Организация производственного процесса КПП трактора Беларус-1221


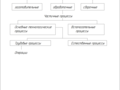
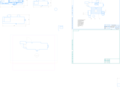
- Добавлен: 25.01.2023
- Размер: 229 KB
- Закачек: 0
Описание
Состав проекта
![]() |
![]() |
![]() |
![]() ![]() |
![]() ![]() ![]() ![]() |
![]() ![]() ![]() |
![]() ![]() ![]() ![]() |
![]() ![]() ![]() |
![]() ![]() ![]() |
![]() ![]() ![]() |
![]() ![]() ![]() |
Дополнительная информация
Схема производственного процесса.cdw

Производственный процесс ремонта на РП
Фазы производственного процесса
Естественные процессы
Титульник.doc
УО «БЕЛОРУССКИЙ ГОСУДАРСТВЕННЫЙ АГРАРНЫЙ ТЕХНИЧЕСКИЙ УНИВЕРСИТЕТ»
Кафедра ремонта тракторов
автомобилей и сельскохозяйственных машин»
по дисциплине «Организация технического сервиса»
на тему: «Организация производственного процесса
КПП трактора «Беларус-1221»
Пояснительная записка
Планировка рабочего места токаря.cdw

Окраска оборудования
Оборудование и оснастка рабочего места
Патрон 3-х кулачковый
Патрон токарный поводковый
- Токарно-винторезный
- стол приёмный передвижной;
- тара ящичная для заготовок;
- стол подъемно-поворотный;
- тумбочка инструментальная;
- планшет для документации;
- лоток для инструмента;
- светильник с кронштейном;
- тара для сбора стружки;
Рабочий и измерительный инструмент
Резец проходной прямой
Резец проходной упорный
Резец подрезной торцов.
Индикатор многооборотный
Линейка измерительная
Глубиномер индикаторный
Г И-100 ГОСТ 7661-67
Производственная мебель
Стол приёмный передвижной
Стол подъемно-поворотный
Тумбочка инструментальная
Тара для сбора стружки
- Токарно-винторезный станок 16К20;
Планировка РМ токаря
Содержание.doc
1. Режим работы и годовые фонды времени . . .. 7
2 Принципы организации производственного процесса. .10
3. Расчет параметров производственного процесса. 12 . . 2. Структура производственного процесса 16
Разработка организационных основ рабочего места токаря ..20
1. Обоснование оснащенности рабочего места токаря . 20
2. Планировка рабочего места токаря 22
2.1. Эргономические основы планировки рабочего места 22
2.2. Анализ и проектирование планировки рабочего места ..27
3. Паспорт рабочего места. 29
СПИСОК ЛИТЕРАТУРЫ . .31
Записка по ОТС.doc
Система ремонта и обслуживания МТП АПК несмотря на критику прошлых годов была довольно стройной и эффективной и имела положительные традиции. Высококвалифицированные специалисты работали на специализированных предприятиях и пунктах ТО машин. Строго учитывалась специализация тщательно подбиралось оборудование станки были разработаны прогрессивные технологии внедрялись новейшие разработки.
Однако в годы реформирования экономики страны сервисная база претерпела существенные изменения. Наблюдается переориентация сервисных предприятий на другие работы и обслуживание несельскохозяйственных потребителей. Система комплексного управления сервисной службы нарушена предприятия технического сервиса реформируются.
Поэтому в условиях дефицита сельскохозяйственной техники время заставляет искать пути подъёма сервисных предприятий оперативно и качественно выполнять ТО и Р повышать ответственность за работу. также необходимо проводить расширение реконструкцию и техническое перевооружение старых предприятий а так же вкладывать средства в строительство новых. Эффективность ремонтно-обслуживающих работ во многом зависит от структуры предприятий их производственной мощности кооперирования оснащенности и организации производства.
Основные принципы организации и параметры производственного процесса.
1. Режим работы и годовые фонды времени.
Режим работы ремонтного предприятия характеризуется количеством рабочих дней в году количеством смен работы и продолжительностью рабочей смены.
Количество рабочих дней в году (Nр.д.) определяем по формуле 1.1 [1]:
где Nв.д – количество выходных дней в году Nв.д =105;
Nп.д – количество праздничных дней Nп.д =5.
Подставляем численные значения в формулу 1.1 и находим Nр.д д:
Годовой фонд времени рабочего показывает сколько часов может отработать рабочий в течении года. Годовой фонд времени разделяют на номинальный и действительный.
Номинальным фондом пользуются при расчете явочного количества рабочих непосредственно участвующих в осуществлении производственного процесса.
Годовой номинальный фонд времени (Фн.р) при пятидневной рабочей недели рассчитываем по формуле 1.2[1]:
где tсм – длительность рабочей смены tсм =8ч;
nп.п – количество предпраздничных дней с сокращенными сменами nп.п =3д;
tск – время на которое сокращается рабочая смена в предпраздничные дни (tск =1ч).
Подставляем численные значения в формулу 1.2 и находим Фн.р ч:
Действительный фонд времени рабочего учитывает потери по отпускам и по болезни. Им пользуются при расчете количества рабочих числящихся по списку.
Действительный фонд времени при пятидневной рабочей недели рассчитываем по формуле 1.3[1]:
где dо – число дней отпуска dо =25д;
γ – коэффициент учитывающий потери времени по уважительным причинам ( γ =096-097). Принимаем γ =097.
Подставляем численные значения в формулу 1.3 и находим Фд.р ч:
Номинальный годовой фонд времени оборудования (Фо.н) рассчитываем по формуле 1.4[1]:
где С – число рабочих смен С =2.
Подставляем численные значения в формулу 1.4 и находим Фо.н ч:
Годовой действительный фонд времени оборудования (Фо.д) рассчитываем формуле 1.5[1]:
где о – коэффициент характеризующий использование оборудования по времени (учитывает потери времени на капитальный и средний ремонты оборудования) о =097 (табл. 5.1[1]).
Подставляем численные значения в формулу 1.5 и находим Фо.д ч:
Календарный фонд времени производства (Фп.) (годовой фонд времени работы предприятия) определяем по формуле 1.6[1]:
Подставляем численные значения в формулу 1.6 и находим Фп. ч:
Годовой фонд времени рабочего места определяем по формуле 1.7[1]:
где nр – количество рабочих одновременно работающих на одном рабочем месте (nр =1).
Подставляем численные значения в формулу 1.7 и находим Фрм. ч:
Таблица 1.1 Годовые фонды времени рабочего и оборудования.
Номинальный фонд времени Фн ч
Действительный фонд времени Фд ч
Годовой фонд времени рабочего
Годовой фонд времени оборудования
Годовой фонд времени рабочего места
Годовой фонд времени работ предприятия
2 Принципы организации производственного процесса.
К основным принципам организации производственного процесса
относятся: cпециализация прямоточность пропорциональность непрерывность ритмичность механизация и автоматизация. Их рациональное сочетание положено в основу построения производственных процессов при ремонте машин и их составных частей.
Специализация ремонтного производства это ограничение деятельности ремонтных предприятий ремонтом отдельных объектов выполнением определенных работ либо выполнением определенных функций обслуживания.
Специализация ремонтных предприятий (или их подразделений) в агропромышленном комплексе может быть: предметной детальной технологической функциональной.
Предметная - такая специализация при которой ремонтные предприятия специализируются на ремонте определенных машин.
Детальная - специализация при которой ремонтные предприятия специализируются на ремонте отдельных элементов готовых изделий (агрегатов деталей).
Технологическая - специализация при которой ремонтные предприятия специализируются на выполнении определенных технологических процессов или работ (сварочных наплавочных гальванических обойных и т.п.).
Функциональная - такая специализация при которой ремонтные предприятия специализируются на. выполнении определенных работ обслуживающего характера (технологическое обслуживания машин диагностирование технического состояния и т.п.)
Принцип прямоточности требует соблюдения кратчайшего пути движения предметов труда от поступления ремфонда до выпуска и отгрузки потребителя готовой продукции.
Принцип пропорциональности требует соблюдения равенства производственных возможностей взаимно связанных операционных участков поточной линии или отдельных поточных линий объему работ по заданной производственной программе.
Принцип параллельности требует параллельного (одновременного) выполнения отдельных частей производственного процесса когда в каждый момент на поточной линии обрабатывается несколько экземпляров данного изделия находящихся на разных операциях производственного процесса. Это необходимо в целях уменьшения длительности технологического цикла.
Принцип непрерывности характеризуется отсутствием перерывов в производственном процессе. В условиях поточного производства непрерывность обуславливается непрерывным движением изделий по операциям технологического процессам выполнением отдельных операций при ремонте рабочим и оборудованием без простоев.
Принцип ритмичности характеризуется выполнением взаимосвязанными производственными подразделениями за одинаковые промежутки рабочего времени одинаковых объемов работы соответствующих заданной программе.
Принцип механизации требует замены ручного труда путем использования машин и механизмов проводимых в движение двигателями.
Принцип автоматизации требует освобождения человека от управления отдельными частями производственного процесса и процесса в целом.
3. Расчет параметров производственного процесса.
Производственный процесс предприятия технического сервиса характеризуется такими параметрами как: производственная программа; такт производства; длительность производственного цикла; такт производства; длительность производственного цикла; фронт ремонта (обслуживания); пропускная способность предприятия.
Под производственной программой предприятия технического сервиса понимается годовой выпуск продукции соответствующий фактическому производству (для отчетного периода) или установленный планом (для планового периода.
Производственная программа выражается в физических единицах приведенных и в условных ремонтах а также в стоимости выражении.
Тактом производства называется время между выпуском из ремонта двух смежных объектов. С увеличением производственной программы промежуток времени между выпуском двух единиц продукции уменьшается и наоборот при уменьшении программы – увеличивается.
Такт производства (ремонта) определяется исходя из календарного фонда времени предприятия по формуле 1.8[1]:
где Фп. – годовой фонд времени предприятия Фп. =4074 ч ;
Nр – количество объектов подлежащих выпуску из ремонта за планируемый период (производственная программа предприятия) Nр = 3000 физ. рем.
Подставляем численные значения в формулу 1.8 и находим п.:
В различных цехах участках и на рабочих местах такт может быть разным но во всех случаях он должен обеспечить сохранение общепроизводственного такта.
Длительность производственного цикла – это время необходимое на ремонт объекта (машин агрегата). Она характеризуется периодом от начала первой операции по ремонту объекта до завершения последней и во многом определяется вышеизложенными принципами организации производственного процесса.
Длительность производственного цикла может быть определена аналитическим (расчетным) или графическим способом. Она зависит от трудоемкости работ и количества рабочих одновременно участвующих в производственном процессе и определяем ( tp ) по формуле 1.9[1]:
где Тр. – трудоемкость ремонта ч;
nр. – число исполнителей (рабочих) занятых на ремонте машины nр.=1 чел
Трудоемкость ремонта (Тр )определяем по формуле стр.8[1]:
где T'р – трудоемкость ремонта без коэффициента корректировки T'р =10 ч ;
Кк – коэффициент корректировки трудоемкости Кк =065.
Подставляем численные значения в формулу 1.10 и находим Tp ч.
Подставляем численные значения в формулу 1.9 и находим tp ч:
Фронт ремонта (обслуживания) характеризует число объектов одновременно находящихся в ремонте (обслуживании) на предприятии. Фронт ремонта fp определяем по формуле 1.10[1]:
Подставляем численные значения в формулу 1.11 и находим fp:
С увеличением фронта ремонта возрастает производственная площадь необходимая для организации производственного процесса.
Пропускная способность предприятия характеризуется числом объектов которое можно отремонтировать на предприятии за определенный (заданный) период времени. Ее устанавливают исходя из производительности ремонтно-сборочного участка производственные площади которого обычно ограничивают возможность увеличения выпуска машин из ремонта. Пропускную способность (WМ ) определяем по формуле 1.11[1]:
где ФРС – годовой фонд времени ремонтно-сборочного участка при работе в
nМС – количество машино-мест сборки ремонтно-сборочного участка;
С – число смен ремонтно-сборочного участка С=2;
tp – длительность производственного цикла tp = 65ч.
Подставляем численные значения в формулу 1.12 и находим WМ:
Для обеспечения равномерной (ритмичной) работы ремонтно-обслуживающих предприятий необходимо наличие производственных запасов Z включающих технологические транспортные и страховые запасы. Производственные запасы находим по формуле 1.12[1]:
Zобщ=Zтех+ Zтр+ Zстр (1.13)
где Zтех– технологические запасы шт.;
Zтр– транспортные запасы шт.;
Zстр– страховые запасы шт.
Технологические запасы численно равны фронту ремонта определяемого по формуле 1.11:
Zтех=fp=tp п=479 (1.14)
Транспортные запасы характеризуют количество объектов ремонта и готовой продукции находящихся в состоянии транспортировки от заказчика на ремонтное предприятие и обратно. По формуле 1.14[1] находим транспортные запасы Ттр :
где Ттр– среднее время доставки объектов на ремонтное предприятие и обратно ч (принимаем Ттр=3 ч.)
Подставляем численные значения в формулу 1.15 и находим Zтр:
Страховые запасы (Zстр ) – это запасы объектов ремонта необходимость которых обусловливаются неравномерностью поступления ремонтного фонда вызванной сезонностью сельскохозяйственных работ.
Установлено что для равномерной загрузки предприятия с учетом специфики сельскохозяйственного производства необходимо иметь значительные страховые запасы (25-30% от программы) что обусловливает необходимость рационального комплектования производственной программы ремонтно-обслуживающего предприятия [1].
На основании вышеизложенного Zстр =25% Nр = 0253000 =750
Подставляем численные значения в формулу 1.13 и находим Zобщ:
Zобщ=479+ 221+ 750=757 шт.
Структура производственного процесса.
Под производственным процессом ремонта машин понимаются действия людей и орудий производства проводимые для получения работоспособной машины из частично утративших работоспособность но ремонтнопригодных составных частей.
Производственный процесс на ремонтных предприятиях отличается высоким уровнем сложности что является следствием конструктивных и технологических особенностей современных машин большой номенклатурой деталей разнообразием регулировок различной их стабильностью а следовательно сложностью восстановления деталей и машины в целом.
Производственный процесс протекает при наличии находящихся в рациональном сочетании трудовых ресурсов и предметов труда в виде ремонтного фонда сырья и материалов.
Производственный процесс на ремонтных предприятиях состоит из целого ряда частичных процессов характеризующихся определенной законченностью работ по ремонту машин.
К частичным процессам относят восстановление и изготовление отдельных деталей мойку разборку сборку механизмов и узлов окраску и обработку машины.
Выделяют следующие фазы производственного процесса: заготовительную обработочную сборочную.
Заготовительная фаза ремонтного производства наряду с изготовлением поковок отливок сварочных конструкций пластмассовых заготовок включает в себя процессы подготовки ремонтного фонда к обработке и другие заготовительные работы.
Обработанная и сборочная фазы ремонтного производства аналогичны соответствующим фазам машиностроительного производства.
Частичные процессы подразделяются на основные и вспомогательные.
Основные технологические процессы обеспечивают изменение форм и размеров деталей их физико-механических свойств и качества. Например? Шлифование снятие старого лакокрасасочного покрытия окраска. Различные способы восстановления деталей мойка.
Вспомогательные процессы связаны с обслуживанием и бесперебойным функционирование основных процессов. Результатом вспомогательных процессов является производство электроэнергии воды. Пар сжатого воздуха. К вспомогательным процессам так же относятся изготовление оснастки инструмента транспортировка и хранение ремонтного фонда готовой продукции и др.
Основные технологические процессы на ремонтных предприятиях протекают и осуществляются при непосредственном трудовом участии рабочих использующих средства труда.
На предприятиях по ремонту машин так же имеют место естественные процессы: сушка окрашенных изделий протекающие под наблюдением и контролем человека.
Таким образом основной технологический процесс состоит из трудовых и естественных процессов.
С внедрением методов принудительной сушки созданием контролируемой среды в которой протекают естественные процессы они все более приближаются к трудовым.
Структура производственного процесса на ремонтном предприятии приведена на рис. 2.1.
Рис. 2.1 Структура производственного процесса на ремонтном предприятии
Основной технологический процесс подразделяется на технологические операции.
Технологическая операция - это часть технологического процесса производства. Она представляет собой процесс труда рабочего или группы рабочих осуществляемый на одном рабочем месте над объектом производства с использованием определенного комплекта оборудования.
Технологически обоснованный комплекс технологических операций и естественных процессов образует технологический процесс производства. Технологический процесс включает в себя как трудовые процессы так и естественные сочетание и взаимосвязь которых определяются конкретной технологией ремонтного производства.
Исходя из изложенного производственный процесс ремонта машин представляет собой совокупность технологических и вспомогательных процессов образующих частичные процессы протекающие в соответствующих фазах в результате осуществления которых обеспечивается восстановление работоспособности узлов агрегатов машины в целом.
Процесс ремонта машин на современных предприятиях протекает в виде частичных процессов подготовки ремонтного фонда к восстановлению (заготовительная фаза) технологического восстановления двигателей коробок перемены передач кабин отдельных деталей (обработочная фаза) сборки узлов и деталей в агрегаты и сборки машин в целом (сборочная фаза).
Частичные процессы например в обработочная фазе- это основные технологические процессы восстановления гильз цилиндров блоков головок и вспомогательные процессы обеспечения рабочих мест электрической энергии инструментами специальной оснасткой сжатым воздухом.
Основные технологические процессы подразделяются на операции6 растачивание гильз под ремонтный размер хонингование гильз шлифование коленчатых валов динамическая балансировка восстановление кабин их окраска последующая сушка и т. д. Операция сушки без применения специальных камер будет составлять часть естественного процесса.
Современное ремонтное производство представлено предприятиями различного уровня механизации и автоматизации производства. Те или иные технологические операции на одних предприятиях выполняются вручную в то время как на других они механизированы.
По способу воздействия на предмет труда (деталь узел агрегат. машину) все технологические и вспомогательные операции классифицируются на следующие группы.
Ручные операции. Эта группа операций выполняется вручную с использованием простейших инструментов. К таким операциям относятся: разборка и сборка узла или машины если при этом не применяется механизированный инструмент(с электроприводом с пневмоприводом и т. д.)
Машинно-ручные операции отличаются от ручных тем что рабочий при выполнении работ использует механизированный инструмент подъемно-транспортное или технологическое оборудование. Примером машинно-ручных операций служат: транспортировка ремонтного фонда разборка и сборка машины с применением механизированного инструмента восстановление деталей на станках при непосредственном трудовом части рабочего осуществляющего ручную подачу и другие трудовые действия.
Машинные операции в отличие от машинно-ручных выполняются на станках стендах и другом ремонтно-технологическом оборудовании при участии рабочего в установке деталей узлов контроле за ходом технологического процесса регулировании режимов обработки мойки и т. д.
Автоматизированные операции характеризуются выполнением работ без затрат физического труда рабочих. Они осуществляются на автоматах контроль за которыми выполняет рабочий-оператор. В ремонтном производстве автоматизированные операции принимают на струйной наружной мойке в закрытой камере на мойке деталей в моечных установках.
Резкой грани между отдельными группами операций разграниченных по указанному признаку нет. По мере развития производства с внедрением новой техники повышением уровня механизации и автоматизации производства удельный вес ручных операций будет уменьшаться. А машинных и автоматизированных расти.
Разработка организационных основ рабочего места токаря.
1. Обоснование оснащенности рабочего места токаря.
Рабочим местом называется участок производственной площади цеха на котором расположен станок с комплектом приспособлений вспомогательного и режущего инструмента технической документации и других предметов и материалов находящихся непосредственно в распоряжении токаря. Оснащенность рабочего места и организация труда на нем в значительной мере определяют производительность труда токаря. Рабочее место оснащается: одним токарно-винторезным станком модели 16К20 с постоянным комплектом принадлежностей; комплектом технологической оснастки постоянного пользования состоящим из приспособлений режущего измерительного и вспомогательного инструмента; комплектом технической документации постоянно находящейся на рабочем месте (инструкции справочники вспомогательные таблицы и т. д.); комплектом предметов ухода за станком и рабочим местом (масленки щетки крючки совки обтирочные материалы и т. д.); инструментальным шкафом подставкой планшетам стеллажами и т. п.; передвижной и переносной тарой для заготовок и изготовленных деталей; подножными решетками табуретками. Комплект технологической оснастки и комплект предметов ухода за станком и рабочим местом постоянного пользования.
Правильная организация рабочего места - это такое содержание станка такой порядок расположения приспособлений инструмента заготовок и готовых деталей при котором достигается наивысшая производительность труда при минимальных затратах физической нервной и умственной энергии рабочего. На рабочем месте не должно быть ничего лишнего т. е. не используемого в работе. Все используемые при работе предметы должны иметь постоянные места хранения а те предметы которые используются чаще должны располагаться ближе и в более удобных местах. Создание условий обеспечивающих возможность рационального использования станка его оснащения рабочего времени производственных навыков и творческих способностей рабочего является основной задачей научной организации труда на рабочем месте токаря. Научная организация труда (НОТ) - это система мероприятий направленных на внедрение в практику методов и форм организации труда основанных на достижениях науки и передового производственного опыта и проводимых в целях достижения наиболее высокой производительности труда при одновременном создании благоприятных условий для уменьшения утомляемости и сохранения здоровья рабочего-станочника.
К организации производства на рабочем месте предъявляются следующие основные требования: создание условий для высокопроизводительной работы; механизация и автоматизация производственного процесса максимально устраняющая применение ручного труда; ритмичное снабжение рабочего места сырьем и материалами; повышение квалификации рабочего и обучение его передовым приемам труда; безопасность работы; воспитание у рабочего коммунистического отношения к труду и чувства товарищеской взаимопомощи. Правильная организация рабочего места оказывает заметное влияние на сокращение вспомогательного времени затрачиваемого на выполнение отдельных операций. Удобное расположение необходимых для работы инструментов и приспособлений обеспечивает производительную работу станочника при меньшей его утомляемости.
В процессе труда токарь на рабочем месте в ремонтной мастерской выполняет следующие технологические операции приложение 1 стр. 36[1]:
- обтачивание наружных цилиндрических (конических) поверхностей торцов;
- подрезание наружных канавок и отрезание;
- сверление рассверливание и центрирование;
- растачивание зенкование и развертывание цилиндрических отверстий;
- фрезерование лысок шпонок.
Для выполнения токарных работ выбираем следующий инструмент и приспособления:
) мерительный инструмент:
- измерительная линейка;
- приспособление для фрезерования;
) рабочий инструмент:
Для выполнения токарных работ выбираем станок токарно-винторезный 16К20 в соответствии с рекомендациями приложения 1 [1].
2. Планировка рабочего места токаря.
2.1 Эргономические основы планировки рабочего места.
В системе мероприятий по организации рабочего места токаря ремонтно-обслуживающего предприятия существенное значение имеет обеспечение рациональной его планировки. Под планировкой рабочего места понимают целесообразное пространственное размещение (в горизонтальной и вертикальной плоскостях) функционально взаимоувязанных средств производства – оборудования оснастки и других средств предметов труда и человек.
Расположение средств и предметов труда в оптимальной или менее удобной зонах рабочего места определяет состав трудовых движений их количественные и качественные характеристики площадь рабочего места. Внедрение и закрепление передовых приемов и методов труда устранение лишних и нерациональных трудовых движений максимальное сокращение перемещения самого токаря и материальных элементов трудового процесса основываются на обязательном совершении планировки рабочего места токаря. Нарушение принципов размещения средств и предметов труда приводит к ненужным хождениям наклонам поворотам увеличению траекторий движений их усложнению. В результате снижается эффективность труда повышается утомляемость рабочего увеличиваются потери рабочего времени.
Планировка рабочего места вследствие этого является технологической основой рационализации методов и приемов труда предпосылкой обеспечения наиболее благоприятных и безопасных условий труда.
Экономическое значение рациональной планировки рабочего места определяется также ее ролью в обеспечении экономии производственной площади.
Методологическая основа научно обоснованной планировки – обеспечение ее соответствия эргономическим свойствам человека. Эргономические требования к планировке рабочих мест устанавливаются с целью обеспечения оптимизации эффективности трудовой деятельности человека. Они предусматривают исследование оптимальности рабочей позы трудовых движений дыхательных функций восприятия внимания. Размещение средств и предметов труда должно обеспечивать научно обоснованные зоны досягаемости рабочую позу и оптимальные зоны обзора допустимые для токаря [1]:
Затраты физических усилий ( прил.2 таб.П.2.1) - группа тяжести труда - III
Темп работы ( прил.2 таб.П.2.2) – темп работы – невысокий
Моноторность работы ( прил.2 таб.П.2.3) – средняя
Освещенность рабочего места ( прил.3 ) – 300 люксов
Температура воздуха в зоне рабочего места ( прил.3 ) :
- в холодный период и переходной – 17 19 °С
- в теплый период – 28 23 °С
Относительная влажность воздуха в зоне рабочего места – 30 60 %
Скорость движения воздуха ( прил.3 ) – не более 05 м в сек
Уровень шума в зоне рабочего места ( прил.3 ) - 30 60 ДБ
Содержание вредных веществ в воздухе в зоне рабочего места (мгм3) не более ( прил.3 ) : - окиси углерода – 20 мгм3
- пыли не токсичной – 10 мгм3
- пыли содержащей до 2%
карбида кремния – 6 мгм3
Эргономические требования к планировке рабочего места – важный фактор формирующий оптимальное соответствие элементов комплексной системы
«человек-машина-среда». Они достигаются размещением материальных элементов производства и человека в соответствии с его свойствами - антропометрическими биомеханическими психофизиологическими – на основе обеспечения оперативного пространства позволяющего свободное осуществление необходимых трудовых манипуляций; формирования рациональных рабочих зон и зон досягаемости с учетом антропометрических данных при разных рабочих позах в горизонтальной и вертикальной плоскостях; регулирования удаленности объекта работы от глаз в зависимости от характера выполняемого трудового процесса с учетом угла границ угла зрения и зон обзора; физических зрительных и слуховых связей между исполнителем и оборудованием а также между исполнителями и оборудованием а также между исполнителями; рационального размещения средств защиты по устранению или уменьшению неблагоприятных условий труда и техники безопасности; безопасных проходов [7].
При организации трудового процесса на рабочем месте учитываем зоны обзора углы зрения и видимости рис. 3.1[1].
Наиболее важные органы управления (рычаги кнопка аварийного выкл. и т. д.) и контроля оборудования должны находится в оптимальных зонах обзора с учетом угла зрения при работе «сидя» и «стоя».
Рациональное расстояние от предмета обработки до глаз токаря должно быть 450 мм. В горизонтальной плоскости угол зоны обзора в границах которой человек отчетливо воспринимает форму предмета составляет 120°. Угол мгновенного зрения в рабочей зоне равен 18° угол эффективной видимости - 30°. При поворотах головы угол обзора на рабочем месте составляет 220° [1].
При расположении органов контроля обеспечиваем учет латентного периода (скорости реакции).
Простая сенсомоторная реакция представляет собой ответное элементарное движение человека на заранее известный но внезапно появившийся сигнал с возможной максимальной скоростью.
Наибольшее влияние на время реакции (латентный период) оказывает тип раздражителя его интенсивность и периодичность состояние оператора и другие факторы.
Средняя величина скорости реакции для различных раздражителей и анализаторов приведена в табл. 3.1[1].
Планировка рабочего места должна обеспечивать возможность его эффективного обслуживания.
Возможность свободных нестесненных трудовых манипуляций токаря в соответствии с его антропологическими данными – важное условие требований эргономики. Оно достигается учетом пространства занимаемого токарем и формирования рабочих зон с учетом антропометрических и биомеханических свойств человека при различных рабочих позах.
Далее разрабатываем планировку оборудования рабочего места и размещения предметов предметов труда с учетом требований физиологических санитарногигиенических и эстетических условий.
В первую очередь обеспечим удобную позу токарю. С этой целью основное оборудование и производственную мебель устанавливаем на строго определенной высоте равной 1050мм при положении токаря – стоя для среднего роста человека табл.3.2[1].
Оборудование производственную мебель и предметы труда размещаем таким образом чтобы трудовые движения концентрировались в пределах оптимальных зон деятельности и обзорности.
При расположении органов управления и индикации инструментов и предметов труда для наиболее целесообразного использования каждого участка рабочей зоны обеспечим их комплексную оценку в соответствии с физиологическими и психофизиологическими свойствами человека.
Это достигается микроклассификацией рабочего пространства в горизонтальной и вертикальной плоскостях. Ее графическое изображение в горизонтальной плоскости приведено на рис.3.2[1].
Микроклассификация обеспечивает характеристику каждого участка в соответствии с досягаемостью выполнения трудовых манипуляций и зонами обзора. Рекомендуемые рабочие зоны в зависимости от условий применения органов управления и характера управления приведены на рис. 3.2[1] и табл.3.3 3.4[1] по которым мы выбираем (руководствуемся) наиболее приемлемые позы зоны движения и зону обзора для токаря.
Графическое изображение микроклассификации рабочего пространства в вертикальной плоскости приведено на рис. 3.3[1].
Планировка рабочего места должна обеспечивать минимальное перемещение рабочего и предмета труда в процессе его обработки на данном месте(в горизонтальной и вертикальной плоскостях). Этим обуславливается максимальная производительность труда и минимальная утомляемость работающих.
Условием обеспечения соответствия планировки эргономическим требованиям является также установление физиологически оптимальной рабочей позы. Она формируется размерными соотношениями всех элементов составляющих рабочее место и в особенности размерами рабочей зоны; величиной требуемых рабочих усилий их характером (динимечиским статическим); необходимыми переделами обзора; необходимой точностью выполнения операции напряженностью зрения.
Основными критерием рациональности размещения в вертикальной плоскости наряду с количеством движений является установление правильной рабочей позы то есть рабочего положения вызывающего минимальную утомляемость работника. Она должна обеспечивать прямую осанку и возможности смены поз; удобство положения туловища головы конечностей; оптимальный обзор зоны работы свободу манипуляцией и удобное расположение по высоте органов управления станка.
При проектировании размещения средств и предметов труда в вертикальной плоскости прежде всего обосновывается рабочее положение: «сидя» «стоя» или их сочетание. В основе его выбора лежат характеристики физических усилий необходимых для выполнения работы ее темп и характер размах движений. Так при выполнении работ с усилиями до 5 кг наиболее целесообразна рабочая поза «сидя» при значительном усилии (10-20 кг)- «стоя» а при работе требующей усилии порядка 5-10кг возможна переменная рабочая поза «сидя-стоя». При невысоком темпе работы и небольшом размахе движений рекомендуется рабочее положение «сидя»; при большом количестве движений размах которых превышает 1м по фронту. 300мм в глубину и 400 мм от поверхности рабочей зоны- «стоя»; при работах. Требующих большой точности которые можно выполнять двумя руками- «сидя» при профилактических работах и наблюдении за оборудованием-«сидя-стоя» [1].
Целесообразность выбора рабочего положения определяется на основе учета комплекса факторов характерных для данного рабочего места.
Анализируя выше перечисленные примеры определения рабочей позы для токаря выбираем положение «стоя» т. к. работа за станком требует в основе своей именно это рабочее положение.
Исследования физиологов показали что более утомительной их рассмотренных поз является рабочая поза «сидя-стоя». При ней рабочему приходится затрачивать дополнительную энергию на поддержание тела в вертикальном положении. Так если принимать нагрузку при прямой рабочей позе «сидя» за 1 то при прямой рабочей позе «сидя» она составит 16.
Величина затрат энергии определяется вариантами основных рабочих положений в зависимости от положения корпуса. Так при наклонной рабочей позе «сидя» нагрузка возрастает в 4 раза по сравнению с прямой а при наклонной позе «стоя»- в 10 раз.
Наиболее физиологически обоснованным является рабочее положение
«сидя-стоя» обеспечивающее наименьшее утомление за счет регулирования нагрузок на разные группы мышц.
Неправильная рабочая поза вызывает ускоренное наступление утомляемости и в отдельных случаях профессиональное заболевания. При невозможности их рационализации следует установить соответствующий режим труда и отдыха и применить профилактические меры против профзаболеваний.
Таким образом при размещении предметов и средств труда на рабочем месте руководствуемся следующими правилами:
на рабочем месте должно находиться все необходимые для работы и не должно быть лишнего;
то что требуется для работы чаще должно располагаться ближе к рабочему;
все что берется левой рукой. должно располагаться слева и наоборот;
руки рабочего должны быть свободны от выполнения поддерживающих операций;
предметы используемые последовательно должны располагаться рядом чтобы можно было использовать обратное движение рук;
все предметы должны располагаться в зоне деятельности рук рабочего;
там где позволяет характер работы на рабочем месте должен предусматриваться стул а также выполнение работы в попеременной позе - сидя и стоя;
с учетом массы обрабатываемых деталей (узлов. агрегатов) рабочее место должно быть оборудовано подъемными средствами;
внешнее оформление рабочего места должно соответствовать требованием технической эстетики (приложение 4 [1]).
Эргономические требования к планировке рабочего места охватывают также и установление проходов и проездов обеспечивающих нормальные условия работы. Их величина зависит от производственных условий: проходы между оборудованием для одного или двух человек проезды для внутрицехового транспорта и т. д.
2.2 Анализ и проектирование планировки рабочего места.
Анализ планировки рабочего места охватывает работы по выявлению возможностей наиболее целесообразно расположения оборудования инструмент приспособлений тары и другой технической и организационной оснастки с целью более экономического использования производственных площадей сокращения переходов рабочих и расстояний перемещения на рабочем месте сырья материалов полуфабрикатов и готовой продукции обеспечения рабочему удобной позы и возможности применения передовых приемов и методов труда.
В основе анализа лежит непосредственное целевое изучение пространственного размещения материальных элементов труда а также использование данных фотографий рабочего дня и хронометража для выявления потерь времени связанных с нерациональной планировкой рабочего места.
В этой связи при анализе используем следующие рекомендации последовательности работ [1]:
Изучение технической взаимосвязи рабочего места со смежными выявление основных решений по обеспечению его пространственной связи с другими определение длины и характера транспортировки предметов труда и передвижений рабочего по обслуживанию рабочего места определение протяжности и направления грузопотоков объема перемещаемых грузов.
Оформление схемы размещения средств производства и передвижения рабочего по участку.
Изучение отчетных показателей и данных наблюдений характеризирующих потери рабочего времени связанные с нерациональной планировки рабочих мест на участке.
Изучение расположения предметов и средств труда выявления структуры трудовых действий длины и траектории трудовых движений. Установление основных факторов их определяющих вычерчивание в определенном масштабе планировки отдельных поверхностей рабочего места.
Изучение размещения человека оборудования оснастки на рабочем месте выявление маршрутов передвижения рабочего внутри него определение расстояния протяжности перехода и составление схемы планировки рабочего места в горизонтальной и вертикальной плоскостях.
Планировка рабочего места зависит от многих факторов в том числе от типа станка и его размеров размеров и формы обрабатываемых заготовок типа и организации производства и др. Чаще применяются планировки рабочего места двух типов. По первому типу планировки инструментальный шкаф (тумбочка) располагается справа от рабочего а стеллаж для деталей - слева. Такая планировка является рациональной если преобладает обработка заготовок с установкой в центрах левой рукой. По второму типу планировки инструментальный шкаф (тумбочка) располагается с левой стороны от рабочего а стеллаж - с правой. Такая планировка рабочего места удобна при установке и снятии заготовки правой рукой или двумя руками (при изготовлении длинных и тяжелых деталей). Таким образом проанализировав вышеизложенное разрабатываем планировку по второму типу т. к. на наш взгляд является более рациональным.
Перед станком на полу укладывают деревянную решетку. Высоту расположения решеток выбирают в зависимости от роста рабочего.
В верхнем ящике инструментального шкафа хранят чертежи технологические карты рабочие наряды справочники измерительные инструменты в среднем — резцы сгруппированные по типам и размерам. Ниже последовательно располагают режущие инструменты переходные втулки центры хомутики подкладки. В самое нижнее отделение укладывают патроны а также кулачки к ним. Не следует загромождать шкаф излишним запасом инструмента: все необходимое для работы лучше получать в начале смены из кладовой. Перед началом работы все предметы которые берут правой рукой располагают справа от рабочего; а предметы которые берут левой рукой — слева; предметы которыми пользуются чаще (например ключ патрона) кладут ближе к рабочему чем предметы которыми пользуются реже например ключ резцедержателя). Часто применяемые ключи и подкладки укладывают на лоток который помещают на передней бабке станине или на специальной стойке.
Сохранность и готовность оборудования к безотказной и производительной работе обеспечиваются повседневным уходом за рабочим местом. Рабочее место важно всегда содержать в чистоте так как грязь и беспорядок приводят к потере рабочего времени браку несчастным случаям простою и преждевременному износу станка. Пол на рабочем месте должен быть ровным и чистым не иметь подтеков масла и смазочно-охлаждающей жидкости. Рабочее помещение оборудуется устройствами для удаления загрязненного воздуха и притока свежего.
Большое значение для длительной и бесперебойной работы станка имеет своевременная и правильная его смазка в соответствии с требованиями изложенными в руководстве по эксплуатации. Смазка станка является прямой обязанностью токаря. Периодически токарь должен производить проверку точности работы станка и его регулировку в соответствии с указаниями руководства по эксплуатации. Плохая организация рабочего места загроможденность рабочего места и проходов неисправность станка и приспособлений недостаточное знание рабочим устройства станка и правил его эксплуатации неисправность электрооборудования и электропроводки отсутствие ограждений и предохранительных устройств работа неисправным инструментом загрязненность станка и подножной решетки могут привести к несчастным случаям.
Температура воздуха в цехе должна быть 15 - 18 градусов С.
Для достижения высокой производительности труда при наиболее полном использовании технических возможностей производственного оборудования и при нормальной физической нагрузке работающего организация рабочего места должна отвечать требованиям научной организации труда (НОТ).
Научная организация труда предусматривает: рациональную планировку рабочего места; оснащение рабочего места необходимым комплектом инвентаря приспособлений режущего и измерительного инструмента; своевременную подачу необходимого количества заготовок на рабочее место и вывоз готовых деталей или перемещение их на соседнее рабочее место; своевременный контроль деталей контролером отдела технического контроля (ОТК); четкую организацию получения и сдачи инструментов их своевременную заточку; своевременное обеспечение технической документацией (чертежами операционными картами рабочими нарядами); использование наиболее рациональных режимов резания.
В процессе работы токарь должен быть предельно внимательным так как станок является объектом повышенной опасности. Для безопасной работы необходимо знать устройство всех сборочных единиц (узлов) и механизмов станка правильно назначать режим резания надежно крепить заготовку применять исправный инструмент со стружколомами защитные устройства и т. д.
Токарь обязан обслуживать свое рабочее место: ежедневно убирать станок и околостаночное пространство проводить очистку смазочно-охлаждающей жидкости и т.д.
На основе анализа и с учетом вышеизложенных требований разрабатываем планировку рабочего места токаря которую вычерчиваем на листе графической части формата А2.
Данном курсовой проект разработан по теме «Организация производственного процесса ремонта КПП трактора «Беларус 1221».
В 1-ом разделе курсового проекта были рассмотрены основные принципы организации и рассчитаны параметры производственного процесса. В частности по исходным данным задания были произведены расчеты режима работы и годовые фонды времени (годовой фонд времени годовой фонд времени оборудования годовой фонд времени рабочего места годовой фонд времени предприятии) а так же параметры производственного процесса (такт производства длительность производственного цикла фронт ремонта пропускная способность производственные запасы).
Во 2-ом разделе «Структура производственного процесса» рассмотрели отличительные особенности структуры производственного процесса на ремонтно-обслуживающих предприятиях.
В 3-ем разделе «Разработка основ рабочего места» была разработана и проанализирована планировка рабочего места слесаря с учетом эргономических основ и требований техники безопасности. А так же был разработан паспорт рабочего места.
В целом курсовой проект вобрал в себя большую часть знаний и навыков полученных нами в теоретическом курсе ОТС что помогло на конкретном примере закрепить их.
Организация технического сервиса: методические указания. к.т.н. профессор В. П. Миклуш к.т.н. доцент П.Е. Круглый; БГАТУ 2007 – 52 с.
СТП БАТУ 01.01-96. Указания по оформлению документов курсовых и дипломных проектов. – Минск : БГАТУ 1996. – 198 с.
Ремонт машин. Курсовое и дипломное проектирование: учеб. пособие В. П. Миклуш [и др.]. – Минск : БГАТУ 2004. – 490 с.
Миклуш В.П. Организация технического сервиса в АПК: монография Минск : БГАТУ 2004 – 290 с.
Организация ремонтно-обслуживающего производства и проектирование предприятий технического сервиса АПК: учеб. пособие В. П. Миклуш Т.А. Шаровар Г.М. Уманский; под ред. В.П. Миклуша. – Минск: Ураджай 2001. – 662 с.
Практикум по организации ремонтно-обслуживающего производства в АПК: В. П. Миклуш [и др.]; под ред. В.П. Миклуша. – Минск: – Минск: БГАТУ 2003. – 276 с.
Организация рабочих мест на ремонтно-обслуживающих предприятиях: метод. указания к курсовому и дипломному проектированию и практическим занятиям сост. В.П. Миклуша П.Е. Круглый. – Минск: БГАТУ 1998. – 42 с.
Проектирование ремонтно – обслуживающих предприятий АПК: метод. пособие к курсовому и дипломному проектированию сост. Г.Ф. Бетеня [и др.]. - Минск : БГАТУ 1998 – 144 с.
Нормы технологического проектирования ремонтно-обслуживающих предприятий: метод. указания к курсовому и дипломному проектированию и практическим занятиям сост. Г.Ф. Бетеня [и др.]. – Минск: БГАТУ 1997- 37с.
Рекомендуемые чертежи
Свободное скачивание на сегодня
Другие проекты
- 25.01.2023