Метрология




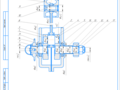
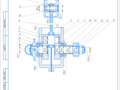
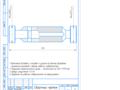
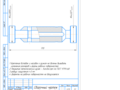
- Добавлен: 24.01.2023
- Размер: 2 MB
- Закачек: 0
Описание
Состав проекта
![]() |
![]() |
![]() |
![]() ![]() ![]() ![]() |
![]() |
![]() |
![]() ![]() ![]() ![]() |
![]() |
![]() ![]() ![]() ![]() |
![]() ![]() ![]() |
![]() ![]() ![]() ![]() |
![]() |
![]() |
![]() ![]() ![]() ![]() |
![]() |
![]() ![]() ![]() ![]() |
![]() |
![]() ![]() ![]() |
![]() ![]() ![]() ![]() |
![]() ![]() ![]() ![]() |
![]() |
![]() ![]() ![]() ![]() |
![]() |
![]() |
![]() ![]() ![]() ![]() |
Дополнительная информация
Д 12испр.cdw

6,1.cdw

6,1испр.cdw

6 ltnfkm.cdw

6.испр.cdw

пробка.cdw

ДВС-00.00.00.00 СБ - Двигатель.cdw

ДВС-00.00.00.00 СБ .cdw

пробкасб.cdw

Д 12.cdw

Рекомендуемые чертежи
- 16.03.2022
- 01.07.2014