение для тихоходной и быстроходной передачи цилиндрического соосного зубчатого редуктора:
Передаточные числа редукторов выберем из единого ряда и оценим процентное отклонение от полученного числа:
Погрешность передаточного числа редуктора в 1 случае меньше и не превышает допускаемых отклонений.
Для курсового проектирования рекомендовать привод состоящий из электродвигателя АИР80В2 мощностью 22 кВт с частотой вращения вала n=2850 обмин исполнения IM1081 (крепления на лапах). Редуктор двух ступенчатый соосный и цепной передачи .
3. Расчет крутящих моментов на всех валах привода
Определить крутящие моменты на валах привода по формулам:
Расчитать частоту вращения и угловые скорости всех валов привода:
Расчет ступеней соосного цилиндрического зубчатого редуктора
В соосном редукторе вести расчёт тихоходной ступени цилиндрической зубчатой передачи т.к. тихоходная ступень больше нагружена.
Назначить материал способ термообработки единицы твёрдости для шестерни и колеса.
В зубьях шестерни и колеса возникают контактные и изгибные напряжения следовательно необходимо обеспечить изгибную и контактную выносливость.
1. Материалы зубчатых колес и способ упрочнения зубьев
Выбор материала колеса и шестерни:
Так как в задании нет особых требований в отношении габаритов передачи назначить материалы со средними механическими характеристиками:
для шестерни - сталь 40XН улучшенная (HB 269..302) и ТВЧ на 1-12мм с твердостью 45 – 50 HRCэ
для колеса - сталь 40XН улучшенная с твердостью HB 269..302.
2. Расчет допускаемых напряжений
Допускаемые контактные напряжения
Предел контактной выносливости (табл. 2.2 стр. 13)
Минимальное значение коэффициента запаса прочности для зубчатых передач с поверхностным упрочнением .
Коэффициент долговечности учитывает влияние ресурса
Ресурс передачи в числах циклов перемены напряжений при частоте вращения n мин и времени работы ч:
- число вхождений в зацепление зуба рассчитываемого колеса за один его оборот.
В расчете учесть переменность режима нагружения: вместо назначенного ресурса Nк подставить эквивалентное число циклов NHE:
В случае постоянной частоты вращения на всех уровнях нагрузки
Коэффициент учитывающий влияние шероховатости сопряженных поверхностей зубьев принимаем .
Коэффициент учитывает влияние окружной скорости. Т.к. мс следовательно .
Допускаемое напряжение для цилиндрической передачи с прямыми зубьями равно меньшему из допускаемых напряжений шестерни и колеса .Следовательно допускаемое контактное напряжение принять
Допускаемые напряжения изгиба
Предел выносливости .
Минимальное значение коэффициента запаса прочности .
Коэффициент долговечности учитывает влияние ресурса:
при условии 2с.15 где и q=9 число циклов соответствующее перелому кривой усталости
В расчете учесть переменность режима нагружения: вместо назначенного ресурса Nк(2.3) подставить эквивалентное число циклов NHE:
Так как и следовательно .
Коэффициент учитывающий влияние шероховатости переходной поверхности между зубьями примем - .
Коэффициент учитывает влияние двустороннего приложения нагрузки.
3 Определение параметров передачи
3.1 Межосевое расстояние
Предварительное значение межосевого расстояния мм:
знак “+” (в скобках) относят к внешнему зацеплению знак “-“ – к внутреннему; - крутящий момент на колесе Н*м; u – передаточное число.
Коэффициент K в зависимости от поверхностной твердости и зубьев шестерни и колеса соответственно равен К=8.
Окружную скорость мс вычислим по формуле:
Степень точности передачи по ГОСТ 1643-81 – 9 (передачи низкой точности).
Уточнить предварительно найденное значение межосевого расстояния по формуле:
где - прямозубых передач;
- коэффициент ширины принять из ряда чисел в зависимости от положения колес относительно опор: при несимметричном расположении принимаем
Коэффициент нагрузки в расчетах на контактную прочность
Коэффициент учитывает внутреннюю динамику нагружения связанную прежде всего с ошибками шагов зацепления и погрешностями профилей зубьев шестерни и колеса. Значения принять по таблице в зависимости от степени точности передачи по нормам плавности окружной скорости и твердости рабочих поверхностей.
Коэффициент учитывает неравномерность распределения нагрузки по длине контактной линии. Рассмотреть коэффициенты неравномерности распределения нагрузки в начальный период и после приработки .
Значение коэффициента принять по таблице в зависимости от коэффициента схемы передачи и твердости зубьев. Значение коэффициента вычислить ориентировочно:
Коэффициент определить по формуле:
- коэффициент учитывающий приработку зубьев и он равен
Начальное значение коэффициента распределения нагрузки между зубьями в связи с погрешностями изготовления определить в зависимости от степени точности по нормам плавности:
для прямозубой передачи
Вычисленное значение межосевого расстояния округлить до мм.
Предварительные основные размеры колеса
Делительный диаметр:мм; 2с.20
Ширину колеса принять b2=52 мм по стандартному ряду. Коэффициент нагрузки при расчете по напряжениям изгиба
Коэффициент учитывает внутреннюю динамику нагружения связанную прежде всего с ошибками шагов зацепления шестерни и колеса. Значения принять по таблице в зависимости от степени точности передачи по нормам плавности окружной скорости и твердости рабочих поверхностей.
- коэффициент учитывающий неравномерность распределения напряжений у основания зубьев по ширине зубчатого венца оценить по формуле:
- коэффициент учитывающий влияние погрешностей изготовления шестерни и колеса на распределение нагрузки между зубьями определить так же как при расчетах на контактную прочность:
Максимально допустимый модуль мм определить из условия неподрезания зубьев у основания
Минимальное значение модуля мм определить из условия прочности:
где =34 10 для прямозубых передач; вместо подставить меньшее из значений и .
Так как заложена закалка ТВЧ для поверхности зубьев шестерни принять значение модуля мм 4 с. 140;
3.3 Числа зубьев шестерни и колеса
Суммарное число зубьев
Принять суммарное число зубьев zs=160.
Число зубьев шестерни и колеса. Число зубьев шестерни
Число зубьев колеса
Фактическое передаточное число
Диаметры колес. Делительные диаметры d:
шестерни .. мм; 2с.23
Диаметры и окружностей вершин и впадин зубьев колес:
Проверка зубьев по контактным напряжениям. Расчетное значение контактного напряжения
для прямозубых передач;
3.4 Силы в зацеплении
Проверка расчета по напряжениям изгиба. Расчетное напряжение изгиба:
Значение коэффициента учитывающего форму зуба и концентрацию напряжений в зависимости от приведенного числа зубьев и коэффициента смещения принять по таблице. и . .
- коэффициент учитывающий перекрытие зубьев. .
4 Проверочный расчет на прочность зубьев при действии пиковой нагрузки.
Целью расчета является предотвращение остаточных деформаций или хрупкого разрушения поверхностного слоя или зубьев при действии пикового момента . Действие пиковых нагрузок оценить коэффициентом перегрузки .
Для предотвращения остаточных деформаций или хрупкого разрушения поверхностного слоя контактное напряжение не должно превышать допустимое значение :
где - контактное напряжение при действии номинального момента Т. Допускаемое напряжение принять
Для предотвращения остаточных деформаций и хрупкого разрушения зубьев напряжение изгиба при действии пикового момента не должно превышать допускаемое :
где - напряжение изгиба вычисленное при расчетах на сопротивление усталости.
Допускаемое напряжение вычислить в зависимости от вида термической обработки и возможной частоты приложения пиковой нагрузки:
- предел выносливости при изгибе; - максимально возможное значение коэффициента долговечности (); - коэффициент влияния частоты приложения пиковой нагрузки (); - коэффициент запаса прочности ().
5 Расчет быстроходной ступени соосной цилиндрической передачи
Расчёт цилиндрической передачи выполнен в программе «TCAD». Выбрана передача с оптимальными габаритами и прочностными и силовыми характеристиками.
Мощность на ведущем валу кВт
Частота вращения шестерни обмин
Расчётный срок службы час
Термообработка шестерни
Термообработка колеса
Обработка выкружки шестерни
Обработка выкружки колеса
Зуборезный инструмент шестерни
Зуборезный инструмент колеса
Кинематические параметры
Фактическое передаточное число
Частота вращения колеса обмин
Линейная скорость мс
Нормальный модуль мм
Межосевое расстояние передачи мм
Угол наклона зубьев град
Суммарный коэффициент перекрытия
Угол зацепления зубчатых колёс град
Число зубьев шестерни
Коэффициент смещения исходного контура шестерни
Коэффициент смещения исходного контура колеса
Диаметр окружности вершин шестерни мм
Делительный диаметр шестерни мм
Начальный диаметр шестерни мм
Диаметр окр-ти впадин шестерни мм
Ширина венца шестерни мм
Диаметр окружности вершин колеса мм
Делительный диаметр колеса мм
Начальный диаметр колеса мм
Диаметр окр-ти впадин колеса мм
Ширина венца колеса мм
Прочностные и силовые параметры
Контактное напряжение МПа
Момент на быстроходном валу Нм
Момент на тихоходном валу Нм
Суммарное давление на вал Н
Окружное усилие шестерни Н
Радиальное усилие шестерни Н
Осевое усилие шестерни Н
Окружное усилие колеса Н
Радиальное усилие колеса Н
Осевое усилие колеса Н
Расчет ременной передачи
В техническом задании по проектированию привода не указан тип ремня ремённой передачи. Поэтому нужно рассчитать несколько видов ремня в программе «TCAD».
По долговечности цепи и по габаритам цепной передачи принят оптимальным расчет зубчатой цепью.
Таблица 1 - Расчет цепной передачи с зубчатой цепью
Частота вращения ведущ. шкива обмин
Проектный срок службы час
Коэффициент внешней динамики
Делительный диаметр ведущ. шкива мм
Делительный диаметр ведом.шкива мм
Диаметр вершин ведущего шкива мм
Диаметр вершин ведомого шкива мм
Число зубьев ведущего шкива
Число зубьев ведомого шкива
Межосевое расстояние мм
Частота вращения ведущей звёздочки обмин
Расчетный срок службы час
Конструирование валов редуктора
Рисунок-1 Эскиз быстроходного вала редуктора
мм; мм – ступень для установки крышки
мм; мм – ступень для установки подшипника 205
мм; мм – промежуточная ступень
– допускаемое напряжение при кручении
Рисунок-2 Эскиз промежуточного вала редуктора
мм l=16мм - ступень установки подшипника 206
- промежуточная ступень
- ступень для установки колеса
- ступень для установки подшипника 206
Рисунок-2 Эскиз тихоходного вала редуктора
мм; мм – ступень для установки подшипника 206
мм; мм – ступень для установки колеса
мм; мм – промежуточная ступень
Конструирование колес редуктора
мм – толщина диска колеса
мм – длина ступицы колеса
мм –диаметр ступицы колеса
Расчет посадки с натягом для колеса выходного вала редуктора
1 Среднее контактное давление
где K- коэффициент запаса сцепления f - коэффициент сцепления Т – вращающий момент колеса Н·м; d- диаметр соединения мм; l- длина сопряжения мм
2 Деформация деталей
где С1 С2- коэффициенты жесткости: С1=1-1;
Е – модуль упругости МПа: для стали – 21·105 ; – коэффициент Пуассона: для стали – 03.
3 Поправка на обмятие микронеровностей
где Ra1 иRa2 – среднее арифметическое отклонение профиля поверностей
[Nmin]=1269+1375+96=3604 мкм
5 Максимальный натяг
[Nmах]=[мах]+u 1 c.89
[Nmах]=6909+1375=8284
где [ma [Pmax] МПа – максимальное давление допускаемое
прочностью охватывающей или охватываемой детали меньшее из двух:
[Pma [Pmax2]= 05·T2[1-(dd2)2]
где T1T2 – предел текучести материала охватывающей и охватываемой детали МПа; d2 – диаметр ступицы колеса.
По значениям [Nm Nmax[Nmах]
Проверочный расчет тихоходного вала по запасу выносливости
Основными нагрузками на вал являются силы от передач. Силы на валы передают через насаженные на них детали: зубчатые колеса шкивы полумуфты. При расчетах принимают что насаженные на вал детали передают силы и моменты валу на середине своей ширины.
Рисунок 7.1– Эпюры внутренних силовых факторов
Составив расчетную схему определим реакции в опорах и внутренние силовые факторы: изгибающие и крутящие моменты для того чтобы впоследствии определить силовые факторы опасных сечений.
1 Консольная радиальная сила от муфты Fм Н
Fцеп= (50 125) 1 с.110
2 Радиальные реакции опор от сил в зацеплении
Проверка:реакции найдены правильно.
Проверка: реакции найдены правильно.
3 Суммарные реакции опор
-суммарная реакция на первую опору
-суммарная реакция на вторую опору
4 Определения внутренних силовых факторов
Составляем расчетную схему для определения изгибающих и крутящих моментов.
4.1 Изгибающие моменты:
Суммарный изгибающий момент
Опасные сечения вала (рис. 7.1) определяются наличием концентраций напряжений. В данном случае к ним относятся:
Сечение A–A –место установки шкива на вал: сечение нагружено крутящим моментом; концентратор напряжений – паз под шпонку на валу.
Сечение Б-Б– место установки правого по рисунку подшипника на вал: сечение нагружено изгибающим и крутящими моментами; концентратор напряжений –галтель и посадка с натягом внутреннего кольца подшипника на вал.
Из двух сечений выбираем наиболее опасное сечение. Расчеты сводим в таблицу 7.1.
Таблица 7.1 – Подсчет критерия напряженности
Источник концентрации напряжений
Таким образом наиболее опасным сечением быстроходного вала по критерию напряженности является сечение А-А.
5 Проверка запаса выносливости в опасном сечении А-А
Для удобства все расчеты сведены в таблицу 7.2
Таблица 7.2 –Подсчет запаса выносливости в сеченииА - А
Эффективный коэффициент концентрации
- по касательным напряжениям
Шероховатость поверхности
Коэффициент состояния поверхности
Масштабный коэффициент
Коэффициент чувствительности к ассиметрии цикла
Коэффициент концентрации напряжений
Коэффициент чувствительности к асимметрии цикла для детали
Изгибающий момент Нм
Момент сопротивления
Полярный момент сопротивления
Продолжение таблицы 8.2
Амплитудное напряжение
Коэффициент запаса выносливости
Общий запас выносливости S
Минимальный запас прочностиSmin
2.1 Коэффициент концентрации напряжений
2.2 Коэффициент влияния асимметрии цикла:
2.3 Коэффициенты запаса прочности по нормальным и касательным напряжениям
2.4 Коэффициент запаса прочности в рассматриваемом сечении равен коэффициенту запаса по касательному напряжению
(10.25) тогда Запас выносливости в опасном сечении обеспечен так как условиеS>Smin=18 выполнено
По диаметру вала и по действию силы прямозубого колеса предварительно назначаем шариковые радиальные подшипники легкой серии 207 ГОСТ 2893-82.
Для принятых подшипников из таблицы 24.10 находим: Cr=25500 H; C0r=13700H; d=35мм; D=72мм; Dw=9525 мм α=00.
Принимаем KБ=14 (1табл.7.6); КТ=1 (t1000C).
Расчет ведем по наибольшей суммарной реакции.
1 Эквивалентные нагрузки
Для типового режима нагружения коэффициент эквивалентности .
2 Эквивалентная динамическая радиальная нагрузка
Pr= (VXFr+ YFa) KБ КТ; 1 с.122
Pr=(10.5610773+0)1.41=845H.
Расчетный срок службы подшипника при а1=1 (вероятность безотказной работы 90%) А23=0.7( обычные условия эксплуатации) k=3 (шариковый подшипник).
Расчетный ресурс больше требуемого: (18·106 ч> 6000ч).
3 Максимальная эквивалентная динамическая радиальная нагрузка
Prmax= (VXFr2max+ YFamax) KБ КТ = (10.561710+0)1.41=1340H. 1с.122
Условие Prmax≤ 05Сrвыполнено: 1340 ≤ 0.532000=16000H.
Так как расчетный ресурс больше требуемого и выполнено условие Prmax≤ 05Сr то предварительно назначенный подшипник 207 пригоден. При требуемом ресурсе надежность выше 90%.
Проверочный расчёт шпонки
Для соединения валов с деталями передающими вращающий момент применяют шпонки. В производстве используют главным образом призматические шпонки изготовленные из чистотянутой стали (чаще всего из стали 45). Длину шпонки выбирают из стандартного ряда. Сечение шпонки выбирается по величине соответствующего диаметра.
Шпонка на тихоходном валу:
Призматические шпонки применяемые в проектируемых редукторах проверяют на смятие. Проверке подлежат все шпонки.
где М – момент на соответствующем валу Н d – диаметр соответствующего вала мм h – сечение шпонки мм t1 – глубина паза вала мм lр – рабочая длина шпонки со скругленными торцами мм l – полная длина шпонки мм b – сечение шпонки мм [см] – допускаемое напряжение на смятие [см]=110 190 Нмм2.
Проверка шпонки на выходе тихоходного вала:
- условие выполняется.
Расчет болтов крепления цилиндрического редуктора к раме
На входном валу редуктора установлена ременная передача (рис.10.1).
Рисунок 10.1 – Нагрузки действующие на редуктор
Соединение выполнено 4 болтами равномерно расположенными на плоскости стыка представляющей собой два платика с размерами 40 и 110мм.
Нагрузки действующие на болты:
Fцеп - консольно расположенная нагрузка от ременной передачи на входном валу редуктора.
Вращающий момент T4 на выходном валу. При переносе силы Fрем в центр тяжести возникают два момента:
My=Fцепh – опрокидывающий момент раскрывающий стык деталей;
Mz=Fцепl1 – закручивающий момент сдвигающий редуктор в плоскости стыка относительно оси z.
1 Расчет болтов крепления по условию не раскрытия стыка
1.2 Условие не раскрытие стыка
где - напряжение в плоскости стыка от силы затяжки болтов;
- напряжение в плоскости стыкаот действия вращающего момента T4на выходном валу редуктора;
- напряжение в плоскости стыка от действия момента My.
1.2Необходимая сила затяжки болта по условию не раскрытия стыка Н
где - площадь опорных платиков
Aст=2ab=240220=17600 мм2;
- момент сопротивления площади стыка относительно оси y
z – число болтов крепления;
К – коэффициент запаса по не раскрытию стыка K=15 20.
Условие не раскрытие стыка (п10.1.2) выполнятся 0032 МПа 002+0005 МПа.
2 Расчет болтов крепления по условию отсутствия сдвига
Во избежание сдвига редуктора относительно плоскости стыка затяжкой болтов необходимо создать момент трения:
где K1- коэффициент запаса сдвига K1=132; f- коэффициент трения f=01502
Рисунок 10.2 – Нагрузки действующие на болты перенесенные на плоскость стыка
2.1 Нагрузка от момента Mz приходящаяся на один болт:
2.2 Нагрузка от момента Mzприходящаяся на один болт:
При условии что на болты крепления редуктора к раме действуют одновременно нагрузки и раскрывающие стык деталей и сдвигающие детали в плоскости стыка сила затяжки болтов должна обеспечить и не раскрытие стыка и отсутствие сдвига деталей.
2.3 Необходимая сила затяжки болта по условию отсутствия сдвига:
где R- максимально результирующая нагрузка равная геометрической сумме Fв
и Mz приходящаяся на один болт (рис.102)
Расчетная нагрузка на болт Fб.расчопределяется по наибольшей силе затяжки рассчитанной исходя из двух условий: условия не раскрытия стыка и условия отсутствия сдвига.
2.3 Условие прочности болта по напряжениям растяжения:
где d1- внутренний диаметр болта мм; допускаемое напряжение растяжения [р]=тn
где т –предел текучести материала болта т=200 МПа для стали Ст3;
n – коэффициент запаса прочности болта n=3
Условие прочности болта по напряжению сдвига выполняется.
Расчет конструктивных элементов редуктора
1 Конструирование крышки подшипника
Для крышек подшипника выбран чугун марки СЧ15. В данной курсовой работе используются привертные крышки. Схема крышки подшипникового узла показана на рисунке 3.
Рисунок 11.1- Схема крышки подшипникового узла
Размеры крышки при диаметре подшипникового узлаD = 60мм:
- диаметр фланца 1 с.159
2 Расчёт стенок корпуса
Размеры корпуса определяет число и размеры размещенных в нем деталей относительное их расположение значение зазоров между ними. Ориентировочные размеры корпуса были определены при составлении компоновочной схемы уточнены при разработке конструкций узлов.
Корпуса современных редукторов очерчивают плоскими поверхностями все выступающие элементы (бобышки подшипниковых гнезд ребра жесткости) устраняют с наружных поверхностей и вводят внутрь корпуса лапы под болты крепления к основанию не выступают за габариты корпуса проушины для транспортировки редуктора отлиты заодно с корпусом. При такой конструкции корпус характеризуют большая жесткость и лучшие виброакустические свойства повышенная прочность в местах расположения болтов крепления уменьшение коробления при старении возможность размещения большего объема масла упрощение наружной очистки удовлетворение современным требованиям технической эстетики. Однако масса корпуса из-за этого несколько возрастает а литейная оснастка — усложнена.
Для удобства сборки корпус выполняют разъемным. Плоскость разъема проходит через оси валов. Плоскость разъема для удобства обработки располагаем параллельно плоскости основания. Верхнюю поверхность крышки служащую технологической базой для обработки плоскости разъема также выполняем параллельной плоскости основания.
Разработку конструкции начинаем с прорисовки контуров нижней (корпуса) и верхней (крышки корпуса) частей.
Основной материал корпусов – СЧ15.
Толщина стенки редуктора определяется следующим образом: 1 с.293
Плоскости стенок встречающихся под прямыми или тупыми углами сопрягаем дугами радиусом и . 1 с.293
Толщина стенки крышки корпуса . Принимаем
3 Конструктивное оформление внутреннего контура редуктора
Рисунок 11.2– Оформление внутреннего контура
Из центра тихоходного вала проводят тонкой линией дугу окружности радиусом
Из центра быстроходного вала проводят дугу радиусом
где - наружный диаметр зубчатого колеса; - наружный диаметр зубчатого колеса; - зазор.
Расстояние между дном корпуса и поверхностью колеса
4 Конструктивное оформление приливов для подшипниковых гнезд
Приливы в которых располагают подшипники конструктивно оформляют по рисунку 11.3.
Рисунок 11.3– Оформление приливов
Диаметры прилива для привертной крышки принимают (мм): 1 с.295
где ф - диаметр фланца крышки подшипника
Длину подшипниковых гнезд определяют конструктивно.
5 Крепление крышки редуктора к корпусу
Для соединения крышки с корпусом используют болты винты с цилиндрической головкой с шестигранным углублением под ключ.
Диаметр d (мм) винтов крепления крышки принимают в зависимости от вращающего момента T (Hм) на выходном валу: тогда принимаем .
Размеры конструктивных элементов:
К=235d=24 мм; 1 с.297
С=11d=1110= 12мм; 1 с.297
D=2d=210=20 мм 1 с.297
Рисунок 11.4– Размеры формы болтов
6 Фиксирование крышки относительно корпуса
При сборке редуктора нужно точно фиксировать положение крышки относительно корпуса. Необходимую точность фиксации достигают штифтами которые располагают на возможно большем расстоянии друг от друга. Диаметр штифтов: 1 с.298
тогда где - диаметр крепежного винта.
Обычно применяют два конических штифта с внутренней резьбой которые устанавливают по срезам углов крышки или в специально выполненных нишах.
7 Конструктивное оформление опорной части корпуса
Опорную поверхность корпуса следует выполнять в виде нескольких платиков расположенных в местах установки болтов или шпилек. Можно выполнять опорную поверхность в виде двух длинных параллельно расположенных платиков. Конструкции мест крепления корпуса к плите или раме показаны на рисунке.
Диаметр винта крепления редуктора к плите (раме) :1 с.300
где - диаметр винта крепления крышки и корпуса редуктора.
Число z винтов принимают в зависимости от межосевого расстояния тихоходной ступени тогда при числоz=4. 1 с.300
Рисунок 11.5 – Оформление опорной части корпуса
8 Оформление сливных отверстий
Наиболее часто в редукторах используют картерную систему смазывания при которой корпус является резервуаром для масла. Масло заливают через верхний люк. При работе передачи масло постепенно загрязняют продукты изнашивания оно стареет – свойства его ухудшаются.
Поэтому масло периодически меняют. Для слива масла в корпусе редуктора выполняют сливное отверстие закрываемое пробкой с цилиндрической резьбой.
Рисунок 11.6– Сливная пробка Рисунок11.7 –Сливное отверстие
Цилиндрическая резьба не создаёт надёжного уплотнения поэтому под пробку с цилиндрической резьбой установлена уплотняющая прокладка из паронита.
Рисунок 11.8 – Маслоуказатель (щуп)
Для наблюдения за уровнем масла в корпусе установлен маслоуказатель жезловой (щуп).
Для предохранения от вытекания смазочного материала из подшипниковых узлов а также защиты от попадания влаги и пыли установлена резиновая армированная манжета для валов ГОСТ 8752-79. Манжета установлена открытой стороной внутрь корпуса это позволяет обеспечить хороший доступ смазочного масла к рабочей кромке манжеты.
9 Оформление прочих конструктивных элементов корпусных деталей
Для подъёма и транспортировки крышки корпуса и собранного редуктора применяют проушины отливая их заодно с крышкой.(рис.11.9)
Для залива масла в редуктор контроля правильности зацепления и для внешнего осмотра деталей делают люки (рис.11.10)
Рисунок 11.9 – Проушина
Рисунок 11.10 – Крышки корпуса
Для данной конструкции привода рекомендуется применить цепную муфту так как редуктор соединяется с электродвигателем через ременную передачу. Достоинство цепных муфт: при монтаже и демонтаже не требуется осевого смещения узлов. Цепные муфты стандартизованы – ГОСТ 20742-93.
Рисунок 13.1– Цепная муфта
Номинальный крутящий момент Н·м = 500;
Частота вращения с-1 не более 1000;
Таблица 12.1 – Основные размеры муфты
Конструирование рамы
Конфигурацию и размеры рамы определяют по размеру редуктора и электродвигателя. Шкив ременной передачи соединяют с валом электродвигателя цепную муфту – с валом редуктора.
Определим основные размеры B и L рамы в плане принимая b0 =0 10 мм и стремясь к образованию простой конфигурации. Затем определим высоту H = (0.08 0.10)L по которой подбирают ближайший размер швеллера (1табл.24.51). Уточняют размеры рамы располагая отверстия dэ и dp примерно на середине ширины полки швеллера.
Швеллеры располагают как правило полками наружу. Такое расположение удобно для крепление узлов к раме осуществляемого как болтами так и винтами.
Для крепления рамы к полу цеха применяют фундаментальные болты их расположение определяется при проектировании рамы.
Диаметр и число фундаментальных болтов принимают в зависимости от длины рамы: при L = 800 мм диаметр болтов D=12 мм число Z=4.
Основные размеры болта (мм):
Рисунок 13.1– Фундаментальный болт
Смазывание зубчатых зацеплений и подшипников
Смазывание зубчатых зацеплений и подшипников применяют в целях защиты от коррозии снижения коэффициента трения уменьшение износа отвода тепла и продуктов износа от трущихся поверхностей снижение шума и вибраций.
Принцип назначения сорта масла следующий: чем выше окружная скорость колеса тем меньше должна быть вязкость масла чем выше контактные давления тем большей вязкостью должно обладать масло.
Выбор сорта масла зависит от значения расчётного контактного напряжения в зубьях и фактической окружной скорости колёс. Окружная скорость одного из колёс данного редуктора 0312 мс а максимальные контактные напряжения 70286 МПа. Следовательно необходима кинематическая вязкость 34 мм2с. Такую вязкость даёт индустриальное масло И–Г–А–32. Сорт масла выбираем(1 по табл. 10.29).
Рассчитываем объём масла в редукторе:
В данный редуктор погружать в масло колеса обеих ступеней передачи.
Смазывание подшипника
Подшипники смазываются тем же маслом которым смазываются детали передач. При картерной смазке колёс подшипники смазываются брызгами масла.
Перед сборкой внутреннюю полость корпуса редуктора тщательно очищают и покрывают маслостойкой краской.
Сборку производим в соответствии со сборочным чертежом редуктора начиная с узлов валов:
- на ведущий вал устанавливают манжеты и шариковые радиальные подшипники предварительно нагретые в масле до 80° 100°С. С другой стороны вала напрессовывают шестерню.
- в ведомый вал напрессовывают зубчатое колесо затем надевают манжеты шариковые радиальные подшипники предварительно нагретые в масле до 80° 100°С.
Собранные валы укладывают в основание корпуса редуктора. Надевают крышку корпуса покрывая предварительно поверхности стыка крышки и корпуса герметиком. Для центровки устанавливают крышку на корпус с помощью двух штифтов затягивают болты крепящие крышку к корпусу. После этого в подшипниковые камеры закладывают пластичную смазку ставят крышки подшипников. Перед постановкой сквозных крышек в них закладывают манжеты проверяют поворачиванием валов отсутствие заклинивания подшипников (валы должны проворачиваться от руки) и закрепляют крышки винтами. Затем ввёртывают пробку в маслоспускное отверстия с прокладкой и маслоуказатель.
Заливают в корпус масло и закрывают смотровое отверстие крышкой с прокладкой из технического картона закрепляют крышку болтами.
Собранный редуктор обкатывают на стенде по программе устанавливаемой техническими условиями.
Расчет цепной передачи с роликовой цепью
Дунаев П. Ф. Леликов О.П. Конструирование узлов и деталей машин: Учебник для ВУЗов М.: Высшая школа 2004-496с.
Лимаренко Г.Н. Сенькин В.И. Максимова А.А. Самосенко С.Н. Соломкин А.А. Щепин А.Н. Детали машин. Техническое и рабочее проектирование: Метод.указания Красноярск: ИПЦ КГТУ 2003-52с
Титовская О. Расчет и проектирование валов редукторов: Метод. указания к выполнению курсового проекта 68с
Чернавский С.А. Снесарев Г. А. Проектирование механических передач: учебно-справочное пособие для вузов -5-е изд. перераб. и доп.-М.: Машиностроение 1984.-560с.
Спецификация привод2.spw

Болт М14-6g x 55.88.40Х ГОСТ 7796-70
Болт М30-6g x 28.88.40Х ГОСТ 7796-70
Винт А. М4-6g x 8.14H ГОСТ 1478-93
Гайка М10-6H.04 ГОСТ 15521-70
Гайка М14-6H.04 ГОСТ 15521-70
Шайба 10 65Г ГОСТ 6402-70
Шайба 12 Т 65Г ГОСТ 6402-70
Шайба 14 Т 65Г ГОСТ 6402-70
Шайба 30 Т 65Г ГОСТ 6402-70
Электродвигатель АИР90L2
-16 - 1У ГОСТ 21424-75
Спецификация редуктор.spw

Крышка подшипника глухая
Вал-шестерня промежуточная
Колесо зубчатое прямозубое
Крышка подшипника сквозная
Вал- шестерня быстроходная
Прокладка уплотняющая
Кол-во по потребности
ол-во по потребности
Шариковый радиальный 206 ГОСТ 8338-75
Шариковый радиальный 205 ГОСТ 8338-75
Шариковый радиальный 208 ГОСТ 8338-75
Винт А.М 8 Х 1-6g x 13.109.30ХГСА ГОСТ 1491-80
Винт М10-6g X 65.88.40Х ГОСТ 11738-84
Винт М8-6g X 12.109.35 ГОСТ 11738-84
Винт М12-6g X 65.88.40Х ГОСТ 11738-84
Шайба 10 Л 65Г ГОСТ 6402-70
Шайба 8 Л 65Г ГОСТ 6402-70
Шайба 12 Л 65Г ГОСТ 6402-70
Шпонка 6 x 6 x 20 ГОСТ 23360-78
Шпонка 8 x 10 x 50 ГОСТ 23360-78
Штифт 2.8 x 35 ГОСТ 9464-79
Масло индустриальное И-Г-А-32
Привод.cdw

План размещения отверстий под
фундаментальные болты М(1:5)
Ось симметрии редуктора
Ось вала электродвигателя
Техническая характеристика
частота вращения вала-2850 обмин
Редуктор цилиндрический специальный
Общее передаточное число привода -45
Вращающий момент на выходном валу привода - 114
Частота вращения выходного вала привода - 126
Межосевое расстояние - 585 мм
Передаточное число - 2
Технические требования
Привод подвергнуть обкатке при рабочей нагрузке в течении двух
При обнаружении во время обкатки каких- либо дефектов обкатку
после их устранения обкатку повторить
После выверки узлов привода все болтовые соединеия затянуть
Перекос и смещение средних плоскостей шкивов -0
Кинематическая схема привода
Рекомендуемые чертежи
- 15.02.2021
- 24.01.2023
- 24.01.2023
- 04.11.2022