Метрология расчеты для раздаточной коробки передач автомобиля Урал 375


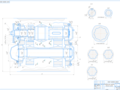
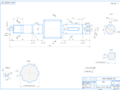
- Добавлен: 24.01.2023
- Размер: 3 MB
- Закачек: 0
Узнать, как скачать этот материал
Подписаться на ежедневные обновления каталога:
Описание
Метрология расчеты для раздаточной коробки передач автомобиля Урал 375
Состав проекта
![]() |
![]() |
![]() ![]() ![]() |
![]() ![]() ![]() |
![]() ![]() ![]() |
![]() ![]() ![]() |
![]() ![]() ![]() |
![]() ![]() ![]() |
![]() |
![]() |
![]() |
![]() ![]() ![]() ![]() |
![]() ![]() ![]() ![]() |
![]() ![]() ![]() |
Дополнительная информация
Контент чертежей
Вал.cdw

Сборочный чертёж11.cdw

Рекомендуемые чертежи
Свободное скачивание на сегодня
Обновление через: 6 часов 59 минут