Привод ленточного конвейра с двухступенчатым цилиндрическим редуктором




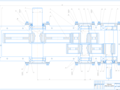
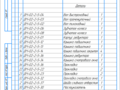
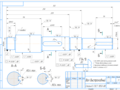
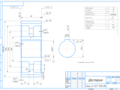
- Добавлен: 24.01.2023
- Размер: 610 KB
- Закачек: 0
Описание
Привод ленточного конвейра с двухступенчатым цилиндрическим редуктором
Состав проекта
![]() |
![]() |
![]() |
![]() |
![]() |
![]() ![]() ![]() ![]() |
![]() |
![]() ![]() ![]() ![]() |
![]() |
![]() |
![]() |
![]() |
![]() ![]() ![]() |
![]() ![]() ![]() ![]() |
![]() ![]() ![]() ![]() |
![]() ![]() ![]() ![]() |
Дополнительная информация
А3 Шестерня.cdw

Спецификация.spw

А3 Чертеж 1го вала.cdw

А1Чертеж СБ вид сбоку.cdw

А1 Чертеж СБ вид сверху.cdw

Рекомендуемые чертежи
- 24.01.2023