Привод общего назначения




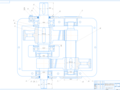
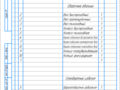
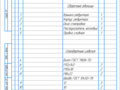
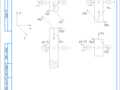
- Добавлен: 24.01.2023
- Размер: 708 KB
- Закачек: 0
Описание
Привод общего назначения
Состав проекта
![]() |
![]() |
![]() ![]() ![]() ![]() |
![]() ![]() ![]() ![]() |
![]() ![]() ![]() ![]() |
![]() ![]() ![]() ![]() |
![]() ![]() ![]() ![]() |
![]() ![]() ![]() ![]() |
![]() ![]() ![]() |
![]() ![]() ![]() ![]() |
![]() ![]() ![]() ![]() |
Дополнительная информация
Схема сил.cdw

Вал.cdw

Неуказанные предельные отклонения
резмеров отверстий по Н14
Колесо.cdw

Термообработка улучшение НВ270
Неуказанные предельные отклонения
резмеров отверстий по Н14
Сталь 40ХН ГОСТ 4543-71
Сборочный чертеж.cdw

Схема редуктора.cdw

Спецификация СБ.spw

Крышка подшипника промежуточного вала
Крышка подшипника тихоходного вала
Кольцо мазеудерживающее
Шарикоподшипник радиально-
упорный однорядный ГОСТ 831-75
Шпонка призматическая
Манжета ГОСТ 8752-79
Муфта УВП 250-38-1.2-58
Муфта УВП 1000-55-1.2-82
Электродвигатель 4А132М6У3
Пояснительная записка.doc
Российской Федерации
Государственное образовательное учреждение
Высшего профессионального образования
«Самарский Государственный технический университет»
Расчетно-пояснительная записка
к курсовому проекту по деталям машин
«Проектирование привода общего назначения»
Задание 18 вариант 4
Техническое задание.
Обобщенная структурная схема проектируемого привода общего назначения представлена на рис. 1.
Рис. 1. Структурная схема привода общего назначения:
- электродвигатель; 2 - упругая муфта; 3 - одноступенчатый зубчатый редуктор; ДО - вал электродвигателя; Б1 - быстроходный вал редуктора; Т2 - тихоходный вал редуктора; П3 - приводной вал рабочей машины.
Схема привода приведенная в техническом задании № 18 представлена на рис. 2.
Рис. 2. Схема привода (техническое задание № 18).
Мощность на тихоходном валу редуктора (приводном валу рабочей машины): Рвых = 6558 кВт.
Угловая скорость на тихоходном валу редуктора (приводном валу рабочей машины): вых = 1128 с-1.
Требуемое межосевое расстояние: [аwT] = 180 мм.
Передаточное отношение: u = 9.
Срок службы: 10 лет.
Коэффициент годового использования: КГ = 08.
Коэффициент суточного использования: Кс = 03.
Тип производства: крупносерийное.
Нагрузка: постоянная.
1. Выбор двигателя. Кинематический и силовой расчет привода.
Мощность на приводном валу рабочей машины:
Рвых = 6558 кВт (см. п. 1).
Общий к.п.д. привода:
М = 098 - к.п.д. муфты ЗП = 097 – к.п.д. зубчатой передачи ПК = 099 – к.п.д. подшипника качения (П.1 [1]).
Требуемая мощность электродвигателя:
Ртр = Рвых = 65580875 = 749 кВт.
Выбираем асинхронный электродвигатель серии 4А с номинальной мощностью Рдв = 75 кВт и синхронной частотой вращения nдв = 970 обмин – электродвигатель типоразмера 4А132М6УЗ.
Расчетное передаточное отношение привода:
Частные передаточные отношения передач входящих в привод:
uМ = 1 – передаточное отношение муфты;
- передаточное отношение тихоходной ступени зубчатой передачи;
Мощности на валах редуктора:
Частоты вращения валов:
n1 = nдвuМ = nдв = 970 обмин;
n2 = n1uБ = 970285 = 340 обмин;
n3 = n2uТ = 340315 = 108 обмин;
nвых = n3uМ = 108 обмин.
Угловые скорости валов:
=1uБ = 1016285 = 3565 с-1;
= 2uТ = 3565316 = 1128 с-1;
Вращающие моменты на валах редуктора:
Т1 = ТдвuММ = 738098 = 7234 Нм;
Т2 = Т1uБЗППК = 7234285097099 = 198 Нм;
Т3 = Т2uТЗППК = 198315097099 = 601 Нм;
Твых = Т3М = 601098 = 5888 Нм.
Результаты кинематического и силового расчета привода представлены в Табл. 1.
Табл. 1. Значения кинематических и силовых параметров на валах.
2. Расчет быстроходной ступени редукторной передачи.
На основании требований технического задания и результатов кинематического и силового расчета привода определяем исходные данные для расчета передачи (Табл. 2).
Табл. 2. Данные для расчета редукторной передачи.
Крутящий момент на колесах
Частота вращения колес
Передаточное отношение
нереверсивная косозубая
Срок службы передачи
Коэффициент использования передачи в течение года
Коэффициент использования передачи в течение суток
2.1. Выбор материала.
Выбираем материал со средними механическими характеристиками (П5 [1]): для шестерни – сталь 40Х термическая обработка – улучшение твердость НВ1= 300; для колеса – сталь 40Х термическая обработка – улучшение твердость НВ2 = 270.
Механические характеристики выбранного материала (П4 [1]):
Dпред = 200 мм – предельный диаметр;
Sпред = 125 мм – предельная толщина;
В = 790 МПа – предел прочности;
Т = 640 МПа – предел текучести.
2.2. Определение допускаемых напряжений.
) Допускаемые напряжения контакта (П6 [1]).
НО = 2НВ + 70 – предел контактной выносливости зубьев при базовом числе циклов (П5 [1]).
SН12 = 11 – коэффициент безопасности (П5 [1]).
-коэффициент долговечности.
- базовое число циклов нагружения;
N12 = 60nt – действительное число циклов нагружения где n – частота вращения колеса для которого определяется допускаемое напряжение t – суммарное время работы передачи под нагрузкой.
t = 36524LhKCKГ = 36524100803 = 21024.
N1 = 60n1t = 6097021024 = 1223596800 (циклов);
N2 = 60n2t = 6034021024 = 428889600 (циклов).
N12 >> NHO12 KHL12 = 1.
За расчетное значение допускаемого напряжения [H] принимаем меньшее из [H]1 и [H]2:
[H]2 [H]1 [H] = [H]2 = 5545 МПа.
) Допускаемые напряжения изгиба (П6 [1]).
FО = 18НВ – предел изгибной выносливости зубьев при базовом числе циклов (П5 [1]).
SF12 = 175 – коэффициент безопасности (П5 [1]).
KFC – коэффициент учитывающий реверсивность передачи. Для нереверсивной передачи KFC = 1.
- коэффициент долговечности.
N12 >> 4106 KFL12 = 1.
За расчетное значение допускаемого напряжения [F] принимаем меньшее из [F]1 и [F]2:
[F]2 [F]1 [F] = [F]2 = 2777 МПа.
) Предельное допускаемое напряжение контакта (П5 [1]).
) Предельное допускаемое напряжение изгиба (П5 [1]).
2.3. Проектный расчет (П7 [1]).
) Коэффициент ширины колеса относительно межосевого расстояния.
НВ1 350 НВ2 350 расположение колес относительного опор в редукторах симметричное а = 03 (П9 [1]).
) Межосевое расстояние.
Согласно исходным данным требуемое межосевое расстояние тихоходной ступени: [аwT] = 180 мм. Согласно же схеме привода (рис. 2) проектируемый редуктор является соосным следовательно межосевое расстояние быстроходной ступени равно межосевому расстоянию тихоходной ступени: [аwБ] = [аwT] = 180 мм.
Km = 58 т.к. передача косозубая;
- предварительный делитель-ный диаметр колеса;
- предварительная ширина колеса;
Принимаем ближайшее стандартное значение: m = 15.
) Суммарное число зубьев.
приблизительный угол наклона зубьев;
) Число зубьев шестерни.
) Число зубьев колеса.
) Фактическое передаточное отношение.
Отклонение от заданного:
) Окончательный угол наклона зубьев.
2.4. Расчет основных геометрических параметров (П10 [1]).
аw = 180 мм (см. пп. 2 п. 2.2.3).
) Делительный диаметр шестерни.
) Делительный диаметр колеса.
) Начальный диаметр шестерни.
) Начальный диаметр колеса.
) Диаметр вершин зубьев шестерни.
) Диаметр вершин зубьев колеса.
) Диаметр впадин зубьев шестерни.
) Диаметр впадин зубьев колеса.
) Угол профиля исходного контура.
2.5. Проверка пригодности заготовок колес (П11 [1]).
) Диаметр заготовки шестерни.
Dзаг = da1 +6 = 979 + 6 = 1036 мм;
Dпред = 200 мм (см. п. 2.2.1);
) Толщина заготовки обода колеса.
Sзаг = 8m = 815 = 12 мм;
Sпред = 125 мм (см. п. 2.2.1);
) Толщина заготовки диска колеса.
Сзаг = 05b2 = 0560 = 30 мм;
2.6. Проверочный расчет на контактную прочность (П12 [1]).
) Окружная скорость.
) Коэффициент динамической нагрузки KHV.
V 4 мс передача косозубая степень точности 9 (П13 [1]);
Степень точности 9 НВ1 350 НВ2 350 V 4 мс передача косозубая KHV = 105 (П14 [1]).
) Коэффициент концентрации нагрузки KH.
Расположение колес относительно опор симметричное НВ 350
) Коэффициент нагрузки.
КН = KHVKH = 105102 = 1071.
) Коэффициент неравномерности распределения нагрузки между зубьями КНα.
V 5 мс степень точности 9 КНα = 113 (П20 [1]).
) Коэффициент торцевого перекрытия.
) Коэффициент повышения прочности косозубой передачи по контактной напряженности.
) Контактное напряжение.
[H] = 5545 МПа H [H].
2.7. Проверочный расчет зубьев колес на изгибную прочность (П16 [1]).
) Эквивалентное число зубьев.
Шестерни: zэ1 = z1cos = 6309958 = 6327;
Колеса: zэ2 = z2cos = 17609958 = 17674.
) Коэффициент формы зуба.
Шестерни: Y1 = 347 + 132 zэ1 - 279х1 zэ1 + 0092х12 = 347 + 1326327 = 368 где х1 - коэффициент смещения исходного контура для шестерни х1 = 0 (т.к. контур без смещения);
Колеса: Y2 = 347 + 132 zэ2 - 279х2 zэ2 + 0092х22 = 347 + 13217674 = 354 где х2 - коэффициент смещения исходного контура для колеса х2 = 0 (т.к. контур без смещения).
) Коэффициент динамической нагрузки KFV.
Степень точности 9 НВ1 350 НВ2 350 V 4 мс передача косозубая KFV = 114 (П18 [1]).
) Коэффициент концентрации нагрузки KF.
d 06 KF = 105 (П19 [1]).
КF = KFVKF = 114105 = 1197.
) Коэффициент неравномерности распределения нагрузки между зубьями КFα.
V 5 мс степень точности 9 КFα = 135 (П20 [1]).
) Коэффициент повышения прочности косозубой передачи по напряжениям изгиба.
) Напряжение изгиба.
следовательно расчет выполняем по колесу 2.
[F]2 = 2777 МПа F2 [F]2.
3. Расчет тихоходной ступени редукторной передачи.
3.1. Выбор материала.
Выбираем материал со средними механическими характеристиками (П5 [1]): для шестерни – сталь 40Х термическая обработка – улучшение твердость НВ3= 300; для колеса – сталь 40Х термическая обработка – улучшение твердость НВ4 = 270.
3.2. Определение допускаемых напряжений.
SН34 = 11 – коэффициент безопасности (П5 [1]).
N34 = 60nt – действительное число циклов нагружения где n – частота вращения колеса для которого определяется допускаемое напряжение t – суммарное время работы передачи под нагрузкой.
N3 = 60n2t = 6034021024 = 428889600 (циклов);
N2 = 60n3t = 6010821024 = 136235520 (циклов).
N34 >> NHO34 KHL34 = 1.
За расчетное значение допускаемого напряжения [H] принимаем меньшее из [H]3 и [H]4:
[H]4 [H]3 [H] = [H]4 = 5545 МПа.
SF34 = 175 – коэффициент безопасности (П5 [1]).
N34 >> 4106 KFL34 = 1.
За расчетное значение допускаемого напряжения [F] принимаем меньшее из [F]3 и [F]4:
[F]4 [F]3 [F] = [F]4 = 2777 МПа.
3.3. Проектный расчет (П7 [1]).
Для тихоходной ступени коэффициент ширины колеса относительно межосевого расстояния выбираем равным:
Согласно исходным данным требуемое межосевое расстояние тихоходной ступени: [аwT] = 180 мм.
3.4. Расчет основных геометрических параметров (П10 [1]).
аw = 180 мм (см. п. 2.2.3 пп. 2).
3.5. Проверка пригодности заготовок колес (П11 [1]).
Dзаг = da3 +6 = 9037 + 6 = 9637 мм;
Сзаг = 05b4 = 05648 = 324 мм;
3.6. Проверочный расчет на контактную прочность (П12 [1]).
Степень точности 9 НВ3 350 НВ4 350 V 2 мс передача косозубая KHV = 103 (П14 [1]).
КН = KHVKH = 103103 = 1061.
3.7. Проверочный расчет зубьев колес на изгибную прочность (П16 [1]).
Шестерни: zэ3 = z3cos = 5809958 = 5824;
Колеса: zэ4 = z4cos = 18109958 = 18176.
Шестерни: Y3 = 347 + 132 zэ3 - 279х3 z31 + 0092х32 = 347 + 1325824 = 37 где х3 - коэффициент смещения исходного контура для шестерни х3 = 0 (т.к. контур без смещения);
Колеса: Y4 = 347 + 132 zэ4 - 279х4 zэ4 + 0092х42 = 347 + 13218176 = 354 где х4 - коэффициент смещения исходного контура для колеса х4 = 0 (т.к. контур без смещения).
Степень точности 9 НВ3 350 НВ4 350 V 2 мс передача косозубая KFV = 107 (П18 [1]).
d 08 KF = 108 (П19 [1]).
КF = KFVKF = 107108 = 11556.
следовательно расчет выполняем по колесу 4.
[F]4 = 2777 МПа F4 [F]4.
4. Нагрузка валов редуктора.
На основании требований технического задания составляем схему сил в зацеплениях редуктора (рис. 3).
Определяем силы в зацеплениях быстроходной и тихоходной ступеней.
Быстроходная ступень:
) Окружная сила в шестерне и колесе.
Ft1 = Ft2 = 2T2d2 = 219810326511 = 1494 H;
) Радиальная сила на шестерне и колесе.
Fr1 = Fr2 = Ft2tgαcos = 1494tg20cos512 = 1494036409958 = 5461 H;
) Осевая сила на шестерне и колесе.
Fa1 = Fa2 = Ft2tgα = 14940364 = 5438 Н;
) Консольная нагрузка от муфты.
Рис. 3. Схема сил в зацеплениях редуктора.
Тихоходная ступень:
) Окружная сила в шестерне и колесе.
Ft3 = Ft4 = 2T3d4 = 260110327265 = 44086 H;
Fr3 = Fr4 = Ft4tgαcos = 44086tg20cos512 = 44086036409958 = 16115 H;
Fa3 = Fa4 = Ft4tgα = 440860364 = 16047 Н;
5. Проектный расчет валов.
Эскизная компоновка редуктора.
Выбираем материал редуктора – сталь 40Х термообработка – улучшение. Твердость 269 302 НВ (П5 [1]).
Определяем диаметры ступеней быстроходного вала.
) Диаметр выходного конца.
[]к = 20 25 МПа – допускаемое напряжение кручения.
С целью обеспечения удобства соединения посредством МУВП быстроходного вала с валом электродвигателя 4А132М6УЗ выбранного в ходе кинематического расчета (см. п. 2.1. пп. 4) принимаем диаметр выходного конца быстроходного вала равным диаметру вала электродвигателя:
) Диаметр вала под подшипник.
t1 – высота буртика вала. dв1 = 38 мм t1 = 4 мм (рис 3.16 [1]).
Выбираем ближайшее большее значение кратное 5: dП1 = 50 мм.
) Диаметр упорной ступени вала.
) Диаметр вала под шестерней.
Диаметр вала под шестерней принимается равным диаметру выступов шестерни так как вал изготавливается слитно с шестерней.
Определяем диаметры ступеней промежуточного вала.
Выбираем ближайшее большее значение кратное 5: dП2 = 40 мм.
dП2 = 40 мм t2 = 4 мм (рис 3.16 [1]).
) Диаметр вала под колесом.
) Диаметр упорного буртика колеса.
Определяем диаметры ступеней тихоходного вала.
Принимаем ближайшее большее стандартное значение: dв3 = 55 мм (П35 [1]).
dв3 = 55 мм t3 = 48 мм (рис 3.16 [1]).
dП3 = 55 мм t2 = 48 мм (рис 3.16 [1]).
Выбираем ближайшее большее значение кратное 5: dП3 = 65 мм.
Определяем параметры эскизной компоновки.
Цель эскизной компоновки - определение положения элементов передач относительно опор (подшипников). Эскизная компоновка выполняется в соответствии с требованиями ЕСКД на миллиметровой бумаге формата А1 содержит одну проекцию – разрез по осям валов. Шестерня и колесо вычерчиваются в виде прямоугольников. Длина ступицы колеса принимается равной ширине венца и не выступает за пределы прямоугольника.
) Диаметры вершин зубьев колес.
d1 = 949 мм;d2 = 26511 мм; d3 = 8737 мм; d4 = 27265 мм.
) Ширина венцов колес.
b1 = 65 мм; b2 = 60 мм; b3 = 698 мм; b4 = 648 мм.
) Межосевые расстояния.
) Толщина стенки корпуса редуктора.
= 0025аw + 1 = 0025180 + 1 = 55 мм.
С целью выполнения условия ≥ 8 мм выбираем = 8 мм.
) Зазор между торцами шестерней и внутренней стенкой корпуса.
Δ1 = 12 = 128 = 96 мм.
) Зазор от окружностей вершин зубьев колес (шестерней) до внутренней стенки корпуса.
Если диаметр окружности вершин зубьев шестерни меньше наружного диаметра подшипника то Δ2 откладывается от наружного кольца подшипника.
) Зазор между днищем корпуса и поверхностью колес.
Δ0 ≥ 4 = 48 = 32 мм.
) Выбор подшипников.
Руководствуясь отношением Fa1Fr1 = Fa2Fr2 = Fa3Fr3 = Fa4Fr4 = 0996 ≤ 1 для обеих ступеней редуктора предварительно выбираем радиально-упорные шариковые подшипники средней серии (П35 [1]) и схему установки враспор (П36 [1]). Параметры подшипников средней серии выбираем по диаметрам dп1= 50 мм dп2 = 40 мм dп3 = 65 мм и заносим их в Табл. 3.
Табл. 3. Параметры подшипников.
) Расстояния от внутренней стенки корпуса до торцов подшипников.
V1 = 472 мс т.е. V1 > 2 мс (см. п. 2.2.6 пп. 1) Δ31 = 5 мм и смазывание подшипников быстроходной ступени осуществляется разбрызгиванием масла залитого в картер вращающимся зубчатым колесом.
V2 = 154 мс т.е. V2 2 мс (см. п. 2.3.6 пп. 1) Δ32 = 10 мм и смазывание подшипников осуществляется пластическим смазочным материалом.
) Расстояния от торцов подшипников до точек приложения их радиальных реакций.
) Расстояние между реакциями в опорах быстроходного вала 2l1 и тихоходного вала 2l2 (определяется измерением).
lТ = 171 мм (l3 = 905 мм l4 = 805 мм).
В приводах общего назначения рекомендуется применять МУВП – муфту упругую втулочно-пальцевую. Типоразмер муфты выбирается по диаметру концов соединяемых валов и расчетному вращающему моменту: Трас = кТ ≤ [T] Т – вращающий момент на соответствующем валу редуктора к – коэффициент учитывающий условия эксплуатации. Согласно исходным данным нагрузка постоянная следовательно к = 12.
) Муфта быстроходного вала.
Трас = кТ1 = 127234 = 8681 Нм концы валов короткие следовательно выбираем муфту МУВП 250-38-1.2 с длиной полумуфт l = 58 мм.
) Муфта тихоходного вала.
Трас = кТ3 = 12601 = 7212 Нм концы валов короткие следовательно выбираем муфту МУВП 1000-55-1.2 с длиной полумуфт l = 82 мм.
7. Определение опорных реакций. Построение эпюр
моментов. Проверочный расчет подшипников.
Расчетная схема тихоходного вала представлена на рис. 4.
Рис. 4. Расчетная схема тихоходного вала.
RCy + Fr4 – RDy = 5176 + 16115 – 21291 = 0.
RCz + Fм2 – Ft4 – RDz = 37689 + 30644 – 44086 – 24247 = 0.
Суммарные реакции в опорах:
FaC = 0; FaD = Fa4 = 16047 H.
Проверяем подшипники по наиболее нагруженной опоре (опоре с наибольшей эквивалентной нагрузкой РЭ). Эквивалентные нагрузки подшипников:
РЭС = (XVFrC + YFaC)kT kб;
РЭD = (XVFrD + YFaD)kT kб;
V = 1; kб = 13; kТ = 1.
Подшипники тихоходной ступени шариковые радиально-упорные e = 068; α = 26; Fa4VFr4 = 1604716115 = 0996 > 068 т.е. > е Х = 041; Y = (1– – X)е = (1 – 041)068 = 087 [П40 (1)].
РЭС = (04138043 + 0870) 13 = 20277 H;
РЭD = (04132268 + 08716047)13 = 35348 H.
РЭD > РЭC следовательно проверяем подшипники по опоре D.
Определяем расчетную долговечность подшипников и сравниваем с требуемой долговечностью заданной в техническом задании.
Сr3 = 113 кН = 113105 Н (см. табл. 3);
n2 = 340 обмин (см. п. 2.1 пп. 8).
LhТр = 10 лет = 87600 часов (см. тех. задание).
1. Конструктивная компоновка привода.
Цель конструктивной компоновки привода - конструктивное оформление деталей и узлов редуктора.
Конструктивная компоновка редуктора выполняется на миллиметровой бумаге формата А1 в масштабе 1:1. Согласно выбранной конструкции (см. «Проектный расчет валов») шестерни выполняются слитно с валами (вал - шестерня).
В ходе конструктивной компоновки определяются конструктивные параметры колес (Табл. 3.5. [1]) приведенные в Табл. 4.
Табл. 4. Конструктивные размеры колес.
da ≤ 500 мм – штампование da ≥ 500 мм - литье
Диаметр ступицы колеса
Диаметр центровой окружности
n = 05m – с округлением до стандартного значения (Табл. 3.6. [1])
Радиусы закруглений и уклоны
Длина выходных концов валов определяется длиной полумуфты. Конструктивно оформляются валы в местах установки ступиц подшипников мазеудерживающих и распорных колец выбираются фаски радиусы закруглений (галтели) размеры элементов сопряжений корпуса.
Размеры мазеудерживающих колец (используются на тихоходном валу).
а = 6 мм; t = 2 мм; α = 60º; b = 53 мм. (рис. 3.14 [1]).
dв1 = 38 мм с1 = 2 мм; dв2 = 40 мм с2 = 2 мм; dв3 = 55 мм с3 = 25 мм (рис. 3.15 [1]).
Радиусы закруглений (галтелей).
dв1 = 38 мм С11 = 25 мм R1 = 2 мм; dв2 = 40 мм С12 = 25 мм R2 = 2 мм; dв3 = 55 мм С13 = 3 мм R3 = 25 мм (рис. 3.16 [1]).
Размеры элементов сопряжений корпуса.
Δ = 8 мм Х = 3 мм; Y = 15 мм; R0 = 5 мм (Табл. 3.10 [1]).
Далее определяются конструктивные размеры крышек подшипников (Табл. 3.14. [1]) приведенные в Табл. 5.
Выбранные размеры крышек подшипников используются для определения конструктивных размеров корпуса редуктора (Табл. 3.8. [1]) приведенных в Табл. 6.
Табл. 6. Конструктивные размеры корпуса редуктора.
Толщина стенки корпуса и крышки редуктора
= 0025аw + 1; 1 = 002aw +1; ≥ 8 мм; 1 ≥ 8 мм.
Толщина верхнего пояса (фланца) корпуса
Толщина нижнего пояса (фланца) крышки корпуса
Толщина нижнего пояса корпуса (при наличии бобышки)
Толщина ребер основания корпуса
Толщина ребер крышки
Диаметр фундаментальных болтов (их число ≥ 4)
Диаметр болтов у подшипников
Диаметр болтов соединяющих основание корпуса с крышкой
Размеры определяющие положение болтов d2
Высота бобышки hб под болт d2
hб выбирается конструктивно так чтобы образовалась опорная поверхность под головку болта и гайку. Желательно у всех бобышек иметь одинаковую высоту hб
Диаметр отверстия гнезда подшипника
Dп – выбирается по наружному диаметру подшипника или стакана
Диаметр фланца гнезда подшипника
Dк = D2 + 5 где D2 – диаметр фланца крышки (табличное значение для выбранного подшипника)
Кроме того определяются размеры смотрового окна корпуса и крышки смотрового отверстия выбираемые конструктивно (Табл. 3.12. [1]). Указанные размеры приведены в Табл. 7.
Табл. 7. Размеры смотрового окна.
Размеры смотрового окна корпуса и крышки смотрового отверстия
Маслоуказатель выбирается жезловый (рис. 3.13 а [1]). Также выбираются размеры сливной пробки приведенные в Табл. 8.
Табл. 8. Размеры сливной пробки.
Размеры сливной пробки
2. Смазывание редуктора
В редукторах общего назначения для смазывания зубчатого зацепления применяется картерное смазывание (окунанием колеса в масло залитое внутрь корпуса) при окружной скорости колеса V ≤ 12мс (V2 = 472 мс V4 = 154 мс согласно п. 2.2.6 пп.1 и п. 2.3.6 пп. 1 соответственно). Зубчатое колесо погружается в масло на высоту зуба.
Объем масляной ванны редуктора определяется из расчета 05 08 л масла на 1кВт передаваемой мощности (P1 = 735 кВт Р2 = 713 кВт следова-тельно объемы масляных ванн быстроходной и тихоходной ступеней примерно одинаковы и равны 5 л). Сорт масла выбираем по табл. П45 [1]. Для обеих ступеней – И - 30А.
Подшипники быстроходной ступени смазываются разбрызгиванием масла из картера колесом (V2 = 472 мс > 2 мс). Подшипники тихоходной ступени смазываются пластичным смазочным материалом (консталин УТ-1 солидол УС-1) (V4 = 154 мс 2 мс). Смазочный материал набивается в подшипниковый узел при сборке на несколько лет.
3. Расчет шпоночных соединений
Для шпоночных соединений быстроходного вала с полумуфтой или шкивом и тихоходного вала с зубчатым колесом или полумуфтой принимаем призматические шпонки со скругленными концами. Размеры поперечных сечений шпонок и пазов для них выбираем по ГОСТу 23360-78 (П47 [1]).
Табл. 6. Параметры шпоночных соединений
Сечение шпонки bh мм
Глубина паза вала t1 мм
Глубина паза втулки t2 мм
Длины шпонок определяем по формуле l = lст – (5 10мм) согласуя со стандартным рядом где lст - длина ступицы детали соединяемой с валом (в случае присоединения муфты – длина полумуфты).
Согласно определенным параметрам шпоночных соединений записываем условные обозначения шпонок:
Шпонка №1: 10.8.50 ГОСТ 23360 – 78.
Шпонка №2: 16.10.70 ГОСТ 23360 – 78.
Шпонка №3: 20.12.100 ГОСТ 23360 – 78.
Шпонка №4: 16.10.80 ГОСТ 23360 – 78.
Проверяем прочность наиболее нагруженной шпонки – шпонки №4 на смятие по формуле:
[]см = 180 МПа (стр. 54 [1]);
Выбираем материал шпонок – сталь 45 термическую обработку - нормализация.
4. Уточненный расчет валов на прочность.
Цель уточненного расчета валов - определение коэффициентов запаса прочности в опасных сечениях валов сравнение их с допускаемым значением [s]=13 3.
Уточненный расчет будем производить для наиболее нагруженного из валов – тихоходного вала.
Для выбранного материала вала (сталь 40Х с термической обработкой – улучшение) определяем предел прочности: в = 790 МПа (П4 [1]). Предел выносливости при симметричном цикле изгиба для углеродистых сталей: -1 = 043в = 043790 = 3397 МПа. Предел выносливости при симметричном цикле касательных напряжений кручения: -1=058-1 = 058790 = 4582 МПа.
Расчетная схема тихоходного вала приведена на рис. 4. Уточненный расчет производим для опасного сечения – сечения А-А испытывающего максимальное напряжение т.е. сечения с наибольшим изгибающим моментом Му = 44873 Нм.
Коэффициент запаса прочности по касательным напряжениям определяем по формуле:
) а – амплитудное напряжение цикла m - среднее напряжение цикла:
) k - эффективный коэффициент концентрации напряжений. в 800 МПа k = 17 (П 50 [1]).
) - масштабный фактор. Сталь вала углеродистая dП3 70 мм = 065 (П 53 [1])
) П - коэффициент влияния шероховатости поверхности (П = 098 09 при Rа = 032 25мкм).
) - коэффициент чувствительности материала к асимметрии цикла (для углеродистой стали = 005).
Подставив полученные значения в формулу для расчета коэффициента запаса прочности по касательным напряжениям получим:
Суммарный изгибающий момент в сечении А-А:
Коэффициент запаса прочности по нормальным напряжениям изгиба:
) а – амплитуда цикла напряжений:
) m – среднее напряжение цикла:
) k = 18 т.к. в 800 МПа (П 50 [1] ).
) = 076 т.к. сталь вала углеродистая dП3 70 мм (П53 [1]).
) П = 098 09 при Rа = 032 25мкм.
) = 005 (для углеродистой стали).
Подставив полученные значения в формулу для расчета коэффициента запаса прочности по нормальным напряжениям получим:
Общий коэффициент запаса прочности:
5. Сборка редуктора.
Сборку производят в соответствии со сборочным чертежом редуктора. Сборка редуктора производится в следующей последовательности. Перед сборкой внутреннюю полость корпуса редуктора очищают и покрывают маслостойкой краской. На ведущий вал насаживают мазеудерживающие кольца и шариковые подшипники предварительно нагретые в масле до 80 1000С. На ведомый вал закладывают шпонку и напрессовывают зубчатое колесо до упора в буртик вала надевают распорную втулку мазеудерживающие кольца и устанавливают шариковые подшипники. Собранные валы устанавливают в основание корпуса редуктора и надевают крышку корпуса. Стыковые поверхности крышки и основания корпуса должны быть покрыты спиртовым лаком. Крышку центрируют с помощью двух конических штифтов и затягивают болтами. В подшипниковые камеры закладывают пластичную смазку и устанавливают крышки подшипников с металлическими прокладками для регулировки. В сквозные крышки перед постановкой закладывают манжетные уплотнения. Собранные валы проверяют на плавное проворачивание от руки и закрепляют крышки винтами. Затем ввертывают пробку маслоспускного отверстия с прокладкой и жезловый маслоуказатель. Заливают в корпус масло и закрепляют крышку смотрового люка болтами.
Собранный редуктор обкатывают и подвергают испытанию на стенде в соответствии с техническими условиями.
Разборка редуктора осуществляется аналогичным образом в обратном порядке.
Рабочая документация.
1. Разработка сборочного чертежа редуктора.
Сборочный чертеж редуктора выполняется в одной - горизонтальной проекции с необходимыми местными разрезами на основании разработанной конструкторской компоновки. На сборочном чертеже указаны следующие размеры:
- габаритные (по предельным внешним очертаниям);
- присоединительные (диаметр и длина концевого участка быстроходного и тихоходного валов);
- посадочные (размеры сопрягаемых поверхностей с указанием по-
- главный параметр редуктора (межосевые расстояния аw зубчатых
В соответствии со спецификацией указаны номера позиций всех сборочных единиц и деталей редуктора. Номера располагаются на полках-выносках параллельных основной надписи на одной горизонтальной или вертикальной линии и одном расстоянии от контура чертежа (не менее 30 мм). Под полкой-выноской деталей зубчатых передач указаны число зубьев (z) и модуль (m).
Над основной надписью чертежа указаны технические характеристики редуктора:
Частота вращения быстроходного вала.
Частота вращения тихоходного вала.
Вращающий момент на тихоходном валу;
Кроме того могут указываться технические требования например:
Валы собранного редуктора должны проворачиваться без толчков и заеданий.
Осевой зазор радиально-упорных подшипников быстроходного и тихоходного валов обеспечить в пределах 03 05мм.
Смазка картерная. Для обеих ступеней - масло индустриальное И-30А ГОСТ 20799-75; общий объем заливаемого масла 10 л.
2. Разработка чертежа общего вида привода.
Чертеж общего вида привода содержит фронтальную проекцию привода дающую полное представление о его конструкции. Элементы привода вычерчены без мелких подробностей но так чтобы их изображение было ясным и четким с необходимыми размерами. На чертеже общего вида привода указаны следующие данные:
- позиции узлов деталей и изделий;
- габаритные присоединительные и установочные размеры.
3. Разработка рабочих чертежей деталей.
Рабочие чертежи деталей содержат минимальное количество проекций видов разрезов и сечений достаточное для понимания формы детали и простановки размеров.
Все детали типа тел вращения (валы колеса и т.п.) расположены на чертеже так что их оси параллельны основной надписи чертежа независимо от их рабочего положения.
На рабочем чертеже детали указаны исчерпывающие данные необходимые для ее изготовления и контроля:
- предельные отклонения (допуски) на посадочные и цепные раз-
- предельные отклонения формы и взаимного расположения поверхностей ( П55-П58 [1]);
- допустимые величины шероховатости поверхности ( П59 П60 [1]);
- технические требования (твердость материала формовочные и
штамповочные уклоны радиусы размеры для справки неуказанные
предельные отклонения размеров: отверстий + t валов – t остальных
± t2 среднего (грубого точного) класса точности и др.);
- таблица основных геометрических параметров для деталей зубчатых передач.
Спецификации сборочного чертежа редуктора и чертежа общего вида выполнены по стандартной форме. Разделы спецификации располагаются в следующем порядке:
) стандартные изделия.
В.Н. Горелов Е.К. Кичаев И.А. Кокорев. Курсовое проектирование деталей машин: учеб.пособ. - Самара. Самар. гос. техн. ун-т 2009. - 250 с.
Иванов М.Н. Детали машин: учебник М.Н. Иванов В.А. Финогенов. -
М.: Высш.шк. 2005. - 408 с.
Решетов Д.Н. Детали машин: учебник для машиностроит. и мех. спец. вузов Д.Н. Решетов. - М.: Машиностроение 1989. - 496 с.
Чернавский С.А. Курсовое проектирование деталей машин: учеб. пособ. для техникумов С.А. Чернавский К.Н. Боков и др. - М.: Машиностроение 1988. - 415 с.
Шейнблит А.Е. Курсовое проектирование деталей машин: учеб. пособ. А.Е. Шейнблит. - Калининград: Янтарный сказ 2005. - 455 с.
Техническое задание .. .2
1. Выбор двигателя. Кинематический и силовой расчет привода . ..4
2. Расчет быстроходной ступени редукторной передачи . 6
3. Расчет тихоходной ступени редукторной передачи 13
4. Нагрузка валов редуктора . .20
5. Проектный расчет валов. Эскизная компоновка редуктора 22
7. Определение опорных реакций. Построение эпюр моментов. Проверочный расчет подшипников .26
Эскизный проект . ..28
1. Конструктивная компоновка привода .28
2. Смазывание редуктора ..32
3. Расчет шпоночных соединений . 33
4. Уточненный расчет валов на прочность 34
5. Сборка редуктора 36
Рабочая документация ..37
1. Разработка сборочного чертежа редуктора . 37
2. Разработка чертежа общего вида .38
3. Разработка рабочих чертежей деталей 38
Список литературы 40
Фронтальный вид.cdw

Спецификация ОВ.spw

Рекомендуемые чертежи
- 09.07.2014
- 24.04.2014