Привод главного движения токарно-винторезного станка





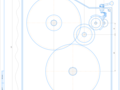

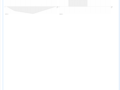
- Добавлен: 25.01.2023
- Размер: 2 MB
- Закачек: 0
Описание
Состав проекта
![]() |
![]() |
![]() ![]() ![]() ![]() |
![]() |
![]() ![]() ![]() ![]() |
![]() ![]() ![]() |
![]() ![]() |
![]() ![]() ![]() |
![]() ![]() ![]() |
![]() ![]() |
![]() ![]() |
![]() ![]() |
![]() ![]() ![]() ![]() |
![]() ![]() ![]() |
![]() ![]() ![]() ![]() |
![]() ![]() ![]() ![]() |
![]() ![]() ![]() |
![]() ![]() |
![]() ![]() ![]() ![]() |
![]() ![]() ![]() ![]() |
![]() ![]() ![]() |
Дополнительная информация
Развертка X1.cdw

схема 4.cdw

График радиальных сил в гориз. пл.
График изгибающих моментов в верт. пл.
График изгибающих моментов в гориз. пл
График крутящих моментов
вал 1.frw

5-й вал (готовый).frw

3-й вал (готовый).frw

Схема 1.cdw

График радиальных сил в гориз. пл.
График изгибающих моментов в верт. пл.
График изгибающих моментов в гориз. пл
График крутящих моментов
4-й вал.frw

схема 2.cdw

График радиальных сил в гориз. пл.
График изгибающих моментов в верт. пл.
График изгибающих моментов в гориз. пл
График крутящих моментов
схема 3.cdw

График радиальных сил в гориз. пл.
График изгибающих моментов в верт. пл.
График изгибающих моментов в гориз. пл
График крутящих моментов
5-й вал.frw

схема 5.cdw

График радиальных сил в гориз. пл.
График изгибающих моментов в верт. пл.
График изгибающих моментов в гориз. пл
График крутящих моментов
Свёртка X1.cdw

Записка КИМ Французов.docx
Проект разработал Французов Е.И. под руководством ассистента кафедры «ТиОМП» А.И. Костюченко.
Объектом курсового проектирования является универсальный токарно-винторезный станок для обработки конструкционных сталей точения наружных и внутренних поверхностей нарезания метрической резьбы.
пояснительной записки 89 страниц;
графической части 3 листа формата А1.
В развитии технологии обработки металлов резанием происходят принципиальные изменения. Интенсификация технологических процессов на основе применения новых конструкций режущих инструментов режущих инструментов из новых инструментальных материалов повышение размерной и геометрической точности достигаемой при обработке таков неполный перечень важнейших направлений развития механической обработки в машиностроении.
Эффективность производства его технический прогресс качество выпускаемой продукции во многом зависит от опережающего развития производства нового оборудования машин станков аппаратов от всемерного внедрения методов технико-экономического анализа. Существующий парк станков насчитывающий в настоящее время около четырех тысяч различных моделей не удовлетворяет все расширяющиеся запросы потребителей. Следовательно в будущем разнообразие станков будет все время увеличиваться и обновляться. В общем количестве станков кроме количественных происходят и качественные изменения. В современных станках широко используются как механические так и электрические гидравлические пневматические и другие устройства что приводит к усложнению их конструкции. В конструкции машин необходимо соблюдать требования технической эстетики. Машины должны иметь красивый внешний вид изящную строгую отделку.
Первоначальной базой той или иной конструкции станка является кинематическая структура станка выражаемая кинематической схемой так как назначением станка является создание относительных движений режущего инструмента и заготовки необходимых для получения в процессе резания заданных поверхностей. Следовательно и при конструировании и при эксплуатации нужно прежде всего знать кинематическую структуру станка.
Развитие производственного оборудования предполагает решение вопросов выбора и оптимизации технических характеристик станка проектирования кинематической схемы станка и его узлов обоснование выбранных конструктивных вариантов. Проектируя машину конструктор должен добиваться всемерного увеличения ее рентабельности и повышения экономического эффекта за весь период работы. Данный проект направлен на решение таких задач.
ОПРЕДЕЛЕНИЕ ТЕХНИЧЕСКИХ ХАРАКТЕРИСТИК СТАНКА
1 Основные сведения о токарно-винторезных станках методах обработки и применяемом инструменте.
Токарно-винторезные станки предназначены для обработки деталей типа тел вращения (валов дисков осей пальцев цапф фланцев колец втулок гаек муфт и др.) а также нарезания резьбы. Однако бывают станки без ходового винта. На таких станках можно выполнять все виды токарных работ кроме нарезания резьбы резцом. Техническими параметрами по которым классифицируют токарно-винторезные станки являются наибольший диаметр D обрабатываемой заготовки (детали) или высота центров над станиной (равная 05 D) наибольшая длина L обрабатываемой заготовки (детали) и масса станка. Ряд наибольших диаметров обработки для токарно-винторезных станков имеет вид: D = 100 125 160 200 250 320 400 500 630 800 1000 1250 1600 2000 и далее 4000 мм. В данном случае для моего станка это значения составляет 320 мм. Наибольшая длина L обрабатываемой детали определяется расстоянием между центрами станка. Выпускаемые станки при одном и том же значении D могут иметь различные значения L. По массе токарные станки делятся на легкие - до 500 кг (D = 100 - 200 мм) средние - до 4 т (D = 250 - 500 мм) крупные - до 15 т (D = 630 - 1250 мм) и тяжелые - до 400 т (D = 1600 - 4000 мм).
На средних станках производится 70 - 80% общего объема токарных работ. Эти станки предназначены для чистовой и получистовой обработки а также для нарезания резьбы разных типов и характеризуются высокой жесткостью достаточной мощностью и широким диапазоном частот вращения шпинделя и подач инструмента что позволяет обрабатывать детали на экономичных режимах с применением современных прогрессивных инструментов из твердых сплавов и сверхтвердых материалов. Средние станки оснащаются различными приспособлениями расширяющими их технологические возможности облегчающими труд рабочего и позволяющими повысить качество обработки и имеют достаточно высокий уровень автоматизации.
В основном для обработки заготовок (деталей) на токарных станках применяются токарные резцы также используются сверла зенкера и развертки. Основные операции производимые на токарных станках и применяемый инструмент приведены на рис. 1.1.
Рис 1.1. Основные виды токарных работ:
а – обработка наружных цилиндрических поверхностей б – обработка наружных конических поверхностей в – обработка торцов и уступов г – вытачивание пазов и канавок отрезка заготовки д – обработка внутренних цилиндрических и конических поверхностей е – сверление зенкерование развертывание отверстий ж – нарезание наружной резьбы з – нарезание внутренней резьбы и – обработка фасонных поверхностей к – накатывание рифлений; 1проходной прямой резец; 2— проходной упорный резец 3— проходной отогнутый резец; 4— отрезной резец; 5— канавочный резец;6— расточной резец; 7— сверло; 8— зенкер; 9— развертка; 10— резьбовой резец; 11— метчик; 12— фасонный резец; 13— накатка (стрелками показаны направления перемещения инструмента вращения заготовки).
Снятие стружки с поверхности вращающейся заготовки осуществляется режущим инструментом. Все способы обработки металлов основанные наудалении припуска и превращении его встружку определяются понятием резание металла. Для успешной работы необходимо чтобы процесс резания протекал непрерывно и быстро. Форма обрабатываемой детали обеспечивается содной стороны относительным движением заготовки и инструмента с другой — геометрией инструмента. Процесс резания возможен при наличии основных движений: главного движения — вращения заготовки ипоступательного движения резца называемого движением подачи которое может совершаться вдоль или поперек изделия атакже под постоянным или изменяющимся углом коси вращения изделия.
2 Анализ способов формообразования обрабатываемых поверхностей.
Главное движение В1 – вращение заготовки движение подачи П1 и П2 – поступательное движение инструмента
Главное движение В1 – вращение заготовки движение подачи П1 – поступательное движение инструмента
Главное движение В1 – вращение заготовки движение подачи П1 – возвратно поступательное движение инструмента
Главное движение В1 – вращение заготовки движение подачи П1 – поступательное движение инструмента (в жесткой кинематической связи с вращением шпинделя)
3 Разработка структурной схемы станка.
Проанализировав способы формообразования обрабатываемых поверхностей принимаю следующую компоновку токарно-винторезного станка:
Рис 1.3 Структурная схема проектируемого станка
М – двигатель; Д – делитель для нарезания многозаходной резьбы; Р – реверс; is – настройка на подачу.
Движение В1П2 является движением формообразования(движение скорости резания). Для создания траектории этого движения соединяются подвижные звенья исполнительных пар жесткой кинематической связью в виде штриховой линии 1 – 2.
Эта связь накладывает условия ограничения на шпиндель и суппорт не позволяя им занимать произвольное положение относительно друг друга и иметь произвольные скорости.
Кинематическая связь включая передачу винт-гайка преобразующую вращательное движение в поступательное соединяющая между собой суппорт и шпиндель создает потенциальную возможность винтового движения. Для реализации этой возможности соединяют кинематическую связь 1 – 2 подобной кинематической связью 3 – 4 с источником энергии движения. При включении электродвигателя энергия движения по кинематической цепи 3 – 4 будет сообщаться через звено 3 в кинематическую связь 1 – 2.
Это вызовет вращение шпинделя и продольное перемещение суппорта. В итоге резец будет совершать относительное заготовки винтовое движение. При этом соотношение элементарных движений В1 и П2 зависит только от передаточного отношения кинематической связи 1 – 2. Следовательно эта связь обеспечивает качественную характеристику движения Фv т.е. его траекторию. Т.о. кинематическая связь воспроизводящая траекторию исполнительного движения называют внутренней связью. Количественную характеристику исполнительного движения т.е. его скорость обеспечивает кинематическая связь 3 – 4 и называется внешней связью.
РАЗРАБОТКА (ИЛИ ВЫБОР) И ОПИСАНИЕ КОМПОНОВКИ СТАНКА
По заданию необходимо разработать или выбрать компоновку станка. Анализ схем обработки и разработка структурной схемы станка предполагает что компоновка проектируемого станка будет иметь классический вид компоновки токарно-винторезного станка.
Рис. 2.1 Компоновка проектируемого станка
Звено 1 – шпиндель совершает главное движение процесса обработки В1 (вращательное); звено 2 – задняя бабка (пиноль) совершает вспомогательное движение процесса обработки П4 (возвратно поступательное вдоль обрабатываемой заготовки); звено 3 – суппорт совершает вспомогательное движение в процессе обработки П1 (возвратно поступательное вдоль обрабатываемой заготовки); звено 4 – резцедержатель совершает вспомогательное движение в процессе обработки П2 и П3(возвратно поступательное вдоль и поперек обрабатываемой заготовки).
КИНЕМАТИЧЕСКИЙ РАСЧЕТ ПРИВОДА
Определяем диапазон регулирования скорости исполнительного органа по формуле:
Простая множительная структура возможна при таким образом простая множительная структура невозможна.
Определяем количество ступеней скорости исполнительного органа по формуле:
Пользуясь ОСТ2.Н11-1-75 принимаем значения ряда ступеней скоростей: 31.5 45 63 90 125 180 250 355 500 710 1000 1400 2000 2800.
Структура привода для Z=14 не расписывается поэтому структурная формула привода будет с перекрытием и определится:
Проверяем возможность применения простой множительной структуры. Простая множительная структура возможна при условии для последней в порядке переключения группы: . Для нашего варианта: следовательно вариант осуществим.
По полученной формуле структуры строим структурную сетку привода – рис.3.1.
Рис.3.1. Структурная сетка привода
В соответствии с компоновкой привода руководствуясь структурной сеткой рисуем кинематическую схему привода – рис.3.2.
Рис.3.2. Кинематическая схема привода
В соответствии со структурной сеткой строим график частот вращения – рис.3.3.
Определяем передаточное отношение передач привода:
Определяем числа зубьев колес привода.
Первая группа определяем число зубьев по [? стр. 99 табл.4.3]:
Наименьшее общее кратное . Принимаем множитель . Тогда сумма зубьев первой группы .
Третья группа определяем число зубьев по [? стр.99 табл.4.3]:
Рис.3.3. График частот вращения привода
ДИНАМИЧЕСКИЕ И ПРОЧНОСТНЫЕ РАСЧЕТЫ УЗЛОВ РАЗРАБАТЫВАЕМЫХ КОНСТРУКЦИЙ
1 Расчет мощности двигателя и определение крутящих моментов
Необходимо отметить что при динамическом расчете привода главного движения максимальный крутящий момент на выходе коробки скоростей определяется не по номинальной а по расчетной частоте его вращения принимаю частоту расположенную в середине диапазона регулирования скоростей также принимаем частоты на валах:
Мощность на первом валу коробки скоростей определяется по формуле:
Т.к. первый вал является валом электродвигателя то
где - мощность электродвигателя
- КПД соответственно электродвигателя ременной передачи пары подшипников .
Таким образом мощность и угловая скорость на первом валу:
Наибольший крутящий момент:
Для того чтобы определить крутящие моменты на валах II III и IV коробки скоростей необходимо найти мощности и угловые скорости на этих валах:
Крутящие моменты на валах II III и IV:
2 Расчет ременной передачи
2.1 Расчет первой ременной передачи
Коэффициент режима работы:
[1 табл. 7.4 стр. 122 ]
Расчетный момент на быстроходном валу:
При значении момента 29.857 Нм в соответствии с рекомендацией принимаем ремень сечения К.
Диаметр меньшего шкива по формуле [1 (7.33) стр. 143]:
По [1 табл. 7.14 стр. 141] принимаем ближайший
Диаметр ведомого шкива
По [ 1 табл. 7.14 стр. 141] принимаем ближайший
Определяем необходимое число клиньев см. рис [ 1 (7.7) стр. 144]
Принимаем число клиньев .
При межосевое расстояние
Длина ремня по формуле [ 1 (7.7) стр. 121]
Принимаем по [ 1 табл. 7.13 стр. 140] .
Условное обозначение ремня: 1250 К 20 РТМ 38-40528-74.
Межосевое расстояние выверенное по принятой длине ремня
Угол обхвата на малом шкиве
Усилие действующее на вал
Ширина шкивов [1 табл. 7.14 стр. 141]
2.2 Расчет второй ременной передачи
При значении момента 406.263 Нм в соответствии с рекомендацией принимаем ремень сечения Л.
Диаметр меньшего шкива по формуле [ 1 (7.33) стр. 143]:
Определяем необходимое число клиньев [см. рис 7.7 стр. 144]
Длина ремня по формуле [(7.7) стр. 121]
Принимаем по [табл. 7.13 стр. ] .
Условное обозначение ремня: 2000 Л 6 РТМ 38-40528-74.
Ширина шкивов (табл. 7.14 стр. 141)
3РАСЧЕТ ЗУБЧАТЫХ ПЕРЕДАЧ
3.1 Выбор материала и проверка на прочность зубчатых колес
3.2 Расчет прямозубых передач
Предварительный расчет выполняем по формуле [4 (10.18) стр. 185]
где Kd = 780 МПа стр. 186 по рекомендации [4 табл. 10.8 стр. 186] принимаем bd = 0.6 по графику[4 рис. 10.21 стр.180] KH = 1.07
Рабочая ширина колес
Выбираем m – по рекомендации табл. 10.9 принимаем m = 10
По [4 табл. 10.1 стр. 160] по ГОСТ 9563-60 принимаем m = 2.
Предварительно определяем:
По [4 табл. 10.1 стр. 160] по ГОСТ 9563-60 принимаем m = 3.
По [4 табл. 10.1 стр. 160] по ГОСТ 9563-60 принимаем m = 4 (в виду конструктивных особенностей).
Основные размеры и характеристики зубчатых колес
Ширина зубчатых венцов мм
Выбор материала валов.
Выбираем для валов Сталь 45 ГОСТ 1050-88 термообработка
нормализация + отпуск НВ 230 – 285.
1 Предварительный расчет валов
Диаметры валов определяем по условному расчету на кручение
где Т – крутящий момент Нмм;
[k] = 20 30 – допускаемое напряжение на кручение МПа.
Предварительные диаметры валов:
Принимаем диаметр равным 30 мм
Принимаем диаметр равным 40 мм
Принимаем диаметр равным 50 мм
2 Проектировочный расчет вала 1
Вал передает момент [6 (11.1)]
В зацеплении со стороны шестерни действуют силы:
радиальная [6 (11.3)]
Нагрузка изгибающая вал в ременной передачи определяется по формуле [6 (9.15)]:
Опорные реакции в вертикальной плоскости:
Опорные реакции в горизонтальной плоскости:
в вертикальной плоскости
в горизонтальной плоскости
Суммарный изгибающий момент в сечении под шестерней (это самое нагруженное сечение) [6 (11.20)].
Эквивалентный момент [2 (3.24)]
Диаметр в рассчитываемом сечении (опасном) [2 (3.25)].
Окончательно принимаем по ГОСТ 6636-69 диаметр вала d = 32 мм.
Диаметр выходного конца вала [6 (11.21)]
Окончательно принимаем по ГОСТ 6636-69 диаметр выходного конца вала dк =24 мм.
dп =25 мм – диаметр участка вала под подшипники.
Производим проверочный расчет вала на выносливость для опасного сечения. В сечении действует наибольший изгибающий момент М и крутящий момент Т.
Момент сопротивления сечения вала [6 (11.22)]
Амплитуда номинальных напряжений изгиба при симметричном цикле изменения напряжений изгиба [6 (11.23)]
Коэффициент безопасности в сечении по изгибу [6 (11.24)]
где К – эффективный коэффициент концентрации напряжений для вала в месте шпоночного паза [6 табл. 11.8];
– коэффициент учитывающий упрочнение поверхности [6 табл. 11.6];
– масштабный фактор в зависимости от диаметра вала [6 табл. 11.5];
= 0.12 – коэффициент характеризующий чувствительность материала к асимметрии цикла изменения напряжений для среднеуглеродистых сталей;
m = 0 – постоянная составляющая цикла изменения напряжений (при симметричном цикле изменения напряжений изгиба равна нулю).
Определяем коэффициент безопасности по кручению. Полярный момент сопротивления по опасному сечению
При нереверсивном вращении вала напряжения кручения изменяются по пульсирующему циклу поэтому переменные составляющие (амплитуды) и постоянные составляющие (среднее напряжение) цикла
Коэффициент безопасности в сечении по кручению
– коэффициент учитывающий состояние поверхности [табл. 11.6];
Общий коэффициент безопасноти по усталостной прочности для сечения [6 (11.28)]
Условие прочности выполняется.
3 Проектировочный расчет второго вала 2
Суммарный изгибающий момент в сечении под колесом (это самое нагруженное сечение).
Эквивалентный момент
Диаметр в рассчитываемом сечении (опасном).
Окончательно принимаем по ГОСТ 6636-69 диаметр вала d = 48 мм.
dп = 40 мм – диаметр участка вала под подшипники.
Момент сопротивления сечения вала
Амплитуда номинальных напряжений изгиба при симметричном цикле изменения напряжений изгиба
Коэффициент безопасности в сечении по изгибу
где К – эффективный коэффициент концентрации напряжений для вала в месте шпоночного паза [табл. 11.8];
– коэффициент учитывающий упрочнение поверхности [табл. 11.6];
– масштабный фактор в зависимости от диаметра вала [табл. 11.5];
4 Проектировочный расчет второго вала 3
Окончательно принимаем по ГОСТ 6636-69 диаметр вала d = 54 мм.
dп = 45 мм – диаметр участка вала под подшипники.
5 Проектировочный расчет второго вала 4
Окончательно принимаем по ГОСТ 6636-69 диаметр вала d = 60 мм.
dк = 42 мм – диаметр конца вала
dп = 50 мм – диаметр участка вала под подшипники.
6 Подбор шпоночных соединений
Принимаем материал шпонки Сталь 45 с
Для соединения этого вала со шкивом подбираем шпонку по [7 табл. 4.64 стр. 235] с размерами b × h = 8 × 7 t1 = 4 – глубина паза вала.
Из условия прочности определяем lр
Принимаем по ГОСТ 23360-78 для соединения вала 1 со шкивом призматическую шпонку 8 × 7 × 28 мм
Для соединения этого вала подбираем шпонку по [7 табл. 4.64 стр. 235] с размерами b × h = 14 × 9 t1 = 5.5 – глубина паза вала.
Принимаем по ГОСТ 23360-78 для соединения вала 2 с колесами призматическую шпонку 14 × 9 × 36 мм.
Для соединения этого вала подбираем шпонку по [7 табл. 4.64 стр. 235] с размерами b × h = 12 × 8 t1 = 5 – глубина паза вала.
Принимаем по ГОСТ 23360-78 для соединения вала с колесами призматическую шпонку 12 × 8 × 32 мм
7 Подбор шлицевых соединений
Для соединения этого вала подбираем шлицевое соединение по [дет.маш табл. 8.11 стр. 172] с размерами z × d × D = 6 × 28 × 32
Расчетная поверхность
Для соединения этого вала подбираем шлицевое соединение по [дет.маш табл. 8.11 стр. 172] с размерами z × d × D = 8 × 42 × 48
Для соединения этого вала подбираем шлицевое соединение по [дет.маш табл. 8.11 стр. 172] с размерами z × d × D = 8 × 46 × 54
Для соединения этого вала подбираем шлицевое соединение по [дет.маш табл. 8.11 стр. 172] с размерами z × d × D = 8 × 52 × 60
1 Расчет подшипников для первого вала привода
Определяем реакции опор [6 (12.1) (12.2)]
Желаемая долговечность L = 3500 ч.. Температура в подшипнике не превышает 100. КЕ = 0.63.
Предварительно принимаем шариковый радиальный подшипник 105 ГОСТ 8338-75.
Для этих подшипников определяем по [2 табл. 5.33 стр. 156] динамическую Cr = 11.2 кН и статическую Cor = 5.6 кН грузоподъемности.
Находим эквивалентную нагрузки [6 (12.3 (12.4) (12.5)]
Расчет производим для первой опоры как более нагруженной Fr = Fr1
Определяем отношение
Определяем отношение V = 1 при вращении внутреннего кольца.
При для шариковых радиальных подшипников окончательно принимаем X = 1 и Y = 0.
Эквивалентная динамическая радиальная нагрузка [6 (12.5)]
где K = 1.4 – коэффициент безопасности [6 табл. 12.2];
KT = 1 – температурный коэффициент [6 табл. 12.3].
Требуемая динамическая грузоподъемность [6 (12.6)]
р = 3 – для шариковых подшипников.
Стр = 9.45 кН Cr = 11.2 кН
Выбранный подшипник подходит.
2 Расчет подшипников для второго вала привода
Предварительно принимаем шариковый радиальный подшипник 108 ГОСТ 8338-75.
Для этих подшипников определяем по [2 табл. 5.33 стр. 156] динамическую Cr = 16.8 кН и статическую Cor = 9.3 кН грузоподъемности.
Расчет производим для второй опоры как более нагруженной Fr = Fr2
Стр = 6.303 кН Cr = 16.8 кН
3 Расчет подшипников для третьего вала привода
Предварительно принимаем шариковый радиальный подшипник 109 ГОСТ 8338-75.
Для этих подшипников определяем по [2 табл. 5.33 стр. 156] динамическую Cr = 21.2 кН и статическую Cor = 12.2 кН грузоподъемности.
Стр = 7.736 кН Cr = 21.2 кН
4 Расчет подшипников для четвертого вала привода
Предварительно принимаем шариковый радиальный подшипник 111
Для этих подшипников определяем по [2 табл. 5.33 стр. 156] динамическую Cr = 28.1 кН и статическую Cor = 17.0 кН грузоподъемности.
Стр = 6.089 кН Cr = 28.1 кН
ОПИСАНИЕ КОНСТРУКЦИИ ДЛЯ СПРОЕКТИРОВАННЫХ УЗЛОВ
В данном курсовом проекте необходимо было спроектировать токарно-винторезный станок максимальный диаметр детали над станиной у которого 320 мм.
Коробка скоростей представляет собой совокупность передач при помощи которых можно передать 16 частот вращения начиная от 31.5 мин-1 до 2800 мин-1. В коробке скоростей установлены шлицевые валы -шестерни на которые насажены единичные и блочные передачи. Всего в коробке один блок состоящий из трех колёс и восьми одиночных колёс.
Так как компоновка станка не отличается от компоновки станка – прототипа то все остальные конструктивные элементы и узлы взяты из него.
Основное назначения системы смазки коробки скоростей и коробки подач сводится к уменьшению потерь мощности на трение сохранению точности работы предотвращению вибрации снижению интенсивности износа трущихся поверхностей а также к предохранению их от заедания задирав и коррозии.
В качестве смазочных материалов для подшипников возможно применение масла индустриального 20 (веретенное 3) или турбинного 30 (турбинное УТ) т.к. диаметры валов под подшипники не превышают 60 мм а число оборотов составляет 2800 мин-1.
В качестве смазочных материалов для зубчатых передач применяют жидкие минеральные масла. Выбор сорта минерального масла производится в зависимости от условий работы коробки скоростей и коробки подач передаваемой мощности окружной скорости в зацепление а также температуры масла в картере коробок.
Также значение имеет вязкость чем она меньше тем выше окружная скорость т.к. в спроектированной коробке скоростей окружная скорость не превышает 25 мс то принимаем масло цилиндровое 24 (вискозин).
Кроме вязкости масла на выбор смазки зубчатых колёс большое влияние оказывает его маслянистость – способность образовывать на поверхности трение прочные абсорбированные плёнки с пониженным сопротивление сдвига.
Учёт маслянистости при выборе масла обеспечивает минимальный износ зубчатых передач т.к. удельное давление при скорости 25-5 мс составляет 1-5 кгмм2 то выбранный сорт масла цилиндровое 24 (вискозин) удовлетворяет нашим условиям.
Все передачи и подшипники расположенные в общем корпусе целесообразно обслуживать от одно централизованной системы смазки что позволяет применить один и тот же смазочный материл.
В спроектированном станке применяем картерную систему смазки когда масло из общей ванны увлекается и разбрызгивается зубчатыми передачами образующийся при этом туман смазывает размещённые внутри коробки подшипники и передачи. Кроме того масло стекая по стенкам корпуса также попадает на подшипники качения. Зубчатое колесо разбрызгивающее масло не должно быть слишком глубоко погружено в ванну т.к. излишне высокий уровень заливки масла приводит к потерям мощности и перегреву всей системы. Зубчатые цилиндрические колёса достаточно нагружать в масло наполовину высоты зуба.
ОПИСАНИЕ СИСТЕМЫ УПРАВЛЕНИЯ СТАНКОМ
Главным движение в станке является вращение шпинделя которое он получает от электродвигателя мощностью 5 кВт через поликлиновую передачу со шкивами 90 мм и 180 мм коробку скоростей и еще одну поликлиновую передачу со шкивами 224 мм и 224 мм. Вращение шпинделя осуществляется по следующей цепи зубчатых колёс: 19-53 или 24-48или 30-42 или 36-36 на вал III затем через колёса 20-40 или 40-20 движение передаётся на вал IV а затем через зубчатые передачи либо 19-53 либо 53-19 движение передаётся на шпиндель V. Переключая блоки колёс можно получить 16 вариантов зацепления.
Движение подачи: механизм подачи сообщает движение суппорту по четырём кинематическим цепям: винторезной продольной и поперечной подачи быстрого перемещения.
Продольная и поперечная подачи осуществляются путём ряда зубчатых колёс и блоков на ходовой вал.
В ходе курсового проектирования был спроектирован привод главного движения токарно-винторезного станка. Он удовлетворяет поставленным требованиям т.е. диапазон частот регулирования мощность электродвигателя и раздельность привода главного движения.
Проектирование производилось на базе токарно-винторезного станка 1А616 соблюдением конструкционных особенностей и сохранением коробки подач станка. В итоге спроектированный станок можно отнести к средним станкам.
СПИСОК ИСПОЛЬЗОВАННОЙ ЛИТЕРАТУРЫ
Курсовое проектирование деталей машин: Учеб. пособие С.А. Чернавский К.Н. Боков и др. – 2-е изд. перераб. и доп. – М.: Машиностроение 1988 – 416с.
Курсовое проектирование деталей машин: Справ. пособие. В 2-ух частях. В. Кузьмин Н. Н. Макейчик и др. – Мн.: Выш. школа 1982.
Конструирование узлов и деталей машин: Учеб. пособие для машиностроит. спец. вузов. – 4-е изд. Дунаев П. Ф. Леликов О. П. – М.: Выш. шк. 1985.
Детали машин. Учебник для вузов. Изд. 3-е доп. и перераб. Иванов М. Н. – М Высш. школа 1976.
Проектирование. Детали машин. 2-е изд. доп. и перераб. Курмаз Л. В. Скойбеда А. Т. – Мн. УП «Технопринт» 2002.
Практикум по курсам «Детали машин» Детали машин и подъемно-транспортные устройства» для студентов спец. 1-36 01 01 1-36 01 03 и др. А. Л. Лисовский Н. Л. Кравченко Т. В. Вигерина – УО «ПГУ» 2006.
Допуски и посадки. Справочник. В 2-х ч.В.Д. Мягков М.А. Палей и др. – 6-е изд. перераб. и доп. – Л.: Машиностроение Ленингр. отд-ние 1983. Ч. 2. 448 с.
Рекомендуемые чертежи
- 10.02.2022
- 29.05.2022